«Библиотека станочника»
Вид материала | Книга |
- Библиотека Хельсинского Университета была написана небольшая статья, 63.53kb.
- Инструкция по охране труда при выполнении, 437.7kb.
- Городских библиотек, 1814.45kb.
- «Металлообрабатывающие станки и комплексы», 14.41kb.
- Библиотека Альдебаран, 2189.93kb.
- Нейшем "Автор" с одной стороны, и Научная медицинская библиотека Ярославской государственной, 39.73kb.
- Библиотека православной культуры, 94.2kb.
- РосБизнесКонсалтинг Список онлайн-библиотек экономической тематики, 63.04kb.
- 1. Александрова Т. Домовенок Кузька…(с продолжениями), 69.48kb.
- Министерства Российской Федерации по делам печати и телерадиовещания Диссертации Библиотека, 617.88kb.
при обработке с продольными подачами Qsпр = 0,046 I1,68;
при обработке с поперечными подачами Qsпоп = 0,077I1,51; где Qs —максимальная производительность, мм³/мин; I —сила рабочего тока , А.
Производительности при продольной Snp и поперечной Sпоп подачах различны вследствие различных условий эвакуации продуктов электроэрозии из зоны обработки. Максимальная для данного электрического режима производительность достигается при глубинах h1 и h2 (рис. 28), равных 2—5 мм. При увеличении глубины наработки производительность уменьшается. При достаточной глубине обработки минимальная производительность Qs min, где К — коэффициент. Для продольных подач К= 0,4-0,45; для поперечных подач К=0,5-0,8. В табл. 13 приведена производительность электроконтактной обработки заготовок хромоникелевого чугуна при различных скоростях вращения и направлениях подачи.
Таблица 13
Производительность электроконтактной обработки заготовок из хромоникелевого чугуна
Рабочий ток,А | подача | Глубина обработки,мм | Производительность, см³/мин, при окружной скорости детали, м/с | ||
0,02 | 0,1 | 0,2 | |||
100 | Поперечная продольная | 10 15 | 0,64 0,52 | 0,62 0,52 | 0,61 0,51 |
300 | Поперечная продольная | 10 25 | 5,6 3,48 | 5,11 3,05 | 4,43 2,44 |
500 | Поперечная продольная | 11 25 | 14,15 7,38 | 12,11 6,10 | 9,96 5,44 |
Качество обработанной поверхности при электроконтактной обработки зависит от режима обработки и теплофизических констант материала заготовки. Величина рабочего тока — основной фактор, регулированием которого достигается получение поверхности с заданным качеством. Принимая напряжение на межэлектродном промежутке постоянным и равным 26 В, можно выразить зависимость высоты микронеровностей от рабочего тока эмпирическими формулами
Ra = 5,56 I0,61 или Ra = 0.57 I0,61,
Где Р-мощность, кВт.
Термическое воздействие разрядов вызывает структурные изменения поверхностных слоев металла. Толщина слоя с измененной структурой также определяется режимом обработки и теплофизическими константами материала заготовки. При обработке деталей из корозийно-стойких и жаропрочных сталей и сплавов глубина тою слоя 0,1—0,3 мм; при обработке деталей из углеродистых сталей 0,3—0,5 мм, из титана 0,5 мм, из отбеленного чугуна 0,2-0,9 мм.
Электроконтактную обработку применяют главным образом на заготовительных операциях и на операциях черновой обработки заготовок с большими припусками.
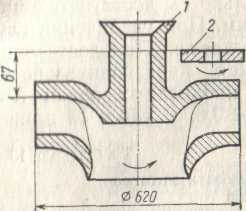
Рис. 29. Схема отрезки ступицы колеса:
1 — заготовка; 2 — инструмент
На рис. 29 показана схема отрезки ступицы колеса электроконтактным способом. Электроконтактное разрезание заготовок отличается высокой производительностью ( 2000 мм3/мин). Отрезку производят либо вращающимся диском, либо бесконечной лентой с линейной скоростью движения инструмента 40—60 м/с (плотность тока до 200 А/см2). Электроконтактная обдирка характеризуется большими рабочими токами 2000—3000 А) и высокой производительностью (до 3000000 мм3/мин )
Упрочнение поверхностного слоя металлов. Одним из преимуществ электроискрового метода обработки материалов является то, что при определенных условиях резко повышаются прочностные свойства поверхности заготовки: твердость, износостойкость, жаростойкость и эрозионная стойкость. Эту особенность используют для повышения износостойкости режущего инструмента, штампов, пресс-форм и деталей машин, упрочняя металлические поверхности электроискровым способом.
При электроискровом упрочнении применяют обратную полярность (заготовка является катодом, инструмент —анодом) обработку производят обычно в воздушной среде и, как правило, вибрацией электрода. Аппаратура, с помощью которой осуществляется процесс упрочнения, малогабаритна и очень проста в эксплуатации. Основные преимущества электроискрового способа нанесения покрытий заключаются в следующем: покрытия имеют большую прочность сцепления с материалом основы; покрываемой поверхности не требуют предварительной подготовки; возможно нанесение не только металлов и их сплавов, но и их композиций; на ограниченных участках обрабатываемой поверхности возможно проводить сложнейшие микрометаллургические процессы.
Процессы, происходящие при электроискровом упрочнении, сложны и являются предметом тщательных исследований. Сущность упрочнения состоит в том, что при электроискровом разряде в воздушной среде происходит полярный перенос материала электрода на заготовку. Перенесенный материал электрода легирует металл заготовки и, химически соединяясь с диссоциированным атомарным азотом воздуха, углеродом и материалом заготовки образует диффузионный износоустойчивый упрочненный слой. В этом в слое возникают сложные химические соединения, высоки стойкие нитриды и карбонитриды, а также закалочные структуры. По мнению специалистов, при электроискровом упрочнении в поверхностном слое, например, стали происходят процессы, приведенные в табл. 14.
Таблица 14
Процессы, происходящие в поверхностном слое заготовки при электроупрочнении.
Упрочняемый материал | процесс | |
наименование | особенности | |
Углеродистая сталь, содержащая углерод, в количестве свыше 0,6%,а также легирующие элементы в большом количестве | Сверхскоростная закалка | Кратковременный нагрев до высокой температуры и мгновенное охлаждение нагретых и расплавленных участков массой холодного металла |
Инструментальная сталь | азотирование | Диссоциация атмосферного азота в разряде с образованием атомарного азота. Соединение азота с элементами поверхностного слоя и образование нитридов металлов (титана, хрома, железа и др.). |
Малоуглеродистая и легированная сталь | Цементация | Растворение в расплавленном и высоконагретом металле углерода, электрода или окружающей среды с образованием карбидов железа, хрома, титана и др |
сталь | Обогащение легирующими элементами | Контактный перенос материала электрода на заготовку при соприкосновении их под давлением в расплавленном состоянии и газовая диффузия. Последующая диффузия в поверхностном слое |
При электроискровом упрочнении микротвердость белого слоя в углеродистых сталях может быть доведена до 230 МПа, высота микронеровностей обработанной поверхности до Ra = 2,5 мкм. Толщина слоя покрытия, получаемого на некоторых установках,0,003—0,2 мм. При упрочнении поверхностей деталей машин высокой мощности упрочнения (например, на установлении ИЕ-2М) можно получить глубину слоя упрочнения до 0,5-1,6мм с микротвердостью 50—60 МПа (при упрочнении феррохромом)
Различают чистую обработку, которая соответствует высоким напряжениям и небольшим значениям токов короткого замыкания (до 20 А), и грубую (глубокое легирование) при низких напряжениях (50—60 В) и токах короткого замыкания свыше 20 А.
4. ОБОРУДОВАНИЕ, СТАНКИ И ИНСТРУМЕНТ ДЛЯ ЭЛЕКТРОЭРОЗИОННОИ ОБРАБОТКИ
Генераторы импульсов. Формирование импульсов тока, подводимых к электродам эрозионного станка, производится с помощи генератора импульсов, питаемого от сети промышленного тока. Генераторы импульсов можно разделить на два класса: зависимы и независимые. К первым относятся такие генераторы, в которых создание импульсов напряжения и тока осуществляется при участии межэлектродного промежутка. Во вторых электрические пульсы создаются без участия межэлектродного промежутка. Они формируются в генераторе и подводятся к межэлектродному промежутку для обеспечения эффекта эрозии. Зависимые генераторы используют при электроискровом методе обработки, независимые генераторы применяются при электроимпульсном методе. В современных электроэрозионных станках используют много различных генераторов импульсов. Ниже рассмотрены некоторые из них.
Генератор типа RC. Сокращенное название схемы генератора происходит от обозначения основных ее элементов: резистор R и емкости — С. Генератор получил широкое распространение вследствие простоты и надежности (релаксационными называются генераторы, энергия которых накапливается в реактивных элементах цепи — конденсаторе или индуктивной катушке). Накопительный конденсатор 2 (рис. 30) заряжается от источника постоянна тока напряжением 100—200 В через токоограничительный резистор 1. Межэлектродный промежуток 3 включен параллельно конденсатору. По мере заряда конденсатора напряжение на его обкладках и между электродами эрозионного промежутка увеличивается. При достижении пробивного напряжения Uпр происходит пробой межэлектродного промежутка, и запасенная в накопительном конденсаторе энергия выделяется в виде короткого импульса большой мощности, вызывая эрозию электродов.
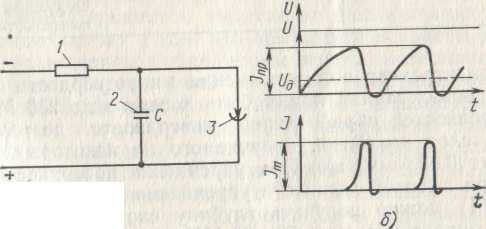
Рис. 30. Генератор типа RC:
а-схема; б — график изменения напряжения на электродах и силы тока в межэлектродном
промежутке.
При разряде конденсатора напряжение на межэлектродном промежутке уменьшается довеличины, при которой разряд между электродами не может поддерживаться. Сопротивление межэлектродного промежутка резко увеличивается, ток быстро уменьшается и прекращается совсем. Электродный промежуток восстанавливает свои диэлектрические свойства; начинается зарядка накопительного конденсатора.процесс повторяется с частотой, зависящей от параметров расстояния между электродами и качества жидкого диэлектрика. Изменяя величину токоограничивающего резистора, можно менять частоту следования импульсов и энергию, передаваемую в межэлектродный промежуток. Частоту импульсов можно определить по следующей формуле:
При некотором критическом сопротивлении резистора паузы между отдельными импульсами исчезают, и заряд из искрового переходит в дуговой. Размерная обработка в этом случае невозможна. Между напряжением источника питания, напряжением пробоя и напряжением горения дуги должно соблюдаться соотношение.
Достатком генератора типа RC следует отнести низкий КПД (около 35%), наличие больших пауз между импульсами (скважность10 —100), значительное влияние состояния среды межэлектродного промежутка на характеристику электрических импульсов.
Генератор типа RLC. Схема генератора RLC представляет собой дальнейшее развитие схемы RC. Для повышения эффективности действия генератора в цепь заряда конденсатора включена индуктивность L (рис. 31, а). Введение индуктивности изменяет форму напряжения зарядки конденсатора (рис. 31, б). В начале процесса зарядки напряжение растет медленнее, чем в схеме без индуктивности, что благоприятно сказывается на процесс восстановления диэлектрической прочности межэлектродного промежутка. Поэтому удается повысить частоту разрядов, не опасаясь перехода импульсного процесса в дуговой. Далее напряжение зарядки растает, и процесс зарядки при наличии индуктивности в заканчивается быстрее, чем без нее. К этому времени электрическая прочность межэлектродного промежутка полностью восстанавливается. Благодаря наличию индуктивности конденсатор оказывается заряженным до напряжения, значительно превышающего напряжение источника питания (эффект последовательном включения в цепь индуктивности и емкости).
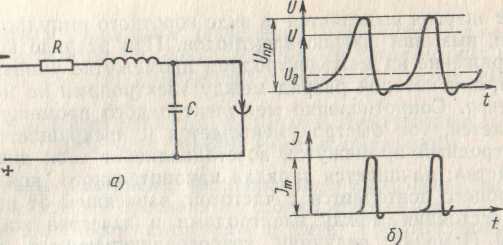
Рис. 31. Генератор типа RLC:
а — схема; б — график изменения напряжения на электродах и силы тока в межэлектродном промежутке
Величину индуктивности, вводимой в цепь заряда, выбирают по формуле L = 0,25R²C Включение индуктивности в цепь зарядного контура генератор импульсов повышает КПД и интенсивность съема металла и 20—40% по сравнению с генераторами типа RC.
Генератор типа LC. В практике электроэрозионной обработки используют также LC-генератор, в зарядном контуре которого отсутствует резистор. Потери энергии в зарядной цепи такого генератора существенно меньше. Подобный генератор без дополнительных устройств, стабилизирующих процесс зарядки-разрядки разрывающих дугу, оказывается неработоспособным. Наиболее просто стабилизация процесса может быть достигнута с помощью электромагнитного вибратора, обмотку которого используют в качестве индуктивности зарядного контура. Такое устройство заставляет электрод автоматически совершать колебательные движения, управляя процессом.
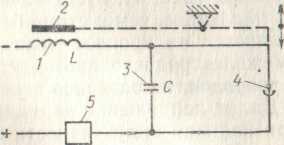
Рис. 32. Генератор типа LC
При включении схемы от источника питания через обмотку 1 вибратора (рис. 32) потечет зарядный MI конденсатора 3. Постепенно возрастая, ток притянет якорь электромагнитного вибратора и поднимет электрод, что увеличит межэлектродный промежуток 4. Через некоторое время зарядим ток конденсатора (и ток через обмотку электромагнитного вибратора), а также сила притяжения якоря уменьшаться и электроды начнут сближаться. К этому времени напряжение на конденсаторе возрастет до величины, почти в 2 раза превышающей напряжение источника питания, и, когда промежуток между электродами 1 станет достаточно мал, произойдет разряд конденсатора через этот промежуток. Затем цикл работы повторится, и процесс будет идти с частотой, определяемой в основном величинами L и С.
Генераторы, выполненные по описанной схеме, работают достаточно устойчиво. Однако при значительной глубине обработки случайное короткое замыкание может вызвать появление дуги, которая будет разорвана автоматическим регулятором станка лишь после полного извлечения электрода из обрабатываемого отверствия за это время заготовка может быть испорчена. Во избежание такого явления обычно применяют быстродействующий выключатель 5, который при коротком замыкании отключает на небольшой период времени генератор от источника питания, ликвидируя короткое замыкание.
Машинные генераторы импульсов. Рассмотренные выше генераторы вырабатывают импульсы относительно малой длительности. Применение импульсов значительной длительности позволяет существенно увеличить производительность обработки на единицу мощности и уменьшить износ электродов-инструментов. Импульсы параметров могут создавать специальные электрические имя — машинные генераторы импульсов. Как правило, эти генераторы вырабатывают импульсы с частотой повторения 400-2000 имп/с длительностью от долей миллисекунды до миллисекунды. По принципу работы машинные генераторы можно разделить на коммутаторные (коллекторные) и индукторные (бесколлекторные). В коммутаторных электрических генераторах выпрямление знакопеременного импульсного напряжения осуществляется с помощью механического коммутатора, встроенного в машину. Краткие технические характеристики некоторых коммутаторных генераторов импульсов приведены в табл. 15.
Таблица 15
Техническая характеристика коммутаторных генераторов импульсов
Параметры | МГИ-2М | МГИ-3М | МГИ-4 |
Частота импульсов, Гц Средняя сила тока, А Среднее напряжение холостого хода, В Мощность приводного электродвигателя, кВт Скважность на холостом ходу | 400 100 25 7 2,8 | 400 360 25 28 3,2 | 400 600 30 40 2,8 |
Бесколлекторные импульсные генераторы, например типа МИГ, создают переменное напряжение, состоящее из полуволн обеих полярностей (рис. 33). Благодаря специальному выполнению их электромагнитной системы достигается получение несимметричной напряжения с различными амплитудами полуволн положительной и отрицательной полярности. При достаточно малой величине амплитуды обратной полуволны напряжения пробой межэлектродного промежутка вызывается только импульсами напряжения основной полярности.
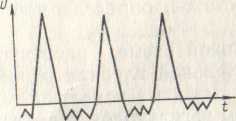
Рис. 33. График напряжения индукторного машинного генератора импульсов типа МИГ
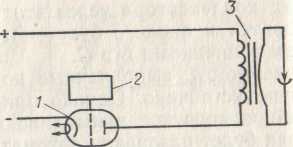
Рис. 34. Схема лампового генератора импульсов
Генераторы импульсов на электронных и полупроводниковых усилителях. Ламповые генераторы импульсов позволяют создавать импульсы в широком интервале их энергий и длительности, а также с высокой частотой повторения. В качестве накопителя энергии может быть использован конденсатор (рис. 34) или индуктивность выходного импульсного трансформатора. Генератор в этом случае состоит из источника постоянного тока высокого напряжении, электронной лампы 1, высокочастотного маломощного генератора 2, управляющего электронной лампой, выходного импульсного трансформатора 3. Через первичную обмотку импульсного трансформатора 3 пропускают импульсы электрического тока требуемой силы и частоты повторения, с вторичной обмотки снимают импульсы с параметрами, необходимыми для обеспечения электроэрозионной обработки. Используя импульсные генераторные лампы, можно создавать генераторы мощностью в несколько десятков киловатт, вырабатывающие импульсы мгновенной мощности до нескольких меговатт при частоте 100—150 кГц.
В промышленности широко применяют широкодиапазонные транзисторные генераторы импульсов (типа ШГИ), упрощенная схема которых показана на рис. 35. Напряжение источника Uc=60-70B подают к транзисторным ключам Т1, Т2 и т. д.от транзисторных ключей, управляемых задающим генератором 3Г, ток к межэлектродному промежутку подается через резисторы R и диод Д. К межэлектродному промежутку подается высокое напряжение (100—300 В) от маломощного блока поджигающих импульсов Uп. В качестве ключа К в цепи поджигания могут быть также использованы транзисторы. После пробоя межэлектродного промежутка поджигающими импульсами через промежуток идет ток от транзисторов силового блока. Длительность этих импульсом определяется временем пребывания транзисторов в открытом состоянии. Цепь поджигания при этом разорвана ключом К. Такси генератор позволяет получать импульсы гребенчатой формы (рис36). Каждый импульс состоит из следующих друг за другом коротких импульсов со сравнительно большим напряжением и серией импульсов с меньшим напряжением.
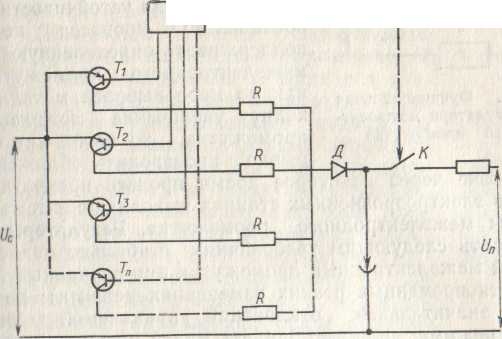
Рис. 35. Схема транзисторного генератора импульсов
Импульсы гребенчатой позволяют повысить производительность электроэрозионной обработки и снизить износ электрода-инструмента. В табл. 16 приведены характеристики
Широкодиапазонных транзисторных генераторов импульсов.
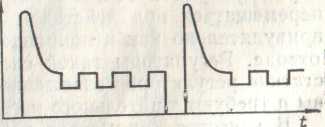
Рис. 36. Импульсы гребенчатой формы
Таблица 16
Характеристики генераторов импульсов типа ШГИ
Тип генератора импульсов | Сила тока, А, не более | Диапазон частот, кГц | Произво-дительность, мм³/мин не более | Шероховатость поверхности, мкм | Износ инструмента на чистовых режимах, % | Потреб-ляемая мощность, кВт, не более |
ШГИ-40-440 ШГИ-63-440 ШГИ-125-100 ШГИ-16-880 ШГИ-63-44/2 ШГИ-63-44/3 ШГИ-21-440/3 ТГ-250-0,15 ТГ-100-3/3 ГКИ-250 | 40 63 125 16 62*2 63*3 21*3 300 300 250 | 8-440 1-440 0,4-100 3-880 1-41 1-41 1-440 0,15 0,1-3 8-22 | 300 500 1500 75 1200 1900 450 4000 3500 35 | 0,5 0,5 1,2 0,2-0,4 3-4 3-4 0,4-1,0 - - 3-4 | 0,5-1,5 0,5-1,5 0,5-1,0 - 0,5-1,0 0,5-1,0 0,5-1,0 - - - | 4 6 7,5 - 12 18 6 18 17 - |
Автоматические регуляторы межэлектродного промежутка.
Для сохранения устойчивости электроэрозионного процесса необходимо поддерживать определенную величину межэлектродного промежутка. Так как по мере выброса металла происходит увеличение межэлектродного промежутка, то необходимо непрерывно производить сближение электродов, иначе через некоторое время процесс прекратится.
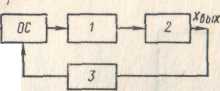
Рис. 37. Функциональная схема регулятора межэлектродного промежутка
Эту функцию в электроэрозионных станках выполняют автоматические регуляторы межэлектродного промежутка. Регуляторы должны удовлетворять следующим требованиям: стабильно поддерживать выбранный межэлектродный промежуток при случайных возмущениях (кратковременных резких изменениях режима); не должны допускать значительных отклонений управляемой величины от заданного режима; должны обладать малой инерционностью, быть малогабаритными, экономичными, простыми и надежными в работе.
Функциональная схема регулятора построена по принципу автоматических систем с обратной связью по выходному сигналу (рис. 37). С датчика 3 выходной величины сигнал подается в орган сравнения ОС. Разность выходного Хвых и заданного Хзад сигналом усиливается схемой 1 и поступает на исполнительный орган 2. Эту разность привод подачи электрода-инструмента отрабатывает так, чтобы она обратилась в нуль. При этом электрод-инструмент перемещается, а заданная величина межэлектродного промежутка поддерживается в пределах, определяемых погрешностью системы. Автоматические регуляторы межэлектродного промежутка по принципу действия можно разделить на «взвешенные» и «жесткие». Автоматические регуляторы взвешенной системы характеризуются наличием устройства, автоматически поддерживающего и равновесном состоянии электрод-инструмент, который под влиянием собственного веса стремится опуститься вниз до соприкосновения с обрабатываемой заготовкой. Необходимым условием нормальной работы таких систем является уменьшение силы тяги регулятора при увеличении межэлектродного промежутка. Тогда под влиянием собственного веса подвижная система будет опускаться вниз до восстановления прежней величины промежутка между электродами. Автоматические регуляторы жесткой системы характеризуются тем, что подвижная система не может свободно перемещаться под действием собственного веса, а передвигается принудительно как в направлении подачи, так и в направлении отвода. Регуляторы такой системы свободны от некоторых недостатков регуляторов взвешенной системы. Однако они более сложны и требуют тщательного изготовления.
В качестве параметров регулирования в большинстве случаен используют напряжение или ток, а иногда напряжение и ток одновременно. Наиболее распространенным регулятором взвешенной системы является. регулятор соленоидного типа ( рис.38).
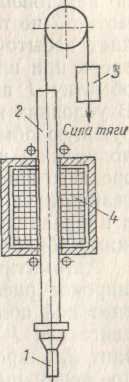
Рис. 38. Регулятор соленоидного типа
Подвижная система, включающая электрод-инструмент 1, шпиндель 2 и противовес 3, влиянием веса инструмента и шпинделя способна опускаться вниз по направляющим. Сила соленоида 4 уравновешивает подвижную систему и при установившемся режиме обработки удерживает ее во взвешенном состоянии, поддерживая заданный промежуток между электродами, тяги соленоида зависит от величины тока, протекающего по его обмотке, поэтому для каждого режима обработки и веса электрода-инструмента можно подобрать такие соотношения между протекающим через соленоид, и током через межэлектродный промежуток, чтобы подвижная система находилась в равновесии. При всяком изменении тока или напряжения сила тока соленоида будет изменяться, что вызовет перемещение подвижной системы в нужном направлении до востановления устойчивой работы станка.
Схема включения регулятора, предназначена для регулирования по параметру среднего тока, протекающего через межэлектродный промежуток, показана на рис. 39. Обмотка, соленоида включена последовательно в зарядный контур рабочего конденсатора С. Подбирая в зависимости от силы рабочего тока определенное число витков в регулирующей обмотке / и изменяя резистором в обмотке 2, можно добиться устойчивого регулирования в сильном диапазоне режимов обработки. После выключения подвижная система вместе с электродом-инструментом опускается под действием собственного веса вниз, поэтому в конструкции соленоидного регулятора необходимо вводить устройство, автоматически тормозящее подвижную систему при выключении станка. Более гибкой является схема регулятора, показанная на рис. 40. В качестве параметра регулирования принято среднее напряжение на межэлектродном промежутке, незначительно изменяющееся.
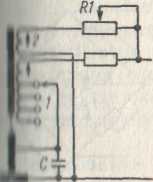
Рис. 39. Схема включения автоматического регулятора, параметром регулирования которого является среднее значение тока, протекающего через межэлектродный промежуток
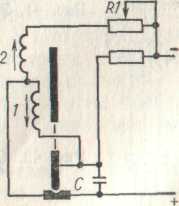
Рис. 40. Схема включения автоматического регулятора, параметром регулирования которого является среднее напряжение на межэлектродном промежутке
Обмотка 2 не только компенсирует вес подвижной системы, но и создает избыточную силу тяги, поднимающую электрод-инструмент вверх при включении генератора импульсов. Через регулирующую обмотку 1 пропускается ток, ослабляющий силу тяги соленоида. В условиях нормального режима работы станка ток через регулирующую обмотку таков, что результирующая сила равна весу подвижной части. Всякое изменение режима вызовет изменение среднего напряжения на электродах, а следовательно, и изменение результирующей силы соленоида и перемещение подвижной части в направлении, необходимом для восстановления нормального режима обработки,
Автоматическим регулятором с жесткой связью, получившие широкое распространение, является электродвигатель-регулятор винтовой подачей (рис. 41). Он состоит из реверсивного электродвигателя 1 постоянного тока, приводящего во вращение ходовой винт 2, закрепленный в подшипниках, исключающих его продольное перемещение. Винт 2, вращаясь в гайке 3, закрепленной в подвижной системе 4 станка, сообщает последней движение подачи или отвода в зависимости от направления вращения электродвигателя. Схема включения электродвигателя показана на рис. 42. При одинаковых напряжениях на R1 и R2 напряжение на якоре электродвигателя равно нулю. Электродвигатель не работает, это соответствует заданному межэлектродному зазору. При увеличении или уменьшении рабочего тока от заданного напряжения в резисторе R3 соответственно изменяется. Это приводит к вращению якоря электродвигателя (ОВ— обмотка возбуждения).
На рис. 43 приведена схема регулятора с гидравлической дачей. Гидравлический привод подачи электрода-инструмента состоит из гидрораспределителя 5 с электроуправлением, рабочего гидроцилиндра 2, шток которого выполняет роль шпинделя станка гидрораспределителя 3 и установки питания с насосом 1. Paспределитель 12 предназначен для разгрузки насоса в нерабочем стоянии. Масло в процессе работы поступает в гидрораспределитель 5 и далее в зависимости от положения его плунжера в соответствующую полость гидроцилиндра, осуществляющего вращение электрода-инструмента.
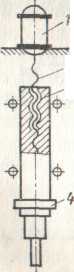
Рис. 41. Электродвигатель-регулятор с винтовой подачей
Рис. 42. Схема включения якоря электродвигателя подачи

Рис . 43 . Схема регулятора с гидравлической подачей .
Одновременно масло через постоянное гидравлическое сопротивление поступает в торцовую камеру 4, откуда через сопло, частично перекрытое иглой 8, в сливной бак. Игла жестко связана с катушкой 7, помещенной в поле постоянного магнита 6, и нагружена сверху силой пружины. Электрические сигналы, подводимые в обмотку катушки, создают электромагнитную силу, перемещающую иглу. Это вызывает изменения давления в камере 4 и соответствующее перемещение подпружиненного снизу плунжера 10. В процессе работы станка сигнал пропорциональный среднему напряжению в межэлектродном промежутке, сравнивается с эталонным (установленным) напряжением. Разность напряжений поступает в обмотку катушки управления дросселирующего гидрораспределителя и действует в направлении уменьшения рассогласования. Масло от цилиндра плавления через турбинку 11, приводящую во вращение плунжер 10 для повышения точности работы регулятора. Электрогидравлический регулятор привода подачи позволяет расширить диапазон регулирования скорости и повысить быстродействие привода и точность поддержания регулируемого параметра, а также обеспечить остаточную мощность для перемещения тяжелых электродов.
Оборудование для электроэрозионной обработки. Основными элементами электроэрозионных станков являются станина 1 коробчатой или иной формы со стойкой (рис 44), стол 2, ванна инструмент 4, связанный с инструментальной головкой 5, устройсяства 6—9 перемещения инструментальной головки в трех взаимно перпендикулярных направлениях, пули управления 10, трубопроводы подачи рабочей жидкости в ванну ,13 и на слив 12, насос 13.
На некоторых станках стол ванну можно перемещать в относительных вертикальных направлениях. Точные станки снабжены оптической системой отсчета координат, выполняют с цифровой индикацией, с программным управлением, с управлением от ЭВМ.
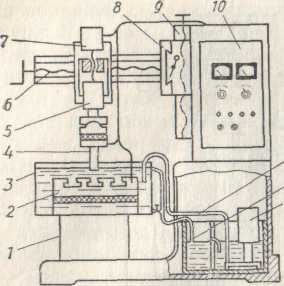
Рис. 44. Устройство станка для электроэрозионной обработки
В крупных станках шкафы с аппаратурой устанавливают отдельно. Станки снабжены фильтрами рабочей жидкости, холодильниками для охлаждения и т. д. В качестве основных размеров универсальных электроэрозионных станков приняты размеры стола и наибольшее расстояние от торца шпинделя инструментально головки до поверхности стола. Длина столов установлена по геометрическому ряду с показателем ф=1,8 (ГОСТ 15954—70), ширина — по геометрическому ряду с показателем ф= 2, а ряд расстояний от торца шпинделя до поверхности стола — с ф=1,6
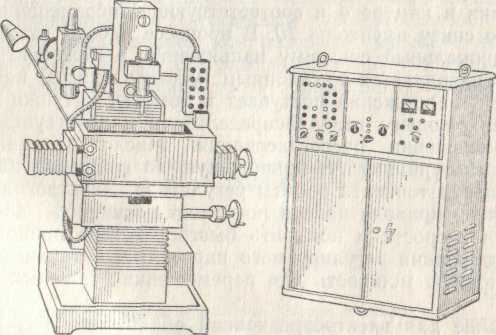
На рис. 45 показан общий вид специального электроэрозионного станка мод ОФ-81. станок предназначен для обработки заготовок сложной формы, изготовленных из труднообрабатываемых токопроводящих материалов, а также для проведения разнообразных фрезерных работ. С наибольшим эффектом станок может быть использован в инструментальных цехах для изготовления разноместных штампов, кондукторов, приспособлений, кокилей; в экспериментальных, ремонтных цехах, а также в основном производстве. Станок оснащен прецизионным вращающимся шпинделем, позволяющим осуществлять электроэрозионную обработку отверстий с высокой точностью; плавное регулирование межэлектродного зазора с помощью автоматического регулятора и подачи винт-гайка качения; эффективной системой подачи, очистки и охлаждения жидкости. Станок оснащен головкой ориентации электрода, микроскопом ЦО-2, тисками, электродной головкой, виброголовкой, орбитальной головкой, сверлильным патроном, центроискателем и др. На рис. 46 показан общий вид электроэрозионного копировально-прошивочного станка мод.4Д721. Наиболее эффективно использование станка в инструментальном производстве, точном приборостроении, радиоэлектронной промышленности.
Выбор материала электрода-инструмента для электроискровой и электроимпульсной обработки определяется материалом заготовки, режимом обработки и стойкостью инструмента или его относительным износом у = -- 100',',,
Износ электродов-инструментов зависит от материалов электродов, параметров импульсов тока и напряжения, свойств рабочей жидкости, жесткости оборудования и т. д.
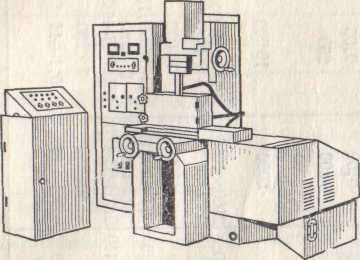
Рис. 46. Электроэрозионный копировально-прошивочный станок мод. 4Д721
Материалы для электродов-инструментов, нашедшие наибольшее применение, можно расположить в ряд по убыванию стойкости: графитированные материалы (ЭЭГ, ЭЭПГ) и пористая медь (МПГ-7, МП-75, МП-8П), вольфрам, медь, латунь ЛС59, серый чугун, алюминий и его сплавы. При оптимальных условиях обработки сталей износ электрода-инструмента из углеграфита составляет 0,1—0,3% на черновых режимах и 0,5—1,2% на чистовых. Износ медных электродов 0,6—1% и 1,5—4% соответственно. При нерациональных режимах обработки и неправильно выбранном материале электрода-инструмента износ может достигать 100% и более. Большое влияние на стойкость инструмента оказывает форма рабочих импульсов.
Наилучшими показателями стабильности процесса обладают электроды-инструменты с рабочей частью из компактной меди. Однако высокая стоимость этого материала, его дефицитность и сравнительно высокий износ ограничивает его применение. Электроды из меди применяют при обработке твердосплавных заготовок, прошивании щелевидных отверстий и отверстий сравнительно малого диаметра, при чистовой обработке на повышенных частотах. Электроды-инструменты из алюминия применяют при предварительной обработке полостей и отверстий без резко выделяющихся в стальных деталях и деталях из жаропрочных сплавов, викой стойкостью отличается вольфрам, однако дефицитность нудность обработки ограничивают его применение для изготовления инструментов.
Методы изготовления фасонных инструментов. Для изготовления фасонных электродов-инструментов применяют следующие методы: металлизация напылением; метод гальванопластики; изготовление методами порошковой металлургии; метод вихревого копирования.
При металлизации напылением исходный материал (порошок или пруток) подается в зону нагрева, расплавляется и струей сжатого газа переносится на подложку (модель инструмента). Затем нанесенный слой от модели отделяют, если его используют самостоятельно, или используют вместе с моделью. Модель по размерам и форме представляет копию того изделия, которое предполагается изготовлять электроэрозионным методом, с учетом припуска межэлектродного зазора. Модель изготовляют из графита МПТ6, ЭЭПГ, АРВу, ГТМ, МПГ7, 9 также из литейных типографских сплавов по гипсовым моделям. Модели изготовляют также стальными. Стальные модели перед металлизацией подвергают дробеструйной обработке.
Для улучшения электроэрозионных свойств напыленный слой подвергают восстановительному отжигу (нагрев до 600° С, изотермическая выдержка в течение 1 ч, .подъем температуры до 800-850° С, выдержка в течение 1 ч, охлаждение в водороде или инертном газе). Этим методом получают напыленный слой до 5 мм шероховатости поверхности до Rz = 40 мкм. Инструмент - газовый металлизатор.
Метод гальванопластики основан на электролитическом осаждении металлов на модель. Толщина осажденного слоя металла 1-5 мм.
Этот метод позволяет получить высокую точность и малую шероховатость поверхности (не хуже Ra = 2,5 мкм). Модели могут быть разового употребления (разрушаемые), например, из гипса или восковых сплавов, или постоянные, изготовляемые из эпоксидных смол, типографских сплавов, хромоникелевых сталей и графита. По конструкции модель должна иметь технологические (нерабочие) поля 30—50 мм. Базовые элементы (штифты, отверстия и др.) выносят на технологические поля.
Изготовление инструментов методом порошковой металлургии рентабельно лишь в крупносерийном или массовом производстве, так как требует изготовления дорогостоящих и сложных пресс-форм из закаленных сталей и твердых сплавов. Технология изготовления электродов-инструментов методом порошковой металлургии предусматривает холодное или горячее прессование порошка в пресс-форме и спекание.
Технология изготовления фасонных углеграфитовых электродом инструментов методом вихревого копирования разработана в СССР. Сущность этого способа состоит в том, что при наличии поступательного перемещения углеграфитовой заготовки фасонному инструменту сообщают возвратно-поступательное колебательное движение, при котором все точки на поверхности инструмента перемещаются по круговым траекториям (совершают вихревое движение). Режущий инструмент для вихрекопировальных станков изготовляют литьем режущей композиции в закрытых формах собираемых из унифицированных деталей. Опыт изготовления электродов-инструментов систематизирован в книге (6).
Размеры электродов-инструментов определяют измерительными приборами. Для измерения толщины нанесенного слоя применяли специальное приспособление, содержащее щуп и рейку с делений ми. Для измерения зазоров в межэлектродном промежутке применяют щупы и индикаторы, а также оптические методы. Эффективным методом измерения зазоров является фотографирование с последующим увеличением. В этом случае необходимо изготовление многослойной модели заготовки, позволяющее проконтролировать величину фактического межэлектродного промежутка на различных уровнях. Зафиксировав инструмент и модель заготовки после обработки и убрав их со станка, снимая пластины заготовки, начиная с нижней, определяют величину межэлектродного зазора.
Для закрепления электрода-инструмента электроэрозионные станки снабжены электродержателями в виде шпинделей с посадочными отверстиями, патронов, цанговых зажимов и др. уточнения положения инструмента относительно заготовки применяют приспособления, позволяющие регулировать его положение как по двум взаимно перпендикулярным осям, параллельным плоскости стола, так и относительно вертикали. Для выполнения прецизионных работ электрод-инструмент устанавливают в приспобление (кондуктор) с направляющими.
Для ускорения выведения продуктов износа заготовки и инструмента из межэлектродного зазора применяют электромагнитный вибратор, сообщающий возвратно-поступательные колебания и инструменту с амплитудой, соответствующей увеличению зазора в 2-3 раза. Частоту колебаний принимают равной 50 или 100 Гц. Для вращения инструмента при обработке отверстий применяют электродовращатель. При нежестких электродах используют направляющие кондукторы. Для сообщения электроду-инструменту плоскопараллельного кругового движения применяют орбитальные головки, приводящие в круговое движение инструмент без вращения вокруг своей оси.
Характеристика оборудования для выполнения электроэрозионной обработки непрофилированным электродом-проволокой, приведена в табл. 20.
Основные требования к электроду-проволоке: 1) малое электрическое сопротивление; 2) высокая прочность на разрыв; 3) невысокая стоимость и недефицитность.
В производстве применяется медная, латунная и вольфрамовая проволока. Медная проволока отвечает первому и третьему требованиям, но ее низкая прочность на разрыв не позволяет работать в интервале оптимальной производительности по натяжению при наименьшей скорости перемотки. Вольфрамовая проволока имеет высокую прочность на разрыв, но дефицитна и обладает большим удельным сопротивлением, что снижает производительность. Ее и применяют при прорезке узких пазов (менее 0,1 мм). Латунная проволока по сравнению с медной имеет большее удельное сопротивление, что компенсируется ее хорошими эксплуатационными качествами (второе и третье требование).
Под действием электрических импульсов проволока-катод в процессе обработки изнашивается. Величина износа зависит от режима обработки, толщины заготовки и скорости перемотки. Скорость перемотки находится в пределах от нескольких миллиметров в секунду до нескольких десятков миллиметров в секунду. Электрод-проволока имеет одноразовое использование, так как после прохождения через зону обработки он становится непригодным для повторного использования (независимо от степени износа). Влияние эрозии особенно резко проявляется при применении проволоки малого диаметра, так как при этом величина эрозии от единичного разряда соизмерима с диаметром проволоки.
Оборудование, применяемое при электроконтактном методе обработки, приведено в табл. 21. Электроконтактное точение выполняют широкими металлическими дисками (толщиной 40—50 мм ), фрезерование — чашечным инструментом, сверление — трубчатым инструментом. Разрезка осуществляется металлическими дисками и дисками, покрытыми абразивно-изоляционным материалом. Для обтачивания крупногабаритных деталей, растачивания отверстий и подрезки торцов целесообразно использовать чашечные электроды-инструменты из серого чугуна диаметром 150—300 мм и высотой 60—90 мм, а для отрезки — дисковые электроды из стали диаметром 250—500 мм и толщиной 2—4 мм.
Характеристики установок для электроискрового упрочнения приведены в табл. 22. Стоимость установок находится в пределах 2-2,5 тыс. руб.
В качестве электродов для электроискрового упрочнения на заводах применяют феррохром с содержанием Сг 3%, графит ЭГ2 и ЭГ4 с зольностью до 2 %; твердые сплавы Т15К6 и Т30К4; специальные сплавы или материалы, получаемые порошковой металлургией.
Накладка электроэрозионных станков и их неисправности. Подготовка электроэрозионных станков к работе заключается в установке заготовки и электрода-инструмента и выверки их взаимного расположения, подготовке ванны к работе и системы прокачки рабочей жидкости, выбору и настройке электрических режимов генератора.
Заготовку устанавливают и закрепляют непосредственно на столе станка или в приспособлении. Электрод-инструмент хвостовиком устанавливают в шпиндель головки.
Для выверки положения электроды-инструменты снабжают контрольными углами или разметкой. При выверке используют индикаторы, оптические приборы, приспособления, позволяющие изменять положение инструмента по отношению к заготовке и угол наклона.
Осуществив выверку положения электрода-инструмента, заполняют ванну рабочей жидкостью (или погружают стол с заготовкой в ванну), проверяют работоспособность системы прокачки. В соответствии с технологической инструкцией устанавливают необходимое давление прокачки. По технологической инструкции станка в соответствии с выбранным режимом работы задают электрический режим генератора импульсов, пользуясь соответствующими таблицами и номограммами, приведенными в инструкции (полярность форму импульсов, скважность, частоту следования импульсов, средний рабочий ток и др.).
Изменение полярности напряжения генератора импульсов в зависимости от требований процесса производится путем переключения на штепсельном разъеме токоподводов к станку. При работе с прямой полярностью на электрод подается отрицательный потенциал, а на обрабатываемую заготовку положительный потенциал Для работы с обратной полярностью производят обратное переключение. Изменение полярности обычно не требует дополнительной изоляции обрабатываемой заготовки от станка.
Установку электрических параметров и режимов работы генератора импульсов осуществляют с помощью переключателей, расположенных на панелях пульта управления. Настраивают регулятор подачи, устанавливая рекомендуемое напряжение регулятора, устанавливают скорость подвода инструмента. Средние значения напряжения при холостом ходе и в работе и средний рабочий ток фиксируют по приборам. Средний рабочий ток зависит как от настройки генератора, так и установки регулятора подачи. Настройку регулятора осуществляют рукоятками «Подача» и «Скорость подвода» и контролируют по приборам, показывающим средние значения токов и напряжений.
Неисправности электроэрозионных станков. Неисправности в кинематике станка сводятся к обычным неисправностям его механизмов, вызванным поломками или износом (например, механизмов установочных перемещений), появлением люфтов, заеданием в подвижных парах и т. п. На прецизионных станках, оснащенные индуктивными системами отсчета перемещений, возможно появление рассогласования индуктивных датчиков мостовых схем. Отказ головки с механическим приводом может быть вызван низким качеством изготовления деталей и сборки, в том числе редуктора, шариковых винтовых пар, направляющих качения и гильз. Снижение чувствительности может быть обусловлено излишним натягом в винтовой паре. О качестве кинематики головки можно судить по току, потребляемому ее электродвигателем. При напряжении 5 В потребляемый ток не должен превышать 50—60 мА при движении шпинделя вниз и 70—90 мА при движении шпинделя вверх.
Нестабильность работы головки соленоидного типа может быть обусловлена заеданием элементов магнитной системы. Отказы головки с гидравлическим приводом обычно вызываются загрязнением масла гидросистемы, появлением утечек и перетечек масла вследствие износа элементов аппаратуры управления, выходом из строя гидроклапанов. На стабильность работы этих головок существенно влияет изменение температуры масла, колебание рабочего давления в гидросистеме. При работе таких головок с генераторами типа ШГИ отмечено, что в диапазоне высоких частот технологического напряжения возникает дрейф нуля следящей системы, что требует ее загрубления.
При появлении течи рабочей жидкости необходимо немедленно вменить прокладки ванны. Отсутствие подачи рабочей жидкости и наполнения ванны может быть обусловлено разрывом цепи
электродвигателя насоса блокировками станка или тепловым реле, горением фильтров грубой и тонкой очистки.