Секторные экономические инструменты и варианты обязательств по ограничению выбросов парниковых газов
Вид материала | Обзор |
- Методика расчета выбросов парниковых газов Содержание, 1290.76kb.
- Сертификации сокращения уровня антропогенных выбросов парниковых газов, 83.51kb.
- 22 ноября предварительный, 28.36kb.
- Регулирование парниковых выбросов: риски и возможности для социально-экономического, 2619.87kb.
- Пункт 5 предварительной повестки дня Прочие вопросы "Круглый стол" по проблемам изменения, 600.53kb.
- Урок «изменение климата» Евсеенко Ольга Николаевна, 271.14kb.
- «Коммерческое использование нетрадиционных ресурсов метана», 49.17kb.
- Пилотная программа Мирового банка по созданию потенциала сопротивления последствиям, 1717kb.
- Стандарты в борьбе с изменением климата, 28.54kb.
- Исо тк 207 , 731.54kb.
По общим удельным выбросам СО2 на единицу продукции различия между странами очень невелики. Однако, это «искусственный» эффект, вызванный тем, что большая часть выбросов зависит лишь от состава цемента, от доли в нем клинкера. При этом клинкера может быть меньше и в современных смесовых цементах и в низкосортных «старых» сортах.
Средние выбросы CO2 при производстве цемента в различных странах и регионах21
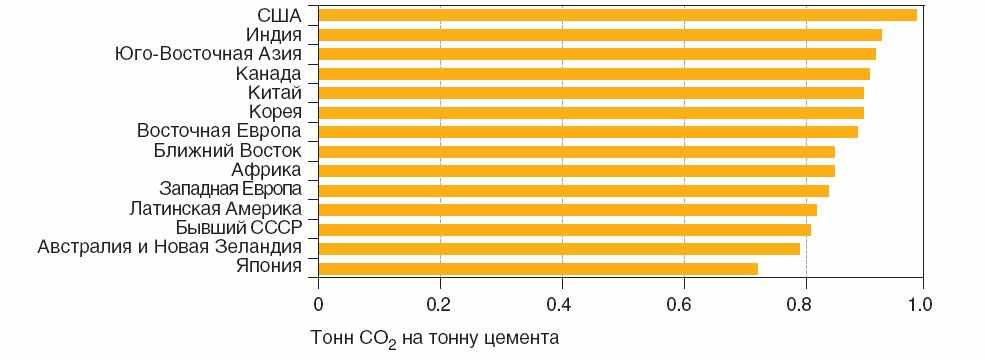
Выбросы СО2 состоят из двух частей. Больший объем (от половины до двух третей) дает эмиссия СО2 при прокаливании известняка до температуры более 9500С, что необходимо для производства клинкера – основной части «обычного» цемента. Доминирующим в мире типом цемента является портландцемент, который на 95% состоит из клинкера и на 5% из гипса. Снизить эту часть выбросов можно, только снижая долю клинкера в цементе, переходя на смесовые цементы или даже на цемент без клинкера, что технологически возможно. В качестве добавок используется поццолана (вулканический туф), летучая зола или гранулированный шлак доменных печей.
Важной альтернативой клинкеру для портландцемента являются негашеная известь и поццолановые смеси. Они широко применяются в Германии и Италии. Однако получаемый в результате бетон чувствителен к воде, а поэтому не может использоваться во всех случаях. Кроме того, наличие шлаковых отходов ограничено, а поццолана может добываться только в определенных местах. При транспортировке цемента или цементного сырья на длинные расстояния может быть дополнительно потрачено большое количество энергии, что увеличит стоимость заведомо дешевой продукции. Тем не менее, заменители клинкера обладают высоким потенциалом, даже в странах ОЭСР. В США можно заменить около 5% всего клинкера.
Состав различных видов цемента
Вид цемента | Портландцемент (%) | Портландцемент с добавкой летучей золы (%) | Цемент на основе доменного шлака (%) | Цемент с активированными шлаками (%) |
Клинкер | 95 | 75 | 30 | 0 |
Зольная пыль | 0 | 25 | 0 | 45 |
Доменный шлак | 0 | 0 | 65 | 0 |
Синтетический шлак | 0 | 0 | 0 | 45 |
Жидкое стекло | 0 | 0 | 0 | 10 |
Гипс | 5 | 0 | 5 | 0 |
В дальнейшем, вероятно, будут разработаны новые виды цемента, в которых в качестве первичного сырья не будет использоваться известняк. Эти новые виды носят название «геополимеров»; технологическая осуществимость, экономическая и энергетическая эффективность этих альтернативных цементов требуют изучения. В целом потенциал сокращения выбросов CO2 к 2050 г. при использовании смесовых цементов и геополимеров оценивается величиной от 200 до 400 млн. т.
Глобальные перспективы технологий смесовых цементов и геополимеров22
Смесовый цемент | 2003-2015 | 2015-2030 | 2030-2050 |
Технологическая стадия | Коммерческая | Коммерческая | Коммерческая |
Размер инвестиций (долл./т) | 0-10 | 0-10 | 0-10 |
Снижение выбросов CO2 (%) | <35% | 35-65% | 35-65% |
Снижение выбросов CO2 (млрд. т/год) | 0 – 0,15 | 0,05 – 0,2 | 0,2 – 0,4 |
Меньшая часть, от трети до половины выбросов СО2 – энергозатраты на измельчение сырья и сушку продукции, которые сильно зависят от технологии. В мире используются 4 основные технологии. Наиболее широко используемым процессом изготовления клинкера является энергоэффективный сухой способ, который постепенно замещает мокрый способ. В последние несколько десятилетий в качестве меры по сбережению энергии применяется также технология предварительного прокаливания, своего рода «полусухой» метод. Одним из способов повышения энергоэффективности барабанных печей для сушки и обжига является увеличение числа подогревателей. Так, увеличение числа циклонных подогревателей с 4 до 6 приводит к снижению потребления топлива барабанной печью примерно на 10%.
Технологии, используемые в производстве цемента в развивающихся странах (особенно в Китае), отличаются от используемых в развитых странах. В то время как в Китае в большей степени применяются небольшие вертикальные печи для обжига и сушки (килны), в развитых странах чаще всего встречаются большие барабанные печи. Большие печи намного более энергоэффективны. Наилучшие технологии производства клинкера на 30-40% более энергоэффективны, чем устаревшие.
Современные сухие барабанные клинкерные печи характеризуются достаточно высокими показателями экономии топлива, потребляя около 3 ГДж на тонну клинкера. Термодинамический минимум, необходимый для поддержания эндотермической реакции, примерно равен 1,8 ГДж на тонну (около 60 кг условного топлива на тонну продукции). В течение нескольких лет проводились исследования, направленные на замену существующей барабанной печи альтернативной конструкцией на основе технологии кипящего слоя. Такая пилотная установка мощностью 20 т в сутки успешно работает в Японии. Использование подобной технологии позволяет небольшим заводам повысить эффективность, однако в случае больших заводов рост эффективности либо незначителен, либо вообще отсутствует. Как результат, данная технология пока не нашла коммерческого применения. Прекрасные технико-экономические характеристики барабанных печей позволяют с большой долей уверенности предполагать, что именно они станут основной технологией в следующие десятилетия. Тем не менее, задача совершенствования технологий существует, и их внедрение может привести к снижению выбросов CO2 на 200-400 млн. т к 2050 г.
Глобальные перспективы улучшения печей - килнов
Улучшение характеристик печи | 2003-2015 | 2015-2030 | 2030-2050 |
Технологическая стадия | Коммерческая | Коммерческая | Коммерческая |
Размер инвестиций (долл./т) | 50-80 | 40-60 | 30-50 |
Снижение выбросов CO2 (%) | 10-15% | 10-15% | 10-25% |
Снижение выбросов CO2 (млрд. т/год) | 0,01-0,02 | 0,1-0,2 | 0,2-0,4 |
Дополнительным фактором является состав используемого топлива. Замещение части ископаемого топлива отходами или биотопливом уже достаточно широко применяется в Европе. Печи для обжига и сушки цемента хорошо подходят для сжигания отходов из-за высокотемпературного режима, а также, поскольку клинкер и известняковое сырье действуют как газоочистительные реагенты. Изношенные шины, древесина, пластмасса, химикаты и другие виды отходов в больших количествах сжигаются вместе в печах для обжига и сушки цемента. В Бельгии, Франции, Германии, Нидерландах и Швейцарии за счет замещения топлива получают в среднем от 35 до 70% и более всей используемой энергии. На некоторых заводах за счет отходов достигнут даже 100%-ный уровень замещения. Тем не менее, очень высокий уровень замещения возможен лишь при наличии систем предварительной обработки и контроля. Например, бытовые твердые отходы необходимо предварительно обработать для получения гомогенных показателей теплотворной способности и характеристик сырья.
Цементная промышленность США ежегодно сжигает 53 млн. изношенных шин (387 тыс. т), что составляет 41% от общего числа сжигаемых шин; при этом высвобождается около 15 ПДж энергии (около 500 тыс. т у.т.). Однако, около 50 млн. шин по-прежнему закапывается. Еще одним потенциальным источником энергии являются битумные дорожные покрытия. Ежегодно, вместо того чтобы сжигаться в цементных печах, это сырье закапывается в отвалы. Общее количество эквивалентно примерно 100ПДж (3,3 млн. т у.т.).
Хотя указанные альтернативные топливные материалы используются довольно широко, последствия их применения противоречивы, поскольку цементные печи не так строго контролируются с точки зрения выбросов, как мусоросжигательные установки. По данным МЭА, в 2003 г. цементная промышленность стран ОЭСР потребила 66 ПДж (2,25 млн. т у.т.) энергии сжигаемых возобновляемых ресурсов и отходов, половину которых составляли промышленные отходы и половину – древесные отходы. В целом по всему миру для производства цемента было использовано 112 ПДж (3,8 млн. т у.т.) энергии биомассы и 34 ПДж (1,15 млн. т у.т.) энергии отходов. Альтернативные виды топлива мало используются за пределами ОЭСР. С технической точки зрения, применение альтернативного топлива можно повысить до 1-2 ЭДж (примерно 30-60 млн. т у.т.), хотя уровень применения в разных регионах мира будет разным – в зависимости от наличия тех или иных топливных ресурсов.
В целом процесс снижения выбросов в отрасли можно разделить на 2 стадии.
1) Повсеместный переход на современную «сухую» технологию.
2) Использование отходов в качестве топлива и снижение содержания клинкера в цементе позволит существенно экономить энергию и снизить выбросы СО2.
Суммарный технический потенциал новых технологий оценивается в среднем в 30% – от 20 до 50% снижения выбросов СО2 в различных регионах мира. Более подробное исследование возможностей внедрения различных цементных технологий в разных странах и мире в целом было выполнено МЭА в докладе 2008.
Потенциал снижения выбросов СО2 при производстве цемента
(от уровня и при объемах производства 2005 г.)23
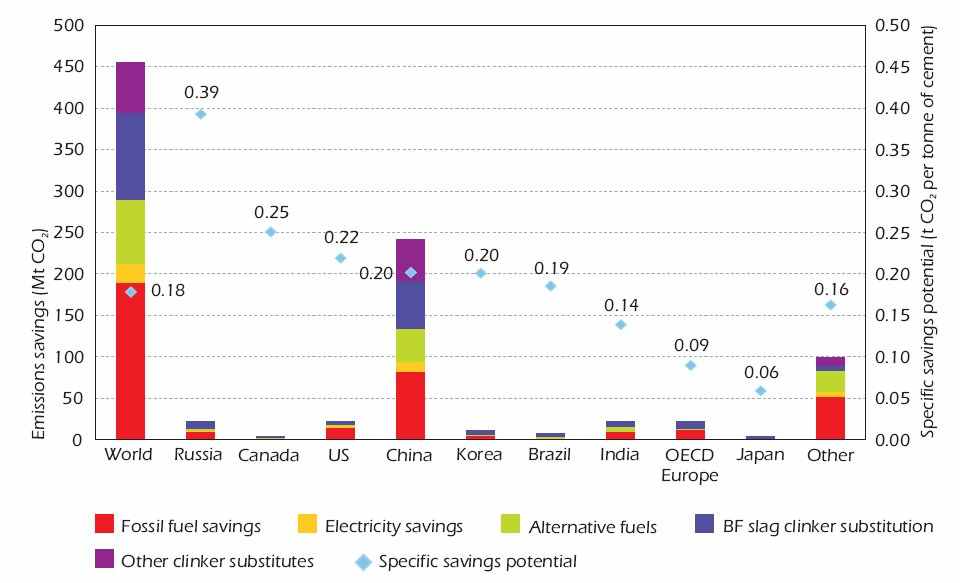
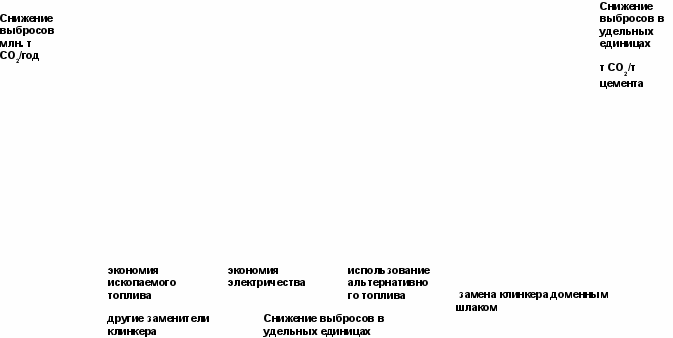
В целом в мире потенциал снижения выбросов оценивается как 450 млн. т СО2/год, где ведущая роль принадлежит Китаю – около 250 млн. т СО2/год. На долю России приходится порядка 20-25 млн. т СО2/год (порядка 1% наших нынешних выбросов парниковых газов или до 1,5% от выбросов СО2 от сжигания ископаемого топлива). Примерно такой же потенциал в абсолютных единицах имеют США и Индия, а также развитые европейские страны (вместе взятые). С другой стороны, в удельных единицах потенциала снижения выбросов на единицу продукции положение России совершенно уникально.
Потенциал России 0,39 тСО2/т цемента, что в 2 раза выше, чем в мире в целом. Следующие вслед за Россией Канада, США, Китай, Корея и Бразилия имеют потенциалы равные 0,25 – 0,19 тСО2/т. Япония может сэкономить только 0,06 тСО2/т, а развитые европейские страны 0,09 тСО2/т.
Возможности России в основном делятся на 2 основные части: больше всего даст переход на «сухую» технологию и связанная с этим экономия топлива – 10 млн. т СО2/год. Экономия электричества может добавить еще 1,5 млн. т СО2/год. Вторая большая часть – замена клинкера доменным шлаком и выпуск современных «смесовых» сортов цемента – 8,5 млн. т СО2/год. Использование альтернативного топлива, в частности, отходов (отработанных шин и битумных покрытий, древесных отходов и т.п.) может снизить выбросы на 3 млн. т СО2/год.
А.2 Черная металлургия
В 2007 г. производство стали в мире превысило 1250 млн. т. Выбросы СО2 могут быть оценены как на основании общего энергопотребления отрасли равного 23ЭДж (или примерно 800 млн. т у.т.). Это дает выброс СО2 порядка 1,5 - 2 млрд. т или 3-4% от глобальных выбросов всех парниковых газов от всех антропогенных источников, включая сведение лесов и потери почвенного углерода. Тем самым, средний удельный выброс равен примерно 1,2 - 1,7 тСО2/т стали. Более точный расчет сделать очень сложно, так как в разных случаях в выбросы включаются, или не включаются такие этапы производства как добыча и обогащение руды, агломерация и производство кокса.
Оценки возможного внедрения лучших технологий в мире в целом показывают, что можно снизить энергопотребление примерно на 20% и выбросы на 340 млн. т СО2. Китай обладает наибольшим потенциалом в абсолютных единицах, однако, это во многом результат больших объемов производства в этой стране. Удельное снижение выбросов может быть больше всего на Украине - 0,70 тСО2/т. Затем идут Индия, Бразилия и Китай. Потенциал России 0,35 тСО2/т или в 2 раза ниже, чем у Украины. Потенциал в развитых странах Европы и в США примерно одинаков и 2 раза ниже, чем у России, а в Южной Корее и Японии в 4-5 раз ниже, чем у России.
Потенциал снижения выбросов СО2 при производстве стали
(от уровня и при объемах производства 2005 г.)24
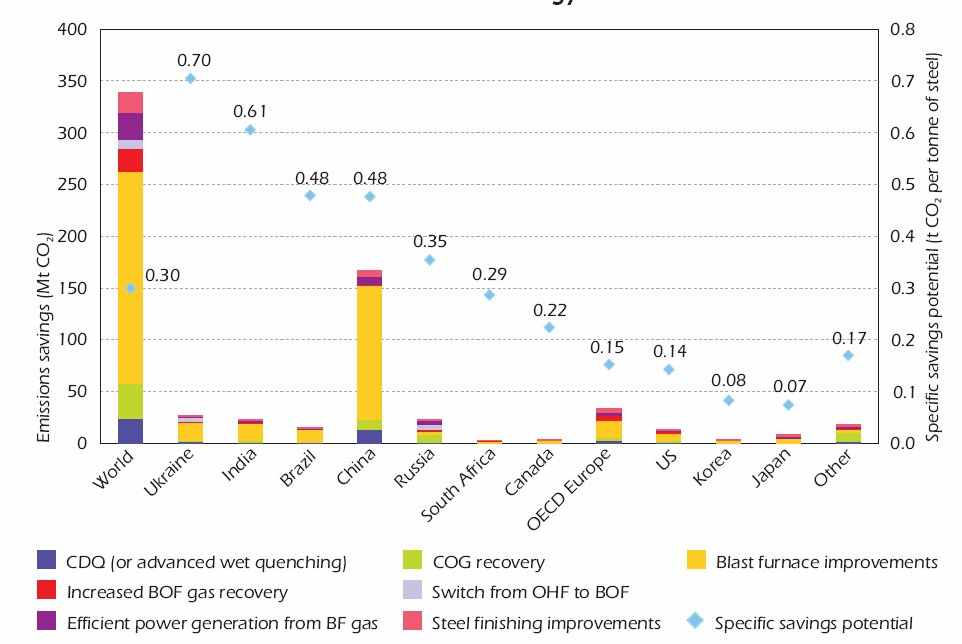
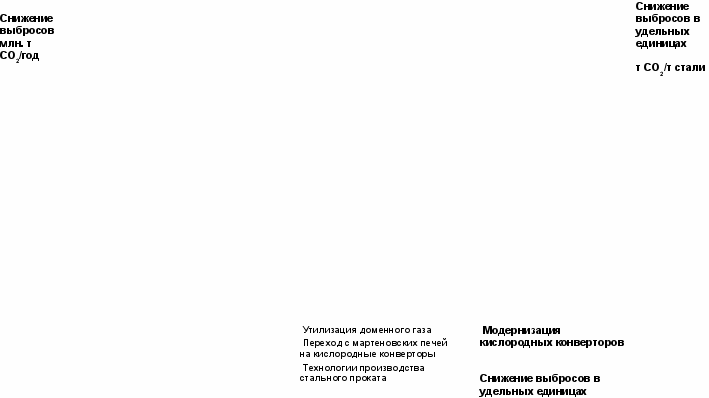
Сухое охлаждение кокса
Утилизация газов на кислородных конверторах
Более эффективное производство энергии из доменного газа
В абсолютных цифрах возможности России оцениваются в 30 млн. т СО2 в год, что составляет около 1,5% всех выбросов парниковых газов в нашей стране. Более 15 млн. т СО2/г снижения выбросов связано с утилизацией доменного газа. Модернизация доменного производства и повышение эффективности управления доменным процессом может дать 6 млн. т СО2/г. Такой же эффект даст переход с мартеновского производства на кислородно-конверторные печи.
По энергоэффективности лучше всего электродуговая плавка (EAF) из металлолома или же из железа прямого восстановления. Тогда расход энергии может быть в 3 раза меньше, чем при наиболее распространенном использовании кислородных конверторов и чугуна из рудного сырья. Процессы выплавки стали по схеме «доменная печь – кислородно-конверторная печь» (BF-BOF) и схеме «железо прямого восстановления – электродуговая печь» (DRI-EAF) являются более энергоемкими, чем переработка металлолома, так как восстановление железной руды требует около 6,6 ГДж химической энергии на тонну железа (при использовании красного железняка – самой богатой руды с точки зрения выхода конечной продукции) и эта энергия не нужна при переработке стального металлолома. Однако переработка металлолома ограничена его наличием, которое определяется масштабами потребления стали в прошлом и скоростью возвращения металла в оборот. Количество стали, которое «запасено» в зданиях, оборудовании, автомобилях и других товарах, больше среднегодового производства стали в десять раз, и объем «запасенного» металла постоянно увеличивается. Поэтому переработка металлолома может покрывать только часть общего производства стали. Также при производстве стали важно наличие руды пригодной для получения недорогого железа прямого восстановления.
В целом, в отрасли сформировалось понимание важности снижения энергетических потерь при коксовании и при агломерации руды, поэтому были предприняты усилия по развитию альтернативных производственных процессов, которые исключили бы энергозатратные фазы производства. К новым технологиям относятся:
- Инжекция угольной пыли в доменную печь в качестве заменителя кокса.
- Новая конфигурация печей, позволяющая использовать уголь вместо кокса (процесс COREX).
- Новая конфигурация печей, позволяющая использовать угольную и рудную мелочь (FINEX и циклонный конвертер).
Фактическое потребление энергии и практически достижимый минимум в основных процессах выплавки чугуна и стали
Продукт/процесс | Фактическое потребление (ГДж/т) | Практически достижимый минимум энергопотребления (ГДж/т) | Фактические выбросы (т/т) | Практически достижимый минимум выбросов СО2 (т/т) | Потенциал снижения (%) |
Жидкий передельный чугун (5% С) | 13 - 14 | 10,4 | 1,45 – 1,56 | 1,16 | 20-26 |
Жидкая сталь (процесс EAF) | 2,1 – 2,4 | 1,6 | 0,36 – 0,42 | 0,28 | 24 - 33 |
Полосовое железо горячей прокатки | 2,0 – 2,4 | 0,9 | 0,11 – 0,13 | 0,05 | 55 - 62 |
Полосовое железо холодной прокатки | 1,0 – 1,4 | 0,02 | 0,17 – 0,24 | 0 | 98 |
Потребление угля и кокса в доменных печах в разных странах сильно различается, оно зависит от размера печи и от доли инжектируемой угольной пыли.
Даже в пределах одной категории доменных печей существуют значительные различия в энергоэффективности, в зависимости от качества руды и производительности печи. Для доменных мини-печей увеличение содержания железа в руде от 50% до 55% снижает потребление топлива с 750 до 600 кг на тонну горячего металла (Tonne Hot Metal – THM), то есть на 20%. Увеличение ежедневной производительности доменной печи с 1 до 1,5 т/м3 снижает расход топлива с 750 до 600 кг/THM. Качество железной руды и угля также влияет на энергопотребление. При достаточно строгом сопоставлении, различия в качестве могут привести к изменению энергоэффективности до 20% величины.
Инжекция угольной пыли является достаточно широко применяемой технологией. Она является финансово привлекательной, так как позволяет заменить кокс. Она приводит также к значительной экономии энергии, так как одна единица энергии кокса заменяется одной единицей энергии угля. На опыте было показано, что уголь может заменить половину кокса в доменных печах. Полагая, что уголь и кокс имеют одинаковую внутреннюю энергию, что половина кокса заменяется углем и что энергия, использующаяся при производстве кокса, равна 8 ГДж на тонну кокса, можно получить экономию за счет инжекции угля до 1 ЭДж в год, а снижение выбросов СО2 в размере 100 млн. т/год.
Перспективы внедрения технологии инжекции угля
Инжекция угля | 2003-2015 | 2015-2030 | 2030-2050 |
Стадия технологии | Коммерческая | Коммерческая | Коммерческая |
Инвестиции (долл./т) | 50-55 | 50 | 50 |
Экономия энергии (%) | 5 | 7 | 10 |
Снижение выбросов СО2 (млрд. т/год) | 0 – 0,05 | 0,05 – 0,1 | 0,1 – 0,2 |
Для замены кокса и угля в доменных печах могут также использоваться пластиковые отходы. Технология была разработана и применена в Германии и Японии. Пластиковые отходы могут также добавляться в коксовальную печь; эта технология впервые внедрена в Японии. В целом на нужды японской черной металлургии идет около 0,4 млн. т пластиковых отходов в год, что примерно соответствует 20 ПДж в год (примерно 0,7 млн. т у.т.).
Применению пластиковых отходов в качестве топлива в металлургии противостоит целый ряд довольно серьезных препятствий. Есть необходимость контролировать содержание поливинилхлорида, так как законодательство некоторых стран, жестко регулирует использование отходов в качестве топлива. Есть необходимость получения разрешительной документации от экологов на использование отходов в качестве топлива. Нужны инвестиции, необходимые для реконструкции системы подачи топлива в доменной печи.