Методическое пособие к курсу лекций "Логистика" (в схемах, таблицах, определениях)
Вид материала | Методическое пособие |
- Программа курса и темы практических занятий; Логика в таблицах и схемах. Логика как, 1722.34kb.
- А. В. Теория государства и права в схемах, определениях и комментариях: учебное пособие, 2034.57kb.
- Юридический институт, 833.44kb.
- Учебно-методическое пособие по дисциплине «Логистика» Учебно-методическое пособие для, 223.95kb.
- Учебное пособие в схемах и таблицах по дисциплине финансы, денежное обращение и кредит, 1065.36kb.
- Учебное пособие в удобном формате рассматривает курс учебной дисциплины "Теория государства, 6715.11kb.
- Требования к уровню подготовки пятиклассников, 21.9kb.
- Краткий курс лекций по философии учебно-методическое пособие для студентов всех специальностей, 2261.57kb.
- Курс лекций по основам программирования Учебно-методическое пособие, 726.7kb.
- Методическое пособие по курсу: «История и философия науки», 337.53kb.
ЛОГИСТИЧЕСКИЕ ПРОИЗВОДСТВЕННЫЕ СИСТЕМЫ
В настоящее время производственные системы в логистике рассматриваются в 2-х аспектах.
1. Управленческий аспект (управленческая технология) – набор подходов и методов к процессам планирования и организации производства (управления производством). Методология управления.
2. Информационный аспект (информационная технология) – набор ПО, аппаратных средств и прочих средств, поддерживающих управление производством.
Первый тип/класс производственных систем получил названия толкающие системы.
Толкающие системы – это такие системы планирования и организации производства, в которых сырьё, материалы, комплектующие подаются с одной операции на другую в соответствии с жёстким планом-графиком.
Другими словами, процесс производства сформирован централизованно. В системах толкающего типа каждый технический агрегат, каждый передел производства имеет информационные и управляющие связи с центральным органом управления (см. рис. Ниже).
Существуют также системы управления запасами в каналах сферы товарного обращения, в которых решение о пополнении запасов на периферийных складах принимаются централизованно (или стратегия сбыта, направленная на опережающее, по отношению к спросу, формирование товарных запасов в оптовых и розничных предприятиях).
Наиболее известными системами толкающего типа являются два поколения MRP-систем и два поколения DRP-систем.
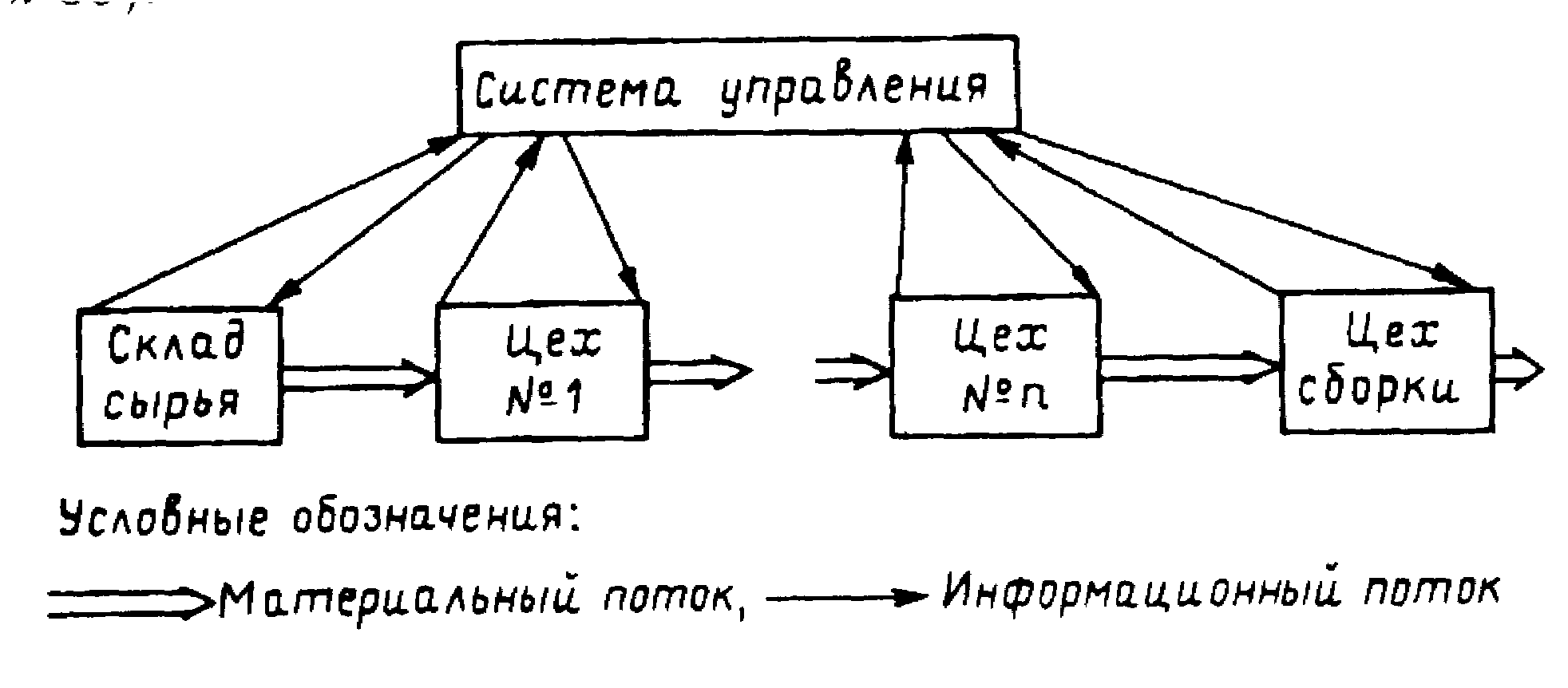
Расчет необходимых материалов (пример использования MRP-систем)
Алгоритм работы MRP II состоит из следующих шагов:
1. Определение независимых (входящих) потребностей. Независимыми потребностями для системы MRP II могут являться следующие:
а) заказы клиентов;
б) прогнозы;
в) основной производственный план;
г) потребности в пополнении страхового запаса.
2. Расчет брутто-потребностей. Покажем это на примере изделия, спецификация которого приведена на рис выше.
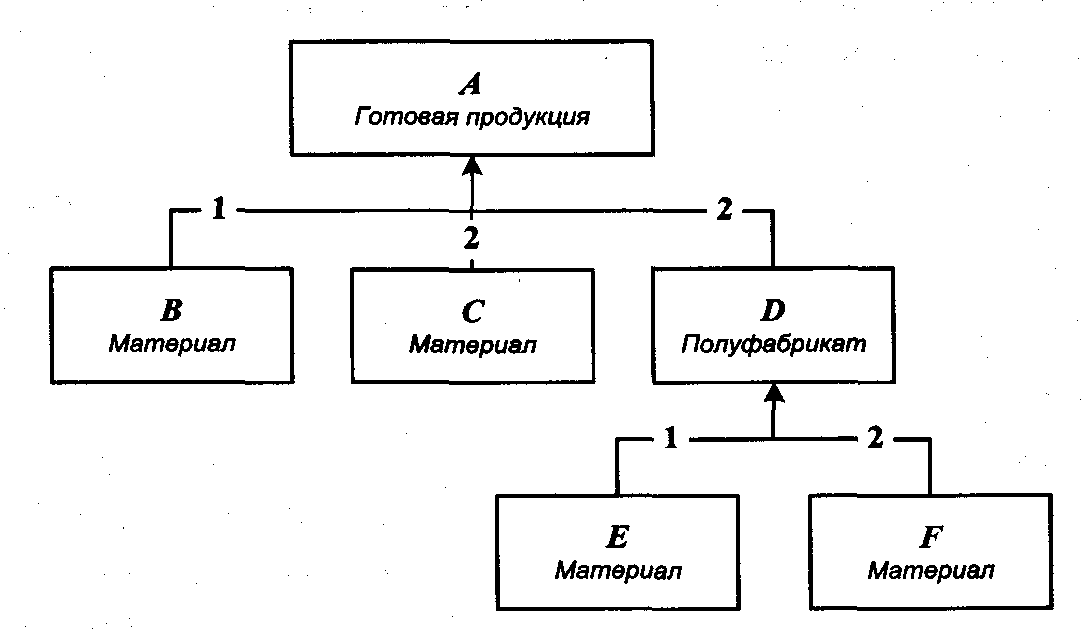
Типовая спецификация изделия
Предположим, что для изделия А существует производственный план (заказ клиента или прогноз) в размере 100 единиц. Исходя из этого требуемое количество компонентов составит:
В - 100 единиц;
С - 200 единиц;
D - 200 единиц;
Е - 200 единиц;
F - 400 единиц.
3. Расчет нетто-потребностей. На данном этапе производится расчет потребностей в материалах, узлах и компонентах с учетом имеющихся в наличии или в незавершенном производстве.
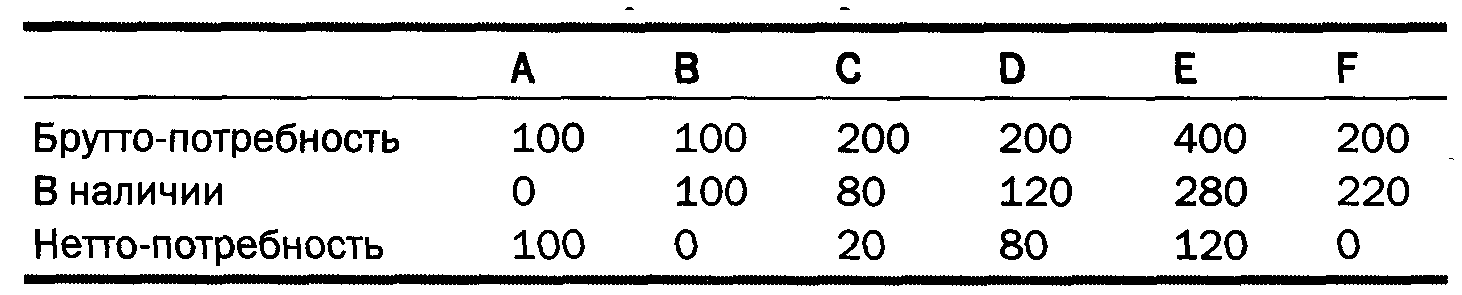
4. Расчет нетто-потребностей во времени. На этом этапе необходимые количества рассчитываются с учетом всех приходов и расходов материалов. Если на этом шаге система выявляет снижение уровня материала ниже определенного уровня, то определяется количество, которое нужно закупить или произвести для удовлетворения потребности.
Также возможен расчет нетто-потребностей с учетом правила партии (минимальная партия заказа, кратность партии, периодичность заказа).
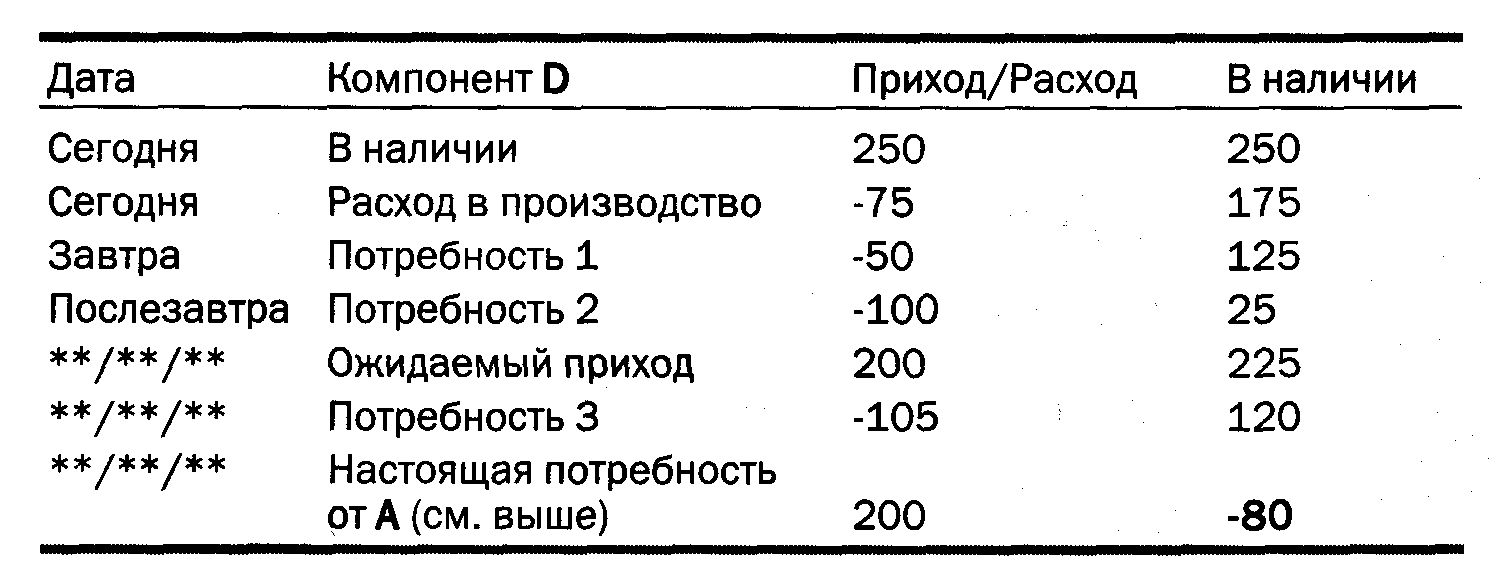
5. Определение сроков закупки и изготовления. На этом этапе для отдела планирования (отдела снабжения) система определяет сроки начала действий по реализации рассчитанных нетто-потребностей. Алгоритм MRP берет за начало дату реализации конечной потребности и «раскручивает» назад во времени процесс изготовления изделия или закупки материалов, определяя, таким образом, даты начала производственных операций с компонентами (деталями) нижнего уровня, вплоть до определения дат формирования заказов поставщикам.
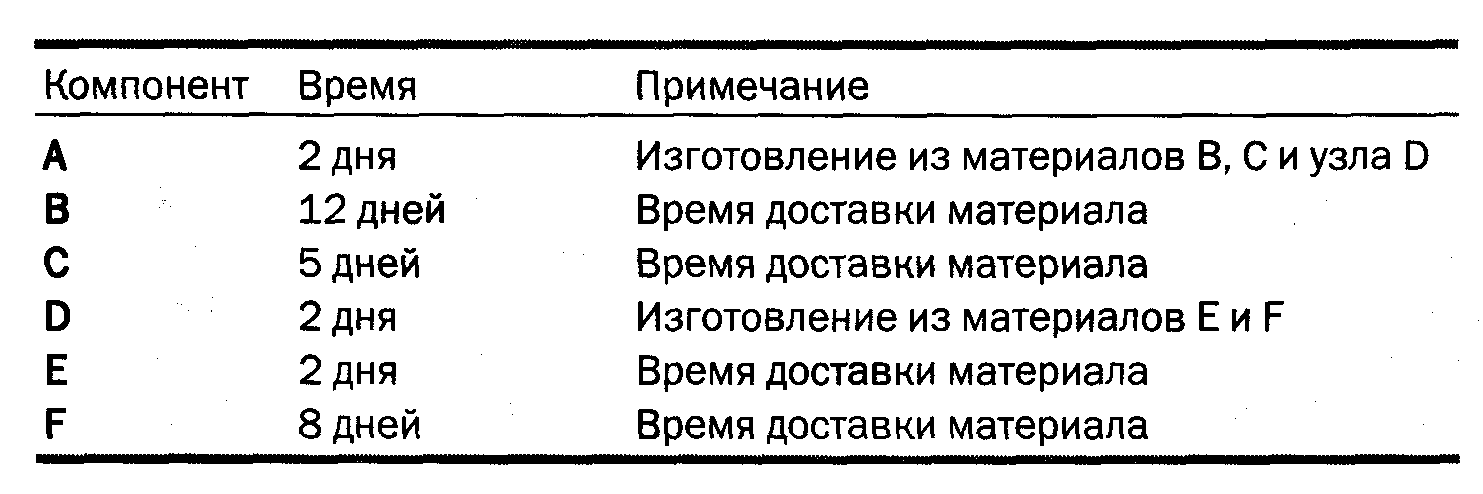
Алгоритм расчёта можно проиллюстрировать на рисунке, представленном ниже.
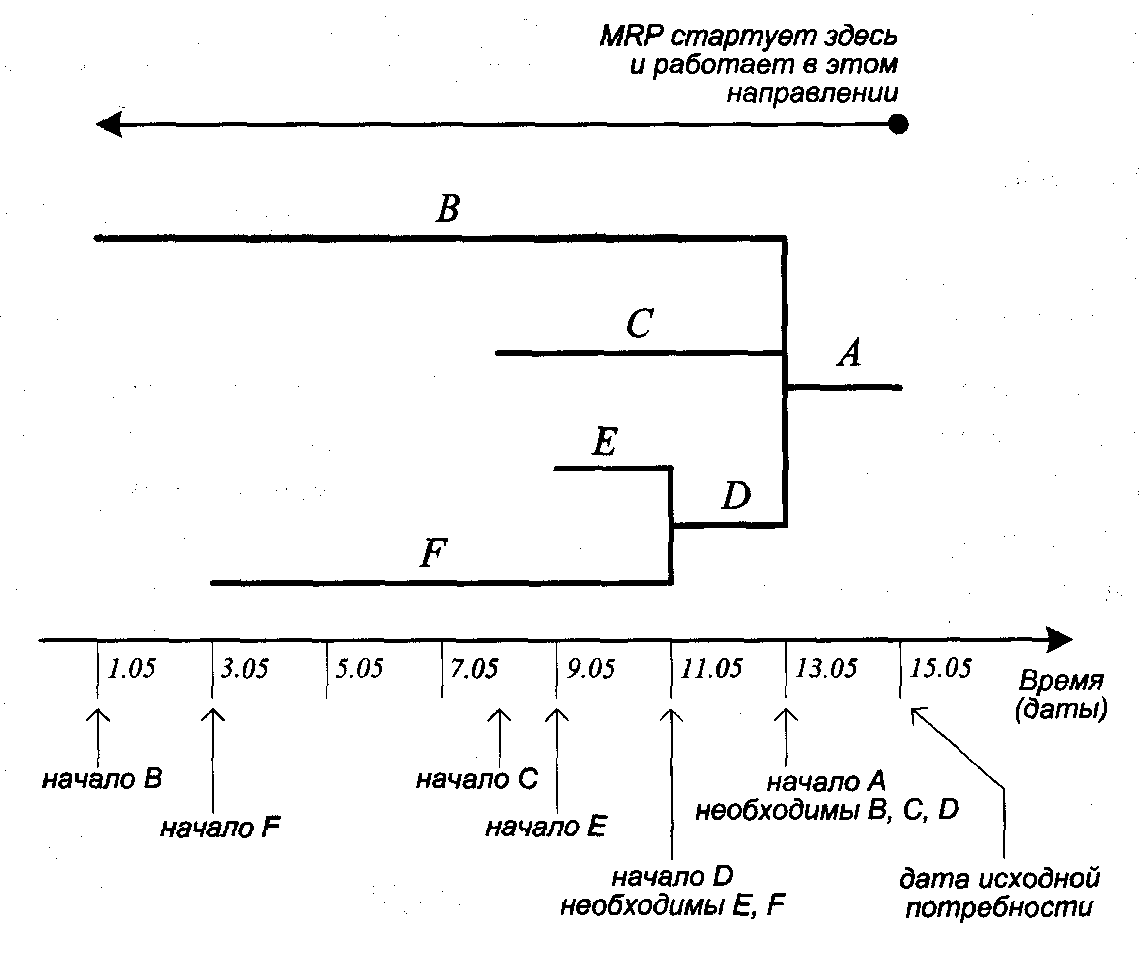
Схема расчета текущих потребностей
Структура корпоративной информационной системы класса MRP-II
(MRP II ISO Standard System)
1. Планирование продаж и операций (Sales and Operation Planning) 2. Управление спросом (Demand Management) 3. Основной календарный план производства (Master Production Scheduling – MPS) 4. Планирование потребности в материалах (Material Requirements Planning – MRP) 5. Ведомость материалов (Bill of Materials – BOM) 6. Подсистема операций с запасами (Inventory Transaction Subsystem) 7. Подсистема запланированных поступлений по открытым заказам (Scheduled Receipts Subsystem) 8. Оперативное управление производством (Shop Flow Control – SFC) 9. Планирование потребности в мощностях (Capacity Requirement Planning – CRP) 10. Управление входным/выходным материальным потоком (Input/output control) 11. Управление снабжением (Purchasing) 12. Планирование распределения (Distribution Recourse Planning – DRP) 13. Планирование и контроль производственных операций (Tooling Planning and Control) 14. Планирование финансовых ресурсов (Financial Recourse Planning – FRP) 15. Моделирование ( Simulation) 16. Оценка/измерение результатов деятельности (Performance Measurement) |
Второй тип/класс производственных систем получил названия тянущие системы.
Тянущие системы – это такие системы планирования и организации производства, в которых сырьё, материалы, комплектующие подаются с одной операции на другую по мере необходимости (т.е. жёсткий план-график отсутствует).
При работе по тянущей системе на каждом производственном участке создаётся строго определённое количество деталей, узлов. Последующий участок заказывает и вытягивает с предыдущего участка изделия строго в соответствии с нормой и временем производственного потребления.
С
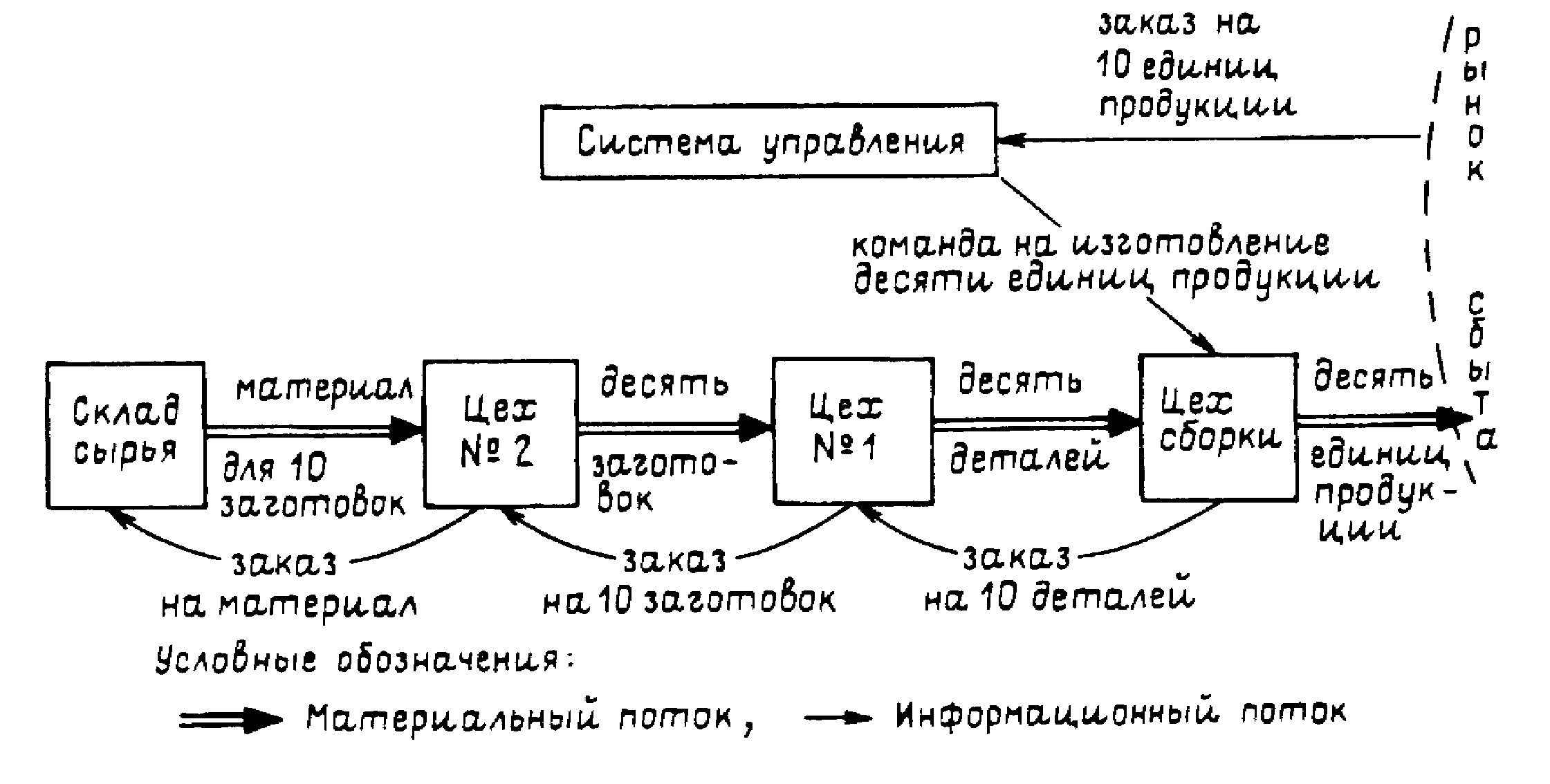
уществуют также системы управления запасами в каналах сферы товарного обращения, в которых решение о пополнении запасов на периферийных складах принимаются децентрализовано (стратегия сбыта, направленная на опережающее, по отношению к формированию товарных запасов, стимулирование спроса на продукцию розничного звена).
Основные преимущества тянущих систем: гибкость по отношению к изменениям, децентрализация управления и принятия решений. Однако, более сложна в практической настройке, также, как и толкающая, требует больших временных и организационных затрат.
Наиболее известными системами тянущего типа является система (концепция) точно-в-срок, концепция «бережливого производства» (LP – lean production), система Канбан и система ОПТ.
Концепция «точно-в-срок»
Сравнение концепции JIT с традиционными методами управления
Факторы | ЛТ-подход | Традиционный подход |
Запасы | Играют негативную роль. Все усилия направлены на их минимизацию. Страховые запасы отсутствуют (или минимальны) | Необходимый элемент управления. Защищают производство (и продажи) от ошибок прогнозирования и ненадежных поставщиков. Большая часть запасов - «страховые». Большие объемы запасов объясняются скидками при покупке большой партии; экономией на масштабе; страховыми запасами |
Размер запаса, число закупок MP | Размер запаса показывает только текущую потребность. Минимальный объем MP в поставке применяется как для производителя, так и для поставщика. Для определения объема поставки используется модель EOQ | Объем запаса определяется нормативом или по формуле EOQ. Не учитывается изменение запаса при изменении затрат в сбыте при переходе на меньшие объемы ГП или MP |
Распределение | Высокий приоритет. Учет изменений спроса путем быстрой переналадки оборудования. Производство небольших партий ГП | Низкий приоритет. Цель – максимизация объема выпуска ГП |
Запасы НП | Устранение запасов НП. Если имеются небольшие запасы между производственными подразделениями, необходимо их фиксировать и устранить как можно раньше | Необходимый элемент. Запасы НП аккумулируются между структурными подразделениями, являясь основой последующих производственно-технологических циклов |
Поставщики | Рассматриваются как партнеры по производству. Отношения только с надежными поставщиками. Небольшое количество поставщиков | Поддерживаются профессиональные длительные отношения с поставщиками. Как правило, большое количество поставщиков, между которыми искусственно поддерживается конкуренция |
Качество | Цель - «ноль дефектов». Исключение входного контроля качества MP и ГП. Идеология TQM | Допускается небольшое число дефектов. Выборочные инспекции качества ГП |
Поддержка технологическим оборудованием | Предварительная поддержка существенна. Процесс может быть прерван, если поддержка не обеспечивает непрерывность доставки MP, НП вовремя | По мере необходимости. Не критична, пока запасы поддерживаются |
Продолжительность логистических циклов | Сокращение продолжительности логистических циклов. При этом возрастает скорость реакции логистических решений и уменьшается неопределенность, связанная с прогнозом потребности | Длительные логистические циклы. Нет потребности в их сокращении, пока имеется компенсация за счет страховых запасов |
Персонал | Требует согласованности действий рабочего и управляющего персонала. Нельзя вносить изменения в логистический процесс, пока нет согласованности | Управление осуществляет общий менеджмент. Изменения не зависят от низших звеньев персонала |
Гибкость | Короткий производственный цикл; максимальная гибкость | Продолжительный производственный цикл; минимальная гибкость |
Транспортировка | Полный комплекс услуг, надежность | Минимальные издержки в пределах базового уровня обслуживания |
Использование гибкой организации труда в системе
«точно в срок» (выдержки из проекта компании McKinsey)
1. Строить работу в первую очередь на организации процессов, а не на решении отдельных задач. Ориентироваться на целевые нормативы, связанные с удовлетворением запросов потребителей, такие как низкие цены и быстрое обслуживание. Выделить процессы, отвечающие (или не отвечающие) этим нормативам – привлечение и исполнение заказов или, скажем, разработка нового продукта. Именно эти процессы – а не функциональные подразделения, такие как отдел продаж или производственный отдел, - становятся главными компонентами компаний.
2. Выровнять иерархию (придав ей более плоскую структуру), минимизируя дробление процессов. Лучше формировать параллельные команды так, чтобы каждая выполняла большую часть или все операции отдельного процесса, чем цепочку команд, выполняющих одну или несколько отдельных операций для многих процессов.
3. Возложить на ведущих руководителей ответственность за организацию и осуществление процессов.
4. Привязать целевые нормативы деятельности и систему оценки результатов к каждому виду работ, связанных с удовлетворением потребителей.
5. Сосредоточить усилия на организации и планировании работы команд, а не отдельных исполнителей. Отдельные исполнители поодиночке не в состоянии постоянно совершенствовать операции.
6. При любой возможности совмещать управленческие и неуправленческие функции и операции. Предоставить командам полномочия самостоятельно нанимать работников, оценивать результаты работы и осуществлять календарное планирование.
7. Уделить особое внимание тому, чтобы каждый работник обладал навыками в нескольких видах деятельности. Вам не нужно много узких специалистов.
8. Информировать и обучать людей своевременно, именно тогда, когда это требуется для выполнения конкретной работы. Абстрактные числа дойдут до тех, кому они нужны в работе, без управленческой волокиты только в том случае, если Вы дали себе труд научить рядовых исполнителей – продавцов, механиков и др. – как ими пользоваться.
9. Максимизировать контакты всех сотрудников организации с поставщиками и потребителями. Это означает, что все работники объединённых команд должны постоянно находиться в местах свершения сделок, непосредственно общаясь с партнёрами и клиентами.
10. Мотивировать не только материальными благами, повышением квалификации отдельных сотрудников, а наращивать компетентность команд в целом.
Бережливое производство (lean production) основано на том, что высокое качество продукции, более высокая производительность труда и его гибкая организация могут быть обеспечены за счёт более передовой организации труда, а именно:
1) наделение работников полномочиями и правом принятия решений;
2) работой в команде, групповой организацией труда;
3) ротацией труда, перекрёстной подготовкой;
4) мотивация творчества, самореализации. В основе концепции лежит оптимизация процессов путем их ранжирования по признакам, определяемым понятиями Муда. Под этими понятиями подразумеваются процессы, которые не приносят добавленной ценности потребителям, или уменьшают ее. Выделяют до восьми видов таких процессов.
1. Процессы ожидания.
2. Процессы, ведущие к перепроизводству.
3. Процессы лишней транспортировки.
4. Процессы излишней обработки.
5. Процессы, приводящие к избытку запасов.
6. Процессы, содержащие лишние движения.
7. Процессы, создающие дефекты.
8. Восьмая группа процессов связана с потерями, обусловленными игнорированием человеческого фактора.
Последовательное или взрывное уменьшение таких процессов позволяет приблизить время и уровень издержек к минимуму, определяемому только временем передела.
Канбан система (в переводе с японского яз. – карточка) основывается на управлении материальными потоками в зависимости от фактической загрузки производственных площадей.
Канбан представляет собой комплексную систему производства, претворяющей в жизнь принципы общей теории систем. Система Канбан состоит их трех подсистем.
Социальная подсистема (подбор и подготовка персонала, мотивация, продвижение по службе). Социальная подсистема предполагает создание определённого климата, взаимного уважения между работниками и работодателями (больше работников, меньше служащих). Работники поощряются за выявление проблем, идеи, улучшающие процесс. Трудовой день заканчивается только после выполнения плана; графики разрабатываются с точностью до нескольких минут, при этом приоритетом является выполнение текущих заданий.
Техническая подсистема (оптимально использование ПМ, высокое качество продукции; встроенная система качества, вместо инспектирования). Назначение технической подсистемы – своевременное реагирование на качественные и количественные изменения спроса, минимизация запасов. Достигается это сокращением до минимума времени переналадки оборудования благодаря техническим и организационным мероприятиям. Используется групповая организация труда и групповая технология, основанная на приспособлении машинного парка и организации производства к обработке однотипных изделий. В основе лежит промышленный инжиниринг, простое оборудование, крепежи (причём, оборудование покупается лишь у ограниченных поставщиков).
Производственная подсистема (управление производственным процессом) включает процесс точного планирования производства и 100 5 надёжность поставщиков и заказчиков.
Информационное управление в системе Канбан обеспечивает карточка.
Система Канбан позволяет к минимуму свести запасы (в традиционном понимании их там вообще нет), значительно ускорить оборачиваемость оборотных средств (японские фирмы достигают 150-кратного оборота запасов в течение года, в то время как американские – 20-30-кратного, отечественные – 4-кратного), снизить время на выполнение транспортно-складских операций, повысить эффективность и конкурентоспособность производства.
OPT (в переводе с англ. яз. – оптимизационная производственная технология, Optimized Production Technology) представляет собой компьютеризированный вариант система Канбан, и была разработана израильскими и американскими специалистами в 80-е гг. XX века.
Данная система основана на выявлении «узких» мест, или «критических ресурсов». В качестве критических ресурсов могут выступать: 1) запасы, 2) оборудование, 3) технологические процессы, 4) персонал.
От эффективности использования критических ресурсов и зависят темпы производства, в то время как повышение использования других – на эффективности практически не сказывается. Фирмы, использующие OPT, не стремятся обеспечить 100 % загрузку рабочих мест, занятых на некритически операциях, поскольку интенсификация труда этих работников приводит к росту НП и других нежелательных последствий. Данные системы поощряют использование резерва рабочего времени для повышения квалификации, проведение кружков качества, совмещение профессий.
Эффект от внедрения данной системы заключается в снижении запасов НП и длительности ПЦ, увеличении выхода ГП, снижении издержек, увеличении гибкости и приспособляемости производства.
Программа снижения затрат
Содержание | Причины | Методы | Мероприятия |
Затраты, вызванные перепроизводством продукции | |||
Суть проблемы раскрывает одна фраза «Производим больше, чем можем продать». | К перепроизводству приводят недостатки планирования выпуска продукции, неадекватное понимание потребностей клиентов, значительные производственные заделы. В результате затрачивается масса ресурсов, времени и т.д., что, в конечном счёте, приводит к издержкам, а отдачи (выручки) нет. | 1.Выявить проблему. Для того, чтобы решить, выпуск какой продукции следует продолжить, а какой прекратить, компании обычно используют 4 инструмента сбора необходимой информации: анализ по Парето, анализ стоимости по видам деятельности, анализ ассортимента и оборота наличных средств. 2.Улучшение качества планирования производства. 3. Применение модели «вытягивающего» производства. 4.Сокращение времени на переналадку и наладку производственных линий. 5. Проведения исследования потенциального спроса. 6. Отсрочка – классический в логистике стратегический ход для преодоления проблем, вызванных перепроизводством продукции. | Для преодоления проблем, связанных с перепроизводством, многие компании разработали программы или установили правила, подтверждённые практическим опытом, которые помогают им решать, какие продукты/услуги им стоит выпускать, а от каких следует отказаться. 1.Одни компании контролируют период оборачиваемости складских запасов, используя показатели, которые должны сигнализировать руководству о слишком низком обороте отдельных видов продукции. 2. Другие вводят правила, требующие того, чтобы из ассортимента выпускаемой продукции исключалась какая-либо позиция при появлении новой. 3. Некоторые фиксируют минимальный объём запасов для отдельных видов продукции. Если объём запасов какого-либо товара в течение определённого времени будет превышать лимит, то этот товар будет снят с продажи (продукция – с производства). 4. Есть компании, которые устанавливают особые задачи для каждого вида продукции по тому вкладу, который они должны вносить в развитие бренда и прибыль компании. 5. Многие регулярно исследуют продуктовые позиции, созданные для удовлетворения специфических требований покупателя, проверяя, сохраняется ли потребность в этих продуктах. |
Затраты, обусловленные дефектами и переделкой | |||
Дефекты и переделка – это исправимый и неисправимый брак. | Они вредны с точки зрения порождения непроизводительных затрат по той же причине – на них тратятся ресурсы, а отдача отсутствует. Основные причины – устаревшие и несовершенные технология и оборудование, брак материалов «на входе» (от поставщиков), человеческий фактор. | 1.Внедрение систем «защиты от дурака», не позволяющих совершить действия, ухудшающие качество готовой продукции. Это может быть датчик, останавливающий производственную линию при обнаружении брака, или же посадочные гнёзда деталей, расположенные таким образом, чтобы невозможно было перепутать порядок сборки изделий. 2.Внедрение систем контроля над выполнением операций. | Снижение затрат, обусловленных высоким уровнем производственного брака, должно происходить за счёт следующих мероприятий: 1) уменьшение количества переналадок оборудования; 2) своевременная зачистка производственных линий; 3) соблюдение очередности ассортимента без резких переходов технологических параметров производственного процесса; 4) исключение пересортицы в готовой продукции (очистка бункеров). Сокращение поступления бракованных изделий, путём усиления входного контроля над поставкой запчастей и материалов. Система контроля качества «Шесть сигма». Рабочие участка совместно с администрацией разрабатывают «Положение о браке». В нём ставится задача – не пропускать брак дальше рабочего места его происхождения. Рационализация заключается в минимизации потерь от брака, чтобы не допустить бракованные детали в готовое изделие. Работник, допустивший брак и передавший бракованную деталь на последующие операции, штрафуется за все последующие потери, обусловленные этим браком. Одновременно рабочий на последующей операции, использовавший деталь с явным браком, также штрафуется. |
Затраты, связанные с излишним передвижением и перемещением материалов, деталей, инструмента | |||
Обусловлены их нерациональным расположением. | Простые примеры: рабочий вынужден идти за получением нужного инструмента в подсобное помещение, вместо того, чтобы протянуть руку и взять его со стоящего рядом стеллажа; заготовки постоянно перекладывают из одного цеха в другой, а не перемещают их последовательно на минимальное расстояние между участками. Такие передвижения и перемещения не добавляют ценности конечному продукту и, следовательно, просто бесполезны. | 1.Оптимизация перемещения материалов, деталей, инструмента в производственных процессах. 2.Рационализация рабочих мест, производственных линий, расположения мест хранения. | Могут проводиться следующие мероприятия. 1.Минимизация перемещения деталей в процессе обработки за счёт применения вертикальной конструкции центра. 2. Система рационализации рабочего места «Тойота 5S». Процессной команде ставится задача еционализировать трудовой процесс на каждом рабочем месте. Разрабатываются планировки ебочих мест, обеспечивающие расположение предметов труда и инструмента в зоне досягаемости работника и максимального использования совмещённых и обратных движений рук. Рационализация заключается в устранении перемещений человека в рабочей зоне и ликвидации излишних движений, особенно наклонов и поворотов туловища, а также в увеличении количества трудовых действий, выполняемых двумя руками и сокращении движений рук без предмета. |
Затраты, обусловленные наличием запасов | |||
Излишние запасы «омертвляют» оборотный капитал, а также требуют дополнительных расходов на хранение. | Причиной их возникновения являются недостатки планирования потребностей, тяготение к закупке «про запас», наличие неликвидов. Например, в одной компании планировалось создать подсобное приусадебное хозяйство и был приобретён соответствующий инвентарь. Но проект был заморожен, и немалые запасы пролёживали на складах компании в течение длительного времени. | 1. Оптимизация планирования запасов. 2. Применение системы «Точно в срок», внедрение системы Канбан. | Система «Канбан». Продуктовый команде ставится задача сократить межоперационные запасы заготовок и материалов, и обеспечить информацию об этих запасах в режиме реального времени. Разрабатывается «Список продуктов», обрабатываемых на линии, форма и требования к мерным ёмкостям для хранения, ведомости материалов и узлов, необходимых для изделия. Эти сведения дополняются характеристиками технологического процесса и служат информацией для разработки ёмкостей межоперационных «Контейнеров Канбан» и нормативов минимальных межоперационных запасов. Минимальные запасы в контейнере зрительно выделяются. При их достижении рабочий должен сигнализировать в диспетчерскую службу. Рационализация заключается в профилактике простоев рабочих и оборудования и оптимизации межоперационных запасов. |
Затраты, вызванные проведением излишней обработки | |||
Излишняя обработка означает добавление продукции таких качеств и свойств, которые не востребованы потребителем и за которые он не готов платить. | Например, зачем продавать позолоченные чайники, если и в обычных можно прекрасно кипятить воду? Основная причины связана с непониманием вкусов и предпочтений клиентов. | 1. Изменение потребительских свойств продукта. 2. Изменение технологии производства. 3. «Подключение» клиентов к процессам производства и управления заказом. | Необходимость корректирования потребительских свойств товара определяется сравнением удовлетворённости потребителей товарами. Для этого можно провести фокус-группу для определения потребительских предпочтений, получения новых идей относительно усовершенствования существующих товаров. Например, в ходе проведения маркетинговых исследований, было выявлено, что большинство людей не используют Wi-Fi (беспроводной Интернет) в своём телефоне и боятся большого количества кнопок. Поэтому было принято решение убрать эту функцию и упростить меню для более удобного использования. |
Затраты, связанные с ожиданием/простоями | |||
Простои для предприятия – это недополученная прибыль. | Они возникают по различным причинам – необязательность поставщиков (внешних и внутренних), длительные переналадки оборудования, ремонтные работы, некачественное планирование загрузки производственных мощностей и др. Так, на предприятии, основная продукция которого – макаронная, приходилось периодически останавливать производственную линию из-за того, что полностью заполнялись склады готовой продукции. | 1. Выравнивание производственных линий. 2. Синхронизация процессов. 3. Управление взаимоотношениями с поставщиками. | Мероприятия. 1.Система постоянного улучшения «Кайдзен». Процессной команде ставится задача проанализировать трудовой процесс производственного участка. Командой на основе «Транспортно-технологической схемы производственного процесса в цехе» разрабатывается «Карта формирования потока ценностей на линии». Она характеризует последовательность операций, межоперационные запасы, расстояние перемещения и время «пролёживания» предметов труда. Далее наступает этап рационализации трудового процесса, который заключается в формировании эффективного такта линии и сокращении межоперационных запасов путём оптимизации размеров партии заготовок, минимизации перемещений предметов труда, оснащения линии передаточными устройствами и даже перестановкой оборудования. В целом на предприятии «Картирование» позволяет создать предсказуемые и измеряемые производственные процессы и объективно оценивать результаты их оптимизации. 2.Сокращение времени коммерческих простоев за счёт совершенствования работы с покупателями и заказчиками, поставщиками – жёсткого соблюдения графиков поставки для обеспечения равномерности загрузки оборудования. Для этого необходимо: - составлять планы продаж/закупок с учётом равномерности загрузки оборудования и остатков на складах; - предусматривать в договорах с покупателями и поставщиками штрафные санкции на несвоевременный вывоз/поставку, либо отказ от продукции и жёстко контролировать соблюдение каждого пункта. |
Формирование перечня мероприятий по сокращению издержек – довольно сложная задача. Общая последовательность действий следующая:
1. Сбор данных о структуре издержек компании.
2. Анализ данных об издержках.
3. Определение перспективных направлений снижения затрат.
4. Выработка мероприятий по сокращению затрат.
5. Детальная проработка мероприятий как инвестиционных проектов.
Понятно, что реализация Программы сокращения издержек на практике может столкнуться с рядом технических, финансовых и психологических проблем. Однако эти проблемы можно минимизировать за счёт ряда способов, представленных ниже.
Группа проблем | Содержание | Способы минимизации |
Технические | Связаны с внедрением нового оборудования и технологий, изменением бизнес-процессов | Качественное планирование и осуществление проектов по техническому перевооружению и реконструкции, тщательный выбор поставщиков и подрядных организаций |
Финансовые | На реализацию большинства мероприятий требуются значительные финансовые ресурсы | Приобретение оборудования в лизинг, либо с помощью программ льготного кредитования, использование векселей и т.п. |
Психологические | Сокращение затрат неминуемо сказывается на персонале, вызывает недовольство и раздражение; сопротивление персонала, особенно в связи с сокращением численности | Предварительный внутренний PR для Программ сокращения затрат, пересмотр системы материального стимулирования для повышения заинтересованности работников в реализации мероприятий |
Залогом успешной реализации Программы мероприятий по сокращения затрат будут:
- качественное планирование и исполнения проекта снижения затрат;
- независимая экспертиза мероприятий с привлечением внешних экспертов и консультантов;
- поддержка персонала и высокая заинтересованность руководства в реализации программы;
- привлечение надёжных источников финансирования для реализации затратных мероприятий.
УПРАВЛЕНИЕ ЗАПАСАМИ В ЛОГИСТИКЕ
Товарно-материальные запасы (ТМЗ) всегда считались фактором, обеспечивающим безопасность системы снабжения, производства и сбыта, обеспечивали «гибкость» функционирования организации и являлись своего рода страховкой. До определённого времени, в период промышленного бума, управление запасами стояло на втором месте. Однако в 70-80-е гг прошлого века (в развитых странах мира) произошли существенные изменения в сфере производства: темпы экономического роста замедлились, что привело к существенным переменам на рынке. Покупатель стал требовать максимально разнообразной продукции, или максимальной свободы выбора. Количество продукции/услуг, требуемых для насыщения рынка, становится всё большим, соответственно жизненные циклы товаров – всё короче. Всё это привело к расширению номенклатуры товаров и во многих случаях – к повышению издержек производства. Среди прочих вопросов, которые встали на первое место, стала решаться проблема и эффективного управления запасами, снижения издержек, повышение эффективности и конкурентоспособности.
Функции запасов
Функция | Описание |
Уравновешивание спроса и предложения | Данная функция связана с существованием разрыва между производством и потреблением (сезонность, возможные пики спроса). Главная проблема управления – определение объёма, обеспечивающего максимальный сбыт (производство) при минимальном риске перехода остатков на другой сезон. |
Географическая специализация | Запасы обеспечивают географическую специализацию отдельных хозяйственных единиц, т.к. предприятия может находиться далеко, как от основных рынков сбыта, так и поставщиков (что делает нецелесообразным небольшие поставки). Более того, произведённая в разных местах продукция должна накапливаться на складах для подготовки и комплектации партий по заказам клиентов. Более того, возникают запасы в пути. Главная проблема управления – определение экономически целесообразных партий закупки и реализации, выбор экономически целесообразной формы закупки/сбыта (транзитной, или складской). |
Консолидация ресурсов | Реализация данной функции позволяет немедленно обслуживать потребителей не только в необходимом объёме, но и ассортименте. Консолидация ресурсов отличается от географической специализации тем, что способствует росту эффективности производства на отдельном предприятии, тогда как последняя повышает эффективность производств, разбросанных в пространстве. Современные информационные технологии, системы доставки и обработки грузов уменьшают экономические выгоды от консолидации ресурсов путём накопления запасов, но устранить такие запасы в ближайшее, по крайней мере, время не удастся. |
Сглаживание неопределённости спроса или снабжения (создание страховых запасов) | Эта неопределённость может быть связана с изменением планов у потребителей (потребитель заказывает больше продукта), возможным срывом поставки поставщиками, собственными сбоями в производстве, могут возникнуть задержки и по вине транспортных компаний. В промышленности страховые запасы часто создаются и из-за непрерывности технологии (например, сталелитейное производство), когда издержки на остановку производства из-за нехватки сырья во много раз превышают издержек на создание запасов. |
Однако распоряжение запасами всегда связано с высоким риском и оказывает серьёзное воздействие на логистику, основные её процессы и подходы к оптимизации. Отсутствие нужного ассортимента товаров может вызвать сокращение объёма продаж и разочарование потребителей. Нехватка сырья может повлечь за собой закрытие предприятия, либо изменение производственного графика, что, в свою очередь, может обернуться дополнительными расходами или дефицитом готовой продукции. Если дефицит продукции грозит срывом производственных планов, то избыточный объём запасов тоже чреват проблемами. Из-за чрезмерных запасов растёт потребность в складских площадях, в оборотном капитале, в расходах на страховку и выплату налогов. К тому же хранящаяся на складе продукция может устареть и утратить часть стоимости.
Таким образом, сегодня запасы рассматриваются с точки зрения издержек фирмы. Невозможность удовлетворения потребностей (производства или потребителей) ведёт к издержкам, связанными с потерей потребителей, простоями оборудования и работников, необходимостью выполнения дополнительных заказов, сверхурочные и т.п. (что сказывается, в конечном счёте, на прибыли и конкурентоспособности предприятия в долгосрочной перспективе). С другой стороны, в запасах могут быть «заморожены» значительные оборотные средства, они также требуют дополнительных затрат на хранение, учёт и контроль, страхование и т.п.
Такой подход к запасам позволяет сформулировать и политику в области управления запасами.
Цель управления запасами – нахождение оптимального соотношения между издержками и выгодами, связанными с созданием запасов
Подходы к классификации запасов
Виды запасов (как текущих активов)
- Сырьё, материалы, топливо, комплектующие, упаковка, используемые для производства продукции (производственные запасы).
- Полуфабрикаты собственного производства и незавершённое производство (промежуточные производственные запасы).
- Конечная (готовая) продукция (сбытовые запасы).
- Закупленные товары с целью перепродажи (в торговом предприятии – товарные запасы).
Различают также изделия для ремонта и содержания оборудования, запасы МР, используемых для текущего и капитального ремонта, обслуживания зданий и сооружений
Категории запасов
(в зависимости от целевого назначения и природы возникновения)
Категория | Характеристика |
Текущие (производственные, промежуточные, сбытовые и товарные) запасы | Их главная цель – обеспечить текущее потребление и непрерывность процессов производства и реализации, они подлежат регулярному пополнению. Причинами возникновения текущих запасов являются реализация второй и третьей функций, позволяющих выработать подходы к их оптимизации |
Страховые запасы | Предназначены для обеспечения непрерывного потребления в случае непредвиденных обстоятельств и в нормальных условиях являются величиной постоянной и неприкосновенной. Главной причиной создания страховых запасов является неопределённость спроса. Таким образом, анализ причин возникновения неопределённости позволяет снизить величину страховых запасов или максимально точно определить их необходимый уровень (почему происходит срыв поставки, почему потребитель заказывает больше, почему происходит остановка производства, с чем связана задержка выполнения заказа?) |
Подготовительные запасы | Предназначены для непрерывности потребления в случае, если продукции требуется время для подготовки к потреблению в производстве или реализации. Т.е. главными причинами образования подготовительных запасов является необходимость дополнительной подготовки к потреблению – разгрузка, погрузка, комплектация, фасовка, контроль качества, сортировка и др. (реализация второй и третьей функций). Знание причин (природы) возникновения позволяет выработать подходы к снижению и данных запасов – использование услуг посредников, механизация процессов разгрузки, погрузки, комплектования, использование информационных технологий (например, штрихового кодирования) |
Технологические запасы | Основной причиной их создания являются требования технологического процесса, необходимость дополнительной подготовки к процессам производства и реализации – сушка, утруска, нарезка, упаковка. Основными направлениями оптимизации технологических запасов являются (наряду с совершенствованием технологии) передача части функций специализированным компаниям (в связи с этим появилось понятие «глубокая переработка»), создание цепочки компаний или обособленных подразделений (например, ремонтных) |
Сезонные запасы | Обеспечивают непрерывность производства и потребления либо в сезонные разрывы, либо в сезонные пики (причина образования связана с первой функцией запасов) |
Транспортный запас (запас в пути) | Запасы – отправленные/отгруженные или ожидающие транспортировки. С точки зрения управления запасы в пути являются источником двух сложных обстоятельств. Во-первых, запасы в пути представляют собой реальные активы, которые должны быть оплачены, хотя они пока недоступны (предприятия могут оплачивать груз и по факту прибытия, тогда с точки зрения текущих активов оборотный капитал не будет заморожен в транспортном запасе). Необходимо заметить, что если права собственности передаются в пункте отправления, то они составляют часть текущих запасов. Во-вторых, с ними связана некоторая неопределённость, поскольку часто трудно точно определить, где в данный момент времени находится груз, почему он опаздывает и когда точно оно прибудет к месту назначения, а также содержимое контейнера. Распространение практики заказывать чаще, но мелкими партиями, а также стратегия «точно в срок» привели к тому, что запасы в пути могут составлять большую часть суммарных запасов, чем прежде |
В настоящее время руководители и специалисты компаний стараются выделить из общей классификации запасы нематериальных активов. Не все виды материальных активов сегодня можно оценить с помощью денежной оценки, но предприятия начинают проявлять интерес именно к созданию данного вида запасов, вместо традиционных – материальных. К запасам нематериальных активов можно отнести: 1) опыт и квалификацию сотрудников; 2) знания (например, рынка); деловые связи с партнёрами; 3) репутация фирмы; 4) информация.
Сегодня предприятия управляют нематериальными активами в рамках экономики знаний и такого направления в менеджменте как «управление знаниями».