Учебно-методический комплекс дисциплины Бийск бпгу имени В. М. Шукшина
Вид материала | Учебно-методический комплекс |
- Учебно-методический комплекс дисциплины Бийск бпгу имени В. М. Шукшина, 2836.1kb.
- Учебно-методический комплекс дисциплины Бийск бпгу имени В. М. Шукшина, 2979.19kb.
- Учебно-методический комплекс дисциплины Бийск бпгу имени В. М. Шукшина, 2143.51kb.
- Учебно-методический комплекс дисциплины Бийск бпгу имени В. М. Шукшина, 785.31kb.
- Учебно-методический комплекс дисциплины Бийск бпгу имени В. М. Шукшина, 793.69kb.
- Учебно-методический комплекс дисциплины Бийск бпгу имени В. М. Шукшина, 901.29kb.
- Учебно-методический комплекс дисциплины Бийск бпгу имени В. М. Шукшина, 2591.69kb.
- Учебно-методический комплекс дисциплины Бийск бпгу имени В. М. Шукшина, 814.76kb.
- Учебно-методический комплекс дисциплины Бийск бпгу имени В. М. Шукшина, 2075.7kb.
- Учебно-методический комплекс дисциплины Бийск бпгу имени В. М. Шукшина, 1147.22kb.
10. ОСНОВЫ ТЕХНОЛОГИИ ОБРАБОТКИ МЕТАЛЛОВ ДАВЛЕНИЕМ, ЛИТЕЙНОГО ПРОИЗВОДСТВА И СВАРКИ
10.1. ХАРАКТЕРИСТИКА ОСНОВНЫХ СПОСОБОВ ОМД
Обработкой давлением называют технологические процессы изготовления изделий или заготовок путём пластического деформирования материалов приложенным извне усилием.
Достоинствами ОМД являются высокая производительность, экономный расход металла, улучшение механических свойств металла.
Основными видами ОМД являются: прокатка, волочение, прессование, свободная ковка, объёмная и листовая штамповка.
10.1.1. Прокатка металлов
Прокаткой называется процесс обжатия заготовки между вращающимися валками прокатного стана.
П
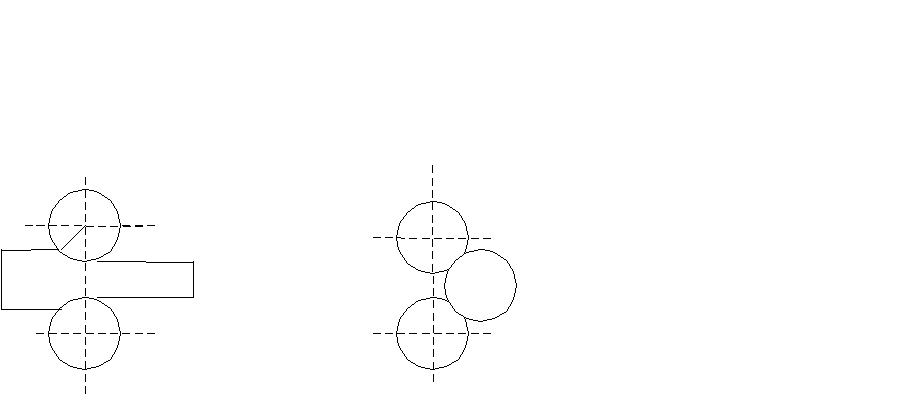
Взаимное расположение валков и заготовки, форма и число валков могут быть различными. Выделяют три основных вида прокатки: продольную, поперечную и поперечно-винтовую (косую).
При продольной прокатке заготовка деформируется между двумя валкам и, вращающимися в разные стороны, и перемещается перпендикулярно к осям валков. (Рис. 1)
h0 h
Рис. 1 Рис. 2
Важнейшей характеристикой деформации является обжатие.
Абсолютное обжатие: h = h0 - h
Относительное обжатие:
= {(h0 – h)/h}·100%
Т.к. h = 2D·(1 – cos), то абсолютное обжатие увеличивается с увеличением диаметра (D) валков и угла захвата ( = 5…30°). Для увеличения силы трения производят насечку валков.
При поперечной прокатке волки, вращаясь в одном направлении, придают вращение заготовке в противоположном направлении и деформируют её. (Рис. 2)
При поперечно-винтовой прокатке валки расположены под углом и сообщают заготовке при деформации вращательное и поступательное движения. Применяется для получения бесшовных труб и в других случаях.
Форму поперечного сечения прокатанной полосы называют профилем. Совокупность форм и размеров профилей, получаемых прокаткой, называют сортаментом. Сортамент прокатываемых профилей разделяется на четыре основные группы: сортовой прокат, листовой, трубы и специальные виды проката.
Сортовой прокат делят на профили простой геометрической формы (квадрат, круг, прямоугольник, шестигранник) и фасонные (швеллер, рельс, угловой и тавровый профили и т.д.)












































Швеллер Рельс Угловой Тавровый
Листовой прокат из стали и цветных металлов используют в различных отраслях промышленности. Листовую сталь делят на автотракторную, трансформаторную, котельную, судостроительную, жесть, броневую, кислото- и жаропрочную и др. Расширяется производство листовой стали с оловянным, цинковым, алюминиевым и пластмассовым покрытиями. Кроме того, листовую сталь разделяют на толстолистовую (толщиной 4-160 мм) и тонколистовую (< 4 мм). Листы толщиной менее 0,2 мм называют фольгой.
Трубы разделяют на бесшовные и сварные. Производство бесшовных труб осуществляется в два этапа: 1) прошивка заготовки (получение гильзы) при поперечно-винтовой прокатке, где на пути движения металла устанавливается на длинном стержне оправка (дорн), прошивающая заготовку; 2) получение трубы путём прокатывания гильзы в нагретом состоянии на раскатных станах. Сварные трубы изготавливают из полосы (штрипса) при помощи различных методов сварки.
К специальным видам проката относят: колёса, кольца, шары, периодические профили с периодически изменяющимися формой и площадью поперечного сечения вдоль оси заготовки. Их получают в основном на станах поперечной и поперечно-винтовой прокатки.
10.1.2. Прессование и волочение
Прессование – это технологический процесс ОМД, заключающийся в выдавливании металла пуансоном из закрытого контейнера через отверстия в матрице. Профиль изделия определяется профилем отверстия в матрице.
Прессованием можно обрабатывать такие специальные стали и сплавы цветных металлов, которые ввиду их низкой пластичности другими видами ОМД деформировать невозможно или затруднительно. Точность прессованных профилей выше, чем прокатанных.
Различают прямую и обратную схемы прессования. При прямом методе направления течения металла и движения пуансона совпадают; при обратном – металл движется в направлении противоположном движению пуансона.
К недостаткам прессования можно отнести большие потери металла, т.к. весь металл не может быть выдавлен из контейнера, и в нём остаётся так называемый пресс-остаток, который после окончания прессования отрезается от полученного профиля.
Волочение – это процесс ОМД, при котором материал протягивается через отверстие волоки (фильеры), площадь выходного сечения которой меньше площади заготовки. В результате поперечные размеры изделий уменьшаются, а длина увеличивается.
Волочение осуществляется в холодном и горячем состояниях с применением смазки. Исходными заготовками служат прокатанные или прессованные прутки и трубы из стали и цветных металлов. Применяется волочение для изготовления проволоки малого диаметра (от 4 до 0,002 мм), а также для калиброванных прутков различного профиля и тонких труб. Изделия, полученные волочением имеют гладкую поверхность и точные размеры.
Волоки изготавливают из инструментальных сталей У8…..У12; Х12М; твёрдых сплавов ВК2, ВК3; рубина, алмаза.
10.1.3. Ковка и штамповка
Ковка – это один из способов ОМД, при котором инструмент оказывает многократное прерывистое воздействие на нагретую заготовку, в результате чего она, деформируясь, приобретает заданную форму и размеры.
Различают ковку в штампах (штамповка) и без применения штампов (свободная ковка).
При свободной ковке перемещение деформированного металла не встречает сопротивления своему движению со стороны инструмента.
Ковка является единственно возможным способом изготовления тяжёлых поковок (до 250 т) типа валов гидрогенераторов, турбинных дисков, коленчатых валов судовых двигателей, валков прокатных станов и т.д.
К основным операциям ковки относятся: осадка, протяжка, прошивка, рубка, гибка.
Осадка – операция уменьшения высоты заготовки при увеличении площади её поперечного сечения. Разновидностью осадки является высадка, при которой металл осаживают лишь на часть длины заготовки.
Протяжка – операция удлинения заготовки или её части за счёт уменьшения площади поперечного сечения.
Прошивка – операция получения полостей в заготовке за счёт вытеснения металла.
Рубка – операция отделения части заготовки по незамкнутому контуру путём внедрения деформирующего инструмента, например, топора.
Гибка – операция придания заготовке изогнутой формы по заданному контуру.
Ковка подразделяется на ручную и машинную. Ручную осуществляют молотом на наковальне и применяют для индивидуального изготовления мелких изделий при ремонтных работах. Машинную ковку производят на ковочных молотах и прессах.
Штамповка представляет собой процесс ОМД, формообразование изделия при которой происходит в штампах, т.е. обеспечивается принудительное получение изделием формы и размеров.
Горячая объёмная штамповка применяется в основном для массового и серийного производства поковок и позволяет получать изделия с высокой точностью формы и размеров. Технологический процесс состоит из разрезки металла на заготовки, нагрева заготовок, штамповки, термообработки, отделки поковок.
Холодная объёмная штамповка применяется для поковок небольшого размера.
Листовой штамповкой изготовляют плоские или пространственные тонкостенные изделия. Толщина используемых листовых заготовок при холодной штамповке до 4 мм; при горячей – более 4 мм. Продукция отличается высокой прочностью и не нуждается в последующей обработке на металлорежущих станках. Сортамент изделий очень разнообразен – от деталей часов до корпусов морских судов.
Штамповку взрывом с использованием тротила, аммонала и др. взрывчатых веществ используют для изготовления мелкосерийных крупногабаритных деталей из толстолистовых заготовок.
При электрогидравлической штамповке кратковременный электрический разряд в жидкой среде создаёт ударную волну, давление которой достигает нескольких сотен МПа. Установки не требуют фундамента, малогабаритны, легко перемещаются.
10.1.4. Новые направления обработки металлов давлением
Обработку давлением некоторых сталей и сплавов осуществляют в условиях сверхпластичности. Сверхпластичность – значительное увеличение пластичности и уменьшение сопротивления деформации при температуре фазовых превращений и вполне определённых скоростях деформации. В этих условиях проявляется в основном межкристаллитная деформация, и отсутствует какое-либо значительное упрочнение металла.
Изотермическую штамповку используют для сталей и сплавов с узким температурным интервалом обработки и не допускающих больших скоростей деформации. Штамп для такой штамповки изготовлен из жаропрочного сплава и установлен в индукционном нагревателе, обеспечивающем одинаковую и постоянную температуру заготовок и штамповых вставок. Изотермическая штамповка осуществляется на гидропрессах и улучшает структуру и свойства поковок.
Применение вибрации при волочении, горячей объёмной и холодной листовой штамповке благодаря уменьшению контактного трения снижает усилия деформирования и приводит к повышению пластичности металла в процессе его обработки. Одновременно улучшаются структура и качество изделия.
Для изготовления изделий из низкопластичных и труднодеформируемых металлов и сплавов применяют гидростатическое выдавливание, при котором жидкость оказывает высокое давление с торца и боков на заготовку, установленную в контейнере. Для горячего выдавливания подбирают жидкую среду, которая является одновременно и нагревателем для заготовки. При достижении требуемого давления металл заготовки выдавливается через матрицу с огромной скоростью, достигающей сотни метров в секунду.
10.2. ЛИТЕЙНОЕ ПРОИЗВОДСТВО
Литейное производство – отрасль машиностроения, занимающаяся изготовлением фасонных заготовок или деталей путём заливки расплавленного металла в специальную форму, полость которой имеет конфигурацию заготовки (детали). Получающаяся при затвердевании деталь или заготовка называется отливкой.
Литьём получают разнообразные конструкции отливок массой от нескольких граммов до 300 т.
10.2.1. Модельный комплект
Модельный комплект – это совокупность технологической оснастки и приспособлений, необходимых для образования в форме полости, соответствующей контурам отливки. В модельный комплект включают: модели, модельные плиты, стержневые ящики, модели элементов литниковой системы и другие приспособления.
Литейная модель – приспособление, при помощи которого в литейной форме получают полость с формой и размерами близкими к конфигурации требуемой отливки. Литейные модели бывают: неразъёмными, разъёмными, с отъёмными частями и др.Изготовляют из древесины, металла, пластмассы, воска или парафина.
Модельная плита – металлическая плита с закреплёнными на ней моделями и элементами литниковой системы.
Стержневой ящик – приспособление, служащее для изготовления стержней. Бывают цельными, разъёмными, вытряхными. Изготавливают из древесины или металла.
10.2.2. Формовочные и стержневые материалы
Формовочные материалы – это совокупность природных и искусственных материалов, используемых для приготовления формовочных и стержневых смесей. В качестве исходных материалов используют формовочные кварцевые пески и литейные формовочные глины. Глины обладают связующей способностью и термохимической устойчивостью, что позволяет получать отливки без пригара. Кроме того, используют противопригарные добавки (каменноугольную пыль, графит), защитные присадочные материалы (борную кислоту, серный цвет) и др. добавки.
Формовочные смеси должны иметь высокую огнеупорность, достаточную прочность и газопроницаемость, пластичность и податливость.
Огнеупорность – способность смеси и формы сопротивляться размягчению или расплавлению под воздействием температуры расплавленного металла. Чем крупнее песок, чем меньше в нём примесей и пыли, тем более огнеупорна смесь. При низкой огнеупорности на поверхности отливки образуется пригар (побочное соединение формовочной смеси с поверхностью отливки.
Прочность – способность материала формы не разрушаться при извлечении модели из формы, транспортировке и заливке формы. Прочность формовочной смеси увеличивается с увеличением содержания глины и с уменьшением размеров зёрен песка.
Газопроницаемость – способность смеси пропускать через себя газы. Она тем выше, чем больше песка в формовочной смеси и чем он крупнее, а также чем меньше содержание глины.
Пластичность – способность деформироваться без разрушения и точно воспроизводить отпечаток модели. Пластичность смеси увеличивается с повышением в ней (до определённого предела) связующих материалов и воды, а также песка с мелкими зёрнами.
Податливость – способность формы или стержня сжиматься при усадке отливки.
Стержневая смесь – это многокомпонентная смесь формовочных материалов, соответствующая условиям технологического процесса изготовления литейных стержней. Стержни при заливке расплавленного металла испытывают значительные тепловые и механические воздействия по сравнению с формой, поэтому стержневые смеси должны иметь более высокие огнеупорность, газопроницаемость, податливость, малую газотворную способность, легко выбиваться из отливки.
10.2.3. Литниковая система
Литниковая система – это система каналов, через которые расплавленный металл подводят в полость формы. Она должна обеспечивать заполнение литейной формы с необходимой скоростью, задерживание шлака и других неметаллических включений, выход паров и газов из полости формы, непрерывную подачу расплавленного металла к затвердевающей отливке.
10.2.4. Технология изготовления литейных форм и получения отливок.
Для получения отливок по чертежу детали изготавливают деревянную или металлическую модель, а также разъёмные стержневые ящики для стержня, формирующего внутренние полости отливки. Затем готовят литейную форму, для чего на модельную плиту устанавливают половину модели, опоку (опока – жёсткая рама или ящик без дна; служит для удержания формовочной смеси, изготавливается из металлического сплава) и засыпают формовочную смесь в опоку. После уплотнения смеси опоку переворачивают на 180°, устанавливают вторую половину модели с моделями элементов литниковой системы, вторую опоку и повторяют формовочные операции. По окончании формовки снимают верхнюю полуформу, извлекают обе половины модели, модели литниковой системы, устанавливают стержень и вновь накрывают нижнюю полуформу верхней. В подготовленную таким образом форму через литниковую систему заливают жидкий металл, который, кристаллизуясь в полости формы, образует отливку.
Охлаждение отливок в литейных формах после заливки продолжается до температуры выбивки. Небольшие тонкостенные отливки охлаждаются в форме за несколько минут, а толстостенные (массой 50-60 т) в течение нескольких суток и даже недель. Для сокращения продолжительности охлаждения отливок, особенно массивных, используют различные методы принудительного охлаждения: форму обдувают воздухом; в формы при формовке укладывают змеевики или трубы, по которым пропускают воздух или воду. При этом качество отливок не ухудшается.
Обрубка отливок – процесс удаления с отливки прибылей, литников, выпоров и заливов (облоев) по месту сопряжения полуформ.
Очистка отливок – процесс удаления пригара, остатков формовочной и стержневой смеси с наружных и внутренних поверхностей отливки.
10.3. СВАРКА МЕТАЛЛОВ
Сваркой называется технологический процесс образования неразъёмных соединений за счёт сил взаимодействия атомов (молекул) контактирующих поверхностей сопрягаемых деталей.
10.3.1. Способы сварки
Все способы сварки подразделяются на две основные группы: сварка плавлением и сварка давлением (пластическим деформированием). Остальные способы – это их разновидности или комбинации.
При сварке плавлением формирование сварного шва осуществляется за счёт местного сплавления соединяемых деталей без приложения давления. Расплавляются кромки свариваемых деталей (основной металл) либо дополнительный присадочный или электродный металл.
При сварке давлением сближение атомов в контактирующих поверхностях происходит в результате упруго-пластической деформации слоёв, в процессе которой в поверхностных слоях свариваемых изделий выравниваются микронеровности, разрушаются оксидные плёнки, осуществляется взаимодействие атомов с образованием металлической связи. Сварка давлением может производиться без предварительного нагрева соединяемых изделий – механическая сварка и с предварительным нагревом до пластического состояния или до оплавления – термомеханическая.
Технологическое свойство материалов, характеризующее способность к образованию сварных соединений, называется свариваемостью.
При сварке плавлением источник тепла расплавляет металл на отдельном участке соединения. Образуется сварочная ванна, ограниченная поверхностью нерасплавленного металла. Источник теплоты (дуга, пламя, электронный луч, луч лазера) «давит» на металл в ванне, оттесняя его от центра к краям и образуя углубление – кратер. При перемещении источника тепла жидкий металл оттесняется к заднему краю ванны – в хвостовую часть. Там происходит кристаллизация и формируется шов. А дуга в это время «подмывает» переднюю, головную часть ванны, расплавляя всё новые и новые порции металла.
Изучая ванну и шов, сварщики установили очень важные закономерности. Зная, что глубина проплавления пропорциональна тепловой мощности дуги, можно рассчитать примерный режим сварки изделий определённой толщины. В такой же зависимости находится и объём сварочной ванны, изменяющийся при различных способах сварки от десятых долей до нескольких десятков см3.
К сварке плавлением относятся: дуговая, плазменно-дуговая, электронно-лучевая, электрошлаковая, лазерная, газовая, термитная.
К сварке давлением относятся: контактная, индукционная, диффузионная, термокомпрессионная (термомеханическая сварка); холодная, ультразвуковая, взрывом, трением (механическая сварка).
10.3.2. Виды сварных соединений
В реальных производственных условиях сварочная ванна может занимать различные положения в пространстве. Сварка может проводиться:
а






б) в потолочном положении






в















Очевидно, что лучше иметь дело с нижними швами, но не всякое изделие можно поворачивать в удобное для сварки положение.
В зависимости от взаимного расположения свариваемых элементов различают следующие виды соединений:
С







П



















собираются в виде букв «Т» или «Г». Швы при этом соединении называют угловыми.
П














В

Обычно выбор сварных соединений и вида шва зависит от конструкции изделия. А уже в зависимости от вида шва, толщины соединения, от свойств металла, наличия оборудования и др. условий устанавливаются приёмы и режимы сварки.