Резцы (гребенки), имеющие наибольшее применение, и резьбонакатные головки с роликами к ним, как один из самых перспективных и производительных видов инструмента
Вид материала | Литература |
СодержаниеДвухступенчатые метчики Регулируемые метчики для нарезания крупных резьб Профилирование резьбонарезных резцов |
- Заключение, 110.93kb.
- Театр один из самых древних видов зрелищного искусства. Его история насчитывает более, 47.73kb.
- Краска один из самых необходимых материалов при ремонте. Ее окрашивают стены, потолки,, 644.37kb.
- Методика проектирования инструмента. Содержание рабочего чертежа на него. Формы, геометрия, 172.74kb.
- А, роста и продуктивности нетрадиционных видов птицы представляет собой одну их интересных, 493.97kb.
- А. А. Эрли Красноярский государственный педагогический университет им. В. П. Астафьева,, 64.58kb.
- Задачи: познакомить с краткой историей возникновения инструмента; рассказать о самых, 92.97kb.
- Московский международный дом музыки концерты декабря, 72.69kb.
- Рекомендации для расчета режущего инструмента при выполнении дипломного и курсового, 204.72kb.
- Е. Ю. Захарова применение инструмента факторинга в процессе обновления парка воздушныхсудов, 42.04kb.
Этап 6.

Этап 8.

Этап 9. Наружные диаметры метчиков определяются по той же формуле, за исключением чистового и предпоследнего метчика комплекта с номером п—1, диаметры которых равны dоп.
Этап 10. Для метчиков комплекта с номерами (п—1) и (n—3)

для остальных метчиков

Этап 11.
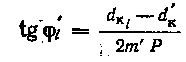
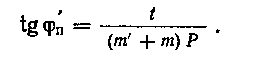
Хорошие результаты при нарезании резьбы в деталях из высокопрочных закаленных сталей, жаропрочных и титановых сплавов показывают корригированные метчики [8], у которых угол профиля меньше угла профиля нарезаемой резьбы (рис. 7).
В результате между обрабатываемым материалом и боковыми поверхностями режущих зубьев возникают зазоры, что уменьшает момент трения, устраняет защемление зубьев во впадинах резьбы и способствует лучшему проникновению смазочно-охлаждатощей жидкости в зону резания.
Получение заданного профиля резьбы достигается в результате обратной конусности по среднему диаметру метчика. Угол обратного конуса может быть рассчитан по формуле
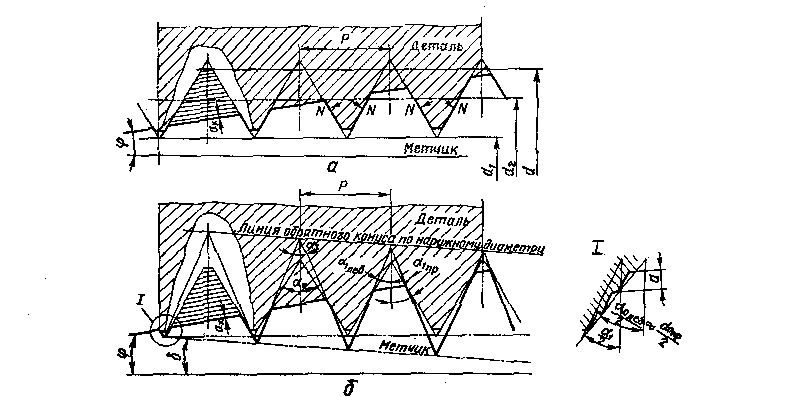
Рис. 7. Схемы резания нормальным (а) и корригированным (б) метчикам

где δ— половина угла обратного конуса;
αо,α1—углы профиля резьбы и метчика соответственно.
При нарезании метрической резьбы (я=60°) угол профиля α1=55°, что обеспечивает появление достаточных зазоров между зубьями метчика и обрабатываемой деталью и позволяет контролировать средний диаметр метчиков с помощью инструментов, предназначенных для проверки дюймовых резьб (рис. 8).
В табл. 3 приведены основные размеры и область применения метчиков (d=6÷42 мм, Р=1÷ 2 мм, z=3÷ 4).
Эффективность применения корригированных метчиков подтверждается табл. 4, в которой приведены данные по стойкости метчиков М14х1,5 (z=3) из стали Р9К5 различной конструкции при работе на различных материалах и при охлаждении сульфофрезолом с расходом 6—8 л/мин.
Корригированные метчики можно успешно применять и при нарезании резьбы в глухих отверстиях при условии использования комплектных метчиков [8].
При нарезании глухой резьбы величина допустимого сбега резьбы, определяющая работоспособность чистовых метчиков, должна быть возможно больше.
Шероховатость вследствие несоответствия углов профиля резьбы и метчика Rа<2,5 мкм.
Один из резервов повышения стойкости метчиков при нарезании резьбы в труднообрабатываемых материалах - воздействие на
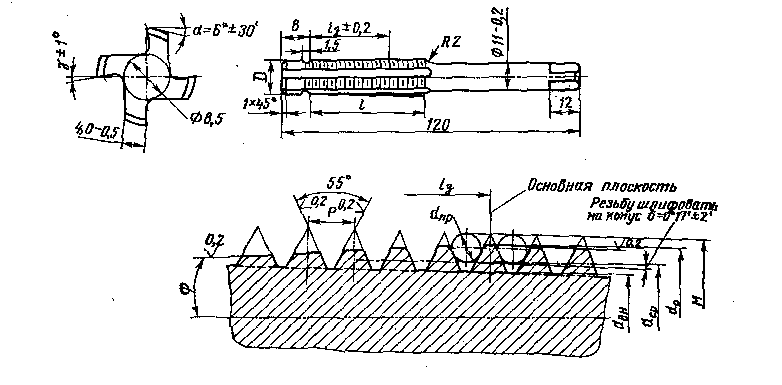
Рис. 8. Конструкция корригированного метчика
Таблица 3
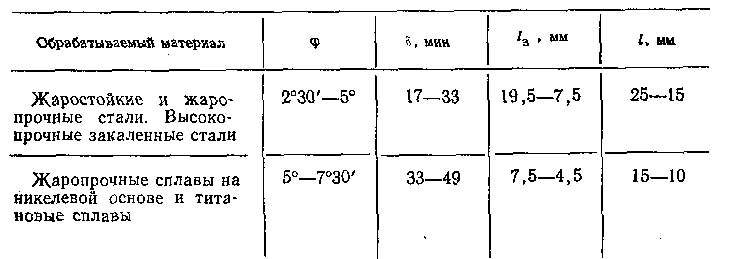
процесс резания ультразвука. Особенно эффективно воздействие ультразвуковых колебаний при изготовлении метчиками мелко размерной резьбы М1—М8 [14]: крутящий момент уменьшается в 1,3—1,6 раза, устраняет заклинивание метчиков, процесс нарезания стабилизируется, стойкость метчиков возрастает в два раза.
Метчики известных конструкций полностью пригодны для ультразвукового нарезания, причем в отличие от метчиков М10 и более, длину которых необходимо рассчитывать с учетом резонансных условий и выдерживать с точностью ±5%, мелкоразмерные метчики для нарезания с воздействием ультразвука не отличаются по своим размерам от стандартных метчиков.
Таблида 4
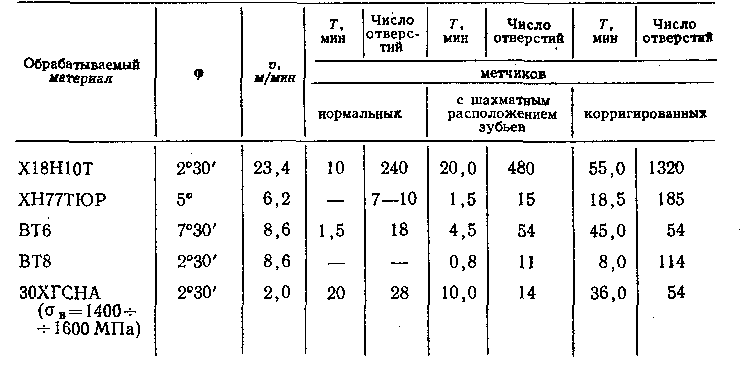
Основная конструктивная особенность метчиков для ультразвукового нарезания резьбы связана с необходимостью изменения переднего и заднего углов заборной части. Лучшие результаты показывают метчики с уменьшенным передним и увеличенным задним углами; они меньше изнашиваются по задней поверхности, а режущий клин их достаточно прочен—сколов не наблюдается даже при обработке высокопрочных сталей с Ơв==1600—1800 МПа.
Рекомендуемые углы заточки заборной части метчиков и скорость резания при нарезании резьбы в различных материалах приведены в работе [14]. В частности, для сплавов на основе титана (Ơв=700-1400 МПа) для метчиков М1—М2,5 γ=4°, α=20° и для метчиков МЗ—М8 γ=8°, α=12°; скорость резания находится в пределах 0.3—0,5 м/мин (М1—М2), 0,7—0,9 м/мин (М2.5—МЗ), 1,2—1,5 м/мин (М4—М5) и 3—5 м/мин (М6—М8).
Ультразвуковые колебания не оказывают влияние на точность нарезаемой резьбы. Рекомендуются следующие амплитуды колебаний: 1—2 мкм для метчиков М1—М1,8; 3—4 мкм для метчиков М2—М4: 5—6 мкм для метчиков М5—М8.
ДВУХСТУПЕНЧАТЫЕ МЕТЧИКИ
Применение двухступенчатых метчиков со второй ступенью несколько большего диаметра, т. е. две ступени метчика работают по схеме метчиков в комплекте (см, рис. 6, а), значительно уменьшает явление подрезания боковыми кромками зубьев метчика витков резьбы.
В этом случае подрезанный первой (черновой) ступенью профиль резьбы будет в значительной мере исправлен второй (чистовой) ступенью, работающей в основном только боковыми сторонами и срезающей сравнительно небольшой припуск—от 0,04 до 0,07 мм.
Для увеличения стойкости (производительности) и улучшения качества нарезаемой резьбы метчики конструируются из расчета толщины срезаемого слоя а = 0,008 — 0,015 мм и с винтовыми канавками с левым направлением (для правой резьбы) для получения одинаковых передних углов на боковых кромках.
Поскольку качество резьбы по точности и шероховатости определяется главным образом работой второй ступени, на главных режущих кромках ее предусмотрен передний угол γ=20° (рис. 9), обусловливающий на боковых режущих кромках передний угол γб≈10˚, обеспечивающий хорошие условия резания для гаммы обрабатываемых материалов с различными физико-механическими свойствами.
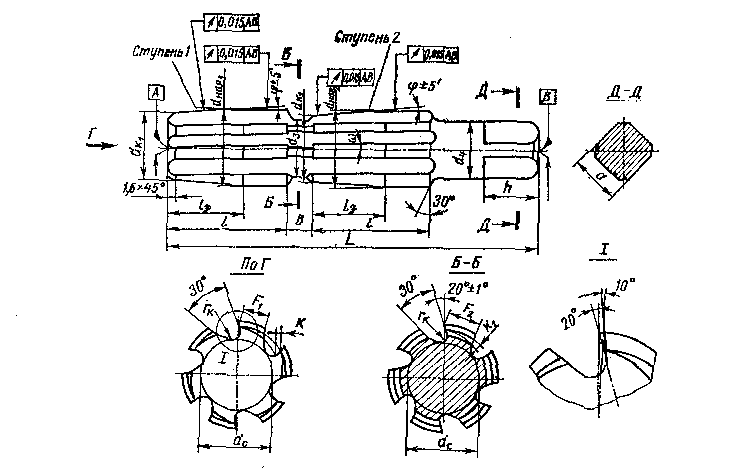
Рис. 9. Двухступенчатый метчик
Передний угол на первой ступени принимается равным 6—8°. Середина профиля резьбы первой и второй ступеней должна быть расположена на одной винтовой линии.
Применение двухступенчатых метчиков при нарезании в сквозных отверстиях различных видов резьб как в обычных, так и в труднообрабатываемых материалах обеспечивает нарезание резьбы с полем допуска 4Н, шероховатость поверхности Rz≤10 мкм, повышение производительности не менее чем в два раза.
Методика расчета двухступенчатых метчиков состоят из следующих этапов:
1. Определение номинальных размеров резьбы второй ступени метчика и допускаемых отклонений наружного, среднего и внутреннего диаметров dнар, dср и dвн, шага Р и половины угла профиля резьбы α/2.
В случае метрической резьбы используются СТ СЭВ 182—75, СТ СЭВ 842—78, ГОСТ 16925—71 (назначение верхнего отклонения наружного диаметра).
Допуски на средний диаметр метчика должны соответствовать первому классу по СТ СЭВ 842—78.
Наружный, средний и внутренний диаметры первой ступени метчиков равны этим диаметрам второй ступени за вычетом следующих величин: 0,16 мм — Р=0,75÷2,0; 0,20 мм — Р=2,5÷3,0; 0,24 мм— Р=3,5÷4,0; 0,28—Р=4,5÷5,0.
2. Установление параметров и количества стружечных канавок (табл.5).
Таблица 5
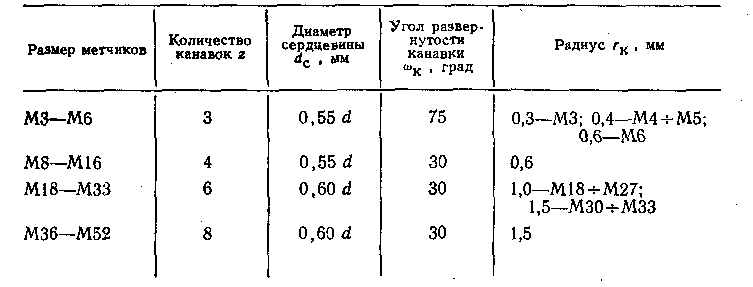
Ширина пера первой и второй ступеней F1 и F2 определяется
размерами стружечных канавок F2=0,3d.
3. Расчет угла уклона φ заборной части первой и второй ступеней (см, формулу 3), с учетом толщин срезаемого слоя: 0,008 мм—для метчиков МЗ—Мб; 0,01 мм—для метчиков М8— М10; 0,012—0,015 мм—для метчиков М12—МЗЗ; 0,015—0,02 мм— для метчиков М36—М52.
Рекомендуемые значения толщин срезаемого слоя могут быть изменены в большую сторону для сокращения длины метчика, но в этом случае обязательна проверка условий размещения стружки [см. формулу (1)].
4. Определение длины заборной части первой и второй ступеней [см. формулу (2)].
5. Определение основных размеров метчика (см. рис. 9): начальные диаметры: заборного конуса dк1, [см. формулу (4)];
dк2 = dк1 + Δd (Δd для шагов 0,75—0,1 мм; 1,0÷4,0—0,2 мм; 4,5÷5,0—0.3мм);
длина рабочей части каждой ступени; l=lз+10Р, диаметр хвостовика d4 и размеры квадрата h и а по ГОСТ 3449—71; ширина и диаметр выточки b=5Р; d3= d4; общая длина метчика при длине нарезаемого отверстия ≤13Р:

6. Определение угла подъема винтовых канавок:

7. Установление величин затылования по наружному диаметру заборной части К и по профилю К1 из расчета получения задних углов α=3º÷3º30´ и αб=7º÷10º (для обычных материалов).
Двухступенчатые метчики изготовляют с обратной конусностью (уменьшением диаметров в направлении к хвостовику), которая на 100 мм длины должна быть по среднему и внутреннему диаметрам 0,03—0,05 мм и по наружному диаметру 0,05— 0,10мм (для обычных материалов).
ВНИИ разработаны двухступенчатые метчики для нарезания резьбы в круглых плашках с резьбой МЗ—М52 (Р=0,5÷5 мм) и 1/8" труб.—11/2" труб. (Р=0,907÷2,309мм).
Методика расчета двухступенчатых метчиков для нарезания резьбы в плашках имеет следующие отличительные особенности.
Этап 1. Наружный диаметр dнар2, метчиков принимается для метрической резьбы равным номинальному наружному диаметру резьбы по СТ СЭВ 182—75 и для трубной резьбы—номинальному наружному диаметру за вычетом допускаемого нижнего отклонения на наружный диаметр резьбы по ГОСТ 6357—73.
Средний диаметр dср2, метчиков определяется по формуле

где d2 и Δd2 —номинальный средний диаметр резьбы и половина допускаемого нижнего его отклонения соответственно.
Для метрической резьбы нижнее отклонение соответствует полю допуска 6h (Р=0,75÷2,0 мм) и 6g (Р=2,5÷5,0 мм), для трубной резьбы — классу А.
Для резьб с полем допуска 8h—8g и класса В целесообразно иметь метчики с отклонением, соответствующим данным полям допусков.
Для метрической резьбы внутренний диаметр dвн= d1– 0,216Р+δ2, мм (d1—номинальный внутренний диаметр резьбы, мм; δ2 — допуск на изготовление метчика, равный 0,01—0,02 мм (Р=0,5÷1,5) и 0,02—0,035 мм (Р=2÷5).
Для трубной резьбы внутренний диаметр метчиков равен номинальному внутреннему диаметру резьбы за вычетом допускаемого нижнего отклонения на наружный диаметр резьбы (ГОСТ 6357—73).
Этап 2. Количество канавок метчика

где zпл—количество перьев плашки;
С=3—для метчиков М45Х4,0; М45Х4.5; М48Х5; 11/8" труб. и 11/2" труб.
С=2—для метчиков 1";11/4" и 13/8″труб.;
С= 1 —для всех остальных метчиков.
Ширина пера второй ступени F2 принимается из расчета перекрытия просвета между перьями плашки по внутреннему диаметру на 5% и более.
Этап 4. При расчетах длины заборной части метчиков высота для трубной резьбы принимается t=0,72Р (с учетом занижения диаметра начального конуса относительно внутреннего диаметра резьбы).
Этап 5. Диаметр начального конуса первой ступени определяется по формуле dк1 = dвн1 —0,15Р мм.
Длина калибрующей части каждой ступени равна высоте плашки Нп.
Расстояние между ступенями b≈Нпл/2 —1,4Р мм.
МЕТЧИКИ-ПРОТЯЖКИ
Метчики-протяжки рекомендуются для нарезания внутренней резьбы с относительно большим шагом в сквозных отверстиях, когда длина резьбы в несколько раз превышает ее диаметральные размеры.
Применение этого инструмента позволяет резко уменьшить число проходов. Так, при нарезании резьбы метчиками-протяжками машинное время сокращается до пяти раз по сравнению с нарезанием обычными метчиками и до 20 и более раз по сравнению с нарезанием резцами. Особенно эффективно применение данного инструмента при получении многозаходной резьбы.
Обрабатываемый материал — стали, чугуны, цветные металлы и сплавы; рекомендуемый диапазон диаметров нарезаемых резьб — 8—75 мм.
Во ВНИИ разработаны руководящие материалы, содержащие рекомендации по проектированию метчиков-протяжек, предназначенных для обработки материалов средней твердости Ơв≤750 МПа, а также чертежи на метчики-протяжки широкой гаммы размеров [15].
Метчик-протяжка состоит из следующих основных частей: переднего направления, заборного и калибрующего резьбовых участков и хвостовой части.
Переднее направление предназначено для центрования обрабатываемого изделия относительно оси инструмента в начальный момент. Оно должно быть такой длины, чтобы после установки заготовки крепежная часть была свободной и выступала за торец изделия. Диаметр переднего направления выполняют с полем допуска h9, принимая за номинал внутренний диаметр нарезаемой резьбы.
Хвостовая часть может быть гладкой или иметь режущие элементы для снятия возможных заусенцев. Во втором случае ее диаметр делают на 0,1—0,2 мм полнее внутреннего диаметра нарезаемой резьбы.
Известны три метода нарезания резьбы метчиками-протяжками [13].
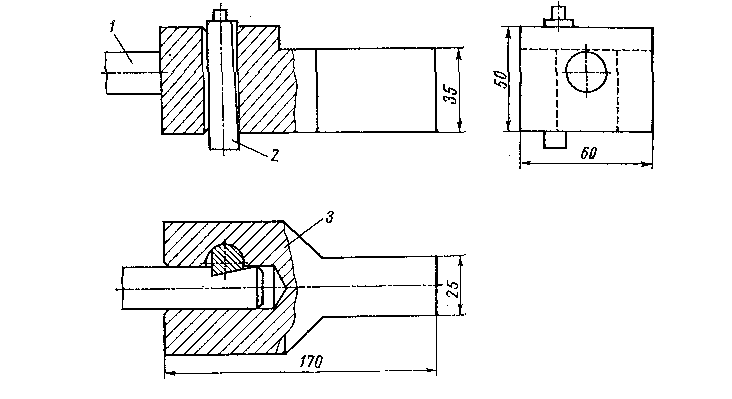
Рис. 10. Устройство для закрепления метчика-протяжка в рездедержателе токарного станка:
1 — метчик: 2 — клин; 3 — державка
Наиболее распространен метод, при котором обрабатываемую заготовку с метчиком, установленным в ней передним направлением, закрепляют в токарном патроне и метчик находится в переднем шпинделе станка. Выступающую из заготовки часть переднего направления закрепляют в устройстве (рис. 10), установленном на суппорте.
В процессе нарезания суппорт станка вместе с инструментом перемещается от ходового винта в сторону задней бабки. Шпиндель станка вращается вместе с заготовкой. При, нарезании правой резьбы шпинделю сообщается обратное вращение.
При втором методе обрабатываемую заготовку закрепляют на суппорте станка, а метчик-протяжку пропускают через отверстие заготовки и свободный конец инструмента зажимают в патроне.
Недостаток этого метода, применяемого в том случае, когда метчик не может войти в отверстие шпинделя,—необходимость применения специального приспособления для центрирования и закрепления заготовки.
При нарезании резьб большой длины (больше 100 мм) возможно применение третьего метода, при котором заготовку закрепляют на суппорте станка, а режущий инструмент устанавливают в центрах и передают вращение на два его конца от шпинделя станка и с помощью специального устройства.
При проектировании метчиков-протяжек и назначении их комплектности необходимо исходить из двух основных требований: обеспечения достаточной прочности метчиков и благоприятных условий для размещения стружки.
Достаточная прочность обеспечивается при условии, что длина заборной части метчиков-протяжек рассчитана при соблюдении соотношения

где k—число заходов нарезаемой резьбы.
Эта формула установлена по данным [15] с некоторыми уточнениями.
Условия для размещения стружки характеризуются коэффициентом, который определяется по ранее установленной формуле (1) и не должен быть меньше 0,5.
Согласно данным [15], максимальная длина инструмента Lmax=40d≤550 мм. В общем случае длина переднего направления (до начала заборного конуса) равна ;о+50 мм, хвостовой части (до начала резьбы) —25—50 мм и калибрующей части—4Р мм.
Расчет метчика-протяжки начинается с определения толщины срезаемого слоя, допустимой по прочности, и суммарной длины заборной части (формула (2) без учета сомножителя соз φ).
Применительно к трехканавочному метчику-протяжке для нарезания трехзаходной резьбы трап. 26Х (3Х8) в отверстиях длиной lо=80 мм (d1=18 мм—ГОСТ 9484—73): a=0,0116 мм; ;lз = 1065 мм.
При расчете lз значение t принято равным 4,64 мм с учетом превышения наружного диаметра метчика над номинальным значением приблизительно на половину допуска по СТ СЭВ 185—75 для многозаходных резьб.
Рассчитанная длина заборной части метчика может быть реализована в комплекте из трех-четырех метчиков.
При n=4 длина заборной части каждого метчика должна быть равна ~260 мм.
При конструировании одинарных метчиков-протяжек для трапецеидальной резьбы следует руководствоваться положениями, изложенными при рассмотрении двухступенчатых метчиков.
При конструировании метчиков-протяжек:
обратная конусность и затылование по профилю назначаются, как для обычных метчиков [16], т. е. обратная конусность 0,1— 0,15 мм на 100 мм длины и задние боковые углы αб=7/÷10/ (возможно увеличение обратной конусности);
профиль резьбы корригируется с учетом обратной конусности;
для фрезерования канавок необходимо предусмотреть фрезы по ГОСТ 3266—71: диаметр сердцевин для трех и четырехканавочных метчиков равен ~0,25d и ширина пера соответственно 0,4d и 0,25d;
для многозаходных резьб необходимы винтовые канавки, противоположные по направлению резьбы, но с одинаковыми углами подъема.
РЕГУЛИРУЕМЫЕ МЕТЧИКИ ДЛЯ НАРЕЗАНИЯ КРУПНЫХ РЕЗЬБ
Процесс нарезания резьб большого диаметра обычными метчиками, как правило, сопровождается большой величиной разбивания резьбы по среднему диаметру. С целью получения годных деталей при нарезании их новым метчиком последний выполняют по среднему диаметру близко к нижнему пределу поля допуска среднего диаметра резьбы изделия. Но в этом случае в процессе работы или после первой переточки метчик начинает нарезать резьбу, с которой не свертывается резьбовой калибр ПР, т. е. он становится непригодным к эксплуатации.
Разработанная конструкция регулируемых метчиков [17] позволяет управлять размером среднего диаметра нарезаемой резьбы и добиться нужного расположения центра группирования размеров партии деталей.
Рабочая часть метчика для нарезания резьб в сквозных отверстиях (рис. 11) состоит из трех секций: режущей 1, калибрующей 2 и ведущей 4. Калибрующая 2 и ведущая 4 секции выполнены в виде колец, надевающихся на хвостовик 8, выполненный заодно с режущей секцией /, и фиксируются относительно последней с помощью шпонок 3 и 5. При этом шпонка 3 выполняется треугольной, а на внутреннем диаметре калибрующей секции 2 сделано несколько треугольных шлицев. Ведущая секция с хвостовиком имеет шпоночное соединение. При изготовлении и в процессе работы калибрующая и ведущая секции метчика закрепляются режущей гайкой 6 и контргайкой 7.
Во время изготовления калибрующая секция метчика, имеющая несколько положений, устанавливается на хвостовике 8 так, чтобы шпонка 3 входила в средний шлиц (шлиц отмечен риской), после чего производятся заточка инструмента по передней грани и шлифование резьбы одновременно на всех трех секциях. При этом на режущей и калибрующей секциях зубья затылуются по профилю.
Величина затылования на режущей секции К1= (0,0035÷О.ОО6) Fп мм. Такая величина обусловливает значение заднего бокового угла в цилиндрическом сечении резьбы метчика 7'—10' и является оптимальной с точки зрения точности нарезаемой резьбы и стойкости метчиков [16].
Рис. 11. Конструкции сборных регулируемых метчиков
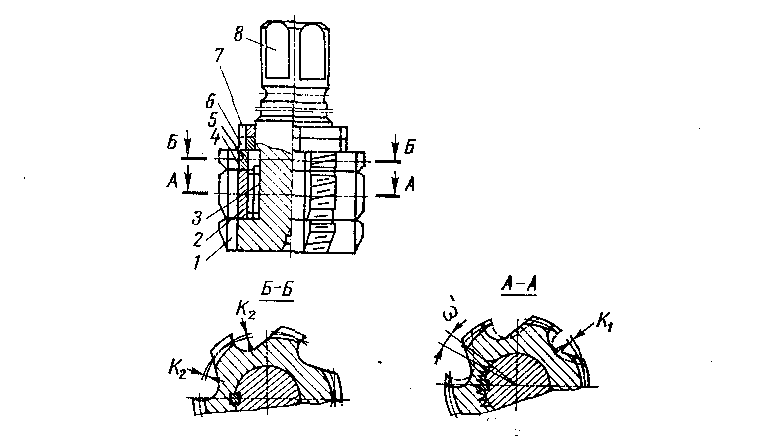
Величина затылования на ведущей секции К2=0,03—0,05 мм. Изменение размеров нарезаемой резьбы осуществляется при повороте калибрующей секции относительно режущей и ведущей секций на некоторый угол ω΄, что обеспечивает определенное осевое смещение зубьев относительно зубьев двух других секций.
Такое рассогласование секций позволяет увеличить ширину профиля нарезаемой резьбы и соответственно средний диаметр на некоторую величину

Трехсекционный метчик может быть использован для нарезания резьб как в сквозных, так и в глухих отверстиях. Однако для нарезания резьб в глухих отверстиях не требуется ведущая секция, и конструкция метчика в этом случае может быть упрощена.
Для нарезания резьбы в сквозных отверстиях необходимо изготовление ведущей секции с бочкообразными зубьями, так как в противном случае после выхода из отверстия последнего зуба режущей секции калибрующая не может обеспечить резания. При наличии ведущей секции, зубья которой вошли в витки нарезанной резьбы детали, после выхода из отверстия режущей части резание калибрующими зубьями будет обеспечиваться за счет рассогласования между калибрующей и ведущей секциями метчика.
В этом случае при резании правыми боковыми кромками зубьев калибрующей секции (секция повернута вперед) метчик будет упираться в профиль нарезанной резьбы левыми вершинками бочкообразных зубьев ведущей секции, а при резании левыми боковыми кромками (секция повернута назад) —правыми вершинками зубьев ведущей секции.
Такие метчики могут быть использованы для нарезания точных резьб большого диаметра за один проход. В случае необходимости они могут быть использованы для нарезания резьбы в два и более проходов, а также в качестве последнего калибрующего метчика в комплекте метчиков при нарезании крупных точных резьб.
Шлифование резьбы двухсекционных регулируемых метчиков не отличается от шлифования обычных цельных метчиков.
ПРОФИЛИРОВАНИЕ РЕЗЬБОНАРЕЗНЫХ РЕЗЦОВ
И ГРЕБЕНОК
Один из наиболее эффективных способов увеличения производительности процесса—увеличение суммарной длины одновременно работающих режущих кромок.
Применительно к резьботочению это обеспечивается за счет выбора оптимальной схемы резания и оптимального распределения удаляемого припуска по проходам при работе однолезвийным инструментом или между режущими элементами многолезвийного инструмента.

Рис. 12. Схемы резания при резьботочении
При работе одним резцом схемы резания в зависимости от направления подачи резца относительно оси резьбы можно свести к трем схемам [18]: профильной (рис. 12, а), последовательной (рис. 12, б) и профильно-последовательной (рис. 12, в).
При профильной схеме резания направление подачи перпендикулярно к оси резьбы, при реализации остальных схем резания подача резца осуществляется под углом к оси резьбы, причем при последовательной схеме резания направление подачи совпадает с углом наклона стороны профиля, а при профильно-последовательной—под углом меньшим, чем угол наклона стороны профиля.
Профильная схема резания является наиболее распространенной. При реализации профильной схемы режущие кромки резца при внедрении в материал детали срезают его последовательными слоями и окончательно формируют профиль резьбы на последнем проходе. Удаляемые сечения имеют жесткую коробчатую форму, и поэтому для их срезания требуются значительные усилия резания. Наиболее загруженным в силовом и тепловом отношениях участком является его вершина, так как она работает в зоне несвободного резания, имеет небольшое поперечное сечение и участвует в резаний на протяжении каждого из проходов.
При последовательной схеме условия работы резца будут более благоприятными, однако резьба получается менее точной.
При профильно-последовательной схеме резания одна из режущих кромок резца может срезать весьма тонкие стружки, что приводит к снижению стойкости резца и ухудшению качества нарезаемой резьбы [18].
Для устранения этих недостатков используют комбинированную схему резания, т. е. несколько резцов для раздельного удаления припуска: профилирующий резец и один или больше предварительных резцов (форма профиля не лимитируется).
Одна нз разновидностей такой схемы получила наибольшее распространение на токарно-резьбонарезных полуавтоматах, в частности французской фирмы Kridan и западногерманской фирмы Етаg (рис, 12, г).
Необходимо отметить, что при комбинированной схеме резания количество проходов чистового резца зависит от точности попадания его в прорезанную резьбовую канавку, а последнее—от точности относительного расположения чистового и чернового резцов.
Наиболее оптимальная с точки зрения производительности—дифференцированная схема резания, при которой весь припуск срезается несколькими резцами за один проход.
На практике наибольшее распространение получили профильная и комбинированная схемы резания.
В работе [18] установлено, что оптимальный способ подачи—обеспечение постоянства площадей сечения вырезаемого материала по проходам. Переход от способа постоянства подач к указанному способу обеспечивает при одинаковом числе обработанных резцом деталей возможность уменьшения на 20—40% общего числа проходов и тем самым повышения производительности резьботокарных полуавтоматов по машинному времени в среднем на 30%.
Однако, согласно исследованиям ВНИИ, для создания приблизительно одинаковых условий работы резца на всех проходах целелесообразно иметь некоторое уменьшение вырезаемой площади на последних проходах.
Технические требования к большинству изготовляемых резьб допускают определенную величину сбега резьбы. Очевидно, в таких случаях для увеличения стойкости инструмента и производительности целесообразно применение многозубых резьбонарезных гребенок, каждый зуб которых является резцом и, следовательно, рассмотренная закономерность рационального распределения вырезаемой площади по проходам может быть применима для каждого зуба гребенки.
При проектировании гребенок за основу принимается профильная схема резания, при которой каждый предыдущий зуб гребенки по сравнению с последующим имеет определенное занижение как по вершине, так и по боковым сторонам.
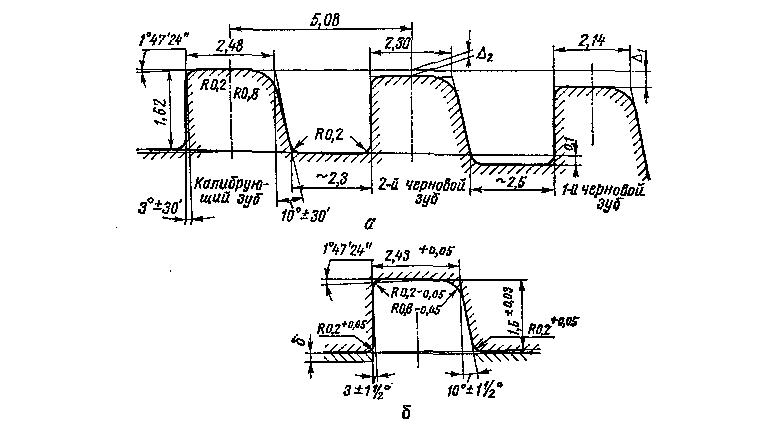
Рис. 13. Профиль:
а — трехзубой гре6енки для резьбы ОТТМ1 и ОТТГ1; б — резьбы ОТТМ1 и ОТТГ1 (δ — припуск под резьбу)
ВНИИ разработана и внедрена гамма многозубых (двух-, трех- и четырохзубых) твердосплавных резьбонарезных гребенок для нарезания внутренних цилиндрических и конических резьб с условным диаметром 60—219 мм (для призматических гребенок) и 219—324 мм (для гребенок-столбиков) в муфтах и наружных резьб на трубах нефтяного сортамента на муфто- и трубонарезных станках.
Применение резьбонарезных гребенок обеспечивает работу на скорости резания до 120 м/мин, точность резьбы степени 6, шероховатость Rz≤3,2 мкм при обработке сталей различных групп прочности.
При конструировании гребенок по возможности соблюдалось основное требование, заключавшееся в том, чтобы при заданном количестве проходов деление по высоте профиля для каждого из проходов (глубина врезания) обеспечивало уменьшение или равенство площади вырезаемого металла от прохода к проходу и от зуба к зубу при меньшей средней площади металла, вырезаемого чистовым зубом по сравнению с металлом, вырезаемым любым из черновых.
ВНИИ разработана методика профилирования резьбонарезных гребенок, обеспечивающая такую рациональную загрузку отдельных зубьев (рис. 13,14).
У спроектированной гребенки ширина каждого зуба меньше ширины последующего на величину, учитывающую наибольшую погрешность станка по шагу, допуск на изготовление и обеспечивающую при этом возможность резания боковыми сторонами.
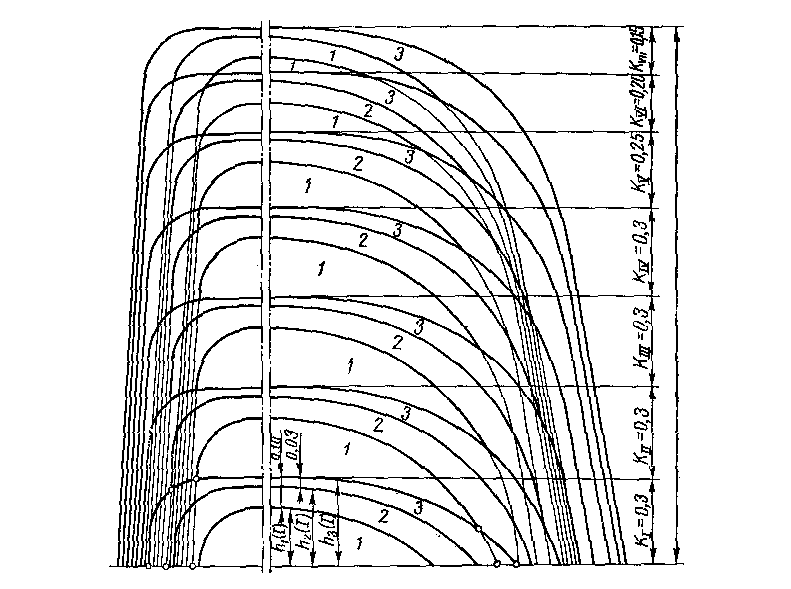
Рис. 14. Схема вырезания профиля резьбы ОТТМ1 трехзубой гребенкой за семь проходов (Δ1=0,10 мм; Δ2=0,03 мм; δ=0,18; KVIII=0). Цифрами обозначены порядковые номера зубьев гребенки.
Величины занижения Δ1 и Δ2 черновых зубьев по сравнению с чистовым определяют распределение вырезаемой площади между зубьями.
При числе проходов i=7 более оптимальны Δ1=0,10мм и Δ2==0,03 мм, обусловливающие уменьшение вырезаемой площади от зуба к зубу (1,97; 1,46 и 1,30 мм2), тогда как при Δ1=0,12 мм и Δ2=0,03 мм наибольшую площадь вырезает второй зуб, что нерационально (таб. 6). В то же время величины Δ1=0,12 мм и Δ2=0,03 мм обусловливают относительно рациональную загрузку зубьев при меньшем количестве проходов (i=5).
При конструировании гребенок необходимо иметь в виду, что конструкция гребенки может быть оптимальной только для определенного количества проходов.