Десятые академические чтения раасн, 2006 г
Вид материала | Документы |
- Десятые академические чтения раасн, 2006, 1092.49kb.
- Десятые академические чтения раасн, 2006, 1519.63kb.
- Концепция устойчивого развития в стратегии градостроительства франции 05. 23. 22 Градостроительство,, 332.07kb.
- Резолюция районной детской экологической конференции Десятые Басарукинские чтения, 39.32kb.
- План организационно-педагогической деятельности с детьми, имеющими ярко-выраженные, 77.33kb.
- Новосибирский государственный педагогический университет, 43.06kb.
- Академические программы и экзаменационные курсы в австралии международные центры Embassy, 146.35kb.
- Экология человек общество, 371.15kb.
- Министерство образования и науки российской федерации московский государственный областной, 2810.15kb.
- Рассказывайте детям о ценности чтения. Показывайте связь чтения с их успехами в учебе, 97.26kb.
ВЛИЯНИЕ ТЕХНОЛОГИИ ИЗГОТОВЛЕНИЯ НА СОСТАВ И СВОЙСТВА
ЗОЛОЦЕМЕНТНЫХ ВЯЖУЩИХ
Объединение в 2004 г. в единый торговый дом двух крупных производителей в Западно-Сибирском регионе Топкинского и Искитимского заводов практически монополизировало рынок цемента. В результате цена на портландцемент за последние два года увеличилась более чем в два раза. В связи с этим проблема получения смешанных вяжущих в регионе, альтернативных традиционному портландцементу, не теряет своей актуальности.
Наиболее перспективным компонентом таких смешанных цементов в Сибири могут являться высококальциевые золы ТЭЦ (ВКЗ) от сжигания бурого угля Канско-Ачинского месторождения.
Однако применение ВКЗ в составе золопортландцемента (ЗПЦ) сопряжено с определенными трудностями: значительными колебаниями их состава и свойств, высоким содержанием в них свободного СаО, приводящим к деструкции материалов.
Исследования в этом направлении проводились многочисленными авторами. Ими показано, что для предупреждения деструктивных явлений в уже сформировавшейся структуре золоцементных вяжущих необходимы различные способы активации ВКЗ или применение добавок, связывающих свободную известь, находящуюся в золе в виде пережога.
Несмотря на большое количество работ, посвященных вопросам использования зол бурых углей (КАБ), четкие принципы выбора способов, устраняющих деструкцию, не сформулированы. В связи с этим нами было детально изучено влияние технологии изготовления золоцементных вяжущих на их состав и свойства.
В работе были использованы ВКЗ Барнаульской ТЭЦ-3 и портландцемент М400 Д20 Искитимского цементного завода. В качестве мелкого заполнителя для изготовления растворов состава 1:3 использовался мелкий Обской песок с модулем крупности 1,38.
Золоцементные вяжущие (ЗЦВ) изготавливались по трем технологиям:
1) сырьевые компоненты (ВКЗ и ПЦ) в различных соотношениях просто перемешивались;
2) сырьевые компоненты подвергались совместному помолу в лабораторной шаровой мельнице с соответствующей энергией помола 50, 100 и 150 % от энергии стандартного помола клинкера на цемент;
3) один из сырьевых компонентов, а именно ВКЗ, подвергался измельчению в шаровой мельнице также с энергией 50, 100, 150% и далее перемешивался с ПЦ.
Первоначально было изучено влияние помола на состав ВКЗ, а именно на изменение содержания свободной извести в золе и золопортландцементах (ЗПЦ). Экспериментальные данные свидетельствуют о том, что в зависимости от степени измельчения зол количество дополнительно вскрываемого оксида кальция увеличивается как в чистой золе, так и в ЗПЦ, однако этот процесс не бесконечен и имеет не прямо пропорциональную зависимость (рисунок 1).
После достижения максимального вскрытия свободной извести за счет разрушения остеклованной оболочки, «открытые» частицы СаОсвоб активнее начинают гидратировать и карбонизироваться, т.е. количество свободной извести в гидратированных ЗПЦ сокращается. Нами установлено, что наибольшая интенсивность вскрытия достигается уже при энергии помола 50% от энергии помола клинкера на цемент. За это время вскрывается 70-80% свободной СаО от количества суммарной свободной извести. Аналогичная картина наблюдается и в золопортландцементах. Это означает, что количество закрытой свободной извести значительно уменьшилось, что снижает вероятность возникновения деструктивных процессов в отдаленные сроки твердения.
Оценивая влияние помола на свойства ЗЦВ, можно отметить, что с увеличением дисперсности материалов соответственно уменьшается остаток на сите №008, увеличивается водопотребность (в 1,2-1,5 раза) и сокращаются сроки схватывания, однако последние соответствуют требованиям ГОСТ 310.3.
Температурный эффект ранней гидратации (критерий ∆T) в процессе помола возрастает как у чистых зол, так и у ЗЦВ. Испытания на равномерность изменения объема выдержали 80% из 100% составов на молотых ЗЦВ.
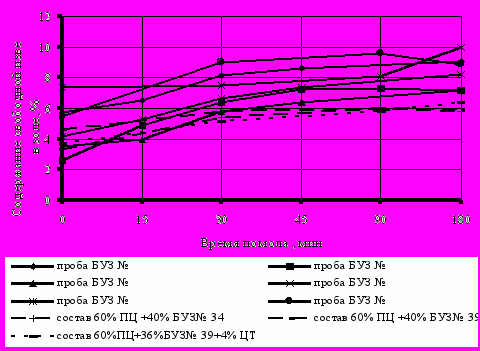
Рисунок 1 – Влияние помола на содержание свободной извести в ВКЗ и ЗПЦ
Далее было оценено влияние технологии изготовления вяжущих на их активность (рисунок 2, 3). При сопоставлении вяжущих одинакового состава, но изготовленных разными способами (путем простого перемешивания и помола), видно что при низком содержании золы (20%) активность их примерно одинакова и соответствует контрольному ПЦ. При увеличении количества добавки ВКЗ до 40% в молотых составах тенденция аналогична. Напротив, в немолотых вяжущих увеличение добавки ВКЗ до 40%приводит к снижению 28 суточной активности по сравнению с ЗПЦ, изготовленных посредством помола, на 25%, а по достижении 90 суток твердения в нормальных условиях – на 35%. При дальнейшем увеличении количества добавки ВКЗ в немолотых ЗЦВ до 60% и 80% наблюдается значительное отставание в активности относительно молотых вяжущих и ПЦ и в 28, и в 90 суток. При введении в состав вяжущего предварительно молотой ВКЗ в количестве 40% снижение активности ЗЦВ по сравнению с контрольным цементом отмечается всего на 10-15% как в нормальных условиях, так и при тепловлажностной обработке (ТВО).
Немолотые вяжущие при ТВО имеют отставание от молотых ЗПЦ по активности в 2,8-3 раза при расходе БУЗ до 40% и в 2 раза при 60%-ном содержании золы в вяжущем.
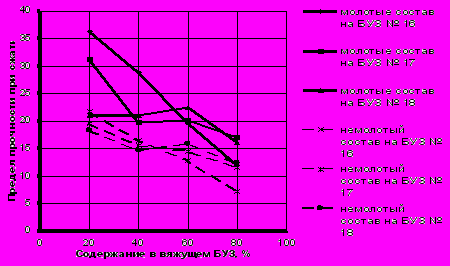
Рисунок 2 - Зависимость активности золопортландцемента изготовленных по разным технологиям, от количества золы в вяжущем (90 суток нормального твердения)
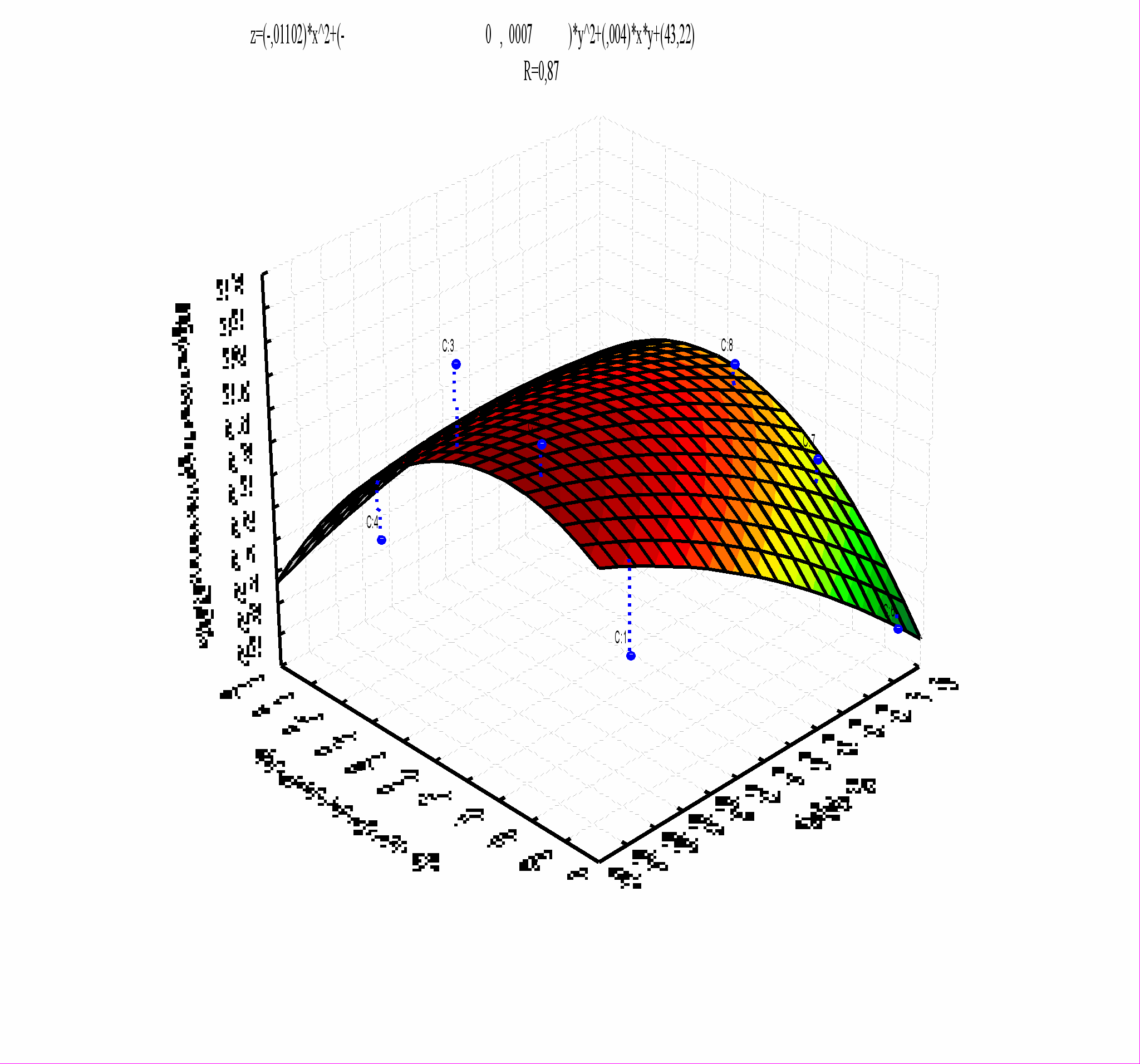
Рисунок 3 – Зависимость активности ЗЦВ от содержания молотой ВКЗ и энергии помола
Анализируя полученные данные мы предлагаем оптимальную дозировку добавки ВКЗ в ЗЦВ, составляющую 40% при совместном помоле золы с цементом, несмотря на то что результаты зависят от постоянно колеблющихся состава и свойств используемой золы.
УДК 691.059
Перекатов С.В., инженер
ОАО «Новолипецкий металлургический комбинат»
Михайлов В.В., д-р техн. наук, профессор, Корнеев А.Д., д-р техн. наук, профессор
Липецкий государственный технический университет
ПРОГНОЗИРОВАНИЕ ДОЛГОВЕЧНОСТИ КРОВЕЛЬНЫХ ПОКРЫТИЙ ЗДАНИЙ
ЛИСТОПРОКАТНОГО ПРОИЗВОДСТВА И ИХ МЕЖРЕМОНТНЫХ СРОКОВ СЛУЖБЫ
Обрушения конструкций покрытия Трансвааль-парка, плавательного бассейна в Пермской области, производственных цехов в Таганроге, Норильске, литейного цеха на Липецком тракторном заводе, литейного цеха на Мичуринском заводе поршневых колец и других показали, что условия приводящие к обрушению могут создаваться как на стадии проектирования, изготовления и монтажа так и на стадии эксплуатации. Поэтому проблема прогнозирования долговечности работы строительных конструкций покрытия является весьма актуальной.
Металлургическое прокатное производство является сложным технологическим процессом, при котором на строительные конструкции каркаса оказываются как силовые статические и динамические воздействия, так и влияние технологической среды. Прокатные цеха отличает большая протяженность и различная технологическая среда на отдельных участках. Это прежде всего повышенная температура, влажность, пары кислот, пылевыделения и другие. Подобные условия вызывают необходимость дифференцированно оценивать разрушающие факторы и прогнозировать сроки проведения обследований и ремонтов.
Для оценки коррозии металла и бетона в цеховой среде прокатного производства были установлены стенды с образцами. Стенды для испытания размещались в уровне осветительных галерей различных участков цехов (9 стендов в ЛПП и 8 стендов в ЛПЦ-5 ОАО «НЛМК») являющихся ключевыми в технологии производства металла и включающими непрерывно-травильный агрегат, стан и склады металла. Эти образцы развешивались в уровне покрытия здания на различных участках цехов и с принятой периодичностью производился замер потерянной массы в результате коррозии.
Анализ математических моделей развития коррозионного процесса строительных материалов позволяет заключить, что для описания зависимости скорости коррозии от времени можно использовать формулу
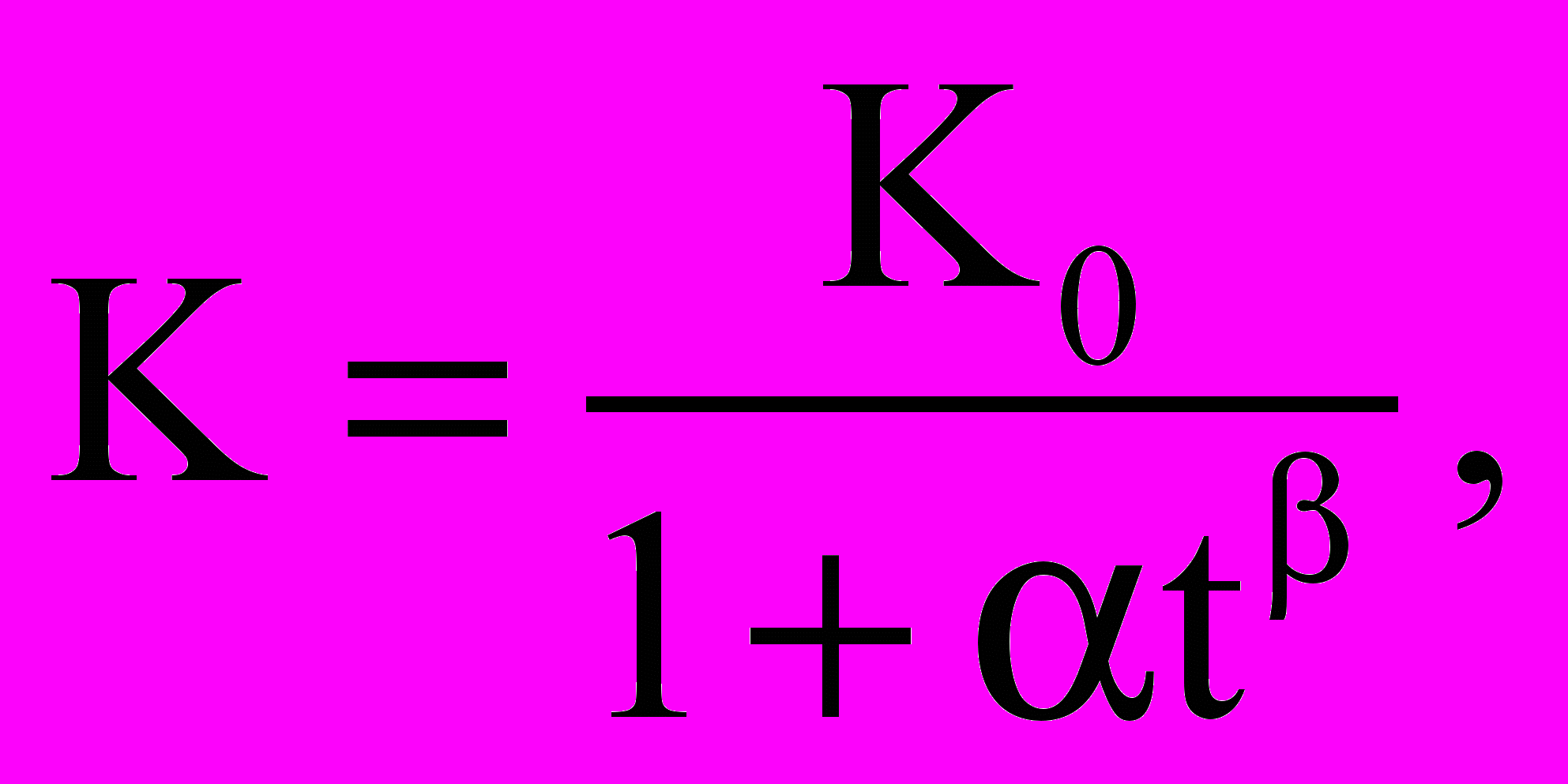

где К0 – начальная скорость коррозии; t – время; α и β – коэффициенты, зависящие от условий эксплуатации.
Определению подлежит не только величина начальной скорости коррозии, но и коэффициенты α и β. Эти коэффициенты являются эмпирическими и зависят от условий эксплуатации материала. По результатам стендовых испытаний была определена начальная скорости коррозии, её величина для ЛПП составила 931 г/м2 год.
Анализ влияния коэффициентов α и β на скорость коррозии металлов показал, что в эксплуатационных условиях цехов листопрокатного производства развитие скорости коррозии во времени может быть рассчитано по формуле
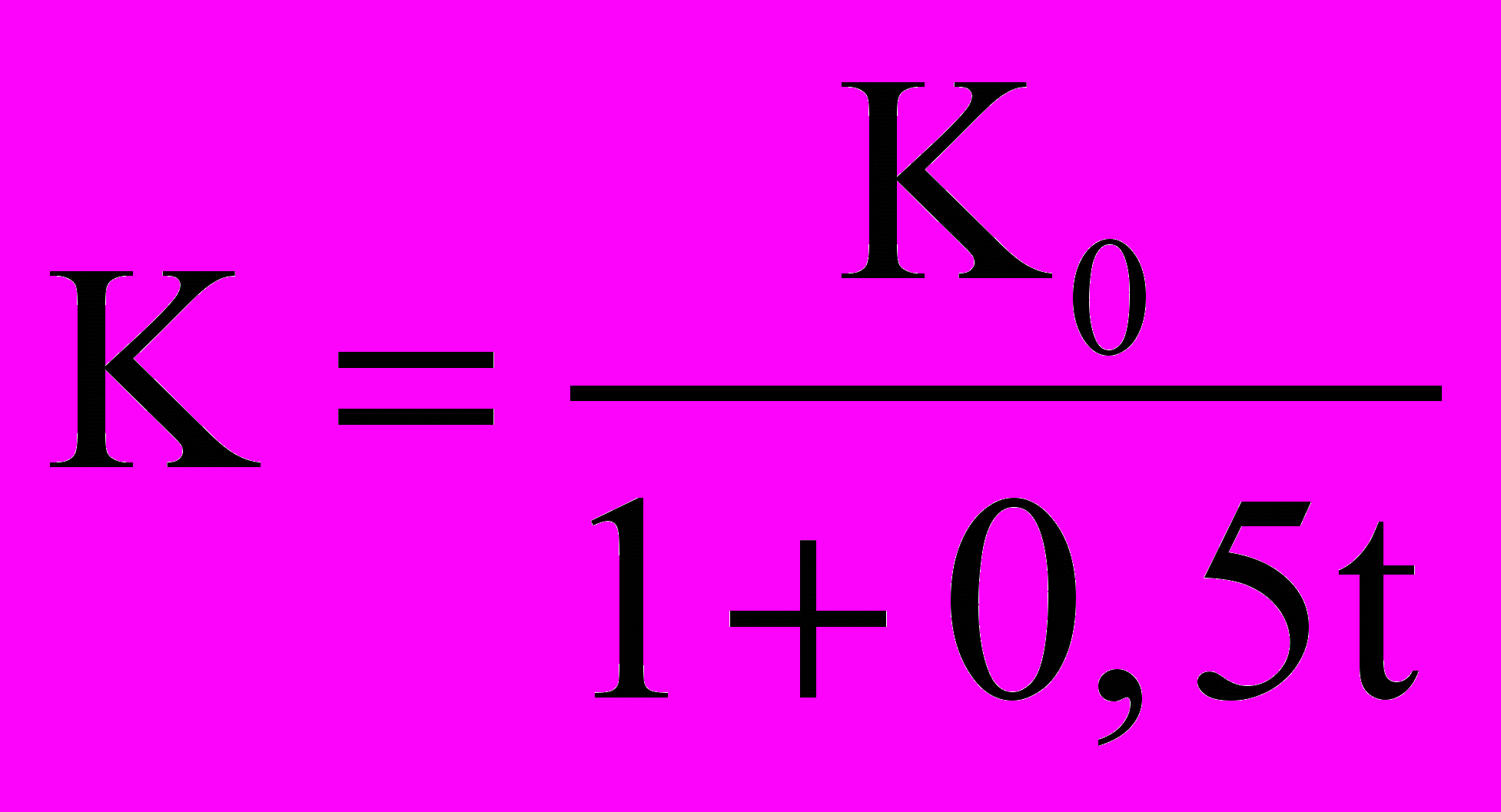
Для оценки глубины проникновения коррозионных поражений в металл и бетон осуществляли пересчет массового показателя коррозии в глубинный. Результаты свидетельствуют, что наибольшая начальная скорость коррозии наблюдается на входе и выходе непрерывно-травильного агрегата, наименьшая – на участке листоотделки металла. Из результатов стендовых испытаний распределение коррозионных потерь по участкам цеха видно, что значение скорости коррозии, найденное на участке листоотделки можно считать фоновым, отвечающим постоянным потерям металла в условиях отсутствия влияния технологических факторов цеха. Коррозия образцов на участках ЛПП имеет равномерный характер на всех технологических участках, за исключением пятиклетьевого стана и склада холоднокатаных рулонов металла, где она имеет преимущественно язвенный характер. Причиной этого на наш взгляд, может являться ускоренное увлажнение поверхности металлоконструкций.
Наряду со стендовыми испытаниями проводились замеры концентрации коррозионно-активных компонентов в цехах. Отбор проб воздуха проводили на тех участках цеха, где были размещены стенды коррозионных испытаний. Результаты показали, что наибольшее количество хлороводорода наблюдается на территории непрерывно-травильного агрегата (0,61 и 0,68 мг/м3). Высокое содержание хлороводорода отмечено также на участках склада горячекатаных рулонов металла и пятиклетьевого стана. На основании
полученных данных можно прогнозировать интенсивность развития технологической коррозии металлических и бетонных конструкций, сопоставляя результаты стендовых коррозионных испытаний и содержания паров хлороводорода в воздухе.
Полученные зависимости скорости коррозии строительных материалов в агрессивных условиях листопрокатного производства позволили спрогнозировать сроки их службы.
Как показали обследования кровельных покрытий зданий листопрокатного производства срок службы конструктивных элементов из бетона при максимальной концентрации хлоридов 11,7 мг/м3 находится в пределах от 22,5 до 35 лет. На момент обследования через 28 лет эксплуатации была заменена 151 железобетонная плита, что составляет 7,15% от первоначального количества, через 29 лет еще 110 плит или 5,2%, а через 35 лет эксплуатации было заменено уже 400 плит или 18,8%.
Срок службы теплоизоляционных материалов в условиях листопрокатного производства колеблется от 6 до 15 лет. При этом по данным фактическим обследований эффективными из них являются газосиликатобетон, минераловатные плиты и фибролит. Увлажнение теплоизоляционного слоя приводит к увеличению нагрузки в 1,2 раза, а теплопроводности на 50%, что способствует образованию конденсационной влаги на поверхности конструктивных элементов и длительному ее сохранению.
Таким образом, по результатам проведенной работы были установлены межремонтные сроки службы конструкционных элементов кровельных покрытий для зданий листопрокатного производства, периодичность и виды ремонтов.
СПИСОК литературЫ
1. Перекатов С.В. Комплексная оценка технического состояния покрытия объектов листопрокатного производства/С.В. Перекатов, В.В. Михайлов//Сб. науч. трудов преподавателей и сотрудников, посв. 35-летию НИС ЛГТУ. Часть 1. – Липецк: ЛГТУ, 2003. – С. 88 – 91.
2. Перекатов С.В. Анализ работы строительных ферм, эксплуатирующихся в газовоздушных средах различных помещений листопрокатного производства/С.В. Перекатов, В.В. Михайлов, А.Д. Корнеев, П.В. Требухин//Международ. сб. научных трудов «Совершенствование качества строительных материалов и конструкций (Модели, составы, свойства, эксплуатационная стойкость)». – Новосибирск: НГАУ, 2004. – С. 220 – 221.
УДК 666.972
Петропавловская В.Б., доцент, Шлапаков Ю.А., доцент, Новиченкова Т.Б.
Тверской государственный технический университет
СОВЕРШЕНСТВОВАНИЕ БЕЗОБЖИГОВОЙ
ТЕХНОЛОГИИ ПОЛУЧЕНИЯ ГИПСОВЫХ ИЗДЕЛИЙ
Одним из основных требований рынка строительных материалов является их соответствие современному дизайну, повышенным эксплуатационным требованиям и качеству. Они должны быть конкурентоспособными по отношению к аналогичным импортным материалам, широко представленным на отечественном рынке. С другой стороны, сам материал, технология его производства и эксплуатация должны быть безопасными и соответствовать требованиям не только отечественных, но и международных стандартов по безопасности и охране окружающей среды, в том числе требованиям Киотского протокола по сокращению выбросов углекислого газа в атмосферу. В наибольшей степени этим требованиям удовлетворяют гипсовые материалы, что делает их наиболее привлекательными на рынке строительных материалов за рубежом. В настоящее время рост гипсового производства превосходит рост мировых рынков всех других строительных материалов. Однако Россия в число стран лидеров по потреблению гипса, по данным Американского ежегодника «Mineral Yearbook», не входит [1]. Многие регионы России, не имеющие своего природного сырья, практически не используют гипсовые материалы и изделия из-за их высокой стоимости вследствие больших затрат на доставку. Однако практически все регионы страны имеют промышленные предприятия, на которых образуются многотоннажные техногенные гипсосодержащие отходы, представляющие собой «энергетические запасники». Использование таких отходов местной промышленности в производстве строительных материалов экономит топливные и энергетические ресурсы за счет исключения затрат на разведку и обустройство новых карьеров, на добычу и транспортировку сырья, а зачастую также на их первичную переработку, так как гипсовые отходы могут быть достаточно дисперсными и содержать полезные примеси. К таким предприятиям, на территории Тверского региона, относится Конаковский завод фаянсовых изделий. Отходы этого производства в виде отработанных гипсовых форм для литья керамических изделий представляют собой ценное, экологически чистое сырье, соответствующее по своему химическому составу гипсовому камню первого сорта.
Кроме того, во многих регионах применение гипса ограничивается только производством отделочных материалов, таких как сухие строительные смеси и гипсокартонные листы. Использование местных отходов промышленности в производстве гипсовых изделий позволяет значительно расширить область применения гипсовых вяжущих и материалов на их основе.
При использовании гипсовых отходов местных производств перспективным является встраивание небольших гибких технологических линий, которые можно разместить на существующих предприятиях по производству строительных изделий. Это дает возможность обеспечить покупателя дешевыми эффективными материалами и изделиями различного назначения, формы и размеров, в том числе и стеновыми изделиями.
Использование негидратационного твердения при получении гипсовых материалов позволяет повысить эффективность производства за счет экономии энергетических ресурсов на предварительный обжиг сырья. Возможность получения строительных материалов на основе двуводного гипса без традиционного перевода его в вяжущее путем термообработки показана в работах А.Ф. Полака [1]. Процесс негидратационного твердения согласно [2], обусловлен растворением мелких частиц и кристаллизацией растворенного вещества на поверхности крупных частиц в условиях фильтрационного прессования, имеющего ряд существенных недостатков.
Использование полусухого прессования для получения гипсовых изделий позволяет существенно упростить технологию и снизить энергозатраты за счет исключения операции сушки готовых изделий. Согласно гипотезе, принятой в работе [3], образование кристаллизационной структуры негидратационного твердения двуводного гипса при использовании бинарных сырьевых смесей обусловлено перекрыванием неподвижных приповерхностных слоев раствора с индивидуальной концентрацией, зависящей от размеров частиц. Одним из основных факторов, обуславливающих образование негидратационной структуры, в этом случае является давление прессования. Величина давления, используемого при прессовании изделия, должна обеспечивать сближение крупных и мелких частиц двуводного гипса на расстояния, при которых происходит перекрывание их приповерхностных слоев [2]. По результатам предыдущих исследований установлено, что это давление при использовании только двуводного гипса должно составлять 28 - 30 МПа. Именно в этом интервале наблюдался максимальный прирост прочности материала. Однако равновеликое общее давление прессования не гарантирует одинаковое давление в индивидуальном контакте между крупной и мелкой частицами прессуемого порошка. В связи с этим, представляет интерес использование гиперпрессования при формовании изделий на основе двуводного гипса.
В работе исследовалось влияние величины давления прессования на процесс структурообразования гипсовых материалов негидратационного твердения.
В исследованиях использовались бинарные сырьевые смеси из порошков тонкого и крупного помола двуводного гипса. Давление прессования варьировалось от 30 до 300 МПа.
По результатам исследований установлено, что с увеличением давления прессования от 30 до 200 МПа происходит увеличение прочности и плотности материала, что объясняется переходом коагуляционных контактов между частицами в конденсационно-кристаллизационные, доля которых увеличивается с ростом давления. Наибольшая прочность прессованного гипсового материала составляет 58,2 МПа, при средней плотности 2200 кг/м3. При дальнейшем увеличении давления прессования до 300 МПа снижается прочность и плотность материала вследствие упругого расширения материала и разрушения части конденсационно-кристаллизационных контактов. Прочность образцов при давлении прессования 300 МПа составила 42 МПа.
Таким образом, подтверждается физико-химическая роль давления прессования в процессах структурообразования систем на основе двуводного гипса по негидратационной схеме.
СПИСОК литературЫ
- Полак А.Ф., Ляшкевич И.М., Бабков В.В., Раптунович Г.С., Анваров Р.А. О возможности формирования кристаллизационных структур на основе двугидрата сульфата кальция // Известия вузов. – 1987. – №10. – с.60
- Мирсаев Р.Н., Бабков В.В., Юнусова С.С., Кузнецов Л.К., Недосеко И.В., Габитов А.И. Фосфогипсовые отходы химической промышленности в производстве стеновых изделий. – М.: Химия, 2004. – 176 с.
- Петропавловская В.Б., Кедрова Н.Г. Получение прессованных гипсовых материалов на основе гипсосодержащих отходов // Повышение эффективности производства и применения гипсовых материалов и изделий: Материалы II Всероссийского семинара с международным участием. – М.: ЛМ-ПРИНТ, 2004.
УДК 666.974.2
Печеный Б.Г., д-р техн. наук, профессор, Тотурбиев А.Б., инженер
Северо-Кавказский государственный технический университет
ТЕОРЕТИЧЕСКИЕ ПРЕДПОСЫЛКИ ПОЛУЧЕНИЯ НЕАВТОКЛАВНОГО ТЕПЛОИЗОЛЯЦИОННОГО ПЕНОБЕТОНА НА БЕСЦЕМЕНТНОМ КОМПОЗИЦИОННОМ ВЯЖУЩЕМ
Одним из главных направлений решения проблемы энергосбережения является сокращение потерь тепла через ограждающие конструкции зданий, сооружений, промышленного оборудования, тепловых сетей, которое не может быть обеспечено без применения высокоэффективных теплоизоляционных материалов.
Большой интерес представляют теплоизоляционные ячеистые бетоны получаемые на различных видах вяжущих (портландцементе, ВНВ, ТМЦ, гипсовом вяжущем, фосфогипсе, ГНЦВ, перлитоизвестковом вяжущем и др.), мелкозернистых заполнителей, тонкомолотых наполнителей, химических добавок, пенообразователей и т.д. Однако, значение средней плотности теплоизоляционного ячеистого бетона выпускаемого промышленностью автоклавированием, высокая и составляет 500-600 кг/м3 при достаточной прочности. Это еще более усугубляется при получении ячеистых теплоизоляционных бетонов (пенобетонов) неавтоклавного твердения.
Поэтому перспективными направлениями совершенствования технологии и повышения качества теплоизоляционных ячеистых бетонов являются дальнейшие теоретические проработки и экспериментальные исследования, направленные на упрощение технологических процессов, энергосбережение, (безавтоклавная технология); применение бесцементных вяжущих из местного минерального сырья и отходов производства; снижение средней плотности тем самым теплопроводности, и повышение прочности на сжатие.
В этой связи в Дагестанском государственном техническом университете в результате всесторонних теоретических и экспериментальных исследований получены эффективные виды безводных силикат-натриевых композиционных вяжущих и на их основе строительные материалы различного назначения 1, 2.
Обобщая результаты многочисленных исследований по применению безводных силикатов натрия, можно сделать вывод о том, что эти исследования были направлены в основном на разработку жаростойких материалов, получаемых по энергосберегающим технологиям, а именно жаростойким бетонам, теплоизоляционным материалам, для футеровки и теплоизоляции тепловых агрегатов с температурой службы 800-1600 оС.
Несмотря на большие преимущества жаростойких (в том числе и теплоизоляционных) бетонов на безводных силикат-натриевых композиционных вяжущих практически отсутствуют исследования направленные на разработку обычных стеновых теплоизоляционных материалов из этих вяжущих.
Это связано с тем, что безводные силикаты натрия являются наиболее дорогими компонентами в составе композиционного вяжущего. Согласно традиционной технологии изготовление безводных силикатов натрия (силикат-глыбы) достаточно энергоемкое и сложное производство. Их получают преимущественно сплавлением кварцевого песка с карбонатами или сульфатом натрия восстанавливающихся добавкой угля при 1400 оС с целью удешевления, а также по технологической необходимости. Для получения жидкого стекла (водного раствора силиката натрия) безводные силикаты натрия растворяют в автоклавных или специальных котлах при температуре 90-100 оС путем перемешивания, что увеличивает себестоимость вяжущего.
Поэтому возможность получения растворимого стекла и вяжущих композиций на его основе путем упрощения технологических переделов и применение в качестве сырья более доступного местного минерального сырья и технологических отходов позволит расширить область их применения и снизить затраты на производство теплоизоляционных изделий на основе этих вяжущих.
Целью наших исследований является разработка энергосберегающей технологии неавтоклавного теплоизоляционного пенобетона на бесцементном силикат-натриевом композиционном вяжущем с использованием местного сырья и отходов производств.
Для достижения поставленной цели были приняты рабочая гипотеза, заключающаяся в том, что для снижения стоимости единицы продукции теплоизоляционного пенобетона путем исключения из состава дорогостоящего компонента силиката натрия и уменьшения количества пенообразователя, целесообразно получить пеносиликат-натриевую массу путем предварительного нагрева в процессе мокрого перемешивания системы состоящей из кремнеземистой породы и соапстока – жидкого отхода получаемого при щелочной рафинации рыбьего жира. Известно 3, что ряд горных пород, содержащих высокий процент аморфного SiO2, хорошо растворяются в едких щелочах, образуя растворы силикатов щелочных металлов.
При этом можно предположить что:
- во-первых, тонкодисперсный диатомит в процессе совместного мокрого перемешивания с соапстоком при низкотемпературной (80-90 оС) тепловой обработке вступает в химическое взаимодействие с щелочью NаОН, содержащейся в соапстоке до установления «равновесия» между ними, образуя при этом высокомодульный водный раствор силиката натрия. Известно1, 2, что с увеличением кремнеземистого модуля силиката натрия, а, следовательно, вяжущего и материала на его основе повышается водостойкость;
- во-вторых, предварительные поисковые опыты показали повышенную способность разрабатываемого двухкомпонентного (mSiO2 nH2O: соапсток) вяжущего к пенообразованию, что создает мелкопористую структуру, необходимую для получения теплоизоляционного пенобетона;
- в-третьих, тонкомолотый карбонатный наполнитель, с развитой поверхностью являясь своего рода адсорбентом при перемешивании с пеномассой будет поглощать высокомодульное силикат-натриевое вяжущее обладающее высокими адгезионными свойствами, клеящая способность которого в 3-5 раза выше чем у цементов, после затвердения создает внутриповерхностную оболочку повышающую прочность мелкого наполнителя, следовательно, прочность теплоизоляционного пенобетона;
- в-четвертых, соапсток одновременно являясь пластификатором, придавая пенобетонной смеси повышенную подвижность и удобоукладываемость, снижает расход воды, что в свою очередь приводит к повышению прочности связующей пленки в пенобетоне.
Исходя из вышеизложенного и опираясь на результаты многочисленных исследований по применению силикатов натрия для получения различных строительных материалов, а также, учитывая его высокую активность по отношению к ряду веществ, можно сделать заключение о перспективности дальнейших исследований, направленных на разработку неавтоклавного теплоизоляционного пенобетона на бесцементном композиционном вяжущем.