Методические рекомендации к лабораторным работам по курсу «Основы проектирования и конструирования» для студентов немашиностроительных специальностей: 080502 «Экономика и управление на предприятии»
Вид материала | Методические рекомендации |
- Методические указания к выполнению курсовой работы для студентов специальностей: 080502, 335.54kb.
- Методические указания по выполнению курсовых работ для студентов специальностей: 080502, 458.19kb.
- И. М. Губкина Лопатина С. Г., Шпакова З. Ф. Методические рекомендации, 174.81kb.
- Методические рекомендации по курсу «Организационные основы приема и обслуживания туристов», 745.32kb.
- Методические указания к изучению дисциплины и выполнению контрольной работы для студентов, 518.49kb.
- Методические рекомендации по выполнению курсовой работы по дисциплине «Управление инновационной, 76.2kb.
- Методические указания по выполнению курсовых работ по дисциплине Экономика отрасли, 233.2kb.
- Учебно-методический комплекс Для специальностей: 080502 Экономика и управление на предприятии, 1435.64kb.
- Методические указания по курсу «Управление инновационными процессами» для студентов, 491.1kb.
- Методические указания по дипломному проектированию на тему «организация рекламной деятельности, 266.3kb.
4.12 Контрольные вопросы
1. Перечислите основные типы резьб и области их применения.
2. Перечислите основные параметры резьбы.
3. Перечислите основные типы крепежных деталей.
4. Для чего применяются шайбы?
5. Назовите способы стопорения резьбовых соединений.
6. Как определить экспериментально момент закручивания Tк и силу затяжки Fa?
^ 5 ЛАБОРАТОРНАЯ РАБОТА № 4. ПОДШИПНИКИ КАЧЕНИЯ
(4 часа)
Выполняя лабораторную работу, студент обязан изучить конструкции и особенности основных видов подшипников качения по натурным образцам, представленным на стенде и в литературе, ознакомиться с их классификацией и условными обозначениями.
Экспериментальное определение момента сопротивления вращению в подшипнике качения в зависимости от направления приложенных сил требует от студента вдумчивого отношения к работе, развивает навыки экспериментальной работы и способствует углубленному изучению подшипников качения и условий их работы.
Лабораторная работа завершается составлением отчета с последующей его защитой.
^ 5.1 Общие сведения о подшипниках качения
Подшипники служат опорой для валов и осей. В настоящее время подшипники качения являются основными видами опор в машинах. Основные виды подшипников качения стандартизованы. Подшипники качения изготовляют диаметром от 1 до 2600 мм с диаметром шариков от 0,35 до 203 мм с массой от 0,5 г до 3,5 т.
На стенде в лаборатории представлены основные виды подшипников (для изучения подшипников их можно снимать со стенда).
Подшипники качения (см. стенд и рисунок 5.1) состоят из следующих деталей: наружного и внутреннего колец с дорожками качения, тел качения, сепараторов, разделяющих и направляющих тела качения. В некоторых видах подшипников одно или оба кольца могут отсутствовать. В них тела качения катятся непосредственно по канавкам вала или корпуса. Подшипники некоторых видов не имеют сепараторов. Подшипники других видов дополнительно снабжены защитными шайбами для защиты от загрязнения или для удержания смазки в узле, установочными кольцами и т.п.
Кольца и тела качения подшипников изготовляют в основном из стали марок ШХ15.
Основные преимущества подшипников качения по сравнению с подшипниками скольжения:
- значительно меньшие потери на трение, а следовательно, более высокий коэффициент полезного действия (до 0,995);
- момент трения при пуске в 10–20 раз меньше, чем в подшипниках скольжения;
- экономия дефицитных цветных металлов;
- меньшие габаритные размеры в осевом направлении;
- простота обслуживания и замены;
- меньший расход масла;
- малая стоимость вследствие массового производства стандартных подшипников.
Недостатки подшипников качения:
- ограниченная возможность применения при очень больших нагрузках и значительных угловых скоростях валов;
- непригодны для работы при значительных ударных и вибрационных нагрузках из-за высоких контактных напряжений и плохой способности демпфировать колебания;
- большие, чем у подшипников скольжения, габаритные размеры в радиальном направлении.
^ 5.2 Классификация, условные обозначения, основные типы и критерии
работоспособности подшипников качения
5.2.1 Классификация
Принято классифицировать подшипники качения по следующим признакам:
- по направлению воспринимаемой нагрузки:
- радиальные, радиально-упорные, упорные;
- по форме тел качения: шариковые, роликовые с цилиндрическими, коническими и бочкообразными роликами;
- по числу рядов тел качения – однорядные и многорядные;
- по способности компенсировать перекос валов: несамоустанавливающиеся, самоустанавливающиеся (сферические).
В зависимости от нагрузочной способности и размеров при одном и том же диаметре расточки внутреннего кольца подшипники подразделяются на серии: сверхлегкая, особолегкая, легкая, средняя, тяжелая.
Основные классы точности подшипников в порядке повышения точности:
- 0, 6, 5, 4, 2, Т – для шариковых радиальных и радиально упорных, а также роликовых радиальных;
- 0, 6, 5, 4, 2 – для упорных и упорно-радиальных;
- 0, 6Х, 6, 5, 4, 2 – для роликовых конических.
Предусмотрены два дополнительных класса точности (8 и 7) более низкие, чем класс точности 0 (нормальный).
^ 5.2.2 Условные обозначения
Номера подшипников качения – условные обозначения, состоящие из ряда цифр и букв, содержат информацию о внутреннем диаметре внутреннего кольца, серии, типе и конструктивных особенностях подшипников.
Последние две цифры номера подшипника характеризуют внутренний диаметр внутреннего кольца: ...00 (d=10 мм); ...01 (d=12 мм); ...02 (d=15 мм); ...03 (d=17 мм). Начиная от ...4 (d=20 мм) и кончая ...99 (d=495 мм), для получения диаметра внутреннего кольца подшипника две последние цифры его условного обозначения следует умножить на 5.
Третья справа цифра условного обозначения указывает серию подшипника. Четвертая цифра справа обозначает тип подшипника.
^ 5.2.3 Основные типы
Радиальные однорядные шарикоподшипники (смотри подшипники на стенде и рисунок 5.1) способны воспринимать радиальную и осевую нагрузки. Они получили наибольшее распространение в машиностроении. При одинаковых размерах с другими подшипниками имеют наименьшие потери на трение и допускают наибольшую частоту вращения. Возможен перекос колец до 10'. Среди подшипников качения радиальные однорядные имеют самую низкую стоимость.
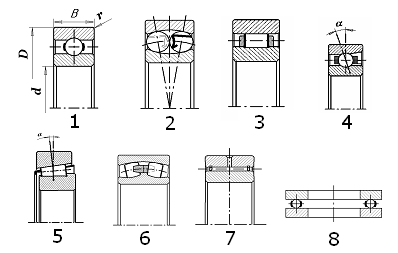
1– радиальный шариковый подшипник; 2 – самоустанавливающийся шариковый
подшипник; 3 – радиальный роликовый подшипник; 4 – радиально-упорный
шарикоподшипник; 5 – радиально-упорный роликовый конический подшипник;
6 – самоустанавливающийся роликовый подшипник; 7 – игольчатый подшипник;
8 – упорный подшипник
Рисунок 5.1 – Типы подшипников качения
Радиальные двухрядные сферические шарикоподшипники предназначены для восприятия радиальной нагрузки. Благодаря сферической форме дорожки наружного кольца допускают значительный перекос колец (до 2…3) и могут воспринимать небольшие осевые нагрузки.
Радиальные роликоподшипники с короткими и длинными цилиндрическими роликами воспринимают только радиальную нагрузку (если имеются борта на кольцах, то могут воспринимать незначительную осевую нагрузку).
Нагрузочная способность роликоподшипников приблизительно на 70 % больше, чем у шариковых, однако, они не допускают перекоса колец, так как ролики начинают работать кромками, и подшипники быстро выходят из строя. Эти подшипники допускают осевое взаимное смещение колец; их применяют для установки коротких жестких валов, а также в качестве "плавающих" опор.
Радиально-упорные шарикоподшипники применяют в подшипниковых узлах, воспринимающих одновременно радиальные и осевые нагрузки.
Конические роликовые подшипники также предназначены для восприятия радиальной и осевой нагрузок. По сравнению с радиально-упорными шариковыми подшипниками обладают большей грузоподъемностью. Недостатком этих подшипников является большая чувствительность к несоосности и относительному перекосу колец.
Упорные шарико- и роликоподшипники предназначены для восприятия только осевой нагрузки. Эти подшипники могут быть выполнены самоустанавливающимися. Применяют их при средней и малой скоростях вращения во избежание заклинивания тел качения от действия центробежных сил.
В машиностроении применяют и другие типы как шариковых, так и роликовых
подшипников, устройство и характеристика которых приводятся в специальной литературе.
^ 5.2.4 Критерии работоспособности подшипников качения
Основные виды разрушения деталей подшипников качения:
- усталостное разрушение (выкрашивание) рабочих поверхностей тел качения и беговых дорожек колец вследствие циклического контактного нагружения – это основной вид разрушения подшипников наблюдается после длительной работы и сопровождается повышением шума и вибрации;
- пластические деформации в виде вмятин, лунок на дорожках качения, наблюдаемые у тяжело нагруженных тихоходных подшипников при действии больших нагрузок без вращения или ударных нагрузок;
- абразивное изнашивание в результате недостаточной защиты от абразивных частиц (пыли и грязи), является основной причиной выхода из строя подшипников автомобилей, тракторов, строительных машин и т.п., применение уплотнений подшипниковых узлов уменьшает износ.
5.3 Определение момента сопротивления вращению в подшипниках качения
5.3.1 Устройство и работа прибора ДПА
Для определения момента сопротивления вращению в подшипниках качения в лабораторной работе использован прибор ДП1-IA. Принципы и методы измерения на приборе следующие: в каждом учебном опыте производят определение момента сопротивления вращению одного радиального шарикоподшипника при вращающемся внутреннем и неподвижном наружном кольце.
Мерой момента служит степень деформации плоской пружины, на конце которой укреплена шторка, перекрывающая световой поток, направленный на фотодиод.
Электрический ток в цепи фотодиода, измеряемый тарированным микроамперметром, в первом приближении пропорционален деформации плоской пружины и, следовательно, моменту сопротивления в шариковом подшипнике. Скорость вращения внутреннего кольца шарикоподшипника определяют с помощью связанного с ним тахогенератора и включаемого в цепь микроамперметра. Значение на шкале микроамперметра задается тумблером "момент" - "скорость". Нагрузка на подшипник (осевая и радиальная) создается сменными грузами.
Соотношение между осевой и радиальной нагрузкой определяется наклоном оси вращения внутреннего кольца, задается поворотом вертикальной плиты в заданное положение.
Прибор ДПА состоит из привода, шпинделя с рабочим валиком для испытуемых шарикоподшипников и измерительных устройств.
Механические узлы прибора установлены на вертикальной плите, которая, в свою очередь, смонтирована на литой стойке, закрепленной на основании прибора.
Органы управления, микроамперметр и другие элементы электрической схемы расположены на передней панели.
Привод прибора осуществляется электродвигателем постоянного тока типа СЛ 261. Электродвигатель заключен в корпус и соединен с вертикальной плитой посредством четырех амортизаторов, уменьшающих передачу вибрации от электродвигателя испытуемым подшипникам.
На выходном валу электродвигателя закреплен ведущий шкив, который посредством круглого ремня передает движение на ведомый шкив, закрепленный на рабочем валу прибора. Корпус электродвигателя имеет направляющие, которые позволяют регулировать натяжение ремня ременной передачи с помощью регулировочного винта.
Рабочий вал прибора установлен на двух шариковых подшипниках в корпусе, закрепленном на вертикальной плите. Верхняя часть рабочего вала выполнена с внутренним отверстием, оканчивающимся резьбой, в которую ввинчивается валик узла испытуемого подшипника. Вес стаканов испытуемых узлов одинаковый и равен 1,265 Н. Центры тяжести грузов и стаканов в собранном виде совпадают с центром тяжести подшипника. При установке каждого из прилагаемых грузов на стакан общий вес груза и стакана (нагрузка) соответственно равен 4,905; 9,81 и 19,62 Н. Груз закрепляют на стакане винтом с рифленой головкой, а поводок, укрепленный на грузе, устанавливают в седловину плоской пружины.
При вращении внутреннего кольца подшипника, приводимого в движение рабочим валом, наружное кольцо подшипника, вместе с насаженными на него стаканом и грузом, силами трения увлекаются в сторону вращения внутреннего кольца. При этом поводок груза надавливает на верхний конец плоской пружины и изгибает ее соответственно величине момента сопротивления в подшипнике.
Тахогенератор механически связан с рабочим валом прибора и служит для определения угловой скорости внутреннего кольца испытуемого подшипника.
Плита, с установленными на ней механизмами и измерительным устройством, может поворачиваться относительно своей горизонтальной оси в пределах 90°, чем достигается изменение соотношения радиальной и осевой нагрузок на подшипник. Поворот
плиты осуществляют рукояткой с пружинным фиксатором. На задней стороне стойки
укреплен сектор с пазами, позволяющими фиксировать положение вертикальной плиты
через 15.
5.3.2 Подготовка прибора к работе
После изучения и тщательного осмотра прибора ДПА следует приступить к его опробованию и тарировке его измерительных устройств.
Для измерения угловой скорости испытуемого подшипника использован микроамперметр.
Тарировку микроамперметра для измерения угловой скорости рабочего вала (внутреннего кольца испытуемого подшипника) производят при отладке прибора ДПА или его ремонте. Результаты тарировки приведены в таблице 5.1.
Таблица 5.1 – Результаты тарировки микроамперметра для измерения
угловой скорости рабочего вала
Показания микроамперметра, мкА | Угловая скорость рабочего вала, рад/с |
10 | 71,2 |
20 | 104,7 |
30 | 141,4 |
40 | 172,9 |
50 | 203,15 |
60 | 232,5 |
70 | 259,7 |
80 | 288,0 |
95 | 319,4 |
Тарировку микроамперметра для измерения момента сопротивления следует выполнять следующим образом.
Включить прибор в электрическую сеть, переключить микроамперметр для измерения момента; убедиться, что стрелка микроамперметра стоит на нуле при переключении тумблера диапазонов измерения в первое и второе положение. (Если это условие не выполняется, следует обратиться к преподавателю).
Отвернуть винт крепления измерительного устройства к вертикальной плите. Установить измерительное устройство в горизонтальное положение, повернув его относительно верхнего шарнира, и закрепить его в этом положении винтом.
Под действием собственного веса плоская пружина прогнется; шторка, связанная с ней, приоткроет отверстие на пути светового потока, и стрелка микроамперметра отклонится от нулевого положения на 5–10 делений. (Если это условие не выполняется, следует обратиться к преподавателю). Показание микроамперметра, обусловленное собственным весом пружины, следует записать и считать его условным «0» отсчета. Положив имеющуюся в комплекте прибора гирьку весом 0,00981Н на конец плоской пружины, определить изменения a1 показания микроамперметра относительно «0» отсчета, и результаты занести в таблицу 5.2. Увеличивая вес гирьки в 2, 3, 4 раза, определить показания микроамперметра a2, a3, a4. Определить расстояние от оси вала вращения подшипников до середины пружины L в миллиметрах. Рекомендуется для определения угловой скорости и момента построить тарировочные графики на миллиметровой бумаге.
Таблица 5.2 – Результаты тарировки микроамперметра для измерения момента
Наименование | Номер опыта | ||||
1 | 2 | 3 | 4 | 5 | |
Нагрузка на пружину, Н | | | | | |
Показания микроамперметра, мкА | | | | | |
Цена деления, ![]() | | | | | |
Момент относительно оси вращения, ![]() | | | | | |
5.3.3 Выполнение эксперимента
Установить испытуемый подшипниковый узел (по указанию преподавателя) на рабочий вал прибора и укрепить на нем груз (по указанию преподавателя). Соединить поводок груза с пружиной.
После включения вилки прибора в сеть включить тумблер "сеть", установить регулятор скорости вращения в среднее положение и включить двигатель.
Включить микроамперметр для измерения угловой скорости; изменяя скорость вращения рабочего вала (внутреннего кольца подшипника) поворотом регулятора скорости, убедиться в исправной работе прибора. Установить среднее значение угловой скорости.
Переключив микроамперметр для измерения момента сопротивления (положение тумблера "момент"), проверить работу прибора на одном диапазоне измерений при всех режимах работы.
Установить угол наклона оси вращения внутреннего кольца подшипника (по указанию преподавателя).
При постоянной скорости вращения вала последовательно изменять угол наклона оси вращения относительно вертикали: 0°, 30, 45, 60, 90 и регистрировать показания микроамперметра: a1, a2, a3, a4, a5.
Для измерения угловой скорости внутреннего кольца подшипника следует включить тумблеры "сеть", "двигатель", переключить микроамперметр для измерения скорости
(положение тумблера – "скорость"), регулятором скорости задать среднюю скорость вращения внутреннего кольца подшипника, показания прибора занести в протокол эксперимента.
Результаты измерений и расчетов представить в виде таблицы 5.3. По результатам опыта построить графики на миллиметровой бумаге.
Таблица 5.3 – Результаты испытания подшипника при различных углах наклона
оси вращения
Наименование | Номер опыта | |||
1 | 2 | 3 | | |
Вес груза и стакана, Н | | | | |
Угол наклона оси вращения внутреннего кольца подшипника к горизонту, град | | | | |
Осевая нагрузка на подшипник, Н | | | | |
Радиальная нагрузка R на подшипник, Н | | | | |
Показания микроамперметра при измерении скорости вращения, мкА | | | | |
Угловая скорость внутреннего кольца подшипника, рад/с | | | | |
Показания микроамперметра при измерении момента (диапазон 1), мкА | | | | |
Момент сопротивления вращению в подшипнике, Н·мм | | | | |
5.3.4 Составление отчета
Отчет о лабораторной работе должен быть написан на листах формата А4, сшит и снабжен обложкой. Отчет должен содержать:
- титульный лист;
- цели и задачи лабораторной работы;
- краткое описание прибора ДПА с приведением схем и рисунков;
- описание подготовки прибора к работе, его тарировки;
- описание выполнения исследования с приведением его результатов в виде таблиц и графиков;
- анализ результатов исследования, выводы и их обоснование.
5.3.5 Контрольные вопросы
1. Подшипники качения, их достоинства и недостатки.
2. Основные типы подшипников качения и их характеристика.
3. Условное обозначение подшипников качения.
4. Конструкции подшипниковых узлов.
Литература
1. Орлов, П.И. Основы конструирования: справочно-методическое пособие в 2-х книгах / П.И. Орлов [и др.]. – М.: Машиностроение, 1998. – 745 с.
2. Дунаев, П.Ф. Конструирование узлов и деталей машин / П.Ф. Дунаев, О.П. Леликов. – М.: Высшая школа, 1998. – 416 с.
3. Анурьев, В.И. Справочник конструктора-машиностроителя: в 3-х томах /
В.И. Анурьев [и др.]. – М.: Машиностроение, 2001. – 864 с.
4. Артемьев, М.М. Патентоведение: учебник для вузов / М.М. Артемьев [и др.]. – М: Машиностроение, 1994. – 352 с.
5. Иванов, М.Н. Детали машин / М.Н. Иванов. – 4-е изд. – М.: Высшая школа, 1984.
6. Решетов, Д.Н. Детали машин / Д.Н. Решетов. – 4-е изд. / М.: Машиностроение, 1989.
7. Кудрявцев, В.Н. Курсовое проектирование деталей машин / В.Н. Кудрявцев. – Л.: Машиностроение, 1984. – 400 с.
8. Детали машин. Атлас конструкций / под редакцией Д.Н. Решетова. – М.: Машиностроение, 1979.
9. Перель, П.Я. Подшипники качения и обслуживание опор: справочник / П.Я. Перель, А.А. Филатов. – М.: Машиностроение, 1992.
10. Чернавский, С.А. Курсовое проектирование деталей машин / С.А. Чернавский, К.Н. Боков. – М.: Машиностроение, 1999. – 559 с.
11. СТП 12700-02.
12. Башев, С.М. Детали машин в примерах и задачах / С.М. Башев [и др.]. – Минск: Высшая школа, 1990. – 593 с.
13. Кудрявцев, В.Н. Детали машин / В.Н. Кудрявцев. – 4-е изд. – М.: Машиностроение, 1989.
14. Чернавский, С.А. Курсовое проектирование деталей машин: учебное пособие для учащихся машиностроительных специальностей / С.А. Чернавский, К.Н. Боков. – М.: Машиностроение, 1999.
15. Иванов, М.Н. Детали машин. Курсовое проектирование деталей машин /
М.Н. Иванов. – М.: Машиностроение, 1980.
16. Бейзельман, Р.Д. Подшипники качения: справочник / Р.Д. Бейзельман. – М.: Машиностроение, 1975.
17. Перель, Л.Я. Подшипники качения: справочник / Л.Я. Перель. – М.: Машиностроение, 1993.
Учебное издание
Дунин Максим Сергеевич
Жеранин Александр Вадимович
Климонова Надежда Михайловна
^ ОСНОВЫ ПРОЕКТИРОВАНИЯ И КОНСТРУИРОВАНИЯ
Методические рекомендации к лабораторным работам по курсу
«Основы проектирования и конструирования»
для студентов немашиностроительных специальностей:
080502 «Экономика и управление на предприятии»,
260204 «Технология бродильных производств и виноделия»
Редактор Идт Л.И.
Корректор Малыгина И.В.
Технический редактор Малыгина Ю.Н.
Подписано в печать 11.12.08. Формат 6084 1/8
Усл. п. л. 2,15. Уч.-изд. л. 2,31
Печать – ризография, множительно-копировальный
аппарат «RISO TR -1510»
Тираж 75 экз. Заказ 2008-96
Издательство Алтайского государственного
технического университета
656038, г. Барнаул, пр-т Ленина, 46
Оригинал-макет подготовлен ИИО БТИ АлтГТУ
Отпечатано в ИИО БТИ АлтГТУ
659305, г. Бийск, ул. Трофимова, 27
М.С. Дунин, А.В. Жеранин, Н.М. Климонова
^ ОСНОВЫ ПРОЕКТИРОВАНИЯ И КОНСТРУИРОВАНИЯ
Методические рекомендации к лабораторным работам
по курсу «Основы проектирования и конструирования»
для студентов немашиностроительных специальностей:
080502 «Экономика и управление на предприятии»,
260204 «Технология бродильных производств и виноделия»
Бийск
Издательство Алтайского государственного технического университета
им. И.И. Ползунова
2
008
1 в противном случае передача электромеханическая, гидравличеcкая, пневматичеc- кая;
2 в червячной передаче оси червяка и червячного колеса скрещиваются;
3 так называемое реечное зацепление