Теоретические и экспериментальные исследования магнитных полей дефектов конечных размеров и создание специализированных сканеров для дефектоскопии трубопроводов
Вид материала | Автореферат |
ГЛАВА 2. Анализ дефектов в стенках трубопровода и разработка устройства к дефектоскопам, не нарушающих режима перекачки продукта Р трубопровод |
- Методы дефектоскопии трубопроводов нефтеперерабатывающих заводов, 49.38kb.
- Возможности формирования магнитных полей с заданным распределением индукции на центральной, 9.53kb.
- Лабораторная работа по физике №2-24. Экспериментальные исследования электростатических, 311.12kb.
- Магнитное поле в вакууме, 56.29kb.
- Первоначальные сведения о магнетизме, 53.52kb.
- Устойчивость состояний тонкопленочных слоев магнитных носителей к внешним импульсным, 96.67kb.
- Рабочая программа учебной дисциплины (модуля) Метод конечных элементов и программы, 141.68kb.
- Луцький национальный технический университет, 95.19kb.
- Теоретические и экспериментальные Исследования распространения упругих волн в поврежденных, 277.14kb.
- Метод эпр для измерения магнитной индукции переменных полей, 65.24kb.
ГЛАВА 2. Анализ дефектов в стенках трубопровода и разработка устройства к дефектоскопам, не нарушающих режима перекачки продукта
В главе рассмотрены причины возникновения дефектов, вопросы разбиения дефектов на классы и вопросы создания устройств, обеспечивающих постоянство скорости движения дефектоскопа при изменении скорости транспортируемого продукта в пределах от 4 до 15 м/сек. Дефекты трубопроводов (параметры диагностирования) по происхождению могут быть разделены на три группы:
1 - дефекты процессов производства труб в заводских условиях;
2 - дефекты монтажных и строительных работ;
3- дефекты эксплуатируемых трубопроводов.
Своевременное обнаружение дефектов каждой стадии — производства труб, монтажа и строительства трубопроводов способствует повышению запаса прочности трубопровода.
Появление эксплуатационных дефектов трубопроводов вызвано многообразными факторами, хорошо изученными и прогнозируемыми, а также случайными (например, повреждение трубопровода сторонними лицами и т.д.). Для обеспечения надежности трубопроводов необходим периодический контроль их параметров как конструктивных, так и функциональных (в процессе эксплуатации).
При производстве труб появляются дефекты металлургического происхождения, отклонения толщины стенки, дефекты изготовления сварных швов, а также дефекты изоляционных покрытий. При монтажных и строительных работах появляются дефекты поперечного сварного шва, деформации трубы, дефекты изоляционных покрытий. Дефектами в элементах конструкции объектов, появляющимися в процессе эксплуатации, являются потери металла объектов, трещины, деформации труб, нарушения изоляции. Дефекты функциональных элементов транспортного трубопровода, появляющиеся в процессе эксплуатации, это частичные разрушения объектов и утечки транспортируемого продукта.
Сварной шов, как конструктивный элемент трубопровода, является концентратором напряжений в стенке трубы и увеличивает напряжения в 1,516 раза. Дефектный сварной шов представляет собой серьезную опасность, так как увеличивает напряжения более чем в 2 раза.
Все дефекты швов, выполненных сваркой плавлением, делятся на наружные и внутренние. Наружные дефекты формы шва и дефекты сплошности. Внутренние - дефекты структуры и дефекты сплошности.
Дефектами формы являются наплывы и натеки, а наружными дефектами сплошности - прожоги и кратеры. Внутренними дефектами сплошности являются непровары, трещины, шлаковые включения и поры.
Трещины в околошовной зоне, ориентированные перпендикулярно и параллельно оси шва, холодные трещины возникают при сварке закаливающихся легированных сталей, средне и высокоуглеродистых сталей в результате напряжения и наличия водорода в металле. Продольные трещины в металле шва, горячие трещины образуются в углеродистых и легированных сталях в результате воздействия на кристаллизующийся металл шва растягивающих напряжений. Трещины и поры в виде скопления или цепочки пор уменьшают статическую и вибрационную прочность швов и являются опасными дефектами.
К дефектам трубы, как конструктивного элемента трубопровода, относятся механические повреждения и деформации труб и нарушения изоляционных покрытий, возникающие на разных стадиях (при транспортировании, монтаже и эксплуатации трубопроводов), а также повреждения технологических элементов конструкций (крепление и др.). Главным фактором, приводящим к снижению надежности прямолинейных участков трубопровода, является коррозионное повреждение наружных поверхностей трубопроводов вследствие нарушения изоляции и эрозионное повреждение внутренних поверхностей трубопроводов вследствие наличия межкристаллитной коррозии и гидродинамических ударов транспортируемого продукта, приводящих к потере металла в стенках трубы. Эти два вида повреждения трубопроводов приводят к уменьшению толщины стенок трубопровода; при определенных условиях могут привести к трещинообразованию и разрыву металла.
На скорость коррозии влияют: качество металла трубопровода и его поверхности, состояние изоляционного покрытия, климатические условия и внешние агрессивные свойства почвенной среды и компонентов перекачиваемого продукта.
Экспериментальным путем установлены критерии опасности коррозионных повреждений стенок трубопровода. Все виды коррозионных повреждений подразделяются на три группы. К первой группе относится сплошная коррозия — равномерная или неравномерная, в зависимости от скорости се протекания на отдельных участках поверхности трубы. Ко второй группе — местная коррозия, к которой относятся одиночные поражения на расстоянии более 150 мм друг от друга. К третьей группе относят групповые коррозионные поражения с расстояниями между краями соседних коррозионных пятен 5—150 мм и протяженные коррозионные поражения при расстоянии между соседними поражениями менее 5 мм.
Одиночные коррозионные поражения, как правило, не приводят к возникновению отказов участков трубопроводов. Они предшествуют образованию свищей и при своевременно принятых мерах по ремонту или переизоляции (в случае, если глубина не достигла критического значения) опасность образования свищей снижается.
Групповые и протяженные коррозионные поражения при достижении ими критической глубины приводят к возникновению отказов участков трубопроводов.
Наиболее опасным видом коррозионных поражений является межкристаллитная коррозия (МКК) коррозионно-стойких хромоникелевых сталей, а также сталей аустенитного, аустенитно-ферритного, ферритного, мартенситного, аустенитно-мартенситного классов. МКК обусловлена как структурным состоянием металла, так и влиянием агрессивной среды. Различие физико-химических свойств граничных и внутренних областей кристаллов металла способствует диффузии углерода и хрома и выделению вторичных фаз в пограничных зонах. Электрохимическая коррозия по границам кристаллитов вызывает образование трещин, идущих от поверхности в глубь металла, в результате появляется межкристаллитное поражение.
Одним из направлений, по которому осуществляется защита от ММК, является разработка надежных методов обнаружения и определения степени поражения металла межкристаллитной коррозией.
Металл трубопровода находится под ударным воздействием двухфазной среды в виде потоков газа или жидкости, содержащих инородные включения. В этих условиях наблюдается эрозия унос массы металла трубопровода в виде отдельных частиц или слоев. Для уменьшения скорости потери металла вследствие кавитационной эрозии применяется катодная защита. Катодная защита эффективна при достаточно высоких катодных потенциалах, при которых происходит образование водорода на поверхности металла.
Взаимодействие химического и механического видов коррозии вызывает различные и сложные формы разрушения материала.
Эрозионная коррозия как параметр диагностирования подлежит изучению физическими методами неразрушающего контроля.
Разрушения трубопроводов для жидких и газообразных продуктов (газ, нефть, нефтепродукты, вода и т.д.) распространяются на участке протяженностью от нескольких десятков сантиметров до нескольких десятков метров. Разрушения газопроводов обычно имеют большую протяженность, иногда несколько километров.
Основой задачей дефектоскопии на данный момент является своевременное выявление перечисленных выше дефектов трубопроводов.
Исходя из этого, проведено деление дефектов основного металла труб на классы, приведённые на схеме (рис.1.).
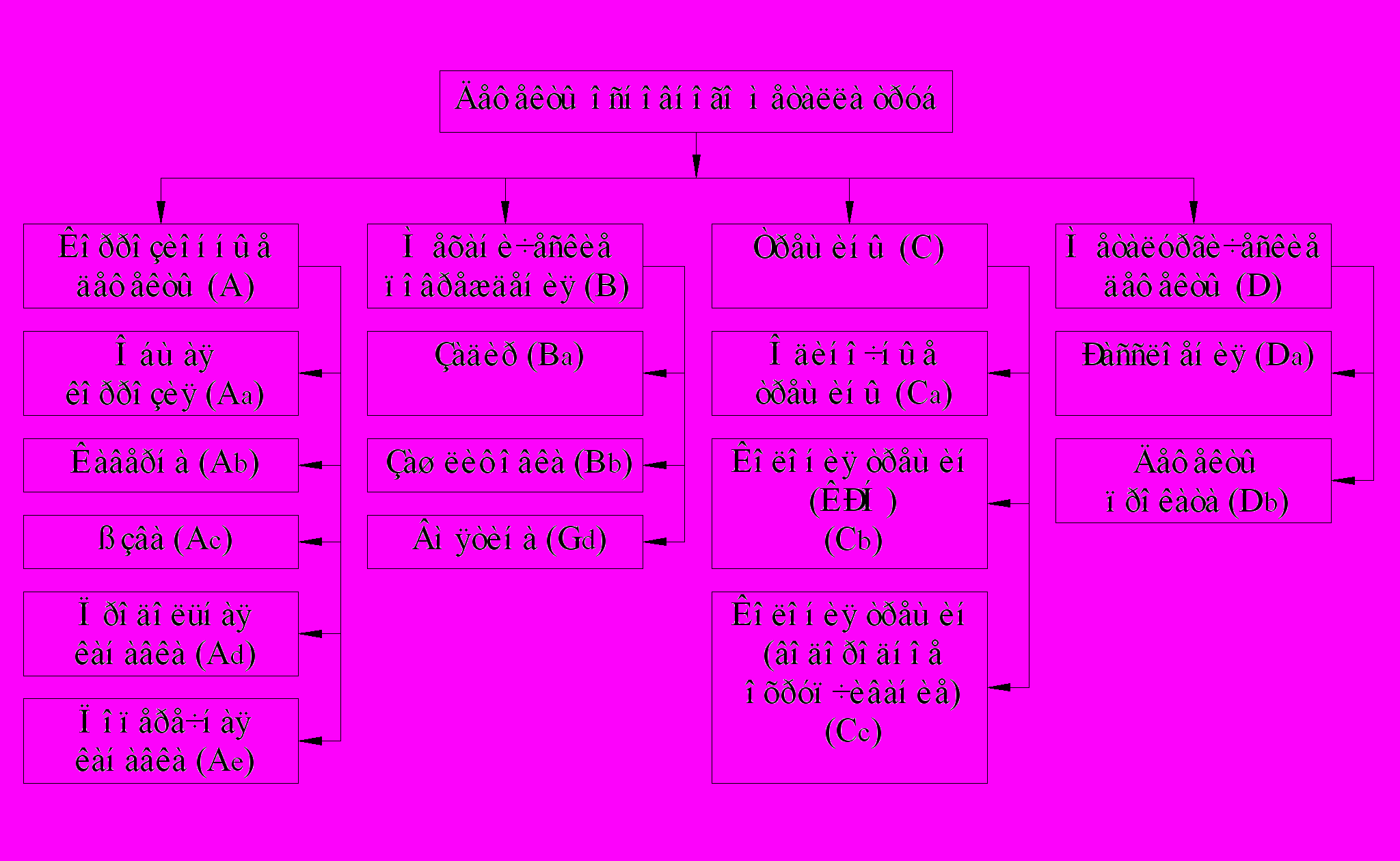
Рис. 1. Идентификационное деление дефектов основного металла труб на классы.
Как показывает анализ топографии магнитного поля рассеивания над дефектами, её принято характеризовать тангенциальными Hx и нормальными Hy составляющими магнитного поля рассеяния над дефектами. Анализ топографии показывает, что для распознавания дефектов в качестве критериев может быть использовано большое количество признаков например: расстояние между экстремумами Hy и Hx, амплитуда и длительность сигнала на различных уровнях и т.д. Все это связано с конкретными условиями контроля, поэтому необходимо проводить предварительное обучение системы контроля на образцах с модельными дефектами, максимально приближенными к реальным дефектам. Задача распознавания вида несплошности формулируется следующим образом: на основе поперечных характеристик из анализа кривых распределения нормальных или/и тангенциальных составляющих поля несплошностей найти подходящий алгоритм распознавания различных видов модельных несплошностей в контролируемом материале.

Рис. 2. Алгоритм модели имитации, используемый для решения обратной задачи при контроле трубопроводов
Из этого следует, что распознавание дефектов является инверсной задачей, т.е. задачей, где ПРМП сигналы, измеренные датчиками, интерпретируются в терминах формы, размеров и местоположения дефектов. Для решения данной задачи были применен подход, при которых МКЭ играет существенную роль представлен на (рис. 2), здесь МКЭ используется в итеративной схеме. Изменение сигнала может происходить не только из-за изменений формы дефектов, но и из-за других причин, таких как способность стенки трубы к намагничиванию, скорости снаряда, напряженного –деформированного состояния материала и т.д… В модель вводится вектор параметров, характеризующий профиль дефекта, который сравнивается в процессе итерации с экспериментально полученными сигналами до тех пор, пока прогнозируемая модель не сойдется с экспериментально полученным сигналом ПРМП. При движении газа по трубопроводу происходит значительное падение давления по длине в результате преодоления гидравлических сопротивлений. В этих условиях плотность газа уменьшается, а линейная скорость увеличивается.
Для обеспечения надежного распознавания дефектов трубопровода скорость дефектоскопа не должна превышать 2-3 м/с. Снижение скорости движения дефектоскопа может быть достигнуто за счет регулирования на компрессорной станции потока газа по газопроводу. Однако это связано с нарушением режима транспортировки газа и приводит к экономическим потерям. Этот недостаток может быть устранен регулированием скорости движения дефектоскопа за счет байпасирования (перепускания) через него части газа. В настоящей работе выполнен газодинамический расчет для дефектоскопа диаметром 1420 мм на рабочее давление 75 кгс/ см2 с целью определения основных параметров байпасной системы. Анализ байпасных систем действующих дефектоскопов приводит с следующей расчетной схеме (рис.3)
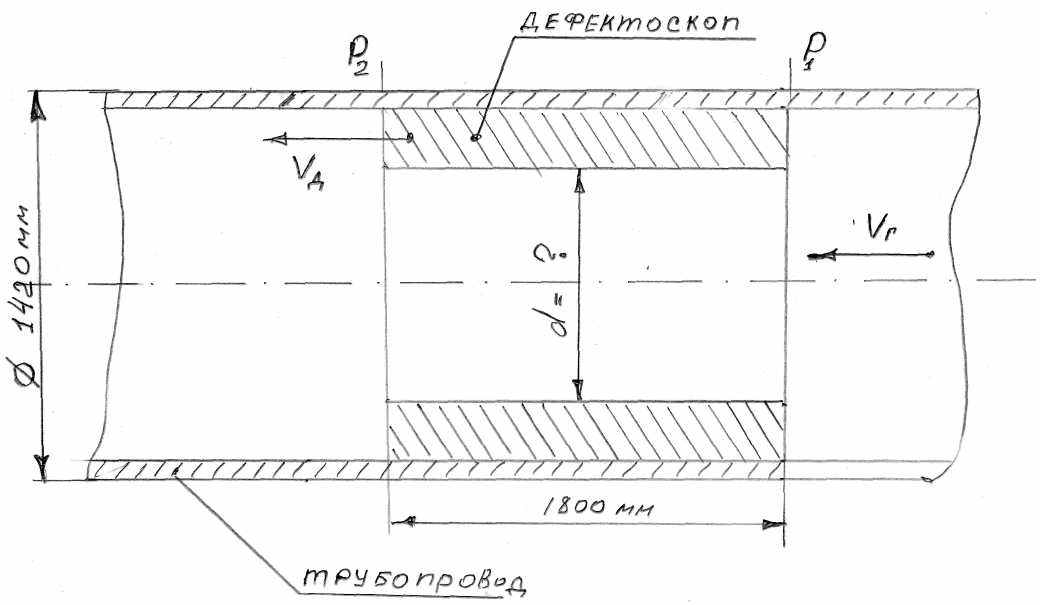
ДЕФЕКТОСКОП
Р
ТРУБОПРОВОД
ис.3. Расчетная схема байпасного устройства
Где Р1-Р2 –перепад давления на дефектоскопе
Vд-скорость дефектоскопа
Vг-скорость газа
d-диаметр внутреннего перепускного отверстия
Ниже приведены результаты расчета площади перепускного сечения дефектоскопа (в процентах от площади сечения трубопровода) от скорости потока газа в трубопроводе.
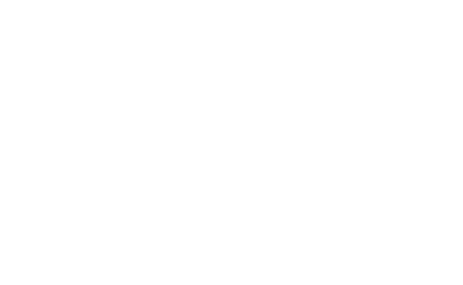
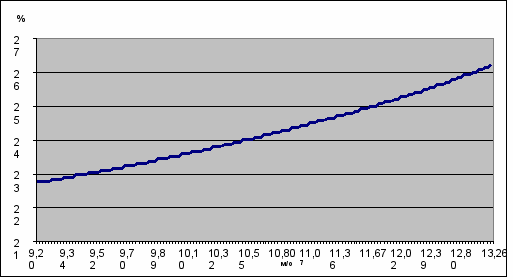
Рис 4. Зависимость площади поперечного сечения от скорости газа
Из рис 4. следует что, для того чтобы дефектоскоп при заданном весе сохранял заданную скорость движения, не изменяя режима перекачки газа в трубе, в нем должена изменяться площадь перепускного сечения в зависимости от скорости потока в определенных пределах.
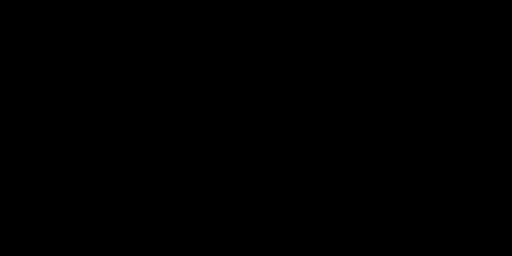
Рис. 5. График изменения скорости газа вдоль трубопровода
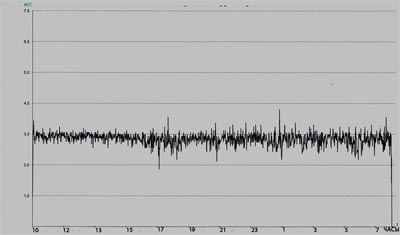
Рис. 6. График изменения скорости движения дефектоскопа вдоль трубопровода
На рис.6. показано изменение скорости дефектоскопа при пропуске его по трубопроводу, который проложен через Уральские горы. Скорость газа в трубопроводе менялась согласно графика, приведенного на рис. 5., откуда следует, что отношение максимальной скорости газа в трубопроводе к средней скорости движения дефектоскопа равно 4,5. На рисунке 7. представлено сменное устройство регулирования скорости движения дефектоскопа, устанавливаемое на дефектоскоп КОД4М-1420у.
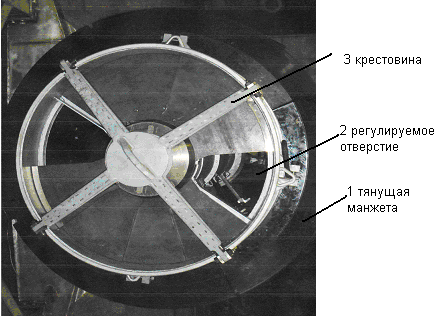