Міністерство освіти І науки, молоді та спорту України Професійний гірничий ліцей м. Комсомольська Дипломна робота на тему
Вид материала | Диплом |
- Міністерство освіти І науки, молоді та спорту України Професійний гірничий ліцей, 368.16kb.
- Міністерство освіти І науки, молоді та спорту України Професійний гірничий ліцей, 550.31kb.
- Міністерство освіти, науки, молоді та спорту україни мукачівський професійний ліцей, 464.46kb.
- Головне управління освіти І науки полтавської обласної державної адміністрації професійний, 108.24kb.
- Міністерство освіти, науки, молоді та спорту україни мукачівський професійний ліцей, 291.98kb.
- Міністерство освіти І науки, молоді та спорту україни, 59.16kb.
- Міністерство освіти І науки, молоді та спорту України, 61.58kb.
- Автореферат дисертації на здобуття наукового ступеня, 657.16kb.
- Міністерство освіти І науки, молоді та спорту україни інститут інноваційних технологій, 238.57kb.
- Міністерство освіти, науки, молоді та спорту україни мукачівський професійний ліцей, 2673.82kb.
Міністерство освіти і науки, молоді та спорту України
Професійний гірничий ліцей м. Комсомольська
Дипломна робота на тему:
«Технологія РДЗ покритими електродами
аспіраційної установки (СІОТ чи ЛІОП).»
Учня групи 3/07
За професією: «Електрогазозварник.
Електрозварник на автоматичних та напівавтоматичних машинах»
Корабльова Олексія Миколайовича
Керівник – викладач спецтехнології
Роман Юрійович Гулий
2010р.
Зміст
1. Титульний лист ……………………………………………………………… 1
2. Завдання ……………………………………………………………………... 2
3. Зміст ………………………………………………………………………….. 3
4. Розділ І. Навісні самохідні автомати …………. ……………………….. …4
5. Розділ ІІ. Інверторні джерела живлення …………… …..……………….10
6. Розділ ІІІ. Ацетиленові установки …..………...………………………….16
7. Розділ ІV. Технологія РДЗ покритими електродами аспіраційної уста-новки (СІОТ чи ЛІОП). ….. ..……………………….…………….........................21
8. Розділ V. Індивідуальні засоби захисту ектрогазозварника……………...38
9. Висновки …………………………………………………………………… 45
10. Література …………………………………………………………………. .46
Навісні самохідні автомати Розділ І. Навісні самохідні автомати.
Один з найбільше широко застосовуваних у промисловості самохідний універсальний автомат під шаром флюсу АБСК (рис. 1) призначений для зварювання прямолінійних і кругових швів всіх видів зварених з'єднань із товщиною елементів, що зварюють, 5-30мм. Автомат АБСК складається із трьох основних частин, з яких методом агрегатування можна компонувати різні за рівнем механізації й ступеня оснащеності апарати: підвісну головку А; підвісний автомат АБ з піднімальним механізмом і флюсо-апаратом і самохідний автомат АБС.
Автомат АБСК розрахований на зварювальні струми до 1000А. Шляхом заміни мундштука й деяких інших вузлів апарат можна пристосувати для зварювання розщепленим електродом або відкритою дугою, а також для наплавочних робіт, у тому числі для наплавлення стрічкою.
Механізм подачі й ходовий візок автомата АБСК оснащені електродвигунами змінного струму; швидкості подачі й зварювання регулюють змінними шестірнями. Підйом головки й маршове переміщення апарата здійснюють вручну. Автомат оснащений флюсо-апаратом змішаного типу.
Зварювальний автомат АБСК протягом тривалого часу успішно експлуатується в промисловості. Він надійний у роботі й простий в обслуговуванні, однак через невисокий рівень механізації мало придатний для використання у високоавтоматизованих установках і лініях.
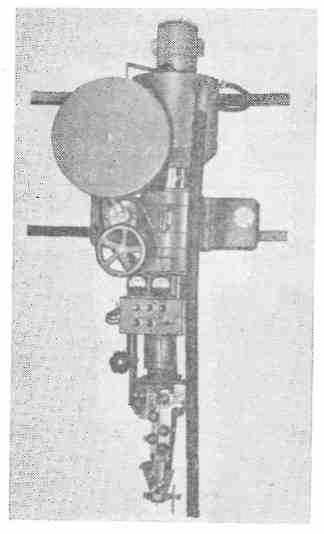
Рис. 1. Універсальний самохідний зварювальний автомат АБСК
Можна розглянути серію важких зварювальних автоматів серії А1400 (мал. 2). Базовим у цій серії є автомат А1401 (мал. 2, а), що складаэться з окремих агрегатів: зварювальної головки, піднімального механізму, флюсо-апарата, штанги, велосипедного візка й ін.
Автомат А1401 оснащений електродвигунами постійного струму, що дозволяє регулювати швидкості подачі й зварювання. Підйом і опускання головки, закріпленої на нижньому торці вертикальної штанги, механізовані.
Ходовий візок, поряд з робочою (зварювальної) швидкістю, забезпечує можливість швидкого переміщення автомата на маршовій швидкості, не порушуючи настроювання робочої швидкості. Це виконується шляхом включення спеціального електродвигуна й відключення електромагнітної муфти.
Флюсовий апарат складається із двох камер — верхньої й нижньої, ізольованою заслінкою. Верхня камера перебуває під розрідженням і служить для відсмоктування нерозплавленої частини флюсу, нижня — є ємністю, з якої подається флюс у зону зварювання.
Автомати для зварювання плавким електродом у захисних газах. Ці автомати відрізняються від описаних вище тем, що вони не мають флюсо-апарата, оснащені спеціальним пальником, що забезпечує газовий захист зони зварювання й водяне охолодження сопла, а також оснащені необхідними газовими апаратурами.
Серія А1400 поряд з автоматами для зварювання під флюсом містить у собі автомати для зварювання в захисних газах.
Наприклад, у складі цієї серії є самохідний автомат А1417 (мал. 2, б), призначений для зварювання сталі у вуглекислому газі й газових сумішах на постійному струмі до 1000А. Автомат оснащений пальником з водоохолоджувальним соплом. Наявність водяного охолодження дозволяє зменшити прилипанння бризків до сопла, підвищує строк його служби.
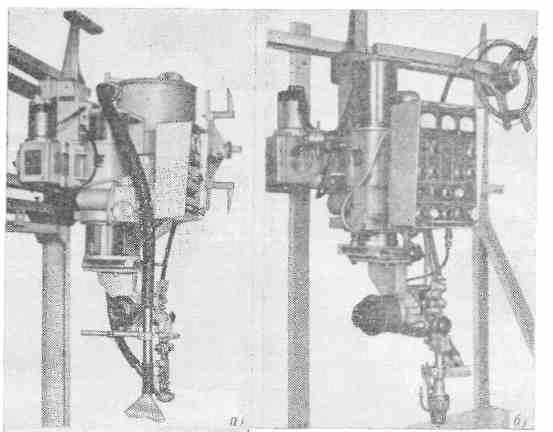
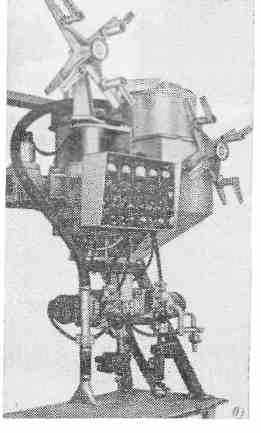
Рис. 2. Зварювальні автомати загального призначення серії А1400
а - А1401, б - А1417, в – А1412
У конструкцію автоматів серії А1400 входять наступні вузли:
1) супорт;
2) механізм подачі;
3) механізм вертикального перміщення;
4) самохідний візок;
5) флюсова апаратура;
6) касета з електродним дротом;
7) пульт керування.
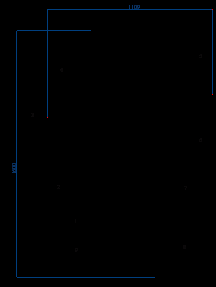
Автомат складається з:
1) механізму подачі електродного дроту;
2) супорту поперечного настроювання;
3) самохідного візка;
4) штанги
5) Флюсо-апарату;
6) котушки з гальмом;
7) механізму підйому;
8) датчика спостереження;
9) флюсовідсмокту;
Автомати для наплавлення плавким електродом можуть виконуватися за допомогою автоматів, призначених для зварювання (як і у випадку застосування напівавтоматів), однак більший ефект дає застосування автоматів, спеціально призначених для наплавлення.
Наплавочні автомати оснащені спеціальними пристроями для виконання широкого наплавлення стрічковим електродом або розщепленим електродом, що складається з декількох дротів, розташованих поперек напрямку руху автомата (наплавлення гребінкою), або одиночним електродом, що робить поперечні коливальні рухи. Крім того, наплавочні автомати розраховані на тривалу роботу без перерв.
Автомат А580М (мал. 3) для наплавлення під флюсом тонким електродним дротом являє собою легку підвісну головку, закріплену на колонку, що забезпечує вертикальне переміщення. Як правило, автомат А580М використають для наплавлення тіл обертання діаметром 40мм і більше.
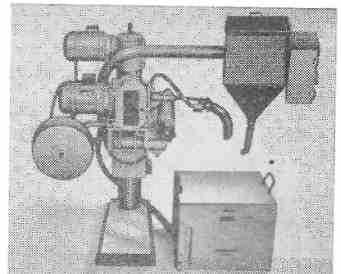
Рис. 3. Автомат А580М для наплавлення
Самохідний наплавочний автомат А874Н (мал. 4) призначений для наплавлення тіл обертання, плоских деталей і деталей складної форми. Широкі технологічні можливості автомата забезпечуються комплектом змінних вузлів і приставок, а також системою керування, що дозволяє вести наплавлення з незалежною швидкістю подачі або з автоматичним регулюванням швидкості залежно від напруги на дузі.
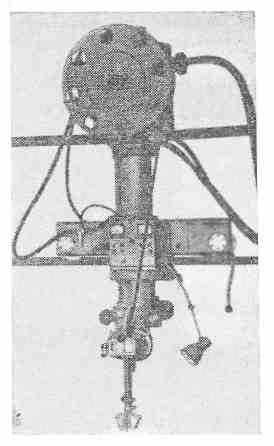
Інверторні джерела живленняРозділ ІІ. Інверторні джерела живлення.
Останнім часом (починаючи приблизно з початку 80-х років двадцятого століття) все більше поширення одержують зварювальні інверторні джерела живлення. Основним блоком такого випрямляча є інвертор - пристрій, що перетворить постійну напругу у високочастотну змінну.
Криві напруг
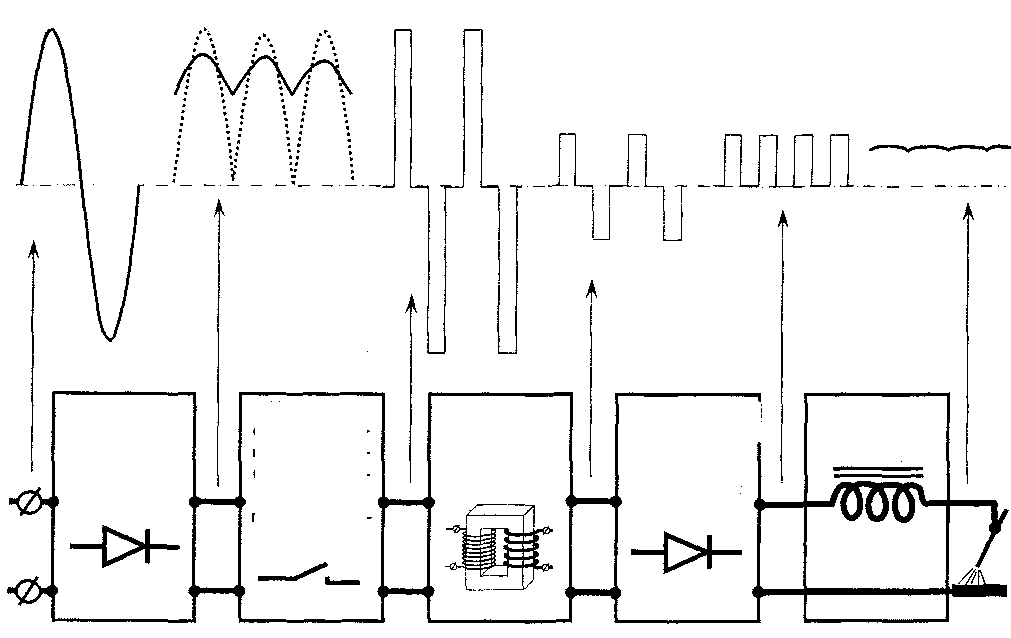
Мережний Інвертор Понижуючий Випрямляч Згладжуючий
випрямляч трансформатор фільтр
Зварювальний інвертор працює в такий спосіб. Мережний випрямний блок перетворить змінну напругу мережі в постійну. Потім ця напруга перетвориться за допомогою інвертора в однофазну змінну високої частоти (до 50кГц і вище). Далі напруга знижується трансформатором, знову випрямляється, згладжується й подається на дугу. Завдяки тому, що на виході інвертора напруга має високу частоту, розміри й вагу трансформатора можуть бути різко знижені, тому що ефективність трансформації підвищується із частотою змінного струму. При цьому також знижується довжина первинної й вторинної обмоток. На малюнку нижче це показано на прикладі трансформатора потужністю 20кВт: в одному випадку трансформатор розрахований на роботу при частоті 50 Гц, а в іншому - 50кГц.
Завдяки малій вазі й розмірам понижуючого трансформатора інверторні джерела живлення також виявляються невеликими по габаритах і легшими, що, власне кажучи, і є основним достоїнством цих джерел. Їх рекомендують використати в тих випадках, де мають значення малі маса й габарити - при зварюванні на монтажі, у побуті, на ремонтних роботах.
Іншим достоїнством є їхня універсальність, тому що їх зовнішні вольт-амперні характеристики можуть бути будь-якої форми, оскільки формуються штучно за допомогою системи керування з використанням зворотних зв'язків по струму й напрузі (тобто в реальному масштабі часу).
Завдяки своїм високим динамічним властивостям (тобто високій швидкодії) і можливості керування параметрами зварювання в реальному масштабі часу ці джерела живлення мають кращі зварювальні властивості в порівнянні з іншими типами джерел живлення, а також часто наділяються додатковими функціями, які сприяють поліпшенню процесу зварювання, такими як дистанційне керування, м'який старт і ін.
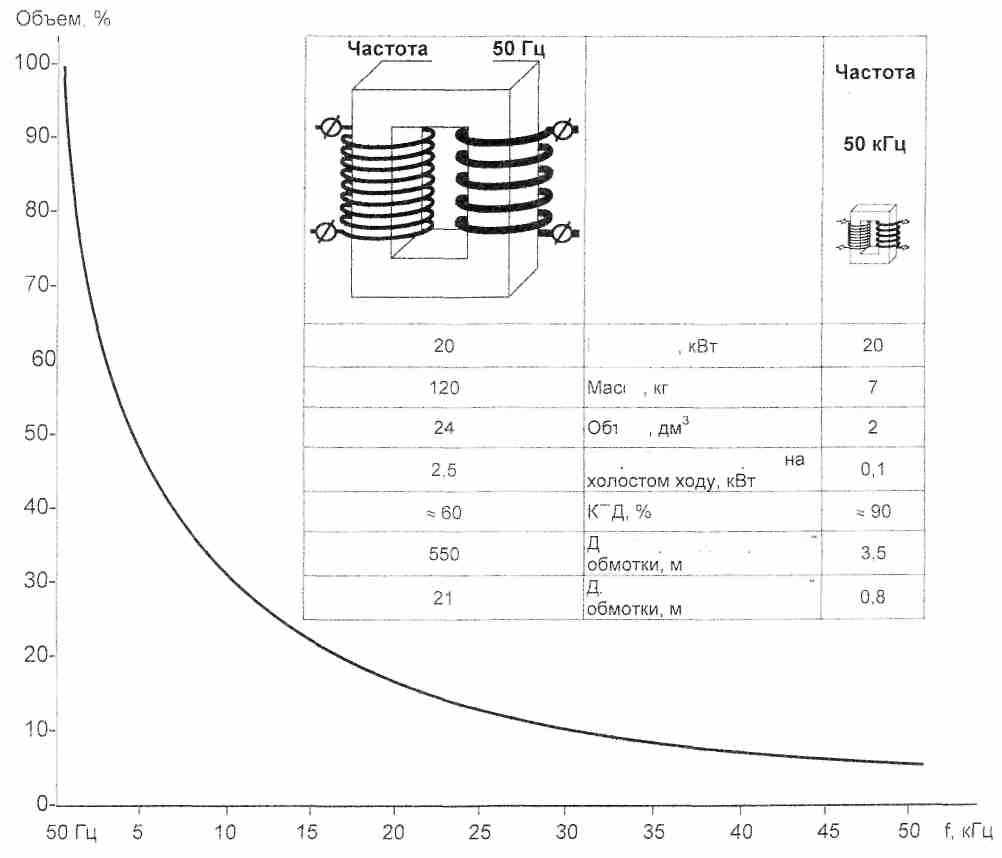
У відповідності зі стандартом ДСТУ ІЄС 60974-1 «Устаткування для дугового зварювання» Частина 1 «Джерела живлення для зварювання» вводяться наступні умовні позначки типів зварювальних джерел живлення.
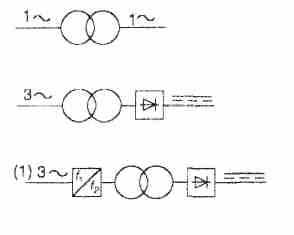
Однофазний трансформатор; одно- чи трифазний випрямляч; одно- чи трифазний інвертор
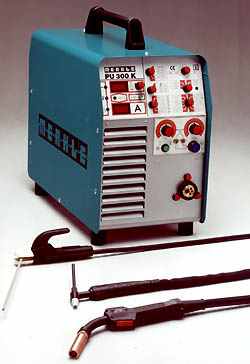
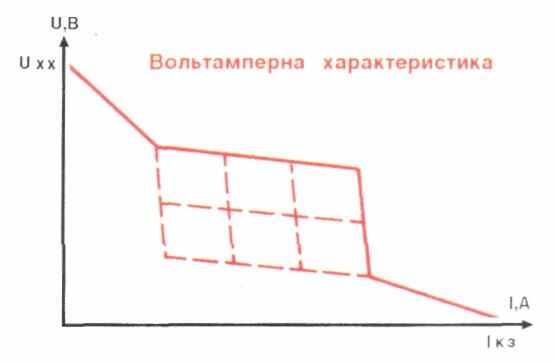
Ділянка 1 – забезпечую високу напругу холостого ходу, що сприяє стабільному запаленню дуги.
Ділянка 2 – дозволяє вести напівавтоматичне чи механізоване зварювання.
Ділянка 3 – реалізує процес зварювання плавким електродом, або неплавким в середовищі аргону.
Ділянка 4 – виключає примерзання електроду при закінчуванні зварювання та заварювання кратера.
Ацетиленові установки Розділ ІІІ. Ацетиленові установки.
Для механізації й автоматизації важких і трудомістких робіт (розкриття барабанів з карбідом кальцію і їхнє транспортування, завантаження генератора карбідом кальцію, видалення вапняного мулу й т.п.) застосовували автоматизовані ацетиленові установки.
На мал. 1 показана автоматизована установка, обладнана стаціонарним генератором «Автогенд-М» продуктивністю 40-60м3/год на надлишковий робочий тиск 0,035МПа (0,35 кгс/см2) [максимальний 0,07МПа (0,7 кгс/див2)]. Генератор призначений для роботи на карбіді кальцію будь-якої грануляції без відсівання пилу. Дрібний карбід кальцію грануляції 2/8 мм можна переробляти в ньому тільки разом з карбідом кальцію більшої грануляції. Температура води в газоутврювачі при нормальній роботі не вище 80° С, температура газу після промивача не вище 35° С.
Генератор складається з газоутворювача 15 системи «карбід у воду», регулятора 16 скидання надлишку води, дистанційного, пульта керування 18 і закритого стрічкового транспортера 10. Прийомний бункер 6 транспортера разом із пневмопогрузчиком 1 розташовані в завантажувальному відділенні ацетиленової станції, а газоутворювач і пов'язані з ним апарати - в іншім відділенні. З метою забезпечення вибухової безпеки в даній установці використана пневмоавтоматика, що діє від заводської магістралі стисненого повітря з надлишковим тиском 0,4МПа (4 кгс/см2).
Барабани з карбідом кальцію розкривають спеціальним верстатом, що має головку з різцями, розташованими по окружності. Днище барабана прорізається при опусканні головки під дією зусилля, що розвиває гідроциліндром головки. Розкриті барабани подають (вручну або кроковим транспортером) на транспортер пневмопогрузчика 1. З пульта керування роблять підняття герметизуючого притиску 5, що, ідучи нагору, натискає пневмокнопку для впуску стисненого повітря в циліндр 8.
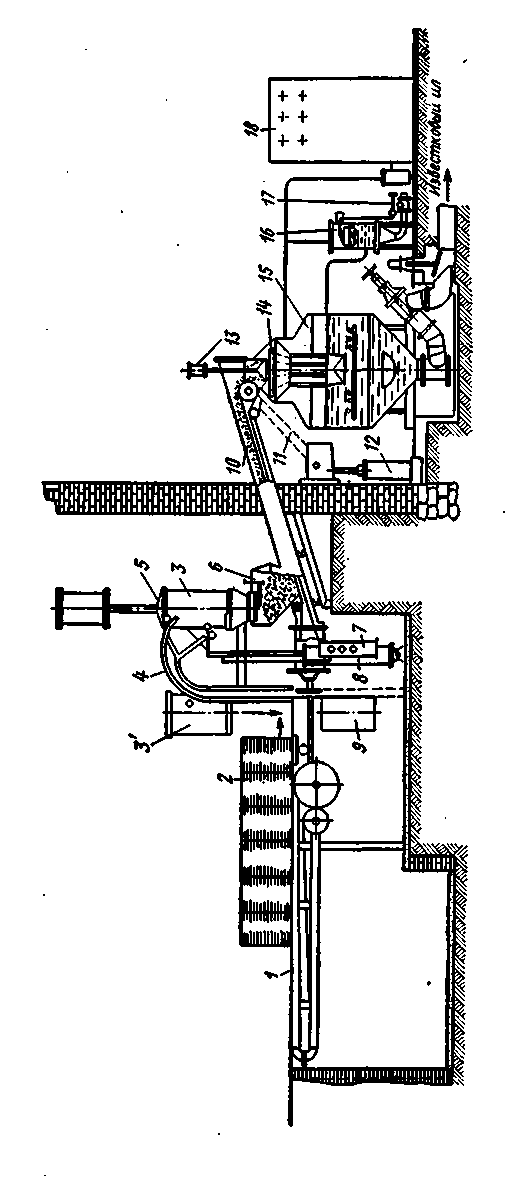
Рис. 1. Ацетиленова установка «Автогенд-М»
Поршень циліндра переміщається й рухає по напрямній 4 поворотний кожух 3, ставлячи його в положення 3' відкритим кінцем униз. При цьому з кожуха випадає порожній барабан 9, а від транспортера відокремлюється візок із черговим розкритим барабаном 2 з карбідом кальцію. Барабан захоплюється кожухом, що, переміщаючись назад по напрямній 4, установлюється на горловину бункера 6; одночасно автоматично включаються опускання герметизуючого притиску 5 і продувки кожуха азотом. Ці операції виконуються автоматично, шляхом перемикання пневматичних кранів, розташованих на панелі 7. Одночасно за допомогою троса на щит пульта керування 18 надходить повідомлення про положення кожуха 3 у кожний даний момент.
Подача карбіду кальцію в газоутворювачі здійснюється за допомогою закритого транспортера 10, що приводиться у рух через ланцюговий привод 11 періодично рейкою пневмоциліндра 12, що штовхає храпове колесо приводного барабана транспортера. Роботою пневмоциліндра 12 управляє пневморегулючий клапан, установлений на пульті 18 Регулятор 16 служить для автоматичного скидання надлишку води з газоутворювача за допомогою наявного в регуляторі поплавка, що відкриває клапан 17.
При зупинці транспортера 10 горловина газоутворювача автоматично закривається ущільнюючим конусом за допомогою пневмоциліндра 13. У момент завантаження карбіду кальцію автоматично включається подача води через сопла кільцевої труби 14 для швидкого гасіння карбідного пилу й дріб'язку, що втримується в карбіді кальцію; при перервах у роботі газоутворючий карбід, що перебуває в карбідоподаючому пристрої, кальцію може зберігатися тривалий час, оскільки система подачі карбіду кальцію герметично закрита.
Автоматизація ацетиленових установок забезпечує також безпеку роботи генераторів. Автоматизації підлягають:
- Включення й вимикання двигуна привода шнека, що подає карбід кальцію в газоутворювач.
- Включення й вимикання насоса, що подає воду в напірний бак.
- Відключення подачі карбіду кальцію в газоутворювач при відсутності води в напірному баці, а також подача попереджувального сигналу.
- Відключення подачі карбіду кальцію в генератор і насосів для води з появою ацетилену в повітрі виробничих приміщень, при відсутності напруги в ланцюгах автоматики, при аварійній продувці трубопроводів азотом, при зниженні тиску повітря, що подається на потреби пневмоавтоматики, і при зниженні тиску азоту, що подається на ацетиленову станцію для продувки.
- Відключення ацетиленових компресорів при падінні тиску ацетилену в усмоктувальній лінії нижче 40мм вод. ст.
- Регулювання режиму роботи блоків адсорбційної осушки ацетилену й відключення електропідігрівачів регенеруючих адсорбент азоту.
7. Крім того, на ацетиленових станціях передбачається також система примусової вентиляції, включає автоматично в потрібний момент.
Технологія РДЗ покритими електродами аспіраційної установки (СІОТ чи ЛІОТ).
Розділ ІV. Технологія РДЗ покритими електродами
аспіраційної установки (СІОТ чи ЛІОП).
Навчаючись у Професійному гірничому ліцею я тричі перебував на виробничій практиці у цехах ВАТ ПГЗК.
Вперше я проходив виробничу практику в ГДМ, де виконував зварювання покритими електродами траків гусениць бульдозерів, гасове різання стержнів для цього, напівавтоматичне зварювання та газове зварювання.
Вдруге я проходив практику в дільниці ремонту бурових станків (МБУ), де виконував РДЗ покритими електродами, гасове різання та киснево-дугове різання.
Втретє я працював від управління «ГОК-сервис» у ЦВО, де разом із наставником та бригадою виконував зварювальні роботи по виготовлення аспірацій них установок.
Циклони СІОТ сухі призначені для грубого й середнього очищення повітря від сухого волокнистого пилу, що не злипається, для очищення газів, що виділяються при деяких технологічних процесах (сушінні, випалі, агломерації, спалюванні палива і т.д.).
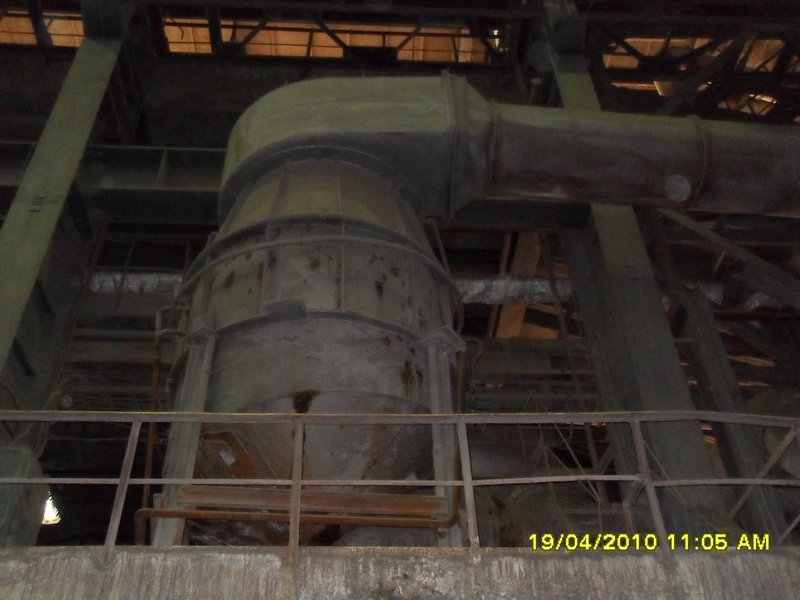
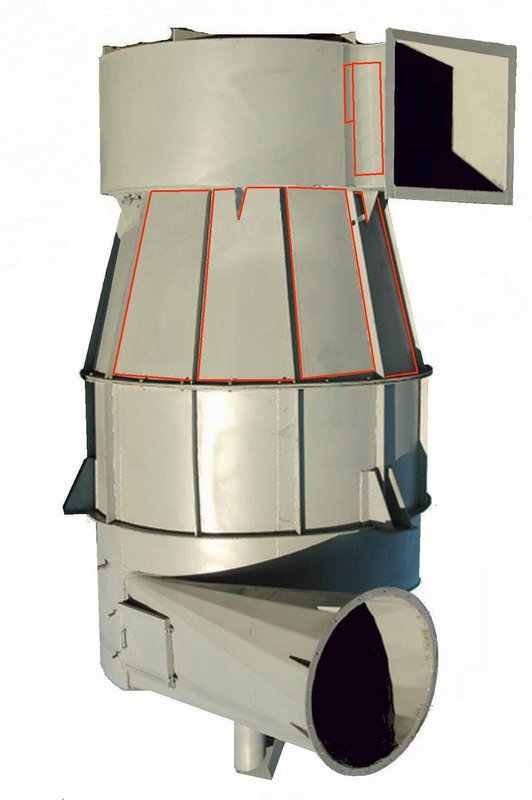
Також циклони СІОТ використовують для очищення аспіраційного повітря в різних галузях промисловості: металургії, хімічній, нафтовій й машинобудівній промисловості, енергетиці, при виробництві будівельних матеріалів.
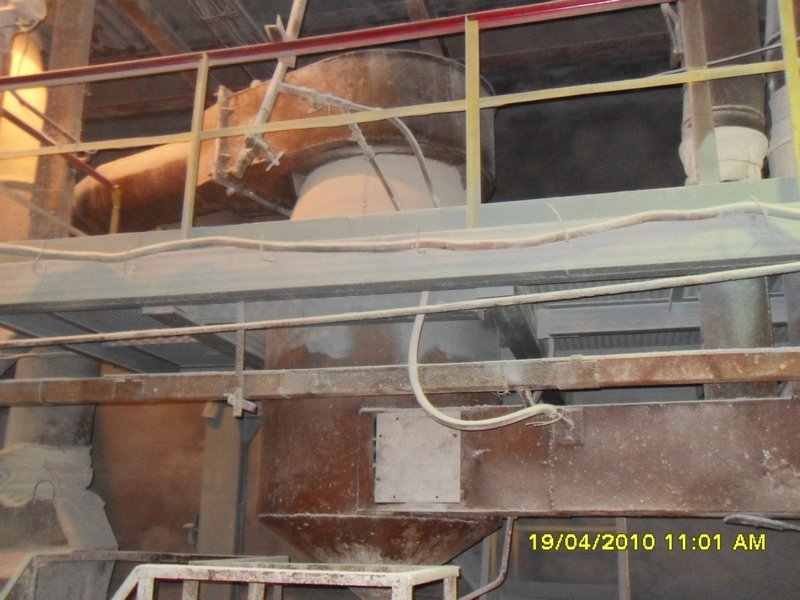
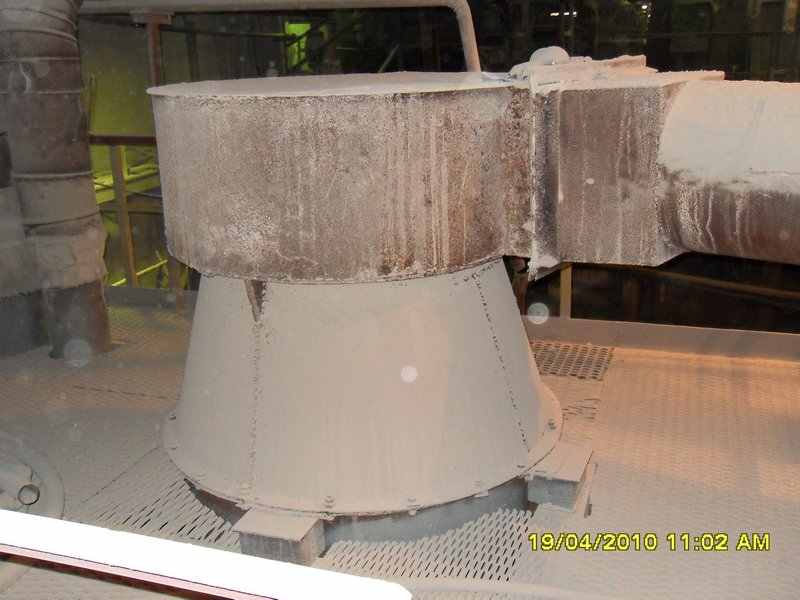
Циклони СІОТ не можна застосовувати в умовах токсичних або вибухонебезпечних середовищ, а також для вловлювання пилу, що сильно злипається.
Температура повітряного потоку не повинна перевищувати 400°С.
Циклони СІОТ установлюють як на усмоктувальній, так і на нагнітальній стороні вентилятора. При абразивних пилах циклон СІОТ слід установлювати тільки на усмоктувальній стороні, при цьому нижню частину циклону СІОТ необхідно бронювати корунд-цементом.
Конструкція циклону СІОТ характеризується відсутністю циліндричної частини корпуса й трикутною формою вхідного патрубка. Конусоподібний корпус створює інтенсивний гвинтоподібний рух повітряного потоку по всій висоті циклону СІОТ, що збільшує очищення повітря від пилу. Для видалення пилу встановлюється пилозбірний бункер. Бункер циклону СІОТ і пиловідвідний патрубок виконані герметичними, тому що підсмоктування повітря через них різко знижує ступінь очищення.
Для зручності циклони СІОТ виготовляють правого й лівого виконання.
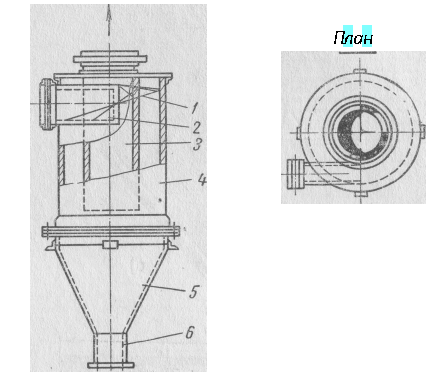
Ефективність очищення повітря в циклонах СІОТ становить 75-85% і залежить від характеру й дисперсності пилу, а також діаметра циклону. При зменшенні діаметра циклону СІОТ, ступінь очищення повітря збільшується.
Коефіцієнт гідравлічного опору, віднесений до швидкості входу газу, становить для циклону з равликом (із гвинтовою кришкою) - 4,2;
Циклони СІОТ різняться по номерах від 1 до 10. Чим більше номер циклону СІОТ, тим більше обсяг повітря, що очищається, відповідно тим вище продуктивність циклону СІОТ.
Продуктивність циклонів:
1 2 3 4 5 6 7 8 9 10
Обсяг повітря, що очищається, м3/год:
1500 3000 4500 6000 7500 8500 10000 12000 14000 15000
При роботі циклону СІОТ повинне проводитися безперервне або періодичне видалення пилу з бункера тому що скупчення пилу в нижній частині циклону значно знижує ступінь очищення повітря й викликає зростання опору. При цьому верхній рівень пиу в бункері повинен бути нижче площини кришки бункера на 400мм.
Циклон СІОТ установлюється на постаменті висотою, достатній для вивантаження пили у візок або в автокару.
Циклон СІОТ може встановлюватися в закритім приміщенні або на відкритім повітрі. При очищенні газів з високою температурою повинна бути виконана теплоізоляція газоходів.
Зварювальні роботи виконують по ГОСТ 5264-80.
Найпоширенішими поперечними коливальними рухами є такі
(рис. 1):
а — прямі за ламаною лінією з кроком 2-3мм (для зварювання листів устик без скосу кромок у нижньому положенні та коли неможливий пропал металу);
б — півмісяцем, повернутим кінцями до наплавленого шва (для стикових швів зі скосом кромок і для кутових із катетом менше 6мм у будь-якому положенні);
в — півмісяцем, повернутим кінцями в напрямку зварювання (для стикових швів зі скосом кромок і для кутових із катетом менше 6мм у будь-якому положенні);
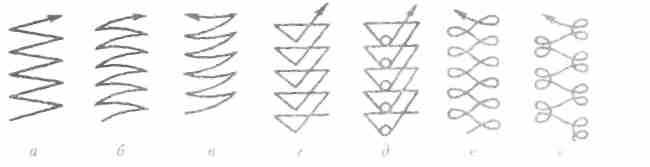
Рис. 1. Коливальні рухи кінцем електрода впоперек шва:
а — прямі за ламаною лінією; б — півмісяцем, повернутим кінцями до шва; в — півмісяцем, повернутим кінцями в напрямку зварювання; г — трикутником; д — трикутником із затримкою електрода в корені шва; е і є — петлеподібні
г - трикутником (для стикових швів зі скосом кромок у будь-якому положенні та для кутових швів із катетом більше 6мм);
д — трикутником із затримкою електрода в корені шва (для зварювання товстостінних конструкцій з гарантованим проплавленням кореневої ділянки шва);
е, є — петлеподібні (для більшого прогріву кромок шва і при зварюванні листів із високолегованих сталей, через їх високу текучість і щоб уникнути пропалів у центрі шва).
Стикові з'єднання без скосу кромок зварюють односторонніми швами із застосуванням електродів діаметром рівним товщині металу, якщо вона не перевищує 4мм. Дугу збуджують із краю скосу кромки в точці А (рис. 2 а), а потім, перемістивши її вниз, проварюють корінь шва. На скосах кромок рух електрода уповільнюють, щоб краще їх проварити. При переході дуги з однієї кромки на іншу швидкість руху електрода збільшують для того, щоб уникнути пропаду в місці зазору.
Листи без скосу кромок товщиною 4-8мм зварюють двостороннім швом. Тонколистовий метал товщиною до 1 -2мм зварюють із відбортуванням кромок або складають без зазору і зварюють на мідній чи сталевій підкладці, що залишається після зварювання. Це дає можливість уникнути наскрізних пропалів.
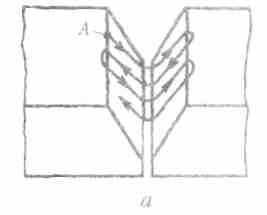
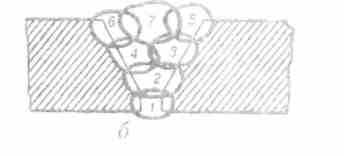
Рис. 2. Зварювання стикових швів:
а — одношарового; б— багатошарового; 1-7— послідовність накладання швів
Метал товщиною понад 8мм зварюють із розчищанням кромок. Залежно від товщини металу, шви виконують одношаровими, багатошаровими або багатопрохідними. Великий кут розчищання кромок (80-90°) більш зручний для зварника, зменшує небезпеку непровару кореня, але збільшує об'єм наплавленого металу, відповідно зменшує продуктивність і збільшує деформації виробу. Нормальним вважається кут розчищання 60°. Його збільшують до 65° для тонких листів і зменшують до 55° для листів товщиною понад 15мм. При цьому зазор і притуплення кромок становить від 1,5 до 4,0мм залежно від товщини листів, режимів зварювання й конструкції виробу.
Одношарові та однопрохідні шви з V-подібним скосом кромок виконують для металів товщиною від 4 до 8мм із поперечними коливальними рухами у вигляді трикутника без затримки у корені шва (товщиною 4мм) і затримкою у корені шва (8мм).
Листи товщиною понад 8мм зварюють багатошаровими або ба-гатопрохідними швами з V-подібним (рис. 2 б) і Х-подібним розчищанням кромок. Вибір багатошарового або багатопрохідного шва залежить від товщини зварюваного металу та його хімічного складу. Багатошаровий шов виконується швидше багатопрохідного. Після накладання кожного наступного шару попередній шар детально зачищають від шлаку. Багатопрохідний шов виконується тонкими й вузькими валиками без поперечних коливальних рухів електрода.
Кожний шар багатошарового шва має збільшений переріз порівняно з перерізом кожного валика при багатопрохідному зварюванні, тому багатошаровий шов забезпечує вищу продуктивність. Багатошарове зварювання має переваги над одношаровим:
- зменшується об'єм зварної ванни, в результаті швидкість охолодження металу збільшується і розміри зерен зменшуються;
- кожний наступний шар термічно обробляє метал попереднього шару і біляшовна зона має дрібнозернисту структуру з підвищеною пластичністю та в'язкістю;
- хімічний склад основного металу близький до хімічного складу наплавленого металу тому, що мала сила зварювального струму сприяє розплавленню незначної кількості основного металу.
Щоб метал достатньо прогрівався і відпалювався, кожний шар шва повинен мати товщину не більше 4-5мм і не менше 2мм. При зварюванні з Х-подібним скосом кромок металу товщиною 12мм треба накласти 4-6, а при товщині 40мм — 10-16 шарів. Двобічні Х-подібні шви мають переваги над однобічними V-подібними:
- зменшення деформацій;
- зменшення об'єму наплавленого металу, а значить підвищення продуктивності зварювання;
- можливий непровар у корені шва розташований в нейтральному перерізі, тому менш небезпечний.
Стикові шви листів великої товщини (понад 20мм) доцільно зварювати з криволінійним скосом двох кромок, що дає можливість застосовувати електроди великого діаметра, забезпечувати надійний провар і рівномірну усадку металу шва.
Для зменшення жолоблення виробу рекомендують виконувати шви почергово то з одного, то з іншого боку листа.
При зварюванні відповідальних конструкцій виконується зворотне підварювання кореня шва (рис. 3). Для цього виріб перевертають і зубилом, різцем чи фрезою утворюють в корені шва канавку шириною 8-10мм і глибиною 3-4мм. Цю канавку заварюють за один прохід підварним швом з невеликим підсиленням електродом діаметром 3мм. Останніми проходами створюється підсилення шва висотою 2-3мм над поверхнею основного металу. Термічна обробка металу верхнього шару виконується нанесенням відпалювального (декоративного) шару товщиною 1-2мм, який забезпечує високу швидкість охолодження металу і дрібнозернисту структуру верхнього шару електродами діаметром 5-6 мм.
Орієнтовні режими зварювання стикових швів вказані в табл. 1 і 2.
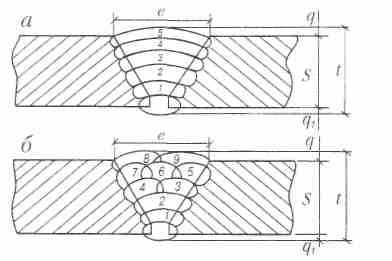
Рис. Зварювання багатошарових і багатопрохідних швів із зворотним підварюванням кореня:
Таблиця 1 Орієнтовні режими зварювання стикових швів без скосу кромок
Товщина металу, мм | Шов | Зазор, мм | Діаметр електрода, мм | Середнє значення сили струму, А | |
нижнє положення шва | вертикальне і стельове положення шва | ||||
3-4 | Однобічний | 1,0 | 3-4 | 180 | 160 |
5-6 | Двобічний | 1,0-1,5 | 4-5 | 180-260 | 160-230 |
7-8 | Двобічний | 1,5-2,0 | 5 | 260 | 230 |
10 | Двобічний | 2,0 | 6 | 330 | 290 |
Таблиця 2 Орієнтовні режими зварювання v-подібних стикових багатошарових швів
Товщина металу, | Зазор, мм | Число шарів, крім підварного і декоративного | Діаметр електрода, мм | Середнє значення сили струму, А | |||
перший шар | наступні шари | положення шва | |||||
нижнє | горизонтальне | вертикальне | |||||
10 | 1,5-2,0 | 2 | 4 | 5 | 180-260 | 160-220 | 150-210 |
12 | 2,0-2,5 | 3 | 4 | 5 | 180-260 | 160-220 | 150-210 |
14 | 2,5-3,0 | 4 | 4 | 5 | 180-260 | 160-220 | 150-210 |
16 | 3,0-3,5 | 5 | 4 | 5 | 180-260 | 160-220 | 150-210 |
18 | 3,5-4,0 | 6 | 5 | 6 | 220-320 | 200-300 | 180-280 |
Примітка. Максимальне значення сили струму встановлюється за даними, вказаними в паспортах електродів.
Кутові шви застосовуються при зварюванні кутових і таврових з'єднань, а також з'єднань внапуск. Зварювання кутових швів виконують похилим електродом і «у човник».
При зварюванні кутових швів «у човник» (рис. 4, в) наплавлений метал буде накладатися в жолоб, утворений двома поличками. Це забезпечує нормальний провар кореня шва і правильне його формування. Зварювання кутових швів «у човник» з товщиною листів до 14мм можливе без скосу кромок (двобічне зварювання) або з частковим розчищанням кромок і збільшеним розміром притуплення. Зазор між кромками не повинен перевищувати 10% товщини листа.
Для уникнення непровару й підрізів кромок, зварювання «у човник» краще вести електродом, який дозволяє впирання покриття на кромки.
При зварюванні кутових швів похилим електродом (рис. 4 а, 6) можливий не-провар кореня шва і кромки нижнього листа. Щоб уникнути непровару дугу збуджують на нижній поличці у точці А, відступивши від катета шва 3-4мм. Потім дугу переміщують до вершини шва, де її трохи затримують для кращого провару кореня шва і піднімають догори, проварюючи вертикальну поличку.
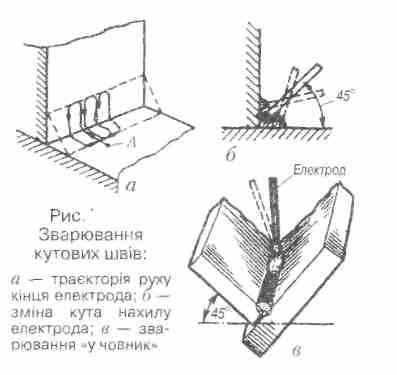
Цей же процес повторюють у зворотному напрямку. Починати зварювання на вертикальній поличці не можна через те, що розплавлений метал з електрода буде напливати на ще холодний основний метал нижньої полички, в результаті чого утвориться непровар. На вертикальній поличці можливе утворення підрізів. Прогрівання кромок досягається правильним положенням електрода, який треба тримати під кутом 45° доповерхні листів і виконувати поперечні коливальні рухи трикутником без затримки або з затримкою в корені шва (рис. 5). Кут нахилу електрода змінюється в процесі зварювання залежно від того, на якій поличці в даний момент горить дуга.
Кутові шви в нижньому положенні з катетами до 10мм зварюють в один шар електродами діаметром до 5мм (інколи без коливальних рухів).
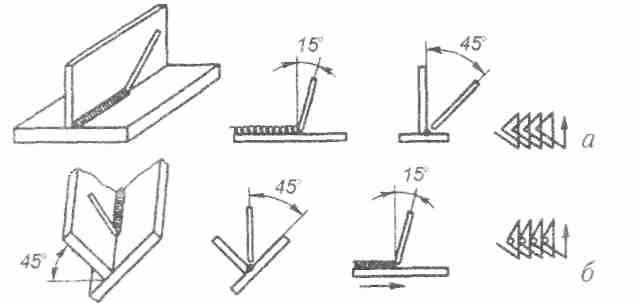
Рис. 5 Зварювання кутових швів із коливальними рухами електрода: а — трикутником без затримки в корені шва; б — трикутником із затримкою в корені шва
Таблиця 3
Орієнтовні режими зварювання кутових швів «у човник» з впиранням електрода
Товщина зварних листів, мм | Катет шва, мм | Діаметр електрода, мм | Сила струму, А |
4-6 6-8 10-14 | 5 6 8 | 5 6 8 | 250-300 300-350 480-560 |
Таблиця4
Орієнтовні режими зварювання кутових швів зі скосом кромок
Вид шва | Товщина металу, мм | Число шарів або проходів | Діаметр електрода, мм | Сила струму, А |
Однобічний | 4 6 8 12 20 | 1 1 1-2 3-4 6-8 | 3-4 4-5 4-5 4-6 4-6 | 120-160 160-220 160-220 160-300 160-320 |
Двобічний | 10 20 40 60 80 | 2-4 4-8 8-16 16-30 30-40 | 4-6 4-6 4-6 5-6 5-6 | 160-320 160-360 160-360 220-360 220-360 |
Примітка. Максимальне значення сили струму встановлюється за даними, вказаними у паспортах електродів.
За розташуванням швів у просторі в момент їх виконання розрізняють: нижні, горизонтальні, вертикальні й стельові шви. Проміжні положення відносять до одного з них відповідно до схеми (рис. 6.)
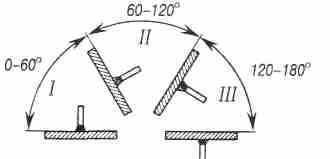
Рис. 6 Схема просторового розташування швів: І— нижнє; II — вертикальне та горизонтальне; III — стельове
Зварювання швів у вертикальному, горизонтальному та стельовому положеннях на відміну від нижнього має ряд особливостей.
Нижні шви найзручніші для зварювання тому, що краплі електродного металу під власною масою легко переходять у зварну ванну. Крім того у цьому положенні зручно спостерігати за процесом зварювання.
Вертикальні шви зварюються знизу вверх і зверху вниз. При цьому основний і електродний метали скапують униз. Тому при вертикальному зварюванні зварювальний струм зменшують на 10-15% порівняно із зварюванням у нижньому положенні, а діаметр електрода не повинен перевищувати 4-5мм. Щоб метал не витікав з ванни, слід підтримувати дуже коротку дугу, при якій відстань між краплями електродного і основного металу настільки мала, що між ними виникає взаємне притягування.
При зварюванні знизу вверх (рис. 7 а) дуга збуджується в найнижчій точці шва і після утворення зварної ванни електрод, спочатку встановлений горизонатально (оложення 1), відводиться догори (положення 2) на кут 45-50°. При цьому нижня частина зварної ванни починає кристалізуватися і утворюється поличка, на якій утримуються краплі металу. Щоб запобігти витіканню металу з ванни необхідно здійснювати поперечні коливальні рухи електродом із відводом його вверх і почергово в різні сторони. Це забезпечує швидку кристалізацію рідкого металу.
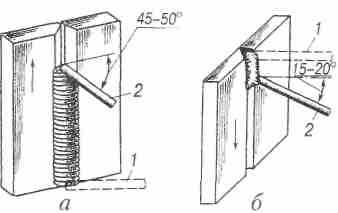
Рис. 7. Зварювання вертикальних швів:
а — знизу вверх; б — зверху вниз
При зварюванні зверху вниз (рис. 7. ) у початковий момент електрод розташовується перпендикулярно до основного металу і дуга збуджується у верхній точці шва. Після утворення зварної ванни електрод нахиляють на 15-20° так, щоб дуга направлялась на основний і наплавлений метал. У цьому випадку рідкий метал частково підтікає під дугу і товщина металу штучно збільшується, що дає можливість уникати пропалів. Тому зварювання зверху вниз використовують для зварювання тонких металів. Для зменшення скапування металу застосовують електроди з целюлозним або пластмасовим покриттям органічного виду (ОЗС-9, АНО-9, ВСЦ-2, ВСЦ-3 та ін.). Продуктивність зварювання зверху вниз вища порівняно із зварюванням знизу вверх. Вертикальні шви зручно зварювати електродами з впиранням покриття на зварювані кромки.
Горизонтальні шви (на вертикальній площині) зварювати складніше вертикальних (рис. 8. На верхньому листі можливі підрізи. Тому зварювання ведуть короткою дугою і електродами діаметром до 4-5мм. Силу зварювального струму зменшують на 10-15% порівняно з нижнім положенням. Щоб запобігти скапуванню рідкого металу скіс кромок виконують на одному верхньому листі (рис. 8 а) під кутом 50 ±5°. Дуга при цьому збуджується на нижній горизонтальній кромці (положення 1), а потім переноситься на похилий скіс {положення 2), піднімаючи догори краплю металу. Електродом виконують спіральні коливальні рухи. Горизонтальні шви внапуск зварювати легше стикових тому, що кромка нижнього листа сприяє утриманню розплавленого металу від скапування вниз (рис. 8 б). Коли зварюють горизонтальні шви з двома скосами кромок (рис. 8 в), установлюють такий порядок накладання нівів, при якому в процесі проварювання верхньої кромки вдасться уникнути стельового положення кратера з розплавленим металом. При зварюванні горизонтальних швів високу якість забезпечують електроди з целюлозним покриттям (виконують упиранням покриття в кромки металу).
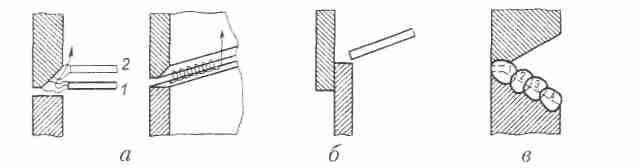
Рис. 8. Зварювання горизонтальних швів:
а — стикове з'єднання із скосом однієї кромки; 1 і 2 — послідовність руху електродів; б — з'єднання внапуск; в — стикове з'єднання із скосом двох кромок; 1-4 — порядок накладання швів
Стельові шви зварювати найскладніше. їх виконують зварники найвищої кваліфікації. Складність зварювання полягає в тому, що краплі металу намагаються скапувати вниз та утруднюється перенесення крапель із електродного металу у зварну ванну. Складностей можна уникнути, зменшуючи силу зварювального струму на 15-20% порівняно з нижнім положенням, використовуючи електроди діаметром до 4мм. При цьому зменшиться об'єм зварної ванни. Основною умовою одержання якісного шва є підтримання дуже короткої дуги шляхом періодичних замикань електрода з металом ванни. Кут нахилу електрода до основного металу становить 70-80° (рис. 9). У момент короткого замикання крапля металу під виливом сили поверхневого натягу втягується у зварну ванну, а коли електрод віддаляється, дуга гасне і метал шва кристалізується. Одночасно виконують поперечні коливальні рухи. Метал шва товщиною понад 8 мм зварюють багатопрохідними швами. При цьому перший валик виконують електродом діаметром 3мм, а наступні — діаметром не більше 4мм. Для зварювання стельових швів використовують електроди з впиранням у покриття.
При виконанні стельових швів за допомогою покритих електродів виділяються гази, які піднімаються вверх і можуть залишитися у шві. Тому електроди перед зварюванням необхідно добре просушити.
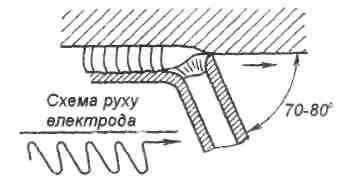
Рис. 9. Зварювання стельових швів
Засоби індивідуального захисту електрогазозварника Розділ V. Засоби індивідуального захисту електрогазозварника.
Для захисту очей і обличчя зварників від світлової радіації електричної дуги застосовують ручні щитки, маски або каски,які виготовляють відповідно до вимог ГОСТу. Ці вимоги регламентують захисні характеристики (відсутність проникнення випромінювання дуги, стійкість матеріалу корпусу до бризок розплавленого металу, питома електрична міцність матеріалу корпусу, опір ізоляції каски), а також масу, габаритні розміри й міцність щитка. Найважливішим і відповідальним елементом щитків є світлофільтри, призначені для захисту очей від ультрафіолетового, видимого та інфрачервоного випромінювань. Світлове випромінювання дуги повинне бути ослаблено світлофільтрами.
При цьому світлофільтри повинні мати достатню величину пропускання у видимій області спектра, що необхідно для спостереження за місцем зварювання.
Нині широко застосовують скляні світлофільтри серії С, які поділяють на 13 класів. Вони забезпечують захист очей від випромінювань при зварюванні та струмах від 5 до 1000 А.
Рекомендовані світлофільтри при дуговому зварюванні.
Спосіб зварювання | Сила струму, А залежно від класу світлофільтра | |||||||||||
С-1 | С-2 | С-3 | С-4 | С-5 | С-6 | С-7 | С-8 | С-9 | С-10 | С-11 | С-12 | |
Покритими електродами сталі, чавуну і міді | − | − | 15-30 | 30-60 | 60-150 | 150-275 | 275-350 | 350-600 | 600-700 | 700-900 | 900 і вище | − |
Плавким електродом в інертних: сталі | − | − | 20-30 | 30-40 | 40-80 | 80-100 | 100-200 | 200-300 | 300-500 | 500-700 | 700-900 | 900 і вище |
легкі сплави | − | − | − | 15-30 | 30-50 | 50-90 | 90-100 | 150-275 | 275-350 | 350-600 | 600-800 | 800 і вище |
вольфрамовими електродами в інертних газах сталі і легованих сплавів | − | − | 10-15. | 15-20 | 20-40 | 40-80 | 80-100 | 100-175 | 175-275 | 275-300 | 300-400 | 400-600 |
Плавким електродом у вугликислому газі сталі | 30-60 | 60-100 | 100-150 | 150-175 | 175-300 | 300-400 | 400-600 | 600-700 | 700-900 | 900 і вище |
Шитки випускають двох видів: із світлофільтром для нормального огляду (розмір 52×102мм) і збільшеного (90×120мм).Від подряпин, пропалів та інших пошкоджень зовні світлофільтр захищає скло товщиною до 2,5мм. Захистні ручні й наголовні щитки для електрозварників із світлофільтрами для нормального та збільшеного огляду призначені для зварювання швів складної конфігурації (перехід з нижнього положення у стельове, вертикальне та в зворотньому напрямку, для зварювання з підвищеною швидкістю або у важкодоступних місцях).
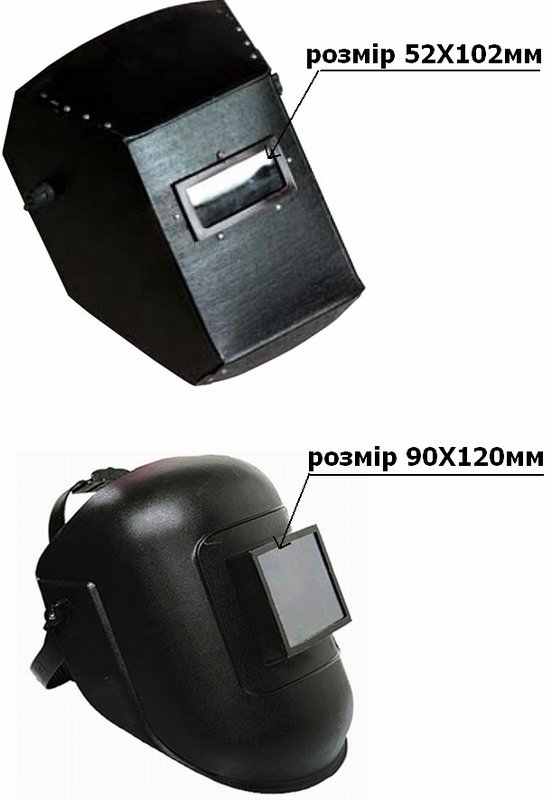
Виробництво спеціального одягу для зварників і його раціональне використання є однією з важливих умов забезпечення безпеки праці, профілактики травматизму та професійних захворювань.
Для захисту від випромінювання, переохолодження при роботі на відкритому повітрі в холодну пору року зварники використовують спеціальний одяг вказаний в таблиці.
Вибір спеціального одягу залежить від виду зварювання та умов праці.
Вид зварювання | Умови праці | Призначення одягу | Рекомендований одяг | |||
Покритими електродами,порошковим дротом у вуглекислому газі | У середині замкнутих просторів із попереднім підігрівом виробів до 400°С | Захист тіла від підвищених температур та інтенсивного розбризкування розплавленого металу | Ізольовані іскростійкий костюми у комплекті з охолоджувальними елементами | |||
Теж з попереднім підігрівом виробів до 150°С | Захист передньої частини тіла від підвищених температур, інтенсивного розбризкування металу | Брезентовий костюм з вогнестійким просочуванням і захисними накладками, виготовлений з іскростійкого й термостійкого матеріалу в комплект з охолоджувальними елементами | ||||
У виробничих приміщеннях | Захист тіла від інтенсивного розбризкування в умовах нормального мікроклімату | Брезентовий костюм з вогнестійким просочуванням із спілка (ТУ 17-08-123-85) | ||||
Теж у холодну пору року | Теж в умовах пониженої температури повітря | Брезентовий костюм з вогнестійким просочуванням і захисними прокладками, з іскростійкого матеріалу з помірним покриттям в комплекті з утепленими прокладками залежно від кліматичних зон країни (ТУ-17-08-122-85,тип Б) | ||||
В інертних газах | У виробничих приміщеннях | Захист передньої частини тіла і обличчя від електромагнітних випромінювань оптичного діапазону (ультра фіолетового) І незначного розбризкування металу | Костюм із полегшеного брезенту із полегшеними накладками із тканини фенілон, стійкий проти опромінювання; костюм із феніло-бавовняної тканини (ТУ 17-08-325-91),халат із феніло-бавовняної тканини (ТУ 17-08-237-85) | |||
Під флюсом | У виробничих приміщеннях | Захист від незначного розбризкування гарячого шлаку та окалин | Брезентовий костюм з вогнестійким просочуванням (ТУ 17-08-237-85) |
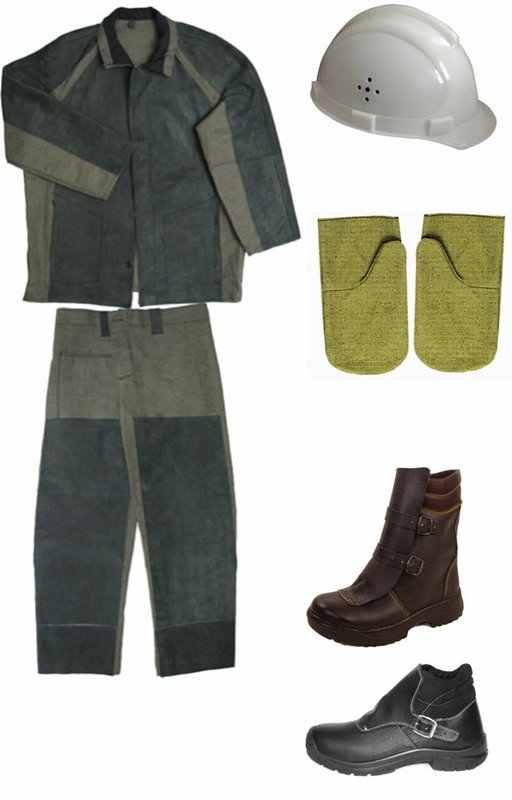
Як було відзначено вище, у виробничих умовах не завжди вдається усунути всі шкідливі фактори, що діють на організм зварника, шляхом застосування наприклад установки вентиляторів і інших пристроїв.
В умовах підвищеного забруднення повітря зварювальним аерозолем, при роботі з замкнутих і напівзамкнутих просторах (резервуари, труби й т.п.), а також при зварюванні кольорових металів і сталей із цинковим покриттям потрібен додатковий захист органів дихання зварника.
Всі засоби захисту органів дихання за принципом дії розділяють на дві групи: фільтруючі респіратори й протигази, при застосуванні яких використовується повітря навколишньої атмосфери, але попередньо очищений за допомогою фільтрів; ізолюючі шлангові й автономні дихальні апарати за допомогою яких в органи дихання по дається чисте повітря від повітродувок, компресорів або балонів.
Найбільш широке застосування в промисловості знайшли фільтруючі протипилові респіратори: ШБ-1, «Лепесток», «Астра», Ф-62Ш, РП-К, У-2к, «Малыш», «Снежок», «У60-М».
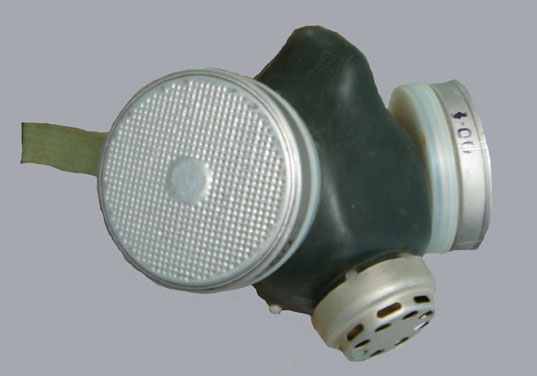
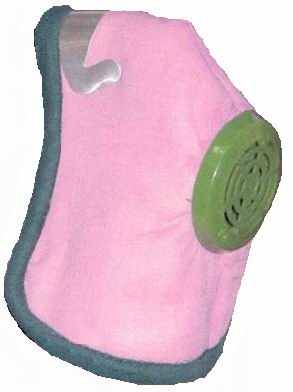
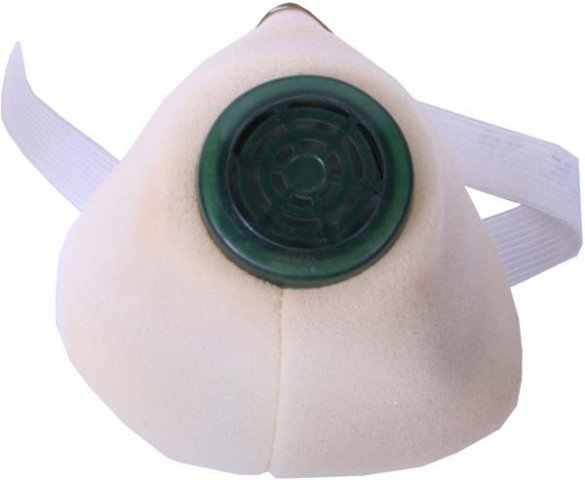
Специфіка зварювальних робіт, виконуваних у монтажних умовах, висуває особливі вимоги до конструкції захисного пристрою із примусовою подачею повітря в зону дихання. Воно повинне бути компактним і універсальним, повинне мати невелику масу, допускати перенесення й підйом на висоту одним зварником.
На мал. показана конструкція пристрою із примусовою подачею повітря в зону подиху зварника. Пристрій складається із щитка 1 спеціальної конструкції, у який по гнучкому шлангу 2 від вентиляційного агрегату 3 подається очищене й підігріте повітря.
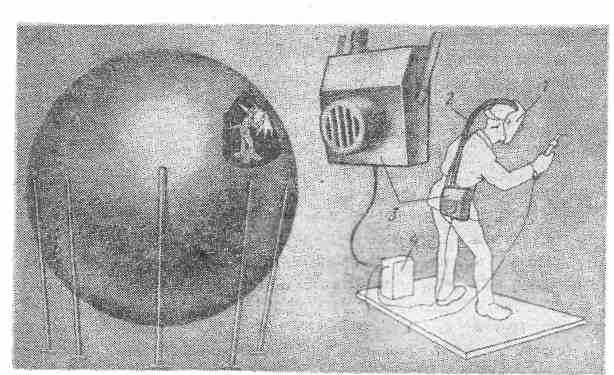
Висновки
Зварювання - технологічний процес виготовлення виробів за допомогою зборки й з'єднання окремих заготовок і деталей, При цьому з'єднання здійснюється не механічними засобами у формі болтів, заклепок, стяжок і ін., а за рахунок сил міжатомної взаємодії деталей, що з'єднують.
Зварювання універсальне: цим способом можуть з'єднуватися метали у виробах різних розмірів при товщині металу, що з'єднують від сотих часток міліметра до метрів, при масі виробу від часток грама до сотень і тисяч тонн. Розміри зварних виробів можуть бути від часток міліметра до гігантських розмірів (пролітні конструкції залізничних і шосейних мостів, корпуса океанських лайнерів, трубопроводи довжиною в тисячі кілометрів).
Зварюванням можна з'єднувати не тільки метали, але й деякі інші матеріали (стекло, кераміку, пластмаси). Можливе зварювання різнорідних металів, наприклад сталі з міддю або алюмінієм. Можна зварювати й зовсім різнорідні матеріали, наприклад метали зі склом.
Література
- Инженер-сварщик. К.К. Хренов – Киев, Вища школа, 1979, 128с.
- Инструмент и средства защиты электросварщика. Р.А. Равлусевич – Москва, Машиностроение, 1984, 96с.
- Иллюстрированное пособие сварщика. В.А. Лосев – Москвка, Соуэлло, 2000, 56с.
- Оборудование для механизированной дуговой сварки и наплавки. А.И. Чвертко – Москва, Машиностроение, 1981, 264с.
- Технологія електродугового зварювання. І.В. Гуменюк – Київ, Грамота, 2006, 512с.