В.І. Склабінський (Вступ, розіл 4, висновки) доцент кафедри «Процеси та обладнання хімічних І нафтопереробних виробництв»
Вид материала | Документы |
- Проект з дисципліни «процеси й апарати харчових виробництв», 136.13kb.
- Програма фахового вступного випробування для навчання за освітньо-кваліфікаційним рівнем, 104.48kb.
- Методичні рекомендації до написання розділу дипломної роботи "Охорона праці" для студентів, 258.61kb.
- Робоча програма навчальної дисципліни для студентів (назва навчальної дисципліни), 233.48kb.
- Робоча навчальна програма дисциплiни " Перспективні технологiї харчових виробництв", 120.84kb.
- Завідувач кафедри М. П. Рагозін затверджено: на засіданні навчально-видавничої ради, 230.44kb.
- Кисельова Ольга Олексіївна, ст викладач кафедри хлібопекарського та кондитерського, 94.5kb.
- Типовий перелік навчального обладнання для кабінетів математики загальноосвітніх навчальних, 34.41kb.
- Зв'язок між поколіннями не втрачено, 31.16kb.
- Укладач: ст викл. В. О.Євстіфєєв, 388.32kb.
3.3 Зіставлення розглянутих пристроїв. Особливості і переваги поличкових апаратів.
Як випливає з викладеного, для проведення розглянутих процесів найчастіше застосовуються три типи апаратів, між якими є велика схожість.
У найбільш простому з цих пристроїв, що є каналом з вільним перетином, особливості гідромеханічних процесів визначаються закономірностями висхідного рухомого прямолінійного двофазного потоку. При цьому висхідний потік турбулізований місцевим опором, який є вузлом введення початкового продукту (патрубок) і струменем матеріалу, що вводиться в канал.
Далі відбувається гідродинамічна стабілізація потоку по висоті каналу, в ході якої зменшується його турбулізація, а також швидкість руху часток. Епюри швидкостей потоку і концентрацій часток стають більш симетричними. Зменшується градієнт концентрації часток по висоті. Стабілізація потоку закінчується за, так званою, розгінною ділянкою, де всі перераховані параметри набувають практично постійних значень.
Залежно від витрат матеріалу, що вводиться в цей апарат, а також співвідношення між швидкостями потоку і швидкістю витання часток, можливе або повне винесення матеріалу через верх апарату, або повний його провал донизу, або розділення на винесення (більш дисперсна частина матеріалу) і провал (крупніша його частина).
При обробці полідисперсних матеріалів механізм розглянутих вище процесів ускладнюється, оскільки в кожному перетині каналу частки різних розмірів рухаються з різними швидкостями.
Короткочасність взаємодії фаз, що не перевищує декілька секунд, обмежує сферу застосування таких апаратів. Так, з їх допомогою вдається знепилити лише матеріал з невеликим вмістом дрібних часток, які може зважити і винести потік через верх апарату при даній швидкості його руху.
В цьому відношенні зручніші апарати з псевдозрідженим шаром, де завдяки більшому часу перебування матеріалу, вдається видалити з нього значні кількості дрібних часток. Повноту протікання цих процесів лімітує порівняно невелика швидкість потоку газу на виході апарату. Її збільшення призводить до зростання пиловинесення, що погіршує якість продукції, яка виробляється в апараті. При цьому у винесеному потоці з'являються крупніші частки.
При експлуатації таких апаратів виникають труднощі із-за забивання отворів решіток, їх деформації, а також при розвантаженні або перевантаженні матеріалу в багатосекційних апаратах. Обмежує поширення таких апаратів і значне пиловинесення, коли воно стає небажаним явищем. Більшість з цих недоліків відсутні у апаратах з суцільними і перфорованими полицями, які займають проміжне положення між ними. Так, переміщаючи перфоровану полицю до стінки апарату, ми наближаємося до апарату з псевдозрідженим шаром, а висуваючи її з апарату і звільняючи його перетин - до апарату з вільним перетином, типу труб-сушарок. Апарати з полицями зберігають і навіть підсилюють деякі переваги апаратів, що розглядалися раніше. Полиці подовжують час перебування матеріалу в апараті. Підвищуючи швидкість і турбулентність потоку газу і створюючи вихровий рух в місці їх встановлення, вони збільшують інтенсивність контакту фаз. Наявність вільного простору між кінцями полиць і стінками апарату усуває потребу в схильних до забивання перетіканнях. Змінюючи живий перетин полиць, кути їх нахилу, відстань від кінця полиць до стінки апарату, а також число полиць і відстань між ними по вертикалі, вдається впливати на інтенсивність контакту фаз і створювати самі різні режими як на окремих полицях, так і по висоті апарату.
Завдяки перерахованим вище особливостям, апарати з полицями дозволяють досягати при здійсненні гідромеханічних процесів розділення значно вищий технологічний ефект, ніж апарати з вільним перетином і з псевдозрідженним шаром.
Як випливає з вищевикладеного, при взаємодії висхідного турбулентного потоку із струменем матеріалу, або при русі потоку через псевдозріджений на газорозподільних решітках шар, окремі частки або їх агрегати викидаються у простір над шаром. Цей простір часто називають фонтануючим, оскільки в ньому інтенсивно переміщаються вгору за інерцією пакети часток і окремі частки, швидкість яких може навіть перевищувати швидкість висхідного потоку. Досягнувши певної висоти, пакети і найбільш крупні частки починають опускатися вниз. Частина пакетів при цьому руйнується. Потік сильно турбулізований як зміною швидкості потоку газу при виході з шару, так і рухомими пакетами і частками. Найбільш дрібні частки потрапляють в наступну зону, зону сепарації, де швидкість їх поступово зменшується до сталої величини.
Турбулентність потоку також поступово знижується до величини, яка відповідає усередненій швидкості висхідного потоку. У наступній по висоті частини апарату, званою пневмотранспортною, всі параметри двофазного потоку набувають постійного значення. Кількість часток певної величини, які потік може тут транспортувати при будь-якій конкретній швидкості, називається транспортуючою здатністю потоку. Значніша кількість матеріалу, яка циркулює в двох нижче розташованих зонах, називається здатністю потоку, що зважує. Ця величина визначається місцевою швидкістю потоку в умовах стиснутого руху часток, пакетів і струменів потоку газу.
Щоб досягти вказаної граничної величини, необхідно забезпечити досить ефективний і тривалий контакт певної кількості матеріалу з потоком. Останнє визначається витратою матеріалу, що вводиться у вертикальний канал струменем, і висотою псевдозрідженого на решітках шару часток.
Переміщення і розділення полідисперсних матеріалів на фракції в даних пристроях засноване на використанні різниці в швидкостях і направленні руху часток різного розміру у висхідному потоці в основному під дією гравітаційного поля. Із-за малого значення коефіцієнта опору повітря різниця в швидкості руху часток різних розмірів порівняно невелика, час їх перебування в апараті малий, і чіткого розділення на фракції не завжди вдається досягти. Тому в апаратах для розділення матеріалів за допомогою пневмокласифікації використовується сукупна дія на частки і інших сил, насамперед відцентрових і інерційних. Останні і створюють полиці, що вимушують висхідний потік змінювати направлення свого руху.
Полиці, підвищуючи швидкість і турбулентність потоку, в місці їх установки мають сильний вплив як на швидкість руху, так і на розподіл часток в поперечному перетині і по висоті каналу. Істотно змінюється як транспортуюча, так і зважуюча здібності потоку, оскільки на рух часток починає впливати інерційні сили.
Щоб забезпечити чітке розділення на класи, пневмокласифікатори конструюють таким чином, щоб дрібні і крупні частки рухалися в різних напрямках. Наприклад, дрібні частки виносяться вгору під впливом потоку, а крупні випадають вниз під дією сили тяжіння або виводяться в напрямку, перпендикулярному напрямку руху потоку під дією інерційних сил. Вказані сили, що викликають розділення часток по крупності, є різними функціями розміру часток. Сила дії потоку на поверхню частки (сила тертя), залежить від величини шорсткості і форми цієї поверхні часток і в першому наближенні пропорційна квадрату лінійного розміру. Об'ємні (гравітаційні і інерційні) сили визначаються величиною маси часток, вони пропорційні третьому ступеню визначального розміру часток. Крім того, поверхневі сили є функцією відносної швидкості між потоком і частками, яка визначає режим обтікання частки потоком.
Щоб з апарату виносилися близькі по розмірах частки, на виході багатьох пневмокласифікаторів створюється однорідне поле швидкостей потоку. Для цього за допомогою спеціальних контактних пристроїв вирівнюють епюру швидкостей потоку таким чином, щоб максимальна швидкість як можна ближче наближалася до середньої для всього перетину апарату. Якщо швидкості у вихідній ділянці апарату неоднакові, то в тих місцях, де швидкість потоку максимальна, виносяться найбільш крупні частки, розміри яких не відповідають середньої для перетину вихідної ділянки апарату. Оскільки вирівнювання потоку вимагає спеціальних пристроїв і значних по висоті ділянок апарату, то часто від нього відказуються, здійснюючи багатократну класифікацію по висоті апарату за допомогою каскаду суцільних або перфорованих полиць, серії решіток, зигзагоподібних ділянок і тому подібне. При цьому від однієї ділянки до іншої, розташованої вище, спостерігається часткова класифікація, тобто збагачення матеріалу частками необхідного розміру.
Порівняльні дослідження типових конструкцій апаратів завислого шару показали, що процеси пневмокласифікації зернистих матеріалів доцільно проводити на поличкових апаратах. В цих апаратах питома витрата повітря для досягнення тієї ж ефективності пневмокласифікації на 30-40% нижче [32]. Завдяки інтенсивному контакту фаз, в поличкових апаратах забезпечується максимальне знепилення продукту при високих питомих навантаженнях, які досягають 15-20 кг/м2с, що значно перевищує питомі навантаження 0,1-1,5 кг/м2с, при яких працюють апарати киплячого шару. Концентрація пилу у викидних газах після поличкового охолоджувача – пневмокласифікатора складає 200-500 г/м3 при питомих витратах охолоджуючого повітря 0,5-0,6 м3/кг, а після апаратів киплячого шару відповідно 25-30 г/м3 при 1,4-2,8 м3/кг [33]. Аналіз дослідних даних по вивченню залежності значення виносу дрібних часток і ефективності охолодження матеріалу від режимних (швидкості повітряного потоку, витрат матеріалу) і конструктивних параметрів (значення живого перетину полиць, їх кількості і відстані від кінця полиць до стінок апарату) [34, 35, 36], а також аналіз залежності граничної несучої здатності газового потоку і висоти зони сепарації від швидкості потоку і витання часток [37, 38], дозволили розробити оптимальні конструкції поличкових апаратів для ефективного проведення процесів пневмокласифікації.
3.4 Дослідження пневмокласифікації гранульованих матеріалів в полкових апаратах.
При встановленні у робочому об’ємі апарата похилої полки із значенням відношення l/B, що змінюється в межах від l/B = 1 (вільний канал) до l/B = 0,3, збільшуються значення винесення і ефективність вилучення з матеріалу дрібної фракції у винос, яка для полиць с живим перетином рівним 5 % досягає максимального значення (рис. 22).
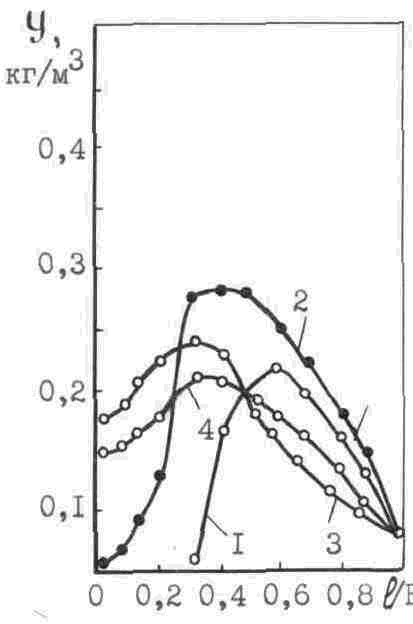
Рисунок 22. Вплив конструктивних параметрів поличкового контакту на величину виносу.
Живий перетин полиці: 1-4 – відповідно 0,5; 15 і 30%.
Закономірне підвищення величини винесення дрібної фракції із зменшенням відношення l/b пояснюється підвищенням швидкості повітряного потоку через розвантажувальний простір. Процес пневмокласифікації матеріалу для полиць живим перетином 0% (суцільна полиця) і 5 % відбувається інтенсивніше, ніж для полиць з живим перетином більше 15 %. Це пояснюється тим, що при малих значеннях живого перетину поличкового контакту, повітряний потік проходить переважно через розвантажувальний простір, а при великих - частина його проходить через отвори полиці, викликаючи тим самим зменшення швидкості повітряного потоку у розвантажувальному просторі.
Ефективність вилучення дрібної фракції на винесення (рис. 23), при величині відношення l/b = 0,5, має максимальне значення для полиці з живим перетином рівним 5 % і мінімальне для полиці з живим перетином рівним 15 %. При встановленні в робочому об'ємі апарату суцільної полки (fп = 0 %) весь повітряний потік проходить через розвантажувальний простір, обумовлюючи винесення дрібної фракції матеріалу саме в цій зоні. Наявність же перфорації в полиці (живий перетин до 5 %) викликає перерозподіл повітряного потоку, направляючи частину в отвори полиці.
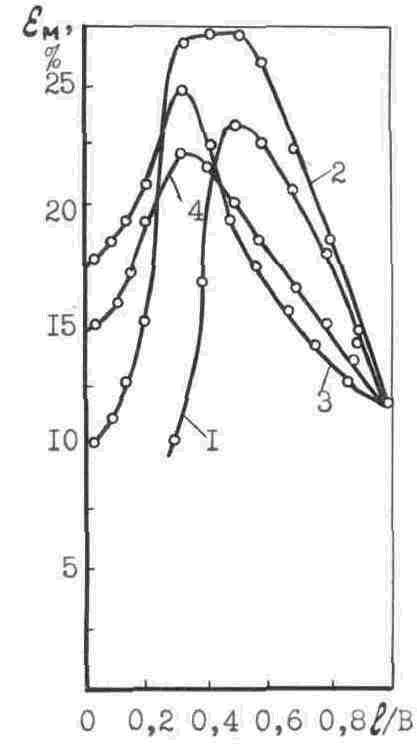
Рисунок 23. Вплив конструктивних параметрів полкового контакту на ефективність вилучення дрібної фракції в винос.
Живий перетин полки: 1-4 – відповідно 0; 5; 15 і 30%.
При цьому повітряний потік інтенсивно взаємодіє з матеріалом не лише в зоні розвантажувального простору, але і на поверхні полиці. Це обумовлює підвищення ефективності винесення дрібної фракції матеріалу на 20 % в апаратах з перфорованими полицями в порівнянні з апаратами з суцільними полицями. Подальше зменшення ефективності винесення дрібної фракції при збільшенні живого перетину похилої полиці до 15 % викликано посиленням ефекту перерозподілу повітряного потоку. Швидкість повітряного потоку у розвантажувальному просторі зменшується настільки, що процес вилучення дрібної фракції матеріалу в цій зоні не відбувається досить інтенсивно, а число отворів не забезпечує достатнього контакту фаз. Таке зменшення ефективності винесення дрібної фракції з оброблюваного в апараті матеріалу веде до зменшення витрат на пилоочищення повітря.
У діапазоні зміни величини відношення l/b, що відповідає збільшенню ефективності винесення дрібної фракції, матеріал проходить обробку в апараті в режимі "гравітаційно спадаючого шару". При цьому енергії висхідного повітряного потоку достатньо для ефективного виносу дрібних часток з тонкого шару матеріалу, зваженого на поверхні стінки апарату в зоні розвантажувального простору. При зменшенні величини відношення l/b нижче за значення 0,3 для перфорованої полиці і значення 0,5 для суцільної полиці відбувається зниження ефективності виносу дрібної фракції матеріалу, оскільки частки матеріалу, які при цьому проходять обробку в режимі "зваженого шару", активно перемішуються, концентрація, а отже і зцепленість циркуляційному руху часток підвищується в робочому об'ємі апарату і енергії повітряного потоку недостатньо для ефективного винесення дрібного компоненту з шару матеріалу. Однак активна дія повітряного струменя, що входить у зріджений шар оброблюваного матеріалу, підвищує величину винесення і ефективність винесення дрібної фракції матеріалу в гравітаційних поличних апаратах в порівнянні з апаратами псевдозрідженого шару (l/b = 0) в 1,2 - 1,5 раз.
Ефективність винесення дрібної фракції матеріалу залежить від кута нахилу перфорованої полиці і для кутів нахилу 25 - 30° досягає свого максимального значення, а для кутів нахилу менше і більше вказаної межі знижується. Зменшення ступеня ефективності винесення дрібної фракції матеріалу при збільшенні кута нахилу полиці пояснюється тим, що полиця при цьому не має гальмівну дію на потік матеріалу, який не досить інтенсивно взаємодіє з повітряним потоком на поверхні полиці і в зоні розвантажувального простору. При зменшенні кута нахилу полиці, за рахунок часткового гальмування часток матеріалу об поверхню полиці, відбувається зменшення кінетичної енергії потоку матеріалу, який значно легше зважується повітряним потоком в робочому об'ємі апарату. Проте зменшення кута нахилу полиці до значень менше 20 - 30° сприяє надмірному накопиченню щільного шару матеріалу на поверхні полиці, що утруднює винесення дрібного компонента з вихідного матеріалу.
Таким чином, зміна конструктивних параметрів і розташування полиць в апараті дозволяє шляхом зміни гідродинамічних режимів і інтенсивності зважування часток матеріалу в робочому об'ємі апарату регулювати процес винесення дрібного компоненту в широких межах.
Швидкість повного винесення дрібної фракції матеріалу за відсутності у ньому крупних часток, назвемо першою критичною швидкістю винсення, значення якої визначиться як
Re1кр = 0,1 Ar 0,7 при Ar ≤ 62000 (5.1)
Для кожного положення похилої полиці існує певне значення швидкості повітряного потоку, при якому в результаті зміни гідродинамічних режимів спостерігається зниження ефективності винесення дрібної фракції. Оскільки при встановленні в робочому об'ємі апарату суцільних полиць таке значення швидкості нижче, ніж в разі встановлення перфорованих полиць, то пневмокласифікатори з перфорованими полицями мають великі можливості їх використання для пневмокласифікації ширшого класу полідисперсних зернистих і гранульованих матеріалів в порівнянні з апаратами з суцільними полицями.
З рис. 3.11 витікає, що величина винесення окремих фракцій матеріалу з апарату закономірно підвищується із збільшенням швидкості повітряного потоку, і, що існує певне значення швидкості повітряного потоку, при якому винесення крупної фракції матеріалу перевищує винесення дрібної. Цю швидкість назвемо другою критичною швидкістю винесення. Граничне її значення характеризує припинення процесу пневмокласифікації і визначається рівнянням:
W 2кр = 3( U1B – U2B) 0,2 (5.2)
де: U 1B, U2B - швидкості вітання відповідно найбільшого розміру часток дрібної фракції і найменшого розміру часток крупної фракції матеріалу.
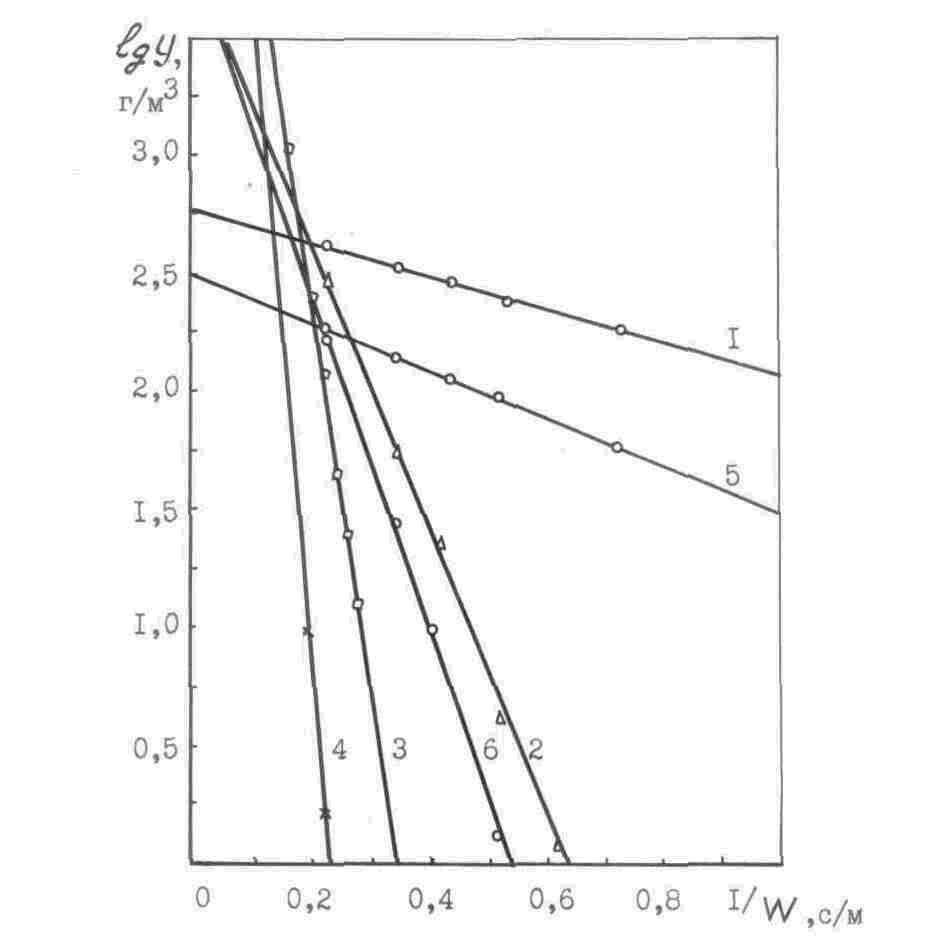
Рисунок 24. Залежність значення виносу окремих фракцій матеріалу від швидкості повітряного потоку.
Із залежностей, представлених на рис. 24 витікає, що установка в робочому об'ємі апарату похилої перфорованої полиці викликає збільшення ефективності виносу дрібної фракції матеріалу в 1,5 - 2 рази в порівнянні з апаратами з вільним перетином типу пневмотруб. Це зумовлюється різним характером розподілу повітряного потоку по перетину робочого об'єму апарату - нерівномірним в поличному апараті і рівномірним в апаратах з вільним перетином.
Процес пневмокласифікації при оптимальних конструктивних параметрах рівних l/b = 0,5 і fп = 5% проходить досить ефективно при швидкості повітряного потоку у вільному перетині апарату рівної 3,5-4,0 м/с, значення якої значно менше величини швидкості витання часток розміром 2 мм рівною 5,5 м/с. При цьому виноситься до 20 - 25 % фракції менше 2 мм, що міститься у вихідному матеріалі. Такий суперечливий факт зумовлює необхідність обліку реального розподілу швидкостей повітряного потоку для правильного виявлення особливостей протікання процесу пневмокласифікації в гравітаційному поличковому апараті. В даному випадку має місце двоякий механізм протікання цього процесу. З одного боку, процес винесення дрібної фракції матеріалу з шару біля поверхні стінки в розвантажувальному просторі, відбувається за рахунок повітряного потоку, швидкість якого в даному місці дорівнює 5,6 м/с, тобто більше швидкості витання винесених часток розміром 2 мм. Швидкість повітряного струменя, що виходить з простору розвантажувальної щілини, знижується за рахунок її розширення на виході, а частки матеріалу, отримавши імпульс в зоні розвантажувального простору, продовжують рухатися із швидкістю, що поступово зменшується, більшою за швидкість повітряного потоку. Їх швидкості вирівнюються на висоті зони сепарації апарату рівною 1,5 - 2 довжини перетину його робочого об'єму. Вище за цей рівень починається стаціонарна ділянка зони сепарації апарату заввишки до 1 - 2 м, у якому механізм пневмокласифікації відбувається лише за рахунок дії повітряного потоку, швидкість якого більше швидкості витання часток найбільшого розміру, що виносяться. З іншого боку, часткам надається імпульс за рахунок удару їх об поверхню стінки і зіткнень один об одного в зоні розвантажувального простору, оскільки сила інерції часток, що рухаються в даному випадку в режимі "гравітаційно спадаючого шару", зберігається при їх русі по поверхні похилої полиці. Тому за рахунок дії на процес пневмокласифікації як енергії повітряного потоку, так і енергії за рахунок зіткнення часток матеріалу, можна зменшити висоту стаціонарної ділянки зони сепарації апарату або повністю її виключити, що зменшить габарити апарату по висоті. При цьому знижуються витрати повітря, що подається в апарат, оскільки процес пневмокласифікації ведеться при швидкостях повітряного потоку в перетині апарату значно менших, ніж швидкість витання часток найбільшого розміру, що виносяться.
Таким чином, поличний апарат для проведення процесу винесення з вихідного матеріалу часток розміром до 2 мм є ефективнішим і економічнішим по витратам повітря в порівнянні з апаратами з вільним перетином і псевдозрідженим шаром.
Висновок по главі
У хімічній технології гідромеханічне розділення гранульованих матеріалів по розмірах проводять в основному за допомогою грохотів. Інколи використовують апарати киплячого шару [22, 39, 40, 41]. При цьому велика частина енергії газового потоку витрачається на гідродинамічну стабілізацію киплячого шару, висота якого досягає 0,2-0,5 м, що обумовлює підвищені енерговитрати і стирання часток, що призводить до необхідності встановлення енерго- та металоємних систем пилоочищення.
Таким чином, на нашу думку наукові дослідження в області гідромеханічних процесів розділення гранульованих матеріалів слід направити на розробку перш за все енергозберігаючих апаратів зваженого шару, у яких достатня ефективність поєднувалася б з мінімальними витратами на проведення процесу і пилоочищення. Таким завданням відповідають поличкові апарати.
У поличкових апаратах реалізуються активні аеродинамічні режими зважування твердих часток, причому умови їх створення, на відміну від типових апаратів зваженого шару, легко змінювати в широких межах швидкостей газового потоку, не змінюючи докорінно конструкцію.
Дана особливість дозволяє створювати в поличкових апаратах різні види дисперсних потоків, в яких відбувається не лише кількісна зміна основних характеристик потоку (щільності, швидкостей, коефіцієнта тепло- і массовіддачі), але – за певних критичних умов – і якісні зміни структури потоку, механізму руху фаз і умов тепло- і масопереносу. Наявність в поличкових апаратах різних гідродинамічних режимів перенесення твердих часток (від гравітаційно спадаючого до зваженого шару), аналогічне відомим критичним режимам Рейнольдса, висуваються як робоча гіпотеза, яка підтверджена теоретично і експериментально [32]. Завдяки виявленим гідродинамічним режимам, поличкові контактні елементи забезпечують більш високу ефективність пневмокласифікації і теплоообменних процесів і при менших витратах газу і гідравлічному опорі [42], ніж решітки з псевдозрідженим шаром і пристрої з вільним перетином. Використання поличкових елементів і виявлених особливостей газодисперсного потоку дозволило розробити високоефективні апарати для знепилювання, пневмокласифікації і охолоджування гранульованих матеріалів [36, 43].
Висока ефективність, менші капітальні і експлуатаційні витрати, незначні габарити і гідравлічний опір, вища питома продуктивність поличкових апаратів в порівнянні з типовими апаратами зваженого шару робить перші вельми перспективними апаратами для застосування в різних галузях промисловості.
- Математичне моделювання процесу грануляції
4.1 Програма розрахунку апарата
Блок-схема розрахунку матеріальних потоків представлена на рис 25.
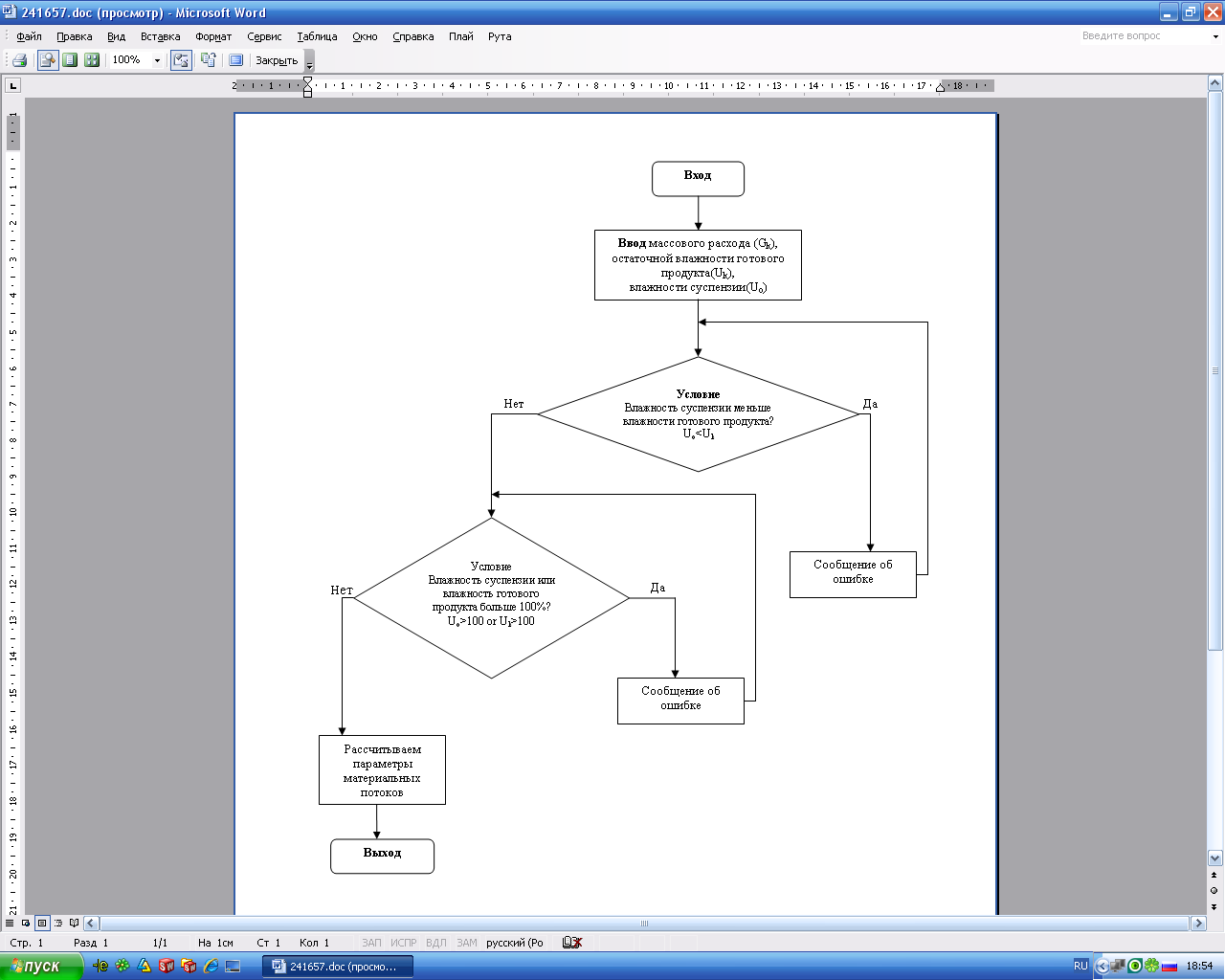
Рисунок 25 – Блок-схема процедури розрахунку матеріальних потоків
Структура процедури розрахунку швидкості теплоносія, параметрів решітки і сепараційного простору: умови перевірки аналогічни умовам процедури розрахунку матеріальних потоків.
Блок-схема розрахунку швидкості теплоносія, параметрів решітки і сепараційного простору представлена на рисунке 26.
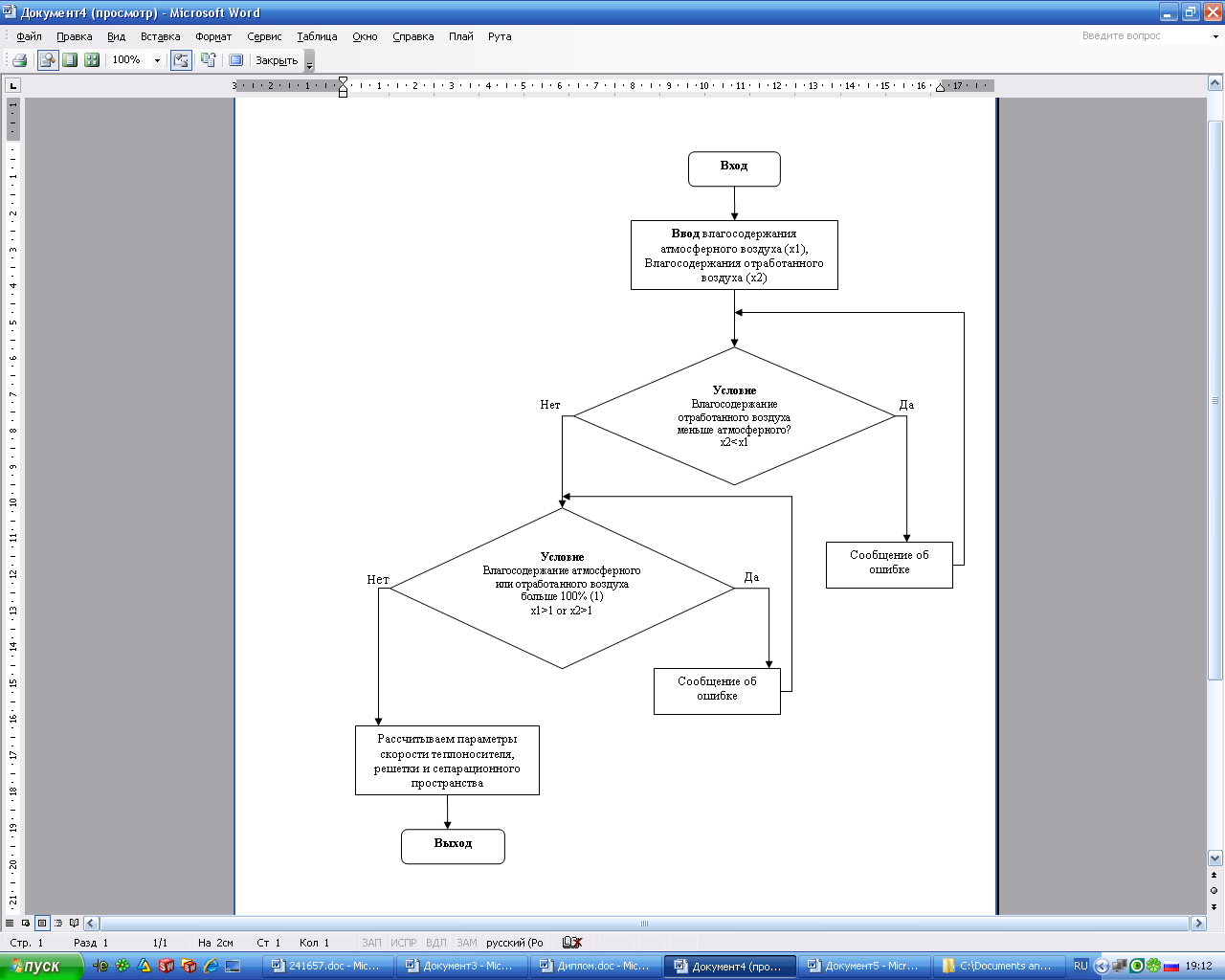
Рисунок 26 – Блок-схема процедури розрахунку швидкості теплоносія, параметрів решітки і сепараційного простору
Для реалізації програмного коду було вибране середовище програмування Borland Delphi 7.
Borland Delphi – це інтегроване середовище розробки програмного забезпечення. Delphi предоставляє повне вирішення для розробки корпоративних додатків від проектування до розвертання по архитектурі, керованої моделлю (MDA), яка дозволяє інтегрувати моделювання, розробку і розвертання додатків і систем електронного бізнеса для платформи Windows.
Програма включає в себе один модуль, який складається з трех процедур: процедура розрахунку матеріальних потоків, процедура розрахунку швидкості теплоносія, параметрів решітки і сепараційного простору, часу перебування матеріалу в апараті, процедура формування звіту.
Інтерфейс програми представляє собою форму, яка має структуру вкладень. Розрахунок матеріальних потоків представлений на рис. 27.
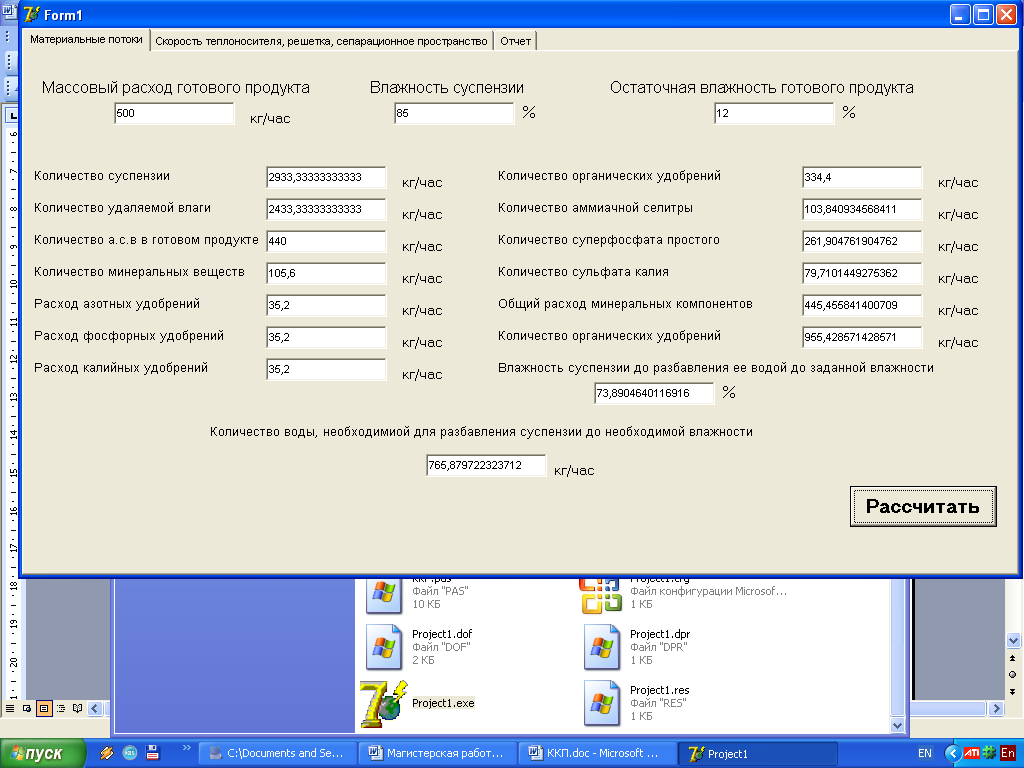
Рисунок 27 – Розрахунок матеріальних потоків
Після розрахунку матеріальних потоків визначаємо швидкість теплоносія, параметри решітки і сепараційного простору (рис.28).
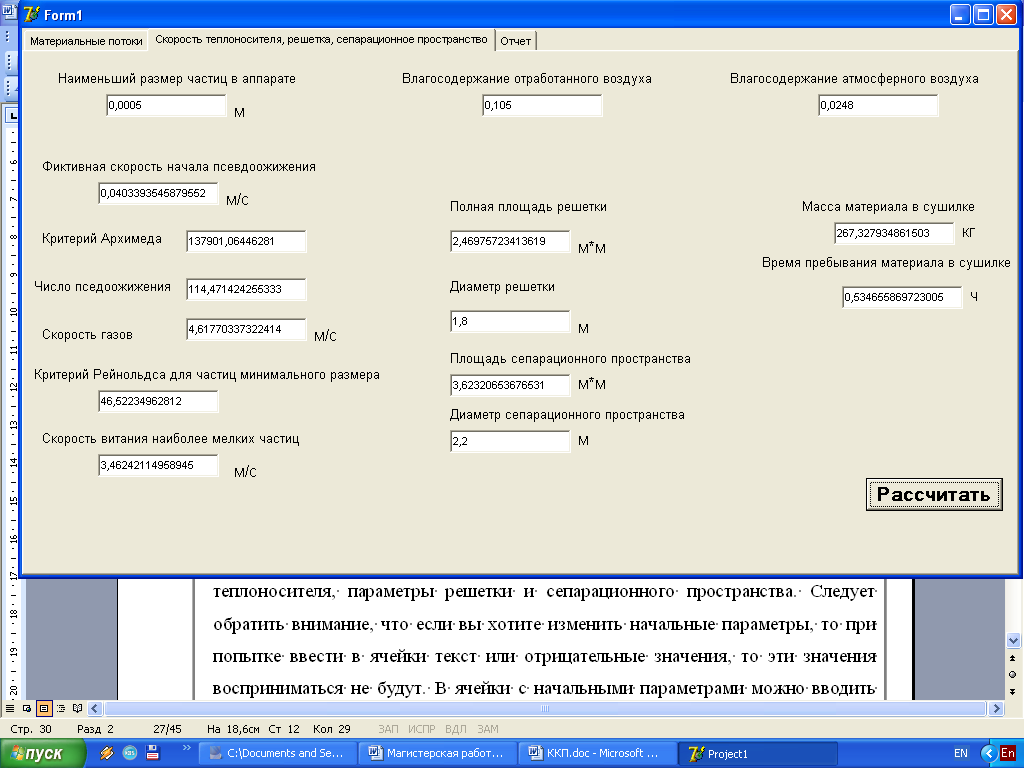
Рисунок 28 – Розрахунок швидкості руху теплоносія в апараті, параметрів решітки і сепараційного простору, часу перебування матеріалу в грануляторі
Розроблена програма дозволяє прискорити процес обчислення, підвищити якість проектування, знизити похибки при розрахунках і округленні.
Перевірку роботоспроможності програми було здійснено у порівнянні з існуючою методикою технологічного розрахунку, виконаного вручну. Час ручного розрахунку складає приблизно 30 хв. Аналогічні вихідні значення були задані для програмного розрахунку. Точність розрахунку вище, час розрахунку на сучасному комп’ютері складає приблизно 5 секунд. Одержані результати свідчать про коректність роботи програми.
ВИВСНОВКИ ПО ГЛАВІ:
- розроблена програма розрахунку матеріальних потоків, швидкості теплоносія в апараті, розміру решітки і сепараційного простору в Borland Delphi 7;
- розроблена структура і інтерфейс програми розрахунку технологічного процесу, яка представляє собою форму з вкладковою структурою;
- здійснена перевірка роботоспроможності програми в порівнянні з існуючою методикою технологічного розрахунку, виконаного вручну.
В данній науково-дослідній роботі:
- вивчено вплив різних факторів на процес гранулювання у псевдозрідженому шарі;
- вибрана оптимальна конструкція гранулятора у виробництві гранульованих органомінеральних добрив;
- вивчені різні методики розрахунку швидкості теплоносія і розмірів решітки, вибрана оптимальна методика розрахунку;
- розроблена програма розрахунку матеріальних потоків, швидкості теплоносія в апараті, розміру решітки і сепараційного простору в Borland Delphi 7;
- розроблена структура і інтерфейс програми розрахунку технологічного процеса, яка представляє собою форму з вкладковою структурою;
- здійснена перевірка роботоспроможності програми в порівнянні з існуючою методикою технологічного розрахунку, виконаною вручну.