Методические указания рассмотрены и утверждены на заседании кафедры Технологии машиностроения
Вид материала | Методические указания |
- Методические указания для проведения лабораторных занятий по дисциплине «Автоматизация, 598.59kb.
- Методические указания по дипломному проектированию для студентов всех форм обучения, 838.63kb.
- Методические указания по лабораторным работам По дисциплине, 929.67kb.
- Методические указания по лабораторным работам По дисциплине, 803.46kb.
- Методические указания по практическим занятиям По дисциплине, 519.54kb.
- Методические указания по лабораторным занятиям По дисциплине, 487.31kb.
- Методические указания по лабораторным занятиям По дисциплине, 531.16kb.
- Методические указания к выполнению курсовой работы По дисциплине, 218.3kb.
- Методические указания к выполнению курсовой работы По дисциплине, 255.91kb.
- Методические указания по выполнению курсовых работ, 297.99kb.
Разработка маршрутного технологического процесса механической обработки детали.
При разработке технологического процесса должны применяться современные и новейшие достижения науки и техники в области технологии машиностроения. Выбор действующего типового или поиск аналога технологического процесс проводится в соответствии с рекомендациями [].
Последовательность операций технологического процесса определяется:
- принадлежностью к этапу технологического процесса;
- формой детали;
- простановкой размеров;
- производственными факторами.
Рационально вначале выполнять операции, относящиеся к одному этапу, по обработке тех поверхностей, относительно которых указано положение других поверхностей.
Для определения последовательности выполнения операций классифицируют поверхности:
- основные - поверхности, образованные контурами детали (в деталях типа тел вращения основные - наружные поверхности - цилиндрические, конические, а также торцы и центровые отверстия. В корпусных деталях - плоскости и цилиндрические поверхности, которые формируют наружный и внутренние контуры детали);
- поверхности 1 ранга - поверхности, которые расположены на участках основных поверхностей (шпоночные пазы, отверстия, фаски, канавки);
- поверхности 2 ранга - поверхности, которые образуются в результате отсечения объемного элемента с участков поверхностей 1 ранга (резьбовое отверстие в шпоночном пазу).
Анализ технологических процессов показывает, что на этапах получистовой и чистовой обработки последовательность обработки в рамках одного этапа осуществляется в порядке повышения рангов поверхностей. Последовательность обработки поверхностей одного ранга, но различных видов следует устанавливать на основе анализа простановки размеров на чертежах деталей. Наиболее рациональной будет такая последовательность, при которой обеспечивается принцип единства баз.
Определение содержания операции.
Устанавливается последовательность обработки поверхностей и возможность совмещения переходов во времени (концентрация и дифференциация переходов). Выбор схемы построения операции зависит от конкретных условий выполнения операции (последовательная, параллельная или последовательно-параллельная работа инструментов, возможность одно- или многопозиционной обработки и т.п.) Наибольшую производительность обеспечивает многопозиционная многоинструментальная схема. Наибольшую точность и качество поверхностей обеспечивает одноинструментальная одноместная схема обработки. Формулируют выполнение операции по переходам.
Установление режимов резания [].
К основным факторам, определяющим режимы резания, относятся: обрабатываемость материала детали, материал применяемого режущего инструмента и его режущие свойства, износ режущего инструмента, а также геометрические параметры режущей части инструмента, требования к шероховатости и точности обрабатываемой поверхности. Режимы резания рассчитывают в определенной последовательности:
1. Определяется глубина резания.
2. Выбирается максимальная технологически допустимая подача в соответствии с требуемой шероховатостью обработанной поверхности. При обработке на токарных станках рекомендуемую технологически допустимую подачу необходимо проверить по прочности и жесткости резца; прочности и жесткости обрабатываемой детали; прочности механизма подачи станка; шероховатости обрабатываемой поверхности. При обработке на фрезерных станках рекомендуемую таблицами технологически допустимую подачу на зуб фрезы необходимо проверить по прочности механизма подачи станка, жесткости фрезерной оправки. При обработке на сверлильных станках рекомендуемую таблицами технологически допустимую подачу необходимо проверить по прочности сверла и прочности механизма подачи станка.
3. Определяется стойкость режущего инструмента, обеспечивающая наименьшую стоимость обработки и наибольшую норму выработки (по таблицам справочников).
4. Определяется скорость резания.
5. Определяется число оборотов шпинделя в минуту.
6. Расчитывается фактическая скорость резания по принятому числу оборотов.
7. Расчитывается усилие резания.
8. Определяется мощность, затрачиваемая на резание.
Нормирование операции [1,4].
При выполнении курсовой работы техническая норма времени определяется аналитическим расчетным путем.
Основное время То вычисляется на основании принятых режимов резания по формулам содержащимся в литературе по режимам резания [].
Нормативы на отдельные элементы вспомогательного времени, время на обслуживание рабочего места и время перерывов на личные надобности для серийного производства приведены в литературе [].
Выбор баз и разработка схем базирования
детали на операциях.
Каждое приспособление должно обеспечивать выполнение всех функций, обусловленных операцией. Среди них главной является базирование заготовки. После базирования заготовку необходимо закрепить, чтобы она сохранила при обработке неподвижность относительно приспособления.
Базирование и закрепление – это два разных элемента установки заготовки. Они выполняются последовательно. Базирование нельзя заменить закреплением. Если из шести опорных точек отсутствует одна или несколько, то у заготовки остается одна или несколько степеней свободы. Это значит, что в направлении отсутствующих опорных точек положение заготовки не определено и заменить отсутствующие опорные точки закреплением с целью базирования нельзя.
Опорные элементы разделяются на основные и вспомогательные опоры. Кроме того, опоры бывают неподвижными, подвижными, плавающими и регулируемыми.
Основные опорные элементы характеризуются тем, что каждый из них реализует одну или несколько опорных точек для базирования заготовки. Будучи соответствующим образом размещенными в приспособлении, они образуют необходимую при выбранном способе базирования совокупность опорных точек. К основным опорам относятся: опорные штыри, пальцы, пластины, центры, призмы
Вспомогательные опорные элементы отличаются тем, что они подводятся к заготовке после того, как она получила необходимое базирование с помощью основных элементов. Такие опоры используются для увеличения числа точек контакта заготовки с приспособлением с целью повышения жесткости системы. К вспомогательным опорам относятся регулируемые и плавающие одиночные опоры, люнеты
Неподвижные опоры используют только в качестве основных. К ним относятся опорные штыри, пластины, призмы, центры.
Регулируемые опоры применяются в качестве основных и вспомогательных опор. Как основные они служат для установки заготовок необработанными поверхностями при больших изменениях припуска на механическую обработку, а также при выверке заготовок по разметочным рискам.
Плавающие опоры обычно применяют в качестве вспомогательных, но если заготовка имеет сложную форму и установить ее только на постоянные опоры трудно, то плавающие опоры можно применять в качестве основных.
В табл. 1.3 показано графическое обозначение опор в технологической документации.
Таблица 1.3 Графическое обозначение опор
Наименование опоры | | | |
| Спереди, сзади | Сверху | Снизу |
Неподвижная | ![]() | ![]() | ![]() |
Подвижная | ![]() | ![]() | ![]() |
Плавающая | ![]() | ![]() | |
Регулируемая | ![]() | ![]() | ![]() |
При установке заготовки на опорные элементы необходимо правильно выбрать форму рабочей поверхности опоры в зависимости от вида базовой плоскости заготовки и метода ее обработки.
Для выполнения базирования заготовки плоской базой в приспособлении необходимо иметь три опорные точки, расположенные в одной заданной плоскости, но не на одной прямой. Это достигается с помощью различных сочетаний основных опорных элементов: трех опорных штырей, двух опорных пластин, плоскостью опорного элемента.
Базирование с помощью трех опорных штырей применяется в основном, когда плоская главная база заготовки не обработана. В данном случае используют штыри с насеченной и сферической головками. Для установки заготовок с обработанными базами используют штыри с плоской головкой.
Базирование с помощью двух опорных пластин – наиболее распространенный способ ориентирования заготовок с обработанным базами. Две опорные пластины реализуют три опорные точки, поэтому базирование на две пластины полностью отвечает требованиям теоретической механики.
Базирование на плоскость опорного элемента используется только для ориентирования чисто и точно обработанных баз. Примером такого базирования является установка заготовок на плоскость магнитной плиты.
Для базирования заготовок, имеющих основную базу в виде обработанной цилиндрической поверхности, используют широкие опорные призмы, самоцентрирующие патроны, оправки, центры, цанги, гидропластные патроны, конуса.
Для базирования необработанных цилиндрических баз используют узкие призмы, трехкулачковые патроны.
Для установки деталей типа тел вращения используются установочные устройства: центры, оправки и патроны.
Схемы базирования детали должны содержать эскизы детали и расположение опорных точек [].
Главной задачей расчета зажимных усилий при проектировании приспособления является нахождение минимально необходимых усилий.
Факторами, ограничивающими максимальную величину зажимных усилий, могут быть: недопустимая величина повреждения базовых поверхностей и поверхностей зажима, упругие деформации обрабатываемой заготовки, нарушающие правильной обработанной поверхности или повышение погрешности закрепления и установки заготовки.
Исходными данными для расчета усилий зажима являются силы резания, массовые силы, а также силы второстепенного характера. Учитывая, что массовые силы и силы второстепенного характера в большинстве случаев малы по сравнению с усилиями резания, при составлении расчетных схем учитываются силы резания, а влияние остальных сил может быть компенсировано коэффициентом запаса.
Таким образом, при составлении расчетных схем к заготовке приложены силы резания, реакции опор и искомые усилия. На этой схеме также отражаются базирование заготовки и точки приложения усилий закрепления.
На основе расчетных схем или по схемам, приводимым в таблицах данного руководства, находят формулы для расчета потребных зажимных усилий. Найденные по этим формулам усилия закрепления заготовки используются для проектирования рабочих элементов и приводов зажимных устройств приспособлений.
При использовании универсальных приспособлений возникает задача выполнения поверочного расчета. В этом случае по величине действующих усилий резания определяют достаточность создаваемых этим устройством усилий. Если это условие не выдерживается, то производят корректировку режимов обработки в сторону их уменьшения.
При расчете сил зажима необходимо учитывать упругую характеристику зажимного устройства. По этому признаку все зажимные устройства приспособлений делятся на две группы (1).
Зажимные устройства 1-ой группы характеризуются тем, что упругие отжатия в них прямо пропорциональны приложенным силам. К этим устройствам относятся зажимные механизмы самотормозящего типа (винтовые, клиновые, эксцентриковые и др.) независимо от характера привода (ручной, пневматический, гидравлический и т.п.)
К устройствам 2-ой группы относятся пневматические, гидравлические и пневмогидравлические механизмы, непосредственно передающие усилия на заготовку, а также магнитные зажимные устройства. Если приложенная сила меньше, им созданная указанными выше устройствами, то никаких смещений в системе не происходит. Когда приложенная сила превысит противодействующую силу зажима, происходит скачкообразное перемещение на большую величину, и заготовка может быть вырвана из приспособления.
С учетом приведенной выше классификации зажимных устройств в таблицах и расчетных формулах будет оговариваться группа, для которой эти формулы справедливы. Для зажимных устройств 1-ой группы должны быть учтены величины жесткости зажимных устройств и установочных систем приспособлений.
Величины составляющих усилий резания, а также их взаимное расположение определяются в зависимости от характера выполняемой обработки по нормативам режимов резания или по расчетным формулам теории резания металлов. Таким образом, зная условия обработки, всегда можно найти величины действующих сил резания.
2 Основные схемы расчета потребных зажимных усилий
В таблице 2.1 приведены схемы расчета усилий зажима, которые предупреждают поступательное смещение заготовки от действия сил резания.
В таблице 2.2 даны схемы расчета зажимных усилий, когда зажим предупреждает поворот заготовки от действия момента сил резания.
В таблице 2.3 дана расчетная схема и формулы для определения зажимных усилий, когда зажим предупреждает поворот заготовки на базовой плоскости.
В указанных выше таблицах приняты следующие обозначения:
Р1, Р2, Р3 - усилия резания и их составляющие,
Q - расчетная величина усилия зажина заготовки,
f1, f2 - коэффициенты трения соответственно на поверхностях зажима и базирования,
j1 - жесткость зажимного устройства,
j2 - жесткость установочной системы,
К - коэффициент запаса.
Для практического использования формул, приведенных в таблицах 2.1, 2.2, 2.3, необходимо иметь данные по жесткостным характеристикам, коэффициента запаса.
Для численной оценки характеристик жесткости можно пользоваться следующими отношениями:
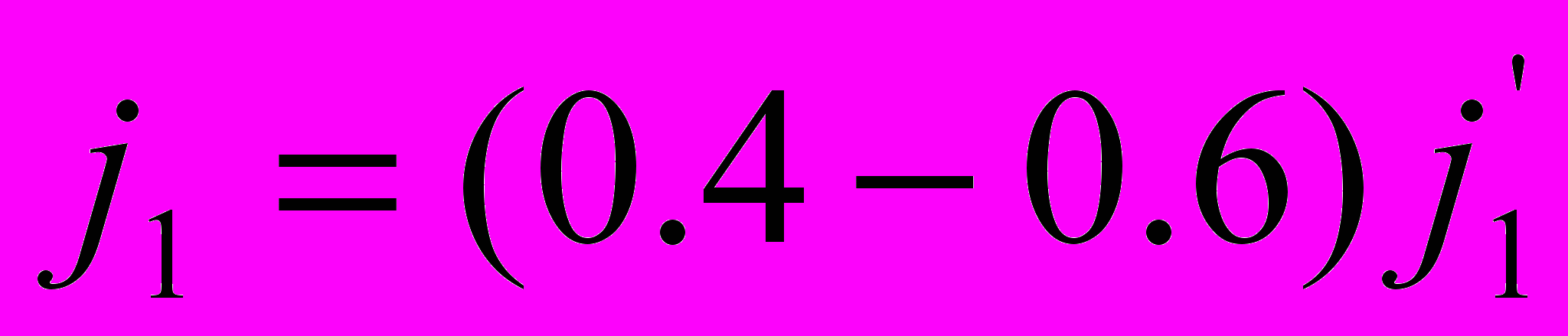
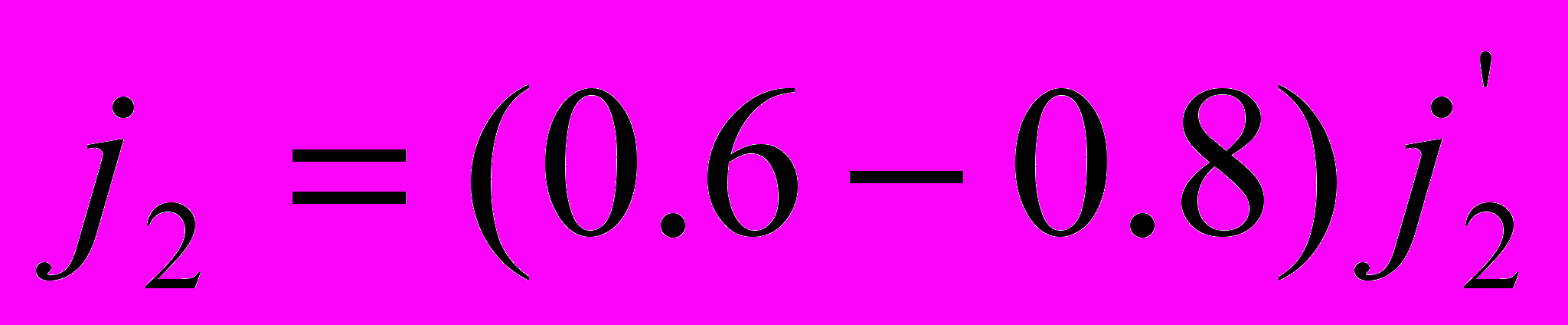
где
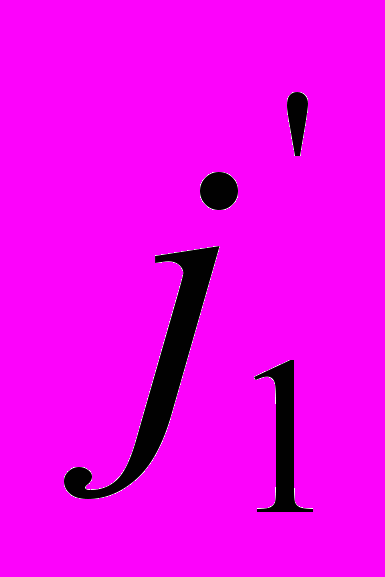
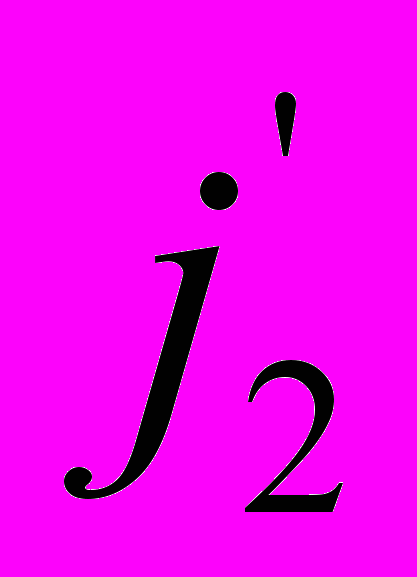
Меньшие значения коэффициентов относятся к многозвенным, нежестким системам. Величина, жесткости установочных систем обычно больше жесткости зажимных элементов и может быть выражена следующим соотношением:

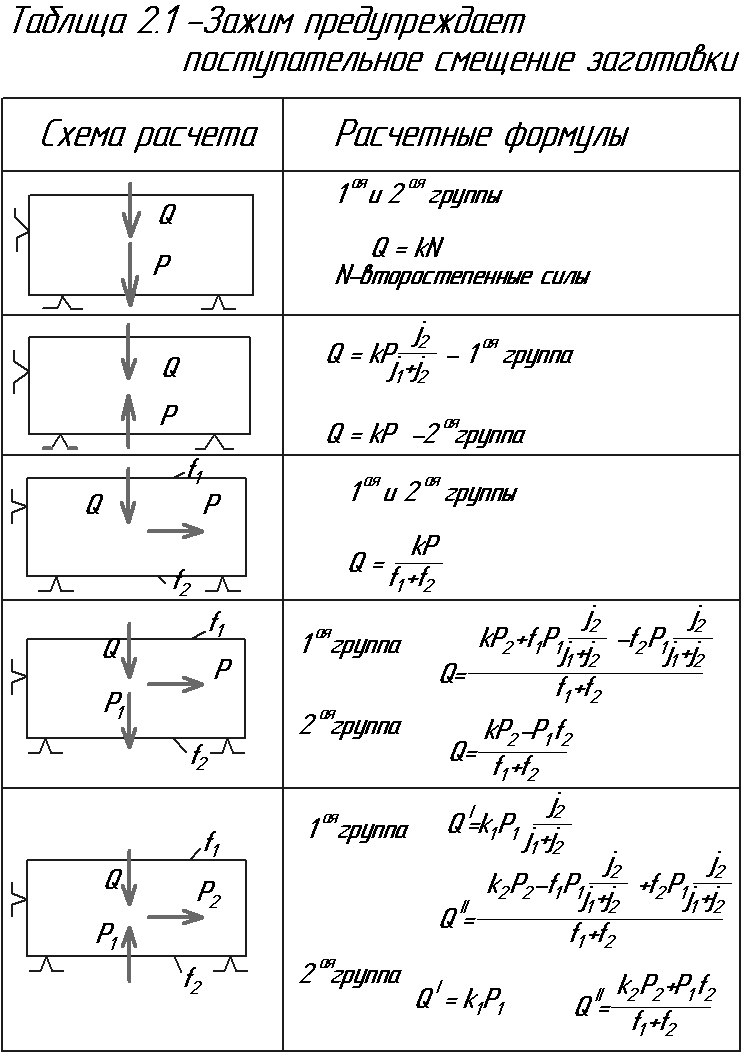
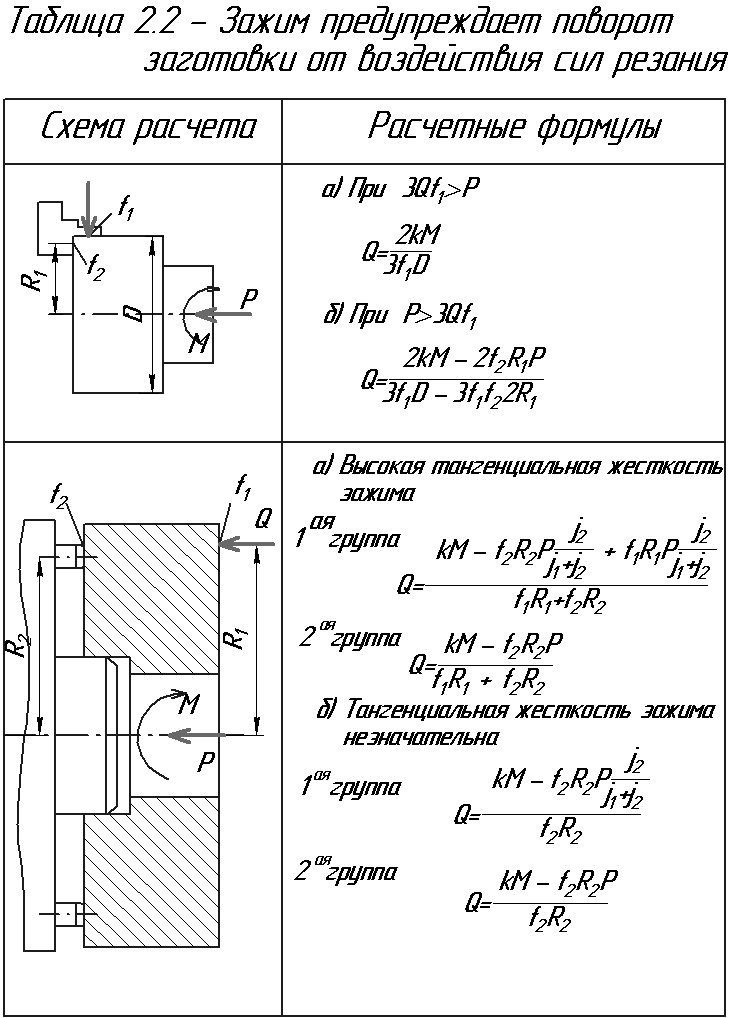
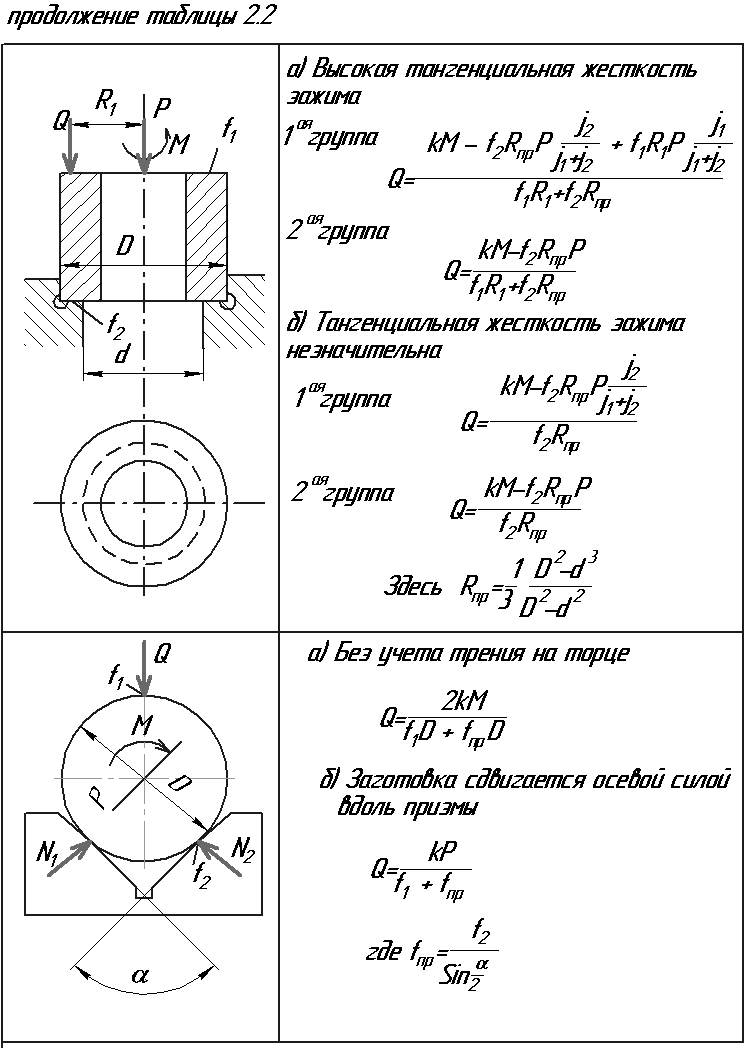
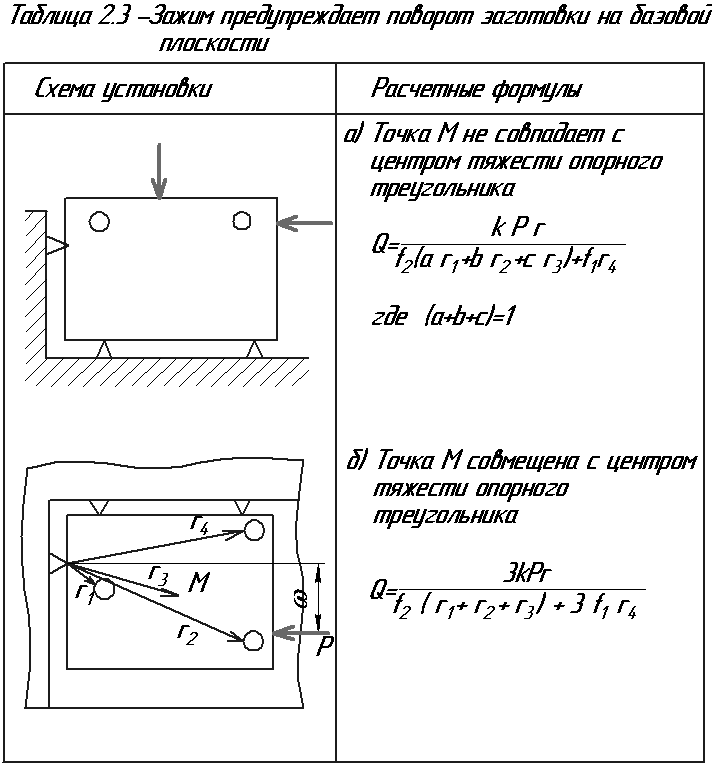
В первом приближении жесткость стыка заготовок из стали и чугуна с установочными и зажимными элементами может быть принята в зависимости от состояния контактной поверхности элементов приспособления.
Элементы с рифлениями - 25 - 55 кН/мм.
Элементы со сферической поверхностью - 50-80 кН/мм.
Плоские обработанные стыки:
шероховатость Rz = 300 - 400 кН/мм
шероховатость Rz = 400 - 600 кН/мм
шероховатость Rz = 700 - 900 кН/мм.
Если неизвестны величины жесткостей зажимных и установочных элементов, то в формулах для расчета зажимных сил можно брать приближенно.
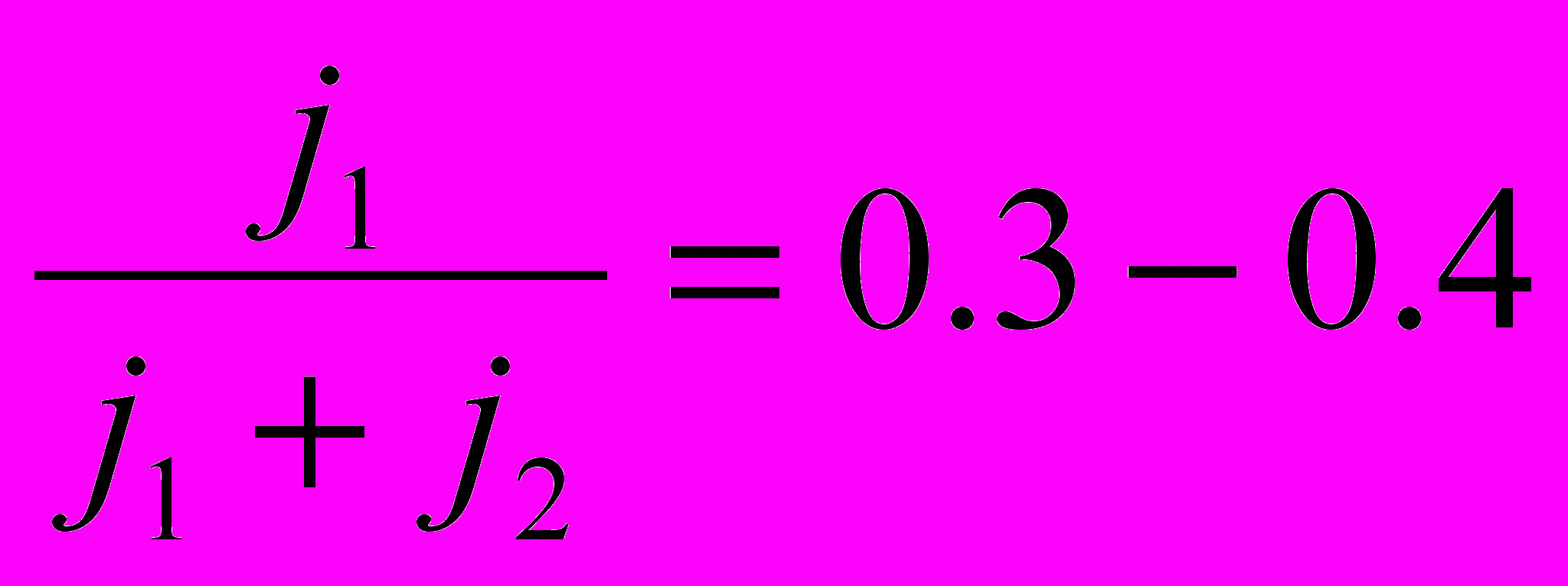
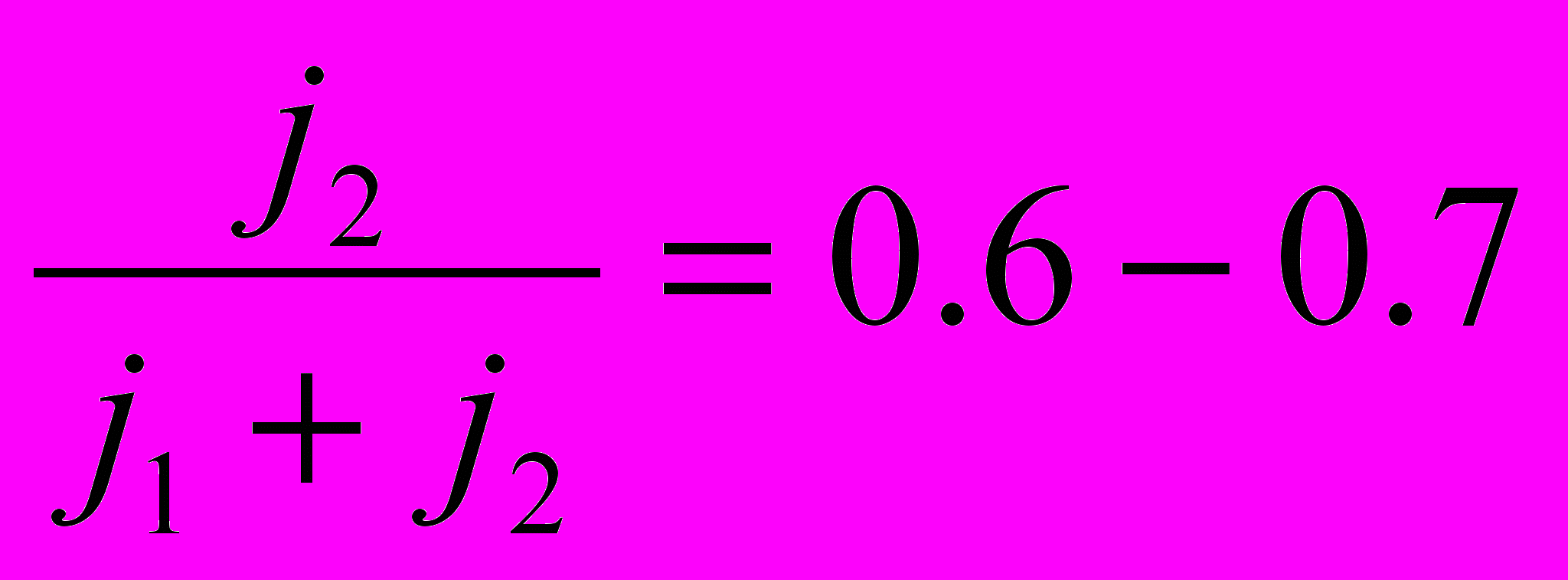
Меньшие значения в первом соотношении и большие во втором соотношении следует брать для зажимных систем пониженной жесткости.
Величина коэффициента трения может быть рекомендована для следующих условий контакта сопрягающихся поверхностей. Контакт по обработанным поверхностям f = 0,16
Необработанные поверхности, в контакте с элементами приспособлений, имеющих сферическую поверхность, имеют коэффициент трения, определяемый по формуле:
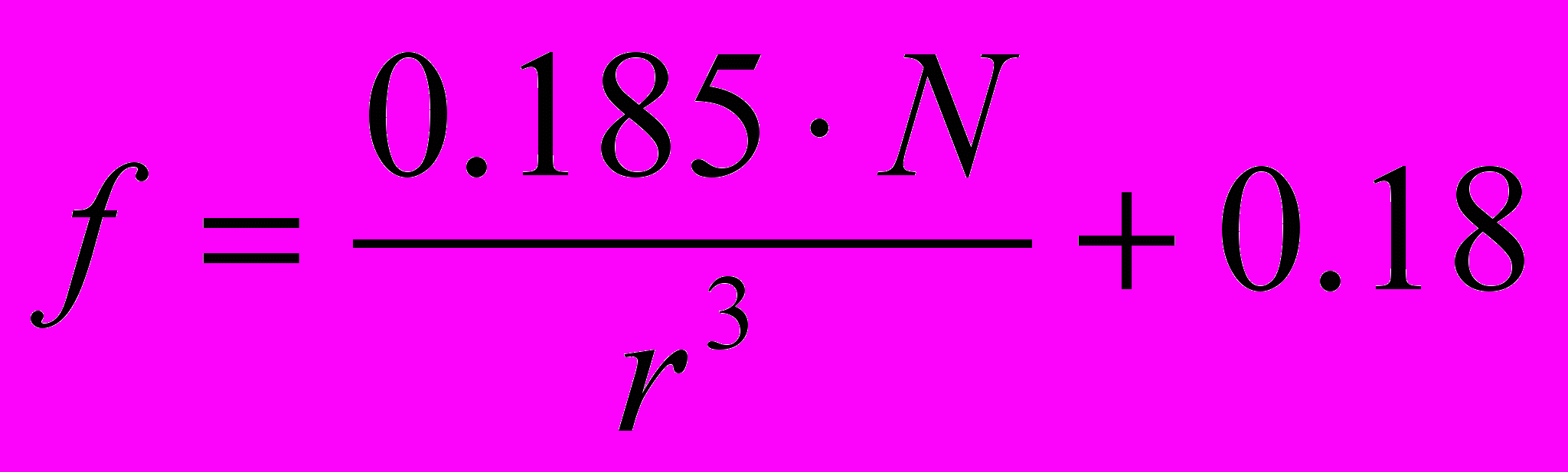
где N - нормальная сила, приходящаяся на опору, в кН
r - радиус сферического элемента в мм.
Наибольшие значения коэффициента трения для этих условий могут достигать величины 0,30.
При наличии рифлений на установочных или зажимных элементах приспособлений коэффициент трения определяется по формуле:
f = 0,005∙q + 0,2
где q - номинальное удельное давление на поверхность стыка, в мПа.
Наибольшее значение коэффициента трения при значительных удельных давлениях (до 100 мПа) могут достигать величины - 0,20.
Приведенные выше значения коэффициентов трения и расчетные формулы справедливы для заготовок из стали и чугуна. Для заготовок из цветных металлов и сплавов величины коэффициентов трения принимать по специальной справочной литературе
Величина коэффициента запаса рассчитывается по формуле, учитывающей влияние целого ряда факторов, а именно:
К = К0∙К1∙К2∙К3∙К4∙К5∙К6
К - минимальный запас для всех случаев, равный - 1,5;
К1- влияние случайных неровностей обрабатываемой поверхности:
черновая обработка - 1,2,
чистовая обработка - 1,0;
К2 - влияние износа и затупления режущего инструмента - 1,0-1,9;
более подробно см. табл. 3.4.
К3 - прерывистый характер резания -1,2
К4 - постоянство создаваемых зажимным устройством усилий:
закрепление вручную - 1,8.
закрепление от постороннего источника энергии, если допуск на размер заготовки не влияет на зажимную силу - 1,0;
К5 - удобство расположения рукоятки при закреплении вручную:
удобное положение, малый угол поворота рукоятку-1,0,
неудобное положение или большой угол поворота (более 90°) -1,2;
К6 - учитывается при наличии моментов, стремящихся повернуть заготовку на базовой плоскости:
опоры с ограниченной поверхностью -1,0,
установка на планки и другие элементы с большой поверхностью контакта - 1,5.
Таким образом, коэффициент запаса должен определяться в каждом отдельном случае с учетом указанных выше факторов и конкретных условий обработки.
Таблица 2.4 – Значение коэффициента К2
Метод обработки | Компоненты усилия резания | К2 |
Сверление | Крутящий момент осевая сила | 1,15 для 1,10 чугуна |
Зенкерование предварительное (по корке) | Крутящий момент осевая сила | 1,3 чугун 1,2 износ до 1,4 мм |
Зенкерование предварительное | Крутящий момент осевая сила | 1,2 износ 1,4 мм 1,2 износ -0,7+0,8 |
Точение и растачивание предварительное | Pz Py Px | 1,0 – сталь 1,0 – чугун 1,4 – сталь 1,2 –чугун 1,6 – сталь 1,25 –чугун |
Точение и растачивание чистовое | Pz Py Px | 0,95 – сталь 1,05 – чугун 1,05 – сталь 1,25 –чугун 1,0 – сталь 1,5 –чугун |
Фрезерование цилиндрическое предварительное и чистовое | Окружная сила | 1,25-1,9-для мягких сталей 1,2-1,4 – твердых сталей и чугуна |
Торцевое фрезерование предварительное и чистовое | Тангенциальная сила | То же |
Шлифование | Окружная сила | 1,15-1,20 |
Протягивание | Сила протягивания | 1,55 – износ до 0,6 мм |
3 Расчет элементарных зажимных устройств приспособлений
3. 1 Винтовые зажимные устройства. Проектный расчет
Номинальный (наружный) диаметр определяется по формуле
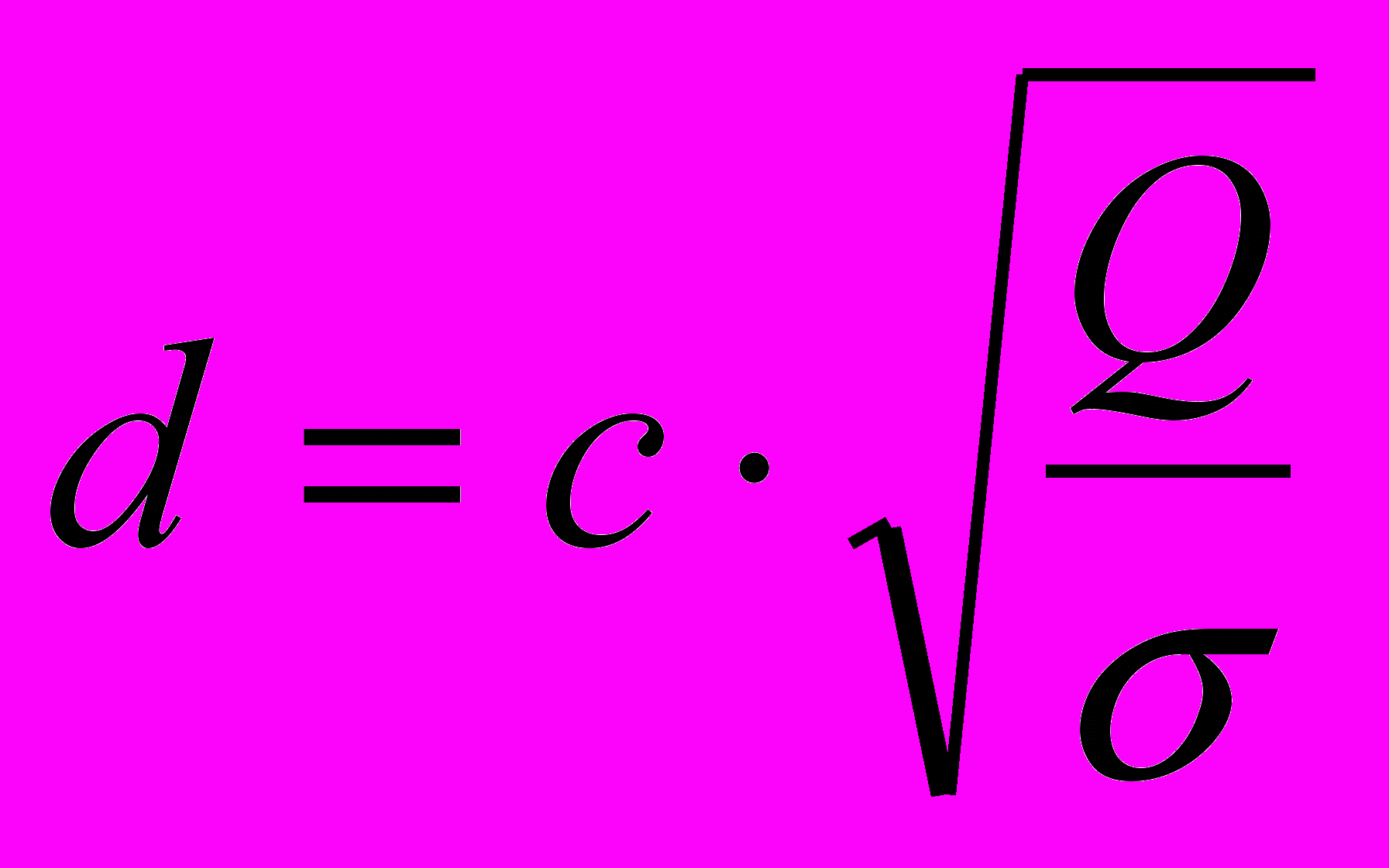
где с =1,4 - для основной метрической резьбы;
Q - усилия, действующие на винт при закреплении заготовки в Н;
- допускаемое напряжение растяжения (сжатия): для винтов из стали 45 можно принимать 80- 100мПа.
Для винтов из других материалов значения допускаемых напряжений растяжения приведены в таблице 3. 1.
Момент, развиваемый на рукоятке или маховичке, для получения заданной силы зажима Q определяется по формуле:
М = 0,001rсрQtg(a + p) + Mmp [HM],
где rср - средний радиус резьбы в мм;
Q - сила зажима в Н;
a - угол подъема резьбы;
р - угол трения в резьбе;
Mmp - момент трения на опорном торце гайки или торца винта в контакте с заготовкой в Нм.
Величина момента трения зависит от характера соприкосновения гайки или торца винта и определяется по следующим расчетным формулам.
Для гаек или звездочек, имеющих кольцеобразную поверхность трения, момент трения определяется по формуле:
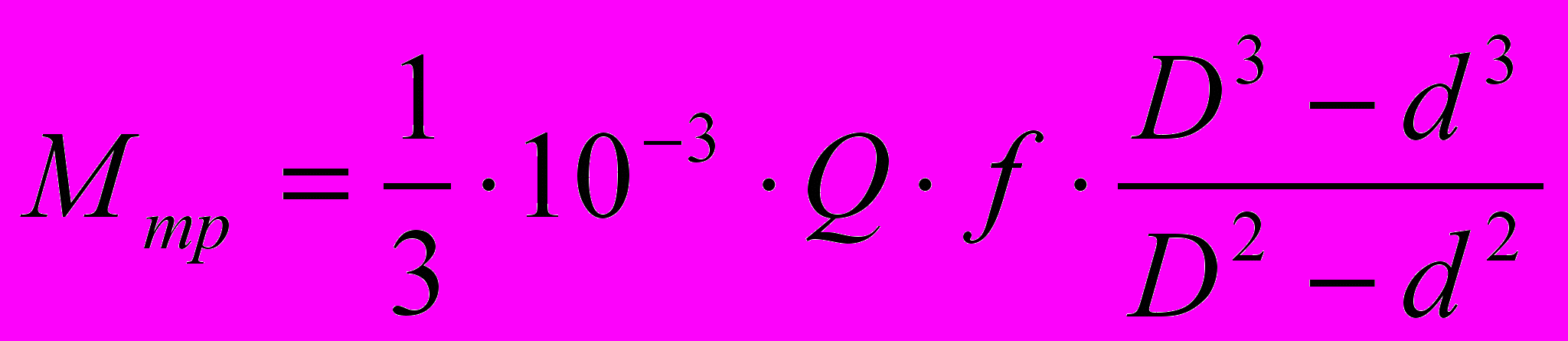
где D l,7d - наружный диаметр кольцеобразной поверхности в мм;
d - внутренний диаметр, равный диаметру резьбы, в мм;
f - коэффициент трения на торцевой поверхности, равный 0,15.
Для винтов с башмаком, предупреждающим повреждение поверхности заготовки, момент трения находится по формуле:
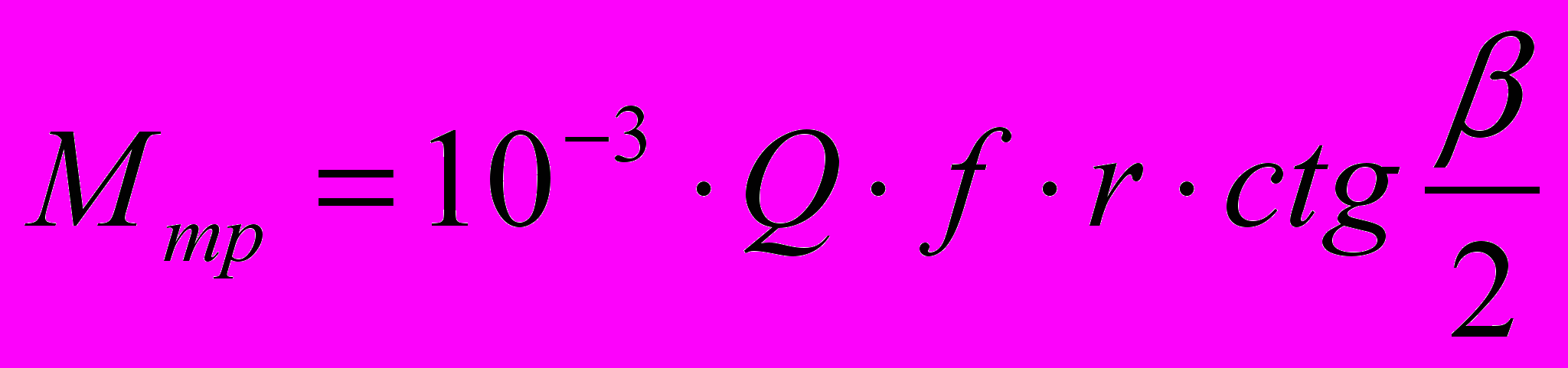
где r -радиус сферы винта в мм,
- угол конуса башмака.
Для винтов с плоским торцом, имеющим размер d1, момент трения находится по формуле:
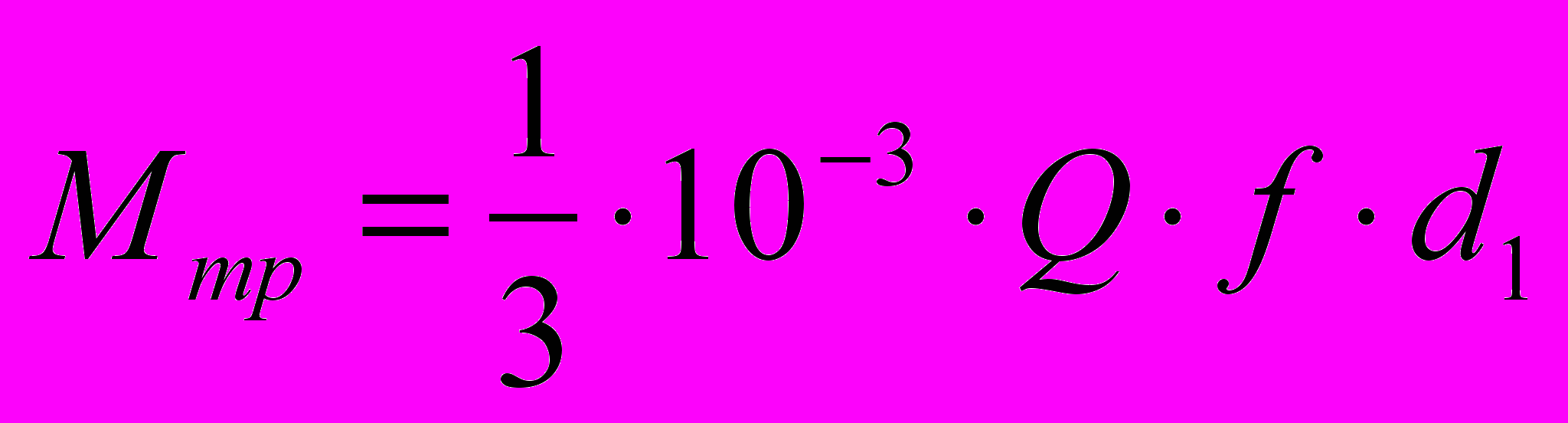
Таблица 3.1 – Допускаемые напряжения растяжения (сжатия) для винтовых зажимов [3]
Марка стали | Термообработка | Предел текучести, мПа. | Допускаемое напряжение [], мПа | |
При статической нагрузке | При переменной нагрузке | |||
10 | - | 200 | 60-20 | 30-40 |
Ст3 | - | 220 | 20-80 | 30-40 |
А12 | - | 240 | 80-90 | 40-50 |
35 | - | 300 | 100-110 | 50-60 |
45 | Отжиг | 300 | 100-120 | 50-60 |
45 | Нормализация | 350 | 120-140 | 60-20 |
45 | Улучшение | 500 | 150-120 | 70-80 |
45 | Закалка | 700 | 190-210 | 80-90 |
40Х | Отжиг | 500 | 140-160 | 70-80 |
40Х | Улучшение | 650 | 170-190 | 85-95 |
40Х | Закалка | 900 | 280-300 | 110-120 |
30ХН | - | 700 | 180-200 | 90-100 |
Для винтов со сферическим торцом момент трения мал (менее 3%) и им можно пренебречь.
В целях ускорения расчетов можно пользоваться приближенными зависимостями, в которых приняты некоторые средние значения параметров.
Для винтов со сферическим торцом М = 10 -4 Q d [Hм].
Для винтов с гайкой или звездочкой М = 2104 Q d [Hм].
Для винтов с плоским торцом (при d1 = 0,6d) M = 1,3 104 Qd[Hм].
Для винтов с башмаком ( = 118°, f = 0,16) М= 10-4 Q (d +r)[Нм]. Предельные моменты, создаваемые рукой рабочего при различных конструкциях приводного элемента, приведены в таблице 3.2 в зависимости от размера этого элемента.
Таблица 3.2 - Предельные моменты, получаемые при различных конструкциях привода винтовых зажимов [1]
Гайка с накат-кой (Z=D) | Барашек | Звездочка | Вороток | Рукоятка | |||||
Значения М приведены в Нм | |||||||||
Z, мм | М, Нм | Z, мм | М, Нм | Z, мм | М, Нм | Z, мм | М, Нм | Z, мм | М, Нм |
20 | 0,7-1,5 | 30 | 1,2-2,5 | 40 | 4,0-6,5 | 80 | 7,0-8,5 | 75 | 8,5-13 |
24 | 0,9-1,8 | 35 | 2,5-5,0 | 50 | 5,0-7,0 | 100 | 8,0-9,5 | 94 | 9,2-14 |
30 | 1,0-1,8 | 45 | 4,0-6,5 | 60 | 6,0-8,0 | 120 | 9,0-11 | 117 | 10-15 |
36 | 1,2-2,5 | 50 | 5,0-7,5 | 80 | 8,0-9,5 | 140 | 10-13 | 150 | 11-16 |
Пользуясь этой таблицей, можно обоснованно выбирать конструкцию головки по найденному значению момента привода.
При использовании других приводных элементов (гаечные ключи, маховики, штурвалы и т.д) величину момента привода можно определить по формуле:
Мтр =Рр Z 10-3 [Нм],
где Рр - усилие, создаваемое рабочим на рукоятке (Рр = 100-150 Н);
Z - плечо действия силы на рукоятке, мм.
Если размеры приводных элементов получаются слишком большие, а сами устройства становится громоздкими, то необходимо отказаться от зажима вручную пли пересмотреть схему закрепления заготовки.
Величину усилий, создаваемых винтовыми зажимами с метрической резьбой, (по СТ СЭВ 182 - 75) при допускаемом напряжении 10 мПа, приведены в таблице 3.3.
Таблица 3.3 – Допускаемые силы, создаваемые винтовыми зажимами с метрической резьбой (по СТ СЭВ 182-75)[3]
Резьба | М6 | М8 | М10 | М12 | М14 | М16 | М18 |
Шаг | 1 | 1,25 | 1,5 | 1,75 | 2 | 2 | 2,5 |
Допуск.сила,Н | 1800 | 3200 | 5000 | 7200 | 9800 | 12000 | 16200 |
Резьба | М20 | М22 | М24 | М27 | М30 | М33 | М36 |
Шаг | 2,5 | 2,5 | 3 | 3 | 3,5 | 3,5 | 4 |
Допуск.сила,Н | 20000 | 24200 | 28800 | 36450 | 45000 | 55550 | 64800 |