Системы управления товарно-материальными запасами при независимом спросе в этой главе
Вид материала | Документы |
- План и программа аудиторской проверки операций 26 с материальными запасами Выводы, 109.95kb.
- Кафедра экономики и управления курсовая работа по курсу: «Информационные технологии, 872.46kb.
- Оптимизационные модели и методы управления товарно-материальными запасами 08. 00., 408.67kb.
- Тема Планирование и управление товарно-материальными запасами, 367.45kb.
- Задачи и функции производственной логистики. Основы управления материальными потоками, 28.34kb.
- Реферат по дисциплине «Математические методы системного анализа и теории принятия решений», 254.37kb.
- Управление запасами, 346.19kb.
- Задачи дипломной работы: рассмотреть понятие, сущность и виды запасов на предприятии;, 167.6kb.
- Иложение для анализа движения товарно-материальных ценностей на предприятии, являющееся, 23.66kb.
- Тема: «Информационные технологии в управлении материальными запасами», 428.38kb.
ГЛАВА 15
Системы управления товарно-материальными запасами
при независимом спросе
В этой главе...
Сущность товарно-материальных запасов
Цели создания товарно-материальных запасов
Расходы, связанные с поддержанием запаса
Зависимый и независимый спрос
Системы управления запасами
Модели с фиксированным объемом
Модели с фиксированным периодом
Специальные модели
Другие системы и проблемы
Резюме
Ключевые термины
ABC-анализ (ABC Analysis)
Готовая (конечная) продукция (Finished Products)
Двухбункерная система (Two-Bin System
Единица учета запасов (Storekeeping Unit – SKU)
Модель со ступенчатой (переменной) ценой) (Price-Break Model)
Модель с фиксированным объемом – Q-модель (Fixed-Order Quantity Model)
Модель с фиксированным периодом – P-модель (Fixed-Time Period Model)
Незавершенное производство (Work in Process)
Независимый и зависимый спрос (Independent and Dependent Demand)
Однобункерная система (One-Bin System)
Однопериодная модель (Single-Period Model)
Размер заказа при ступенчатой цене (Price-Break Order Quantity)
Резервный запас (Safety Stock)
Сырье (Raw Materials)
Товарно-материальные запасы (Inventory)
Точность учета запасов (Inventory Accuracy)
Уровень запаса (Inventory Position)
Уровень обслуживания (Service Level)
Циклический переучет (Cycle Counting)
Ресурсы WWW
Ford Motor (
General Motors (ссылка скрыта)
Wal-Mart (http: //www. wal-mart. com)
Стремясь продать потребителю именно такой автомобиль, какой ему нужен, и обеспечить доставку заказанного товара в пределах суток с момента заказа, компания General Motors всерьез задумалась над изменением способа поставки готовой продукции своим дилерам.
По утверждению хорошо осведомленных людей, в соответствии с новой программой, которая должна охватить все модели GM, большие запасы легковых автомобилей и легких грузовиков будут храниться не на складах, принадлежащих дилерам, а в региональных сбытовых центрах, размещенных по всей территории США. В результате дилер, на складе которого нет нужной модели, сможет в течение суток получить ее в соответствующем региональном центре.
По оценкам GM, примерно 35% покупателей автомобилей не могут найти у дилеров именно ту модель, которая им нужна, и вынуждены идти на тот или иной компромисс; еще 21% прибегают к услугам другого дилера, а 11% просто покупают автомобили других изготовителей. Остальные покупают тот тип автомобиля, о котором у них сложилось некое обобщенное представление.
План, разработанный в GM, заключается в том, чтобы существенно расширить программу под названием Custom Xpress Delivery, которая уже выполняется в подразделении, отвечающем за сбыт автомобилей марки Cadillac. GM использовала программу Cadillac (реализация которой началась два года тому назад, с ввода в действие регионального сбытового центра в Орландо, штат Флорида) с экспериментальной целью для выявления и устранения ошибок, которые неизбежно присутствуют в любых новых системах, и чтобы дать дилерам возможность привыкнуть к переменам (http: //gm. com).
По утверждению Ford Motor, они рассматривали концепцию региональных сбытовых центров, но решили все же проверить другую концепцию, которая сохраняет в неизменном виде их прежнюю систему сбыта, однако предусматривает изменение системы производства для сокращения времени исполнения в основном специальных заказов до 15—20 дней. Ford испытывает эту программу применительно к автомобилям марки Mustang и собиралась распространить ее на автомобили других марок к концу 1998 года (.
Источник. Gabriella Stern, "GM Expands Plan to Speed Cars to Byers", The Wall Street Journal, October 21, 1996. Перепечатано с разрешения The Wall Street Journal © 1996 Dow Jones & Company, Inc. Все права защищены по всему миру.
Зададим себе вопрос: зачем СМ нужно вносить подобные изменения в свою систему сбыта? Ответить на этот вопрос не так-то просто. Все сводится к проблеме обслуживания и затрат. Что лучше: множество небольших складов, принадлежащих разным дилерам, или несколько крупных складов, в которых потребители могут быстро получить приглянувшийся им автомобиль? Математически можно показать, что GM могла бы обеспечить более качественное обслуживание и сократить затраты на поддержание товарно-материальных запасов, отдав предпочтение варианту со сбытовыми центрами. Есть ли еще какие-то факторы? Действительно ли потребители хотят иметь все разнообразие вариантов? Может быть, потребитель предпочел бы обратиться к крупному дилеру, на площадке которого можно найти весь спектр выпускаемых автомобилей? Интересно было бы убедиться в дееспособности подхода, избранного GM.
Рассмотрим следующие соображения. Средние затраты на поддержание запасов по всем производителям в Соединенных Штатах Америки составляют 30-35% стоимости этих запасов. Если, например, фирма хранит запас стоимостью 20 миллионов долларов, это обойдется фирме в 6 миллионов долларов в год. Эти расходы связаны со старением и износом, страхованием, издержками неиспользованных возможностей и т.п. Если, например, объем запасов сократить до 10 миллионов долларов, фирма сэкономила бы свыше 3 миллионов долларов, которые стали бы ее чистой прибылью. Другими словами, экономия в результате сокращения запасов оборачивается повышением прибыли.
В этой главе мы представляем стандартные модели товарно-материальных запасов, которые должны помочь руководству сэкономить часть расходов, удовлетворив одновременно с этим производственные требования, а также требования к обслуживанию потребителей. Кроме того, здесь приведено описание моделей специального назначения (например, при ступенчатом снижении цены — Price-Break), а также ABC-метода. В этой главе мы также обсудим понятие точности запаса и продемонстрируем применение описанных моделей в магазинах и системах снабжения запчастями для автомобилей.
Что касается методики изложения классических моделей управления товарно-материальными запасами, то на этот счет существуют противоположные точки зрения. Одни утверждают, что модели экономичного размера заказа (Economic Order Quantity — EOQ) неправильны. Другие, наоборот, настаивают на необходимости их использования. Мы полагаем, что правы обе стороны — каждая со своих собственных позиций. Если подходить к использованию этих моделей с известной осторожностью, то в некоторых ситуациях, нередко встречающихся в производстве, применение EOQ-моделей вполне оправданно. Например, JIT-производство основано на обсуждаемой в этой книге классической модели управления товарно-материальными запасами для производства и потребления. Классические модели вполне подходят для многих тысяч компаний, занимающихся сбытом продукции и комплектующих.
Что же касается JIT и резервного (буферного) запаса, то можно вспомнить, что JIT предусматривает резервный запас! Это объем или количество заготовок в контейнерах между каждыми двумя соседними участками (станциями) в производственной цепочке. Кроме того, системами, подобными JIT, пользуются все изготовители, поставляющие запчасти и комплектующие. Изготовитель, использующий у себя систему JIT, комплектующие для которой поставляются на производственную линию дважды в день, наверное удивится, узнав, что его поставщик однократно выпускает месячную норму этих комплектующих, руководствуясь формулой EOQ! Выбор метода определения потребности в запасе зависит от многих факторов и для этого годятся все методы — при условии, что они соответствуют конкретным обстоятельствам. Поэтому придется познакомиться со всеми ними.
Сущность товарно-материальных запасов
Товарно-материальный запас (Inventory) — это запас какого-либо ресурса или предметов, используемых в организации. Система управления товарно-материальными запасами (Inventory System) — это совокупность правил и способов регулирования, с помощью которых можно контролировать уровни запасов и определять, какие уровни следует поддерживать, какой запас следует пополнять и каким должен быть объем заказа.
Этот рекламный плакат от GE Information Services указывает на одну из главных проблем, с которыми сталкиваются компании: несмотря на то, что товарно-материальный запас является достоянием компании, он может приносить ей убытки, если хранится слишком долго. Текст на плакате поясняет суть услуг, предоставляемых GE. Эти услуги включают рекомендации по установлению электронной связи с поставщиками, производителями и дистрибьюторами, которая помогает избежать дорогостоящего хранения запасов.
П
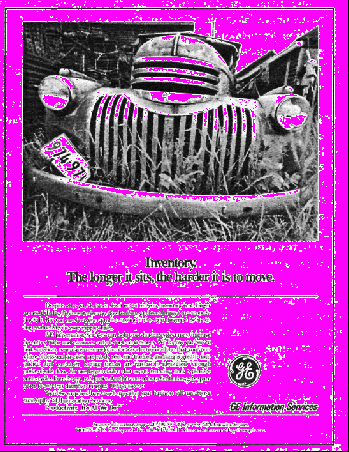
Основное назначение анализа товарно-материальных запасов в сфере производства и складских услуг — показать, когда необходимо заказывать те или иные компоненты и какой должна быть величина заказа. Многие фирмы склонны вступать в долговременные отношения с поставщиками, которые должны в этом случае обеспечивать их потребности, например, в течение целого года. В этом случае вопросы "когда" и "какой должна быть величина заказа" превращаются в вопросы "когда" и "сколько поставлять".
Цель создания товарно-материальных запасов
Все фирмы (в том числе и те, которые работают по модели JIT) хранят определенный запас товарно-материальных ценностей. При этом они руководствуются следующими соображениями.
- Обеспечение независимости своей производственной деятельности. Запас материалов на некотором рабочем месте обеспечивает определенную гибкость в производстве. Например, в связи с неизбежностью затрат времени на переналадку для каждого нового изделия, наличие товарно-материального запаса позволяет сократить потери времени.
- Независимость рабочих мест желательна и на сборочных линиях. Время, которое требуется на выполнение идентичных операций, естественно, меняется от одного изделия к другому. Поэтому на рабочем месте желательно иметь запас из нескольких деталей, чтобы при превышении плановой нормы времени на выполнение операции с конкретной деталью можно было из запаса деталей скомпенсировать такую задержку обработки. Это обеспечивает высокое постоянство производительности.
- Необходимость учета колебаний спроса на продукцию. Если спрос на продукцию известен точно, ее можно производить в точном соответствии с этим спросом (хотя это и не всегда экономически оправдано). Однако обычно спрос невозможно определить абсолютно точно, и поэтому, чтобы сгладить колебания спроса, необходимо поддерживать определенный резервный, или буферный, запас готовой продукции.
- Обеспечение гибкости производства. Наличие товарно-материальных запасов позволяет ослабить давление объема выпуска продукции на производственную систему. Запас позволяет увеличить время подготовки к выпуску продукции, что в свою очередь дает возможность спланировать более равномерный и дешевый производственный процесс за счет выпуска более крупных партий продукции. Например, при высоких затратах на размещение заказа выгоднее выпуск больших объемов готовой продукции.
- Обеспечение защиты от колебаний периода поставки сырья. Когда у поставщика заказывают тот или иной материал, могут возникать различные задержки, которые объясняются рядом причин. Среди этих причин можно отметить обычные колебания продолжительности доставки; дефицит материала на заводе поставщика, вызывающий задержки в выполнении заказа; неожиданную забастовку на заводе поставщика или в одной из компаний, занимающихся доставкой продукции; утерю заказа и доставку дефектного материала или не того материала, который требовался заказчику.
- Использование преимуществ экономичного размера заказа на закупку. Размещение заказа связано с определенными расходами: трудозатраты, телефонные переговоры, набор соответствующих текстов на пишущей машинке или компьютере, пересылка по почте и т.п. Таким образом, чем больше объем каждого отдельного заказа, тем меньше количество заказов, которые необходимо подготовить. Кроме того, расходы на доставку также свидетельствуют в пользу более крупных заказов: чем больше объем поставки, тем меньше расходы на единицу поставляемой продукции.
Рассматривая каждую из перечисленных причин (особенно это касается пп. 3, 4 и 5), необходимо помнить, что поддержание запаса связано с определенными расходами и что большие запасы в общем случае нежелательны. Необходимость создания больших запасов обычно обусловлена чрезмерно продолжительными циклами поставок.
Расходы, связанные с поддержанием запаса
Принимая решение по выбору размера товарно-материального запаса, необходимо принимать во внимание следующие расходы.
- Издержки хранения. Эта широкая категория затрат включает расходы на складское оборудование и помещения, обработку, страховку, а также расходы, связанные с мелкими кражами, порчей, старением, обесцениванием, налогами, и издержки неиспользованных возможностей капитала. Очевидно, издержки хранения запасов, как правило, подталкивают к созданию наименьших запасов и частому их пополнению.
- Расходы по освоению новой продукции. Изготовление каждого нового продукта связано с получением необходимых материалов, организацией определенных комплексов оборудования, заполнением требуемой документации, выделением соответствующего времени и материалов, изъятием предыдущего запаса материалов.
- Расходы, связанные с пуско-наладочными работами при изменении продукции. Если бы с переходом от одного продукта к другому не были связаны никакие расходы и потери времени, продукция производилась бы мелкими партиями. Это позволило бы снизить уровни запасов, что привело бы к экономии затрат. Поэтому компании пытаются снизить пуско-наладочные расходы, чтобы иметь возможность выпускать более мелкие партии продукции. (Это — цель производственной системы JIT.)
- Расходы, связанные с размещением заказов. Эти затраты относятся к управленческим и канцелярским расходам, связанным с подготовкой заказа на покупку или производство. Расходы на размещение заказов включают учет наличного количества изделий или материалов, вычисление необходимого объема заказа и документальное размещение заказов. В сумму расходов на размещение заказов включаются также затраты, связанные с отслеживанием выполнения заказов.
- Потери, связанные с нехваткой запаса (дефицитом). Когда запас какого-либо изделия или материала исчерпывается, заказ на это изделие или материал либо ожидает, пока его запас будет пополнен, либо должен быть отменен. Существует определенный компромисс между расходами на поддержание уровня запаса и потерями, являющимися следствием исчерпания запаса. В этом случае иногда не удается добиться разумного баланса, поскольку часто невозможно оценить упущенную прибыль, последствия утраты клиентов и величину штрафов за несвоевременное исполнение условий контракта. Зачастую оценка величины этих расходов является не более чем предположением, хотя часто можно указать их диапазон.
Установление правильной величины заказа и размера партии продукции, необходимой для полного использования производственных мощностей фирмы, связано с определением минимальных общих затрат, вытекающих из совместного влияния четырех видов расходов: издержки хранения, расходы на пуско-наладочные работы, расходы на размещение заказов и потери, связанные с дефицитом. Разумеется, на издержки по поддержанию уровня запасов оказывает сильное влияние и составление графика поставок.
Зависимый и независимые спрос
При организации управления товарно-материальными запасами очень важно понимать разницу между зависимой и независимой потребностью.
Если говорить коротко, то разница между зависимой и независимой потребностью, или спросом (Independent/Dependent Demand), заключается в следующем. Когда мы говорим о независимой потребности, речь идет о потребностях в различных изделиях, которые не зависят один от другого. Например, рабочая станция может выпускать множество деталей, не связанных между собой, но удовлетворяющих требованиям некоторой "внешней потребности". Когда же мы говорим о зависимой потребности, потребность в каком-то одном изделии выступает непосредственным следствием потребности в другом изделии — обычно изделии более высокого уровня, частью которого оно является.
С концептуальной точки зрения, определение зависимой потребности представляет собой относительно простую вычислительную задачу. Необходимое количество изделий с зависимой потребностью можно вычислить довольно просто, основываясь на количестве этих изделий в каждом изделии более высокого уровня. Если, например, автомобильная компания планирует выпускать 500 автомобилей в день, тогда совершенно очевидно, что для этого ей понадобятся 2000 колес и шин (плюс запасные). Необходимое количество колес и шин зависит от объема выпускаемой продукции, т.е. оно определяется не независимо. В то же время потребность в автомобилях независима — она определяется множеством факторов, внешних по отношению к данной автомобильной компании (автомобиль не является частью другой продукции и потребность в автомобилях не связана с потребностью в других продуктах).
Чтобы определить количество независимых изделий, которые необходимо изготовить, фирмы обычно прибегают к услугам своих отделов сбыта и исследований рынка. Эти отделы используют ряд методов, в частности опросы потребителей, методы прогнозирования, определение экономических и социологических тенденций (см. раздел, посвященный прогнозированию, в главе 13). Поскольку независимая потребность величина неопределенная, в запас приходится включать дополнительные изделия. В этой главе представлены модели для определения количества изделий, которое необходимо заказать, а также количества дополнительных изделий, которое необходимо для гарантирования определенного уровня обслуживания.
Системы управления запасами
Система управления запасами реализует организационную структуру и текущую политику, обеспечивающие поддержание запаса изделий и эффективное управление им. С помощью этой системы осуществляется разработка графиков размещения заказов, размещение заказов и получение материалов и контроль выполнения заказов. Эта система позволяет отслеживать прохождение заказов и получать ответы на следующие вопросы: получил ли поставщик заказ, отгрузил ли он заказанные материалы, соблюдаются ли сроки, предусмотрены ли процедуры повторной выдачи заказов и возврата ненужных или дефектных материалов?
Классификация систем управления запасами
Существуют две основные модели систем управления товарно-материальными запасами — модель с фиксированным объемом (называемая также модель экономичного размера заказа, или Q-модель) и модель с фиксированным периодом (называемая также периодической моделью, моделью периодического контроля, или Р-моделью).
Основное различие между ними заключается в следующем. В модели с фиксированным объемом производится очередной заказ на поставку, когда запас материала снижается до определенного уровня. Это событие может произойти в любой момент, в зависимости от скорости потребления материала. Что же касается модели с фиксированным периодом, то в ней осуществляется размещение очередного заказа через заранее определенный (контрольный) период времени.
Использование модели с фиксированным объемом (при которой очередной заказ размещается, когда остаток запаса снижается до заранее определенного уровня R) предполагает постоянный контроль остатка запаса. Таким образом, модель с фиксированным объемом представляет собой непрерывно действующую систему, которая требует, чтобы каждый раз, когда проводится изъятие материалов из запаса или добавление их в запас, обновлялись соответствующие записи и выполнялась проверка, достигнута ли точка очередного заказа. В модели с фиксированным периодом вычисление остатка запаса проводится лишь по истечении контрольного периода времени. (Далее мы обсудим также некоторые разновидности систем, сочетающих черты обеих этих моделей.)
Ниже перечислены некоторые дополнительные различия, которые обычно оказывают влияние на выбор той или иной системы (табл. 15.1).
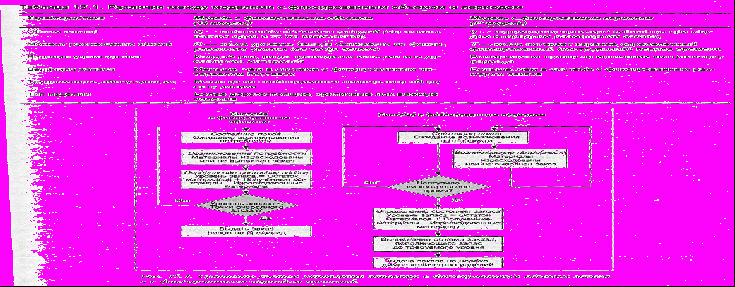
- Модель с фиксированным периодом в среднем имеет больший запас, поскольку запаса материалов должно хватать до момента следующей поставки через фиксированный интервал поставок Т. В модели с фиксированным объемом никакого фиксирования интервала поставок не предусматривается, т.е. очередные поставки осуществляются по потребности и дополнительного запаса на какой-то период времени создавать не нужно.
- Модель с фиксированным объемом используется для управления запасами дорогостоящих материалов, поскольку она обеспечивает меньший средний размер запаса.
- Модель с фиксированным объемом больше подходит для ответственных (важных) материалов, называемых критическими, поскольку в ней предусматривается более жесткий контроль за запасами, а следовательно, и более быстрая реакция на угрозу исчерпания запаса.
- Модель с фиксированным объемом имеет большую трудоемкость обслуживания, поскольку каждое добавление или изъятие материала должно регистрироваться в системе.
На рис. 15.1 показано действие каждой из рассматриваемых систем.
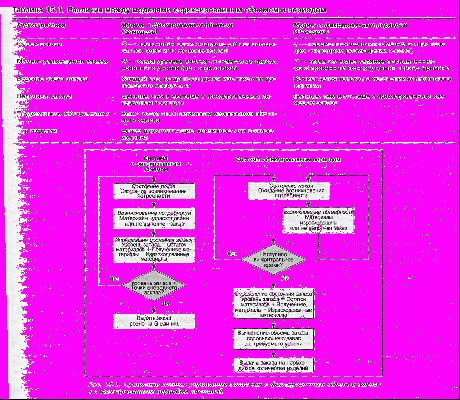
Рис. 15.1. Сравнение систем управления запасами с фиксированным объемом заказа
и с фиксированным периодом поставок
Как нетрудно заметить, работа системы с фиксированным объемом заказа основывается на непрерывном сравнении запаса и точки очередного заказа. С процедурной точки зрения, каждый раз, когда материал изымается из запаса, это изъятие регистрируется в системе, а количество оставшегося материала немедленно сравнивается с точкой очередного заказа. Если количество изделий, оставшихся в запасе, упало до этой точки, размешается заказ на Q изделий. Если нет, система продолжает оставаться в состоянии покоя до следующего изъятия.
В системе с фиксированным периодом поставок решение о размещении заказа принимается после подсчета запаса через контрольный период времени.
Модели с фиксированным объемом
Принцип действия систем с фиксированным объемом заказа основан на определении конкретного момента времени, когда нужно размещать заказ, соответствующий определенному уровню запаса (точке заказа), — R, а также размера этого заказа Q. Точка заказа R — это всегда совершенно определенное количество материала. Заказ размером Q размещается в тот момент, когда уровень запаса достигает точки R. Уровень запаса (Inventory Position) определяется как остаток материалов перед прошлой поставкой, плюс количество полученных материалов при прошлой поставке, минус израсходованное количество. Решение, принимаемое в моделях с фиксированным объемом, можно сформулировать, например, так: "когда уровень запаса снижается до 36, разместить заказ на 57 дополнительных единиц материала".
Действие модели с фиксированным объемом можно упрощенно описать исходя из предположения, что все характеристики движения запасов доподлинно известны. Например, если годовая потребность в каком-то изделии равна 1000 штук, то это именно 1000 штук, а не 1000 ±10%. То же самое можно сказать о затратах на размещение заказа (или пуско-наладочных затратах) и издержках хранения запасов. Несмотря на то, что предположение о полной определенности далеко не всегда реально, оно дает хорошую основу для описания моделей движения запасов.
Рассмотрим определение оптимальной величины заказа, используя упрощенную модель, приведенную на рис. 15.2, и следующие допущения. (Эти допущения, конечно, далеки от реальности, но они могут служить отправной точкой и позволяют нам воспользоваться довольно простыми примерами.)
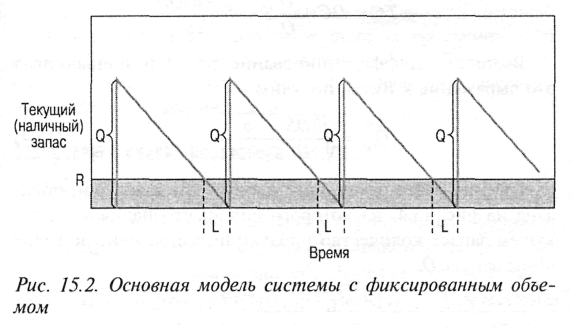
Рис. 15.2. Основная модель системы с фиксированным объемом
- Потребность в материале постоянна и равномерно распределена по всему периоду.
- Время выполнения заказа (время с момента выдачи заказа до получения заказанных материалов) неизменно.
- Цена единицы материалов постоянна.
- Издержки хранения запасов рассчитываются по средней величине запаса.
- Затраты на размещение заказа и пуско-наладочные затраты постоянны.
- Для закупок любых количеств материала имеются необходимые ресурсы и исключается возможность невыполнения заказа.
Текущий запас материала, как показано на рис. 15.2, изменяется по "пиле" и, при его снижении до уровня R (точка заказа), размешается повторный заказ. Заказанные изделия будут получены через интервал времени L, который в данной модели остается неизменным.
Вначале для разработки модели управления запасами необходимо установить функциональную взаимосвязь между интересующими нас переменными. В данном случае нас интересуют общие затраты на создание запасов, которые можно выразить следующим уравнением:
Суммарные годовые затраты =
Годовые затраты на закупки +
Годовые затраты на размещение заказов +
Годовые затраты на хранение или
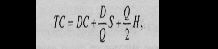
(15.1)
где
ТС — суммарные годовые затраты;
D — годовая потребность в материале;
С — цена единицы закупаемого материала;
Q — количество материала, которое необходимо заказать. Оптимальное количество называется экономичным размером заказа (Economic Order Quantity — EOQ, или Qopt);
S — затраты на размещение одного заказа;
R —- точка повторного заказа;
L — период выполнения заказа;
H — годовые издержки хранения единицы среднего запаса материала. Зачастую затраты на хранение определяются как процент от цены материала, т.е. Н = iС, где i — процент от цены С.
DC в правой части уравнения представляет собой стоимость закупки годовой потребности материала; (D/Q)S — годовые затраты на размещение заказов (фактическое количество размещенных заказов D/Q, умноженное на затраты на размещение одного заказа S), а (Q/2)H — годовые издержки хранения (средний запас Q/2, умноженный на годовые издержки хранения одного изделия H). Зависимости между этими величинами представлены в графическом виде на рис. 15.3.
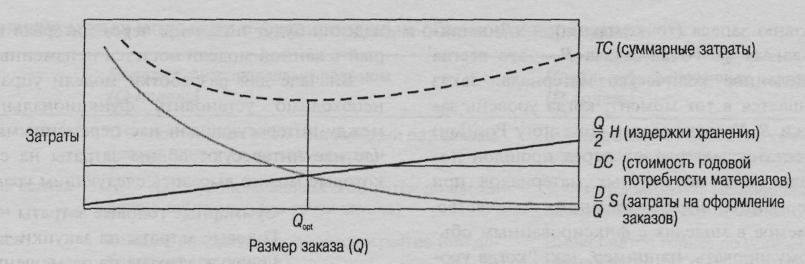
Рис. 15.3. Зависимости различных составляющих затрат
на создание запаса материала от размера заказа
Затем для разработки модели управления запасами необходимо определить ту величину заказа Qopt при которой суммарные затраты минимальны. На рис. 15.3 суммарные затраты достигают минимума в точке, где тангенс угла наклона кривой суммарных годовых затрат равен нулю. Для нахождения точки минимальных затрат возьмем производную от суммарных годовых затрат по Q и приравняем ее к нулю. Для рассматриваемого здесь уравнения эти преобразования будут иметь следующий вид:
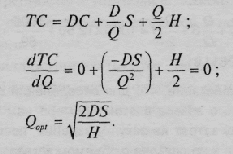
(15.2)
Поскольку эта простая модель предполагает, что потребность и время выполнения заказа являются постоянными величинами, резервный (буферный) запас не требуется, и точка повторного заказа, R, определяется как:
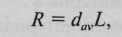
(15.3)
где
dav - средняя дневная потребность в материале (постоянная величина);
L — время выполнения заказа в днях (постоянная величина).