Алехин Алексей Николаевич исследование
Вид материала | Исследование |
- Алёхин Анатолий Николаевич (доктор медицинских наук, профессор, заведующий кафедрой, 393.89kb.
- «Охотник и рыболов Поволжья и Урала» №9 (202), сентябрь 2009, 85.58kb.
- Рассказ натуралиста, 16.42kb.
- А. И. Герцена психолого-педагогический факультет методологический семинар, 1499.2kb.
- Законодательное собрание новосибирской области, 55.35kb.
- Маслов, Алексей Николаевич, 5.83kb.
- Алексей Николаевич Плещеев, 320.93kb.
- Алёхин Анатолий Николаевич: Уважаемые коллеги! Мы рады приветствовать вас на кафедре, 573.62kb.
- Петрухин Станислав Михайлович, Жеребцов Алексей Юрьевич, Комогорцев Игорь Борисович,, 37.1kb.
- Алёхин Анатолий Николаевич (доктор медицинских наук, профессор, заведующий кафедрой, 476.2kb.
ФЕДЕРАЛЬНОЕ АГЕНСТВО ПО ОБРАЗОВАНИЮ
Государственное образовательное учреждение высшего
профессионального образования
САМАРСКИЙ ГОСУДАРСТВЕННЫЙ ТЕХНИЧЕСКИЙ УНИВЕРСИТЕТ
________________________________________________________
Факультет «Машиностроения и автомобильного транспорта»
Кафедра «Инструментальные системы и сервис автомобилей»
Алехин Алексей Николаевич
ИССЛЕДОВАНИЕ ПРОЦЕССА ТОРЦОВОГО ФРЕЗЕРОВАНИЯ ИНСТРУМЕНТАМИ С СМП С ЦЕЛЬЮ ПОВЫШЕНИЯ ПРОИЗВОДИТЕЛЬНОСТИ И ТОЧНОСТИ ОБРАБОТКИ
Специальность 55.29.05 – Технология, оборудование и автоматизация машиностроительных производств
АВТОРЕФЕРАТ
Магистерской диссертации
Самара 2009
Работа выполнена в Государственном образовательном учреждении высшего профессионального образования Самарском Государственном Техническом университете (СамГТУ) на кафедре «Инструментальные системы и сервис автомобилей»
Научный руководитель: кандидат технических наук,
доцент Иванов Ювеналий
Иванович
Официальный рецензент: кандидат технических наук,
доцент Лысенко Николай
Васильевич
Ведущая организация: Самарский государственный
технический университет
(СамГТУ)
Защита состоится «30» июня 2009 г. в 9 часов на заседании ГАК ГОУ ВПО «Самарский государственный технический университет» по адресу: 443010 г.Самара, ул. Молодогвардейская, д. 133, корпус №3, ауд.39 .
С диссертацией можно ознакомиться на сайте кафедры «Технология машиностроения» ГОУ ВПО «Самарского государственного технического университета».
Секретарь ГАК Карлова М.Д.
ОБЩАЯ ХАРАКТЕРИСТИКА РАБОТЫ
Актуальность темы. В настоящее время при металлообработке широко применяются режущие инструменты со сменными многогранными режущими пластинами (СМП). Известные инструментальные фирмы такие как «Сандвик Коромант» (Швеция), «Мицубиси» (Япония), «Хертель» (Германия) и др. широко рекомендуют и поставляют потребителю широкую номенклатуру пластин СМП и конструкций инструментов. Конструкции инструментов отличаются друг от друга способом крепления пластин в корпусе инструмента, а так же закреплением инструмента на станке (конструкцией державки). Требованиям современного производства по производительности, надежности, стойкости, экономичности и другим показателям удовлетворяют разнообразные конструкции резцов с надежными способами крепления пластин. Поэтому необходимо объективно оценить и правильно выбрать инструмент наиболее подходящий для условий обработки. При выборе системы крепления пластины в корпусе резцов необходимо учитывать прогиб вершины резца при работе, от которого зависит точность обработки. Износ пластин должен быть благоприятным и обеспечивать работу с максимальной скоростью резания и подачей. Режимы резания рассчитываются или выбираются по нормативным таблицам, однако при этом не учитывается стоимость обработки, что очень важно при работе дорогостоящими инструментами с СМП. Правильно выбранный инструмент с широкими технологическими возможностями позволяет быстрее окупить затраты и получить экономический эффект в производстве за счет оптимальных режимов резания, сокращения времени наладки, количества применяемых инструментов и числа необходимых операций.
Цель работы. Сделать анализ существующих конструкций фрез с СМП по ИСО (Международная организация по стандартизации). Исследовать напряженно-деформированного состояния в узлах крепления торцовых фрез с СМП. Исследовать прогиба вершины пластины при затяжке различных схем крепления по ИСО совместно с приложенными силами резания. Разработать методику исследования. Изучить износ пластин при работе. Определить оптимальные режимы резания на ЭВМ с учетом технических ограничений и себестоимости. Построить номограмму для определения прогиба резцов в зависимости от силы резания, сделать выводы и дать практические рекомендации для производства, по применению и выбору инструментов с СМП.
Методы исследования, достоверность и обоснованность результатов.
Прогиб вершины пластины, возникающий при торцовом фрезеровании, для фрез с СМП пятигранной и квадратной формы с различными способами крепления исследован при помощи программы ANSYS.
Определение оптимальных режимов резания приведено с учетом минимальной себестоимости операций с помощью ЭВМ.
Научная новизна работы:
- выполнена оценка и обзор различных конструкции торцовых фрез с учетом их достоинств и недостатков.
- определен прогиб вершины пластины торцовых фрез различных конструкций, и созданы номограммы, позволяющие определить прогиб резца при работе, а так же сделать выбор системы крепления фрезы в зависимости от силы резания и требуемой точности обработки.
- изучен износ пластин СМП при фрезеровании, получена картина распределения величины износа.
- определены оптимальные режимы резания с учетом себестоимости операции, построены графики с оптимальными областями режимов резания для различных материалов в соотношении к различным инструментальным материалам.
- разработаны рекомендации по применению торцовых фрез с целью повышения точности и производительности.
Практическая ценность работы:
- разработана методика исследования напряженно-деформированного состояния СМП на фрезах с помощью программного продукта ANSYS.
- построены номограммы, позволяющие определить прогиб вершины сменной многогранной пластины при работе, а так же сделать выбор системы крепления фрезы в зависимости от силы резания и требуемой точности обработки.
- определены экономическая стойкость и скорость резания, позволяющие получить максимальный экономический эффект при работе фрезами с СМП.
Апробация работы.
В 2007г. с частью данной работы выступал на 63 научной конференции студентов и магистров – Самара, СамГТУ.
В 2007г. – выступление на факультетской конференции с докладом на тему «Определение экономической скорости резания фрезами с СМП при торцовом фрезеровании».
В 2009г. с докладом на тему: «Исследование напряженно-деформированного состояния и прогиб вершины СМП, и определение оптимальных режимов резания» на 64 научной конференции студентов и магистров – Самара, СамГТУ, награжден почетной грамотой.
Публикации.
В 2007 г – опубликована работа «Определение экономической скорости резания фрезами с СМП при торцовом фрезеровании» в сборнике студенческих работ на инструментальной Интернет-конференции
В 2008г – опубликован доклад на Всероссийской научно-технической Интернет-конференции с международным участием на тему «Высокие технологии в машиностроении».
Структура и объем работы. Работа состоит из введения, 7 глав, выводов, заключения, списка литературы и приложений. Основное содержание работы изложено на 90 страницах и содержит 39 рисунков, 13 таблиц, 9 листов графического материала и список литературы, состоящий из 12 источников.
СОДЕРЖАНИЕ РАБОТЫ
Во введении изложена актуальность темы и представлено краткое содержание диссертации. Сформулированы цель, научная новизна и практическая ценность работы.
В первой главе «Обзор конструкций торцовых фрез, недостатки и область применения» приведен анализ типовых конструкций торцовых фрез, который показал, что существует большое разнообразие конструкций, которые имеют свои достоинства и недостатки. Сделаны выводы, о том какие конструкции торцовых фрез удовлетворяют современным требованиям производства по точности и производительности.
Во второй главе «Особенности торцевого фрезерования» изложены особенности торцевого фрезерования: режимы резания, силы резания, толщина срезаемого слоя.
К элементам режима резания при фрезеровании относятся (рис.1):
– сила резания (Pz);
– нормальная сила (Py);
– осевая сила (Px);
– глубина резания (t);
– скорость резания (V);
– подача (S);
– ширина фрезерования (B).
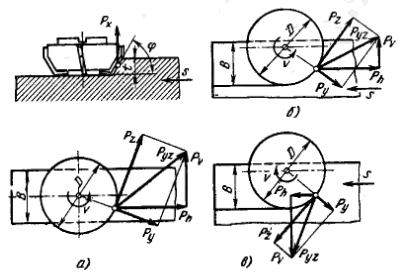
Рисунок 1 - Составляющие режимов и сил резания при торцовом фрезеровании: а) симметричном, б) несимметричном встречном, в) несимметричном попутном.
Глубину резания (t) выбирают в зависимости от припуска на обработку, мощности и жесткости станка. Надо стремиться вести черновое и получистовое фрезерование за один проход, если это позволяет мощность станка. Обычно глубина резания составляет 2...6 мм. На мощных фрезерных станках при работе торцовыми фрезами глубина резания может достигать 25 мм. При припуске на обработку более 6 мм и при повышенных требованиях к величине шероховатости поверхности фрезерование ведут в два перехода: черновой и чистовой.
При чистовом переходе глубину резания принимают в пределах 0,75...2 мм. Независимо от высоты микронеровностей глубина резания не может быть меньшей величины. Режущая кромка имеет некоторый радиус округления, который по мере износа инструмента увеличивается, при малой глубине резания материал поверхностного слоя подминается и подвергается пластическому деформированию. В этом случае резания не происходит. Как правило, при небольших припусках на обработку и необходимости проведения чистовой обработки (величина шероховатостей Ra = 2…0,4 мкм) глубина резания берётся в пределах 1 мм.
При малой глубине резания целесообразно применять фрезы с круглыми пластинами (ГОСТ 22086-76, ГОСТ 22088-76). При глубине резания, большей 3...4 мм, применяют фрезы с шести-, пяти- и четырехгранными пластинами.
Подача при фрезеровании - это отношение расстояния, пройденного рассматриваемой точкой заготовки в направлении движения подачи, к числу оборотов фрезы или к части оборота фрезы, соответствующей угловому шагу зубьев.
Таким образом, при фрезеровании рассматривается подача на оборот So(мм/об) - перемещение рассматриваемой точки заготовки за время, соответствующее одному обороту фрезы, и подача на зуб Sz(мм/зуб) - перемещение рассматриваемой точки заготовки за время, соответствующее повороту фрезы на один угловой шаг зубьев.
Помимо этого рассматривается также скорость движения подачи vs (ранее определялась как минутная подача и в старой литературе и на некоторых станках такой термин ещё применяется), измеряемая в мм/мин. Скорость движения подачи - это расстояние, пройденное рассматриваемой точкой заготовки вдоль траектории этой точки в движении подачи за минуту. Эта величина используется на станках для наладки на необходимый режим, поскольку у фрезерных станков движение подачи и главное движение резания кинематически не связаны между собой.
Применение соотношения скоростей подачи и резания помогает правильно определить величины So и Sz. Используя зависимости: So = Sz · z, vs = So · n где z - число зубьев фрезы, n - число оборотов фрезы (об/мин) определим vs = So · n = Sz · z · n.
Ширина фрезерования B (мм) - величина обрабатываемой поверхности, измеренная в направлении, параллельном оси фрезы - при периферийном фрезеровании, и перпендикулярном к направлению движения подачи - при торцовом фрезеровании. Ширина фрезерования определяется наименьшей из двух величин: ширины обрабатываемой заготовки и длины или диаметра фрезы.
Скорость резания при фрезеровании v определяется как линейная скорость точки фрезы (м/мин). Действительная скорость резания определяется по формуле
г
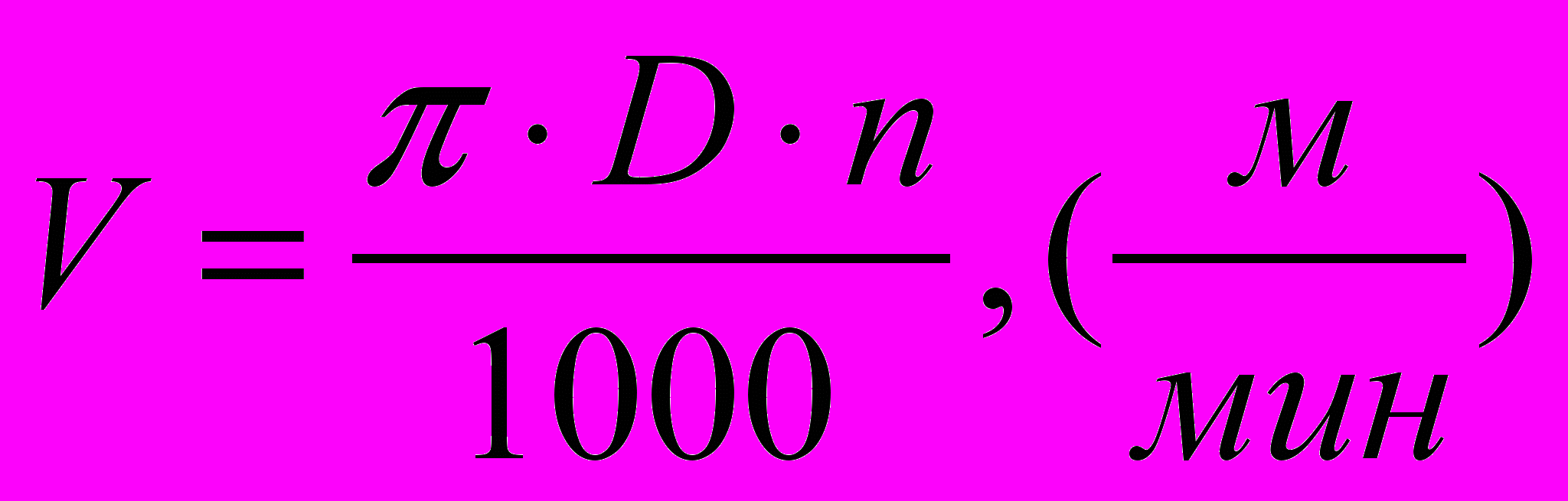
де D - диаметр фрезы (мм) по наиболее удалённой от оси вращения точке режущей кромки, n - число оборотов фрезы (мм/об).
Д

опустимая (расчётная) скорость резания определяется по эмпирической формуле
где Cv - коэффициент, характеризующий материал заготовки и фрезы;
T - стойкость фрезы (мин);
t - глубина резания (мм);
Sz - подача на зуб (мм/зуб);
B - ширина фрезерования (мм);
Z - число зубьев фрезы;
q, m, x, y, u, p - показатели степени;
kv - общий поправочный коэффициент на изменённые условия обработки.
Величины Cv q, m, x, y, u, p приведены в справочнике технолога-машиностроителя под ред. А.Г.Косиловой и Р.К.Мещерякова стр. 281-292.
Средние значения периода стойкости торцовых фрез при диаметре фрезы следующие
Таблица 1. Зависимость диаметра фрезы от стойкости
Диаметр фрезы (мм) | 40...50 | 65...125 | 160...200 | 250...315 | 400...650 |
Стойкость (мин) | 120 | 180 | 240 | 300 | 800 |
При фрезеровании торцовыми фрезами глубина фрезерования t определяется шириной Е фрезеруемой плоскости, измеренной перпендикулярно направлению движения подачи Ds, причем обычно Е = t
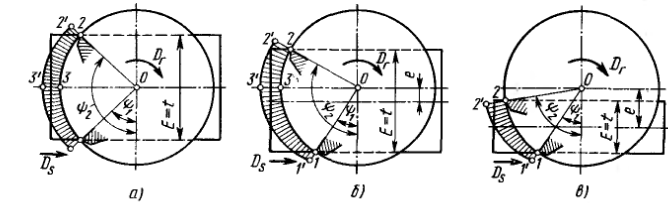
соs ψ1 = Е/D
Этому значению угла соответствует толщина az срезаемого слоя, выражаемая
az=Sz sin ψj как az1=Sz sin ψ1
На протяжении первой половины рабочего цикла толщина срезаемого слоя возрастает и в точке З, лежащей на оси симметрии обрабатываемой заготовка, толщина срезаемого зубом слоя максимальна и равна azmax=Sz . Далее толщина az постепенно убывает и в точке 2 толщина az2 = az1. На рис2,а условно показана эпюра толщины срезаемого слоя, которая в графической форме выражает закономерность изменен и я величины аz за рабочий цикл зуба фрезы. Она сохранит свой вид, сели рассматривать вращение фрезы против часовой стрелки.
При асимметричном ном фрезеровании ось симметрии заготовки, оставаясь параллельной направлению движения подачи Ds, смещена на расстояние е с оси О вращения фрезы. В зависимости от соотношения размера Е и диаметра D фрезы, а также смещение е ось вращения фрезы может находиться в пределах заготовки (рис.2,б) или вне ее (рис.2,в).
При вращении фрезы по ходу часовой стрелки и при движении подачи слева направо каждый зуб фрезы независимо от смещения е вступает в контакт с заготовкой в точке 1 начала рабочего цикла, лежащей на нижней по рисунку стороне обрабатываемой заготовки. При этом резание начинается при толщине
срезаемого слоя, определяемой выражением az1=Sz sin ψ1. Значение угла ψ1 для точки 1 при любом смещении е можно получить из уравнения
cos ψ1 =2(0,5E + e)/D=(E + 2e)/D
При асимметричном расположении обрабатываемой поверхности и прохождения оси вращения фрезы внутри контура обрабатываемой поверхности толщина az срезаемого слоя достигает максимального о значения в точке З рабочего цикла, лежащей на траектории перемещения оси вращения фрезы, и равна
azmax=Sz.
Толщина срезаемого слоя аz2 на выходе зуба фрезы из обрабатываемой заготовки при завершении рабочего цикла определяется выражением
az2=Sz sin ψ2
-где угол ψ2 для случаев асимметричного фрезерования (рис2,б,в) находят по уравнению
cos ψ2 =2(2е - 0,5Е)/D=(2е - Е)/D
Таким образом, торцевое фрезерование отличается от других видов обработки плоских поверхностей: различными видами фрезерования (встречное, попутное) режимами резания, направлением сил резания, методикой расчета толщины срезаемого слоя
В третьей главе «Разработка методики исследования напряженно-деформированного состояния СМП на фрезах с помощью ANSYS» разработка методики исследования напряженно-деформированного состояния СМП на фрезах с помощью ANSYS.
Методика представлена для трех типичных конструкции фрез с СМП
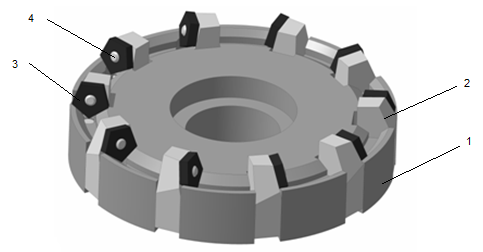
Рисунок 3 - Фреза, оснащенная пятигранными неперетачиваемыми твердосплавными пластинами, где корпус (1), державка (2), пластина (3), штифт (4). Державка, подтягивается крепежным винтом (на рисунке не изображен).
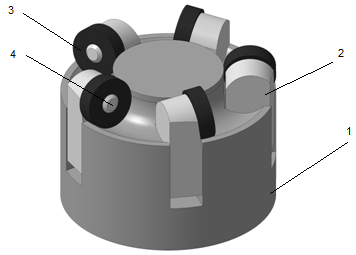
Рисунок 4 - Фреза, оснащенная круглыми неперетачиваемыми твердосплавными пластинами, где корпус (1), державка (2), пластина (3), штифт (4). Державка, подтягивается крепежным винтом (на рисунке не изображен).
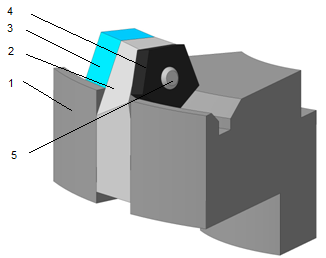
Рисунок 5 – Сегмент фрезы повышенной жесткости где сегмент корпуса (1), державка (2), дополнительная опора (3), пластина (4), штифт (5). Державка, подтягивается крепежным винтом (на рисунке не изображен).
В работе проведены исследования, в ходе которых анализировались прогибы вершины зуба фрезы, усиленной и обычной с пятигранными СМП без стружколомающей канавки, а также фрезы с круглой пластинкой. Все исследования проводились с помощью CAE пакета ANSYS.
В начале были смоделированы трехмерные модели простой и « усиленной» фрез. Была смоделирована 1/10 часть фрез. В качестве материала державки, резца и болта с гайкой была использована Сталь40, для СМП-Т14К8. В соответствии с этими материалами были заданны свойства каждому из объемов. Далее была произведена свободная разбивка на конечные элементы. Разбивка производилась свободно и с использованием опции Smart Size. Так же были заданы необходимые контактные пары и необходимые закрепления
После этого были рассчитаны по известным формулам составляющие силы резания, исходя из того, что обрабатываемый материал Сталь 45, глубина резания 3 мм, число зубьев 10, ширина шлифования 100 мм, диаметр фрезы 320 мм.
Рассчитанные силы резания по справочнику технолога-машиностроителя под ред. А.Г.Косиловой и Р.К.Мещерякова:
PY=3184 Н, PX=1361 Н, PZ=4620 Н.Результирующая сил резания:

Расчеты проводились с силами 1/3 R ,1/2R, R, 1.5 R, 2R. В результате получен график - зависимости прогиба δ от результирующий сил резания R.
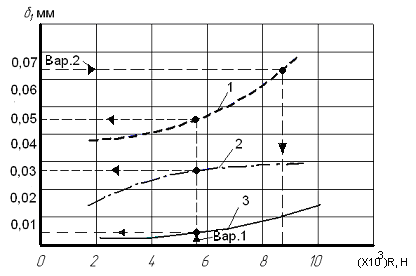
Рисунок 6 - График прогибов вершины пластины у торцовых фрез различных конструкций, где – обычная фреза(1); – фреза повышенной жесткости(2); – фреза с круглыми пластинами(3)
По графику сделаны выводы и даны рекомендации.
График имеет огромное практическое значение для технолога, задавая силы резания, может учесть предполагаемый прогиб пластины и скорректировать свои действия для получения требуемой точности.
В четвертой главе «Исследование напряженно-деформированного состояния в узлах крепления торцовых фрез с СМП» показано исследование напряженно-деформированного состояния в узлах крепления торцовых фрез с СМП.
Существуют различные схемы крепления по ИСО. На рисунке 7 представлены 3 вида, по которым проводились исследования.
Таблица 6. Схемы крепления по ИСО.
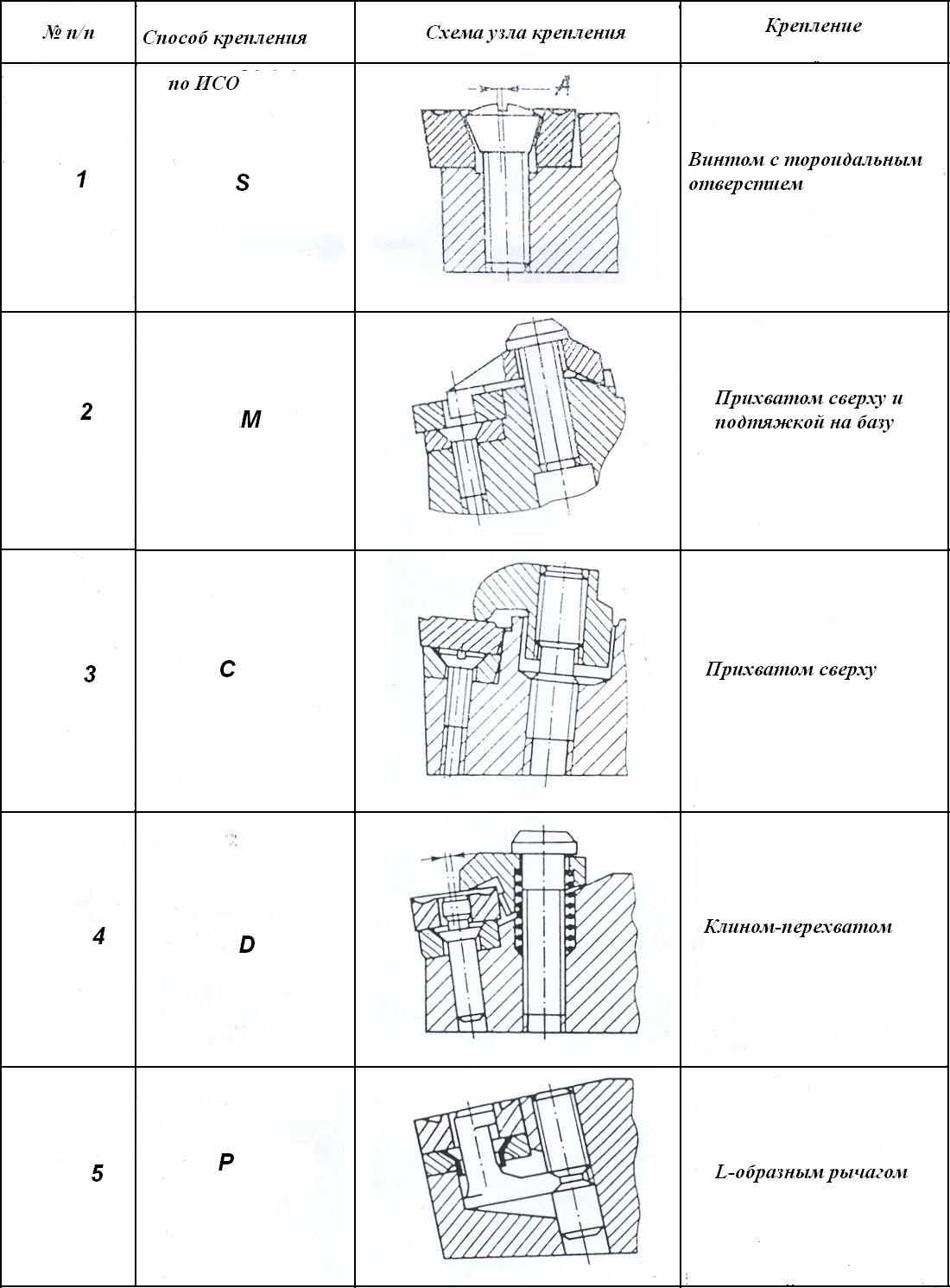
На рисунке 7 представлены спроектированные исследуемые фрезы.
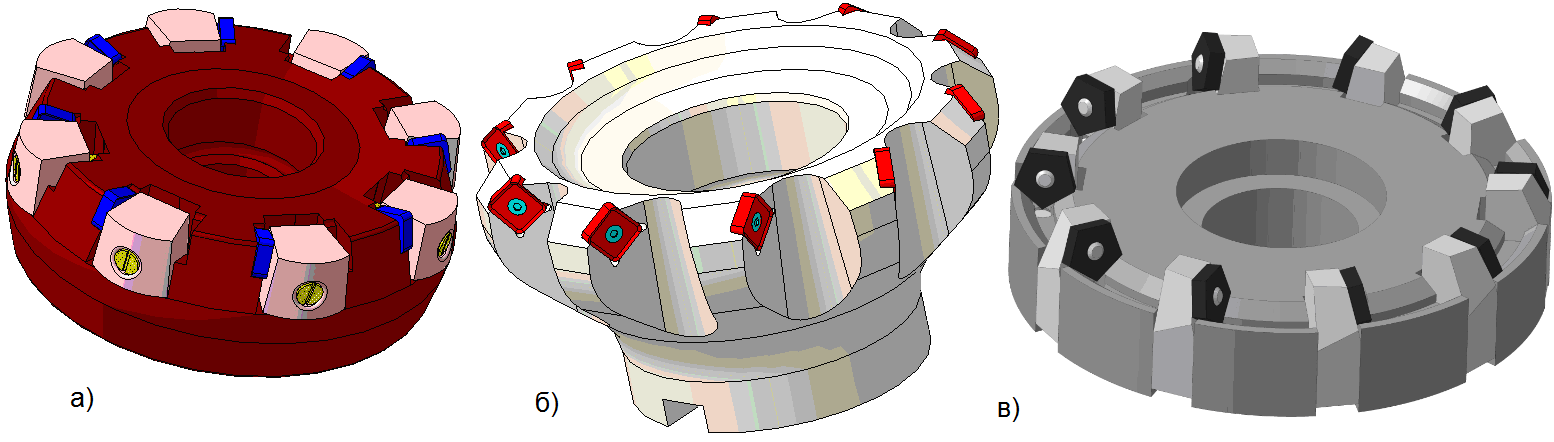
Рисунок 7 – Виды фрез: крепление С (а); крепление S (б); крепление Р (в).
Используя методику описанную в предыдущей главе: для определения прогиба вершины пластины СМП целесообразно применить программу ANSYS которая широко применяется в технике. Решение задачи в пакете ANSYS проходит в несколько этапов: выбираются типы конечных элементов и задаются их свойства; задается тип материала и его свойства; строится геометрическая модель; присваиваются атрибуты элементам геометрической модели (материал, тип конечного элемента); разбивается модель на конечные элементы; задаются граничные условия (закрепления модели и действующие силы); производится решение задачи.
Учитывая многозвеньевую систему креплений торцовых фрез, получили результаты в виде таблицы 7.
Таблица 7. Прогиб вершин пластин при различной результирующей силе резания R.
R =5700Н | Прогиб δ, при способе крепления: | ||
С | S | P | |
1/3 | 0,038 | 0,088 | 0,076 |
1/2 | 0,046 | 0,096 | 0,078 |
1 | 0,05 | 0,104 | 0,09 |
1.5 | 0,092 | 0,154 | 0,126 |
2 | 0,12 | 0,198 | 0,168 |
Из приведенных результатов видно, что прогиб вершины пластины прямопропорционально зависит от величины силы R. С увеличение результирующей силы величина прогиба так же увеличивается.
Прогиб имеет такую большую величину, по сравнению с рисунком 6 в связи с тем, что фреза с СМП состоит не только из пластинки и державки, но и из различных элементов крепления (рычаги, прихваты, винты и др.). Элементы крепления пластины так же деформируются под действием сил резания, что в свою очередь влияет на прогиб, а, следовательно, и на точность обработки. Определять прогиб вершины пластины с помощью формул представляет большие трудности, так как это многозвеньевая система, требует принять ряд допущений и сложного математического расчета.
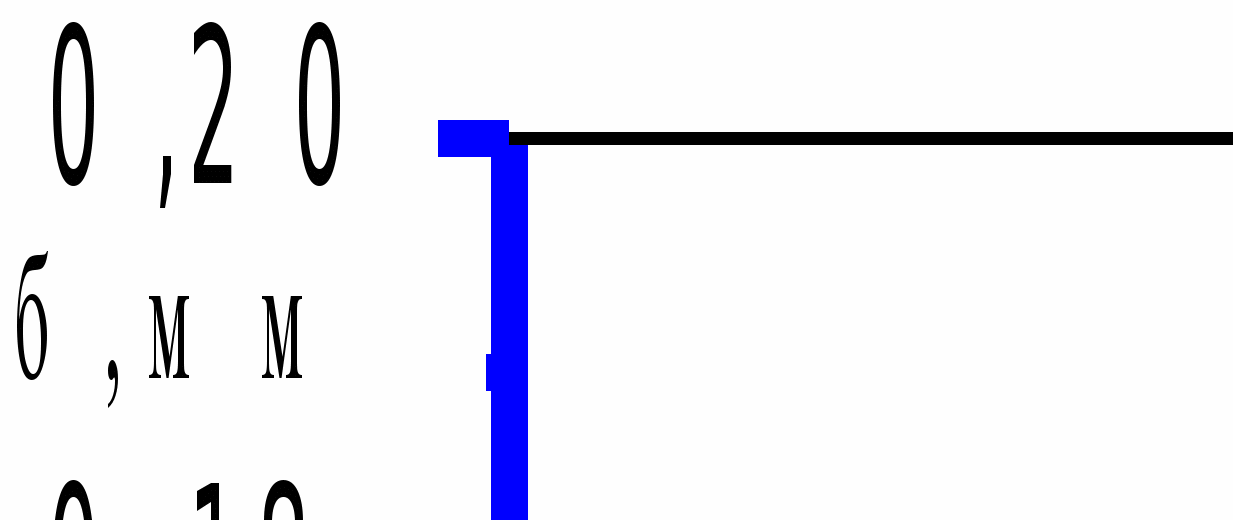
По результатам полученных исследований построен график (рисунок 8) имеющий практическое значение. По графику можно по значению R определить величину δ. Например, 1 вариант, зная величину силы резания R=5700Н, технолог может определить величину предполагаемого прогиба, для крепления С – δ=0,05мм, крепления S – δ =0,104мм, крепления Р – δ=0,09мм. Отсюда видно, что наименьший прогиб имеет пластина на фрезе со схемой крепления С, значит технологу рекомендуется выбрать именно эту фрезу. Для 2 варианта, технолог, зная требуемую величину точности обрабатываемой поверхности, получаемую при прогибе пластины δ=0,038мм, может определить производительность (в данном случаи величина силы резания) различных схем крепления.
В пятой главе «Износ сменных многогранных пластин при фрезеровании сталей» показано исследование износа режущих пластин. Величина износа пластин измерялась с помощью инструментального микроскопа. По величине износа сделаны выводы о характере износа и правильности выбора режимов резания. Получена график распределения величины износа пластин, из которого видно, что кривая фактического распределения наиболее близко соответствует теоретической кривой нормального распределения по закону Гаусса
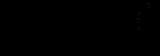
Таблица 8. Способы устранения износа при фрезеровании.
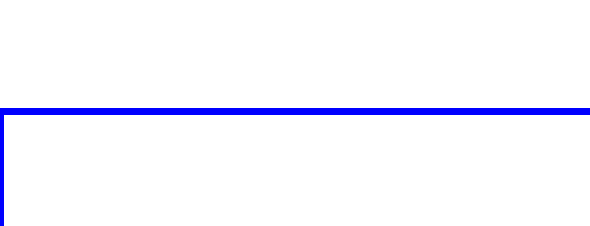
В шестой главе «Исследование оптимальных режимов резания фрез с СМП с помощью ЭВМ» приведено исследование оптимальных режимов резания фрез с СМП с помощью ЭВМ с учетом следующих ограничений:
1 - Ограничение по мощности привода главного движения станка;
2 - Ограничение по прочности механизма подачи станка;
3 - Ограничение по минимальной частоте вращения шпинделя;
4 - Ограничение по максимальной частоте вращения шпинделя;
5 - Ограничение по минимальной подаче;
6 - Ограничение по максимальной подаче;
7 - Ограничение по стойкости инструмента;
8 - Ограничение по шероховатости, обрабатываемой поверхности.
Исследование проводилось для двух инструментальных материалов (твердый сплав и быстрорежущая сталь) при обработке стали 40Х, серого и ковкого чугуна.
В качестве целевой функции принята себестоимость операции F, которая выражается через режимы обработки виде :
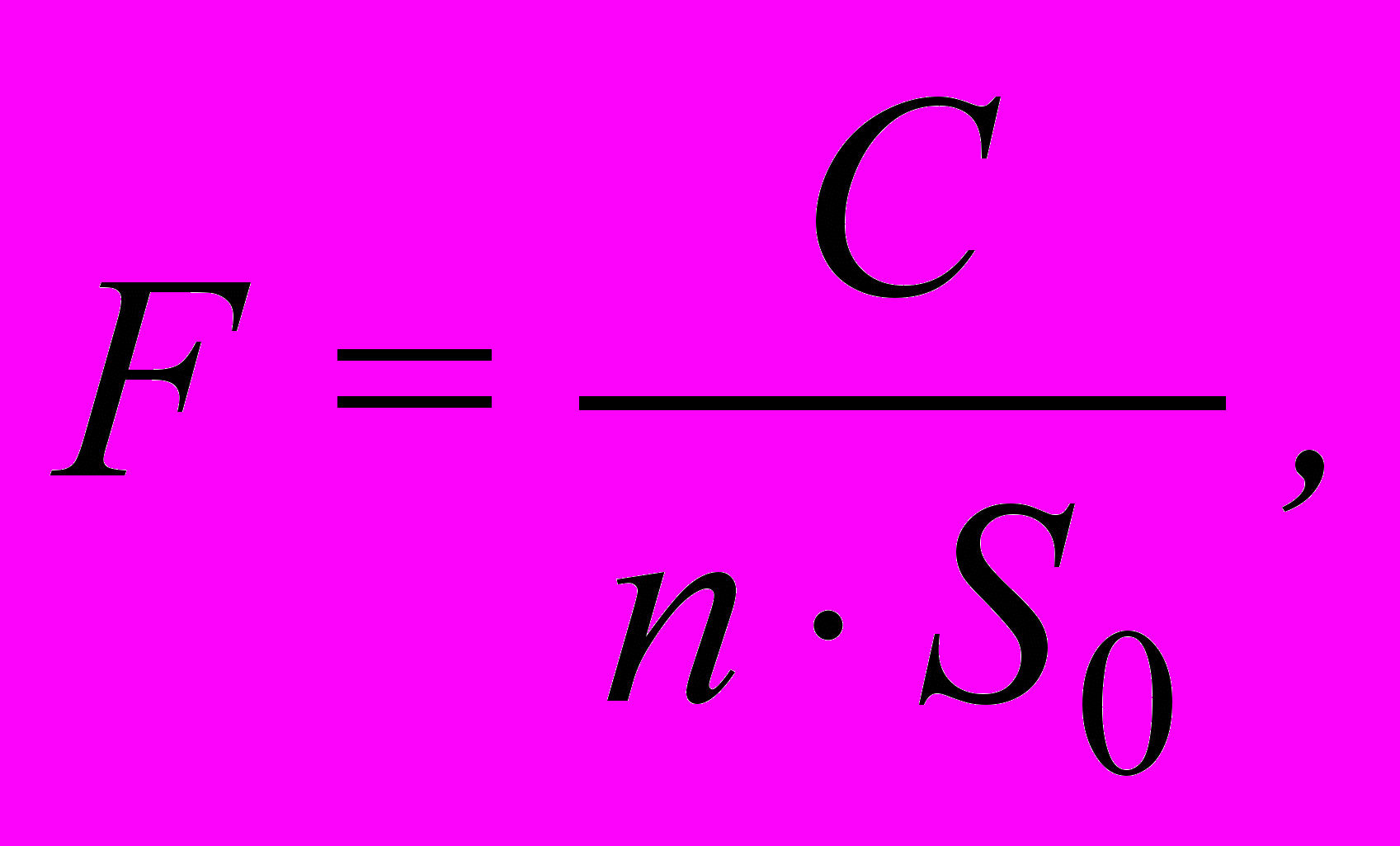
где коэффициент С зависит от условий обработки, но не зависит от режимов резания.
Математическая модель оптимального режима резания содержит систему технических ограничений, выраженных в виде линейных неравенств, и линейное уравнение целевой функции. Поэтому необходимо привести все технические ограничения и целевую функцию к линейному виду путем логарифмирования. Например, ограничение по стойкости инструмента будет иметь вид:

где
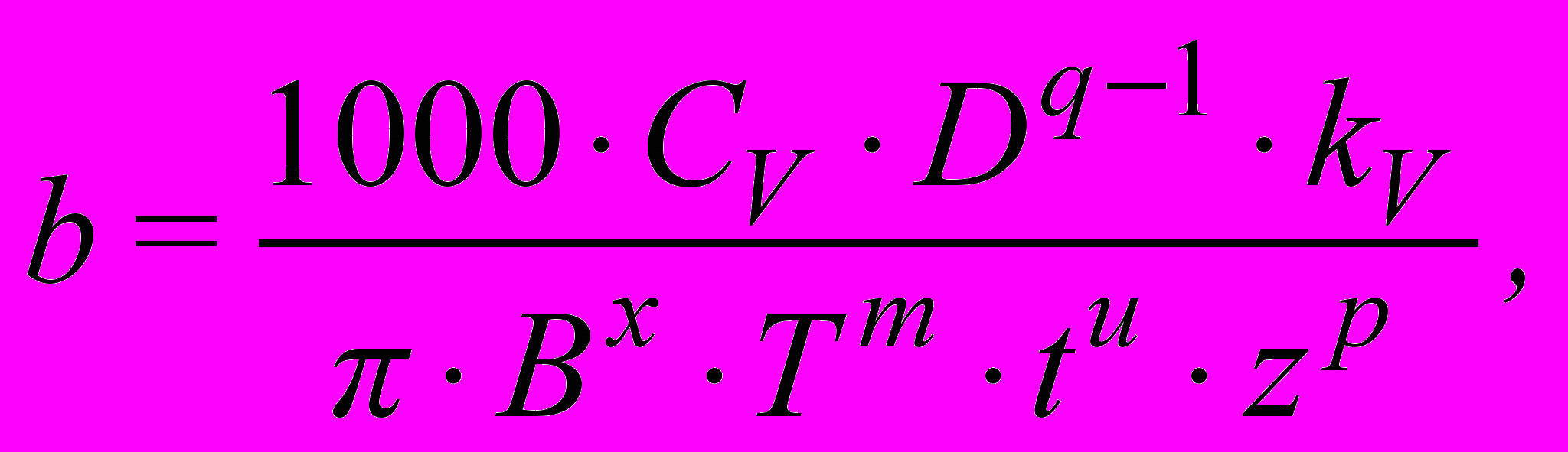
Отметим, что подача умножается на 100, чтобы избежать получения отрицательных значений логарифмов. Введем обозначения: x1=ln п; x2=ln(100·Sz). Тогда выражение (2) примет вид:
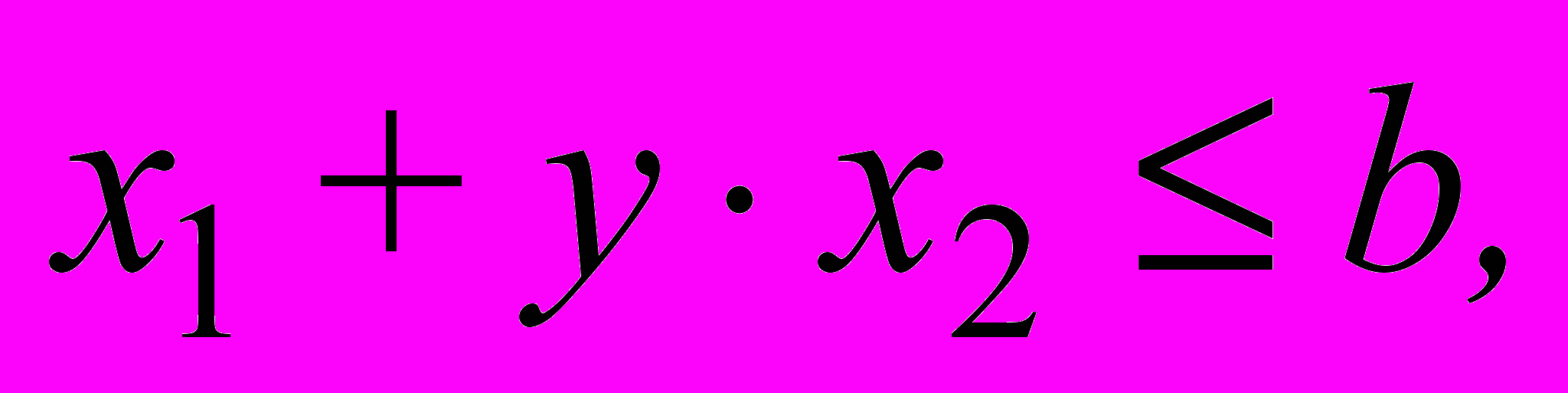
Уравнение целевой функции (1) преобразуется к виду6
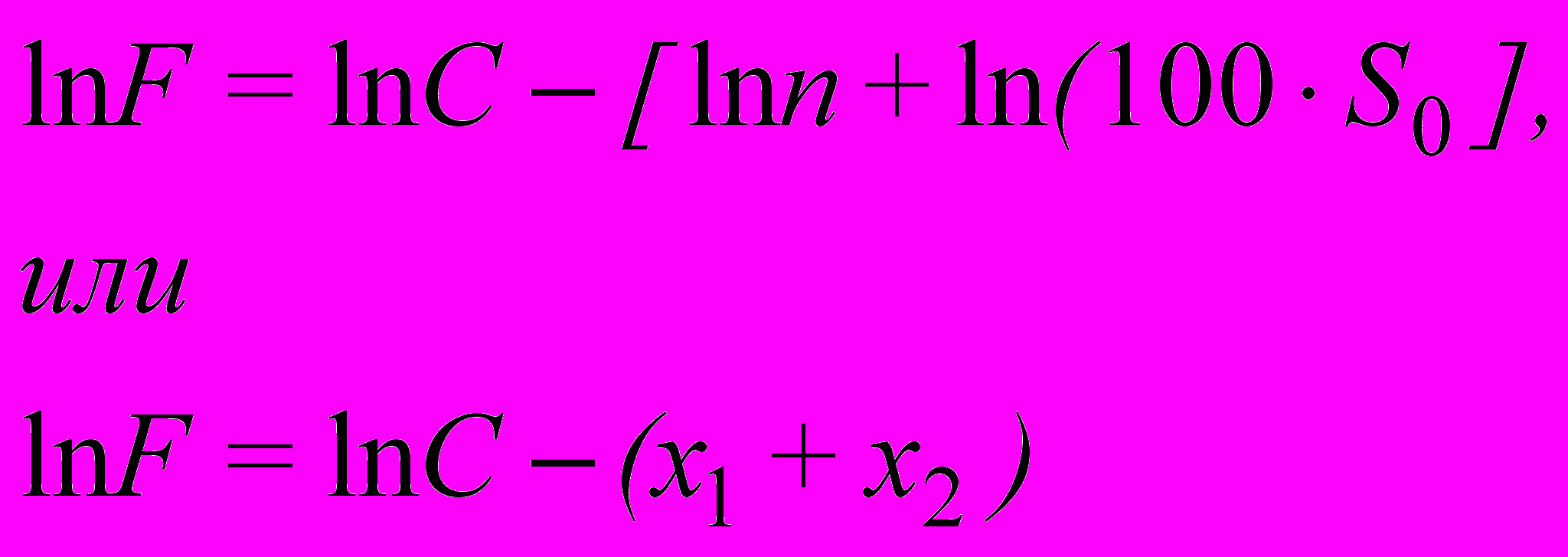
Обозначим: lnF=f; lnC=A, тогда выражение (4) примет вид:
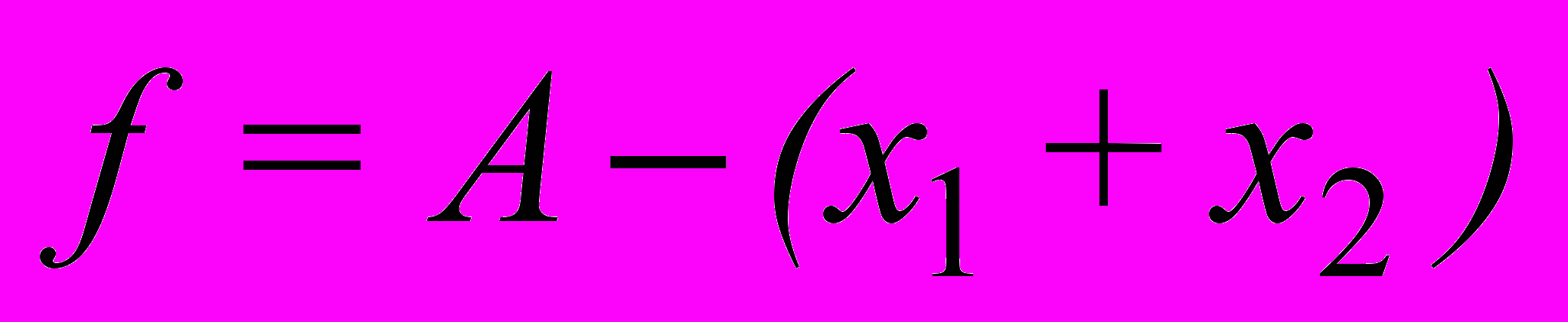
Очевидно, величина f будет равна максимуму или минимуму, если cкобка (x1+x2) будет соответственно стремиться к минимуму или максимуму. Поэтому целевую функцию f для нашей задачи минимизации себестоимости обработки представим в виде: f=(x1+x2)→max (6)
Определение оптимальных режимов обработки может быть выполнено графически. В этом случае каждое техническое ограничение представляется граничной прямой, которая определяет полуплоскость, где возможно существование решений системы неравенств. Граничные прямые, пересекаясь, образуют многоугольник решений, внутри которого координаты любой точки удовлетворяют всем без исключения ограничениям. В теории линейного программирования показано, что экстремальное значение целевой функции при выпуклом многоугольнике решений обеспечивается для х1 и х2, соответствующих точке, лежащей на одной из граничных прямых, или точке их пересечения.
Поэтому задача отыскания оптимальных значений х1 и х2 сводится к последовательному вычислению координат всех возможных точек пересечения граничных прямых и определению для них наибольшей суммы f= (х1 + х2)= mах.
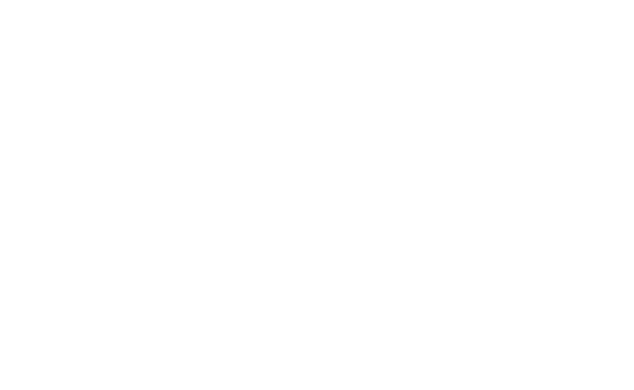
Рисунок 9 – Оптимальные области режимов резания для инструментального материала быстрорежущая сталь при фрезеровании разных материалов.

Рисунок 10 – Оптимальные области режимов резания для инструментального материала твердый сплав при фрезеровании разных материалов.
После определения координат х1 и х2, обеспечивающих выполнение условия (6), вычисляются оптимальные значения элементов режима резания
n=ex1,об/мин (7)
Sz= ex2/100, мм/зуб (8)
Эффективным средством решения задач, связанных с поиском оптимальных значений параметров, является симплекс-метод линейного программирования, реализуемый с помощью ЭВМ.
На графиках показаны оптимальные точки – значения режимов резания. Они находились из условия x1+x2→max. Такие точки обычно находятся в правом верхнем углу области оптимальных режимов. По графикам видно, что более максимальное положение у точек с фрезой с СМП с ИМ Т15К6, чем с ИМ Р6М5. Эти данные свидетельствуют о том, что фрезы из ТС имеют более высокие оптимальные режимы резания, чем фрезы из БС. Отсюда производительность фрез с СМП с ИМ Т15К6 выше.
Графики показывают, что с наиболее высокой скоростью фрезой из БС можно обрабатывать материал медные сплавы, а фрезой из ТС сталь 40Х. Об этом говорит высокая производительность, отвечающая условию x1+x2→max. Следует отметить, что при обработке данных материалов более высокие показатели n·S имеет фреза с СМП с ИМ Т15К6. Это говорит о ряде преимуществ твердосплавных фрез перед фрезами из быстрорежущего материала.
Для каждого инструментального материала при обработке одной из фрез найдены оптимальные режимы n и Sz для каждого из обрабатываемых материалов. На основе этих данных можно сделать рекомендации, что при равных условиях точности производительность обработки твердым сплавом выше, чем фрезой из быстрорежущего сплава. Об этом говорят более на порядок высокие скорости резания фрезы из Т15К6.
В седьмой главе «Разработка практических рекомендаций при торцовом фрезеровании» разработаны практические рекомендации по применению торцовой фрезы со сменными многогранными пластинами.
Даны общие рекомендации:
- по выбору торцовых фрез при обработке плоских поверхностей в зависимости от точности и производительности;
- по составлению методика исследования напряженно-деформированного состояния при торцовом фрезеровании фрезами со сменными многогранными пластинами;
- по выбору схемы крепления в зависимости от точности обработки, при которой прогиб вершины пластины торцовой фрезы будет минимальным;
- по устранению износа сменных многогранных пластин при фрезеровании;
- по выбору режимов резания, при которых производительность обработки максимальна, а себестоимость минимальна.
ОБЩИЕ ВЫВОДЫ
По результатам, полученным в представленной работе, можно сделать следующие выводы:
- Проведен анализ существующих конструкций торцовых фрез по ИСО.
- Указаны особенности торцевого фрезерования.
- Разработана методика исследования напряженно-деформированного состояния сменных многогранных пластин на фрезах с помощью программы ANSYS. Построен график зависимости прогибы от сил резания.
- Исследовано напряженно-деформированное состояние в узлах крепления в торцовых фрезах с помощью программы ANSYS и определены прогибы вершины пластин с различными системами крепления СМП (винтом, рычагом, прихватом сверху).
- Измерения износа пластин показали, что после обработки благоприятный износ, вызванный истиранием и не превышающий
= 0,5 имеют 60% пластин, выкрашивании режущих кромок при
> 0,6 присутствует на 33,3% пластин, а скол пластины
> 1.0 составляет 6,7%.
- Получены оптимальные режимы резания с помощью ЭВМ с учетом целевой функции себестоимости, с учетом различных ограничений. Построены графики, оптимальных областей режимов резания для двух инструментальных материалов, при обработке стали и чугуна. Найдены точки, где производительность обработки наиболее высокая.
- Построены номограммы для определения прогиба резцов в зависимости от силы резания и различных схем закрепления. Эти номограммы имеют большое практическое значение для конструкторов и технологов при работе.
- Полученные по работе практические рекомендации могут быть применены: при разработке и конструировании торцовых фрез и инструментов с СМП, для выбора способа закрепления пластины и создания более жестких конструкций при разработке технологического процесса изготовления деталей, при определении точности и более высокой производительности на операциях, а так же для осуществления заказа по каталогам фирм оптимальных конструкций инструмента.
ПУБЛИКАЦИИ:
1. Материалы научно-технической интернет-конференции с международным участием, Иванов Ю.И., Алехин А.Н., «Определение экономической скорости резания фрезами с СМП при торцовом фрезеровании», с. 153-158., Самара, 2007, www.konferencia-isap.narod.ru.
2. Всероссийская научно-техническая интренет-конференция с международным участием «Высокие технологии в машиностроении», Иванов Ю.И., Алехин А.Н., Утянкин А.В., «Исследование напряженно-деформированного состояния на торцовых фрезах с СМП», с.29-31., Самара,2008