Методические рекомендации и Контрольные задания для учащихся заочной формы обучения специальности 2 36 07 01 «Машины и аппараты химических производств и предприятий строительных материалов»
Вид материала | Методические рекомендации |
- Методические рекомендации и контрольные задания для учащихся заочной формы обучения, 346.07kb.
- Методические рекомендации и контрольные задания для учащихся заочной формы обучения, 340.97kb.
- Методические рекомендации и контрольные задания для учащихся заочной формы обучения, 730.2kb.
- Методические рекомендации и выполнение контрольных заданий для учащихся заочной формы, 667.06kb.
- Методические рекомендации и выполнение контрольных заданий для учащихся заочной формы, 667.12kb.
- Методические рекомендации и выполнение контрольных заданий для учащихся заочной формы, 779.21kb.
- Методические указания к выполнению практических работ по дисциплине «Экономика и управление, 238.85kb.
- Рабочая программа по дисциплине дс №09 Машины и аппараты химических производств для, 240.33kb.
- Методические указания по дипломному проектированию по специальности 170500 «Машины, 167.73kb.
- Планирование на предприятии Анализ хозяйственной деятельности, 78kb.
Изготовление отливок литьем по выплавляемым моделям
Рассмотрите последовательность изготовления моделей из легкоплавкого состава в пресс-формах, сборку моделей в блок, изготовление литейной формы, подготовку ее к заливке, заливку расплавленным металлом, выбивку и очистку отливок. Обратите внимание на особенности этого способа: разовая модель не имеет разъема и знаковых частей, а ее контуры повторяют форму отливки; форма, полученная по выплавляемым моделям, представляет собой тонкостенную, не имеющую разъема оболочку; форма изготовляется из специальной огнеупорной смеси, состоящей из пылевидного кварца и гидролизованного раствора этилсиликата; для обеспечения высокой прочности и удаления остатков модельного состава литейные формы прокаливают при температуре 850-900 С, после чего заливают расплавленным металлом. Отметьте основные преимущества литья по выплавляемым моделям. Этим способом наиболее экономично изготовлять мелкие, но сложные и ответственные отливки с высокими требованиями по точности геометрических размеров и шероховатости поверхности, а также детали из специальных сплавов с низкими литейными свойствами. Рассмотрите недостатки способа. Обратите внимание на технологические возможности и области применения способа.
Изготовление отливок литьем в кокиль
Металлические формы (кокили) – литейные формы многократного использования. Их изготовляют из стали, чугуна и алюминиевых сплавов.
Рассмотрите конструкции кокилей: неразъемных, разъемных (с вертикальным, горизонтальным разъемом, комбинированные) и створчатых. Для получения внутренних полостей отливок широко применяют металлические стержни. Обратите внимание на устройство каналов для отвода газов из полостей форм и на устройства, используемые для удаления отливок, а также на конструкции металлических стержней. Уясните назначение предварительного подогрева форм, теплозащитных покрытий, наносимых на рабочие поверхности форм, последовательность сборки кокилей.
Повышенные скорости затвердевания и охлаждения отливок в одних случаях способствуют получению мелкозернистой структуры и повышению механических свойств, а в других случаях вызывают отбел.
Для изготовления отливок литьем в кокили широко используют однопозиционные и многопозиционные кокильные машины и автоматические линии. Рассмотрите принцип работы однопозиционной кокильной машины.
Отметьте основные достоинства литья в кокили: высокую точность геометрических размеров и низкую шероховатость поверхностей отливок, повышение механических свойств отливок, увеличение производительности, экономию производственных площадей. Недостатки способа: сложность изготовления кокилей и их низкая стойкость.
Уясните технологические возможности способа и области его применения.
Изготовление отливок литьем под давлением
Рассмотрите устройство машины литья под давлением с горизонтальной холодной камерой прессования и последовательность операций изготовления отливок, устройство пресс-форм и приспособлений для удаления отливок.
Обратите внимание на то, что скорость впуска расплавленного металла в пресс-форму составляет 0,5-120 м/с, а конечное давление достигает 100 МПа. Следовательно, форма заполняется за десятые, а для особо тонкостенных отливок – за сотые доли секунды. Сочетание особенностей процесса – металлической формы и внешнего давления на металл – позволяет получать отливки высокого качества. Основные достоинства литья под давлением: высокая точность геометрических размеров и низкая шероховатость поверхностей отливок, возможность изготовления сложных, тонкостенных отливок из алюминиевых, магниевых и других сплавов, высокая производительность способа. Недостатки способа: сложность изготовления пресс-форм, ограниченный срок их службы. Обратите внимание на технологические возможности способа и области его применения.
Изготовление отливок центробежным литьем
Сущность процесса заключается в свободной заливке расплавленного металла во вращающуюся форму, формование отливки в которой осуществляется под действием центробежных сил. Рассмотрите устройство машин с горизонтальной и вертикальной осями вращения и последовательность операций изготовления отливок. Обратите внимание на достоинства центробежного литья, технологические возможности способа и области применения. Уясните недостатки центробежного литья.
Технический контроль
Технический контроль ведут на всех стадиях изготовления отливок, начиная с приготовления формовочных и стержневых смесей, изготовления литейной оснастки, форм и стержней. Основные виды брака отливок: газовые. Песчаные и усадочные раковины, горячие и холодные трещины, спаи и недоливы. Уясните причины их образования и методы предупреждения дефектов. Ознакомьтесь с современными методами контроля в литейном производстве.
Методические указания по выполнению контрольного задания 1
Первый вопрос вариантов контрольной работы относится к способу ручной формовки в опоках по разъемной модели, чтобы ответить на него, следует изучить тему и методические указания к ней. Для ответа на второй вопрос требуется изучение темы по специальным методам литья. Внимательно ознакомьтесь с методическими указаниями.
Основа для разработки технологического процесса изготовления отливки – чертеж детали (в контрольном задании даны эскизы деталей). На чертеже детали в соответствии с ГОСТ 2.423 – 73 наносят технологические указания, необходимые для изготовления модельного комплекта, формы и стержня, и получают чертеж отливки с модельно-литейными указаниями. Кроме того, разрабатывают документацию (технологическую карту), которая содержит необходимые сведения для всех этапов изготовления отливки.
На рисунке 2 в качестве примера приведены эскизы стальной (а) и чугунной (б) деталей. Обратите внимание на поверхности деталей, подвергающиеся механической обработке. Условно они обозначены знаком . Остальные поверхности механической обработке на подлежат, на что указывает знак (в правом углу эскиза).
При разработке эскиза отливки с литейно-модельными указаниями на эскиз детали условно наносят (рис. 2, в):
- плоскость разъема модели и формы (1), их обозначают РМ и двумя стрелками с буквами В (верх) и Н (низ);
- припуски на механическую обработку (2), их обозначают тонкими линиями у поверхностей, где указан знак обработки ;
- отверстия, не получаемые при литье, зачеркивают тонкими линиями (5);
- контуры стержня со стержневыми знаками (3), их обозначают тонкими линиями и штриховкой у контура;
- формовочные уклоны (4), на вертикальных стенках их обозначают тонкими линиями.
Помимо этих обозначений указывают процент усадки сплава, из которого изготавливают отливку. Кроме того, на технологический чертеж отливки наносят литниковую систему, прибыли, выпоры, которые на рассматриваемом эскизе для простоты не указаны.
На рис. 2, г дан эскиз чугунной отливки с модельно-литейными указаниями. Для этой отливки используется горизонтальный стержень. Обратите внимание на различие в конструкции стержневых знаков: конусные знаки – у вертикального стержня (рис. 2, в) и цилиндрические – у горизонтального.
При разработке технологических указаний исходят из условия обеспечения качества отливки и экономической целесообразности. Так, выбирая плоскость разъема, следует помнить, что наиболее ответственные поверхности отливки лучше располагать в нижней части формы или вертикально, так как в верхней части отливки скапливаются дефекты – газовые раковины и шлаковые включения. Плоскость разъема выбирают с учетом удобства формовки и извлечения модели из формы. Кроме того, желательно, чтобы отливка или, по крайней мере ее базовые поверхности для механической обработки были расположены в одной полуформе.
Величины припусков на механическую обработку и размеры знаковых частей стержня определены ГОСТом.
На рис. 2, д дан эскиз деревянной модели для ручной формовки. Модель имеет стержневые знаки (они закрашены черным цветом), причем верхний знак – отъемный, формовочные уклоны и радиусы скруглений в местах перехода стенок r. Размеры модели выполняют с учетом припусков на механическую обработку и усадки сплава. Деревянный разъемный ящик для ручной набивки стержня показан на рис. 2, е.
Эскизы собранных форм для чугунной и стальной отливок даны на рис. 3. Обратите внимание на различие литниковых систем:
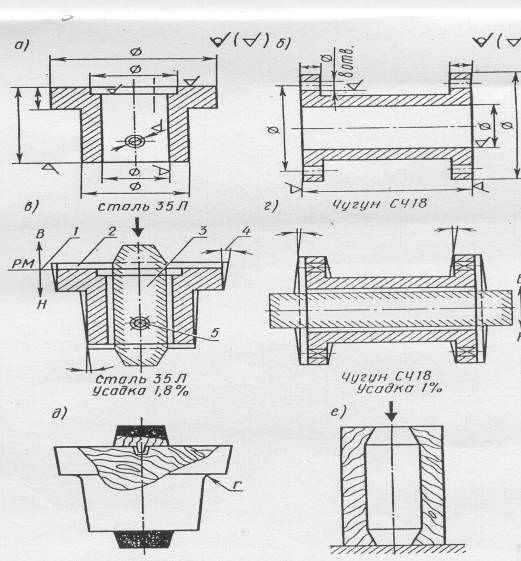
Рис.2
В форме для чугунного литья (рис. 3, а) имеются шлакоуловитель и выпоры; в форме для стального литья (рис. 3, б) шлакоуловитель отсутствует, а для компенсации большой усадки стали и предупреждения усадочных раковин предусмотрены прибыли.
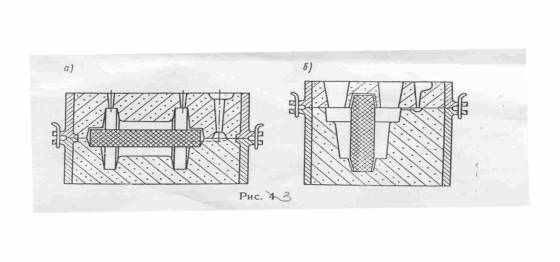
Рис.3
Для создания условий направленного затвердевания в форме стальной отливки часто применяют холодильники (металлические вставки). Обратите внимание на графическое изображение каждого элемента формы.
Эскизы готовых отливок с литниковой системой приведены на рисунке 4: на рис. 4, а – отливка из чугуна, на рис. 4, б – из стали.
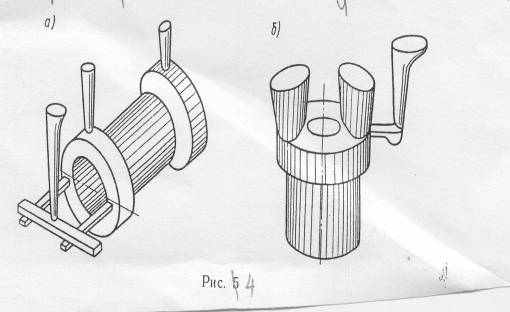
Рис. 4
Варианты контрольного задания 1
Вариант 1
1. По эскизу детали (рис. 5) разработайте эскиз отливки с модельно-литейными указаниями. Приведите эскизы модели, стержневого ящика и собранной литейной формы (в разрезе). Опишите последовательность изготовления формы методом ручной формовки.
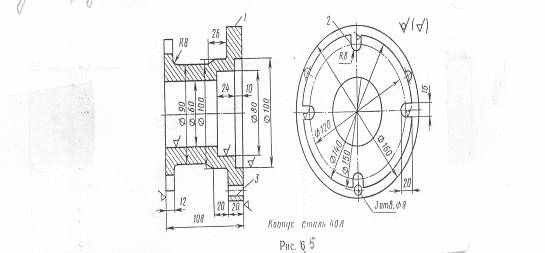
Рис.5
2. Изложите сущность способа литья под давлением. Приведите схему изготовления отливок литьем под давлением на машинах с горизонтальной камерой прессования. Укажите достоинства, недостатки и области применения этого способа литья.
Вариант 2
1. По эскизу детали (рис. 6) разработайте эскиз отливки с модельно-литейными указаниями, приведите эскизы модели, стержневого ящика и собранной литейной формы (в разрезе). Опишите последовательность изготовления формы методом ручной формовки.
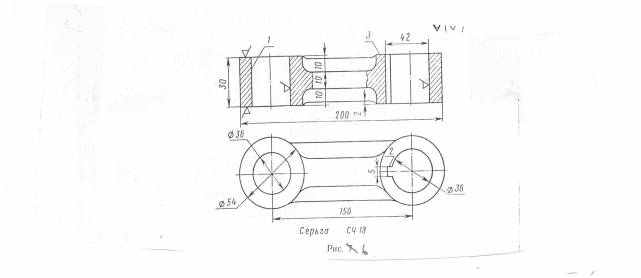
Рис.6
2. Опишите технологию изготовления стержней. Какими свойствами должны обладать стержневые смеси.
Вариант 3
1. По эскизу детали (рис. 7) разработайте эскиз отливки с модельно-литейными указаниями, приведите эскизы модели, стержневого ящика и собранной литейной формы (в разрезе). Опишите последовательность изготовления формы методом ручной формовки.
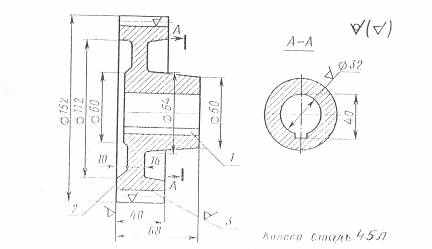
Рис.7
2. Приведите характеристику литейных свойств сплавов; укажите их влияние на качество отливок. Изложите принципы конструирования отливок с учетом литейных свойств.
Вариант 4
1. По эскизу детали (рис. 8) разработайте эскиз отливки с модельно-литейными указаниями, приведите эскизы модели, стержневого ящика и собранной литейной формы (в разрезе). Опишите последовательность изготовления формы методом ручной формовки.
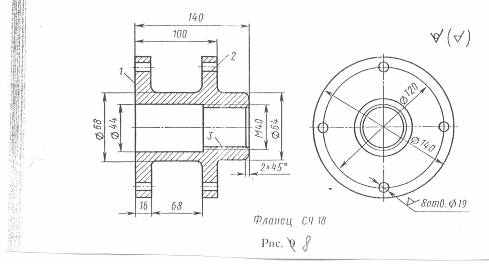
Рис.8
2. Изобразите схему центробежного литья на машинах с горизонтальной осью вращения. Изложите сущность и особенности этого способа литья; укажите достоинства, недостатки и области применения.
Вариант 5
1. По эскизу детали (рис. 9) разработайте эскиз отливки с модельно-литейными указаниями, приведите эскизы модели, стержневого ящика и собранной литейной формы (в разрезе). Опишите последовательность изготовления формы методом ручной формовки.
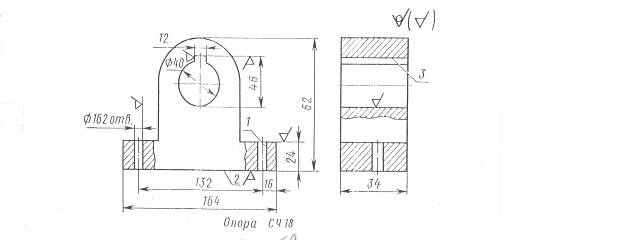
Рис.9
2. Изложите сущность способа литья в оболочковых формах и приведите поясняющие эскизы. Укажите достоинства, недостатки и области применения этого способа литья.
Вариант 6
1. По эскизу детали (рис. 10) разработайте эскиз отливки с модельно-литейными указаниями, приведите эскизы модели, стержневого ящика и собранной литейной формы (в разрезе). Опишите последовательность изготовления формы методом ручной формовки.
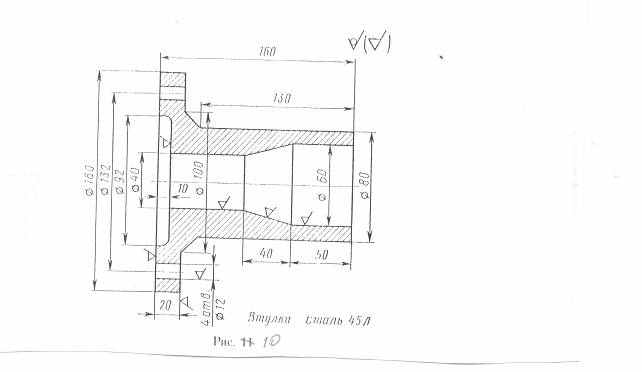
Рис.10
2. Опишите последовательность производства отливок по выплавляемым моделям и приведите поясняющие эскизы. Укажите преимущества, недостатки и области применения этого метода литья.
Вариант 7
1. По эскизу детали (рис. 11) разработайте эскиз отливки с модельно-литейными указаниями, приведите эскизы модели, стержневого ящика и собранной литейной формы (в разрезе). Опишите последовательность изготовления формы методом ручной формовки.
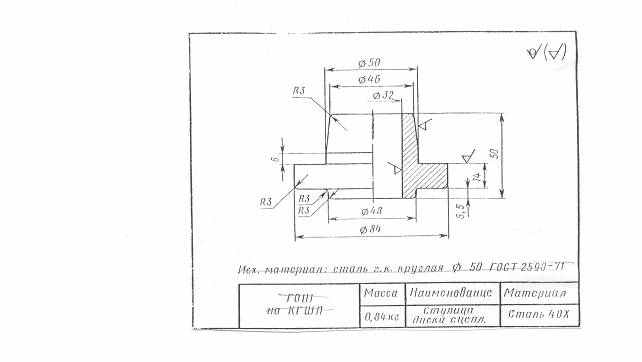
2. Изложите сущность способа литья в кокиль; изобразите схемы конструкций кокилей. Укажите применяемые сплавы, достоинства, недостатки и области применения этого способа.
Вариант 8
1. По эскизу детали (рис. 12) разработайте эскиз отливки с модельно-литейными указаниями, приведите эскизы модели, стержневого ящика и собранной литейной формы (в разрезе). Опишите последовательность изготовления формы методом ручной формовки.
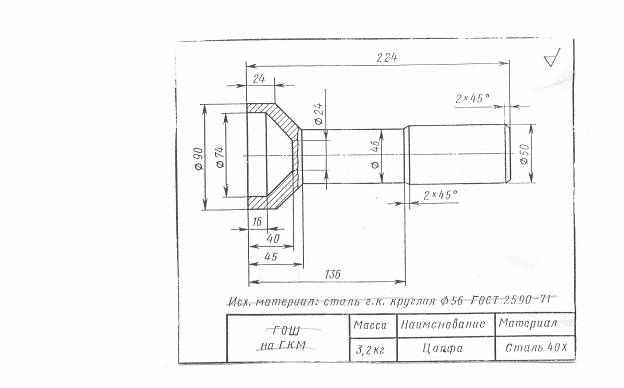
2. Изобразите схему центробежного литья на машинах с вертикальной осью вращения. Изложите сущность и особенности этого способа литья; укажите достоинства, недостатки и области применения.
Вариант 9
1. По эскизу детали (рис. 13) разработайте эскиз отливки с модельно-литейными указаниями, приведите эскизы модели, стержневого ящика и собранной литейной формы (в разрезе). Опишите последовательность изготовления формы методом ручной формовки.
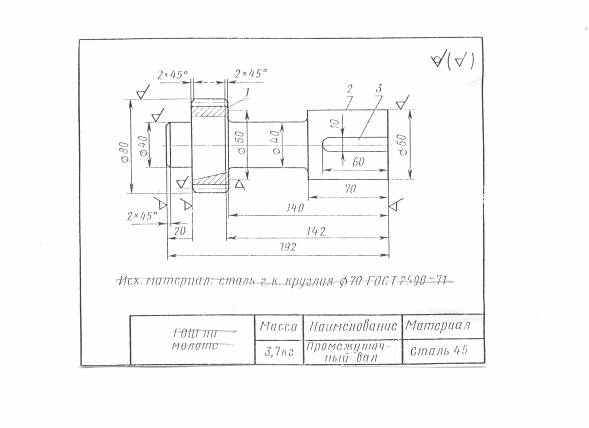
2. Опишите назначение литниковой системы и из каких элементов она состоит.
Вариант 10
1. По эскизу детали (рис. 14) разработайте эскиз отливки с модельно-литейными указаниями, приведите эскизы модели, стержневого ящика и собранной литейной формы (в разрезе). Опишите последовательность изготовления формы методом ручной формовки.
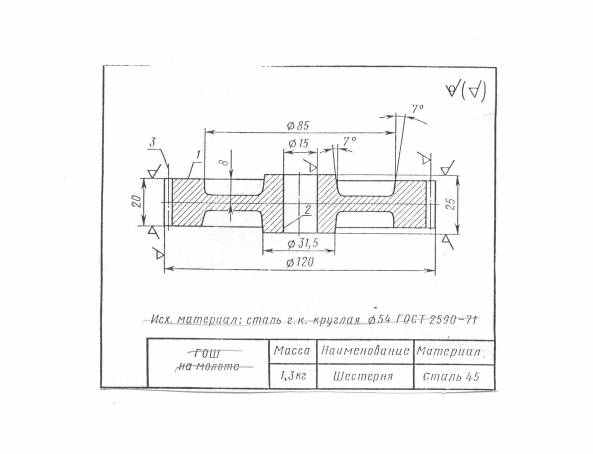
2. Опишите виды литейного брака, в чем их причины.
Методические указания к разделу
Технология обработки металлов давлением
Общая характеристика обработки металлов давлением
Обработке давлением подвергают более 90% выплавляемой стали и 60% цветных металлов и сплавов. При этом получают изделия, различные по назначению, массе, сложности, причем не только в виде промежуточных заготовок для окончательной обработки их резанием, но и готовые детали с высокой точностью и низкой шероховатостью. Процессы обработки давлением очень разнообразны и их обычно делят на шесть основных видов: прокатку, прессование, волочение, ковку, объемную и листовую штамповку. Запомните их технологические возможности и области применения в машиностроении. Применение процессов обработки давлением определяется возможностью формообразования изделий с высокой производительностью и малыми отходами, а также возможностью повышения механических свойств металла в результате пластического деформирования.
Физико-механические основы обработки металлов давлением
Обработка давлением основана на способности металлов в определенных условиях получать пластические деформации под действием внешних сил. Пластическая деформация поликристаллических тел, которыми являются конструкционные металлы, образуется за счет сдвигов между отдельными кристаллами (зернами) и их пластической деформации. Поэтому вначале необходимо рассмотреть механизм пластической деформации монокристалла – скольжение и двойникование, а затем деформацию металла, имеющего поликристаллическое строение. Деформация зерен металла при пластическом деформировании приводит к изменению его физико-механических свойств. Если это изменение сохраняется после пластической деформации, ее называют холодной, а все явление в совокупности называют упрочнением или наклепом.
При нагреве металла, получившего упрочнение, происходит внутренняя перестройка кристаллической структуры. Таким образом, при определенной температуре происходит замена деформированных зерен новыми, равноосными. Это явление называют рекристаллизацией, а деформацию, при которой рекристаллизация происходит во всем объеме металла, называют горячей.
Рассматривая изменения в строении металла при пластической деформации, необходимо помнить, что конструкционные металлы содержат неметаллические включения, которые располагаются между зернами поликристалла. При пластической деформации эти включения вытягиваются в виде волокон, обусловливая различие свойств металла в направлениях вдоль и поперек волокон. При пластическом деформировании происходит не только изменение формы заготовки, но и изменение свойств металла. Для получения изделий необходимой формы и качества надо знать основные законы пластической деформации и влияние условий обработки на свойства деформируемого металла.
Основные технологические свойства деформируемого металла – пластичность и сопротивление деформированию. Эти свойства зависят от химического состава металла или сплава, температуры и скорости деформирования, схемы приложения сил и предшествующей обработки.
При разработке процессов обработки давлением считают, что объем металла до деформации равен объему металла после деформации (закон постоянства объема) и каждая точка деформируемого тела перемещается в направлении наименьшего сопротивления (закон наименьшего сопротивления). Перемещению металла противодействуют силы трения, возникающие на поверхности контакта деформирующего инструмента и металла. Эти силы трения оказывают существенное влияние на пластичность металла и его сопротивление деформированию.
Нагрев металлов перед обработкой давлением
Нагрев металла перед пластическим деформированием – один из важнейших вспомогательных процессов при обработке давлением и производится с целью повышения пластичности и уменьшения сопротивления деформированию. Любой металл или сплав должен обрабатываться давлением во вполне определенном интервале температур. Например, сталь 10 может подвергаться горячему деформированию при температурах не выше 1260º С и не ниже 800º С. Нарушение температурного интервала обработки приводит к отрицательным явлениям, происходящим в металле (перегреву, пережогу) и в конечном итоге к браку. При нагреве необходимо обеспечить равномерную температуру по сечению заготовки и минимальное окисление ее поверхности. Для качества металла большое значение имеет скорость нагрева: при медленном нагреве снижается производительность и увеличивается окисление (окалинообразование), при слишком быстром нагреве в заготовке могут появиться трещины. Склонность к образованию трещин тем больше, чем больше размеры заготовки и меньше теплопроводность металла (у высоколегированных сталей, например, теплопроводность ниже, чем у углеродистых сталей, и меньше скорость нагревания).
Знакомясь с принципом работы и конструкцией печей и электронагревательных устройств, обратите внимание на их технологические возможности и области применения, характеризуемые типоразмером и величиной партии заготовок.
Прокатка и прессование
Прокатка – один из распространенных видов обработки металлов давлением. При прокатке металл деформируется в горячем или холодном состоянии вращающимися валками, конфигурация и взаимное расположение которых различно. Различают три схемы прокатки: продольную, поперечную и поперечно-винтовую.
При наиболее распространенной продольной прокатке в очаге деформации происходит обжатие металла по высоте, уширение и вытяжка. Величина деформации за проход ограничивается условием захвата металла валками, которое обеспечивается наличием трения между валками и прокатываемой заготовкой.
Инструмент прокатки – гладкие и калиброванные валки; оборудование – прокатные станы, устройство которых определяется прокатываемой на них продукцией.
Исходной заготовкой прокатки являются слитки.
Продукцию прокатки (прокат) обычно подразделяют на четыре основные группы. Наибольшая доля приходится на группу листового проката. Группу сортового проката составляют профили простой и сложной (фасонной) формы. Прокатанные трубы разделяют на бесшовные и сварные. К специальным видам проката относят прокат, поперечное сечение которого по длине периодически меняется, а также изделия законченной формы (колеса, кольца).
Прокат используют в качестве заготовок в кузнечно-штамповочном производстве, при изготовлении деталей механической обработкой и при создании сварных конструкций. Поэтому сортаменту основных групп проката следует уделить особое внимание.
Для получения из проката профилей небольших размеров, с высокой точностью и малой шероховатостью применяют волочение, осуществляемое как правило, в холодном состоянии. Рассматривая схему деформирования металла при волочении, надо отметить, что в очаге деформации металл испытывает значительные растягивающие напряжения тем больше, чем больше усилие волочения. Чтобы усилие не превысило допустимой величины, ведущей к обрыву изделия, ограничивают обжатия за один проход, принимают меры для уменьшения трения между металлом и инструментом и вводят промежуточный отжиг, поскольку при холодном волочении металл упрочняется.
Процесс прессования, осуществляемый в горячем или холодном состоянии, позволяет получать профили более сложной формы, чем при прокатке, и с более высокой точностью. Заготовками являются слитки, а также прокат.
Рассматривая схему деформирования металла при прессовании, надо отметить, что в очаге деформации металл находится в состоянии всестороннего неравномерного сжатия. Эта особенность дает возможность прессовать металлы и сплавы, обладающие пониженной пластичностью, что является одним из преимуществ этого процесса. Прессованием более экономично изготовлять небольшие партии профилей, поскольку переход от изготовления одного профиля к другому осуществляется легче, чем при прокатке. Однако при прессовании значителен износ инструмента и велики отходы металла.
Прессование производят на специализированных гидравлических прессах. Знакомясь с устройством инструмента, обратите внимание на расположение и взаимодействие его частей при прессовании сплошных и полых профилей.