20 июля 2001 г. Оглавление
Вид материала | Документы |
Содержание2.2.8 Средняя себестоимость производства алюминия в России и сопоставление со среднемировой себестоимостью |
- Принят Государственной Думой 13 июля 2001 года Одобрен Советом Федерации 20 июля 2001, 191.08kb.
- Принят Государственной Думой 13 июля 2001 года Одобрен Советом Федерации 20 июля 2001, 359.09kb.
- Приказ Минздрава РФ от 30 июля 2001 г. N 291 "О мерах по предупреждению распространения, 434.44kb.
- Принят Государственной Думой 13 июля 2001 года Одобрен Советом Федерации 20 июля 2001, 668.35kb.
- Принят Государственной Думой 13 июля 2001 года Одобрен Советом Федерации 20 июля 2001, 238.54kb.
- Принят Государственной Думой 13 июля 2001 года Одобрен Советом Федерации 20 июля 2001, 1598.83kb.
- Принят Государственной Думой 13 июля 2001 года Одобрен Советом Федерации 20 июля 2001, 207.72kb.
- Принят Государственной Думой 13 июля 2001 года Одобрен Советом Федерации 20 июля 2001, 406.6kb.
- Принят Государственной Думой 13 июля 2001 года Одобрен Советом Федерации 20 июля 2001, 290.92kb.
- Принят Государственной Думой 13 июля 2001 года Одобрен Советом Федерации 20 июля 2001, 275.4kb.
2.2.8 Средняя себестоимость производства алюминия в России и сопоставление со среднемировой себестоимостью
В начале 90-х гг. российский алюминий был самым дешевым, и было выгодно производить его при сложившихся мировых ценах. В середине 90-х годов он, напротив, стал более дорогим, и даже возросшая цена перестала покрывать издержки. Этому способствовали как внешние, так и внутренние факторы: экспоненциальный рост цен на энергию и транспорт, рост экологических штрафов, переход крупнейших мировых производителей алюминия на более экономичную и экологически более безопасную технологию производства.
Это обуславливает низкую рентабельность заводов по производству проката в России, хотя на мировом рынке прибыль на тонну алюминиевого проката высоких стадий передела доходила до 1500 долл. США (против 200 долл. США за тонну первичного алюминия).
Особенно заметна разница в заработной плате. Если российский рабочий-электролизник получает в среднем 5 тыс. рублей в месяц, то его западный коллега - до 5 тыс. долларов США. В настоящее время в структуре затрат на производство 1 тонны алюминия на отечественных заводах затраты на заработную плату составляют всего 7%. При этом на электроэнергию приходится в среднем до 17—18%.
На себестоимость продукции в конечном счете влияет применяемая на предприятии экономическая схема. Так, оборотной стороной толлинга, например, стали значительные транспортные издержки, которые в ряде случаев составляли до 15-16% себестоимости производства алюминия. Тем самым транспортные расходы стали практически сопоставимы с затратами на электроэнергию. В свою очередь, рост энерготарифов закономерно вел к тому, что в определенный период времени энергозатраты стали буквально доминирующим элементом затрат в общей себестоимости конечной продукции. Ответным ходом на этот процесс стало лоббирование интересов алюминиевой отрасли на всех властных уровнях. Были также предприняты попытки переподчинить “под себя” энергетическую инфраструктуру страны.
Производство алюминия не только энергозатратно, но и сопряжено с загрязнением окружающей среды. В ходе строительства самих заводов отсутствовал опыт в проектировании и эксплуатации систем газоочистки. В результате на сегодняшний день выбросы алюминиевых заводов превышают все санитарно-гигиенические нормативы в десятки раз. Например, согласно исследованиям, проведенным Сибирским отделением Российской академии наук, в общем загрязнении атмосферы города Красноярска на долю КрАЗа приходится до 50% окиси углерода, около 30% пыли и 15% двуокиси серы. Наряду с этим в промышленных выбросах содержатся особо вредные бензо(а)пирен и фтористые соединения. Несовершенство газоочистки оборачивается для населения массовым ухудшением здоровья, а для самих предприятий — удорожанием конечной продукции за счет штрафных экологических санкций.
Между тем промышленные выбросы можно рассматривать как прямые потери ценных исходных сырьевых компонентов, которые буквально выбрасываются “в трубу”. Это касается как составляющих анодной массы, так и смеси “глинозем-криолит”. Предварительная экспертная оценка показала, что именно эти потери ведут к существенному удорожанию конечной продукции. Существует альтернативный подход к решению данной проблемы. Имеется недорогой отечественный проект, не имеющий мировых аналогов, внедрение которого гарантированно позволит почти на 50% сократить потери сырья в промышленных выбросах и тем самым значительно оздоровить окружающую среду.
Для сравнения приведем схему распределения расходов при выплавке тонны первичного алюминия на “Волгоградском алюминии” (5% от общероссийского производства) и в мире (данные на 1998 год):
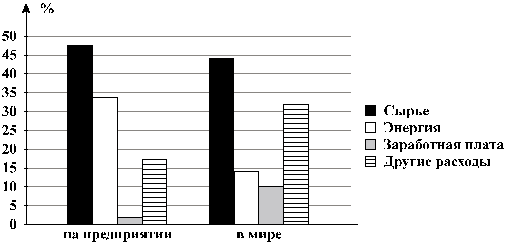
Рентабельность собственного капитала по чистой прибыли в среднем по отрасли в России составила в 1998 году – 2,3%, в 1999 году – 12,1%. Рентабельность продаж составила в 1998 году – 17,8%, в 1999 году – 19%.
2.2.9. Транспортные издержки поставок российского алюминия на мировые рынки, сравнение средней себестоимости российского алюминия (с учетом транспортных издержек) со среднемировой себестоимостью (с учетом транспортных издержек)
Транспортные издержки в ряде случаев составляют 15—16% от себестоимости производства алюминия. Тем самым транспортные расходы становятся практически сопоставимыми с затратами на электроэнергию.
Так, железнодорожные перевозки холдинга «Русский алюминий» составляют ежемесячно 34 - 35 млн. долларов, при объемах всех перевозок компании около 12 млн. тонн в год.
Кроме того, с 1 августа текущего года, в связи с переходом внутренних грузовых перевозок по российским железным дорогам на единый тариф, стоимость перевозки алюминия возрастет в два раза. Это связано с тем, что в отношении перевозки цветных металлов со стороны Министерства путей сообщения будет применяться повышенный тарифный коэффициент.
В структуру ценообразования, кроме затрат на вывоз готовой продукции, включаются также расходы на импорт необходимого для производства сырья. Анализ структуры себестоимости на Богословском, Волгоградском, Братском, Красноярском, Новокузнецком, Волховском, Уральском и Кандалакшском заводах показывает, что фактор дальности перевозки импортируемого глинозема поднимает долю себестоимости сырья и материалов до 67 %, тогда как за рубежом этот показатель составляет около 45 %, что почти в 1, 5 раза ниже.