Отчёт Опроведённых мероприятиях в сфере образования для населения г. Москвы в целях повышения качества образовательных услуг по договору №4 от 08. 12. 2011 г раздел 4
Вид материала | Отчет |
- Отчет о проведённых мероприятиях в сфере образования для населения города Москвы, 240.51kb.
- Аннотация научно-образовательного материала (ном), 32.65kb.
- Оценка качества образовательных услуг в средних школах города москвы совершенствование, 1063.9kb.
- Постановление Правительства Москвы от 24 апреля 2007 г. N 299-пп о мерах по приведению, 900.03kb.
- Система рейтинговой оценки деятельности педагогов как средство повышения качества образовательных, 140.61kb.
- Кабинет Министров Республики Татарстан постановляет: Утвердить прилагаемые: методические, 1561.95kb.
- Приказ 10. 05. 2011 №307 г. Вытегра Об утверждении Порядка подготовки и публикации, 85.37kb.
- Распоряжение от 6 августа 2011 г. N 820-р о переходе на преимущественно одноканальное, 132.48kb.
- Информация о результатах социологического исследования мнения населения Нижневартовского, 13.17kb.
- Отчет о проведении круглого стола для руководителей и менеджеров образовательных учреждений, 341.07kb.
6.4.1.1.3. Подраздел. Проходка горных выработок и добыча крепких руд бурением скважин большого диаметра
6.4.1.1.3.3. Варианты технологических схем добычи крепких руд бурением скважин большого диаметра
Технологические схемы добычи крепких руд выбуриванием. Применение буровых установок для добычи крепких руд требует решения целого ряда задач: от обеспечения точности бурения и полноты извлечения руды из залежи с заданной производительностью до доставки и транспортирования рудной мелочи и обеспечения высокого качества обогатительного передела. Одной из главных проблем в настоящее время является порядок ведения очистных работ, обеспечивающий поточность технологии и предотвращающий опасное проявление горного давления. Кроме того, для промышленного производства добычи руды из тонких залежей необходимо решать вопрос уменьшения габаритных размеров добычных агрегатов.
В настоящее время, как отмечалось выше, отклонение от заданного направления бурения наиболее сложных горизонтальных выработок и скважин составляет от 0,2–0,5 % до 1,0–1,5 %; разработаны лазерные и компьютерные установки, позволяющие осуществлять бурение с высокой степенью точности в заданном направлении. Имеются технические решения, позволяющие осуществлять направленное бурение вслед за изменяющейся гипсометрией рудного тела в различных направлениях.
Производительность буровых установок при бурении в крепких породах достигает 80 тыс. т. в год и более (с учетом возможности чистого времени бурения). Такая производительность (по предварительным расчетам) обеспечивает экономически целесообразную добычу крепких руд из залежей мощностью 0,6 м и менее. В последнее время разработаны буровые головки с соплами для подачи воды под давлением более 300 МПа, что позволяет увеличить скорость проходки вдвое.
Габариты буровых самоходных установок типа Рино-400 или «ВМ50N» позволяют осуществлять технологическое бурение из выработок сечением 15–18 м2. По данным фирм-производителей технические возможности позволяют изменить габариты этих установок для работы в выработках сечением 10–12 м2 без изменения буровой мощности станков.
Для предотвращения проявления горного давления и концентрации напряжений в выработках, где находятся люди, разработана технологическая схема выбуривания, позволяющая управлять процессом перераспределения напряжений во время проведения очистных работ.
Ниже описаны принципиальные технологические схемы применительно к разработке Ловозерского месторождения с углом падения рудной залежи 10…30о, крепости руд f = 12–14 по шкале М.М. Протодьяконова и их балансовой мощности 0,6 м. Характерной особенностью состава полезного ископаемого в рудной залежи является максимальное его расположение в центральной части, то есть при мощности извлечения 0,5…0,6 м.
Технологические схемы добычи руд выбуриванием скважин большого диаметра отличаются вариантами различных диаметров расширения скважин, видом доставки и транспорта.
По первой схеме добычу ведут выбуриванием скважин диаметром 1,0 м с предварительным бурением опережающих пилот-скважин диаметром 0,25…0,27 м и продувкой скважины сжатым воздухом. Улавливание шлама и его доставку осуществляют самоходными вагонами до восстающего с последующей электровозной откаткой.
По второй схеме добычу руды ведут выбуриванием скважин диаметром 0,8 м с предварительным бурением пилотных скважин диаметром 0,25…0,27 м. Сначала проходят пилотные скважины на расстоянии друг от друга, равном 4…6 их диаметрам, а затем посредине между пробуренными уже скважинами.
Расширение скважин выполняют через одну с окончательным разбуриванием перфорированных целиков после упрочнения отдельных скважин на расстоянии, определяемом по формуле:
L = 6,0 (jnD+Wr)/jnD–0,8 (jnD

где L – расстояние между раскрепляемыми скважинами, м; j – объемная плотность пород кровли, кН/м3; n – коэффициент глубины разработки, n = 0,6–0,12 соответственно для глубин 300-1000 м; D – диаметр разбуриваемых (расширяющих) скважин, обеспечивающих выемочную мощность залежи, м; Wr – сопротивление пород кровли растяжению, МПа;

Откатку получаемого шлама до ствола выполняют электровозами.
По третьей схеме добычу руды ведут комбинированным сочетанием скважин диаметрами 1,0 и 0,8 м с предварительным бурением опережающих пилот-скважин диаметром 0,25…0,27 м.
Для снижения потерь руды в «гребешках» кровли и почвы залежи перед расширением первичных скважин на равном расстоянии между ними у почвы и кровли залежи вприсечку к вмещающим породам бурят дополнительные скважины малого диаметра. Указанные скважины бурят на расчетном расстоянии друг от друга.
По четвертой схеме добычу руды ведут комбинированным сочетанием скважин диаметром 0,5 м, 0,8 м и 1,0 м с предварительным бурением передовых пилот-скважин по одной оси. Улавливание шлама и доставку его к откаточному горизонту осуществляют по уклону 4…10º в сборочный зумпф с последующей погрузкой в вагонетки и электровозной откаткой до ствола.
По пятой схеме добычу руды ведут скважинами на полное сечение. Из накапливаемого шлама приготавливается текучая смесь с добавлением к ней противоморозных компонентов, которая передвижной гидротранспортной установкой доставляется до участкового секционного зумпфа (или центральной гидротранспортной установки) и далее поступает на обогатительную фабрику.
При шестой схеме по падению (или по простиранию залежи) добычным комбайном проходят пилот-скважины диаметром 0,27 м, затем обратным ходом их расширяют до необходимого диаметра. Комплексом подготовки руды к сепарации рудную массу разбивают по крупности на несколько классов и подают в сепаратор, где происходит предварительное обогащение. Общая технологическая схема представлена на рис 21.
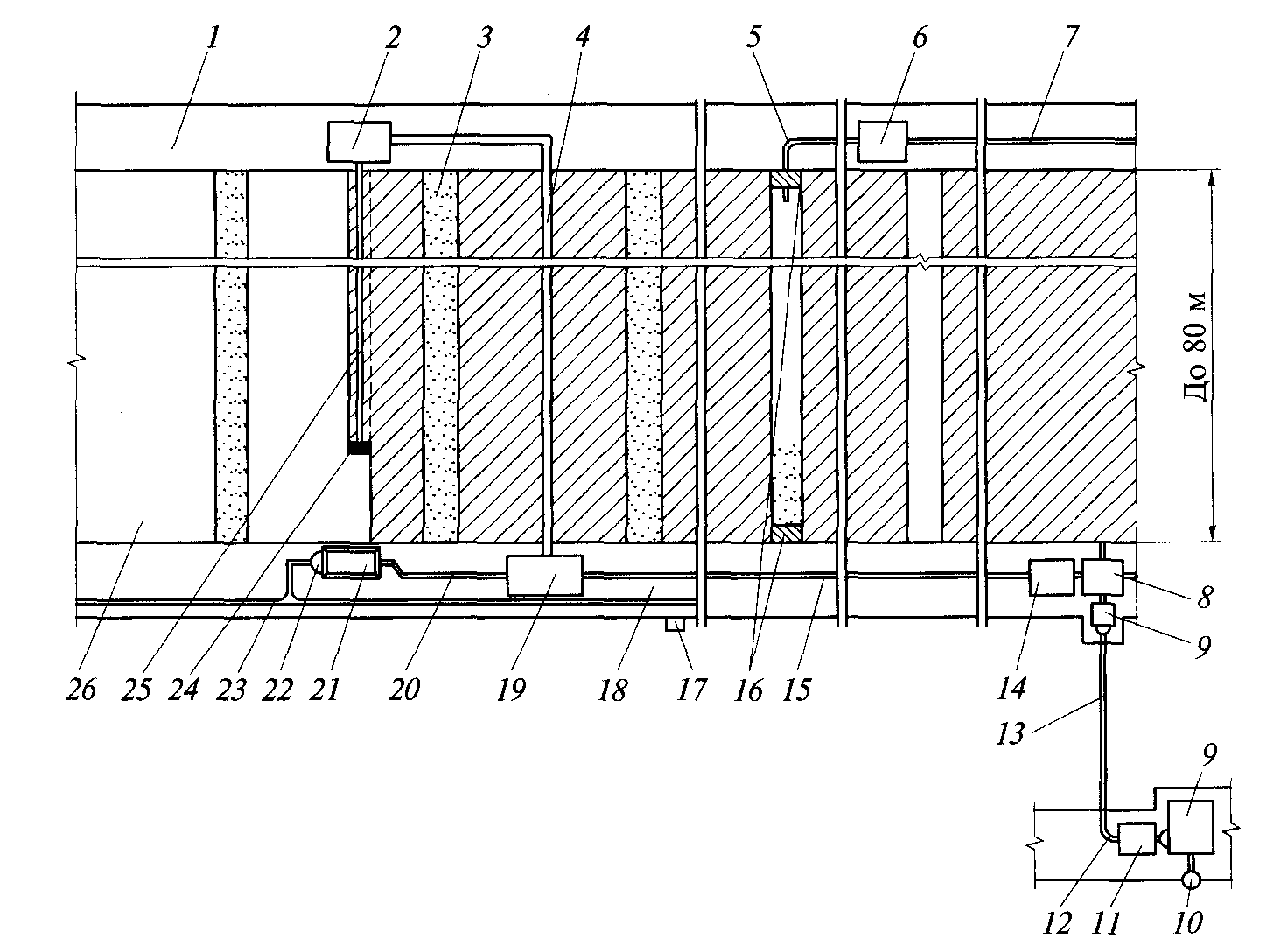
Рис. 21. Шестая технологическая схема отработки тонких наклонных и пологих рудных тел с комплексной механизацией основных производственных процессов:
1 — буровой штрек; 2 — буровой добычной комбайн типа КД800Э; 3 — междублоковый искусственный целик; 4 — шламовая скважина; 5 — трубопровод подачи закладочной смеси; 6 — закладочный комплекс; 7 — трубопровод подачи компонентов закладки; 8 — сепаратор; 9 — высоконапорный насос с аккумулирующей емкостью; 10 — рудоприемная скважина; 11 — комплекс подготовки руды к выдаче на поверхность; 12 — трубопровод для обогащенной рудной массы; 13 — нисходящая скважина; 14 — комплекс подготовки руды к сепарации; 15 — трубопровод для транспортировки рудной массы; 16 — закладочные перемычки; 17 — водосборник (зумпф); 18 — транспортно-сортировочный штрек; 19 — передвижной комплекс подготовки рудной массы к транспортировке; 20 — трубопровод для транспортировки рудной массы; 21 — улавливатель рудной массы; 22 — муфта поддува; 23 — воздухопровод сжатого воздуха; 24 —
расширитель; 25 — пилот-скважины; 26 — очистное пространство
Все рассмотренные схемы требуют опытно-промышленной проверки, необходимым условием которой является наличие бурового оборудования. Ввиду отсутствия отечественных и зарубежных добычных комбайнов для разработки тонких залежей крепких руд институтами Гипроцветмет и ВНИПИрудмаш для выемки руд из маломощных залежей выбуриванием скважин большого диаметра был создан экспериментальный образец добычного комбайна КД800Э, прошедший успешные промышленные испытания в условиях удароопасного месторождения «Карнасурт» Ловозерского ГОКа.
Испытания комбайна КД800Э проведены на руднике «Карнасурт». Ниже приведены результаты испытания технологии выбуривания крепких руд с применением добычного комбайна КД800Э. Рудная залежь опытного участка представлена мощностью 0,5…0,6 м, углом падения 10–12º, имеет выдержанную гипсометрию, падение юго-западное, вскрыта штольней.
Транспортирование руды осуществлялось через горизонт + 430 м и штольню «Уртитовую» на обогатительную фабрику рудника.
Параметры блока выбраны в зависимости от физико-механических свойств горного массива и применяемого оборудования. В условиях рудника «Карнасурт» расстояние между участковыми штреками составляет 120–130 м. Техническая возможность КД800Э позволяет бурить скважины диаметром 0,9…1,2 м на длину 60 м с расчетным отклонением около 0,35–0,50 %. Длина скважин принята 50 м, при отклонении по вертикали в пределах 15…20 см. Длина блока определена из возможности средств доставки и принята равной 100 м (по 50 м на каждую сторону по оси блока).
Балансовая мощность залежи составляет 0,6 м. Наиболее богатая часть представлена мощностью 10…20 см в центральной части.
Вначале добычным комбайном КД800Э выполняли бурение пилот-скважин. Через каждые 10–15 м скважины заполняют твердеющей закладкой. В участковом водосборнике аккумулируют рудную мелочь струйным насосом. Через восстающий обезвоженную, более крупную фракцию подают в вагонетки на откаточном горизонте. Бурение и расширение скважин проводят из буровых штреков. Устройство позволяет обезвоживать буровой шлам и разделять его по фракциям. Транспортирование руды по буровому штреку осуществляют в вагонетках. Расширение скважины осуществляют расширителем из нижнего бурового штрека вентиляционного блока.
После отработки рудной части опытного блока переходят на верхний буровой штрек. Весь технологический цикл повторяется.
Таким образом, почти все технологические процессы, каждый в отдельности, удовлетворяют требованиям новой технологии, однако требуются опытно-промышленные испытания применения буровых установок для технологии добычи руды из тонких рудных залежей в целом, с увязкой всех технологических процессов и обеспечения экономической целесообразности применения данной технологии в каждом конкретном случае.
Выбор технических средств доставки в опытно-промышленном блоке. По условиям технологического процесса доставку гидросмеси горной массы осуществляют от каждой технологической скважины диаметром 0,81,0 м. Скважины проводили добычным буровым комбайном обработкой забоя шарошками и промывкой его водой при содержании в среднем твердого к жидкому, как 1:5 по массе. Основной класс выбуренной руды представлен крупностью 0,2…24 мм с выходом до 96 %. Количество выдаваемой каждой скважиной рудной гидросмеси в зависимости от горно-геологической характеристики рудного тела и режима бурения находится в пределах от 1 до 2 м3/ч.
Результаты опытно-промышленных испытаний технологии отработки тонких залежей крепких руд комбайном КД800Э в полном объеме отражены в акте испытаний, утвержденном приемочной комиссией.
Применение добычного комбайна в условиях Ловозерского ГОКа позволяет:
– повысить производительность труда в 1,5–2,5 раза и снизить трудозатраты на добыче и переработке руды;
– исключить стадии крупного, среднего, мелкого дробления и грохочения при обогатительном переделе;
– значительно снизить затраты на транспорт; снизить потери полезного ископаемого на добыче и переработке на 20–30 %; снизить уровень разубоживания в 2,3 раза и извлекаемость руды из недр на единицу конечного продукта;
– вовлечь в эксплуатацию маломощные рудные залежи, отнесенные к забалансовым из-за низкой рентабельности их разработки традиционным буровзрывным способом;
– исключить вредное влияние факторов буровзрывной отбойки на устойчивость и срок службы горных выработок; значительно повысить уровень механизации и безопасность работ, вывести рабочих из опасной зоны очистного пространства и превратить их в операторов, дистанционно управляющих процессом добычи полезного ископаемого;
– осуществить экологически чистую циклично-поточную и поточную технологию добычи и переработки полезного ископаемого.
Главными критериями оптимальности выбуривания руд являются показатели извлечения полезного ископаемого: разубоживание и потери. Они зависят от технических характеристик применяемого оборудования, которые влияют на точность бурения, отклонения скважин при бурении от заданного профиля, в зависимости от глубины бурения и гипсометрии залежи. При бурении скважины происходит ее отклонение в вертикальной плоскости, при этом ось скважины отклоняется от средней плоскости залежи. Необходимо учитывать, что для обеспечения полноты извлечения диаметр расширяющей скважины принимают больше мощности залежи.
Бурение скважины прекращают, исходя из анализа содержания полезного ископаемого в добываемой руде и его ценности.
Опыт отработки рудных залежей малой мощности средней крепости шнековым бурением показывает, что наиболее целесообразным являются технологические схемы, отличающиеся видом применяемого транспорта, подъема, средствами и способами первичного обогащения [20].
Более 15 % запасов полезных ископаемых цветных и 60 % редких металлов России отнесены к забалансовым вследствие малой мощности рудных тел – менее 0,8 м. Освоение таких запасов с применением традиционных систем разработки в большинстве случаев экономически не целесообразно из-за высокого разубоживания руды и низкого уровня механизации работ. Из добываемых более 20 млн. тонн руды цветных металлов в год с применением ручного труда основная их доля связана с разработкой маломощных рудных участков.
Вовлечение в эксплуатацию маломощных залежей полезных ископаемых с высоким извлечением из недр и эффективной производительностью возможно на основе применения технологии добычи руд из маломощных залежей выбуриванием скважинами большого диаметра, обеспечивающей высокое извлечение полезного ископаемого из недр без присутствия людей в очистном пространстве.
6.4.1.1.3.4. Экономическая целесообразность добычи крепких руд выбуриванием
Согласно «Единым правилам безопасности при разработке рудных, нерудных и россыпных месторождений подземным способом», ширина (высота) очистного пространства должна быть не менее 0,6 м при крутом падении (более 50º) и 0,8 м при пологом падении для нахождения человека в очистном пространстве. Следовательно, при мощности рудного тела менее 0,6 м добыча руды неизбежно связана с необходимостью расширения очистного пространства (для обеспечения присутствия человека в нем) и разубоживанием рудной массы. Учитывая неточность отбойки, трещиноватость горного массива и другие факторы, на практике выемочное пространство (за небольшим исключением) редко бывает меньше 1,2–1,5 м. Соответственно, коэффициент разубоживания при разработке тонких залежей, как правило, превышает 40–60 %, что при обогатительном переделе приводит к высоким энергетическим затратам и потерям, недопустимым при добыче ценных руд. При этом чем меньше мощность рудного тела, тем больше разубоживание, тем меньше экономическая целесообразность отработки месторождений традиционными системами разработки.
Экономическая целесообразность применения того или иного варианта системы разработки зависит от технических возможностей оборудования и его стоимости, от геологического строения месторождения, физико-механических свойств рудного тела, ценности руды и в каждом конкретном случае определяется отдельно.
Критерием для расчета экономической эффективности рассматриваемой технологии, позволяющим учесть все факторы, является минимум приведенных затрат или сводный хозрасчетный эффект от использования новой техники. Ниже выполнено сравнение применяемой при отработке пологих тонких залежей камерно-столбовой системы разработки с технологией выбуривания полезного ископаемого скважинами. Сравнение проведено по сводному хозрасчетному эффекту от использования новой техники. Прирост прибыли определен по отраслевой инструкции. За базовый вариант принята применяемая на комбинате камерно-столбовая система разработки с регулярно оставляемыми внутриблоковыми целиками и большим разубоживанием руды (более 40 %).
Одной из основных статей расхода являются расходы, связанные с вентиляцией рудника ввиду необходимости проведения большого объема буровзрывных работ в узком очистном пространстве.
Сравнение вариантов разработки камерно-столбовой системой и двух вариантов выбуривания проведено по простиранию – 100 м, ширине по падению – 55 м, мощности рудной залежи – 0,6 м, угле падения – 10…12о.
В первом варианте добычу руды ведут выбуриванием скважин диаметром 0,8 м с предварительным бурением пилотных скважин диаметром 0,25–0,27 м. Сначала проходят пилотные скважины на расстоянии друг от друга, равном 4…6 их диаметрам, а затем посредине между пробуренными уже скважинами.
Расширение скважин выполняют через одну с окончательным разбуриванием перфорированных целиков после упрочнения отдельных скважин на расстоянии, определяемом по формуле:
L = 6,0 (jnD+Wr)/jnD–0,8 (jnD

где L – расстояние между раскрепляемыми скважинами, м; j – объемная плотность пород кровли, кН/м3; n – коэффициент глубины разработки, n = 0,6…0,12 соответственно для глубин 300…1000 м; D – диаметр разбуриваемых (расширяющих) скважин, обеспечивающих выемочную мощность залежи, м; Wr – сопротивление пород кровли растяжению, МПа;

Откатку получаемого шлама до ствола выполняют электровозами.
По второму варианту добычу руды ведут комбинированным сочетанием скважин диаметрами 1,0 и 0,8 м с предварительным бурением опережающих пионерных скважин диаметром 0,25…0,27 м.
Для снижения потерь руды в «гребешках» кровли и почвы залежи перед расширением первичных скважин на равном расстоянии между ними у почвы и кровли залежи вприсечку к вмещающим породам бурят дополнительные скважины малого диаметра. Указанные скважины бурят на расчетном расстоянии друг от друга.
Сводный хозрасчетный эффект определен из выражения:
Эх = П – Ен К,
где Эх – сводный хозрасчетный эффект от использования новой техники в -м году, у. е.; П – прирост прибыли от внедряемых мероприятий в -м году, у. е.; Ен – нормативный коэффициент эффективности, Ен = 0,15; К – капитальные вложения на все мероприятия по плану новой техники в -м году, у. е.
Прирост прибыли определен согласно отраслевой инструкции из
выражения:
П = (Ц – С)А – (Ц1 – С1)А1,
где Ц – оптовая цена, у. е.; С – себестоимость производства единицы новой продукции в -м году, у. е.; Ц1 – оптовая цена в предшествующем внедрению новой техники году, у. е.; С1 – себестоимость производства единицы продукции в предшествующем внедрению новой техники году, у. е.; А и А1 – объем производства новой продукции в -м году и в предшествующем внедрению новой техники году.
Ввиду неравномерности содержания минерала в руде и сложной конфигурации выемочной мощности расчет показателей извлечения выполнен интегрированием содержания с шагом 0,1 м. Из схемы распределения минерала в рудной залежи вытекает, что максимальное содержание минерала приходится на мощность 10–15 см в центральной части залежи. Мощность рудной залежи с балансовым содержанием минерала составляет 0,6 м. Технико-экономические показатели базового и двух вариантов технологий выбуривания приведены в табл. 4.