Резцы (гребенки), имеющие наибольшее применение, и резьбонакатные головки с роликами к ним, как один из самых перспективных и производительных видов инструмента
Вид материала | Литература |
- Заключение, 110.93kb.
- Театр один из самых древних видов зрелищного искусства. Его история насчитывает более, 47.73kb.
- Краска один из самых необходимых материалов при ремонте. Ее окрашивают стены, потолки,, 644.37kb.
- Методика проектирования инструмента. Содержание рабочего чертежа на него. Формы, геометрия, 172.74kb.
- А, роста и продуктивности нетрадиционных видов птицы представляет собой одну их интересных, 493.97kb.
- А. А. Эрли Красноярский государственный педагогический университет им. В. П. Астафьева,, 64.58kb.
- Задачи: познакомить с краткой историей возникновения инструмента; рассказать о самых, 92.97kb.
- Московский международный дом музыки концерты декабря, 72.69kb.
- Рекомендации для расчета режущего инструмента при выполнении дипломного и курсового, 204.72kb.
- Е. Ю. Захарова применение инструмента факторинга в процессе обновления парка воздушныхсудов, 42.04kb.
При работе головку, установленную на поперечном суппорте автомата, от кулачка подают на вращающуюся заготовку. При совпадении оси резьбонакатных роликов с осью заготовки головка быстро отводится назад в исходное положение.
Простота конструкции и технологичность изготовления головки—преимущества ее по сравнению с тангенциальными головками с синхронным вращением резьбонакатных роликов.

Недостатки головки:
1) небольшой диапазон диаметров накатываемых резьб из-за наличия в конструкции эксцентриковых осей. что увеличивает номенклатуру головок по сравнению с существующими тангенциальными головками с синхронным вращением роликов.
2) нестабильность накатывания резьб с точностью выше седьмой степени при шероховатости профиля Rа≥1,25 мкм.
РАСЧЕТ СИЛ ПРИ НАКАТЫВАНИИ РЕЗЬБ
Силы при накатывании резьб и их распределение по отдельным виткам роликов и роликам—основные факторы, определяющие конструктивные размеры отдельных узлов резьбонакатных головок и работоспособность роликов.
Однако до настоящего времени не были установлены общие основные параметры процесса накатывания резьб, определяющие нагрузки на ролики, и их влияние на силы, возникающие при накатывании.
Проведенные эксперименты выявили влияние на силы при накатывании только отдельных частных факторов, как, например, шаг резьбы, диаметр роликов и т. д., причем изменяющихся в узких диапазонах [19, 28].
Такие исследования носят ограниченный характер, и рекомендации оказываются неправомочными при изменении условий накатывания, например, диаметра ролика или заготовки, длины заборной и калибрующей частей ролика и др.
Исследованиями ВНИИ установлены основные параметры процесса накатывания и их влияние на возникающие силы при различных условиях эксплуатации.
За основные параметры процесса накатывания, определяющие нагрузку на отдельные витки роликов и ролики в целом, приняты •средняя толщина выдавливаемого слоя аср, приходящаяся на периметр контакта 1ц витков заборной части ролика с заготовкой в плоскости, проходящей через ось заготовки, площадь контакта Sк витков ролика и периметр контакта lп.к витков калибрующей части ролика.
Тогда в общем виде зависимость радиальной силы Рр, возникающей при накатывании, может быть выражена зависимостью

где х, у, и z—степени влияния соответствующих параметров;
С—величина, постоянная для данных условий.
Аналогично может быть выражена тангенциальная сила Рт.
Средняя толщина выдавливаемого слоя

где F—площадь выдавливаемого слоя в плоскости контакта.
Площадь контакта второго и всех последующих витков ролика

где lк—длина дуги контакта,
Для первого витка

Значения площадей контакта, рассчитанные по этим формулам, превышают фактические площади на 3—7% в зависимости от диаметров ролика Dр и заготовки Dз и величины внедрения витков Нв.н что не оказывает практического влияния на величину определяемых сил.
Подставив значения аср и Sк в уравнение (5) получим в общем виде следующую зависимость:

Среднее значение силы, действующей на ролик:

где f, lк.з, lп.к —средние значения параметров процесса накатывния, относящиеся к одному ролику;
f—выдавливаемая площадь, мм2;
lп.з, lк.з —периметр и длина дуги контакта витков заборной части, мм;
lп.к — периметр контакта витков калибрующей части, мм.
Произведение lп.з lк.з не является средней контактной площадью, а лишь косвенно ее характеризует. Результаты экспериментов и математический вывод зависимостей показали целесообразность использования в качестве одного из основных параметров процесса накатывания такого произведения, что не исключает возможность замены его на площадь контакта.
В схемах для расчета параметров F, lп. и lк. (рис. 21) выдавливаемая площадь и периметр контакта зависят от величины внедрения витков ролика и их формы, а длина дуги контакта—от величины внедрения и диаметров ролика и заготовки.
В зависимости (6) степени влияния х, у и z и постоянная С определяются экспериментальным путем. Для расчета средних значений параметров f, lп.з, lк.з, lп.к предварительно определяются параметры F, lп. и lк для каждого витка роликов и находится их сумма. При этом учитывается, что каждый виток роликов, за исключением первого вступающего в работу витка, воздействует и на металл, выдавленный предыдущими витками (рис, 22).
В табл. 7 приведены основные формулы и коэффициенты для определения параметров процесса накатывания приминительно к резьбам: трапецеидальной однозаходнойпоГОСТ 9484—73, трубной цилиндрической по ГОСТ 6357—73 и резьбы насосно-компрессорных труб и муфт по ГОСТ 633—63 (при Нв.н≥НR для F и lп).
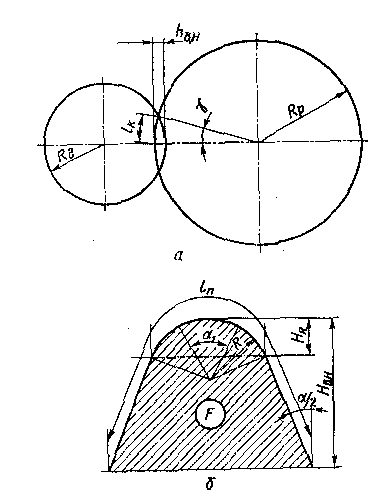
Рис. 21. Схема для расчета: а - длины дуги контакта; б — выдавливаемой площади и периметре контакта
Длина дуги контакта (см. рис. 22) определяется по формуле

Угол γ определяется из зависимости

где

Методика расчета значений основных параметров процесса накатывания состоит из следующих этапов.
1. Определение полной (накопленной) величины внедрения Нв.н для каждого витка по фактическим перепадам высот витков роликов и величина внедрения калибрующих витков Нвнк в заготовку от ее диаметра;

где hi —перепад между вершинами калибрующего и рассматриваемого витка,
2. Определение фактической величины внедрения hвн.

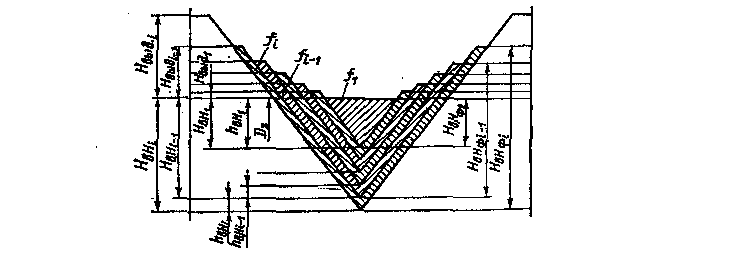
Рис. 22. Совмещенное расположение витков и выдавливаемая ими площадь. Индексами 1, i-1, i обозначены порядковые номера витков
Таблица 7
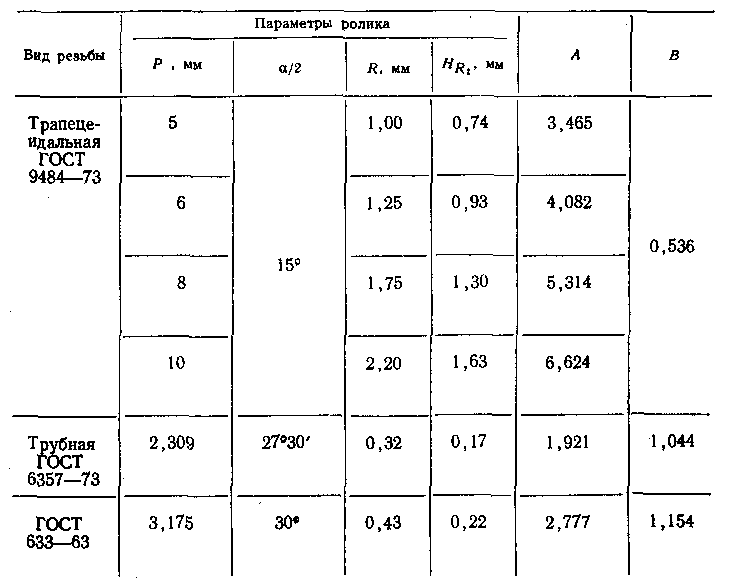
Продолжение
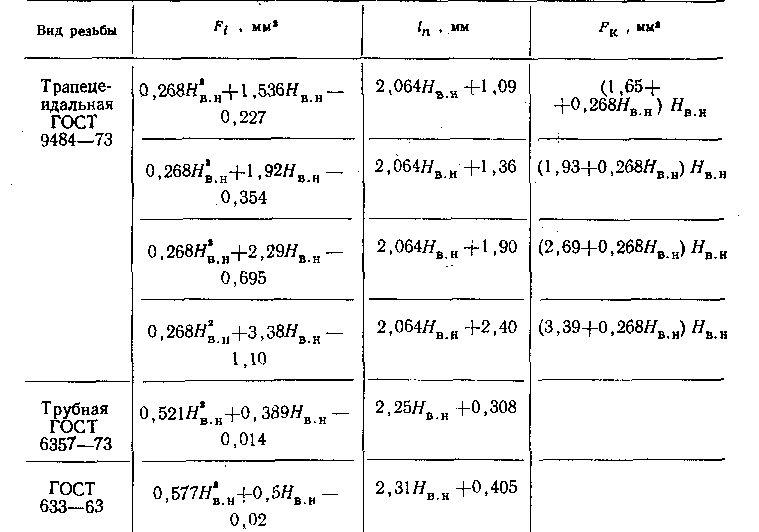
3. Определение величины выдавливания Нвыд, которая устанавливается из условий постоянства объема до и после деформации.
Для удобства расчетов произведена замена объема на площадь, что для практических случаев накатывания головками обусловливает погрешность в величине Нвыд не более 3%:

Формулы для определения Fi и значения коэффициентов А и В приведены в таблице.
Расчетные и экспериментальные величины Нвыд хорошо согласуются между собой.
При определении величины выдавливания Нвыдк калибрующего витка в формулу подставляются значения Нвнк и Fк.
При определении Fк в формулы F=f(Нвн) для витка с радиусной вершиной и Fк=φ(Нвн) для витка с плоскосрезанной вершиной (см. табл. 7) подставляются значения Hвн=Hвнк.
Значение Нвнк рассчитывается из условия равенства площадей Fк и Fвыд до и после деформации, что обеспечивается при H´внк =t´—Hвдк, где t´=t+Δt- наибольшая высота профиля накатываемой резьбы, мм; t —номинальная высота профиля резьбы, мм;
Δt —половина нижнего отклонения на внутренний диаметр резьбы, мм.
4. Определение полной (накопленной) величины внедрения Нвн.ф с учетом металла, выдавленного предыдущими витками:

5. Определение общей (накопленной) площади деформации F, нарастающей от витка к витку (см. табл. 7) путем подстановки значений Нвн.ф.
6. Определение условной величины H´вн.ф от внедрения данного витка:

7. Определение условной величины F´ путем подстановки значений H´вн.ф.
8. Расчет фактической площади, деформируемой одним витком:

9. Расчет периметра контакта lп путем подстановки значений Hвн.ф.
10. Расчет длины дуги контакта lк [см, формулу (7)], причем значение х определяется по фактической величине внедрения hвн.
В результате экспериментов при накатывании резьбы на стали 45 твердостью НВ 190—212 получена следующая зависимость:

где f/lп.з—средняя толщина деформируемого слоя.
Зависимость (9) получена при накатывании наружной трапецеидальной резьбы с шагом 5, 6, 8 и 10 мм с использованием заготовок роликов Dз=140÷112 мм и Dр =80÷130 мм, что обусловило следующие параметры процесса накатывания: f/lп.з =0,05÷0,25 мм, lп.з=6÷20 мм, lк.з=5÷10 мм, lп.к = 10÷56 мм.
Расчетное значение сил с достаточной для практики точностью согласуется с экспериментальными данными.
Полученная зависимость отличается универсальностью и позволяет определять значения сил независимо от типа и шага накатываемой резьбы, диаметров роликов и заготовки и различий в конструктивных параметрах резьбовых витков роликов.
С помощью этой формулы может быть проверена, в частности, оптимальность создаваемых конструкций роликов.
Значение тангенциальной силы по экспериментальным данным составляет 0,12—0,15Рр.
Анализ полученной зависимости показывает, что с уменьшением толщины выдавливаемого слоя, произведение периметра и длины дуги контакта витков заборной части и периметра контакта витков калибрующей части силы при накатывании уменьшаются. Оптимальность конструкций отдельных витков роликов и роликов в целом может быть оценена по величинам параметров процесса накатывания, которые они обусловливают. В частности, оптимальное количество витков на калибрующей части роликов nк=2.
В установленной зависимости произведение lп.з lк.з косвенно характеризует площадь контакта Sк.
В дальнейшем предполагается установить зависимость, в которой это произведение будет заменено Sк.
Таблица 8
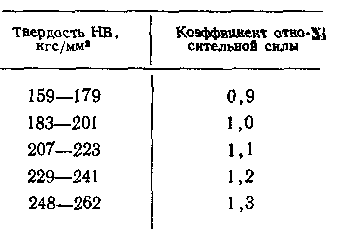
Установленная зависимость действительна при накатывании резьб в конструкционной углеродистой стали твердостью НВ 183—201.
При изменении твердости необходимо пользоваться поправочными коэффициентами (табл. 8), установленными из условий пропорциональной зависимости величин сил от твердости.
РАСЧЕТ РОЛИКОВ К РЕЗЬБОНАКАТНЫМ ГОЛОВКАМ
В большинстве рассмотренных конструкций резьбонакатных головок (типов ВНГН, ГУР, РНГМ и др.) перемещение роликов к оси и от оси заготовки осуществляется с помощью эксцентрикового устройства. Диаметр роликов при этом должен быть выбран таким образом, чтобы обеспечить надежную работу механизма раскрытия и минимально необходимый зазор между роликами и деталью при отводе головки.
Зазор Δ между роликами и деталью (рис. 23) аналитически может быть представлен зависимостью
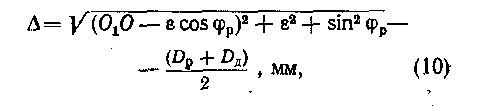
где О1О—межцентровое расстояние между эксцентриковой осью и деталью, мм (величина, постоянная для данной конструкции головки определенного типоразмера);
ε—эксцентриситет, мм;
φр — угол раскрытия, град;
Dр—наружный диаметр ролика, мм;
Dд — наименьший внутренний диаметр детали, мм.
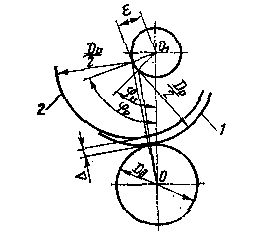
Рис. 23. Схема расположения ролика и заготовки: 1 — в момент накатывания;
2—3 момент раскрытия
В момент накатывания зазор Δ=0 и φр=φн. При этих условиях

Во избежание заклинивания эксцентриковых осей и обеспечения безотказного быстрого раскрытия головки в конце хода угол φн следует принимать равным 50—55°.
После раскрытия головки зазор должен быть:

где Δ'—зазор между наружными диаметрами роликов и накатываемой резьбы;

где t — теоретическая высота профиля накатываемой резьбы, мм;
Н0d1—нижнее отклонение по внутреннему диаметру, принимаемое для меньшей степени точности накатываемы резьб.
Зазор Δ' принимается равным для метрических резьб диаметром до 5 мм 0,5 мм, диаметром 5—20 мм—1 мм, для резьб большего диаметра— 1,5 мм. Для трапецеидальных резьб зазор Δ'=2—4 мм в зависимости от длины, диаметра и шага накатываемой резьбы.
При величине зазора Δ, определенной по формуле (11), угол раскрытия φр не должен превышать 170°:

При φр> 170° накатывание рекомендуется производить головкой другого типоразмера.
Рассчитанное значение наружного диаметра ролика обычно округляют до целого числа.
Наружный диаметр резьбы ролика для резьбонакатных головок тангенциального типа может быть определен [29] по зависимости

где Kр и Kи—число заходов ролика и изделия;
dз и dв—диаметр заготовки и внутренний диаметр накатываемой резьбы, мм;
Pср = (3,5—4) Ơт—удельное среднее давление, МПа;
Е—модуль упругости обрабатываемого металла, МПа;
Ơт — предел текучести, МПа.
После определения наружного диаметра ролика определяют его средний и внутренний диаметры, для чего рассчитывают значение высот головки t1р и ножки t2р витка ролика (расстояния от среднего диаметра до вершин выступов и впадин витков калибрующей части), обеспечивающие возможность работы как открытым, так и замкнутым контуром.
Для трапецеидальной резьбы

где ;t1 и t2—номинальная рабочая высота головки и ножки накатываемой резьбы;
Р— шаг накатываемой резьбы, мм;
Δизг—допуск на изготовление, мм;

где H1— рабочая высота профиля резьбы, мм.
Радиус при вершине R=0,19 Р.
Допуск на изготовление принимается равным для шагов Р≤2 мм 0,02 мм; для Р=2,5÷5 мм—0,03 мм и для Р>5 мм—0,04 мм.
В случае прямолинейной вершины у витков калибрующей части роликов

где ас — номинальный зазор в резьбовом соединении (ГОСТ 9484—73).
Для метрической резьбы

где t2=0,217Р и t1=0,325Р.
Радиус при вершине R=0,126Р.
Допуск на изготовление принимается равным 0,01 мм (Р≤1 мм); 0,02 мм (Р=1,25—3,0 мм) и 0,03 мм для больших шагов.
В случае прямолинейной вершины у витков калибрующей части роликов

где t1=t2=0,32Р (ГОСТ 6357—73).
Радиусы при вершине и впадине витка ролика R1=(0,136Р—0,043) мм и R2= (0,137Р+0,026) мм.
Ширина роликов Вр определяется по максимальному шагу резьбы, накатываемой данной головкой. За основу берется ролик с односторонней заборной частью (первый в комплекте):

где nз—количество витков на заборной части;
l1—расстояние от переднего торца до первого витка заборной части;
l´1—расстояние от заднего торца до последнего витка калибрующей части.
При определении ширины ролика принимали nз=2 или nз=3 (максимально возможное количество витков), С целью уменьшения сил накатывания число витков калибрующей части следует назначать наименьшим, т. е. nк=2 читывая уменьшение расстояния l1от ролика к ролику за счет смещения витков на величину P/z приводящее к уменьшению количества полных калибрующих витков на ряде роликов, принимаем для первого ролика nK=3.
С уменьшением шага накатываемой резьбы при неизменном l1 размер l´1 будет увеличиваться.
Ширина первого ролика при двусторонней заборной части связана с параметрами ролика соотношением

где l1=Р/2+Δl и l´1=(z-1)P/z+l1, причем поправка Δl≥0.
Здесь учтено, что при работе другой стороной ролика первый ролик должен работать, как последний.
При заданных ширине и параметрах ролика поправка Δl на величину l1 и l´1 определяется из зависимости

Основные методические положения по конструированию заборной части роликов с конической схемой расположения кольцевых витков на заборной части (см. рис. 22), разработанные применительно к роликам для накатывания резьбы на водогазопроводных трубах [30], распространяются также на ролики для накатывания резьбы на сплошных изделиях и сводятся к следующему;
1) выбор закона распределения Fi=f(i) площадей, деформируемых отдельными витками;
2) определение общей (накопленной) площади деформирования ΣFi=ψ(i), нарастающей от витка к витку с учетом установленного закона распределения;
3) установление закона изменения F=φ(Hвн). Деформируемой площади от величины Hвн подъема витков (глубины внедрения вершины витка в заготовку) при принятой форме витков заборной части;
4) определение величины Hвн подъема каждого витка из зависимости F=φ(Hвн) путем подстановки в нее значения ΣFi , относящегося к данному витку.
В этих закономерностях i—порядковый номер витка, количество которых может изменяться от 1 до п (п—количество витков на заборной части).