Учебное пособие для студентов нефтехимических колледжей и техникумов Специальность 1701 "Монтаж и техническая эксплуатация промышленного оборудования (по отраслям)"
Вид материала | Учебное пособие |
- Учебное пособие для студентов среднего профессионального образования Специальность, 3369.62kb.
- Программа и контрольные задания для студентов заочного отделения Специальность: 1701, 688.94kb.
- Методические указания и контрольные задания для студентов заочной формы обучения гоу, 2389.4kb.
- Методические указания и контрольные задания для студентов заочного отделения специальность:, 848.08kb.
- Федеральный государственный образовательный стандарт среднего профессионального образования, 1074.58kb.
- Государственный образовательный стандарт среднего профессионального образования государственные, 1346.06kb.
- «Материаловедение», 179.95kb.
- Формирование профессионально-значимых качеств личности в условиях личностно-ориентированного, 51.94kb.
- «Монтаж и техническая эксплуатация промышленного оборудования (в пищевой промышленности)», 1138.79kb.
- Курс 150411 «Монтаж и техническая эксплуатация промышленного оборудования», 58.89kb.
В зависимости от расположения шва на свариваемом изделии различают швы нижние (обыкновенные), верхние (потолочные), горизонтальные и вертикальные. Наиболее труден процесс сварки потолочных швов.
17.1 Классификация способов сварки
Одним из признаков классификации способов сварки является применение давления для сжатия деталей в процессе сварки. Сварка может осуществляться:
- без приложения давления, путем расплавления металла свариваемых частей и слияния его; после затвердевания образуется шов (сварка плавлением);
- с применением давления, способствующего плотному контакту и взаимной диффузии металла в месте соприкосновения свариваемых частей (сварка давлением).
Сварка плавлением применяется шире вследствие меньшей стоимости, простоты оборудования и универсальности.
По виду используемой для сварки энергии сварка подразделяется на химическую, при которой для нагревания используется тепло химической реакции (например, горение твердого или газообразного топлива); к ней относятся газовая, кузнечная и термитная сварка; электрическую, при которой для нагревания используется электрический ток (электродуговая, электрошлаковая, электроконтактная); механическую (сварка трением, холодная сварка); ультразвуковую; сварку электронным лучом, а также диффузионную сварку в вакууме. Наиболее распространенными являются электродуговая, электрошлаковая, электроконтактная и газовая сварка.
Кузнечная сварка применяется для низкоуглеродистых сталей. Она осуществляется при температуре, близкой к точке плавления стали (1350-14500С), при проковке наложенных свариваемых концов. Этот старинный способ сварки трудоемкой и малопроизводительный, поэтому применяется редко.
Термитная сварка производится при помощи порошковой смеси одной части алюминия с тремя-четырьмя частями окиси железа. Термит легко зажигается и при бурном горении достигается температура 30000С. Наплавленным железом заполняют стыки соединений. Этот способ удобен для сварки рельсов и др.
Сварка трением применяется для соединения стержней встык. В сварочной машине один стержень закрепляется неподвижно, другой вращается, касаясь торцом неподвижного. От трения температура повышается. По достижении пластического состояния вращение прекращают, стержни сдавливают, и они свариваются. Сваркой трением соединяют однородные и разнородные металлы.
Холодная сварка производится без подогрева, но при больших удельных давлениях. Она применяется для меди, алюминия, свинца, никеля, серебра и их сплавов. Холодная сварка делится на стыковую, точечную и шовную.
Ультразвуковая сварка основана на преобразовании ультразвуковых колебаний в механические, что приводит к пластической деформации поверхностей свариваемых деталей и срастанию кристаллов. Этот способ применяется для соединений металлов внахлестку, а также для сварки пластмасс.
Сварка электронным лучом производится путем помещения в вакуумную камеру изделий из тугоплавких металлов (вольфрама, молибдена и др.). На место, подлежащее сварке, направляют фокусированный электронный луч, под действием которого металл расплавляется и сваривается.
17.2 Электрическая сварка
Электрическая сварка металлов – русское изобретение.
Русский ученый Василий Владимирович Петров в 1802 г. открыл явление электрической дуги и показал возможность плавления металлов в дуге. В 1882г. русский инженер Николай Николаевич Бенардос предложил применить электрическую дугу для сварки металлов угольным электродом, а в 1888г. горный инженер Николай Гаврилович Славянов заменил графитовый электрод металлическим.
Электросварка подразделяется на дуговую и контактную. При дуговой сварке энергия, необходимая для нагрева и расплавления металла, выделяется электрической дугой. Сварочная дуга питается постоянным током от сварочных машин-генераторов и переменным током от сварочных трансформаторов. Дуговая сварка может быть ручной и автоматической. Автоматическая обеспечивает получение высококачественного шва и резко увеличивает производительность труда.
При электродуговой сварке электрический ток по одному проводу подводится к свариваемому металлу, а по другому – к электродержателю, в котором зажат электрод. При приближении электрода к металлу между ними образуется электрическая дуга, расплавляющая металл.
При сварке листов 1 (рис.17.2) металлическим электродом 3 по способу Н.Г.Славянова электрод сам плавится в сварочной дуге 2 и образует жидкий металл, заполняющий промежутки между свариваемыми частями. Для повышения качества направляемого металла электрод покрывается специальной обмазкой, которая также расплавляется и покрывает капли жидкого металла слоем шлака, защищая его от вредного влияния кислорода и азота окружающего воздуха. Ток к электроду подводится через электрододержатель 4 по проводу 5.
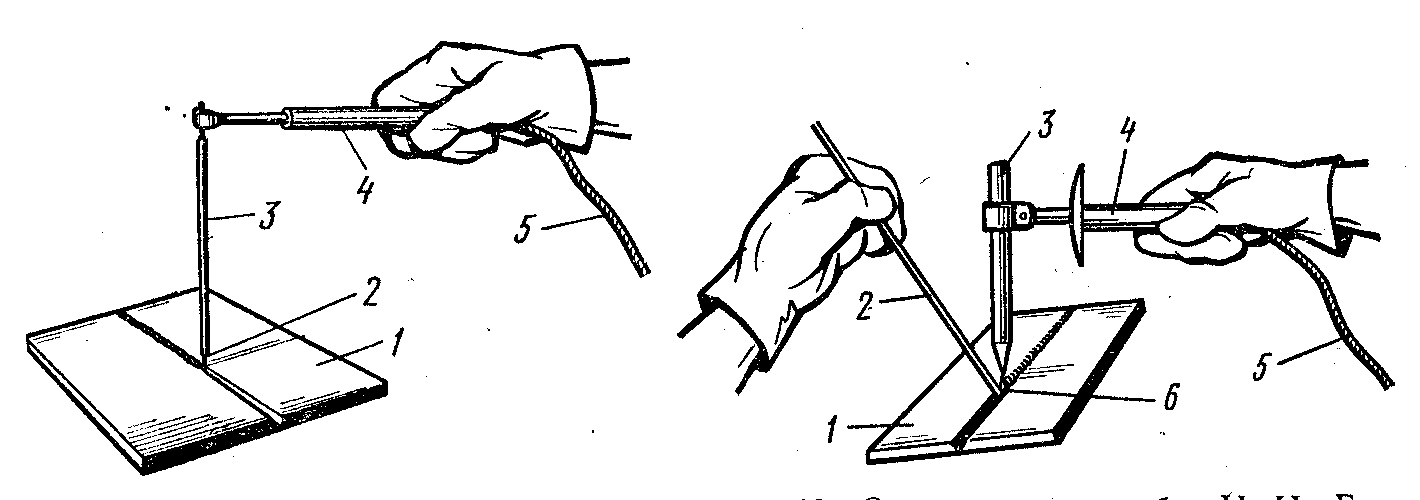
Рисунок 17.2 Сварка по способу
Н.Г.Славянова
Рисунок 17.3 Сварка по способу
Н.Н.Бенардоса
При сварке листов 1 (рис. 17.3) угольным электродом 3 по способу Н.Н.Бенардоса электрод не плавится. Заполнение шва производится расплавлением проволоки 2, вводимый со стороны в пламя сварочной дуги 6. Ток к электроду подводится по проводу 5 через электрододержатель 4. Этот способ применяется редко, так как менее удобен и не дает высокого качества наплавляемого металла.
Контактная сварка основана на использовании тепла, выделяющегося при прохождении электрического тока через свариваемый участок. Свариваемые детали в мест контакта нагревают до пластического состояния и сдавливают под определенным усилием, получая, таким образом, неразъемное соединение. Контактная сварка делится на стыковую, точечную и роликовую.
17.3 Газовая сварка и резка
Газовая сварка относится к способам сварки плавлением. При этом способе сварки кромки свариваемых деталей соединяются швом совершенно так же, как при дуговой сварке, но источником тепла служит не дуга, а сварочное пламя, которое образуется при сгорании горючего газа (ацетилена, а также коксового и светильного газа, водорода, бензола и др.). Горючие газы, смешиваясь с кислородом, дают пламя 4 высокой температуры (около 36000С – рис. 17.4, б).
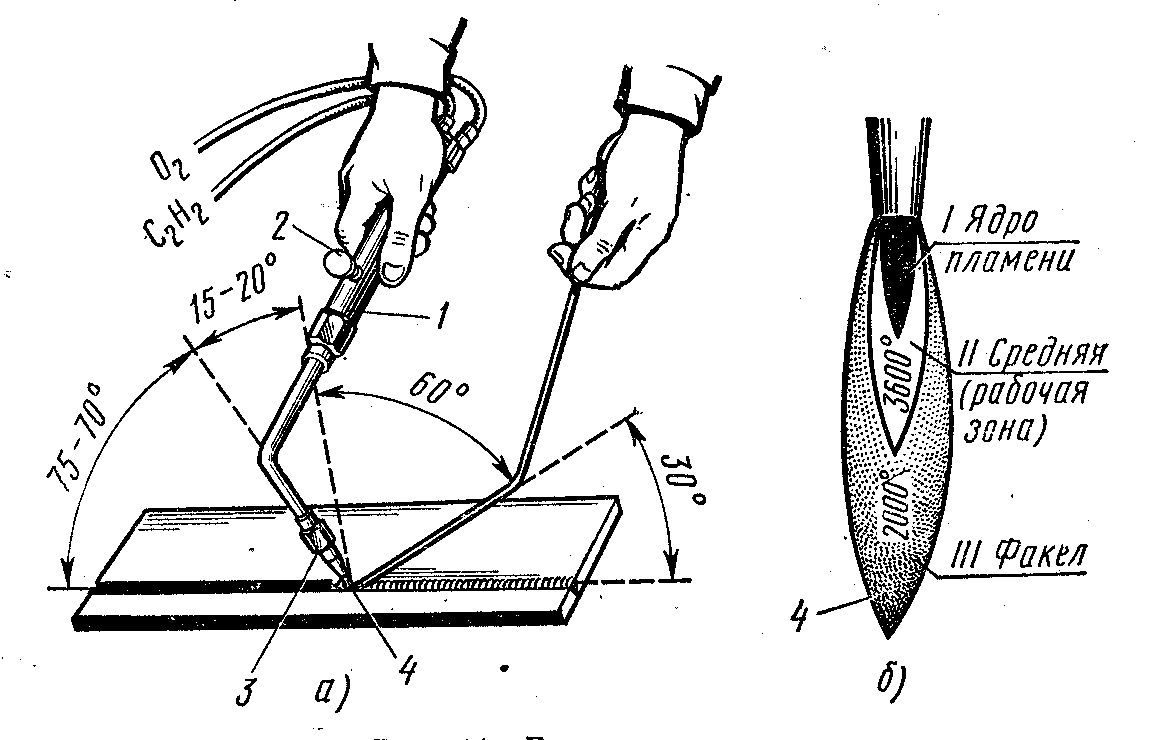
а - схема процесса, б - строение пламени
Рисунок 17.4 Газовая сварка
При сварке горелку продвигают вдоль шва, соблюдая необходимый угол наклона мундштука и проволоки к свариваемой поверхности. Угол наклона мундштука (рис. 17.4, а) колеблется от 150 (для сварки листов толщиной 1 мм) до 800 (при толщине 15 мм и выше).
Подвод газового пламени осуществляется сварочной горелкой (рис.17.4, а), в которой происходит смешивание кислорода и горючего газа, а корпус 1 позволяет удерживать горелку в рабочем положении. На корпусе расположены вентили 2, регулирующие подвод кислорода и ацетилена. На конце горелки имеется мундштук 3, через который выходит из смесительной камеры горючая смесь.
Газовая резка применяется для разделения металла на части – при разрезке листового материала большой толщины, рельсов, сортового проката; при вырезке деталей сложного контура из толстого листа. Кроме резки, струей кислорода прожигают отверстия в металле толщиной от 100 до 3000 мм.
Газокислородную резку выполняют вручную и специальными машинами. Для ручной резки применяют универсальный резак, имеющий сменные мундштуки – два подогревательных и пять режущих. Конструкция резака (рис.17.5) в той части, где обеспечивается смешение горючей смеси, принципиально не отличается от сварочной горелки.
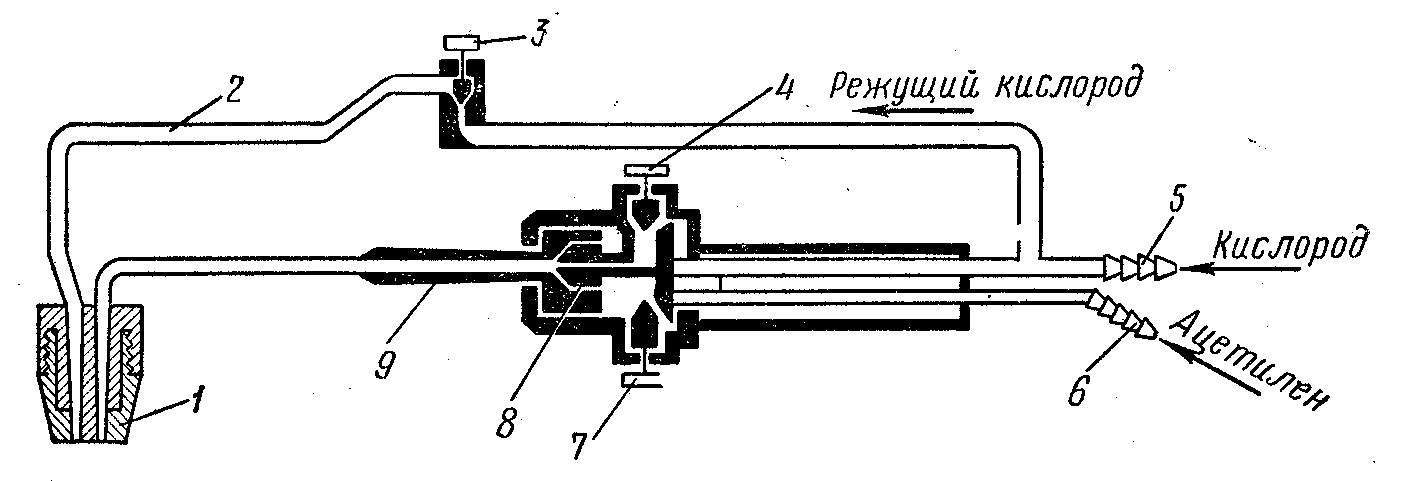
1 - наконечник, 2, 5, 6 - трубки, 3, 4, 7 - вентили, 8 - инжектор, 9 - смесительная камера
Рисунок 17.5 Ацетиленовый резак
Техника безопасности при выполнении сварочных работ. К обслуживанию сварочных установок и аппаратуры, к производству сварочных работ допускаются только рабочие, знающие правила техники безопасности и имеющие право на производство этих работ.
Контрольные вопросы:
Каково значение сварки в технике и народном хозяйстве?
- Перечислите способы сварки, расскажите об особенностях их.
- Какие примеси в металла влияют на свариваемость? Какие стали не свариваются?
- Что такое контактная сварка и как она выполняется?
- В чем заключаются особенности газовой сварки?
- Как осуществляется термитная сварка?
- Для выполнения каких работ применяют газовую резку металлов?
17.4 Наплавка
Наплавка занимает важное место в сварочной технологии и широко применяется при ремонте и восстановлении изношенных деталей, а также при изготовлении новых деталей, у которых необходимо обеспечить особые свойства поверхностей (например, твердость, износостойкость, коррозионную стойкость, жаростойкость).
Наплавку осуществляют нанесением расплавленного металла на поверхность изделия, нагретую до оплавления или до температуры надежного смачивания жидким наплавленным металлом. При этом наплавленный слой составляет одно целое с основным металлом за счет образования металлических связей.
Для наплавки могут быть использованы различные источники нагрева: газовое пламя, электрическая дуга, высокочастотный нагрев, электрошлаковый процесс, луч лазера и др. Толщина наплавленного металла может быть различной: 0,5 – 10 мм и более.
Для того чтобы свойства наплавленного металла не существенно изменялись за счет «разбавления» его основным металлом при наплавке поверхностей с особыми свойствами, глубина проплавления металла изделия и соответственно доля его участия в образовании поверхностного слоя должны быть минимальными.
Наплавку можно выполнять ручным и механизированным способами. Механизированная наплавка обеспечивает более высокие качество и производительность. Для дуговой наплавки больших по площади поверхностей используют специальное оборудование, в которых плавящимся электродом является лента. Применяют ленточные электроды сплошного сечения и порошковые ленты. Порошковая лента имеет металлическую оболочку, внутри которой заключена шихта, содержащая шлакообразующие компоненты и легирующие добавки. При выполнении ремонтных работ по восстановлению изношенных поверхностей иногда весьма нежелательной оказывается деформация изделия, вызываемая неравномерным нагревом. Способ вибродуговой наплавки позволяет получать наплавленный слой с незначительной деформацией изделия.
Сущность его в том, что наплавку выполняют электродом 3 (рис.17.6), которому сообщают механические колебания в направлении изделия 1 с помощью электромагнита 4 с частотой 30-100Гц и амплитуды 0,5 - 1 мм. Электрическая дуга при этом периодически закорачивается на свариваемое изделие и снова возбуждается. При каждом замыкании частицы электрода остаются на поверхности изделия. В зону наплавки непрерывно подают охлаждающую жидкость (раствор щелочи) или струю воздуха через сопло 2. Принудительное охлаждение поверхности повышает твердость наплавленного слоя. Наиболее часто этот способ применяют при наплавке цилиндрических изделий небольшого диаметра при восстановлении изношенных шеек валов.
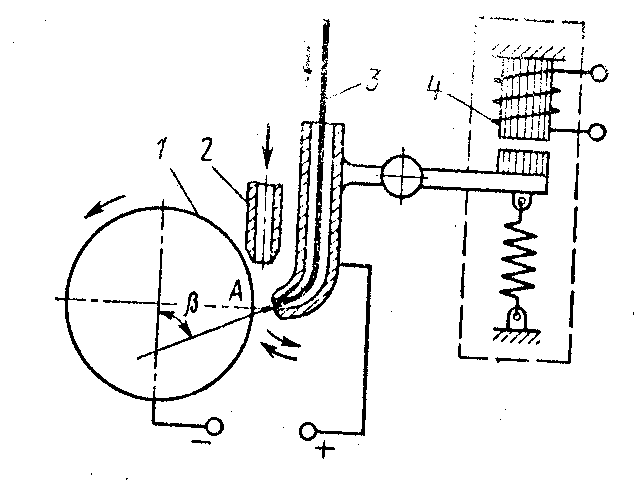
1 - наплавляемое изделие; 2 - сопло для подачи охлаждающей жидкости; 3 - электродная проволока; 4 - электромагнитный вибратор
Рисунок 17.6 Схема вибродуговой наплавки
Металлизация представляет собой процесс осаждения распыленного струей газа жидкого металла на поверхность изделия. К источнику нагрева (им может быть газовое пламя, электрическая дуга, плазменная струя) подают проволоку, которая расплавляется. Жидкий металл подхватывается струей газа, подаваемого под давлением в зону плавления, и выбрасывается с большой скоростью через сопло металлизатора в виде распыленных капель. Поток брызг расплавленного металла направляют на поверхность изделия. Ударяясь о поверхность, капли соединяются с ней и образуют слои покрытия.
Материал покрытия может подаваться в металлизатор в виде проволоки (стальной, алюминиевой, медной, цинковой и др.), а также в виде неметаллических порошков (стекла, эмалей, пластмасс). Таким образом, термин «металлизация» оказывается неточным, поскольку включает в себя процессы нанесения в неметаллических покрытий.
По сравнению с наплавленным слоем металлизационный слой, состоящий из мелких поверхностно-окисленных частиц металла, имеет меньшую прочность.
Металлизацию применяют для восстановления изношенных поверхностей деталей машин, для защиты поверхности от коррозии, изнашивания, в декоративных целях.
Тема 18 Комплексная работа
Студент должен:
уметь:
- организовать рабочее место для определенной слесарной операции;
- подобрать необходимый инструмент;
- прочесть чертеж;
- определить технологический процесс изготовления детали;
- контролировать процесс изготовления в соответствии с техническими условиями;
- соблюдать правила техники безопасности.
Комплексные работы учащиеся выполняют после изучения и выполнения упражнений по всем видам слесарной обработки, предусмотренным учебным планом и программой практики. В пределах времени, отведенного на комплексную работу (четыре занятия по 6 уч.часов), учащиеся получают индивидуальные задания на изготовление (обработку) деталей или изделий, включающие различные виды слесарных операций: опиливание, разметку, шабрение, сверление, нарезание резьбы, клепку, пайку или лужение.
Изделиями, которые должны изготовить учащиеся при выполнении комплексных работ, могут быть плоскогубцы, воротки, ручные тиски, кронциркули и др., а также детали, которые входят в продукцию, изготовляемую учебной мастерской для оснащения кабинетов и лабораторий техникума или реализуемую как товарная продукция. Например, при изготовлении слесарных тисков учащиеся выполняют объемную разметку, опиливание, сверление различных деталей тисков. При выпуске настольно-сверлильных станков все слесарные операции, входящие в технологический процесс изготовления различных деталей и узлов станка, могут быть также поручены учащимся для выполнения комплексных работ.
Каждое комплексное задание должно содержать не менее 3...4 различных по своему характеру слесарных операций. Количество заготовок, которое учащийся должен обработать, зависит от их трудоемкости и должно быть рассчитано на загрузку учащегося работой не мене чем на 3 рабочих дня, оставив часть последнего дня практики для сдачи работы и зачета по практике.
Оценка знаний по слесарной практике проставляется на основе качества выполнения работы (или количество обработанных заготовок), времени, затраченного на обработку, бесед с учащимися и проверки дневников-конспектов. Учащийся обязан не только уметь выполнять те или иные слесарные операции, освоенные во время практики, но хорошо знать теоретический материал и отвечать на контрольные вопросы, такие, как: наименование и назначение слесарных инструментов; правила работы ножовками, молотками, зубилами, напильниками; устройство слесарных тисков; правила работы и заточки на заточных (точильных) станках; устройство и приемы работы на простом сверлильном станке; маркировка и наименование обрабатываемых материалов; правила применения и чтение размера при измерении простым контрольно-измерительным инструментом (штангенциркулем, микрометром и т.п.), организация рабочего места, правила техники безопасности при выполнении конкретных слесарных операций. Вопросы учащимся могут задаваться либо устно, либо в виде контрольных билетов.
ЗАКЛЮЧЕНИЕ
В соответствии с государственными требованиями к минимуму содержания и уровню подготовки выпускников по специальности 1701 "Монтаж и техническая эксплуатация промышленного оборудования (по отраслям), утвержденными 16 мая 2002 г. и примерной программой по группе специальностей 1700 от 2 февраля 2004 г., автор, с учетом специфики специальности 1701, обобщил многолетний опыт слесарной и станочной практики в данном учебном пособии "Учебная практика в ГОУ СПО для получения первичных профессиональных навыков".
В пособии описаны основные слесарные операции, оборудование, инструменты и приспособления, приемы выполнения слесарных работ и средства их механизации. Даны сведения об организации рабочего места слесаря, видах и мерах предотвращения брака, технике безопасности, противопожарных и экологических мероприятиях, научной организации труда слесаря. Изложены сведения о материалах, применяемых в машиностроении, технических измерениях.
Описаны специфические работы для нефтехимических предприятий.
Основная цель составленного методического пособия по учебной практике помочь будущим выпускникам специальности 1701 быстро адаптироваться в ремонтно-механических заводах и цехах нефтехимических предприятий при ремонте, сборке и монтаже нефтехимического оборудования.
Пособие может быть использовано при подготовке рабочих-слесарей и проведении различных видов практик студентами, мастерами профессиональных учебных заведений.
ЛИТЕРАТУРА
Государственный Образовательный Стандарт МО России ст. 16.05.2002.
- Примерная программа: «Производственная (профессиональная) практика» по специальности 1701 «Монтаж и техническая эксплуатация промышленного оборудования (по отраслям) среднего профессионального образования (базовый и повышенный уровень)», Москва, 2004.
- Грецкая Г.Т. Основы организации и методика проведения производственной практики учащихся средних специальных заведений. М.: 1982.
- Аршинов В.А., Алексеев Г.А. Резание металлов и режущий инструмент. М., Машиностроение, 1967. - 500 с.
- Генкин А.Э. Оборудование химических заводов: Учебное пособие для техникумов. - 4-е изд.пepepaб. и доп. - М.: Высшая школа, 1986. - 280 с.
- Макиенко Н.И. Слесарное дело с основами материаловедения. Учебник для подготовки рабочих на производстве. Издание 6-е переработано. М.: Высшая школа, 1976. - 464 с.
- Мокрецов A.M., Елизаров А.И. Практика слесарного дела: Учеб. пособие для проф.обучения рабочих на производстве, - М.: Машиностроение, 1989. - 288 с.
- Недоступов Ю.К. Охрана труда в образовательных учреждениях. Ч.II. Справочник для руководителей и специалистов. Изд.6-е (доп. и перераб.). Серия "Библиотека руководителя", Мышевици, изд. УПЦ "Талант". 2002. - 224 с.
- Нефедов Н.А. Практическое обучение в машиностроительных техникумах. Учебная практика: Учебное пособие для техникумов. - 2 издание переработано и дополнено. М.: Высшая школа, 1990. - 311 с.
- Никифоров В.М. Технология металлов и других конструкционных материалов. Учебник для техникумов. 8-е изд. перераб. и доп., СПб Политехника, 2000.
- Покровский Б.С. Слесарное дело: Учебник для нач. проф. образования, Б.С.Покровский, В.А.Скакун. - М.: издательский центр «Академия», 2003. - 320 с.
- Справочник по производственному контролю в машиностроении. Издание 3-е переработано и дополнено. Под редак. доктора технических наук проф. А.К.Кутая. Машиностроение (Ленинградское отделение), 1974. - 676 с.