Методическое пособие Новосибирск, 2009 удк 658. 562
Вид материала | Методическое пособие |
- Удк 658. 562. 012 + 660. 2 + 006, 52.12kb.
- Учебно-методическое пособие Йошкар-Ола, 2009 ббк п 6 удк 636, 3772.57kb.
- Учебно-методическое пособие Москва, 2009 ббк-63. 3 /2/я 73 удк-930. 24 Степнова, 154.54kb.
- Ю. В. Олейников Философско-методологические основы экологического знания, 76.92kb.
- Учебно-методическое пособие Ростов-на-Дону 2009 удк 66 Отечественная история: Учебно-методическое, 1490.23kb.
- Учебно-методическое пособие Ярославль, 2009 Скопин А. А., Разработка и технологии производства, 2904.37kb.
- Учебное пособие Донецк 2009 ббк с 562. 21я73, 1413.89kb.
- Учебно-методическое пособие Сургут Издательский центр Сургу 2009 удк 001. 8 (072), 497.58kb.
- Учебное пособие Волгоград 2007 удк 631. 16. 658. 155 Ббк 65. 321, 1185.97kb.
- Учебно-методическое пособие Ярославль, 2009 удк 615. 12: 659. 1 Ббк 65., 797.47kb.
qi = Хi/ Хiб или qi = Хiб / Хi,
где Хi - значение i -го показателя качества оцениваемой продукции, Хiб - значение базового показателя, i изменяется от 1 до n. qi > 1, если наблюдается улучшение показателей и qi < 1, если имеет место ухудшение показателей. При использовании дифференциального метода можно не вычислять значения относительных показателей. Достаточно фиксировать результат сопоставления по каждому показателю в качественной форме. Могут быть сформулированы следующие результаты оценивания:
- уровень качества оцениваемой продукции выше уровня базового образца, если все значения qi
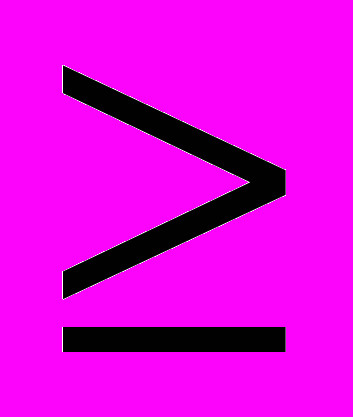
- уровень качества оцениваемой продукции равен уровню базового образца, если все значения q i = 1 (т.е. продукция по всем показателям соответствует базовому образцу),
- уровень качества оцениваемой продукции ниже уровня базового образца, если все значения qi
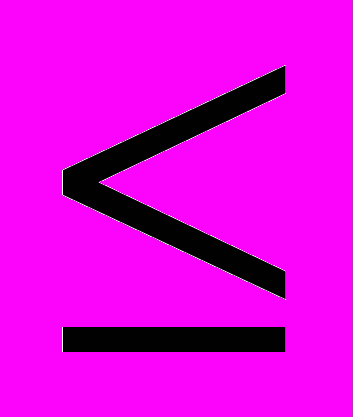
В случае, когда часть значений относительных показателей качества больше 1, а часть меньше, дифференциальный метод не дает результата.
Комплексный метод оценки уровня качества продукции предусматривает использование комплексного (обобщенного) показателя качества. Уровень качества определяется отношением обобщенного показателя качества оцениваемой продукции (Qоц) к обобщенному показателю базового образца (Qбаз): Q = Qоц / Qбаз
Обобщенный показатель может быть выражен главным показателем, интегральным или средневзвешенным. Главный показатель - это показатель, который может, по мнению экспертов, в основном охарактеризовать качество изделия. Интегральный показатель используется тогда, когда можно установить суммарный полезный эффект от эксплуатации или потребления продукции и суммарные затраты на создание и эксплуатацию продукции:
I = Э / (Зс + Зэ)
Средневзвешенные показатели применяют, если нельзя установить функциональную зависимость главного показателя от исходных показателей качества, но возможно с достаточной степенью точности определить параметры весомости усредненных показателей. Недостаток средневзвешенного показателя - субъективность коэффициентов весомости. Например, средневзвешенный показатель Q = Σmiqi,
где mi - коэффициент весомости i-го показателя.
Смешанный метод основан на одновременном использовании единичных и комплексных показателей качества продукции. Часть единичных показателей объединяют в группы и для каждой определяют соответствующий комплексный показатель, при этом отдельные важные показатели можно не объединять, а использовать, как единичные. Метод применяется тогда, когда совокупность единичных показателей является достаточно обширной.
4.2. Методы оценки уровня качества разнородной продукции
Используют индексы качества и дефектности.
Индекс качества (Ик) - это комплексный показатель качества разнородной продукции, который равен среднему взвешенному относительных значений показателей качества этой продукции. Определяется он по формуле: Ик = Σ bi Ki / Kiб,
где bi - коэффициент весомости i-го вида продукции, Ki - комплексный показатель качества i-го вида продукции, Кiб - базовый комплексный показатель качества i-го вида продукции. Коэффициент весомости определяется: bi = Сi / Σ Сi,
где Сi -стоимость продукции i-го вида.
Индекс дефектности (Ид) - это комплексный показатель, равный среднему взвешенному коэффициентов дефектности продукции: Ид = Σ BiQi,
где Qi - относительный коэффициент дефектности продукции i -го вида, являющийся показателем качества изготовления продукции. Коэффициент дефектности можно вычислить:
Q = Д / Дб,
где Д – дефектность оцениваемой продукции, Дб – дефектность базовой продукции [4, 9-10].
5. ПОКАЗАТЕЛИ НАДЁЖНОСТИ
Надежностью называют свойство объекта сохранять во времени и в установленных пределах значения всех параметров, характеризующих способность выполнять требуемые функции в заданных режимах и условиях применения, технического обслуживания, хранения и транспортирования. Особенностью проблемы надежности является ее связь со всеми стадиями жизненного цикла продукции, начиная с идеи создания и заканчивая принятием решения о списании [11]. Надежность объекта является комплексным свойством, формируемым такими составляющими, как: безотказность, долговечность, ремонтопригодность и сохраняемость.
5.1. Показатели для оценки безотказности
Безотказность – свойство объекта непрерывно сохранять работоспособность в течение заданного времени или наработки. Это свойство особенно важно для изделий, отказ в работе которых связан с опасностью для жизни людей, остановкой сложного производства или производства с непрерывным технологическим циклом. Безотказность характеризуется рядом показателей: вероятностью безотказной работы, средней наработкой до отказа (или средним временем безотказной работы), средней наработкой на отказ, средней наработкой между отказами, интенсивностью отказов, средней частотой отказов, вероятностью отказов.
Основным показателем является вероятность безотказной работы - вероятность того, что в пределах заданной наработки отказа объекта не произойдет. Она определяется по формуле: Р(t) = Ntp / No,
где Ntp - число объектов, исправных к моменту t, No - число объектов, исправных в начальный момент времени. Для вычисления вероятности безотказной работы используются данные, накапливаемые путем наблюдений за работой при эксплуатации или при испытаниях. Чем больше изделий подвергается наблюдениям, тем точнее определяется вероятность безотказной работы других однотипных изделий. Вероятность противоположного события называется вероятностью отказа. Она дополняет вероятность безотказной работы до единицы.
Q(t) = 1 - P(t).
Кривые Р(t) и Q(t) пересекаются в точке, соответствующей среднему сроку службы объекта, при котором Р(t) = Q(t) = 0,5. Для невосстанавливаемых и восстанавливаемых объектов понятие наработки различается: в первом случае подразумевается наработка до первого отказа (он же является и последним), во втором случае - между двумя соседними во времени отказами (после каждого отказа производится восстановление работоспособного состояния).
Средняя наработка на отказ – отношение суммарной наработки за рассматриваемый период времени восстанавливаемого изделия к суммарному числу отказов этих изделий за тот же промежуток времени: То = Ti /mi
Средняя наработка до отказа Т – некоторая часть расходуемого ресурса машины, в течение которого она не должна иметь сбоев в работе (т.е. отказов). Она указывает на невозможность работы машины длительно и непрерывно. Наработка до отказа предопределяет режим работы машины в виде периодических порций: активной работы и остановки для профилактики. Она определяется по формуле: Т =Σ ti / No,
где ti - время наработки i-го элемента до отказа, No – число объектов, поставленных на испытания.
Средняя наработка между отказами – это математическое ожидание наработки изделия от окончания восстановления его работоспособного состояния после отказа до возникновения следующего отказа: Тср = Ti / m
Для оценки безотказности невосстанавливаемых объектов используется показатель интенсивность отказов. Интенсивность отказов λ – условная плотность вероятности отказа невосстанавливаемого объекта, определяемая для рассматриваемого момента времени при условии, что до этого времени отказ не возник. Показатель равен отношению среднего числа объектов, отказавших в единицу наработки Nотк к числу объектов, оставшихся работоспособными Nраб: λ = Nотк / N раб
Если время испытаний разбить на отрезки
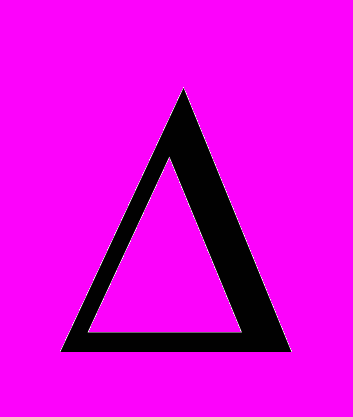
где ti – момент времени, соответствующий концу i -го интервала.
Типичная форма интенсивности отказов «корытообразная» (рис. 3).

Рисунок 3. Типичная форма интенсивности отказов.
Первый период – период приработки (ранние отказы, зачастую вызываемые производственными дефектами), второй период – период нормальной эксплуатации, третий период – период появления износовых отказов. В период старения или износа происходят необратимые физико-химические изменения, когда интенсивность отказов монотонно возрастает и надежность соответственно снижается. Для изделий с такой интенсивностью отказов можно оптимизировать надежность на период эксплуатации путем начальной приработки до момента времени t1 с целью исключения ранних отказы и замены изделий в момент времени t2 c целью избежания износовых отказов. Интенсивность отказов в общем случае подчиняется закону распределения Вейбула. Обычно в расчетах надежности первый участок кривой не учитывают, расчеты производят, начиная со второго участка.
Сравнительно реже в практике используют гамма-процентную наработку до отказа – наработку, в течение которой отказ объекта не возникает с вероятностью γ, выраженной в процентах.
5.2. Показатели для оценки долговечности
Долговечность – свойство объекта длительно сохранять работоспособность до наступления предельного состояния, то есть в течение всего периода эксплуатации при установленной системе технического обслуживания и ремонтов. Для невосстанавливаемых объектов понятия безотказности и долговечности практически совпадают. Показатели представлены на рис. 4.
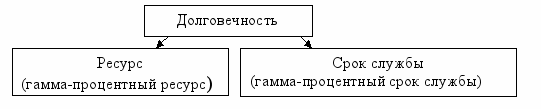
Рисунок 4. Показатели долговечности.
Ресурс – наработка объекта от начала эксплуатации или возобновления эксплуатации после ремонта до предельного состояния. Наработка - это продолжительность или объем работы, поэтому ресурс исчисляется в единицах времени работы (часах), километрах пути, количестве циклов нагрузки до разрушения и другое. Ресурс изделия определяется по формуле: R = N /
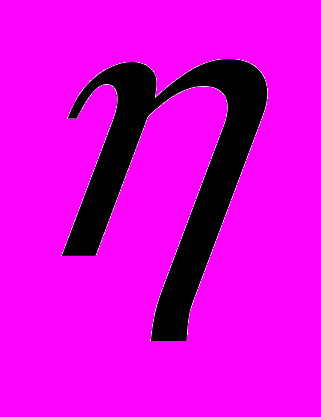
где N – сопротивление усталости объекта или его агрегатов,
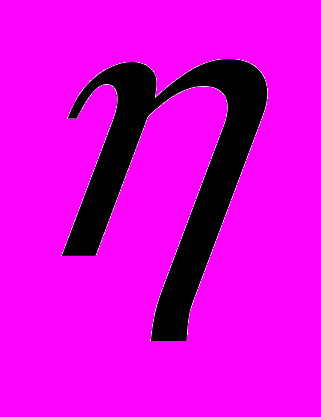
Срок службы – календарная наработка изделия до наступления предельного состояния. Обычно выражается в годах. По аналогии используют средний, назначенный и установленный срок службы. Часто используют понятие «календарный срок эксплуатации изделия по календарному сроку службы основной части, агрегата, системы».
5.3. Показатели для оценки ремонтопригодности
Трудоемкость восстановления зависит от конструкции машины, ее технологичности, удобства монтажа и демонтажа, контролеспособности узлов и агрегатов, поставок запасных частей и другого. Обыкновенно вырабатывается схема технического обслуживания. Сроки проведения работ определены из статистики ремонтов ранее эксплуатируемых машин. Используют следующие показатели. Время восстановления - продолжительность восстановления работоспособного состояния объекта. Среднее время восстановления работоспособности – математическое ожидание времени восстановления работоспособного состояния.
Вероятность восстановления работоспособности в заданные сроки - вероятность того, что время восстановления не превысит заданного: Рв = Nb /N0,
где Nb – количество объектов, восстанавливаемых за время, меньше заданного, Nо - общее количество объектов.
Средняя трудоемкость восстановления: ∑Твi/n,
где Твi – трудоемкость восстановления i-го объекта после отказа, n – количество объектов.
5.4. Показатели для оценки сохраняемости.
Они характеризуют свойство технического изделия сохранять исправное и работоспособное состояние при хранении и (или) транспортировании. Сроком сохраняемости называется календарная продолжительность хранения и транспортирования изделия в заданных условиях, в течение и после которой значения показателей качества остаются в установленных пределах. Используют понятия среднего срока сохраняемости, полученного при анализе сроков сохраняемости группы изделий и назначенного срока хранения – календарной продолжительности хранения в заданных условиях, по истечении которой применение изделия по назначению не допускается независимо от технического состояния. Установленный срок хранения – технико-экономически обоснованный срок хранения, в пределах которого показатели безотказности, долговечности и ремонтопригодности остаются теми же, какими они были до начала хранения или транспортирования.
6. ПОКАЗАТЕЛИ НАзначения
Группа показателей назначения характеризует степень соответствия изделия его целевому назначению, а также свойства, определяющие основные функции, для выполнения которых изделие предназначено. Показатели назначения предопределяют и область применения данного изделия. При определении показателей назначения выбирают только наиболее существенные, характеризующие важнейшие свойства продукции. Группа показателей назначения состоит из следующих подгрупп: классификационные, функциональные и технической эффективности, конструктивные, состава и структуры продукции.
6.1. Классификационные показатели
характеризуют принадлежность данной продукции к определенной классификационной группе, так как любая совокупность однородной продукции имеет свою классификацию. Классификация однородной продукции позволяет установить классификационную группу, в пределах которой возможно сопоставление оцениваемой продукции с другими аналогами, сформулировать общие требования к качеству продукции отдельной группы, обосновать и принять к осуществлению единые для данной группы продукции методы экспертизы качества, служит основанием для определения групповой номенклатуры показателей качества. На практике используют 2 основных вида классификации: фасетный и иерархический. Фасетный метод представляет параллельное разделение множества объектов на независимые классификационные группы – фасеты. Например, по качеству химического состава стали классифицируются на 4 группы. Главными признаками качества стали являются показатели содержания в ней вредных примесных элементов, таких как сера и фосфор (табл. 13).
Содержание примесей в сталях. Таблица 13
Стали | P | S |
-обыкновенного качества, -качественные, -высококачественные, -особовысококачественные | 0,040 0,035 0,025 0,025 | 0,050 0,035 0,025 0,015 |
Иерархический метод - это последовательное разделение множества объектов на соподчиненные классификационные группы. Каждая последующая ступень классификации конкретизирует признак вышестоящей ступени. Такая классификация обычно многоступенчата и сложна. Например, классификация машин по техническим признакам.
1. Машины орудия или станки (токарные, фрезерные, сверлильные, швейные и другие);
2. Машины двигатели, необходимые для выработки и передачи другим машинам двигательной (механической) энергии;
3. Транспортирующие машины – автомобиль, самолет, лифт, мостовой кран, насос и другие;
4. Машины – генераторы по своему назначению противоположны двигателям. Эти машины вырабатывают необходимый вид энергии путем преобразования механической энергии двигателя (генераторы электрической энергии, компрессоры, холодильные машины и т.д.).
Исходными для классификации являются такие параметрические признаки, как мощность двигателя, грузоподъемность крана, скорость автомобиля и т.д. Универсального и всеобщего классификатора машин не существует.
6.2. Показатели функциональные и технической эффективности
характеризуют полезный эффект от эксплуатации и потребления продукции, а также прогрессивность технических решений, реализованных в данной продукции. Функциональные показатели изделий – это те, которые являются выходными и характеризуют техническую эффективность выполнения функций изделий по назначению. К ним относятся:
производительность (количество произведенной продукции в единицу времени), рабочая вместимость, установленная мощность, подача станка, рабочий режим или производительность, напор, давление, скорость и другое.
6.3. Конструктивные показатели технических изделий
характеризуют основные проектно-конструкторские решения, удобство монтажа и установки, возможность агрегатирования и взаимозаменяемости продукции. К конструктивным показателям относятся: коэффициент сборки, который характеризует простоту и удобство монтажа, уровень механизации или автоматизации, наличие дополнительных устройств (например, домкрата, ключей для машины), масса изделия, габаритные размеры, занимаемая площадь и другое. Конструктивные показатели технических изделий рассчитывают преимущественно на этапе их разработки, но учитывают и на всех последующих этапах жизненного цикла образцов техники.
6.4. Показатели состава и структуры продукции
Эти показатели технических изделий входят в подгруппу конструктивных показателей, а вот показатели состава и структуры различных материалов, а также их связь с потребительскими свойствами рассматриваются самостоятельно. Показателями состава материала являются: процентное содержание компонентов, процентное содержание серы и золы в коксе, концентрация различных примесей в кислотах, щелочах и другое. От состава материала зависят, например, прочностные характеристики изделий, их характеристики долговечности. Это вызывает необходимость знать количественные характеристики показателей состава и структуры.
7. Социально ориентированные показатели качества технических изделий.
К этим показателям можно отнести те, которые непосредственно связаны с человеком, работающим с техникой. В их числе показатели эргономичности, экологичности, безопасности и эстетичности.
7.1. Эргономические показатели качества
Эргономические требования к технике – совокупность показателей, определяемых свойствами и возможностями человека выполнять функции управления, обслуживания и использования техники с требуемым качеством и без ущерба для его здоровья. Эргономические показатели характеризуют машину в системе «человек – машина» и учитывают ее приспособленность к антропометрическим, биомеханическим, физиологическим и инженерно-психологическим свойствам человека, проявляющимся в производственных процессах. Эргономический уровень изделия – обобщающая относительная характеристика совокупности всех эргономических свойств оцениваемого изделия, основанная на сопоставлении значений эргономических показателей его качества со значениями соответствующих показателей базового образца.
Группу эргономических показателей технических изделий разделяют на 4 подгруппы:
а) гигиенические и биомеханические - показатели, используемые при определении соответствия изделия гигиеническим условиям работы человека с изделием. В эту подгруппу входят количественные характеристики освещённости, температуры, влажности, напряженности магнитного и электрических полей, запыленности, излучения, токсичности, шума, вибрации, перегрузок от ускорения и другого;
б) антропометрические - показатели, используемые при определении соответствия изделия размерам, форме и весу человека, работающего с изделием;
в) физиологические и психофизиологические – показатели соответствия изделия физиологическим свойствам человека и особенностям функционирования его органов чувств (силовые
и скоростные возможности человека, пороги слуха, зрения, тактильные ощущения и т.п.);
г) психологические - показатели соответствия изделия психологическим особенностям людей соответствующей профессии, отраженным в инженерно – психологических требованиях. В эту подгруппу входят показатели соответствия изделия возможностям восприятия и переработки информации, закрепленным и вновь формируемым навыкам работы человека с изделием.
Перечень и метод выбора эргономических показателей регламентированы нормативной документацией. За базовые значения принимают эргономические требования, приводимые в специальных ГОСТах, РД, НТД, справочниках и др. Оценка эргономических показателей производится также экспертным методом специалистами в области эргономики применительно к конкретной области промышленности.
7.2. Экологические показатели
Экология – это наука, изучающая условия существования живых существ и взаимоотношения их со средой обитания. Актуальной проблемой стало опасное для людей воздействие на природу в процессе их жизнедеятельности. Материальными носителями опасных и вредных факторов для природы и человека становятся различные объекты, используемые в трудовых процессах – это средства труда (машины, оборудование и другое), предметы и продукты труда, технологии, работающие изделия машиностроительного производства. Экологические показатели характеризуют уровень вредного воздействия на окружающую среду в процессе эксплуатации технического изделия. Производится анализ работы изделия с целью выявления возможных вредных химических, радиационных и других воздействий на окружающую природную среду. Различают несколько подгрупп экологических показателей, связанных с влиянием используемой техники на атмосферу, водные ресурсы (гидросферу), на землю, на живые организмы и т.д. С другой стороны, экологические показатели техники можно разделить на 3 основные группы:
1. Показатели, связанные с использованием материальных ресурсов природы.
Это ресурсоемкость изготовления техники, показатели потребления невосполнимых материальных ресурсов при эксплуатации, ремонтах и утилизации техники;
2. Показатели, связанные с использованием природных энергетических ресурсов;
3. Показатели, связанные с загрязнением окружающей среды.
При определении экологических показателей качества новой техники находят относительные значения фактических значений, например, концентрации вредных веществ или уровней вредных механических, физических и других воздействий на природную среду к их предельно допустимым значениям. Должно соблюдаться условие: Σ