Локальная коррозия оборудования из нержавеющих сталей при эксплуатации установок переработки нефти 05. 17. 03 Технология электрохимических процессов и защита от коррозии
Вид материала | Автореферат |
- Состояние структуры, электрохимическое поведение и магнитные свойства наноструктурируемых, 327.79kb.
- Катодные процессы на силицидах металлов триады железа в кислых электролитах 05. 17., 237.17kb.
- Выделение серебра из концентрированных хлоридных растворов 05. 17. 03 Технология электрохимических, 229.4kb.
- Получение оптически селективных и чёрных оксидных плёнок на алюминии и его сплавах, 222.41kb.
- Коррозия металлов, 64.77kb.
- Электрохимическое получение наноразмерных pt/c катализаторов для твердополимерных топливных, 944.18kb.
- Аннотация дисциплины «коррозия и защита металлов», 13.74kb.
- Высокопроизводительные процессы электроосаждения никеля и сплава никель-фосфор из электролитов,, 468.58kb.
- Урок в 9-м классе по теме "Коррозия", 149.58kb.
- Нестационарные процессы деградации в щелочных аккумуляторах, закономерности и технологические, 585.56kb.
На правах рукописи
ПАРПУЦ Татьяна Петровна
ЛОКАЛЬНАЯ КОРРОЗИЯ ОБОРУДОВАНИЯ ИЗ НЕРЖАВЕЮЩИХ СТАЛЕЙ ПРИ ЭКСПЛУАТАЦИИ УСТАНОВОК ПЕРЕРАБОТКИ
НЕФТИ
05.17.03 – Технология электрохимических процессов и защита от коррозии
Автореферат
диссертации на соискание ученой степени
кандидата химических наук
Пермь
2007 г.
Работа выполнена в ОАО «Всероссийский научно-исследовательский институт нефтехимических процессов» (Санкт-Петербург)
Научный руководитель:
доктор технических наук,
старший научный сотрудник Бурлов Владислав Васильевич
Официальные оппоненты:
доктор химических наук,
профессор Кузнецов Юрий Игоревич
кандидат химических наук,
старший научный сотрудник Кичигин Владимир Иванович
Ведущая организация: ООО «ПО «Киришинефтеоргсинтез»
Защита состоится « » _____2007 г. в « » часов на заседании диссертационного совета Д.212.189.04 в Пермском государственном университете по адресу: 614990, г. Пермь, ул. Букирева, 15.
С диссертацией можно ознакомиться в библиотеке Пермского государственного университета.
Автореферат разослан « » ______2007 г.
Ученый секретарь
диссертационного Совета И.В. Петухов
ОБЩАЯ ХАРАКТЕРИСТИКА РАБОТЫ
Актуальность работы. Локальная коррозия металла оборудования нефтеперерабатывающих производств продолжает оставаться острой проблемой, несмотря на совершенствование опыта защиты от коррозии на заводах. Большинство аварийных ситуаций происходит гораздо чаще, чем можно было бы предсказать по результатам определения скорости общей коррозии. Это согласуется с результатами многолетних промышленных испытаний образцов и опытом эксплуатации оборудования установок. Наиболее часто выходы из строя оборудования связаны с локальными видами коррозии (питтинговой, язвенной, межкристаллитной и коррозионным растрескиванием) нержавеющих сталей, прогнозирование и контроль которых сложен и неоднозначен.
При исследовании локальных видов коррозии на установках нефтеперерабатывающих заводов (НПЗ), в основном, традиционно рассматривались агрессивность технологических сред и условия эксплуатации в рабочем технологическом режиме. Однако необходимо учитывать, что общая коррозионная стойкость металла определяется суммарным воздействием агрессивных сред на всех технологических этапах эксплуатации. При этом даже относительно незначительная длительность отдельных этапов (пропаривание аппаратов, осуществляемое перед проведением ремонтных работ, регенерации катализаторов, простои оборудования при ремонтах или по др. причинам) по сравнению с продолжительностью рабочего регламентного режима оказывает существенное влияние на общую коррозионную стойкость металла. Анализ и обобщение случаев локального коррозионного разрушения оборудования установок переработки нефти, выяснение влияния на процессы питтингообразования и коррозионного растрескивания сталей различных анионов, присутствующих в технологических средах на всех этапах эксплуатации, является актуальной задачей, решение которой позволит контролировать протекание коррозионных процессов и увеличить срок службы оборудования.
Цель работы. Исследование и оценка влияния различных факторов и состава (природы) коррозионной среды на локальное коррозионное разрушение аустенитных нержавеющих сталей при различных режимах эксплуатации установок переработки нефти.
В задачи исследования входило:
▪ обобщение опыта эксплуатации технологических установок НПЗ с учетом коррозионной агрессивности технологических сред и результатов технологического освидетельствования и ревизии оборудования;
▪ определение основного оборудования установок первичной переработки нефти и риформинга, способного подвергаться локальным коррозионным разриоды пропаривания, ремонта и простоев;
▪ исследование влияния различных технологических параметров и факторов на возникновение и развитие питтинговой, межкристаллитной коррозии и коррозионного растрескивания под напряжением аустенитных сталей (на примере стали 12Х18Н10Т);
▪ разработка технических указаний НПЗ по снижению вероятности возникновения локальных коррозионных поражений аустенитных сталей в процессе эксплуатации оборудования переработки нефти в различных режимах.
Научная новизна. Выявлены и систематизированы виды, особенности и причины локальных коррозионных поражений аустенитных сталей в условиях эксплуатации оборудования установок переработки нефти в различных режимах. Предложена и экспериментально обоснована принципиальная схема протекания локальных коррозионных процессов на нержавеющих сталях типа Х18Н10Т и аустенитных сварных швах в низко- и высокотемпературном оборудовании установок первичной переработки нефти и риформинга с указанием основных причин возникновения локальной коррозии на отдельных этапах функционирования установок.
Впервые химическим и электрохимическим методами систематически исследована стойкость аустенитных сталей (на примере стали 12Х18Н10Т) к питтинговой коррозии в водных растворах электролитов, моделирующих конденсаты пропаривания установок НПЗ, в широком диапазоне концентраций хлор-, сульфат-, тиосульфат-, сульфид-ионов и их соотношений в растворе.
Предложена система корреляционных зависимостей химических и электрохимических показателей питтингостойкости сенсибилизированной аустенитной стали (на примере стали 12Х18Н10Т) от состава раствора электролита, позволяющая прогнозировать вероятность зарождения питтинга на стадии пропаривания оборудования перед ремонтом.
Практическая ценность. Для снижения питтинговой коррозии и коррозионного растрескивания нержавеющих сталей и аустенитных сварных швов оборудования блоков предгидроочистки установок риформинга рекомендована и внедрена на ряде НПЗ водно-аммиачная промывка при эксплуатации установок в рабочем режиме, позволяющая практически полностью исключить вероятность возникновения локальной коррозии аппаратов и трубопроводов по тракту газопродуктовой смеси и нестабильного гидрогенизата.
Выданы технические рекомендации НПЗ о применении перлитных электродов типа ЦЛ17 (взамен аустенитных) для сварки трубопроводов из хромомолибденовых сталей с последующей термообработкой сварных соединений для снятия в них внутренних напряжений. Это позволит сократить случаи коррозионного растрескивания сварных швов трубопроводов установок.
Результаты промышленных испытаний коррозионной стойкости нержавеющих сталей в условиях переработки нефти и анализ причин локальных коррозионных поражений оборудования могут быть использованы для прогнозирования коррозионного поведения металлов на всех этапах эксплуатации оборудования и выдачи обоснованных рекомендаций по его материальному оформлению.
Результаты лабораторных исследований по определению стойкости нержавеющих сталей к питтинговой коррозии в растворах, моделирующих анионный состав сред пропаривания оборудования, позволят оценить возможность протекания питтинговой коррозии и могут быть использованы в качестве рекомендаций для оценки степени пропаривания для предотвращения образования питтингов на металле оборудования в процессе его очистки и, как следствие, уменьшения вероятности дальнейшего их развития в период ремонта и последующей эксплуатации аппаратов установок в рабочем режиме.
Апробация работы. Основные результаты работы докладывались на отраслевом совещании главных механиков нефтеперерабатывающих предприятий России и СНГ (Кириши, 2003 г.); на 7-ой международной научно-практической конференции «Новые материалы и технологии защиты от коррозии» (Санкт-Петербург, 2004 г.); на международной конференции «Физико-химические основы новейших технологий ХХ1 века (Москва, 2005 г.).
Публикации. По теме диссертации опубликовано 5 статей и 3 тезиса докладов.
Объем диссертации. Диссертация состоит из введения, 4 глав, выводов, списка литературы; содержит 160 стр., в т.ч. 15 таблиц и 41 рисунок, 161 ссылку на публикации отечественных и зарубежных авторов (на 15 стр.).
ОСНОВНОЕ СОДЕРЖАНИЕ РАБОТЫ
Во введении обоснована актуальность работы, сформулированы цель и задачи работы, научная новизна, практическая ценность, дана аннотация по главам и общая характеристика диссертации.
Глава 1 состоит из 2-х разделов и представляет собой литературный обзор, в котором систематизированы сведения о коррозионной агрессивности технологических сред в процессах переработки нефти и ее влиянии на стойкость оборудования из нержавеющих сталей. Обобщена информация об условиях возникновения, стадиях и механизмах образования питтинга на сталях типа 12Х18Н10Т в водных растворах электролитов.
Исследования локальных коррозионных поражений сталей типа Х18Н10Т и аустенитных сварных швов в условиях эксплуатации технологических установок нефтеперерабатывающих производств (глава 2)
Экспериментальные исследования проводились на закаленной и сенсибилизированной стали 12Х18Н10Т, как наиболее широко применяемой в нефтеперерабатывающей промышленности для изготовления оборудования. Стойкость к межкристаллитной коррозии сталей определялась по стандартному методу АМ по ГОСТ 6032. Оценка стойкости сталей к питтинговой коррозии проводилась в модельных водных растворах электролитов в соответствии с ГОСТ 9.912 по химическому и электрохимическому методам. В качестве активаторов питтингообразования исследованы анионы солей: NaCl, Na2SO4, Na2S2O3·5H2O, Na2S ·9H2O с добавлением НС1 до рН 4,5. Продолжительность испытаний химическим методом при температуре 20± 10С составляла ~400 ч. В качестве характеристик питтинговой коррозии принято среднее число питтингов на поверхности образца, глубина (h) и диаметр (d), в мм, самого глубокого питтинга, ПФ – питтинговый фактор (ПФ) и условный объем самого глубокого питтинга (V · 103, мм3).
П
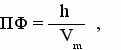
где: h- глубина самого глубокого питтинга, мм; Vm - скорость общей коррозии по изменению массы образца (за период испытаний), мм. Ошибка в расчете и определении ПФ - ±2% отн. Условный объем самого глубокого питтинга рассчитывается (с допущением о форме питтинга в виде шарового сегмента) по формуле: V = 1/6 π h (3r2 + h2), где V - объем, мм3; r - радиус плоского сечения, мм. Ошибка в расчете условного объема - ±5% отн.
По электрохимическому методу определены основные характеристики питтингостойкости: Еcor - потенциал свободной коррозии; Epc, Eb, Erp - граничные потенциалы питтинговой коррозии; ∆Epc - основной, ∆Eb, ∆Erp - дополнительные базисы питтингостойкости. Потенциодинамические кривые поляризации сенсибилизированной стали снимались в естественно аэрируемой модельной воде с помощью потенциостата ПИ 50-1.1 и двухкоординатного самописца ПДА-1 в открытой стеклянной трехэлектродной термостатированной ячейке. В качестве задатчика потенциала и постоянного тока использовался программатор ПР-8. Учитывая, что тиосульфат – ионы на исследуемом электроде способны подвергаться электрохимическим превращениям, протекающим параллельно с процессами образования пассивирующих слоев, проведены исследования по поляризации платинового электрода в тиосульфатных растворах.
Изучение структуры металла, характера и размеров коррозионных поражений проводилось металлографическим методом с использованием микроскопов «Neophot -21» и «Axivert» фирмы Zeiss (Германия) и программы Видео Тест-Мастер. Экспериментальная ошибка в определении геометрических размеров питтинга - ±0,002 мм.
На основании систематического обследования коррозионного состояния оборудования установок (коррозионный мониторинг, вырезка дефектных участков образцов с последующим металлографическим исследованием, дефектоскопия, визуальный контроль) обоснована и составлена схема протекания возможных локальных коррозионных процессов на сталях типа Х18Н10Т и аустенитных сварных швах и обсуждены основные причины коррозионных поражений металла (рис.1).
В наибольшей степени питтинговой коррозии и коррозионному растрескиванию подвержены сварные соединения плакирующих слоев аппаратов и аустенитные сварные швы трубопроводов из хромомолибденовой стали 15Х5М. Значительная часть разрушений приходится на периоды пропаривания и простоя, что связано со следующими основными факторами:
- при пропаривании происходит растворение отложений в аппаратуре с образованием конденсатов различной степени агрессивности, стекающих по стенкам;
- в оборудовании установок, несмотря на проведение пропаривания, всегда остаются отложения. Под действием кислорода при простое и пропаривании возрастает кислотность осадков в результате гидролиза и окисления сульфидов железа (продуктов коррозии стали на рабочем режиме) до сульфатов и соединений железа (II) до соединений железа (III), а также сульфидов железа до соединений серы более высокой валентности (политионовые кислоты, тиосульфаты, сульфиты и др.). Отложения гигроскопичны и способны адсорбировать влагу из воздуха при простое установок. В результате образуются коррозионно-агрессивные пасты, имеющие, как правило, кислую реакцию.
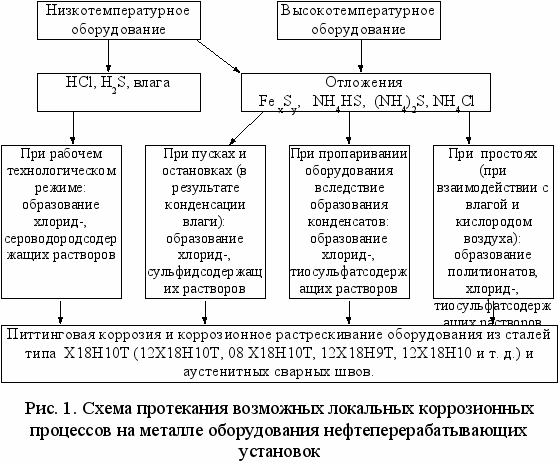
Таким образом, наиболее существенное, в иных случаях основное, влияние на коррозионную стойкость аустенитных сталей оказывает агрессивность сред, образующихся в условиях, отличных от рабочего технологического режима (пропаривание и простои оборудования). Об это свидетельствуют зафиксированные локальные разрушения аппаратов, эксплуатирующихся при высоких температурах, где конденсация влаги и, следовательно, протекание электрохимической коррозии невозможно на рабочем режиме, например, сварных швов плакирующих слоев атмосферных колонн.
Детальное изучение процессов коррозии в условиях эксплуатации оборудования переработки нефти в различных режимах позволило определить виды коррозионных разрушений и круг аппаратов с повышенной коррозионной агрессивностью среды, разработать принципиальные схемы установок с указанием возможных видов коррозионных разрушений и предложить варианты защиты от коррозии. Для защиты блоков предварительной гидроочистки установок риформинга по тракту газопродуктовой смеси предложена и внедрена на ряде заводов водно-аммиачная промывка в рабочем режиме, позволившая практически полностью исключить образование отложений, снизить концентрацию агрессивных компонентов в технологической среде и, как следствие, не менее чем в 20 раз – в конденсатах пропаривания и практически полностью исключить питтингообразование и коррозионное растрескивание металла аппаратов.
Исследование стойкости аустенитной нержавеющей стали 12Х18Н10Т к питтинговой коррозии в водных растворах электролитов, моделирующих конденсаты пропаривания установок НПЗ (глава 3)
Установление видов и скоростей коррозии металлов в процессе пропаривания весьма затруднительно в связи с технической сложностью обустройства аппаратуры зондами (или др. устройствами) для контроля за коррозионным состоянием образцов и малым сроком испытаний (до 120 ч). Однако даже начальные стадии зарождения питтинга в период пропаривания, не представляя большой опасности сами по себе, определяют его дальнейшее развитие в рабочем режиме эксплуатации, приводя в большинстве случаев к растрескиванию аппаратов. В связи с этим, вопрос о величинах концентраций коррозионно-активных компонентов в конденсатах пропаривания, при которых резко снижается вероятность питтингообразования, является одним из самых технически важных.
На основании многолетних экспериментальных исследований установлены границы изменения в конденсатах пропаривания оборудования установок ПО «КИНЕФ» концентраций основных ионов-активаторов:
▪ на установках первичной переработки нефти: [Cl-] от 1 до 900; [SO42-] от 10 до 900; [S2O32-] от 1 до 70 мг/дм3;
▪ на установках риформинга: [Cl-] от 10 до 8000; [SO42-] от 100 до 15000; [S2O32-] от 1 до 600 мг/дм3;
▪ на установках гидроочистки: [Cl-] от 1 до 1000; [SO42-] от 1 до 3000; [S2O32-] от 2 до 500 мг/дм3.
Учитывая данные по содержанию анионов в реальных конденсатах пропаривания основных установок НПЗ, для модельных экспериментов были выбраны интервалы концентраций: [Cl-] = 0-5000 мг/дм3 ( 0-140 ·10-3 г-ион/дм3);
[SO42-] = 0-5000 мг/дм3 (0-52·10-3 г-ион/дм3); [S2O32-] = 0-100 мг/дм3 (0-1,25 ·10-3 г-ион/дм3). Соотношения концентраций анионов (г-ион/дм3) изменялись в интервалах: [Cl-]/[SO42-] = 1,346-8,077; [Cl-]/[S2O32-] = 11,2-560; [SO42-]/[S2O32-] = 4,16-83,2.
В табл.1 приведены результаты коррозионных испытаний сенсибилизированной стали 12Х18Н10Т на стойкость к питтинговой коррозии в некоторых модельных растворах.
Таблица 1.
Результаты ускоренных коррозионных испытаний сенсибилизированной стали 12Х18Н10Т на стойкость к питтинговой коррозии в некоторых модельных растворах рН ~ 4,5, содержащих Сl-, SO42-, S2О32-, по химическому методу
ГОСТ 9.912. τ
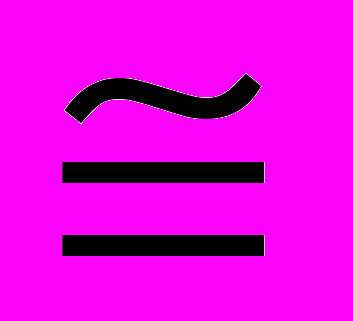
Конц. в растворе, мг/дм3 | Потеря массы, г/м2 сутки | Среднее число питтингов | Хар-ка самого глубокого питтинга | V· 103, мм3 | ПФ | |||
Сl- | SO42- | S2O32- | ||||||
h, мм | d, мм | |||||||
500 | 0 | 0 | 0,040 | Питтинги отсутствуют | ||||
0 | 500 | 0 | 0,028 | |||||
500 | 500 | 0 | 0,036 | |||||
0 | 0 | 100 | 0,026 | |||||
500 | 0 | 100 | 0,0075 | 3 | 0,008 | 0,103 | 0,330 | 503,1 |
0 | 500 | 100 | 0,215 | 10 | 0,22 | 0,480 | 25,450 | 480,5 |
5000 | 5000 | 100 | 0,492 | 22 | 0,028 | 0,148 | 0,252 | 26,7 |
5000 | 500 | 100 | 0,640 | 2 | 0,200 | 0,662 | 38,560 | 146,7 |
1000 | 1000 | 100 | 0,465 | 12 | 0,080 | 0,288 | 2,870 | 80,8 |
1000 | 500 | 100 | 0,170 | 12 | 0,240 | 0,992 | 38,110 | 663,0 |
500 | 1000 | 100 | 0,295 | 15 | 0,088 | 0,458 | 7,597 | 141,5 |
500 | 500 | 100 | 0,280 | 24 | 0,180 | 0,600 | 28,468 | 337,7 |
500 | 500 | 50 | 0,420 | 13 | 0,090 | 0,180 | 1,525 | 100,6 |
500 | 500 | 40 | 0,412 | 5 | 0,088 | 0,209 | 1,864 | 100,2 |
500 | 500 | 25 | 0,367 | 4 | 0,048 | 0,135 | 0,401 | 61,4 |
500 | 500 | 10 | 0,296 | 11 | 0,030 | 0,153 | 0,289 | 47,6 |
100 | 100 | 10 | 0,308 | 25 | 0,042 | 0,193 | 0,652 | 61,0 |
500 | 500 | 5 | 0,018 | Питтинги отсутствуют* | ||||
100 | 100 | 5 | 0,159 | Питтинги отсутствуют | ||||
500 | 500 | 2 | 0,018 |
*питтинги имеют место на торцах
В хлоридных, сульфатных и хлоридно-сульфатных растворах в отсутствие S2O32- питтинги на сенсибилизированной и закаленной стали за период испытаний не зафиксированы, что возможно связано с торможением катодного процесса из-за недостаточной концентрации деполяризатора – кислорода (проведение опытов в закрытом сосуде без перемешивания). В тиосульфатном растворе питтинги на стали не образуются, по-видимому, вследствие отсутствия ионов С1- и SO42-, инициирующих питтингообразование. Полученные данные согласуются с существующим представлениям о процессе питтингообразования на нержавеющих сталях и указывают на то, что тиосульфат-ион выступает в качестве катодного деполяризатора и стабилизатора питтинга по реакции:
S2O32- + 6Н+ + 4е-

Об этом свидетельствуют результаты опытов, где питтинги инициированы хлоридами (или сульфатами) в присутствии тиосульфат-ионов. Нами впервые обнаружено, что питтинги в сульфатном растворе в присутствии S2O32- в несколько раз глубже, чем в хлоридном, даже при их большем количестве. Это, по-видимому, можно объяснить участием сульфат-ионов в катодных реакциях, стабилизирующих питтинг:
SO42- + 8Н+ + 6е-

В хлоридных растворах (без сульфат-ионов) в присутствии тиосульфат-ионов с ростом концентрации С1- размеры питтинга увеличиваются, что совпадает с представлениями ряда авторов о роли хлор-иона в качестве подкислителя в формировании питтинга. Показатели питтингообразования на сенсибилизированной стали зависят как от абсолютных концентраций агрессивных ионов в растворах, так и их соотношений.
Полученные результаты являются наглядной иллюстрацией роли тиосульфат-иона не только как катодного деполяризатора, но и стабилизатора питтинга, усиливающего действие хлор- и сульфат-ионов при недостаточной концентрации последнего для пассивации питтинга (рис.2).
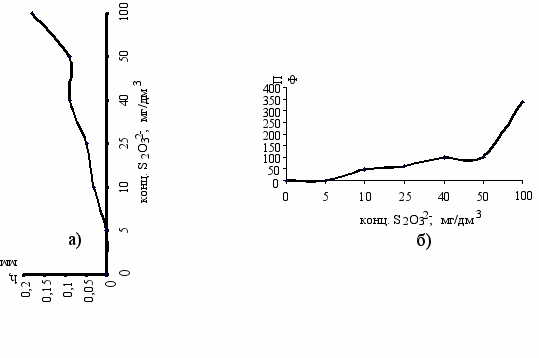
Рис. 2. Зависимость характеристик питтингов на сенсибилизированной стали 12Х18Н10Т от концентрации тиосульфат-ионов в модельных растворах конденсатов пропаривания при содержании хлор - и сульфат-ионов по 500 мг/ дм3:
а) глубина питтинга (h, мм); б) питтинговый фактор (ПФ).
В большинстве из исследованных растворов электролитов на закаленной стали 12Х18Н10Т питтинги не возникают.
Однако при их появлении ПФ и геометрические размеры для закаленной стали больше, чем для сенсибилизированной стали в одних и тех же электролитах. Это объясняется, прежде всего, тем, что общая скорость коррозии закаленной стали ниже, чем сенсибилизированной. Большая глубина питтингов на закаленной стали обусловлена различием числа образовавшихся питтингов: на закаленной стали процесс анодного растворения концентрируется в редких питтингах, в то время как на сенсибилизированной - распространяется на большее количество, тем самым приводя к уменьшению катодного тока, необходимого для развития и стабилизации питтинга, и соответствующему уменьшению их размеров.
Общие закономерности изменений в характеристиках питтингообразования в растворах электролитов при повышении рН раствора с 4,5 до ~6,8 с ростом концентрации S2O32- сохраняются. Однако геометрические размеры питтингов, образовавшихся при рН ~6,8, и ПФ больше, чем при рН ~4,5. Причин этого явления может быть несколько. При увеличении рН раствора могут тормозиться реакции 1 и 2, но и становится возможным протекание реакций анодного окисления тиосульфат-иона:
S2O32- +Н2О - 2е-


вызывающих закисление раствора в питтинге, а также серии других реакций с участием S0, приводящих к каталитическому растворению металла в питтинге: S0 + 2Н+ + 2е-


FeНS-адс


Большое количество теоретически возможных реакций на поверхности стали и в глубине питтинга усугубляют сложность интерпретации полученных результатов, которая может носить только предположительный характер.
Из рассмотрения экспериментальных данных становится очевидным, что ПФ (или V) одновременно зависит от концентраций ионов и их отношений (от X и Z), т.е. зависимости вида ПФ (или V) = f (Х1,Х2,Х3) или
ПФ (или V) = f (Z1, Z2,Z3) не могут быть использованы для построения корреляционных зависимостей показателей питтингостойкости стали от состава агрессивного раствора. Наиболее правильным является представление искомых зависимостей в виде ПФ (или V) = f (Х1, Х2, Х3, Z1, Z2, Z3) (9).
Здесь: Х1,Х2,Х3 – концентрации, г-ион/дм3, соответственно, С1-, SO42- и S2O32-;
Z1 = [Cl-] / [SO42-] , Z2 = [Cl-]/[S2O32-] и Z3 = [SO42-]/[S2O32-].
Аппроксимация экспериментальных результатов математическими зависимостями проведена с помощью векторно-матричной лаборатории МАТLАВ 6.5 с использованием метода сингулярного разложения матрицы исходных данных (оператор SVD), который обеспечивает наилучшую сходимость экспериментальных и расчетных результатов для прямоугольных (неквадратных) матриц. В массив данных, использованных для построения корреляционной зависимости вида (9) были включены данные опытов, в которых концентрации всех анионов отличны от нуля. Расчетные значения ПФ наиболее близки к экспериментальным по полиномиальной зависимости 4-ой степени (10). Разница составляет не более ±2% отн., что находится в пределах экспериментальной ошибки в определении ПФ.
Y = b1· x1 + b2· x2 + b3· x3 + b4 · z1 + b5 · z2 + b6 · z3 + b7 · x21 + b8 · x22 + b9 · x23 +
+ b10 · z12 + b11 · z22 + b12 · z32 + b13 · x13 + b14 · x23 + b15 · x33 + b16 · z13 + b17 · z23 + b18 · z33 + b19 · x14 + b20 · x24 + b21 · x34 + b22 · z14 + b23 · z24 + b24 · z34 (10),
где Y = ПФ или Y = V · 102, b1 b24 - коэффициенты полинома.
На основе формальных корреляционных зависимостей сложно делать выводы о преимущественном влиянии концентраций анионов и их соотношений на показатели питтингостойкости стали, но можно считать твердо установленным, что ПФ (и V) увеличиваются при росте концентраций хлор - и тиосульфат-ионов и отношений [Cl-] / [SO42-] и [Cl-]/[S2O32-] и уменьшаются при увеличении концентрации сульфат-иона и отношения [SO42-]/[S2O32-].
Предложенная методология оценки ПФ (или V) имеет определенные ограничения. На основании полинома (10) с наибольшей достоверностью может быть оценена вероятность появления питтингов в концентрационных пределах: С1- и SO42- от 100 до 1000; S2O32- от 5 до 100 мг/дм3, расширение которых в сторону значительного увеличения, или уменьшения резко снижает точность прогнозирования, особенно при Х и Z, выходящих за границы матрицы, использованной при определении коэффициентов b1 …b24, при этом по корреляционной зависимости можно оценивать только возможность появления питтинга (в основном, знак и порядок величин, иначе говоря, вероятность появления питтинга).
Электрохимические исследования стойкости сенсибилизированной стали 12Х18Н10Т к питтинговой коррозии в водных растворах электролитов (глава 4)
Результаты исследований стойкости сенсибилизированной стали 12Х18Н10Т к питтинговой коррозии в водных растворах электролитов электрохимическим методом ГОСТ 9.912 сведены в табл.2.
Таблица 2.
Электрохимические характеристики сенсибилизированной стали 12Х18Н10Т в водных растворах, содержащих Сl-, SO42-, S2O32-. рН ~ 4,5.
Условный № опыта | Конц. в растворе, мг/дм3 | Электрохимические характеристики (±0,03 В) | ||||||||
Сl- | SO42- | S2O32- | Ecor, B | Epc, B | Eb, B | Erp, B | ∆Epc, B | ∆Eb, B | ∆Erp, B | |
1 | 500 | 0 | 0 | 0,17 | 0,49 | 0,49 | 0,36 | 0,32 | 0,32 | 0,19 |
2 | 0 | 500 | 0 | 0,31 | - | 1,45 | 1,48 | - | 1,14 | 1,17 |
3 | 500 | 0 | 100 | 0,06 | 0,12 | 0,14 | 0,06 | 0,06 | 0,08 | 0,00 |
4 | 0 | 500 | 100 | 0,28 | - | 1,40 | 1,40 | - | 1,11 | 1,11 |
5 | 500 | 500 | 0 | 0,29 | 0,45 | 0,99 | 0,38 | 0,16 | 0,70 | 0,09 |
6 | 500 | 500 | 10 | 0,22 | 0,40* | 0,94 | 0,09 | 0,18 | 0,72 | -0,13 |
7 | 500 | 500 | 25 | 0,18 | 0,30* | 0,87 | -0,09 | 0,12 | 0,69 | -0,27 |
8 | 500 | 500 | 50 | -0,04 | 0,08 | 0,05 | -0,06 | 0,12 | 0,09 | -0,02 |
9 | 500 | 500 | 100 | -0,02 | 0,02 | 0,03 | -0,03 | 0,04 | 0,05 | 0,04 |
10 | 500 | 1000 | 100 | -0,06 | 0,04* | 0,02 | -0,07 | 0,10 | 0,08 | 0,05 |
11 | 1000 | 500 | 100 | -0,04 | 0,00 | 0,01 | -0,04 | 0,04 | 0,05 | 0,00 |
12 | 1000 | 1000 | 10 | 0,14 | 0,45 | 0,66 | 0,33 | 0,31 | 0,52 | 0,19 |
13 | 1000 | 1000 | 100 | -0,06 | -0,05 | 0,01 | -0,07 | 0,01 | 0,07 | -0,01 |
14 | 250 | 750 | 50 | -0,06 | 0,13 | -0,02 | -0,06 | 0,19 | 0,04 | 0,00 |
15 | 750 | 250 | 50 | -0,03 | -0,01 | 0,02 | -0,05 | 0,02 | 0,05 | -0,02 |
16 | 100 | 100 | 2 | 0,18 | 0,53 | 1,35 | 0,41 | 0,35 | 1,17 | 0,23 |
17 | 100 | 100 | 5 | 0,22 | 0,40* | 1,47 | 0,00 | 0,18 | 1,25 | -0,22 |
18 | 100 | 100 | 10 | 0,22 | 0,34* | 1,08 | 0,00 | 0,12 | 0,86 | -0,22 |
19 | 5000 | 500 | 100 | -0,07 | -0,05 | -0,04 | -0,08 | 0,02 | 0,03 | -0,01 |
20 | 5000 | 5000 | 100 | -0,11 | 0,11* | 0,23 | -0,11 | 0,22 | 0,34 | 0,00 |
*)Определение Ерс вызывало определенные затруднения из-за значительных колебаний потенциала при гальваностатической поляризации.
В чисто сульфатном растворе (оп.2) сталь находится в устойчивом пассивном состоянии. На потенциодинамической кривой поляризации отсутствует область активного растворения вплоть до Е = 1,45В, соответствующего перепассивации стали.
Введение сульфат-ионов в хлоридсодержащие растворы приводит к повышению потенциала питтингообразования Еb, что указывает на их ингибирующее действие. В хлоридно-сульфатных растворах сталь подвергается питтинговой коррозии без наложения поляризации (Есоr ≈ Егр) при концентрации S2O32- 50-100 мг/дм3 независимо от соотношения в них С1- и SO42- (оп.9-11, 13-15, 19,20 – табл.2). В этих растворах в сравнении с растворами с концентрацией S2O32- <50 мг/дм3 не только значения базисов питтингостойкости ниже, но Есоr на 150-250 мВ более отрицательны и на потенциодинамических кривых исчезает область пассивности. По мере увеличения концентрации хлор-ионов при постоянном содержании тиосульфат-ионов (100 мг/дм3) наблюдается обычная тенденция к разблагораживанию Ерс (оп.9,11,19). При более высоком относительном содержании сульфат-ионов (оп.10 и оп.14), а также при [Cl-]/[SO42-] = 1:1 (оп.20) с максимально высоким содержанием сульфат-иона в ходе поляризации отмечаются значительные амплитуды колебаний потенциалов, причем в оп.10 и 14 Ерс>Еb, что не совсем согласуется с представлениями о питтингообразовании на стали: Еb должен быть больше, чем Ерс, что, по-видимому, связано с неустойчивостью пассивного состояния стали вследствие конкурирующих процессов с участием хлор-, сульфат-ионов в присутствии восстановителя S2O32- .
Базисы питтингостойкости ∆ Ерс и ∆Еb (метастабильной пассивности) с увеличением концентрации тиосульфат-иона уменьшаются, что указывает на снижение питтингостойкости. Зависимость ∆Еrp (устойчивой пассивности) от концентрации S2O32- значительно сложнее. При малых концентрациях тиосульфат-иона (10-25 мг/дм3) Еrp на ~200 мВ отрицательнее Есоr. С ростом концентрации S2O32- Еrp смещается к Есоr и при [S2O32-] = 100 мг/дм3 Есоr ≈ Егр, что указывает на возможность протекания питтинговой коррозии без анодной поляризации.
Питтинги, образовавшиеся в ходе экспериментов по химическому методу, имели большие геометрические размеры, чем при электрохимических исследованиях. Причины этого понятны, т.к. связаны с разницей в продолжительности экспериментов и c неустойчивостью системы при поляризации стали. С увеличением концентрации тиосульфат-ионов геометрические размеры питтингов, образовавшихся после гальваностатической и потенциодинамической поляризаций, уменьшаются. Причиной такой зависимости, обратной полученной при испытаниях стали химическим методом явилась, по-видимому, неустойчивость системы при малых концентрациях тиосульфат-иона, о чем свидетельствуют периодические колебания анодного тока на анодной поляризационной кривой (рис.3).
Стимулирующее действие тиосульфат-ионов может быть объяснено электрохимическими превращениями тиосульфат-ионов с образованием на поверхности стали серы и других серусодержащих соединений.
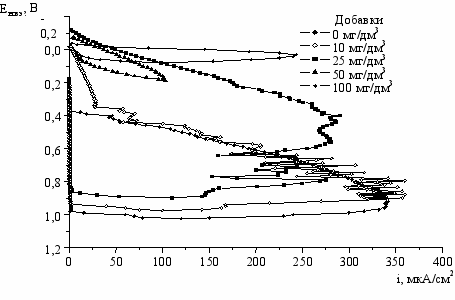
Рис. 3. Потенциодинамические кривые поляризации стали в растворах, содержащих по 500 мг/дм3 Cl- и SO42-, с добавками S2O32-.
Из поляризационных кривых на платине в растворах без и с добавками S2O32- следует, что введение в раствор тиосульфат-ионов приводит к повышению анодных токов и смещению Ест в отрицательную область, причем сдвиг Ест (относительно базового раствора) в хлоридном растворе больше (от 0,63 В до 0,44 В), чем в смешанном хлорид-сульфатном растворе (от 0,59 В до 0,47 В). Полученные результаты свидетельствуют о преимущественном протекании на платине анодных реакций окисления тиосульфат-ионов. По-видимому, это справедливо и для превращений тиосульфат-ионов на поверхности стали:
2S2O32- - 2е-

В то же время незначительное увеличение катодного тока свидетельствует о возможном протекании реакций (1) и (5), а также:
S2O32- + 8е- + 8Н+

S2O32- + 6е- + 6Н+


В присутствии сульфат-ионов возможно протекание реакции (2) при катодной поляризации, о чем свидетельствует меньший сдвиг Ест и повышение анодного тока в хлоридно-сульфатном растворе. Таким образом, стимулирование процесса питтингообразования на сенсибилизированной стали добавками тиосульфат-ионов к хлоридно-сульфатным растворам может быть объяснено преимущественным протеканием реакций анодного окисления тиосульфат-ионов, а также реакции восстановления тиосульфатов до серы.
Для описания зависимостей основного (∆Ерс) и дополнительных (∆Еrр и ∆Еb) базисов питтингостойкости сенсибилизированной стали 12Х18Н10Т от состава раствора электролита была использована полиномиальная зависимость 3-ей степени, где у = ∆Ерс (или ∆Еrр, или ∆Еb), при этом достигнута высокая точность расчета - 2% отн (см. уравнение 10).
В результате анализа корреляционных зависимостей химических и электрохимических показателей питтингостойкости сенсибилизированных аустенитных сталей (на примере 12Х18Н10Т) от состава растворов электролитов может быть сделан вывод о целесообразности проведения операций пропаривания установок до содержания в дренажных водах: тиосульфат-ионов – не более 5 мг/дм3; хлор- и сульфат-ионов – не более 100-150 мг/дм3, при этом допустимо превышение концентрации сульфат-ионов по отношению к хлор-ионам до 2-х кратного и недопустимо обратное соотношение. При достижении рекомендуемых величин вероятность зарождения питтингов на этапе пропаривания и их дальнейшего развития на аустенитных сталях, особенно на сенсибилизированных участках (сварные швы), в период ремонта и при последующей эксплуатации установок в рабочем режиме существенно снижается.
В Ы В О Д Ы
1. На основе экспериментальных данных промышленных испытаний, результатов технического освидетельствования и ревизии оборудования выявлены и систематизированы виды, особенности и причины локальных коррозионных поражений аустенитных нержавеющих сталей на всех этапах эксплуатации установок переработки нефти.
2. Предложена и экспериментально обоснована принципиальная схема протекания локальных коррозионных процессов на сталях типа Х18Н10Т и аустенитных сварных швах в низко- и высокотемпературном оборудовании установок первичной и вторичной переработки нефти на различных технологических этапах эксплуатации.
3. Показано, что основными причинами локальной коррозии аустенитных сталей и аустенитных сварных швов является наличие агрессивных компонентов в технологических средах, накопление отложений в аппаратах и трубопроводах при эксплуатации в рабочем режиме, образование агрессивных конденсатов (растворов электролитов) при пропаривании оборудования перед ремонтом, агрессивных паст при взаимодействии остающихся на стенках аппаратов отложений с атмосферной влагой в период ремонта установок.
4. Обоснован состав растворов, моделирующих конденсаты пропаривания основного оборудования нефтеперерабатывающих и нефтехимических производств для исследования стойкости аустенитных сталей к питтинговой коррозии.
5. Впервые химическим и электрохимическим методами в соответствии с ГОСТ 9.912 детально исследована склонность аустенитных сталей к питтинговой коррозии (на примере стали 12Х18Н10Т в закаленном и сенсибилизированном состоянии) в растворах электролитов, моделирующих состав конденсатов пропаривания в широком диапазоне концентраций анионов и их соотношений: концентрации хлор и сульфат-ионов – от 0 до 5000 мг/дм3, тиосульфат-ионов – от 0 до 100 мг/дм3, сульфид-ионов - от 0 до 100 мг/дм3. Установлено, что в растворах, моделирующих конденсаты пропаривания, сенсибилизированные нержавеющие стали более склонны к питтинговой коррозии, чем закаленные.
6. Показано, что основные факторы, характеризующие стойкость аустенитной стали (на примере сенсибилизированной стали 12Х18Н10Т), к питтинговой коррозии:
▪ питтинговый фактор и условный объем самого глубокого питтинга, определяемые химическим методом;
▪ гальваностатический (∆Ерс ) и потенциодинамические ( ∆Еrр, ∆Еb) базисы питтингостойкости, определяемые по поляризационным кривым, зависят от концентраций агрессивных анионов и их соотношений в растворах.
7. Впервые предложена система корреляционных (функциональных) зависимостей химических и электрохимических показателей питтингостойкости сенсибилизированной аустенитной стали (на примере стали 12Х18Н10Т) от состава раствора электролита, позволяющая прогнозировать вероятность зарождения питтинга в конденсатах пропаривания оборудования установок НПЗ перед ремонтом.
8. Показано, что предложенная система корреляционных (функциональных) зависимостей позволяет оценивать необходимую степень очистки оборудования при пропаривании, обеспечивающую снижение вероятности образования питтингов на стали на этапе пропаривания и их дальнейшего развития в период простоев при ремонтах и при последующей эксплуатации установок в рабочем режиме.
9. В результате электрохимических исследований на платине в хлоридно-сульфатных растворах, содержащих тиосульфат-ионы, показано, что стимулирующее действие тиосульфат-ионов на питтингообразование стали связано с преимущественным протеканием реакций анодного окисления с участием тиосульфат-ионов и воды.
10. Обоснована возможность снижения питтингообразования и коррозионного растрескивания нержавеющих сталей и аустенитных сварных швов в оборудовании и сформулированы следующие рекомендации нефтеперерабатывающим заводам:
▪ применение на блоках предварительной гидроочистки установок рифор-
минга водно-аммиачной промывки при эксплуатации оборудования в рабочем режиме (по тракту газопродуктовой смеси и нестабильного гидрогенизата);
▪ выполнение сварки хромомолибденовых сталей перлитными электродами типа ЦЛ17 (взамен аустенитных) с последующей термообработкой сварного соединения для снятия в нем внутренних напряжений.
Публикации по теме диссертации
- Тесля Б.М., Демешко О.А., Андреева Г.А., Парпуц Т.П. Коррозионная стойкость печных змеевиков при регенерации катализаторов риформинга
// Химия и технология топлив и масел. № 8. 1985. С. 9-12.
- Бурлов В.В., Парпуц И.В., Парпуц Т.П. Коррозионное растрескивание аустенитных сварных швов оборудования и мероприятия по его предотвращению // В кн.: Материалы отраслевого совещания гл. механиков нефтеперераб. и нефтехимич. предприятий. Кириши, 7-10 декабря 2003 г. М.: Компрессорная и хим.техника. 2004. С. 69-76.
- Бурлов В.В., Парпуц Т.П. Исследование питтингообразования на нержавеющих сталях в водных средах, моделирующих конденсаты пропаривания установок нефтеперерабатывающих заводов // Тезисы докладов 7 межд. научно-практической конференции «Новые материалы и технологии защиты от коррозии». СПб: Ленэкспо. 2004. С. 47.
- Бурлов В.В., Парпуц И.В., Парпуц Т.П. Коррозионное растрескивание сварных швов нефтеперерабатывающего оборудования, выполненного с плакирующим слоем из стали 08Х13 // Коррозия: материалы, защита. 2004. № 7. С. 22-35.
- Бурлов В.В., Парпуц И.В., Парпуц Т.П. Проблема локальных коррозионных поражений нержавеющих сталей и аустенитных сварных швов в условиях эксплуатации оборудования технологических установок переработки нефти // В кн. «Процессы нефтепереработки и нефтехимии». СПб: ГИОРД. 2005.
С. 271-289.
- Парпуц Т.П., Алцыбеева А.И., Бурлов В.В., Кузинова Т.М., Кузичкин Н.В. Исследование зависимости величины питтингового фактора сенсибилизированной стали 12Х18Н10Т от содержания агрессивных ионов (С1-, SO42-, S2O32-) в водных растворах, моделирующих конденсаты пропаривания установок НПЗ // Там же. С. 248-258.
- Бурлов В.В., Парпуц И.В., Парпуц Т.П. Локальные коррозионные поражения оборудования из стали Х18Н10Т и аустенитных сварных швов в процессах нефтепереработки // Вестник УДГУ, сер. Химия. Ижевск. 2005. № 8.
С. 3 -12.
- Парпуц Т.П., Алцыбеева А.И., Бурлов В.В., Кузинова Т.М. , Кузичкин Н.В. Зависимость величины питтингового фактора сенсибилизированной стали 12Х18Н10Т от содержания агрессивных ионов в водных растворах электролитов // Тезисы докл. межд. конференции «Физико-химические основы новейших технологий ХХ1 века». М.: ИФХ РАН. 2005. Т.2. С. 166.
50>