Методические рекомендации и Контрольные задания для учащихся заочной формы обучения специальности 2 36 07 01 «Машины и аппараты химических производств и предприятий строительных материалов»
Вид материала | Методические рекомендации |
СодержаниеГорячая объемная штамповка Холодная штамповка Варианты контрольного задания 2 |
- Методические рекомендации и контрольные задания для учащихся заочной формы обучения, 346.07kb.
- Методические рекомендации и контрольные задания для учащихся заочной формы обучения, 340.97kb.
- Методические рекомендации и контрольные задания для учащихся заочной формы обучения, 730.2kb.
- Методические рекомендации и выполнение контрольных заданий для учащихся заочной формы, 667.06kb.
- Методические рекомендации и выполнение контрольных заданий для учащихся заочной формы, 667.12kb.
- Методические рекомендации и выполнение контрольных заданий для учащихся заочной формы, 779.21kb.
- Методические указания к выполнению практических работ по дисциплине «Экономика и управление, 238.85kb.
- Рабочая программа по дисциплине дс №09 Машины и аппараты химических производств для, 240.33kb.
- Методические указания по дипломному проектированию по специальности 170500 «Машины, 167.73kb.
- Планирование на предприятии Анализ хозяйственной деятельности, 78kb.
Ковка
Ковку применяют при производстве небольшого количества одинаковых заготовок. Это единственно возможный способ получения массивных заготовок (до 250 т).
Процесс ковки, осуществляемый только в горячем состоянии, состоит из чередования в определенной последовательности основных операций ковки. Прежде чем перейти к рассмотрению последовательности изготовления поковок, следует изучить операции ковки, их особенности и назначение.
Разработка процесса ковки начинается с составления чертежа поковки по чертежу готовой детали. Ковкой получают поковки относительно простой формы, требующие значительной обработки резанием.
Припуски и допуски на все размеры, а также напуски (упрощающие конфигурацию поковки) назначают в соответствии с ГОСТ 7062 – 79 (для стальных поковок, изготовляемых на прессах) или 7829 – 70 (для стальных поковок, изготовляемых на молотах).
В качестве исходной заготовки при ковке используют для мелких и средних по массе поковок сортовой прокат и блюмы; для крупных поковок – слитки. Массу заготовки определяют исходя из ее объема, который рассчитывают как сумму объемов поковки и отходов по формулам, приводимым в справочной литературе.
Поперечное сечение заготовки выбирают с учетом обеспечения необходимой уковки, которая показывает, во сколько раз изменилось поперечное сечение заготовки в процессе ковки. Чем больше уковка, тем лучше прокован металл, тем выше его механические свойства.
Последовательность операций ковки устанавливают в зависимости от конфигурации поковки и технических требований на нее, от вида заготовки.
С разнообразным универсальным кузнечным инструментом, применяемым для выполнения операций ковки, нужно ознакомиться при изучении этих операций. Изучая принципиальное устройство машин для ковки (пневматического и паровоздушного молотов, гидравлического пресса), обратите внимание, что применение типа оборудования обусловливается массой поковки.
В результате изучения процесса ковки необходимо иметь четкое представление о требованиях к конструкции деталей, получаемых из кованых поковок.
Горячая объемная штамповка
При объемной штамповке пластическое течение металла ограничивается полостью специального инструмента – штампа, который служит для получения поковки определенной конфигурации. Горячая объемная штамповка по сравнению с ковкой позволяет изготовить поковку по конфигурации очень близкую к готовой детали, с большей точностью и высокой производительностью. Однако необходимость использования специального инструмента для каждой поковки делает штамповку рентабельной лишь при достаточно больших партиях поковок. Штамповки получают поковки с массой 100-200 кг, а в отдельных случаях – до 3 т.
Исходные заготовки для объемной штамповки, как правило получают отрезкой сортового проката разнообразного профиля: круглого, квадратного, прямоугольного. В большинстве случаев для штамповки поковок сложной конфигурации нужно получить фасонную заготовку, т. е. приблизить ее форму к форме поковки. С этой целью исходную заготовку обычно предварительно деформируют в заготовительных ручьях многоручьевых штампов, в ковочных вальцах или другими способами. При штамповке больших партий поковок применяют прокат периодического профиля.
Наличие большого разнообразия форм и размеров поковок, сплавов, из которых они штампуются, привело к возникновению различных способов горячей объемной штамповки. При классификации этих способов в качестве основного признака принимают тип штампа, которым определяется характер деформирования металла в процессе штамповки. В зависимости от типа штампа выделяют штамповку в открытых и штамповку в закрытых штампах (безоблойную штамповку). Изучая эти способы штамповки, обратите внимание на их преимущества, недостатки и области рационального использования.
Для штамповки в открытых штампах характерно образование заусенца в зазоре между частями штампа. Заусенец при деформировании закрывает выход из полости штампа для основной массы металла, в то же время в конечный момент деформирования в заусенец вытесняются излишки металла.
При штамповке в закрытых штампах их полость в процессе деформирования металла остается закрытой. Преимущество способа – значительное уменьшение расхода металла, поскольку нет отхода в заусенец. Трудность применения штамповки в закрытых штампах – необходимость строгого соблюдения равенства объемов заготовки и поковки.
Кроме различия по типу инструмента (штампа) штамповку различают по виду оборудования, на котором она производится. Горячая объемная штамповка осуществляется на паровоздушных молотах, на кривошипных горячештамповочных прессах, горизонтально-ковочных машинах, гидравлических прессах. Штамповка на каждой из этих машин имеет свои особенности, преимущества и недостатки, которые необходимо четко представлять. Рассмотрев схемы машин объемной штамповки и принципы их действия, необходимо уяснить, для какого типа деталей рационально использовать то или иное оборудование с учетом его технологических возможностей. Большое внимание следует уделить особенностям конструкции поковок, штампуемых на каждом типе машин.
Разработка процесса объемной штамповки так же, как при ковке, начинается с составления чертежа поковки по чертежу готовой детали с учетом вида оборудования, на котором будет производиться штамповка. Большое значение при этом имеет правильный выбор расположения плоскости разъема штампов. На поковку, получаемую штамповкой, устанавливают припуски, допуски, напуски, штамповочные уклоны, радиусы закругления и размеры наметок под прошивку в соответствии с ГОСТом.
Массу заготовки под штамповку определяют, исходя из закона постоянства объема при пластическом деформировании, подсчитывая объем поковки и объем технологических отходов по формулам, приводимым в справочной литературе. Размеры заготовки и форму ее поперечного сечения определяют в зависимости от формы поковки и способа ее штамповки.
После штамповки поковки подвергают отделочным операциям, которые являются завершающей частью процесса горячей объемной штамповки и способствуют получению поковок с необходимыми механическими свойствами, точностью и шероховатостью поверхностей. От этих операций зависит трудоемкость последующей механической обработки.
Холодная штамповка
Холодную штамповку делят на объемную и листовую. При объемной штамповке – холодном выдавливании, высадке и формовке – заготовкой служит сортовой прокат. При этом получают изделия с высокими точностью и качеством поверхности. Однако из-за того, что усилия при холодной объемной штамповке значительно больше, чем при горячей, ее возможности ограничены из-за недостаточной стойкости инструмента.
К листовой штамповке относят процессы деформирования заготовок в виде листов, полос, лент и труб.
Процессы листовой штамповки можно разделить на операции, последовательно применение, которых придает исходной заготовке форму и размеры детали. Операции листовой штамповки можно объединить в две группы: разделительные и формоизменяющие. При выполнении разделительных операций деформирование заготовки происходит вплоть до ее разрушения. При выполнении формоизменяющих операций, наоборот, стремятся создать условия, при которых может быть получено наибольшее формоизменение заготовки без ее разрушения.
Изучая разделительные операции, обратите внимание, как влияют на качество получаемых изделий технологические параметры процесса (например, величина зазора между режущими кромками). Большое значение при разработке процессов вырубки изделий имеет правильное расположение вырубаемых деталей на листовой заготовке (раскрой материала). Правильный раскрой обеспечивает минимальные отходы при вырубке и достаточную величину перемычек между деталями, так как от их величины зависит качество получаемых деталей. Основным показателем экономичности раскроя можно принять коэффициент использования металла, равный отношению площади детали к площади листа, полосы или ленты, из которых эти детали вырубают. Следует отметить, что вырубка деталей из рулонной полосы или ленты экономичнее.
Рассматривая формоизменяющие операции, обратите внимание на то, что при операциях гибки и вытяжки без утонения изменения толщины стенки заготовки практически не происходят.
При гибке в каждом сечении по толщине заготовки одновременно действуют сжимающие и растягивающие напряжения, вследствие чего упругая деформация может быть относительно большой. Поэтому при гибке необходимо учитывать угол, на который «отпружинивает» изделие. Значение углов пружинения для каждого конкретного случая находят из справочников.
Растягивающие напряжения в изгибаемой заготовке зависят от отношения радиуса гибки к толщине материала и могут превышать допустимую величину при малом радиусе. В справочной литературе даются минимальные значения радиуса гибки для различных материалов.
При вытяжке полых изделий из плоской заготовки дно изделия, находящегося под пуансоном, практически не деформируется, а остальная часть заготовки (фланец) растягивается в радиальном направлении и сжимается в тангенциальном. При сжатии фланца иногда происходит образование складок; для предотвращения этого явления необходим прижим фланца к торцу матрицы.
Усилие, действующее со стороны пуансона на заготовку, увеличивается с ростом отношения диаметра заготовки к диаметру вытягиваемого изделия и может достигать величины, превышающей прочность стенки вытягиваемого изделия. При этом происходит отрыв дна. Для характеристики предельного формоизменения вводится коэффициент вытяжки.
В справочной литературе даются минимальные значения коэффициента вытяжки. Если необходимо получить изделие с коэффициентом вытяжки меньше предельного, применяют вытяжку в несколько переходов без утонения или с утонением стенок.
Для расчета массы заготовок используют закон постоянства объема, в соответствии с которым сохраняется постоянным объем металла до деформации и после нее. Но на практике всегда имеют место технологические отходы, в результате чего объем заготовки больше объема поковки на величину объема отходов. Во всех случаях в объем отходов входят угар (объем металла, окислившегося при нагреве заготовки) и технологические отходы, зависящие от способа обработки давлением.
При разработке процессов ковки необходимо пользоваться ГОСТ 7829-70 (ковка на молоте) и 7062-79 (ковка на прессе). Напуски при ковке применяют для упрощения формы поковки. Необходимость их применения и размеры указаны в ГОСТах.
При ковке технологические отходы зависят от формы поковки, а следовательно, и от операций или переходов ковки. Поэтому сначала необходимо установить переходы (операции) ковки, требующие для изготовления заданной детали, и изобразить их эскизы, показав взаимодействие заготовки и инструмента. Если для получения поковки необходим переход протяжки, то отходом будут обсечки; если необходима прошивка, то отходом будет выдра. Определив объемы угара и отходов, получают объем заготовки, а затем с учетом заданного профиля рассчитывают ее длину.
При разработке процессов горячей объемной штамповки прежде всего следует установить, как происходит штамповка. Горячую объемную штамповку подразделяют на различные виды в зависимости от многих факторов. По типу применяемого оборудования различают штамповку на молотах, горячештамповочных кривошипных прессах (в дальнейшем КГШП) и горизонтально-ковочных машинах (в дальнейшем ГКМ). Существуют и другие типы штамповочного оборудования, но их применяют значительно реже и в заданиях они не предусмотрены.
По характеру течения металла в штампе различают штамповку: в открытом штампе с образованием облоя (заусенца) на молотах, прессах и ГКМ; в закрытом штампе без облоя на прессах и ГКМ; выдавливанием грибовидных поковок на прессах; прошивкой на прессах и ГКМ.
В зависимости от расположения заготовки в штампе различают штамповку плашмя и в торец. При штамповке плашмя ось заготовки располагают перпендикулярно торцу штампа. Так штампуют поковки типа ступенчатых валиков, шатунов, вилок и прочие на молотах и КГШП. При штамповке в торец ось заготовки параллельна направлению действующего усилия. Так штампуют поковки типа колец и втулок на молотах и КГШП и все типы поковки на ГКМ.
Тип штамповочного оборудования указан на чертеже задания, а вид штамповки и расположение поковки в штампе устанавливают в зависимости от ее формы. Затем следует установить положение плоскости разъема штампа, т.е. определить, какая часть поковки будет оформляться в верхней части штампа, а какая – в нижней (для молота и КГШП) и какая часть – в матрицах, а какая – в пуансоне (для ГКМ).
Для построения чертежа поковки по ГОСТ 7505-74 необходимо установить: а) припуски на механическую обработку на те поверхности, где стоит знак обработки; б) штамповочные уклоны для облегчения выема поковки из штампа; в) радиусы скруглений для предотвращения зажимов металла в углах ручья штампа и концентрации напряжений в штампе.
Напуски на штампованных поковках образуются штамповочными уклонами. Уклоны необходимы на всех поверхностях поковки, располагающихся параллельно направлению движения бабы молота, ползуна КГШП, главного ползуна ГКМ.
Сквозные отверстия в поковках, штампуемых на молотах и КГШП. Получать нельзя во избежание поломки последних. В поковках делают наметки сверху и снизу, а между ними остается пленка, толщина которой S = 0,1dотв поковки. При штамповке на ГКМ в поковках колец и втулок получают сквозные отверстия методом просечки. Эта операция одновременно служит для отделения кольца от прутка. Так как штамп ГКМ имеет две плоскости разъема и поковка сама из него выпадает, на наружных поверхностях уклонов не предусматривают, а дают уклон только на поверхности отверстия для выхода прошивного пуансона.
Разработку процесса холодной листовой штамповки начинают с выбора необходимых технологических операций и определения формообразующей операции, по которой ведется расчет размеров заготовки.
Если деталь изготовляют вырубкой, то определяют необходимую ширину полосы. При наличии у детали сложного контура вначале следует продумать расположение деталей на полосе, чтобы расход металла был минимальным. Затем в зависимости от толщины материала устанавливают величину перемычек как между деталями а, так и между краями полосы и деталями а1 (рис. 17). Минимальную расчетную ширину полосы определяют расчетом. Затем выбирают вид стандартного исходного материала – лист, ленту, полосу. Для заданных деталей рекомендуется применять ленту по ГОСТ 503-74. Ширину ленты В получают, увеличивая Врасч до ближайшего стандартного размера. Коэффициент использования материала определяют по формуле
Ким = [Fдет/(АхВ)]х100%,
где Fдет – площадь детали, мм2; А – расстояние между центрами соседних деталей, мм; В – стандартная ширина ленты, мм.
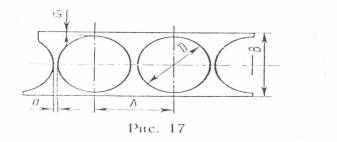

Если деталь изготовляют вытяжкой, то вначале необходимо определить диаметр заготовки (Dз) исходя из равенства площадей поверхностей детали и заготовки (рис. 18): Fпов.заг. = Fпов.дет., где Fпов.дет. – сумма площадей поверхностей геометрических фигур, образующих данную деталь. Тогда Dз = 1,13 Fпов.дет.
Ввиду того, что расчеты по этой формуле получаются громоздкими, рекомендуется использовать готовые формулы из справочника. Затем производят расчет заготовки по указанной выше методичке.
Если деталь изготовляют гибкой, то ширина полосы или ленты равна ширине детали, а длину заготовки определяют, как сумму длин прямых и изогнутых участков. В процессе гибки наружные слои растягиваются, а внутренние сжимаются, а разделяет их недеформирующийся нейтральный слой.
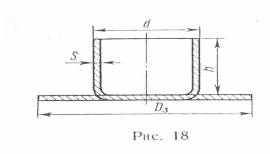
Длина каждого изогнутого участка равна длине его нейтрального слоя и определяется по формулам из справочника. В работе следует сделать все технологические расчеты, указанные в задании, используя учебник, справочник и данные методических указаний.
Варианты контрольного задания 2
Вариант 1
1. Изобразите схемы продольной и поперечно-винтовой прокатки. Изложите сущность прокатки и условие захвата заготовки валками.
2. По эскизу готовой детали (рис.) разработайте схему технологического процесса изготовления поковки способом ковки на гидравлическом ковочном прессе. При выполнении работы следует:
1) Описать сущность процесса ковки и указать область ее применения;
2) Установить температурный интервал ковки, вид нагревательного устройства;
3) Выполнить чертеж детали в масштабе по заданному варианту;
4) Определить форму и размеры заготовки, рассчитать припуски и допуски;
5) Выполнить чертеж заготовки с расчетными размерами в масштабе;
6) Составить схему технологического процесса (см. приложение А).
Вариант 2
1. Изобразите эскизы пяти профилей сортового проката. Перечислите прокатные операции технологического процесса получения сортового проката, начиная с указания исходного материала.
2. По эскизу готовой детали (рис.) разработайте схему технологического процесса изготовления поковки способом ковки на гидравлическом ковочном прессе. При выполнении работы следует:
1) Описать сущность процесса ковки и указать область ее применения;
2) Установить температурный интервал ковки, вид нагревательного устройства;
3) Выполнить чертеж детали в масштабе по заданному варианту;
4) Определить форму и размеры заготовки, рассчитать припуски и допуски;
5) Выполнить чертеж заготовки с расчетными размерами в масштабе;
6) Составить схему технологического процесса (см. приложение А).
Вариант 3
1. Составьте таблицу «Кузнечный инструмент и приспособления» по схеме:
Наименование инструмента, приспособления | Назначение |
| |
2. По эскизу готовой детали (рис.) разработайте схему технологического процесса изготовления поковки способом ковки на гидравлическом ковочном прессе. При выполнении работы следует:
1) Описать сущность процесса ковки и указать область ее применения;
2) Установить температурный интервал ковки, вид нагревательного устройства;
3) Выполнить чертеж детали в масштабе по заданному варианту;
4) Определить форму и размеры заготовки, рассчитать припуски и допуски;
5) Выполнить чертеж заготовки с расчетными размерами в масштабе;
6) Составить схему технологического процесса (см. приложение А).
Вариант 4
1. Опишите сущность процессов упругой и пластической деформации с точки зрения кристаллического строения металлов. Дайте определение пластичности и изложите влияние на нее химического состава, структуры, температуры нагрева; скорости и степени деформации.
2. По эскизу готовой детали (рис.) разработайте схему технологического процесса изготовления поковки способом ковки на гидравлическом ковочном прессе. При выполнении работы следует:
1) Описать сущность процесса ковки и указать область ее применения;
2) Установить температурный интервал ковки, вид нагревательного устройства;
3) Выполнить чертеж детали в масштабе по заданному варианту;
4) Определить форму и размеры заготовки, рассчитать припуски и допуски;
5) Выполнить чертеж заготовки с расчетными размерами в масштабе;
6) Составить схему технологического процесса (см. приложение А).
Вариант 5
1. Перечислите способы холодной объемной штамповки. Опишите сущность холодного выдавливания. Изобразите схемы пяти разновидностей холодного выдавливания.
2. По эскизу готовой детали (рис.) разработайте схему технологического процесса изготовления поковки способом ковки на гидравлическом ковочном прессе. При выполнении работы следует:
1) Описать сущность процесса ковки и указать область ее применения;
2) Установить температурный интервал ковки, вид нагревательного устройства;
3) Выполнить чертеж детали в масштабе по заданному варианту;
4) Определить форму и размеры заготовки, рассчитать припуски и допуски;
5) Выполнить чертеж заготовки с расчетными размерами в масштабе;
6) Составить схему технологического процесса (см. приложение А).
Вариант 6
1. Опишите явления, происходящие в металле при холодном деформировании, и укажите сущность процесса упрочнения.
2. По эскизу готовой детали (рис.) разработайте схему технологического процесса получения деталей методом холодной объемной штамповки:
1) Описать сущность холодной объемной штамповки и указать область ее применения;
2) Вычертить деталь в масштабе, в соответствии с заданным вариантом;
3) Определить вид исходного материала;
4) Определить размеры заготовки;
5) Вычертить схему штамповки на холодновысадочном автомате и описать рабочий цикл изготовления винта (см. приложение Б).
Вариант 7
1. Изложите сущность процесса волочения и укажите области его применения. Изобразите схему процесса. Опишите типы волочильных станов. Укажите необходимые условия для успешного ведения процесса.
2. По эскизу готовой детали (рис.) разработайте схему технологического процесса получения деталей методом холодной объемной штамповки:
1) Описать сущность холодной объемной штамповки и указать область ее применения;
2) Вычертить деталь в масштабе, в соответствии с заданным вариантом;
3) Определить вид исходного материала;
4) Определить размеры заготовки;
5) Вычертить схему штамповки на холодновысадочном автомате и описать рабочий цикл изготовления винта (см. приложение Б).