Лекция 10. Основные способы обработки металлов давлением, их характеристика. Прокатка Прокатка
Вид материала | Лекция |
СодержаниеПоперечная прокатка Поперечно – винтовая прокатка Сортовой прокат Листовой прокат Трубный прокат Специальный прокат |
- Курсовая работа по курсу "Металлургия, часть LLL Обработка металлов давлением", 358.63kb.
- Научные основы и технологические способы обработки гетерофазных сплавов с высоким уровнем, 572.64kb.
- Развитие научных основ и разработка совмещенных методов обработки металлов давлением,, 606kb.
- Лекция Общая характеристика абразивной обработки. Абразивные материалы. Основные способы, 158.28kb.
- Обработка металлов давлением при обработке металлов давлением, 131.9kb.
- Рекомендовано Минобразованием России для направления подготовки диплом, 89.5kb.
- Задачи дисциплины получение знаний по технологическим процессам получения и обработки, 11.83kb.
- Лекция 11. Ковка и горячая объемная штамповка. Ковкой, 107.86kb.
- Секция “Краевые задачи в физике и химии твердого тела”, 31.36kb.
- Лекция 19. Специальные способы литья, 177.96kb.
Лекция 10. Основные способы обработки металлов давлением,
их характеристика.
Прокатка
Прокатка – это вид обработки металлов давлением, при котором заготовка силами трения втягивается в зазор между вращающими валками прокатного стана и пластически деформируется ими с уменьшением площади поперечного сечения.
Прокатке подвергают до 90 % всей выплавляемой стали и большую часть цветных металлов.
Существуют три основных способа прокатки: продольная, поперечная, поперечно – винтовая (рис.1).
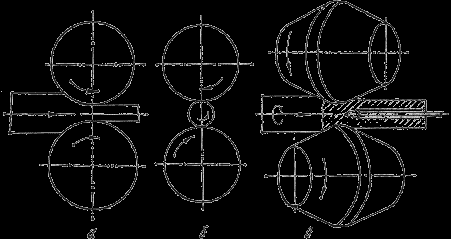
Рис. 1. Схемы основных видов прокатки:
а – продольная; б – поперечная; в – поперечно – винтовая
При продольной прокатке деформация осуществляется между вращающимися в разные стороны валками (рис.1 а). Заготовка втягивается в зазор между валками за счет сил трения и перемещается перпендикулярно осям валков. Этим способом изготавливается около 90 % всей катаной продукции – сортовой прокат, ленты, полосы, листы.
Поперечная прокатка (рис. 1б). Валки вращаются в одну сторону, приводя во вращательное движение заготовку.
В процессе поперечной прокатки обрабатываемое тело удерживается в валках с помощью специального приспособления. Обжатие заготовки по диаметру и придание ей требуемой формы сечения обеспечивается профилировкой валков и изменением расстояния между ними. Данным способом производят специальные периодические профили, изделия представляющие тела вращения – шары, оси, шестерни.
Поперечно – винтовая прокатка (рис. 1в). Валки, вращающиеся в одну сторону, установлены под углом друг другу. Прокатываемый металл получает и вращательное и поступательное движение. В результате сложения этих движений каждая точка заготовки движется по винтовой линии. Применяется для производства труб и периодического проката.
Теоретические основы прокатки
Для того чтобы начался процесс прокатки, необходимо выполнить условие захвата заготовки валками. В момент захвата металла со стороны каждого валка действуют на металл две силы: нормальная сила
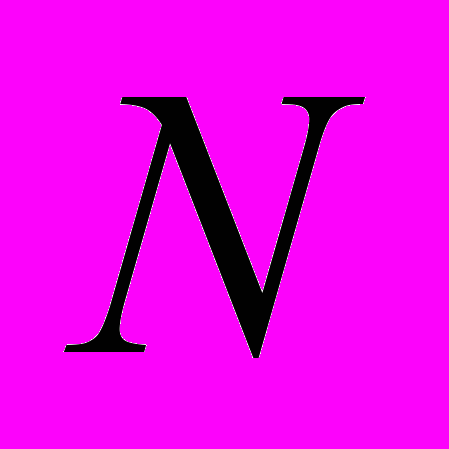
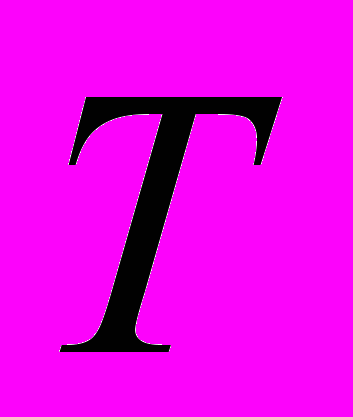
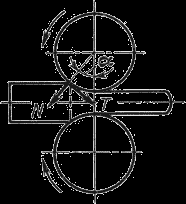
Рис. 2. Схема сил, действующих при прокатке
Угол
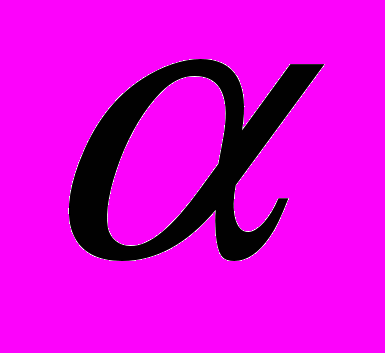
Проекция нормальной реакции
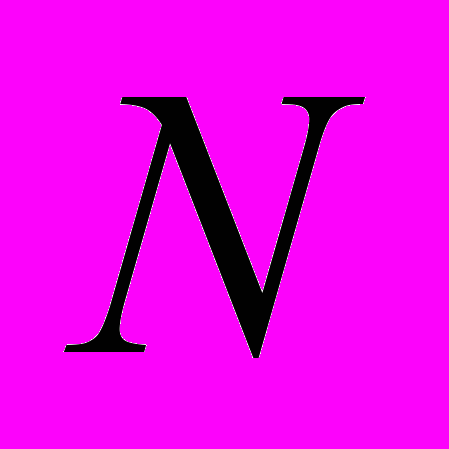
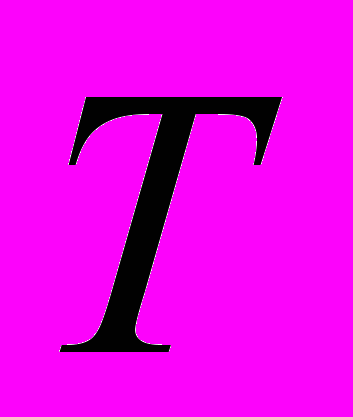

Известно, что
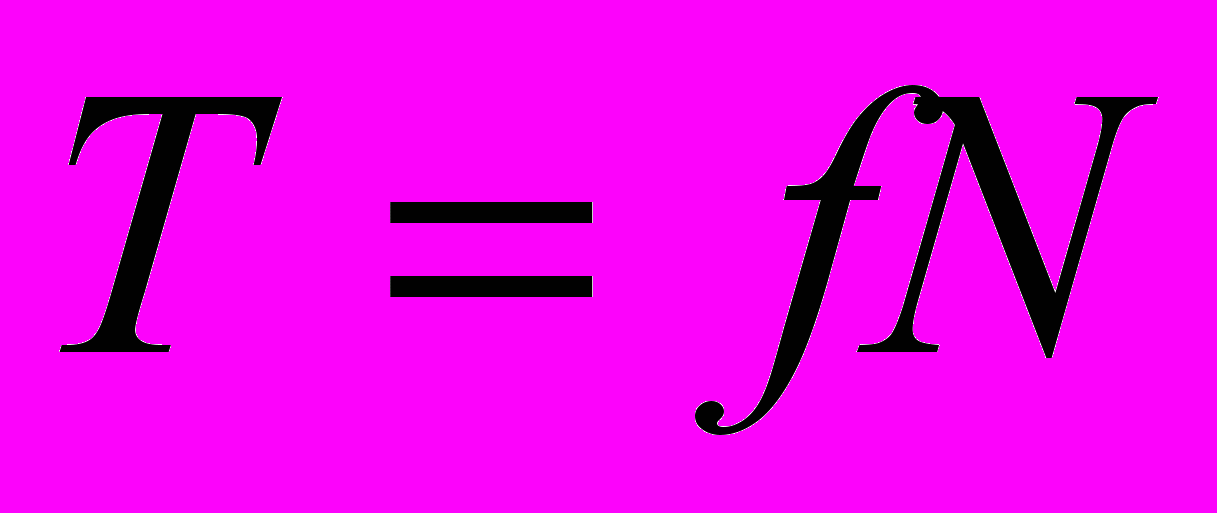
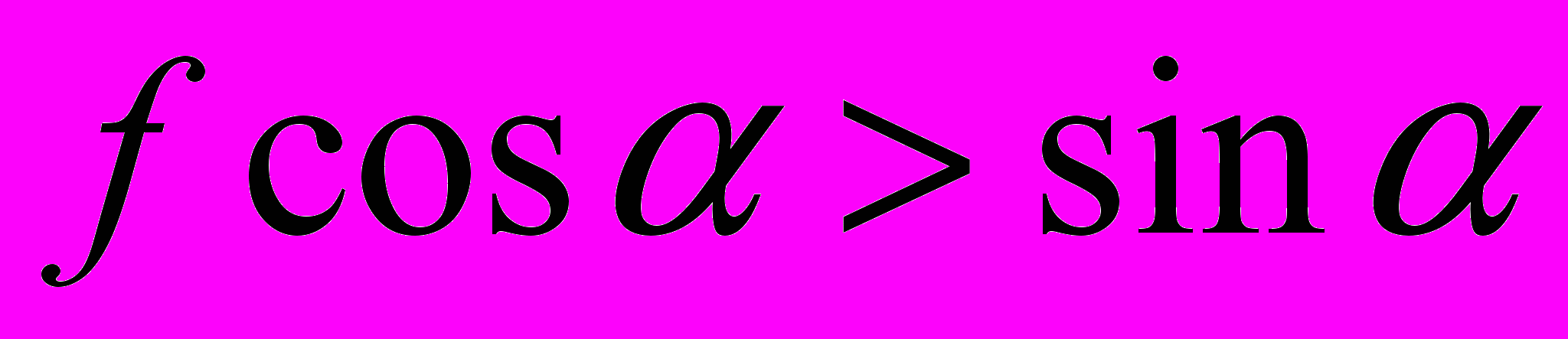
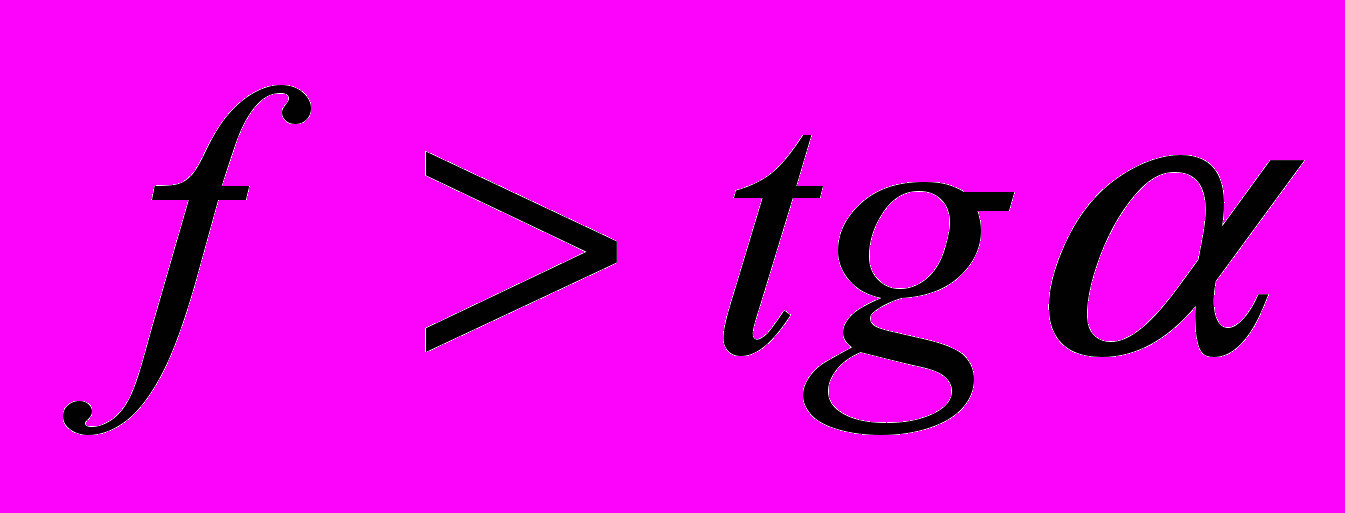
Таким образом, для захвата металла валками необходимо, чтобы коэффициент трения между валками и заготовкой был больше тангенса угла захвата.
Абсолютное обжатие – разность исходной Н и конечной h толщин
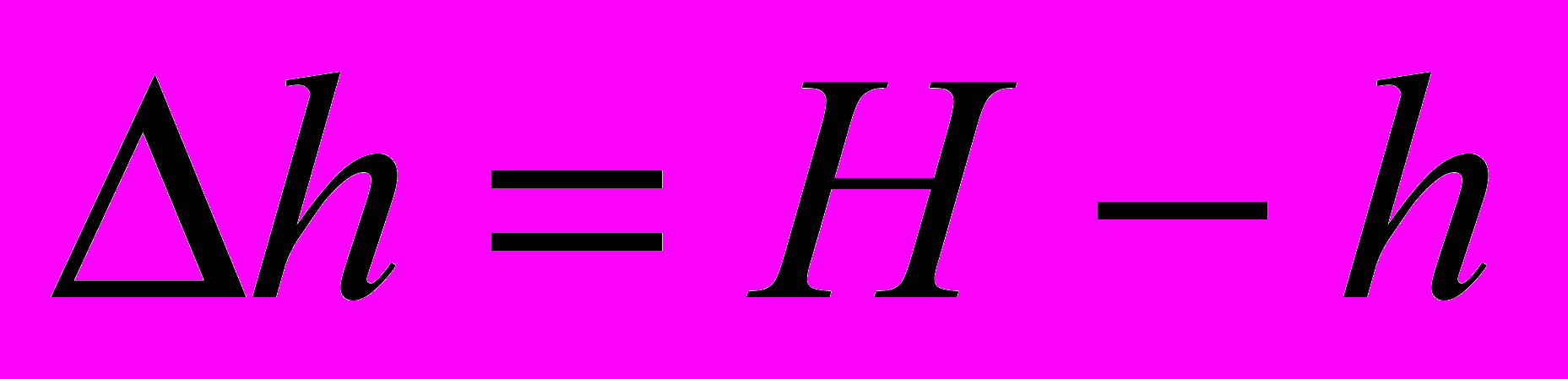
Относительное обжатие или степень деформации

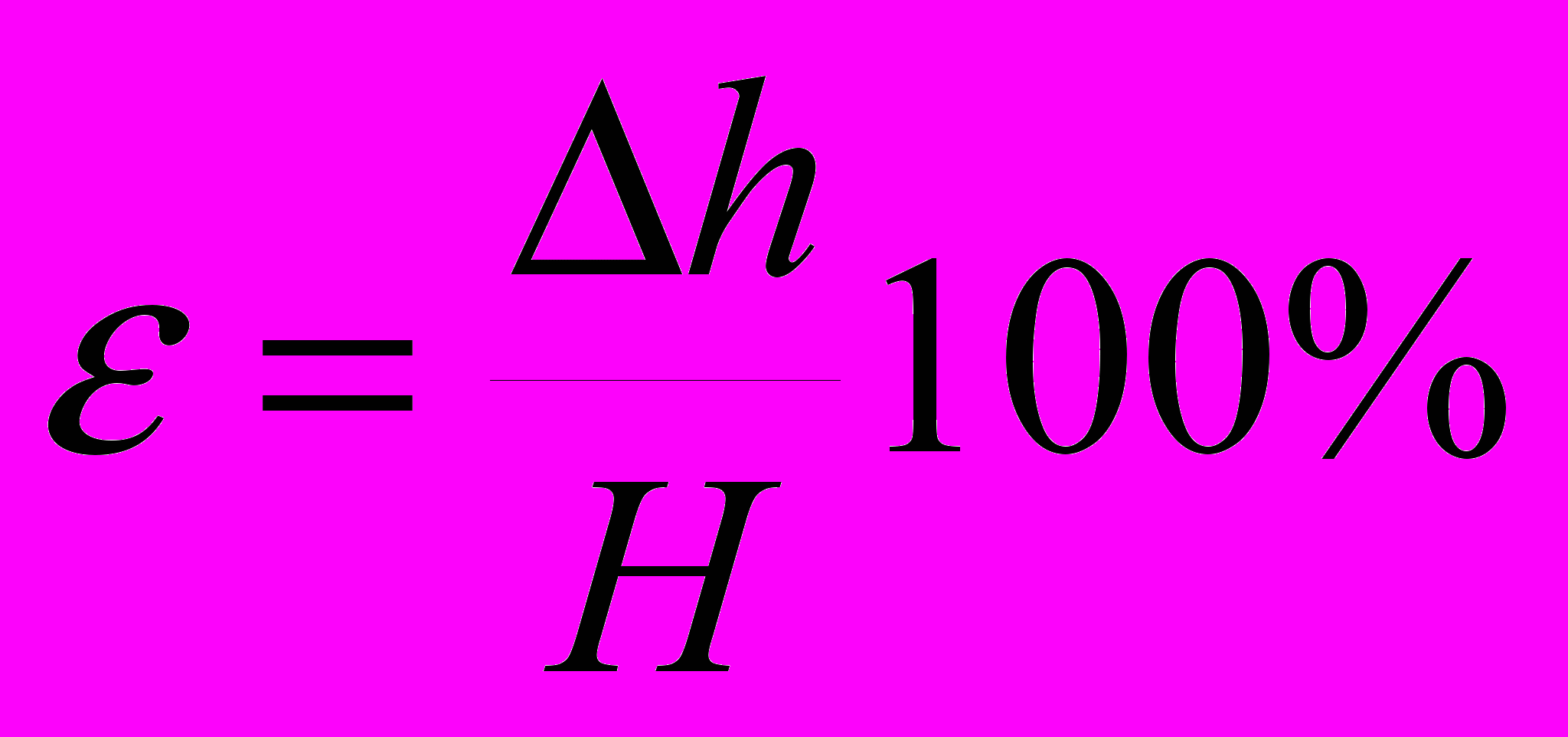
Максимальное значение степени деформации составляет 20–50%.
Продукция прокатного производства
Форма поперечного сечения называется профилем проката. Совокупность профилей различной формы и размеров – сортаментом проката Различают пять групп сортамента проката: сортовой, листовой, трубный, специальный и периодический.
1) Сортовой прокат. Среди сортового проката различают:
- заготовки круглого, квадратного и прямоугольного сечения для ковки и прокатки;
- простые сортовые профили (круг, квадрат, шестигранник, полоса, лента);
- фасонные сортовые профили:
- профили общего назначения (уголок, швеллер, тавр, двутавр);
- профили отраслевого назначения (железнодорожные рельсы);
- профили специального назначения (профиль для рессор, напильников).
- профили общего назначения (уголок, швеллер, тавр, двутавр);
2) Листовой прокат. Листовой прокат из стали и цветных металлов подразделяется на толстолистовой (4…60 мм), тонколистовой (0,2…4мм) и жесть (менее 0,2 мм). Толстолистовой прокат получают в горячем состоянии, другие виды листового проката – в холодном состоянии. Прокатку листов и полос проводят в гладких валках.
3) Трубный прокат. Трубный прокат получают на специальных трубопрокатных станах. Различают бесшовные горячекатаные трубы диаметром 25…550 мм и сварные диаметром 5…2500 мм.
Трубы являются продуктом вторичного передела круглой и плоской заготовки.
Общая схема процесса производства бесшовных труб предусматривает две операции: 1– получение толстостенной гильзы (прошивка); 2 – получение из гильзы готовой трубы (раскатка).
Первая операция выполняется на специальных прошивочных станах в результате поперечно-винтовой прокатки. Вторую операцию выполняют на трубопрокатных раскатных станах различных конструкций: пилигримовых, автоматических и др.
Схема прокатка труб на пилигримовом стане представлена на рис. 3.
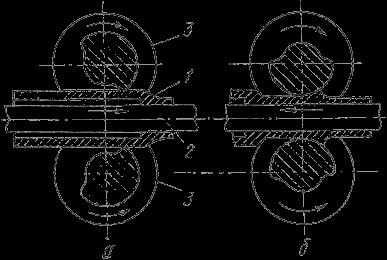
Рис.3. Схема прокатки труб на пилигримовом стане
В толстостенную гильзу 1 вводят оправку (дорн) 2 подающего механизма, длина которой больше длины гильзы. Гильза перемещается к валкам 3, калибр которых разделяется на две части: рабочую и холостую. Рабочая часть валка имеет рабочий и калибрующий участки. Процесс работы заключается в периодической подаче на определенную длину гильзы вместе с оправкой в зазор между валками в момент совпадения холостой части обоих валков (рис.3.а). Затем выполняется процесс прокатки, и гильза перемещается в направлении вращения валков, т.е. обратном ходу прокатываемой трубы (рис. 3.б). При этом рабочий участок обжимает гильзу по диаметру и толщине стенки, а калибрующий участок обеспечивает выравнивание диаметра и толщины стенки. После выхода из рабочей части оправка с гильзой продвигаются вперед, поворачиваясь на 900 вокруг продольной оси. По окончании прокатки валки разводят, и подающий механизм обратным ходом вытягивает оправку из трубы.
Сварные трубы изготавливают на трубосварочных агрегатах различными способами: печной сваркой, контактной электросваркой и др. из полос – штрипсов. Процесс получения трубы состоит из получения заготовки в виде свернутой полосы и сварки ее в трубу.
Особое место занимают станы спиральной сварки. Трубы получают завивкой полосы по спирали на цилиндрических оправках с непрерывной сваркой спирального шва автоматической сварочной головкой.
4) Специальный прокат – продукция законченной формы – венцы зубчатых колес, тракторный башмак, автообод колеса).
5) Периодический прокат – прокат, профиль которого периодически изменяется по длине (вагонные оси, полуоси автомобилей и др.). Периодические профили получают продольной, поперечной и винтовой прокаткой.
Инструментом прокатного производства являются валки. Они бывают гладкие для прокатки листов и лент, ступенчатые – для прокатки листовой стали, ручьевые – для получения сортового проката.
Валки состоят из бочки – рабочей части валка, шейки, которая опирается на подшипники станин и треф, имеющих форму крестовин для шарнирного соединения со шпинделем.
Профиль выреза на боковой поверхности валка называется ручьем. Ручей верхнего и нижнего валка образуют калибр. На каждой паре валков делают несколько калибров. Необходимый профиль на исходной заготовке получают путем последовательного пропуска заготовки через серию калибров.
Оборудованием для прокатки служат прокатные станы. Они состоят из рабочей клети (клетей), передаточного механизма и электродвигателя. Станы классифицируют по трем основным признакам:
- По назначению.
- По расположению рабочих клетей.
- По количеству валков в рабочей клети.
По назначению прокатные станы делятся на:
- Обжимные и заготовительные, предназначены для получения полупродукта. На обжимных станах получают:
- блюм, имеет квадратное сечение с размерами, мм
125×125…450×450.
Исходной заготовкой при прокатке блюмов являются слитки весом 6…10 тонн, прокатка осуществляется на блюмингах.
- сляб, имеет прямоугольное сечение с размерами, мм
толщина S=50…300
ширина В=400…1800.
Исходной заготовкой при прокатке слябов является слиток весом до 25 тонн, прокатка осуществляется на слябинге.
Технологический процесс производства блюмов и слябов состоит из следующих основных операций:
- нагрев слитков до
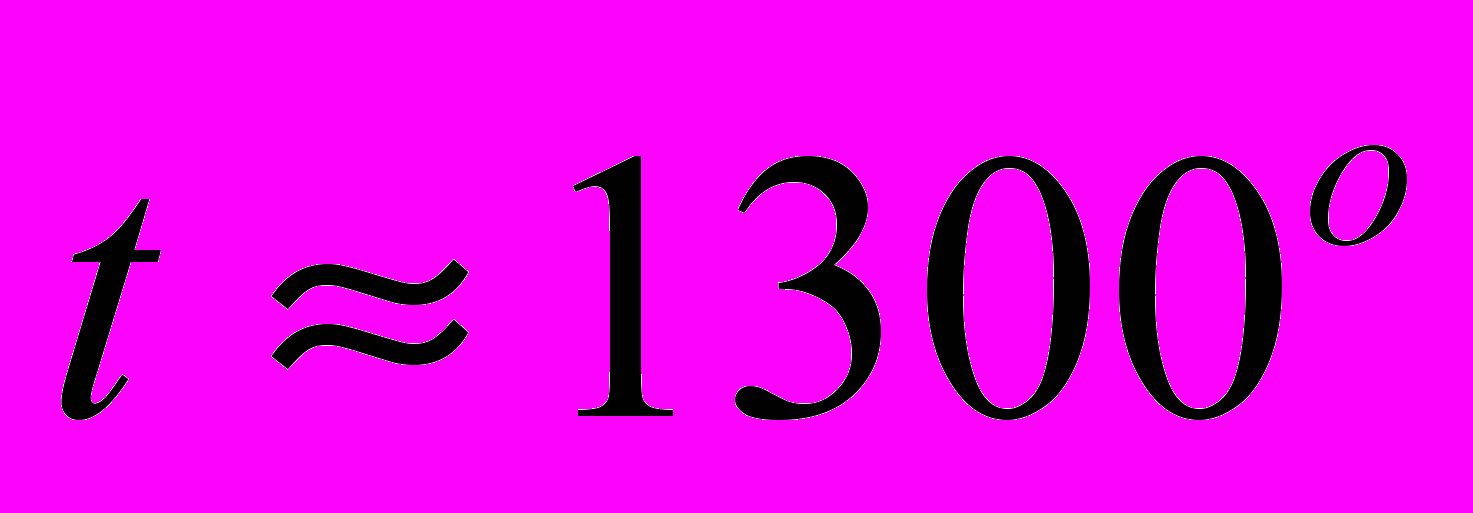
- прокатка
- резка раската на мерные куски длиной 2-6м специальными ножницами (усилием до 2000тонн)
- охлаждение, удаление поверхностных дефектов.
Прокатку производят в калибрах с обжатием в двух-взаимноперпендикулярных направлениях за 12-15 пропусков за 1-2 мин.
На заготовительных станах получают:
- заготовки, имеют квадратное сечение с размерами, мм
40×40…200×200.
Исходной заготовкой при прокатке заготовки являются блюмы.
- сутунку, имеет прямоугольное сечение с размерами, мм
толщина S=6…50
ширина В=150…600.
Сутунку прокатывают из слябов.
- Рельсобалочные, служат для прокатки рельсов, балок, швеллеров, уголков и других профилей из блюмов и слябов.
- Сортные, служат для получения крупно-, средне- и мелкосортной стали. Заготовками для прокатки крупносортной стали являются блюмы и слябы, для прокатки средне- и мелкосортной стали – заготовки различных размеров.
- Проволочные, служат для прокатки проволоки –катанки диаметром 5-12 мм. Меньшие размеры получают волочением.
- Листопрокатные. Делятся на толстолистовые и тонколистовые. Толстые листы, толщиной более 4 мм, катают из слябов, тонкие 0,2-3,75 мм катают из сутунки.
- Трубопрокатные, служат для прокатки сварных и бесшовных труб.
- Колесо- и бандажепрокатные, служат для получения железнодорожных колес и бандажей.
По количеству валков в рабочей клети и их расположению станы бывают двухвалковые (дуо): нереверсивные и реверсивные; трехвалковые (трио), четырехвалковые (кварто), многовалковые и универсальные.
Волочение
Сущность волочения состоит в том, что заготовка (чаще всего в холодном состоянии) протягивается через отверстие в волоке (фильере), поперечное сечение которого меньше поперечного сечения заготовки.
Степень деформации

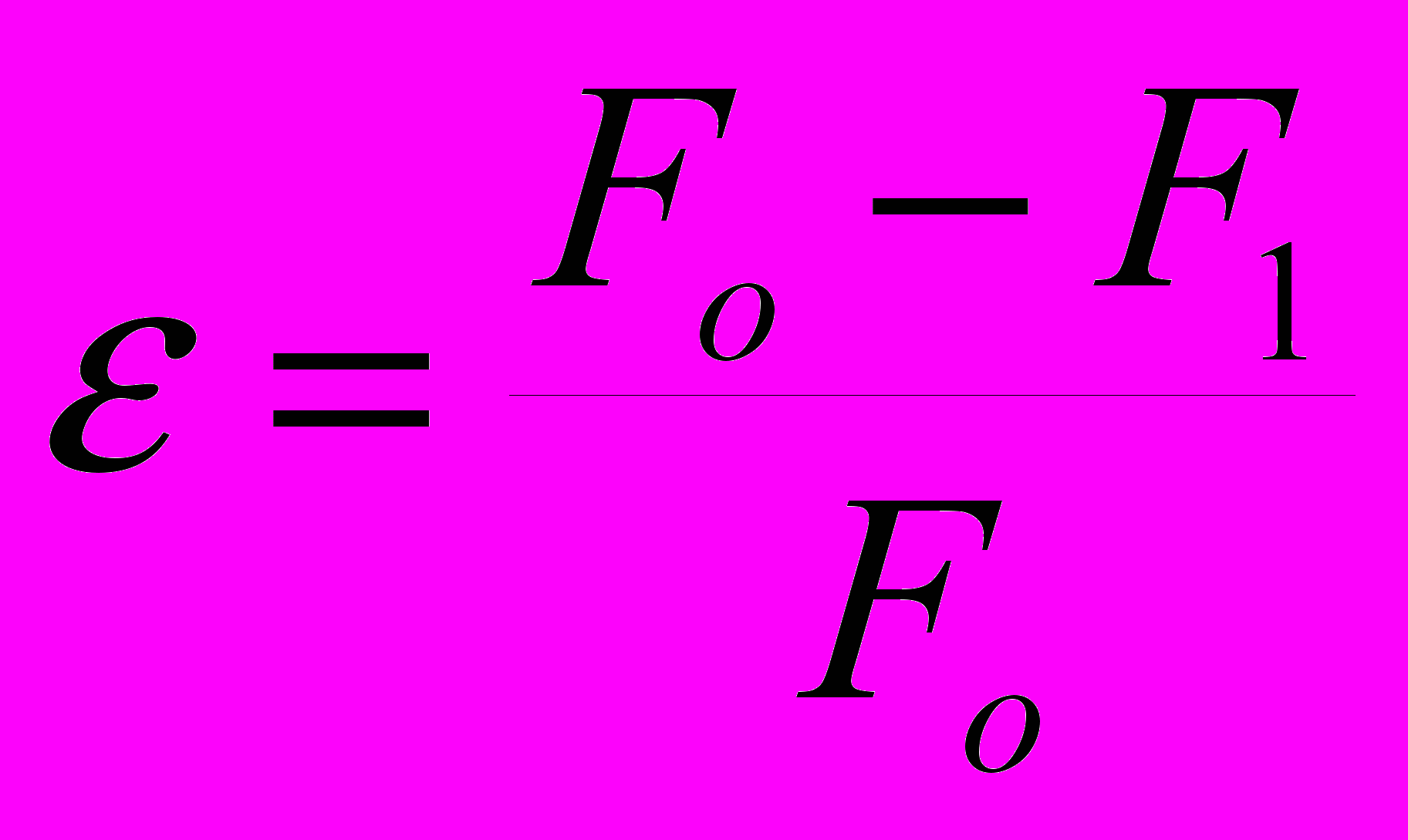
где:
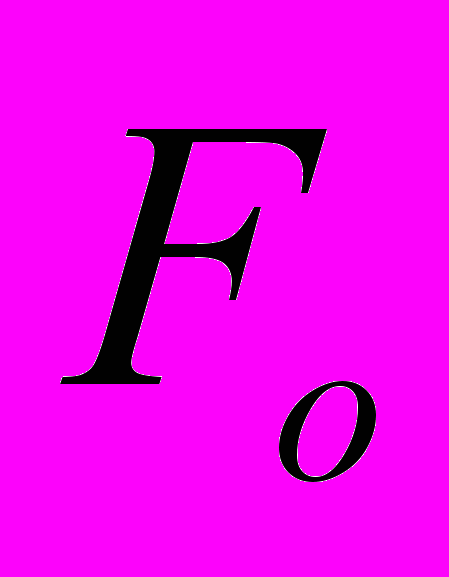
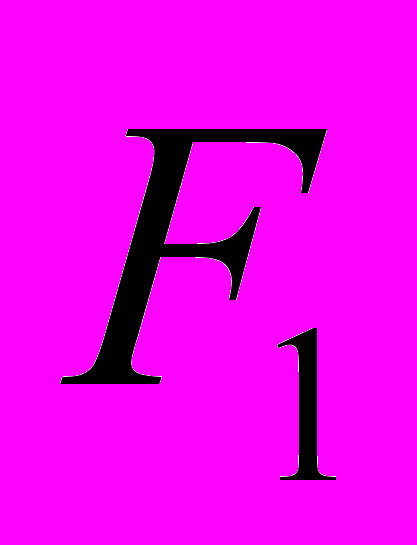
Волочение применяется:
- для изготовления тонкой проволоки, которую нельзя получить прокаткой
( диаметром 10…0,002 мм);
- для получения тонкостенных труб;
- для калибровки –придания точных размеров и высокого качества поверхности;
- для получения фасонных профилей.
Исходным материалом для волочения являются горячекатаный сортовой прокат (круглый, квадратный, шестигранный и др.), проволока, трубы из стали, цветных металлов и сплавов.
Перед волочением производится отжиг или нормализация для получения мелкозернистой структуры. Окалина, образующаяся в процессе горячей прокатки вызывает быстрый износ волочильного инструмента, поэтому для ее удаления применяется травление в 10–25% растворе серной кислоты. Затем металл подвергают промывке для того, чтобы снять травильный слой. После этого производят заострение концов под молотом или в ковочных вальцах и подают для волочения в волочильные станы. Так как после волочения образуется наклеп, то готовая продукция подвергается отжигу.
Инструментом для волочения является волока или фильер, рис.4. Состоит из обоймы 2, в которую вставлена волока 1. Волока имеет по длине четыре характерные зоны.
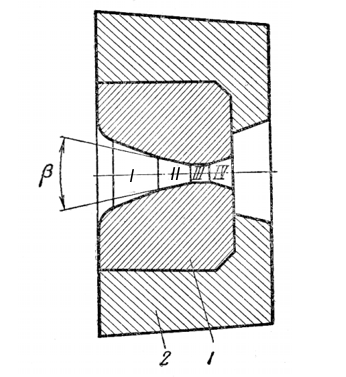
Рис. 4. Разрез волоки
I–входной или смазочный конус для введения заготовки в волоку с углом ~40о;
II–рабочий или деформирующий конус с углом 10-24о;
III–калибрующая часть (цилиндрической формы);
IV–выходной конус с углом 45-60о.
Волоки изготовляют из инструментальных сталей и твердых сплавов ВК6, ВК8. Для получения проволоки с диаметром менее 1,2 мм волоки изготовляют из алмаза.
Волоки с одним глазком называются фильером, с несколькими – волочильной доской.
Максимальное обжатие за одну протяжку ограничено. При этом напряжение волочения
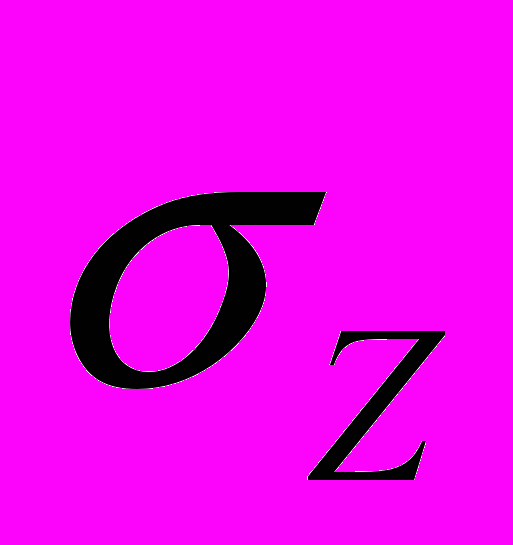
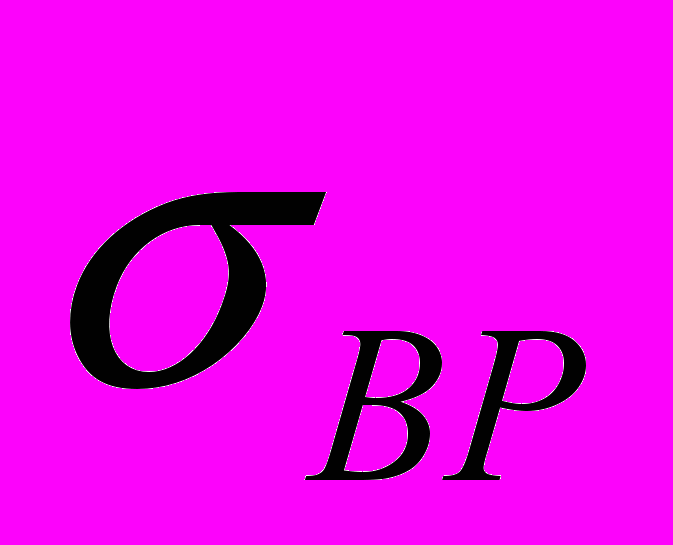
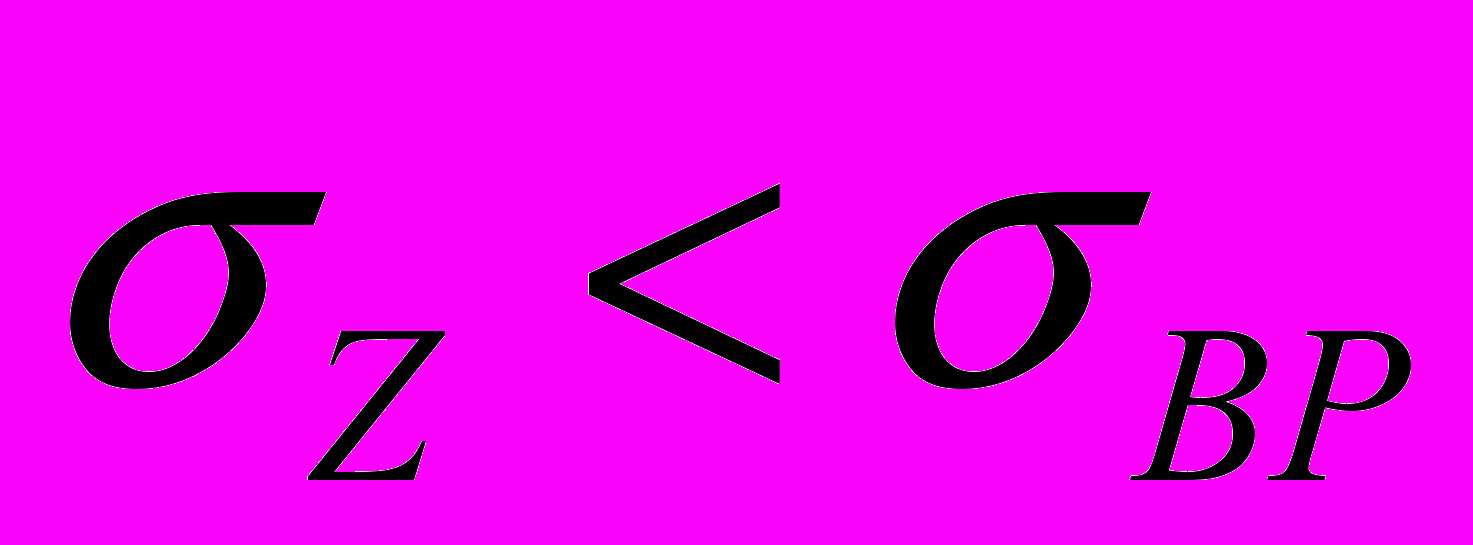
где:
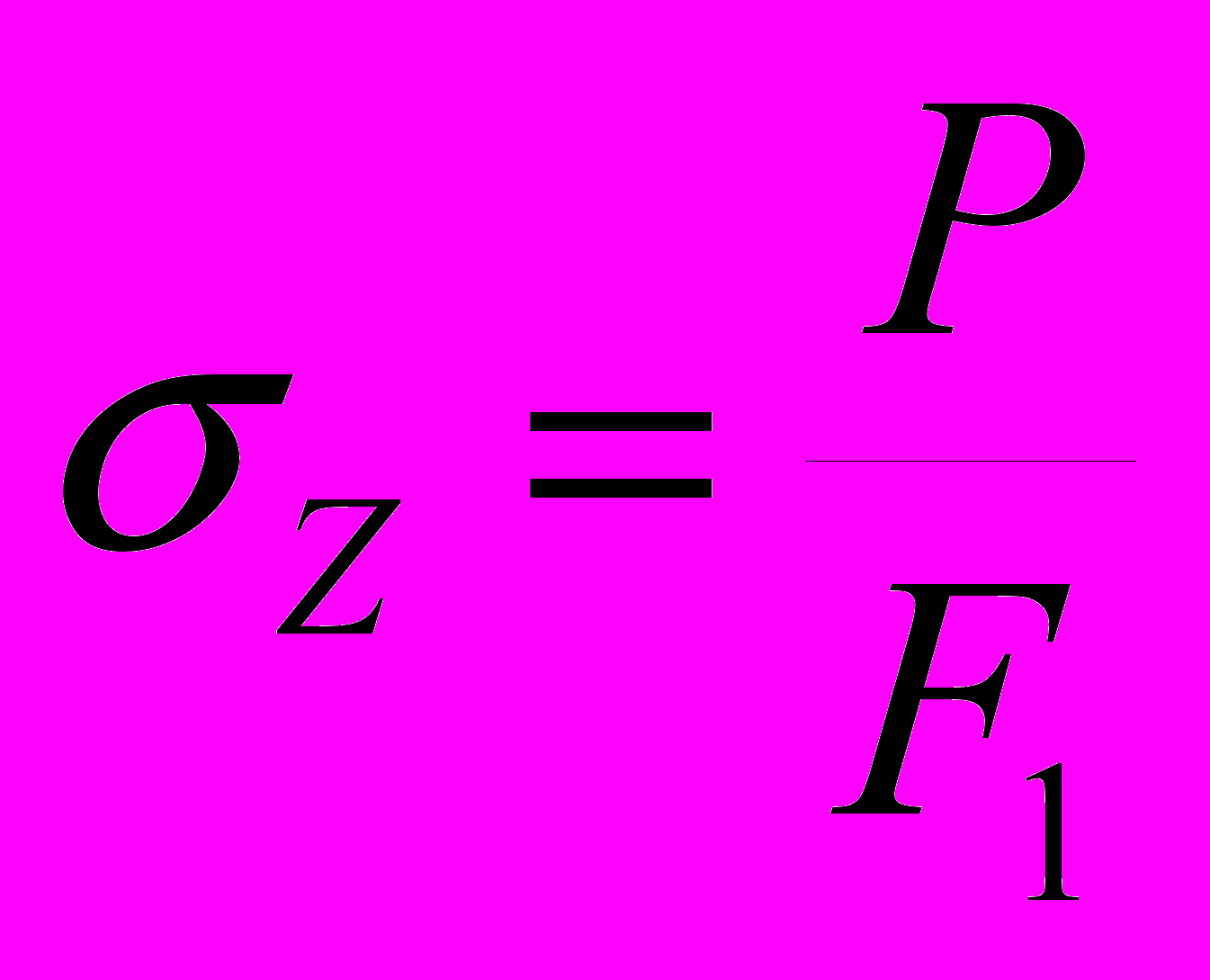
В качестве оборудования для волочения применяют волочильные станы, которые по принципу работы тянущих устройств делятся на две группы:
1) с прямолинейным движением тянущих устройств – цепные, реечные и др.
2) с наматыванием обрабатываемого металла на барабан – барабанные.
Барабанные волочильные станы делятся на станы однократного и многократного волочения, в которых заготовка последовательно проходит через несколько (до 20) волочильных матриц. Схема работы барабанного стана однократного волочения приведена на рис.5.
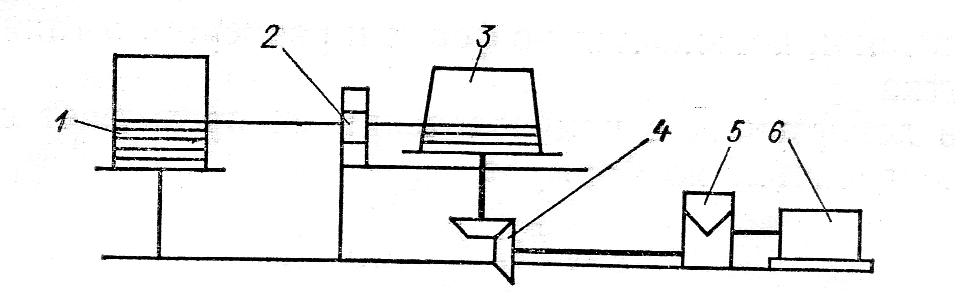
Рис. 5. Схема волочильного стана барабанного типа
В станах однократного волочения имеется вертушка 1 для установки бунта проволоки. Конец проволоки пропускают через волоку 2 и наматывают после закрепления на вращающийся барабан 3. Через коническую зубчатую передачу 4 и редуктор 5 барабан приводится во вращение от электродвигателя 6.
В станах многократного волочения зубчатые передачи подобраны так, что по мере волочения в связи с изменением сечения проволоки скорость вращения каждого последующего барабана возрастает. На станах барабанного типа протягивают проволоку диаметром 0,002–6 мм и прутки диаметром до 25 мм, сматываемые в бунты. Скорость волочения 6–3000м/мин, диаметр барабанов 150–1000 мм.
Для уменьшения потерь на трение применяются смазки жидкие и твердые. Твердой смазкой служит мыло, жидкой – смесь масла с графитом.
Готовая продукция подвергается контролю. Контролируется ее геометрия, химический состав, механические, технологические и физические свойства, структура и т.д. Трубы дополнительно подвергаются гидравлическим испытаниям.
Прессование
Прессованием называется процесс выдавливания металла заготовки из замкнутой полости инструмента-контейнера через отверстие матрицы с площадью меньшей, чем площадь поперечного сечения заготовки.
Прессованию подвергается главным образом цветные металлы и сплавы (олово, свинец, медь и ее сплавы), а в некоторых случаях сталь.
В качестве исходного материала служат слитки, а также предварительно деформированные кованые или катаные заготовки диаметром до 500 мм и более и длиной до 1200 мм. Черные металлы и сплавы прессуют в горячем состоянии, цветные – как в горячем так и в холодном. Нагрев осуществляется в газовых или электрических методических печах.
Применяются два метода прессования – прямой и обратный. При прямом методе прессования (рис.6) заготовку 1 укладывают в полость контейнера 2. Давление пресса передается на заготовку пуансоном 3 через пресс-шайбу 4. При этом металл вынужден выдавливаться через матрицу 5, укрепленную в матрице-держателе 6. Матрица и пуансон перед началом работы нагреваются до 200-300оС. Истечение металла происходит в направлении движения пуансона.
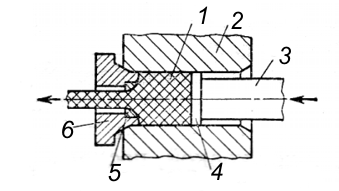
Рис.6. Прямой метод прессования
При обратном методе прессования (рис.7) контейнер 2 закрыт с одного конца упорной шайбой 7, а давление пресса передается через полый пуансон 3 с укрепленной на нем матрицей 5 на заготовку 1. Истечение металла из отверстия матрицы происходит в направлении обратном движению пуансона.
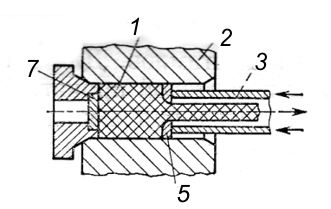
Рис.7. Обратный метод прессования
Обычно выдавить полностью из контейнера весь металл заготовки не удается. Часть металла, остающуюся в контейнере, называют пресс-остатком. Этот металл удаляется отрезкой. Отходы металла составляют: при прямом методе 12-15%, при обратном методе 5-6%.
При прямом методе прессования преодолевается трение металла о матрицу и стенки контейнера, при обратном методе трение возникает только при перемещении металла через матрицу.
Контейнер и матрица смазываются смесью машинного масла с графитом во избежание приваривания металла к стенкам. Часто в качестве смазки используют жидкое стекло.
Оборудованием для прессования служат гидравлические прессы усилием до 25 тысяч тонн. При прямом прессовании в силу вышеуказанных причин усилия затрачиваются больше, чес при обратном методе. Однако обратный метод прессования получил меньшее распространение ввиду сложности конструкции пуансона и пресса, меньшей производительности и более низкого качества поверхности.
После прессования изделия подвергают термообработке – отжигу, закалке, старению.
Степень деформации

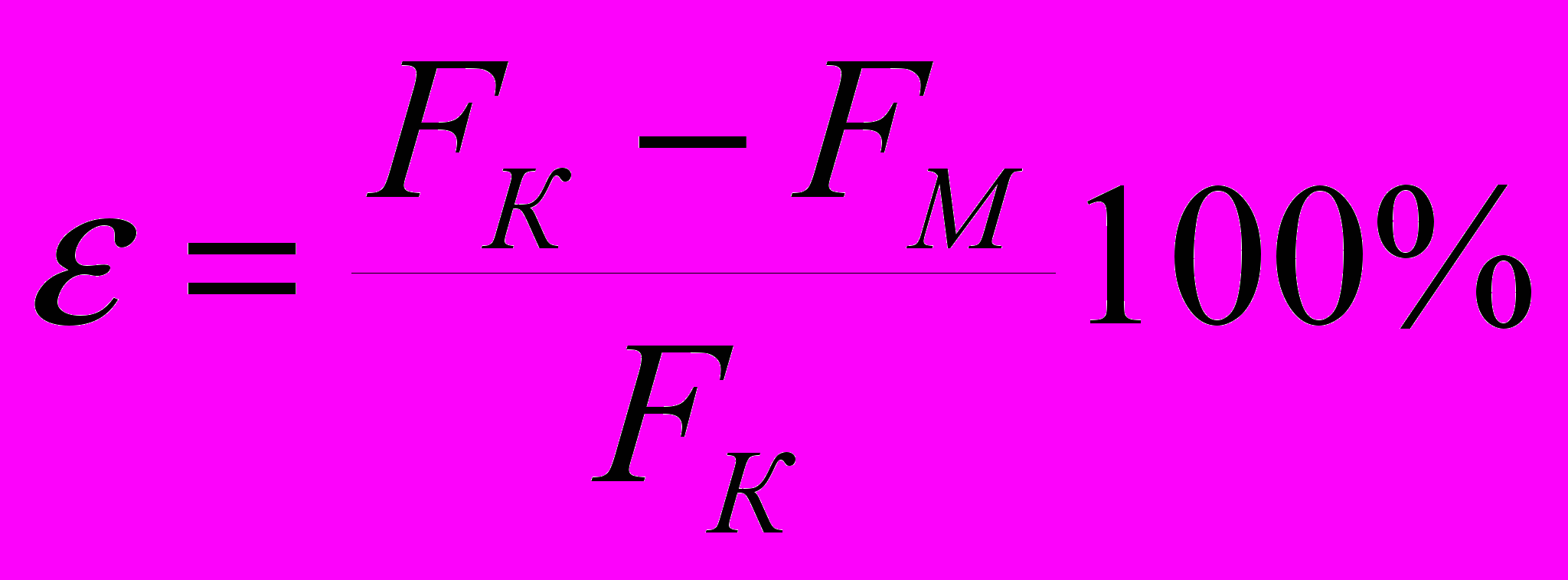
где:
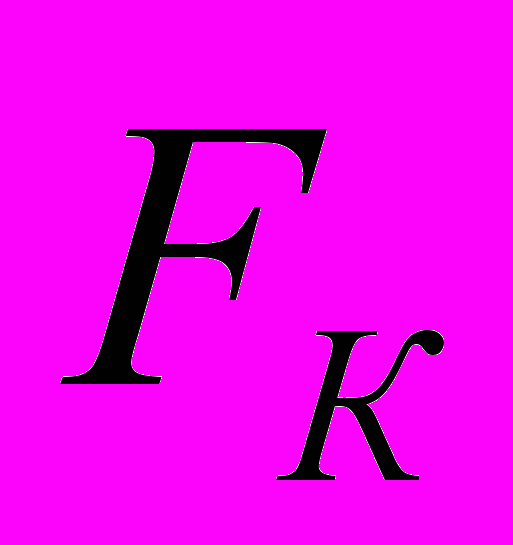
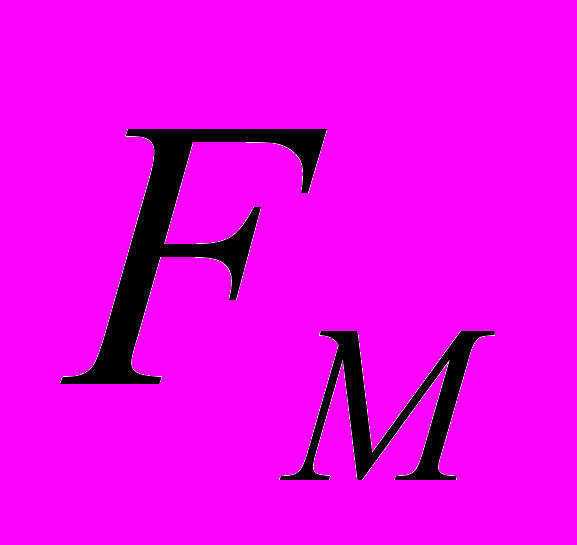
К положительным сторонам прессования относят: более высокую точность изготовления профилей по сравнению с прокаткой; высокую производительность; возможность получения сложных профилей. Недостатки: значительный износ инструмента; большие отходы металла (при производстве труб отходы составляют ~40%.
Инструмент изготавливают из высоколегированных сталей – 5ХНВ, 7Х3, 3Х2В8 и др.