Д. В. Левый исследование влияния условий обработки на протекание
Вид материала | Исследование |
- Исследование влияния условий процесса лазерной поверхностной обработки нагруженных, 56kb.
- I. Исследование влияния тренировочных нагрузок на изменение уровня физической работоспособности, 95.1kb.
- Алехин Алексей Николаевич исследование, 247.92kb.
- Исследование влияния геометрических параметров оборудования на форму и размеры трещины, 74.33kb.
- Левачков Василий Васильевич исследование, 142.51kb.
- Курсовая работа по дисциплине: маркетинговые исследования На тему «Исследование влияния, 87.43kb.
- Батышев Константин Александрович исследование, 709.6kb.
- Исследование свойств сельскохозяйственных сред и материалов, продуктов растениеводства, 60.18kb.
- Рабочей учебной программы дисциплины б в. 09. «Гигиена физического воспитания», 13.17kb.
- Cx-x электроразрядная обработка порошков твердых сплавов с целью изменения структуры, 33.2kb.
ISBN 5-89838-172-4 Вестник Брянского государственного технического университета. 2006. № 2 (10)
УДК 621.9.015
Д.В. Левый
ИССЛЕДОВАНИЕ ВЛИЯНИЯ УСЛОВИЙ ОБРАБОТКИ НА ПРОТЕКАНИЕ
ПРОЦЕССА РЕЗАНИЯ И ШЕРОХОВАТОСТЬ ДЕТАЛЕЙ
ИЗ ГРАФИТОВЫХ МАТЕРИАЛОВ
Рассмотрены особенности разрушения материала и формирования шероховатости в процессе обработки хрупких (графитовых) материалов. Установлена взаимосвязь условий обработки с параметрами качества поверхности.
Одной из наиболее актуальных задач машиностроительного производства является задача повышения качества машиностроительной продукции. Низкое качество и невысокие эксплуатационные показатели отдельных деталей из графитовых материалов приводят к экономически неоправданным высоким затратам в сфере использования продукции и как следствие снижению ее конкурентоспособности. В машиностроении используется очень много деталей, изготовляемых из графитовых материалов. По назначению - эти материалы можно разделить на 4 группы: 1) конструкционный материал; 2) антифрикционный материал; 3) электротехнический материал; 4) абляционного покрытия (абляция – унос массы с поверхности твердого тела потоками горячего газа в результате оплавления, испарения, разложения и химической эрозии материала).
Детали из материалов первых трех групп благодаря свойствам графита хорошо обрабатываются методами механической обработки (абразивной и лезвийной). Графитовые материалы могут обрабатываться шлифованием мелкозернистыми абразивами, причем получаемые точность и шероховатость могут быть такие же, как и у металлов. Однако по возможности рекомендуется избегать применения абразивов, так как при их использовании всегда имеется опасность внедрения в графитовую поверхность мелких частиц абразивов, что ухудшает эксплуатационные свойства детали. Так, после обработки пар трения частицы абразива могут вызвать появление на контактных поверхностях местных очагов износа, рисок и царапин, что приводит к повышенному износу. Кроме того, графит быстро заполняет поры абразивного круга, происходит засаливание, поэтому необходимо устройство правки круга в процессе обработки. Учитывая все сказанное, целесообразно применять лезвийную обработку графитовых деталей.
Процесс резания графита по сравнению с резанием пластичных материалов имеет ряд особенностей, обусловленных его свойствами. Это приводит к цикличности процесса стружкообразования, который сопровождается образованием микростружки (пылевидной) и макростружки (надлома) (рис.1). При перемещении лезвия инструмента из положения I, в котором сформировалась макростружка 1, на срезаемый слой зоны 2 заготовки будут действовать нормальные и касательные нагрузки (рис. 1б), величина которых будет увеличиваться до σв графита, что неизбежно приведет к контактному разрушению графита в условиях сжатия с образованием мелкой (пылевидной) микростружки. Данный процесс будет продолжаться до тех пор, пока площадь контакта по передней поверхности лезвия не увеличится до некоторой критической величины, при которой вновь произойдет скол и образование макростружки (положение лезвия инструмента II, рис.1а).
Благодаря специфичным свойствам графита (невысокая твердость и отсутствие площадки текучести) процессы, протекающие в ходе обработки, будут существенно отличаться от известных закономерностей, полученных для других материалов. С целью изучения процесса лезвийной обработки графита были проведены экспериментальные исследования графита марки МГ1.
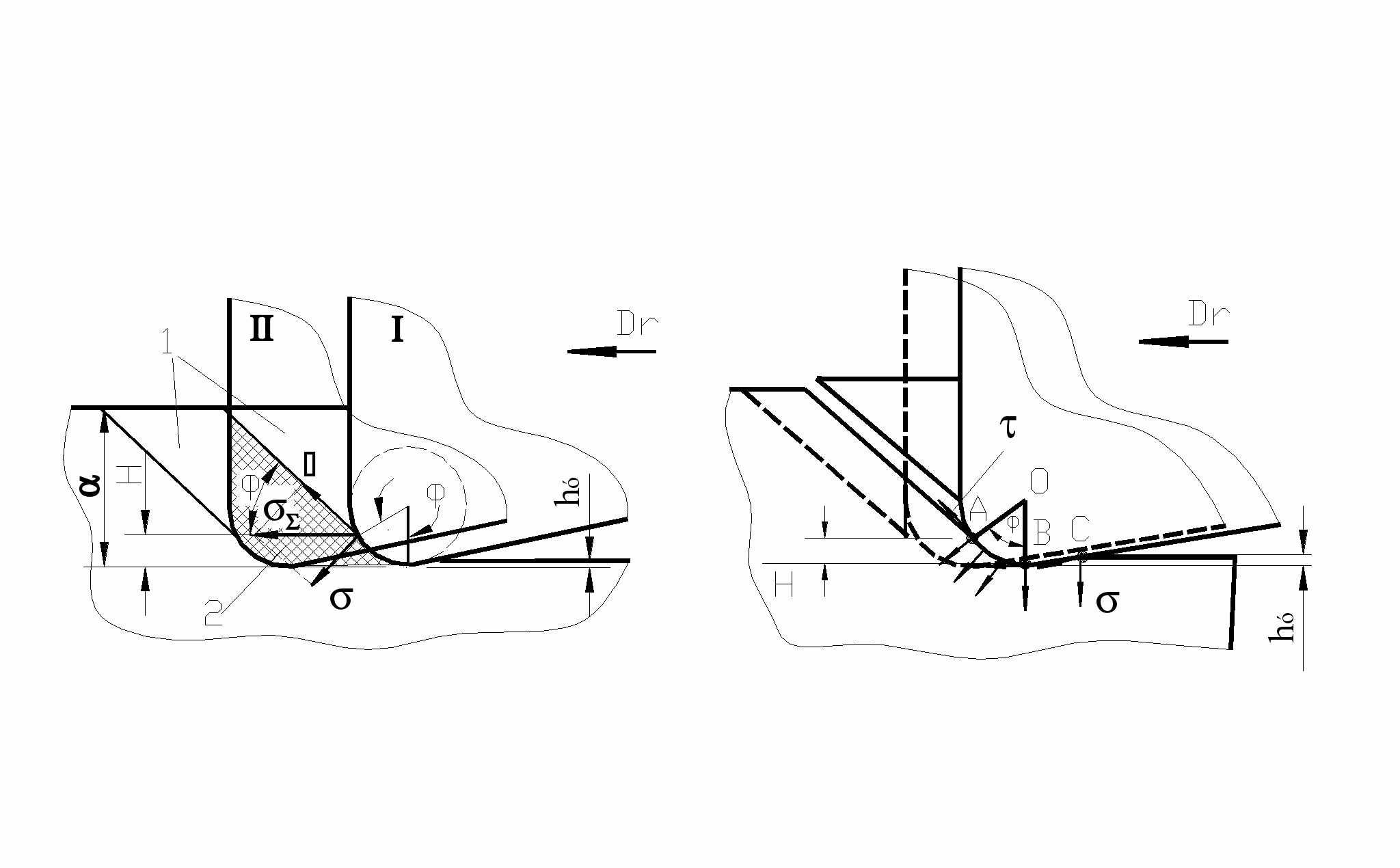
Рис. 1. Схема зоны стружкообразования: а - последовательность циклов стружкообразования; б - условия формирования микростружки; 1 - макростружка; 2 - превращение материала в микростружку; I, II – положения лезвия инструмента при формировании макростружки.
На первом этапе были проведены исследования для нахождения оптимального радиуса округления режущей кромки. При токарной обработке определялось изменение радиуса округления ρ, температуры в зоне обработки Θ, износа по задней поверхности hз и высотного параметра шероховатости Rz в зависимости от пути обработки. Результаты измерений перечисленных параметров в ходе обработки представлены на рис. 2.
,
С
h3, мм
, мм
Rz, мкм
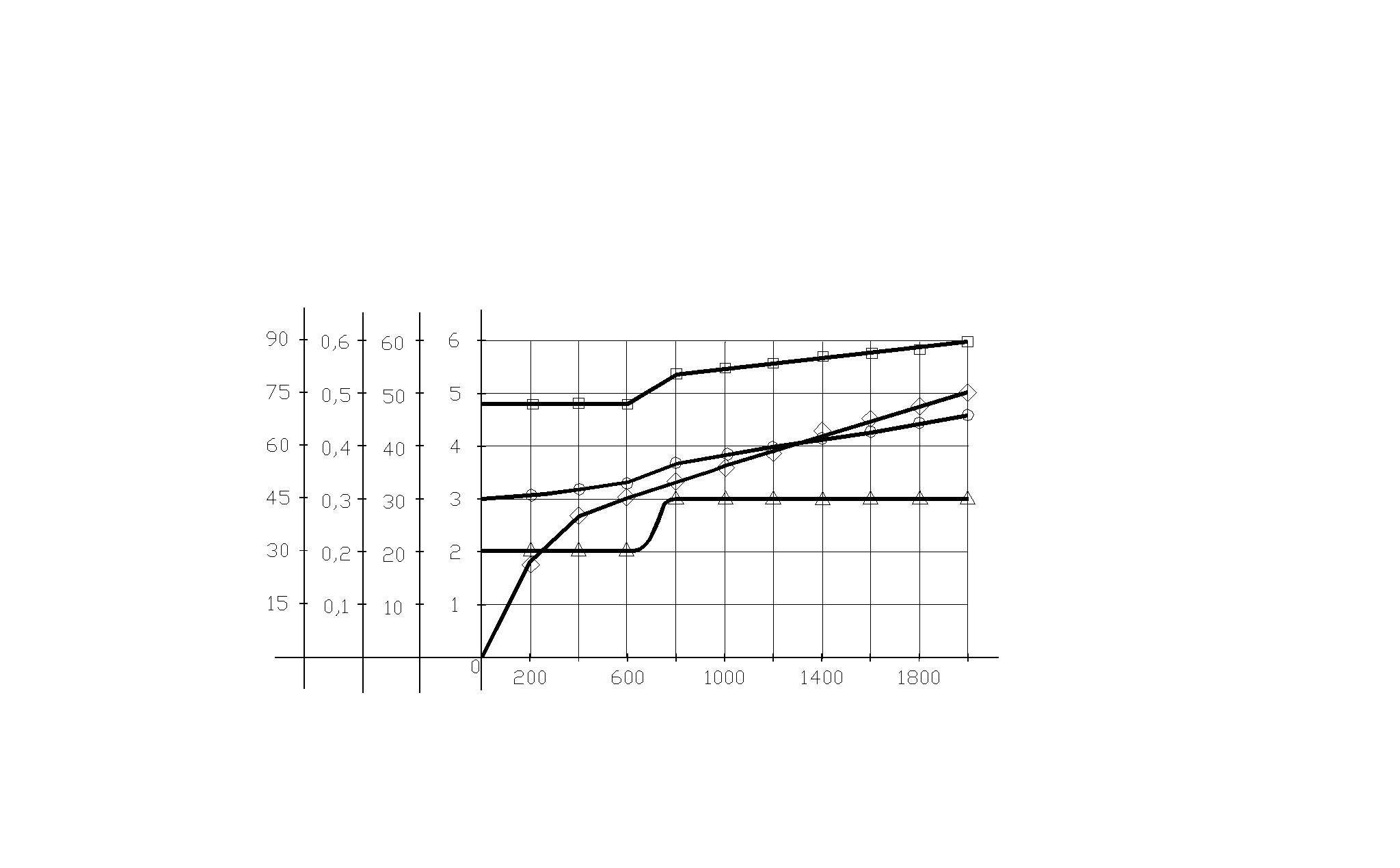
L, мм
Р

По приведенным графикам можно сделать вывод, что для обеспечения более низких значений параметра шероховатости необходимо затачивать резец острее. Для твердосплавного инструмента оптимальным будет радиус округления, равный 20 мкм.
На следующем этапе были проведены экспериментальные исследования для нахождения взаимосвязи между высотным параметром шероховатости Rz и условиями лезвийной обработки при сверлении, зенкеровании, развертывании, торцевом фрезеровании и точении. А также экспериментальные исследования для нахождения взаимосвязи между температурой и условиями лезвийной обработки при точении. Обработка точением была выбрана из-за универсальности и простоты (один режущий клин), в связи с чем результаты, полученные в процессе точения, могут быть использованы для других лезвийных методов обработки.
Анализ методов измерения температуры резания показывает, что наиболее точным является метод измерения с помощью естественной термопары. Однако данный метод конструктивно решается очень сложно, так как в большинстве случаев необходимо обеспечить снятие сигнала с вращающейся заготовки (точение) или инструмента (сверление, фрезерование). Основными условиями при разработке конструкций подвижного контакта является обеспечение его постоянного электрического сопротивления.
Анализ схем подвижных контактов позволил разработать конструкцию токосъемного узла с использованием радиального шарикоподшипника, внутренняя часть которого заполняется пластической смазкой с графитом, что обеспечивает электрическое сопротивление между внутренним и наружным кольцами в пределах 0,1 Ом.
Общий вид термопары и схема токосъемного узла представлены на рис. 3.
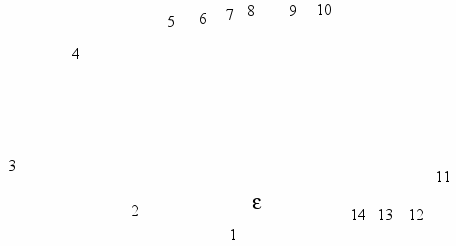
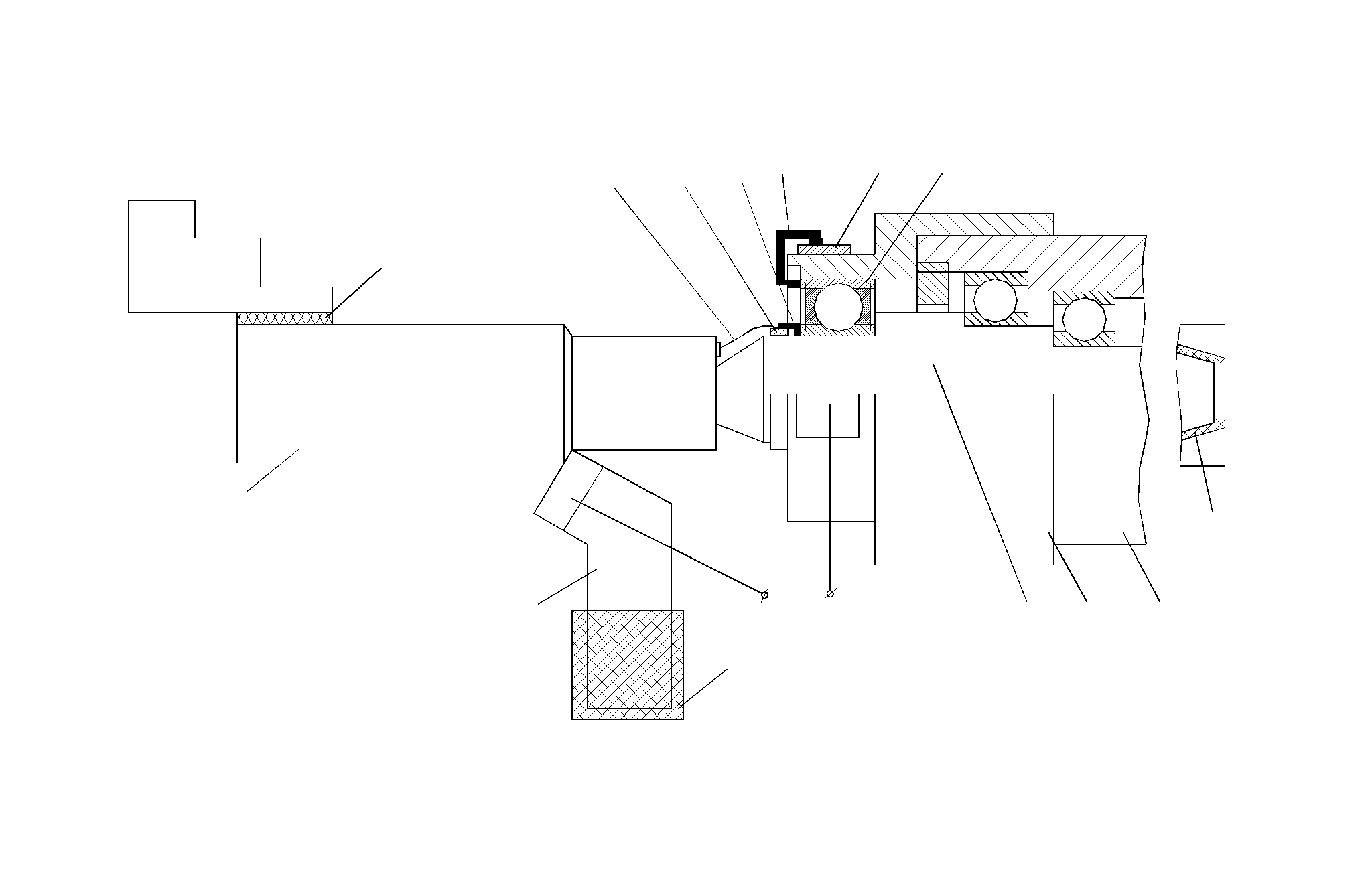
а)
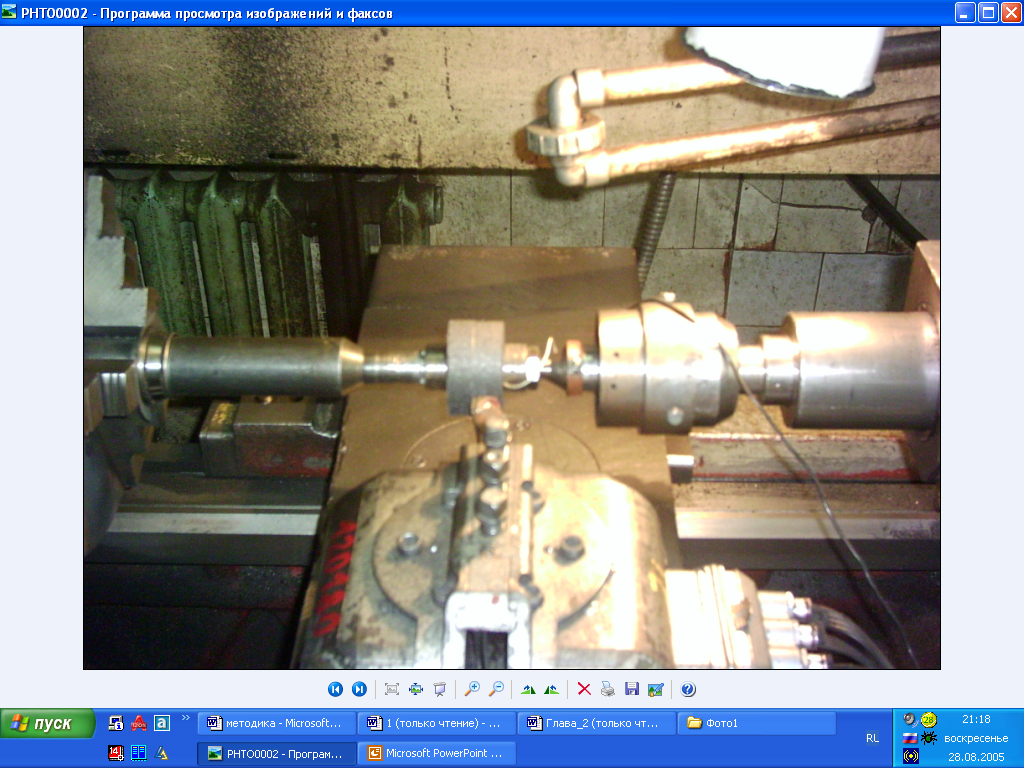
б)
Рис. 3. Естественная термопара: а - схема термопары и токосъемного узла; б - внешний вид термопары на токарном станке.
Для изготовления токосъемного узла был модернизирован стандартный вращающийся задний центр мод. А-1-3-НП, ГОСТ 8742-75, для чего были изготовлены удлиненный центр 14 и корпус 13, устанавливаемый на корпус вращающегося центра 12. Шарикоподшипник 10 установлен на центр 14, на который посадкой с натягом установлено кольцо 6, соединенное проводником 7 с внутренним кольцом подшипника 10, наружное кольцо которого проводником 8 соединено с пластиной 9, закрепленной на корпусе 13.
При установке на станок заготовка проводником 5 соединяется с кольцом 6. Заготовка 3, резец 2 и вращающийся центр 12 изолируются от станка с помощью диэлектрических втулок 4, 11 и прокладок 1, вращающийся центр заземляется.
При точении между инструментом 2 и заготовкой 3 возникает термо-ЭДС, которую измеряют между инструментом 2 и пластиной 9.
Естественная термопара «ВК8- Графит МГ1» протарирована, получены зависимости = f(ε); = 40 + 62,5ε, где - температура резания, С; ε – термо-ЭДС, мВ.
После проведения экспериментов и математического анализа были получены следующие зависимости:
- при сверлении (станок -2Н135,глубина резания t= 4,1 - 4,9 мм, скорость резания V = 31 - 43 м/мин, подача S0 = 0,14 - 0,28 мм/об )
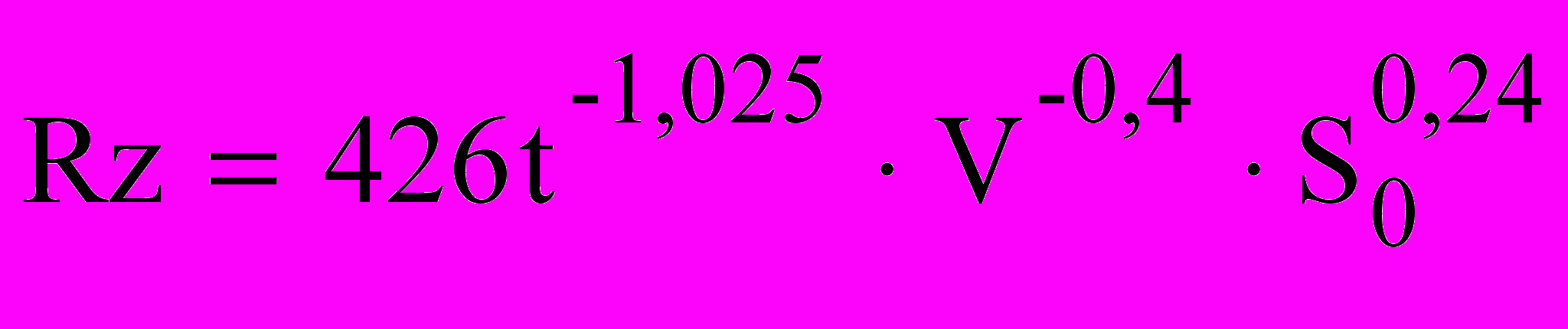
(1)
;
- при зенкеровании(станок 2Н135, глубина резания t = 1,05 - 1,84 мм, скорость резания V =24,5 - 35 м/мин, подача Sz = 0,19 - 0,27 мм/зуб)
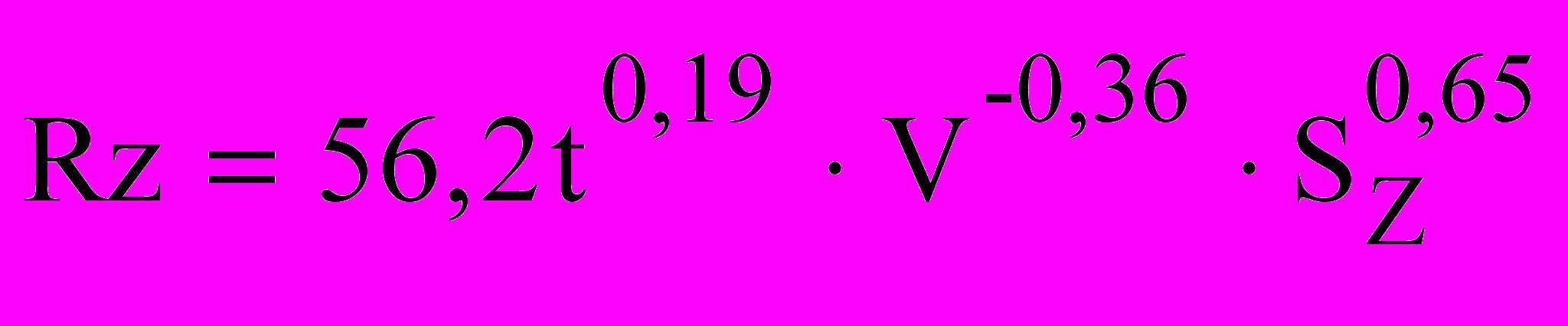
(2)
;
- при развертывании (станок -2Н135,глубина резания t= 0,06 - 0,53 мм, скорость резания V = 9,2 - 13,2 м/мин, подача Sz = 0,14 - 0,28 мм/зуб)
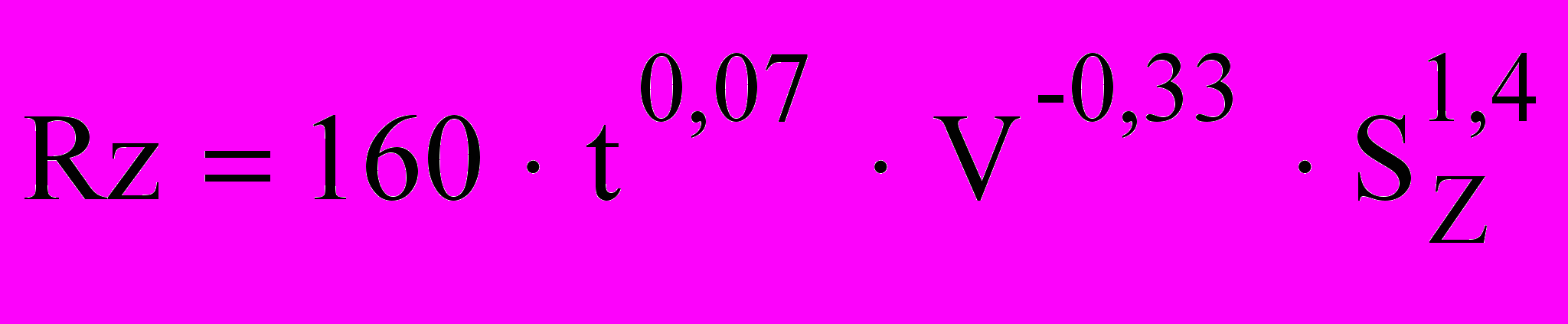
(3)
;
- при торцевом фрезеровании (станок 675П, глубина резания t = 0,5 мм, скорость резания V = 100 - 200 м/мин, подача Sz = 0,05 - 0,1 мм/зуб, радиус округления ρ = 20 - 100 мкм)

(4)
;
- при точении (станок 16К20, глубина резания t = 0,5мм, скорость резания V = 100 - 200 м/мин, подача S0 = 0,1 - 0,2 мм/об, радиус вершины rв = 0,4 - 0,8мм, вспомогательный угол в плане φ1 = 5 - 45º)

(5)
.

(6)
.
По полученным зависимостям (1 - 6) можно сделать следующий вывод: при чистовой обработке для обеспечения более низких параметров шероховатости необходимо увеличивать скорость резания, уменьшать подачу инструмента, а также уменьшать радиус округления режущей кромки.
Материал поступил в редколлегию 20.02.06.