Лекция 11. Ковка и горячая объемная штамповка. Ковкой
Вид материала | Лекция |
- Точная объемная штамповка изделий из алюминия и стали, главным образом при использовании, 210.17kb.
- Лекция 12. Холодная штамповка, 99.48kb.
- Художественная ковка металла становится все более модной и популярной, 61.01kb.
- Технологичность деталей машин, 94.77kb.
- «Социальная стратификация и социальная мобильность», 46.19kb.
- Холодная штамповка является одним из прогрессивных методов получения узлов и деталей, 263.85kb.
- Специальная ковка, 467.18kb.
- П. С. Мартышко, д-р физ мат наук, 80.13kb.
- Технологических сред (горячая и холодная вода, нефть, нефтепродукты и другие) по трубопроводным, 28.05kb.
- Горячая линия консультаций 955-999 Тел/факс: (8482) 70-10-02, 67-01-87 www infsystema, 71.58kb.
Лекция 11. Ковка и горячая объемная штамповка.
Ковкой называется процесс горячей обработки металлов давлением, при котором путем многократного действия инструмента, например, бойков металл пластически деформируется, постепенно приобретая заданные форму, размеры и свойства.
Изделие, получаемое ковкой, называют поковкой.
Существует два вида ковки: свободная и в штампах.
Свободной ковкой называется процесс, при котором формообразование поковок происходит под ударами молота или нажимом пресса. Течение металла в стороны свободное и не ограничено поверхностями инструмента.
Штамповкой называют ковку в стальных формах-штампах. Течение металла ограничивается поверхностями полостей, вырезанных в штампе.
1. Свободная ковка
Применяется в мелкосерийном и индивидуальных производствах, а также является единственным способом изготовления тяжелых поковок (весом 250 тонн и более) – валы гидрогенераторов, турбинные диски и т.д.
Исходным материалом для ковки служат слитки, блюмы и сортовой прокат. Свободная ковка может быть ручная и машинная. Ручная ковка применяется для небольших поковок при мелких ремонтных работах и выполняется с помощью наковальни и кувалды.
Машинная ковка производится на молотах и прессах.
Операции свободной ковки
1) Осадка – уменьшение высоты заготовки за счет увеличения площади поперечного сечения.
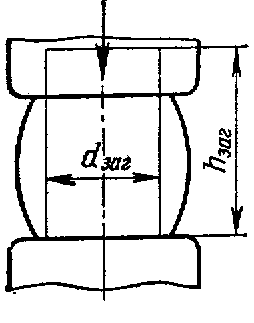
Во избежание продольного изгиба отношение высоты осаживаемой заготовки к ее диаметру должно составлять не более 2,5. Вследствие действия сил трения по контактным поверхностям боковая поверхность заготовки приобретает бочкообразную форму.
2) Высадка – осадка на части высоты заготовки. Осуществляется нагревом определенной части заготовки или ограничением деформации кольцевым инструментом.

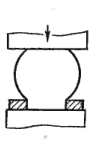
Осадка применяется:
- для получения поковок с большими поперечными сечениями при относительно малой толщине (зубчатые колеса, диски);
- как предварительная операция перед прошивкой при изготовлении пустотелых поковок (колец, барабанов);
- как предварительная операция для уничтожения литой дендритной структуры слитка и улучшения механических свойств.
Деформация при осадке выражается величиной уковки
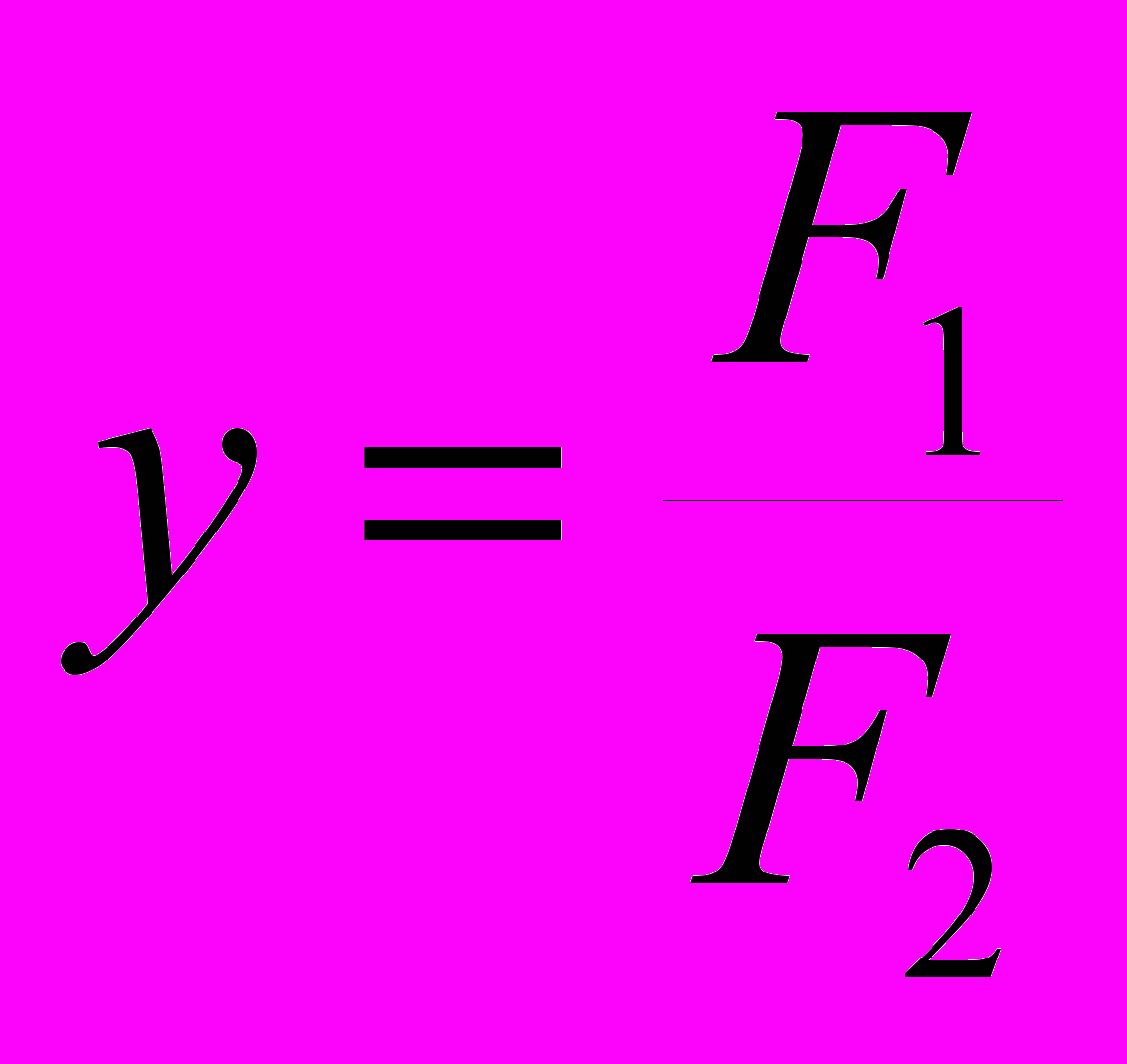
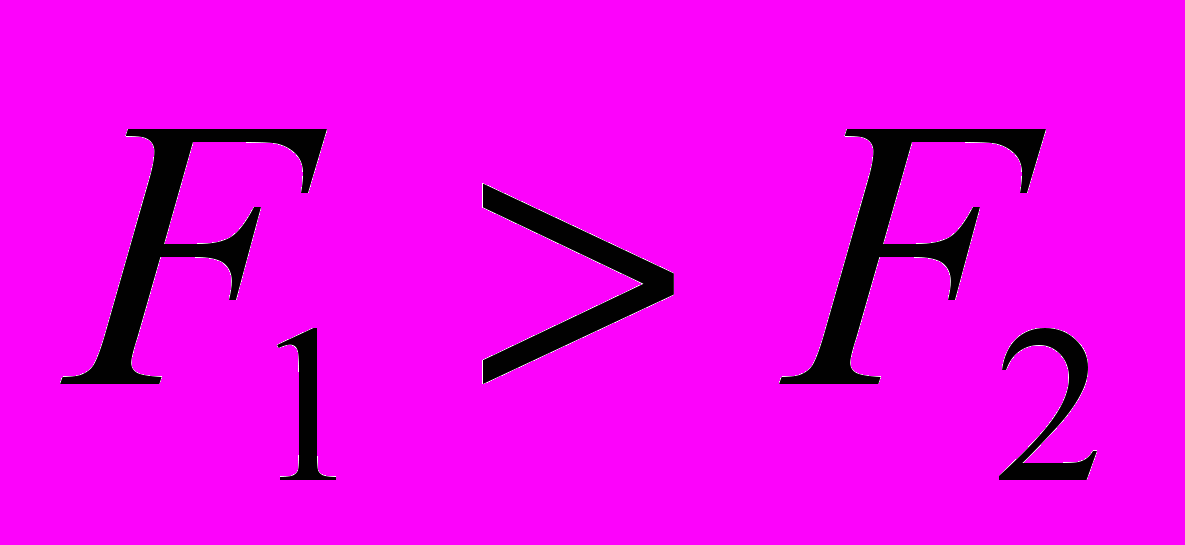
где F1– площадь поперечного сечения заготовки после осадки;
F2 – площадь поперечного сечения заготовки до осадки.
3) Протяжка – увеличение длины заготовки за счет уменьшения ее поперечного сечения. Протяжку производят последовательными ударами или нажатиями на отдельные прилегающие друг к другу участки заготовки с подачей заготовки вдоль оси и поворотами ее на 90о вокруг этой оси. Протяжку можно выполнять плоскими и фигурными бойками.
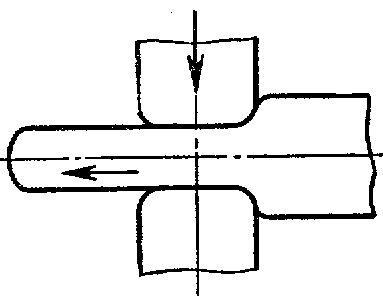
Деформация при протяжке выражается величиной уковки
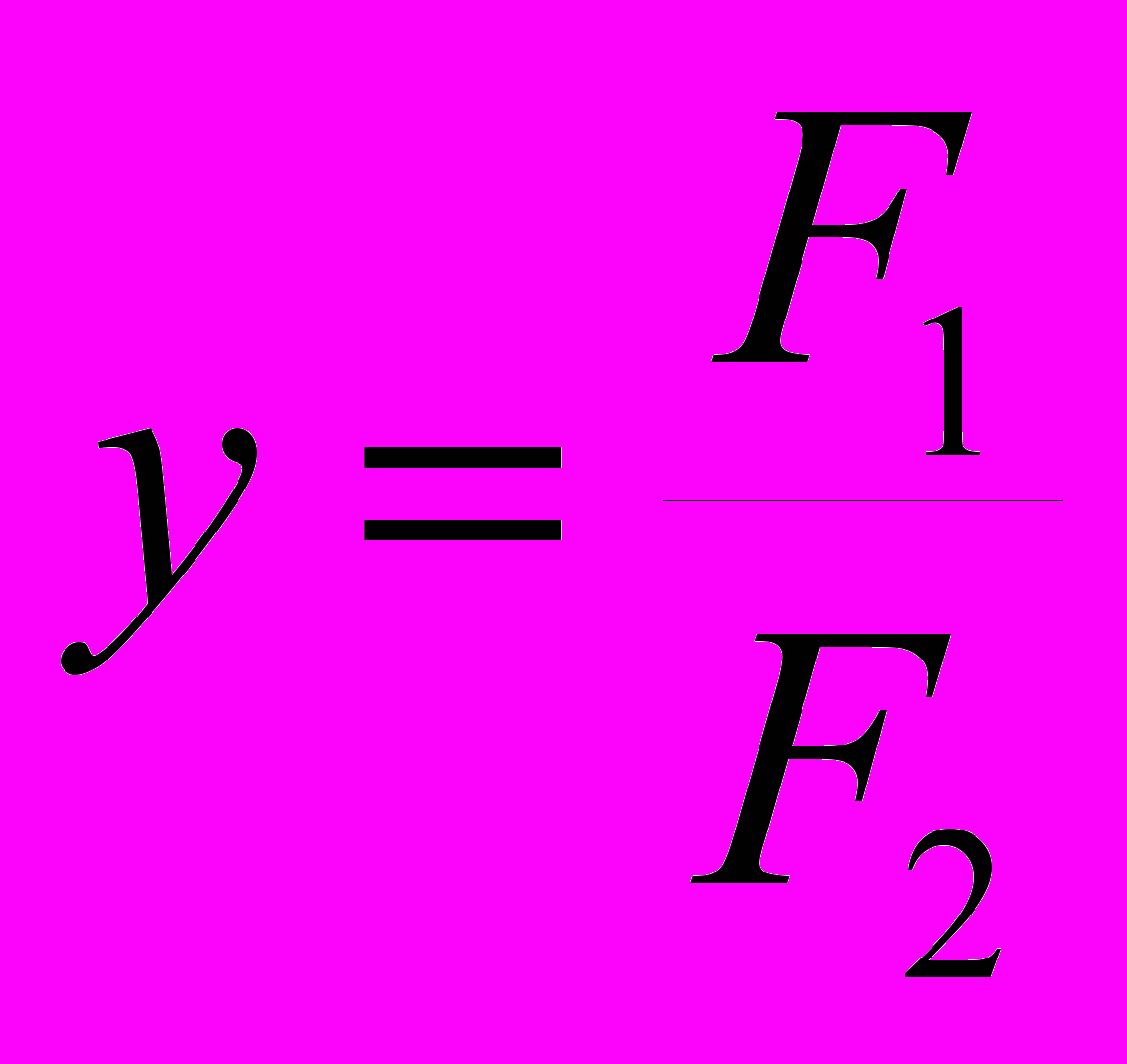
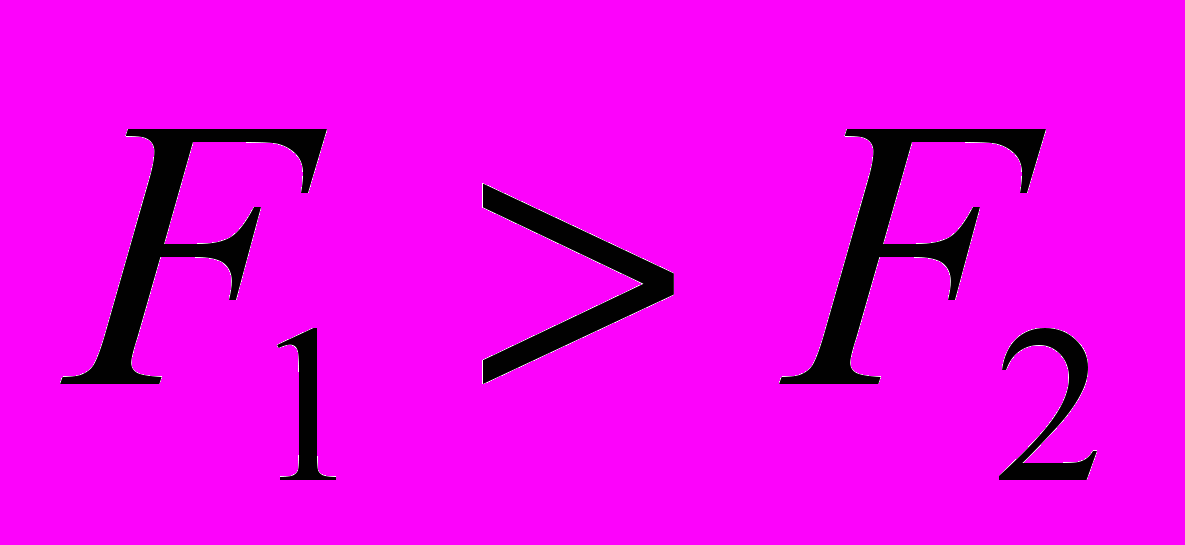
где F1– площадь поперечного сечения заготовки до протяжки;
F2 – площадь поперечного сечения заготовки после протяжки.
Чем больше уковка, тем лучше прокован металл, тем выше его механические свойства. Поэтому часто протяжку применяют в чередовании с осадкой для большей уковки металла заготовки.
Протяжкой получают поковки с удлиненной осью (валы, оси, тяги и т.п.).
4) Раскатка на оправке – увеличение диаметра кольцевой заготовки 1 при вращении за счет уменьшения ее толщины с помощью бойка 3 и оправки 2. Оправка устанавливается в люнете 4.
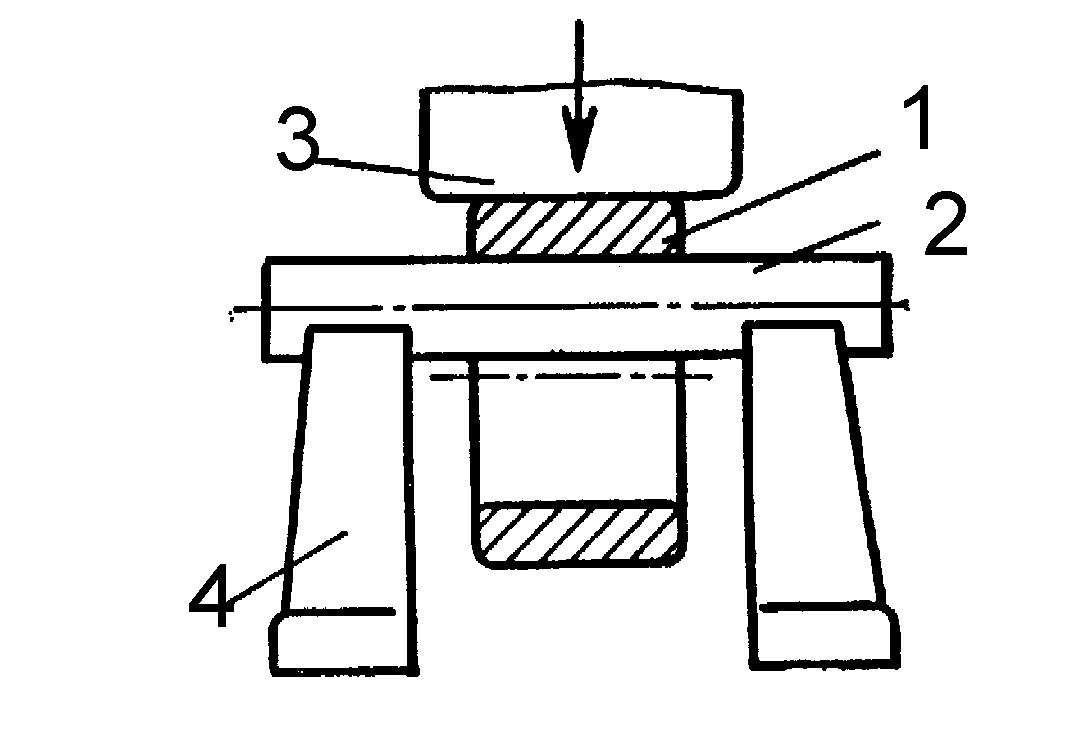
5) Протяжка с оправкой – операция увеличения длины пустотелой заготовки за счет уменьшения толщины ее стенок. Протягивают в одном направлении–к расширяющему концу оправки 1, что облегчает ее удаление из поковки.
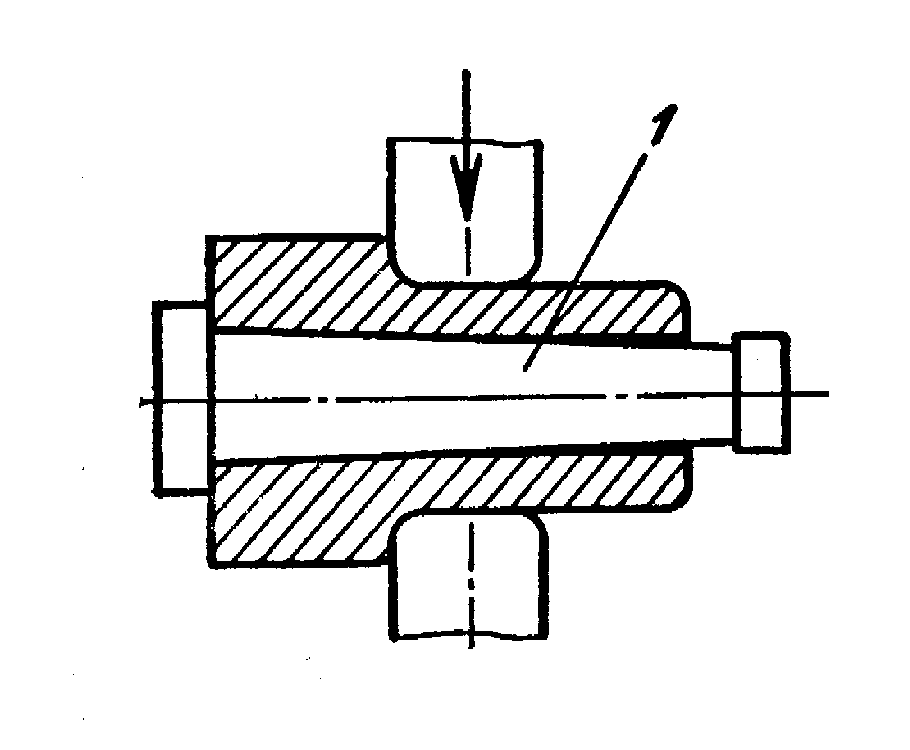
6) Прошивка – получение сквозного или глухого отверстия в заготовке. Для выполнения этой операции применяют сплошные или пустотелые прошивни. Часть металла, удаляемая в отход вместе с прошивнем, называют выдрой.
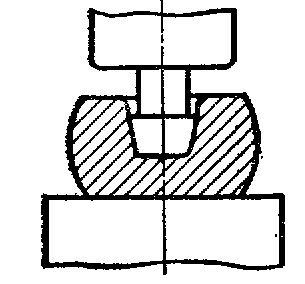
7) Разгонка – операция увеличения ширины части заготовки за счет уменьшения ее толщины.
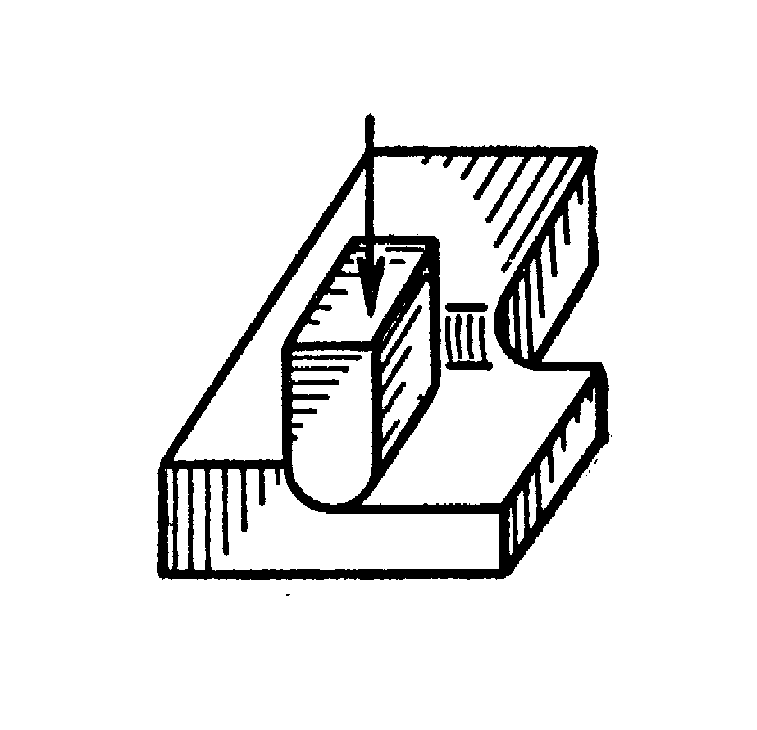
7) Гибка – образование или изменение углов между частями заготовки или придание ей криволинейной формы. Применяется для изготовления крюков, коленчатых валов, скоб и т.д.
8) Закручивание – поворот части заготовки относительно другой на заданный угол. Применяется при изготовлении коленчатых валов, сверл и т.п. При закручивании используют воротки, лебедки, ключи.
9) Рубка – полное отделение части заготовки по незамкнутому контуру. Инструментом служат топоры.

Оборудование для свободной ковки
Машинная ковка производится на ковочных молотах и ковочных гидравлических прессах.
Молоты действуют ударом и характеризуются весом падающих частей. Продолжительность деформации при ковке на молотах порядка 10-3сек, а скорость деформации (6–6,5) м/сек.
Гидравлические прессы развивают статическое усилие и характеризуются усилием в тоннах. Продолжительность деформации доходит до десятков секунд, а скорость деформации составляет 2–3 м/мин.
Для ковки мелких поковок массой до 20 кг используются пневматические ковочные молоты. Для поковок средней массы до 2000 кг – паровоздушные ковочные молоты. На молоте верхний боек крепится к падающей части молота – бабе, а нижний боек – к подушке, закрепленной на шаботе, не связанном со станиной молота. Масса шабота превышает массу падающих частей в 10–15 раз. Масса падающих частей молота составляет 50–1000 кг (для пневматического молота) и 1000–8000 кг для паровоздушного).
Для производства крупных поковок применяют гидравлические прессы. Они развивают усилие до 20000 тонн.
2. Горячая объемная штамповка (ГОШ)
Горячая объемная штамповка – это процесс изготовления поковок в штампах.
По сравнению со свободной ковкой штамповка имеет следующие преимущества:
- в 50–100 раз большая производительность;
- большая однородность и точность поковок (припуски и допуски на поковку в 3–4 раза меньше, чем при ковке);
- возможность получения поковок сложной формы, которые нельзя получить свободной ковкой.
Однако штамповке свойственны и некоторые недостатки:
- ограниченность штампуемых изделий по весу – до 200 кг (иногда до 1500 кг);
- каждая поковка требует свой штамп, а это сложный в изготовлении и дорогой инструмент
Штамповку целесообразно применять в крупносерийном и массовом производстве.
Инструмент для ГОШ
Полость штампа, которую заполняет металл при штамповке, называют ручьем. Различают штамповку в открытых и в закрытых штампах.
В открытых штампах между подвижной и неподвижной частями штампа имеется зазор – заусеночная (или облойная) канавка, в которую вытекает избыточный объем металла при штамповке. Образующийся при этом облой или заусенец затем обрезается на специальных обрезных штампах.
Заусеночная канавка имеет следующее назначение:
- в нее вытекает избыточный объем металла;
- при соударении верхней и нижней половин штампа заусенец предохраняет штамп от жесткого удара, что способствует продлению срока службы штампа;
- быстрое остывание заусенца создает в конце штамповки большое сопротивление течению металла, что способствует лучшему заполнению ручья штампа.
Для штамповки в открытых штампах характерны следующие особенности:
- объем металла заготовки, находящийся в ручье, не постоянен, часть металла вытекает в заусенец, поэтому к точности заготовки по объему высоких требований не предъявляется;
- по месту обрезки заусенца у поковки волокна металла оказываются перерезанными;
- в открытых штампах делаются специальные штамповочные уклоны в ручьях для облегчения извлечения готовой поковки (3–10о).
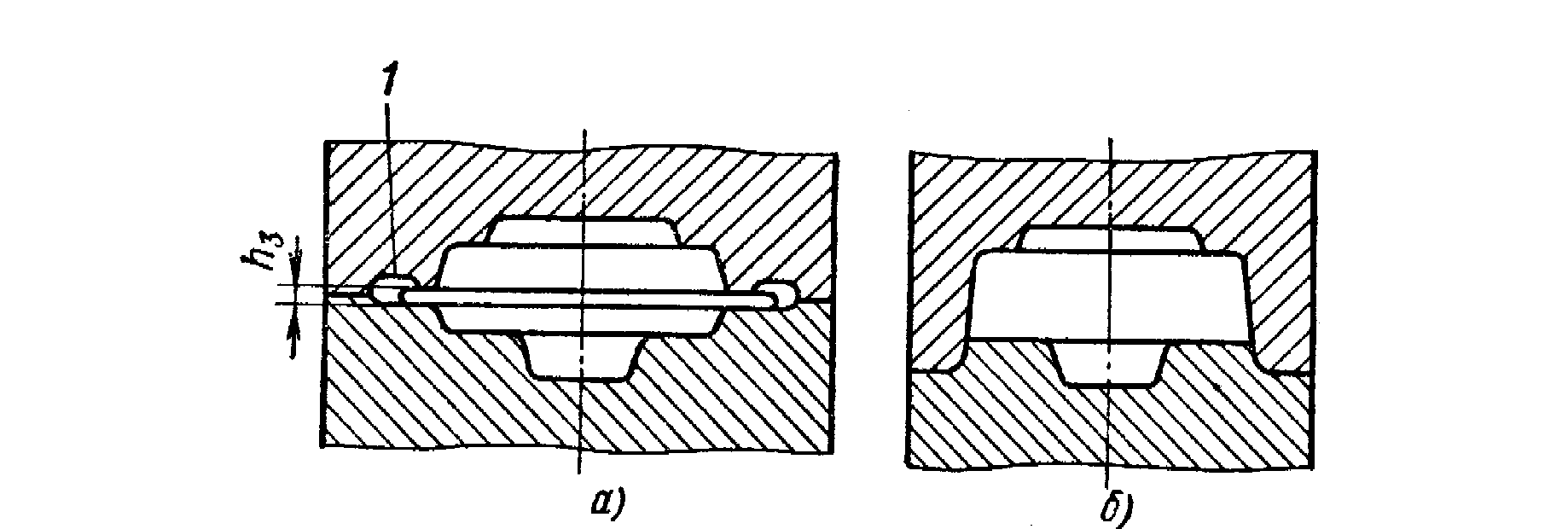
Рис. Схемы штамповки в открытых и закрытых штампах: 1 – облойная канавка
В закрытых штампах деформирование металла протекает в закрытой полости.
Для штамповки в закрытых штампах характерны следующие особенности:
- штамповка происходит без образования заусенца, и в этом случае расход металла меньше, но предъявляются повышенные требования к точности объема заготовки.
- макроструктура поковок весьма благоприятна, так как волокна обтекают контур и нигде не перерезаются после штамповки;
- при штамповке без облоя нужны специальные выталкивающие устройства для извлечения поковки из штампа.
В зависимости от сложности конфигурации поковки для ее изготовления применяют либо одноручьевую штамповку, выполняемую в штампе с одним ручьем, либо многоручьевую штамповку, выполняемую последовательно в штампе, имеющем несколько ручьев. Обработку заготовок в одном ручье штампа называют переходом. Чем сложнее поковка по форме, тем большее число переходов требуется для ее получения.
Ручьи в штампах разделяются на заготовительные и штамповочные. Заготовительные предназначены для перераспределения металла заготовки с целью приближения ее формы к форме поковки. В заготовительных ручьях производят: осадку, протяжку, формовку, подкатку, пережим, гибку, отрубку.
Ручьи для получения окончательно оформленной поковки называют штамповочными. Штамповочных ручьев два: черновой или предварительный и чистовой или окончательный. Черновой ручей служит главным образом для повышения стойкости чистового ручья. Чистовой ручей является точной копией поковки, но с размерами, большими на величину усадки металла при охлаждении (около 1,5%). По периметру чистового ручья располагается облойная канавка. Черновой ручей облойной канавки не имеет. Поскольку штамповка в окончательном ручье требует наибольшего усилия, чем в остальных ручьях, его располагают обычно в центре штампа с целью предохранения от поломки самого штампа и оборудования, на котором он установлен.
В качестве заготовок для штамповки используют сортовой и периодический прокат, заготовки, подготовленные ковкой.
ГОШ осуществляется на штамповочных молотах, кривошипных горячее-штамповочных прессах, горизонтально-ковочных машинах и т.д.
Штамповка на горизонтально-ковочных машинах (ГКМ)
ГКМ предназначены для штамповки поковок типа стержней с утолщениями на концах (болтов, заклепок, винтов, и т.д.), втулок, колец. Преимуществами штамповки являются:
высокая производительность ( сотни деталей в час),
возможность штамповки без заусенца и штамповочных уклонов,
получение поковок типа колец без отхода металла на образование отверстия.
Применяются многоручьевые закрытые штампы, состоящие из пуансона и разъемных матриц. Схема штамповки изделия представлена на рис.
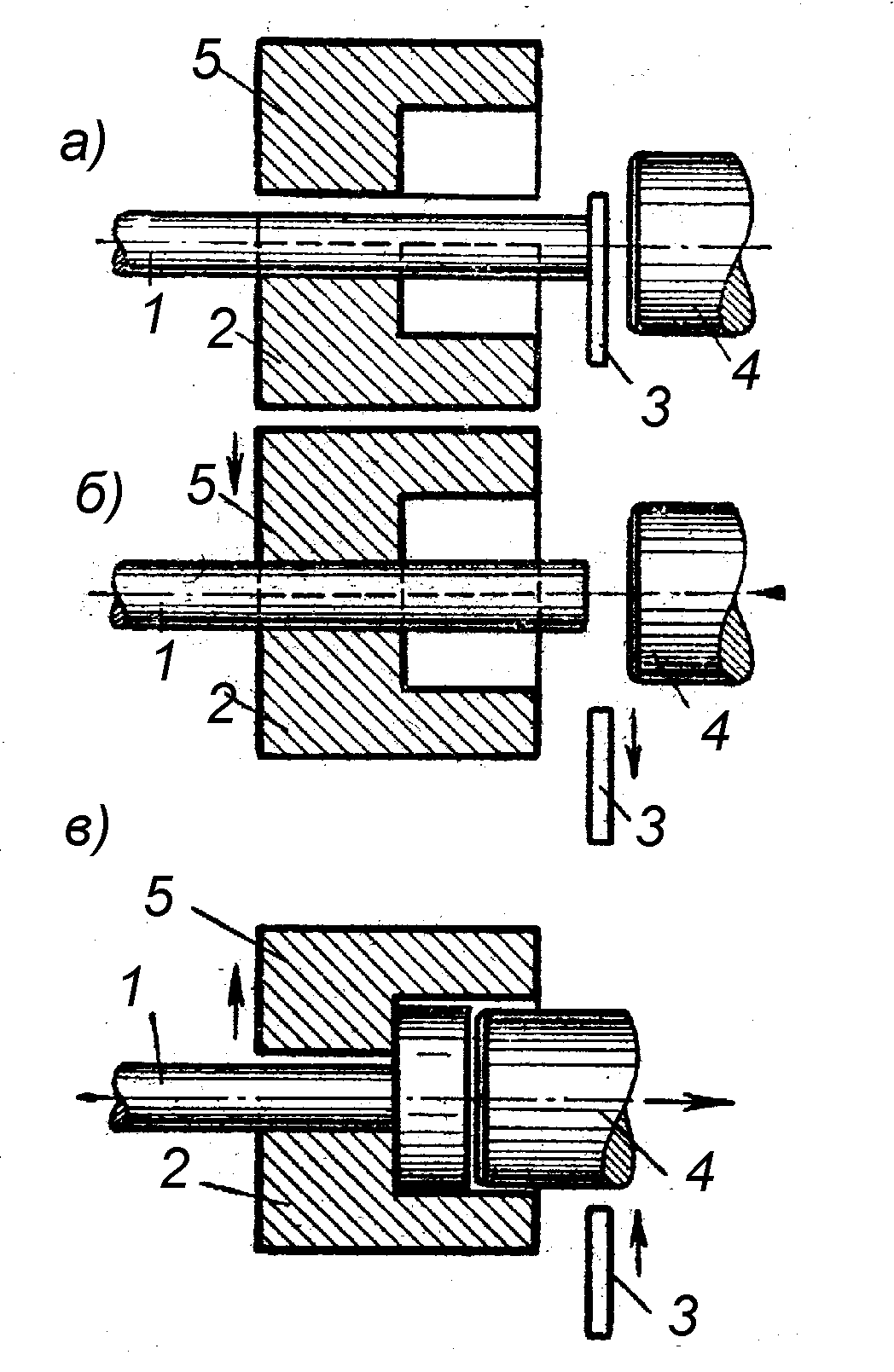
Пруток 1 нагретым концом укладывается в неподвижную половину 2 матрицы до упора 3. Пуансон 4 в это время находится в крайнем правом положении.
Далее подвижная часть 5 матрицы зажимает пруток, образуя полость для деформирования выступающей части прутка. При этом упор 3 автоматически переходит в другое положение. А пуансон 4 начинает движение в направлении стрелки.
Пуансон деформирует конец прутка до тех пор, пока не образуется готовая поковка. После этого подвижная часть матрицы и пуансон отходят в первоначальное положение, а пруток с поковкой переносятся в следующий ручей, где их отделяют друг от друга.
Рис. Схема штамповки на ГКМ
Технологический процесс ковки
Технологический процесс ковки представляет собой совокупность операций, связанных с изменением формы исходной заготовки до получения поковки.
1. Составление чертежа поковки
Разрабатывается на основе чертежа изделия с учетом припусков, допусков и напусков.
Припуск – поверхностный слой металла в поковке, подлежащий удалению при механической обработке для получения требуемых размеров и качества поверхности готовой детали.
Чем больше размеры поковки, тем больше припуск.
Допуск – разность между наибольшим и наименьшим предельными размерами поковки.
Допуск назначают на все размеры поковки.
Напуск – местное увеличение припуска для упрощения формы поковки с целью облегчения ковки ( отверстия малого диаметра, шпоночные и шлицевые пазы, малый перепад ступеней вала и др.).
2.Выбор заготовки
По размерам поковки подсчитывают ее объем и массу. В зависимости от массы поковки выбирают вид заготовки – слиток или прокат. Массу слитка вычисляют по формуле

Где: МПОК – масса поковки,
МПР – масса прибыльной части слитка (14-30%),
МДОН – масса донной части слитка (4-7%),
МУГ – масса металла на угар (2,5%),
МТЕХН – масса технологических отходов, зависит от формы поковки и последовательности ковки.
При расчете массы заготовки из проката можно пользоваться приведенной формулой, исключив из нее массы прибыльной и донной части слитка.
Назначив величину укова
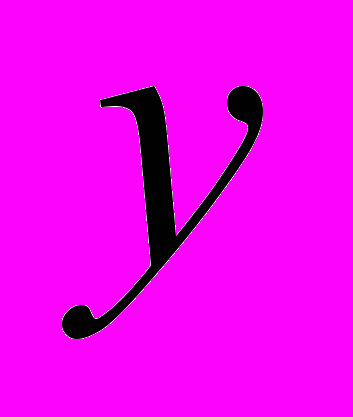
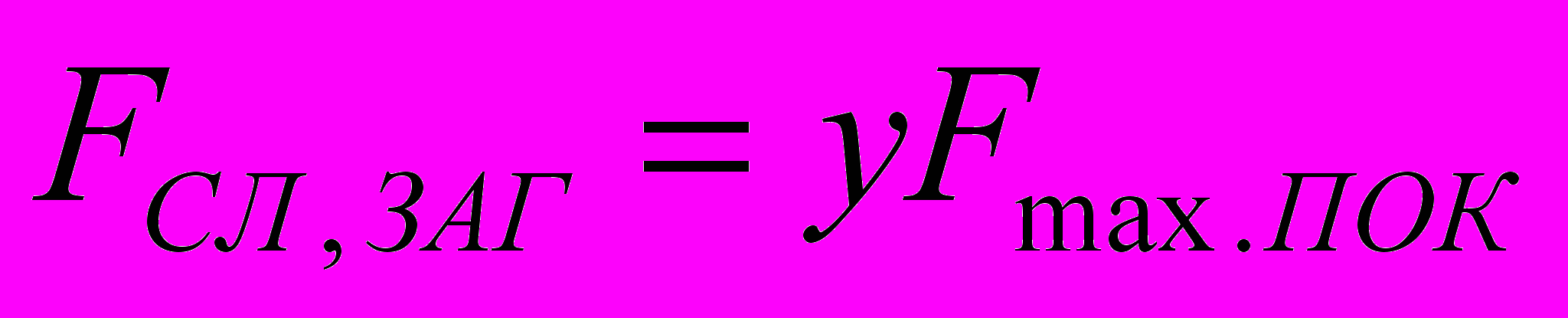
где: у – коэффициент укова (у
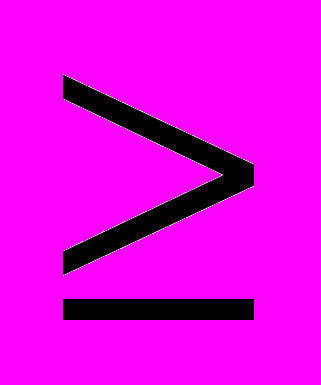
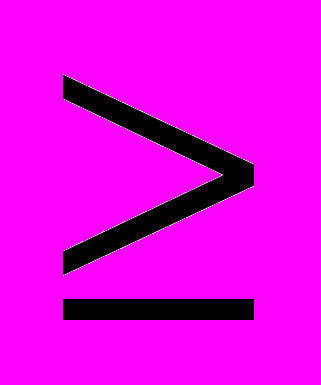
Fmax. ПОК – площадь максимального поперечного сечения поковки.
3. Отрезка мерной заготовки
Основными способами резки являются:
- резка на кривошипных пресс-ножницах
- ломка на хладноломах
- резка механическими пилами
- газовая резка и др.
4. Нагрев заготовок
Проводится с целью повышения пластичности металла.
5. Ковка или штамповка
6. Обрезка заусенцев и прошивка сквозных отверстий
Проводится после штамповки в открытых штампах. Операции выполняются на обрезных кривошипных прессах.
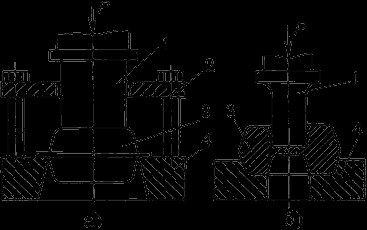
Рис. Схема обрезки заусенца и пробивки пленки
При нажатии пуансоном 1 на поковку 3 режущие кромки матрицы 4 срезают заусенец по всему периметру поковки, и она проваливается в тару. Заусенец снимается с пуансона при его ходе вверх съемником 2 и удаляется в другую тару.
При пробивке перемычек (пленок) для получения сквозных отверстий в поковках поковку 3 укладывают в матрицу 4 и с помощью пуансона 1 пробивают. Отход проваливается в отверстие матрицы и собирается в тару.
В штампах совмещенного действия обе эти операции выполняются на один ход.
7. Термообработка
Проводится отжиг или нормализация для снятия внутренних напряжений.
8. Очистка от окалины
Производят во вращающихся галтовочных барабанах (окалина удаляется посредством ударов поковок друг о друга и о металлические звездочки, закладываемые в барабан); дробеструйная очистка (поковки перемещаются на ленте транспортера, и окалина сбивается потоком быстро летящей дроби диаметром 1–2 мм); травлением в 15–18% растворе серной кислоты, нагретой до 60оС.
9. Калибровка поковок
Производится для повышения точности размеров поковок и улучшения качества их поверхностей. Различают плоскостную и объемную калибровку (чеканку). Выполняется в холодном и нагретом состоянии.
П
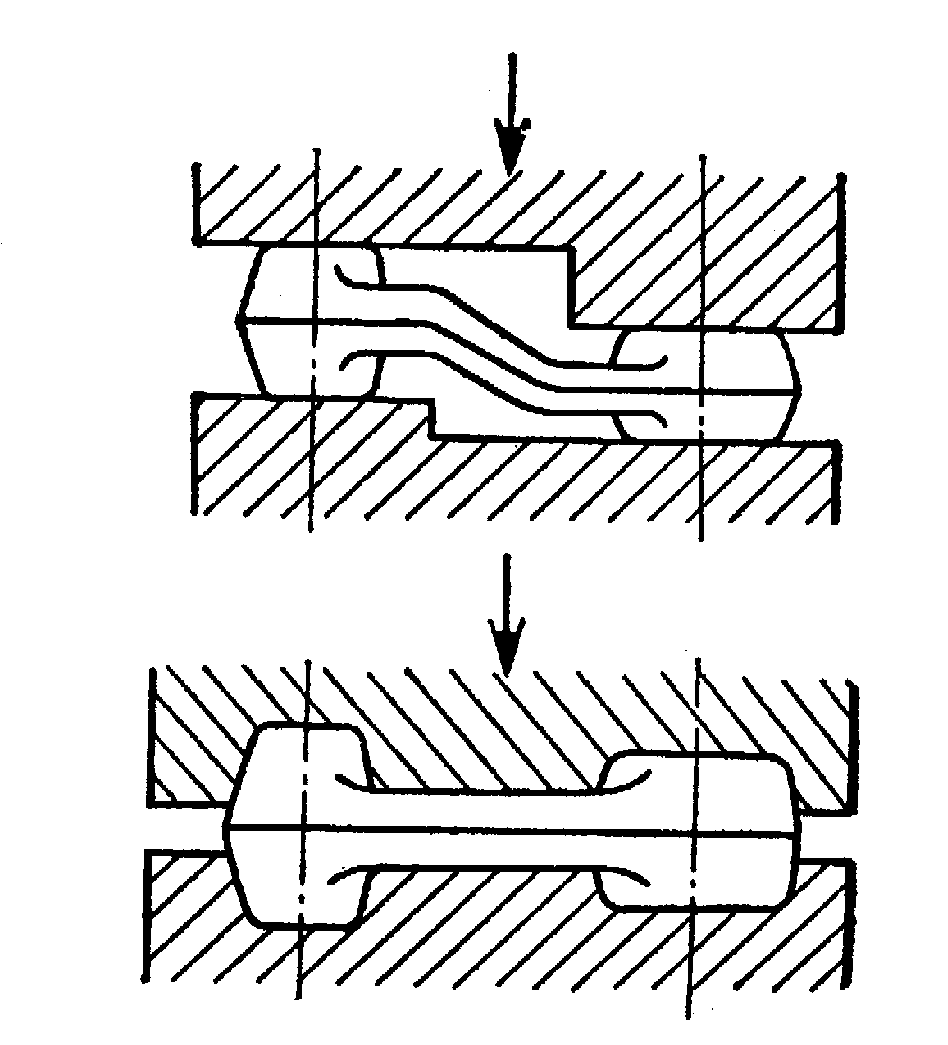
При объемной калибровке боковые стенки ручья затрудняют течение металла в горизонтальном направлении. При этом возможно образование заусенца. Объемная калибровка (с подогревом до 850–900оС) по существу является доштамповкой поковки до нужных размеров и осуществляется на кривошипных горяче-штамповочных прессах в одноручьевом ручье с последующей обрезкой облоя.
Точность размеров после калибровки составляет 0,05–0,25 мм, поэтому последующую обработку резанием исключают или ограничивают только шлифованием.
10. Контроль поковок
Несколько поковок из партии проверяются на соответствие размерам по чертежу и делается их внешний осмотр. А отдельные экземпляры из партии подвергаются полному металлографическому исследованию.