Лекция Общая характеристика отделочной обработки. Виды отделочной обработки: полирование, доводка, хонингование, суперфиниширование
Вид материала | Лекция |
- Лекция Общая характеристика абразивной обработки. Абразивные материалы. Основные способы, 158.28kb.
- Организация эис по обработке банковской информации общая характеристика технологии, 8.72kb.
- Общая характеристика обработки резанием. Сущность процесса резания. Виды стружек. Силы, 129.66kb.
- Лекция 10. Основные способы обработки металлов давлением, их характеристика. Прокатка, 117.37kb.
- Общая характеристика процессов сбора, передачи, обработки и хранения информации. Методы, 362.07kb.
- Примерный перечень вопросов к экзамену по дисциплине «Технологии автоматизированной, 18.17kb.
- Лекция Виды обработки точением. Основные типы токарных резцов. Элементы и геометрические, 109.95kb.
- Технологическое обеспечение финишной ультразвуковой обработки вязких высокопрочных, 823.11kb.
- Д. В. Левый исследование влияния условий обработки на протекание, 57.53kb.
- Государственный образовательный стандарт среднего профессионального образования государственные, 711.52kb.
Лекция 7. Общая характеристика отделочной обработки. Виды отделочной обработки: полирование, доводка, хонингование, суперфиниширование.
1.Общая характеристика отделочной обработки.
Увеличение нагрузок на детали машин, увеличение скоростей, повышение надежности машин вызывает необходимость дополнительной отделочной обработки для повышения точности, уменьшения шероховатости.
Отделочная обработка делается также для улучшения внешнего вида, что важно для эстетических целей. Для отделочных методов обработки характерны малые силы резания, небольшие толщины срезаемых слоев материала, незначительное тепловыделение в процессе обработки. Обработку производят с приложением относительно малых по величине сил закрепления заготовок, поэтому заготовки деформируются незначительно.
Отделочными видами обработки являются:
- тонкое обтачивание, тонкое растачивание, тонкое шлифование
- полирование
- притирка или доводка
- абразивно-жидкостная обработка
- хонингование
- суперфиниширование
2. Тонкое обтачивание, тонкое растачивание, тонкое шлифование
Тонкое обтачивание применяют как метод отделки, заменяющий шлифование. Процесс происходит при высоких скоростях резания, малых глубинах и подачах. Применяются токарные резцы с широкими режущими кромками, которые расположены строго параллельно оси обрабатываемой заготовки. Подача на оборот заготовки составляет не более 0,8 ширины режущей кромки В, а глубина резания не более 0,5 мм. Шероховатость обрабатываемой поверхности уменьшается.
Для обточки цветных металлов и сплавов, неметаллических материалов (пластмасс) применяют алмазные резцы. Метод обработки обеспечивает высокую точность. Тонкое обтачивание требует применения быстроходных станков высокой жесткости и точности, а также качественной предварительной обработки заготовок.
Тонкое растачивание применяется как метод, заменяющий шлифование, особенно для тонкостенных деталей из вязких сплавов и сталей. Целесообразно при обработке глухих отверстий и в тех случаях, когда абразивные зерна не должна оставаться в порах обработанной поверхности. Расточные резцы изготовляются из твердых сплавов или алмазов.
Тонкое шлифование производится мягкими мелкозернистыми кругами при скорости резания V>40м/с, малой скорости вращения обрабатываемой детали (до 10м/м), малой глубине резания (до 5 мкм). Применяется обильное охлаждение и «выхаживание». Подача на глубину резания выключается, а продольная подача осуществляется по-прежнему. Процесс обработки продолжается благодаря упругим силам, которые возникли в станке и заготовке (подобно сжатой пружине), в то время как они были деформированы силой резания. В таком режиме станок продолжает работать некоторое время, силы резания постепенно снижаются, а точность обработки существенно повышается.
3. Полирование
Полирование – это абразивная обработка материалов с помощью притирочных паст или абразивных порошков, смешанных со смазкой.
Полирование уменьшает шероховатость поверхности, получают зеркальный блеск. Применяют для ответственных частей деталей машин (дорожки качения подшипников) или для декоративных целей (полировка облицовочных частей автомобиля). Погрешности формы и местные дефекты от предыдущей обработки этим методом не исправляются. Полирование поверхностей приводит к повышению усталостной прочности и антикоррозионной стойкости. Часто полирование предшествует поверхностной обработке – хромированию, азотированию и другим методам.
Полирующие материалы наносят на быстровращающиеся эластичные круги, абразивные ленты (рис.1).
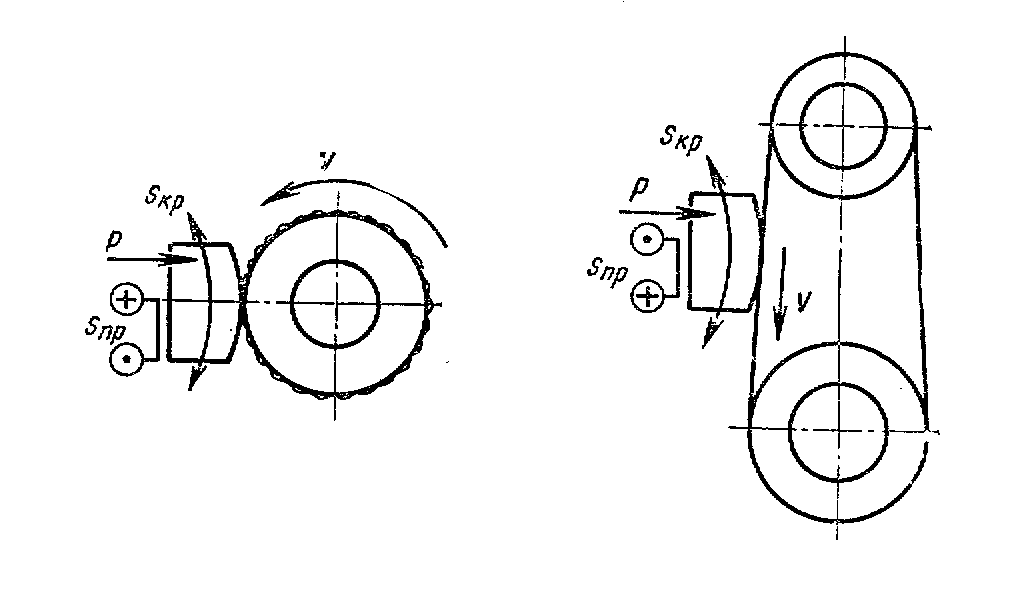
Рис.1 Полирование поверхностей
Полировальные круги изготовляют из войлока, кожи, фетра, капрона, спрессованной ткани и других материалов. В качестве абразивного материала при полировании заготовок из стали применяют порошки из электрокорунда и окиси железа, при полировании заготовок из чугуна – из карбида кремния и окиси железа, при полировании заготовок из алюминия и медных сплавов – из окиси хрома и наждака. Порошок смешивают со смазкой, которая состоит из смеси воска, сала, парафина и керосина. Зернистость абразива колеблется от 80 до 3 и выбирается в зависимости от припуска на обработку.
Заготовка вручную прижимается к кругу или ленте силой Р, совершает продольную подачу Sпр и круговую Sкр. Скорость резания V=40-50 м/с.
Применение ленты более благоприятно – рабочая поверхность ленты значительно превышает рабочую поверхность круга, благодаря чему происходит большое рассеяние теплоты.
Полировка производится вручную (при полировании фасонных поверхностей) и на полировальных станках.
4. Абразивно-жидкостная отделка
Для отделки криволинейных и фасонных поверхностей, где применение обычных методов вызывает затруднения, применяют антикоррозионные жидкости, в которых имеются частицы абразивного порошка.
Абразивная суспензия перемещается под давлением с большой скоростью, и частицы абразива, ударяясь о поверхность заготовки, сглаживают микронеровности, создавая эффект полирования (рис.2). Интенсивность съема материала обрабатываемой заготовки регулируется зернистостью порошка, давлением струи и углом
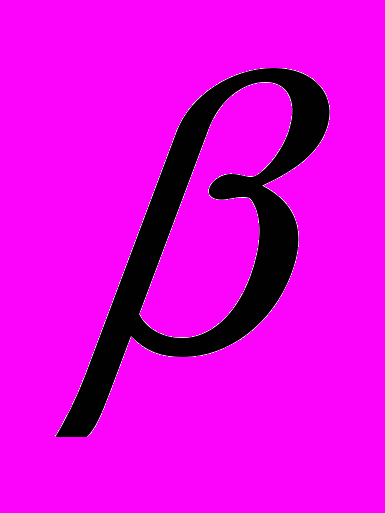
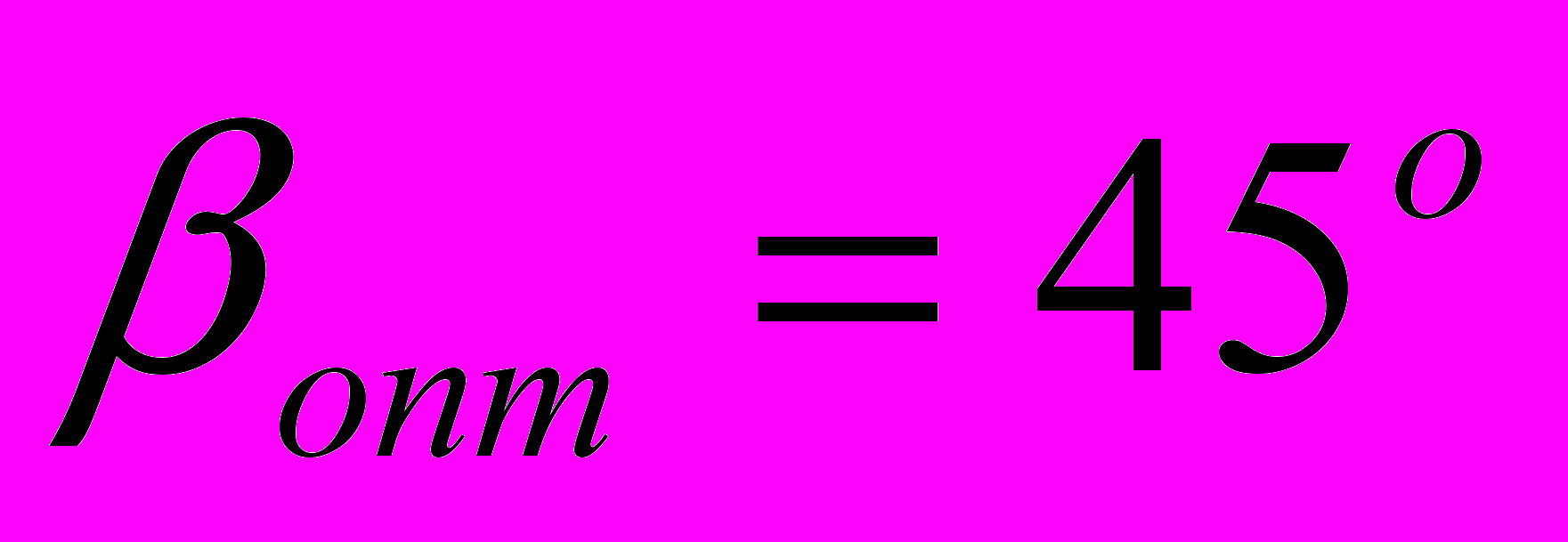
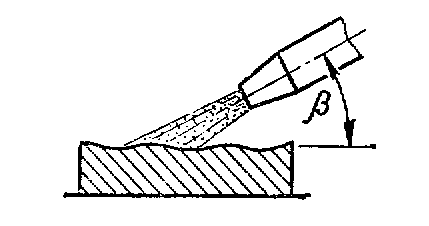
Рис.2. Абразивно-жидкостная обработка
В качестве абразива часто применяют электрокорунд. Содержание абразива в суспензии составляет 30-35% по массе.
Жидкостная отделка особенно эффективна при обработке внутренних фасонных поверхностей. Этот вид обработки не повышает точность размеров и формы, а только уменьшает шероховатость поверхности.
5. Притирка или доводка поверхностей
Отклонения поверхностей, обработанных на металлорежущих станках – волнистость, неплоскостность, нецилиндричность и другие – могут быть устранены доводкой. Доводка обеспечивает получение очень точных размеров (5-6 квалитет) и малой шероховатости поверхности, которая достигает RZ 0,1 – RZ 0,025.
Доводка производится как цилиндрических (конических), так и плоских поверхностей. Припуск для доводки круглых поверхностей 0,005-0,02 мм, плоских 0,0075-0,0125 мм.
Доводка выполняется с помощью притиров, на поверхность которых наносится притирочная паста или мелкий абразивный порошок со связующей жидкостью. Притиры изготовляются из чугуна, мягкой стали, меди, латуни. Материал притира должен быть мягче обрабатываемой детали. Сравнительный износ притиров: чугун – 1, сталь – 1,25, медь – 2,6.
Выбор рода абразива зависит от материала обрабатываемой детали. Доводка мягких и закаленных сталей наиболее успешно производится электрокорундом нормальным и белым. Для доводки чугуна, бронзы, твердых пластмасс применяется карбид кремния. Эффективность процесса доводки значительно повышают рабочие жидкости – олеиновая и стеариновая кислоты. Они проникают в микротрещины на поверхности металла и облегчают снятие неровностей. Одновременно они являются связующим материалом. Могут применяться пасты ГОИ (Государственного оптического института).Они содержат в качестве абразива окись хрома (76%) и в качестве связки - олеиновую и стеариновую кислоты (22%) и 2% керосина.
Схемы притирки цилиндрических поверхностей приведены на рис.3.
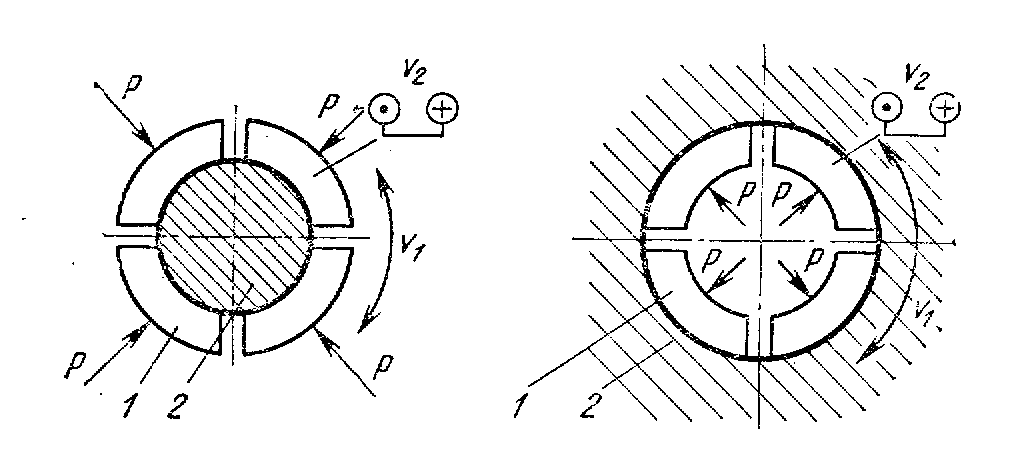
а) б)
Рис.3. Доводка наружных (а) и внутренних (б) поверхностей
Притир 1 представляет собой втулку, имеющую ряд прорезей, которые необходимы для того, чтобы обеспечить под действием силы Р полное его прилегание к обрабатываемой поверхности. Притиру сообщают одновременно возвратно-вращательной движение V1 и возвратно-поступательное движение V2. Возможно вместо движения V1 равномерное вращательное движение заготовки 2 с наложением движения V2. При обработке наружных поверхностей притир сжимается, а при обработке отверстий – разжимается под действием силы Р. Эти схемы обработки осуществляются как вручную, так и на металлорежущих станках, например, токарных.
Схема притирки плоских поверхностей приведена на рис.4.
Чугунные диски 3 играют роль притиров и имеют плоские торцовые поверхности. Вращение дисков производится в противоположных направлениях и с разной частотой. Заготовки 4 располагаются в окнах сепаратора 5. Сепаратор располагается с эксцентриситетом е, поэтому при вращении дисков притираемые детали совершают сложные движения со скольжением, и снятие металла происходит одновременно с их параллельных торцов.
Производительность доводки зависит от давления притира на обрабатываемую поверхность (р=0,2-2,5 кГ/см2). Съем металла увеличивается с увеличением скорости дисков, однако он ограничивается ввиду сильного нагрева дисков, нарушения их плоскостности и ухудшения точности. Разность оборотов дисков создает проскальзывание деталей.
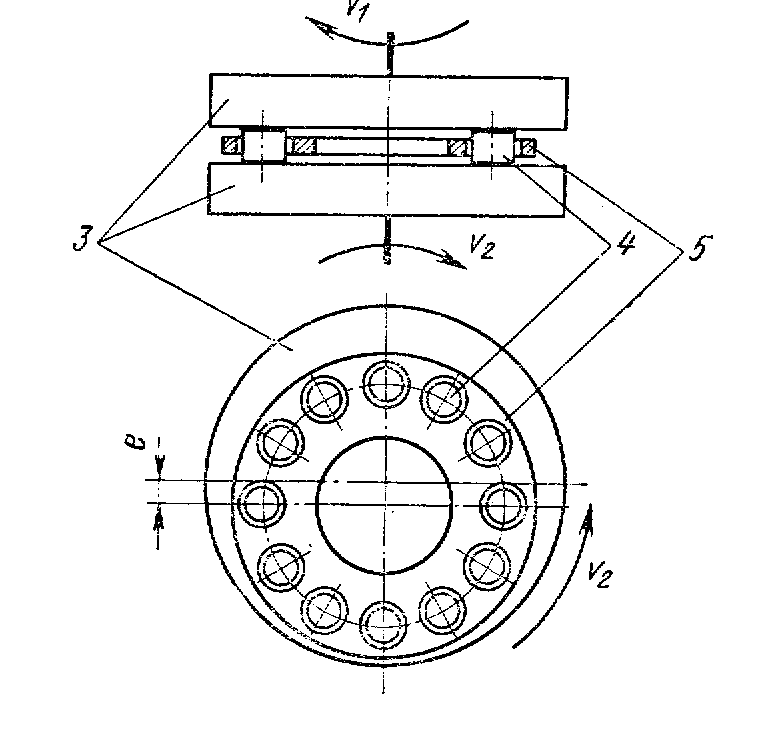
Рис.4. Доводка плоских поверхностей.
6. Хонингование
Применяется для окончательной обработки цилиндрических отверстий. Сущность процесса заключается в том, что специальный инструмент - хонинговальная головка (хон), оснащенный абразивными брусками, совершает одновременно вращательное и поступательное движения в неподвижной детали (рис.5), исправляя неточность и неровность поверхности.
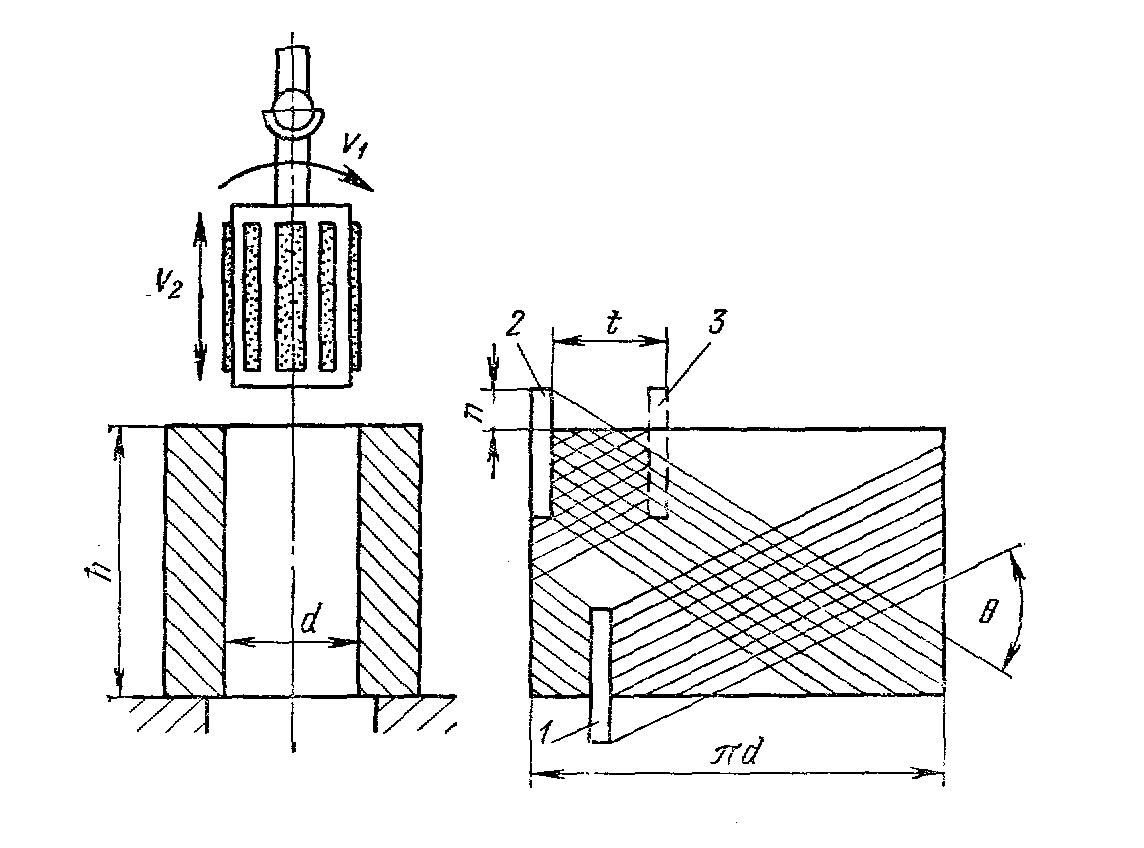
Рис.5. Схема хонингования
Применяя хонингование можно получить точность отверстий IT7-IT6 и шероховатость до Rа0,04, уменьшить овальность и конусность до 5 мкм.
На обрабатываемой поверхности появляется специфический микропрофиль – сетка мелких винтовых царапин, улучшающих удержание смазки (например, двигатели внутреннего сгорания).
Величина снимаемого слоя 0,01-0,2 мм, Ø5-1300 мм, длины до 20000мм. Исправляются такие погрешности снимаемого слоя как овальность, конусообразность, нецилиндричность. Погрешности же расположения оси отверстия (например, увод ее или криволинейность) этим методом не исправляют.
Применяется предварительное хонингование для исправления погрешностей предыдущей обработки и чистовое )окончательное) хонингование для уменьшения шероховатостей.
Хонинговальные бруски изготавливают из электрокорунда или карбида кремния, как правило, на керамической и бакелитовой связке, зернистость 3-8 или М20, М28. Применяется также и алмазное хонингование, главное преимущество которого состоит в эффективном исправлении погрешностей геометрической формы обрабатываемых отверстий, а также уменьшении износа брусков в 150-200 раз по сравнению с износом обычных абразивных брусков.
Количество брусков в головке выбирают из условия, что их суммарная ширина должна составлять 0,2 -0,5 длины окружности отверстия. Рекомендуется четное число брусков в головке (8,6,4,2) с диаметральным расположением их по окружности. Крепление брусков производится клеями. Используется целлулоидный клей -25-30% целлулоида и 70-75% ацетона. Подача на глубину резания осуществляется за счет радиального раздвижения брусков механическим, гидравлическим или пневматическим устройством.
Процесс хонингования сопровождается охлаждением зоны резания. Используются керосин, смесь керосина и веретенного масла, водно-мыльные эмульсии. Скорость подачи жидкости 50-60 л/м для своевременного удаления пыли и стружки.
Скорость резания
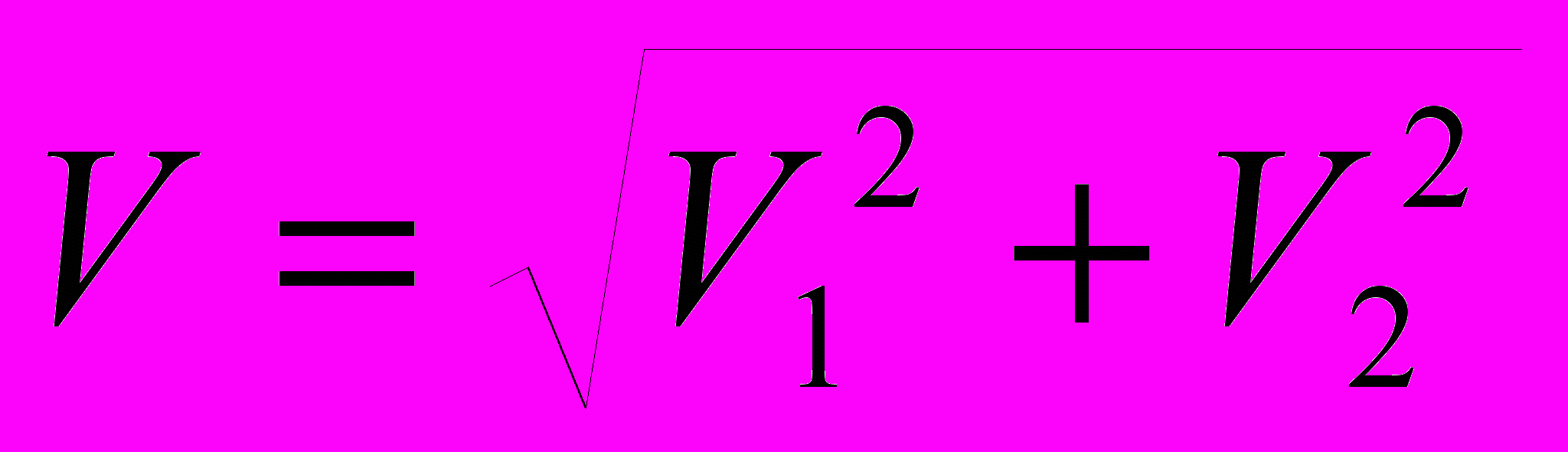
где: V1 – скорость вращения головки; V2 –скорость осевого перемещения головки. (Соотношение скоростей V1 и V2 составляет 1-10).
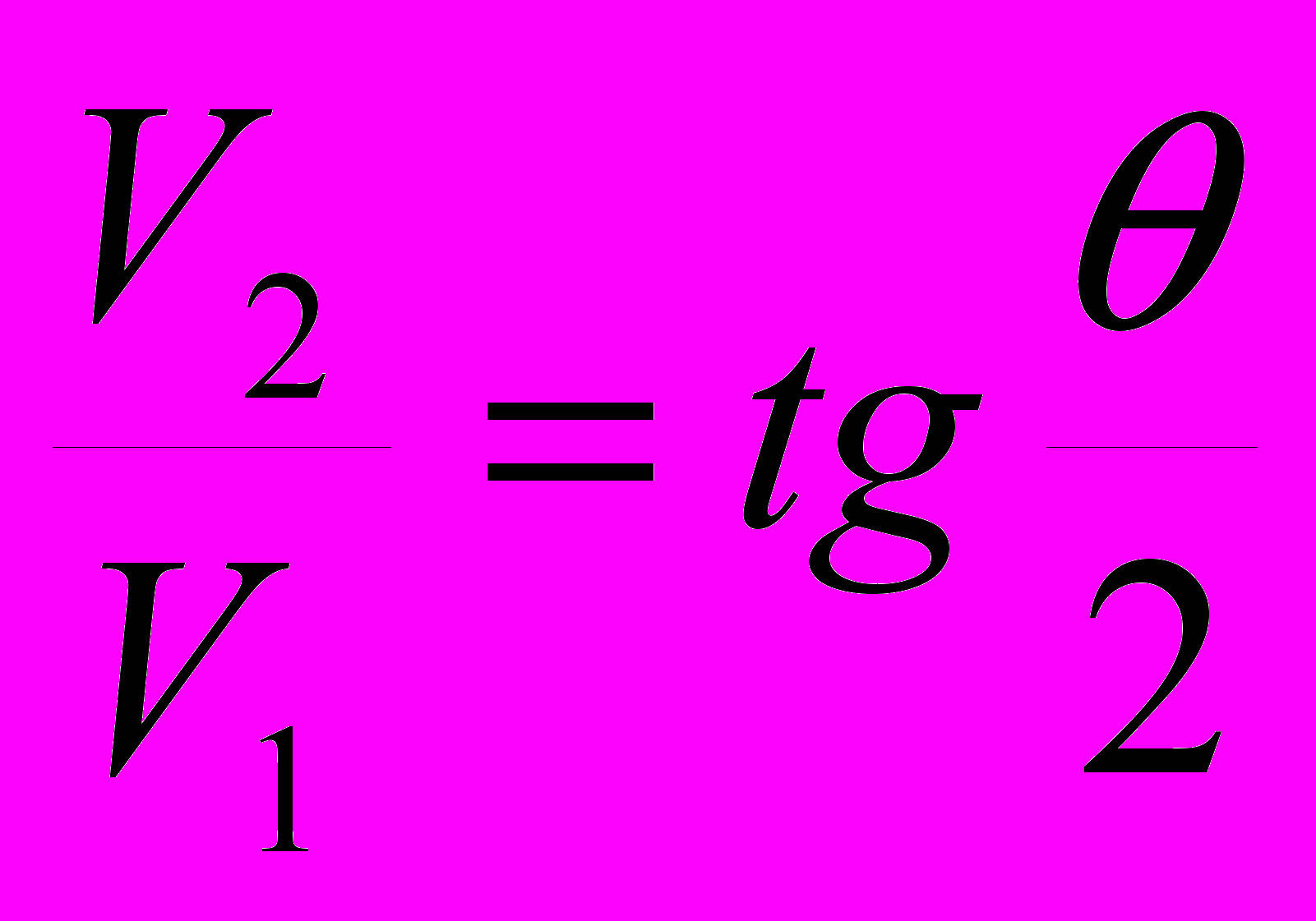
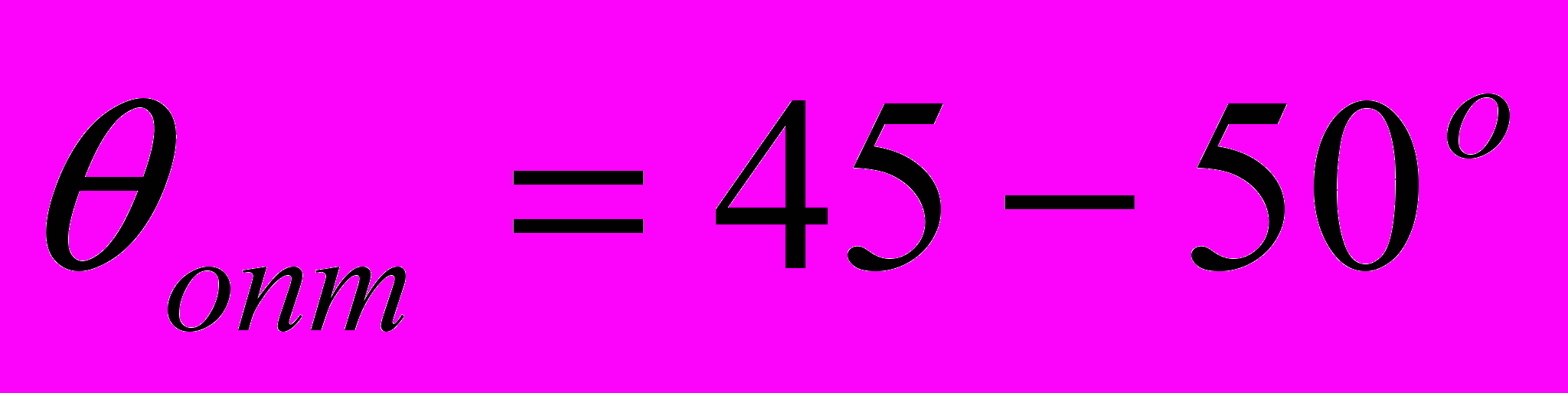
При большом угле сетки
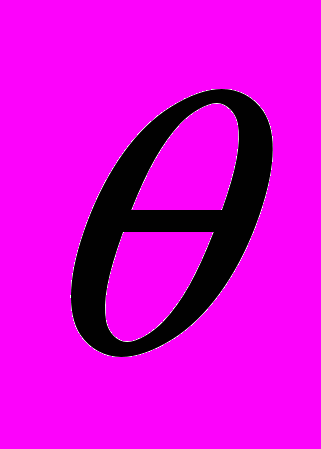
Для заготовок из стали закаленной
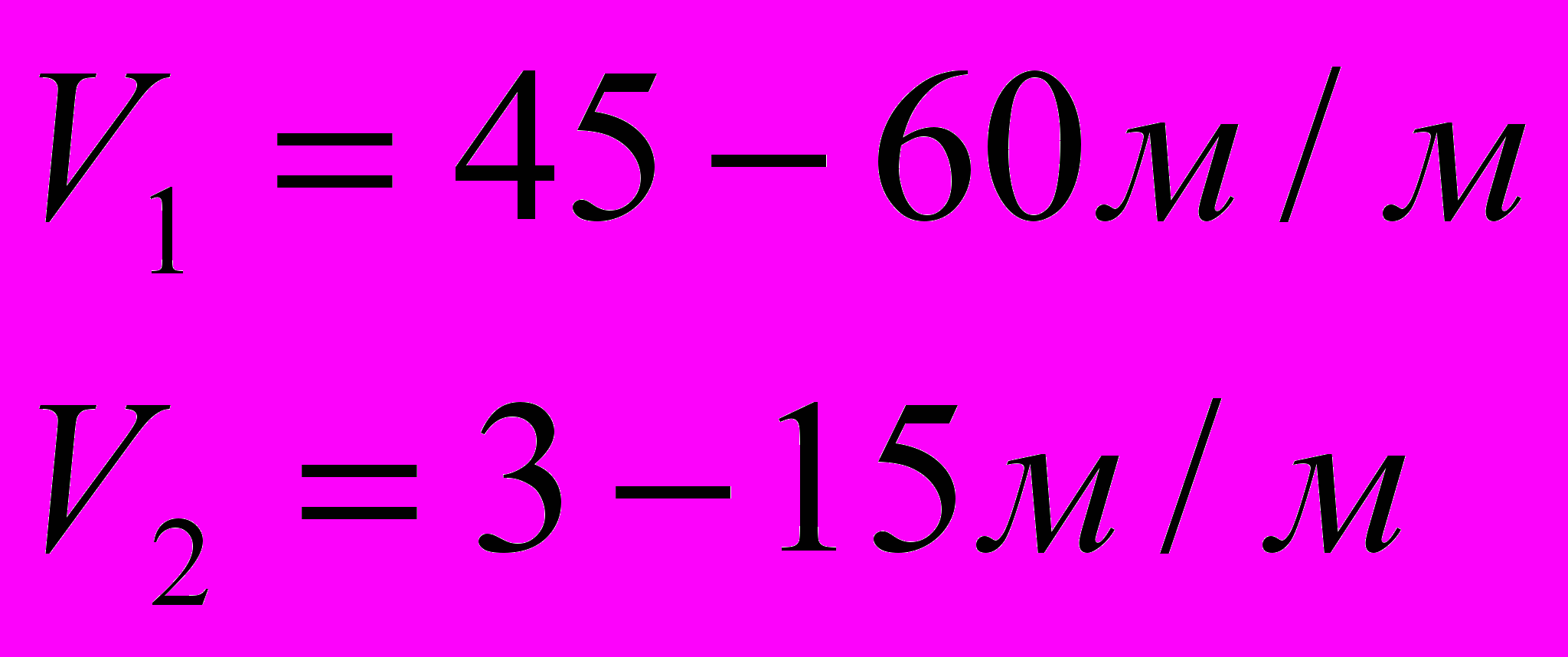
Для заготовок из чугуна, бронзы, сырых сталей
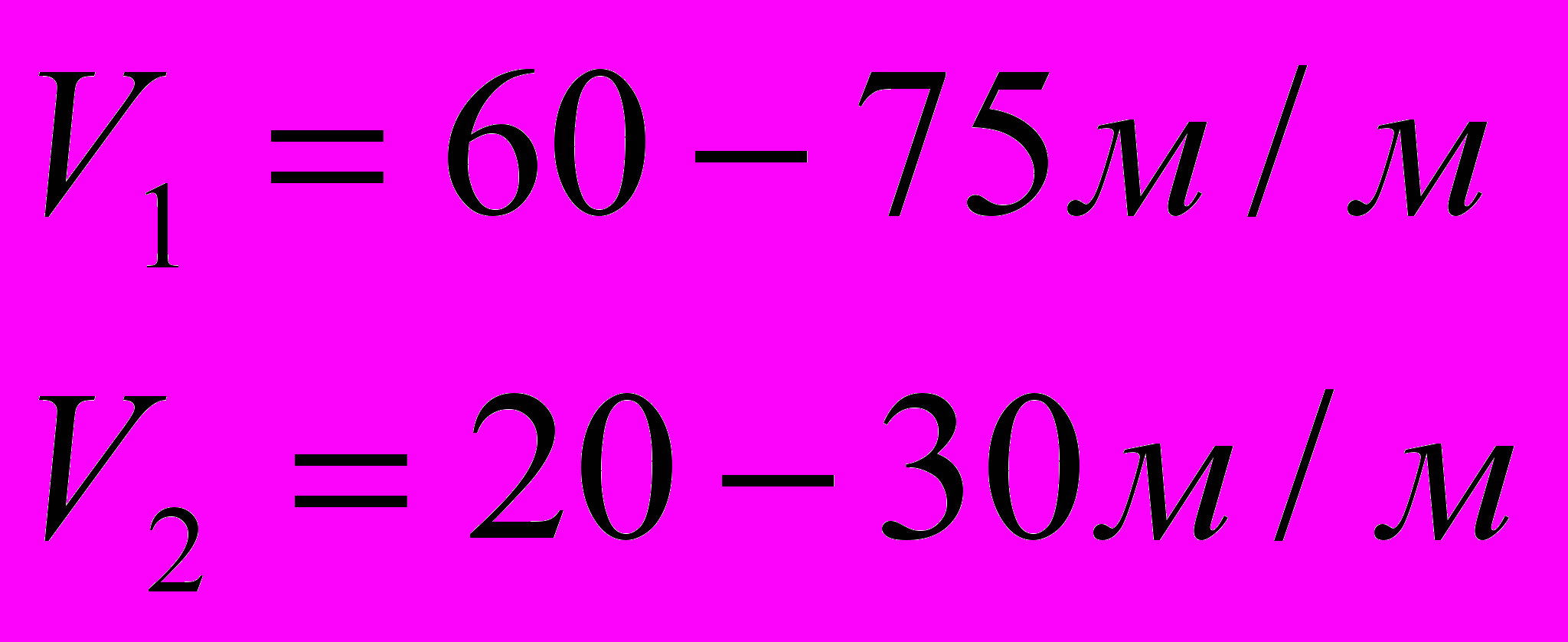
При обработке цветных сплавов

Среднее удельное давление брусков 3-6 кГ/см2. При засаливании брусков нужно уменьшать V1 и увеличивать V2. Чем выше прочность обрабатываемого материала, тем легче достигается высокая чистота поверхности.
7. Суперфиниширование
Суперфиниширование проводится с целью уменьшения высоты микронеровностей, полученных после предыдущей обработки. При этом меняется и вид микровыступов. Обработанная поверхность имеет сетчатый рельеф, а каждый микровыступ скругляется. Методом суперфиниширования обрабатывают плоские, цилиндрические (наружные и внутренние), конические и сферические поверхности из закаленной стали, а также чугуна и бронзы.
Обработка производится мелкозернистыми абразивными брусками, установленными в специальных головках (рис.6). Процесс осуществляется при сочетании вращательного движения детали, поступательного вдоль оси продольного передвижения брусков и колебательного (осциллирующего) движения брусков со скоростью V. Главное рабочее движение – колебательное перемещение брусков.
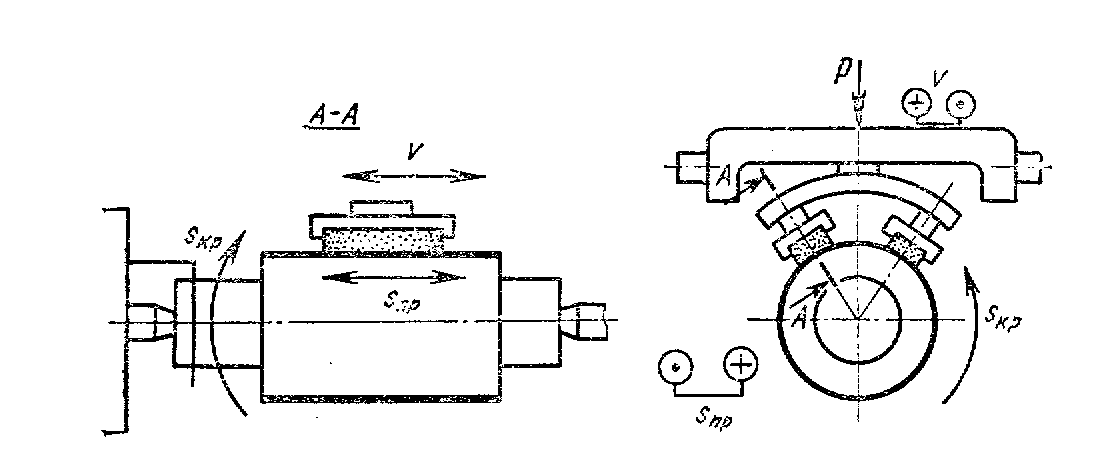
Рис.6. Схема суперфиниширования
Скорость резания весьма низкая – от 1 до 2,5 м/м. Амплитуда колебаний брусков составляет 1,5 – 6 мм, а частота колебаний 400-1200кол/м. Припуск на диаметр 0,002 – 0,02 мм. Давление брусков 1-4 кГ/см2, продолжительность процесса 1-2 мин.
Для обработки стали применяют бруски из электрокорунда белого, твердость С1-СТ1. Для обработки хрупких материалов – чугуна, бронзы применяются бруски из карбида кремния зеленого, твердость СМ1-С. В большинстве случаев применяются бруски на керамической и бакелитовой связках, зернистость 3-8 и менее. Применяются также и алмазные бруски, стойкость которых больше в 80-100 раз.
Важную роль при обработке играет СОЖ. В качестве смазывающих жидкостей при суперфинишировании применяется керосин с добавкой 10-20% веретенного масла и 3% олеиновой кислоты. В начале процесса, когда на поверхности имеются острые гребешки, масляная пленка под давлением абразивных брусков прорывается, и гребешки срезаются. Когда же они сглаживаются, смазка образует беспрерывную пленку, давление бруска недостаточно, чтобы ее прорвать, и резание автоматически прекращается.
Суперфинишированием значительно уменьшается величина шероховатости поверхности, но практически не устраняются погрешности формы, полученные в процессе предыдущей обработки.
Точность размеров и шероховатость поверхностей деталей,
соответствующие различным видам обработки
Вид обработки | Квалитет | Ra, мкм |
Доводка | 5…8 | 0,1…0,4 |
Доводка тонкая | 5 | 0,05 |
Долбление | 14,15 | 25…50 |
Долбление чистовое | 12,13 | 3,2…12,5 |
Литье: в песчаные формы в кокиль | 14…17 14…16 | 100 25 |
Обтачивание: обдирочное получистовое чистовое тонкое, алмазное скоростное | 15…17 12…15 7…13 6 11 | 25…100 6,3…12,5 1,6…3,2 0,4…0,8 1,6 |
Обработка зубчатых колес: строгание фрезерование шлифование шевингование | 7…10 7…10 5,6 5,6 | 3,2…6,3 3,2 0,4…0,8 0,8…1,6 |
Притирка | 6…8 | 0,4…3,2 |
Притирка тонкая | 5 | 0,1…1,6 |
Протягивание | 7…9 | 0,8…6,3 |
Протягивание отделочное | 7 | 0,2…0,4 |
Развертывание | 7…10 | 1,6…12,5 |
Развертывание тонкое | 6,7 | 0,8 |
Растачивание: черновое получистовое чистовое тонкое, алмазное | 15…17 12…14 6…9 6…9 | 50…100 12,5…25 1,6…3,2 0,4…0,8 |
Резьбонарезание: плашкой, метчиком резцом, гребенкой фрезой | 6…8 6…8 8 | 3,2…12,5 3,2…6,3 3,2…6,3 |
Сверление | 12…14 | 6,3…25 |
Сверление по кондуктору | 10,11 | 6,3…25 |
Строгание | 10…14 | 3,2…25 |
Строгание тонкое | 7…10 | 1,6 |
Фрезерование: черновое чистовое тонкое скоростное | 11…14 10,11 7,8,9 11…14 | 6,3…50 3,2…6,3 1,6 0,8…3,2 |
Хонингование | 6…8 | 0,2…0,4 |
Суперфиниширование | 4,5 | 0,1…0,4 |
Шлифование: получистовое чистовое тонкое | 8…11 6…8 4…7 | 3,2…6,3 0,8…1,6 0,2…0,4 |