Советник раасн, профессор каф. Строительного материаловедения и специальных технологий д т. н. Акулова М. В
Вид материала | Документы |
- Разработчики программы повышения квалификации: Галимов Энгель Рафикович, д т. н., профессор,, 226.46kb.
- Региональное Отделение Российского Философского Общества Саратовский государственный, 223.62kb.
- Разработчики программы повышения квалификации: Алиева Б. Ш. д пед н., профессор, каф, 274.72kb.
- Концепция устойчивого развития в стратегии градостроительства франции 05. 23. 22 Градостроительство,, 332.07kb.
- Десятые академические чтения раасн, 2006, 1519.63kb.
- Заровняев Борис Николаевич, д т. н., профессор, зав. Каф. Огр открытых горных работ, 204.45kb.
- Лечение недержания мочи у мужчин о. Б. Лоран, член корр. Рамн, профессор, зав каф урологии, 39.64kb.
- Племяшов К. В., зав кафедрой акушерства, к в. н., Андреев Г. М., профессор каф акушерства,, 51.58kb.
- Кязимов Карл Гасанович Доктор педагогических наук, профессор ргсу, Государственный, 88.92kb.
- Программа для поступающих на Направления подготовки бакалавров 150700 «Машиностроение», 505.68kb.
Стеклянное волокно для теплоизоляции применяют в виде изделий следующих видов: гибкие – маты штучные или в рулонах, шнуры или жгуты; полужесткие – плиты, полуцилиндры, сегменты; жесткие – плиты.
Гибкие изделия. Маты выпускаются как со связующим так и без него. Их прошивают или формуют на металлической сетке. В матах с короткими волокнами используются связующие – фенолформальдегидные или карбамидные смолы. Пропитка происходит в камере волокноосаждения. Шнуры имеют оплетку из металлической проволоки или стеклянной нити.
Полужесткие изделия изготавливают с применением синтетических связующих. При получении жестких плит из супертонкого волокна применяют отливку из суспензии. В других случаях связующее вводят методом пролива с вакуумированием.
Обкладочными материалами при производстве матов и полос могут также служить: битуминизированная бумага, асбестовый картон, бумага или ткань, стеклоткань различных марок или стеклосетка марок ССА и ССТЭ.
Области применения стеклянной ваты.
По сравнению с минераловатными изделиями изделия из стекловолокна характеризуются лучшими свойствами, однако стоимость их выше, поэтому объем их производства значительно меньше минераловатных
В настоящее время стеклянную вату и изделия из нее выпускают более 3 млн.м³/год, увеличение выпуска предусматривается небольшое. В общем балансе теплоизоляционных материалов на долю стекловолокна приходится около 10%.
Как отличный звуко- и теплоизоляционный материал, отвечающий требованиям санитарной техники, стекловату широко применяют для изоляции внутренних перегородок и стен.
Благодаря вибростойкости она может служить для тепловой изоляции трубопроводов, подверженных сотрясениям и вибрации, а также подвижного состава железных дорог, в авиастроении, автомобилестроении, холодильных установках и др. сооружениях.
Широкое применение стекловолокно находит в судостроении вследствие их небольшой массы, устойчивости к действию соленой воды, способности выдерживать вибрацию без усадки, отсутствия водопоглощения и высокой химической стойкости. Стекловолокно не содержит и не выделяет корродирующих металл веществ.
Изделия на основе вспучивающихся горных пород и минералов
Общие сведения
Вспучивающиеся горные породы и минералы используются как эффективный теплоизоляционный материал. Способность пород и минералов вспучиваться при высоких температурах объясняется тем, что порода при этом размягчается, а содержащаяся в ней в растворенном состоянии вода переходит в пар, который и вспучивает размягченную массу. Важнейшим представителем горных пород является вспучивающийся перлит, а минералов – вспучивающийся вермикулит.
Вспученный перлит
Вспученный перлит получают из водосодержащих горных пород вулканического происхождения стекловидной структуры, называемых вулканических стекол. Они образовались в результате выноса из недр земли природного кислого силикатного магматического расплава, который изливается на поверхность в виде лавы.
Вулканические стекла в зависимости от содержания в них воды разделяются на обсиданы (до 1% воды), перлиты (1-6%), пехштейны, виброфиры и др. (более 6%). В производстве вспученного перлита все применяемые как сырьевой материал вулканические породы (с 1-10% воды) принято называть перлитом. Химический состав перлита (масс. %): SiO2 – 70-75; AI2O3 – 11-15; Fe2O3 – 0.2-4; СаО + MgO – 0.3-6; Ti2O – 2.5-9; Н2О – 0.3-10.
Вспученный перлит представляет собой сыпучий материал в виде пористых зерен преимущественно светлой окраски. В зависимости от размера частиц классифицируется на песок и щебень. Вспученный перлитовый песок (размер до 5мм) имеет марки от 75 до500 по средней плотности и теплопроводность в пределах 0.07-0.093 Вт/мºС.
Вспученный перлитовый песок имеет высокопористую структуру – поры сферической и щелевидной формы размером 0.5-10 мкм. Объем замкнутых пор 13-25% объема зерна. Общая пористость песка, включая межзерновые пустоты, находится в пределах 90-98%. Из песка насыпной массой 80-120 кг/м³ изготовляют теплоизоляционные изделия, 150-300 кг/м³ - заполнитель для легких бетонов. Перлитовый щебень используют как заполнитель легких бетонов (размер 5-20 мм). Марки по средней плотности от 300 до 600. Вспученный перлит огнестоек, химически инертен, биостоек и не имеет запаха. Размер зерна сильно влияет на его физико-механические характеристики, поэтому материал необходимо получать с заданной крупностью. Он имеет большие гигроскопичность и водопоглощение достигает 90% по объема (около 300% по массе), у зерен больших размеров оно еще возрастает.
Влажность влияет на теплопроводность перлита. При влажности 10% теплопроводность увеличивается в 2 раза, а при 80% в 3-4 раза. На величину теплопроводности влияют также форма и гранулометрический состав частиц, размеры и расположение пор, температура. Вспученный перлитовый песок обладает значительным звукопоглощением и используется для изготовления звукопоглощающих штукатурок, плит и блоков.
Наиболее богатые месторождения перлитовых пород в Закавказье, Закарпатье и Забайкалье.
Технология вспученного перлита
Основой технологии переработки перлитов является процесс вспучивания, который влияет на структуру и свойства продукта.
Оценку перлитового сырья производят по коэффициенту и температуре вспучивания.
Коэффициент вспучивания – число, показывающее во сколько раз увеличивается объем материала при обжиге. Он зависит от химического состава породы, вида содержащейся в ней воды, размера зерен и режима обжига, вязкости и поверхностного натяжения расплавленных пород. При малой вязкости образовавшийся газ выходит наружу, не образовывая пористой структуры. Так же он зависит от количества связанной воды и характера связи этой воды со стеклом. Вода в вулканических стеклах находится в виде молекулярной воды Н2О и гидроксила ОН ˉ. От характера связи воды с перлитом зависит и температура вспучивания – чем больше молекулярной воды, тем ниже температура вспучивания.
Температура вспучивания – это температура, при которой происходит максимальное вспучивание перлита. Лучшим сырьем для получения вспученного перлита являются породы, вспучивающиеся при температуре менее 1050 ºС, если температура более 1050 ºС – породы относятся к трудновспучиваемым, получаемый продукт имеет высокую среднюю плотность.
Температура обжига обуславливается моментом соответствия между вязкостью размягченной стекломассы и добавлением водяного пара, образующегося при испарении содержащейся в сырье «эффективной» воды. Эта температура колеблется в зависимости от сырья от 850 до 1250ºС.
Развитая удельная поверхность перлита, наличие в ней свободных зарядов и обменных ионов обуславливают высокую реакционную способность его к растворам щелочей, образуя гидроалюминаты и гидросиликаты и к извести и цементу, образуя гидроалюминаты и гидросиликаты кальция.
Технологический процесс получения вспученного перлита состоит из операций по добыче породы, дробления, фракционирования и обжига с последующей сортировкой на фракции готового продукта. Иногда в зависимости от свойств сырья породу перед вспучиванием подвергают термической обработке для удаления избыточной влаги.
Перлит добывают открытым способом. Если влажность породы больше нормы, то она проходит предварительную сушку в сушильном барабане. После этого порода дробится в две стадии в щековой и молотковой дробилках до необходимой крупности. Дробленая порода разделяется на фракции на виброгрохотах или в сите-бурат.
Некоторые породы перед обжигом проходят специальную термическую подготовку во вращающихся барабанных печах (нагрев до температуры 250..500ºС), при которой удаляется часть воды, что уменьшает растрескивание зерен перлита в процессе обжига.
Обжиг (вспучивание) перлита производится в вертикальных шахтных или во вращающихся печах.
Вспучивание перлита в вертикальных печах
Получают перлитовый песок. Вспучивание происходит во взвешенном состоянии при температуре 1000…1100ºС.
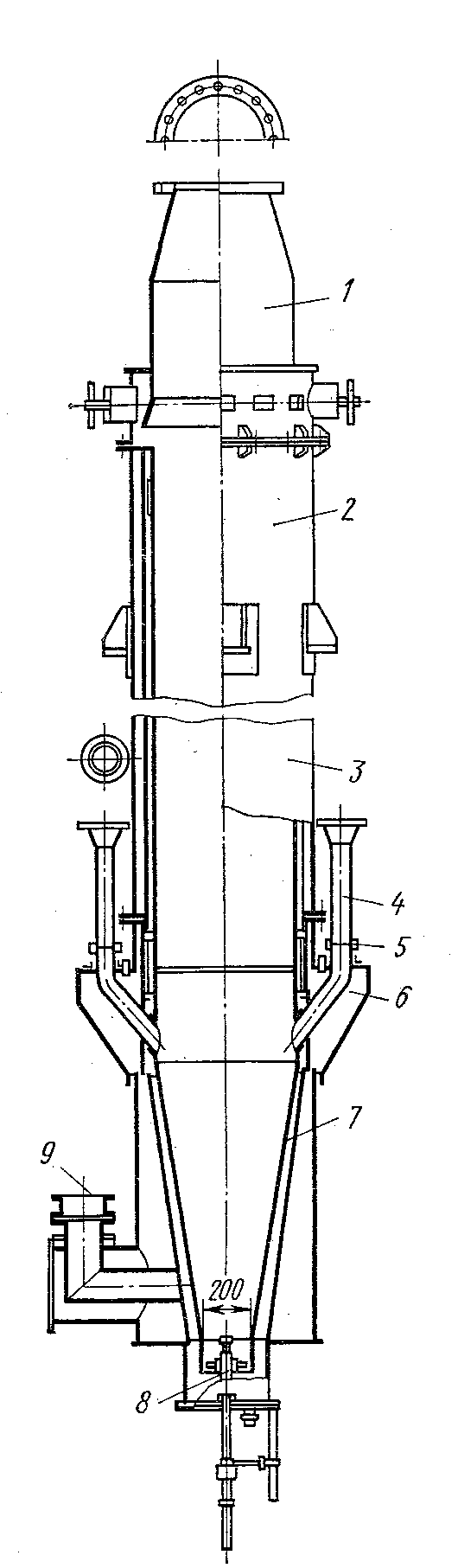
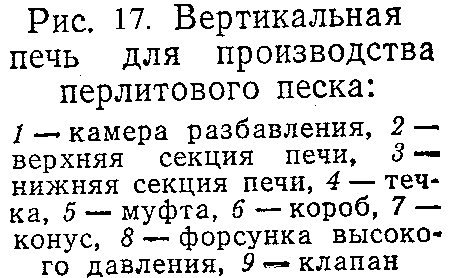
Измельченный перлит подается в печь через загрузочную течку 1, находящуюся немного выше форсунки 2, в месте наибольшей температуры газов.
Вертикальная шахтная печь вспучивания – круглая шахта внутренним диаметром 0.6 м и высотой 7.7 м, в которой снизу вверх подается поток раскаленных газов.
Частицы перлита в потоке горячих газов вспучиваются в течение нескольких секунд и уносятся с выходящими потоками дымовых газов в циклоны – классификаторы.
Перед циклонами дымовые газы с находящимися в них частицами вспученного перлита разбавляют холодным воздухом до температуры 300ºС. Неосевшие в циклонах мельчайшие частицы перлита уносятся с дымовыми газами в трубчатый аппарат – скруббер, где улавливаются «мокрым» способом при орошении водой. Производительность шахтной печи для обжига перлита составляет 15 - .22 м³/ч в зависимости от конструкции печи и вида перлитового сырья. Вспученный перлитовый песок из бункеров расходуется на производство теплоизоляционных изделий или упаковывается в бумажные или полиэтиленовые мешки и отправляется потребителю. Вспученный перлит нужно предохранять от увлажнения.
Вращающаяся печь
6000 150
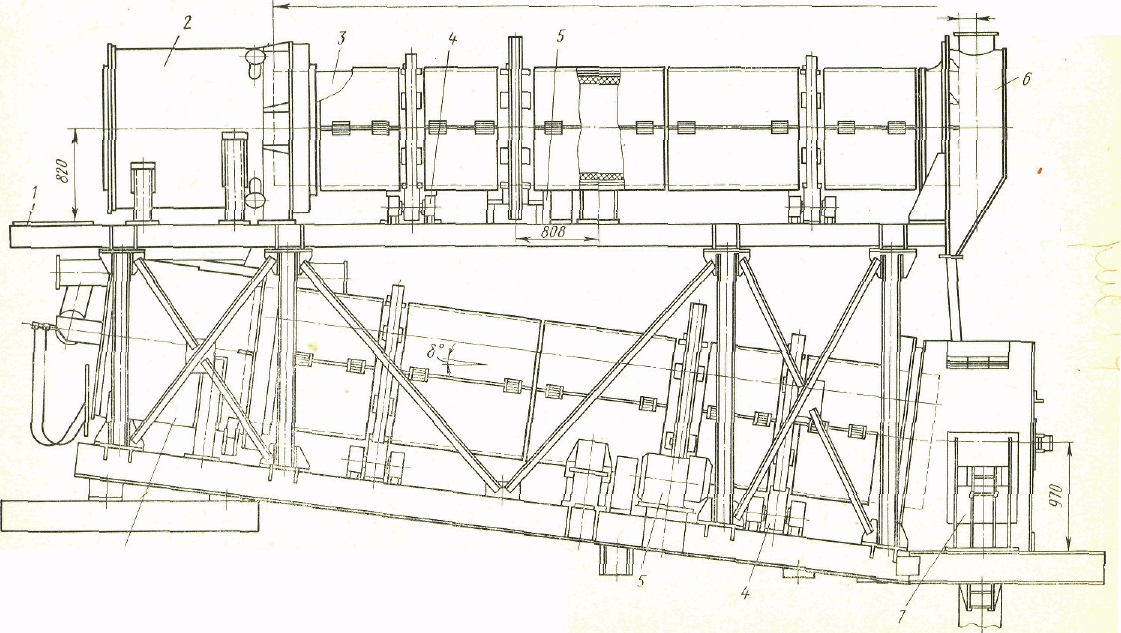
Рис. 18. Агрегат для вспучивания перлита:
1 — рама, 2 — топка, 3 —барабанная печь термоподготовки, 4 — опоры,
5— электродвигатели, 6 — загрузочная камера, 7 — камера выгрузки, 8— печь вспучивания
При ее использовании можно регулировать время пребывания материала в печи, что позволяет обжигать крупное сырье для получения крупного песка и щебня.
Эта печь состоит из барабанной печи термоподготовки и собственно вращающейся печи обжига.
Печь обжига представляет собой вращающийся барабан длиной 6м, внутренним диаметром 0.77 мм. Вспучивание перлитового щебня происходит в процессе перемешивания его по раскаленной футеровке печи, омываемой факелом пламени от сгорания жидкого или газообразного топлива. Так как барабан вращающейся печи установлен под углом 6º в сторону камеры выгрузки, вспученные зерна перлита постепенно передвигаются от загрузочной камеры к выходу из печи. Мелкие частицы перлита уносятся вместе с дымовыми газами и улавливаются в циклонах. Из приемной камеры печи перлитовый щебень транспортируется в металлические бункера. Производительность печи – 1200 кг/час при температуре вспучивания 1000-1150 ºС, частота вращения барабана печи – 8,10 и 16 об/мин. На печах следует работать в предохранительных темных очках, брезентовой спец. одежде, рукавицах.
Разработана новая конструкция обжигового агрегата с направленным кипящим слоем инертного твердого теплоносителя для обжига кускового и гранулированного материала. В качестве твердого инертного теплоносителя используют кварцевый песок размером 0.6-1.2 мм. Горячий газ сгорает в слое песка и обеспечивает обжиг перлита с размером зерен 5-15 мм в высокотемпературном кипящем слое твердого теплоносителя. Вспученный перлит всплывает на поверхность песка и с частью песка выгружается из печи через разгрузочный люк. Производительность 20 тыс. м³ в год. Увеличивается коэффициент теплопередачи, сокращается расход топлива и длительность обжига.
Вспученный вермикулит
Вермикулитами называют минералы из группы гидрослюд. Они образуются в природных условиях в результате гидратации и других вторичных изменений различных слюд. При нагревании вермикулит обладает способностью вспучивания, образуя мелкие поры. Практическое значение имеют вермикулиты, образовавшиеся из магниево-железистых слюд – флогопита и биотита путем их гидратации, причем молекулы воды входят в кристаллическую решетку слюды, заменяя ионы К+. В решетке образуются гидратные слои.
Химический состав вермикулита колеблется в следующих пределах (%): SiO2 – 37-41; AI2O3 – 10-14; Fe2O3 – 3-15; СаО – 0.6-1.8; MgO – 15-24; FeO – 1-5; Na2O+K2O – 5-13; Н2О – 1.4-11.
При быстром нагревании при температуре 850-1200 ºС происходит выделение паров воды, которые направлены перпендикулярно плоскости спайности и, раздвигая слюдяные пластинки, расщепляют минерал, на отдельные пластинки, увеличиваясь в объеме до 15…20 раз (в среднем в 6 раз). Образуются поры, направленные параллельно плоскостям спайности, вытянутой формы.
В природном вермикулите, кроме межпакетной молекулярной воды содержится еще и гидратная вода, входящая в состав молекулярной структуры минерала. Плотность вермикулита 0,05-2,71 г/см³, температура плавления около 1300ºС, влажность породы должна быть не более 10%.
Основным фактором, обеспечивающим вспучивание вермикулита при нагревании, считают выделение межпакетной воды. Она начинает удаляться при температуре 170-200 ºС, наибольшая часть ее уходит при 270-290 ºС, а окончательное ее удаление происходит при 700-800ºС. При 850-880ºС удаляются гидроксил ионы, что сопровождается разрушением слюдяной структуры.
Вспучивание вермикулита оценивают коэффициентом вспучивания Кв – это отношения объема вспученного материала к объему исходного сырья, Кв≈6.
Вспученный вермикулит – сыпучий зернистый материал чешуйчатого строения. Средняя плотность 80-200 кг/м³, теплопроводность 0.056-0.07 Вт/(м·ºC). Имеет высокое звукопоглощение, огнестойкость, невысокую гигроскопичность и биостойкость. В зависимости от размера зерен, согласно стандарту он делится на три фракции: крупную (5-10мм), среднюю (0.6-5мм), мелкую (<0.6 мм). По средней плотности вспученный вермикулит делится на 3 марки: 100,150,200.
Водопоглощение вспученного вермикулита большое, так как он имеет сообщающуюся пористость. Оно зависит от объемной массы, зернового состава, режима обжига и природных свойств вермикулита.
Теплопроводность вермикулита зависит от средней плотности и размера зерен. У очень больших зерен она снижается из-за конвективного теплообмена внутри пор. Вспученный вермикулит в отличие от перлита обладает упругостью.
Строение зерен вермикулита анизотропное: в направлении, параллельном плоскостям спайности, прочность их больше, чем в направлении, перпендикулярном плоскости спайности.
При повышении температуры и увеличении продолжительности обжига хрупкость зерен вспученного вермикулита увеличивается. Вспученный вермикулит обладает хорошими адсорбционными свойствами.
Вспученный вермикулит применяют в качестве теплоизоляционной засыпки при температуре изолируемых поверхностей от -260 до +1100ºC (до 900ºC – при изоляции вибрирующих поверхностей), для изготовления теплоизоляционных изделий, а также в качестве заполнителя для легких бетонов и для приготовления штукатурных теплоизоляционных и огнезащитных растворов.
Технология вспученного вермикулита
Технологических процесс получения вспученного вермикулита состоит из операций по добыче породы, ее обогащению, дроблению крупных пластин вермикулита и обжига. Обжигают вермикулит в шахтных и трубчатых печах. Обжиг вермикулита происходит в потоке горячих дымовых газов, образующихся от сгорания жидкого или газообразного топлива.
Ф1750
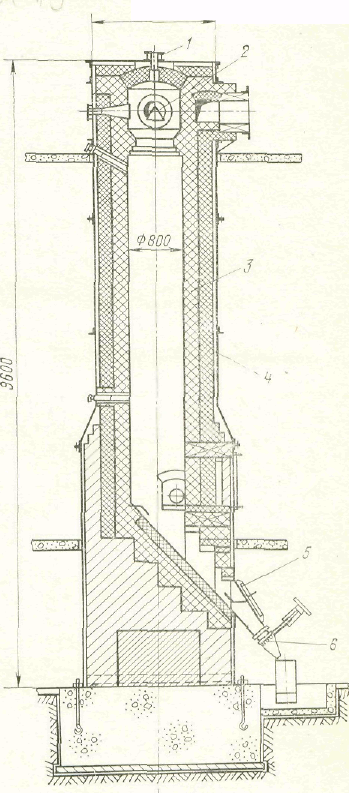
1 - загрузочный патрубок, 2 - конус-рассекатель, 3 - шахтная печь, 4 -труба, 5 - течка, 6 - затвор
Она представляет собой вертикальную металлическую трубу 3, футерованную изнутри огнеупорным и теплоизоляционным кирпичом. Сырье подается через загрузочный патрубок 1, расположенный в верхней части печи, и проходит конус-рассекатель 2, служащий для равномерного распределения породы по поперечному сечению шахты. Падая вниз, вермикулит попадает в восходящий поток горячих газов, создаваемых форсункой 6 низкого давления. Вспученный вермикулит, преодолевая сопротивление газовоздушного потока, падает на наклонный под, который сообщается с течкой 4, снабженной затвором 5, и скатывается в бункер готовой продукции.
Для обжига используют измельченную вермикулитовую породу размером от 0.5 до10 мм. Фракция меньше 0.5 мм считается отходом производства, а крупнее 10 мм идет на дополнительное дробление.
Трубчатая печь – составная часть сушильно-печного агрегата (комбайна).
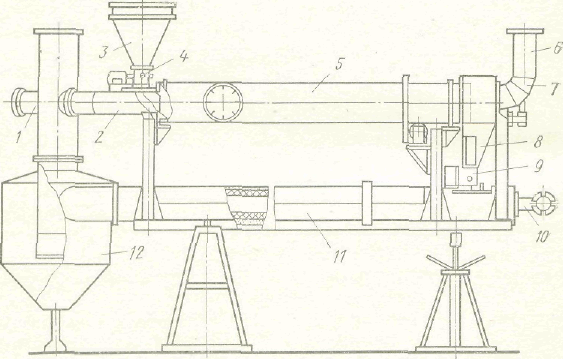
1 - всасывающий воздухопровод, 2 - воздухопровод, 3 - загрузочный бункер, 4, 9 - барабанные питатели, 5 - сушильный барабан, 6 - вытяжная труба, 7 - вентилятор, 8 - бункер для сухого сырца, 10 - форсунка, 11 - трубчатая печь, 12- циклон
В этот агрегат кроме трубчатой печи, входят еще сушильный барабан 5 и циклон 12. Сырье загружается в бункер 3 и барабанным питателем 4 подается во вращающийся сушильный барабан 5, в котором перемещается из одного конца в другой. Перемещение сырья обеспечивается наклоном барабана под углом около 5º и винтообразными полками внутри него.
Высушенный и нагретый до 100ºC вермикулит загружается барабанным питателем 9 в печь обжига 11, где попадает в горячий газовоздушный поток. Температура вспучивания вермикулита 1000-1200ºC, производительность агрегата – до 6 м³/ч. Сырье быстро вспучивается и потоками газов и воздуха выносится в осадительную камеру, а мелкие частицы осаждаются в циклоне. Вспученный вермикулит очищают от пустой породы в сепараторе, который установлен за осадительной камерой.
Печь работает по принципу прямотока, поэтому мелкие частицы, быстро нагреваясь, вспучиваются и выносятся из печи, а крупные и менее гидратированные задерживаются в печи дольше, до вспучивания, после чего они выносятся потоком воздуха.
Во вращающихся печах вермикулит практически не вспучивают, так как он разрушается там на отдельные пластины.
Изделия на основе вспученных перлита и вермикулита
Виды изделий из вспученных перлита и вермикулита
В зависимости от температуры применения перлитовые и вермикулитовые теплоизоляционные материалы и изделия можно разделить на три основные группы:
1) для обычных положительных и низких отрицательных температур (включая область глубокого холода) – вспученные перлитовые порошок и пудра (до -200ºC), мелкий вспученный вермикулит до 0.6 мм (до -260ºC), перлито - и вермикулитобитумные изделия (от-60 до+100 ºC), битумно-перлитовая или вермикулитовая масса (от -60 до +130ºC);
2) для средних положительных температур (до 600ºC) – перлито - и вермикулитоцементные, перлитофосфогелевые изделия, перлитовый и вермикулитовый легковес;
3) для высоких температур – перлито - и вермикулитокерамические изделия (до 900ºC), жароупорный перлито - или вермикулитобетон (до 1000ºC), керамоперлитофосфатные изделия (до 1100ºC), перлитовые ультралегковесные огнеупоры плотностью до 400 кг/м³ (до 1150ºC); перлитовые легковесные огнеупоры плотностью 500-800 кг/м³ (до 1300ºC). Кроме того разработана технология производства перлитовых и вермикулитовых теплоизоляционных изделий и штукатурок на известковом и гипсовом вяжущем, на синтетических смолах и др.
В зависимости от технологии изготовления перлитовые изделия делятся на безобжиговые и обжиговые. При производстве первых заключительной стадией в технологическом процессе является сушка, вторых – после сушки следует высокотемпературный обжиг.
Безобжиговые – битумные, цементные, силикатные, гипсо-, стекло -, пласто -, карбоперлит или вермикулит.
Обжиговые – керамоизделия, керамоперлитофосфат, перлитофосфат, перлитовый легковес на основе легкоплавких связок.
Производство всех видов изделий включает следующие операции: подготовку и дозировку сырьевых материалов, смешивание сырьевых материалов, смешивание компонентов, формование изделий и тепловую обработку. Исключение составляет битумо-перлит, который не требует тепловой обработки. Подготовка сырьевых компонентов заключается в основном в измельчении и просеивании, чтобы получить нужный гранулометрический состав. В случае необходимости производится подсушка.
При смешивании вспученных перлита и вермикулита со связующими особое внимание следует уделять сохранению структуры зерен, предохранению их от истирания. Этими требованиями предопределяется характер применяемых смесительных аппаратов, время введения перлита и длительность перемешивания. В основном используются лопастные смесители время перемешивания 1-2 мин.
Связующие при производстве изделий из перлита и вермикулита могут быть разными: это гидравлические вяжущие (цемент), битумные вяжущие, жидкое стекло, полимерные смолы, глина. Формование перлитовых и вермикулитовых теплоизоляционных изделий осуществляется с помощью устройств, которые вызывают минимальное уплотнение материала и не разрушают зерна перлита или вермикулита. Наиболее широко применяется прессование при давлении 0,05 МПа.
Цементные изделия из перлита и вермикулита
Перлито - и вермикулитоцементные изделия изготавливают из сырьевой смеси, состоящей из вспученного перлитового или вермикулитового песка, цемента и водной асбестовой пульпы с последующим формованием и сушкой. Промышленность выпускает их в виде плит, полуцилиндров (скорлуп) и сегментов. Изделия служат для тепловой изоляции промышленного оборудования и трубопроводов при температуре изолируемой поверхности до 600ºC. Средняя плотность перлитовых изделий – 225-350 кг/м³, вермикулитовых 250-500 (плотность 500 изделия имеют в том случае, если формуются без добавления цемента).
Вспученного перлита или вермикулита плотностью 75-100 кг/м³ берется 43% по массе, портландцемента марки не ниже 400 – 43% по массе, асбеста не ниже 6 сорта – 14% по массе. Вода вводится в количестве 230-300% от массы сухих веществ. Цемент и асбест дозируются по массе, перлит или вермикулит и вода – по объему.
Асбест обминается на бегунах при увлажнении о 30…35% в течение 15-20 мин., а затем распушивается либо в пропеллерной мешалке, либо в аппарате распушки (при разбавлении асбеста 15…20 кратным количеством воды) в течение 20 мин. В производстве вермикулитовых изделий применяют двукратную распушку. Для смешивания материалов применяют лопастные горизонтальные мешалки или винтовой смеситель (шнек). Сначала в мешалку подается асбестовая пульпа, затем цемент, перемешивают 5 мин, и вводят перлит или вермикулит, перемешивая еще 1.5-2 мин.
После смесителя полученная гидромасса подается на формование в гидравлический пресс или конвейерный станок. Прессование изделий производится на металлических поддонах при удельном давлении 0.05МПа. Производительность 1.5…2 м³/ч. Правильная геометрическая форма изделий получается при формовании в прессах или на конвейерах, снабженных узлом подпрессовки.
Отформованные изделия подвергаются тепловой обработке в туннельных или конвейерных сушилках. Их выдерживают при температуре 170…200ºC в течение 3-4 ч. В это время изделия прогреваются, основная масса воды испаряется. Затем температуру снижают и выдерживают изделия при температуре 90-100ºC в течение 6-8 ч. За это время пропариваются и приобретают необходимую механическую прочность. В заключение температуру повышают до 150-180ºC и изделия досушивают до остаточной влажности 20-30%. Общая продолжительность сушки 13-16ч. Готовые изделия укладывают в жесткую тару с бумажными прокладками. Хранить в закрытых складах в штабелях не выше 1.7-2 м.
Перлито- и вермикулитобитумные материалы и изделия
Изготовляют два вида материалов на битумном связующем – перлито - или вермикулитобитумные плиты средней плотностью 200-300 кг/м³ и битумно-перлитовую или вермикулитовую массу 350-600 кг/м³.
Плиты изготавливают из вспененного перлитового или вермикулитового песка марок 75 и 100 (60…65% по массе), битума марок БМД-40/60 (9…15%), высокопластичной или среднепластичной глины (5…11%), асбеста марки П-6-45 (15…20%), клея карбоксиметилцеллюлозы (КМЦ) – 1.5% от массы сухих компонентов или сульфитно-дрожжевую бражку (СДБ) – 3% от массы сухих компонентов и воду. Общее содержание битума и глины в массе – 20%.
Подготовка асбеста аналогична для всех изделий, где применяется асбест.
Обезвоженный и разогретый до температуры 150-160ºC битум смешивается в лопастной мешалке с глиняным шликером (глина и вода в соотношении 1:1.5) относительной влажностью до 60% в течение 10 мин. до получения однородной по окраске массы темно-серого цвета без крупинок битума. Полученная паста разбавляется водой до 50-60% относительной влажности и перекачивается в расходный бак. Для приготовления пасты используют лопастные смесители.
Битумно-глиняная паста, асбестовая пульпа и КМЦ или СДБ предварительно перемешиваются в общем расходном баке, а затем подаются в смеситель приготовления формовочной массы. КМЦ или СДБ предварительно разбавляют водой до 10-13% концентрации.
Эта смесь затем перемешивается с перлитом 2 мин. Относительная влажность формовочной массы колеблется от 75 до 80%. Плиты формуют на металлических поддонах или в формах. Плиты сушатся в туннельных сушилках в течение 12-15 ч. по следующему режиму: испарение основной массы воды при температуре 200ºC – 5-6 ч., испарение оставшейся воды при температуре 120-130ºC – 4-6 ч., расплавление битума при 150-160ºC – 3 ч. Готовые плиты охлаждают вентилятором до температуры 30ºC.
Битумно-перлитовую или вермикулитовую массу изготовляют путем смешивания вспученного перлитового или вермикулитового песка с горячим нефтяным битумом марок не ниже БМ -70/30. полученную массу укладывают на поверхность кровельных покрытий или в формы для получения изделий и уплотняют. Кроме того, эту массу применяют в качестве изоляции стальных труб тепловых сетей.
Вспученный перлитовый или вермикулитовый песок, поступающий из бункера, смешивают в растворосмесителе с расплавленным и обезвоженным при температуре 150-180ºC битумом в течение 3 мин. После перемешивания горячая масса поступает в расходный бункер, откуда подается на пресс.
Перлитовые и вермикулитовые изделия на жидком стекле
Изделия на жидком стекле выпускаются двух видов – перлито - или вермикулитофосфогелевые и перлитовый обжиговый легковес.
Перлито - или вермикулитофосфогелевые изделия состоят из вспученного перлитового или вермикулитового песка (60-70% по массе) и жидкого стекла плотностью 1.3 г/см³ (40-30% по массе). Чтобы обеспечить равномерное твердение изделий по всей толщине и снизить их водопоглощение, в состав смеси вводят незначительное количество ортофосфорной кислоты и гидрофобизирующей (водоотталкивающей) добавки ГКЖ-10 или ГКЖ-11.
Изделия применяют для огнезащиты и тепловой изоляции строительных конструкций, горячих поверхностей оборудования и трубопроводов при температурах до 600ºC. При устройстве специального гидроизоляционного покрытия из бумаги, наклеенной битумом, плиты могут применяться для изоляции строительных конструкций при температурах от -80 до +60ºC.
Изделия выпускают в виде плит, полуцилиндров (скорлуп) и сегментов. По средней плотности изделия изготовляют от 200 до 300 кг/м³.
Технологический процесс изготовления изделий на жидком стекле включает в себя перемешивание компонентов в растворосмесителе, прессование и сушку. Время перемешивания должно быть не более 1 мин. для предотвращения разрушения зерен. Жидкое стекло используется товарное или оно готовится на заводе. Формовочная масса получается полусухая и сыпучая, поскольку ее относительная влажность не превышает 50%. Изделия формуются в прессе под давлением от 0.3 до 0.8 МПа или на конвейерной линии между двумя движущимися лентами. Тепловая обработка (сушка) изделий производится в туннельной или конвейерной сушилке при температуре до 350ºC. Продолжительность сушки изделий толщиной 60-100 мм составляет 4-6 ч. Высушенные изделия поступают на склад готовой продукции.
Перлитовый обжиговый легковес применяют для изоляции энергетического оборудования при температуре теплоизолируемой поверхности 600-700ºC, а также для теплоизоляции покрытий кровли по профилированному металлическому настилу. Технологический процесс этого материала отличается от описанного выше тепловой обработкой – вместо сушки материал обжигают при 800ºC в туннельных или конвейерных печах. Для получения 1 м³ обжигового легковеса расходуется 85-160 кг перлитового песка и 11-21 кг жидкого стекла (плотностью 1.4 г/см³). Средняя плотность изделия 100-200 кг/м³.
Плиты из перлитопластобетона
Их получают вспениванием при тепловой обработке композиции, состоящей из тонкоразмолотой смеси новолачной фенолформальдегидной смолы (65% по массе) и вспученного перлита (25%) с добавками отвердителя (уротропина) – 8,5% и газообразователя (порофора) – 1,5% от массы смолы. Плиты используют для тепловой изоляции строительных конструкций в промышленности и сельском хозяйстве. Температура применения от +150 до -50ºC. Средняя плотность плит 100-175 кг/м³.
Технологический процесс изготовления плит из перлитопластобетона включает в себя: дробление кусковой смолы, дозирование исходных компонентов, совместный помол компонентов, засыпку смеси в форму или в формующий агрегат и тепловую обработку для вспенивания и отверждения плит.
Вермикулитовые изделия также формуют, применяя синтетические смолы, но смесь не вспенивают. В изделие входит так же асбест.
Перлито - и вермикулитокерамические и легковесные изделия
Перлитокерамические изделия изготовляют из смеси вспученного перлитового песка 50-60% по массе и огнеупорной пластичной глины 40-50% по массе. Средняя плотность изделий 250-400 кг/м³.В состав изделий вводится небольшое количество воздухововлекающих полимерных добавок, снижающих их плотность. Изделия выпускаются в виде плит, кирпичей, полуцилиндров и сегментов.
Огнеупорную пластичную глину измельчают, замачивают водой и смешивают с перлитовым песком. Влажность гидромассы составляет 63-65% и 35-40% при полусухом формовании. Гидромасса подается в формующий конвейер или пресс; плиты формуются, а затем сушатся при 75-170ºC в течение 20-25 ч. Высушенные изделия обжигают в туннельных печах при температуре 850-900ºC. Общая продолжительность обжига составляет 20-26ч.
Крахмально-бентонитовые асбестовермикулитовые изделия изготавливают из вспученного вермикулита 68% по массе, асбеста 18% по массе, бентонитовой глины 10% по массе, крахмала 4%. Идет только сушка изделий. Средняя плотность 280-380 кг/м³.
Легковесные огнеупорные перлитошамотные изделия изготавливают на основе вспученного перлитового песка (13-3%), огнеупорной глины (16%) и шамота (71-81%). Средняя плотность – 400-800 кг/м³.
Жароупорный теплоизоляционный перлито - или вермикулитобетон
Они применяются для тепловой изоляции (футеровки) промышленных печей, дымовых труб и других тепловых агрегатов. Они являются разновидностью легких бетонов.
В состав бетонов входят в качестве заполнителя перлитовый или вермикулитовый щебень и песок, а в качестве вяжущего – портландцемент, жидкое стекло или глиноземистый цемент.
В зависимости от вида вяжущего температура применения их колеблется от 600 до 1000ºC. Изготовляют бетоны средней плотностью от 400 до 1000 кг/м³.
Сырьевые компоненты перемешиваются в бетоносмесителях принудительного действия. Весь цикл приготовления смеси составляет около 3 мин. Приготовленную смесь укладывают в металлические формы и уплотняют вибрированием. По окончании твердения (от 3 до7 суток) бетонные блоки (панели) распалубливают и пакуют. Твердение в автоклаве.
Керамические теплоизоляционные изделия
Эта группа материалов включает ряд разновидностей высокопористой керамики: диатомитовые (трепельные), перлитокерамические, огнеупорные (шамотные, динасовые), высокоглиноземистые, корундовые и др.
Во всех случаях в производстве этих материалов присутствует стадия обжига, что позволяет объединить их в одну группу керамических изделий.
Высокопористое строение этих изделий обеспечивается различными способами:
- Введение в формовочную массу пористых компонентов применяется при производстве керамических изделий мало (только перлит и шамот) из-за удорожания материалов и недостаточного снижения средней плотности;
- Метод вспучивания при обжиге применяется в промышленности крайне ограниченно из-за сложности придания изделиям требуемых размеров и формы. Необходимо иметь высокоогнеупорные формы либо прибегать к механической обработке после обжига;
- Способ введения выгорающих добавок применяется очень широко. Недостатки способа: сложность получения пористости более 65% и низкая прочность материала, особенно при повышении пористости. Однако этот способ технологичен, позволяет точно регулировать среднюю плотность изделий, при формовании изделий требуется меньшее количество воды, уменьшается время сушки сырца; при выгорании добавок образуются в перегородках микротрещины, которые увеличивают термостойкость изделий. Важнейшими факторами, влияющими на процесс выгорания органических добавок, являются: толщина обжигаемого изделия, его плотность, газопроницаемость, вид содержание и размер зерен добавки, режим обжига, расстояние между изделиями в садке, избыток воздуха в печных газах. На продолжительность выжигания добавки большое влияние оказывает крупность зерен, плотность и глубина запрессовки. Газовыделение продуктов сгорания должно происходить раньше процесса спекания, иначе могут образоваться трещины в изделии.
В качестве выгорающей добавки кроме опилок, золы можно использовать и вспученные зерна полистирола, фракции менее 0.5мм (отход производства). Пористость материалов увеличивается до 80%, прочность довольно высокая, а после сгорания полистирол не оставляет золы.
4) Пеновой способ получения пористой керамики имеет большое практическое значение. Он позволяет получать изделия с наибольшей пористостью. Способ основан на введение в керамический шликер пенообразователей или на смешивании заранее приготовленной пены со шликером. Изделия, получаемые этим способом, характеризуются высокой прочностью. Недостатки: (они технологического характера) применение способа связано с необходимостью тонко измельчать исходные материалы, чтобы предотвратить разрушение пены; способ связан с введением в формовочные массы большого количества воды затворения для получения устойчивой во времени пенокерамической массы. Высокая влажность пеномасс приводит к значительному увеличению продолжительности сушки сырца (иногда до 5 сут.). Изделия дают большую усадку, коробятся, их приходится обрезать и шлифовать. Производство перлитокерамических изделий мы рассмотрели выше.
Диатомитовые изделия
Основным сырьем для производства диатомитовых керамических изделий служат диатомиты и трепелы, представляющие собой кремнеземистые осадочные породы.
Диатомит – рыхлая, землистая, пористая и легкая осадочная горная порода, образованная из обломков панцирей диатомитовых водорослей, которые часто сохраняют свою структуру. Диатомит состоит в основном из аморфного кремнезема. Плотность диатомита 400…600 кг/м³. Пористость достигается 85..89%. Водопоглощение и абсолютная влажность 150% по массе. Цвет меняется от белого до светло-желтого в зависимости от наличия окислов железа. Огнеупорность от 1570 до 1650ºС. Добываются в карьерах открытым способом, снимая механизмами верхний слой.
Трепел – осадочная порода, аналогичная по свойствам диатомиту, имеющая такой же химический состав, но почти лишенная органических остатков.
Химический состав 80-90% SiO2, 5-10% Al2О3 и 2-3% СаО+MgO. Содержится некоторое количество связанной воды.
Наиболее крупные месторождения диатомитов и трепелов в Ульяновской области, Закавказье, в Московской, Орловской, Калужской областях, на Урале, Дальнем Востоке, Украине.
Теплоизоляционные изделия из диатомитов изготовляют в виде кирпича, сегментов и скорлуп и применяют до температур 800-900ºС. Производство изделий осуществляют двумя способами: способ выгорающих добавок и пеновой. Свойства изделий, получаемых различными способами – разные.
Способ выгорающих добавок
Обычно производство изделий организуется непосредственно в районе месторождения основного сырья и состоит из следующих операций: приготовления формовочной массы, формования, сушки и обжига изделий.
В качестве выгорающих добавок применяют древесные опилки, лигнин (отход гидролизной промышленности), нефтяные отходы и т.д. Количество выгорающих добавок зависит от теплоты их сгорания и составляет: 50% по объему формуемой массы – для древесных опилок, 25% - для лигнина, 15-20% - для нефтяных отходов.
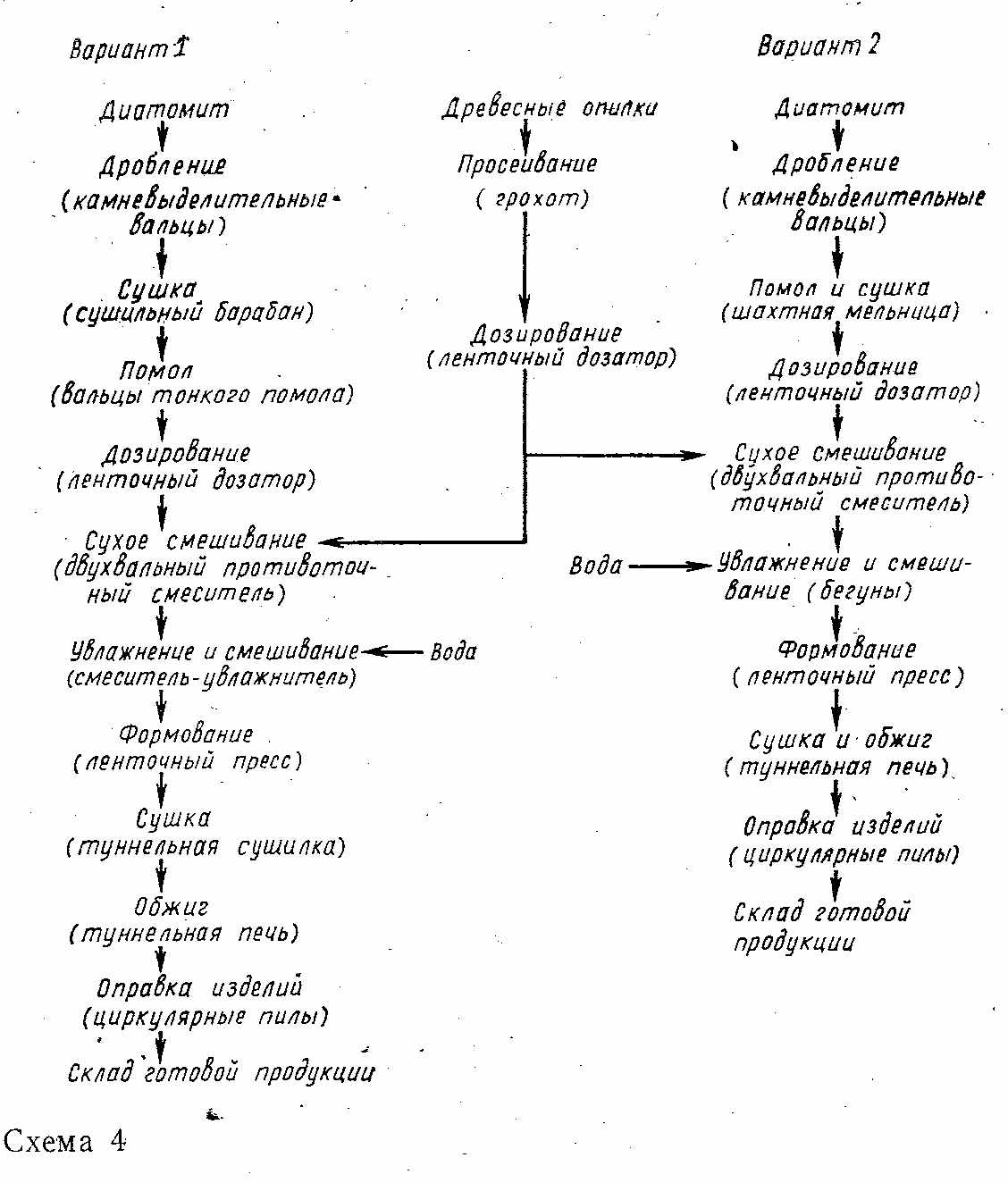
Рис. 21. Схема получения диатомитовых изделий способом выгорающих добавок
Диатомит (трепел), поступающий с карьера, предварительно дробят, высушивают в сушильном барабане до влажности 10%, измельчают на вальцах или мельнице и просеивают через сито с отверстиями 5…6 мм. Возможен совмещенный помол и сушка. Опилки просеивают через сито с отверстиями не более 10 мм и подают в распределительные бункера.
Опилочно-диатомитовую массу готовят путем последовательного применения двух операций: сухого смешивания и смешивания с увлажнением в этом же смесителе. Для получения диатомитовых изделий с плотностью 500-700 кг/м³ содержание опилок должно составлять соответственно 35-25% (по массе). Формовочные диатомитовые массы должны иметь в пределах 60-65%, а при использовании трепела – 40-45%. После перемешивания формовочная масса поступает в ленточный пресс с мундштуками нужной конфигурации, который представляет собой винтовой конвейер. Масса выдавливается через прессовую головку в виде бесконечной ленты, форма которой определяется видом изделия. Лента разрезается на отрезки нужной длины.
Сушка изделий протекает в более жестких условиях, чем сушка обычного глиняного кирпича. Для сушки используются противоточные туннельные сушилки; общая продолжительность сушки не более 12 ч., температура сушки около 250-280ºС. Сушка производится дымовыми газами, которые движутся в туннеле навстречу сырым диатомитовым изделиям. Остаточная влажность сырца не более 15-17%, усадка изделий после сушки составляет 4-5%.
Обжиг изделий осуществляется в туннельных печах, что позволяет не делать перегрузку изделий из вагонеток.
Обжиг продолжается в течение 25 ч. Сначала поднимают температуру до 850-900ºС в течение 12 ч., после чего изделия выдерживают при этой температуре в течение 1 ч., затем их охлаждают до температуры 80…100ºС в течение 12 ч. Обжиг изделий проводят до спекания диатомитового сырья и образования керамического черепка. Необходимое для обжига изделий тепло выделяется в результате сгорания древесных опилок или других выгорающих добавок. Топливо затрачивается только на розжиг печи.
Пенодиатомитовые изделия
Способ выгорающих добавок не позволяет изготавливать изделия со средней плотностью ниже 500 кг/м³. пенодиатомитовые изделия могут иметь среднюю плотность 300 кг/м³, но изготовление их дороже.
Пенодиатомитовые изделия получают из смеси диатомита и пенообразующих веществ с возможной добавкой небольшого количества выгорающих опилок. Изделия формуют из гидромассы, сушат и обжигают.
В качестве пенообразующего вещества используют смолосапониновый пенообразователь, приготовляемый из мыльного корня, а также казеино-канифольного пенообразователя.
Диатомит, измельченный в молотковой дробилке и просеянный через сито, поступает в емкость трехбарабанной пенобетонной мешалки. В другой барабан загружают пенообразователь, где из него готовится техническая пена. Диатомитовый шликер и пена поступает в третий барабан, где готовится пенодиатомитовая масса. Время перемешивания не более 5 мин.
Формуют изделия путем заливки массы в стальные или алюминиевые очищенные и смазанные формы нужной конфигурации. Заливка осуществляется с помощью разливочной машины. Очень высокая влажность пеномассы 200-250%, обуславливает значительные усадочные деформации при сушке изделий от 5-7 до 20-25%. Это учитывается при изготовлении и заливке форм.
Изделия сушат в формах до остаточной влажности 10-12% - что замедляет сушку. Сушка проводится в туннельных противоточных сушилках на поточных вагонетках. Сначала температура 45-50ºС, чтобы избежать вспучивания массы, затем ее поднимают до 140ºС, сушка кирпича продолжается 48 ч., скорлуп и сегментов – 75-96 ч.
Обжигают пенодиатомитовые изделия в туннельных печах по одинаковому режиму с диатомитовыми изделиями на выгорающих добавок. Т.к. прочность диатомитовых изделий не велика, их следует упаковывать в картонную или деревянную тару.
Огнеупорные материалы
Они применяются широко в двух направлениях.
Первое – тепловая изоляция и тепловая защита. В этом случае эффективность огнеупоров определяется теплопроводностью и средней плотностью.
Второе – связано с использованием развитой поверхности высокопористых огнеупоров – фильтры, газораспределители, катализаторы в процессах, протекающих при высоких температурах. Они характеризуются пористостью, газопроницаемостью.
Пористые огнеупоры применяются главным образом для устройства тепловой изоляции промышленных печей, теплопроводов и другого термического оборудования. 50% - используют в черной металлургии, 20% - в машиностроении, остальные в промышленности строительных материалов, химии и др.
Для тепловой изоляции главным образом применяют шамотные и динасовые легковесы, стали использоваться высокоглиноземистые, при очень высоких температурах (выше 1450ºС) – корундовые.
Шамотные изделия входят в группу алюмосиликатных, которые в зависимости от содержания в них оксида алюминия подразделяются на: полукислые (Al2О3 до 28%), шамотные (28-45%), высокоглиноземистые (свыше 45%). Сырьем для производства алюмосиликатных огнеупорных изделий служат природные огнеупорные глины или их смеси с добавками оксидов.
Шамот – обожженная до спекания огнеупорная глина, подвергнутая затем измельчению. Шамот является отощителем, снижает усадки. Шамотными называют изделия, получаемые путем обжига сырца, изготовленного из огнеупорных глин или каолинов с отощением шамотом, полученным из тех же или близких по химическому составу глин. Средняя плотность шамотных легковесов 0.4 г/см³. Они по огнеупорности делятся на 4 класса О, А, Б, В, огнеупорность от 1750-1580ºС.
В нашей стране шамотные изделия производят способом выгорающих добавок, пеновым способом и введением в состав шихты пористых гранул, получаемых путем дробления обожженных пеношамотных масс.
Высокопористые теплоизоляционные изделия из чистых оксидов
Изделия из чистых оксидов (Al2О3, ВеО, ZrO2, MgO и др.) обладают кроме высокой огнеупорности (более 2000ºС) рядом ценных свойств (химической инертностью, низкой электропроводностью, высокой стойкостью к коррозии и др.), что позволяет их использовать в различных условиях. В производстве таких изделий широкое применение получил лишь способ выгорающих добавок.
Корундовая керамика
Содержит не менее 95% оксида алюминия в виде α - Al2О3 – минерала корунда, встречающегося в природе. Основное сырье – технический глинозем, содержание Al2О3 в котором составляет 97-99%.
При нагревании до 1600-1700ºС глинозем разлагается, в результате чего образуется α - Al2О3, а сопутствующие оксиды выделяются в газообразном состоянии.
Второй вид сырья для корундовой керамики – электрокорунд. Чаще всего используют белый электрокорунд, получаемый плавлением в электродуговых печах технического глинозема и последующим раздувом расплава. При этом образуются зерна корунда размером от нескольких микрон до нескольких десятков микрон. Содержание Al2О3 составляет 98% и более. Его вводят в состав шихты для снижения огневой усадки.
Промышленное производство корундовых легковесных изделий осуществляют способом литья, а поризацию – способом выгорающих добавок. Обжиг около 1400ºС.
Изделия характеризуются: средняя плотность 1.1-1.4 г/см³, прочность при сжатии 7-10 МПа, огнеупорность 1330ºС.
Асбестосодержащие теплоизоляционные материалы
Асбестосодержащие теплоизоляционные материалы различны по составу сырья, технологии и применению, но все они содержат асбест в количестве от 10 до 30% (по массе). В зависимости от состава сырья их можно разделить на ряд групп:
- Асбесто-известково-кремнеземистые материалы получают из асбеста, извести и кремнеземистого компонента с применением автоклавной обработки. Кремнеземистым компонентом служат песок, диатомит или трепел.
- Асбестомагнезиальные материалы представляют собой смесь асбеста и основной магнезиальной соли состава 4MgCO3·Mg(OH)2·4H2O.
- Асбестодоломитовые материалы изготовляют из доломита и асбеста.
- Асбестотрепельные (диатомитовые) композиции – это сыпучие порошкообразные смеси, состоящие в основном из асбеста и трепела (диатомита) с добавками различных веществ.
- Асбестогипсовые материалы получают из свежеосажденного гипса и асбеста.
Наиболее эффективными по технико-экономическим показателям оказались асбесто-известково-кремнеземистые материалы. Намечается развитие их производства.
Асбест и его свойства
Асбестом называют минералы группы серпентинов или амфиболов волокнистого строения, способные при механическом воздействии разделяться на тончайшие волоконца.
По химическому составу асбестовые минералы являются водными силикатами магния, железа, кальция и натрия.
Волокнистое строение наиболее ярко выражено из асбеста серпентиновой группы, куда относится только один вид асбеста – хризотил-асбест, он больше всего применяется в промышленности, на его долю приходится 96% мировой добычи асбеста. Наиболее крупные месторождения на Среднем Урале, в Тувинской, Кустанайской, Оренбургской областях, а за рубежом – в Канаде и Южной Африке.
Из амфиболовых асбестов наибольшую промышленную ценность представляют крокидолит и амозит, крупные месторождения – в Африке. Амфиболовые асбесты более кислотостойки, чем хризотил-асбест, а некоторые более теплостойкие.
Мы будем рассматривать только хризотил-асбест.
Асбест хризотиловый представляет собой гидросиликат магния 3MgO·2SiO2·2H2O. Содержание окислов в % по массе следующее: MgO – 43.5; SiO2 – 43.5; H2O – 13. В состав хризотил-асбеста могут входить загрязняющие минеральные примеси. Карбонат кальция, например, вреден, он цементирует волокна асбеста, что снижает эластичность и распушиваемость волокон. Вода в асбесте содержится в виде связанной и адсорбционной.
Асбест имеет кристаллическую структуру волокнистого строения. Волокна хризотил-асбеста характеризуются плотной упаковкой элементарных волокон (фибрил). Каждая фибрила является трубкой. Стенки трубок образованы примерно 20 двойными ленточными слоями.
Механические свойства
Хризотил-асбест обладает высокой прочностью на разрыв по оси волокнистости. В зависимости от эластичности различают три разновидности: нормальную, полуломкую и ломкую. После деформации изгиба или скручивания механическая прочность волокон меняется – нормальное волокно сохраняет значительную долю начальной прочности, ломкое – ничтожную. Прочность волокон асбеста на разрыв составляет 3000 МПа, а например, капрона 600 МПа, стекловолокна 1300 МПа, стальной проволоки 1400 МПа.
Важная характеристика асбеста – модуль упругости, его средние значения от 16·104 до 21·104 МПа.
Температуростойкость
Хризотил-асбест несгораем, но при высоких температурах его физические свойства изменяются. При температуре 110ºС – прочность снижается на 10%, при 370ºС – на 25-30% - теряет адсорбционную воду, при 600ºС – на 77% при этом удаляется химически связанная вода, нарушается структура молекул решетки, что приводит к разрушению волокон. Это процесс необратимый. Поэтому температура применения изделий из асбеста ограничивается 600ºС. Хризотил-асбест плавится при 1500ºС.
Асбест обладает развитой поверхностью, поэтому имеет хорошие сорбционные свойства. Добытая в карьере асбестовая руда обрабатывается на обогатительных фабриках, где после ее дробления пустую породу отделяют от асбеста. В результате переработки образуются куски, иголки и волокна асбеста.
По степени распушки и сохранности пучков волокна после механического обогащения асбест делится на четыре вида: жесткий (Ж), промежуточный, полужесткий (П) и мягкий (М). В промышленности теплоизоляционных материалов обычно используют полужесткий асбест.
В зависимости от длины волокна после распушки и по содержании. Пыли (частиц менее 0.25 мм) и гали (частиц пустой породы более 0.25мм) асбест подразделяют на восемь сортов (0-7). Чем длиннее волокно, тем выше сорт асбеста. Для производства теплоизоляционных изделий используется 5 и 6 сорта (2.5-1 мм).
Качество хризотил-асбеста характеризуется его маркой, которая определяет текстуру и сорт асбеста, а также длину волокна в пределах данного сорта. Длину волокна оценивают как величину остатка (в %), получаемого при просеивании асбеста на сите. Условное обозначении марок включает три эти признака. Например, асбест мягкой текстуры VI сорта, дающий 30% остатка на сите, имеет марку М-6-30. Асбест самых коротковолновых сортов характеризуется сортом и средней плотностью, например, у асбеста VIII сорта, средней плотностью 750 кг/м³ марка 8-750.
Расщепляемость асбеста очень велика. Плотность хризотил-асбеста в зависимости от содержания химически связанной воды и железа находится в пределах 2.4-2.6 г/см³.
При производстве теплоизоляционных материалов асбестовое волокно дополнительно подвергается расщеплению – распушке. При этом возрастает его удельная поверхность, что создает благоприятные условия для образования большого количества пор.
Распушка асбеста производится обычно в два этапа – обмятие на бегунах и затем обработка в быстроходных вертикальных пропеллерных мешалках, работающих в замкнутом цикле.
Бегуны представляют собой два катка катящиеся в горизонтальной чаше.
Под давлением катков слегка смоченных водой (до 20…30%) волокна обминаются, расщепляются и перемешиваются. После обработки на бегунах асбест поступает в быстроходный пропеллерный смеситель, частота вращения которого 500-700 об/мин. В смесителе асбест разбавляется водой в соотношении 1:20 по массе. Время мокрой распушки 15-20 мин.
Добавка асбестового волокна к основному компоненту теплоизоляционного материала способствует снижению средней плотности, повышению прочности, предотвращает трещинообразование, как в процессе сушки, так и при эксплуатации.
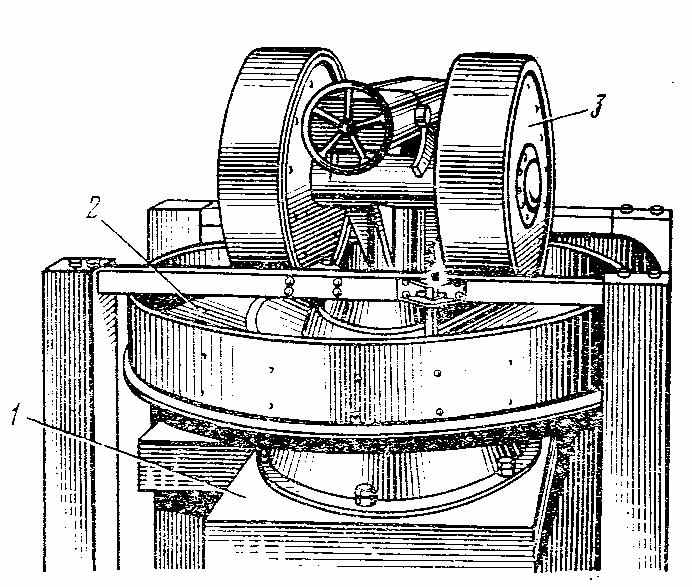

Асбестотрепельные материалы
Наиболее широко распространен асбестотрепельный материал – асбозурит, состоящий из 15-30% (по массе) асбеста и 70-85% трепела. Материалы с добавками слюды, шиферных отходов, вермикулита называют асбослюдой, асботермитом, асбозонолитом.
Это порошки, которые при затворении водой применяют как мастичную изоляцию, главным образом для заделки швов. Например, Асбозурит – материал, в состав которого входит не менее 15% асбеста 6-го сорта. Он применяется в виде мастики при температуре не более 900ºС, нанося ее на предварительно нагретую до 150ºС поверхность. По плотности мастика разделяется на три марки: 600, 700, 800, теплопроводность мастики при температуре 298ºК (25ºС) в зависимости от марки колеблется от 0.17 до 0.22 Вт/(м·К)
Асбестодоломитовые (совелитовые) изделия
Совелит – теплоизоляционный материал, состоящий из основного углекислого магния MgCO3, углекислого кальция СаСО3 и распушенного асбеста. Сырьем для производства совелита служат доломит и асбест не ниже 6-го сорта. Доломит – осадочная горная порода, состоящая из карбоната кальция и магния СаСО3·MgCO3. Требуется доломит с содержанием окиси магния не менее 18%.
Совелитовые изделия выпускаются в виде плит, реже в виде полуцилиндров и сегментов. Совелитовые изделия применяют для тепловой изоляции промышленных установок и трубопроводов при температуре изолируемых поверхностей до 500ºС. По плотности изделия делятся на марке 350 и 400.
Технологический процесс производства совелитовых изделий состоит из: распушки асбеста, сортировки и обжига доломита, гашения его после обжига, карбонизации доломитового молока, перекристаллизации соли магния, формования и тепловой обработки. Доломит определенного фракционного состава вместе с углем поступает в шахтную пересыпную печь для обжига. Обожженный при температуре 900-1000ºС доломит, представляющая собой смесь окисей магния и кальция, подается в гасильный аппарат, где образуется доломитовое молоко. Для гашения используется горячая вода температурой 60-70ºС. Затем молоко разбавляется холодной водой. При гашении обожженного доломита получаются мелкие частицы плотного продукта обжига.
Полученное доломитовое молоко подвергается карбонизации, т.е. насыщается углекислым газом. Для этой цели используют углекислый газ, полученный в шахтной печи при обжиге доломита и охлажденный. Карбонизация молока проходит в аппаратах – карбонизаторах при давлении 0.1-0.15 МПа при 25-35ºС. В результате получается мелкий осадок углекислого кальция и игольчатые кристаллы трехводного углекислого магния.
Для получения основы совелита – легкой магнезии – в проваривателе (перекристаллизаторе) происходит перекристаллизация магнезиальной составляющей – трехводного углекислого магния в доломитовом молоке при температуре 95-98ºС. В проваривателе вместе с молоком находится асбест, предварительно прошедший дополнительную распушку на бегунах. В процессе перекристаллизации при работающем смесителе проваривателя сначала перекачивается карбонизированное молоко, а затем подается асбестовая взвесь, предварительно приготовленная в смесителе. Насыщенный пар давлением 04.-0.6 МПа подается после окончания загрузки асбестовой взвеси, температура смеси достигает 96-98ºС.
В результате химической переработки доломита содержание углекислых солей кальция и магния в совелитовой гидромассе достигает 85% по массе. Из полученной гидромассы на прессах при удельном давлении от 0.5 до 1.2 МПа формуют совелитовые изделия – плиты или скорлупы. При этом систематически проверяют температуру и относительную влажность гидромассы (80-90 ºС, 91-92%).
Отпрессованные изделия с относительной влажностью до 75% подвергают тепловой обработке – сушке и прокаливанию.
В результате прокаливания совелитовых изделий на 13- 15% снижается их плотность, при этом незначительно снижается механическая прочность. Основная масса карбоната магния переходит в окись магния с выделением углекислого газа, а карбонат кальция остается без изменений.
Температура теплоносителя в зоне прокаливания должна быть равна 450-600 ºС и со стороны загрузки сырых изделий – 120 ºС. Продолжительность тепловой обработки 14-16 ч. влажность изделий не должна превышать 1,5%.
Совелитовые изделия должны быть правильной формы с прямыми ребрами с углами и ровными гранями, иметь равномерную толщину и однородное строение без пустот и раковин. Изделия упаковывают в деревянные решетчатые ящики. Хранят их в закрытых помещениях в условиях, не допускающих их увлажнения и повреждения.
Асбестоизвестковые кремнеземистые изделия
Их изготовляют из извести, кремнеземистого материала (диатомита, трепела, кварцевого песка), асбеста и воды путем автоклавной обработки. Такие изделия выпускаются в виде плит и полуцилиндров и применяют для тепловой изоляции горячих поверхностей трубопроводов и промышленного оборудования с температурой до 600ºС. Плотность изделий 200-225кг/м³, предел прочности при изгибе 0.3-0.35 МПа, теплопроводности 0.062-0.065 Вт/м·К.
Известково-кремнеземистые изделия изготовляют по литьевой технологии иногда применяется фильтр-прессовая технология.
Литьевая технология
В этом случае используют формовочную гидромассу с основностью известково-кремнеземистой смеси:
(CaO+MgO)акт/(SiO2+Al2O3)=0.65-0,8
Содержание асбеста – 20-25% по массе. Относительная влажность гидромассы 80-82%. В качестве кремнеземистого компонента применяют породы с большим содержанием высокодисперсного активного кремнезема – трепелы, диатомиты, реже кварциты и кварцевые пески.
В основе технологического процесса лежит химическое взаимодействие в процессе тепловлажностной обработки гидрата окиси кальция Са(ОН)2 (гашеной извести) с двуокисью кремния SiO2, содержащейся в диатомите и др. В результате этого взаимодействия образуются гидросиликаты кальция, которые придают изделиям прочность. Асбестовое волокно играет роль армирующего вещества.
Известь получают из известняка в шахтной печи и гасят, получая известь-пушонку. При производстве известково-кремнеземистых изделий состав по массе в % формовочной массы: известь – 30, гипс – 10, диатомит – 45, асбест 6-го сорта – 15. Относительная влажность формовочной массы 80-82% по массе.
Гашение извести, дробление гипса, распушка асбеста производится непосредственно перед использованием.
Основность известково-кремнеземистой смеси:
(CaO+MgO)акт/(SiO2+Al2O3)=0,65-0,8
Известь гасят в молоко в известегасильном аппарате. Молоко насосом или самотеком подают в расходные мешалки. Активность известкового молока должна быть не менее 60% в пересчете на сухое вещество.
Известковое молоко смешивают с кремнеземистым компонентом и водой в мешалке до получения известково-кремнеземистого шлама относительной влажностью 70-72%.
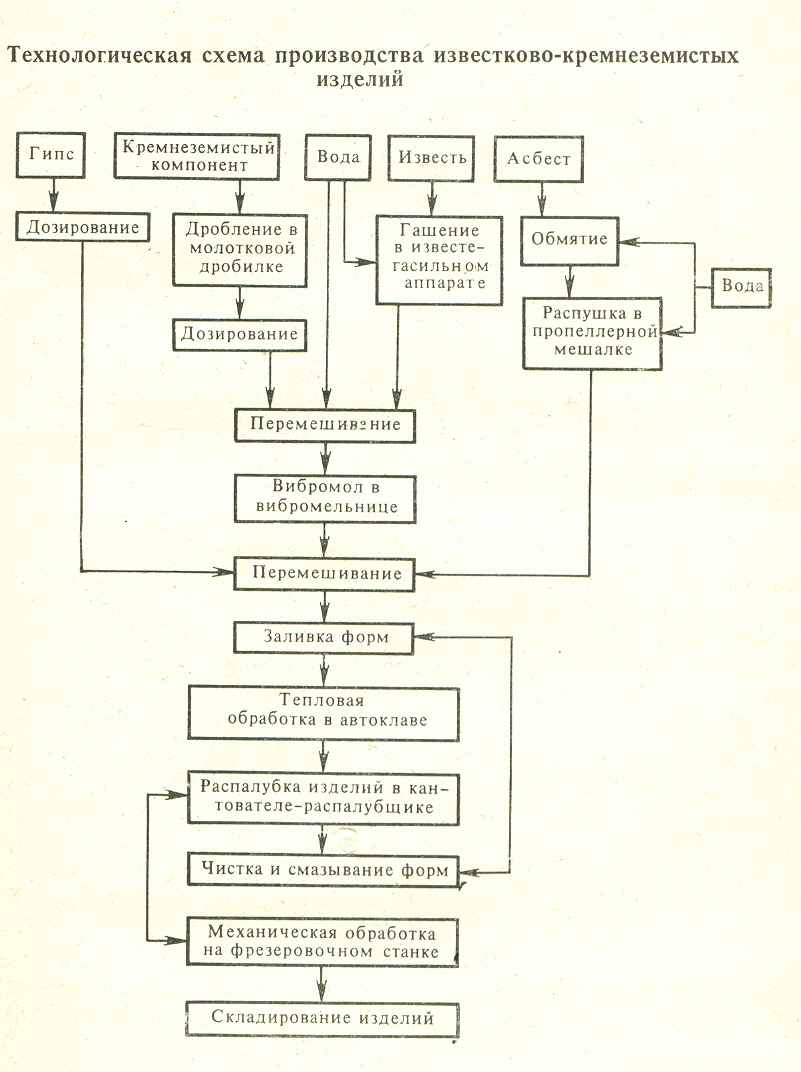
Рис. 21.
Асбест загружают в бегуны порциями по 125-170 кг, увлажняют из мерного бачка до относительной влажности 20-30%, обминают в течение 20-30 мин. порцию обмятого асбеста размешивают с водой в соотношении 12:1 (вода: асбест). Распушивают асбест путем обработки асбестовой пульпы в быстроходной пропеллерной мешалке в течение 15…20 мин. Степень распушки должна быть не менее 60%.
Известково-кремнеземистый шлам размалывают в вибромельницах до частиц менее 0.085 мм. Шлам и асбестовую суспензию дозируют в расчетном соотношении по объему и смешивают в мешалке для получения гидромассы. Чтобы сократить сроки твердения при тепловлажностной обработке, в мешалку добавляют гипс.
Компоненты перемешивают в мешалке до получения гомогенной гидромассы в течение 15-30 мин. Гидромассу заливают в смазанные металлические сварные формы. Борта форм выполнены с уклоном для облегчения выемки затвердевших изделий. Массу заливают через патрубки с пробковыми кранами. При изготовлении известково-кремнеземистых изделий применяют совмещенный метод тепловлажностной обработки и сушки изделий под давлением в автоклаве.
В автоклав, загруженный формами с гидромассой, подается неострый пар. Теплоноситель поступает в нагревательные панели, установленные внутри автоклава. Масса в формах нагревается, вода постепенно начинает испаряться и давление в нем растет. Когда давление достигает 0.8-1 МПа, избыточный пар сбрасывается через клапан, поддерживая давление на заданном уровне. Пар выпускают из автоклава до тех пор, пока влажность изделий не достигнет заданной величины. При этом образуется структура материала и производится сушка изделий в одном аппарате, что сокращает время изготовления изделий.
Режим совмещенного процесса для плит размером 1000х500х80 мм следующий: подъем давления в автоклаве до 0.8-1 МПа – 1ч; сушка при давлении 0.8-1 МПа и температуре 230-250ºС – 18 ч; сброс давления до атмосферного – 3 ч; конечная абсолютная влажность плит – 10-15%.
Изделия после тепловлажностной обработки подвергаются механической обработке. Затем электрокарами они транспортируются на склад готовой продукции, где укладываются в штабеля высотой до 1.5 м.
Фильтр-прессовая технология
Состав гидромассы, подготовка компонентов и помол известково-диатомитового шлама такой же, как и при литьевой технологии. Гидромасса разбавляется водой до В/Т=13-14 и нагревается острым паром до температуры 95-96ºС в мешалке. После выдерживания гидромассы при температуре 95ºС в течение 2-3 ч. изделия формуют методом фильтр-прессования. Отформованные изделия с влажностью 78-80% направляют в контейнере на гидротермальную обработку и сушку в автоклав совмещенной обработки. По окончании обработки кран-балка переносит контейнер с изделиями на склад готовой продукции, где изделия укладываются в штабеля.
Фильтр-прессовая технология по сравнению с литьевой упрощает технологический процесс, улучшает санитарно-технические условия, т.к. не нужны формы и механическая обработка изделий.
Асбестомагнезиальные изделия
Они представляют собой смесь асбеста и основной магнезиальной соли (магнезия-альба) состава 4MgCO3·Mg(OH)2·4H2O. Основной гидрокарбонат магния имеет много воздушных пор, которые находятся между его мельчайшими кристаллами. Магнезию-альбу изготовляют из магнезита, доломита или рапы (морская вода с высокой концентрацией соли). Наиболее распространен магнезиальный порошок – ньювель. Это высококачественный теплоизоляционный материал, однако, вследствие сложности технологического процесса он оказался менее конкурентоспособным, чем другие теплоизоляционные материалы.
Магнезия «Ньювель» - порошкообразный материал, состоящий из магнезии (карбоната магния) – 85% и асбеста не ниже 3-го сорта – 15%. Сырьем для производства магнезии служит магнезит – горная порода, состоящая из углекислой соли магния. Магнезия – это мелкокристаллический порошок высокой пористости (до 94%) и малой плотности. Плотность магнезии «Ньювель» составляет не более 198 кг/м³, а теплопроводность – 0.08 Вт/(м·К). Из «Ньювеля» получают изделия в виде скорлуп, плит, сегментов плотностью до 300 кг/м³ и теплопроводностью 0.1 Вт/(м·К). Предельная температура применения этого материала 330ºС.
Технология органических изоляционных материалов
Древесноволокнистые плиты
Древесноволокнистыми плитами (ДВП) называют крупноразмерные изделия в виде листов, получаемые последовательным измельчением древесины в волокнистую массу, формованием из неё плит и тепловой их обработки. В зависимости от назначения и свойств они делятся на: изоляционные (мягкие плиты), используемые для устройства тепло- и звукоизоляции зданий, и твёрдые (полутвёрдые, твёрдые и сверхтвёрдые плиты), применяемые в качестве отделочного и конструктивного материала для строительства, мебельного, тарного и других производств.
Виды и свойства ДВП
ДВП различаются по внешнему виду, размерам и свойствам. В зависимости от степени уплотнения при изготовлении ДВП могут быть мягкими (М), полутвёрдыми (ПТ), твёрдыми (Т) и сверхтвёрдыми (СТ). Здесь основным показателем служит средняя плотность.
Поверхность плит бывает необработанной, покрытой краской либо эмалью или облицованной плёнкой, чаще всего имитирующей текстуру ценных пород древесины.
Плиты могут быть сплошными, перфорированными с несквозной или сквозной круглой или щелевидной перфорацией, однослойными, либо двухслойными.
Одним из основных достоинств древесноволокнистых плит является анизотропия свойств у изделий больших размеров.
Прочность плит при растяжении меньше прочности при изгибе в 1,5 раза. Пористость ДВП можно регулировать, изменяя тонкость помола волокна, давление подпрессовки при отливе ковра и другие технологические факторы. Пористость ДВП важна только для мягких видов, используемых для теплоизоляции и звукопоглощения. Пористость мягких плит достигает 30%.
Водостойкость ДВП всех видов невысока. У мягких плит она достигает за 2 ч. 12-13%, водопоглощение твёрдых плит 7-12%, гигроскопичность мягких плит при относительной влажности воздуха 100% составляет 10-12%, а твёрдых 7-8%.
Влажные плиты разбухают, особенно у кромок коробятся, прочность их снижается, а теплопроводность возрастает, развиваются грибки.
Для придания плитам водоотталкивающих свойств их пропитывают гидрофобными веществами перед отливом гидромассы на отливной машине либо после прессования, которому подвергаются только твёрдые плиты.
Теплопроводность плит низкая, а её абсолютные значения зависят от пористости и влажности. Теплопроводность у мягких плит – 0,054-0,093 Вт/(моС), для твёрдых – 0,163-0,233 Вт/(моС).
ДВП легко воспламеняются и могут долго тлеть. Повышают их огнестойкость, вводя в гидромассу антипирены или покрывая готовые плиты огнезащитными составами. Предельная температура применения ДВП – 100оС. Они обладают хорошими акустическими свойствами, для большего усиления этих свойств на поверхности плит нарезают канавки или наносят перфорацию.
Сырьевые материалы
ДВП можно изготовлять из любого волокнистого материала растительного происхождения, если его волокна достаточно длинные, гибкие и прочные.
Сырьём для производства ДВП служит древесина, а также стебли некоторых растений. Можно использовать непромышленную древесину хвойных (сосна, ель, пихта, кедр) и лиственных (осина, берёза, тополь, ива, липа) пород; отходы при заготовке леса (сучья, ветви), отходы от распила (горбыль, рейка) и деревообработки; отходы целлюлозно-бумажной промышленности (сучки, непроваренные волокна), макулатуру и др. Что применять, зависит от стоимости доставки и заготовки в данном районе.
Основным видом сырья служит древесина. Она состоит из целлюлозы, лигнина и гемицеллюлозы, образующих оболочку клеток, а также смол, эфирных масел, дубильных веществ, красящих, веществ.
Целлюлоза – химически стойкое вещество, не растворяющееся в воде и гидролизующиеся (распадается под действием воды на отдельные молекулы) при давлении 1-1,5 МПа и температуре 180оС . Строение её кристаллическое, состоит она из кристаллитов-мицелл в виде палочек длиной 500-700оА и толщиной 50-60оА. Мицеллы образуют фибриллы толщиной 3000-5000оА. Фибриллы и мицеллы составляют клетки удлинённой волокнообразной формы. У древесины хвойных пород клетки длиннее и прочнее, поэтому ей отдаётся предпочтение. Особенно при изготовлении плит мокрым способом, где содержание лиственных пород должно быть не более 30%.
Лигнин является аморфным веществом со сложным химическим составом. Химически он менее стоек по сравнению с целлюлозой, но он гидролизуется. В производстве ДВП лигнин повышает выход массы и в процессе прессования способствует образованию дополнительных связей между волокнами. Гемицеллюлоза по составу близка к целлюлозе и состоит из пентозанов и гексозанов. Гексозаны при горячем прессовании гидролизуются и способствуют образованию смолоподобных продуктов.
Технология ДВП
Получение ДВП состоит из двух основных этапов: последовательного измельчения древесины в волокнистую массу и изготовления из неё плит. Распространены два способа производства ДВП – мокрый и сухой. При сухом способе изделия изготавливают из сухой волокнистой массы, при мокром из гидромассы. Мокрым способом можно получать плиты всех видов, а сухим – только твёрдые и сверхтвёрдые.
Физико-химические основы получения ДВП
Принцип производства ДВП основан на свойствах растительных волокон образовывать каркас в процессе удаления воды из суспензии волокна на сетке. При мокром способе в процессе формирования полотна гидромасса обезвоживается сначала за счёт свободной фильтрации воды через сетку, а затем с помощью вакуумирования и подпрессовывания происходит свойлачивание волокнистого ковра.
Если масса состоит из коротких волокон, ковёр получается рыхлый и прочность плит невелика; если волокна длинные, то свойлачивание большое, прочность высокая, однако плохо удаляется вода из гидромассы.
Мягкие ДВП получают только формованием ковра на сетке. Полутвёрдые и твёрдые плиты должны обладать более высокой прочностью, поэтому после формования полотна его подвергают горячему прессованию. При прессовании происходит сближение волокон, увеличивается их сцепление, а значит и прочность плит. Под действием высокой температуры Гексозаны, входящие в гемицеллюлозу, гидролизуются и способствуют образованию смолоподобных продуктов, которые являются связующими.
Сухой способ получения ДВП предусматривает образование ковра в воздушном потоке, потому значение переплетения волокон здесь невелико. Прочность плит, полученных сухим способом, обеспечивают, вводя специальные связующие в момент переработки щепы в волокно. При горячем прессовании под действием высокой температуры пропитанные волокна склеиваются, происходит отвердение связующего. Мы рассмотрим мокрый способ приготовления ДВП.
Производство ДВП мокрым способом
Приготовление щепы. Поступившее на завод сырьё окоривают в корообдирочных барабанах, водоструйных корообдирках или на ножевых корообдирочных станках. Кора ухудшает внешний вид плит, увеличивает их водопоглощение и снижает механическую прочность.
Длинномерную древесину распиливают дисковыми пилами с горизонтальной (балансирные пилы) или вертикальной (маятниковые пилы), качающейся рамкой на балансирных станках.
Толстые чурки раскалывают на дровокольных станках неподвижным или движущимся поступательно-возвратно клином.
Щепа для приготовления волокна должна быть следующих размеров: длина вдоль волокон 10-35 мм, поперёк волокон – до 25мм, толщина щепы не должна превышать 7мм.
Содержание гнили в щепе не более 5%. Крупная щепа снижает производительность машин, мелкая щепа влияет на уменьшение прочности плит.
Для получения щепы применяют дисковые либо барабанные рубильные машины. Механизмом резания рубильных машин является диск или барабан с закреплёнными на нём режущими ножами. При измельчении щепа получается разных фракций, поэтому её сортируют на сортировочных машинах. Перед сортировкой она проходит электромагнит для отделения металлических включений. Щепу кондиционных фракций промывают сначала в промывочном баке при полном погружении щепы в воду, а затем на обезвоживающем винтовом конвейере, где щепу дополнительно обрабатывают свежей водой. Затем щепа подаётся к размолочным агрегатам, где превращается в волокнистую массу.
Получение древесного волокна. Размол древесины состоит в разделении щепы вдоль волокон на пучки волокон или отдельные волокна, укорачивания их и дальнейшего расщепления волокон в продольном направлении. Размол может быть тонким и грубым. Тонкий размол характеризуется длинными, тонкими, гибкими, медленно обезвоживающимися волокнами, что обеспечивает хорошее переплетение волокон и высокую прочность плит. При грубом размоле масса состоит из укороченных либо неукороченных, плохорасщеплённых волокон, быстро отдающих воду и образующих рыхлый ковёр с плохим переплетением волокон. Если волокна настолько укорочены, что не образуют переплетения и свежесформированное полотно не обладает транспортной прочностью, размол называют “мёртвым”.
Таким образом, тонкость помола массы определяет скорость её обезвоживания, для её определения сконструированы специальные приборы. Средняя длина и диаметр волокон древесной массы составляют соответственно от сотых долей миллиметра до 3-4 мм и 30-50 мм.
Существует три способа получения волокна из древесины: механический, термомеханический и химико-механический.
Механический основан на истирании чурков быстровращающимися рифлёными дисками или цилиндрами с прогревом или без прогрева древесины, с использованием химических средств облегчающих размол или без них. Этот способ практически не нашёл применения.
Термомеханический способ заключается в нагреве древесины горячей водой (не ниже 70оС) или паром высокого давления и последующем расщеплении древесины на волокна между двумя рифлёными дисками, вращающимися с разной скоростью или в разные стороны. Под действием тепла и влаги лигнин древесины размягчается, ослабляя связи между волокнами. Способ характеризуется сохранением структуры волокон при высокой тонкости помола. В зависимости от требуемой тонкости размол осуществляют в одну или в две стадии. Для первичного размола применяют быстроходные рафинеры и дефибраторы, для повторного – рафинаторы, рафинеры, голлендеры. Этот способ наиболее распространён, он требует малых затрат энергии.
Химико-механический способ основан на различной растворимости компонентов древесины в слабом растворе щёлочи и реализуется в два этапа: проваривание древесной щепы в слабом щелочном растворе и механический размол проваренной щепы. При варке древесины в горячем слабощелочном растворе происходит полное постепенное растворение лигнина и других веществ, соединяющих волокна. Это способствует получению эластичных длинных волокон, пригодных в производстве высококачественных мягких плит. Но способ не получил широкого распространения из-за сложности процесса и малого выхода древесины (60%).
Полученную при первичном размоле древесную массу разбавляют водой до концентрации 0.3-0.5% и подвергают мокрой сортировке, а недомолотые и плохо гидратированные частицы сгущают до концентрации 4-5% и измельчают вторично.
Проклейка ДВ массы. Из размольных агрегатов волокнистая масса поступает в массные бассейны для выравнивания концентрации и обработки эмульсиями химических веществ (проклейки), чтобы улучшить свойства готовых плит. Прочность ДВП повышают проклейкой массы водными эмульсиями окисляющих масел (льняного, конопляного), либо синтетических (фенолформальдегидных) смол. Повышение водостойкости обеспечивается введением гидрофобных эмульсий, в основном парафиновой, канифольной, битумной в количестве до 2%.
Осаждается эмульсия на волокно в кислой среде рН=4-5. Для получения такой среды в гидромассу вводят осадительную серную кислоту (1%) или сернокислый глинозём (0,5%).
Для повышения биостойкости в гидромассу вводят антисептики (фтористый и кремнефтористый натрий, креозол). Огнестойкость повышают за счёт введения антипиренов (сернокислого аммония, железоаммонифосфата). Однако введение этих водорастворимых добавок эффективно лишь при сухом способе производства. При производстве плит мокрым способом значительная часть добавок уходит с отжимными водами. Вводят добавки при интенсивном перемешивании гидромассы в ящике непрерывной проклейки. Проклеенную массу разбавляют водой до концентрации 0,9-2,2% и подают в отливочную машину.
Формование плит. Обезвоживание волокнистой массы на отливочных машинах происходит последовательно путём свободной фильтрации воды через сетку, отсоса её вакуумированием и отжима прессованием.
При фильтрации взвешенные волокна сближаются и переплетаются, происходит свойлачивание. Гидромасса обезвоживается и на сетке машины формируется ковёр с относительной влажностью 90-92%. Дальнейшее понижение влажности ковра (до влажности 65-70%) производят вакуумированием и отжимом.
Формование ДВП осуществляют на отливочных машинах трёх основных типов: периодически действующих с формующим ящиком, длинносеточных вакуумфильтрующих непрерывного действия. Больше всего применяют длинносеточные отливочные машины.
Гидромасса через щель поступает на непрерывно движущуюся ленту отливочной машины, ограждённую бортами. Чтобы улучшить переплетение волокон, на отливочных машинах устанавливают вертикальный вибратор. При концентрации массы 7-10% свободная фильтрация воды прекращается, и гидромасса поступает в отсасывающую часть машины, где концентрация её повышается до 12-16%. Дальнейшее обезвоживание полотна происходит между двумя сетками в прессовой части машины, состоящей из системы нескольких прессов. По мере прохождения ковра через прессы давление на него увеличивается. Отформованный влажный ковёр, пройдя пилы продольной и поперечной резки, подвергается тепловой обработке.
Тепловая обработка плит. Мягкие плиты с относительной влажностью 60-65% сушат в трёхзонных многоэтажных роликовых сушилках непрерывного действия в процессе противоточной сушки с рециркуляцией. Длина роликовых сушилок достигает 30-90 м, чаще 36 м; длительность сушки при температуре 130-160оС – около 3 часов. В конце сушки предусмотрена зона охлаждения.
Твёрдые плиты влажностью 65-70% подвергают прессованию в горячих гидравлических многоэтажных прессах, обогреваемых паром высокого давления или электричеством. Применение горячего прессования обеспечивает удаление влаги и сближение волокон, при котором между волокнами возникают внутренние молекулярные силы сцепления. Высокая температура прессования (свыше170оС) способствует размягчению оставшегося лигнина, что увеличивает пластичность волокон и их большее уплотнение при прессовании. В отечественной практике применяют горячие гидравлические прессы общей мощностью 4-5,3 тыс. т. с давлением при прессовании до 5,5 МПа. Длительность цикла прессования составляет 8-15 мин.
Для повышения качества твёрдых плит после прессования их пропитывают высыхающими маслами – тунговым, льняным и т.п. Пропитку ведут, погружая плиты в ванну с горячим маслом (110-120оС), в течение 30 сек. Для понижения водопоглощения и повышения прочности твёрдые плиты подвергают закалке горячим воздухом с температурой 150-170оС в закалочных камерах в течение 2-3 часов. Из камеры плиты выходят сухими и для избежания коробления их пропускают через увлажнительные камеры до достижения влажности 6-10%. В камерах используют в течение 6-8 часов прогретый воздух. Плиты раскраивают в соответствии в заданными размерами на форматно-обрезных станках. Отделка заключается в окраске эмалями или облицовке твёрдых плит плёнками.
Применение ДВП. Мягкие ДВП широко используются в строительстве для утепления стен, полов и потолков щитовых панельных и каркасных домов стандартного домостроения. Их также применяют в качестве выравнивающих слоёв под твёрдые покрытия полов и звукоизоляционных прокладок.
Твёрдые ДВП идут для облицовки каркасных перегородок, стен и потолков жилых, общественных и производственных зданий, для изготовления щитовых дверей, деталей встроенных шкафов, мебели, тары различных видов.
Фибролит
Фибролит представляет собой плитный материал из спрессованной древесной шерсти, склеенной затвердевшим минеральным вяжущим. По назначению фибролит может быть теплоизоляционным, теплоизоляционно-конструкционным и акустическим. В СССР фибролит выпускают более чем на 40 предприятиях общим объёмом около 3 млн. м3 плит в год – это свыше 9 % общего выпуска теплоизоляционных материалов. Известны разновидности фибролита: магнезиальный, магнезиально-доломитовый, термоксизол, известковый, цементно-известковый, известково-трепельный, гипсовый.
Свойства цементного фибролита
Пористость. Фибролит имеет крупнопористое неоднородное волокнистое строение с сообщающимися порами. При средней плотности 300-500 кг/м3 пористость 87-77%.
Плотность и прочность. В зависимости от средней плотности выпускают фибролит марок 300, 350, 400 и 500. 80% объёма продукции занимает фибролит с маркой 300. Средняя плотность у теплоизоляционного фибролита 300-350 кг/м3, акустического 350-400, теплоизоляционно-конструкционного – 400-500 кг/м3. С увеличением средней плотности увеличивается прочность на изгиб, огнестойкость плит, теплозащитные свойства ухудшаются. На прочность фибролита влияют также размеры и качество древесной шерсти, расход вяжущего, толщина плит, усилие прессования, режим тепловой обработки. Прочность на изгиб фибролита составляет 0,4-1,2 МПа. У фибролита мягкая водостойкость, его защищают от увлажнения. Водопоглощение составляет 35-60%, что снимает прочность в 1,5-2 раза. Гигроскопичность цементно-фибролитовых плит маленькая.
Теплопроводность. Фибролит имеет низкую теплопроводность 0,099-0,151 Вт/(моС). Но при увлажнении плит на 1% теплопроводность повышается на 5-14%.
У фибролита хорошее звукопоглощение благодаря открытой сильно развитой пористой структуре. Коэффициент звукопоглощения неоштукатуренных плит при частоте колебаний 1000Гц и толщине плит 30 мм составляет 0,4.
По огнестойкости фибролитовые плиты относятся к трудносгораемым материалам; фибролит не горит, но тлеет. В сухом состоянии фибролит биостоек, но при увлажнении свыше 35% он поражается домовым грибом. Фибролит легко подвергается механической обработке, хорошо держит гвозди, он хорошо поддаётся оштукатуриванию и окраске.
Сырьевые материалы. Сырьём для изготовления цементного фибролита является древесина в виде древесной шерсти, цемент, минерализующие добавки, вода.
Древесную шерсть получают из неделовой древесины в виде дровяника, тонкомерного кругляка и отходов лесопиления без гнили. В древесине содержатся водорастворимые вещества, простые сахара, которые вредно влияют на процессы схватывания и твердения цемента. Содержание этих веществ зависит от породы, части дерева и его возраста, времени рубки, сроков выдержки на складах. Наименьшее количество веществ у ели, затем идут пихта, тополь, сосна. Поэтому древесную шерсть получают преимущественно из хвойных пород.
Древесная шерсть – длинная тонкая древесная стружка длиной 200-500 мм, шириной 25 мм и толщиной 0,3-0,5 мм. Если толщина меньше – снижается прочность плит; - больше – стружка менее эластичная и ломкая. В качестве добавки иногда используют обычную древесную стружку от строительных станков.
Для изготовления фибролитовых плит обычно применяют портландцемент марки не ниже 400, быстротвердеющий цемент либо шлакопортландцемент. Выбор марки зависит от назначения фибролита. Для нейтрализации вредного действия на цемент водорастворимых веществ шерсти и улучшения её сцепления с цементом, древесную шерсть пропитывают растворами минеральных веществ – минерализаторов. Это хлористый кальций, растворимое стекло и др. Вводят минерализатор в строго определённом количестве, отклонение резко снимает прочность плит.
Технология цементного фибролита
Физико-химическая основа технологии. Получение фибролитовых плит основано на возможности получения из древесины длинной стружки и её скрепления гидравлическим вяжущим.
Особенности взаимодействия древесины с цементом. Древесина содержит сложный комплекс веществ органического происхождения: целлюлозу, лигнин, гемицеллюлозу, экстрактивные и смолистые вещества, простейшие сахара и минеральные соли. При попадании в щелочную среду раствора цемента гемицеллюлоза гидролизуется и переходит в простейшие водорастворимые сахара (сахарозу, фруктозу, глюкозу), являющиеся сильнейшими “цементными ядами”. Остальные вещества древесины не оказывают влияние на процесс твердения цемента. Простейшие сахара же замедляют процесс твердения цемента вплоть до полного прекращения, снижают его прочность. Для устранения вредного действия сахаров проводят специальную биохимическую, физическую и химическую обработку древесины.
Производство фибролитовых плит
Оно может быть организованно по сухому и мокрому способу.
Мокрый способ заключается в окунании древесной шерсти в ванную с водным раствором цемента и минерализатора с последующим удалением излишнего раствора на виброгрохоте. Этот способ требует постоянного перемешивания цементного раствора во избежание его расслоения, введения в массу большого количества воды, что отрицательно сказывается на качестве плит. Кроме того, цемент часто отверждается в ванне, что приводит к значительным потерям материала и рабочего времени. Наиболее распространён сухой способ изготовления цементного фибролита, включающий получение шерсти, приготовления формовочной смеси, формование, прессование и тепловую обработку плит.
Подготовка сырья. Поступающую на завод древесину окоривают и отправляют на выдержку, чтобы устранить вредное действие “цементных ядов”. Древесину выдерживают на открытом воздухе не менее 4-6 весенне-летних месяцев. Под действием солнечных лучей и тепла происходит окисление веществ и перевод простейших сахаров в менее растворимые формы. После выдержки древесину распиливают на чурки, удаляют гниль и другие пороки. Затем чурки попадают к древошерстным станкам. Строгальные ножи, укреплённые по торцам ножевой плиты станка, сострагивают шерсть параллельно волокнам древесины. Затем шерсть подсушивают до влажности 20-22% с целью уменьшить отрицательное воздействие экстрактивных веществ на цемент и улучшить минерализацию шерсти, т.к. чем суше древесина, тем глубже проникает в поры раствор минерализатора.
Приготовление формовочной смеси. Минерализацию древесной шерсти проводят, окуная её или обрызгивая 3-4%-ным водным раствором хлористого кальция или растворимого стекла на различных устройствах – шерстетрясах, конвейере с перфорированной лентой, в барабанных смесителях. На шерстетрясах из древесной шерсти отсеивается мелочь и стряхивается излишек раствора минерализатора. Влажность минерализованной шерсти 140-160%. Если используют затем белитовый цемент с малым содержанием алита С3S, то обработку шерсти минерализатором не проводят.
Количество цемента в фибролите зависит от марки плит и вида шерсти. Для плит марки 300 соотношение по массе между древесной шерстью и цементом колеблется в пределах от 1:2,3 до 1:2,7. Влажность шихты для получения плит хорошего качества должна быть 45-50%.
Смешивают компоненты шихты в мешалках принудительного действия, либо в смесителях свободного падения, обеспечивающих перемешивание шерсти без уплотнения.
Формование
Готовая шихта загрузочным конвейером со специальным валковым разделителем и разрыхляющим устройством распределяется по формам и начёсывается вручную или валиками начёса. Прессование плит осуществляется в механических, пневматических или гидравлических прессах при удельном давлении 0,06-0,1 МПа – для получения теплоизоляционного фибролита.
Более тяжелые плиты вырабатывают на гидравлических прессах при удельном давлении прессования 0,25-0,4 МПа.
Тепловая обработка фибролитовых плит осуществляется в два этапа: вначале в формах и затем без форм. Формы в пакетах поступают в камеру твердения, где их выдерживают при относительной влажности 60-70% и температуре 30-35оС. Время выдержки в камерах твердения 8 часов при использовании быстротвердеющего портландцемента до 24 часов при обычном портландцементе. Затем плиты освобождают из форм, обрезают боковые и торцевые кромки и сушат 5-7 суток до остаточной влажности 15-20% на открытом воздухе под навесом или в сушильных отделениях при температуре 59-60оС, относительной влажности 60-70% в течение1-2 суток. По окончании сушки остывшие плиты сортируют и отправляют на склад. Созданы автоматические поточные линии производства цементного фибролита.
При изготовлении фибролита необходимо соблюдать правила охраны труда и техники безопасности, а именно: оградить движущиеся и вращающиеся части всех механизмов, а также резервуары, бассейны и другие ёмкости; заземлить электрооборудование и устройство теплоизоляции на всех тепловых установках и паропроводах. Необходимо устраивать вентиляцию, особенно в местах выделения паров вредных и токсичных веществ. Меры пожарной и взрывобезопасности сводятся к регулярному удалению древесной пыли у мест её интенсивного выделения и с нагретых поверхностей, устройству вентиляции у мест окраски плит и т.п.
Области применения фибролитовых плит
Фибролит – транспортабельный жёсткий утеплитель, перевозки которого не ухудшают его качества. При изготовлении 1 м3 теплоизоляционного фибролита расходуется 0,4 м3 древесины, 170-200 кг цемента, 7 кг хлористого кальция.
Теплоизоляционные фибролитовые плиты марки 300 применяют для утепления ограждающих конструкций щитовых и стандартных каркасных деревянных домов, сельскохозяйственных построек различного назначения, жилых, общественных и промышленных зданий. Их используют для изготовления утеплённых стеновых железобетонных панелей, облегчённых фибролито-асбестоцементных панелей и т.п.
Акустические фибролитовые плиты толщиной 30 мм применяют как декоративно-акустический материал для помещений, требуется специальный акустический режим – машинописных бюро, операционных залов, зрительных залов и т.п.
Конструктивные фибролитовые плиты используют для устройства перегородок и покрытий сельскохозяйственных построек, а также стен в стандартном деревянном домостроении.
Торфяные теплоизоляционные изделия
Торфяные теплоизоляционные изделия изготовляют в виде плит, скорлуп и сегментов. Наибольшее распространение получили торфяные плиты размером 1000х500х30 мм. Их изготавливают из слаборазложившегося торфа, содержащего не менее 80% мха-сфагнума. В процессе переработки волокна склеиваются из торфа. В зависимости от назначения плиты могут быть обыкновенными и со специальными добавками: водостойкими В, трудносгораемыми О, биостойкими Б, комплексными – имеющих несколько этих свойств. Их выпускают более 6 млн. м³ в год.
Свойства торфяных плит
Пористость. Торфяные плиты имеют однородную волокнистую структуру мелкопористого строения с открытыми сообщающимися порами. Абсолютные значения пористости колеблются в пределах 84-91%.
Плотность и прочность. При производстве плит структура торфа нарушается незначительно, и средняя плотность их близка к плотности торфа сырца и составляет 170-260 кг/м³.
По средней плотности торфяные плиты относятся к группе высокоэффективных теплоизоляционных материалов. Предел прочности на изгиб 0.3-0.5 МПа, что позволяет легко их транспортировать и монтировать.
Водопоглощение плит высокое. Так водопоглощение обычных плит (по массе) за 24 ч. составляет 190-180%, а специальных водостойких – 50%.
Теплопроводность торфяных плит в сухом состоянии невелика 0.052-0.075 Вт/(мºC).
Огнестойкость. Торфяные плиты – сгорающий материал. Температура их воспламенения около 160ºC, а самовоспламенения 300ºC. В увлажненном состоянии в штабелях они самовозгораются при более низкой температуре, поэтому их предельная температура эксплуатации 100ºC для обыкновенных плит.
У торфяных плит удовлетворительное звукопоглощение, высокая адсорбционная способность (хорошо впитывают газы), отсутствие запаха, и невосприимчивость к запахам хранящихся продуктов.
Сырьевые материалы
Торф является продуктом естественного отмирания и неполного распада болотных растений в условиях избыточного увлажнения и затрудненного доступа воздуха. Сырьем для плит служит только сфагновый торф, сохраняющий рыхлое волокнистое строение торфообразующих растений (85-90% остатков мхов рода сфагнум). Средняя степень разложения торфа должна быть в пределах 5-10, но не более 12%. Торф в естественном состоянии характеризуется значительной влажностью 91-96%, пористость 96-97%, плотность в сухом состоянии 0.3 г/м³.