М. Ю. Подходы к исследованию чувствительности модели экосистемы шельфа к вариациям ее параметров соловьёва Н. В. Институт океанологии ран, г. Москва Разработка математической модели морского шельфа, как решение
Вид материала | Решение |
СодержаниеРасчет скруббера с акустическими форсунками во второй ступени улавливания пыли продукта Методика расчета теплоутилизатора кипящего слоя для систем кондиционирования воздуха |
- Задачи лп, а именно того, как возможные изменения параметров исходной модели повлияют, 75.03kb.
- С. Н. Трапезников московский инженерно-физический институт (государственный университет), 22.46kb.
- Доклад на Всероссийской научной конференции «От СССР к рф: 20 лет итоги и уроки», 140.15kb.
- Законодательная, нормативная, правовая база и экономика освоения континентального шельфа, 22.67kb.
- Рельеф шельфа морей российской арктики, 523.06kb.
- Программа по курсу «Дифференциальные уравнения», 41.77kb.
- А. В. Истомин Основные направления и приоритеты устойчивого развития Арктической зоны, 115.76kb.
- Проблемы раздела и освоения арктического шельфа, 172.74kb.
- Министерство образования и науки российской федерации, 61.83kb.
- Решение 7-й международной конференции и выставки по освоению ресурсов нефти и газа, 51.11kb.
РАСЧЕТ СКРУББЕРА С АКУСТИЧЕСКИМИ ФОРСУНКАМИ ВО ВТОРОЙ СТУПЕНИ УЛАВЛИВАНИЯ ПЫЛИ ПРОДУКТА
Кочетов О.С., Ходакова Т.Д.
Московская финансово-юридическая академия
Рассмотрим расчет скруббера с акустическими форсунками во второй ступени улавливания пыли продукта на примере режима распылительной сушилки, работающей по принципу параллельного тока движения раствора и теплоносителя. В качестве теплоносителя используется воздух, нагреваемый в газовом калорифере. В качестве распыливающего устройства используется механическая центробежная вихревая форсунка. Вывод готового продукта из сушильной установки производится с помощью скребков 7 в приемный короб 8 для готового продукта, а затем в бункер 9 для сбора готового продукта. В качестве первой ступени очистки воздуха от пыли продукта используются циклоны 6, размещенные в стояках 5, а окончательная очистка его производится в мокром скруббере 12, который орошается раствором, подаваемым насосом из емкости 11. В качестве распыливающих устройств скруббера используются акустические форсунки, конструкция которых представлена на рис. В скруббере происходит предварительное сгущение раствора до требуемой влажности. Отработанный и очищенный теплоноситель выбрасывается в атмосферу, а сгущенный раствор поступает в емкость11, и после перемешивания его с исходным раствором поступает в диспергатор 3.
Акустическая форсунка в системе орошения мокрого скруббера работает следующим образом. Распыливающий агент (рис), например воздух, подается по штуцеру 3 в коллектор 2, связанный через отверстия 4 с полостью 5, которая выполнена в виде усеченного конуса. Акустические колебания распыливающего агента способствуют более тонкому распыливанию раствора, подаваемого в распределительную головку 7 через полый стержень 6, из которой раствор подается в виде пленки жидкости, перекрывающей выход распыливающего агента из генератора звуковых колебаний, образованного резонатором 8. Эта пленка дробится под воздействием акустических колебаний воздуха на мелкие капли, в результате чего образуется факел распыленного раствора с воздухом, корневой угол которого определяется величиной угла наклона конической поверхности крышки распределительной головки 7.
Физический эффект работы акустической системы основан на том, что при резонансном совпадении собственной и возбуждающей частот амплитуда скорости колебания воздуха в горловине резонатора, резко возрастает, вызывая значительное возрастание мощности падающей звуковой волны (эффект резонатора Гельмгольца) [1].
Максимальное увеличение энергии для резонатора будет наблюдаться на резонансной частоте:

где kр - проводимость отверстий, соединяющих резонаторную камеру объемом Vр (м3);
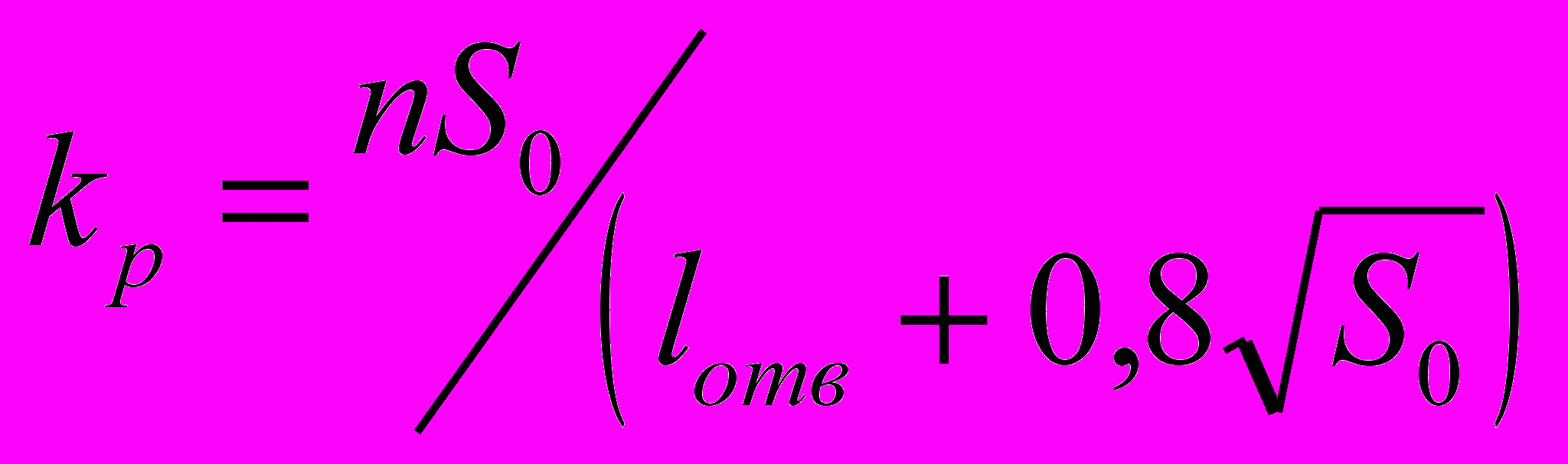
где n – количество отверстий; So – площадь одного отверстия диаметром do, м2 ; lотв – глубина отверстия, м.
При этом частота акустических волн, излучаемых резонатором, лежит в оптимальном диапазоне частот от 15 до 16 кГц с интенсивностью звука от 2 до 3 Вт/сек.
Расчет параметров скруббера начнем с построения I-d диаграммы на примере со следующими техническими условиями на протекание процесса сушки:
максимально допустимая температура нагрева в процессе сушки исходного раствора – 110°С; часовая производительность по сухому продукту G1 = 400 кг/час; начальная и конечная влажность раствора и продукта w1 = 64,3 % и w2 =5 %; начальная температура воздуха перед сушилкой t1 = 300 °С, температура воздуха за сушилкой t2 = 300 °С;
Для сушки используется наружный воздух с параметрами:
t0 = –10 °С ; d0 =1,47 г/кг; φ = 80 %; I0 = 1,53 ккал/кг.
Начальная точка В процесса сушки будет иметь параметры t1=300 °С и d1 = d0 =1,47 г/кг. Оценим количество подсасываемого воздуха на тракте от сушилки до вентилятора величиной 10 %; тогда количество воздуха, проходящего через скруббер, равно
Lск = 1,1 L = 1,1∙8050 = 8855 кг/час.
Параметры воздуха, подсасываемого из помещения цеха:
t′0 = 20 °С; φ′0 = 80 %, d′0 = 12 г/кг.
Из построения на диаграмме I-d процесса смешения отработанного воздуха сушилки и воздуха из помещения цеха находим параметры воздуха перед скруббером, которые будут: d′ск = 64 г/кг, t′ск = 93 °С.
Построим действительный процесс сгущения раствора в скруббере, который, согласно расчету аналогичного процесса сушки, выражается линией ММ′. При определении конечной точки процесса исходим из относительной влажности воздуха за скруббером φ″ск= 60 %. Параметры воздуха в точке М′ будут: d″ск = 77 г/кг, t″ск = 62 °С.
Количество испаряемой влаги в скруббере:
Wск = Lск /1000 (d″ск - d′ск) = 8855 / 1000(77 – 64) = 115 кг/час. (3)
Влажность раствора после скруббера
w′1 = (G1 - Gсух - Wск ) / (G′1 - Wск )100 = (1065 – 380 – 115 ) / (1065 – 115 ) ∙100 = 60 %, что соответствует принятой ранее величине влажности раствора перед сушилкой. Понижением влажности раствора за счет улавливания пыли продукта из воздушного потока пренебрегаем.
При соответствующей изоляции сушилки принимаем потери тепла в окружающую среду равными q5 = 60 ккал/кг, тогда суммарные потери тепла составят:
Δ= υ1- qм – q5 = 48 – 11,7 – 60 = 23,7 ккал/кг.
Для нахождения влагосодержания отработанного воздуха в процессе сушки используем диаграмму I-d и отрезок Ее: в результате получим d2 =70 г/кг.
Подсчитаем расход сухого воздуха на 1 кг испаренной влаги:
l = 1000/ (d2 – d1) = 1000/( 70 – 1,47 ) = 14,6 кг/кг. (4)
При этом часовой расход сухого воздуха составит:
L = l∙W = 14,6∙550 = 8050 кг/час.
Удельный объем влажного воздуха, отнесенный к 1 кг сухого воздуха, равен
v0 = 4,64∙10-6 (622 + d)(273 + t), (5)
причем на входе в сушилку υ0 =1,65 м3/кг, а на выходе из сушилки υ"0 =1,19 м8/кг.
В первый период сушки температура поверхности равна температуре мокрого термометра, т. е. υn = tм ≈ 5З °С. Этот период продолжается до тех пор, пока влажность частиц не станет равной гигроскопической, т. е. для данного раствора wгc = 40 % (влажность, отнесенная к абсолютно сухому весу).
Исходя из скорости воздуха в скруббере uск = 1 м/сек, определяем диаметр скруббера:
______________________ ________________________
Dск= √ ( Lскvск /(0,785 ∙ 3600∙ uск ) = √ (8855∙1,085 / (0,785∙3600∙1) = 1,84 м. (6)
Скруббер работает с рециркуляцией раствора из расчета, чтобы плотность орошения составляла А = 3 т/м2 час.
Количество распыливаемого раствора
Gр = А(π∙Dск2)/4 = 3(3,14∙1,842)/4 = 7,92 т/час = 7920 кг/час. (7)
Влажность раствора перед скруббером
wск =( G1w1 + (Gр - G1) w1’)/ Gр = (1065∙64,3 + (7920 – 1065)∙60)/7920 = 60,7%.
В скруббере устанавливаем четыре акустические форсунки тонкого распыла (рис). Распыление производится при давлении 3,0 ати.
![]() |
Рис. Схема акустической форсунки: 1– корпус, 2 – коллектор, 3,9 – штуцер, 4 –дроссельное отверстие, 5 – полость, 6 – полый стержень, 7 – корпус распределительной головки, 8 – торцевая выточка, 10 – демпфирующая полость, 11 – калиброванные отверстия. |
Рабочая высота скруббера
H ск = Vск / Fск = 11,0 / 2,64 = 4,17 м. (8)
Из построения на диаграмме I-d процесса смешения отработанного воздуха сушилки и воздуха из помещения цеха находим параметры воздуха перед скруббером, которые будут: dск = 64 г/кг, tск = 93 °С. Строим действительный процесс сгущения раствора в скруббере. При определении конечной точки процесса исходим из относительной влажности воздуха за скруббером φск″ = 60 %. Количество испаряемой влаги в скруббере
Wск = Lск /1000 (d″ск - dск) = 8855 / 1000 (77 – 64) = 115 кг/час. (9)
Исходя из скорости воздуха в скруббере uск = 1 м/сек, определяем диаметр скруббера: ______________________ ________________________
Dск= √ ( Lскvск /(0,785 ∙ 3600∙ uск ) = √ (8855∙1,085 / (0,785∙3600∙1) = 1,84 м. (10)
Скруббер работает с рециркуляцией раствора из расчета, чтобы плотность орошения составляла А = 3 т/м2 час.
Объем скруббера:
Vск = Q ск / (αvск Δt ср) = 66000 / (235 ∙25,5) ≈ 11 м3.
Рабочая высота скруббера
H ск = Vск / Fск = 11,0 / 2,64 = 4,17 м. (11)
Таким образом, в работе представлен расчет скруббера с акустическими форсунками, эффект работы которых основан на том, что при резонансном совпадении собственной и возбуждающей частот, амплитуда скорости колебания воздуха в горловине резонатора, резко возрастает, вызывая значительное возрастание мощности падающей звуковой волны. При этом пленка жидкости, перекрывающей выход распыливающего агента из генератора звуковых колебаний, дробится под воздействием акустических колебаний воздуха на мелкие капли, в результате чего образуется факел мелкодисперсного распыленного раствора с воздухом, и повышается скорость сушки на 10 %.
ЛИТЕРАТУРА
- Розенберг Л.Д. Физика и техника мощного ультразвука. – М.: Наука, в 3-х кн.
Книга 3: Физические основы ультразвуковой технологии, 1970. Гл. 9 и 10.
МЕТОДИКА РАСЧЕТА ТЕПЛОУТИЛИЗАТОРА КИПЯЩЕГО СЛОЯ ДЛЯ СИСТЕМ КОНДИЦИОНИРОВАНИЯ ВОЗДУХА
Кочетов О.С., Ходакова Т.Д.
Московская финансово-юридическая академия
Рациональное использование топливно-энергетических ресурсов является одним из основных принципов функционирования современного промышленного производства. Рассчитаем систему кондиционирования воздуха с утилизатором тепла кипящего слоя для гребнечесального цеха ОАО «Троицкая камвольная фабрика». Аппараты с кипящим слоем широко применяют в системах оборотного водоснабжения (для охлаждения рециркулирующей воды) в хлебопекарной промышленности и на предприятиях общественного питания. Однако наиболее эффективно их использование в вентиляционных системах предприятий, где по технологическим требованиям необходимо поддержание в течение всего года повышенной относительной влажности воздуха, что характерно для производственных цехов текстильных предприятий, так как при повышенной влажности воздуха уменьшается вероятность обрыва нитей, и, следовательно, повышается в целом производительность технологического процесса. При использовании аппарата с кипящим слоем сокращается до 50 % расход теплоты на нагрев приточного воздуха и достигается охлаждение его в летний период, что обеспечивает достаточно малый срок окупаемости необходимых капитальных вложений.
Площадь цеха составляет 2 122 м2, высота – 3,2 м. На продольной стене цеха, обращенной на юг, имеются 32 окна, на восток – 10 окон, с двойным остеклением в деревянных переплетах, размером 1,81,4 м. Технологическое оборудование состоит из 54 ленточных и гребнечесальных машин мощностью электродвигателей 2,8 кВт. В цехе одновременно работают 47 человек.
Сумма теплопоступлений от всех источников для теплого периода года ΣQ = 1004397 кДж/ч. Примем расчетные параметры Б наружного воздуха для г. Троицка [1]: tн = 28,5°С, iн = 54 кДж/кг. Внутренние параметры принимаем равными tв = 25 °С при φ = 50 %.
Цех находится на верхнем этаже, поэтому теплопотери происходят через наружные стены, окна и потолок. Подсчитав теплопотери по каждому ограждению в отдельности и просуммировав их, получим общую величину теплопотерь в цехе: ΣQ = 21 016 кДж/ч. Таким образом, избыточное тепло в летнее время составит: ΣQп =1025413 кДж/ч
Количество воздуха, которое необходимо подавать в цех, определим по формуле:

Производительность системы кондиционирования воздуха будет равна

При выборе кондиционера будем учитывать параметры, рассчитанные для лета. Принимаем к установке кондиционер типа КТ-200 расчетной производительностью 182000 м3/ч при номинальной производительности 200000 м3/ч с утилизатором тепла. Аппарат с кипящим слоем работает следующим образом. Шары подвижной насадки 4 под воздействием, восходящего потока воздуха и поступающей на нее воды перемещаются, сталкиваясь друг с другом, и тем самым значительно интенсифицируют процессы тепло- и массообмена между распыляемой водой и воздухом, поступающим в аппарат. Интенсификации процесса тепло- и массообмена способствует установленный на опорной решетке 6 вибратор.
Начало псевдоожижения соответствует равенству подъемной силы и силы тяжести частицы. Для всего аппарата полный перепад давления
![]() | (3) |
а перепад давления в слое
![]() | (4) |
где G, h – масса и высота слоя; S – полное сечение аппарата; ρч, ρг – плотность частицы материала и газа; – порозность слоя.
![]() | ![]() |
Рис.1. Кривая псевдоожижения полидисперсных систем. | Рис. 2. Кривая идеального вытеснения. |
Для полидисперсных систем считается характерным наличие переходной области между областями с режимами фильтрации и псевдоожижения. На рис. 1 показана примерная зависимость ΔP от υ для этого случая. При некоторой скорости υ = υн начинает теряться устойчивость слоя и перестают двигаться мелкие частицы. Полное псевдоожижение всего слоя и ΔP = Сonst наблюдаются при более высокой скорости газа υ > υн. В переходной области υн < υ < υк все большая доля частиц переходит во взвешенное состояние, и сопротивление слоя медленно возрастает ΔP ~ υn (n = 0,1…0,2).
Кипящий слой характеризуется следующими параметрами: порозностью слоя (относительный объем пустот в слое), скоростью на живое сечение υ/, числом псевдоожижения W=υ/υкр, высотой слоя h, скоростью витания частиц υвит и показателем полидисперсности i (отношение диаметров частиц крупной и мелкой фракций):
![]() | (5) |
Предложена обобщенная полуэмпирическая зависимость для описания всего интервала существования взвешенного слоя:
![]() | (6) |
где А = 18 и В = 0,61 – константы.
Для случая идеального перемешивания твердого материала в кипящем слое кривая распределения концентраций по времени пребывания газовой фазы приближается к кривой идеального вытеснения (рис.2). Этот случай реализуется при малых размерах слоя и примерно одинаковой его протяженности в различных направлениях. Для описания гидродинамики кипящего слоя в условиях различных режимов обтекания частиц наиболее применима интерполяционная формула Тодеса (для шарообразных частиц).
Выражение (6) при = 0,4 превращается в формулу (5) для определения критической скорости псевдоожижения, а при = 1,0-скорости витания
![]() | (7) |
![]() |
Рис.3. Схема утилизатора тепла кипящего слоя для систем кондиционирования воздуха: 1-сепаратор, 2-распределитель воды, 3-форсунки, 4-подвижная насадка из полых пластмассовых шаров («кипящий слой»), 5-поддон, 6-опорная решетка, 7-металлический корпус, 8-направляющий аппарат, 9-поплавковый клапан, 10-фильтр. |
Зависимость Re = f(Аr) изменяется с изменением зависимости Ly = f(Аr), причем
υ = f(dч). Зависимость Ly = f(Аr) представлена графически [2], а область существования псевдоожиженного слоя лежит между кривыми порозности = 1 и = 0,4.
При расчете аппарата с кипящим слоем в качестве исходных данных задают следующие показатели процесса: производительность по готовому продукту G2, кг/ч; начальную и конечную влажность материала ωн и ωк, %; температуры воздуха: наружного t0, на входе в аппарат t1 и выходе из него t2, °С; начальную θн и конечную θк температуры материала. Как показывают результаты экспериментов, можно принимать
θк = t2 – (3...5)˚C.
Для расчета геометрических размеров аппарата с кипящим слоем рассчитывают критическую скорость псевдоожижения для частиц материала максимального размера dmax по соотношению
![]() | (8) |
где
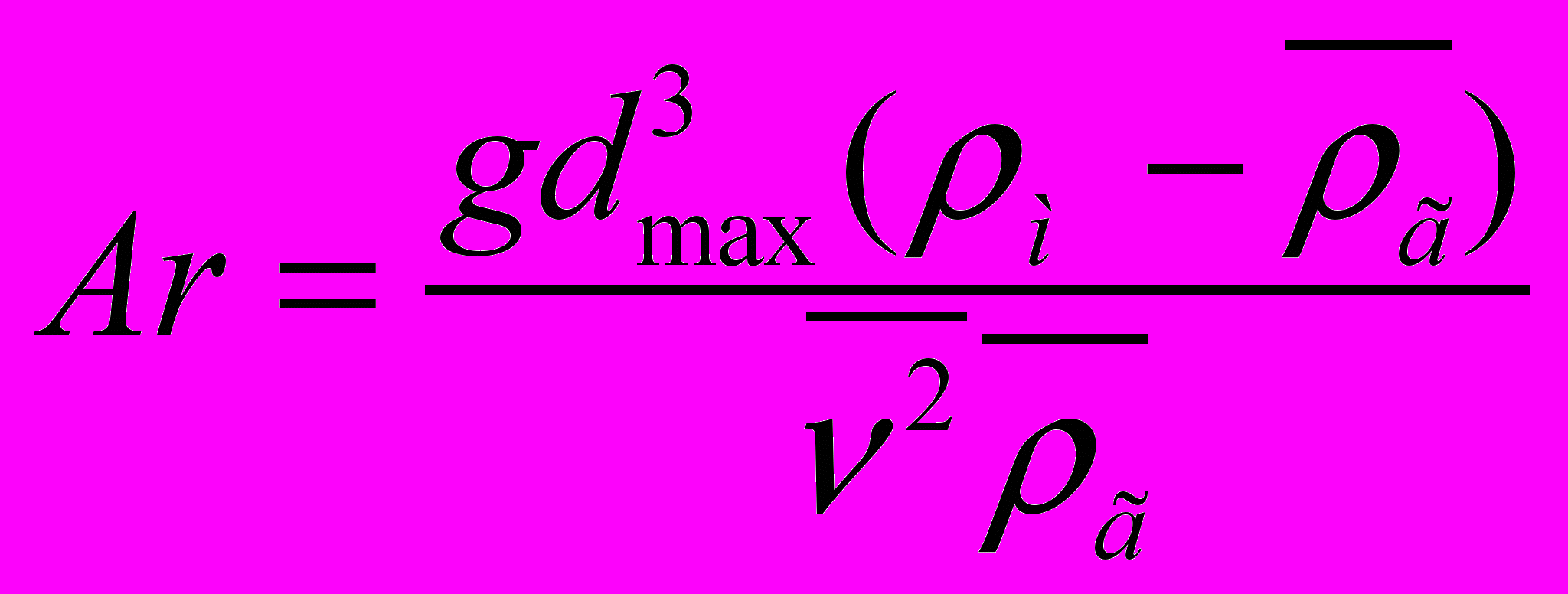
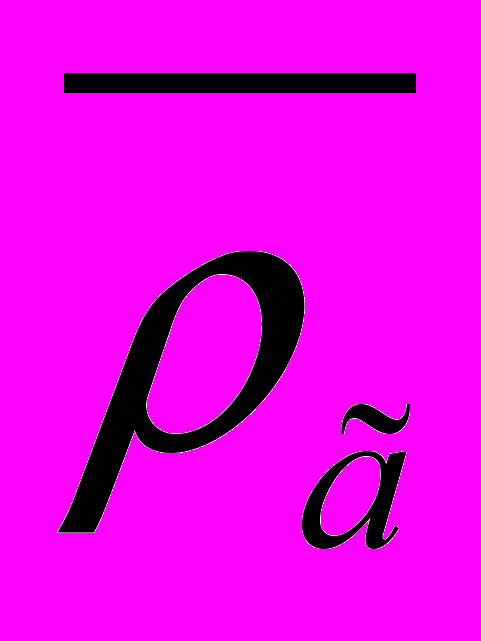
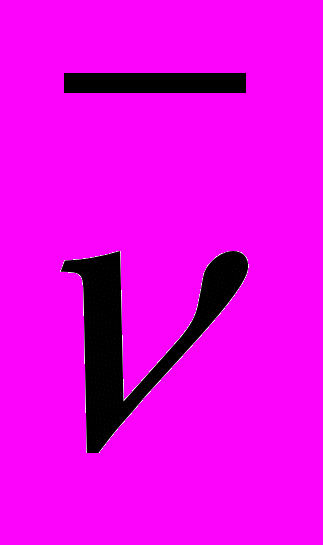
Критическая скорость (в м/с):
![]() | (9) |
Для обеспечения устойчивого режима псевдоожижения средняя скорость газа в аппарате составляет:
![]() | (10) |
Тогда площадь газораспределительной решетки аппарата (в м3) равна:
![]() | (11) |
Коэффициент межфазного теплообмена для частиц материала, имеющих средний объемно-поверхностный размер
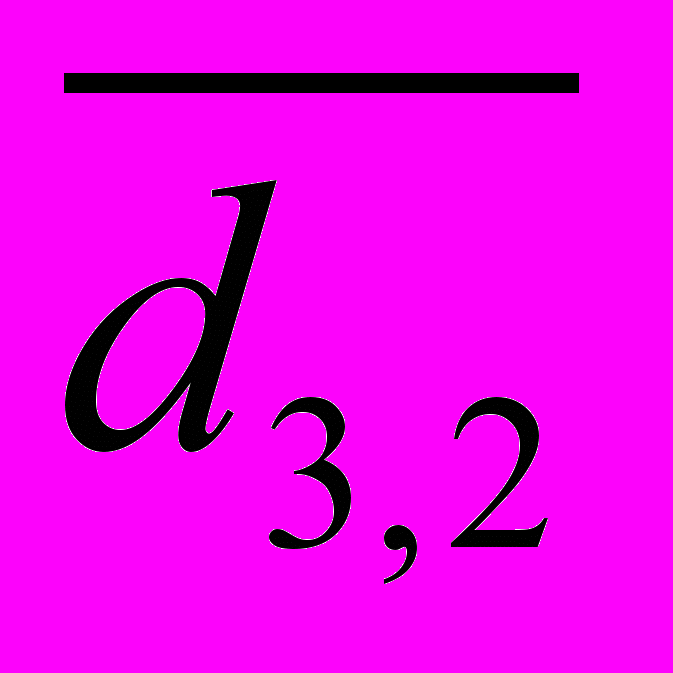
![]() | (12) |
где
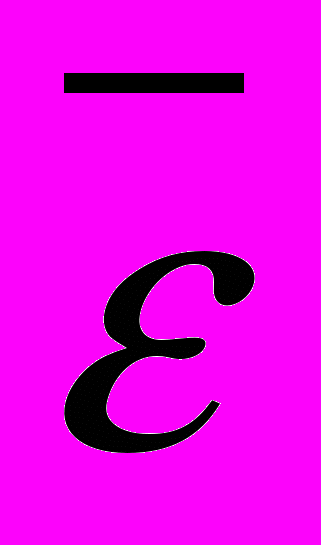
![]() | (13) |
Pr = ν/a - число Прандтля; a – коэффициент температуропроводности газа при
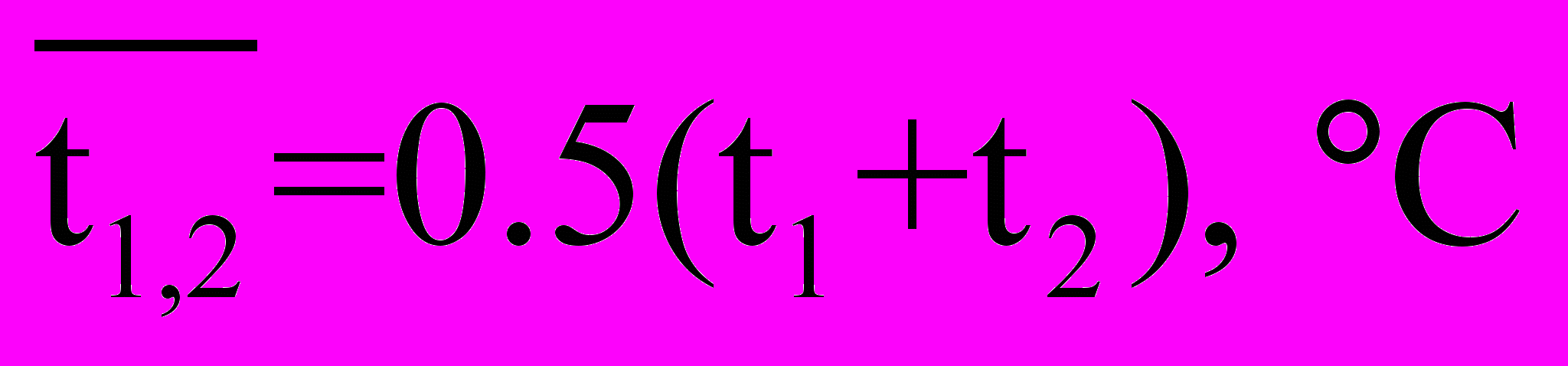
Коэффициент межфазного теплообмена [в Вт/(м2 К)]:
![]() | (14) |
где λ – коэффициент теплопроводности газа при
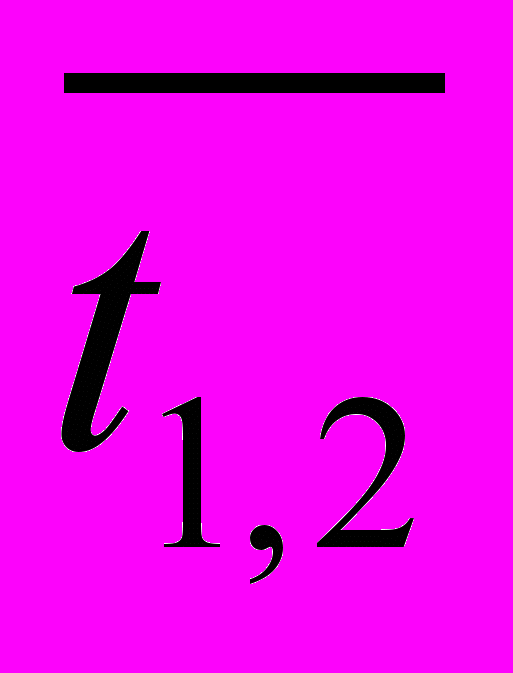
Минимальная высота слоя материала в аппарате (в м)
![]() | (15) |
Реальную высоту слоя материала в аппарате
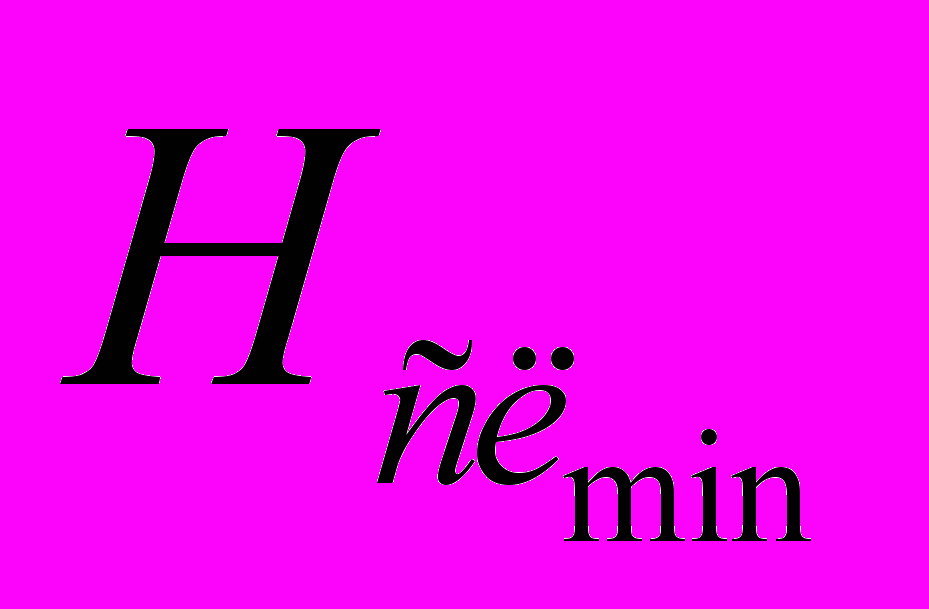
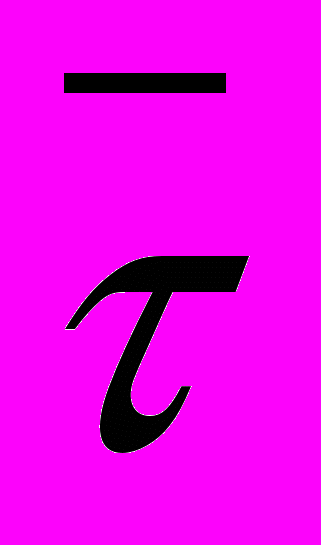
![]() | (16) |
Учитывая, что реальное время пребывания отдельных частиц в аппарате отличается от
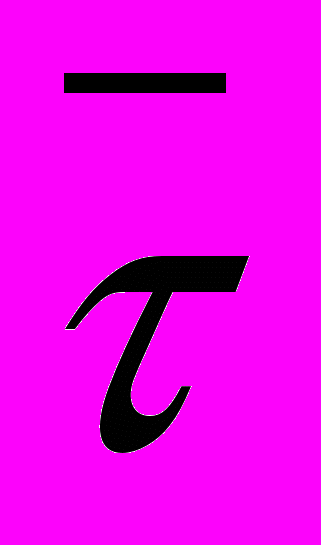
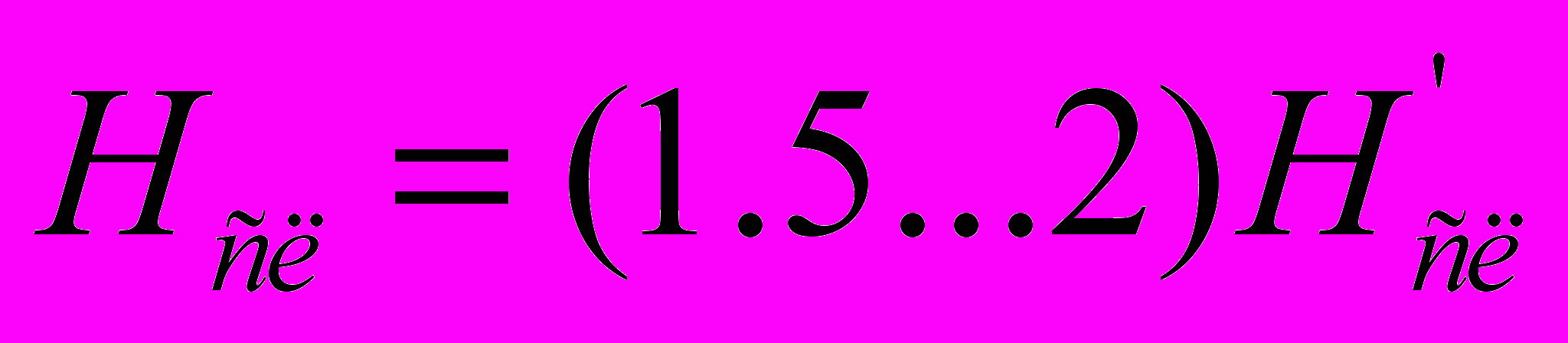
При этом должно обеспечиваться условие:
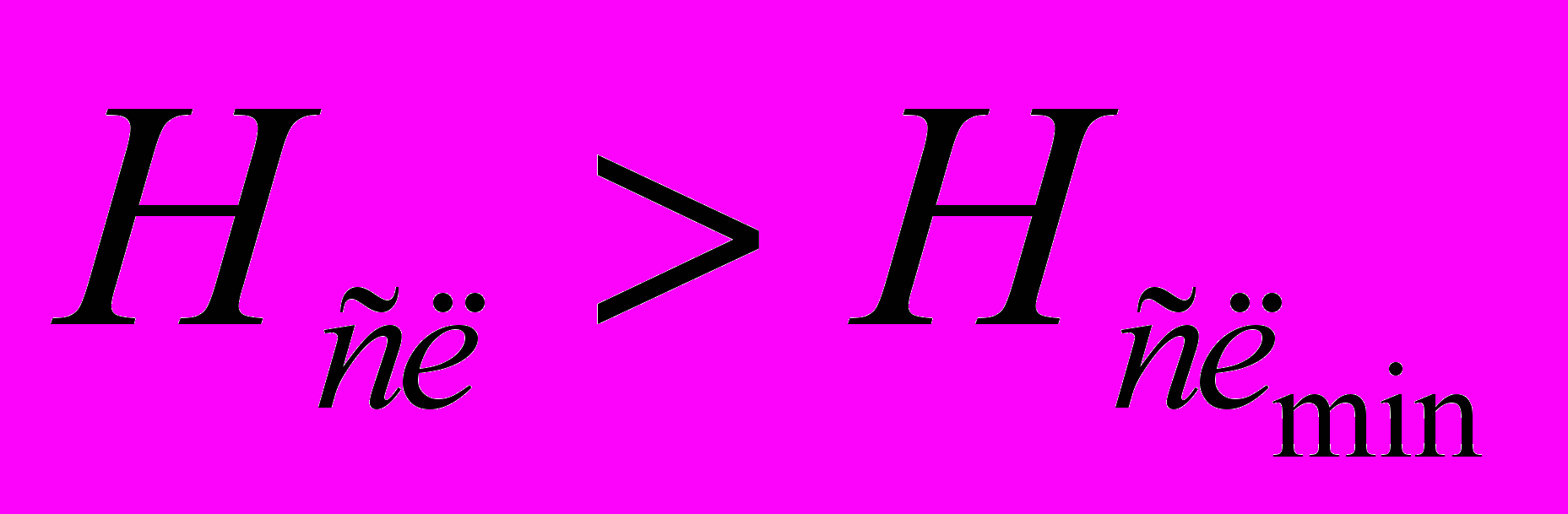
Гидравлическое сопротивление слоя материала при стационарном режиме определяют по соотношению (в Па):
![]() | (17) |
При номинальной производительности аппарата и давлении воды перед форсункой 98 кПа насадка 4 неподвижна при массовой скорости воздуха до 2,7…2,9 кг/(м2с), а при увеличении этой скорости до 3…3,1 кг/(м2с) начинается движение шаров 4, процесс тепло- и массообмена значительно интенсифицируется, но возрастает и аэродинамическое сопротивление аппарата. Поэтому принимать массовые скорости воздуха выше 4,1…4,3 кг/(м2с) не следует, так как шары выходят из рабочей зоны, прижимаясь к сепаратору 1, и резко увеличивается аэродинамическое сопротивление аппарата, которое составляет: 0,12 кПа при массовой скорости 2 кг/(м2с), 0,2 кПа – при 3 кг/(м2с) и 0,35 кПа – при 4 кг/(м2с). Размеры аппарата 0,650,651,9 м, площадь живого сечения в рабочей зоне 0,42 м2.
Таким образом в работе рассмотрена методика расчета параметров теплоутилизатора кипящего слоя систем вентиляции и кондиционирования воздуха для гребнечесального цеха ОАО «Троицкая камвольная фабрика», для кондиционера типа КТ-200 расчетной производительностью 182000 м3/ч. Выявлено, что принимать массовые скорости воздуха выше 4,1…4,3 кг/(м2с) не следует, так как полые пластмассовые шары инертной насадки выходят из рабочей зоны, прижимаясь к сепаратору, при этом увеличивается аэродинамическое сопротивление аппарата, которое составляет: 0,12 кПа при массовой скорости 2 кг/(м2с), 0,2 кПа – при 3 кг/(м2с) и 0,35 кПа – при 4 кг/(м2с). Получены оптимальные размеры аппарата: 0,650,651,9 м (при площади живого сечения в рабочей зоне 0,42 м2).
ЛИТЕРАТУРА
1. Сажин Б.С., Кочетов О.С. Научные основы создания систем жизнеобеспечения для текстильных производств. – М.: Изд. МГТУ, 2004.–318 с.
2. Сажин Б.С. Основы техники сушки. – М.: Химия, 1984. –320 с.
3. Удалов В.П. Расчет и проектирование теплоутилизаторов отходящих газов / Учебное пособие к курсовому проектированию по дисциплине: "Использование ВЭР теплотехнологических установок" для студентов специальности 100800.–Саратов: Изд. СГТУ, 1999. - 50с.
4. Павлова Г.А. Теплоутилизационные аппараты / Учебное пособие. – Магнитогорск: Изд. Магнитогорского ГТУ им. Г.И. Носова, 2000. - 68 с.