В.І. Склабінський (Вступ, розіл 4, висновки) доцент кафедри «Процеси та обладнання хімічних І нафтопереробних виробництв»
Вид материала | Документы |
- Проект з дисципліни «процеси й апарати харчових виробництв», 136.13kb.
- Програма фахового вступного випробування для навчання за освітньо-кваліфікаційним рівнем, 104.48kb.
- Методичні рекомендації до написання розділу дипломної роботи "Охорона праці" для студентів, 258.61kb.
- Робоча програма навчальної дисципліни для студентів (назва навчальної дисципліни), 233.48kb.
- Робоча навчальна програма дисциплiни " Перспективні технологiї харчових виробництв", 120.84kb.
- Завідувач кафедри М. П. Рагозін затверджено: на засіданні навчально-видавничої ради, 230.44kb.
- Кисельова Ольга Олексіївна, ст викладач кафедри хлібопекарського та кондитерського, 94.5kb.
- Типовий перелік навчального обладнання для кабінетів математики загальноосвітніх навчальних, 34.41kb.
- Зв'язок між поколіннями не втрачено, 31.16kb.
- Укладач: ст викл. В. О.Євстіфєєв, 388.32kb.
УДК 66.099.2:936.43.001
КП
№ держреєстрації 0106U013015
Інв. №
Міністерство освіти і науки України
Сумський державний університет
(СумДУ)
40007, м. Суми, вул. Римського-Корсакова, 2, тел. (0542) 33-41-08
info@nis.sumdu.edu.ua
ЗАТВЕРДЖУЮ
Проректор з наукової
роботи СумДУ, д.ф.-м.н., проф.
____________А.М. Чорноус
2009.10.05
ЗВІТ
ПРО НАУКОВО-ДОСЛІДНУ РОБОТУ
Оптимізація процесів гідродинаміки та тепломасообміну
в дисперсних системах при кристалізації та грануляції добрив
ОПТИМІЗАЦІЯ ТА АПАРАТУРНЕ ОФОРМЛЕННЯ ПРОЦЕССІВ ТЕПЛОМАСООБМІНУ ПРИ КРИСТАЛІЗАЦІЇ ТА ГРАНУЛЯЦІЇ ДОБРИВ
(заключний)
Начальник НДЧ,
к.т.н., доц. В.А. Осіпов
2009.12.05
Керівник НДР,
д.т.н., проф. В.І. Склабінський
2009.12.05
2009
Рукопис закінчено 5 грудня 2009 року
Результати даної роботи розглянуто на засіданні НТР,
протокол № 4 від 10.12.2009.
СПИСОК АВТОРІВ
Завідувач кафедри «Процеси та обладнання хімічних і нафтопереробних виробництв», д.т.н., професор (керівник) | 2009.12.05 | В.І. Склабінський (Вступ, розіл 4, висновки) |
доцент кафедри «Процеси та обладнання хімічних і нафтопереробних виробництв», к.т.н | 2009.12.05 | С.І. Якушко (розділи 1, 2, 4, 5) |
доцент кафедри «Процеси та обладнання хімічних і нафтопереробних виробництв», к.т.н | 2009.12.05 | Я.Е. Михайловський (розділи 1,2) |
доцент кафедри «Процеси та обладнання хімічних і нафтопереробних виробництв», к.т.н | 2009.12.05 | М.П. Юхименко (розділ 3) |
доцент кафедри «Процеси та обладнання хімічних і нафтопереробних виробництв» | 2009.12.05 | С.М. Яхненко (розділ 5) |
РЕФЕРАТ
Звіт про НДР: 95 с., табл. 3, 30 рис., 46 джерел.
Об’єкт дослідження: гранульовані органічні та органо-мінеральні добрива.
Мета роботи: створення науково обґрунтованої методики розрахунку грануляторів псевдозрідженого шару та полкових пневмокласифікаторів.
Методи дослідження: Експериментальне та математичне моделювання процесів псевдозрідження та пневмокласифікації проводилося за стандартними методиками.
Дослідження спрямовані на оптимізацію процесів гранулювання органічної сировини з домішками мінеральних компонентів та визначення методики розрахунку апаратів псевдозрідженого шару.
За результатами досліджень розроблені установки комплексної переробки органічних відходів сільськогосподарського виробництва з одержанням гранульованих органічних та органо-мінеральних добрив за енергозберігаючими технологіями, які захищені патентами.
ОРГАНО-МІНЕРАЛЬНІ ДОБРИВА, ГРАНУЛЮВАННЯ,
псевдозріджений шар, пневмокласифікатор,
МЕТОДИКА РОЗРАХУНКУ
ЗМІСТ
Вступ........................................................................................................................... | 6 |
1 Літературний огляд | 7 |
1.1 Аналіз добрив та способів їх виробництва......................................................... | 7 |
1.2 Гранулювання …………………………………………………………………. | 16 |
1.2.1 Гранулювання у псевдозрідженому шарі …………………………………... | 19 |
Висновки по главі ………………………………………………………………….. | 23 |
Постановка задачі дослідження …………………………………………………… | 23 |
2 Дослідження впливу різних факторів на процес гранулювання у псевдо зрідженому шарі ……………………………………………………………………. | 24 |
2.1 Дослідження апаратів різних конструкцій ……………………………………. | 24 |
2.2 Дослідження впливу місця розташування і конструкції розподільника рідини | 26 |
2.3 Дослідження впливу конструкції газорозподільної решітки ……………….. | 28 |
2.4 Дослідження впливу порозності шару ………………………………………... | 31 |
2.5 Дослідження різних методик розрахунку апаратів псевдозрідженого шару .. | 32 |
2.5.1 Виведення залежності для розрахунку критерія Архимеда і програми для його розрахунку ……………………………………………………………………. | 35 |
2.5.2 Вибір оптимального метода розрахунку швидкості теплоносія ………….. | 39 |
Висновки по главі ………………………………………………………………….. | 49 |
3 Класифікація гранул органо-мінеральних добрив ……………………………... | 52 |
3.1 Конструкція пневмокласифікаторів …………………………………………… | 52 |
3.1.1 Пневмокласифікатори гравітаційні і псевдозрідженого шару …………….. | 52 |
3.1.2 Поличкові апарати ……………………………………………………………. | 57 |
3.2 Оптимальні конструкції поличкових пневмокласифікаторів ……………….. | 59 |
3.3 Зіставлення розглянутих пристроїв. Особливості і переваги поличкових апаратів ……………………………………………………………………………… | 65 |
3.4 Дослідження пневмокласифікації гранульованих матеріалів в поличкових апаратах ……………………………………………………………………………... | 70 |
Висновки по главі | 76 |
4 Математичне моделювання процесу грануляції ……………………………… | 78 |
4.1 Програма розрахунку апарата ………………………………………………… | 78 |
Висновки по главі | 82 |
5 Установки для комплексної переробки органічних відходів …………………. | 83 |
Висновки та рекомендації………………………………………………………….. | 90 |
Перелік посилань | 91 |
ВСТУП
На сучасному етапі розвитку сільського господарства загострився ряд проблем. Насамперед, втрата родючості ґрунтів, забруднення ґрунтів залишками пестицидів, радіонуклідами, важкими металами тощо. Це змушує переглянути агротехнічні, агрохімічні та меліоративні заходи. Альтернативна система землеробства для даного господарства повинна бути спрямована на подолання цих негативних ефектів та отримання продукції, яка придатна для дієтичного харчування.
Добрива за агрономічним призначенням поділяють на прямі, які вносять в грунт для поліпшення живлення рослин (наприклад, аміачна селітра, суперфосфат та ін.), і непрямі, які вносять для поліпшення властивостей грунту і нагромадження в ньому елементів живлення рослин (наприклад, органічні добрива). За походженням, способом і місцем добування виділяють: місцеві добрива, які виробляються безпосередньо в господарстві (наприклад, гній) і промислові добрива [1].
Сільському господарству необхідна переорієнтація на використання місцевих ресурсів стабілізації та відтворення родючості ґрунтів, які здатні забезпечити рослини основними елементами живлення. У зв’язку з цим перспективним засобом є органо-мінеральні добрива. Використання органо-мінеральних добрив є дуже актуальним, оскільки традиційні мінеральні добрива вже не відповідають вимогам ринку. Тому основним завданням є розробка технологічного процесу одержання добрив нового покоління – органо-мінеральних добрив заданого складу.
Як і будь-який продукт, органо-мінеральні добрива повинні поставлятися споживачу у зручному для його використання вигляді. Оскільки вся існуюча сільгосптехніка повністю пристосована для масового внесення добрив у гранульованому вигляді, нашою задачею є створення високоефективних установок для виробництва гранульованих органо-мінеральних добрив заданого складу.
1 Літературний огляд
1.1 Аналіз добрив та способів їх виробництва
Сучасне сільськогосподарське виробництво неможливо уявити без використання мінеральних добрив. Застосування добрив дає можливість збільшити врожайність і поліпшити якість продукції рослинництва. В результаті застосування добрив підвищується стійкість рослин проти хвороб, рослини швидше дозрівають, краще використовують вологу, тощо [1].
Добрива за агрономічним призначенням поділяють на прямі, які вносять в грунт для поліпшення живлення рослин (наприклад, аміачна селітра, суперфосфат та ін.), і непрямі, які вносять для поліпшення властивостей грунту і нагромадження в ньому елементів живлення рослин (наприклад, органічні добрива). За походженням, способом і місцем добування виділяють: місцеві добрива, які виробляються безпосередньо в господарстві (наприклад, гній) і промислові добрива [1].
На практиці виділяють такі основні добрива: мінеральні (азотні, фосфорні, калійні) складні та змішані; органічні (гній, гноївка, пташиний послід, торф, зелене добриво, компости); бактеріальні. Польові культури по-різному реагують на органічні, мінеральні добрива та їх комбінації.
Азот, який міститься в азотних добривах, входить до складу найважливіших рослинних сполук. Він міститься в білках, нуклеїнових кислотах, фосфатидах, пептонах, поліпептидах, амінокислотах, хлорофілі, ферментах, вітамінах та ін. Тому нестача азоту призводить до зниження вмісту в рослині вказаних сполук, і в результаті – до порушення нормального перебігу життєвих процесів. Особливо сильно нестача азоту позначається на рості рослин. В результаті підсилення азотного живлення рослини розвивають міцну вегетативну масу: в них збільшується вміст білка, спостерігається загальне зростання врожайності. Регулюючи азотне живлення рослин, можна не тільки впливати на абсолютну величину врожаю, а й на його якість та структуру [1].
Азотне живлення рослин регулюють переважно застосуванням різних мінеральних азотних добрив: насамперед аміачної селітри, карбаміду та нітроамофосу. Ці добрива поряд з позитивними якостями (висока концентрація основних поживних елементів), мають також суттєвий недолік – їх значна розчинність у грунті, що може привести до створення умов пригнічення росту та розвитку рослин, а також сприяє вимиванню добрив з грунту [2]. При цьому значно зменшується коефіцієнт використання добрив.
Для запобігання цього негативного фактору азот у ряді азотних добрив переводять в компоненти з відносно низькою розчинністю, що забезпечує довготривалість їхньої дії на грунт та рослину. Для зниження розчинності використовують три технологічні прийоми: дражування гранул добрив інертними матеріалами (наприклад, сіркою, воском), капсулювання гранул добрив полімерним покриттям та залучення азоту до складу з'єднань з відносно низькою розчинністю.
Капсулювання азотних добрив, тобто покриття гранул добрив тонкою плівкою із незначною проникністю, дозволяє значно подовжити термін дії добрив у грунті, зменшити їх здатність до злежаності та гігроскопічності, а також вирішити питання транспортування добрив насипом. Для капсулювання можуть використовуватися різні речовини [3]. Наприклад, для капсулювання карбаміду на підприємстві ДВП "Об'єднання Азот", м. Северодонецьк зараз використовується карбамідоформальдегідна смола марки КФС-К. Основним її недоліком є високий вміст вільного формальдегіду – токсичної речовини, а також труднощі в одержанні на поверхні гранул суцільної полімерної плівки [4].
Перспективним є зниження розчинності азоту у грунті за рахунок залучення азоту до складу з'єднань з відносно низькою розчинністю. Це насамперед так звані органо-мінеральні добрива (ОМД), які виготовляються на органічній основі шляхом додавання до неї мінеральної речовини. Поєднання мінеральної і органічної частин в ОМД поліпшує баланс та умови живлення рослин при внесенні в грунт.
Встановлено [5], що мінеральні добрива хоча і стабілізують продуктивність сівообігу, але цей вплив нестійкий. На відміну органічна система з високою дозою гною (24 т/га) та органо-мінеральні добрива, які забезпечують бездефіцитній або позитивний баланс гумусу та біогенних елементів, навпаки щорічно підвищують продуктивність на 1—3 ц к.од./га. Таким чином, продуктивність ріллі поступово та закономірно підвищується при систематичному використанні збалансованих органо-мінеральних добрив.
Біоенергетичний аналіз, запропонований автором [5], показує, що органо-мінеральні системи добрив позитивно впливають на накопичення енергії в дерново-підзолистих грунтах щорічно в межах 2—6 ГДж/га. На чорноземі опідзоленому 12 т/га гною разом з мінеральними туками стабілізує енергетичний стан грунту, а на чорноземі типовому та звичайному дія органо-мінеральних систем добрив на грунтовий енергопотенціал така ж, як і органічних.
Застосовують ОМД під всі види сільськогосподарських (зернові, овочеві, плодово-ягідні) та декоративних культур, квітів, створювання газонів (в тому числі спортивних) для довготривалого підживлення грунту. У Лівобережному Лісостепу та Степу в результаті використання органо-мінеральних добрив вихід енергії врожаю збільшується відповідно до 122 та 144 ГДж/га, а при використанні тільки гною — 104 и 103 ГДж/га. У Чернігівському Поліссі органо-мінеральна система збільшує вихід енергії до 126 ГДж/га, що на 6—7 ГДж/га більше, ніж при окремому внесенні органічних та мінеральних добрив. У Київському Поліссі цей показник при поєднанні гною та мінеральних добрив складає 112 ГДж/га, а при окремому їх використанні — на 10—12 ГДж/га менше. Найбільше накопичення енергії (165,0 ГДж/га) органо-мінеральна система добрив забезпечує на черноземі опідзоленому з перевагою над окремим використанням гною та NPK на 14—19 ГДж/га, або на 9—11%. Тому, виходячи з продуктивності агроекосистем, одержані експериментальні данні вказують на доцільність та перспективність комбінованих органо-мінеральних систем добрив на різних типах грунтів [5].
До того ж, на відміну від органічних добрив, ОМД не містять життєдіяльного насіння бур'янів, повністю нешкідливі.
У технологічному процесі одержання ОМД мінеральні елементи живлення утворюють з гуміновими з'єднаннями органо-мінеральні комплекси, що дозволяє закріпити азот і калій в обмінній формі та зменшити їх рухливість, а фосфор перевести в форму, що легко засвоюється рослинами. За рахунок цього коефіцієнт використання поживних елементів з ОМД сягає вище 90%, що дозволяє знизити дози внесення цих добрив порівняно з мінеральними.
Оптимальне співвідношення елементів живлення в ОМД запобігає надлишковому накопиченню нітратів в продуктах, забезпечує не тільки приріст врожаю, але й поліпшує поживну цінність продукції. Вивчення впливу органо-мінеральних добрив на оточуюче середовище показує їх ефективність також і з екологічних позицій. Використання таких добрив знижує винесення особливо небезпечних у відношенні забруднення водних джерел нітратних іонів. Вважається, що це відбувається в основному за рахунок вмісту в органо-мінеральних добривах лігніну (30-50 %), який фіксує рухомий амоній [6].
Відомо, що грунт повинен мати високу ємність поглинання і буферність, щоб утримувати велику кількість мінеральних солей і поступово віддавати їх рослинам. Важливо, щоб ці якості зберігалися тривалий час. Органо-мінеральні добрива відповідають цим вимогам, оскільки при їх використанні покращуються фізико-хімічні властивості грунту, збільшується ємність вологи за рахунок властивості утримувати вологу в гранулах впродовж тривалого часу, грунт стає більш пухким, знижується його об'ємна маса. При використанні ОМД не відбувається засолення грунтів, що спостерігається при використанні високих доз мінеральних добрив. Головне, що з ОМД елементи живлення звільняються у відповідності з потребою рослини, а також внесення ОМД сприяє рівномірному розподіленню елементів живлення в грунті, що забезпечує його високу якість.
Таким чином, до переваг органо-мінеральних добрив можна віднести наступні позитивні моменти. По-перше, органо-мінеральне добриво містить велику кількість свіжого лігніну, який є повільно діючим джерелом елементів мінерального живлення, джерелом для утворення гумусу, середовищем для розвитку мікроорганізмів, а значить надійним джерелом поживних речовин для рослин. По-друге, кальцій, що міститься в органо-мінеральних добривах, з одного боку, сприяє закріпленню органічної речовини в грунті, а з іншого є джерелом поповнення грунту кальцієм, тобто забезпечує сприятливі умови для формування оптимальних водно-фізичних властивостей грунту. По-третє, в органо-мінеральних добривах міститься певна кількість рухливих поживних речовин, макро- та мікроелементів, необхідних для рослини. По-четверте, використання органо-мінеральних добрив, які містять до 6 % органічного вуглецю, дозволить вирішити одну з важливіших проблем сучасного сільськогосподарського виробництва - забезпечення бездефіцитного балансу гумусу в грунті. По-п'яте, одержана суміш може бути використана як універсальний меліорант, тому що в процесі нейтралізації можливо спланувати одержання добрива з різною реакцією середовища та з різним вмістом кальцію, який є основним меліоруючим компонентом серед меліорантів. Якщо органо-мінеральне добриво планується вносити на солонцюватих грунтах, то програмується одержання підкисленої суміші, яка містить СаSO4, а в разі кислих грунтів - то відповідно слабо лужною, насиченою СаСОз [6].
Технології виробництва ОМД відрізняються по органічній речовині, яка використовується як основа для виробництва добрив, по виду добрив (проста суміш або гранульовані добрива), та по домішкам, які поліпшують властивості добрив.
В якості органічної речовини використовують торф, сапропель, гідролізний лігнін, гній, послід, тверді побутові відходи, решки деревини та опалого листя, буре вугілля, інші.
Одним з перших органо-мінеральних добрив, який почала випускати промисловість, були торфо-мінерально-аміачні добрива (ТМАД). Готували їх торфопідприємства польовим способом, змішуючи торф з мінеральними добривами.
Зараз торфомінеральні аміачні добрива виготовляють шляхом обробки торф’яної кришки, яка має вологість не більше 63 %, аміачною водою, фосфоритною мукою, суперфосфатом, хлористим калієм та іншими калійними добривами. Для виробництва ТМАД беруть торф, який має ступінь розкладення не нижче 15 % та зольність не вище 25 %. ТМАД промислового виробництва повинні мати вологість не вище 63 %, зольність - не більше 30, містити розчинний азот, фосфор та калій - 0,5-0,6 % на абсолютно суху речовину. Випускають його з таким вмістом поживних речовин, г діючої речовини на 1 кг: азоту — 6—11; фосфору — 7,5—22; калію—11—20; рН суміші 6,4—8,1.
Встановлені такі типи торфо-мінеральних добрив для сільського господарства: гумофос, гумофоска, торфомінеральні (ТМД), торфоаміачні (ТАД), торфомінеральноаміачні (ТМАД), гумати натрію та амонію.
Зараз з'являються нові види добрив на основі торфу, наприклад, торфомінеральноцеолітові гранульовані добрива з пролонгованою дією [7]. Цього досягають за рахунок гранулювання торфо-мінеральної суміші і внесення до складу гранул додаткового сорбенту природного цеолітового туфу. Перевірка ефективності і пролонгованої дії показала, що внесення в грунт гранульованих торфомінеральних добрив в порівнянні з сумішшю мінеральних туків приводить до зниження невиробничих втрат елементів мінерального живлення (в 2,4 разу азоту, 3,3 фосфору, 2,6 разу калію); до більш різкого зниження втрат (2,5 разу азоту, 2,8 разу калію) приводить використання торфомінеральноцеолітових гранул. Це дозволяє розглядати гранульовані торфомінеральноцеолітові добрива як пролонговані та використовувати їх не тільки в рік внесення , але й в наступні.
Нові види органо-мінеральних добрив пропонують створювати шляхом утилізації твердих побутових відходів (ТПВ) [6], в яких міститься велика кількість речовини органічного походження: харчові відходи, залишки паперу, тканини, деревини, інші. В перерахунку на суху речовину вони містять 0,6-0,7 %N; 0,8 % К2О; 0,5-0,6 % Р2О5, до 7-9 % СаО, різні мікроелементи. До цього необхідно додати підвищене накопичення побутових відходів рослинного походження в літньо-осінній період - це опале листя та плодоовочеві відходи. Згідно запропонованого способу попередньо відсепаровані ТПВ накопичуються у спеціальній ємності, де змішуються з каталізатором. При проведенні "вологого" спалювання виділяється певна кількість тепла, частина якого використовується для подальшого підсушування добрив, що виробляються. При цьому гинуть збудники хвороб та яйця гельмінтів. Процес завершують нейтралізацією надлишків каталізатора шляхом вапнування (дефекатом, вапняком і т.і.) і додаванням лесу або лесового суглинку, що містить окрім карбонатів кальцію, вторинні колоїднодисперсні мінерали, які мають властивість фіксувати рухомі форми важких металів, переводячи їх у нерухомі форми. Одержана таким чином органо-мінеральна суміш містить (в перерахунку на суху речовину) 0,6-1,2 % N; 0,8-1,0 % K2O; 0,5-0,9 % P2O5; до 20 % СаО, лігнін та глинисті мінерали, мікроелементи тощо.
Спеціалістами Київського національного аграрного університету запропонований твердофазний процес переробки бурого вугілля на органо-мінеральне добриво [8]. Процес включає твердофазну взаємодію бурого вугілля з поташем (K2CO3) під час підігрівання з наступною нейтралізацією продуктів реакції моноамонійфосфатом, грануляцію і висушування. Запропоновано новий комплекс процесів отримання рідких та гранульованих мінеральних і органо-мінеральних добрив на основі гідрослюд з залученням промислових решток та решток тваринництва.
Розроблений спосіб одержання органо-мінерального добрива шляхом обробки лігніну слабкою азотною кислотою з подальшою нейтралізацією аміаком та компостуванням з торфом [9]. Проведені дослідження показали високу ефективність та перспективність такого добрива. Основою для виробництва запропонованих органо-мінеральних добрив є гідролізний лігнін як багатотоннажний відхід гідролізної промисловості. Оскільки в момент виходу лігніну він представляє собою стерильний продукт з високою кислотністю рН 2 - 2,5 та низькою хімічною активністю, його природне розкладання у грунті мікроорганізмами відбувається дуже повільно і в такому вигляді він малоефективний. Пошуки шляхів найбільш ефективного використання лігніну у сільському господарстві ведуться у декількох напрямах: один з них - приготування компостів із гноєм та послідом; другий - одержання на його основі органо-мінеральних добрив шляхом подальшої хімічної обробки лігніну.
Підстилковий гній, тверда фракція безпідстилкового рідкого гною та пташиний послід раніше використовували на добриво у чистому вигляді, або у складі простих компостів. Дози органічних добрив зазвичай становили 30 – 40 т/га, на які накладали оптимальне мінеральне удобрення. Нині така технологія є низькорентабельною у зв’язку з високими транспортними витратами. На зміну традиційним способам використання добрив сучасна аграрна наука потребує альтернативних технологій, що полягають у поєднанні в одній гранулі органічних і мінеральних компонентів. На Черкащині, у селі Червона Слобода Черкаського району ввійшов до складу діючих завод ЗАТ “Еко-Азот” із виробництва органо-мінеральних добрив “Гармонія” [10]. Добрива “Гармонія” майже на 90% складаються із органіки і застосовуються у садівництві і городництві для підживлення газонів, декоративних рослин. Добриво «Гармонія» виготовляється на основі знезараженого термічно висушеного курячого посліду з введенням необхідних мінеральних складових та мікроелементів. Воно містить азот (5%), фосфор (5%), калій (5%). У процесі виробництва послід змішується із соломою і фосфоро-калієво-азотними домішками. Таке добриво має тривалу дію, поступово підживлює рослини протягом 60 днів після внесення у грунт.
Запропоновано підвищення сорбіційних, іонообмінних і біогенних властивостей органо-мінеральних добрив. Новим аналогом таких добрив є торгова марка “Добрі Добрива”, що виробляються на промисловій лінії біля Полтавської птахофабрики в с. Стасі Диканського району Полтавської області [11]. Технологічний процес передбачає компостування нативного безпідстилкового пташиного посліду та виготовлення готової продукції – грануляту, що містить пташиний послід, мінеральні добрива (NРК), сорбенти і йонообміники. Перевагою “Добрі Добрива” над простими органо-мінеральними сумішами є включення до їх складу сорбентів та іонообміників, що забезпечують грунт мікроелементами, створюючи оптимальні умови для стартового росту рослин, та мають пролонговану дію. Вміст мікроелементів у “Добрі Добрива” становить (мг/кг): марганцю – до 400, міді 20 – 40, кобальту 10 – 12, цинку 20 – 40 мг/кг. Вміст важких металів, зокрема, кадмію у 100 разів і свинцю у 25 разів менше від граничнодопустимих концентрацій, прийнятних для органічних добрив.
“Добрі Добрива” мають гранули розміром 4-5 мм, вони міцні і придатні для будь-яких способів внесення в грунт – основного, локального, і рядкового, що забезпечується серійною технікою. Зважаючи на високий вміст основних елементів живлення для рослин оптимальні їх дози за розкидного внесення під просапні культури становить 1,0 – 1,5 т/га, зернових 0,8 – 1,0 т/га.
Польові досліди, проведені ННЦ «Інститут грунтознавства і агрохімії УААН» показали, що за використання органо-мінеральних «Добрих добрив» можна розраховувати на одержання приростів зерна ячменю, насіння соняшника, бульб картоплі, коренів цукрових буряків – в межах 30 - 40%.
Всі зазначені технології використовують в основному для виробництва ОМД тверду або висушену фракцію гною або посліду. Перспективним є використання в якості органічної основи рідких відходів тваринництва або птахівництва. Це дозволить одночасно вирішити питання захисту оточуючого середовища від його забруднення біогенними речовинами, які містяться у гної та посліді.
Органічні та органо-мінеральні добрива „Оптима” почало виробляти ТОВ „УкрТехноФос” [12]. В залежності від складу виготовляють ОМД „Оптима” чотирьох марок: марка „Стандарт” – органо-мінеральне добриво із вмістом макроелементів (NPK) – 2.0-2.4-2.0 %; марка „3-3-3” – вміст макроелементів (NPK) – 3.0-3.0-3.0 %; марка „5-5-5” – вміст макроелементів (NPK) – 5.0-5.0-5.0 %; марка „10-6-8” – вміст макроелементів (NPK) – 10.0-6.0-8.0. Для виготовлення ОМД використовуються наступні компоненти: свіжий осад очисних споруд, сухий осад очисних споруд, органічний наповнювач – низинний торф, мінеральний компонент (фосфогіпс або лісоподібний суглинок, мергель, розмелені туфи), калій хлористий із вмістом К2О– 55%, амофос із вмістом Р2О5 – 52%, азот – 12%, аміачна селітра із вмістом азоту – 34,4%.
Аналіз наведених прикладів показує, що на ринку вже з'явилися та продовжують з'являтися ниві види добрив, які характеризуються значно вищою ефективністю в порівнянні з традиційними добривами. При цьому особливого значення набувають добрива пролонгованої дії із заданими властивостями і структурою. Для забезпечення рослин біогенними елементами протягом всього вегетаційного періоду розроблені основні принципи формування складу універсальних органо-мінеральних добрив пролонгованої дії, що містять у збалансованому співвідношенні поживні речовини органічного матеріалу, природні мінерали та біологічно активні сполуки [13].
Як будь-який продукт, органо-мінеральні добрива повинні поставлятися споживачу у зручному для його використання вигляді. Найбільш зручний і розповсюджений вигляд, в якому добрива поставляються споживачу – гранули.
- Гранулювання
Гранулювання - це сукупність фізико-хімічних і фізико-механічних процесів, що забезпечують формування часток певних розмірів, форми, структури і фізичних властивостей. Водорозчинні мінеральні добрива у гранульованому вигляді мають гарні фізичні властивості – вони краще зберігають сипкість, не порошать, легко вносяться у грунт, з великою ефективністю використовуються рослинами, оскільки повільно вимиваються грунтовими водами і в меншому ступені деградують внаслідок меньшої поверхні контакту з компонентами грунту [4].
Гранулі можуть маті форму грудочок або сферичну. Останні мають певні переваги – сферичні зерна міцніше і менше стираються при пересипанні.
Взагалі гранулювання включає наступні стадії: підготовку початкової сировини (дозування і розподіл компонентів); власне гранулювання (агрегатування, напластовування, кристалізація, ущільнення та ін.); стабілізацію структури (сушка, термостатуювання, полімеризація та ін.); видалення товарного продукту (класифікація за розмірами, подрібнення крупних фракцій).
Гранулювання здійснюють з рідкої, твурдої, газоподібної фаз, а також з будь-якої їх комбінації. Утворення твердих часток необхідного розміру при гранулюванні відбувається або миттєво, або поступово. Тому розрізняють процеси гранулювання, що протікають без зміни розмірів часток в часі, із зміною розмірів часток в часі і змішаного типа. Залежно від вимог, що пред'являються до гранулометричного складу продукту, отримувані при гранулюванні дрібні частки або повертають на переробку (ретурний процес), або не повертають (безретурний процес).
Для гранулювання матеріалів застосовують різні методи, які можна класифікувати таким чином:
- обкочування (формування гранул, що досягається агрегатуванням і нашаровуванням часток з ущільненням структури);
- диспергування рідини у вільний об’єм або нейтральне середовище (утворення і твердіння крапель рідини при охолодженні у газі або рідині);
- диспергування рідини на поверхню гранул у завислому стані (кристалізація тонких плівок в результаті їх зневоднення або охолодження на поверхні гранул);
- диспергування рідини в активне середовище (формування і твердіння часток в результаті утворення нової речовини у вільному об’ємі або на поверхні гранул);
- лускоутворення (охолодження рідини на чужорідній поверхні з наступним подрібненням одержаної плівки);
- прессування (одержання плиток, брикетів, таблеток з сухих порошків з наступним подрібненням та розсіюванням пресату);
- формування, або екструзія (продавлювання пастоподібної маси через отвори, подрібнення та зміцнення джгута);
- спікання (нагрівання з утворенням агломератів, їх охолодження, подрібнення і розсів);
- конденсація, або сублімація (утворення твердих часток з газу, їх нашаровування та агрегатування).
1.2.1 Гранулювання у псевдозрідженому шарі
У промисловій практиці широко розповсюджені процеси гранулювання, в яких технологічний процес одержання гранул здійснюється у завислому стані. Псевдозрідження є одним з найбільш прогресивних методів здійснення гетерогенних технологічних процесів з твердою фазою. В останні роки цей метод одержав широке впровадження у хімічну, нафтопереробну, гірнорудничу, металургійну, харчову тв. інші галузі промисловості. Використання цього метода взаємодії між твердою і газоподібною фазами дозволяє інтенсифікувати процес гранулювання, автоматизувати його, підвищити не тільки ефективність роботи апаратів і створити установки великої потужності, але й підвищити продуктивність праці.
Широке впровадження метода псевдозрідження у промислову практику обумовлено наступними його основними перевагами:
- Інтенсивне перемішування твердої фази, що призводить до практичного вирівнювання температур і концентрацій в об’ємі псевдозрідженого шару. Завдяки цьому усувається небезпека локального перегріву (або переохолодження) твердих часток, що протидіє оптимальному протіканню ряду теплових, каталітичних та інших процесів.
- Високі значення коефіцієнтів ефективної теплопроводності і тепловіддачі від псевдозрідженого шару до поверхні теплообміну (або навпаки), сумірні з відповідними значеннями коефіцієнтів для крапельних рідин. Ця важлива особливість псевдозрідженого шару дозволяє не тільки економити поверхню теплообміну і робочі об’єми апаратів, але також здійснювати хімічні та інші процеси з великим тепловим навантаженням при тонкому температурному регулюванні.
- Можливість використання твердих часток малих розмірів, тобто твердої фази з розвинутою питомою поверхнею, для зниження дифузійних гальмувань і підвищення продуктивності апаратів.
- Рухомість (текучість) псевдозрідженого шару дозволяє створювати апарати з безперервним введенням свіжої і відведенням відпрацьованої твердої фази, використовуючи при цьому виносні пристрої для теплообміну і керування температури.
- Невеликий гідравлічний опір і незалежність його значення від швидкості зріджуючого агенту у межах здійснення псевдозрідженого шару.
- Широкий діапазон властивостей твердых часток, що використовуються, та зріджуючих агентів, включаючи можливість живлення апаратів з псевдозрідженим шаром пастоподібними матеріалами і суспензіями.
- Порівняно простий устрій апаратів з псевдозрідженим шаром, легкість їх механізації і автоматизації.
Окрім переваг, метод псевдозрідження має деякі недоліки, найбільш суттєві з яких зводяться до наступного:
- Неможливість противотоку фаз в межах окремого псевдозрідженого шару внаслідок інтенсивного перемішування і, відповідно, неможливість здійснення процесів хімічного перетворення, тепло- і масообміну при максимальній рушійній силі.
- Нерівномірність часу перебування у псевдозрідженому шарі часток твердої фази і зріджуючого агенту.
- Можливість в ряді випадків небажаного змінення властивостей твердих часток (стирання, розтріскування, злипання, спікання і т.і.).
- Необхідність установки потужних пиловловлюючих апаратів на виході газів з псевдозрідженого шару, особливо при широкому гранулометричному складі твердої фази.
- Ерозія апаратури в зоні псевдозрідженого шару, особливно значна у випадку використання часток з високими абразивними властивостями.
- Обмеженість робочих швидкостей зріджуючого агента межами, які відповідають початку псевдозрідження твердої фази і її виносу з шару.
- Утворення значних зарядів статичної електрики при псевдозрідженні часток діелектричних матеріалів – вибухонебезпечність системи.
Перелічені недоліки метода псевдозрідження не є, як правило, визначающими, а деякі з них можуть бути частково або повністю усунені. Переваги метода псевдозрідження, безумовно, превалюють над його недоліками. Цим пояснюється широке застосування метода псевдозрідження у різноманітних хімічних, теплових, масообмінних, механічних та інших важливих процесах багатьох галузей промисловості.
Псевдозрідження є складним зв’язаним рухом рідини і твердих часток з утворенням зрідженого (псевдозрідженого, киплячого) шару, за своїми властивостями аналогічного рідині. Тверда речовина, яка вводиться до зрідженого шару з рідкою фазою, частково відкладається на поверхні часток в шарі. Друга її частина утворює самостійні частки, тобто нові центри гранулоутворення. Зростання гранул по поверхні тим вірогідніше, чим більше сили зцеплення краплі рідини з твердими частками.
Адгезійна спроможність краплі залежить від шорсткості поверхні гранул, а також від властивостей рідини, найбільш важливим з яких є співвідношення в краплі радкої і твердої фаз Р. Значення Р для краплі залежить від температури, вологості, хімічного складу пульпи. При попаданні гарячої рідини у зріджений шар з більш низькою температурою відбувається швидке охолодження насиченого розчину з видаленням порції кристалів, що знижує спроможність пульпи до адгезії. З зменшенням вологості пульпи адгезія також зменшується і збільшується кількість часток, які утворюються з пульпи.
Існують і інші можливості утворення нових гранул, наприклад, при подрібненні як механічним, так і тепловим. В останньому випадку частки розміром більше певного, циркулюючи між зоною активного теплообміну і основним об’ємом шару, що має значно більш низьку температуру, не встигають прогріваться на всю товщину. В результаті виникає термічна напруга, спроможна розколоти гранулу.
Інший механізм розтріскування поверхні часток полягає в тому, що при температурі шару, яка набагато перевищує температуру кипіння рідини, остання при контакті з гранулою інтенсивно кипить з видаленням великої кількості розчинника в парову фазу. Тиск, який при цьому створюється, розриває плівку твердої речовини.
Окрім утворення нових гранул у зрідженому шарі відбувається зростання існуючих гранул. Як вказано вище, це можливо при відкладення на поверхні часток речовини, яка видаляється з рідини. Другий шлях зростання гранул – їх зрощування між собою. Агрегатування можливо при достатньо великих силах зцеплення між частками в момент їх стикання. Джерелом таких сил є рідка фаза. При надлишку рідини на поверхні часток (причиною може бути велика локальна вологість або температура матеріалу) сили поверхневого натягнення становляться більше сил, які забезпечують взаємний рух часток, і відбувається злипання. При наступному зникненні рідкої фази (сушіння, охолодження і т.і.) утворюються кристалічні містки, які міцно зв’язують частки між собою. Якщо кристалізація не відбувається, тобто пульпа містить нерозчинну речовину, то при достатньо інтенсивному русі часток агрегати руйнуються з утворенням вихідних часток. Аналогічний процес відбувається, якщо утворюється недостня кількість кристалів і зв’язки в агрегаті часток непрочні.
Із сказаного виходить, що гранулювання у зрідженому шарі представляє собою складний комплексний процес збільшення розміру існуючих гранул і утворення нових. Тому, поряд з впровадженням у промислову практику проводяться широкі дослідження по вивченню загальних закономірностей псевдозрідженого стану і окремих особливостей конкретних процесів, зокрема, процеса гранулювання; одночасно розробляються принципи апаратурного оформлення технологічних процесів у псевдозрідженому шарі. Результати багатьох робіт в цієй галузі опубліковані у періодичних виданнях і тематичних збірниках, а також у вигляді авторськіх свідоцтв і патентів.
ВИСНОВКИ ПО ГЛАВІ:
Гранулятори з псевдозрідженим шаром мають ряд переваг: развинута поверхня фазового контакту; висока інтенсивність процесів тепло- і масообміну; висока питома продуктивність; невеликі капітальні витрати на виготовлення і монтаж апарату; висока якість гранульованого продукту; можливість безперервного ведення процесу при його повній автоматизації і механізації; поєднання процесів зневоднення (охолодження) і гранулювання, що спрощує схему виробництва [9].
До недоліків цих апаратів слід віднести: підвищені енерговитрати, пов’язані з нагнітанням сушильного агенту; необхідність точного дозування рідкої фази, що значно ускладнює керування високопродуктивним виробництвом і повною зупинкою апарату при порушенні технологічного режиму.
ПОСТАНОВКА ЗАДАЧІ ДОСЛІДЖЕННЯ
1. Дослідити вплив різних факторів на процес гранулювання органічної речовини у псевдо зрідженому шарі.
1.1. Дослідити різні конструкції апаратів псевдозрідженого шару, вибрати оптимальну конструкцію гранулятора.
1.2. Дослідити вплив місця розташування і конструкції розподільника рідини, вибрати оптимальну конструкцію.
1.3. Дослідити вплив конструкції газорозподільної решітки, вибрати оптимальну конструкцію.
1.4. Дослідження впливу порозності шару.
1.5. Дослідження різних методик розрахунку апаратів псевдозрідженого шару.
1.6. Вибір оптимального метода розрахунку швидкості теплоносія.
2 Дослідження впливу різних факторів на процес гранулювання у псевдо зрідженому шарі
2.1 Дослідження апаратів різних конструкцій
Для гранулювання у псевдозрідженому шарі використовують апарати різних конструкцій [14]. На рис. 1 наведені різні конструкції апаратів з псевдозрідженим шаром.
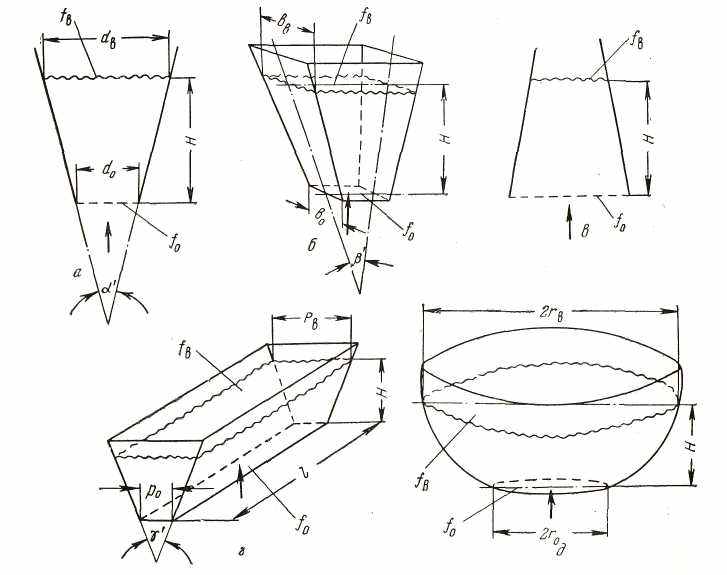
Рисунок1 – Конструкції апаратів з використанням псевдозрідженого шару:
а – конічний, вершиною донизу; б – пірамідальний, вершиною донизу;
в – конічний (пірамідальний), вершиною догори; г – призматичний;
д – сферичний.
У конічних апаратах з вершиною донизу (рис.1, а) у зв’язку із збільшенням площі поперечного перетину апарату у спрямуванні руху зріджуючого агенту відбувається пневмокласифікація часток по розмірам і сепарація найбільш дрібної фракції. Це суттєва перевага при проведенні процесу грануляції, оскільки дрібні частки повертаються на дорощування для одержання товарної фракції.
Цього не відбувається у конічних апаратах з вершиною доверху (рис.1, в), оскільки зменшення площі попереднього перетину апарату у напрямку руху зріджуючого агенту призводить до збільшення швидкості руху теплоносія і винесення часток з апарату.
Застосування пірамідальних апаратів з вершиною донизу (рис.1, б) має недоліки перед конічними апаратами, у зв’язку з труднощами розпилювання рідини по всьому перетину апарату. Факел розпилювання рідини має конічну форму, тому біля ребер апарату не буде відбуватися зрошенняе часток та їх зростання.
Застосування призматичних (рис.1, г) апаратів з направленим рухом часток має ряд переваг і недоліків. До переваг відносяться можливість більш плотного зрошення часток (порівняно з конічними апаратами), мінімальний гідравлічний опір шару, максимальні значення коефіцієнтів тепло- і масообміну. До недоліків відносяться важкість підтримання стабільного завислого шару, складність конструкції газорозподільної решітки, її забивання, утворення застійних зон, або повна зупинка апарату. До того ж в апаратах призматичної форми з спрямованим рухом часток дуже тяжко контролювати час перебування гранул в апараті, можливість утворення агломератів і ''проскок'' дрібних часток.
Застосування апаратів сферичної форми не рекомендується у зв’язку з їх дорожнечою.
Порівнюючи різні конструкції апаратів з псевдозрідженим шаром можна зробити висновок, що використання конічного апарату з вершиною внизу найбільш доцільно для проведення процесу гранулювання. Ці апарати мають оптимальні значення гідравлічного опору, коефіцієнтів тепло- і масообміну, можливість регулювання часу перебування часток в апараті, рівномірне зрошення рідини по всьому перетину апарата, стабільний псевдозріджений шар, простоту конструкції газорозподільної решітки.
Форма апарату визначає його гідродинамічні особливості. У конічних апаратах з кутом розкриття до 20° відбувається рівномірне псевдо зрідження по всьому перетину, тоді як при більшому куті розкриття виникає розріджене центральне ядро і утворюється більш щільний шар біля стінок, тобто відбувається фонтанування. Відомі апарати з декільками зонами локального фонтанування.
2.2 Дослідження впливу місця розташування і конструкції розподільника рідини
Гранулятори з псевдозрідженим шаром відрізняються також місцем розташування і конструкцією розподільника рідини, живильника твердої фази, пристроєм для вивантаження продукту, а також способом підведення тепла. Рідину подають зверху на дзеркало псевдозрідженого шару, у шар спрямуванням до газорозподільної решітки або горизонтально, а також знизу. При роботі в режимі фонтанування рідину подають в разбавлену фазу, яка утворюється в центральній частині апарата.
Пневматичне розпилювання рідини над шаром завдяки взаємодії двох протилежно спрямованих потоків приводить або до подавлення псевдозрідження, або до значного винесення дрібної фракції з апарату. Однак при правильно вибраному конструктивному оформленні такий спосіб подачі рідини стає вельми ефективним, оскільки відбувається хвилеподібне викривлення поверхні шару, при якому різко збільшується площа контакту двох зустрічних потоків і тим самим інтенсифікуються процеси тепло- і масообміну.
До недоліків пневматичних форсунок слід віднести: значне винесення дрібної фракції шару, підвищені витарти енергії на розпилювання, необхідність у розпилюючому агенті і обладнанні для його подачі, розпилювання тільки чистих рідин, вірогідність забивання сопла при використанні рідин з механічними домішками.
Найбільш поширений спосіб розпилювання рідини – гідравлічне розпилювання. Цей спосіб найбільш простий в конструктивному відношенні і економічний по витратам енергії.
Якщо вміст вологи у відпрацьованому сушильному агенті дозволяє одержати продукт потрібної якості, то найбільш раціональна подача рідини у псевдозріджений шар. При такій подачі знижується винесення бризк і ствоорюються сприятливі умови для розвитку факелу і збільшення поверхні зрошення. При подачі рідини у шар гарне її диспергування можливо тільки при наявності вільного простору, що дозволяє розвиватися струму рідини. Цей простір утворюється при витоку распилюючого агента, який створює у псевдозрідженному шарі газовий факел. Чим більше витрати рідини, тим більше повинен бути об'єм факелу, отже, і його довжина.
При подаванні рідини у шар знизу довжина факелу, а отже і продуктивність форсунки обмежені висотою шару. Тому при переході на великі апарати і зберіганні тієї ж висоти шару, необхідно встанавлювати багато форсунок обмеженої продуктивності, що ускладнює конструкцію і експлуатацію гранулятора. Для подачі рідини у шар найбільш доцільно встановлювати форсунки на боковій стінці гранулятора, щоб розташування факелу рідини було горизонтальним.
В залежності від місця подачі рідини у шар пред'являють різні вимоги до щільності зрошення. Так, при подачі рідини на шар зрошення його поверхні повинно бути рівномірним по всій площі, тоді як при подачі рідини всередину шару повинно забезпечуватися рівномірність зрошення поверхні факелу, а зрошення ядра факела повинно бути мінімальним. Питоме зрошення при розпилюванні рідини всередину шару вище, ніж на поверхню, оскільки перемішування, що забезпечує турбулізація факелом, в цьому випадку краще. Питомк зрошення при інших рівних умовах запропоновано використовувати в якості масштабного фактора, тобто прийняти, що зростання продуктивності форсунки пропорційно збільшенню поверхні зрошення рідини, що розпилюється.
Процес гранулювання у псевдозрідженому шарі ведуть як з подачею тільки рідкої фази, так і з подачею рідкої і твердої фаз. Остання може бути одним з компонентів продукту (наприклад, карбамід у складно-змішаних добривах); речовиною, яка плавиться у шарі (наприклад, міраболіт); рециклом, тобто тим самим продуктом у вигляді дрібних гранул і пилу. Тверду фазу подають у шар механічним або пневматичним способом, використовуючи для цього окремий пристрій або спеціальний вузол для одночасного подавання рідини і твердого компонента. Останній більш компактний і дозволяє значно ефективніше використовувати тверду фазу, яка вводиться у шар, оскільки вона зразу ж змішується з рідиною і бере участь в процесі гранулоутворення до отдуву з шару.
В якості розпилюючого пристрою вибираємо відцентрово-струменеву форсунку с ціліндричним вкладишем [15]. Ця форсунка розподіляє рідину на два потоки: один проходить через гвинтові канали вкладиша, а другий формується в результаті проходження частини рідини через вісевий отвір. Закручений і вісевий потоки взаємодіють в камері змішування і у сопловому каналі. Ця взаємодія є визначальною при формуванні факела рідини, яка розпилюється.
Продукт вивантажується з гранулятора з поверхні шару збоку або по центру апарату, а також на рівні газорозподільної решітки збоку або по центру. Бокове вивантаження переважне, оскільки дозволяє зменшити контакт гарячого теплоносія з матеріалом, що вивантажується. Через нижнє вивантаження виходять гранули всіх розмірів, а також комки, що незріджуються. Це запобігає їх оплавленню і заростанню газорозподільної решітки. При безперервному процесі і вивантеженні з нижньої частини шару необхідна синхронна робота дозаторів рідини і пристроя для вивантаження для запобігання змінення висоти шару.