Том числе и организационных, исторически называемая триз (теория решения изобретательских задач), но фактически давно переросшая в трс (теорию развития систем)
Вид материала | Документы |
СодержаниеНачало 50-х, Toyota Production System |
- Сайт www trizland ru Теория решения изобретательских задач — триз, 404.07kb.
- Программа (16 часов) Введение в теорию решения изобретательских задач (триз), 10.57kb.
- Семинар миэт по развитию творческого мышления. Кафедра «Философии и социологии», 487.96kb.
- Программа по триз предлагает три ступени обучения дисциплине: первая ступень 1-3 классы, 207.14kb.
- Программа по триз предлагает три ступени обучения дисциплине: первая ступень 1-3 классы, 206.85kb.
- Элементарные Преобразования Функций при Решении Изобретательских Задач Методом Функциональных, 91kb.
- Учебный план повышения квалификации профессорско-преподавательского состава по направлению, 157.97kb.
- Родной Alma Mater, ремонт общежития (подсобный рабочий 2 разряда). 4 курс (7 недель), 20.51kb.
- История развития вычислительной техники, 144.54kb.
- Рабочая программа учебной дисциплины «Основы теории решения изобретательских задач», 332.32kb.
Начало 50-х, Toyota Production System
Д
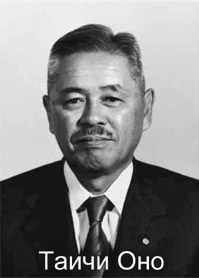
И снова мы сталкиваемся с людьми, вставшими на Путь, имеющими свою ДЦ. Это прежде всего представители семьи Тойтда: Сакиши Тойода (Sakichi Toyoda), его сын Кииширо Тойода (Kiichiro Toyoda) – фактический основатель Toyota Motor Company, Соиширо Тойода (Shoichiro Toyoda) и Эйджи Тойода (Eiji Toyoda). И конечно фактический создатель TPS (Toyota Production System – производственной системы компании Тойота), жесткий и решительный, но полный здравого смысла Таичи Оно (Taiichi Ohno).
Т
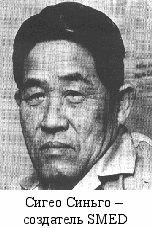
Главное, чтобы потребитель "вытягивал" нужный ему продукт из предприятия. Это позволяет затем предприятию вытягивать нужные ему комплектующие из своих поставщиков [6]. Образуется цепочка поставок – поток, пронизывающий уже не одно предприятие, а всю экономическую систему отдельной страны, да что мы, всего мира. Заметим, что без создания такой цепочки поставок локальное введение БП на одном отдельно взятом предприятии, конечно, будет иметь положительные последствия, но суммарный эффект будет не столь значительным, как хотелось бы.
Задачи, которые решались на этом пути создателями ТРS также были вполне под стать ТРИЗовским. Сократить время переналадки 1000-тонного пресса с 4 до 1,5 часов, а затем (еще через полтора месяца) вообще до 3 минут18 – это требует истинно ТРИЗовской смелости. Сейчас быстрая переналадка (SMED - Single-Minute Exchange of Die, или по-русски, замена штампа менее чем за 10 минут) является важнейшим и неотъемлемым инструментом БП.
И хотя начинается решение таких задач путем предварительного тщательного (то самое внимание к мелочам) анализа существующего процесса переналадки, с выделением в нем операций, которые в принципе можно произвести при продолжающем выдавать продукцию (работающем) оборудовании (так называемое "внешнее время"), завершается оно поиском порой очень неординарных решений [8].
Да, это все еще простой здравый смысл. И при решении задач SMED не используются приемы поиска и устранения противоречий. Но мы не сомневаемся, что использование таких приемов заметно облегчило бы решение этих (как и любых других) задач БП на практике. Ведь современную ТРИЗ (ТРС), БП, ТОС роднит подход к системам как совокупности потоков, использование инструментов потокового анализа и поиска не просто критического звена каждой цепи, а корневого недостатка всей системы, а также готовность к свертыванию отдельных звеньев (элементов системы), вместе с их недостатками. Разница лишь в том, что ТРИЗ опирается на теоретический фундамент, построенный на базе анализа десятков тысяч патентов и подтвержденный сотнями реально решенных с ее помощью задач. Но с нашей точки зрения широкое использование ТРС и ТОС в БП окончательно вывело бы Бережливое производство из метода проб и ошибок, из только называемого "научного" метода "5-ти почему" и различных контрольных вопросов на простор истинного творчества.
Но вернемся к мелочам. Вдумайтесь, оцените, как должно проявляться в одной только системе SMED это самое внимание к ним, проходящее красной нитью через все БП, чтобы получать такие результаты. Отметьте также, как используется интеллект операторов – ведь всю эту работу по сокращению времени переналадки рабочие делают сами. И как ощущается в этой системе уважение к работнику и стремление ценить самое главное, самое ценное на производстве – рабочее время того, кто своим трудом создает ценность. Понятно, что традиционный для нас стиль менеджмента с таким подходом не совместим совершенно. И в этом, кстати, основная трудность внедрения БП: надо, прежде всего, сменить систему взглядов на характер управления предприятием и сотрудниками. Надо перейти от так называемого "репрессивного менеджмента", насильственных методов управления (если ты не сделаешь того-то и того-то, то тебе будет плохо) к намного более эффективным ненасильственным (если ты сделаешь то-то и то-то, то тебе будет хорошо). Именно поэтому, как нам кажется (а вовсе не из-за заметно более высокой производительности системы) за БП будущее.
Нам изначально казалось, что задача данной статьи вовсе не в том, чтобы перечислять и описывать все инструменты (для этого достаточно раскрыть любую книгу по этой теме, слава богу их сейчас уже достаточно) и эффекты внедрения БП, а также его сложности. Мы хотели более полно показать то, что не всегда можно увидеть в книгах – суть этих подходов, исторические закономерности их возникновения и развития, возможные перспективы. Поэтому давайте рассмотрим один, хотя и выдуманный, но как нам кажется полезный и поучительный пример.
Некоторое предприятие – назовем его, скажем, "Победа" – разработало новое изделие "Ух ты –1". Маркетологи этого предприятия отлично поработали (3 месяца напряженных исследований и 300 тыс. рублей за проведение опросов сторонней фирме) и установили, что потенциальная емкость рынка этих изделий составляет 1000 штук в день. Решили запланировать выпуск пока только 960 штук (чтобы не рисковать). Продумали каналы сбыта, заключили необходимые договора и поручили 10 рабочим производить свое детище. Норма выработки довольно жесткая: 5 мин на одно изделие, т.е. по 12 изделий в час. Зато и зарплату им назначили хорошую – 1000 рублей в день. С учетом стоимости материалов (800 рублей на изделие) и накладных расходов (не слишком больших для современного предприятия) рассчитали продажную цену – 3000 рублей за одно изделие (маркетологи подтвердили – пойдет!).
Единственная неточность – продать удалось только 800 штук. И вот что получилось – см. таблицу 1, столбец В. В общем, вполне приличный результат, на котором можно бы и
успокоиться – работай себе, получай прибыль.
Таблица 1.
№ стр. | Параметр | Фор-мула | Модель затрат (традиционная) | |
| А | Б | В | Г |
1 | Количество изготовленной продукции (за день) 10 чел. по 12 шт. в час на 8 час. | | 960 | 800 |
2 | Заработная плана (в день) 10 раб. по 1000 руб. | | 10 000 | 10 000 |
3 | Стоимость материалов (800 руб. на 1 шт) | | 768 000 | 640 000 |
4 | Накладные расходы | | 1 500 000 | 1 500 000 |
5 | Издержки всего | 2+3+4 | 2 278 000 | 2 150 000 |
6 | Себестоимость 1 шт. | 5/1 | 2 373 | 2 688 |
7 | Продажная цена | | 3 000 | 3 000 |
8 | Объем продаж | | 800 | 800 |
9 | Денежные поступления | 7*8 | 2 400 000 | 2 400 000 |
10 | Прибыль | 9-5 | 122 000 | 250 000 |
11 | Остаток на складе | 1-8 | 160 | 0 |
12 | Стоимость незавершенки | 11*6 | 379 667 | 0 |
Однако, директор предприятия – мужик умный, начитанный, знающий, что есть такое БП и ТОС, которые рекомендует всячески бороться с запасами и перепроизводством, узнав детали, решил на следующий же день снизить объемы производства (недаром же предприятие звалось "Победа"). Рабочих было решено не обижать, и платить им столько же (несмотря на снижение выработки)19. А вечером все удивились – см. столбец Г той же таблицы 1. Несмотря на то, что себестоимость изделия немного выросла (те же деньги на меньшее количество продукции) прибыль (а разве не это главное?) увеличилась более чем в два раза (ведь 160 изделий не легло мертвым грузом на складе готовой продукции). И они поверили в силу методов БП.
Таблица 2
№ стр. | Параметр | Фор-мула | Доп. заказ по предельным затратам | Эффект сверхурочных |
| А | Б | Д | Е |
1 | Количество изготовленной продукции (за день) 10 чел. по 12 шт. в час на 8 час. | | +200 | +200 (10 чел +2 час по 10 шт) |
2 | Заработная плана (в день) | | 0 | 4 375 |
3 | Стоимость материалов (800 руб. на 1 шт) | | 160 000 | 160 000 |
4 | Накладные расходы | | 0 | 0 |
5 | Издержки всего | 2+3+4 | 160 000 | 164 375 |
6 | Себестоимость 1 шт. | 5/1 | 800 | 822 |
7 | Продажная цена | | 1 000 | 1 000 |
8 | Объем продаж | | 200 | 200 |
9 | Денежные поступления | 7*8 | 200 000 | 200 000 |
10 | Прибыль | 9-5 | 40 000 | 35 625 |
11 | Остаток на складе | 1-8 | 0 | 0 |
12 | Стоимость незавершенки | 11*6 | 0 | 0 |
Однако история завода "Победа" и их изделия "Ух ты –1" на этом не закончилась. Через неделю к ним приехали представители Северного Вьетнама, познакомились с их продукцией, и очень им захотелось заказать пробную партию этих замечательных изделий. Правда, они стали говорить, что Вьетнам – страна бедная, все цены там очень низкие и им никогда не продать там эти изделия по 3000 рублей за штуку. Они готовы покупать их (чтобы не оказаться в прогаре) только по 1000 рублей. "Как!" – возмущенно закричал главный экономист – "У нас только материалы стоят 800. Ни за что!". А все тот же директор подумал, и согласился. Поговорил с рабочими, убедил их немного поднять производительность (всего-то на 4 штуки в день), для родного-то предприятия. И вот что вышло (см. таблицу 2, столбец Д).
Лишние 40 тыс., без всяких затрат – как с неба свалились. Неплохо, правда? Ну раз пошла такая пьянка… Предложили вьетнамцам купить еще 200 штук. Те были согласные. Конечно, теперь уже рабочим пришлось заплатить за сверхурочные (все по закону: первые два часа с коэффициентом 1,5). Глядь – еще почти 40 тыс. как из воздуха (см. таблицу 2, столбец Е)20. Чудеса, а не БП. Недаром, видимо, в середине прошлого века японцы начали борьбу с потерями и перепроизводством. Умные. Или просто – не лишенные здравого смысла?
Теперь нам осталось лишь подтвердить возникшие у читателя сомнения: внедрение БП и ТОС невозможно не только без изменения стиля менеджмента, но и без изменения системы учета, характера работы бухгалтерии и экономического отдела. Оно затрагивает всю производственную систему, и отдельные инструменты БП – это лишь отдельные проявления системы, под названием "Производственная система конкретного предприятия, организованная по принципам Бережливого производства".
Конечно, процесс перехода к другим принципам учета, скорее всего, будет сопряжен с немалыми трудностями. Ведь БП – это довольно мощный инструмент и его невозможно просто скопировать, его надо каждый раз создавать заново. Хотя сам лин-учет можно считать более простым, чем традиционный. При этом предприятие переходит от стремления к оптимизации отдельных операций к стремлению оптимизировать процесс в целом, подчиняя работу операций целостным, системным требованиям (о необходимости учета которых все время говорит ТРИЗ). Больше того, возникает сильная потребность в стремительном расширении этой системы, включении в нее своих поставщиков и контрагентов, захвате, если можно так сказать принципами БП все большего окружающего пространства с оптимизацией отношений в нем. Но это уже тема совсем другой статьи, а пока сделаем заявление: