Десятые академические чтения раасн, 2006 г
Вид материала | Документы |
СодержаниеСПИСОК литературЫ Технология получения зернистого теплоизоляционного Эксплуатационная долговечность герметизирующих материалов |
- Десятые академические чтения раасн, 2006, 1092.49kb.
- Десятые академические чтения раасн, 2006, 1519.63kb.
- Концепция устойчивого развития в стратегии градостроительства франции 05. 23. 22 Градостроительство,, 332.07kb.
- Резолюция районной детской экологической конференции Десятые Басарукинские чтения, 39.32kb.
- План организационно-педагогической деятельности с детьми, имеющими ярко-выраженные, 77.33kb.
- Новосибирский государственный педагогический университет, 43.06kb.
- Академические программы и экзаменационные курсы в австралии международные центры Embassy, 146.35kb.
- Экология человек общество, 371.15kb.
- Министерство образования и науки российской федерации московский государственный областной, 2810.15kb.
- Рассказывайте детям о ценности чтения. Показывайте связь чтения с их успехами в учебе, 97.26kb.
СПИСОК литературЫ
- Рудаков О.Б. Растворитель как средство управления процессом в жидкостной хроматографии. – Воронеж: Изд-во ВорГУ, 2003. – 300 с.
- Курицкий Б.Я. Поиск оптимальных решений средствами Excel 7.0. – СПб.: BHV-Cанкт-Петербург, 1997. – 384 с.
УДК 666.9.043.2
Свергунова Н.А., аспирант
Братский государственный университет
ТЕХНОЛОГИЯ ПОЛУЧЕНИЯ ЗЕРНИСТОГО ТЕПЛОИЗОЛЯЦИОННОГО
МАТЕРИАЛА С ИСПОЛЬЗОВАНИЕМ ТЕХНОГЕННОГО СЫРЬЯ - МИКРОКРЕМНЕЗЕМА
Промышленность строительных материалов является одной из немногих отраслей, потребляющих значительное количество природных минеральных ресурсов.
Дефицит энергоресурсов и их значительное удорожание сделало актуальной задачу экономии энергоресурсов. В связи с этим в сфере создания строительной продукции доминирующим фактором стало обеспечение минимальных теплопотерь в зданиях и сооружениях за счет использования новых эффективных теплоизоляционных материалов. Важным фактором, определяющим направление развития строительной продукции, стало экологическое изменение природной среды.
Использование отходов промышленности позволяет не только расширить сырьевую базу для производства новых строительных материалов, но и решить проблемы экологической ситуации путем утилизации отходов.
На территории города Братска располагается ряд крупнейших промышленных предприятий, в технологическом цикле которых образуются многотоннажные минеральные и органические отходы, являющиеся перспективными с точки зрения использования в производстве теплоизоляционных материалов.
Среди большого разнообразия промышленных отходов особое внимание заслуживает микрокремнезем – отход производства цеха кристаллического кремния Братского алюминиевого завода, выход которого составляет порядка 14-18 тыс. тонн в год.
Получение кристаллического кремния основано на процессах рудовосстановления. Для выплавки кремния рудным компонентом служит богатый кремнеземом кварцит. Истинная плотность микрокремнезема составляет 2000 – 2630 кг/м3, насыпная плотность 150 – 300 кг/м3, удельная поверхность порядка
35000 см2/г. Химический состав микрокремнезема свидетельствует о высоком содержании оксида кремния (табл. 1).
Таблица 1
Химический состав микрокремнезема
SiO2 | Fe2O3 | CaO | MgO | Na2O+ K2O | Al2O3 | SO2 | SiС |
90-94 | 1-3 | 0,7-1,4 | 0,2-0,4 | 0,1-0,5 | 0,7-0,5 | до 0,09 | до 3 |
Работами кафедры «Строительное материаловедение и технологии» Братского государственного университета установлена возможность получения жидкого стекла из микрокремнезема.
Ультрадисперность микрокремнезема предопределяет его повышенную реакционную способность при взаимодействии со щелочными растворами, что позволяет получать жидкое стекло в одну стадию приготовления.
Отличительной особенностью получения жидкого стекла из микрокремнезема является то, что процесс гидротермальной обработки происходит на одном технологическом переделе при температуре ниже 100 С 1. При этом, углеродистые примеси (такие как графит и карборунд), содержащиеся в микрокремнеземе, обладают высокой теплопроводностью, что способствуют более равномерному распределению тепла в среде суспензии и интенсифицирует процессы взаимодействия микрокремнезема и щелочи, а также приводит к сокращению длительности синтеза жидкого стекла.
При этом возможно получение жидкого стекла с различным силикатным модулем и заданной плотностью.
Разнообразие технических характеристик жидкого стекла из микрокремнезема расширяет направление его использования. При этом жидкое стекло можно реализовать как готовый продукт, либо изготавливать на его основе строительные материалы различного назначения: от стеновых до теплоизоляционных.
В предлагаемой работе рассматривается изготовление зернистого теплоизоляционного материала на основе высокомодульного жидкого стекла. Способ получения зернистого теплоизоляционного материала включает приготовление высокомодульного жидкого стекла из суспензии микрокремнезема в растворе гидроксида натрия с последующей термообработкой гранул из указанного стекла, что позволяет получить материал с насыпной плотностью от 80 до 110 кг/м3, прочностью при сжатие 0,5 – 1,0 МПа, объемным водопоглощением до 7 %, общей пористостью 80 – 95 %.
Полученные данные предполагают, что при использовании высокомодульного жидкого стекла из микрокремнезема возможно снижение концентрации щелочного раствора в 2 раза, что позволяет уменьшить расход дефицитного и дорогостоящего едкого натра; в 1,5 раза уменьшить время гидротермальной обработки жидкого стекла; в 2 раза увеличить долю микрокремнезема в суспензии, что способствует более полному использованию отхода промышленности и улучшению экологического состояния окружающей среды.
В ходе исследований было установлено, что на конечные свойства зернистого теплоизоляционного материала значительное влияние имеет силикатный модуль жидкого стекла, плотность жидкого стекла, щелочность суспензии, водотвердое отношение сырьевой смеси, а также технология тепловой обработки полученных гранул из жидкого стекла.
Для получения зернистого теплоизоляционного материала с требуемыми физико-механическими характеристиками использовали высокомодульное жидкое стекло с силикатным модулем 5, полученное в процессе гидротермальной обработки при атмосферном давлении и температуре 95 С в течение 10 мин. Щелочность сырьевой суспензии находится в пределах 16,8 – 17,4 %, водотвердое отношение сырьевой смеси в пределах 0,9 – 0,94.
С целью получения зернистого теплоизоляционного материала с комплексом требуемых свойств исследованы технологические параметры процесса термической обработки гранулированного материала. При этом технология получения материала проста и может быть осуществлена на технологических линиях по производству керамзита при незначительной реконструкции.
Комплексная оценка свойств гранул теплоизоляционного материала показала, что лучшей совокупностью свойств характеризуется материал, полученный при температуре термообработки гранул при 300 - 400ºС. Оптимальное время, необходимое для продолжительности термообработки, обеспечивающей максимальное вспучивание гранул составляет 20 мин.
Для складирования и транспортирования зернистого теплоизоляционного материала потребителю, необходимо предотвратить слипание гранул, которое происходит из-за высоких когезионных свойств. Для предотвращения слипания гранул возможны следующие варианты: использовать обсыпку гранул дисперсным материалом на стадии формования (грануляции); гранулы подсушить при невысоких температурах для образования корочки, которая предотвратит слипание. Однако при использовании обсыпки происходит увеличение плотности гранул.
Поэтому на следующем этапе работы были изучен двухступенчатый режим термообработки сырцовых гранул. Т.к., по проведенным раннее исследованиям, определили максимальную температуру термообработки гранул, то плавный подъем температуры составил: выдержка при температурах 60, 80 и 100 ºС в течение 10, 20 и 30 мин. с последующей термообработкой при температуре 400 ºС в течение 10 мин.
При двухступенчатом режиме термообработки определили оптимальные параметры предварительной сушки гранул: 100 ºС в течении 10 минут с последующей термообработкой 400 ºС в течении 10 мин.
По результатам проведенных исследований разработаны предложения по получению зернистого теплоизоляционного материала из техногенного отхода промышленности. Предлагаемое решение рассматривает изготовление теплоизоляционного материала на основе высокомодульного жидкого стекла из отхода цеха кристаллического кремния – микрокремнезема 2.
Согласно санитарно-гигиенической оценке стройматериалов с добавлением промотходов применение строительных материалов с добавлением промышленных отходов может быть разрешено только после положительного санитарно-гигиенического заключения. Т. к. отходы часто содержат естественные радиоактивные изотопы в разных концентрациях, то исследование на радиоактивность является обязательным. Согласно ГОСТ 30180-94, удельная эффективная активность микрокремнезема не превышает нормы, поэтому материал соответствует первому классу опасности и может быть использован в строительстве без ограничений.
Таким образом, можно сделать заключение, что зернистый теплоизоляционный материал на основе высокомодульного жидкого стекла из микрокремнезема отличается высокими теплотехническими физико-механическими свойствами, экологической чистотой, малоэнергоемкой и ресурсосберегающей технологией.
СПИСОК литературЫ
- Патент РФ № 2056353. МКИ С 04 В 28/04. Способ получения жидкого стекла / Карнаухов Ю.П., Шарова В.В. – Опубл. БИ. –1996. - № 8.
- ТУ 5712-018-02069295-2003. Материалы теплоизоляционные зернистые на основе жидкого стекла из микрокремнезема.
УДК 625.76
Семенов А.С., ассистент, Андреев Е.И., канд. техн. наук, доцент,
Брехман А.И., д-р. техн., наук, профессор
Казанский государственный архитектурно-строительный университет
ЭКСПЛУАТАЦИОННАЯ ДОЛГОВЕЧНОСТЬ ГЕРМЕТИЗИРУЮЩИХ МАТЕРИАЛОВ
В ДОРОЖНОМ СТРОИТЕЛЬСТВЕ
Устойчивость герметизирующих материалов к старению под воздействием различных физико-химических факторов является непременным условием сохранения эксплуатационных параметров асфальтобетонного покрытия автомобильной дороги в течение нормативного срока службы. Воздействие агрессивных факторов среды (действие температуры, кислорода воздуха, УФ-лучей, осадков и солевых растворов) в процессе эксплуатации дорожной одежды в совокупности с механическим воздействием колес автотранспорта крайне негативно сказывается не только непосредственно на герметизирующем материале, но и оказывает разрушающее воздействие на заделанную трещину в самом ее слабом месте – в месте контакта герметизирующего материала с асфальтобетонным покрытием. В связи с этим, неизменность основных технических свойств герметизирующих материалов в процессе эксплуатации, а, следовательно, их долговечность играет важнейшую роль в повышении межремонтных сроков дорожных асфальтобетонных покрытий и снижении приведенных затрат на санацию трещин в долгосрочный период.
На кафедре автомобильных дорог ИТС КазГАСУ уже не первый год ведется разработка новых составов композиционных герметизирующих материалов для ремонта асфальтобетонных покрытий, отличающихся повышенной стойкостью к старению. Для этого при разработке герметизирующих композиций исследовали возможность применения отходов промышленных предприятий РТ. Одним из таких материалов, представляющих несомненный интерес для дорожного хозяйства, являются изношенные автомобильные покрышки, в процессе переработки которых получаются разнообразные продукты. Например, при низкотемпературной пиролизной обработке шин образуются твердые и жидкие остатки пиролиза, которые могут быть использованы в приготовлении герметизирующих композиций. Установка по переработке автомобильных шин введена в действие в 2001 г. в пос. Карабаш НГДУ “Иркеннефть” ОАО “Татнефть”. Кроме того, при измельчении утильной резины на предприятии «КамЭкоТех» в г. Нижнекамске получают резиновую крошку, которая также может быть использована в качестве модифицирующего наполнителя битумных материалов. Помимо экономического эффекта использование данных продуктов позволяет решить проблему утилизации изношенных автопокрышек и других резиносодержащих отходов и, тем самым, улучшает экологическую обстановку в РТ.
С использованием данных продуктов была разработана герметизирующая композиция с заданными техническими свойствами при использовании наполнителей 10…20% масс., раствора полимера 15..20%, адгезионной присадки около 1% масс. На герметизирующую битумную композицию получен патент на изобретение РФ № 2267506 [1].
Данная работа посвящена исследованию долговечности разработанной композиции. В экспериментах использовали различные методики исследований старения битумных композиций. Для сравнения, помимо разработанной герметизирующей битумполимерной наполненной композиции оптимального состава, в исследованиях были использованы и другие герметизирующие материалы, применяемые в РТ для герметизации трещин асфальтобетонных покрытий, а именно: мастика «БИКАМ» и герметик «Biguma AG».
На первом этапе исследований определяли изменение массы и гибкости герметизирующих материалов, после воздействию ультрафиолетового излучения и солевого раствора по методике ГОСТ 30740-2000 [2]. В дополнение к лабораторным исследованиям были проведены испытания герметизирующих материалов на старение в естественных условиях. Для этого также были подготовлены образцы, в соответствии с ГОСТ 30740-2000. Данные образцы выдерживали на открытом испытательном стенде в течение 3 летних месяцев (90 суток). По истечении каждых 15 суток образцы взвешивали (рис.1), и определяли их гибкость. Производили также визуальную оценку образцов после старения в течение 90 суток. Визуальный осмотр показал, что заметных изменений по поверхности герметизирующих материалов не обнаружено.
Исследовали также изменение технических свойств герметизирующих материалов после температурного воздействия в лабораторных условиях при различных режимах выдержки. Старение проводили по двум режимам.
По первому режиму старение герметизирующих материалов происходило при выдерживании образцов при эквивалентной температуре Тэ, которая на 30 0С выше максимальной температуры покрытия. Для условий г. Казани она составляет +75 0С [3]. Во втором температурном режиме старения герметизирующих материалов проводили выдерживанием слоем 4 мм при температуре 1630С в течение 5, 10, 15, 20, 25 ч. При этом изучали изменение тех же показателей, что и при первом режиме термостарения. Результаты лабораторных испытаний приведены в таблице 1.
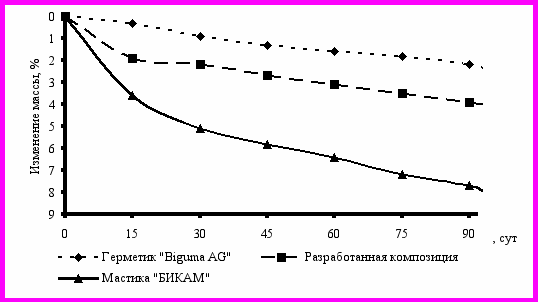
Рис.1 Изменение массы герметизирующих материалов в зависимости от времени выдержки в естественных условиях.
Однако необходимо отметить, что длительное выдерживание при высоких температурах отрицательно сказывается на свойствах материала. Следовательно, необходимо стремиться, насколько возможно, уменьшить время технологических операций, в которых требуется нагревание композиции. Термостабильность разработанной герметизирующей композиции намного превосходит данный показатель у отечественной мастики «БИКАМ» и практически сравнима с термостабильностью зарубежного герметика «Вiguma AG».
Таблица 1
Результаты лабораторных испытаний герметизирующих материалов
Наименование материала | Время выдерж-ки при t=1630С, ч | Темпера- тура размягче- ния по КиШ, 0С | Растяжи- мость при 00С, см | Эластич- ность при 00С, % | Гибкость на брусе d=10 мм, 0С | Адгезия к минераль-ному материалу, контр. обр. № |
Мастика «БИКАМ» | 0 | 78.6 | 4.1 | 25 | -17 | 2 |
5 | 79.4 | 3.0 | 17 | -14 | 2 | |
10 | 81.8 | 1.8 | 11 | -10 | 3 | |
15 | 83.2 | - | - | -8 | 3 | |
20 | 83.8 | 0.5 | 5 | -5 | 3 | |
25 | 84.8 | 0.3 | 2 | -5 | 3 | |
Герметик «Biguma AG» | 0 | 90.0 | 47.5 | 90 | -44 | 1 |
5 | 90.6 | 46.7 | 90 | -42 | 1 | |
10 | 90.8 | 44.2 | 88 | -38 | 1 | |
15 | 91.4 | - | - | -38 | 1 | |
20 | 92.2 | 36.1 | 84 | -38 | 1 | |
25 | 92.4 | 34.8 | 83 | -36 | 2 | |
Разработанная композиция | 0 | 85.6 | 44.3 | 85 | -38 | 1 |
5 | 87.8 | 40.2 | 81 | -33 | 1 | |
10 | 88.6 | 35.1 | 79 | -30 | 1 | |
15 | 89.2 | - | - | -30 | 1 | |
20 | 89.6 | 25.9 | 77 | -30 | 2 | |
25 | 90.0 | 22.4 | 76 | -29 | 2 |
На следующем этапе исследований были проведены испытания герметизирующих материалов в процессе старения в образцах-моделях трещин дорожного покрытия. Образцы-модели трещины готовили путем заливки герметизирующего материала на всю глубину шва, образованного двумя образцами-балочками [1]. Герметизирующие материалы в модели трещины предварительно были растянуты на максимально возможные величины раскрытия трещин в зимний период, зафиксированы в данном положении и помещены в климатическую камеру при установленном режиме на заданное время. После окончания выдерживания в климатической камере модель трещины извлекали из зажимов и оставляли до момента, когда произойдет полная релаксация герметика. Далее образцы помещали в камеру для переменного замораживания-оттаивания на заданное число циклов. После этого оценивали предельное относительное удлинение образца, прочность сцепления с основанием и характер разрушения. Результаты лабораторных испытаний образцов моделей трещин приведены на рис.2, 3.
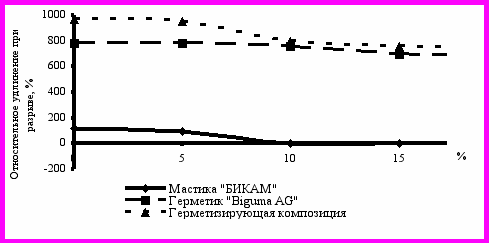
Рис. 2 Зависимость относительного удлинения герметизирующих материалов от ширины раскрытия трещины.
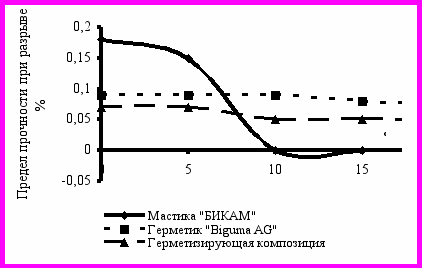
Рис. 3 Зависимость прочности сцепления герметизирующих материалов от ширины раскрытия трещины.
Из рис.2 следует, что ширина раскрытия трещины существенно влияет на изменение упруго-эластичных свойств при старении герметизирующего материала в модели трещины. В наибольшей степени это сказывается при раскрытии трещин более 10% от первоначальной ширины. Старение материала в напряженном состоянии происходит значительно интенсивнее, чем в ненапряженном. Связано это с тем, что при растяжении расстояние между макромолекулами полимера увеличивается, и повышается вероятность его деструкции.
Полученные в результате экспериментальных исследований данные позволяют сделать следующие обобщения и выводы:
- Разработанная герметизирующая битумполимерная наполненная композиция показала относительно высокую стойкость к старению под действием ультрафиолетового облучения и солевого
раствора в сравнении с серийно выпускаемыми герметиками и мастиками. По изменению технических свойств установлено, что наименее устойчива к действию УФ-лучей и солевого раствора мастика «БИКАМ», наиболее устойчив герметик «Biguma AG». Разработанная герметизирующая битумполимерная наполненная композиция по стойкости к агрессивным факторам сравнима с герметиком «Biguma AG».
- Исследование стойкости герметизирующих материалов к старению под действием высоких температур (750С и 1630С) показало, что термостабильность разработанной герметизирующей битумполимерной наполненной композиции находится на высоком уровне, значительно выше, чем у мастики «БИКАМ» и сравнима с термостабильностью герметика «Biguma AG».
- Исследования стойкости разработанной герметизирующей композиции в условиях воздействия различных факторов показали, что старение материала наиболее интенсивно происходит в начальный период времени. В дальнейшем процесс старения существенно замедляется.
- С увеличением ширины раскрытия загерметизированной трещины процесс ее разрушения ускоряется, вследствие более интенсивного ухудшения свойств герметизирующих материалов. При этом наибольшее изменение свойств отмечается при ширине раскрытия трещин превышающей 10% от первоначальной величины.
С использованием разработанной герметизирующей композиции в 2005 г. были произведены работы по санации трещин на опытном участке автодороги в г.Казани. Визуальные обследования опытного участка после проведенной санации трещин после 3 и 6 месяцев эксплуатации показали, что разрушений заделанных трещин не наблюдается. Вылет герметика из пазов трещин не отмечается. Кроме того, были проведены лабораторные исследования качества герметика после 3 и 6 месяцев эксплуатации в дорожном покрытии путем изъятия его из пазов трещин и проведения испытаний (см. табл. 2).
Таблица 2
Результаты лабораторных испытаний герметизирующей композиции
Наименование показателя | Результаты испытаний герметизирующей композиции | Метод испытаний | ||
исходной | после 3 мес. эксплуатации | после 6 мес. эксплуатации | ||
Температура размягчения, 0С | 86 | 88 | 88 | по ГОСТ 11506 |
Температура хрупкости, 0С | -39 | -38 | -37,6 | по ГОСТ 11507 |
Пенетрация при 250С, 0.1 мм | 112 | 108 | 105 | по ГОСТ 11501 |
Растяжимость при 00С | 42 | 40 | 39 | по ГОСТ 11505 |
Гибкость на брусе d=10 мм, 0С | -37 | -36 | -36 | по ГОСТ 30740-2000 |
Адгезия, выдерживает с контр.обр. № | 1 | 1 | 1 | по ГОСТ 11508-74* |
Температура липкости, 0С | >50 | >50 | >50 | по ГОСТ 30740-2000 |
Относительное удлинение при разрыве, % | 800 | 760 | 730 | по ГОСТ 30740-2000 |
Эластичность при 250С, % | 96 | 94 | 92 | - |
Водопоглощение, % | 0.10 | 0.11 | 0.11 | по ГОСТ 25945 |
Из таблицы 2 следует, что основные технических свойств материала в пределах установленных сроков эксплуатации изменялись несущественно. Наблюдение за опытным участком продолжаются.
Таким образом, проведенные исследования показали, что разработанная герметизирующая композиция обладает достаточно высокими физико-механическими характеристиками, высокой устойчивостью к старению под воздействием различных внешних факторов. Разработанная композиция может быть эффективно использована для санации трещин асфальтобетонных покрытий автомобильных дорог II-III дорожно-климатической зоны.