Курс лекций дисциплины «Компьютерные технологии и сапр» для студентов специальностей 120500, 120507, 120700 очной, очно-заочной и заочной форм обучения
Вид материала | Курс лекций |
- Курс лекций дисциплины «Компьютерные технологии и сапр» для студентов специальностей, 559.5kb.
- Методические указания по написанию курсовой работы для студентов очной, заочной и очно-заочной, 318.34kb.
- Учебное пособие для студентов очной, очно-заочной и заочной форм обучения (дистанционное, 929.04kb.
- Реферат как форма самостоятельной работы студента: методическое пособие по выполнению, 325.87kb.
- Курс лекций для студентов заочного факультета самара, 1339.16kb.
- Методические рекомендации по выполнению практических работ по курсу «Экология» для, 474.71kb.
- Методические указания к курсовой работе по дисциплине «Стратегический менеджмент» для, 76.01kb.
- Методические рекомендации для студентов очно-заочной и заочной форм обучения Тематика, 268.03kb.
- Методические указания к курсовой работе по дисциплине «Экономика отрасли» для студентов, 197.88kb.
- Методические указания по выполнению рефератов и контрольных работ по курсу «экология», 187.76kb.
^ Цикл 5-координатной чистовой обработки. Цикл предназначен для чистовой обработки поверхности детали, в том числе с уклонами (рис. 1.68). Инструмент ориентируется по нормали к поверхности, с возможным отклонением в плоскости по направлению обработки и в перпендикулярной плоскости на заданные углы (фронтальное и поперечное отклонения).
Параметры цикла:
• поверхность, несколько патчей поверхности или сборка патчей поверхности;
• линия из точек контакта;
• точность обработки - максимальное расстояние между обработанной и теоретической поверхностью детали;
• припуск на последующую обработку. Если значение параметра положительное, то материал будет оставаться на обрабатываемой детали, если значение параметра отрицательное, то фрезерование будет производиться ниже указанной поверхности;
• начальная и конечная точка обработки;
• режим фронтального отклонения инструмента от нормали к поверхности или от касательной;
• режим изменения угла поперечного отклонения инструмента;
• режим подвода и отвода инструмента, расстояние/угол, на которое система подводит инструмент;
• режим контроля столкновений и зарезов;
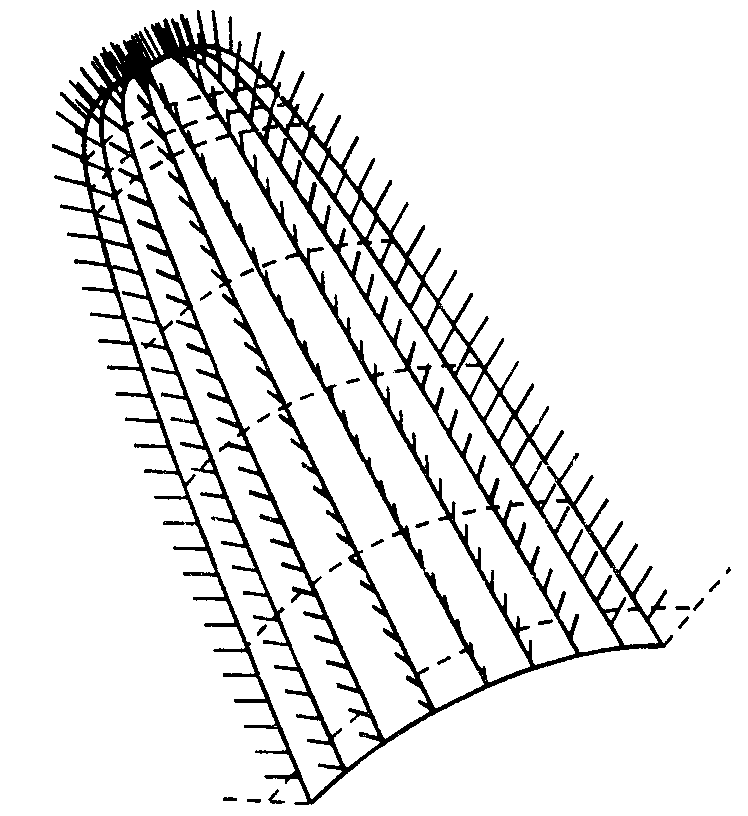
Рис. 1.68. Чистовая обработка поверхности
• режим отклонения инструмента для избежания столкновений:
фронтальное, поперечное отклонение.
Пример визуализации сеанса работы при создании процесса обработки детали показан на рис. 13 на вклейке.
^ 5.5. Процесс механической обработки
Цель этого процесса - получение конечной детали из ее заготовки. Компонентами процесса являются последовательности, операции и циклы.
Далее используются следующие понятия:
• процесс - совокупность последовательностей операций;
• последовательность - совокупность операций, выполняемых данным станком с данной оснасткой (без переустановки детали);
• операция - совокупность циклов механической обработки, выполняемых с данным инструментом. Она включает все необходимые параметры, требуемые для выполнения циклов. Операция создается и инициализируется при загрузке инструмента;
• цикл - элементарный тип механической обработки (контурная, по параллельным плоскостям и т.п.).
Каждый станочный цикл определяет траекторию заданного инструмента, являющуюся траекторией его режущей кромки. Некоторые станочные циклы могут быть выполнены только на определенных станках. Например, фрезерование неплоской поверхности совмещением оси фрезы с нормалью к этой поверхности не может выполняться на 3-координатном станке. Некоторые станки имеют дополнительные технические характеристики, такие, как охлаждение режущего инструмента. Система способна учитывать эти различия в каждом отдельном цикле. Список технических характеристик данного оборудования записан в используемом контроллере.
Станок с ЧПУ оборудован контроллером (стойкой), который управляет различными функциями станка (перемещением инструмента и детали, охлаждением и т.п.). В подсистеме контроллер представляет собой набор функциональных возможностей данного станка. Контроллер распознает только инструкции, заданные на его языке. Поэтому каждый раз, когда создается файл машинных кодов, подсистема переводит каждую последовательность процесса обработки на язык выбранного контроллера.
База данных содержит следующие контроллеры: CLF_MILL (файл формата CL), APT_MILL (файл формата APT) и PCH_MILL (файл формата DIRECT). При необходимости этот список может быть расширен.
Процесс механообработки является упорядоченным объектом древовидной структуры, который связывает последовательности, операции и циклы. Пример процесса фрезерной обработки представлен ниже:
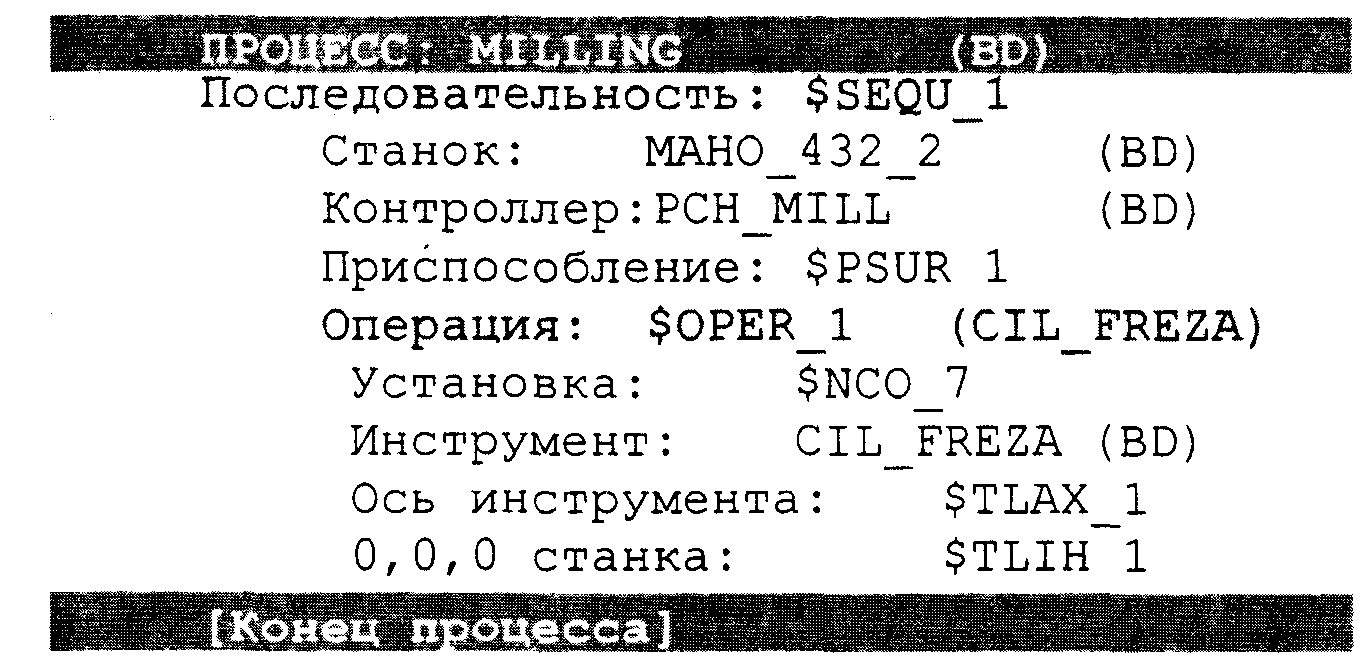
В подсистемах проектирования технологической подготовки производства обычно не определяется жесткий порядок создания технологического процесса. Тем не менее во многих случаях создавать процесс следует определенным образом.
1. Вызвать из базы данных модели элементов среды.
2. Вызвать из базы данных модели конечной детали и заготовки.
3. Создать первую последовательность процесса обработки:
создать первую операцию в последовательности:
- задать исходное положение станка и типы циклов;
- вычислить первый и остальные циклы операции;
- проверить, промоделировать и декодировать первую операцию;
- отредактировать операцию, если требуется;
- создать другие операции в последовательности, если необходимо.
4. Создать другие последовательности процесса обработки, если необходимо.
В результате расчета созданного процесса будут сформированы траектории движения инструмента. Технолог может оперативно управлять ходом вычислений, определяя, какую часть процесса, последовательности или операции необходимо выполнить. Расчет можно продолжить с последней успешно вычисленной точки траектории, соединив ее со следующим рассчитанным элементом.
Стандартные операции контроля корректности сделанных изменений система выполняет при пересчете элементов. В случае обнаружения некорректности выдается соответствующее сообщение. Кроме того, пользователь может определить свои операции проверки, например выполнение частичного пересчета элементов, после каждого внесенного изменения и отображения новой траектории инструмента. Расчет прерывается в случае обнаружения ошибки в траектории цикла.
Контроль качества спроектированных процессов всех видов механообработки выполняется одними и теми же методами. На всех этапах проектирования технологического процесса технолог имеет возможность визуально проверить настройку оборудования, а во время имитации процесса резания - увидеть формирование эквидистант инструмента (рис. 14 на вклейке).
С помощью специальных программ NC Formater, NC Simul выполняется анимация всего процесса обработки изделия с визуализацией удаляемого материала и зарезов (см. рис. 15 на вклейке).
В тех случаях, когда технолог не удовлетворен результатами спроектированного процесса, он может выполнить редактирование как параметров циклов, так и любых других составляющих процесса. Для этих целей существуют следующие функции редактирования.
1. Добавление элементов в структуру процесса.
2. Замена элемента текущего процесса.
3. Обмен местами двух элементов процесса.
4. Удаление элемента процесса.
5. Перемещение элемента процесса.
6. Копирование элементов операции.
7. Изменение параметров элемента процесса.
8. Удаление траекторий инструментов.
9. Отображение геометрических параметров элемента.
10. Отображение выбранного элемента.
11. Поиск элемента процесса.
12. Назначение имени элементу процесса.
Внесенные изменения начинают действовать после пересчета элементов процесса.
Выходная информация процесса. Она может быть представлена в виде:
• управляющей программы на проблемно-ориентированном языке,
• управляющей программы в коде конкретного станка с ЧПУ,
• проектно-технологической документации в требуемом формате.
В зависимости от контроллера, связанного с каждой последовательностью процесса, эти файлы могут иметь различные имена:
• DIRECT - файл, именуемый NAME.AXX, создается для каждой последовательности. NAME - имя процесса, а XX - индекс последовательности (начальное значение 01). Фрагмент файла приведен ниже:
%
N0004GOOG21 G80G90G40
N0008(.Motions.in.millimeters.)
N0012(.Feedrate.speed.m.millimeters/mmute.)
N0016M06Tl(Tool#l)
N0020($$TOOL/T1D5.R.5E2.F.5AO.BO.L60.)
N0024G54
N0028G17
N0032GOOX34.708Y160.705
N0036M03
N0040M08G43H01Z35.
N0044X103.708
N0048S50
N0052G01Z11.F300
N0056GOOX101.036Y103.642
• CLFILE - файл, именуемый NAME.CLX, создается для каждой последовательности. NAME - имя процесса, а Х - индекс последовательности (начальное значение 1);
• APT - файл, именуемый NAME.APX, создается для каждой последовательности. NAME - имя процесса, а Х - индекс последовательности (начальное значение 1). Фрагмент файла выглядит следующим образом:
UNIT/MM
PARTNO/SHTUC
MACHIN/243BMF2*
^ SEQNO /NEXT
DISPLY/ON
PPRINT/END MILL
DISPLY/OFF
CUTTER/ 5.000, 0.500, 2.000, 0.500,$
0.000, 0.000, 60.000
LOADTL/1, LENGTH, 0.000, ADJUST, 1
SPINDL/ 0.000, CCLW
COOLNT/ON
ORIGIN/ -77.183, -90.528, -5.000
^ TLAXIS/ 0.000, 0.000, 1.000 PREFUN/ 54.000
POSIT/ 0.000, 0.000, 0.000, 1.000,$
0.000, 0.000, 0.000, 0.000,$
1.000
RAPID
Проектно-технологическая документация может быть оформлена в виде чертежей, текстовой информации или рисунков. Документы создаются автоматически по указанному шаблону и могут при необходимости редактироваться вручную. Существуют следующие типы документов: список инструментов, карты цикла, карты инструмента, карты последовательности.
^ 5.6. Проектирование технологии токарной обработки
Специализированная подсистема «Токарная обработка» является одной из подсистем комплекса EUCLID3, с помощью которой выполняется подготовка управляющих программ для токарных станков с ЧПУ [8].
Проектирование технологии токарной обработки базируется на тех же подходах, что и проектирование фрезерной обработки. У этих подсистем общая база данных и одни и те же этапы проектирования, но содержательная часть этих этапов у них разная. Чтобы не дублировать изложенную в подразделе «Проектирование технологии фрезерной обработки» (см. с.84) методику построения процесса, в этом подразделе остановимся только на характерных особенностях токарной обработки.
Рассмотрим основные понятия, используемые в проектировании технологического процесса токарной обработки.
^ Удаляемый материал. Это часть заготовки, удаляемая при обработке установленным инструментом в заданном цикле токарной обработки. Для таких циклов, как сверление и контурное точение, удаляемым материалом могут быть:
• незамкнутая линия, соответствующая траектории режущего инструмента;
• призма (например, для обработки выемок, используя точение по оси С);
• отверстие.
Кроме точения по оси С, удаляемый материал должен быть представлен плоскими гранями в плоскости обработки, определяемой осями Х и Z. Для многопроходной обточки по контуру удаляемый материал определяется контуром, который состоит из обрабатываемого контура заготовки и обрабатываемого контура детали. Если существуют объемные модели заготовки и детали, то удаляемый материал выделяется из контуров их образующих (рис. 1.69).
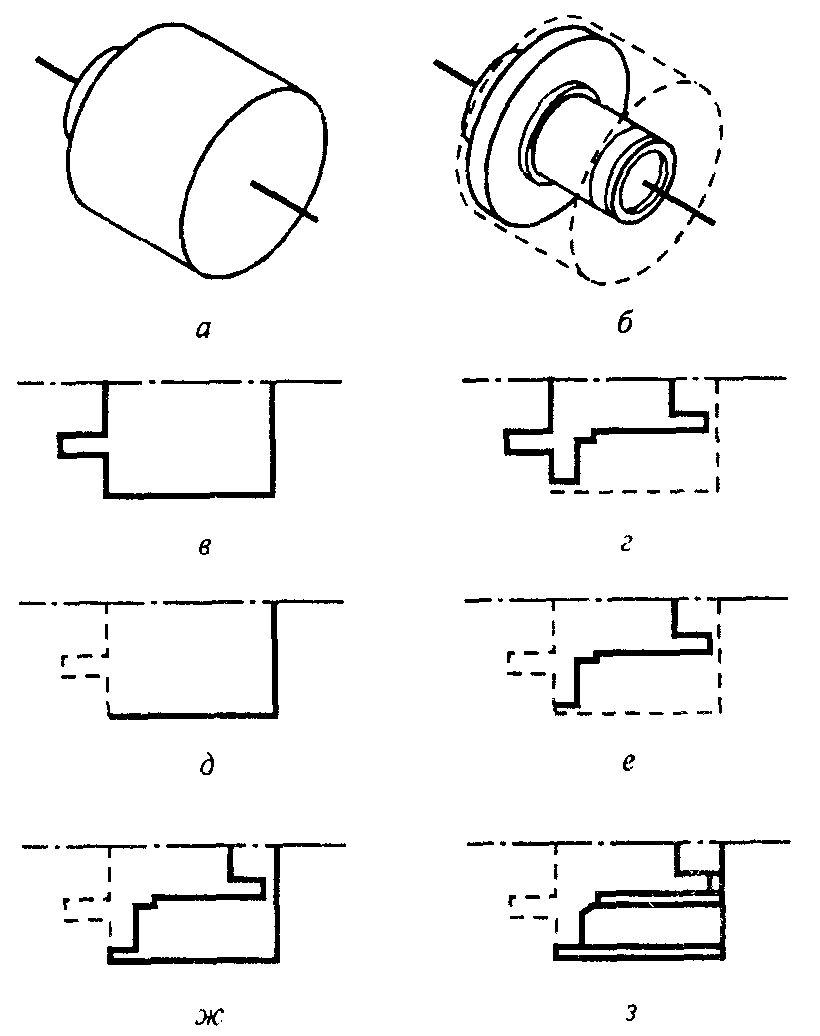
Рис. 1.69. Определение удаляемого материала по контурам заготовки и детали:
а - заготовка; б - деталь; в и г- образующие соответственно заготовки и детали, д и е - обрабатываемые контуры соответственно заготовки и детали; ж - контур удаляемого материала; з - вариант разбиения удаляемого материала; - . - - ось Z станка
^ Система базирования элементов оборудования. Системы базирования отвечают за взаимное расположение всех элементов оборудования: токарного станка, инструмента, инструментальной оснастки, технологической оснастки (приспособления) и детали в процессе обработки. Система базирования элемента создается описанным во фрезерной обработке методом, определяющим положение начала координат элемента и направления его осей X, Y, Z.
^ Среда токарной обработки. Эта среда включает:
• описание имеющихся на предприятии токарных станков с ЧПУ;
• геометрические модели используемых инструментов;
• геометрические модели элементов инструментальной оснастки (резцедержатели, переходные патроны);
• модели элементов технологической оснастки токарного станка;
• модель заготовки;
• модель конечной детали.
Необходимо также указать сведения о материале, из которого будет изготовляться конечная деталь.
Базу данных технологического оборудования, имеющегося на предприятии, следует создать до начала работы с подсистемой технологической подготовки производства. Если геометрические модели станка и инструмента не были построены заранее, в процессе создания макетов оборудования автоматически будет создано точное их представление, достаточное для контроля обработки. Геометрические модели оригинальных элементов оборудования предприятия повышают качество технологического процесса и контроля управляющих программ.
Макеты токарных станков должны быть обязательно протестированы после создания, а сборка макетов и моделей всего оборудования необходима для анимации процесса токарной обработки.
Описание станка в базе данных содержит следующую информацию:
• название токарного станка;
• описание архитектуры;
• технологические параметры;
• геометрические параметры;
• описание кинематической схемы.
^ Архитектура токарного станка. Описание архитектуры станка определяет направления перемещения детали и инструмента станка (X, Z, С), а также положения упоров (рис. 1.70).
Описание токарного станка можно вызвать из базы данных ранее созданных станков.
^ Технологические параметры токарною станка. Существуют следующие технологические характеристики токарных станков:
• время на смену инструмента (с);
• максимальное число оборотов шпинделя в минуту (об/мин);
• максимальная подача (перемещение заготовки) в текущих единицах (мм или дюймы) в минуту (мм/мин);
• максимальная скорость перемещения вдоль осей X, Z в текущих единицах (мм или дюймы) в минуту (мм/мин);
• максимальное число оборотов в минуту вокруг оси С (об/мин):
• возможность подачи охлаждающей жидкости.
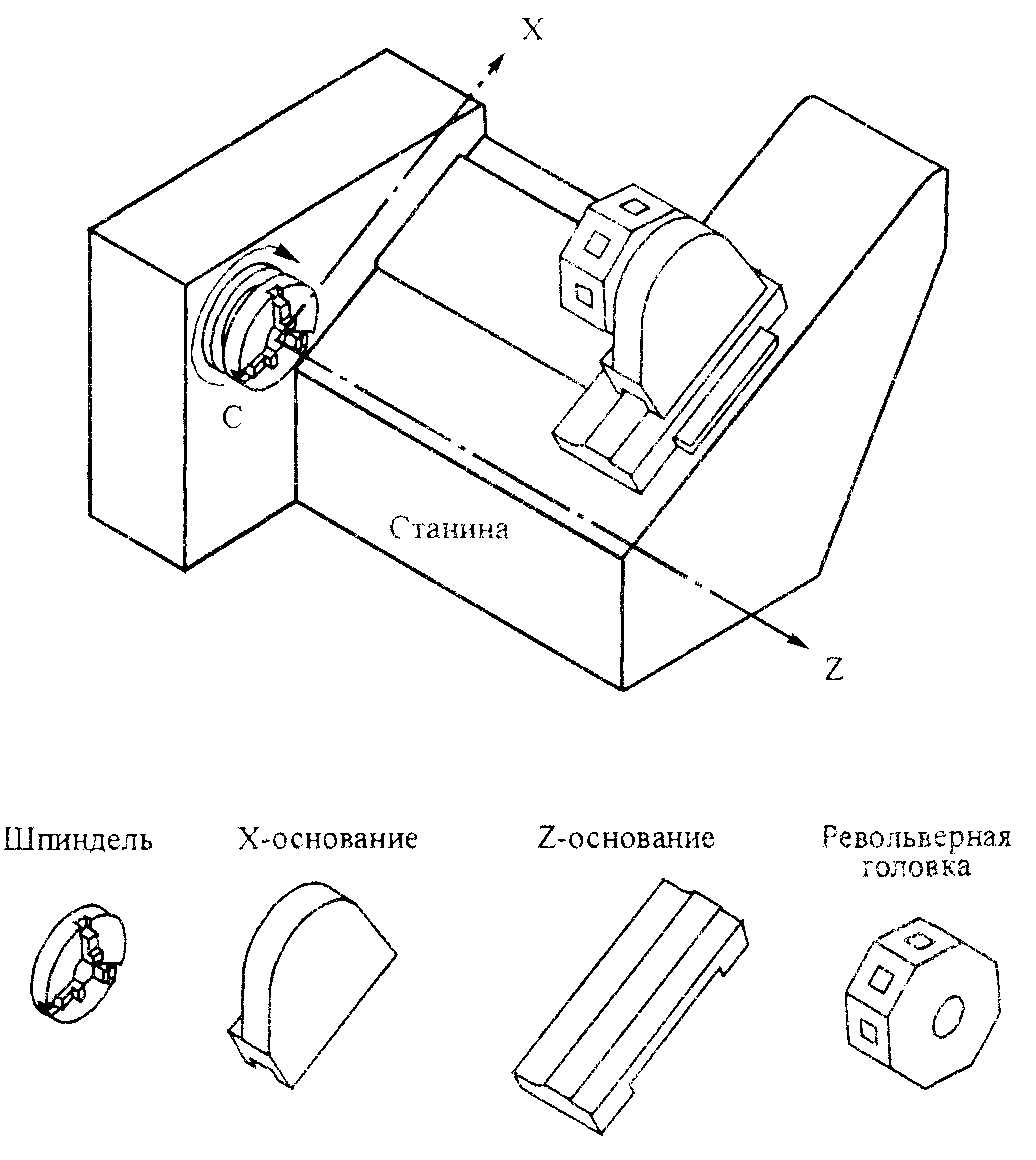
Рис. 1.70. Схема токарного станка
Технолог может описать тип станка и кинематические параметры револьверной головки дополнительными параметрами, такими, как количество устанавливаемых в револьверную головку инструментов, угол поворота револьверной головки при смене инструмента и др.
^ Геометрические параметры станка. Геометрические параметры используются для условного или геометрического представления токарного станка. Если геометрические элементы для представления различных частей станка не созданы заранее и не присутствуют в базе данных, то система создаст схематичное представление нового станка. Для этого необходимо определить неподвижную часть (станину) и подвижные части станка:
• шпиндель;
• часть станка (стол), перемещающуюся вдоль оси Z (оси вращения шпинделя):
• часть станка (стол), перемещающуюся вдоль оси X.
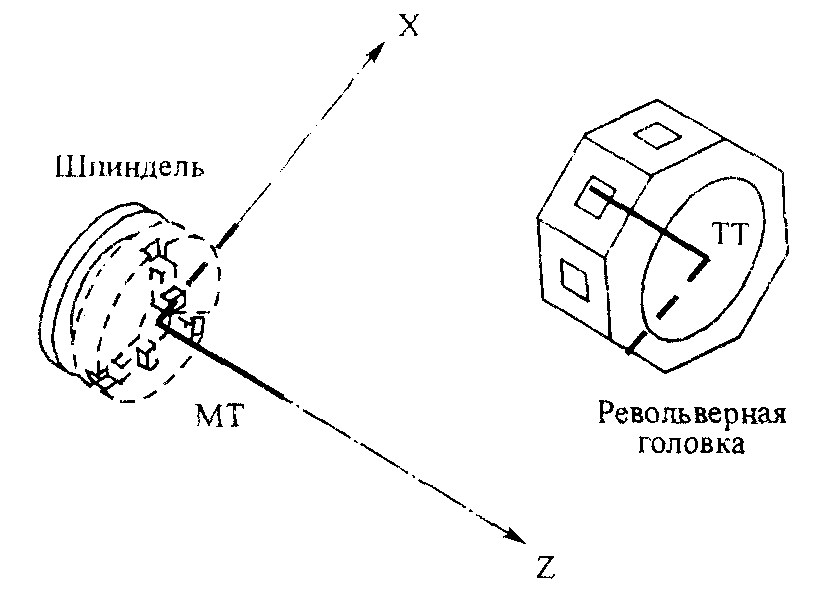
Рис. 1.71. Системы базирования токарного станка
Кинематическая схема токарного станка. Кинематика токарного станка определяет положение плоскости обработки, упоров. револьверной головки и возможность С-координатной обработки Для создания кинематической схемы станка необходимо иметь ранее построенные и сохраненные в базе данных все элементы оборудования. Напомним, что они обеспечат более точный контроль
Кинематическая схема является результатом нескольких операций определения:
• токарного станка;
• элементов инструментальной оснастки;
• инструмента;
• элементов технологической оснастки.
При определении токарного станка задаются положение и ориентация двух элементов: револьверной головки и шпинделя станка (рис. 1.71).
Система базирования станка включает:
• систему базирования шпинделя (МТ) (рис 1.72), определяющую:
- начало координат станка,
- ось вращения шпинделя - направление оси Z станка,
- направление оси Х станка,
- плоскость XOZ станка - плоскость обработки;
• систему базирования револьверной головки (ТТ) (рис. 1.73), определяющую ее положение и направление оси ее вращения Z Направление вращения револьверной головки по ходу часовой стрелки определяется, глядя в направлении вектора оси Z системы базирования головки;
• системы базирования инструмента (ТТ1—ТТ8) (см. рис. 1.73).
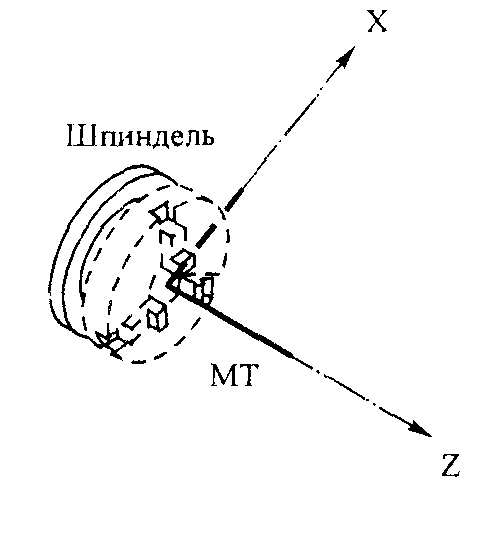
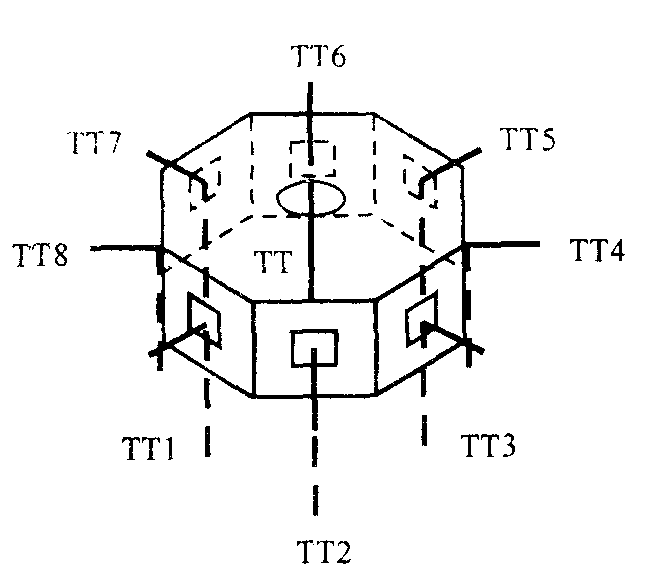
Рис. 1.72. Система базирования шпинделя токарного станка
Рис. 1.73. Системы базирования револьверной головки и инструмента
Чтобы обеспечить безопасную работу токарного станка, вводятся предельно допустимые положения одной или нескольких револьверных головок. Эти значения задаются в виде координат ближнего и дальнего упоров на оси шпинделя (упоры по Z) и координат ближнего и дальнего упоров на оси Х (упоры по X) (рис. 1.74). Для этого на револьверной головке можно создать дополнительные системы базирования.
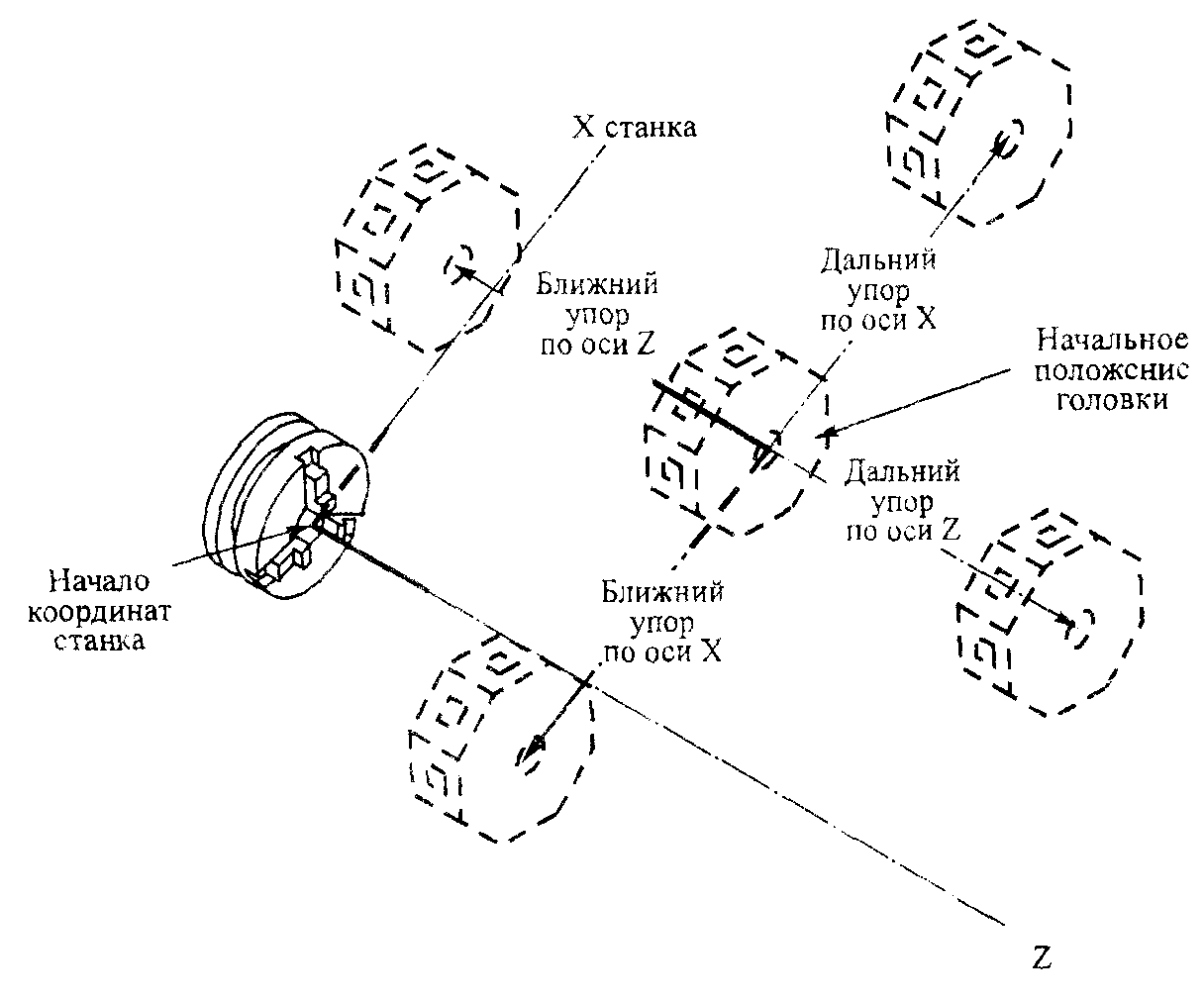
Рис. 1.74. Схема определения положения упоров
Для проверки заданных параметров и настроек в завершении процедуры создания макета токарного станка необходимо выполнить его тестирование. Оно заключается в имитации движений частей станка в плоскости обработки, вокруг и вдоль заданных осей станка, а также в положениях дальних и ближних упоров.
Определение инструментальной оснастки состоит в указании системы базирования револьверной головки и инструмента на геометрических моделях элементов оснастки. Комбинированная инструментальная оснастка может состоять из нескольких элементов (переходников, удлинителей и т.п.). В этом случае следует создать все необходимые системы базирования этих элементов, которые обеспечат их сборку на станке. Пример комбинированной инструментальной оснастки приведен на рис. 1.75.
Переходной элемент 2 имеет две системы базирования:
• револьверной головки (TUR2);
• элемента 1 (TOOL2).
Промежуточный элемент 1 (удлинитель), в свою очередь, тоже имеет две системы базирования:
• элемента 2 (TUR1);
• инструмента (TOOL1).
При сборке данной комбинированной оснастки системы базирования ее элементов TOOL2 и TUR1 будут совмещены. В единой кинематической схеме токарного станка система базирования элемента инструментальной оснастки TUR2 будет совмещаться с соответствующей системой базирования инструмента ТТ1—ТТ8, а TOOL 1 будет совмещаться с системой базирования державки инструмента.
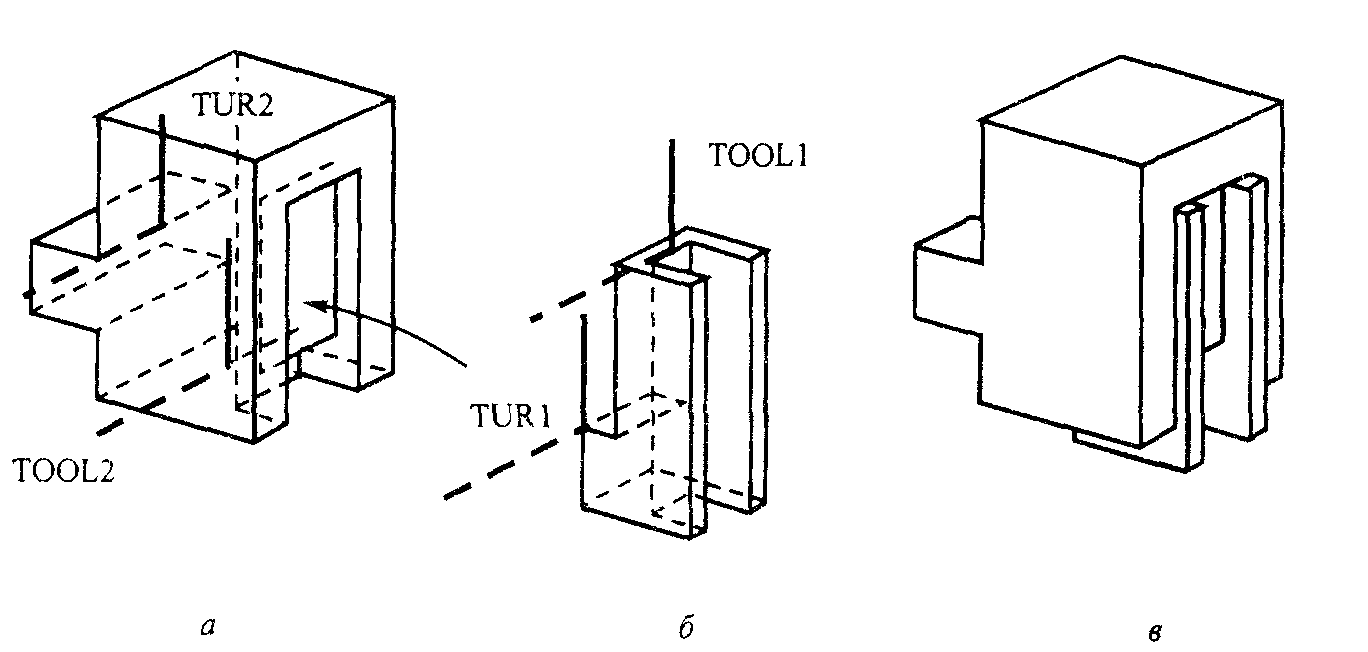
Рис. 1.75. Определение комбинированной инструментальной оснастки и ее сборка:
а - элемент 2; б - элемент 1; в - инструментальная оснастка в сборе
Определение инструмента является продолжением описания кинематической схемы токарного станка и содержит следующую информацию:
• геометрическое описание, условное или реалистичное представление инструмента, являющееся моделью реального токарного резца;
• систему базирования державки, с помощью которой резец фиксируется в инструментальной оснастке;
• систему базирования резца, которая определяет положение режущей кромки резца относительно обрабатываемой заготовки;
• параметры соответствующего типа резца.
Если геометрическая модель оригинального токарного резца не создана заранее в подсистеме твердотельного моделирования и отсутствует в базе данных предприятия, то условное представление типового резца будет создано автоматически (вызвано из стандартной базы данных). При проектировании процесса обработки можно установить инструмент непосредственно в револьверную головку токарного станка либо предварительно создать сборку инструмента с одним или более элементом инструментальной оснастки и затем установить эту сборку в револьверную головку токарного станка.
На рис. 1.76 приведен пример токарного резца и его систем базирования.
Система базирования державки НТ при сборке с элементом 1 инструментальной оснастки совместится с системой базирования TOOL1 (рис. 1.77). Система базирования резца позволит точно рассчитать траекторию движения резца в процессе обработки.
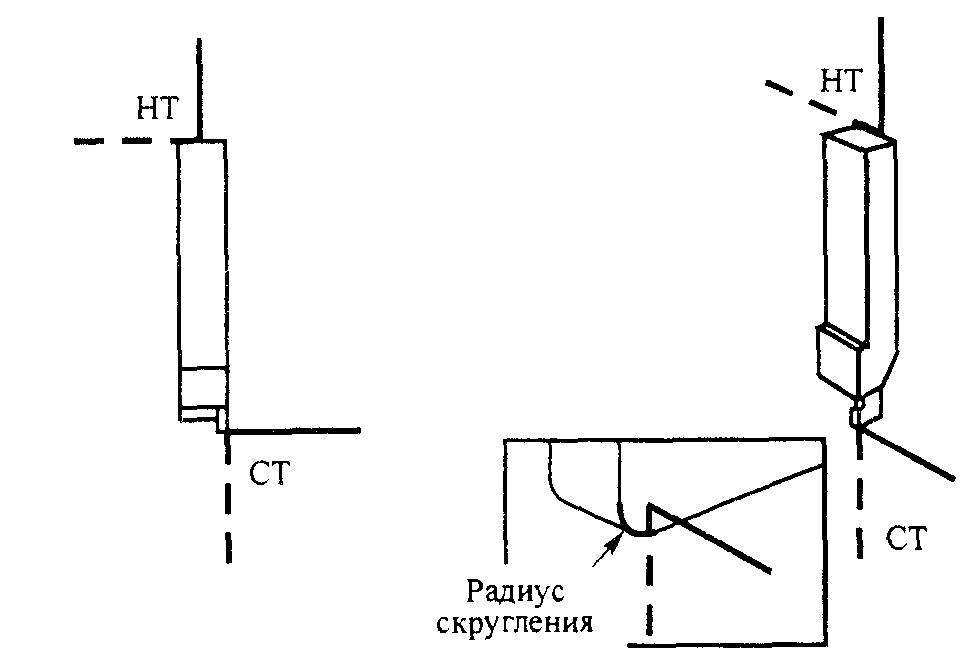
Рис. 1.76. Системы базирования токарного резца:
СТ - система базирования резца; НТ - система базирования державки инструмента
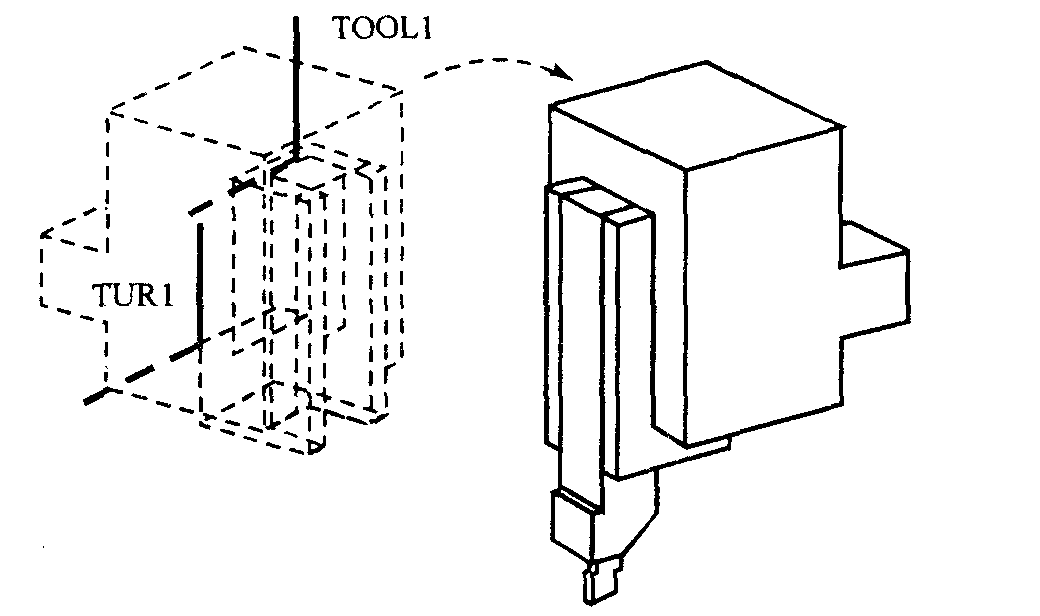
Рис. 1.77. Сборка резца с комбинированной инструментальной оснасткой
База данных токарного инструмента содержит следующие типы резцов, нестандартного и фасонного инструмента: метчик, развертка, сверло, резец резьбовой, резец гравировальный, резец проходной с продольным и поперечным перемещениями.
Для каждого типа инструмента определяются его параметры:
• форма режущей кромки (рис. 1.78), определяемая незамкнутой линией (ломаной и/или дугой);
• глубина резания в одном или двух направлениях, определяемая отрезком или ломаной из двух отрезков (границы обработаю (рис. 1.79);
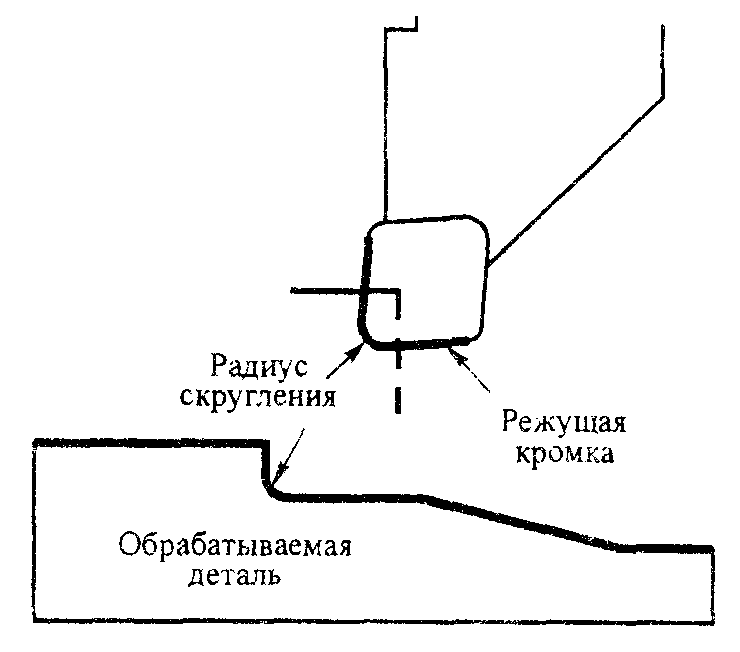
Рис. 1.78. Параметры рабочей части резца:
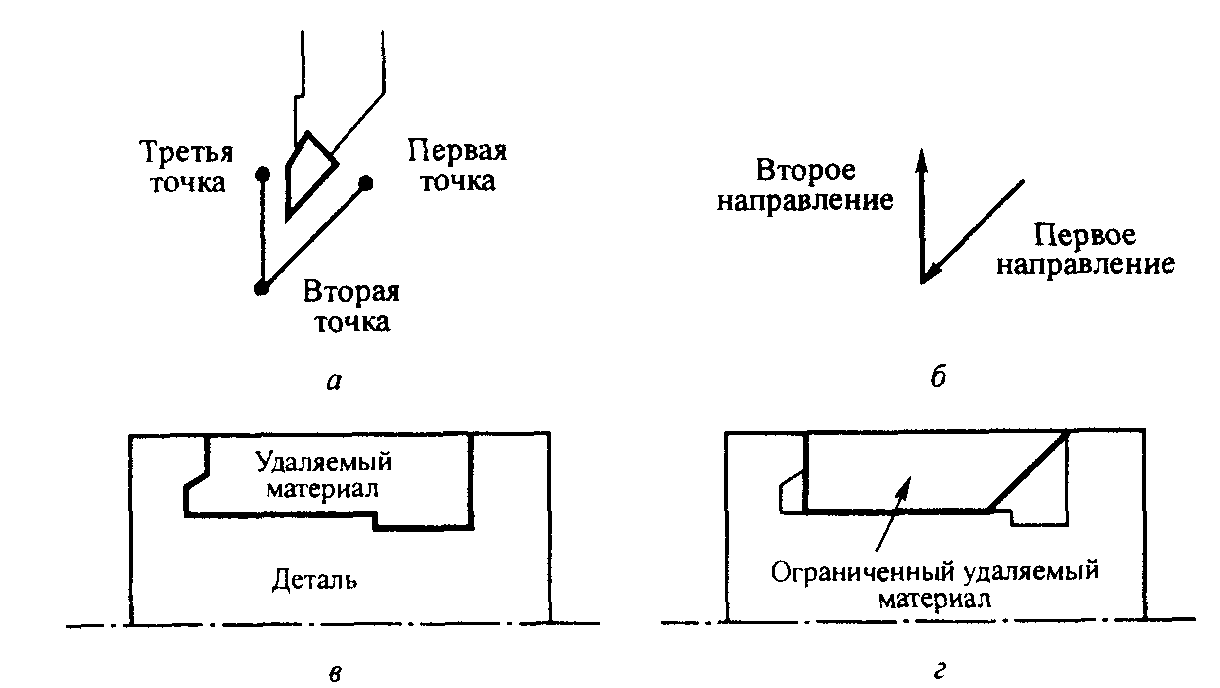
Рис. 1.79. Определение границ обработки тремя точками:
а - указание трех точек; б - полученные два направления обработки;
в - исходный удаляемый материал; г - получаемый после обработки удаляемый материал
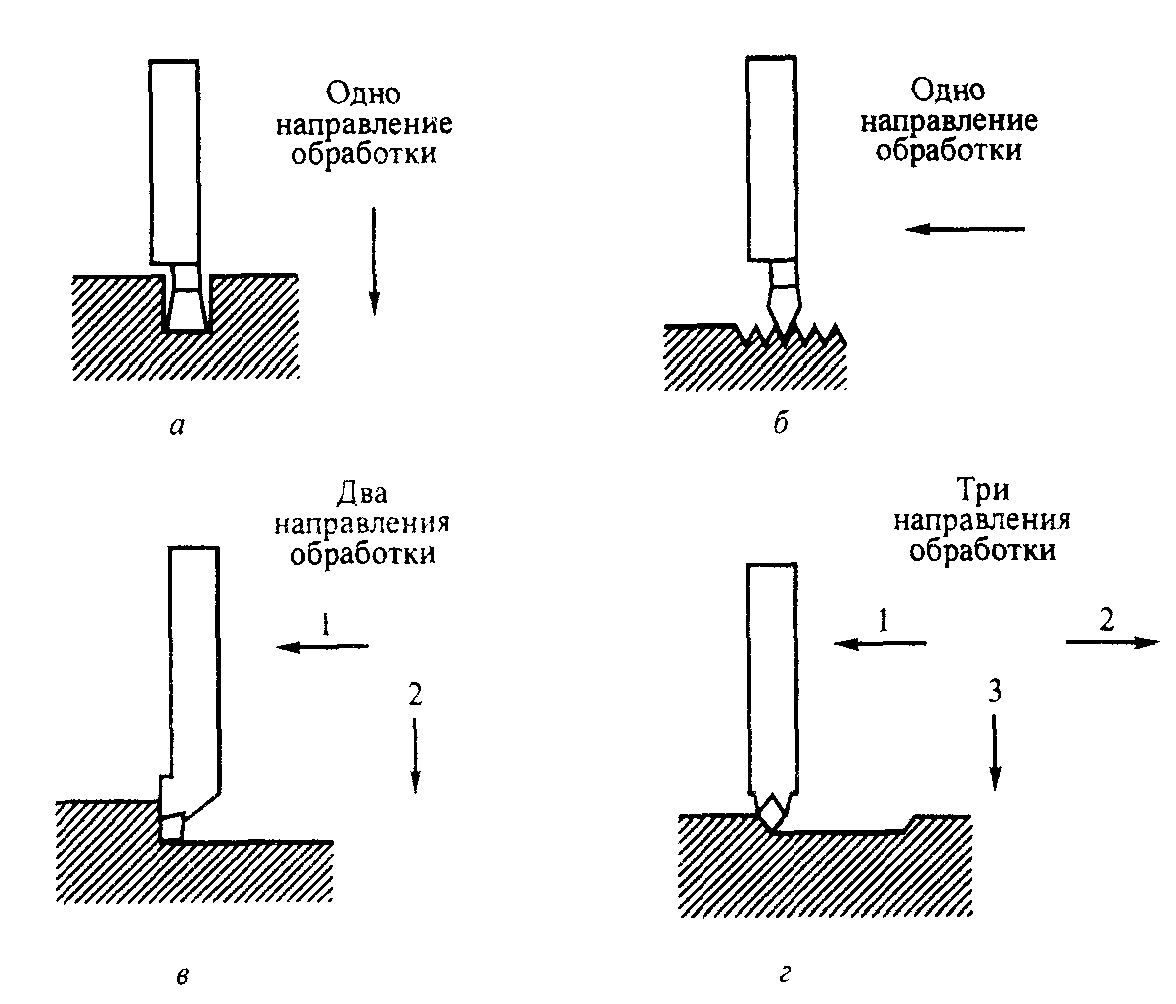
Рис. 1.80. Определение направлений обработки:
гравировальным (а), резьбовым (б), проходным (в) резцами и резцом для контурного точения (г)
• направление обработки, определяемое двумя точками, или первое направление в случае нескольких направлений обработки:
• второе (возможное) и третье (возможное) направления обработки, определяемое двумя точками (рис. 1.80);
• максимальная глубина обработки.
Свойства материала используются вместе с параметрами инструмента для автоматического расчета режима резания в процессе обработки. При обработке резцами, так же, как и при фрезерной обработке, можно документировать все свойства резцов и других инструментов в цепочках ассоциированных объектов «инструмент (тип и параметры) - материал - режим обработки», а затем выбирать их из базы данных по определенным признакам.
Определение элементов технологической оснастки заключается в назначении каждому элементу технологической оснастки его систем базирования. Элементы установки обрабатываемой заготовки детали (крепежного приспособления) закрепляют заготовку в шпинделе токарного станка. С каждым элементом установки заготовки связаны две системы базирования: шпинделя, которая определяет положение приспособления, и заготовки детали, которая указывает положение заготовки относительно приспособления. Определение всех элементов технологической оснастки на станке позволяет точно проконтролировать возможные столкновения при имитации процесса токарной обработки.
Технологическая оснастка, так же, как и инструментальная, может быть сложной и состоять из нескольких крепежных элементов, каждому из которых необходимо создать пару систем базирования. Пример такой комбинированной технологической оснастки приведен на рис. 1.81. Системы базирования элементов технологической оснастки рассмотрим ниже.
Система базирования крепежного приспособления 1 включает в себя системы базирования:
• шпинделя (ST1), которая при сборке должна совместиться с системой базирования станка (МТ);
• крепежного приспособления 2 (РТ1). Система базирования крепежного приспособления 2 включает в себя системы базирования:
• крепежного приспособления 1 (ST2),
• заготовки детали (РТ2).
При сборке данной комбинированной технологической оснастки системы базирования ее крепежных приспособлений 2 и 1 (РТ1 и ST2) будут совмещены. В единой кинематической схеме токарного станка система базирования крепежного приспособления 1 (ST1) будет совмещаться с системой базирования шпинделя станка МТ, а РТ2 будет совмещаться с системой базирования заготовки детали.
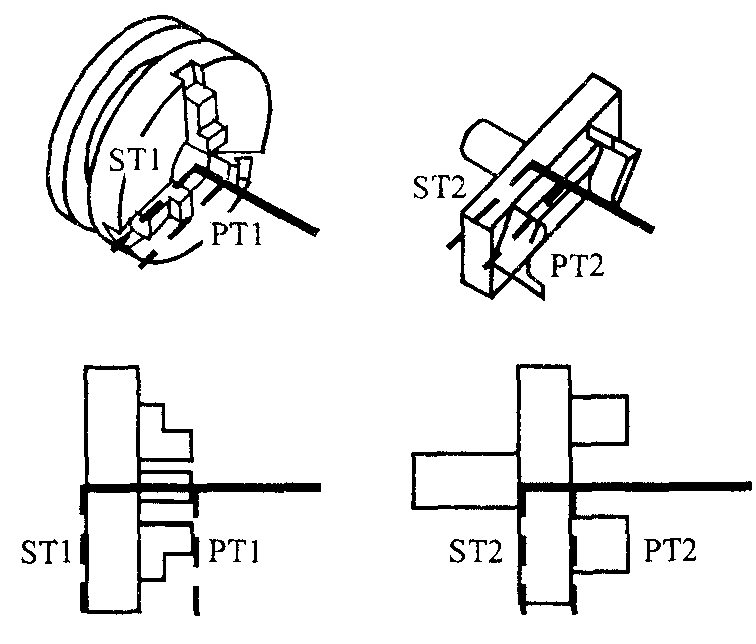
Рис. 1.81. Системы базирования элементов технологической оснастки
Определение всех составляющих кинематической схемы позволяет собрать воедино все составляющие оборудования:
• монтировать инструмент с элементами инструментальной оснастки;
• автоматически закреплять элементы оснастки инструмента в револьверной головке или на суппорте в начале последовательности операций;
• автоматически устанавливать смонтированный инструмент в головку или на суппорт в начале операции;
• автоматически устанавливать станок в исходную позицию (первую точку) обработки детали в начале цикла.
Кинематическая схема оборудования (все ее системы базирования) образует кинематическую цепочку процесса обработки.
^ 5.7. Циклы токарной обработки
Циклы токарной обработки резцом: продольно-поперечная обточка, обточка с проходами в заданном направлении, по ограниченному контуру, многопроходная обточка по контуру, продольно-поперечная обточка с проходом по контуру, обточка с проходами в заданном направлении и с проходом по контуру.
Циклы С-координатной обработки: обработка каналов, обработка в одном или двух направлениях, обработка зигзагом, по спирали, по контуру, сверление, сверление с периодическим отводом сверла, сверление с выводом сверла и удалением стружки, оконтуривание, обработка по проекции контура, обработка призмы, обработка поверхностей вращения, обработка карманов и пазов по спирали, обработка поверхности по спирали, обработка поверхности по спирали вне/внутри контура, обработка поверхности зигзагом, черновая 2,5-координатная обработка, черновая 2,5-коорди-натная обработка по спирали, обработка центровых отверстий, зен-кование, цекование, зенкование и цекование с отводом инструмента. зенкование и цекование глухих отверстий с отводом инструмента. развертывание отверстий, нарезание резьбы метчиком, снятие фаски на отверстии, обработка отверстий «от точки к точке».
В качестве примера рассмотрим цикл токарной обточки заготовки резцом по контуру (рис. 1.82).
Параметры цикла:
• удаляемый материал. Контур удаляемого материала должен лежать в плоскости обработки;
• область выборки удаляемого материала: вне его контура;
• обработать слева или справа от контура удаляемого материала, если смотреть в направлении оси Y станка;
• направление подвода инструмента задается двумя точками;
• направление отвода инструмента задается двумя точками;
• безопасное расстояние медленного подвода инструмента;
• безопасное расстояние отвода инструмента;
• тип коррекции траектории движения инструмента:
- траектория центра с коррекцией;
- траектория центра без коррекции;
- траектория контура инструмента с коррекцией;
- траектория контура инструмента без коррекции;
• переключатель типа обработки изломов контура (вершин острых углов) (рис. 1.83): по окружности (а), без скругленил (б);
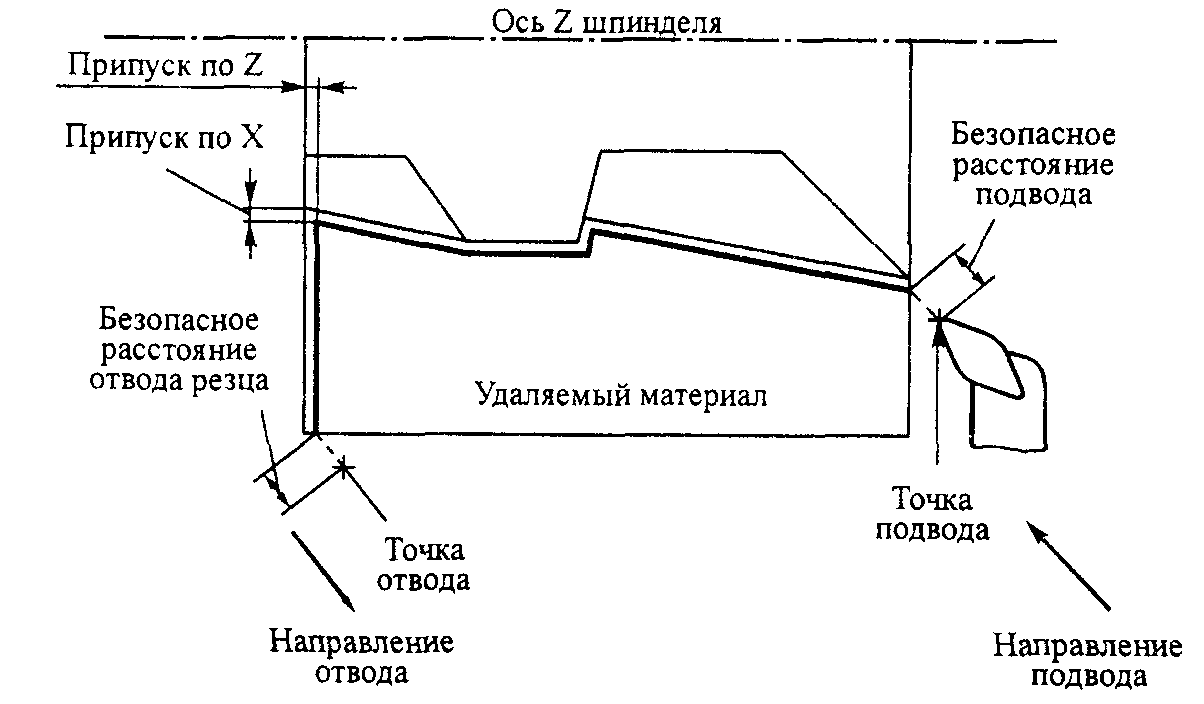
Рис. 1.82. Токарная обточка по контуру
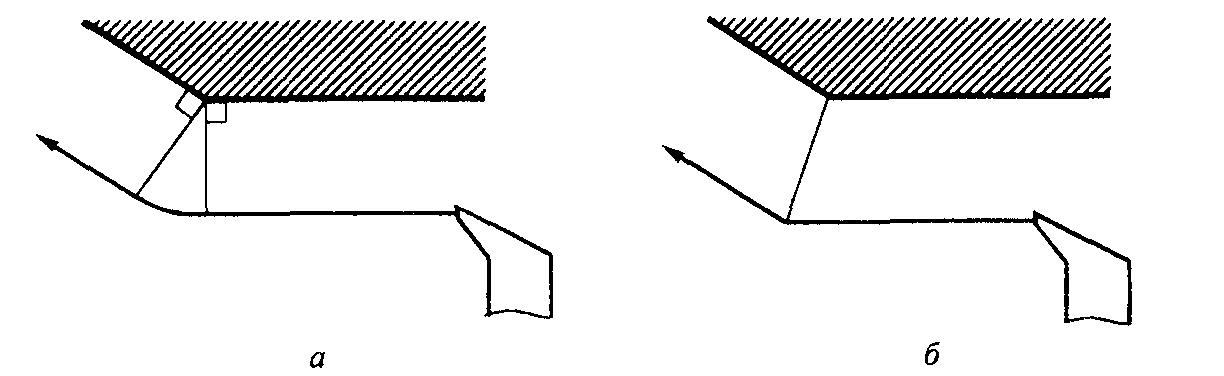
Рис. 1.83. Типы обработки углов контура
• расчет частей удаляемого материала в соответствии с границами глубины резания, определенными при создании модели резца, или без учета глубины резания;
• припуск на обработку по оси^ X;
• припуск на обработку по оси Z;
• точность аппроксимации (см. рис. 1.56). Используется теми станками, которые при вычислении траектории инструмента по кривой выполняют обработку «от точки к точке» и не могут выполнять интерполяцию по окружности.
^ 5.8. Процесс токарной обработки
Как и в любом процессе механообработки, в процессе токарной обработки участвуют последовательности, операции и циклы.
Пример процесса токарной обработки может быть представлен в виде:
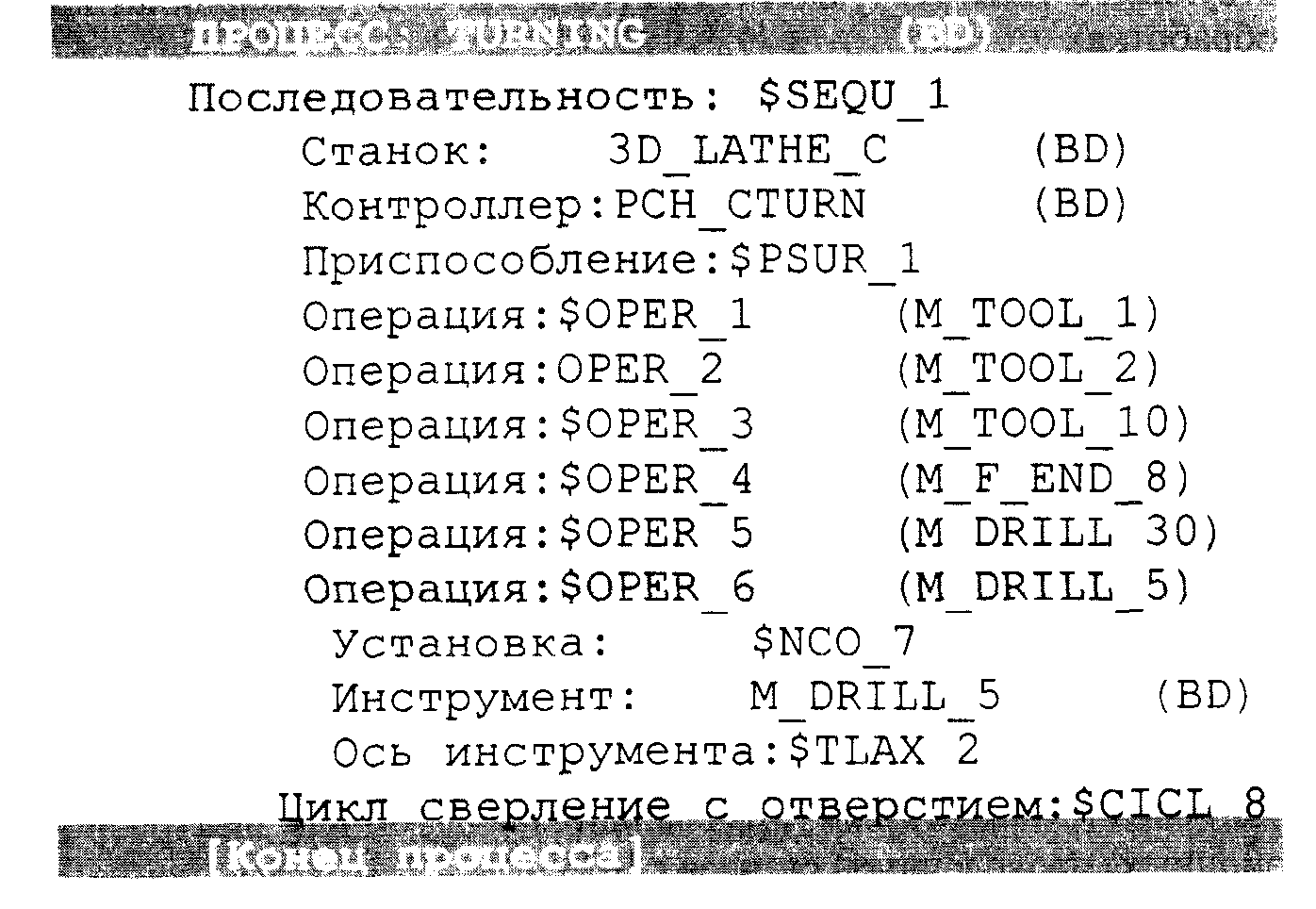
В результате процесса рассчитываются траектории движения инструмента.
База данных содержит следующие контроллеры: CLF_TUKN (файл формата CL), APTJTURN (файл формата APT) и PCH_TURN (файл формата прямого вывода DIRECT), а также PCH_CTURN (файл формата DIRECT - прямой вывод для С-координатного точения).
Последовательность проектирования процесса токарной обработки изложена в подразделе «Процесс механической обработки».
Редактирование параметров процесса содержит такие функции, как добавление элементов, удаление, перемещение, обмен элементов в структуре процесса, изменение параметров элементов процесса, удаление траекторий инструментов и т.д. Изменения в процессе должны быть пересчитаны.
^ Выходная информация процесса может быть представлена в виде:
• управляющей программы на проблемно-ориентированном языке;
• управляющей программы в коде конкретного станка с ЧПУ;
• проектно-технологической документации в требуемом формате.
Выбранный контроллер генерирует для токарного станка или обрабатывающего центра файл управляющей программы соответствующего типа: APT, CL-FILE, FNC и TRAUB (С-координатная обработка).
Проектно-технологическая документация может быть в виде чертежей, текстовой информации или рисунков. Документы создаются автоматически по указанному шаблону: карты цикла, карты инструмента, карты последовательностей,
^ 5.9. Проектирование процессов электроэрозионной обработки
Электроэрозионная обработка приходит на смену традиционным металлорежущим технологиям и особенно широко применяется при изготовлении пресс-форм, вырубных и чеканочных штампов. В системах технологической подготовки производства могут быть реализованы как копировально-прошивочный, так и вырезной вид электроэрозионной обработки по двум-четырем координатам.
Рассмотрим особенности программного обеспечения этого вида обработки на примере специализированной подсистемы «Электроэрозионная обработка» системы EUCLID3, с помощью которой выполняется подготовка управляющих программ для электроэрозионных (проволочных) станков с ЧПУ [9].
Проектирование технологии электроэрозионной обработки во многом аналогично проектированию технологии фрезерной обработки.
В качестве исходных данных для подготовки управляющих программ проволочной электроэрозионной обработки используются геометрические модели детали и заготовки, инструмента (проволоки заданного диаметра), оснастки, макет станка, а также параметры процесса обработки. Все необходимые макеты создаются на основании информации о геометрических моделях соответствующих видов оборудования, что значительно повышает качество обработки.
Среда электроэрозионной обработки создается так же, как и при проектировании фрезерной обработки. Элементы этой среды те же, что и в описанных выше процессах, а именно: макеты имеющихся на предприятии станков, модели инструментов и оснастки. Сохранение этих элементов в разделе стандартов базы данных позволит технологам вызывать созданные элементы среды из базы данных оборудования предприятия.
Описание архитектуры станка (ХУ/2_У)определяет кинематическую связь между шпинделем и положением оснастки, включая положение упоров.
Кинематическая схема электроэрозионного станка соответствует кинематической схеме фрезерного станка.
Инструмент (проволока) характеризуется диаметром и длиной режущей части. Система базирования проволоки создается автоматически.
Существуют следующие циклы электроэрозионной обработки:
обработка окна, 2-координатная обработка по контуру, 4-коорди-натная обработка по двум контурам.
^ Цикл обработки окна предназначен для обработки области внутри контура окна в детали (рис. 1.84). Контур окна должен быть плоским, замкнутым и лежащим в горизонтальной плоскости.