Методические указания рассмотрены и утверждены на заседании кафедры Технологии машиностроения
Вид материала | Методические указания |
- Методические указания для проведения лабораторных занятий по дисциплине «Автоматизация, 598.59kb.
- Методические указания по дипломному проектированию для студентов всех форм обучения, 838.63kb.
- Методические указания по лабораторным работам По дисциплине, 929.67kb.
- Методические указания по лабораторным работам По дисциплине, 803.46kb.
- Методические указания по практическим занятиям По дисциплине, 519.54kb.
- Методические указания по лабораторным занятиям По дисциплине, 487.31kb.
- Методические указания по лабораторным занятиям По дисциплине, 531.16kb.
- Методические указания к выполнению курсовой работы По дисциплине, 218.3kb.
- Методические указания к выполнению курсовой работы По дисциплине, 255.91kb.
- Методические указания по выполнению курсовых работ, 297.99kb.
Примечание: при К.П.Д. равном 1,0.
4.2. Гидравлические и пневмогидравлические приводы
Схемы гидравлических приводов и расчетные формулы для определения усилия на штоке приведены в таблице 4.2.1. В этих формулах приняты следующие обозначения:
Рш, Pш1 - усилие на штоке в Н,
D, Dж - диаметр гидроцилиндра в м,
Dв - диаметр пневмоцилиндра в м,
Р, Рж - удельное давление жидкости в мПа,
Рв - удельное давление воздуха в мПа,
d, d1 - диаметр штока гидроцилиндра в м,
d2 - диаметр штока пневмоцилиндра в м,
N - сопротивление пружины возврата в Н,
- общий К.П.Д. системы.
Замечания, сделанные для расчета пневматических приводов см.4.1, справедливы для гидравлических и пневмогидравлических приводов.
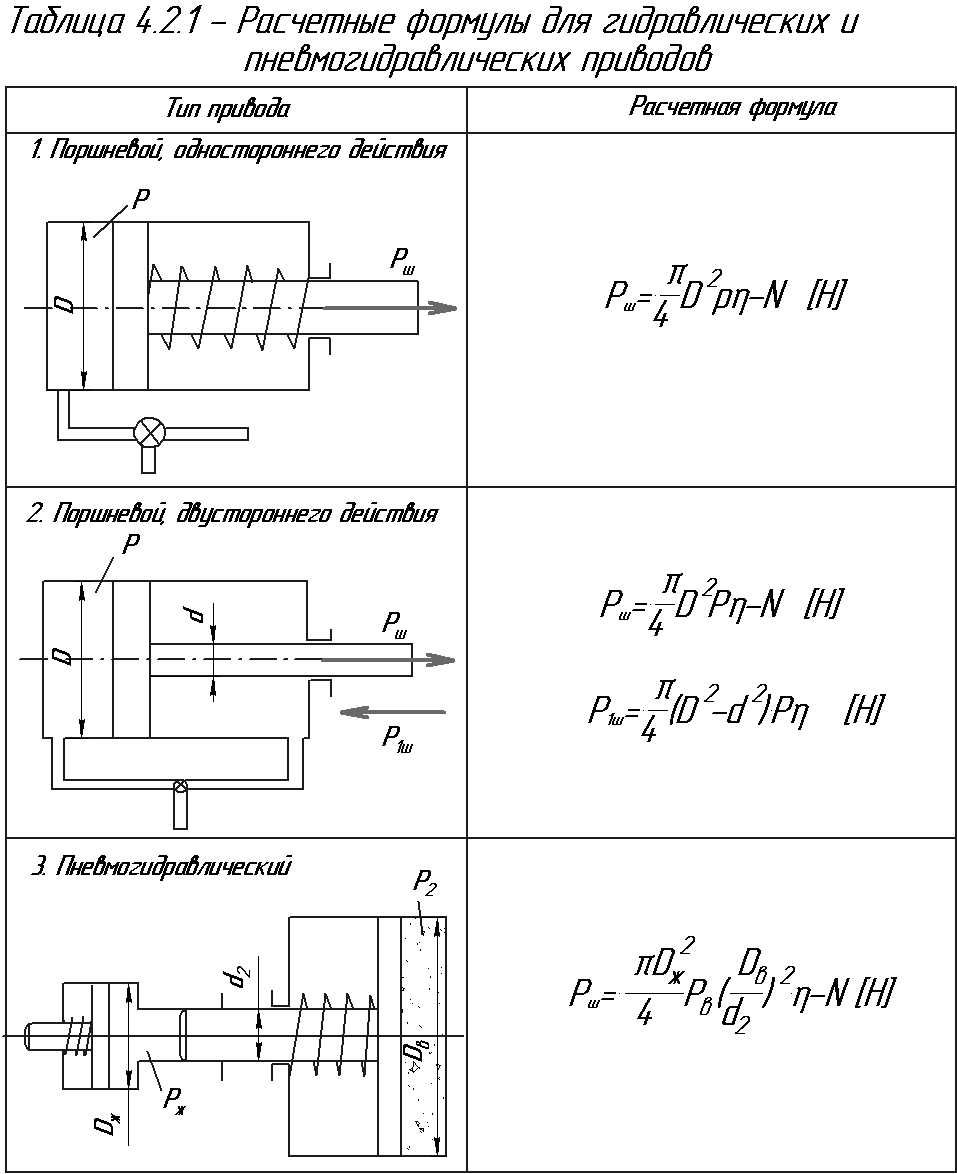
4.3 Электромагнитные приводы
Расчет электромагнитных устройств ведется по схеме на рисунке 4.3.1.
При расчете учитываются геометрические размеры и электротехнические формулы. Более подробно вопросы теории, расчета и области применения электромагнитных и магнитных устройств приспособлений см. в монографии [6].
Участки магнитопровода являются:
l1, l2, l12 - обрабатываемая заготовка,
l3, 111 - зазор между заготовкой и магнитной плитой,
l4, l10 - высота сердечников плиты,
l6, l7, l8 - соединительные планки,
15, 19 - зазоры между соединительной планкой и сердечниками.
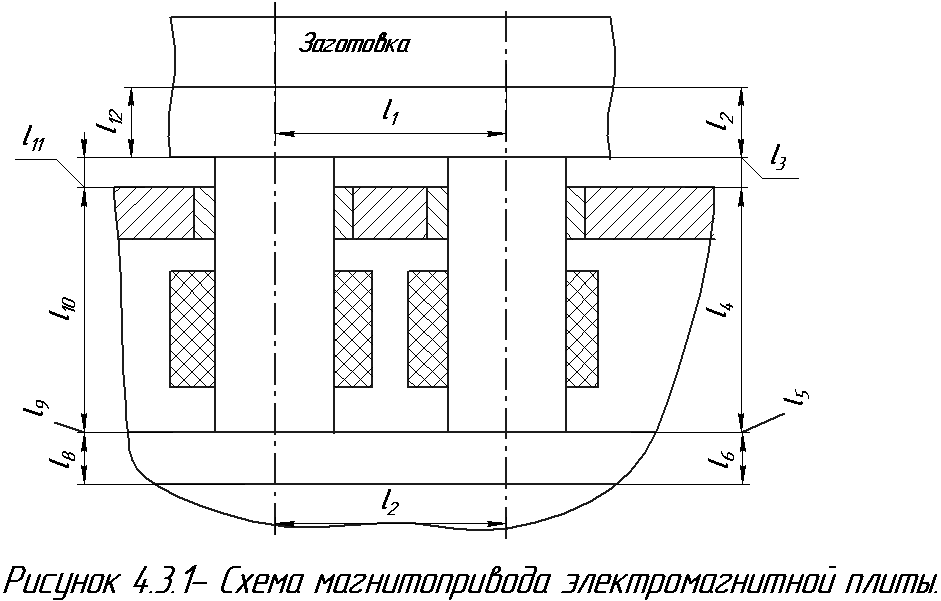
Расчет производится в следующей последовательности:
1. Определяется необходимая удерживающая сила Q по формуле:
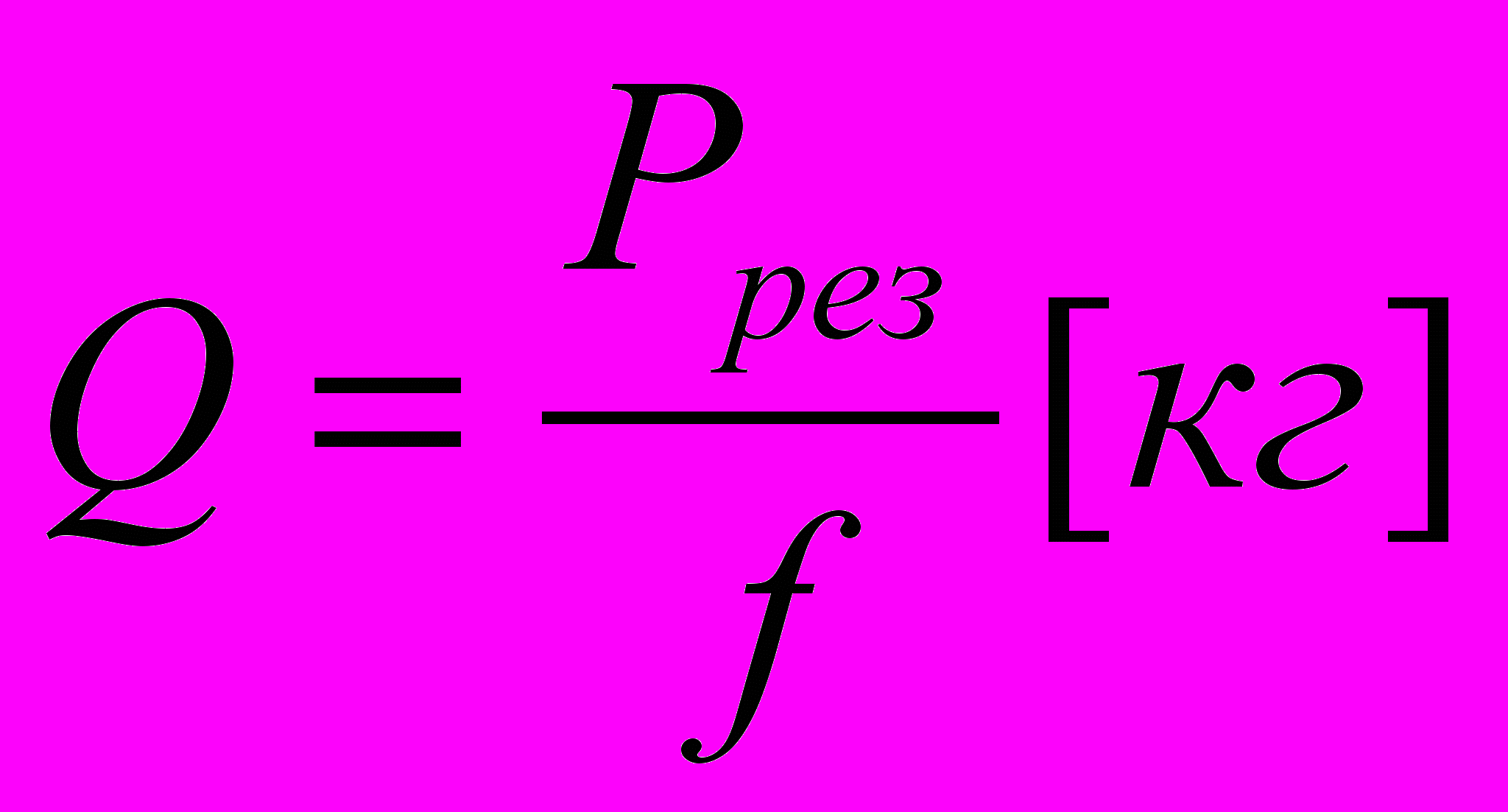
где Ррез - усилие резания, вызывающее сдвиг заготовки в кг (при шлифовании - окружная сила),
f- коэффициент трения между заготовкой и плитой, равный 0,1-0,15.
- Определяется (либо выбирается) число пар полюсов, перекрываемых заготовкой, исходя из ее размеров и конфигурации.
- Определяется удерживающая сила, создаваемая одним полюсом в магнитной системе:
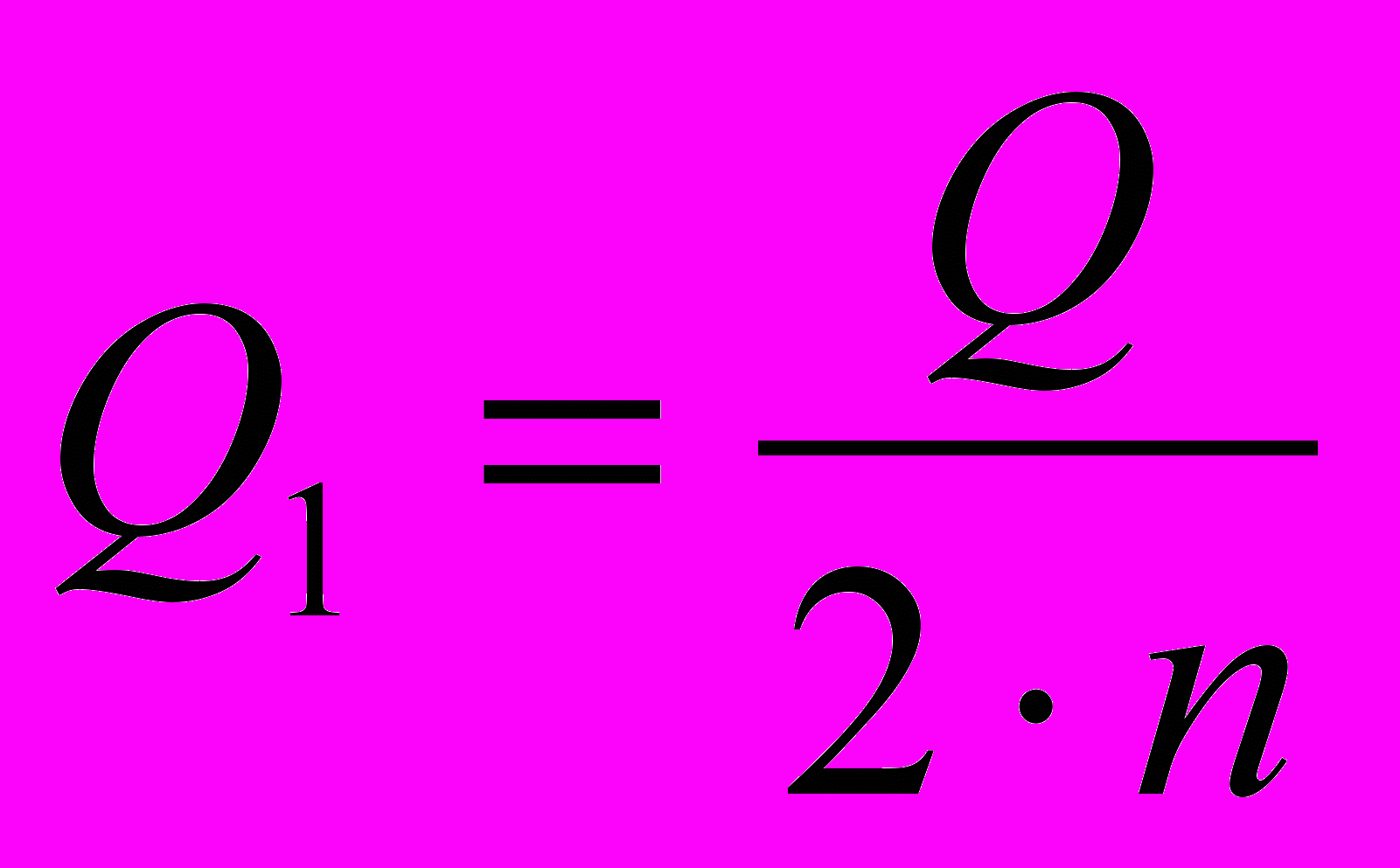
где n - число пар полюсов
- Подсчитывается площадь поперечного сечения сердечника по формуле:
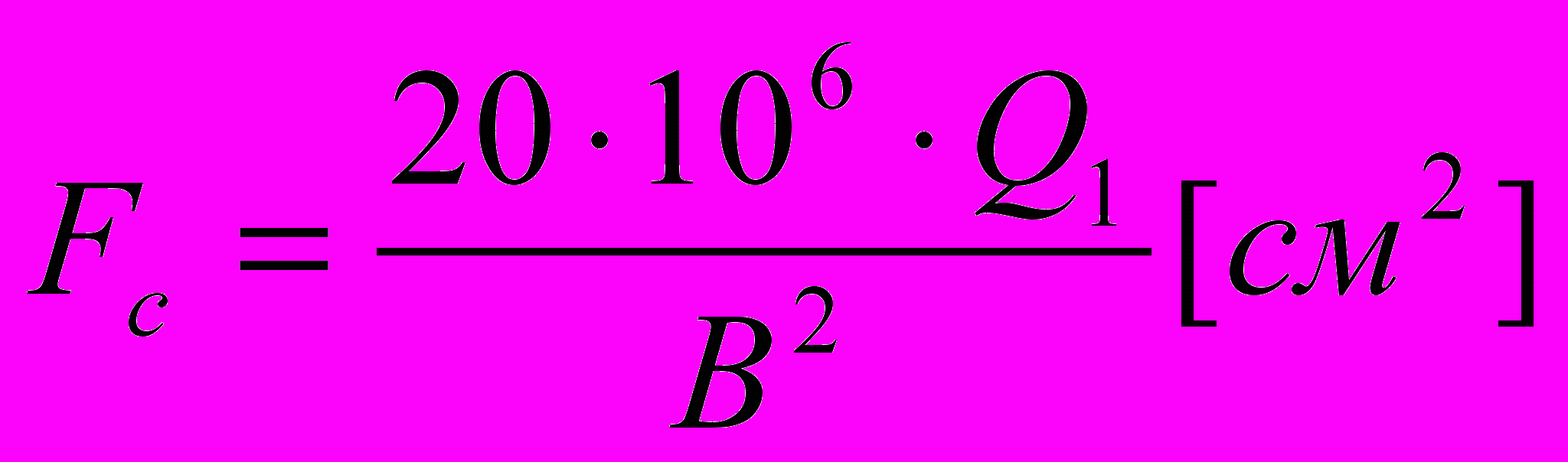
где В - магнитная индукция для материала, из которого изготовлен сердечник - [rс] [5, табл. 124].
5. Определяется общее сопротивление магнитопровода по формуле:
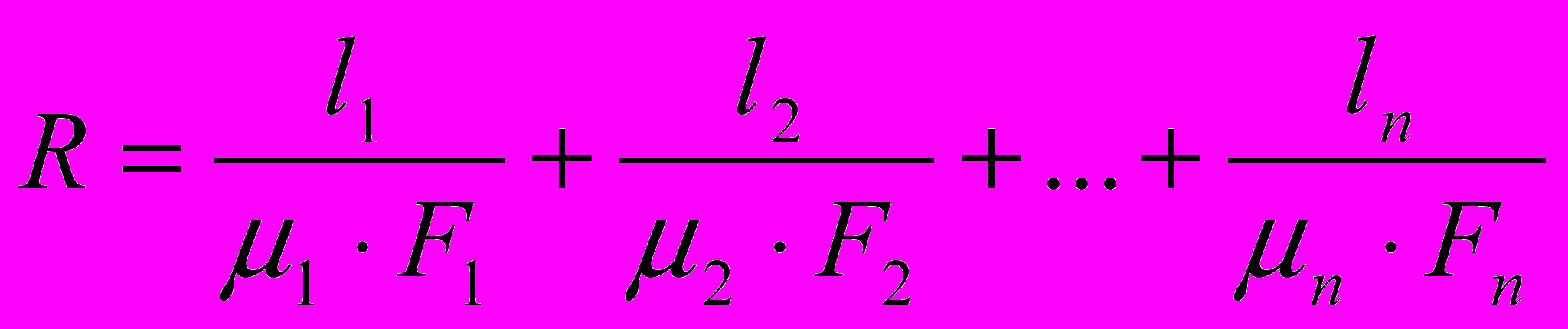
где l1, l2, ln - длина каждого участка магнитопровода в см,
1, 2, 3 - магнитная проницаемость материала каждого участка [5, табл. 124].
F1, F2, F3 - площадь поперечного сечения каждого участка в см2.
6. Определяется общий магнитный поток с учетом 30% потерь
Ф=0,7BFc
7. Рассчитывается количество ампервитков катушки
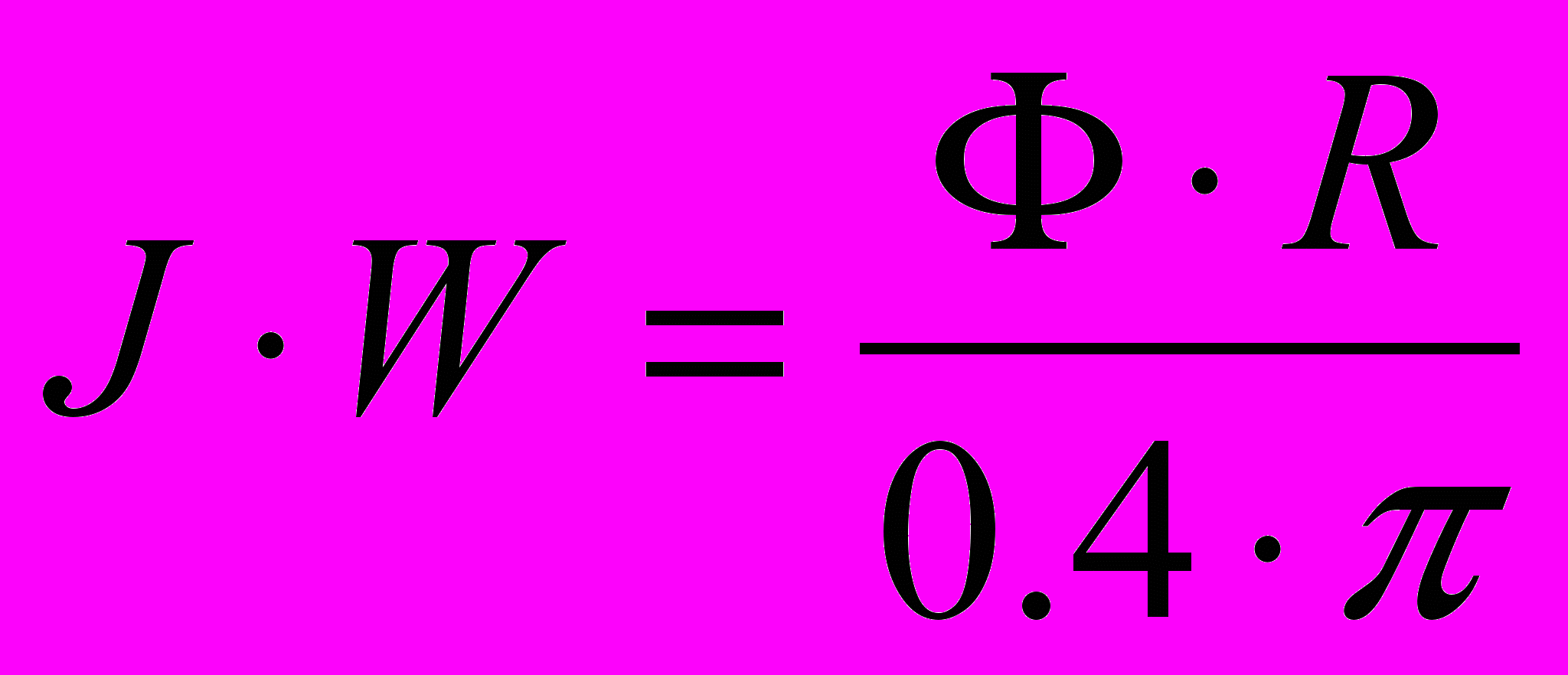
J - сила тока в А,
W - количество витков катушки.
8. Определяется диаметр провода катушки
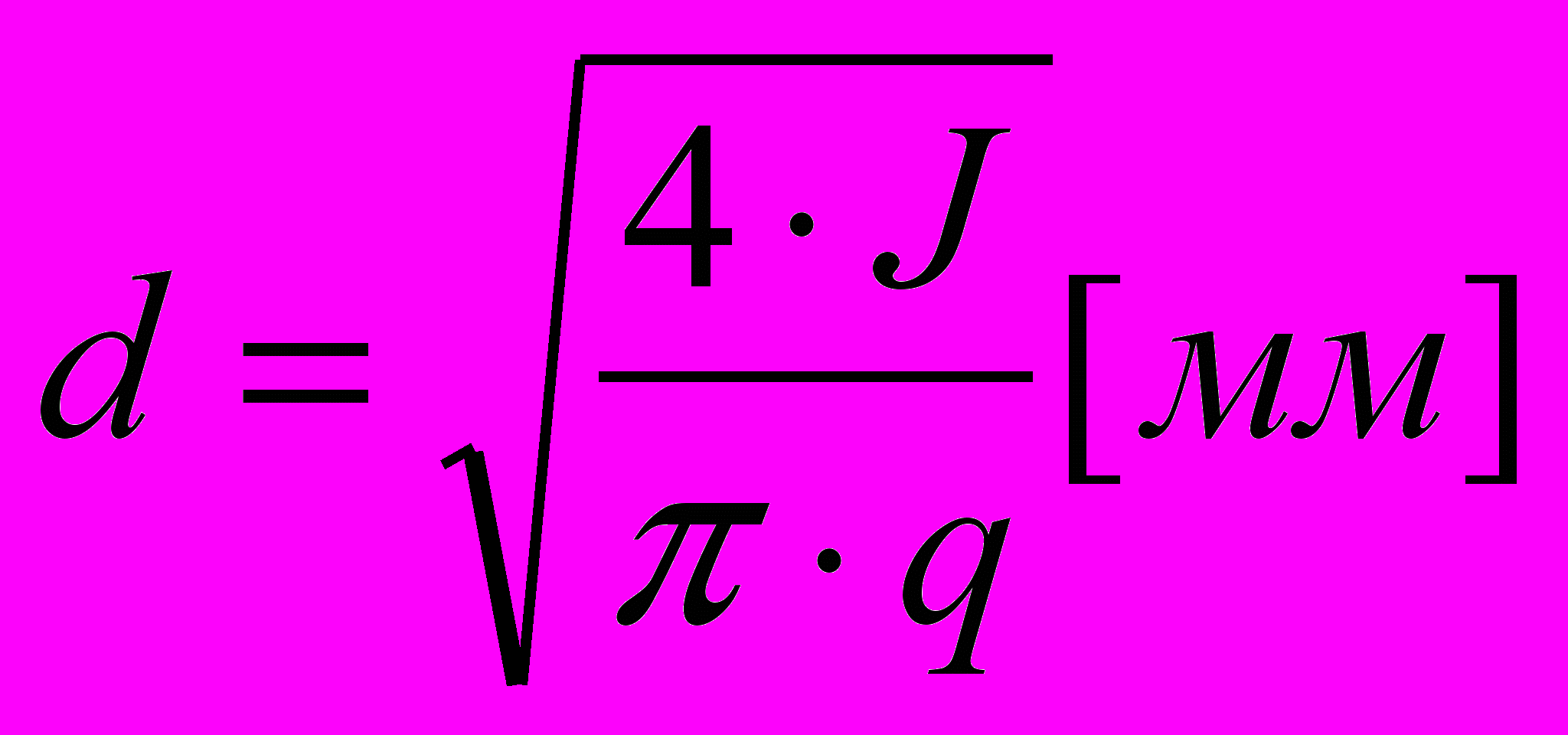
где q - допустимая плотность тока, равная 3-5 А/мм2.
9. После этого производится проверка катушки на нагрев по величине поверхности ее охлаждения, которая приходится на один ватт мощности.
Для стандартных магнитных плит, используемых на плоскошлифовальных станках, производится поверочный расчет, не основании которого решается вопрос о возможности вести обработку заготовок при заданных режимах резания. Если усилия магнитной плиты недостаточны, то уменьшают режимы резания.
- Электромоторные приводы
Одна из схем электромоторного привода показана на рисунке 4.4.1.
Величина усилия, создаваемого тягой электромоторного привода определяется в зависимости от характера используемого приспособления (трехкулачковый патрон, фрезерное, сверлильное и т.п.).
Поэтому при расчете необходимо знать и учитывать влияние конструкции, передающей усилие от привода к обрабатываемой заготовке.
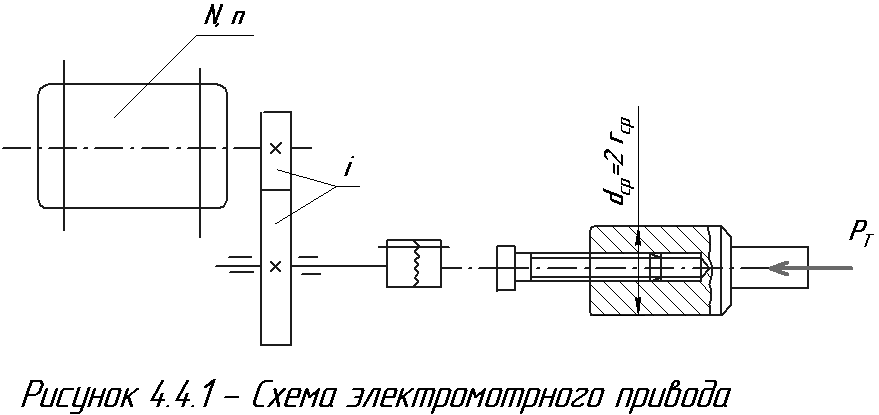
Усилие тяги для указанных выше схем определяется по формуле:
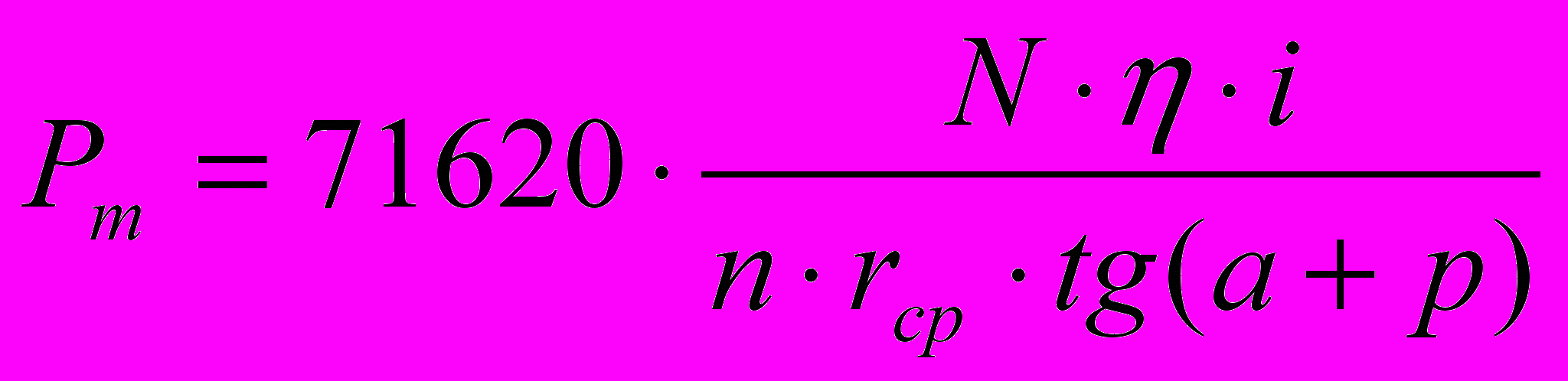
N - мощность электродвигателя в л.с,
n - частота вращения двигателя в мин,
rср - средний радиус резьбы в см,
а - угол подъема в градусах,
- угол трения в резьбе в градусах,
i - передаточное отношение редуктора,
- К.П.Д. редуктора.
Более подробно расчеты для других схем и конструктивных решений электромоторных приводов изложены в монографии [7].
При проектных расчетах по известной величине усилия, которое должно быть создано тягой электромоторного устройства определяется по приведенной выше формуле мощность электромотора. По величине мощности и принятому числу оборотов подбирают электромотор по каталогу электродвигателей переменного тока.
Примеры расчета зажимных усилий и приводов приспособлений.
Пример 1.
Определить потребное зажимное усилие при предварительном обтачивании стальной заготовки до диаметра 50 мм с глубиной резания 3 мм, S = 0,5 мм/об из стали 45 при ее закреплении в трехкулачковом патроне. Заготовка - горячекатаный прокат 60 мм. Проверить достаточность зажима в стандартном трехкулачковом патроне.
Решение
По нормативам определяем усилия резания (Pz и Рх) для заданных в примере условий. Резец проходной, с пластинкой твердого сплава Т15К6, угол =45°; 1=30°; r = 2,0 мм.
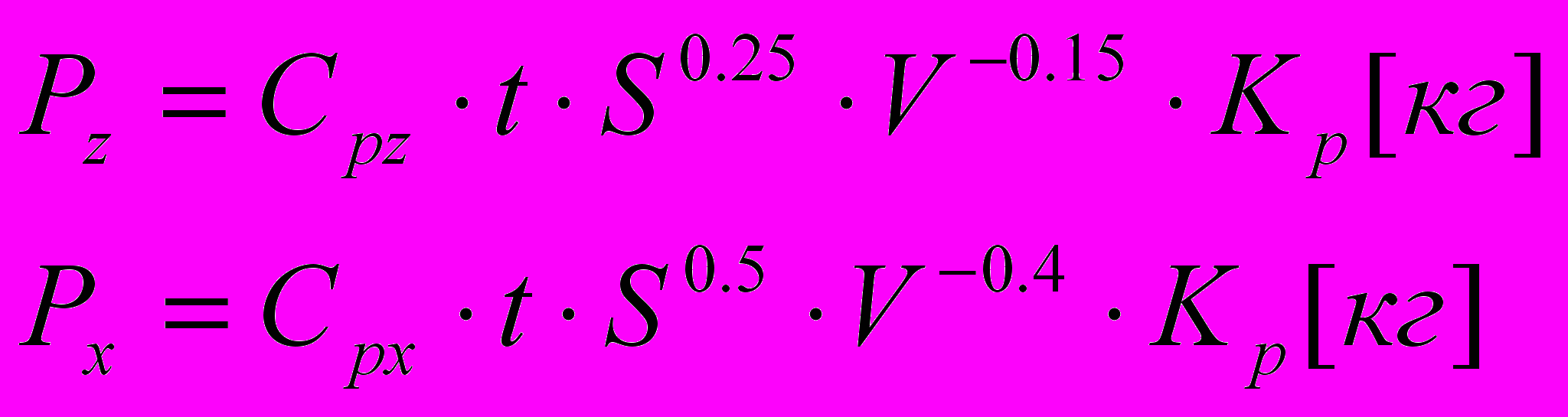
Подставляем данные из таблицы 20 получим:
Рz = 300 3 0,50.25 100-0.15 1 = 270 кг Рх = 111 кг
Учитывая, что поверхность горячекатаного проката груба, а кулачки патрона имеют насечку, примем коэффициент трения по цилиндрической поверхности f1=0,25.
Определим коэффициент запаса по формуле
К = К0∙К1∙К2∙К3∙К4∙К5∙
В соответствии с рекомендациями к этой формуле, с учетом заданных условий обработки, будем иметь следующие значения частных коэффициентов:
К0 = 1,5 К1 = 1,2 (черновая обработка)
К2 = 1,0 (для составляющей Pz, см. таблицу 2.4.)
К2 = 1,6 (для составляющей Рх, см. таблицу 2.4.)
К3 = 1,0 (непрерывная обработка)
К4 = 1,4 (закрепление вручную)
K5 = 1,0 (удобное положение)
Тогда получим:
Для Рz – К= 1,51,21,01,01,31,0 = 2,34
Для Рx – К= 1,51,21,61,01,31,0 = 3,64
Предполагая, что 3Qf1> Рх определим силу зажима по формуле 1а, таблицы 2.2 т.е.
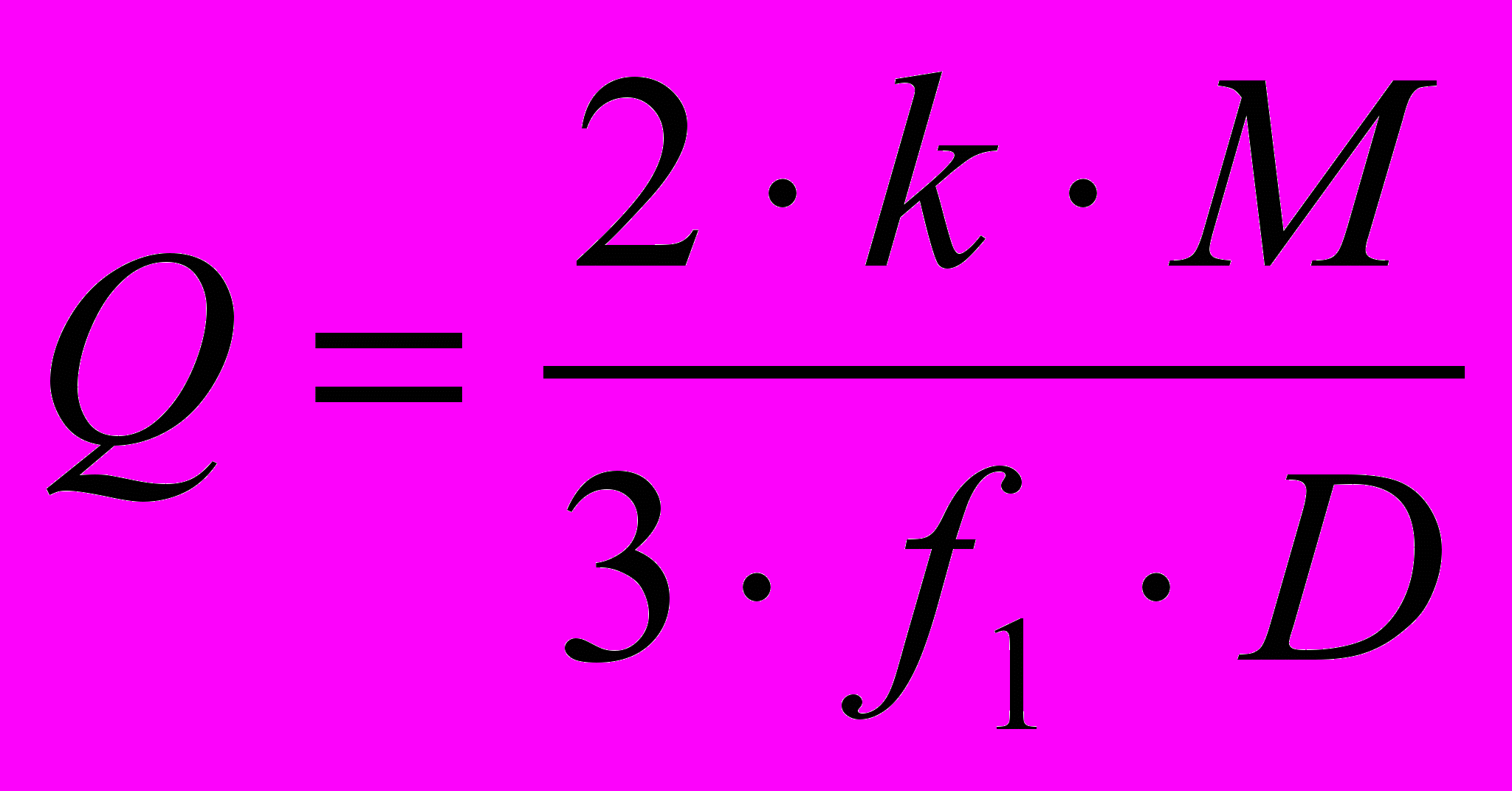
т.к.
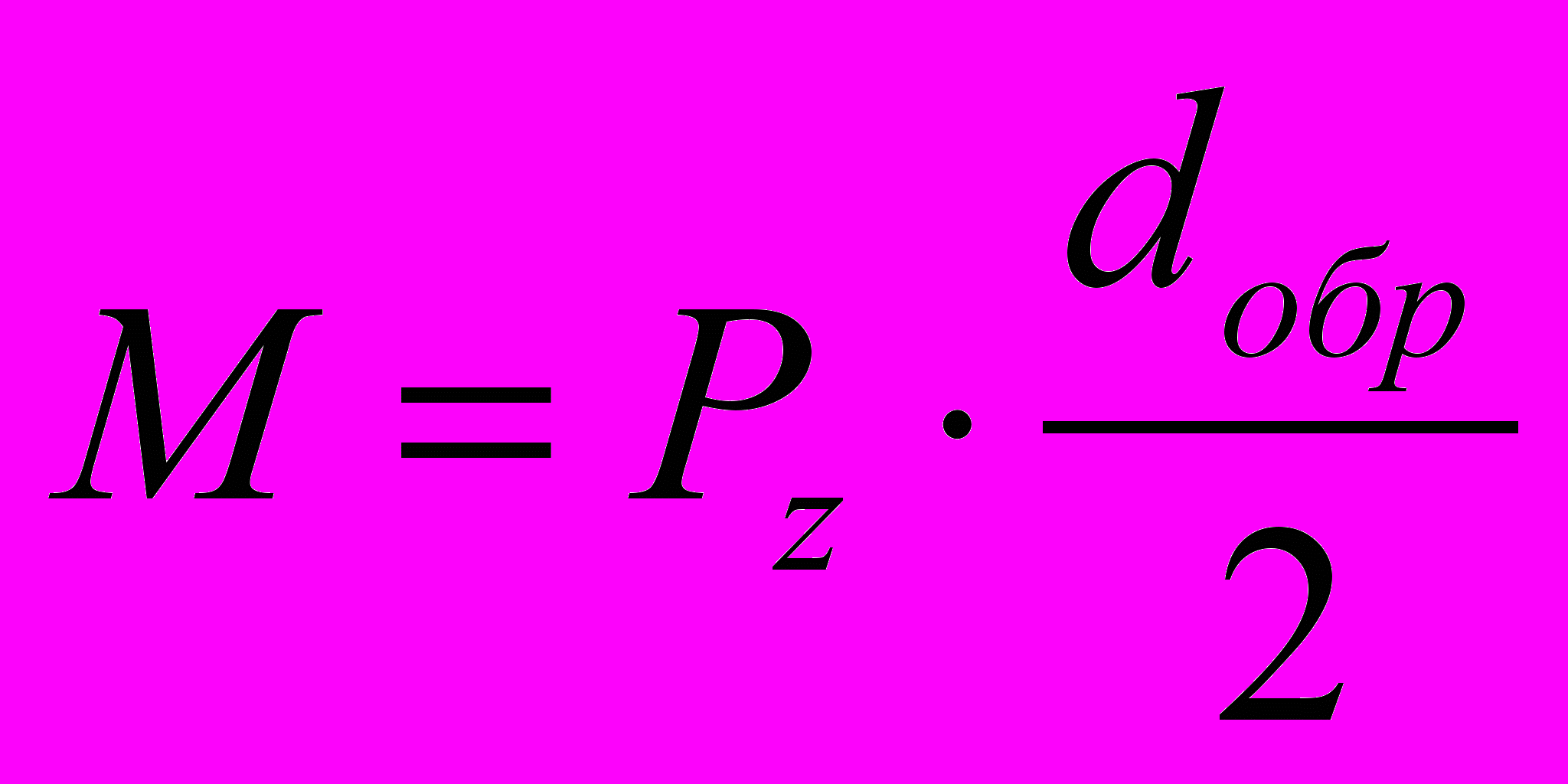

Проверим, выполняется ли сделанное допущение о не смещении заготовки вдоль оси под действием Рх
32,80 PZ > PX 2,0 PZ > PX
Отсюда следует, что, хотя Рх может, за счет затупления инструмента, возрасти в 1,6 раза, a PZ > PX, то условие выполняется.
Таким образом, потребное зажимное усилие Q = 745 кг = 7450 [Н]. Общее усилие, создаваемое тремя кулачками патрона, составит 2240 кг или 22400 Н
Сравним полученные расчетом потребные усилия с усилиями, создаваемыми универсальным спирально-реечным патроном с ключевым зажимом мод. ТС-25. Для этого воспользуемся примером расчета в книге Ансерова М.А. «Приспособления для металлорежущих станков» - М.: Машиностроение, 1964 стр.134-140.
Для патрона модели ТС-25 при усилии на рукоятке ключа патрона 25 кг и длине рукоятки 250 мм может быть создано общее усилие 2420 кг. Так как это усилие больше расчетного, то возможно надежное закрепление заготовки вручную. Однако следует заметить, что при дальнейшем увеличении глубины резания будут возрастать усилия резания, и надежность закрепления будет падать, либо потребуется прилагать на рукоятке более 25 кг.
Пример 2.
Определить зажимное усилие при фрезеровании торцов штампованного валика из стали 45 фрезами, оснащенными твердым сплавом Т15К6. Диаметр наибольшего фрезеруемого торца d=100 мм, величина припуска на обработку 3 мм, штамповочные уклоны по наружным поверхностям 3°, подача на зуб фрезы Sz = 0,1 мм/зуб. Закрепление валика ведется в двух парах сходящихся призм ножевого типа с углом а=90°, привод призм производится через ходовой винт с трапециидальной резьбой d = 30 мм, t = 3 мм. Найти приводной момент на винте и выбрать вид привода (вручную или электроключом).
Решение
Величина момента сил резания будет изменяться в зависимости от глубины резания и ширины фрезерования. Наибольший момент в фрезе будет возникать, когда будет наибольшая ширина равная диаметру обрабатываемой заготовки. Момент, передаваемый заготовке, будет зависеть от величины силы Рz и плеча действия этой силы по отношению к оси вала.
Приближенно наибольший момент сил резания, действующий на заготовку, можно принять равным (Pz)maxD/4.
Учитывая, что нагружение вала ведется с двух сторон и закрепление также ведется двумя парами призм, расчет можно вести для одной пары призм и для одного момента сил резания. При этом условии расчетная формула для определения силы зажима будет иметь вид:
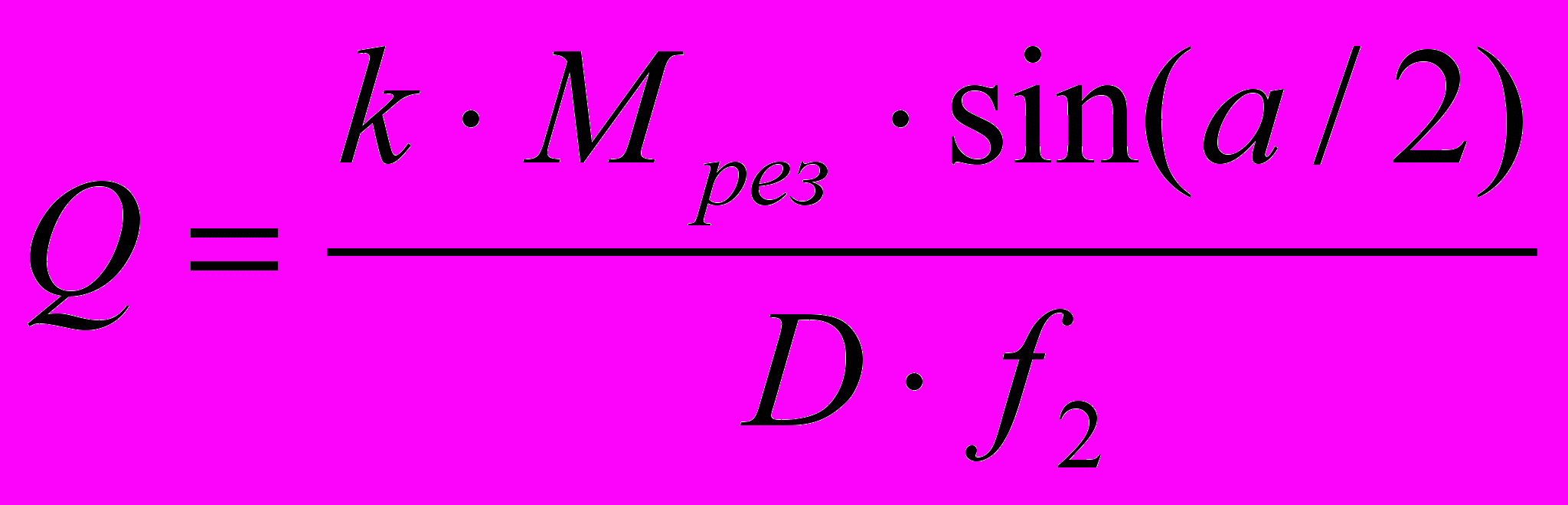
Подставляя значение величины в расчетную формулу, получим:

D=100мм, f2 = 0,2 (черновая базовая поверхность), а = 90°,
К = 1,51,21,81,21,31,0 = 5,15.
Момент привода винта для создания силы Q будет равен удвоенному моменту в резьбе и определяется по формуле:
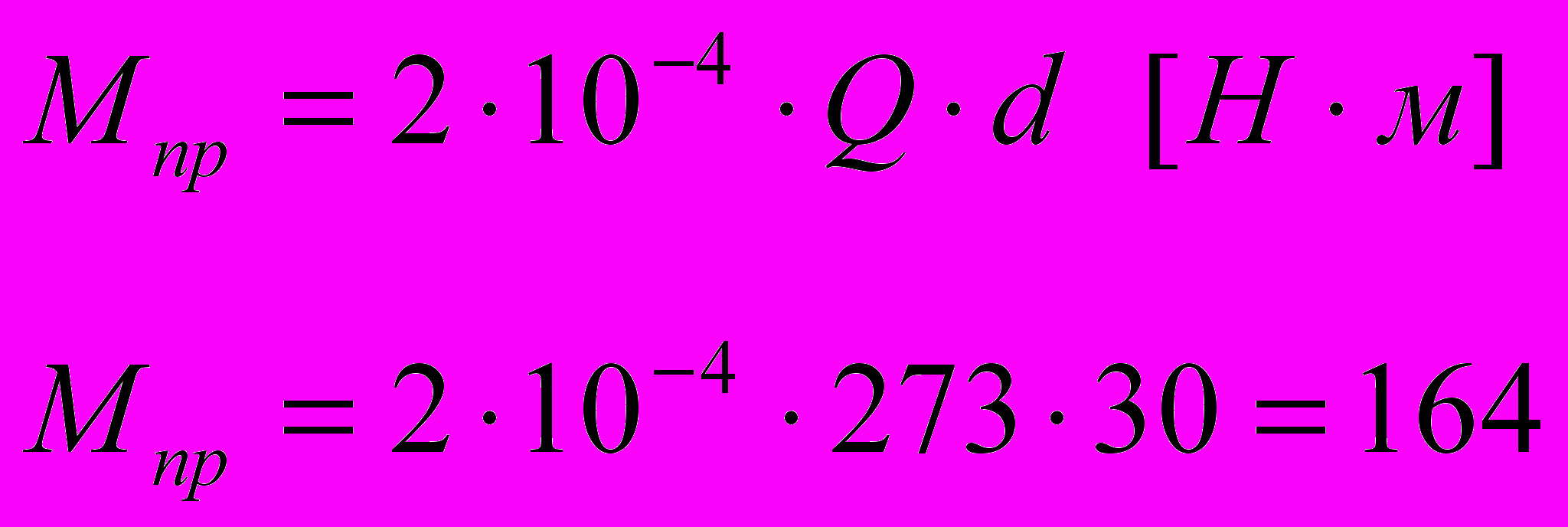
По величине момента привода может быть решен вопрос о характере привода (вручную или механизированный). Для этого, приняв усилие на рукоятке Р=150Н, определим длину рукоятки по формуле:
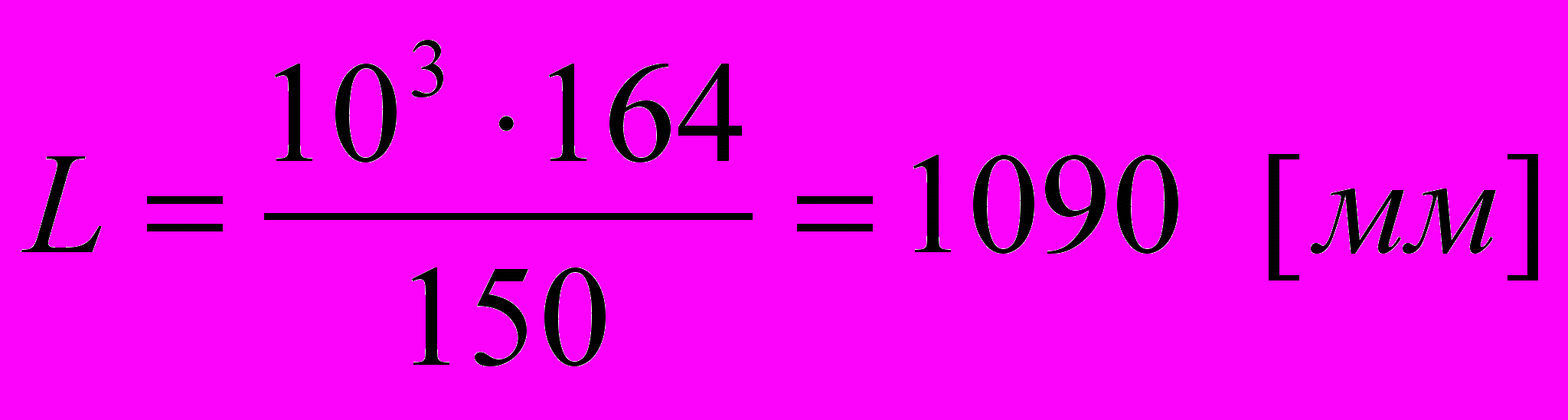
Так как рычаг получается очень большим, то привод зажимного устройства вручную нецелесообразен. Поэтому может быть применен электромеханический привод в виде торсионного ключа.
Подбор типоразмера такого ключа ведем по книге В.П. Вейц, Л.И. Фридман - Электромеханические зажимные устройства станков и станочных линий. - Л.: Машиностроение, 1973-262с.
По таблице 12, стр. 158 указанного выше источника можно использовать для создания расчетного момента зажима заготовки торсионный электромеханический ключ (ЭМК) типа 2У2241- 13 или 2У2241 -14.
В связи с тем, по ЭМК 2У2241 - 14 имеет дополнительный запас крутящего момента за счет регулировки реле максимального тока, принимаем последний в качестве привода зажимного устройства.
Таким образом, для заданных условий примера, зажим будем производить ЭМК 2У2241 - 14.
Библиографический список
- Корсоков B.C. Основы конструирования приспособлений в машиностроении/ B.C. Корсоков.- М.:Машиностроение, 1971.-288с.
- Горошкин А.К. Приспособления для металлорежущих станков. Справочник, изд. 6-е/А.К. Горошкин. - М.: Машиностроение, 1971.- 384с.
- Справочник конструктора по расчету и проектированию станочных приспособлений/В.Е. Антонюк и др.- Минск: Беларусь, 1969.- 392с.
- Дальский A.M. Цанговые зажимные механизмы/A.M. Дальский. - М.: Машиностроение, 1966.-342с.
- Антонюк В.Е. В помощь молодому конструктору приспособлений/ В.Е. Антонюк. - Минск: Беларусь, 1975.-350с.
- Константинов О.Я. Магнитная технологическая оснастка/О.Я. Константинов. - Л.: Машиностроение, 1974.- 284с.
7. Вейц В.Л. Электромеханические зажимные устройства станков и станочных приспособлений/В.Л. Вейц, Л.И. Фридман. - Л.: Машиностроение, 1973. - 264с.
Список рекомендательной литературы по приспособлениям.
1. Абакумов М.М. Современные станочные приспособления/М.М. Абакумов. - М.: Машгиз, 1960. -327с.
- Ансеров М. А. Приспособления для токарных станков/М. А. Ансеров. - Л.: Машгиз, 1957. -125с.
- Ансеров М.А. Приспособления для металлорежущих станков/М.А. Ансеров. - Л.: Машиностроение, 1975. - 654с, ил.
- Баранов А.И. Стандартизация и нормализация в машиностроении/ А.И. Баранов, В.В. Кузьмин. - М.: Машгиз, 1963. -315с, ил.
- Белоусов А П. Проектирование станочных приспособлений/А.П. Белоусов. - М.: Высшая школа, 1980. - 240с, ил.
- Болотин Х.Л. Станочные приспособления/Х.Л. Болотин, Ф.П. Кострамин. - М.: Машиностроение, 1973. - 344с, с черт.
- Болотин Х.Л. Механизация и автоматизация станочных приспособлений/Х.Л. Болотин. - М.: Машгиз, 1962 - 187с, ил.
- Нормализированные станочные приспособления/В.И. Влазнев и др. - М: Оборонгиз,1963. - 280с.
- Волосатов В.А. Элементы пневмопривода/В.А. Волосатов. - Л.: Лениздат, 1975. - 135с, с черт.
- Контрольные приспособления/Б.А Гипп. и др. - М.: Машгиз, 1960.-240с.
11. Зависляк Н.И. Современные приспособления к металлорежущим станкам - 2-е изд. доп. и переработ./Н.И. Зависляк. - Л.. Машиностроение, 1967 - 259с, с черт.