Советник раасн, профессор каф. Строительного материаловедения и специальных технологий д т. н. Акулова М. В
Вид материала | Документы |
Содержание2. Средняя плотность 4. Механические свойства. 5. Водопоглощение и гигроскопичность Средняя плотность Температура спекания Доменные шлаки Горные породы. |
- Разработчики программы повышения квалификации: Галимов Энгель Рафикович, д т. н., профессор,, 226.46kb.
- Региональное Отделение Российского Философского Общества Саратовский государственный, 223.62kb.
- Разработчики программы повышения квалификации: Алиева Б. Ш. д пед н., профессор, каф, 274.72kb.
- Концепция устойчивого развития в стратегии градостроительства франции 05. 23. 22 Градостроительство,, 332.07kb.
- Десятые академические чтения раасн, 2006, 1519.63kb.
- Заровняев Борис Николаевич, д т. н., профессор, зав. Каф. Огр открытых горных работ, 204.45kb.
- Лечение недержания мочи у мужчин о. Б. Лоран, член корр. Рамн, профессор, зав каф урологии, 39.64kb.
- Племяшов К. В., зав кафедрой акушерства, к в. н., Андреев Г. М., профессор каф акушерства,, 51.58kb.
- Кязимов Карл Гасанович Доктор педагогических наук, профессор ргсу, Государственный, 88.92kb.
- Программа для поступающих на Направления подготовки бакалавров 150700 «Машиностроение», 505.68kb.
Теплоизоляционные материалы на основе вспученного жидкого стекла включают широкую гамму материалов, основным структурообразующим элементом которых являются продукты термического или химического вспучивания гидратированных растворимых стекол (гидратированных щелочных силикатов). Эти материалы могут быть классифицированы по следующим признакам: природе структурообразующих элементов изделий, принципу вспучивания, фракционному составу и эксплуатационным свойствам.
Различают вспученные жидкостекольные материалы, представляющие собой продукты вспучивания гидратированных растворимых стекол, и композиционные материалы, включающие гранулированное вспученное жидкое стекло и связующее. По природе вспучивания жидкостекольные материалы разделяются на термовспученные и вспученные в результате химического взаимодействия жидкого стекла со специальными веществами, вводимыми в сырьевую смесь. К термовспученным материалам относятся зернистые, а также обжиговые монолитные материалы. К вспученным химическим путем относят заливочные композиции, в которые вводят газообразующий компонент.
Зернистые материалы в зависимости от гранулометрического состава разделяются на крупнозернистый (называемый стеклопором) с размером зерен более 5 мм и мелкозернистый (силипор) – от 0,01 до 5 мм.
По отношению к воде различают неводостойкие материалы, эксплуатация которых возможна при относительной влажности воздуха на более 75%, и материалы повышенной водостойкости, способные выдерживать длительное воздействие воды. Композиционные материалы, изготовляемые на основе зернистых продуктов, в зависимости от степени заполнения межзерновой пустотности связующими веществами делятся на материалы с контактным и объемным омоноличиванием. Особой формой композиционных материалов являются сотопластовые материалы, представляющие собой сотопластовый каркас из бумаги или ткани, пропитанной специальными растворами и заполненный мелкодисперсным зерновым материалом из вспученного жидкого стекла, например силипором.
Первые экспериментальные исследования по получению теплоизоляционных материалов на основе вспученного жидкого стекла относятся к началу прошлого столетия. Уже в 1932-1937 гг. были предприняты попытки промышленного освоения их производства, однако лишь с начала 70-х годов они стали широко осваиваться отечественной и зарубежной промышленностью.
Распространенность сырьевой базы, простота технологии, низкие капиталовложения и энергозатраты, а также хорошие физико-механические свойства определяют высокую экономическую эффективность материалов на основе вспученного жидкого стекла и обеспечивают их широкое внедрение в различные области народного хозяйства.
Основные свойства
1. Пористость. Этим материалам свойственна ячеистая пористая структура; общая пористость в среднем составляет 98-99,6%.
Размер пор во вспученном продукте зависит от количества химически связанной воды и наличие добавок в исходном щелочном силикате: первые вызывают увеличение, а вторые уменьшение пор. Большое влияние на уменьшение размера пор оказывают активные по отношению к жидкого стеклу добавки (кислоты, кислые соли, спирты и др.)
Большинство веществ, вызывающих коагуляцию жидкого стекла или образование труднорастворимых силикатов, подавляет вспучивание жидкого стекла. При этом после термообработки материал имеет лишь гелевые поры, а их объем невелик. Медленный режим нагрева жидкого стекла или твердых гидратированных щелочных силикатов, также приводит к резкому уменьшению размера пор.
2. Средняя плотность материалов из вспученного жидкого стекла легко регулируется в широких пределах (10-200 кг/м³) изменением дозировки добавок в исходной композиции и условий вспучивания. При свободном вспучивании жидкого стекла без добавок можно получить такой сильно вспученный материал, что стенки пор будут давать цветную интерференцию, а средняя плотность будет равна 5-6 кг/м³.
Несколько большую среднюю плотность имеют гранулированные материалы. Процесс их вспучивания можно рассматривать как промежуточный между процессами свободного вспучивания и вспучивания в замкнутом объеме.
3.Теплопроводность не превышает при нормальных условиях 0,065 Вт/(мºС). С увеличением средней плотности и размера гранул теплопроводность несколько возрастает, с понижением температуры она уменьшается. Материалы на основе жидкого стекла обладают высокой огнестойкостью и температуростойкостью. Рабочая температура применения в среднем находится в пределах от -200 до +660ºС.
4. Механические свойства. Материалы из вспученного жидкого стекла (в частности, гранулированные) обладают определенной пластической деформацией. Так если керамзит или перлит хрупко разрушается по всему объему, то при сдавливании стеклопора разрушенными оказываются лишь верхние слои материала, соприкасающиеся с движущимся пуансоном.
5. Водопоглощение и гигроскопичность зависят от средней плотности и способа изготовления. Вспученные жидкостекольные материалы имеют повышенное водопоглощение из-за высокой пористости и тонких межпоровых перегородок. Однако оно лежит в пределах теплоизоляционных материалов и составляет 12-18% по объему, а водостойкость материалов ограничена.
Сорбционная влажность вспученных жидкостекольных материалов зависит от их пористости и относительной влажности воздуха и, как правило, не превышает 1% по объему.
Технология вспученных жидкостекольных материалов
Производство вспученных материалов включает следующие операции: приготовление смеси раствора жидкого стекла с технологическими добавками, частичная дегидратация полученной смеси, диспергирование (грануляция) смеси и вспучивание гранулята. Сырьем для производства вспученных жидкостекольных материалов служат натриевое жидкое стекло, тонкомолотое минеральные наполнители и специальные добавки.
Назначение тонкомолотых минеральных наполнителей – отощение жидкостекольной смеси, необходимое для достижения оптимальных реологических характеристик смеси и повышения прочности материала. Отощающими добавками служат разнообразные тонкомолотые минеральные наполнители: мел, известняковая мука, тальк, молотый песок, каолин, асбестовая пыль, золы. Специальные добавки предназначены для направленного регулирования эксплуатационных свойств материала. Специальные добавки в зависимости от эффекта, оказываемого или на свойства вспученных материалов, делятся на упрочняющие, гидрофобизирующие, повышающие водостойкость и вспучивание материала.
Сущность процесса изготовления большинства вспученных жидкостекольных материалов заключается в получении гранулированного полуфабриката (бисерного стеклопора) и последующего его низкотемпературного вспучивания.
В производстве силипора грануляция жидкостекольной смеси осуществляется путем распыления в башенной сушилке. В этом случае грануляция и вспучивание совмещаются в одной операции.
В процессе грануляции на поверхности частиц массы образуется слой кремнегеля, который в дальнейшем препятствует их слиянию и придает гранулам прочность. Влажный гранулят стеклопора направляется в сушильное устройство. Здесь бисерный стеклопор подсушивается, освобождаясь от поверхностной влаги, и подается на вспучивание в печь или в формы, направляемые в камерные или щелевые печи.
Вспучивание гранулята осуществляется за счет испарения содержащейся в жидком стекле связанной воды в момент перехода материала в пиропластическое состояние.
Низкая температура вспучивания жидкостекольных материалов (ниже 500ºС) положительно отличает их от всех известных минеральных обжиговых материалов. Для вспучивания пригодно оборудование, предназначенное для сушки различных строительных материалов.
Поскольку процесс изготовления большинства вспученных жидкостекольных материалов разделен на два основных этапа (изготовление бисерного стеклопора и последующего его вспучивания) промышленный выпуск удобно организовать по двухстадийной схеме.
Возможность получения заданного гранулометрического состава гранулированных материалов создают хорошие предпосылки к производству крупнопористых плитных изделий на их основе. Для производства таких изделий используют маловязкие связующие, хорошо смачивающие поверхность гранул. Процесс изготовления включает перемешивание гранул со связующим и формование изделий. Таким способом получают изделия из стеклопора на основе цементного, гипсового, битумного, жидкостекольного связующих, поливинилацетатной эмульсии и др.
После отверждения связующего получается легкий теплоизоляционный материал, характеризующийся прочностью не менее 0,15 МПа и средней плотностью в пределах 200 кг/м³, при этом расход связующего на 1 м³ изделий не превышает 30-60 кг.
Высокоэффективно омоноличивание стеклопора заливочными пенопластами.
Изделия на основе минеральных композиций
Стеклосиликат. Связующим при изготовлении стеклосиликата является жидкое стекло или его смесь со специальными добавками. Различают при разновидности этого материала.
Стеклосиликат первой разновидности относится к крупнопористым легким бетонам: это гранулы стеклопора, омоноличенные контактным способом щелочными силикатами. Стеклосиликат второй разновидности относится к группе омоноличенных наполненных материалов и назван обжиговым стеклосиликатом. Его технология предусматривает вспучивание жидкостекольной связки. Стеклосиликат третьей разновидности также относится к группе омоноличенных наполненных материалов. Формуют его путем заливки самовспенивающейся композиции, на основе жидкого стекла, отверждение которой происходит при нормальных температурах.
Стеклофосфогель является близким аналогом обжигового стеклосиликата. При его изготовлении используют смесь жидкого стекла, ортофосфорной кислоты и измельченного стеклопора. После приготовления смесь загружают, а формы, снабженные крышками, и подвергают термической обработке с крупными порами.
Стеклоцемент. Технология этого крупнопористого теплоизоляционного материала заключается в перемешивании гранул стеклопора с цементным молоком, естественном твердении и сушке изделий. Для изготовления стеклоцемента используют высокомарочные быстротвердеющие цементы (БТЦ, ОБТЦ), а также гипсоцементно-пуццолановые вяжущие.
Изделия на основе полимерных связующих
В промышленности широко применяют вспученный стеклопор для изготовления наполненных пенопластов. Эффективность введения вспученного стеклопора в состав газонаполненных пластмасс заключается в повышении их прочностных показателей, уменьшении деформативности и усадочных явлений, повышение термической стойкости и, что особенно важно, огнестойкости, а также в большинстве случаев в уменьшении расхода полимерных компонентов связующих.
Стеклофенопласт ФСП изготавливают на основе фенолспиртов 50-85%-ной концентрации.
Стеклопенополиуретан. Наибольший технико-экономический эффект от введения стеклопора в заливочные пенопласты получают в производстве пенополиуретановых материалов.
Стеклокарбамид готовят на основе мочевиноформальдегидных смол (предпочтительно УМС). В отличие от заливочных пенопластов при его изготовлении вначале из смолы приготовляют пеномассу, которая затем заполняет межзерновые пустоты вспученного стеклопора.
Стеклобитум изготавливают из стеклопора и битумов марок БМ-IV или БМ-V. В отличие от перлитобитумных изделий стеклобитум характеризуется на 50% меньшим расходом битума.
Теплоизоляционные материалы из искусственного минерального волокна
В зависимости от вида сырья и способа производства искусственное минеральное волокно можно разделить на: минеральное волокно с температурой применения 600ºС (рядовое); стеклянное волокно с температурой применения 400ºС, высокотемпературостойкое и огнеупорное волокно с температурой применения соответственно до 1000ºС и выше.
Минеральное и стеклянное волокно получают переработкой силикатных расплавов. Продукт в виде бесформенной волокнистой массы получил название минеральной или стеклянной ваты в зависимости от химического состава силикатных расплавов. Стеклянная вата характеризуется более высоким содержанием SiO2 и наличием щелочей.
- Минеральная вата
Минеральная вата представляет собой рыхлый материал, состоящий из тонких волокон стекловидной структуры. Цвет минеральной ваты белый, светло-серый, зеленоватый, коричневый, темно-бурый. Высокие теплоизоляционные свойства минеральной ваты обусловлены наличием большого количества воздушных пор: пористость достигает 95-96%. Объем и размер пор зависят от степени уплотнения и диаметра волокон. Диаметр волокон ваты колеблется от 1 до 10 мкм. С увеличением диаметра волокна увеличивается теплопроводность, поэтому стандартом ограничен диаметр волокна – не более 8 мкм. Длина волокна колеблется от 2-3 мм до 20-30 см. Средний диаметр волокон и их длина зависят как от химического состава расплава, так и от ряда технологических факторов. Чем длиннее волокно, тем более упругими и прочными получаются изделия.
Помимо волокон вата содержит частицы расплава, невытянувшиеся в волокно. Эти включения получили название «корольки». Форма этих частиц в основном сферическая. Корольки повышают теплопроводность минеральной ваты, являясь «мостиками» передачи тепла.
Средняя плотность минеральной ваты зависит от среднего диаметра волокна, содержания корольков и степени уплотнения. При одинаковой удельной нагрузке (стандартная 0,002 МПа) средняя плотность возрастает с увеличением диаметра и содержания корольков. Стандартом предусмотрен выпуск ваты марок 75, 100, 125.
Водопоглощение минеральной ваты при погружении в воду очень велико – до 600%. Гигроскопичность колеблется от 0,.2 до 2%. С повышением кислотности состава снижается биостойкость ваты.
Температура спекания ваты 700-800º С, соответственно температура применения 600-700º С. Минеральная вата обладает огнезадерживающими свойствами благодаря негорючести и малой теплопроводности.
Теплопроводность зависит от диаметра волокна, средней плотности и содержания неволокнистых включений в вате. Увеличение диаметра волокна влечет за собой повышение теплопроводности. При увеличении диаметра волокна с 3 до 123 мкм теплопроводность растет на 10%.
Теплопроводность минеральной ваты не должна превышать:
при температуре:
25±5ºC – 0.045 Вт/мºС
125±5ºC – 0.064 Вт/мºС
300±5ºC – 0.105 Вт/мºС
С увлажнением этот показатель резко возрастает.
Технология производства минеральной ваты
Производство минеральной ваты независимо от типа плавильного агрегата и способа переработки силикатного расплава включает в себя следующие технологические операции: подготовку сырьевых материалов путем измельчения и его сортировку; плавление сырья и получение силикатного расплава; переработку расплава в волокно; осаждение минеральной ваты и формирование минераловатного ковра в камере волокно-осаждения.
Сырьевые материалы
Для производства минеральной ваты используют: шлаки, являющиеся отходами черной и цветной металлургии; природные силикатные и карбонатные горные породы; отходы промышленности (бой глиняного кирпича, горелые породы, пыль-унос цементного и керамзитового производства).
Доменные шлаки – наиболее распространенное сырье для производства минеральной ваты – используют как в твердом состоянии в виде щебня, так и в огненно-жидком состоянии. Шлаки представляют собой сплавы силикатов и алюмосиликатов следующего химического состава (%): SiO2 – 35-40; AL2O3 – 10-15; CaO – 35-45; MgO – 5-10; Fe2O3+FeO – 0,5.
Щебень из доменного шлака применяют для плавления в вагранках, огненно-жидкие шлаки – в шлакоприемных ванных печах.
Фосфорные, никелевые, медеплавильные шлаки, являющиеся отходами цветной металлургии, используют для плавления в вагранках.
Недостаток – высокое содержание СаО, что снижает устойчивость к действию воды, прочность, увеличивает пыление и слеживаемость минеральной ваты. Для уменьшения недостатков в силикатную шихту добавляют подкислители, содержащие повышенное количество SiO2 и AL2O3. Использование огненно-жидких шлаков снижает расход тепла на получение расплава, в связи с чем снижается стоимость минеральной ваты. Однако сложно корректировать состав шлаков.
Горные породы. К числу лучших видов горных пород для производства минеральной ваты относятся изверженные горные (базальты, диабазы, габбро), подобные им по химическому составу метаморфические и осадочные (мергели, доломиты, известняки) породы. Содержание оксидов в состпве горных пород колеблется в следующих пределах (%):SiO2 – 45-65; AL2O3 – 10-20; Fe2O3+FeO – 10-15; CaO – 5-15; MgO – 5-15; Na2O+K2O – 1-3.
Для получения силикатного расплава наиболее пригодны изверженные породы, отличающиеся высокой прочностью и равномерностью химического состава. Для плавления в ванных печах по своему химическому составу подходят осадочные породы.
Основным показателем, определяющим пригодность сырья для производства минеральной ваты служит модуль кислотности Мк, который представляет собой отношение суммы процентного содержания в сырье кислых окислов – кремнезема SiO2 и глинозема AI2O3 к сумме основных окислов – кальция СаО и магния MgO. Модуль кислотности минеральной ваты должен быть не менее 1,2, т.е
Мк=( SiO2+ AI2O3)/(СаО+ MgO)≥1,2
Так как в природе редко встречаются сырьевые материалы с необходимым химическим составом и модулем кислотности, то требуемый состав сырьевых материалов подбирают путем составления сырьевой смеси – шихты, состоящий их двух, иногда и нескольких компонентов.
Отходы керамического и силикатного производства широко используются в композиции с менее кислыми или основными компонентами (шлак, доломит, известняк и др.)
С повышением модуля кислотности увеличивается долговечность минеральной ваты и водостойкость. Водостойкость минеральной ваты характеризуется показателем рН; минеральная вата относится к высшей категории водостойкости при рН<5, первой категории при рН<7. Показатель рН гидролитической стойкости минеральной ваты повышается при увеличении содержания в ней кислых окислов SiO2 и AL2O3. Однако рост количества кислых компонентов приводит к увеличению вязкости, что снижает производительность труда и ухудшает условия волокнообразования.
Подготовка сырьевых материалов
В процесс подготовки сырьевых материалов входят следующие операции: получение определенного фракционного состава сырьевых компонентов и топлива путем дробления сырья и последующего рассева его на определенные фракции; составление рабочей шихты из сырья посредством автоматического весового дозирования каждого компонента сырья и топлива; загрузка порций шихты и топлива – рабочей колоши – в вагранку или только шихты в ванные печи (электродуговой). В стадии освоения находятся циклонные и конвейерные печи.
Для подогрева шлаков применяют специальные печи – шлакоприемники.
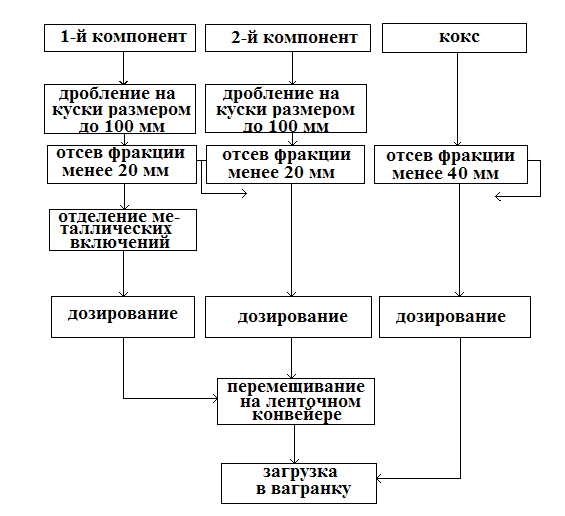
Рис. 4. Схема подготовки сырья при получении расплава в вагранке
Для плавления в вагранках применяют только кусковое сырье с размерами частиц 20-100 мм. При плавлении в ванных печах используют сырье с размером частиц до 5 мм.
Общие требования к сырью для вагранок – недопустимость фракций менее 20 мм, которые резко увеличивают аэродинамическое сопротивление столба шихты. Оптимальный размер кусков сырья зависит от вида сырья. Кроме гранулометрического состава важной характеристикой сырья является механическая прочность кусков, которая должна быть не менее 1,5 МПа.
Использование печи того или иного типа зависит в основном от вида сырья и наличия топливных и энергетических ресурсов. Сравнение плавильных агрегатов по тепловой эффективности показывает, что электродуговая печь – наиболее эффективный плавильный агрегат. Однако при ее применении резко увеличивается расход электроэнергии.
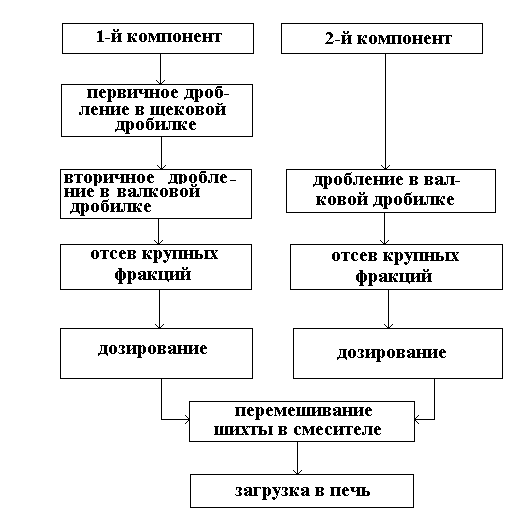
Рис. 5. Схема подготовки сырья при получении расплава в ванных печах
Наиболее широкое распространение в минераловатной промышленности получили вагранки.
Плавление сырья
Шахтная печь – вагранка
Широкое распространение вагранок объясняется высоким коэффициентом использования тепла от сжимаемого топлива, большой производительностью при небольших габаритах, простотой конструкции, незначительными капитальными затратами и простотой обслуживания.
Вагранки представляют собой шахтные плавильные печи непрерывного действия, теплообмен в которых происходит по принципу противотока. Сырье, загружаемое в верхнюю часть вагранки, опускается вниз, превращаясь при этом в расплав, а образовавшиеся в нижней части вагранки продукты горения поднимаются вверх, отдавая тепло расплавляемому материалу. Это вертикальная печь диаметром 1000, 1250 или 1400 мм, состоящая из двух основных частей – горновой и шахтной.
В горновой, нижней части вагранки происходит горение топлива и плавление сырья. Здесь развиваются наиболее высокие температуры, поэтому горновая часть защищена водяной рубашкой – ватержакетом (4). Выше ватержакета шихта защищена от воздействия высоких температур футеровкой из шамотного кирпича. Ватержакет представляет собой металлический цилиндр с двумя стенками, между которыми находится охлаждающая вагранку проточная вода, предохраняющая корпус вагранки от перегрева. Температура воды при выходе из ватержакета не должна превышать 70ºC. Низ ватержакета закрывается двухсекционным днищем (2), подвешенным на шарнирах.
Чтобы уменьшить расход воды, целесообразно применять оборотную систему: нагретая в рубашке вода подается в охладительные устройства или охладительные бассейны, и вновь используется в ватержакете. Перепад температуры поступающей и отходящий из водяной рубашки воды при оборотном охлаждении должен составлять не более 15-20ºC, а при прямоточном – 30-40ºC.
Вагранки бывают с испарительной системой охлаждения, позволяющий резко снизить расход воды. В этом случае следует использовать только химически очищенную воду. Испарительные системы охлаждения могут быть открытыми и закрытыми. В испарительных системах допускается нагревание воды до температуры кипения (100ºC).
Воздух, необходимый для горения топлива, подается в вагранку через специальные устройства – фурмы (3), которые симметрично расположены по окружности вагранки в один – три ряда на определенной высоте, равной 0,5-0,8 диаметра вагранки от ее днища. Количество фурм диаметром 60-150 мм в каждом ряду составляет 8-16. Фурмы каждого ряда соединены между собой общим кольцевым коллектором (13) (фурменным поясом), через который воздух поступает по всему периметру вагранки.
Сортированные сырьевые материалы и кокс из расходных бункеров через весовые дозаторы подаются в загрузочное окно (6), расположенное в боковой стене вагранки. Высота рабочей зоны вагранки равна 4-5-ти ее диаметрам. Расход топлива (кокса) в вагранках составляет 18-20% массы сырья.
Нижнюю часть ватержакета, от оси нижнего ряда фурм до днища, называют горном. В горне накапливается жидкий расплав и происходит его гомогенизация по составу температур. Высота горна колеблется в пределах 600-750 мм.
Загруженные сверху сырье и топливо чередующимися слоями опускаются вниз, а образовавшиеся в нижней части вагранки продукты горения топлива – горячие газы – поднимаются вверх, передавая свое тепло верхним слоям материала.
Таким образом, сырье, опускаясь вниз вагранки, разогревается и превращается в расплав. Образовавшийся расплав вытекает из горна через летку (1) и по лотку направляется к узлу волокнообразования. Леткой называется отверстие диаметром 35-80 мм в водоохлаждаемом корпусе, вставляемом в специальный проем ватержакета.
На скорость плавления, производительность вагранки и температуру расплава влияет интенсивность дутья, которая определяется количеством воздуха на единицу площади за единицу времени и равна 40-110 м³/м²мин. Давление дутья зависит от высоты загрузки вагранки и фракционного состава сырья и кокса.
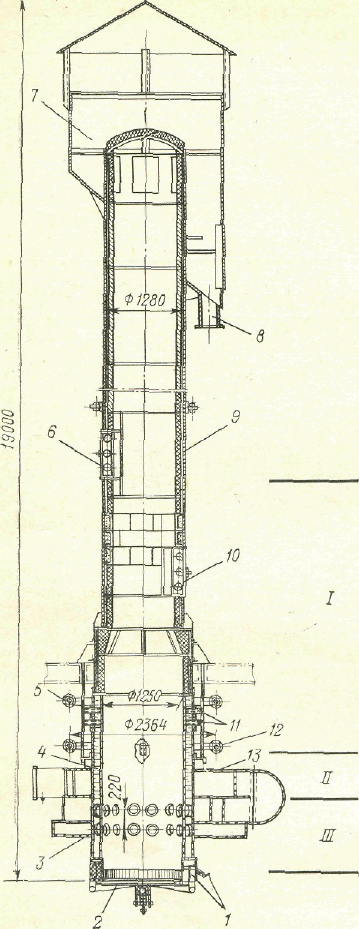
Рис 6. Вагранка для получения минерального расплава: 1 - летка, 2 - днище, 3 - фурмы, 4 - ватержакет. 5 - труба для отвода воды, 6 - загрузочное окно, 7 - искрогаситель, 8 - патрубок для сброса золы, 9 - шахта, 10 - люк для осмотра, 11 - компенсаторы, 12 - труба для подвода воды, 13 - воздушный коллектор; I - зона подогрева и сушки, II - зона плавления, III - зона перегрева
В верхней части вагранки находится искрогаситель (7) для улавливания уносимых газовым потоком искр и частиц пыли. Остывшие частицы скатываются к отверстию патрубка (8) и удаляются.
В зависимости от применяемого способа переработки минерального расплава вагранки устанавливают над уровнем пола на различной высоте (от 2000 до 3500 мм).
Плавление шихты в вагранке
Вагранку по высоте можно условно разделить на три зоны: зону подогрева и сушки сырья – I, зону плавления – II и зону перегрева (гомогенизации) расплава – III.
Зона подогрева и сушки I расположена между зоной плавления и верхним уровнем шихты. Здесь загружаемая холодная шихта подогревается за счет тепла отходящих продуктов горения топлива. В самой верхней части этой зоны при температуре 105-110ºC удаляется механически связанная влага. По мере опускания сырьевых компонентов при температуре 600-1000ºC и выше происходит термическое разложение сырья, если по химическому составу оно содержит карбонатные соединения, способные разрушаться. Если же сырье представляет собой материал, ранее прошедший термическую обработку (например, шлаки), то в этой зоне уже начинается частичное плавление шихты.
II зона – зона плавления, здесь при 1500-1800ºC сырье из твердого состояния переходит в жидкое. Образовавшийся расплав стекает по кускам раскаленного кокса в горн.
Отдельные компоненты сырьевой смеси плавятся неодновременно: легкоплавкие плавятся раньше, тугоплавкие – позднее, растворяясь в легкоплавких. Для ускорения процесса растворения тугоплавкого компонента размеры его кусков должны быть меньше, чем легкоплавкого.
III зона перегрева (гомогенизации) расплава расположена в нижней части вагранки до ее пода. В верхней части зоны III в присутствии кислорода осуществляется интенсивное горение кокса. Основной вид топлива, применяемый в вагранках, - литейный каменноугольный кокс, который обладает большой теплотой сгорания (28560-30240 кДж), высокой механической прочностью, малым содержанием летучих веществ и термической прочностью кусков. По назначению кокс подразделяют на литейный и доменный. В вагранках предпочтительнее литейный кокс, из-за его малой реакционной способности.
Обязательное условие нормальной работы вагранок – однородность кусков сырья и кокса и равномерная загрузка. Наиболее эффективно повышается производительность вагранки при интенсификации дутья, так как ускоряется горение кокса. Однако выше определенного предела потока воздуха снижается температура расплава, увеличивается его вязкость и производительность резко уменьшается.
Повышение расхода кокса способствует росту температуры расплава, но производительность после определенного предела снижается, оптимальный расход - 17-20% массы шихты. Температура расплава и производительность вагранки могут быть повышены при использовании подогретого до 400-500ºC дутья.
К недостаткам вагранок относятся: низкий коэффициент полезного использования тепла, высокие удельные затраты на топливо, плохое качество расплава и недостаточная стабильность струи расплава, неудовлетворительные санитарно- гигиенические условия эксплуатации, обусловленные применением кокса.
В то же время вагранки имеют большую производительность при небольших габаритах, просты по конструкции, требуют невысоких капитальных затрат, просты в обслуживании и ремонте, они могут быть остановлены в любое время и пущены в течение нескольких часов.
Совершенствование ваграночной плавки осуществляется в следующих основных направлениях: модернизация существующих вагранок; применение горячего дутья; создание вагранок, в которых в качестве топлива используется природный газ.
В настоящее время существуют коксогазовые и газовые вагранки, где кокс заменен на 20-30% или полностью природным газом. Это уменьшает расход дефицитного кокса, снижает затраты на тепловую энергию в 2-3 раза, обеспечивает санитарно-технические требования в производстве.
Ванные печи
Небольшие ванные печи используют для получения расплавов при производстве минеральной ваты. По своему устройству они похожи на ванные стеклоплавильные печи. Могут применяться все типы ванных печей: с подковообразным, продольным и поперечным направлением пламени. По способу использования тепла отходящих газов такие печи могут быть регенеративными и рекуперативными. Наибольшее распространение получили регенеративные печи с подковообразным направлением пламени. Для отапливания печей служит газообразное или жидкое топливо.
Ванная регенеративная печь для плавления сырья при производстве минеральной ваты состоит из плавильного бассейна (ванны), горелок (3), вертикальных воздушных регенераторов (2) и выработочной части – фидера (8). С целью подачи на переработку наиболее горячих слоев расплава дно фидера располагают выше дня бассейна.
Газоходы (1) устанавливаются для сброса отходящих газов и загрузчиков сырья. Форма бассейна варочной части (7) печи прямоугольная или суживающаяся к фидеру, глубина бассейна 500 мм.
В бассейн варочной части (7) загрузчиками или гидравлическими толкателями подается через специальные загрузочные окна (6), расположенные в боковых стенках, тщательно подготовленная шихта. В зависимости от производительности печи количество разгрузчиков с каждой стороны может быть от 1 до 4 шт. В плавильной камере установлены от 2 до 4 горелочных устройств, имеющих подковообразное направление пламени.
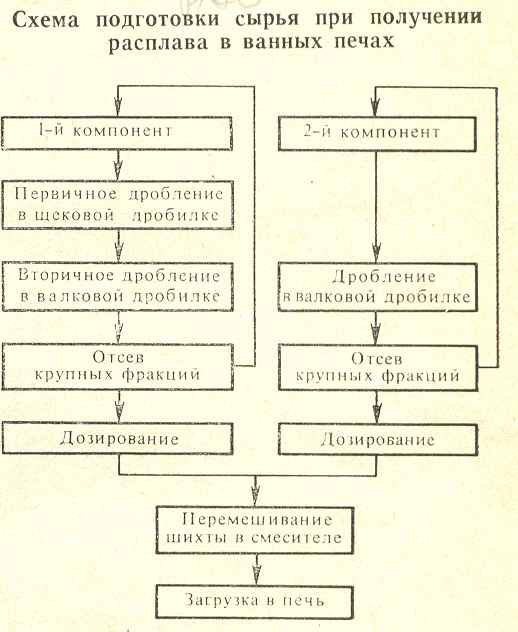
Рис. 7. Схема подготовки сырья при получении расплава в ванных печах
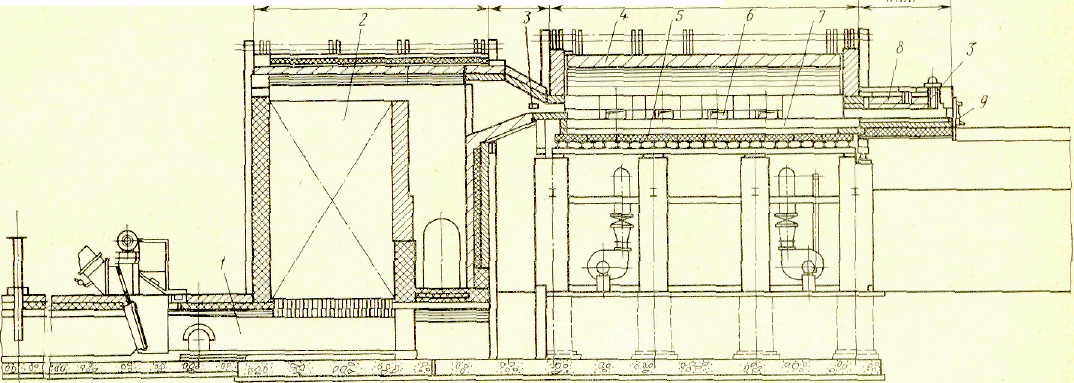
6 - загрузочные окна, 7 - варочная часть, 5 - фидер, 9 - водоохлаждаемая летка
Полученный в варочной части силикатный расплав поступает в фидер (8). Форма фидера, как и в выработочной части – прямоугольная. Между камерой плавления и фидером выложен порог, служащий для предотвращения поступления в фидер нерасплавленных кусков сырья. Расплав из фидера выдается через водоохлаждаемую летку (9) при центробежно-валковом способе его переработки или через фильерные питатели при фильерном способе.
Перед леткой в своде фидера установлено горелочное устройство (3) для перегрева расплава и достижения его однородности. Дно бассейна (под 5) выложено из многошамотных брусьев, которые уложены на металлические полосы, расположенные на донных балках. Стены бассейнов печи и фидера, загрузочные отверстия, влеты горелок выполнены из бакора (огнеупорного материала с большим содержанием окиси циркония и глинозема) свод и верхнее строение печи и фидера – фасонного динаса.
Регенераторы (левый и правый) размещены в одном блоке перед торцевой стеной варочной части печи и соединены с ней горелками и шлаковиками для осаждения частиц уноса сырья. Насадка регенераторов, выполненная из шамота и высокоглиноземистого кирпича, работает периодически, сначала воспринимая (аккумулируя) тепло отходящих газов из печи, а затем отдавая это тепло потоку воздуха, подаваемому на горение топлива. Насадка регенераторов позволяет нагреть воздух до 1000 ºC.
Направление движения пламени в варочной части печи изменяется автоматически, через определенные промежутки времени и, таким образом, поочередно работает то правый, то левый регенераторы.
Рекуперативные ванные печи более экономичны, чем регенеративные, но требуют изменения высокожароупорных элементов.
Рекуператор – устройство для подогрева воздуха или газа, в котором тепло передается от горячих отходящих газов к нагреваемому воздуху через поверхность разделяющей стенки. Температура плавления достигает 1600ºC.
Ванные печи в теплотехническом и технологическом отношении более совершенны, чем вагранки. В этих печах тепло передается в основном лучеиспусканием (около 95%), что обеспечивает удовлетворительную управляемость процессом плавления и получения гомогенного расплава с необходимыми свойствами. Достоинством ванных печей является так же возможность применять дешевые виды топлива (природный газ, мазут) и отсутствие требований к прочности сырья, так как сырье загружают в печь в измельченном состоянии (с размером кусков 1-2 мм).
К недостаткам ванных печей следует отнести то, что они занимают в 4-5 раз больше производственной площади, чем вагранки, при одинаковой производительности; требуют энергоемких шихтоприготовительных отделений для помола и перемешивания сырья; удельные расходы тепла в них в 2 раза превышают удельный расход тепла в вагранках.
Для получения минеральной ваты применяются также шлакоприемные ванные печи, электродуговые печи для получения силикатного расплава, циклонные печи для мелкокусковых отходов минераловатного производства и др.
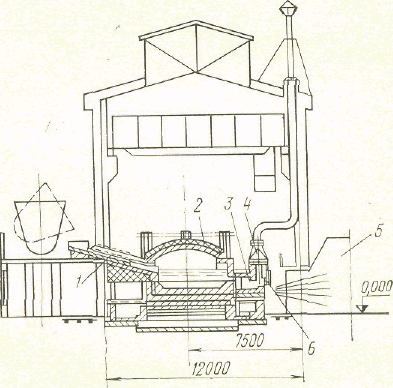
Рис. 9. Шлакоприемная ванная печь:
1 - сливной желоб, 2 – печь - шлакоприемник, 3 -печь-питатель, 4 - вытяжной зонт, 5 - камера волокноосаждения, 6 – летка