Контрольная работа по организации производства организация внутрипроизводственных
Вид материала | Контрольная работа |
Содержание2ПРАКТИЧЕСКАЯ ЧАСТЬ 2.1Условие |
- Вопросы для поступающих по дисциплине «Организация производства», 29.25kb.
- Контрольная работа для студентов первого- второго курса заочного отделения. Контрольная, 11.95kb.
- Лекции по дисциплине «Организация и планирование производства» Тема Сущность и задачи, 76.87kb.
- Курсовая работа По предмету : Организация производства на тему: «Организация автоматизации, 311.23kb.
- Объект и предмет изучения, сущность и цели организации производства, 380.75kb.
- Контрольная работа №1 Прежде чем приступить к выполнению работы необходимо изучить, 68.42kb.
- Вопросы к курсовому экзамену по фармацевтической технологии заводского производства, 113.84kb.
- Тематика курсовых работ по курсу «Организация производства», 25.9kb.
- Контрольная работа по дисциплине «Экономика организаций» на тему: «Производственная, 204.12kb.
- Рабочей программы учебной дисциплины организация производства уровень основной образовательной, 50.63kb.
2ПРАКТИЧЕСКАЯ ЧАСТЬ
2.1Условие
В соответствии с представленными ниже данными рассчитать:
- минимальный размет партии деталей;
- периодичность выпуска этой партии в обработку;
- оптимальный размер партий деталей;
- потребное количество станков для обработки деталей а,б,в,г,д,е, изделия А;
- длительность производственного цикла.
Исходные данные:
- месячный выпуск изделия А в сборочном цехе составляет 1000 штук;
- число рабочих дней в месяце – 20;
- режим работы в сборочном цехе 1- сменный, в механообрабатывающем, 2–сменный;
- продолжительность рабочей смены – 8 часов;
- время на плановый ремонт и переналадку оборудования 6% от номинального фонда рабочего времени.
Пооперационные нормы штучного времени обработки деталей представлены в таблице 4.
Таблица 4 – Состав операций и нормы штучного времени
Операции | Норма штучного времени обработки деталей (ti), мин | Подготовительно-заключительное время, t пз , мин | Допустимые потери времени на переналадках оборудования, а об, % | |||||
а | б | в | г | д | е | |||
Фрезерная | 10 | 16 | 25 | 2 | 6 | 6 | 20 | 4 |
Сверлильная | 15 | 13 | 6 | 2 | 4 | 4 | 20 | 4 |
Шлифовальная | 3 | 6 | 6 | 3 | 2 | 2 | 20 | 4 |
Строгальная | - | 8 | 10 | - | 2 | 2 | 20 | 4 |
Зуборезная | - | 12 | 9 | - | - | - | 60 | 5 |
Токарная | - | - | - | 8 | 4 | 2 | 20 | 4 |
2.2Решение
2.2.1Шаг 1
Рассчитаем минимальный размер партии деталей
Первый способ, когда для обработки деталей применяется оборудование, требующее значительного времени на переналадку.
Применительно к нашей задаче этому требованию отвечает зуборезная операция, для выполнения которой требуется 60 мин подготовительно-заключительного времени. В данном случае для обработки деталей б и в минимальный размер партии определяется по формуле:
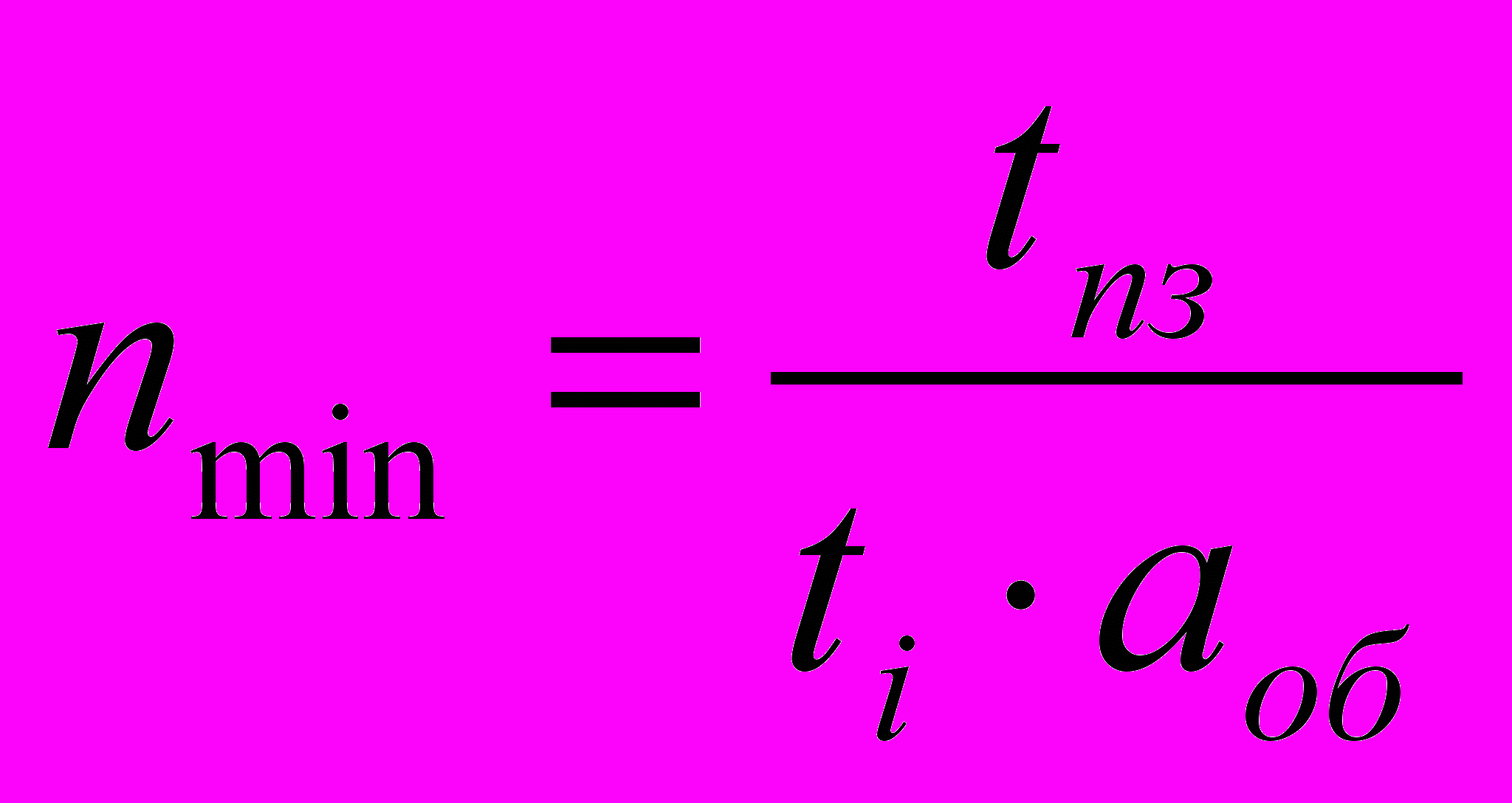
где t пз – подготовительно-заключительное время, мин;
ti – норма времени на изготовление 1 детали, мин;
а об – допустимые потери времени на переналадку, доли единицы
Минимальный размер партии для деталей б и в:
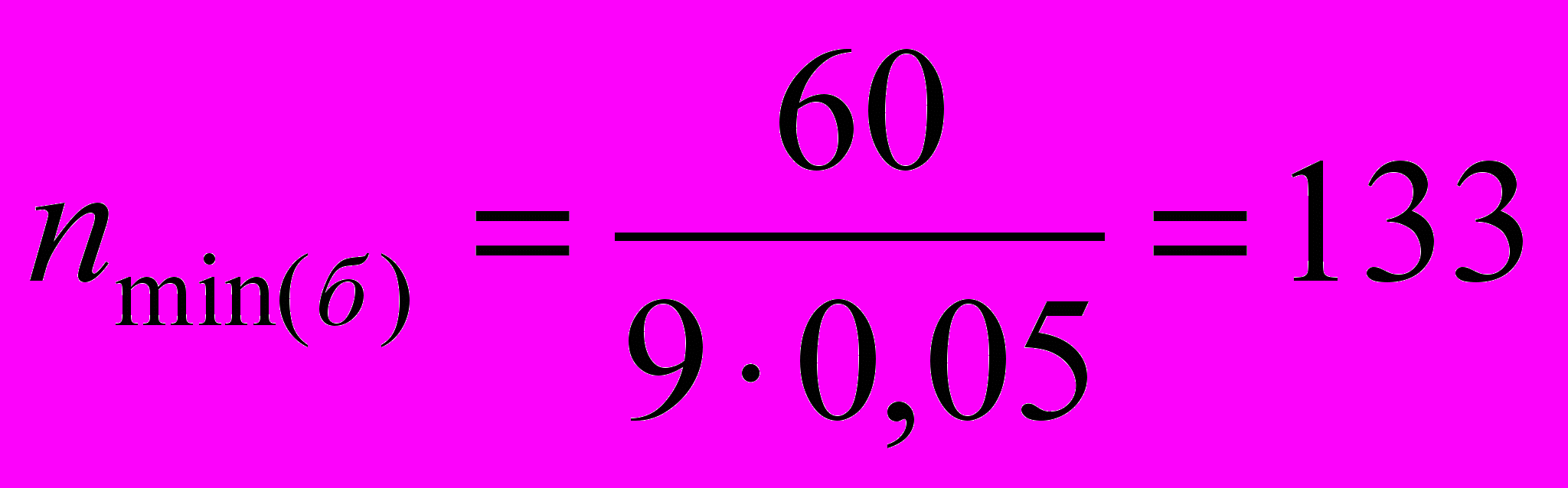
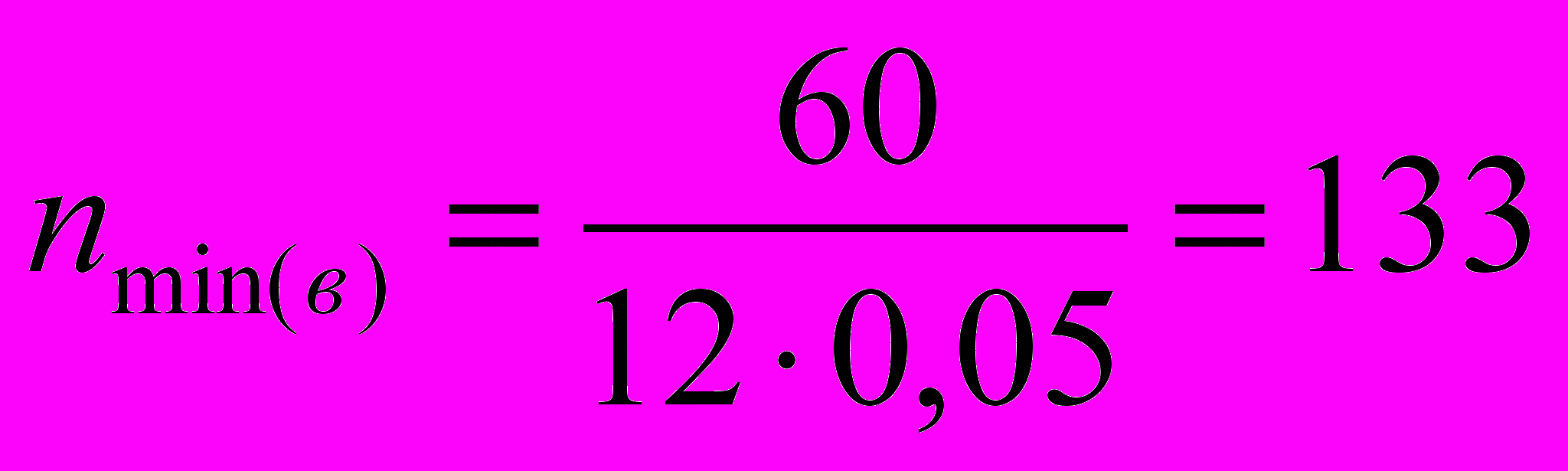
Второй способ, когда для обработки деталей применяется оборудование, не требующее значительного времени на переналадку. Применительно к нашей задаче этому требованию отвечают все остальные операции технологического процесса, требующие 20 мин подготовительно-заключительного времени. В данном случае для деталей а, г, д и е минимальный размер партии рассчитывается по формуле:
n min = t см / ti , (23)
где t см - продолжительность смены;
t - норма штучного времени (минимальная из всех операций)
n min(а) = 480 / 4 = 120 дет,
n min(г) = 480 / 4 = 120 дет,
n min(д) = 480 / 4 = 120 дет,
n min(е) = 480 / 4 = 120 дет,
2.2.2Шаг 2
Периодичность запуска – выпуска партии деталей определяется по формуле:
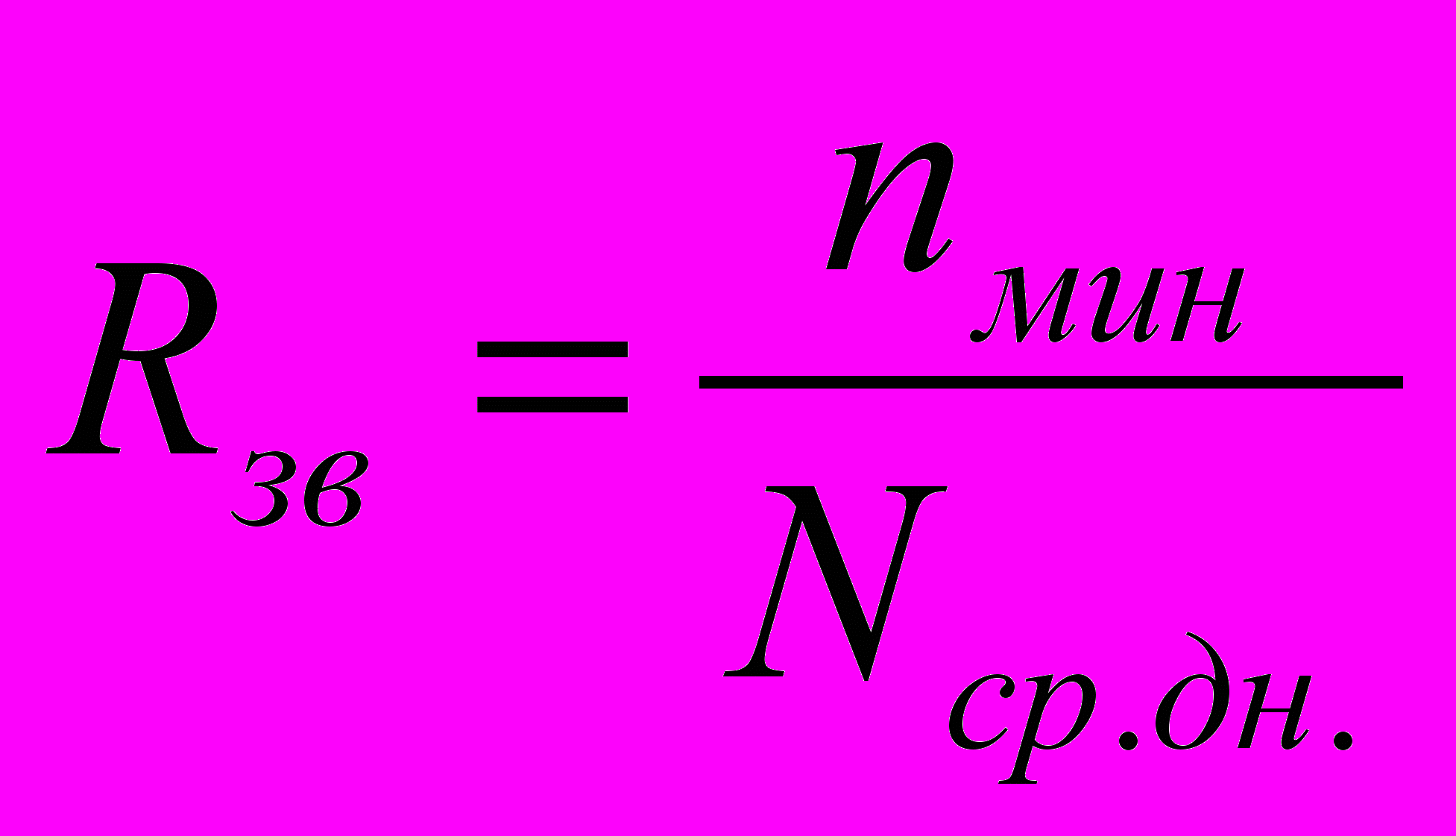
где N ср .дн – среднедневная потребность в деталях.
Последняя рассчитывается по формуле:
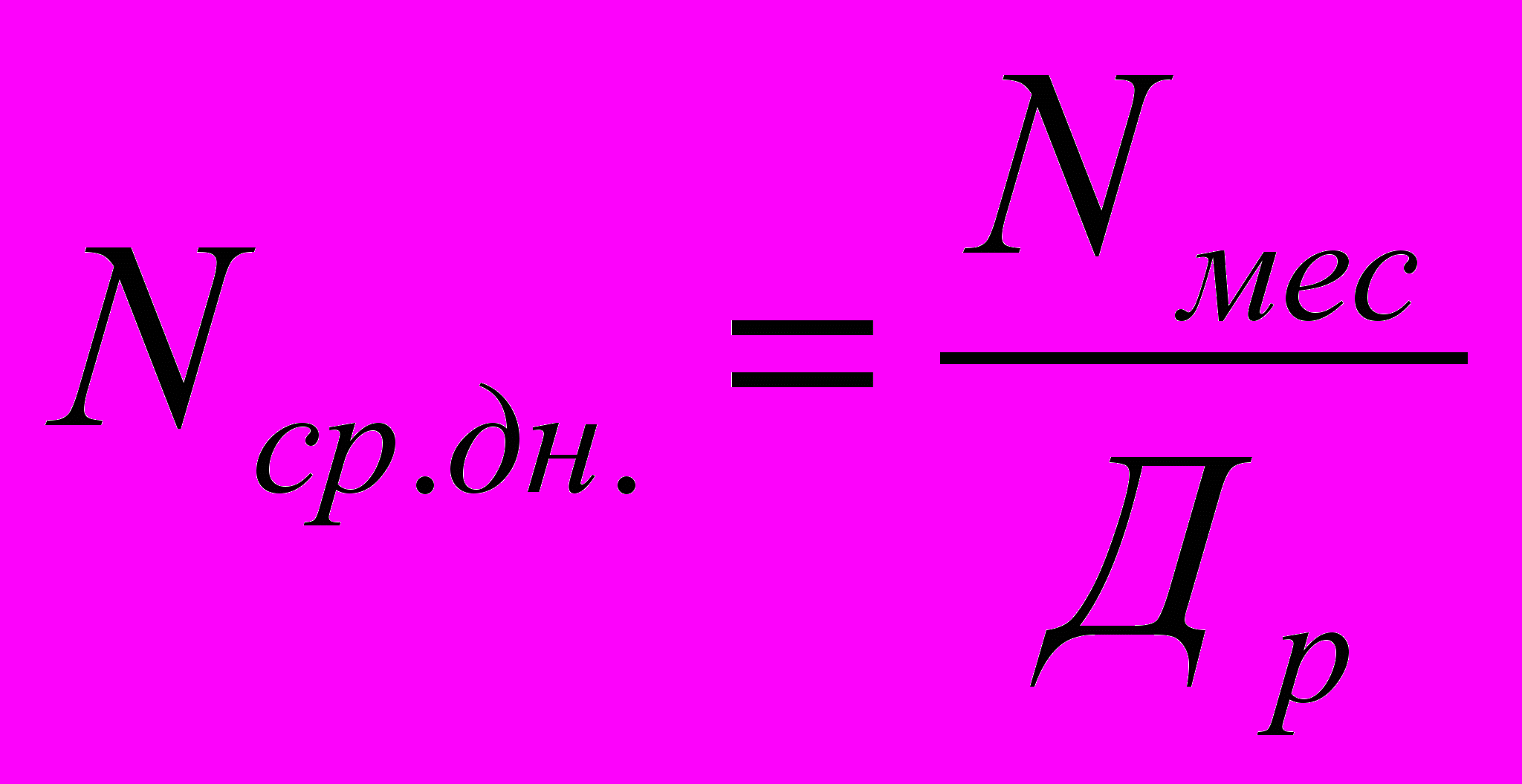
где Nмес – месячный выпуск изделий, шт.,
Др – число рабочих дней в месяце.
Подставляя исходные и полученные данные найдем:
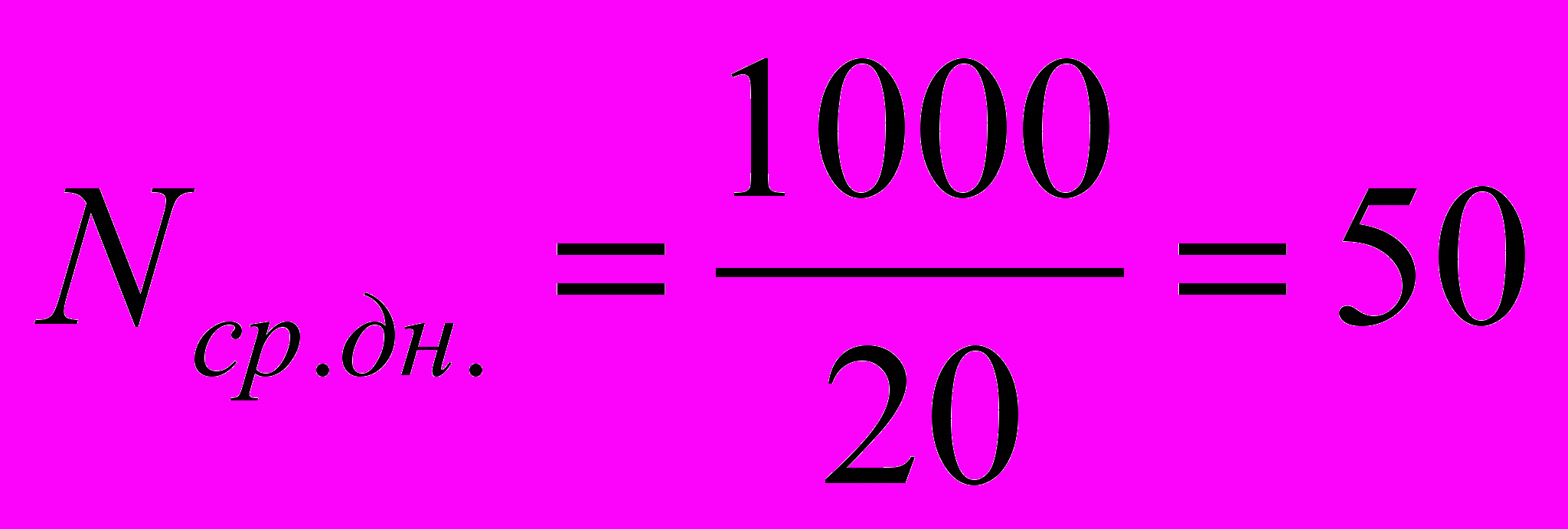
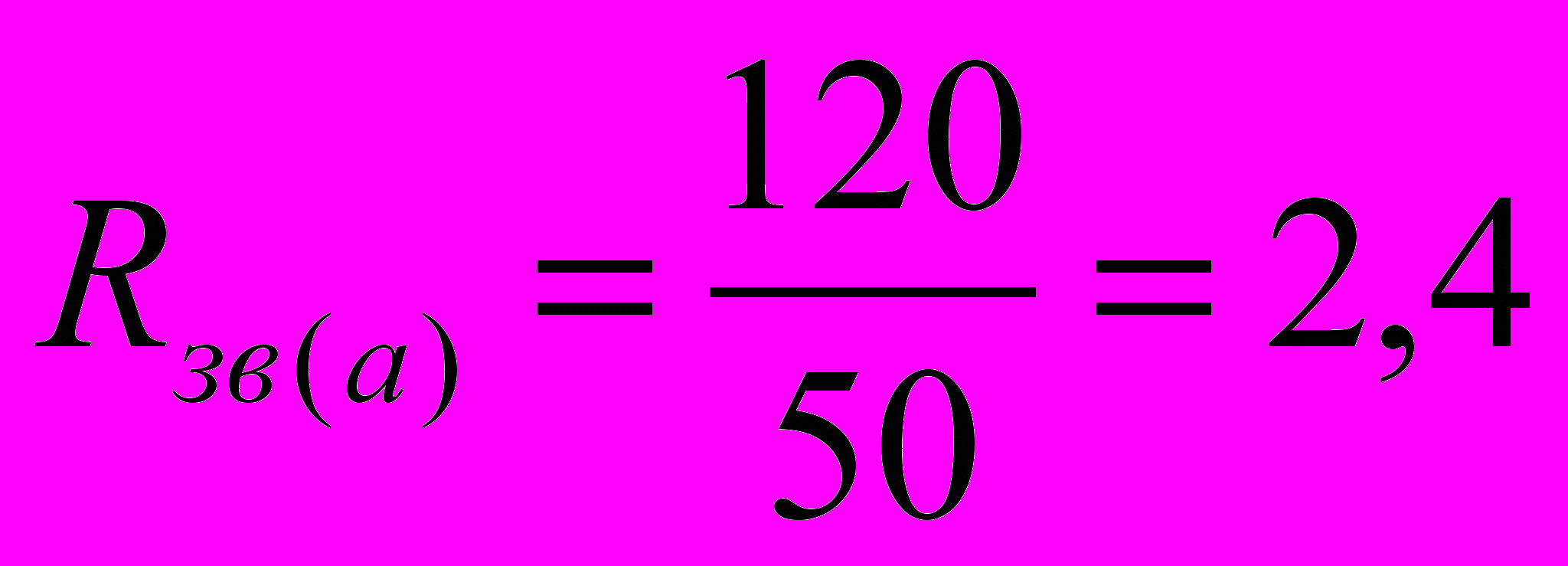
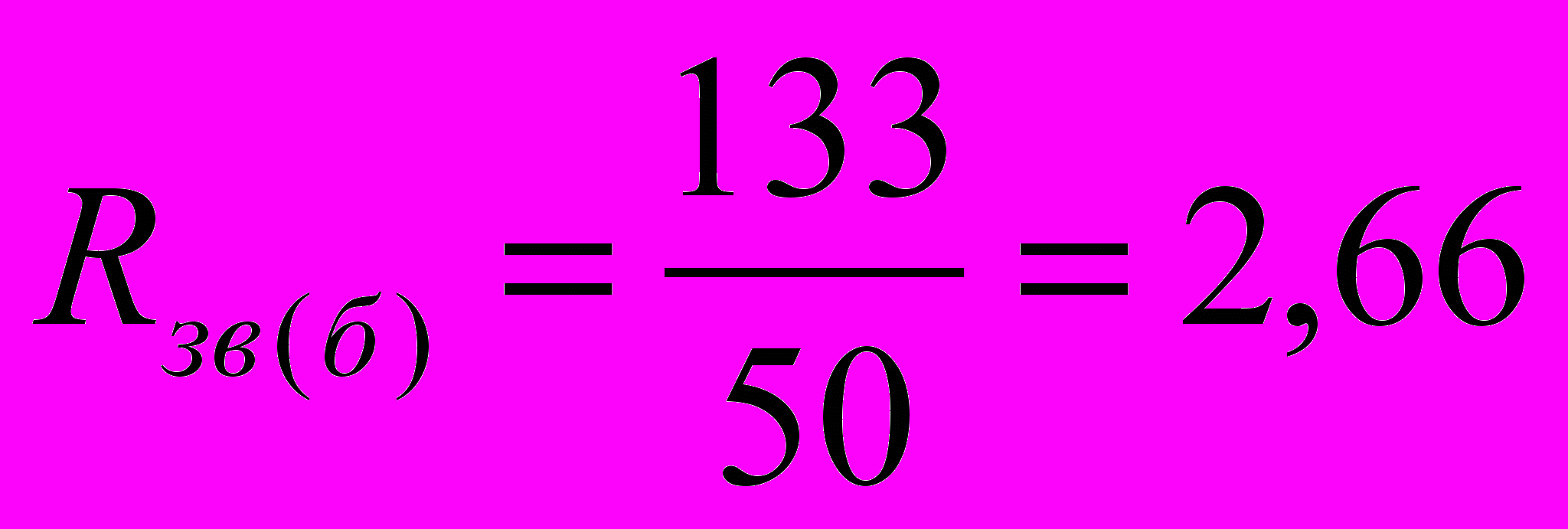
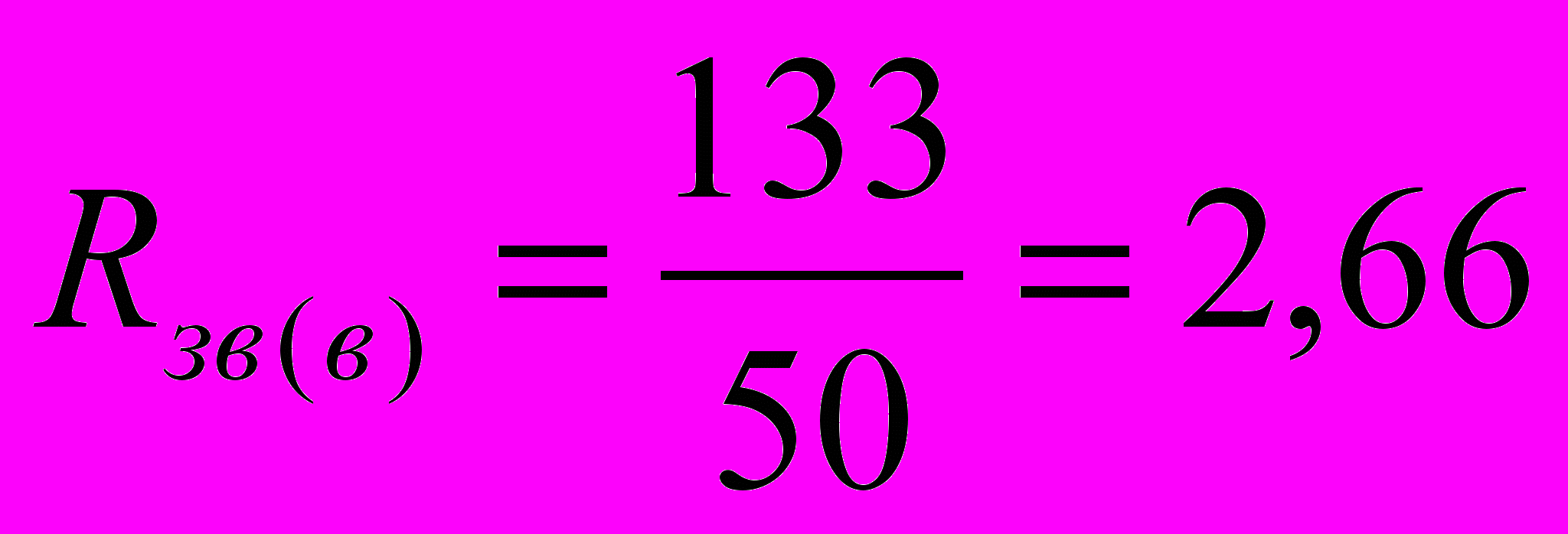
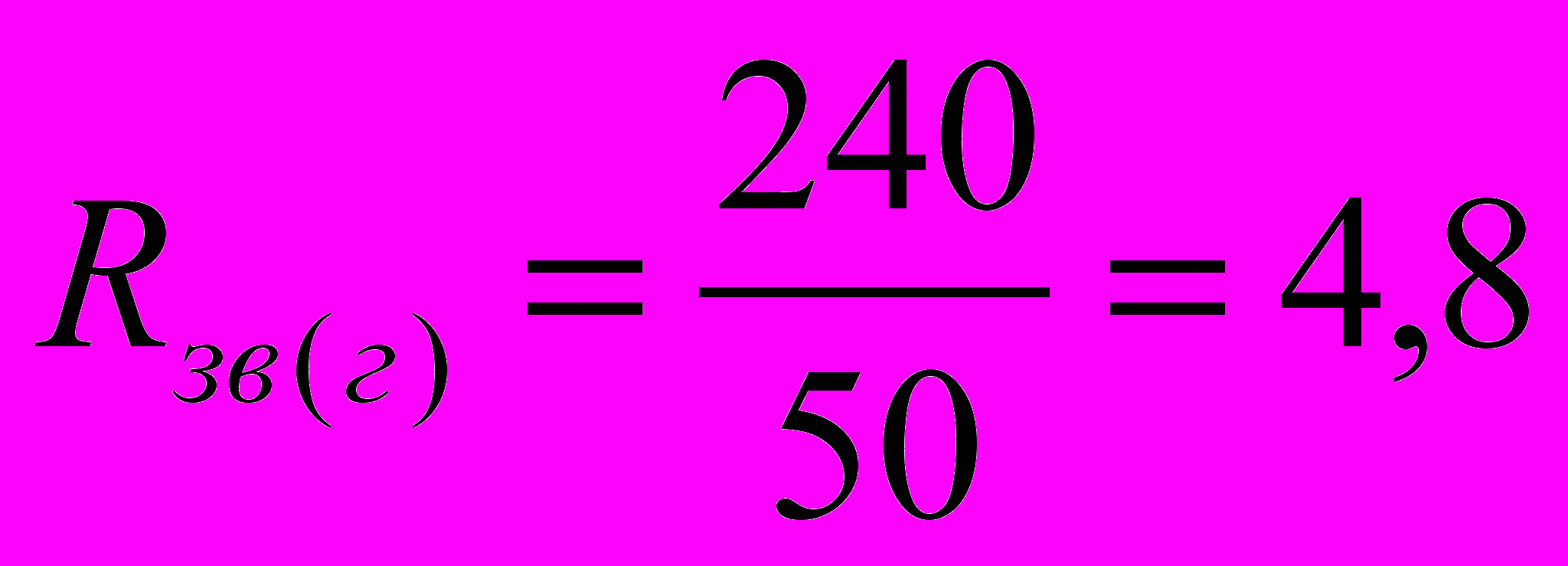
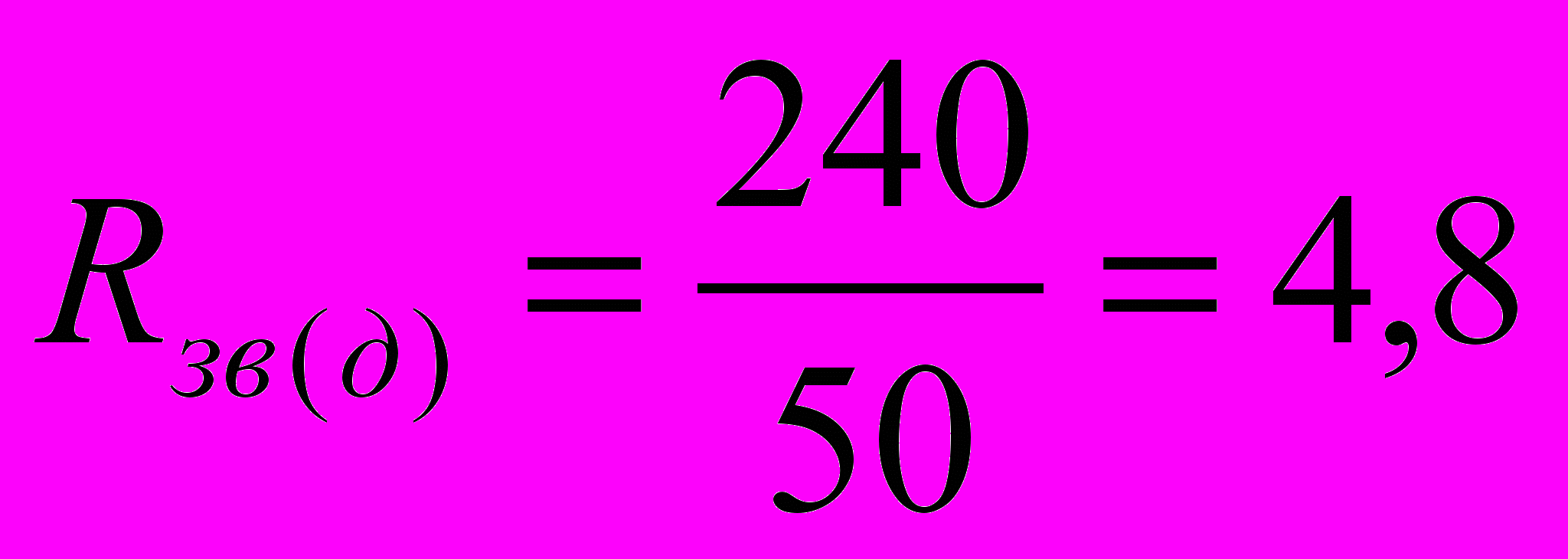
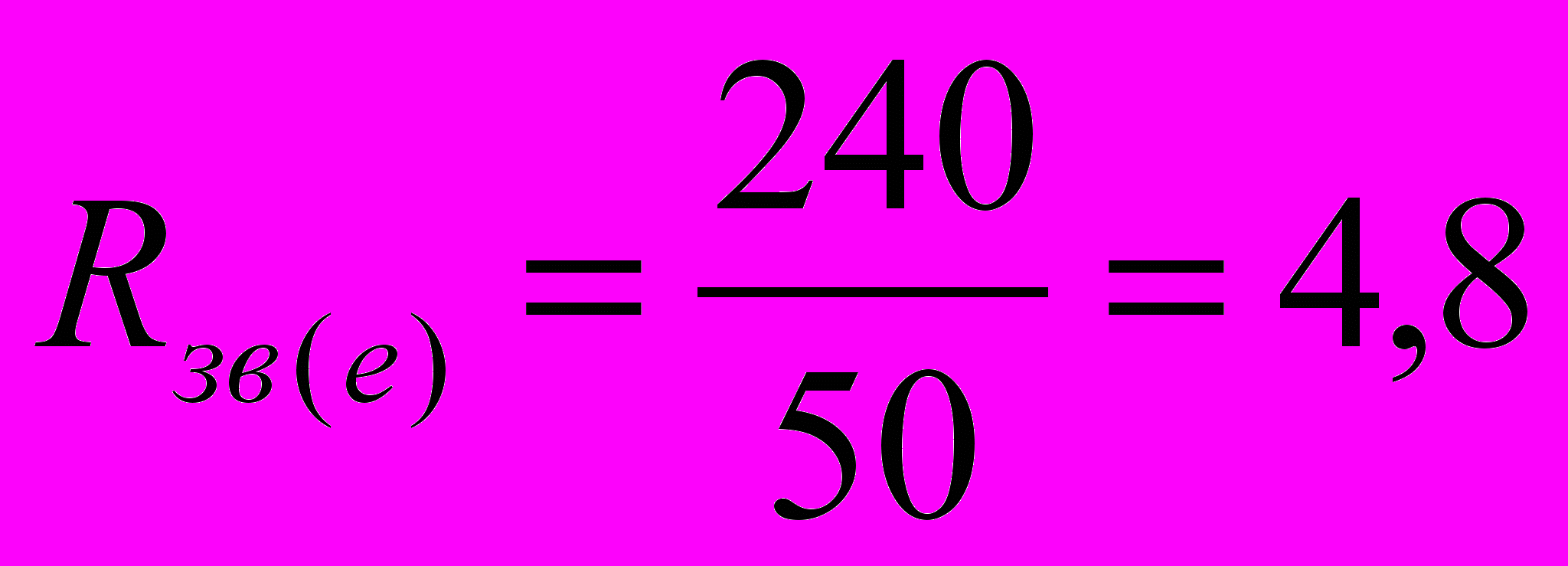
Для обеспечения кратности выпуска деталей необходимо скорректировать данные. Корректировка приведена в таблице 5
Таблица 5 – Корректировка периодичности запуска – выпуска деталей
а | 2,4 | 2,5 |
б | 2,66 | 2,5 |
в | 2,66 | 2,5 |
г | 4,8 | 5,0 |
д | 4,8 | 5,0 |
е | 4,8 | 5,0 |
2.2.3Шаг 3
Оптимальный размер партии деталей определяется по формуле:



2.2.4Шаг 4
Количество партий в месяц определим по формуле:
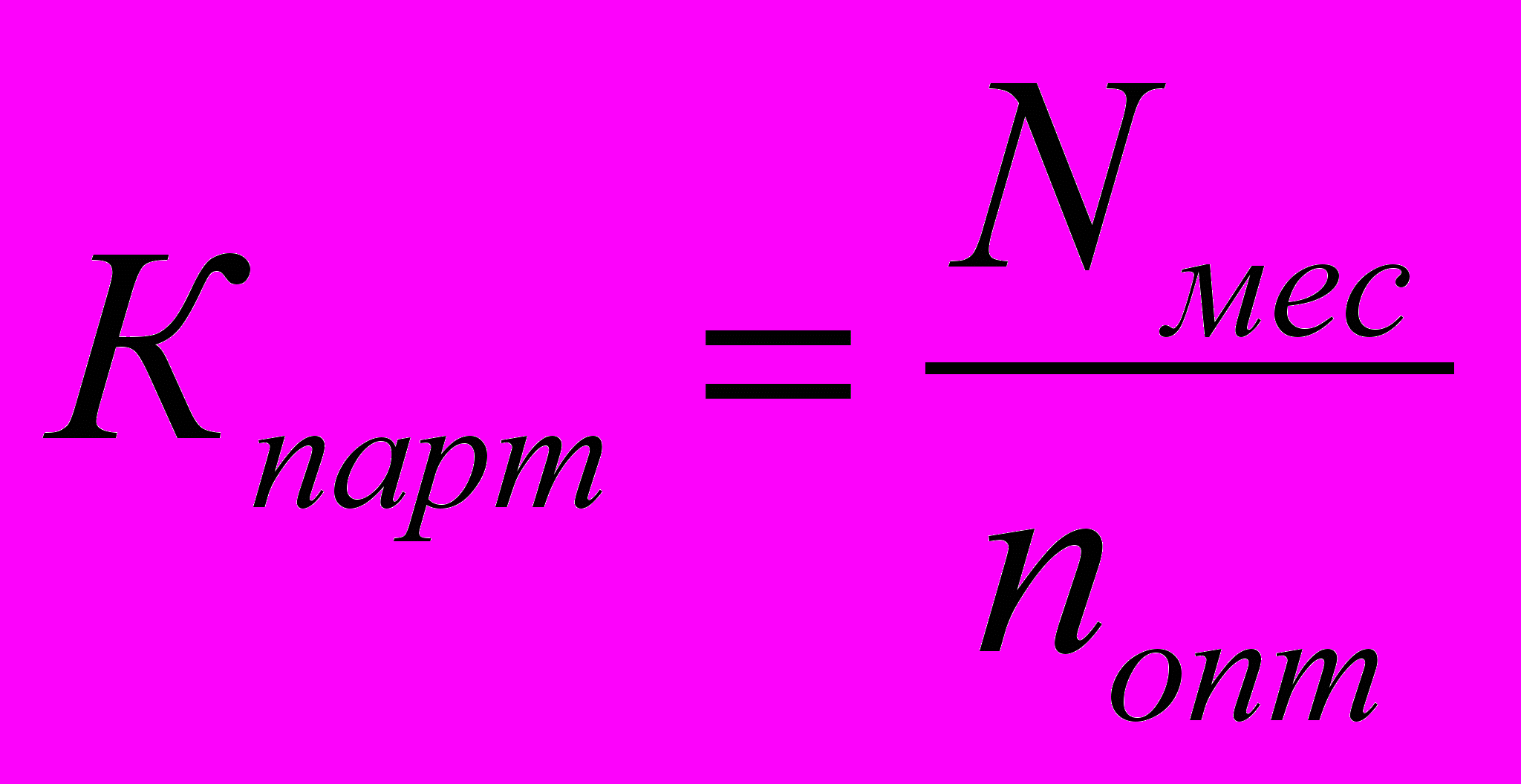
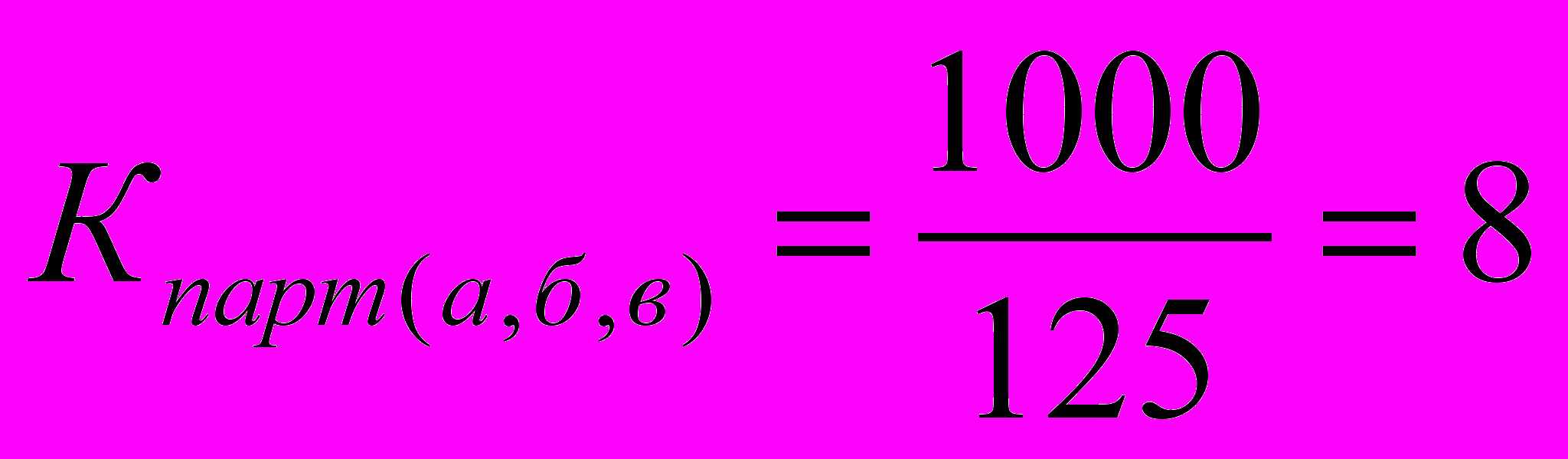
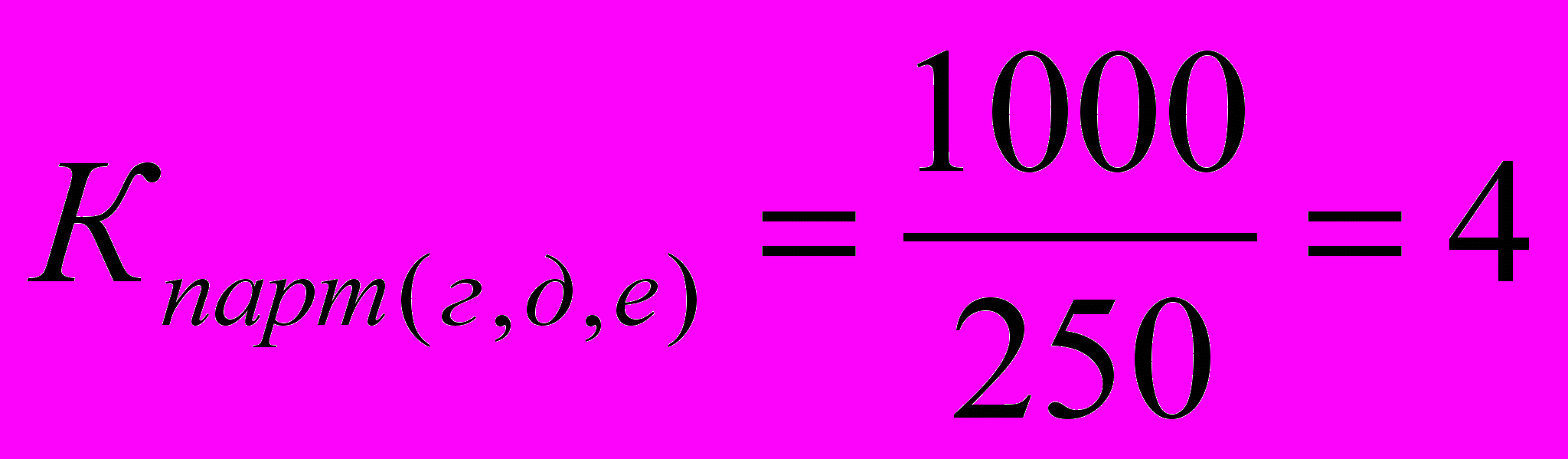
2.2.5Шаг 5
Потребное число станков на месячную программу выпуска деталей рассчитывается по формуле:
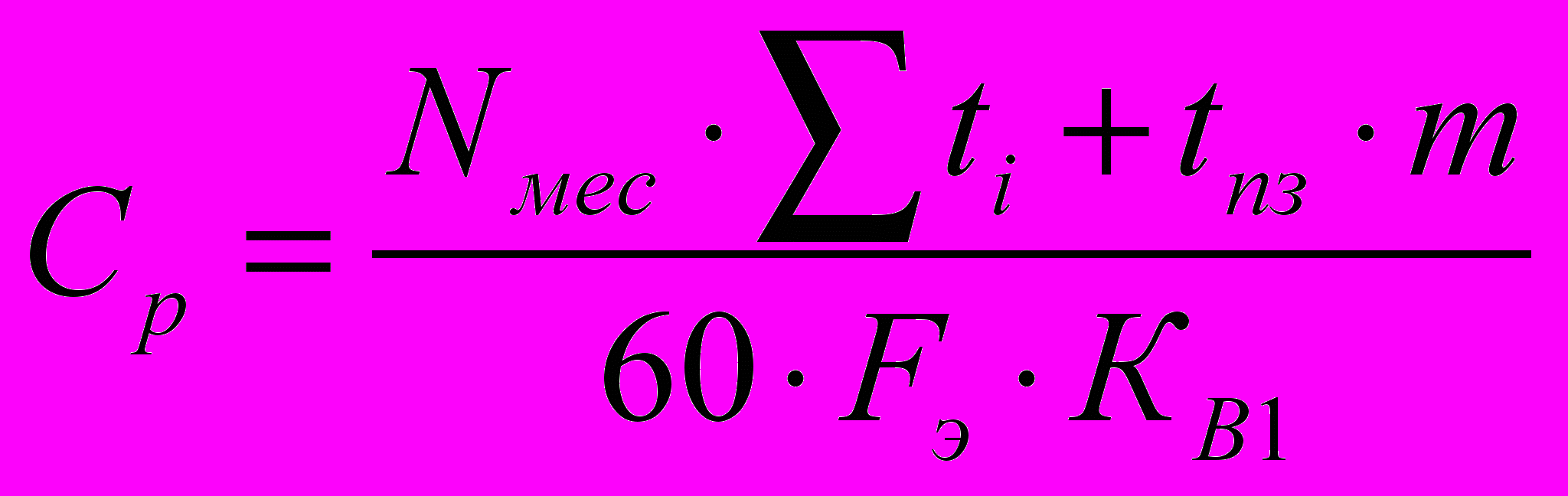
где m – число запусков партий деталей в производство;
Fэ – месячный эффективный фонд времени работы станка;
КВ1 – коэффициент выполнения норм времени и выработки.
Месячный эффективный фонд времени работы станка рассчитаем по формуле:
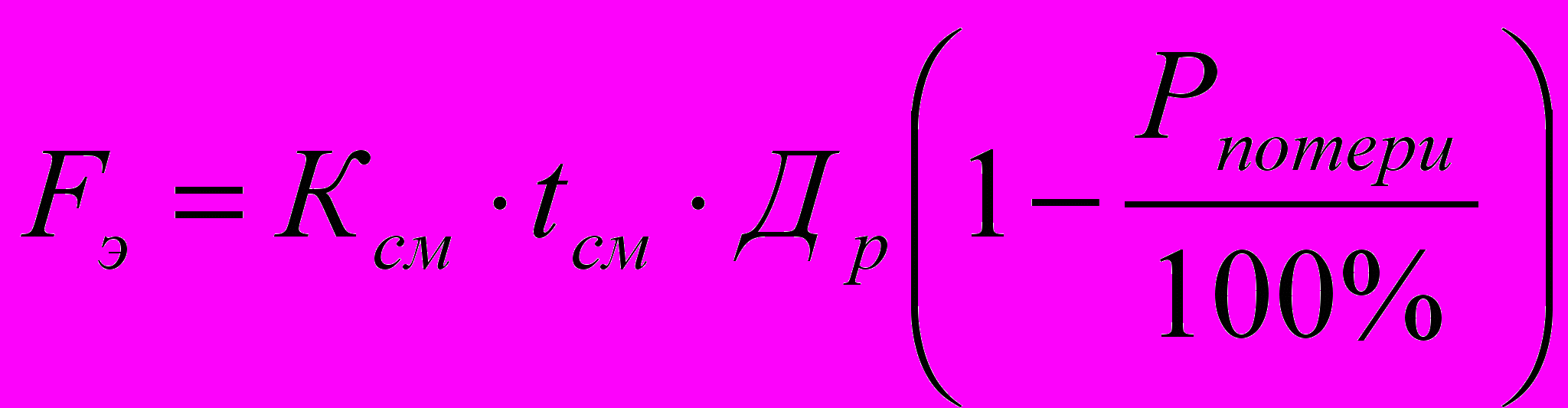
где Ксм – количество смен в графике;
tсм – продолжительность смены, ч
Др - число рабочих дней в месяц,
Р потери – допустимые потери от простоев в месяц, доли единицы

Подставляя в формулу (28) соответствующие значения по станкам, получим:






Принимаем следующие количества станков:
Ср(фр) = 4; Ср (св) =2; Ср(шл) = 1; Ср(стр) =1; Ср(зуб) =1; Ср(ток) =1.
2.2.6Шаг 6
Длительность производственного цикла обработки партии деталей определяется по формуле:

где ni - оптимальный размер партии деталей i-го наименования, шт
ti - норма штучного времени обработки деталей i-го наименования на соответствующей операции, мин
Cпр(i) - принятое число станков i-го наименования, шт
m – число операций по обработке i-го наименования,
tмо – время межоперационного пролеживания деталей, мин
(1 смена = 480 мин)
Кпар - коэффициент параллельности (Кпар = 0,6)
Подставляя численные значения в формулу (30) получим значения длительности производственных циклов обработки партий деталей всех наименований:






ЗАКЛЮЧЕНИЕ
Таким образом, мы определили, что материальный поток, как объект организации производства образует совокупность ресурсов всех наименований, находящихся на протяжении от источника получения до потребителей готовой продукции в пределах определенного временного интервала.
Процесс товародвижения образуется из множества элементарных потоков, составляющих логистические цепи. Главными звеньями цепи являются: поставщики материалов, сырья и полуфабрикатов; склады для хранения закупаемых материалов, сырья и полуфабрикатов, производственные склады и склады и службы материально-технического снабжения и сбыта; потребители готовой продукции.
Организация материальных потоков состоит в объединении отдельных звеньев и стадий товародвижения, установлении необходимых связей между ними и обеспечении взаимодействия с целью минимизации затрат по выполнению заказов при условии их своевременного и качественного исполнения.
Главной сущностной характеристикой организации материальных потоков в пространстве является логистическая структура предприятия
Логистическая структура отражает особенности организационного строения процесса товародвижения, обусловленные числом подразделений, участвующих в продвижении материалов, характером их специализации, формами взаимодействия с поставщиками сырья и потребителями продукции, а также логические взаимоотношения уровней управления предприятия и звеньев логистической цепи.
В числе факторов, оказывающих влияние на логистическую структуру предприятия, можно выделить следующие: диверсификацию производства; объем выпуска продукции; метод организации перемещения грузов; метод организации производства; тип системы управления запасами.
Также мы определили, что интегрированная система управления потоками материалов объединяет все стадии процесса товародвижения.
Исходными принципами построения такой системы выступают планирование материальных ресурсов, выравнивание выпуска продукции в процессе производства, синхронизация стадии закупки материалов, продвижения и сбыта продукции. Основной задачей системы является оптимизация организационных и управленческих решений по формированию и обеспечению функционирования материальных потоков с помощью логистических критериев.
В процессе управления материальными потоками выполняется следующий комплекс работ: прогнозирование спроса на продукцию и разработка средне- и краткосрочных прогнозов потребностей; формирование производственной программы и распределение ее по отрезкам планового периода; объемные и уточненные расчеты загрузки производственных мощностей; установление основного графика производства и плана-графика выпуска для конечного производственного звена; планирование потребностей в материалах; контролирование выполнения производственного заказа; управление сбытом, планирование и контроль затрат.
В процессе решения практического задания мы пришли к следующему выводу: на длительность производственного цикла влияют следующие факторы:
1) оптимальный размер партии деталей
2) норма штучного времени обработки детали
3) число станков
4) число операций по обработке деталей
5) время межоперационного пролёживания деталей
6) тип производства
А длительность производственного цикла влияет на всё производство в целом.
ЛИТЕРАТУРА
- Фатхутдинов Р.А. Организация производства: - М.: ИНФРА – М, 2000.
- Гаджинский А.М. Логистика. М.: ИВЦ «Маркетинг», 1998.
- Саркисов С.В. Управление логистикой: - М.: ЗАО «Бизнес-школа Интернет-Синтез», 2001.
- Туровец О.Г. Организация производства на предприятии: - Ростов-на-Дону: МарТ, 2002.
- Разу М.Л.,Воропаев В.И.,Якутин Ю.В. и др. Управление программами и проектами:17-ммодульная программа для менеджеров. Модуль 8.-М., ИНФРА-М, 2000.
- Соловьева Л.Г. Управление программами и проектами. М., ИНФРА-М,1999.
- Мескон М.Х., Альберт М., Хедоури Ф. Основы менеджмента; пер. с англ. – М., «Дело ЛТД», 1995.( гл. 12, гл.21).