«Библиотека станочника»
Вид материала | Книга |
- Библиотека Хельсинского Университета была написана небольшая статья, 63.53kb.
- Инструкция по охране труда при выполнении, 437.7kb.
- Городских библиотек, 1814.45kb.
- «Металлообрабатывающие станки и комплексы», 14.41kb.
- Библиотека Альдебаран, 2189.93kb.
- Нейшем "Автор" с одной стороны, и Научная медицинская библиотека Ярославской государственной, 39.73kb.
- Библиотека православной культуры, 94.2kb.
- РосБизнесКонсалтинг Список онлайн-библиотек экономической тематики, 63.04kb.
- 1. Александрова Т. Домовенок Кузька…(с продолжениями), 69.48kb.
- Министерства Российской Федерации по делам печати и телерадиовещания Диссертации Библиотека, 617.88kb.
ЭЛЕКТРОХИМИЧЕСКИЕ МЕТОДЫ ОБРАБОТКИ МАТЕРИАЛОВ
1. ЭЛЕКТРОХИМИЧЕСКАЯ ОБРАБОТКА В СТАЦИОНАРНОМ ЭЛЕКТРОЛИТЕ
Электрохимическими называются методы обработки металлов,, основанные на использовании явления электролиза, т. е. явлений,., возникающих при прохождении электрического тока через растворы электролитов. В большинстве электрохимических методов обработки используется преимущественно процесс анодного растворения — переход металла, помещенного в электролитическую ванну в качестве анода, из металлического состояния в различные неметаллические соединения (соли, гидроокиси, окислы).
В электролитах молекулы вещества распадаются на электрически заряженные частицы — ионы, каждый из которых переносит один или несколько электрических зарядов. Число положительных И отрицательных зарядов, переносимых ионами, одинаково, и поэтому в целом электролит электрически нейтрален. Например, молекула хлористого натрия, растворяясь в воде, распадается на катион натрия Na+ и анион хлора С1, кроме того, вода содержит Ионы водорода Н+ и гидроокиси ОН-. Если к электродам, погруженным в этот раствор, приложить разность потенциалов, то анионы гидроокиси ОН~ и хлора С1~ будут двигаться к аноду, а катионы водорода Н+ и натрия Na+ — в сторону катода (рис.68). Электрическая цепь (источник питания — электрод — электролит — электрод — источник питания) при этом замкнется, и источник питания будет перемещать электроны по внешней цепи. Ионы металла Me будут переходить в раствор. Для железа, например, это можно записать следующим образом:
Fe—2eFe+2.
Рис. 68. Схема анодного растворения металла
Рис. 68. Схема анодного растворения металла
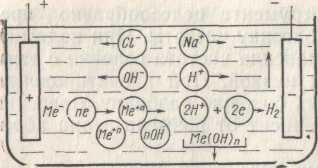
Образующийся ион металла Me связывается с ионом гидроокиси ОН~, образуя гидрат окиси металла Ме(ОН), который плохо растворяется в воде и выпадает в осадок
Fe+2 + 2ОН~ -* Fe (ОН),.
Ионы водорода Н+ разряжаются на катоде, образуя атомы водорода, которые в виде пузырьков уходят из раствора:
Н+ + е -> Н; Н + Н -> H2f.
Кроме указанных основных электродных реакций, возможны и другие побочные. Например, выделение газообразного кислорода «а аноде
2ОН- — 2е
Н2О
О; О + О -> O2f.
Содержащиеся в растворе ионы хлора и натрия переносят электрические заряды, их присутствие может вызвать или образование щелочи NaOH и хлористого железа FeCl, или выделение газообразного хлора на аноде.
Классификация операций электрохимической обработки. Операции электрохимической обработки, осуществляемые по одному и тому же принципу, по существующей классификации могут быть разделены на две различные (по технике проведения и результатам) группы: 1) при невысокой плотности тока в стационарном электролите; 2) при высокой плотности тока в проточном электролите (анодно-гидравлическая обработка).
Электрохимическую обработку в стационарном электролите делят на полирование, профилирование (копирование), заострение' (затачивание), доводку.
Электрохимическую обработку в проточном электролите подразделяют на профилирование (копирование), резание, прошивание, протягивание и калибрование.
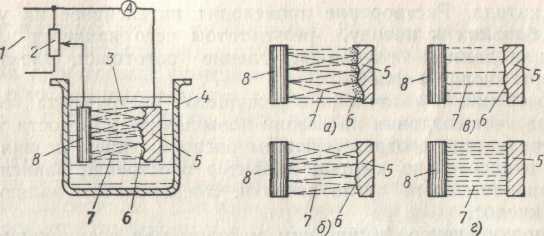
Рис. 69. Схема электрохимической обработки в стационарном электролите
а— схема установки; б—д—последовательные стадии сглаживания поверхности; 1 — источник тока; 2 — резистор; 3 — электролит: 4 — ванна; 5—заготовка; 6 — пленка продуктов растворения во впадинах поверхности; 7 — силовые линии тока; 8 — катод
При электрохимической обработке с высокой плотностью тока необходимо интенсивное удаление из зоны обработки продуктов анодного растворения. Последнее может осуществляться одним из трех способов: поточным электролитом, прокачиваемым под давлением через зону обработки; механическим, электроэрозионным и ультразвуковым воздействием на обрабатываемую поверхность; механическим удалением шлифовальным диском, хонами или абразивными частицами, свободно находящимися в электролите.
На рис. 69 показана принципиальная схема электрохимической обработки в стационарном электролите для наиболее типичной; операции — электролитического шлифования или полирования. Электрический ток, проходя через электролит 3 и электроды 8 и 5, вызывает растворение поверхности анода 5 в электролите и образование продуктов растворения 6, которые, задерживаясь в углублениях шероховатости поверхности, изолируют последние or прохождения тока, сосредоточивая его силовые линии на незащищенных участках поверхности анода. Происходит быстрое растворение выступов, и поверхность анода сглаживается.
Электрополирование имеет многообразное применение. Наилучшее качество поверхности достигается при электрополировании чистых и однородных металлов и сплавов. Полирование турбинных лопаток из легированных и труднообрабатываемых сплавов (удаление поверхностно-напряженных слоев металла после-механической обработки, повышение коррозионной стойкости и уменьшение шероховатости поверхности, уменьшение трудоемкости операции), полирование зубьев зубчатых колес (улучшение прирабатываемости, удаление дефектного поверхностного слоя, снижение трудоемкости операции), наружное и внутреннее полирование труб из легированных сталей и специальных сплавов (улучшение качества поверхности и снижение трудоемкости).
Процесс профилирования осуществляется за счет анодного растворения заготовки, помещенной внутрь полого цилиндрического катода. Растворение происходит интенсивнее на участках, более близких к катоду, результатом чего является изменение формы, в данном случае округление заготовки. Электролит — растворы кислот и солей.
Заострение и затачивание режущего инструмента осуществляют за счет создания на лезвии повышенной плотности тока, что обеспечивается соответствующим расположением лезвия инструмента относительно катода; характер заострения зависит также •от первоначального угла заточки. Электролитом являются растворы кислот.
Доводку электрохимическим методом при стационарном электролите используют для обработки поверхностей штампов, пресс-форм и литейных форм после электроэрозионной обработки. При затачивании и доводке можно получить точность до 0,1 мм при высоте микронеровностей обработанных поверхностей Ra = = 0,32ч-0,63 мкм.
Достоинства электрохимической обработки в стационар ном электролите: возможность получения поверхностей с малой высотой микронеровностей, отсутствие необходимости в специальном инструменте. Недостатки: невысокая удельная производительность, чувствительность к изменениям состава электролита и его состояния, проявляющаяся в нарушении стабильности процесса, влияние на процесс неоднородности строения заготовки.
2. АНОДНО-ГИДРАВЛИЧЕСКАЯ ОБРАБОТКА
При анодно-гидравлической обработке применяют токи высокой плотности. Локализация процесса обработки обеспечивается конструкцией инструмента и созданием малых межэлектродных зазоров. Образующиеся при электролизе продукты растворения удаляются из межэлектродного промежутка потоком электролита. На рис. 70 дана принципиальная схема электрохимической обработки в проточном электролите. Ток, проходя между катодом-инструментом 3 и анодом — заготовкой 1, вызывает растворение поверхности анода, в результате чего в нем воспроизводится про--филь катода-инструмента в виде углубления 4 негативной формы. В начале процесса отдельные участки катода 3 располагаются значительно ближе к заготовке-аноду /, и через них за счет меньшего сопротивления электролита 2 проходит ток большей величины. В результате находящиеся здесь участки заготовки подвергаются анодному разрушению быстрее.
Электрический ток проходит и на других участках, но за счет меньшей плотности тока на этих участках скорость их анодного растворения менее интенсивная.
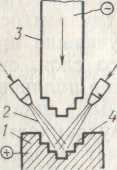
Рис. 70. Схема электрохимической обработки в проточном электролите — воспроизведение профиля катода на аноде
В конце обработки, когда анод приобретает отображенную форму катода, плотность тока выравнивается по всей поверхности. В реальных условиях процесс значительно усложняется, что приводит к неравномерному съему металла. Поэтому рабочая часть электрода-катода представляет собой, в свою очередь, несколько откорректированный профиль обрабатываемого элемента заготовки.
Состав электролитов зависит от химического состава обрабатываемого материала. Для применяемых при обработке большинства марок конструкционных сталей это водные растворы поваренной соли NaCl концентрации 10—20%. Для обработки заготовок из титана рекомендуется 25%-ный раствор серной кислоты. Для обработки деталей из алюминиевых сплавов иногда применяют растворы, содержащие 10% поваренной соли и 10 г/л лимонной кислоты. Применяются электролиты и других химических составов; данные о них приведены в справочной литературе.
Питание установок размерной электрохимической обработки обычно производится выпрямленным током однофазного или трехфазного полупроводникового выпрямителя.
К достоинствам электрохимической обработки в проточном электролите относятся: высокая производительность, достигающая десятков тысяч кубических миллиметров в минуту; отсутствие износа электрода-инструмента; возможность повышения производительности с сохранением или повышением точности обработки при необходимой шероховатости поверхности. Недостатки: высокая энергоемкость процесса; необходимость принятия специальных мер для удаления интенсивно выделяющихся осадков гидроокисей и газов; трудность управления процессом при обработке заготовок сложного профиля с высокой точностью; необходимость обеспечения интенсивной циркуляции электролита при обработке; некоторое снижение выхода по току при возрастании плотности тока.
Производительность процесса может характеризоваться интенсивностью анодного растворения металла или скоростью съема металла (мм3/мин) с обрабатываемой поверхности. Скорость съема металла с обрабатываемой поверхности можно рассчитать ю формуле
где К — электрохимический эквивалент, мм3/мин; U — напряжение на электродах, В; х Эф — эффективная электропроводность (промежутка), Ом-; б — межэлектродный зазор, мм; т] — выход по току, % (представляет собой отношение количества фактически растворившегося металла к теоретическому, рассчитанному из предположения, что на аноде происходит лишь одна реакция растворения металла).
На величину съема, как и на другие технологические показатели, кроме свойств электролита влияют многие факторы электрического и гидродинамического характера, изменяющиеся в широких пределах. Ниже приведены пределы изменения режимов обработки.
Напряжение на электродах, В | 8—24 |
Плотность тока, А/см2 | До 300 |
Скорость потока электролита, м/с | 1—30 |
Межэлектродный зазор, мм | 0,1—6 |
Давление в электролите в промежутке, МПа | До 5 |
Выбор скорости потока электролита определяется в значительной мере допустимым нагревом его в промежутке. Процесс протекает устойчиво, если перепад температур на входе и выходе электролита не превышает 8—10° С; при этом расход электролита должен составлять 200—300 л/мин на каждые 1000 А.
Скорость формообразования при анодно-гидравлической обработке зависит от анодной плотности тока. Предельная плотности тока в межэлектродном промежутке лимитируется минимальным зазором, допустимым по условиям удаления гидроокиси металла. нагрева электролита и возможностью электрического пробоя промежутка. При анодно-гидравлической прошивке и обработке поверхностей небольших площадей (до 50—100 см2) с равномерным припуском минимальный межэлектродный зазор может был снижен до 0,1—0,3 мм. Скорость обработки в этом случае достигает 0,5—2 мм/мин. При обработке поверхностей (0,5—2 м2) с большой неравномерностью припуска обработку ведут при больших зазорах (1-—10 мм). Скорость съема металла в этом случае составляет 0,02—0,2 мм/мин.
Производительность, оцениваемая интенсивностью растворения металла, зависит от количества электричества, реализованного в межэлектродном промежутке. Выпускаемые источники тока позволяют довести интенсивность съема металла до 100—250 Н/ч.
Точность обработки и качество поверхности. При анодно-гидравлической обработке погрешности зависят от неточности изготовления станков, инструментов и приспособлений и других факторов, общих для механической и электрохимической технологии. Однако не эти факторы определяют относительно низкий уровень точности электрохимического формообразования. Основной причиной возникновения погрешностей при анодно-гидравлической обработке является изменение электродного зазора под воздействием специфичных для процесса колебаний электрохимического и гидродинамического характера. В начальный момент обработки межэлектродный зазор в различных сечениях определяется начальной неравномерностью поверхности заготовки (рис. 71), поэтому процесс анодного растворения заготовки происходит с различной скоростью. Там, где зазор меньше, а плотность тока выше, съем идет интенсивнее. Межэлектродный зазор постепенно выравнивается, неровности на обрабатываемой поверхности уменьшаются, достигая к концу обработки какой-то величины А„. Чем скорее идет выравнивание, тем быстрее стабилизируются электрохимические и гидродинамические условия процесса, тем меньше будут погрешности, переносимые с за'готовки на готовую деталь. Выравнивающие свойства процесса можно оценить показателем
Zmin — Дн
где /Св — коэффициент выравнивания; Zmin — минимальный при-1пуск (по впадине), мм; Дн — высота начальных неровностей, мм; Лк — высота конечных неровностей, мм.
При однородном составе электролита и отсутствии концентрационных изменений в межэлектродном промежутке процесс выравнивания профиля сопровождается удалением металла, в десятки раз превосходящего реально необходимый припуск. Коэффициент выравнивания изменяется от 0,1 до 0,9 и зависит от [состава электролита, материала заготовки, межэлектродного [зазора, температуры электролита ,и других факторов. Состав 1 электролита и материал заготовки в большей мере, чем другие |факторы, влияют на коэффициент выравнивания Кв-
По мере усиления пассивирующих явлений процесс выравнивания ускоряется. При применении электролитов, способных защищать впадины от растворения, коэффициент выравнивания Повышается. Например, при обработке в растворах хлорноводокислого натрия процесс съема протекает в основном по выступам при высоком темпе выравнивания. С уменьшением межэлектродного зазора выравнивание также ускоряется. Точность обработки I достигает 0,05—0,15 мм при прошивке отверстий и 0,2—0,5 мм При обработке полостей сложной формы.
Шероховатость поверхности, обработанной анодно-гидравлическим способом, зависит от состава электролита, плотности тока, формы кривой тока и напряжения, скорости потока электролита и его температуры. Состав электролита, его соответствие конкретному материалу заготовки является важнейшим фактором, влияющим на шероховатость поверхности. Наиболее распространенный электролит —раствор хлористого натрия — дает возможность (при соответствующих параметрах процесса) получить обработанную поверхность с высотой микронеровностей до Ra— = 0,32-4-0,64 мкм. С повышением температуры электролита шероховатость обработанной поверхности увеличивается. С повышением плотности тока шероховатость поверхности уменьшается. Это особенно заметно при изменении плотности тока от 2 до 8 А/см2.
Увеличение плотности тока св. 15 А/см2 заметного снижения' шероховатости не дает.
Регулирование процесса анодно-гидравлической обработки,.
Устойчивость электрохимического процесса при необходимых, производительности и качестве обработки обеспечивается системой регулирования.
Направленное анодное растворение без существенного искрообразования обеспечивается при межэлектродных зазорах определенной величины, зависящих от конкретных условий обработки. В связи с этим все существующие системы регулирования электрохимических станков построены на принципе поддержания оптимального зазора между электродами. При работе с малыми зазорами особенно важно согласовать между собой скорость Ущ> движения инструмента-катода и линейную скорость Q/ растворения: обрабатываемого металла. Это важно для обеспечения необходимой производительности процесса и исключения возможности! короткого замыкания.
В реальных условиях величина Q/ не остается постоянной,, и поэтому регулирование подачи катода должно производиться? в соответствии с ее изменением. Поэтому линейную скорость растворения можно назвать прямым параметром регулирования. Однако определить значение Qv' с точностью, достаточной для»' практического использования, не представляется возможным в силу большой -сложности процессов, протекающих при размерной электрохимической обработке. Соотношение между v, и Q/" наиболее целесообразно было бы определять по изменению межэлектродного зазора непосредственно. Но и это невыполнимо,, j поскольку в процессе работы зазор невозможно измерить.
В этих условиях контроль межэлектродного зазора осуществляют при помощи так называемых косвенных параметров регулирования, функционально зависимых от величины зазора. К числу таких параметров можно отнести напряжение на электродах, силу i и плотность тока, давление жидкости в зазоре.
При использовании плоских катодов площадь обрабатываемой поверхности не изменяется в течение всего процесса. В этом слу-1 чае омическое сопротивление столба электролита между электродами определяют по формуле
где рэ — удельное сопротивление электролита; б— величин* зазора между электродами (величина столба электролита); So — площадь обрабатываемой поверхности.
Если в течение процесса обработки площадь обрабатываемо! поверхности постоянна, то в соответствии с законом Ома можно с достаточной для практического использования точностью судит! об изменении зазора б по значениям силы тока и напряжения
Однако явление поляризации электродов (и изменение удельного сопротивления столба электролита в межэлектродном зазоре) исключает достаточно достоверное определение зазора.
Межэлектродный зазор, через который прокачивают электролит, можно представить как дроссель. Расход жидкости через дроссель
Q = САр",
где С —коэффициент, определяемый величиной открытия щели дросселя и состоянием рабочей жидкости; Ар — перепад давлений на дросселе (в данном случае — на межэлектродном зазоре); и — показатель степени, зависящий от конструктивных параметров дросселя.
Расход жидкости в процессе обработки определяется подачей насоса, которую можно считать постоянной. Величины С и а зависят только от размеров зазора. Таким образом, при установленном 1азоре фиксируется вполне определенное значение Ар, которое и ходе электрохимического процесса может служить эталоном регулирования. По мере врезания катода в обрабатываемую заготовку площадь обработки So и путь протекания электролита увеличиваются. Это приводит к изменению Ар и ухудшению процесса регулирования по перепаду давления на межэлектродном зазоре.
Наиболее универсальным можно считать регулирование промесса по анодной плотности тока. Из формулы, определяющей омическое сопротивление столба электролита в межэлектродном !.1зоре, следует, что с увеличением площади обработки при сохранении параметра регулирования постоянным зазор должен уменьшаться (p8 = Rr,So). Это способствует повышению точности обработки к концу процесса. Во избежание чрезмерного уменьшения зазора в конце обработки начальный зазор должен быть определен из условия
Величину бк конечного зазора следует выбирать таким образом, чтобы исключить возможность искрообразования. Напряжение в начале процесса может быть принято равным ЭДС источника питания; напряжение в конце обработки в каждом отдельном случае определяется опытным путем. Предотвращение короткого замыкания обеспечивается снятием питающего напряжения, так как осуществить достаточно быстрое разведение электродов невозможно. Снятие напряжения осуществляется по сигналу схемы предупреждения коротких замыканий о наличии или приближении такого опасного режима (за 0,02—0,05 с до короткого замыкания, что достаточно для срабатывания автоматики защиты).
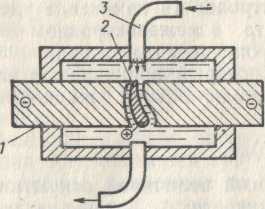
Рис. 73. Схема прошивания отверстия анодно-гидравлическим способом
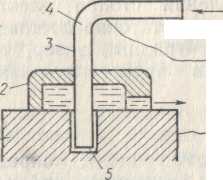
Рис. 72. Схема анодно-гидравлической обработки турбинной лопатки
Электрохимическое формообразование. Высокая эффективность электрохимического формообразования достигается при обработки многих заготовок сложной формы. Одним из распространенных видов этой обработки является обработка рабочего профиля турбинных лопаток (рис. 72). Заготовку 2 помещают между двумя латунными копирами — электродами 1 — соответствующей формы на расстоянии 0,3—0,5 мм от них. Через образовавшийся зазор под давлением около 1 МПа прокачивают 10%-ный раствор поваренной соли, подаваемый через штуцер 3. Режим формообразования: напряжение на электродах 8—11 В, плотность ток* 15—20 А/см2, скорость подачи 0,3—0,4 мм/мин. Металл с заготовки удаляется со скоростью подачи при шероховатости обработанной поверхности a=l,25-f-2,5 мкм.
Исходя из особенностей электрохимического формообразования, полагают, что максимальный припуск, удаляемый с обрабатываемой поверхности, должен быть не более двойного минимального припуска. Так, если в среднем с любой точки снимают п| 0,8 мм, то минимальный съем в любой части заготовки должен быть не менее 0,4 мм.
В процессе электрохимического формообразования одновременно выявляются дефекты обрабатываемой поверхности, в частности, микротрещины. Таким образом, при обработке осуществляется не только формообразование, но и контроль качества, что особенно важно для ответственных деталей, например, турбинных лопаток.
Практика показывает, что электрохимические методы формообразования в 4—10 раз производительнее механической обработки. Электрохимический метод обработки особенно эффективна при обработке заготовок из труднообрабатываемых стали и сплавов.
Электрохимическое прошивание отверстий. Прошивание отверстий анодно-гидравлическим методом выполняют полым электрш дом (рис. 73). Инструментом служит металлическая трубка ■ покрытая снаружи тонким изоляционным слоем 3. В трубы под
давлением подают электролит. Трубка включена в электросеть и качестве катода, а обрабатываемая заготовка 1 — в качестве анода. Интенсивное анодное растворение металла с поверхности метали под торцом трубки приводит к образованию полости 5, |лубина которой может быть задана произвольно поступательным перемещением трубки с электролитом. Диаметр трубки 4 выбирается обычно меньше, чем диаметр отверстия 5, примерно на 025—0,05, а иногда и на 0,1 мм на сторону. Электролит, выходящий из трубки .возвращается по зазору между стенками отверстия и трубки и через местную ванну 2 откачивается в систему циркуляции.
Электролитом служит раствор солей, в частности, хлористого натрия. Плотность тока в зависимости от интенсивности прокачки электролита, состава обрабатываемого материала и других факторов находится в пределах 100—300 А/см2 при напряжении1-12 В. Иногда плотность тока доводят до 600 А/см2. Скорость углубления обычно находится в диапазоне 1—6 мм/мин. Отверстие может быть любой конфигурации, определяемой профилем сечения инструмента.
В потоке электролита производят операции обработки шлицев, Мальцевых каналов и полостей в трубах, утонения сферических поверхностей, и т. д.
Особенности электрохимического формообразования глубоких точных отверстий. Детали с глубокими и точными отверстиями широко применяют в промышленности. Технологические приемы механической обработки таких отверстий, как правило, сложны, сопровождаются большими затратами ручного труда и часто дают низкое качество обработанных поверхностей. Здесь, особенно на отделочных операциях, электрохимический метод обработки весьма эффективен.
Размерную электрохимическую обработку глубоких отверстий выполняют с неподвижным или подвижным катодом. Применение неподвижных катодов без осевой подачи имеет следующие недостатки: трудность точного центрирования длинного катода; необходимость применения фасонного катода для обработки комбинированных ступенчатых отверстий; копирование дефектов поверхности катода обрабатываемой поверхностью.
Для повышения качества обработки катоду-инструменту (или заготовке) придают вращение. При значительном различии параметров заготовки и инструмента применяют схему с эксцентричным расположением неподвижного инструмента при вращении заготовки с частотой 5—20 об/мин. Неподвижные катоды рекомендуется применять при вращении заготовки и в случае обеспечения необходимой жесткости (1/dlQ, где / — длина катода, d — диаметр обрабатываемого отверстия).
Применение подвижных катодов уменьшает или исключает недостатки неподвижных катодов. К достоинствам этого вида обработки относятся: возможность использования катодов простой формы, например, гладких или ступенчатых с цилиндрическими участками; обеспечение необходимого центрирования, что осуществляется применением изолирующих направляющих втулкой и пластин; практического исключения копирования дефектом поверхности инструмента обрабатываемой поверхностью.
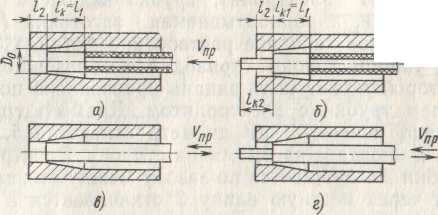