Методические указания к практическим занятиям и курсовому проектированию Самара
Вид материала | Методические указания |
- Методические указания к курсовому проектированию по учебной дисциплине, 1609.55kb.
- М. А. Бонч-Бруевича Методические указания к курсовому проектированию предварительных, 789.79kb.
- Методические указания к изучению курса и практическим занятиям для студентов спец., 914.85kb.
- Методические указания к практическим занятиям и курсовому проектированию Москва 2011, 1168.86kb.
- Методические указания к курсовому проектированию по учебной дисциплине «Управленческие, 1355.04kb.
- Методические указания по курсовому проектированию по дисциплине «страхование» для студентов, 1442.66kb.
- Методические указания по курсовому проектированию по дисциплине «страхование» для студентов, 1282.26kb.
- Методические указания к курсовому проектированию по дисциплине "антикризисное управление", 137.98kb.
- Методические указания к курсовому проектированию по дисциплине «экономика организации», 560.98kb.
- Методические указания к курсовому проектированию по учебной дисциплине «инновационный, 378.33kb.
![]() ФЕДЕРАЛЬНОЕ АГЕНТСТВО ПО ОБРАЗОВАНИЮ ГОСУДАРСТВЕННОЕ ОБРАЗОВАТЕЛЬНОЕ УЧРЕЖДЕНИЕ ВЫСШЕГО ПРОФЕССИОНАЛЬНОГО ОБРАЗОВАНИЯ “САМАРСКИЙ ГОСУДАРСТВЕННЫЙ ТЕХНИЧЕСКИЙ УНИВЕРСИТЕТ” ![]() ![]() |
Кафедра «Технология машиностроения» ТЕХНОЛОГИЧЕСКИЕ РАСЧЕТЫ УЧАСТКА МЕХАНОСБОРОЧНОГО ЦЕХА Методические указания к практическим занятиям и курсовому проектированию Самара Самарский государственный технический университет 2009 |
|
Печатается по решению Редакционно-издательского совета СамГТУ УДК 621.757.06.002.51(075.8) Технологические расчеты участка механосборочного цеха: Метод. указ. к практич. занятиям и курсовому проектированию / Сост. Р.Г. Гришин,. – Самара; Самар. гос. техн. ун-т, 2009. – 27 с. Рассмотрена методика расчета площадей механического и сборочного участков механосборочного цеха. Методические указания могут быть использованы для практических занятий и выполнения курсового проекта по дисциплине «Проектирование машиностроительных производств». Предназначены для студентов, обучающихся по специальностям 151001, 150205 и направлению 150900. Составители: канд. техн. наук Р.Г. Гришин Рецензент: канд. экон. наук М.А. Мельников УДК621. 757.06.002.51(075.8) © Р.Г. Гришин, составление, 2009 © Самарский государственный технический университет, 2009 |
|
При расчете участка механосборочного цеха в условиях серийного производства или поточных и автоматических линий в условиях массового, автоматизированного производства решаются следующие вопросы:
1. на основании расчетов годовой трудоемкости (станко/ч), производимых в экономическом разделе проекта, рассчитывается количество основного и вспомогательного оборудования, а также количество подъемно-транспортных средств;
2. составляется ведомость работающих по профессиям;
3. производится планировка оборудования, подъемно транспортных средств и рассчитывается площадь участка (цеха).
Широкое применение станков с числовым программным управлением (ЧПУ) в мелкосерийном и серийном производствах заставляет проектировать участки с наиболее рациональным размещением этих станков: участки по механической обработке валов, шестерен с использованием станков с ЧПУ и роботизированных технологических комплексов (РТК) с жесткой или гибкими связями. Такие участки или цехи проектировать несколько труднее, так как усложняется их обслуживание в процессе эксплуатации, требуется решение вопроса отвода стружки из зоны резания и от станков.
Рациональное размещение оборудования облегчает управление участком, скомпонованным из станков с ЧПУ или РТК, резко увеличивает скорости перемещения заготовок и обрабатываемых деталей на участке или в цехе. Применение на участках с ЧПУ и РТК дает возможность управлять технологическим процессом с помощью электроники.
РАСЧЕТ УЧАСТКА
Механосборочный или механический цех состоит из отдельных участков или линий. Механические цеха серийного производства обычно состоят из участков по обработке валов, шестерен, корпусных деталей, иными словами, представляют собой предметно-замкнутые линии.
Расчет оборудования, необходимого для обработки годового количества деталей производится в экономическом разделе проекта.
В качестве подъемно-транспортных средств на участках механосборочных цехов используются электрокары, автокары, мототележки, подвесные кран-балки, консольные (поворотные) краны с электротельферами и др. Количество кран-балок, необходимых для обслуживания участка (цеха), определяется на основании справочных данных [3]. При механической обработке деталей массой более 20 кг применяются консольные краны, количество которых берется в зависимости от числа обслуживаемых ими станков.
Расчет работающих в цехе производится в экономическом разделе проекта. На основании этого расчета составляется ведомость состава работающих на участке (цехе).
Планировка оборудования. Станки и все оборудование располагаются на участке в порядке технологического процесса. Наиболее рациональная расстановка применяется студентом, исходя из принципов достижения прямоточности, уменьшения пути перемещения деталей от станка к станку и при более полном использовании подкрановых площадей. При планировке станки вычерчиваются в масштабе 1:100 и 1:200 в зависимости от их общего количества.
Станки располагают с учетом минимальных расстояний (разрывов) между ними и элементами зданий, норм ширины проходов и проездов. При графическом изображении планировки необходимо указать место сбора и удаления стружки от станков, места мастеров и контролеров, а также подъемно-транспорные механизмы, принятые на участке или в цехе, расстояния между колоннами, а также показать все размеры участка или цеха.
Расстояния между стенами и элементами конструкций зданий (колоннами, стенами и т.д.) приводятся в качестве примера для одного-двух станков. Все оборудование, изображенное на планировке, обозначают номерами и вносят в спецификацию, которая оформляется на листах А4 в пояснительной записке или на листах планировки.
При планировке красным цветом указывается направление грузопотока деталей в порядке технологического процесса от станка к станку или с линии на линию.
ЦЕЛЬ ЗАНЯТИЙ
1. Закрепить знания после самостоятельного изучения дисциплины и установочных лекций по курсу ”Проектирование машиностроительных производств”.
2. Подготовить студента к выполнению практических задач, связанных с проектированием участка, мастерской, цеха.
3. Научить располагать оборудование на плане участка (мастерской) с соблюдением норм разрывов между оборудованием и между оборудованием и элементами зданий.
ПОРЯДОК ВЫПОЛНЕНИЯ РАБОТЫ
По последним двум цифрам номера зачетной книжки студент определяет исходные данные: технологический процесс (Приложение П1) выбирается как вариант по предпоследней цифре номера зачетной книжки; годовая трудоемкость – по последней цифре номера зачетной книжки.
Если номер зачетной книжки оканчивается на «00», то для определения задания принимается вариант 10.
В данной работе объем выпуска деталей в производство определяются руководителем занятий.
Годовая трудоемкость изготовления деталей на участке или в цеху определяется исходя из потребности деталей (программы) и штучного времени на изготовление (ремонт) детали или изделия по формуле:
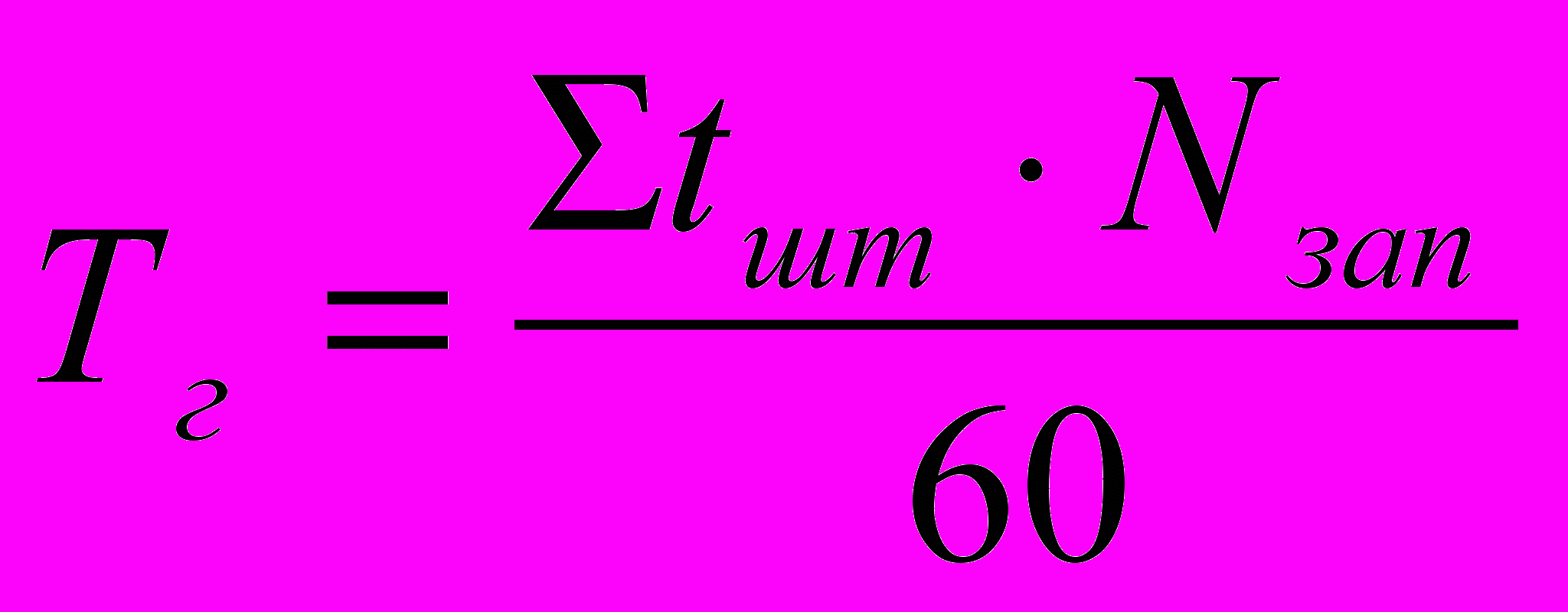
где ∑tшт. – суммарное штучное время изготовления, мин.;
Nзап. – объем запуска деталей в производства, который определяется по формуле:
Nзап. = Nвып. ∙ Кп,
где Кп – коэффициент потерь на брак и подналадку станка (Кп ≈ 2…3%).
После определения трудоемкости изготовления деталей необходимо определить действительный годовой фонд работы оборудования и действительный годовой фонд рабочих.
Фд.ст. = Фн ∙ Кр., ч
где Фн – номинальный годовой фонд работы равный:
Фн = (243 ∙ 8 + 8 ∙ 7) = 2000 ч.
243 – число дней в году, 8 – число предпраздничных дней в году.
Эти данные могут быть изменены по решению правительства.
Кр – коэффициент простоев станка на ремонте (3%).
Тогда действительный годовой фонд работы оборудования будет:
Фд.ст. = 2000 ∙ 0,97 = 1940 ч.
Фонд действительный годовой рабочего будет равен:
Фд.р. = Фн ∙ Кп, ч
где Кп = 0,92 – коэффициент потерь времени рабочего (8%).
Фд.р. = 2000 ∙ 0,92 = 1840 ч.
ПРАКТИЧЕСКОЕ ЗАНЯТИЕ №1
РАСЧЕТ НЕОБХОДИМОГО КОЛИЧЕСТВА ОБОРУДОВАНИЯ
Расчет количества оборудования в данной контрольной работе ведется двумя способами:
По трудоемкости (для мелко- и среднесерийного производства);
По штучному времени и такту выпуска (для крупносерийного и массового производства).
Для этого необходимо предварительно определить коэффициент закрепления операций Кз.
Наиболее точное определение количества станочного оборудования производится на основании детально разработанного технологического процесса.
Расчет по трудоемкости производится по формуле:
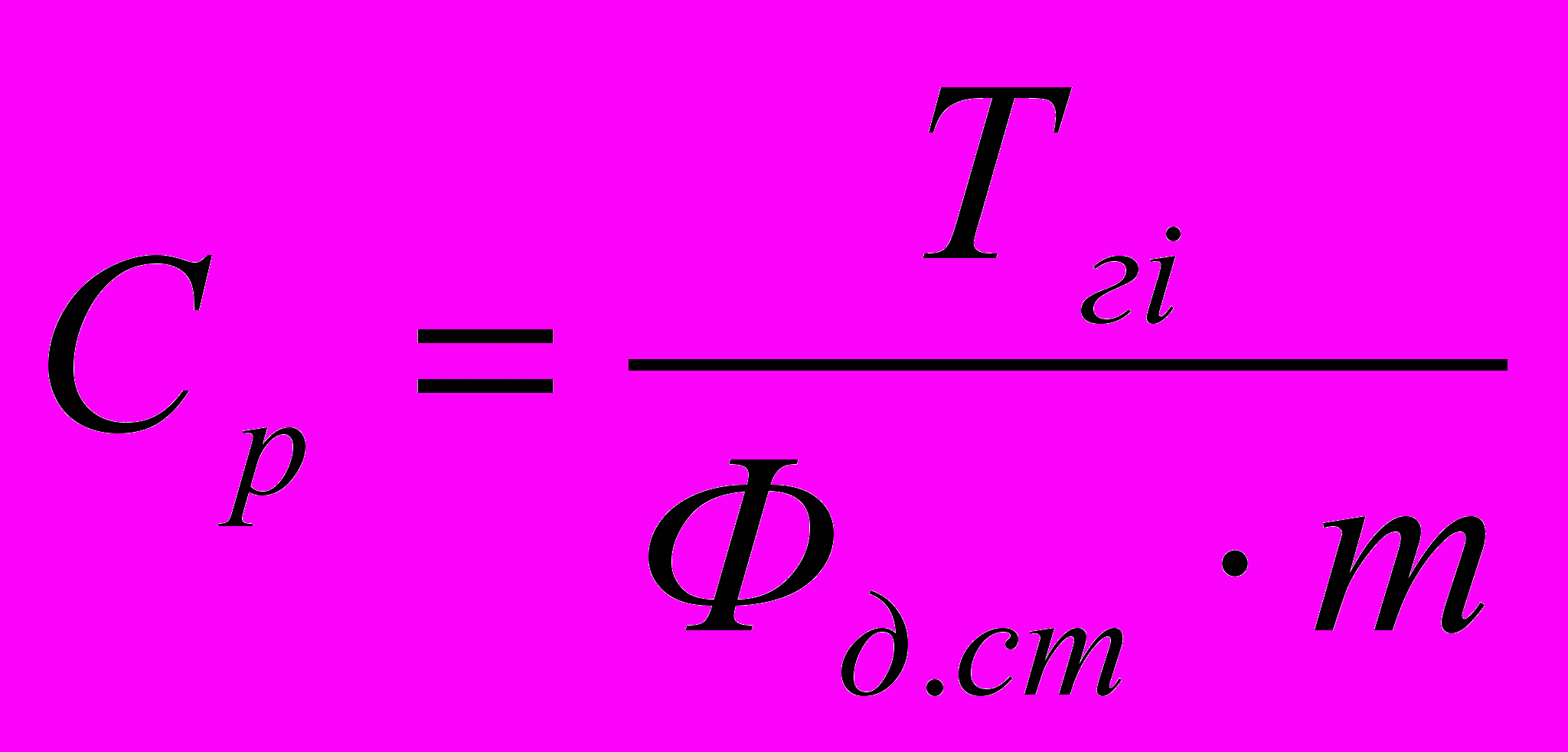
где Тгi – трудоемкость изготовления деталей по программе, в ч; m – число смен работы оборудования.
Расчет по штучному времени и такту выпуска:
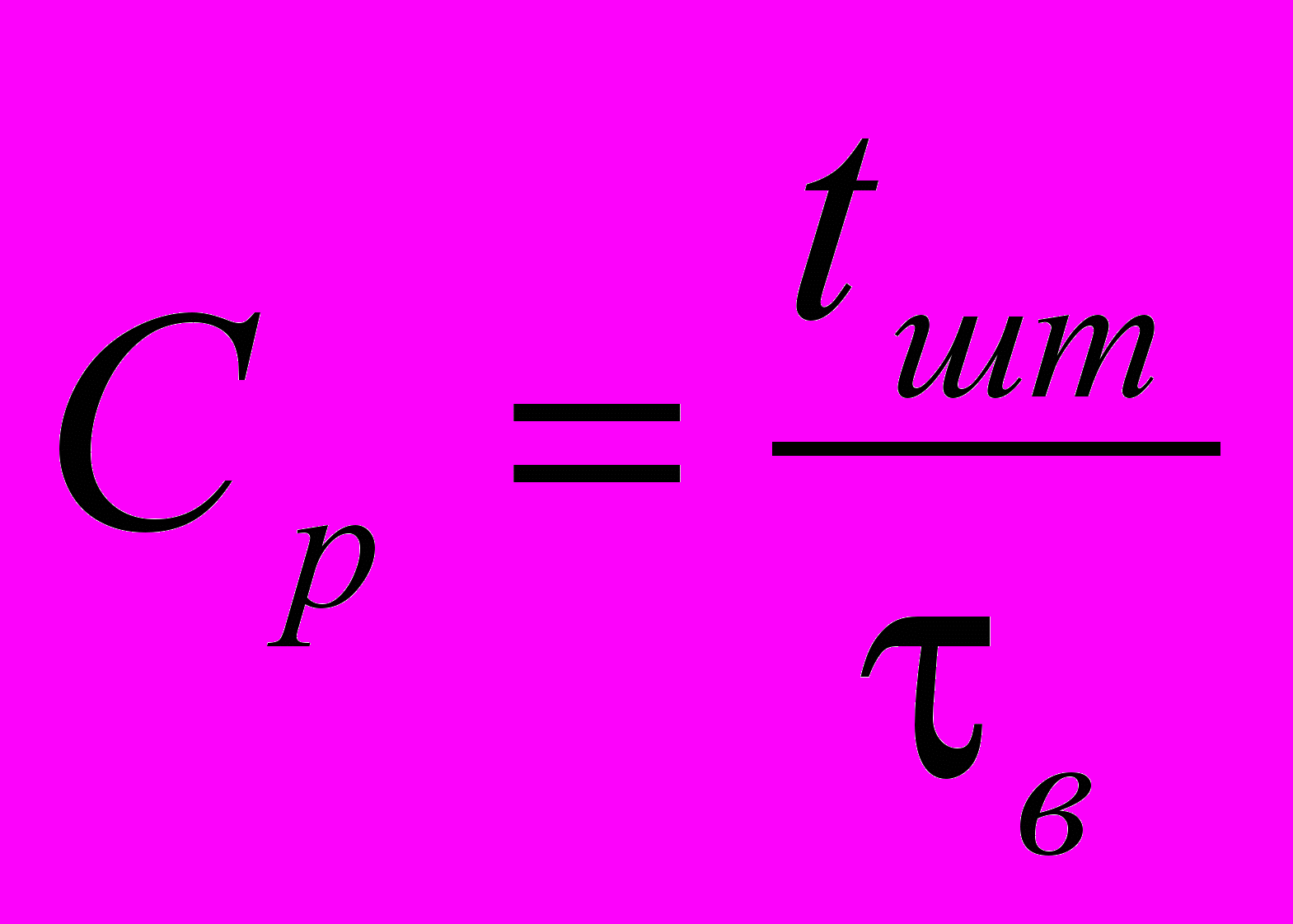
где tшт – штучное время, в мин; τв – такт выпуска деталей, мин.
Такт выпуска определяется:
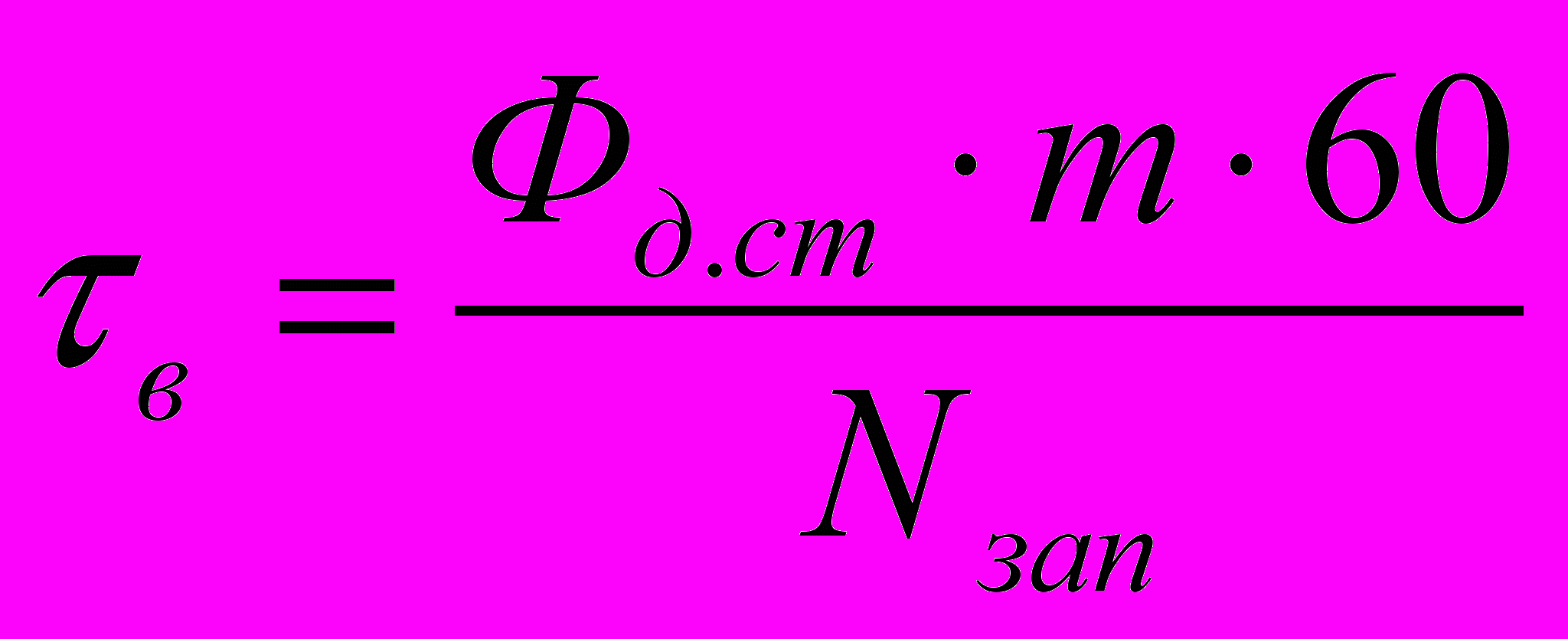
Расчет оборудования производится для каждой операции технологического процесса. Расчетное число оборудования округляется до целого и определяется коэффициент загрузки для каждой операции по формуле:
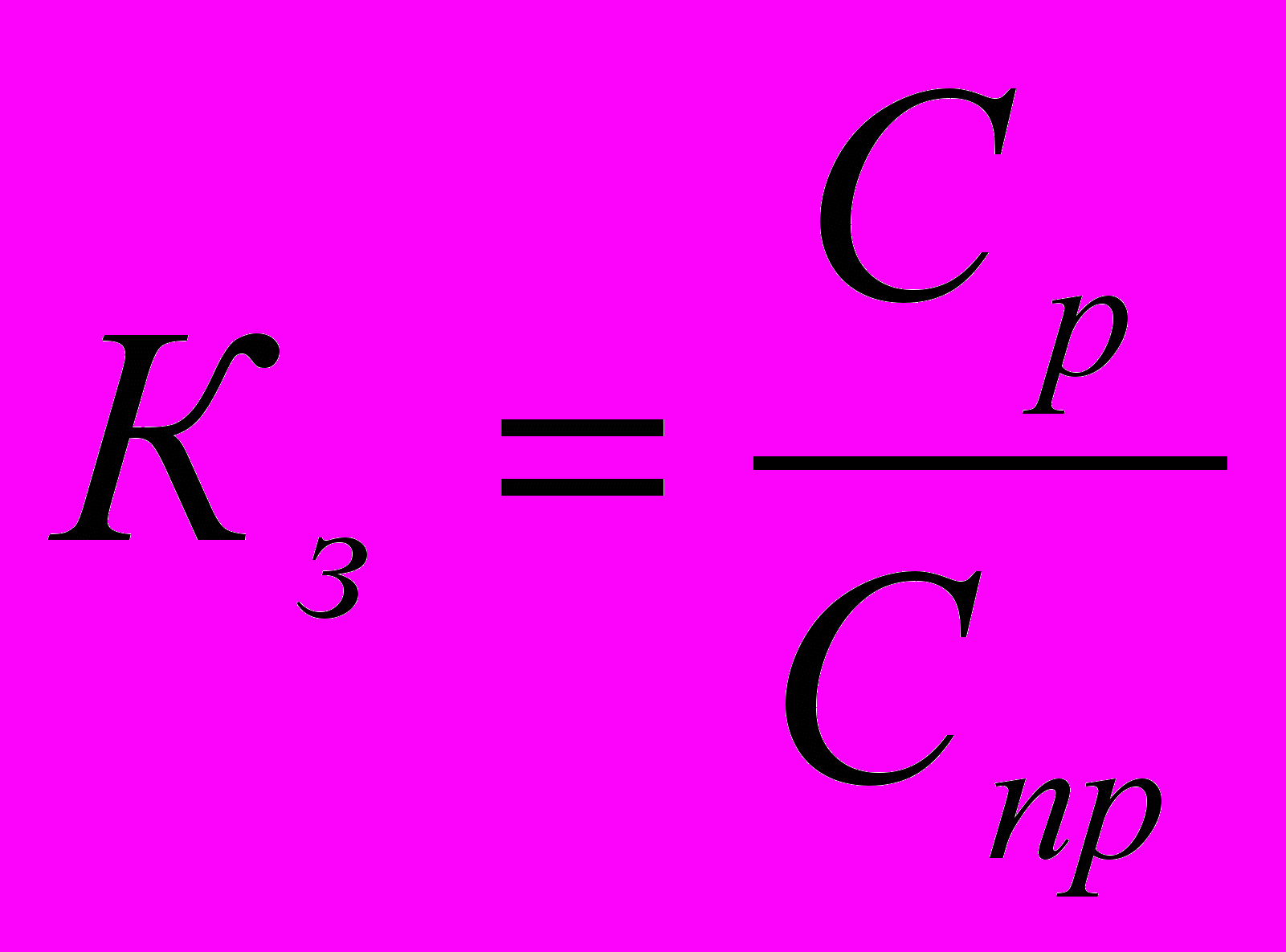
Средний коэффициент загрузки оборудования определяется по формуле:
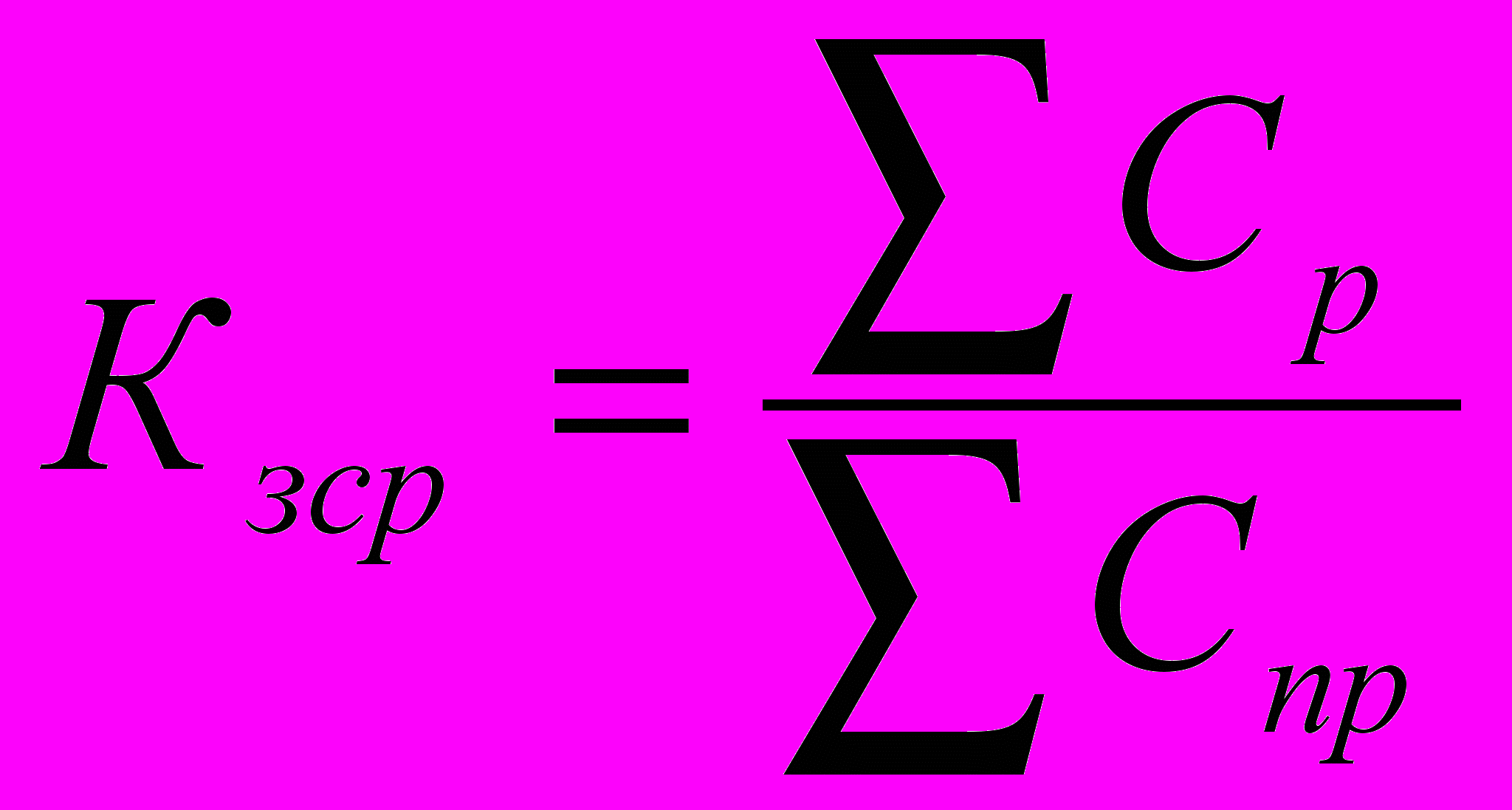
По полученным данным строится график загрузки оборудования.
ПРАКТИЧЕСКОЕ ЗАНЯТИЕ №2
РАСЧЕТ КОЛИЧЕСТВА ОСНОВНЫХ РАБОЧИХ
Расчет количества основных рабочих определяется для мелко- и среднесерийного производства по формуле:
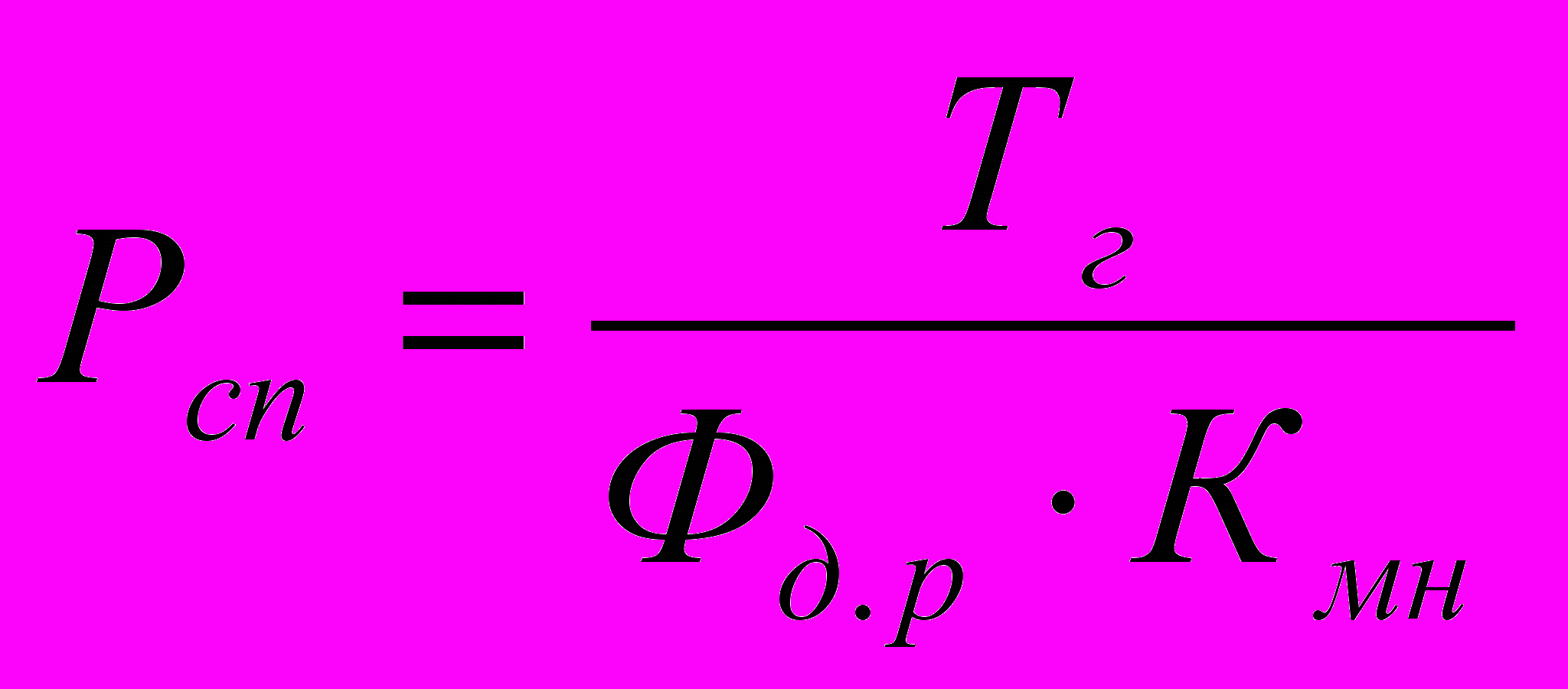
где Кмн – коэффициент многостаночного обслуживания.
Для крупносерийного и массового производства определяется по формуле:
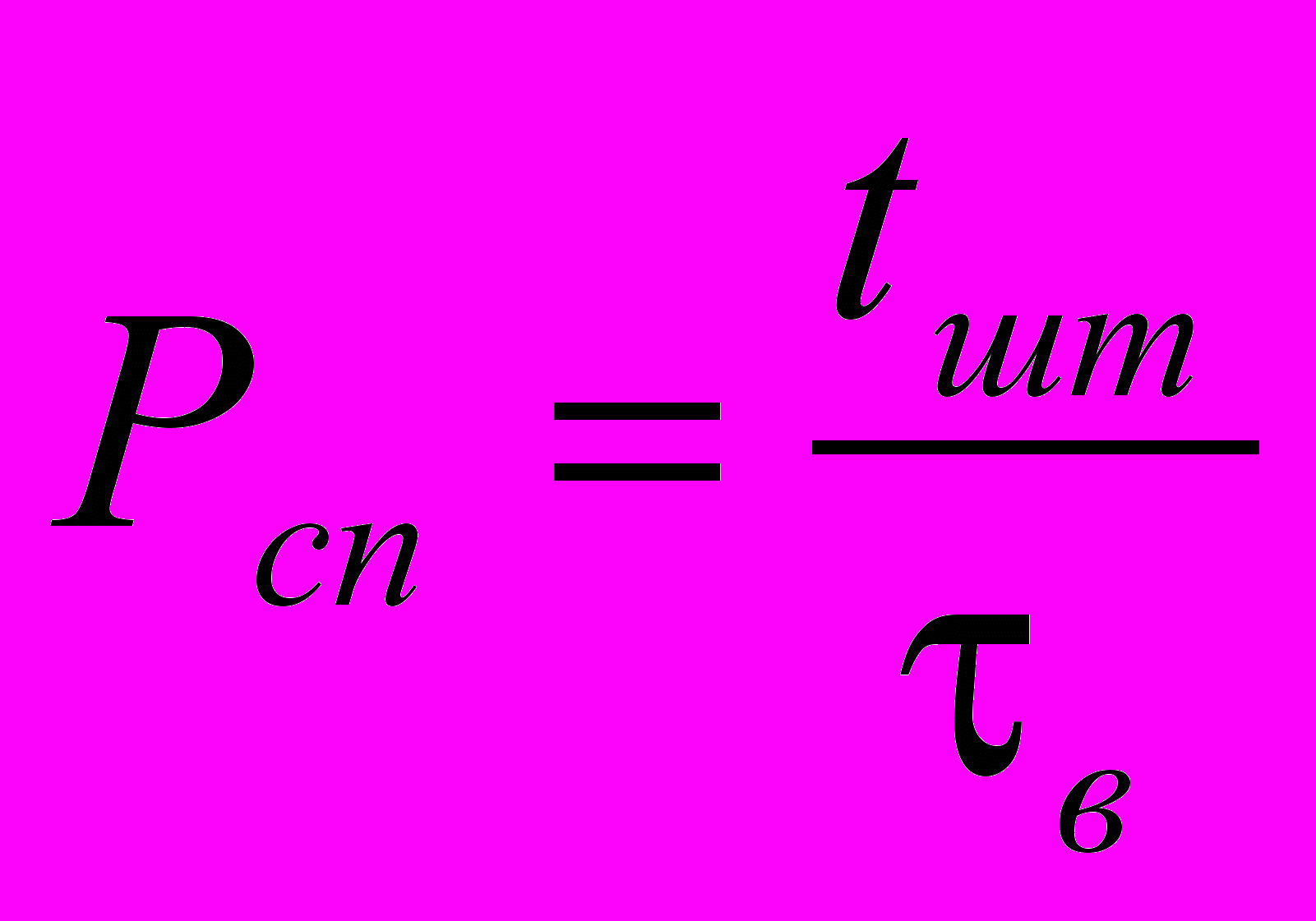
По полученным результатам выполняется таблица.
Состав рабочих участка (цеха)
Таблица 1
Наименование профессии | Всего | Рабочих по разрядам | |||
2 | 3 | 4 | 5 | ||
| | | | | |
| | | | | |
ИТОГО | | | | | |
ПРАКТИЧЕСКОЕ ЗАНЯТИЕ №3
РАСЧЕТ КОЛИЧЕСТВА ВСПОМОГАТЕЛЬНЫХ РАБОЧИХ
При выполнении контрольной работы по проектированию машиностроительных производств можно производить расчет вспомогательных рабочих по укрупненным показателям:
Рвсп ≈ 20 – 30% от основных рабочих участка (мастерской);
служащих 3% … 5% от основных и вспомогательных вместе взятых;
ИТР 10% ... 12% от основных и вспомогательных вместе взятых;
МОП 2% … 3% от основных и вспомогательных вместе взятых.
Контролеры рассчитываются по формуле (если они не рассчитаны по технологическому процессу):
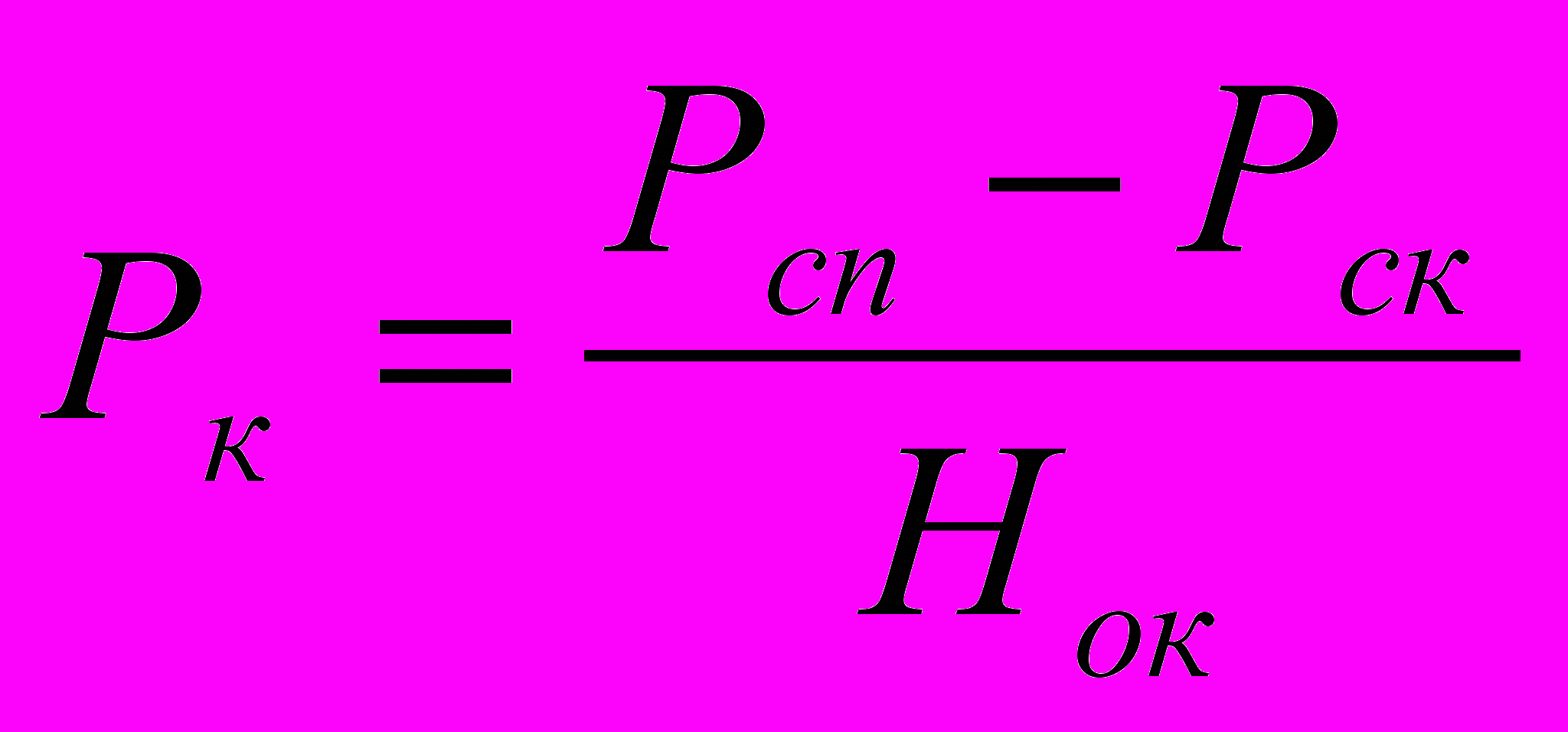
где Рсп – списочное число основных рабочих;
Рск – число рабочих, осуществляющих самоконтроль (30 – 40%);
Нок – норма обслуживания одним контролером (Нок = 14).
ПРАКТИЧЕСКОЕ ЗАНЯТИЕ №4
ОПРЕДЕЛЕНИЕ ПЛОЩАДЕЙ УЧАСТКА (ЦЕХА)
Производственная площадь определяется по формуле:
Sпроизв = ∑Спр ∙ Sуд, м2.
Величину Sуд определяем из таблицы.
Средняя удельная площадь на единицу производственного оборудования:
Таблица 2
Группа оборудования и наименование цехов | Средняя удельная площадь, м2, на штуку производственного оборудования |
Мелкие станки | 10-12 |
Средние станки | 15-25 |
Крупные станки | 30-45 |
Особо крупные станки | 50-150 |
Цех по выпуску грузовых автомобилей | 16-20 |
Цех по выпуску гусеничных тракторов | 15-20 |
Цех по выпуску подшипников качения | 15-20 |
Цех по выпуску металлорежущих станков | 17-20 |
Цех по выпуску валов, шестерен, дисков | 17-20 |
Цех по выпуску базовых и корпусных деталей | 17-20 |
Цех по выпуску средних редукторов | 30-45 |
Цех по выпуску мелких редукторов | 20-23 |
Цех по выпуску изделий авиации | 20-25 |
Цех по выпуску изделий часового производства | 10-12 |
Автоматно-токарный цех | 15-20 |
Вспомогательная площадь
Таблица 3
Наименование вспомогательного отделения | Нормы расчета | Кол-во для расч. | Площади, м2 | |
Sр | Sпр | |||
Цеховая ремонтная база (ЦРБ) | 25-32 м2 на 1 станок ЦРБ | | | |
Ремонтная мастерская приспособлений и инструмента | 20-26 м2 на 1 станок мастерской | | | |
Заточное отделение | 10-14 м2 на 1 заточной станок | | | |
Инструментально-раздаточная кладовая (ИРК) | 0,7-0,25 м2 на 1 производственный станок | | | |
Кладовая абразивов | 0,4 м2 на один шлифовальный или доводочный станок | | | |
Кладовая приспособлений | 0,1-0,5 м2 на 1 станок основного оборудования цеха | | | |
Склад вспомогательных материалов (хозяйственный) | 0,1-0,2 м2 на один станок цеха | | | |
Площадь отделения для переработки стружки | 0,3-0,5 м2 на 1 станок цеха | | | |
Площадь помещения для хранения стружки | 0,25-0,5 м2 на 1 станок цеха | | | |
Участок приготовления СОЖ | 50 – 70 м2 для цеха с количеством станков 101 – 200 | | | |
Кладовая ЦРБ | 10-15% от площади ЦРБ | | | |
Мастерская энергетика | 20% от площади ЦРБ | | | |
Комната мастеров | 6 м2 на 1 мастера | | | |
Помещение ОТК | 3-5% от станочной площади | | | |
Склад материалов и заготовок | 10-15% от станочной площади | | | |
Склад готовых деталей | 10% от станочной площади | | | |
Склад ГСМ | до 20 м2 | | | |
Изолятор брака | до 15 м2 | | | |
Площадь пожарного проезда определяется по вспомогательной площади (40% от Sвсп).
Технологическая площадь представляет собой сумму площадей:
Sучастка = Sпроизв. + Sвсп. + Sпож.пр., м2.
По полученным данным расчетов составляют планировку оборудования для механического и сборочного отделений в масштабе 1 : 100 на листе формата А1 (можно на миллиметровке или в компьютерном варианте).