Справочныематериал ы технадзор а / систематизированные
Вид материала | Документы |
- Отчет о результатах эксперимента это документ, который содержит систематизированные, 38.43kb.
- Показал систематизированные, полные и глубокие знания по всем разделам учебной программы, 64.72kb.
- Учебно-методический комплекс по дисциплине дпп. В. 01. Термодинамика сред в электромагнитном, 163.24kb.
- Античное время, 82.58kb.
- Л. А. Крукиер " " 2010 г. Учебная программа курса, 172.29kb.
- Рабочая программа дисциплины «история» Среднее профессиональное образование, 358.76kb.
- Рабочая программа учебной дисциплины история Цикл, 273.37kb.
- Всего сорок три года, 252.63kb.
- Рабочая программа учебной дисциплины история России Цикл, 265.62kb.
- Пояснительная записка Гигиена питания учебная дисциплина, содержащая систематизированные, 1138.9kb.
Примечание:
- Номинальная толщина сформированного покрытия определяется как среднее арифметическое значение из десяти измерений толщины, выполненных равномерно по периметру трубы, из которых одно находится над усилением сварного шва.
- По требованию Заказчика толщина покрытия может быть увеличена.
- Допускается снижение толщины покрытия над зоной сварного шва до 30 % от номинальной толщины при условии, что диэлектрическая сплошность покрытия на этих участках будет не менее 5 кВ для трубопроводов диаметром до 530 мм включительно, 7,5 кВ – для трубопроводов диаметром до 820 мм включительн и 10 кВ – для трубопроводов диаметром свыше 820 мм.
2.3. Для нанесения покрытия на зону сварных стыков трубопроводов используются следующие комплектные изоляционные материалы:
- двухкомпонентный, не содержащий растворителей, жидкий эпоксидный праймер;
- двухслойная полимерная термоусаживающаяся лента;
- замковая пластина;
- термоплавкий или мастичный заполнитель околошовных зон сварного шва (при необходимости).
2.3.1. Эпоксидный праймер представляет собой двухкомпонентную систему на основе модифицированной эпоксидной смолы и отвердителя. Перед нанесением на изолируемую поверхность смола и отвердитель смешиваются в заданном объемном или весовом соотношении и наносятся равномерным слоем на подготовленную поверхность зоны сварного стыка труб и примыкаающий к ней участок заводского покрытия в соответствии с рекомендациями Поставщика материалов.
2.3.2. Термоусаживающаяся полимерная лента представляет собой двухслойный изоляционный материал, состоящий из термосветостабилизированной, сшитой, ориентированной в продольном направлении, полиэтиленовой пленки-основы и адгезионного подслоя на основе модифицированных термоплавких или мастичных полимерных композиций.
Соотношение между толщинами пленки-основы и адгезионного подслоя ленты должно составлять от 50:50 до 30:70 соответственно.
Для изоляции зоны сварных стыков трубопроводов, прокладываемых методами закрытой прокладки (проколы, «микротоннелирование», ННБ), используются специальные трехслойные термоусаживающиеся ленты с армирующим слоем из стеклоткани или стеклосетки.
Термоусаживающиеся ленты для изоляции зоны сварных стыков производятся и поставляются в виде рулонных материалов шириной 300, 450, 500 мм (до 600, 900 мм по требованию Заказчика), толщиной от 1,2 до 3,0 мм.
Нанесение покрытия из термоусаживающейся ленты должно производиться по согласованной нормативно-технической документации в соответствии с рекомендациями Поставщиков изоляционных материалов.
2.3.3. Замковая пластина предназначена для замыкания в кольцо (вокруг зоны сварного стыка трубопровода) отрезка термоусаживающейся ленты.
В процессе выполнения работ по нагреву и усадке кольцевой термоусаживающейся манжеты замковая пластина должна удерживать манжету от размыкания в зоне нахлеста ленты. Длина замковой пластины должна соответствовать ширине термоусаживающейся ленты (300, 450, 500 и 600 мм), ширина замковой пластины должна составлять от 100 мм до 150 мм, а толщина – не менее 1,0 мм.
2.3.4. Термоплавкий (мастичный) заполнитель представляет собой рулонный ленточный материал на основе мастичных или термоплавких полимерных композиций (аналогичных композициям, используемым для адгезионного подслоя термоусаживающейся ленты). Предназначен для заполнения зоны сварного шва трубопровода (при наличии острых кромок и высоте сварного шва более 3,0 мм) и зоны перехода заводского покрытия к поверхности трубы (при угле скоса кромок покрытия более 30о). Применяется при необходимости в соответствии с рекомендациями Поставщика материалов. Поставляется в виде рулонов или отрезков ленты с согласованной толщиной (от 1,4 мм до 3,0 мм) и шириной (от 50 мм до 450 мм).
- ТРЕБОВАНИЯ К ПОДГОТОВКЕ ПОВЕРХНОСТИ ЗОН СВАРНЫХ
СТЫКОВ ТРУБОПРОВОДА ПЕРЕД НАНЕСЕНИЕМ ПОКРЫТИЯ.
3.1. До нанесения покрытия поверхность зоны сварного стыка трубопровода и прилегающая к нему зона заводского покрытия должны быть очищены абразиво-струйным способом.
В качестве абразивных материалов могут применяться сухой, просеянный речной песок, корунд, купер-шлак, стальная или чугунная дробь.
3.2. Перед проведением абразивной очистки поверхность зоны сварного стыка трубопровода и прилегающая к нему зона заводского покрытия должны быть сухими, свободными от жировых, масляных загрязнений, консервантов и иметь температуру выше точки росы не менее, чем на 3оС.
3.3. После очистки степень очистки сварного стыка труб должна быть не ниже Sa 2
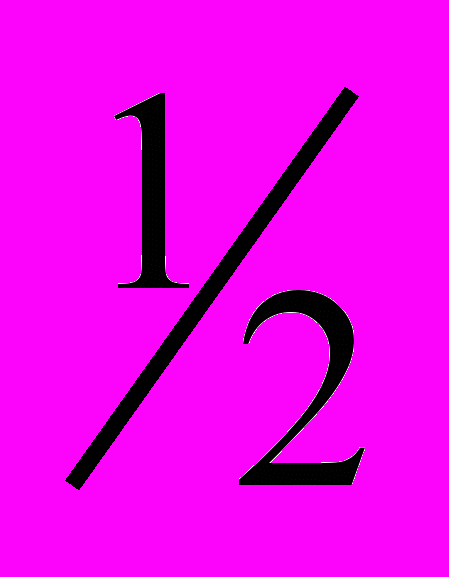
3.4. Заводское покрытие, прилегающее к зоне сварного стыка труб на расстоянии не менее 100 мм, должно быть также очищено абразивоструйным методом по всему периметру трубы, иметь шероховатую поверхность и не иметь острых кромок и мест отслоений от поверхности трубопровода. Угол скоса заводского покрытия к поверхности трубы должен быть не более 30о.
3.5. Перед нанесением покрытия на поверхности зоны сварного стыка и прилегающего заводского покрытия не должно быть пыли, продуктов очистки, жировых и масляных загрязнений.
3.6. Температура трубы в зоне сварного стыка и прилегающего к нему заводского покрытия должны отвечать требованиям, предъявляемым Поставщиками изоляционных материалов. В зависимости от используемых материалов, конструкций (типов) защитных покрытий (с праймером, без праймера) температура трубы в зоне сварного стыка может изменяться от 40–50оС до 140–150оС.
3.7. Нагрев зоны сварного стыка до заданной температуры осуществляется пропановыми, инфракрасными горелками или разъемными индукционными нагревателями.
На очищенной и нагретой до необходимой температуры изолируемой поверхности не должно быть следов копоти, пыли и других загрязнений.
- ТЕХНИЧЕСКИЕ ТРЕБОВАНИЯ К ПОКРЫТИЮ
ЗОНЫ СВАРНОГО СТЫКА.
4.1. Покрытие на основе термоусаживающихся полимерных лент должно наноситься на очищенную и нагретую до заданной температуры поверхность зоны сварных стыков трубопроводов по согласованной нормативно-технической документации (Инструкции, Технологические карты и др.), разработанной с учетом рекомендаций Поставщиков изоляционных материалов.
4.2. Покрытие зоны сварных стыков труб должно обеспечивать выполнение требований ГОСТ Р 51164 «Трубопроводы стальные магистральные. Общие требования к защите от коррозии» и настоящих технических требований.
4.3. Контролируемые показатели качества покрытия зоны сварного стыка:
- внешний вид и сплошность;
- величина нахлеста на заводское покрытие;
- толщина;
- диэлектрическая сплошность (испытание на электрический пробой);
- адгезия к стали;
- адгезия к заводскому покрытию;
- адгезия к стали и заводскому покрытию после испытаний в воде;
- стойкость к катодному отслаиванию;
- переходное сопротивление покрытия;
- прочность при ударе;
- сопротивление пенетрации (вдавливанию);
- степень усадки ленты (манжеты);
- стойкость к растрескиванию;
- стойкость к воздействию УФ радиации;
- грибостойкость;
- прочность при растяжении;
- относительное удлинение при разрыве;
- стойкость к термическому окислению.
4.4. Внешний вид и сплошность покрытия определяются визуально по всей длине и периметру изолированных участков.
Покрытие должно иметь однородную гладкую поверхность, не иметь пропусков, прожогов, пузырей, мест отслоений от трубопровода. Защитное покрытие зоны сварного стыка должно плотно прилегать к поверхности трубы с заводским покрытием.
4.5. Величина нахлеста термоусаживающейся ленты (манжеты, муфты) на заводское покрытие, прилегающее к зоне сварного стыка трубопровода, должна составлять не менее 50 мм для трубопроводов диаметром до 530 мм включительно и не менее 75 мм – для трубопроводов диаметром свыше 530 мм.
4.6. Толщина сформированного защитного покрытия зоны сварного стыка должна соответствовать требованиям таблицы 1 настоящих технических требований.
4.7. Диэлектрическая сплошность покрытия при проверке искровым дефектоскопом должна составлять не менее 5 кВ на 1 мм толщины покрытия.
4.8. По остальным показателям свойств покрытие на участках сварных стыков трубопроводов должно отвечать требованиям таблицы 2.
Таблица 2
ТЕХНИЧЕСКИЕ ТРЕБОВАНИЯ НА НАРУЖНЫЕ АНТИКОРРОЗИОННЫЕ ПОКРЫТИЯ
ДЛЯ ИЗОЛЯЦИИ СВАРНЫХ СТЫКОВ МАГИСТРАЛЬНЫХ НЕФТЕПРОВОДОВ
№ п.п. | Наименование показателей свойств покрытия | Норма для покрытий | Методы испытаний | |||
Нормальное исполнение | Нормальное исполнение | Нормальное тепло-стойкое | Специальное исполнение | |||
Тип 1 | Тип 2 | Тип 3 | Тип 4 | |||
1. | Адгезия покрытия к стали, Н/см ширины, не менее, при температурах испытаний2: (20±5)оС (40±3)оС (60±3)оС | 35 (50)1 20 9 | 35 (50)1 20 9 | 50 (70)1 30 15 | 70 (85)1 30 15 | ГОСТ 411, метод А |
2. | Адгезия покрытия к заводскому покрытию при (20±5)оС, Н/см ширины, не менее2 | 35 (50)1 | 35 (50)1 | 50 (70) 1 | 70 (85)1 | ГОСТ 411, метод А |
3. | Адгезия покрытия к стали, Н/см ширины, не менее, после 1000 ч выдержки в воде при температурах испытаний: (20±5)оС (40±3)оС (60±3)оС (80±3)оС | 30 (35)1 30 (35)1 30 (35)1 – | 30 (35)1 30 (35)1 30 (35)1 – | 40 (50)1 40 (50)1 40 (50)1 40 (50)1 | 50 (60)1 50 (60)1 50 (60)1 – | ГОСТ 411, метод А; Приложение А к техническим требованиям |
4. | Адгезия покрытия к заводскому покрытию, Н/см ширины, не менее, после 1000 ч выдержки в воде при температурах испытаний: (20±5)оС (40±3)оС (60±3)оС (80±3)оС | 30 (35)1 30 (35)1 30 (35)1 – | 30 (35)1 30 (35)1 30 (35)1 – | 40 (50)1 40 (50)1 40 (50)1 40 (50)1 | 50 (60)1 50 (60)1 50 (60)1 – | ГОСТ 411, метод А; Приложение А к техническим требованиям |
5. | Площадь катодного отслаивания покрытия, см², не более, после 30 суток испытаний в 3 % растворе NaCl при потенциале поляризации 1,5 В при температурах: (20±5)оС (40±3)оС (60±3)оС (80±3)оС | 5 (4) 1 10 (8) 1 15 (10) 1 – | 5 (4) 1 10 (8) 1 15 (10) 1 – | 5 (4) 1 10 (8) 1 15 (10)1 20 (15)1 | 4 (3) 1 8 (5) 1 10 (7)1 – | ГОСТ Р 51164, Приложение В |
6. | Переходное сопротивление покрытия в 3 % растворе NaCl при температуре (20±5)С, Ом×м², не менее:
| 1010 109 | 1010 109 | 1010 109 | 1010 109 | ГОСТ Р 51164, Приложение Г |
7. | Прочность покрытия при ударе, Дж, не менее, при температурах испытаний от минус (40±3)С до плюс (40±3)С для трубопроводов номинальным диаметром: до 273 мм вкл. св. 273 мм до 530 мм вкл. св. 530 мм до 820 мм вкл. свыше 820 мм | 4 6 8 10 | 4 6 8 10 | 4 6 8 10 | 8 10 12 15 | ГОСТ Р 51164, Приложение А |
8. | Сопротивление пенетрации (вдавливанию) при (20±5)С, мм, не более | 0,2 | 0,2 | 0,2 | 0,15 | ГОСТ Р 51164, Приложение Е |
9. | Степень усадки ленты (манжеты), %: не менее не более | 15 30 | 15 30 | 15 30 | 15 30 | Приложение Б к Техническим требованиям |
10. | Стойкость к растрескиванию при (60±3)С, ч, не менее | 1000 | 1000 | 1000 | 1000 | Приложение В к Техническим требованиям |
11. | Стойкость к воздействию УФ радиации в потоке 600 кВт·ч/м2 при (50±3)С, ч, не менее | 500 | 500 | 500 | 500 | ГОСТ 16337 |
12. | Грибостойкость, балл, не более | 2 | 2 | 2 | 2 | ГОСТ 9.048, ГОСТ 9.050 |
13. | Прочность при растяжении отслоенного покрытия (ленты) при (20±5)С, МПа, не менее | 12,0 | 12,0 | 12,0 | – | ГОСТ 11262 |
14. | Относительное удлинение при разрыве отслоенного покрытия (ленты), %, не менее, при температурах испытаний: минус (40±3)оС (20±5)оС | 100 200 | 100 200 | 100 200 | – – | ГОСТ 11262 |
15. | Изменение относительного удлинения при разрыве отслоенного покрытия (ленты) после 1000 ч выдержки на воздухе при (1103)оС, %, не более | 25 | 25 | 253 | – | ГОСТ 11262 |
16. | Сопротивление покрытия локальному срезу при (20±5)С, кг/режущий элемент, не менее | – | – | – | 70 (90)1 | Методика АО «ВНИИСТ» |
17. | Сопротивление покрытия кольцевому сдвигу при (20±5)С, кг/см, не менее | – | – | – | 30 (50)1 | Методика АО «ВНИИСТ» |
18. | Сдвиг покрытия по стали под воздействием статической нагрузки при (20±5)С, м/с, не более | – | – | – | 10-10 | Методика АО «ВНИИСТ» |