Учебное пособие для студентов среднего профессионального образования Специальность 1701 "Монтаж и техническая эксплуатация промышленного оборудования (по отраслям)"
Вид материала | Учебное пособие |
- Учебное пособие для студентов нефтехимических колледжей и техникумов Специальность, 3210.24kb.
- Программа и контрольные задания для студентов заочного отделения Специальность: 1701, 688.94kb.
- Государственный образовательный стандарт среднего профессионального образования государственные, 1346.06kb.
- Федеральный государственный образовательный стандарт среднего профессионального образования, 1074.58kb.
- Методические указания и контрольные задания для студентов заочной формы обучения гоу, 2389.4kb.
- Методические указания и контрольные задания для студентов заочного отделения специальность:, 848.08kb.
- «Материаловедение», 179.95kb.
- Формирование профессионально-значимых качеств личности в условиях личностно-ориентированного, 51.94kb.
- Система управления качеством подготовки техников по специальности 150411 – Монтаж, 102.4kb.
- Примерная программа профессионального модуля проведение подземного ремонта скважин, 226.39kb.
Шлифование плоских и цилиндрических
поверхностей
Оснащение рабочего места: плоскошлифовальный станок модели ЗГ71 или другой аналогичной модели с прямоугольным столом, приспособления, магнитная (или электромагнитная) плита; плакаты общего вида и кинематической схемы плоскошлифовального станка, приемов шлифования и контроля заготовок, контрольно-измерительный инструмент; заготовки для настройки станка и пробных проходов; принадлежности для уборки, смазки и ухода за станком; очки защитные.
Станки для плоского шлифования по принципу работы делятся на шлифующие периферией и торцом круга; по форме стола и характеру его движения - с возвратно-поступательным и вращательным движением стола. Наибольшее распространение в серийном производстве, а также в учебных мастерских техникумов получили плоскошлифовальные станки с прямоугольным столом и горизонтальным шпинделем для шлифования заготовок периферией круга моделей ЗГ71, ЗБ722 и др.
Основные механизмы плоскошлифовальных станков: привод вращения шлифовального круга, представляющий собой фланцевый или встроенный электродвигатель, расположенный соосно со шпинделем круга, и привод продольной, поперечной и вертикальной подач.
Продольное перемещение стола в большинстве моделей станков осуществляется гидравлическим цилиндром, шток которого соединен непосредственно со столом. Скорость продольного перемещения стола имеет бесступенчатое регулирование. Периодическая поперечная подача предназначена для поперечного перемещения шлифовальной бабки и осуществляется за каждый одинарный или двойной ход стола в процессе шлифования. Поперечное перемещение задается в долях ширины шлифовального круга. Для правки шлифовального круга и установочных перемещений шлифовальной бабки имеется непрерывная поперечная подача. Вертикальная подача на глубину резания осуществляется автоматическим перемещением шлифовальной бабки. Станки также имеют вертикальное ускоренное перемещение круга.
На рис. 5.16 показан универсальный плоскошлифовальный станок модели ЗГ71. На станине (основании) станка в поперечном направлении перемещается крестовый стол. Верхняя часть стола от гидравлического цилиндра, расположенного между его направляющими, перемещается в продольном направлении. В нижней части стола расположены механизмы продольного и поперечного перемещения и реверсирования стола, а также распределительная и гидравлическая панели. С задней стороны станка установлена стойка, по вертикальным направляющим которой перемещается шлифовальная бабка.
Главное движение резания или вращательное движение шпинделя шлифовального круга осуществляется от электродвигателя через ременную передачу и имеет частоту вращения 2700 об/мин. При работе новым шлифовальным кругом диаметром 250 мм скорость главного движения резания

При работе наиболее изношенным шлифовальным кругом диаметром 150 мм минимальная скорость главного движения резания

Следовательно, по мере износа шлифовального круга скорость главного движения резания уменьшается.
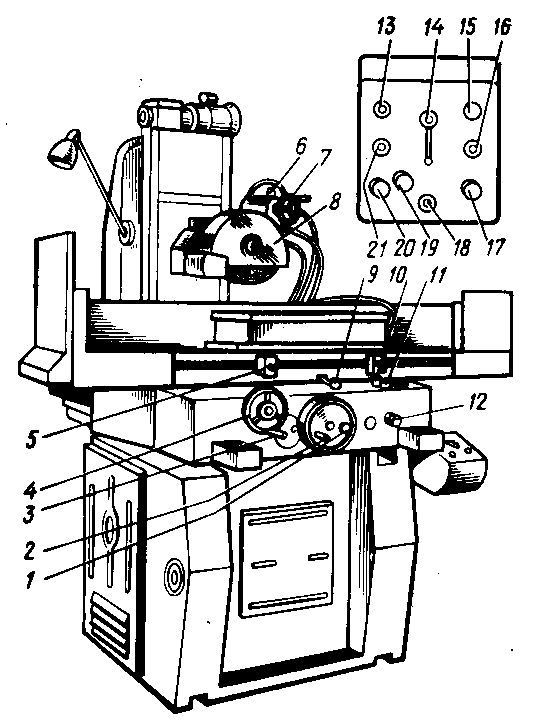
1-лимб ручной поперечной микрометрической подачи стола; 2-маховичок ручного поперечного движения подачи стола; 3-лимб установки величины автоматической поперечной скорости подачи стола; 4-маховичок продольного ручного перемещения; 5-упоры продольного реверсирования стола; 6-рукоятка установки величины автоматической вертикальной подачи; 7-маховичок ручного вертикального движения подачи; 8-предохранительный кожух шлифовального круга; 9-рукоятка ручного продольного реверсирования стола; 10-рукоятка скорости движения стола; 11-рукоятки «Пуск стола» и «Разгрузка гидропривода»; 12-кнопка включения и реверсирования поперечного движения подачи; 13-кнопка выключения «Все стоп»; 14-барабанный переключатель ускоренного перемещения шлифовальной головки; 15-кнопка «Стоп гидропривода»; 16-кнопка «Пуск гидропривода»; 17-переключатель режима работы «С плитой» и «Без плиты»; 18-сигнальная лампочка «Станок включен»; 19-переключатель освещения; 20-кнопка-переключатель магнитной плиты; 21-кнопка «Пуск шпинделя»
Рисунок 5.16 Общий вид и органы управления плоскошлифовального станка модели ЗГ71
Упражнения. Для усвоения пройденного материала по устройству плоскошлифовальных станков, расположению основных органов управления станком, закреплению навыков по настройке на заданный режим работы и управлению станком учащиеся выполняют несколько упражнений по управлению плоскошлифовальным станком в различных режимах шлифования (по указанию мастера).
Тренировочные упражнения по наладке и работе на плоскошлифовальном
станке с прямоугольным столом
На этом занятии учащийся должен настроить плоскошлифовальный станок с прямоугольным столом, работающий периферией круга, выполнить обработку различных плоских заготовок, закрепляемых на магнитной плите и в специальных приспособлениях (на призмах, в рамках и т. п.), и произвести контрольные измерения прошлифованных деталей.
Наладка плоскошлифовального станка во многом схожа с наладкой круглошлифовальных станков и заключается в выполнении следующих приемов:
1. Выбрать шлифовальный круг для данной модели станка и заданных условий обработки: форму и габаритные размеры круга, абразивный материал, номер зерна и индекс зернистости, твердость, структуру, связку и класс круга.
2. Установить и закрепить круг на шпинделе шлифовальной бабки, при необходимости произвести балансировку и правку круга.
3. Установить на прямоугольном столе станка магнитную или электромагнитную плиту. Нижнюю часть плиты (основание) закрепить на столе станка в Т-образных пазах.
Электромагнитные плиты наиболее распространены. Плиты с постоянными магнитами не требуют специальных генераторов и выпрямителей тока, однако сила их притяжения слабее, чем у электромагнитных плит.
Конструкция электромагнитной плиты показана на рис.5.17. Она состоит из стального корпуса /, сердечников 2, катушек 3 и основания 4. При пропускании через катушки постоянного тока сердечники намагничиваются и к ним притягиваются заготовки. После прекращения действия тока в обмотке катушек прекратится и магнитное действие сердечников. Чтобы заготовки не срывались с магнитной плиты в случае прекращения подачи тока в обмотке, на станке предусмотрена автоматическая блокировка. При отключении плиты автоматически выключается подача и стол останавливается.
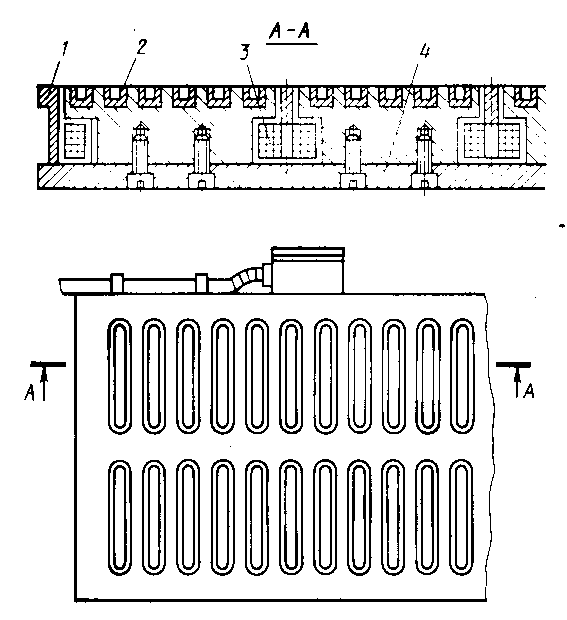
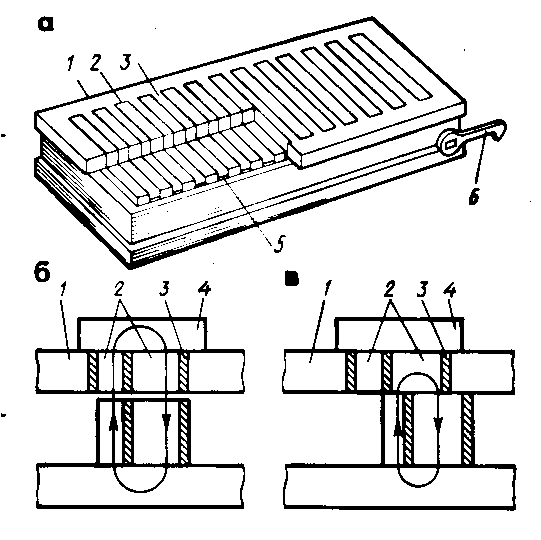
а-общий вид; б-положение магнитов при закреплении и шлифовании заготовок; в-положение магнитов при установке и снятии заготовок
Рисунок 5.18 Магнитная плита с постоянными
магнитами
Рисунок 5.17 Электромагнитная плита
Плиты с постоянными магнитами (рис. 5.18) не требуют специальных установок для питания электрическим током. Верхняя часть плиты состоит из железных пластин 1 и 2 с немагнитными прослойками 3 между ними. Сильные постоянные магниты 5 можно перемещать путем замыкания магнитных силовых линий на железные пластины 1 и 2 либо на закрепляемую заготовку 4. При снятии заготовок надо переместить магниты рукояткой 6 и замкнуть их на железные пластины.
Перед началом работы на станке проверить плоскостность стола и магнитной плиты, для чего индикатор закрепить на шпинделе шлифовальной бабки так, чтобы его мерительный штифт касался верхней поверхности стола (или магнитной плиты), после чего стол вручную переместить в продольном и поперечном направлениях. При неплоскостности, превышающей норму (0,02 мм на длине 1000 мм), стол и плиту шлифуют до достижения нормы.
4. Установить упоры реверсирования хода стола в зависимости от длины и ширины заготовок, закрепленных на магнитной плите. Перебег стола должен быть равен 20...30 мм с каждого края расположения заготовок. Поперечное перемещение шлифовальной бабки ограничивается двумя упорами, которые располагают так, чтобы шлифовальный круг выходил относительно боковых сторон заготовок на 1/3 своей ширины.
5. Проверить и отрегулировать подачу смазывающе-охлаждающей жидкости (СОЖ), состав которой должен соответствовать материалу обрабатываемой заготовки.
6. Подобрать согласно технологической карте, нормативам режимов резания для плоского шлифования или указанию мастера скорость продольного перемещения стола (заготовки), скорость поперечного перемещения шлифовального круга вдоль оси шпинделя (выбирается в долях ширины круга за каждый ход стола) и вертикальную подачу (глубину резания). По выбранной скорости продольного перемещения стола определить и установить соответствующее число двойных ходов стола в минуту:
k = 1000 vc / (2Lc),
где vc - скорость продольного перемещения стола;
Lc - длина хода стола;
Lc=lшл+у,
lшл - суммарная длина заготовок, включая просветы между ними;
у - перебег круга в обе стороны, 20...30 мм.
Скорость продольного перемещения стола зависит от материала заготовки, припуска на обработку и поперечной подачи на ход стола и выбирается по нормативам в пределах 5...8 м/мин для чугуна и мягких сталей, 10...20 м/мин для легированной, инструментальной и закаленных сталей.
Скорость поперечного движения подачи при предварительном шлифовании принимается 0,7...0,8 ширины круга за один продольный ход стола, при окончательном шлифовании скорость подачи принимается 0,2...0,4 ширины круга за ход стола. На некоторых моделях станков скорость поперечной подачи осуществляется в пределах 0,3...0,4 мм за ход стола.
Вертикальное движение подачи, т.е. толщина слоя металла, снимаемого за один рабочий ход, при предварительном шлифовании принимается 0,01...0,05 мм, при окончательном шлифовании -0,005...0,01 мм.
7. Установить и закрепить на магнитной плите или в другом зажимном приспособлении заготовку или несколько заготовок в зависимости от их габаритов и площади рабочей поверхности магнитной плиты.
Заготовку на плите установить так, чтобы магнитный поток проходил через закрепляемую заготовку, являющуюся частью магнитопровода, т.е. заготовку расположить перпендикулярно немагнитным прослойкам. Для установки шлифуемых заготовок на магнитной плите в требуемом положении применяют установочные планки, плиты, угольники, призмы или обоймы, а при обработке плоскостей, расположенных под углом, применяют синусные плиты и поворотные приспособления. При установке заготовки на плите необходимо, чтобы она перекрывала не менее чем два полюса магнитной плиты. После пробной установки заготовок включить магнитную плиту и проверить прочность закрепления заготовок на плите. Так как воздух имеет очень малую магнитную проницаемость, необходимо добиваться очень малого зазора между нижней плоскостью заготовки и рабочей поверхностью магнитной плиты. Зазоры следует выдерживать в следующих пределах: при установке заготовки необработанной поверхностью - (0,1...0,3) мм; при установке на предварительно обработанную поверхность - (0,05...0,1) мм; при установке на окончательно обработанную поверхность - не более 0,02 мм. После установки заготовок включить магнитную плиту и проверить прочность закрепления заготовок.
8. Выполнить пробные проходы при наладке станка, для чего, проделав все необходимые приготовления к работе на станке, включить электродвигатель шлифовальной бабки, предварительно с ручным продольным движением подачи от маховичка переместить стол в оба крайних положения, подвести шлифовальный круг к обрабатываемым заготовкам до появления искры и вручную переместить круг в поперечном направлении. Если при этом искра равномерна по всей длине и ширине обрабатываемой поверхности, то можно включить автоматическое продольное и поперечное движения подачи и, сделав несколько проходов, проверить толщину и параллельность заготовок, взятых из различных зон магнитной плиты.
9. Отрегулировать механизм автоматического выключения вертикальной подачи шлифовальной бабки.
Сняв пробные детали, проверить их годность по размерам и шероховатости обработанной поверхности. Проверив последовательность работы автоматических устройств станка, перемещения рабочих органов, все ограждения станка, требуемые зазоры между кругом и другими частями станка, качество затяжки всех болтов и гаек, используемых при настройке станка, и установку круга, станок можно считать готовым к работе.
Контрольные вопросы:
- Каковы правила техники безопасности при работе на шлифовальных станках?
- Какие связки применяют при изготовлении шлифовальных кругов?
- Что обозначают цифры и буквы в маркировке кругов 25А25ПСМ25К5А; 63С 63Н СТ3 6К6Б; 34 А 16 Н СМ 1 6 К5 А и т.п.?
- Как устанавливают шлифовальные круги на шпинделе станка?
- Перечислите методы шлифования конических поверхностей заготовок?
- Перечислите методы установки заготовок на плоскошлифовальных станках?
6 Комплексная работа на
металлообрабатывающих станках
Студент должен
знать:
- технологический процесс обработки детали;
- технику безопасности при работе на
металлообрабатывающих станках.
уметь:
- выполнять эскизы и рабочие чертежи детали;
- организовать рабочее место станочника;
- подбирать конструкцию и геометрические параметры
инструментов для заданных условий обработки;
- назначать оптимальные режимы резания и корректировать
их по паспортным данным станка;
- изготовлять детали в соответствии с техническими
условиями технологической карты;
- оформлять технологический документ согласно ЕСТД.
Заключительный этап учебной практики для получения первичных профессиональных навыков при работе на металлообрабатывающих станках состоит из 2 разделов: выполнения комплексной работы, включающей обработку заготовки по чертежу и сдачи зачета по устройству, и управлению станком, назначению, конструкции и геометрическим параметрам режущего инструмента, техническим измерениям деталей; организации рабочего места станочника (токаря, фрезеровщика, сверловщика, строгальщика и шлифовальщика) и правила техники безопасности при работе на металлообрабатывающих станках. Для комплексной работы выбирают детали, требующие не менее четырех различных видов станочной обработки, например, обтачка, сверление, рассверливание, расточки, прорезка канавок или фасонных поверхностей, нарезание резьбы: резцами, метчиками, плашками и т.п.
Детали, которое получают студенты при выполнении комплексной работы, могут иметь форму валов, втулок, фланцев и других конструктивных видов, входящих в продукцию, изготавливаемую учебной мастерской для оснащения кабинетов и лабораторий техникума (колледжа) или реализуемый продукции. Например, студенты могут изготовлять различные модели калибров-пробок калибров-втулок, различные виды резьб и червяков для кабинетов деталей машин и инженерной графики, образцы для лаборатории испытания материалов; варотки метчиков, плашкодержателей, центров, валиков и деталей, которые используют при проведении других видов практики (слесарной). Ряд заготовок, обработка которых включает большинство программных операций (не менее четырех), можно получить в виде замеров от предприятий ремонта.
Количество заготовок, которое студент должен обработать, зависит от их трудоемкости и должно быть рассчитано на загрузку учащегося работой не менее 2-4 дней, оставив часть последнего дня практики на сдачу работы и зачета по практике.
Оценку знаний по учебной практике определяют на основе качества выполнения работы (или количества обработанных заготовок), времени, затраченного на обработку, бесед со студентами и проверки дневников-конспектов. Студент обязан не только показать умение выполнять те или иные операции, освоенные на металлообрабатывающих станках, но хорошо знать теоретический материал и отвечать на контрольные вопросы, такие как наименование и назначение режущего инструмента, применяемого на токарном, фрезерном, сверлильном, строгальном, шлифовальном станках; приемы работы на станке; правила применения и чтение размера при измерении штангенциркулем, микрометром, универсальным угломером; организация рабочего места станочника; виды работ, выполняемых на том или ином станке; правила техники безопасности при выполнении конкретных операций и т.п. вопросы студентам могут задаваться устно или в виде контрольных билетов.
7 СТАНКИ С ЧПУ
Тема 7.1 Общие сведения о системах управления и станках с ЧПУ
Под управлением станком принято понимать совокупность воздействий на его механизмы, обеспечивающие выполнение технологического цикла обработки, а под системой управления - устройство или совокупность устройств, реализующих эти воздействия.
Числовое программное управление (ЧПУ) - это управление, при котором программу задают в виде записанного на каком-либо носителе массива информации. Управляющая информация для систем ЧПУ является дискретной и ее обработка в процессе управления осуществляется цифровыми методами. Управление технологическими циклами практически повсеместно осуществляется с помощью программируемых логических контроллеров, реализуемых на основе принципов цифровых электронных вычислительных устройств.
В таблице 7.1 перечислены цели и функции современного многоуровневого устройства ЧПУ (УЧПУ).
Таблица 7.1 - Цели и функции многоуровневых устройств ЧПУ
-
Уровни
Цель
Функции
I
Обеспечение обработки заготовок на станке
Управление циклом работы станка
Контроль перемещения рабочих органов станка
II
Получение информации о функционировании станка
Принятие инженером-технологом и (или) опе-ратором решения о пра-вильности работы станка и выявление неисправностей на основании информации о работе станка
III
Получение исходных данных для организации производства в цеху (на заводе)
Принятие инженером-технологом и(или) оператором на основании информации о работе станка квалифицированных решений по управлению производством
Системы ЧПУ практически вытесняют другие типы систем управления.
По технологическому на значению и функциональным возможностям системы ЧПУ подразделяют на четыре группы:
• позиционные, в которых задают только координаты конечных точек положения исполнительных органов после выполнения ими определенных элементов рабочего цикла;
• контурные или непрерывные, управляющие движением исполнительного органа по заданной криволинейной траектории;
• универсальные (комбинированные), в которых осуществляется программирование как перемещений при позиционировании, так и движения исполнительных органов по траектории, а также смены инструментов и загрузки-выгрузки заготовок;
• многоконтурные системы, обеспечивающие одновременное или последовательное управление функционированием ряда узлов и механизмов станка.
Примером применения систем ЧПУ первой группы являются сверлильные, расточные и координатно-расточные станки. Примером второй группы служат системы ЧПУ различных токарных, фрезерных и круглошлифовальных станков. К третьей группе относятся системы ЧПУ различных многоцелевых токарных и сверлильно-фрезерно-расточных станков.
К четвертой группе относятся бесцентровые круглошлифовальные станки, в которых от систем ЧПУ управляют различными механизмами: правки, подачи бабок и т.д. Существуют позиционные, контурные, комбинированные и многоконтурные (рис. 7.1, а) циклы управления.
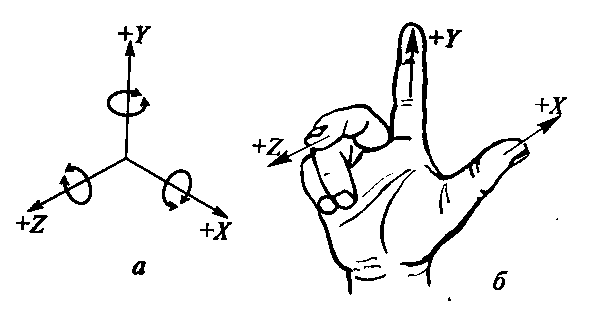
Рисунок 7.1 Расположение осей координат в станках с
ЧПУ(а); правосторонняя система координат (б)
По способу подготовки и ввода управляющей программы различают так называемые оперативные системы ЧПУ (в этом случае управляющую программу готовят и редактируют непосредственно на станке, в процессе обработки первой детали из партии или имитации ее обработки) и системы, для которых управляющая программа готовится независимо от места обработки детали. Причем независимая подготовка управляющей программы может выполняться либо с помощью средств вычислительной техники, входящих в состав системы ЧПУ данного станка, либо вне ее (вручную или с помощью системы автоматизации программирования).
Программируемые контроллеры - это устройства управления электроавтоматикой станка. Большинство программируемых контроллеров имеют модульную конструкцию, в состав которой входят источник питания, процессорный блок и программируемая память, а также различные модули входов/выходов. Для создания и отладки программ работы станка применяют программирующие аппараты. Принцип работы контроллера: опрашиваются необходимые входы/выходы и полученные данные анализируются в процессорном блоке. При этом решаются логические задачи и результат вычисления передается на соответствующий логический или физический выход для подачи в соответствующий механизм станка.
В программируемых контроллерах используют различные типы памяти, в которой хранится программа электроавтоматики станка: электрическую перепрограммируемую энергонезависимую память; оперативную память со свободным доступом; стираемую ультрафиолетовым излучением и электрически перепрограммируемую.
Программируемый контроллер имеет систему диагностики: входов/выходов, ошибки в работе процессора, памяти, батареи, связи и других элементов. Для упрощения поиска неисправностей современные интеллектуальные модули имеют самодиагностику.
Программоноситель может содержать как геометрическую, так и технологическую информацию. Технологическая информация обеспечивает определенный цикл работы станка, а геометрическая - характеризует форму, размеры элементов обрабатываемой заготовки и инструмента и их взаимное положение в пространстве.
Станки с программным управлением (ПУ) по виду управления подразделяют на станки с системами циклового программного управления (ЦПУ) и станки с системами числового программного управления (ЧПУ). Системы ЦПУ более просты, так как в них программируется только цикл работы станка, а величины рабочих перемещений, т.е. геометрическая информация, задаются упрощенно, например с помощью упоров. В станках с ЧПУ управление осуществляется от программоносителя, на который в числовом виде занесена и геометрическая, и технологическая информация.
В отдельную группу выделяют станки с цифровой индикацией и преднабором координат. В этих станках имеется электронное устройство для задания координат нужных точек (преднабор координат) и крестовый стол, снабженный датчиками положения, который дает команды на перемещение до необходимой позиции. При этом на экране высвечивается каждое текущее положение стола (цифровая индикация). В таких станках можно применять или преднабор координат или цифровую индикацию; исходную программу работы задает станочник.
В моделях станков с ПУ для обозначения степени автоматизации добавляется буква Ф с цифрой: Ф1 - станки с цифровой индикацией и преднабором координат; Ф2 - станки с позиционными и прямоугольными системами ЧПУ; Ф3 - станки с контурными системами ЧПУ и Ф4 - станки с универсальной системой ЧПУ для позиционной и контурной обработки. Особую группу составляют станки, имеющие ЧПУ для многоконтурной обработки, например бесцентровые круглошлифовальные станки. Для станков с цикловыми системами ПУ в обозначении модели введен индекс Ц, с оперативными системами - индекс Т (например, 16К20Т1).
ЧПУ обеспечивает управление движениями рабочих органов станка и скоростью их перемещения при формообразовании, а также последовательностью цикла обработки, режимами резания, различными вспомогательными функциями.
Система числового программного управления (СЧПУ) - это совокупность специализированных устройств, методов и средств, необходимых для осуществления ЧПУ станками. Устройство ЧПУ (УЧПУ) станками - это часть СЧПУ, выполненная как единое целое с ней и осуществляющая выдачу управляющих воздействий по заданной программе.
В международной практике приняты следующие обозначения: NC-ЧПУ; HNC - разновидность устройства ЧПУ с заданием программы оператором с пульта с помощью клавиш, переключателей и т.д.; SNC - устройство ЧПУ, имеющее память для хранения всей управляющей программы; CNC - управление автономным станком с ЧПУ, содержащее мини-ЭВМ или процессор; DNC - управление группой станков от общей ЭВМ.
Для станков с ЧПУ стандартизованы направления перемещений и их символика. Стандартом ISO-R841 принято за положительное направление перемещения элемента станка считать то, при котором инструмент или заготовка отходят один от другого. Исходной осью (ось Z) является ось рабочего шпинделя. Если эта ось поворотная, то ее положение выбирают перпендикулярно плоскости крепления детали. Положительное направление оси Z - от устройства крепления детали к инструменту. Тогда оси Х и Y расположатся так, как это показано на рисунке 7.1.
Использование конкретного вида оборудования с ЧПУ зависит от сложности изготовляемой детали и серийности производства. Чем меньше серийность производства, тем большую технологическую гибкость должен иметь станок.
При изготовлении деталей со сложными пространственными профилями в единичном и мелкосерийном производстве использование станков с ЧПУ является почти единственным технически оправданным решением. Это оборудование целесообразно применять и в случае, если невозможно быстро изготовить оснастку. В серийном производстве также целесообразно использовать станки с ЧПУ. В последнее время широко используют автономные станки с ЧПУ или системы из таких станков в условиях переналаживаемого крупносерийного производства.
Принципиальная особенность станка с ЧПУ - это работа по управляющей программе (УП), на которой записаны цикл работы оборудования для обработки конкретной детали и технологические режимы. При изменении обрабатываемой на станке детали необходимо просто сменить программу, что сокращает на 80...90 % трудоемкость переналадки по сравнению с трудоемкостью этой операции на станках с ручным управлением.
Основные преимущества станков с ЧПУ:
• производительность станка повышается в 1,5...2,5 раза по сравнению с производительностью аналогичных станков с ручным управлением;
• сочетается гибкость универсального оборудования с точностью и производительностью станка-автомата;
• снижается потребность в квалифицированных рабочих-станочниках, а подготовка производства переносится в сферу инженерного труда;
• детали, изготовленные по одной программе, являются взаимозаменяемыми, что сокращает время пригоночных работ в процессе сборки;
• сокращаются сроки подготовки и перехода на изготовление новых деталей благодаря предварительной подготовке программ, более простой и универсальной технологической оснастке;
• снижается продолжительность цикла изготовления деталей и уменьшается запас незавершенного производства.