Советник раасн, профессор каф. Строительного материаловедения и специальных технологий д т. н. Акулова М. В
Вид материала | Документы |
- Разработчики программы повышения квалификации: Галимов Энгель Рафикович, д т. н., профессор,, 226.46kb.
- Региональное Отделение Российского Философского Общества Саратовский государственный, 223.62kb.
- Разработчики программы повышения квалификации: Алиева Б. Ш. д пед н., профессор, каф, 274.72kb.
- Концепция устойчивого развития в стратегии градостроительства франции 05. 23. 22 Градостроительство,, 332.07kb.
- Десятые академические чтения раасн, 2006, 1519.63kb.
- Заровняев Борис Николаевич, д т. н., профессор, зав. Каф. Огр открытых горных работ, 204.45kb.
- Лечение недержания мочи у мужчин о. Б. Лоран, член корр. Рамн, профессор, зав каф урологии, 39.64kb.
- Племяшов К. В., зав кафедрой акушерства, к в. н., Андреев Г. М., профессор каф акушерства,, 51.58kb.
- Кязимов Карл Гасанович Доктор педагогических наук, профессор ргсу, Государственный, 88.92kb.
- Программа для поступающих на Направления подготовки бакалавров 150700 «Машиностроение», 505.68kb.
Ячеистые бетоны. Искусственный пористый материал на основе минеральных вяжущих и кремнеземистого компонента, содержит равномерно распределенные поры трех видов: ячеистые, капиллярные и гелиевые.
Теплоизоляционные ячеистые бетоны предназначены для строительной теплоизоляции: утепления по железобетонным плитам покрытий и чердачных перекрытий, в качестве теплоизоляционного слоя многослойных стеновых конструкций различного назначения. Применяют также теплоизоляционные ячеистые бетоны для теплозащиты поверхностей оборудования и трубопроводов при температуре до 400ºС; жаростойкие ячеистые бетоны для теплоизоляции оборудования с температурой поверхности до 700ºС.
Классифицируют ячеистые бетоны по следующим основным признакам:
1. По функциональному назначению. Выделяют при вида ячеистого бетона: теплоизоляционный, теплоизоляционно-конструкционный (для ограждающих конструкций), конструкционный. Рассмотрим только теплоизоляционный ячеистый бетон.
2. По способу поризации. Различают три способа создания пористой структуры ячеистых бетонов: газообразование (газобетоны, газосиликаты), пенообразование, аэрирование.
3. По виду вяжущего вещества. В технологии ячеистых бетонов в качестве вяжущего применяют в основном цементы и известь, реже гипс.
Активные добавки. К этим материалам относятся отходы промышленности и некоторые горные породы (в основном искусственные и природные стекла), содержащие оксиды натрия, кальция, магния, алюминия, железа и кремния. Наиболее широко из этой группы материалов используют металлургические шлаки, отходя глиноземного производства, перлиты. Исходя из вида вяжущего и способа поризации, ячеистые бетоны называют: на цементе – газобетоны, пенобетоны; на извести – газосиликаты, пеносиликаты; на шлаке – газошлакобетоны, пеношлакобетоны и т.д.
4. По виду кремнеземистого компонента. Наиболее широко при производстве ячеистых бетонов используют кварцевый песок. В качестве кремнеземистого компонента применяют также золу-унос. Вид кремнеземистого компонента входит составной частью в название ячеистого бетона. Например, при использовании золы применяют следующие названия: газозолобетон, газозолосиликат.
5. По способу твердения. Ячеистые бетоны делятся на два класса: неавтоклавные или безавтоклавные, предусматривающие пропаривание или электропрогрев при нормальном давлении и автоклавные, которые твердеют при повышенных температуре и давлении, например, пропаренный газосиликат и т.д.
Объем производства ячеистого бетона во всем мире непрерывно возрастает. По себестоимости это один из самых дешевых видов строительной теплоизоляции (около 13 рублей за 1 м³).
Основной объем производства теплоизоляционного ячеистого бетона приходится на газосиликат (62%)
Физико-механические свойства ячеистого бетона
Средняя плотность ячеистого бетона определяется плотностью межпорового материала (силикатного камня в бетоне) и общем объеме пустот, образовавшихся в результате воздухововлечения, искусственной поризации массы и испарения воды затворения.
Плотность силикатного камня бетона меняется в зависимости от применяемых сырьевых материалов. Для ячеистых бетонов на золе ρ=2000-2100 кг/м³, а на кварцевом песке ρ=2600-2650 кг/м³.
Специфика пористой структуры предопределяет анизотропию основных свойств ячеистого бетона. Прочность ячеистого бетона, подвергнутого испытанию нагрузкой, приложенной перпендикулярно направлению вспучивания, как правило, на 15-20% выше предела прочности образцов, испытанных нагрузкой приложенной параллельно направлению вспучивания. Поэтому испытания образцов ячеистого бетона проводятся в положении, соответствующем работе изделия в конструкции. Для оценки качества ячеистых бетонов в практике используют коэффициент конструктивного качества. Прочность ячеистых бетонов в значительной мере зависит от содержания в них влаги. В зависимости от применяемой технологии (литьевой или комплексной вибрационной) влажность ячеистого бетона после автоклавной обработки колеблется в пределах 15-35% по массе. Через 1.5-2 года эксплуатации в нормальных условиях в ячеистых бетонах устанавливается равновесная влажность, равная 6-9% для изделий на кварцевом песке и 10-15% на золе-уносе.
Влажность ячеистого бетона существенно влияет на его теплопроводность. Величина прироста теплопроводности ячеистого бетона на каждый процент влажности равна в среднем 7-8.5%. Решающим фактором снижения теплопроводности ячеистого бетона является повышение общей пористости. Так снижение средней плотности на 100 кг/м³ приводит к уменьшению теплопроводности на 20%.
Морозостойкость ячеистых бетонов, как правило, превышает 25 циклов попеременного замораживания и оттаивания. Существенное влияние на морозостойкость ячеистых бетонов оказывает структура силикатного камня и вид применяемого вяжущего. В частности, ячеистые бетоны на цементе характеризуются более высокой морозостойкостью, чем газосиликаты. Некоторые ячеистые бетоны выдерживают более 100 циклов попеременного замораживания и оттаивания.
В эксплуатационных условиях при снижении влажности окружающей среды наблюдается уменьшение линейных размеров изделий – влажностная усадка. Деформации влажности усадки ячеистого бетона обусловлена главным образом действием капиллярных сил и испарением межкристаллической воды силикатного камня. Эти бетоны обладают также высокими акустическими свойствами: звукопоглощающей звукоизолирующей способностью, а также высокой огнестойкостью. Огнестойкость ячеистых бетонов превышает огнестойкость тяжелых цементных бетонов.
Технология теплоизоляционного ячеистого бетона
Производство теплоизоляционного ячеистого бетона включает следующие технологические переделы: подготовку сырьевых материалов, приготовления ячеистобетонной смеси, формование изделий и тепловлажностную обработку
Чтобы обеспечить повышенную устойчивость поризованной массы используют тонкодисперсные композиции. Тонкому измельчению подвергается кремнеземистый компонент и известь. Цемент и алюминиевая пудра, дисперсность которых велика, помолу не подвергаются.
СХЕМА 1
Применяют два способа подготовки сырьевых материалов:
- мокрый помол основной массы кремнеземистого компонента (песка) и сухой помол известково-песчаного вяжущего. Содержание воды в песчаном шламе поддерживается на уровне, обеспечивающем хорошую текучесть суспензии.
- совместный сухой помол компонентов сырьевой шихты – извести, цемента и песка при влажности последнего не выше 2% по массе.
Совместный помол активизирует цемент и обеспечивает повышенную однородность смеси. Как мокрый, так и сухой помол должен производиться в присутствии ПАВ, что интенсифицирует измельчение, предотвращает слипание частиц, уменьшает намол металла. Дозировка ПАВ – 0.1-0.25% массы сухих компонентов.
Приготовление ячеистобетонной смеси
Способы приготовления формовочных масс зависят от принятой технологии (литьевой или вибрационной) и вида выделяемого порообразователя. При газобетонной технологии приготовление смеси включает дозирование и смешивание всех компонентов до получения однородного раствора с заданными технологическими свойствами. Поризация раствора происходит на стадии формования изделия. При пенобетонной технологии получают готовую поризованную массу. Приготовление формовочной газобетонной смеси состоит в следующем. Отдозированные компоненты ячеисто-бетонной смеси загружаются в вертикальный самоходный газобетоносмеситель вместимостью 5 м³ при включенном перемешивающем механизме в такой последовательности: песчаный или зольный шлам, вода, вяжущее и газообразователь в виде суспензии. Добавки – гипс, жидкое стекло, ПАВ и др. – вводятся в газобетоносмеситель совместно с вяжущим.
Продолжительность перемешивания составляющих до загрузки газообразователя 3-5 мин. после загрузки газообразователя перемешивание осуществляется в течение 1-3 мин. во время перемещения газобетоносмесителя к формовочному посту. При вибрационной технологии перемешивание осуществляется в процессе вибрации корпуса смесителя – виброгазобетономешалки.
При изготовлении смеси для пенобетона в смеситель с готовым раствором подается пена, которую получают в специальном пеновзбивателе. Приготовление формовочных масс для газобетона предусматривает подогрев шлама, и воды до 40-50ºС для достижения температуры смеси не ниже 35ºС, это интенсифицирует газообразование.
Формование ячеистобетонных изделий из газобетона и пенобетона выполняется по-разному. При газобетонной технологии ячеистобетонный раствор заливается в формы, в которых осуществляется вспучивание (поризация) до заданных значений средней плотности. При пенобетонной технологии смесь с заданными значениями пористости заливается в форме, причем в дальнейшем существенного изменения пористости не происходит.
Стадия формования – одна из важнейших операций в технологии газобетонных изделий. На этой стадии должно быть соблюдено основное условие получения поризованной массы с хорошо организованной пористостью. Кинетика газовыделения должна соответствовать изменению реологических свойств массы. При литьевой технологии вспучивание ячеистобетонной массы происходит в неподвижных формах в течение 25-50 мин., при вибровспучивании форму вибрируют в течение всего процесса газовыделения (3-6 мин.).
Средняя плотность газобетона при постоянной дозировке газообразователя зависит от газоудерживающей способности смеси, которая определяется изменением во времени ее структурно-механических характеристик. Если после газовыделения смесь не будет обладать определенной несущей способностью, произойдет ее осадка сопровождающаяся «ложным кипением» - прорывом газа из формуемого изделия. Для образующейся в этих условиях структуры ячеистого бетона характерны наличие пор неправильной формы, большое число сообщающихся пор, неоднородность распределения пористости. Если схватывание опережает газовыделение, то смесь затвердеет до того, как завершатся процессы газовыделения и заданная средняя плотность не будет достигнута, а межпоровые перегородки окажутся пронизанными трещинами. В результате снижаются эксплуатационные показатели материала. В связи с этим основным этапом в управлении процессами вспучивания и структурообразования газобетонных смесей является сбалансирование скоростей этих процессов, причем в начале газовыделения пластично-вязкие свойства массы должны возрастать медленно, а в конце – быстро.
Специальные технологические приемы позволяют активно воздействовать на процессы формирования структуры ячеистого бетона. Наиболее эффективно вибровспучивание.
Под воздействием вибрации происходит тиксотропное растяжение ячеистобетонной массы, обеспечивающее высокую степень гомогенизации смеси во время виброперемешивания и интенсивную поризацию на стадии вибровспучивания. Особо эффективна вибрация с добавками ПАВ.
После прекращения вибрационных воздействий быстро восстанавливаются разрушенные вибрацией структурные связи, и в результате резко возрастают пластическая прочность и несущая способность поризованной массы, исключается ее осадка. Применение вибрационной технологии позволяет значительно снизить водотвердое отношение, использовать грубодисперсные композиции, интенсифицировать технологический процесс изготовления ячеистого бетона. Снижение водотвердого отношения обеспечивает повышение плотности и прочности цементного камня, интенсификацию реакций газообразования и твердения, уменьшения затрат тепла на прогрев изделий в процессе твердения и их послеавтоклавной влажности, улучшение микропористой структуры материала и повышение его физико-технических свойств (снижение усадки, уменьшения водопоглощения, повышение морозостойкости).
Интенсификация технологического процесса при применении вибрации выражается в ускорении: процессов гомогенизации на стадии смешивания за счет оптимизации реологических свойств и вибрационного перемешивания частиц; газовыделения и вспучивания массы вследствие увеличения pH смеси, обнажения новых реакционных поверхностей на частицах алюминиевой пудры при вибрации, усиления диффузионных перемещений среды и газовых пузырьков; схватывание массы и приобретения массивами прочности, достаточной, для резки; тепловлажностного твердения массы из-за повышенной температуры массивов в момент начала тепловой обработки. Таким образом, применение комплексной вибрационной технологии обеспечивает интенсификацию производства, повышение качества и улучшение технико-экономических показателей ячеистого бетона.
Для получения теплоизоляционного ячеистого бетона низкой средней плотности эффективно прибегать к предварительной поризации смеси – так называемой газопенной технологии.
Предварительную поризацию осуществляют, аэрируя песчаный шлам на стадии мокрого помола песка в присутствии ПАВ или формовочную смесь с ПАВ на стадии приготовления ячеистобетонного раствора в смесительном агрегате.
Теплоизоляционные изделия из газобетонных смесей вспучиваются в металлических формах высотой до 600 мм; перед заливкой формы должны быть тщательно очищены, смазаны, собраны, стыки уплотнены, чтобы смесь не вытекала во время заливки.
Формы заливают ячеистобетонной смесью за один прием на высоту, обеспечивающую полное заполнение формы после вспучивания (высота залива составляет примерно 1/3).
Высоту заполнения формы ячеистобетонной смесью определяют по формуле:
h=1.2·h0·ρм/ρр,
где h0 – высота формы, см;
ρм,ρр – соответственно средние плотности ячеистобетонной массы и раствора кг/м³.
Чтобы вспучивание смеси протекало нормально, температура окружающей среды должна быть не ниже 20ºС.
При литьевой технологии применяют агрегатно-поточный метод формования. В этом случае формы устанавливают вдоль пути передвижения газобетономешалки, при этом обеспечиваются условия, предотвращаются какие-либо перемещения или сотрясение форм после заливки газобетонного раствора до затвердения вспучивания и схватывания ячеисто-бетонной смеси.
При вибрационной технологии используют стендовый или конвейерный принцип формования. Изделия из ячеистобетонных смесей формуются на специальном посту, оборудованном виброплощадкой. Металлические формы жестко фиксируются на виброплощадке. Вибрация начинается одновременно с началом заливки форм ячеистобетонной смесью и продолжается до окончания активного газовыделения – прекращения вспучивания смеси.
Назначение предавтоклавной обработки ячеистобетонных изделий – выравнивать открытую поверхность изделий в форме (удаление «горбушки») и разрезать массив (его примерные размеры 6х1.5х0.6 м) на изделия заданных габаритов. Горбушка срезается только с газобетонных изделиях, в пенобетонных она не образуется. Все эти операции выполняются на резательной машине с помощью металлических струн, совершающие возвратно-поступательные движения.
Тепловлажностная обработка эффективных теплоизоляционных ячеистых бетонов осуществляется автоклавированием при давлении 0.9-1.3 МПа и температуре 175-192ºС в среде насыщенного или перегретого водяного пара в автоклавах диаметром 2; 2.6 или 3.6 м.
Автоклавная обработка проходит в три стадии. Первая стадия начинается с момента впуска пара в автоклав и заканчивается при достижении равенства температур теплоносителя и изделий по толщине. Начало второй стадии соответствует моменту выравнивания температуры изделий по его сечению. Решающие факторы, определяющие скорость прогрева изделий, - интенсивность давления пара на первой стадии, значение исходной температуры и влажности ячеистобетонной массы. Быстрый подъем давления в автоклаве, превышение температуры массива и снижение его влажности позволяет значительно сократить длительность первой стадии и всего цикла автоклавной обработки.
Начало второй стадии совпадает с максимальным развитием химических и физико-химических процессов, обуславливающих формирование структуры цементирующего вещества и интенсивный набор материалом прочности. Первоначально в результате избытка насыщенного раствора Са(ОН)2 и недостатка в растворе силикат-ионов (из-за медленного растворения кремнезема) образуются богатые известью двухосновные гидросиликаты кальция С2SH(А). В дальнейшем при полном связывании свободной Са(ОН)2 в высокоосновные гидросиликаты кальция процесс растворения кремнезема приводит к образованию низкоосновных гидросиликатов кальция типа СSH(В) и тобермарита. Формирование этих новообразований сопровождается интенсивным набором прочности.
Продолжительность второй стадии – изобаротермической выдержки – определяется дисперсностью, активностью и соотношением компонентов, водотвердым отношением, температурой обработки. Для третьей стадии показательно снижение температуры и давления. При этом интенсивно испаряется вода. Интенсивное парообразование, связанное со снижением давления пара в автоклаве, вызывает значительные напряжения, иногда превышающие прочность бетона, что приводит к образованию трещин. Для предотвращения трещинообразования при коротких режимах охлаждения применяют ступенчатый режим снижения давления пара в автоклаве.
Готовые изделия из теплоизоляционного ячеистого бетона должны быть упакованы в пакеты и храниться в помещениях с хорошей вентиляцией. Их следует также защищать от возможного увлажнения. Транспортировать изделия нужно в контейнерах, предохраняющих бетон от воздействия атмосферной влаги.
Перспективные направления повышения качества теплоизоляционных ячеистых бетонов.
Экспериментальные исследования показывают возможность дальнейшего снижения средней плотности ячеистого бетона. Поэтому совершенствование технологии должно вестись в сторону стабильного получения в заводских условиях изделий средней плотностью 180-200 кг/м³ с пределом прочности при сжатии 0.4-0.6 МПа и теплопроводностью 0.065-0.07 Вт/(мºС). Это позволяет уменьшить себестоимость изделий более чем на 40%.
Снижение средней плотности ячеистого бетона достигается путем формирования силикатного камня повышенной прочности и создания структуры порового пространства, характеризующейся равномерным распределением пор в объеме изделия и рациональным соотношением ячеистой и капиллярной пористости.
Основными технологическими направлениями повышения прочности силикатного камня являются:
- применение кремнеземистого компонента композиционного полифракционного состава, обеспечивающего снижение пустотности песка и соответственно расхода вяжущего при одновременном повышении плотности межпоровых перегородок;
- повышение однородности ячеистобетонной смеси в результате совместного помола ее твердых компонентов и применения, скоростных вибро- и гидродинамических смесителей;
- дисперсное армирование волокнистой добавкой;
- применение шлакощелочных вяжущих, искусственных или природных стекол, приобретающих в процессе автоклавной обработки в присутствии активизаторов твердения высокие прочностные показатели;
- предавтоклавное «вызревание» ячеистобетонных массивов в специальной камере (туннеле) при температуре 80-90ºС и относительной влажности воздуха не выше 75%, что обеспечивает равномерный прогрев массы и снижение ее влажности более чем в 2 раза.
Формирование высококачественной структуры порового пространства с общим объемом пористости более 90% достигается в результате:
- повышения однородности распределения алюминиевой пудры в ячеистобетонной смеси;
- предварительной поризации массы на стадиях мокрого помола кремнеземистого компонента или в смесителе при подготовке ячеистобетонной смеси в результате применения ПАВ воздухововлекающего типа;
- применения специальных газообразователей – гидрофильных (газопласт и газапенопласт), характеризующихся отсутствием эффекта «старения», хорошим распределением в ячеистобетонной массе, способствующих дополнительному воздухововлечению при перемешиванием ячеистобетонного раствора в смесителе;
- создания интенсивных внешних механических воздействий (вибрационных, колебательных, ударных, ультразвуковых и т.п.) на стадии вспучивания ячеистобетонной смеси.
На стадии автоклавного твердения целесообразны:
- запаривание при интенсивном подъеме температуры и давления предварительно разогретых и подсушенных ячеистобетонных массивов;
- сокращение режимов изобаротермической выдержки, что исключает деструктивные явления в результате рекристаллизации новообразований;
- быстрый ступенчатый сброс давления (1.5-2 ч.) на третьей стадии автоклавной обработки, что обеспечивает получение изделий с пониженной влажностью.
Улучшению экономических показателей производства теплоизоляционного бетона способствует применение пара пониженной температуры (142-151ºС) и давления (0.4-0.5 МПа), что снижает более чем на 50% расход пара и топлива и более чем в 2 раза повышает коэффициент загрузки автоклавов при использовании сосудов прямоугольной конфигурации, в том числе железобетонных.
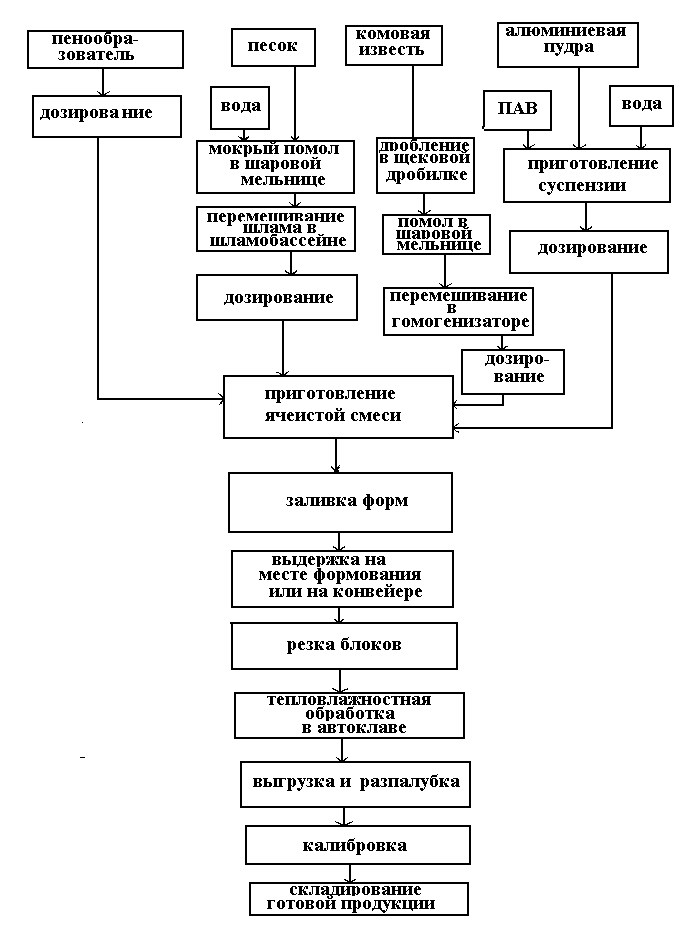
Рис.1.
Ячеистое стекло
1. Пеностекло и изделия из него
Пеностекло представляет собой легкий пористый материал из стекла, в котором равномерно распределенные ячейки разделены тонкими стенками. Свое название оно получило благодаря внешнему виду, напоминающему застывшую пену.
Ячеистая структура стекла может быть получена разными способами:
- введением в состав шихты веществ, вызывающих обильное пенообразование в процессе варки стекла;
- вспениванием размягченного стекла под вакуумом;
- вспениванием измельченного стекла пенообразующими веществами на холоде с последующим фиксированием структуры спеканием частиц стекла (холодный способ);
- спеканием смеси порошкообразного стекла с газообразователем (порошковый способ).
В промышленных масштабах пеностекло получают порошковым способом.
Свойства пеностекла
Пористость. В зависимости от технологии производства, химического состава стекла и вида газообразователя пеностекло обладает открытой или закрытой пористостью (в основном закрытой). Из стекол с низкой температурой начала кристаллизации получается материал с сообщающейся пористостью. Во всех случаях предпочтительнее мелкая пористость. Объем пор в пеностекле колеблется от 80 до 95%. Помимо пор, разобщенных стекловидными стенками, в материале самих стенок содержатся мельчайшие микропоры.
Средняя плотность. Она может колебаться от 150 до 800 кг/м³ в зависимости от изменения температуры и продолжительности вспенивания, подбора газообразователя, степени дисперсности порошков стекла и газообразователя.
Прочность. Характерной особенностью пеностекла является его высокая прочность в сравнении с другими ячеистыми материалами, она объясняется высокой прочностью стекловидной фазы. Например, прочность пеностекла больше прочности ячеистого бетона, при одинаковой средней плотности приблизительно в 3 раза.
Водопоглощение. Пеностекло с закрытой пористостью характеризуется невысоким водопоглощением – от 1 до 10% (по объему). В основном вода адсорбируется в разрушенных ячейках поверхности стекла. Водопоглощение пеностекла с сообщающейся пористостью достигает 70-80% (по объему). Водостойкость пеностекла велика и определяется гидролитическим классом стекла. Гигроскопичность очень мала и исчисляется долями процента по объему.
Морозостойкость. Пеностекло является морозостойким материалом, если его поверхность защищена от увлажнения и, следовательно, от последующего деструктивного воздействия льда в поверхностных открытых порах.
Теплопроводность – низкая – 0,055-0,085 Вт/(мºС) в результате стеклообразного строения каркаса и малого размера пор.
Стойкость к действию высоких температур. Пеностекло негорючий материал, оно устойчиво к действию высоких температур вплоть до температуры размягчения. Обычное пеностекло можно применять в пределах 400-500ºС, бесщелочное стекло – до 600ºС, и высококремнеземистое – до 1000ºС.
Пеностекло характеризуется хорошими звукопоглощающими свойствами, высокой биостойкостью, легко поддается механической обработке, в него можно вбивать гвозди.
Сырьевые материалы
Для производства пеностекла используют стекло, сваренное из следующих исходных материалов: кварцевого песка, известняка, соды и сульфата. Можно также использовать отходы стекольного производства; бой оконного или тарного стекла; легкоплавкие горные породы, содержащие щелочи.
Сваренную в ванной печи стекломассу превращают в гранулы, для этого массу сливают на металлический конвейер и обильно орошают водой.
Отходы стекольного производства и бой стекла неоднородны по химическому составу, что затрудняет их переработку. Для снижения стоимости гранулята соду и глинозем можно заменять щелочесодержащими горными породами и отходами производства: нефелины, перлиты, андезиты, вулканические пеплы, легкоплавкие озерные глины, а также золы ТЭС и другие.
Химический состав стекла должен быть: SiO2 – 72-73%, CaO – 6-7%, MgO – 3-4%, Na2O – 14-16%, AL2O3 – 0.8-2%, SO3 – 0.4-0.5%.
В качестве газообразователей применяют вещества, выделяющие при нагревании газы: антрацит (1,5-2,0 % от массы), металлургический кокс 2-3%, ламповую сажу 0.2-0.5%, торфяной полукокс и мраморную крошку 1-1,5% и др. К ним предъявляются требования: температура выделения газа должна быть на 50-70ºС выше температуры размягчения стекольного порошка, равномерное выделение газа, недефицитность, нетоксичность, невысокая стоимость.
Выбор вида газообразователя зависит от температуры спекания и вязкости стекла, от характера пористости и окраски пеностекла.
Физико-химические основы порошкового способа производства пеностекла
Сущность порошкового способа заключается в следующем: шихту, состоящую из молотого стекла и газообразователя (0.5-3% от массы стекла) засыпают в формы, нагревают до вспенивая и охлаждают.
При нагревании сначала частицы стекла размягчаются. Для большинства стекол это происходит при температуре 600ºС. Вязкость массы в этот период велика. При дальнейшем нагревании начинается разложение газообразователя, а вязкость снижается.
Выделяющиеся газы образуют в стекломассе поры, диаметр которых постепенно возрастает, т.к. пленки стекла растягиваются под влиянием давления газы, и объем стекломассы значительно увеличивается. По достижении массы определенного объема температуру в печи снижают, чтобы прекратить разложение газообразователя и закрепить полученные объем и структуру. При резком возрастании вязкости с понижением температуры структура становится устойчивой. В процессе порообразования вся масса представляет собой пластичную вязкую систему, в которой равномерно распределен газообразователь, выделяющий газ и создающий устойчивую и равномерную пену стекла.
При образовании пены основное значение имеют вязкость жидкости и поверхностное натяжение на границе жидкость - газ. Вязкость противодействует разрыву пленки, а низкое поверхностное натяжение способствует ее утоньшению. При высоком поверхностном натяжении пена не образуется. Пенообразование при высокой вязкости стекломассы возможно лишь тогда, когда давление газовой фазы в состоянии вспенить стекломассу. Это давление может достигнуть 1,1 МПа (680º С). Вязкость и поверхностное натяжение зависят от химического состава стекла, давление газовой фазы зависит от вида газообразователя. Помимо химического состава стекла и вида газообразователя на структуру и на свойства пеностекла влияют следующие технологические факторы: тонкость помола стекла и количество газообразователя, температура и продолжительность вспенивания.
Чем меньше размер зерен спекаемого материала, тем лучше его качества. Применяют порошок, тонкость помола которого определяется полным прохождением через сито с 6400 отв/см², остаток на сите со 10000 отв/см² - 10%. Повышение количества газообразователя в известных пределах приводит к уменьшению средней плотности, но при этом увеличивается диаметр пор. При введении более 3-5% газообразователя получается пеностекло с неравномерной крупнопористой структурой из-за высоких давлений, развиваемых газовой фазой при нагревании.
Влияние температуры сказывается следующим образом: чем выше температура спекания, тем меньше средняя плотность. Это происходит вследствие снижения вязкости и более быстрого разложения газообразователя. Повышение температуры целесообразно до определенного предела, выше которого вязкость уменьшается настолько, что стенки пор прорываются и образуются крупные пустоты. Чем длительнее процесс вспенивания при одной и той же температуре, тем меньше средняя плотность пеностекла вследствие образования большого количества газовой фазы. Увеличивая продолжительность спекания при относительно низких температурах, можно получить те же результаты, что и при кратковременном спекании, но при более высоких температурах.
Технология производства пеностекла (порошковый способ)
Ее можно разбить на следующие этапы: варка стекла и подготовка стекольного гранулята, приготовление шихты, вспенивание при температуре 700-850ºС и отжиг, обработка и упаковка.
Варят стекло в ванных печах. До варки в печи сырьевые материалы предварительно обрабатывают. Сваренную стекломассу гранулируют, для чего через отверстия в выработочной части печи сливают ее на металлический конвейер, орошаемый водой. Рекомендуется обильное орошение, предотвращающее кристаллизацию.
Приготовление шихты заключается в следующем. Стекольный гранулят измельчают на щековых, молотковых дробилках до размеров 1-3 мм. Если используют газообразователь в кусках, то его тоже измельчают до зерен размером не более 1 мм. Затем осуществляют совместный помол и перемешивание стекла и газообразователя в шаровых двухкамерных мельницах непрерывного действия.
Если в качестве сырья используют бой и отходы стекольного производства, то эти материалы дробят в щековой дробилке, промывают в боемолке и сушат в барабане. После этого стекло измельчают в молотковой дробилке.
Чем меньше частицы стеклянного порошка, тем однороднее поры и тем они равномернее распределены в материале. При этом материал получается более прочным. Тонкость помола определяют остатком порошка при просеивании на сите с 10000 отв./см², остаток должен быть не более 10% от массы порошка. Производительность мельницы составляет 1200 кг/ч. Размалывать следует в мельницах с керамической или кремневой футеровкой и кремневыми мелющими телами во избежание загрязнения металлом.
Основная технологическая задача в производстве пеностекла – вспенивание стеклянной шихты, в результате чего материал приобретает ячеистое строение.
Вспенивание и обжиг можно вести по следующим схемам: получение пеностекла в формах из жаростойкого металла одно- и двухстадийным способами; получение пеностекла без форм конвейерным способом на металлических жаростойких поддонах или лентах.
При двухстадийном способе производства формы с шихтой поступают в печь вспенивания, где нагреваются до температуры 800ºС, необходимой до образования пористой структуры, и затем охлаждаются до 600ºС, чем достигается стабилизация пористой структуры. Продолжительность вспенивания 3 часа. Для вспенивания применяют формы из жаростойкого металла, состоящие из одинаковых полуформ. Нижняя полуформа имеет выдвижное днище, облегчающее извлечение блоков. Перед засыпкой шихты формы смазывают каолиновым составом, куда входят каолин, асбест, вода в соотношении 2:1:1 (по массе), во избежание прилипания блоков.
Вспенивание производят в туннельных печах муфельного или полумуфельного типа с подподовыми топками. Они имеют три зоны: подогрева, вспенивания и стабилизации.
Рис. 2. Технологическая двухстадийная схема производства пеностекла
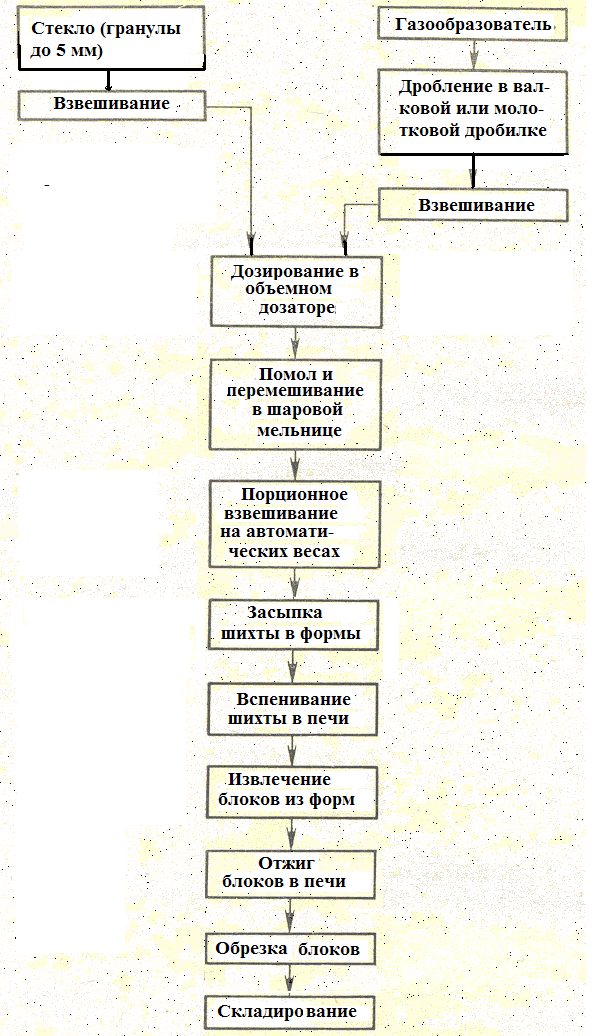
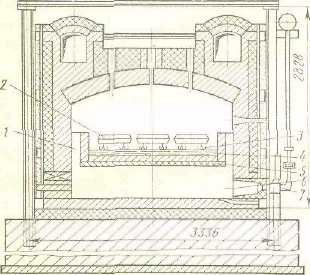
Рис.3. Печь для вспенивания пеностекла: 1— вертикальные каналы,
2 - формы, 3 - ползуны, 4 - направляющие, 5- жаростойкие плиты,
6 - подовые топки, 7 -горелки
Отапливаются печи газом или жидким топливом. Формы 2 с шихтой, установленные в один ряд по высоте и в два или три по ширине, перемещаются на роликовом конвейере или на специальных ползунах по металлическим направляющим 4. По выходе форм из печи из них извлекают блоки, которые передают в печь обжига.
Отжиг блоков из пеностекла заключается в медленном охлаждении их от температуры спекания до температуры наружного воздуха. Благодаря этому объем блоков сокращается равномерно, что предохраняет их от возникновения внутренних напряжений, образующихся при быстром охлаждении. Блоки устанавливают на «ребро» на сетчатый конвейер и направляют в конвейерную печь длиной 30 м и шириной в свету 1,8 м. Разница температур вдоль блока в горизонтальном или вертикальном направлении не должна превышать 5-10ºС, что обеспечивается принудительной циркуляцией теплоносителя в вертикальном направлении. Обжигают до 250ºС в течение 11 часов.
При одностадийном способе производства формы, наполненные шихтой, устанавливают на вагонетки, и они поступают в туннельные печи, где проходят зоны вспенивания и обжига. Общее время вспенивания и обжига 21-22 ч. Температурный режим характеризуется быстрым подъемом температуры до800-830ºС, непродолжительной выдержкой ее при наивысших значениях и значительным периодом обжига пеностекла, который заключается в его медленном охлаждении. Благодаря отжигу происходит равномерное сокращение объема блоков, что предохраняет их от вредных напряжений и растрескивания. Основные показатели процесса вспенивания – температура и время – влияют на плотность получаемого пеностекла; чем выше температура и больше продолжительность процесса, тем ниже плотность. Меняя эти параметры, можно регулировать плотность и другие свойства пеностекла.
Конвейерный способ производства заключается в непрерывной подаче шихты на пластинчатый конвейер из жаростойких элементов, которые представляют собой поддоны, загнутые с двух концов. Поддоны соединены между собой встык и образуют желоб. По мере продвижения желоба в печи шихта нагревается, вспенивается и образует ленту пеностекла. Ровная поверхность ленты пеностекла создается прокаткой валиками. По выходе из печи вспенивания от ленты пеностекла дисковой пилой отрезают плиты заданных размеров. Плиты автоматически передаются в печь отжига.
Механическая обработка необходима для придания плитам точных размеров и ровной поверхности. Опиловка плит осуществляется – маятниковыми, каретными или другими дисковыми пилами. Плиты по толщине распиливают ленточными пилами. Опиловочные и шлифовальные станки оборудованы пылеотсасываемыми устройствами.
Как показал опыт двухстадийный способ производства более совершенный, чем одностадийный. Он позволяет получать пеностекло высокого качества при хороших технико-экономических показателях. Дальнейшее развитие производства должно идти по разработке непрерывных способов получения пеностекла.
В настоящее время расширение производства пеностекла сдерживается высокой стоимостью и дефицитностью сырья.
Теплоизоляционное пеностекло – хороший теплоизоляционный материал для стен перекрытий различных строительных сооружений, а также для изоляции промышленных холодильников и технологического оборудования, работающего при отрицательных температурах, например хранилищ сжиженных газов.