Советник раасн, профессор каф. Строительного материаловедения и специальных технологий д т. н. Акулова М. В
Вид материала | Документы |
- Разработчики программы повышения квалификации: Галимов Энгель Рафикович, д т. н., профессор,, 226.46kb.
- Региональное Отделение Российского Философского Общества Саратовский государственный, 223.62kb.
- Разработчики программы повышения квалификации: Алиева Б. Ш. д пед н., профессор, каф, 274.72kb.
- Концепция устойчивого развития в стратегии градостроительства франции 05. 23. 22 Градостроительство,, 332.07kb.
- Десятые академические чтения раасн, 2006, 1519.63kb.
- Заровняев Борис Николаевич, д т. н., профессор, зав. Каф. Огр открытых горных работ, 204.45kb.
- Лечение недержания мочи у мужчин о. Б. Лоран, член корр. Рамн, профессор, зав каф урологии, 39.64kb.
- Племяшов К. В., зав кафедрой акушерства, к в. н., Андреев Г. М., профессор каф акушерства,, 51.58kb.
- Кязимов Карл Гасанович Доктор педагогических наук, профессор ргсу, Государственный, 88.92kb.
- Программа для поступающих на Направления подготовки бакалавров 150700 «Машиностроение», 505.68kb.
Следующий этап технологии в производстве волокнистых материалов – это получение расплавов. В минеральных расплавах всегда присутствует SiO2, поэтому они называются силикатными расплавами.
При получении расплавов протекают сложные физико-химические процессы, характер которых определяется составом шихты и температурой. Во всех случая происходят процессы силикато- (400-600ºC) и стеклообразования, наиболее интенсивных при появлении жидкой фазы.
Возможность химических взаимодействий определяется законами химической термодинамики и действием кинетических факторов, таких как поверхность контакта. То есть чем мельче шихта, тем больше площадь контакта зерен компонентов, тем быстрее протекают реакции.
Для перевода твердой фазы в жидкое состояние нужно затратить энергию на преодоление сил, действующих между элементами решетки.
В настоящее время наиболее распространен взгляд на силикатные расплавы как на ионные жидкости. Стеклообразователем или сеткообразователем является кремневая кислоты. Установлено, что из всех связей О2- связь с Si4+ - самая прочная, что обуславливает наличие кремнийкислородных комплексов.
Наличие жесткой направленной ковалентной связи Si-O определяет присутствие в расплавленных силикатах устойчивых комплексных ионов (SiхОу)z, образующих анионный скелет расплава. Внутри этого каркаса преобладают ковалентные, а вне - ионные связи.
Структура силикатных расплавов определяет их свойства. Так вязкость расплавов зависит от подвижности анионного каркаса, а электропроводность от подвижности ионов, поляризующих связи Si-O.
Основными свойствами силикатных расплавов, влияющих на свойства минеральных волокон являются вязкость, поверхностное натяжение и кристаллизационная способность.
Вязкость – свойство жидкостей оказывать сопротивление перемещению одной части жидкости относительно другой, обусловленное внутримолекулярным трением. Силикатные расплавы ведут себя в основном как ньютоновские жидкости, при низких температурах наблюдается признаки структурирования, что приводит к ухудшению качества волокна.
Характер изменения вязкости от температуры определяется составом расплавов. По характеру изменения вязкости от температуры различают «длинные» – с большим интервалом вязкости и «короткие» – малый интервал температур от жидкотекучего до хрупкого состояния. Наиболее целесообразны в производстве минеральной ваты жидкие расплавы.
Поверхностное натяжение σ характеризует интенсивность поверхностных межмолекулярных (межатомных, межионных) сил в расплаве. Образование новой поверхности связано с преодолением сил поверхностного натяжения. Чем оно больше, тем большую работу нужно затратить, чтобы образовать единицу новой поверхности.
На поверхностное натяжение влияет состав и температура расплава. Окислы, входящие в состав расплава делятся на 3 группы: поверхностно-неактивные (SiO2, AI2O3, СаО и др.), промежуточные (К2О, В2О3) и поверхностно-активные (Сr2O3, SO3, WO3 и др.). Наименьшим поверхностным натяжением характеризуются SiO2 и Na2O. Снижение поверхностного натяжения благоприятно сказывается на ходе технологических процессов.
Структура и свойства силикатного расплава зависят от его химического состава. Если катион окисла является комплексообразующим, то количество его содержания в расплаве увеличивает вязкость за счет увеличения размера комплексов, это SiO2, AI2O3, Сr2O3.
При добавлении некомплексообразующих СаО, MgO, NaO, K2O и TiO2 вязкость расплавов уменьшается, так как, превращаясь в катионы, они отдают свой кислород комплексам, прекращая их рост.
Переработка силикатных расплавов в волокно происходит в основном в интервале температур 1300-1400ºС, вязкость при этом должна находится в пределах 0,5 – 5 Па∙с.
Каждый компонент влияет на свойства расплава и минеральной ваты по-разному:
SiO2 – повышает вязкость силикатных расплавов и химическую стойкость волокон в любых средах, удлиняет интервал вязкости;
В2О3 – оказывает сильное флюсующее действие, уменьшает поверхностное натяжение расплава и температуру верхнего предела кристаллизации, значительно улучшает выработанные свойства, увеличивает длину волокна, повышает устойчивость к кислотам и щелочам;
AI2O3 – повышает вязкость и поверхностное натяжение расплавов, прочность и модуль упругости волокон, устойчивость к воде, кислотостойкость, температуростойкость;
Fe2O3 – снижает вязкость расплава, повышает поверхностное натяжение и химическую устойчивость;
СаО, MgO – при высоких температурах понижают вязкость расплава, повышают склонность к кристаллизации. При содержании СаО, равном 45%, вязкость возрастает, так как образуется С2S. Влияние MgO на снижение вязкости особенно заметно при повышении содержания до 9% и более. Повышение содержания MgO за счет СаО приводит к значительному повышению химической стойкости волокон;
TiO2 – улучшает химическую устойчивость ко всем средам, является хорошим плавнем и значительно снижает вязкость расплава, но повышает склонность к кристаллизации;
ZrO2 – очень сильно повышает устойчивость ко всем средам и является единственным окислом, который делает многокомпонентные стекла устойчивыми к щелочам; увеличивает тугоплавкость расплава и повышает склонность к кристаллизации. Введение ZrO2 осуществляется, как правило, за счет SiO2;
FeO – снижает вязкость, но повышает поверхностное натяжение расплава, снижает начальную температуру разрушения волокон, одновременно повышая температуру спекания;
MnO – в небольших количествах увеличивает химическую устойчивость, снижает вязкость и склонность к кристаллизации;
Na2O, K2O, LiO – являются плавнями и снижают склонность к кристаллизации, но уменьшают устойчивость волокон в воде. Повышенное содержание K2O уменьшает поверхностное натяжение расплава.
Расплав для получения рядовой минеральной ваты содержит в основном SiO2, AI2O3, СаО и MgO. Содержание их находится в пределах (% по массе): SiO2 – 35-60, AI2O3 – 5-15, СаО – 20-35, MgO – 5-15. В небольшом количестве могут присутствовать Fe2O3, FeO, Na2O, K2O и MgO.
Превращение силикатного расплава в волокно
Полученный в плавильном агрегате жидкий минеральный расплав перерабатывается в волокно следующими способами: дутьевым, центробежным и комбинированными.
При дутьевом способе расплав (3), непрерывно вытекающий из летки (2) (из фидера) плавильного агрегата (1), раздувается струей энергоносителя, поступающего из дутьевой головки (4), его скорость 400-800 м/с.
В качестве энергоносителя можно использовать перегретый и сухой насыщенный пар, сжатый воздух, горячие продукты сгорания топлива. По направлению струи энергоносителя дутьевой способ разделяется на горизонтальный и вертикальный. При горизонтальном струя энергоносителя направлена на струю расплава под углом 15-20 ºС к горизонтали, при вертикальном – направляется сверху вниз по углом 10-11ºС к вертикали с двух сторон струи расплава.
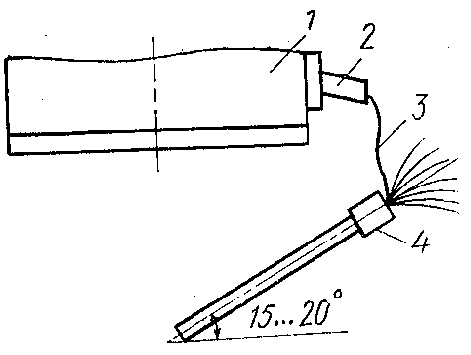
Рис. 10. Схема переработки расплава в волокно дутьевым способом:
1 – плавильный агрегат; 2 – летка плавильного агрегата; 3 – струя расплава;
4 – дутьевая головка
При этом расплав подается на раздув через пластины с отверстиями – фильерами диаметром не более 3 мм. Поэтому способ называется фильерно-дутьевым. При этом способе получается волокно высокого качества с низким содержанием неволокнистых включений.
Применение нагретого пара эффективнее, чем насыщенного сухого пара или газа. Пар поступает из дутьевых головок, которые по принципу действия разделяются на два типа: ударного действия, когда струя пара действует на струю расплава по выходе из дутьевой головки (рис.11), и эжекционные, которые работают по принципу всасывания струи расплава и расчленения внутри головки (рис.11).
Вакуум внутри головки создается за счет высокой скорости движения энергоносителя. С эжекционной головкой получается волокно высокого качества, но они малопроизводительны. Дутьевые головки представляют собой металлические насадки с соплами разных конфигураций. Таким образом, под действием энергоносителя струя расплава 3 температурой 1300 - 1950 ºС дробится на мельчайшие частицы в виде струек и капелек, которые частично вытягиваются в волокно, а частично выпадают в виде неволокнистых включений – «корольков» различной формы. Полученное таким образом волокно поступает в камеру волокно-осаждения.
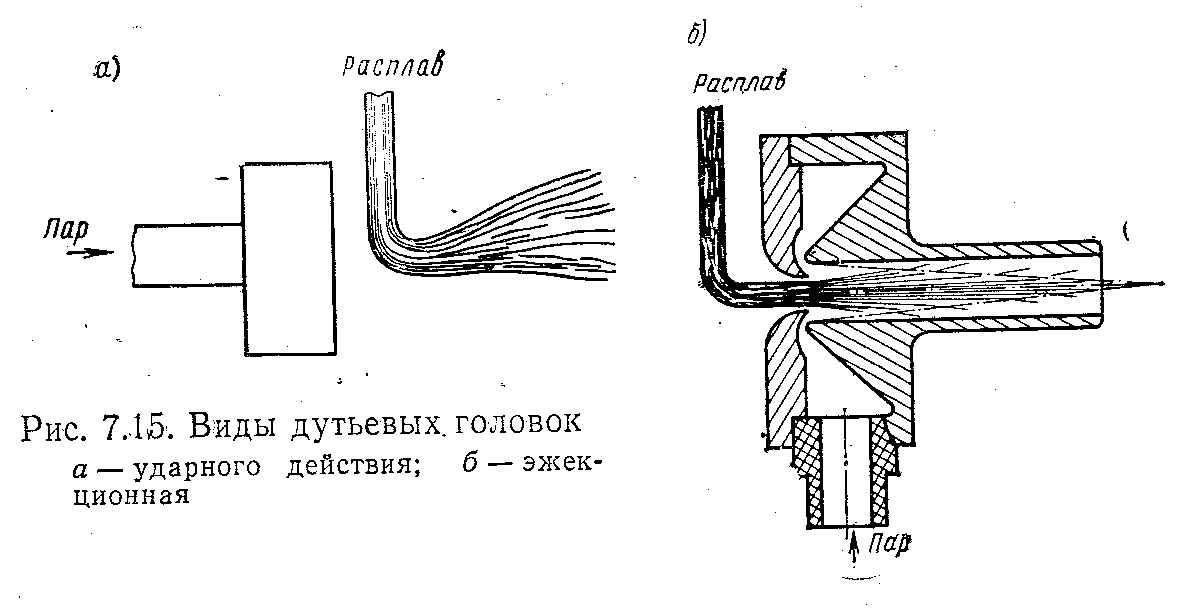
Рис. 11. Виды дутьевых головок:
а – ударного действия; б – эжекционная
Преимущества дутьевого способа – простота и надежность в работе, недостаток – большой расход энергоносителя и низкое качество минеральной ваты.
Центробежный способ. Этот способ основан на использовании центробежной силы вращающихся элементов, на которые подается расплав. Центробежные установки могут быть одноступенчатыми и многоступенчатыми. В одноступенчатой установке расплав обрабатывается в одной центрифуге, в многоступенчатой – последовательно на нескольких центрифугах. По форме рабочего органа центрифуги могут быть дисковыми, чашечными и валковыми; по расположению плоскости вращения – горизонтальными и вертикальными. Наиболее распространены центрифуги со ступенчатым положением валков.
Четырехвалковая центрифуга Ц-5С представляет собой станину П-образной формы, на которой укреплены четыре рабочих валка, приводимых во вращение отдельными электродвигателями. Масса центрифуги 3200 кг, габаритные размеры 2400х1500х2000 мм.
Расплав с температурой около 1400 ºС стекает через лоток на верхний распределительный валок и последовательно обрабатывается всеми валками. Он должен подаваться под углом 30-40º к горизонтальной оси 1-го валка.
Роль первого валка – расцепить струю расплава и предать его в виде множества струй и частиц на второй валок, на котором большая часть расплава передается на 3-й валок. Четвертый валок завершает процесс волокнообразования. Таким образом, основные волокнообразующие валки – второй и третий. Окружная скорость валков различна. Она увеличивается то верхнего валка к нижнему, в связи с понижением температуры и повышением вязкости расплава. Волокно образуется только при прилипании раствора к валкам, оно начинается при прогреве валков до 500-600ºС.
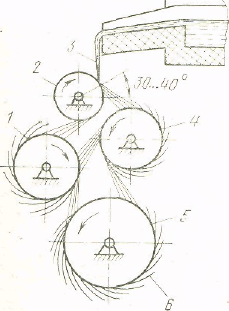
Рис.7. Схема получения стеклянного штапельного волокна многоступенчатым центробежным способом на четырехвалковой центрифуге: 1, 2, 4 и 5 — рабочие валки, 3 — струя расплава, 6 — волокно
Для отдува образующихся волокон на центрифуге установлен вентилятор. Образовавшиеся на валках волокна подхватываются воздушным потоком, подающимся из вентилятора, и уходят в камеру волокноосаждения, где оседают на движущемся конвейере. Застывшие включения падают под центрифугу, откуда удаляются конвейером.
Этот способ позволяет получить продукцию высокого качества. Но имеется ряд конструктивных недостатков – малая стойкость валков, громоздкость, сложность эксплуатации и ремонта.
Комбинированные способы
При комбинированных способах используют как центробежную силу, так и силу дутья. В настоящее время применяют следующие комбинированные способы: центробежно-дутьевой и центробежно-фильерно-дутьевой.
Центробежно-дутьевой способ (ЦДС) включает в себя предварительное механическое центробежное расщепление основной струи расплава и последующее вытягивание частичек расплава в волокна под действием струи энергоносителя (пара или сжатого воздуха). Расплав из вагранки с температурой 1300-1350 ºС по лотку стекает на внутреннюю часть боковой стенки чаши центрифуги. При вращении чаши с частотой 1000-4000 об/мин. расплав распределяется по ее периметру и срывается с кромок чаши в виде пленок, струек и капель. Последние подхватывают поток энергоносителя, и под совместным действием центробежных и аэродинамических сил из струек образуются волокна.
Раздаточные чаши имеют разную конструкцию: медные с водяным охлаждением, керамические неохлаждаемые, стальные с охлаждением и т.д. Вокруг чаши на расстоянии 5-15 мм от ее края находится неподвижное дутьевое кольцо. По окружности его расположены отверстия диаметром 2-4 мм на расстоянии 15-20 мм одно от другого. Чтобы обеспечить большие скорости в качестве энергоносителя, как правило, применяют пар или воздух с давлением 0,6-0,8 МПа. Отверстия в сечение представляют собой сопла. Центрифуги такой конструкции позволяют перерабатывать до 3 т/ч расплава, при выходе минеральной ваты до 75%, средней плотностью 85-120 кг/м³. Они просты в изготовлении и эксплуатации. Устанавливаются по две на вагранку.
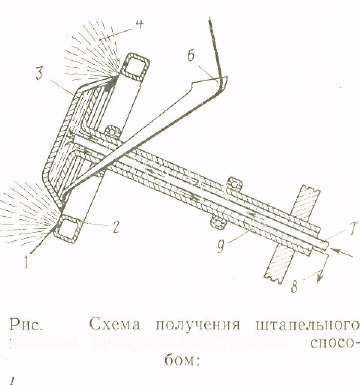
Рис.12. Схема получения штапельного волокна центробежно – дутьевым способом: 1- дутьевое сопло, 2 — паровой или воздушный кольцевой коллектор, 3 — ротор (раздаточная чаша), 4 — волокно, 5 — струя расплава, 6 — лоток, 7 — штуцер для подачи воды. 8 — слив охлаждающей воды, 9 — полый вал раздаточной чаши
Центробежно-фильерно-дутьевой способ (ЦФД) – при нем формируются тонкие струйки за счет центробежной силы вращающейся чаши с отверстиями и последующей их обработки горячими газами. Применение вращающейся чаши с 2000 фильер диаметром менее 1 мм позволяет получить стабильные микроструйки расплава и создать устойчивые и регулируемые условия воздействия аэродинамических сил.
Струя через полый шпиндель поступает в чашу 1. Под действием центробежных сил расплав выходит через отверстия в виде тонких струек и вытягивается как за счет центробежных сил, так и аэродинамических сил горячих газов, выходящих из кольцевого сопла 2. Поток газов направлен вниз и увлекает образовавшиеся волокна в камеру волокнообразования 3.
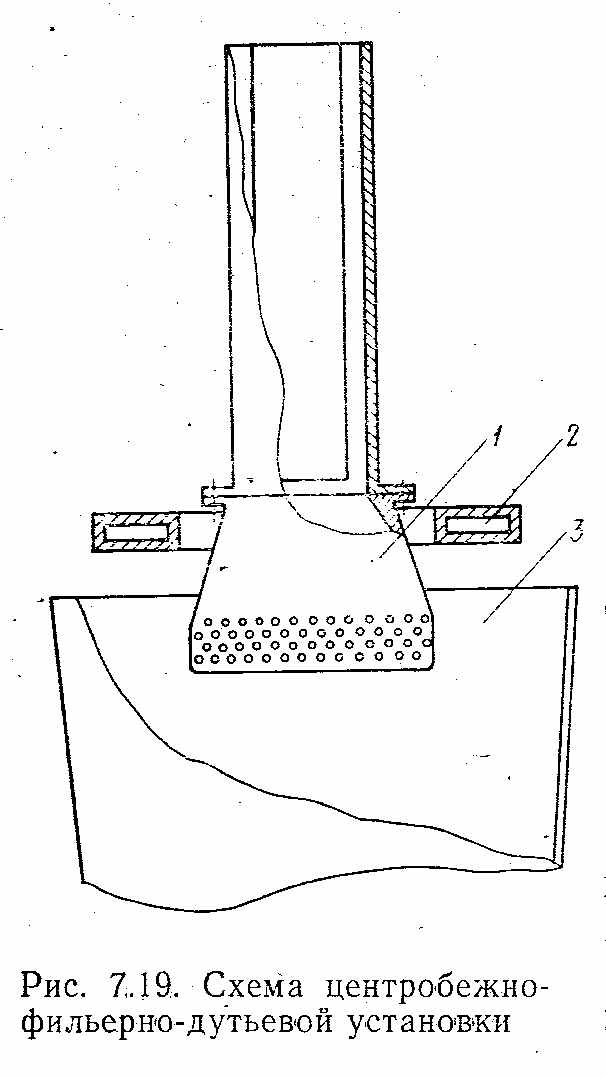
Рис. 13. Схема центробежно-фильерно-дутьевой установки
Этот способ позволяет получать ультратонкое волокно 1-2 мкм, причем неволокнистые включения полностью отсутствуют.
Изделия из минеральной ваты
Виды минераловатных изделий. Они подразделяются на: штучные изделия – плиты, цилиндры, полуцилиндры, сегменты; рулонные – маты прошивные и на синтетическом связующем; шнуровые – шнуры (жгуты); сыпучие – гранулированная вата.
Грануляция ваты дает ей свойство сыпучести и облегчает укладку в конструкции, удаляются корольки, снижается объемная масса, но недостатки как у рыхлой минеральной ваты. Шнуры получают путем набивки измельченной ваты в оплетку из металлической проволоки, стеклянных или хлопковых нитей. Прошивные маты изготавливают путем обкладки слоя минеральной ваты гибкими материалами в виде металлической сетки, асбестовой, стеклянной ткани, водонепроницаемой бумаги. Остальные виды изделий получают с использованием связующего. Связующее скрепляет волокна и создает каркас различной жесткости, в зависимости от его количества и вида.
Связующие для изделий и требования к ним
Основные задачи технологии производства минераловатных изделий – подбор, приготовление, способ введения связующего в волокно и последующая их тепловая обработка.
В качестве связующих используют синтетические смолы, композиционные и битумные связующие.
Синтетические связующие должны: хорошо растворяться в воде, легко диспергироваться, чтобы покрыть волокно тонкой пленкой, обладать хорошей адгезией к волокну, быть недефицитными, не иметь в своем составе легковоспламеняющихся и токсичных веществ. Чтобы придать связующим нужные свойства в них вводят нейтрализующие материалы, отвердители, пластификаторы.
В качестве синтетических связующих применяют: фенолспирты (фенолформальдегидную смолу), карбамидную смолу КС-11 (продукт конденсации карбамида и формальдегида), поливинилацетатную дисперсию.
Композиционные связующие состоят из нескольких компонентов: фенолспиртов, карбамидных смол или других связующих и пластифицирующих добавок. В качестве пластифицирующих добавок добавляют эмульсол, поливинилацетатную дисперсию, латексы синтетических каучуков и т.д.
К композиционным связующих относится крахмальное связующее, применяемое в производстве минераловатных матов и плит. В его состав входят: крахмал, мазут, парафин и вода.
Битумные связующие. Они также используются в производстве как обеспыливающие вещества. Для производства минерального войлока, мягких, полужестких и жестких плит применяют битумы марок БМ -50/50, БМ -70/30 и БМ -90/10.
Для производства жестких минеральных плит применяют битумные эмульсии и пасты, куда кроме битума входят канифоль, каолин или глина, диатомит или трепел. Недостатки – битум может воспламениться, трудно распределяется в волокне. Достоинства – низкая стоимость, недефицитность, высокие водоотталкивающие, вяжущие и эластичные свойства.
Для смазки применяют также петролатум – смесь твердого парафина с высоковязким минеральным маслом.
Способы смешивания связующих веществ с минеральной ватой
Применяют три способа введения связующего в волокно: распыление или пульверизацию, полив с вакуумированием, приготовление гидромассы или пульпы.
Способ распыления наиболее распространен. Водный раствор или эмульсия подается в камеру волокноосаждения, где связующее распыляется паровыми соплами, воздушными или мех. форсунками. Они могут распыляться через полый вал второго, третьего и четвертого валка центрифуги. Рабочие растворы связующего состоят из 50% раствора смолы и воды в соотношении 1:2,1:3,5. Недостаток – большие потери связующего при распылении и неравномерное распределение смолы в минераловатном ковре.
По другому способу водный раствор связующего вводится в минераловатный ковер путем полива и одновременного вакуумирования. Рабочий раствор подается на минераловатный ковер, выходящий из камеры волокноосаждения и смачивает его по всей ширине. В камере отсоса вентилятор высокого давления создает разрежение, что позволяет удалить из ковра излишнее количество раствора связующего. Дополнительно связующее удаляется с помощью отжимного валика. Недостаток способа – наличие дополнительных устройств, большой расход тепла. Достоинства – однородное и равномерное распределение связующего.
При «мокром» способе введения связующего хлопья минеральной ваты смешиваются со связующим (битумной эмульсий или раствором фенолспиртов), образуя гидромассу или пульку. Такой способ используется при производстве жестких плит на битумном связующем, плит повышенной жесткости на синтетическом связующем (ППЖ).
Формование изделий
В зависимости от вида изделия и его жесткости формование изделий идет разными способами. В производстве плит более часто применяются пластинчатые или сетчатые конвейеры. Камера представляет собой два пластинчатых или 2 пластинчатых и 2 сетчатых конвейера расположенных один над другим: нижний – несущий, верхний – прижимной. Скорость конвейеров синхронна. С помощью устройства верхний конвейер опускается или поднимается, обеспечивая заданную толщину изделия. Первая пара конвейеров пластинчатая. В некоторых линиях вводят вторую пару конвейеров – сетчатую, куда поступает уже сформированная плита, которая приобретает необходимую фактуру.
Штучные изделия – например полуцилиндры изготавливают методом горячего прессования. Для этого изготовляют заготовки минераловатного ковра, содержащие связующее. Заготовки снимают с промежуточного конвейера и укладывают на формующую поверхность пресса. Полуцилиндры формуют системой матриц и пуансонов обогреваемых трубчатыми электронагревателями.
Штучные изделия изготовляют также методом фрезерования и навивки (цилиндров).
Способы получения минераловатных плит повышенной жесткости
Технология этих изделий отличается от технологии обычных плит тем, что применяется мокрый способ подготовки формовочной массы и штучное формование изделий.
Жесткие плиты из гидромассы на битумном растворе в фильтрующих пресс-формах, в которых избыток воды удаляется прессованием или прессованием и вакуумированием через перфорированные днища.
Плиты повышенной жесткости (ППЖ) изготовляют на синтетическом связующем конвейерным, мокрым (из гидромасс) и кубовым способами. В конвейерном способе необходимая жесткость плит получается за счет повышения содержания связующего до 8-10% и увеличения давления подпрессовки в камере тепловой обработки.
В мокром способе при приготовлении гидромассы кроме минеральной ваты и связующего добавляют пенообразователь. Формование может осуществляться двумя способами: подпрессовкой гидромассы до заданной толщины ковра и отливкой ковра с последующим вакуумированием и калибровкой.
По кубовой технологии можно получить плиты с вертикальным расположением волокна, что позволяет повысить жесткость плит при той же объемной массе. Он наиболее экономичен. Минераловатный ковер подпрессовывается, разрезается на полосы – заготовки размером 1х1м. Заготовки укладываются в форму карусельной установки для набора минераловатного массива кубической формы. Массив отверждается в форме горячим воздухом, вынимается и идет на резку. Резка осуществляется перпендикулярно направлению волокон в массиве. Твердые плиты прессуются в гидравлических многополосочных прессах.
Тепловая обработка
Тепловая обработка осуществляется путем прососа горячего теплоносителя через минеральный ковер. Это может продукты сжигания топлива в топках или горячий воздух. Подвод теплоносителя осуществляется в камере формовки изделий с тепловой и аэродинамической схемой работы (подвод теплоносителя может быть снизу или сверху, с рециркуляцией или без рециркуляции).
Назначение тепловой обработки – удаление влаги, а также прогрев ковра до температуры, при которой происходит отверждение смолы.
Конструкции камер тепловой обработки плит должны обеспечивать постоянство температуры и скорости газов по всей площади обрабатываемого ковра, наименьшее гидравлическое сопротивление всей системы и расход топлива, исключить возможность выбивания газов в цех.
Основное конструктивное решение, удовлетворяющее этим требованиям – разделение рабочего пространства камеры по длине на отдельные зоны с самостоятельными отопительно-вентиляционными устройствами и многократной циркуляцией теплоносителя с изменением направления его движения в зонах. Если связующее введено распылением достаточно двух зон, а поливом – четырех зон. Длина зоны находится в пределах 6-8 м. Общая длина камеры определяется временем тепловой обработки, объемной массой и толщиной плит. Плиты охлаждаются на открытом конвейере без принудительного отвода тепла. Это позволяет сократить время тепловой обработки или увеличить степень отверждения связующего.
Камера тепловой обработки 6645-02М входит в состав многих технологических линий. Она представляет собой два пластинчатых конвейера, расположенных один над другим: нижний – несущий, верхний – прижимной сверху, с рециркуляцией или без рециркуляции. Параметры режима тепловой обработки изделий в таких камерах весьма разнообразен. Температура для минераловатных плит от 170 до 210 ºС, для цилиндров 140-180 ºС и т.д. Назначение тепловой обработки – удаление влаги и прогрев ковра до температуры, при которой происходит отверждение смолы.
Пропитанный ковер поступает в камеру между двух конвейеров, где он уплотняется и подвергается обработке горячими дымовыми газами путем их прососа через ковер. Теплоноситель подается в камеру дымососом. Пройдя через ковер, большая часть теплоносителя возвращается в топку на рециркуляцию, а другая часть удаляется из рабочего пространства камеры вентилятором. Камера разделена на 3 зоны, каждая имеет топку с дымососом.
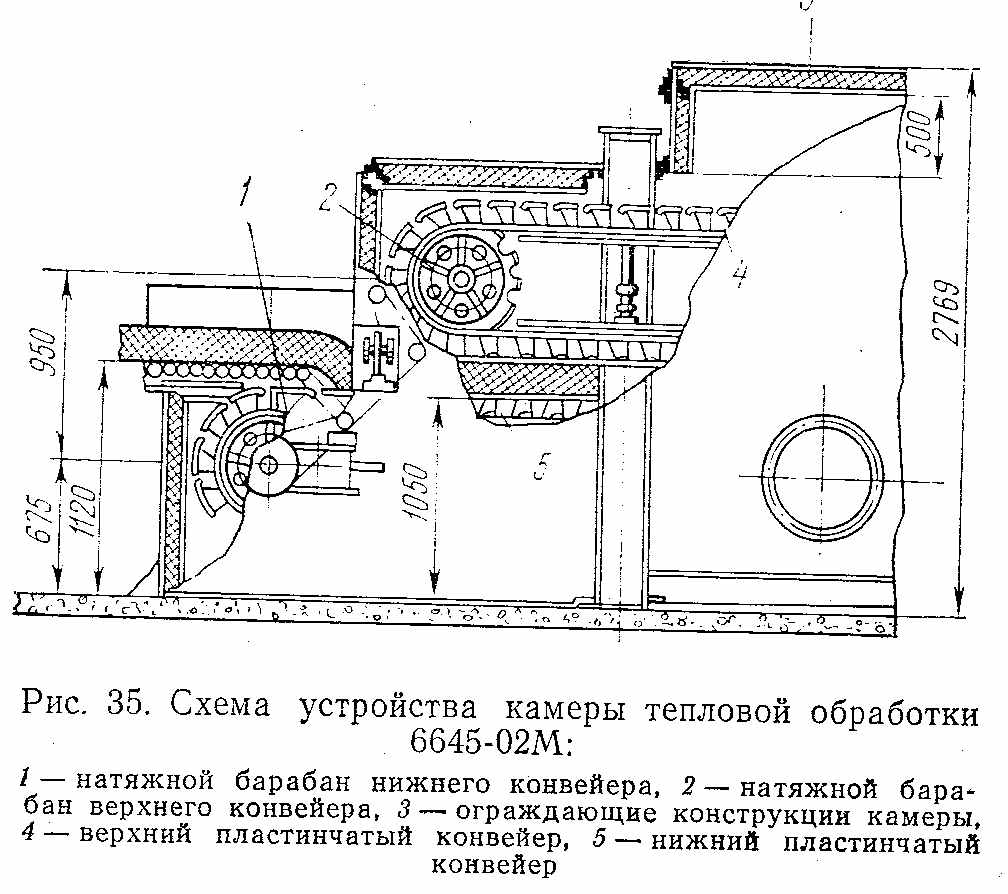
Рис.14. Камера тепловой обработки 6645-02М
Камеры СМТ-128 и СМТ-097 имеют соответственно 3 и 5 зон и соответствующее количество топок с дымососами. Они отличаются от камеры 6645-02 М конструктивным исполнением конвейеров. Первая пара конвейеров – формующая из жестких пластин, а вторая – сетчатая обеспечивает необходимую фактуру изделий. Все конвейеры работают синхронно.
Температура обработки изделий 180-200ºС. Сушка и тепловая обработка жестких плит на битумном связующем проводится в туннельных сушилках. Камера тепловой обработки должна постоянно работать под разрежением.
Области применения минераловатных изделий и их технико-экономическая оценка
Высокие показатели теплоизоляционных свойств минеральной ваты и изделий из нее, недефицитность сырьевых материалов для ее изготовления, сравнительно низкая стоимость определили ее широкое распространение в строительстве.
Минераловатные изделия составляют более половины всего выпуска теплоизоляционных материалов. Они применяются для тепло- и звукоизоляции в жилых зданиях, промышленных сооружениях, оборудовании. Значительно должен увеличиться выпуск плит повышенной жесткости, необходимых для утепления металлических профилированных настилов.
В ближайшие годы предстоит: интенсификация технологических процессов производства минераловатных изделий, внедрение новых видов оборудования, создание автоматизированных конвейерных линий производства минераловатных изделий, создание безотходной технологии, разработка и создание оборудования для производства армированных самонесущих и офактуренных плит для применения в легких конструкциях зданий промышленного и общественного назначения.
Технологический контроль качества в производстве минераловатных изделий
Контроль осуществляется на каждой стадии производственного процесса, причем существует отличие контроля производства изделий на синтетическом связующем от контроля производства изделий на битумном связующем. Это различие определяется разными стадиями производственного процесса – размягчение битумного связующего или приготовления раствора фенолоспиртов и т.д. Контроль качества готовой продукции производится в соответствии с существующими нормативными документами, а также контролируется визуально по равномерности окраски на срезе плит равномерность распределения связующего.
2.Стеклянная вата и изделия из нее
Виды стеклянного волокна
Стекловолокно – материал, получаемый различными способами из сплавов стекломассы. Оно служит полуфабрикатом при производстве тепло- и звукоизоляционных изделий.
В зависимости от способа производства волокно может быть непрерывным и штабельным (длиной от 1 до 50 см). По применению оно подразделяется на текстильное и теплоизоляционное. Текстильное перерабатывается в пряжу и ткани технологического назначения. В зависимости от среднего диаметра различают стекловолокно: ультратонкое (УТВ) диаметром менее 1 мкм, супертонкое 1 - 3 мкм, тонкое (текстильное) – 4-12 мкм, утолщенное (изоляционное) – 12 - 25 мкм и толстое (упругое) – более 25 мкм. Из непрерывного волокна изготавливаются маты, полосы, жгуты, ими армируют стеклопластики и бетон. Жгуты применяют для изоляции трубопроводов.
Из штапельного волокна изготавливают маты, армируют стеклопластики, изготавливают полужесткие клееные, строительные или технические плиты.
Химический состав и свойства стеклянной ваты (волокна)
Стекловолокно характеризуется высокой прочностью, вибростойкостью, тепло - и биостойкостью, малой гигроскопичностью, хорошими диэлектрическими свойствами, а также химической стойкостью.
Для получения стекловолокна применяют как щелочные, так и бесщелочные борсодержащие составы стекла.
Таблица
Химические составы стекол
Составы | Содержание оксидов, % по массе | ||||||
SiO2 | AI2O3 | В2О3 | Fe2O3 | СаО | MgO | Na2O | |
Щелочные | 50-70 | 1-6 | 0-3 | 0.2-1 | 5-20 | 2-7 | 8-20 |
Бесщелочные | 53-60 | 12-16 | 5-10 | 0.2-0 | 7-23 | 4-8 | 0.5-2 |
Прочность, химическая стойкость и температуростойкость выше у борсодержащих, но бораты дороги и дефицитны, поэтому теплоизоляционное волокно изготавливают в основном из щелочных составов. Температуростойкость бесщелочного стекла 600ºС, а щелочного стекла 450ºС.
Способы получения стеклянного волокна и применяемое оборудование
Для производства стеклянной ваты применяют кварцевый песок, известняк (доломит), соду (сульфат натрия), борную кислоту, поташ – в зависимости от требуемого состава окислов.
П
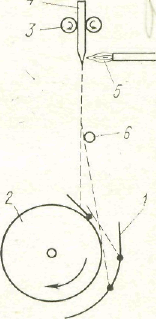
Штабиковый способ основан на подогреве до расплавления стеклянных палочек – штабиков и вытягивании из них стеклянного волокна, наматываемого на вращающийся барабан. Позволяет получить в сутки 55-70 кг стекловолокна с установки.
Рис. 15.Схема получения стекловолокна штабиковым способом: I — щит, 2—барабан, 3 — механизм, подающий штабик, 4 — стеклянный штабик, 5 — газовая горелка, 6 — приспособление для изменения угла падения
Каждый штабик разогревается отдельной горелкой и, плавясь, вытягивается в нитку, падает на барабан, нити наматываются, затвердевшие капли удаляются.
Фильерный способ основан на вытягивании волокон из расплавленной массы через фильеры и наматывании вытягиваемого волокна.
Расплавленное стекло под давлением силы тяжести вытекает из печи через фильеры в виде капель, которые вытягиваются в волокна. Волокна, собранные в пучок, пропускают через замасливающее устройство. Нити наматываются на барабан.
Волокно, полученное этими способами можно применять для высокотемпературной изоляции (1200-1500ºС).
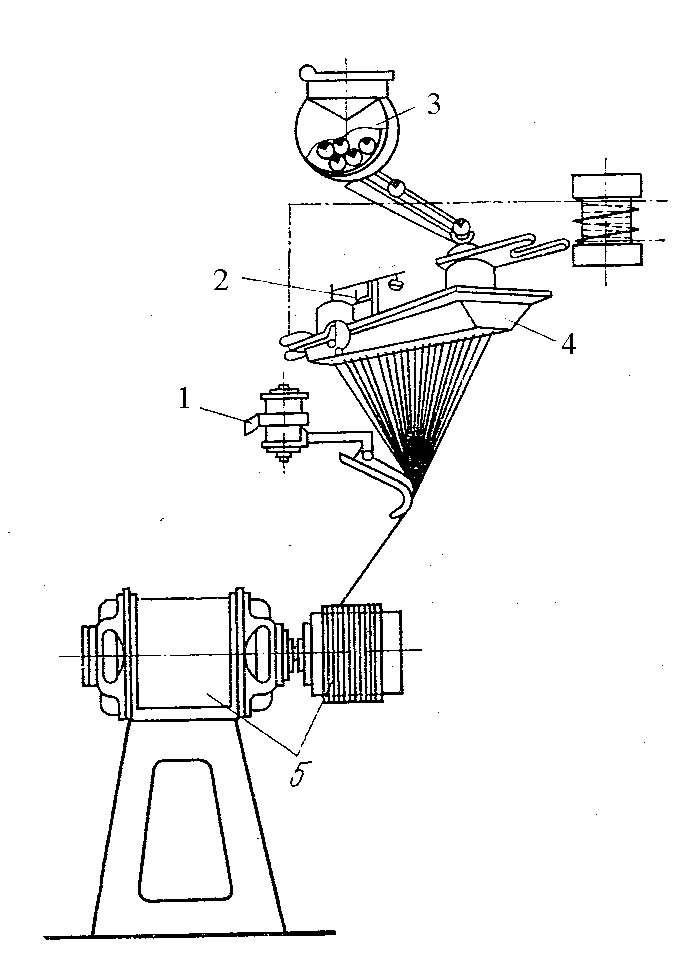
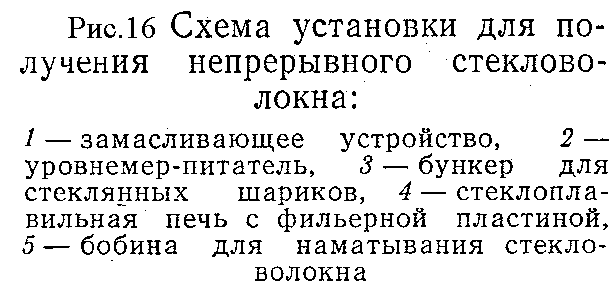
Двухстадийный дуплекс-процесс применяют для получения ультра - и супертонкого волокна. Расплавленная стекломасса через фильеры подается в высокотемпературный газовый поток, выходящий из сопла камеры сжигания со скоростью 250-300 м/с. Под действием газового потока первичные волокна размягчаются и раздуваются в тонкие короткие волокна, которые осаждаются на конвейере.
Штапельное волокно получают способом вертикального раздува паром или воздуха ВРВ или ВРП, центробежным, центробежно-дутьевым, центробежно-фильерно-дутьевым способами, аналогичными способам, применяемым в минераловатном производстве.