Вестник Брянского государственного технического университета. 2008. №2(18)
Вид материала | Документы |
- Вестник Брянского государственного технического университета. 2008. №3(19), 114.86kb.
- Вестник Брянского государственного технического университета. 2008. №1(17), 121.05kb.
- Вестник Брянского государственного технического университета. 2008. №3(19), 138.83kb.
- Вестник Брянского государственного технического университета. 2008. №3(19), 168.61kb.
- Вестник Брянского государственного технического университета. 2008. №2(18) Энергетическое, 198.73kb.
- Вестник Брянского государственного технического университета. 2008. №1(17), 152.78kb.
- Вестник Брянского государственного технического университета. 2008. №3(19) Образование, 201.01kb.
- Вестник Брянского государственного технического университета. 2008. №1(17) Технология,, 141.51kb.
- Вестник Брянского государственного технического университета. 2008. №3(19) Энергетическое, 98.19kb.
- Вестник Брянского государственного технического университета. 2011. №4(32), 114.16kb.
Вестник Брянского государственного технического университета. 2008. № 2(18)
УДК 621.74
И.К. Кульбовский, С.В. Карелин, Д.А. Туркин
Разработка технологического процесса изготовления отливки втулки судового дизеля ДБ14 центробежным литьем
Рассмотрены особенности и возможности внедрения технологии получения отливок втулок судовых дизелей центробежным способом.
Ключевые слова: центробежное литье; отливка; втулка; чугун PVA; разработка техпроцесса.
Одним из новых технологических процессов, направленных на повышение качества втулок, является их центробежное литье. По техническим условиям к отливке предъявляются следующие требования: отсутствие каких-либо несплошностей в теле отливки; обеспечение заданных структуры (серый чугун), химического состава и механических свойств. Деталь имеет следующие габариты: высота – 2425 мм, максимальный диаметр – 985 мм. Толщина стенки отливки варьируется от 110 до 150 мм. Масса готовой детали – 2680 кг. Масса отливки без прибыли при обычной технологии – 5617 кг. Все поверхности отливки подвергаются механической обработке.
Для отливки применяется специальный чугун PVA, имеющий следующий состав: С – 3…3,3 %; Si – 0,8…1,4 %; Mn – 0,6…0,8 %; Р – не более 0,4 %, не менее 0,15 %; S – не более 0,15 %; Ti – не более 0,05 %; V – не менее 0,22 %, не более 0,28 %. Механические свойства металла по ТУ: σв – не менее 170 МПа; НВ = 180…240. Микроструктура отливки: перлитная основа с равномерно распределенными включениями графита; количество цементита в структуре не должно превышать 8-9 %, феррита – 5 %.
Поскольку деталь имеет цилиндрическую форму и несложную конфигурацию, то в качестве метода получения отливки выбрали центробежное литье в металлическую форму. Наиболее распространенный способ литья пустотелых цилиндрических отливок в металлические формы – с горизонтальной осью вращения изложницы. По этому способу отливка формируется в поле центробежных сил со свободной внутренней цилиндрической поверхностью, а внешней формообразующей поверхностью служит внутренняя поверхность вращающейся изложницы. Расплав из ковша заливают во вращающуюся форму через заливочный желоб. Расплав растекается по внутренней поверхности формы, образуя под действием поля центробежных сил пустотелый цилиндр.
Преимуществом центробежного литья является отсутствие литниковой системы и прибыли, что существенно повышает выход годного литья по сравнению с традиционным литьем в песчано-глинистые формы. Чертеж отливки втулки, полученной в существующей форме, приведен на рис. 1, а полученной центробежным литьем – на рис. 2. Еще одним преимуществом данного способа литья является отсутствие стержня, формирующего полость отливки, что приводит к экономии на стержневой смеси и затратах, связанных с его изготовлением.
Изготовление отливок центробежным способом позволяет получать плотный металл (без рыхлот и пористостей) с необходимыми по техническим требованиям механическими свойствами и микроструктурой. При этом уменьшается также объем припусков на механическую обработку втулки.
Основной оснасткой при центробежном литье является металлическая изложница (рис. 3). Размеры изложницы зависят от размеров отливки с учетом припусков на механическую обработку, а также от толщины слоя огнеупорного материала, засыпаемого в изложницу перед заливкой металла.
Внутренняя поверхность изложницы повторяет конфигурацию внешней поверхности отливки (рис. 2). Расстояние между торцевыми крышками определяется как длина детали (рис. 2) в сумме с припусками на механическую обработку. Торцевые поверхности отливки могут подвергаться отбелу. Для устранения отбела применяются футерованные крышки (рис.3). Таким образом, получается отливка с минимальными припусками на торцевых поверхностях.
![]() | ![]() |
Рис. 1. Чертеж отливки втулки ДБ14, изготовленной в песчано-глинистой форме | Рис. 2. Чертеж отливки втулки ДБ14, изготовленной способом центробежного литья |

где dдет.1 – диаметр детали; P – припуск на механическую обработку; h – толщина огнеупорного слоя.
Диаметр изложницы у буртовой части детали равен

где dдет.2 – диаметр буртовой части детали.
Толщину стенки изложницы определяли в соответствии с литературными рекомендациями. В результате получили внешний диаметр изложницы:

где H – толщина стенки изложницы.
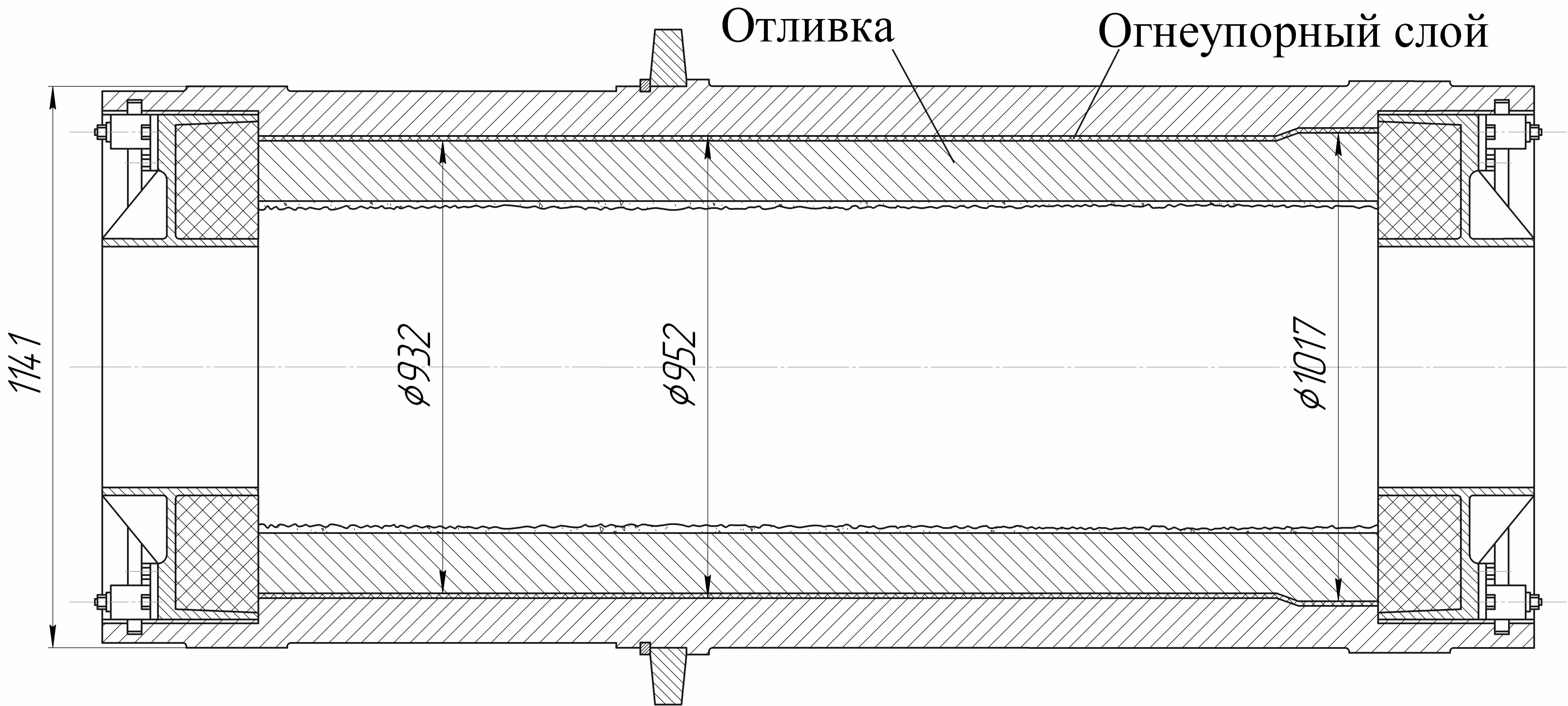
Рис. 3. Размеры рабочей поверхности изложницы для втулки ДБ14
Разработан технологический процесс отливки центробежным способом опытных заготовок втулок с толщиной стенки от 110 до 150 мм из втулочного чугуна с модифицированием и микролегированием металла флюсом во вращающейся форме. Процесс обеспечивает рафинирование металла и воздействует на его кристаллизацию.
В соответствии с разработанным технологическим процессом сконструирована, изготовлена и установлена в чугунолитейном цехе ЗАО «УК «БМЗ» опытная центробежная машина, позволяющая использовать разные изложницы для получения разных втулок.
Для отработки технологического процесса отливки заготовок центробежным способом с применением модифицирующих флюсов использовали разработанную на заводе опытную центробежную машину. Была отлита опытная партия из шести заготовок втулок судового дизеля из чугуна PVA.
Три заготовки отлиты с максимальной толщиной стенки 110 мм, три заготовки – с толщиной 150 мм. Все заготовки отливались на одной и той же центробежной машине. Температура заливки чугуна – 1320…1340 0С.
В качестве огнеупорного покрытия рабочей поверхности изложницы применялся кварцевый песок. Кристаллизация и охлаждение заготовки проходили во вращающейся со скоростью 700 об/мин изложнице в течение 1,5 ч.
Опытные заготовки отливались с использованием модифицирующего флюса, подаваемого на струю металла на заливочном желобе.
В табл. 1 приведен химический состав отлитых заготовок втулок.
Таблица 1
Химический состав чугуна опытных заготовок втулок, полученных центробежным литьем
№ п/п | № плавки | Толщина заготовок, мм | Химический состав, % | |||||||||
C | Mn | Si | P | S | Cr | Ni | V | Ti | Cu | |||
1 | 90 | 110 | 3,0 | 0,75 | 2,02 | 0,75 | 0,041 | 0,40 | 0,40 | 0,16 | 0,02 | 0,66 |
2 | 96 | 150 | 3,0 | 0,89 | 1,69 | 0,068 | 0,034 | 0,20 | 0,08 | 0,14 | 0,02 | 0,48 |
3 | PVA по ТУ | 3,0… 3,3 | 0,6… 0,9 | 0,8… 1,4 | до 0,20 | до 0,15 | - | - | 0,20… 0,30 | 0,05 | 0,3… 0,7 |
При центробежном литье массивных толстостенных цилиндрических заготовок типа втулок возможна ликвация элементов и неравномерный химический состав по сечению отливки. Направленная ускоренная кристаллизация от наружной к внутренней поверхности отливки может приводить к формированию разной структуры и механических свойств по сечению отливки.
Для исследования качества металла опытных заготовок от каждой отливки после удаления 50 мм торцевого эффекта отрезали по одному кольцу толщиной 30 мм со стороны буртовой части втулки.
На рис. 4 приведена схема вырезки образцов из сектора кольца: для механических испытаний, определения химсостава металла по толщине отливки, снятия серного отпечатка по Бауману и исследования структуры чугуна.
Для определения механических свойств чугуна из каждого темплета вырезали 3 образца в тангенциальном направлении. Результаты испытания образцов на прочность приведены в табл. 2.
Твердость образцов №1-3 замеряли от наружной поверхности к внутренней. Для плавки №90 НВ = 229, 229, 217, 217, 217, 212, 212, 207; для плавки №96 НВ = 207, 207, 207, 201, 201, 192, 192, 192.
Микроструктуру металла заготовок определяли от наружной поверхности к внутренней на образцах № 7-10 согласно ГОСТ 3443-87.
Матрица чугуна в отливке плавки №90 показана на рис. 5, а распределение графита – на рис.6.
Таблица 2
Прочность чугуна опытных заготовок втулок, полученных центробежным литьем
№ п/п | № плавки | Предел прочности, МПа | ||
Наружная поверхность заготовки | Середина заготовки | Внутренняя поверхность заготовки | ||
1 | 90 | 270 | 240 | 290 |
2 | 96 | 200 | 225 | 246 |
3 | ТУ | Не менее 170 |
![]() | ![]() |
Рис. 4. Схема вырезки образцов из центробежной заготовки втулки плавки №96: 1 – 3 – образцы для определения прочности; 4, 5 – образцы для определения послойного химсостава; 6 – образец для снятия серного отпечатка и определения послойного содержания С, S, Р; 7 - 10 – образцы для определения микроструктуры | |
Рис. 5. Матрица чугунной заготовки плавки № 90 |
Из шести отлитых опытных заготовок наиболее полно удовлетворяют требованиям ТУ две заготовки:
1) плавка №90, максимальная толщина стенки по бурту – 110 мм, отлита под модифицирующим флюсом состава: флюс АНФ-29 – 30 %, медная окалина – 15 %, ферросилиций ФС75 – 55 %;
2) плавка №96, максимальная толщина стенки по бурту – 150 мм; флюс состава: АНФ-29 – 75%, медная окалина – 25%.
Анализ химсостава проводился от наружной поверхности к внутренней.
На образцах обеих заготовок был проведен послойный химанализ (табл.3), чтобы проследить ликвацию элементов по сечению заготовки.
Таблица 3
Послойный химсостав отливок втулок судовых дизелей, полученных центробежным литьем
Проба | Содержание элементов, % | ||||||||
C | Si | Mn | S | P | Cr | Ni | V | Cu | |
90-1 | 2,70 | 2,24 | 0,74 | 0,036 | 0,069 | 0,45 | 0,52 | 0,21 | 0,71 |
90-2 | 2,75 | 2,24 | 0,73 | 0,037 | 0,074 | 0,43 | 0,59 | 0,18 | 0,67 |
90-3 | 2,99 | 1,95 | 0,78 | 0,037 | 0,066 | 0,43 | 0,52 | 0,17 | 0,59 |
90-4 | 2,92 | 2,29 | 0,72 | 0,052 | 0,066 | 0,42 | 0,51 | 0,20 | 0,62 |
96-1 | 2,83 | 1,97 | 0,94 | 0,035 | 0,060 | 0,19 | 0,50 | 0,22 | 0,54 |
96-2 | 2,76 | 1,88 | 0,85 | 0,033 | 0,054 | 0,17 | 0,39 | 0,19 | 0,51 |
96-3 | 2,75 | 1,82 | 0,91 | 0,034 | 0,088 | 0,16 | 0,36 | 0,17 | 0,50 |
96-4 | 2,89 | 1,90 | 0,89 | 0,043 | 0,074 | 0,17 | 0,32 | 0,16 | 0,47 |
96-5 | 3,03 | 1,74 | 0,91 | 0,054 | 0,078 | 0,17 | 0,36 | 0,15 | 0,50 |
96-6 | 3,36 | 1,70 | 0,91 | 0,030 | 0,074 | 0,20 | 0,35 | 0,16 | 0,47 |
![]() | ![]() |
а) | б) |
![]() | ![]() |
в) | г) |
Рис. 6. Микроструктура графита в чугуне опытной заготовки плавки №90: а – на наружной поверхности заготовки; б – на расстоянии 25 мм от наружной поверхности; в – в середине заготовки; г – на внутренней поверхности заготовки |
В микроструктуре заготовки плавки № 90 наблюдается значительное содержание феррита (до 20 %). Можно предположить, что причиной этому является повышенное содержание кремния в заготовке, который был дополнительно введен в составе модифицирующего флюса.
Анализ результатов исследований позволяет сделать следующие выводы:
1. Массивные толстостенные заготовки из чугуна перлитного класса типа отливок втулок судовых дизелей можно получать с заданными ТУ свойствами и структурой центробежным способом с применением модифицирующего флюса. При этом расход жидкого металла для получения отливки втулки может быть сокращен почти в 2 раза по сравнению с существующим способом.
2. В качестве модифицирующего флюса необходимо применять смесь, состоящую из шлакообразующего флюса АНФ-29 и медной окалины в соотношении 3:1 (вес. част.), подаваемую на жидкую поверхность. Расход такой смеси – около 0,3 кг на тонну жидкого металла.
3. Для увеличения скорости кристаллизации и охлаждения заготовки во вращающейся форме изложницу необходимо охлаждать водой.
4. Для уточнения влияния технологических режимов на качество отливок необходимо продолжить опытно-промышленные испытания новой технологии.
5. Экономический эффект от внедрения центробежной отливки втулок может составить только за счет экономии металла (без учета других факторов) около 8 тыс. руб. на 1т отливок втулок.
Материал поступил в редколлегию 14.04.08.