Общетеоретические основы логистики 3
Вид материала | Документы |
- Аннотации основы логистики и управления цепями поставок, 148.38kb.
- Программа дисциплины по кафедре «Эксплуатация автомобильного транспорта» Основы логистики, 307.32kb.
- Магистерская программа: Менеджмент в электроэнергетике Квалификация (степень) выпускника:, 133.56kb.
- Канаева М. Начальник отдела логистики Lanxess ао «Байер» Основы организации отдела, 127.88kb.
- 1. Объективные основы развития логистики, 1059.15kb.
- Рабочей программы дисциплины Основы логистики (наименование) по направлению подготовки, 22.64kb.
- Основы транспортной логистики [+] История развития логистики. Её функциональные области., 296.26kb.
- С. Э. Лекции по спортивной морфологии. №02-03 «Общетеоретические основы адаптации., 597.82kb.
- Тема кол-во часов, 182.97kb.
- Учебно-тематический план курса «Основы логистики и логистический менеджмент» Очно-заочная, 21.96kb.
Раздел 3. Логистическое управление, направления развития логистики
Тема 14. Управление логистической системой. Контроллинг.
Основными принципами логистики, как известно, являются оптимизация, синхронизация, рационализация всех взаимосвязанных операций и системный подход ко всему процессу в целом. Именно эти принципы позволяют на качественно новой основе организовать управление сложными производственными системами. Естественно, традиционные методы управления производственным процессом, например, в виде производственной программы, нормирования, контроля и т.д., сохраняются. Задачами логистики здесь являются рационализация использования материальных ресурсов для обеспечения оптимального процесса изготовления продукции и организация во времени и пространстве соответствующих производственному циклу материальных и информационных потоков. При этом самым главным параметром оценки внедрения логистических принципов является снижение совокупных затрат на производство продукции.
Организация материальных потоков в соответствии с основными логистическими принципами требует решения комплекса взаимоувязанных задач, к которым, прежде всего, относятся:
- Своевременная поставка сырья, материалов и комплектующих, необходимых для производства, и эффективное управление запасами, так как большое общее количество запасов может привести к дефициту отдельных компонентов. Общее количество запасов – это "омертвленные" деньги, которых может недоставать именно в тот момент, когда производству требуется сырье совершенно другой номенклатуры.
- Достижение оптимального соответствия производственных мощностей (основного и вспомогательного оборудования и рабочей силы) производственному заданию. Здесь, прежде всего, от менеджмента требуется согласование объема принимаемых заказов имеющимся мощностям производства и, конечно, установление приоритетов в исполнении заказов.
- Налаживание согласованной работы всех подразделений предприятия (основных, вспомогательных, управленческих) по единому графику, базой для которого является сроки выполнения конкретного заказа на готовую продукцию.
- Концентрация усилий на обеспечении максимальной непрерывности и ритмичности движения внутрипроизводственного материального потока, а также постоянной во времени загрузки каждого рабочего места. Это особенно важно для условий непоточного производства, в рамках которого, как показывают исследования, простои оборудования и работника приносят многократно большие убытки, чем "пролеживание" деталей и незавершенного производства. При поточном (в частности, конвейерном) производстве фиксируется обратная картина: здесь основным фактором снижения совокупных издержек является ликвидация межоперационных запасов незавершенного производства.
- Упорядоченное и равномерное движение материальных потоков на производственных площадях невозможно без организации типовых (стандартных) внутрипроизводственных маршрутов перемещения деталей, узлов и незавершенного производства для всего производственного цикла, а не по отдельным цехам. Очень важным фактором здесь является также соответствие моментов запуска деталей в производство общей программе (графику) выполнения заказа.
- Возможно более строгое нормирование рабочих процессов. Весь производственный цикл исполнения заказа рассматривается как единая система, при этом расчетные нормативы, устанавливаемые исходя из времени выполнения самой трудоемкой операции, подлежат обязательной корректировке на применение последовательно-параллельного способа организации процесса. Важным является недопущение перевыполнения планового сменного задания, наряду с недовыполнением его.
Рентабельность любого производства зависит от достижения баланса между спросом на производимую продукцию и ресурсами, необходимыми для ее производства.
Прогнозирование спроса обычно производится тремя широко известными способами: временными рядами, причинно-следственными методами и субъективными методами.
К производственным ресурсам относятся производственные мощности (основное и вспомогательное оборудование), рабочая сила, материально-техническое обеспечение.
Объем производственных мощностей, соответствующий спросу на продукцию, вопрос крайне сложный и многовариантный. Прежде всего следует иметь в виду, что любые производственные мощности есть весьма значительные материальные затраты. Вместе с тем объем мощностей устанавливает верхний предел выпуска готовой продукции и нижний предел эксплуатационных издержек.
Составление производственной программы, даже при самом совершенном компьютерном оснащении, является скорее искусством менеджмента, чем математической задачей. Однако существует некий объективный алгоритм составления программы (или производственного расписания). Прежде всего, необходим детальный анализ работы прошлых лет в совокупности с требованиями рынка на данный момент, что может быть серьезной предпосылкой для составления реального прогноза производства. Прогноз является отправной точкой детального планирования на более короткие временные интервалы. Координация отдельных планов и постоянное отслеживание их выполнения с обязательной немедленной корректировкой - дает желаемый результат.
Производственное расписание должно в общем виде дать ответы на следующие вопросы: кто, когда, что и где должно быть сделано и в каком количестве для того, чтобы обеспечить выполнение заказа с требуемым качеством. При этом в должной степени учитывается тот факт, что любое производство располагает ограниченными мощностями и людскими ресурсами и, следовательно, на первое место выдвигается требование по снабжению каждого рабочего места нужными деталями в строго оговоренное время.
Работа по составлению производственного плана (см. Рис. 34) начинается с определения общего объема имеющихся заказов на готовую продукцию (или прогнозных объемов) и ревизии собственных запасов сырья, материалов и комплектующих. Разница между требующимися материалам (в соответствии со спецификациями по заказанной продукции) и имеющимися запасами дает возможность рассчитать потребности в снабжении, трудовых ресурсах и производственных мощностях.
Производственный план дополняется графиком комплектации, в котором указываются все имеющиеся зависимости сроков изготовления готовой продукции. График является основой для плана снабжения и соответствующего ориентирования поставщиков. В плане учитывается длительность циклов поставки сырья и материалов, длительность производственного цикла. Весьма важным является интервал планирования, который, как правило, не может быть меньше 6 месяцев и обычно не превышает 1 года.
Методов планирования производства или составления производственных графиков не так много. Используются обычно три основных метода: "традиционный" – планирование последовательных операций в соответствии с технологическим процессом, метод "ленточной диаграммы" – последовательно-параллельное планирование и сетевое планирование.
Планирование традиционным методом наиболее широко распространено. По своей природе этот метод – "проталкивающий", целью которого является повышение уровня загрузки оборудования. Основным принципом его работы является сохранение одного и того же технологического маршрута. Весь процесс - последовательный и повторяющийся. Весьма удобными с точки зрения управления являются практически обязательные задержки между отдельными стадиями технологического процесса.

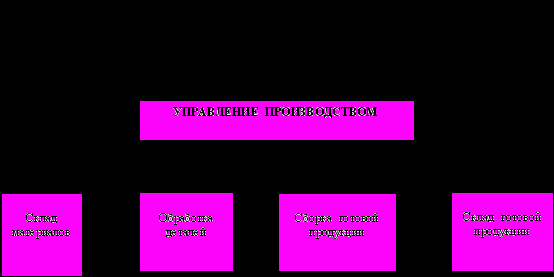
Рисунок 34. Традиционная система планирования и управления производством
Календарно-плановые расчеты этого типа, исходящие из единого для предприятия планового центра (см. Рис. 34), определяют задания по объему, номенклатуре и срокам выполнения работ с соответствующим обеспечением каждого рабочего места необходимыми материалами. Однако при использовании этого метода планирования практически невозможно четко определить последовательность и сроки выполнения конкретных операций даже на несколько дней вперед, что сразу снижает ценность планирования, так как не может быть обеспечена его непрерывность. Обычным является появление неизбежных простоев и авралов, затоваривание отдельными видами деталей и сборочных узлов, сбои во внутрицеховых перевозках, непродуктивная загрузка складских мощностей и, как следствие, рост себестоимости производимой продукции и увеличение суммарных затрат логистической цепочки.
Исследования показывают, что традиционные методы планирования производственных процессов страдают рядом системных недостатков, бороться с которыми можно только введением в план дополнительного времени на производство работ, отстающих от графика цикла, а также планированием дополнительного времени межцехового "пролеживания" незавершенного производства.
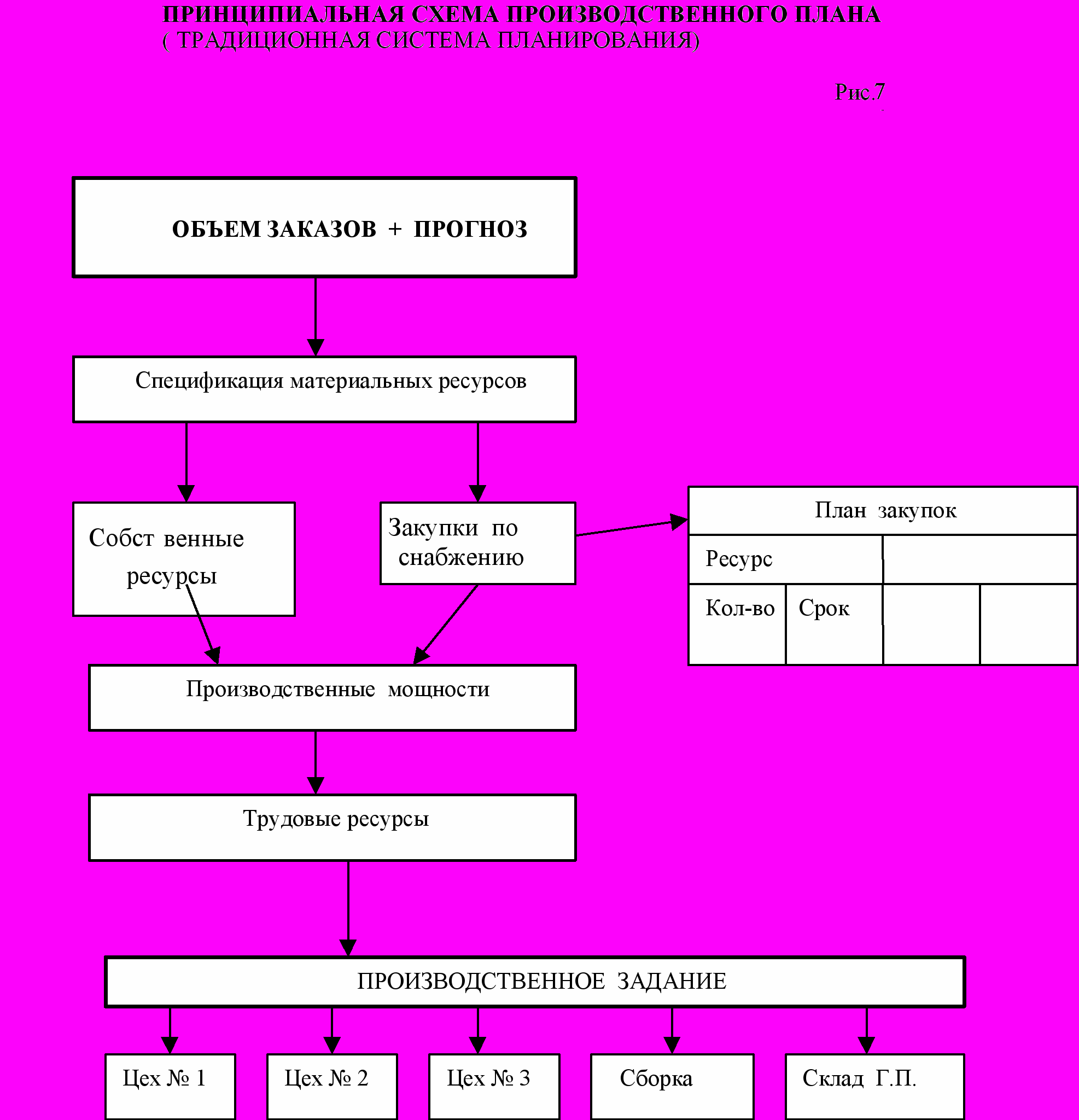
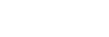
Рисунок 35. Принципиальная схема производственного плана
Согласно принципам логистики, современное производство, снабжение и сбыт готовой продукции должны стремиться, прежде всего, к минимизации запасов материалов, сырья, незавершенного производства и готовой продукции. В принципе, идеальным является вариант с “нулевыми” запасами, однако, внедрить в реальной жизни такой метод работы практически невозможно, хотя бы потому, что нельзя обойтись без так называемых “страховых” (или резервных) запасов. В то же время, кардинальное сокращение запасов служит основой для существенного снижения затрат во всей логистической цепи.
. Внедрение системы кардинального сокращения запасов требует принципиальных изменений во всем комплексе процессов, обеспечивающих производство, таких как транспортировка, складирование, закупки и продажи. Естественно, что на эти преобразования требуются серьезные капиталовложения, которые, впрочем, достаточно быстро окупаются в процессе работ по вновь созданной системе. Что же это за новые системы? Следует сразу оговориться, что эти системы отнюдь не новы, им уже почти полвека.
Первой логистической системой, внедренной в производство промышленной продукции, явилась система КАНБАН, что в переводе с японского означает “Карточка”.
Впервые примененная в японской корпорации "Toyota Motor Corporation" система Kanban представляет собой организацию непрерывно-поточного производства, способную к быстрой перестройке (переналадке) и не требующую больших запасов материалов и комплектующих. Сущность системы состоит в том, что все производственные подразделения снабжаются материальными ресурсами только в том количестве и в то время, которые необходимы для выполнения заказа, выданного подразделением, выполняющим последующий передел или упаковывающим готовую продукцию. Иначе говоря, ни одно из структурных подразделений (цехов, участков, рабочих мест) не имеет общего жесткого графика производства, оно обеспечивает выполнение заказа только следующего в технологическом цикле участка.
. Очень важным элементом системы КАНБАН являются информационные процессы, обеспечивающие ее функционирование. Карточки - это основа информационной системы, поскольку именно в них заложена вся необходимая информация о количестве произведенной и потребленной продукции в каждый конкретный момент времени. Помимо карточек информационными носителями в рамках этой системы являются производственные, транспортные, снабженческие графики, технологические карты, системы контроля качества продукции и т.п. Практическое использование системы КАНБАН и ее последующих модификаций позволило:
- значительно улучшить качество выпускаемой продукции, поскольку качество каждой детали, каждого элемента проверяется практически на месте его изготовления,
- сократить весь цикл снабжения-производства-сбыта, что ускоряет оборачиваемость оборотного капитала фирмы,
- снизить себестоимость продукции за счет кардинального сокращения запасов (на 50% по производственным запасам) и уменьшения незавершенного производства.
Вместе с тем, концепция КАНБАН может успешно применяться в весьма ограниченных масштабах, а именно, только тогда, когда производственный цикл весьма короткий или когда существует непрерывно-поточное производство.
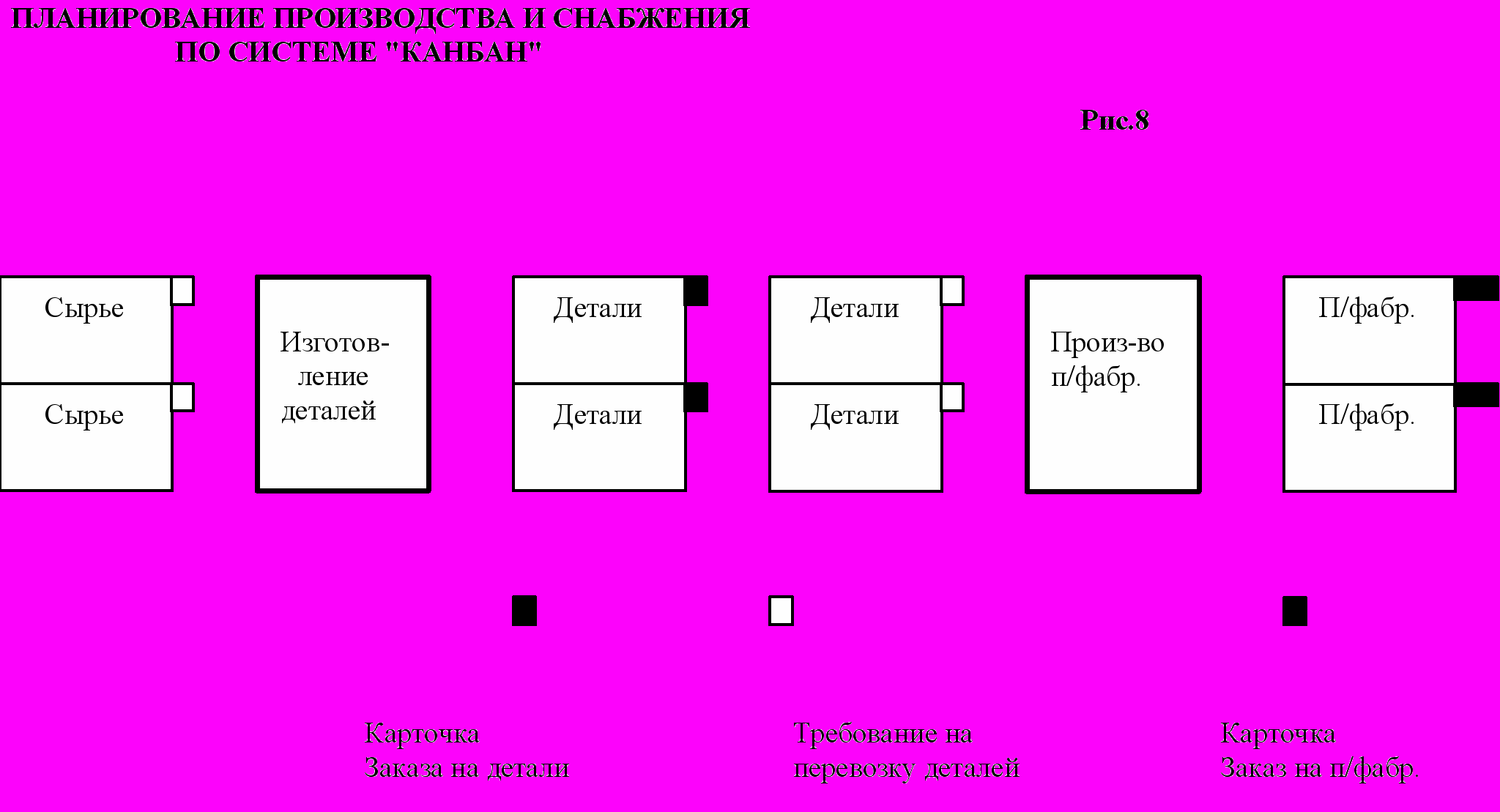


Рисунок 36. Планирование производства и снабжения по системе «Канбан»
На несколько лет раньше и также в Японии была впервые применена еще одна логистическая концепция планирования производства и снабжения, получившая название концепция “точно в срок” (Just in time - JIT). Основная идея этой концепции - полный отказ от любого вида запасов в процессе промышленного производства и, в дальнейшем, в дистрибьюции. Рассуждения здесь достаточно просты: если задано производственное расписание, то возможно так организовать движение материальных потоков, что все сырьевые материалы, детали, компоненты, сборочные узлы будут поступать в строго необходимом количестве, в четко определенное место к назначенному сроку для обеспечения непрерывности сборки или производства. Очевидно, что при таком планировании работ резервные запасы становятся ненужными, что влечет за собой весьма серьезное сокращение производственных издержек из-за высвобождения замороженных в запасах средств. Принципиальная суть этой концепции состоит в том, что заказам потребителей готовой продукции в этом случае соответствуют не предварительно накопленные запасы, а производственные мощности, готовые переработать исходные материалы в готовую продукцию непосредственно “с колес”. В отсутствии запасов материальных ресурсов, организация и управление производственным процессом должны быть практически идеальными, поскольку любой запас в какой-то степени скрывает, нивелирует ошибки и простои в процессе производства. Кроме того, поступающие “с колес” материальные ресурсы просто обязаны быть необходимого качества, брак здесь в принципе невозможен. Безусловно, этот фактор требует выбора абсолютно надежных поставщиков и их заинтересованности в общих результатах бизнеса.
Концепция “точно в срок” применяется, и довольно успешно, на предприятиях, производство на которых осуществляется короткими циклами с небольшими объемами производимой продукции. Только в этом случае появляется реальная возможность синхронизации всех подготовительных, сборочных, упаковочных, транспортных и других видов работ.
Рассматриваемая концепция кардинально изменила практически все принципы управления производством, причем не только для менеджеров, но и для всего персонала компании.
В системе JIT, как видно, появляется несколько существенно новых моментов: во-первых, центральный плановый орган предприятия дает плановые задания не всем без исключения подразделениям предприятия, а только одному - складу готовой продукции (см. Рис. 37). Последний, в свою очередь, отдает распоряжение упаковочному подразделению о необходимости в такой-то срок поставить на склад некоторое количество готовых изделий, тот - задание сборочному цеху и так далее по всей логистической цепочке. Таким образом, классическое производственное задание для всех сразу меняется на конкретные задания для каждого предыдущего участка в технологической цепочке от последующего.
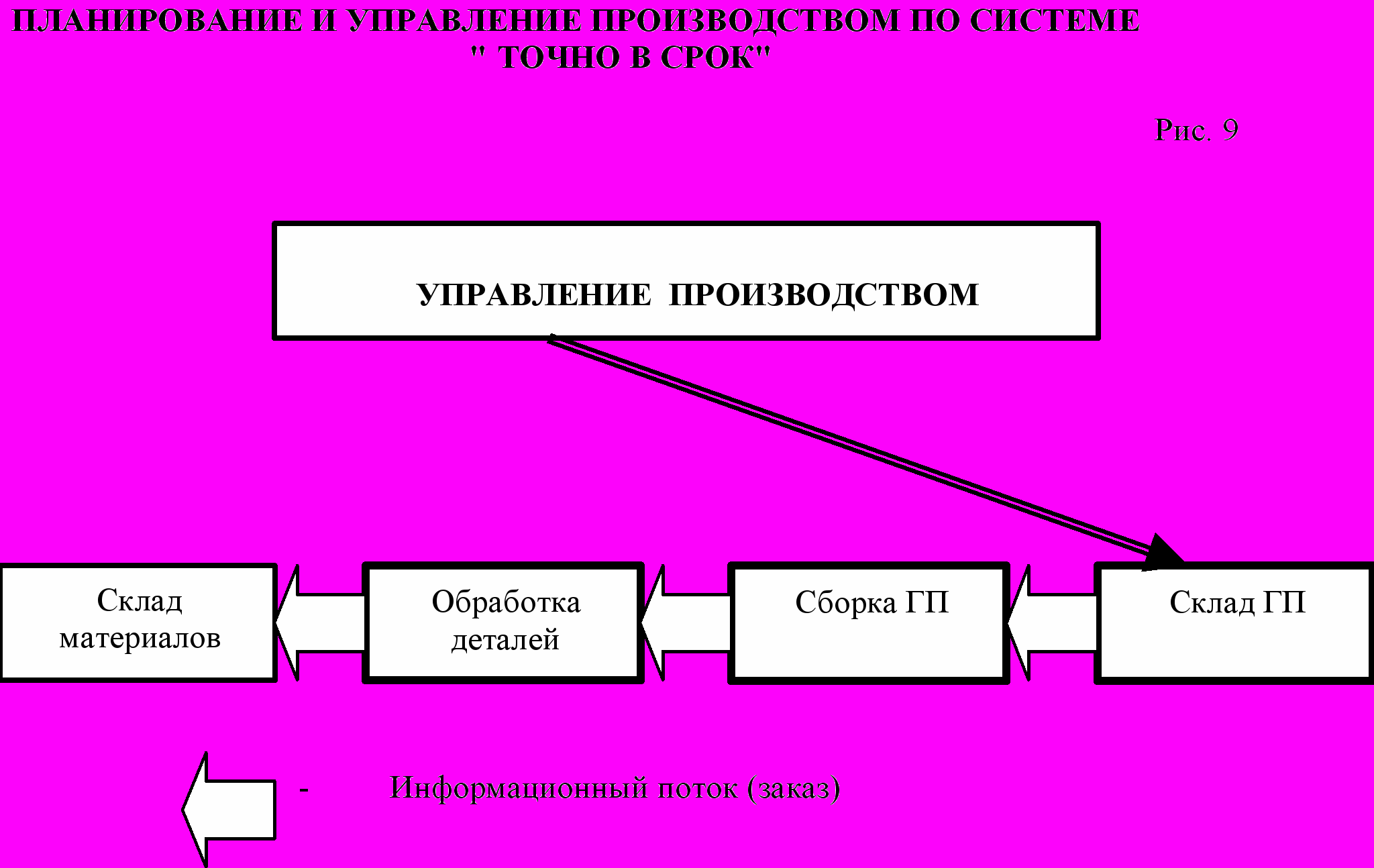

Рисунок 37. Планирование и управление производством по системе «точно в срок»
Внедрение концепции "точно в срок" требует весьма серьезных изменений во всей работе предприятия.
По данным европейских исследователей, результаты внедрения в производство концепции “точно в срок” привело к достижению следующих показателей:
- запасы незавершенного производства снизились в компаниях в среднем на 80%,
- запасы готовой продукции - на 30-35%,
- продолжительность производственного цикла сократилась почти на 40%,
- производственные издержки снизились на 10-20%,
- запасы материальных ресурсов сократились в 7-8 раз.
Системы "Канбан" и “Точно в срок”, как видно из предыдущего, имеют достаточно ограниченное применение: или в сфере непрерывного поточного, чаще, конвейерного производства массовой продукции, или при производстве относительно небольших партий готовой продукции с коротким производственным циклом.
Гораздо более широко применяется популярная ныне логистическая система управления производством, которая носит название “Планирования потребностей в материалах/производственного планирования/ресурсов” или “materials/manufacturing requirements/resours planning” (MRP). Один из авторов системы, американский специалист Дж. Орлиски, определил систему MRP как “планирование логически связанных процедур, переводящих производственное расписание в последовательную цепочку требований, синхронизированных во времени, и покрытия этих требований точным количеством компонентов (материалов, деталей, комплектующих, сборочных узлов), необходимых и достаточных для исполнения расписания”. При этом система MRP дает возможность достаточно надежного перепланирования последовательности “требований” при изменениях либо в производственном расписании, либо в характере продукции, либо в структуре запасов. Рассматриваемую систему планирования и управления производством на основе оперирования запасами материалов и готовой продукции стало возможным использовать на практике только после широкого внедрения быстродействующих компьютеров и соответствующего программного обеспечения.
Cистема планирования MRP-I состоит из ряда логически связанных процедур, правил и требований, переводящих производственное расписание в цепочку требований, синхронизированных во времени, и покрытие этих требований для каждого компонента производства.
Цели системы:
- удовлетворение потребности в материалах, деталях и других компонентах для изготовления готовой продукции и доставки ее потребителю,
- поддержание низкого уровня запасов материальных ресурсов, незавершенного производства и готовой продукции,
- планирования производственных операций, планов закупки и доставки материалов и готовой продукции.
Системы класса MRP-I не только страдают рядом существенных недостатков, но и не обладают возможностями планирования загрузки производственных мощностей, что снижает горизонты их применения.
Принципиальными отличиями второго варианта системы были следующие: ко всем имевшимся в системе MRP-I операциям были добавлены важнейшие функции – планирования производственных мощностей и трудовых ресурсов. Система MRP-II (Manufacturing Resours Planing) способна давать на выходе рекомендации менеджерам по графику выпуска готовой продукции (в расчетном варианте), расчет плана загрузки производственных мощностей, варианты размещения заказов на материальные ресурсы с соответствующим контролем закупок. Интересным новшеством в этой системе является наличие программного блока, который отслеживает объем незавершенного производства в режиме реального времени.
Система MRP-II работает обычно в режиме реального времени с ежедневным обновлением базы данных, что во много раз повысило эффективность планирования производства и управления материальными потоками внутри фирмы и во взаимоотношениях с поставщиками и потребителями. В настоящее время в мире существует несколько сотен прикладных компьютерных программ системы MRP-II, содержащих базовые конфигурации всех необходимых для планирования блоков. Однако нужно отчетливо представлять себе, что любая из этих программ в обязательном порядке должна быть адаптирована к каждому конкретному производству, к каждой конкретной компьютерной сети компании. И еще. Системы планирования MRP-I и MRP-II никогда не выдают, да и не могут, по определению, выдать готовое решение ни по какому вопросу, они предлагают только варианты решения проблем. Окончательное решение во всех случаях принимает менеджер.
На базе системы производственного планирования MRP-II была создана и получила достаточно широкое распространение “Система планирования распределения продукции” DRP-II (distribution requirements/resours planing). Эта система по своим операционным возможностям и особенностям вполне аналогична системе производственного планирования. Основным различием является тот факт, что система MRP базируется на производственном расписании, которое находится под постоянным и действенным контролем самой фирмы, тогда как основой системы DRP является потребительский спрос, который не может контролироваться фирмой. В условиях неопределенности спроса система планирования дистрибьюции безусловно является менее надежной по выдаваемым результатам, однако, она достаточно четко определяет и контролирует запасы продукции на складах фирмы-производителя, на собственных оптовых складах, в товаропроводящей сети и у связанных торговых посредников. Система выдает для обсуждения менеджменту фирмы график (расписание) поставок и пополнения запасов во всей распределительной сети (см. Рис. 38).
Дальнейшим расширением сферы применения идей систем MRP стала разработка программ управления всем предприятием, а не только его производственно-снабженческой деятельностью. Появились и внедряются в практику (правда, с разной степенью успешности) системы планирования и управления ERP (enterprises resours planing) практически всеми функциональными и производственными подразделениями промышленного предприятия.
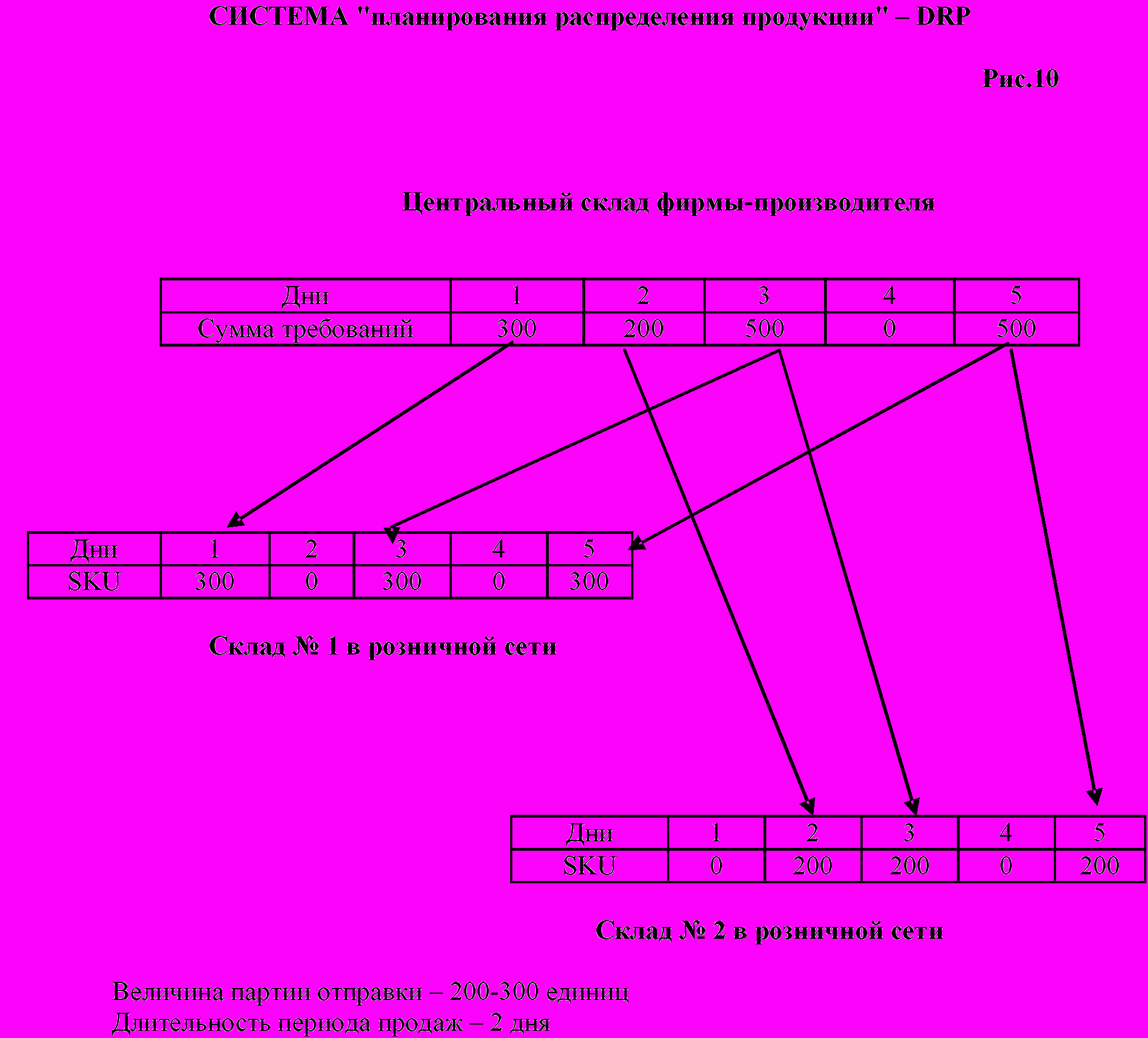

Рисунок 38. Система планирования распределения продукции DSP
Вполне естественным оказалось самое разнообразное сочетание различных элементов всех рассмотренных логистических систем в различных производствах, большинство из которых просто не могут применять без изъятий или, напротив, некоторых дополнений ту или иную концепцию в реальной жизни. Практически любой из суррогатов получил право на жизнь в случаях, если его применение принесло сокращение суммарных издержек на выходе.