Управление процессом производства и эксплуатации
Вид материала | Анализ |
- Формирование системы управления процессом создания и освоения производства новой продукции, 335.06kb.
- Преподаваемые дисциплины, 170.17kb.
- Преподаваемые дисциплины, 188.88kb.
- Разработка методов и средств управления процессом производства капитального ремонта, 331.52kb.
- Управление процессом принятия решений о покупке с использованием моделей маркетинга, 294.05kb.
- Управление инвестиционным процессом с помощью сбалансированной системы показателей, 246.34kb.
- Содержание введение, 94.19kb.
- Лю Чжао Цзюнь управление технологическим процессом высокотемпературной пайки при производстве, 244.3kb.
- Лекция 2 на тему: «Рынок средств производства», 208.62kb.
- Инструкция по эксплуатации Газонокосилка электрическая, 151.5kb.
Промышленное производство/производство услуг
Промышленное производство подразумевает изготовление материальной продукции, например, автомобилей, радиочасов, шаров для гольфа, холодильников, – того, что мы можем увидеть или потрогать. С другой стороны, услуги – это действие. Осмотр у врача, ремонт телевизоров и автомобилей, показ фильма в кинотеатре. Большинство видов услуг подпадают под следующие категории:
Правительство (федеральное, на уровне штата, местное)
Оптовая/розничная торговля (одежда, продовольствие, бытовые приборы, офисное оборудование, игрушки, и т.д.)
Финансовые услуги (банковское дело, брокерская служба, страхование, и т.д.)
Здравоохранение (врачи, стоматология, больницы)
Бытовые услуги (чистка и прачечная, парикмахерские и косметические кабинеты, озеленение и садовые работы, и т.д.)
Деловые услуги (обработка данных, доставка и транспортировка, агентства по трудоустройству, и т.д.)
Образование (школы, колледжи, и т.д.)
Производство и обслуживание часто похожи в том, что сделано, но различаются в том, как это сделано. Так, в обоих случаях необходимы решения по разработке и эксплуатации процесса. Промышленник решает, какого размера ему нужен завод. Организация обслуживания (например, больница) должна определить, какого размера здание необходимо. И оба должны принять решение по месту расположения предприятия, продумать рабочий график и меры по контролю за трудовым процессом, разместить необходимые ресурсы.
Производство и сфера обслуживания отличаются главным образом в том, что производство ориентировано на изделие, а обслуживание – на действие. Различия включают в себя следующее:
- Контакт с потребителем
- Однородность вложений в производство
- Характер и содержание трудового процесса
- Однородность конечного продукта
- Меры производительности
- Гарантии качества
Давайте рассмотрим каждую из этих отличительных черт.
- По своей природе, обслуживание подразумевает большую степень контакта с потребителем, чем производство. Предоставление услуги обычно совпадает с потреблением. Например, восстановление кровли должно происходить непосредственно на крыше, а хирургическая операция требует присутствия хирурга и пациента. Со своей стороны, производство допускает разделение между производством и потреблением, так что производство может происходить далеко от потребителя. Это расширяет возможности выбора методов работы, планирования рабочего графика и осуществления контроля над производством. Сфера обслуживания, из-за необходимого контакта с потребителем, более ограничена в выборе возможных вариантов. Более того, заказчики иногда являются частью системы (например, самообслуживание на АЗС и в супермаркетах), поэтому строгий контроль невозможен. Наконец, в ориентированных на изделие производственных системах можно создавать складские запасы готовых товаров (например, автомобилей или холодильников), которые способны сглаживать неравномерность потребительского спроса. Сфера обслуживания, однако, не может создавать запасы времени и поэтому более чувствительна к изменениям спроса – в банках и универсамах можно увидеть как очереди, так и простаивающих без дела продавцов и кассиров, скучающих в ожидании клиентов.
- Производство услуг предполагает большее разнообразие вложений, чем типичное промышленное производство. Каждый пациент, каждая денежная ссуда и каждый авторемонт является специфической проблемой, которую часто нужно сначала диагностировать, а уже потом только решать. Процесс промышленного производства часто может контролировать изменение во вложениях и таким образом снижать изменения конечного продукта. Соответственно, производственные требования в этом случае будут более однородны, чем в сфере услуг.
- Из-за спонтанного потребления услуг и значительной изменчивости вложений, сфера услуг требует более разнообразного содержания труда – в то время как промышленное производство, за немногими исключениями, может быть более интенсивным и механизированным.
- Из-за того, что высокая механизированность ведет к производству товаров более однородных, сам процесс производства также тяготеет к однородности и эффективности. Деятельность сферы услуг по сравнению с этим кажется более медленной и неуклюжей, а ее конечный продукт более изменчив.
- Измерение производительности труда на производстве более точно, благодаря высокой степени однородности большинства произведенных изделий. В сфере обслуживания неоднородность потребительского спроса и содержания труда делают измерение производительности значительно более сложным. Например, сравните производительность работы двух врачей. Практика одного может включать множество несложных заболеваний и осмотров – в то время как другой не проводит подобных консультаций, так что их производительность покажется различной, если только не будет сделан тщательный анализ.
- В сфере обслуживания гарантировать качество значительно труднее, потому что производство и потребление происходят одновременно. Кроме того, высокая не однородность вложений создает дополнительную угрозу снижения качества продукции, если за этим качеством не следить строго и постоянно. Качество в момент создания обычно более важно для обслуживания, чем для производства, где ошибки можно исправить прежде, чем заказчик получит продукцию.
Таблица 1-5 дает краткий обзор различий между производственными процессами и услугами.
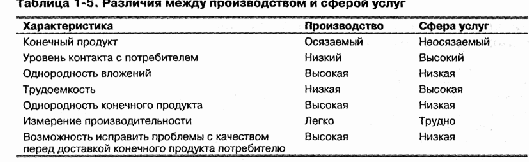
Хотя очень удобно рассматривать системы в чистом виде – производящими только услуги или только товары – в действительности большинство систем представляет собой смешанные типы. Например, обслуживание и ремонт техники и оборудования – это услуги, которые предоставляет практически каждая производственная компания. Подобным образом, большинство предприятий сферы обслуживания обычно продают товары, дополняющие их услуги. Например, фирмы по озеленению лужаек обычно продают препараты для уничтожения сорняков, удобрения и семена различных трав. Больницы обеспечивают не только медицинскими услугами, но также медикаментами и хирургическими инструментами. В ресторанах продаются продукты. В кинотеатрах – попкорн, конфеты и напитки.
Сектор обслуживания и сектор производства равно важны для экономики. В настоящее время сектор обслуживания обеспечивает более 70% всех рабочих мест в Соединенных Штатах. Более того, число работающих в этом секторе продолжает расти, в то время как число занятых в производственном секторе продолжает уменьшаться (см. рис. 1-5).
К сожалению, значительная доля расширения сектора обслуживания приходится на низкоквалифицированную и низкооплачиваемую работу, которая, как правило, имеет и низкую производительность. Производство важно тем, что оно обеспечивает значительную часть экспорта, что выгодно для внешней торговли. Кроме того, многие виды работ в сфере обслуживания прямо зависят от производства; то есть, они являются вспомогательными для производства. Если производственный сектор будет по-прежнему уменьшаться из-за неспособности успешно конкурировать с иностранными компаниями, то связанная с производством сфера услуг (например, технический сервис, служба безопасности, финансовые службы) тоже уменьшится.
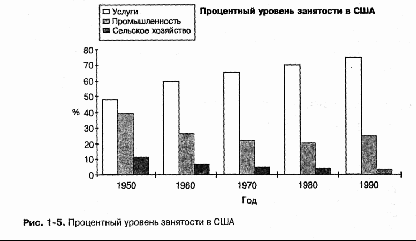
Рис. 1-5. Процентный уровень занятости в США
Значение проектирования и эксплуатации производственных
систем
Различные способы классификации производственных систем имеют важное значение для их проектирования и эксплуатации. Степень стандартизации конечного продукта, тип производства, общая ориентированность системы на товары или на услуги, или же на некую комбинацию товаров и услуг, – все это диктует требования по капиталовложениям, выбору оборудования, планированию мощности производства, определению местоположения предприятия, управлению запасами и ресурсами, найму рабочей силы, определенному графику производства и обеспечению качества.
Руководство проектом весьма отличается от управления сборочной линией, а руководство мастерской, в свою очередь, отличается от руководства проектом или крупномасштабным производством. Определение производственных потребностей будет различным для трех типов систем. Крупномасштабное производство требует стабильного уровня выпуска конечного продукта. Менять этот уровень может оказаться слишком дорого и трудно; следовательно, необходим точный прогноз, чтобы спроектировать систему должным образом. Напротив, у мастерской больше гибкости в работе, поэтому на стадии проекта прогнозирование имеет меньшее значение. Требования по поддержанию запасов для мастерской отличаются от требований для системы, производящей стандартные изделия. Мастерские обычно делают изделия на заказ. Поэтому у них будет небольшой (или вообще никакого) запас готовой продукции, но зато им обычно требуется поддержание запасов сырья и материалов для часто повторяющихся операций. В системах массового производства обычно существуют запасы как сырья, так и готовых изделий; однако закупки и большинство рабочих операций стандартизированы. Проекты, как правило, уникальны и единичны, поэтому их требования каждый раз различаются.
Если говорить о собственно рабочем процессе, то непрерывное и массовое производство дают наибольшую степень определенности, а проекты и мастерские – наименьшую. Следовательно, массовое производство, например, имеет большее количество закрепленных практикой действий, чем мастерские. Различия между системами и значение этих различий для управления производством будут рассматриваться на протяжении всей книги.
Производственный менеджер и процесс управления
Производственный менеджер – ключевая фигура в системе: он несет основную ответственность за производство товаров или услуг.
Виды работ, которыми могут руководить менеджеры, очень различны на различных предприятиях – в основном это обусловлено видом производимых товаров или услуг. Например, банковское дело явно требует управления не такого, как сталелитейное производство. Однако в определенном (и очень важном) отношении, работа в обоих случаях одна и также – это работа по управлению. Это же можно сказать о работе любого менеджера, независимо от вида производимых товаров или услуг. В каждом случае, руководитель производства должен координировать использование ресурсов через процесс управления, планирования, организации, подбора кадров, контроля за производством.
Примеры обязанностей производственных менеджеров приведены в таблице 1-6.

Производственные менеджеры и система принятия решений
Главная обязанность производственного менеджера – это планирование и принятие решений. В этом своем качестве менеджер оказывает значительное влияние на степень реализации целей предприятия.
Повсюду в этой книге вы будете сталкиваться с широким диапазоном решений, которые должен принимать руководитель предприятия, и вы познакомитесь с методикой и инструментами, необходимыми для принятия таких решений. В этом разделе описаны общие подходы к выработке производственных решений, включая использование моделей, количественные методы, анализ сбыта и системный подход.
Использование моделей
М
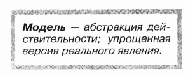
Например, детская игрушечная машинка – модель настоящего автомобиля. Она имеет много тех же визуальных черт (форма, пропорции, колеса), которые делают ее пригодной для игры и обучения ребенка. Но игрушка не имеет настоящего двигателя, не может перевозить людей, и не весит 2000 фунтов. Еще пример: учитель может нарисовать мелом на доске абсолютно все что угодно. Эти рисунки тоже будут моделями, они наглядно представляют информацию – но, в сущности, они не более чем крошки мела.
Другие примеры моделей – аэродинамические трубы, предназначенные для моделирования воздействия потоков воздуха на внешнюю поверхность автомобилей и самолетов; формулы; графики и диаграммы; балансовые отчеты и счета прибылей и убытков; финансовые нормы и коэффициенты. Общие статистические модели включают описательную статистику (среднее значение, диапазон и стандартное отклонение), а также произвольную выборку, нормальное распределение и регрессивные уравнения.
Модели иногда классифицируются на физические, схематические, или математические.
Физические модели напоминают копии с реальной жизни. Примеры физических моделей: миниатюрные автомобили, грузовики, самолеты, игрушечные звери и масштабные модели зданий и поездов. Достоинство этих моделей – их визуальное соответствие действительности.
Схематические модели более абстрактны, чем воспроизведенные в них реальные явления; то есть они имеют меньшее сходство с действительностью. Сюда относятся диаграммы и карты, планы и схемы, картины и рисунки. Преимущество схематических моделей состоит в том, что их относительно просто построить и изменить. Кроме того, они имеют некоторое визуальное соответствие реальности. Математические модели наиболее абстрактны; абсолютно не похожи на те реальные явления, которые в них воспроизводятся. Примеры: числа, формулы и символы. Этими моделями легче всего манипулировать, они являются основной формой входных параметров для компьютеров и калькуляторов. Разнообразие моделей огромно, от простых до самых экзотических; некоторые – достаточно грубы, другие чрезвычайно изящны. Тем не менее, все они имеют определенный набор общих черт. Все модели – это вспомогательные средства для принятия решений и по сути своей упрощения более сложных реальных явлений. Реальная жизнь включает огромное количество деталей и подробностей, многие из которых нерелевантны для решения специфической проблемы. Модели отбрасывают незначительные детали таким образом, чтобы можно было сконцентрировать внимание на самых важных аспектах ситуации, – таким образом увеличивается возможность понимания проблемы и ее решения.
Цель моделирования состоит в разработке модели, которая адекватно воспроизводит какое-либо явление реальной жизни. Когда модель разработана, многое можно узнать о явлении, изменяя основные параметры и наблюдая результаты изменений. Если модель хорошая, полученные знания можно применять к реальной ситуации.
Так как модели играют существенную роль при выработке решений в сфере управления производством, они широко включены в материал этой книги. Для каждой модели старайтесь узнать (1) цель, (2) как она используется для получения результатов, (3) как эти результаты интерпретируются и используются, и (4) какие применимы допущения и ограничения.
Последний пункт особенно важен, потому что практически каждая модель имеет свой собственный набор условий, которые определяют, в каких случаях модель действительна. Несоблюдение этих условий (то есть использование модели там, где это не предполагалось) приведет к недостоверным результатам. Попытка использовать такие результаты при решении производственной проблемы может привести к катастрофическим последствиям. Следовательно, чрезвычайно важно знать допущения и ограничения для каждой модели.
Менеджеры используют модели различными способами и по различным причинам. Модели выгодны, потому что они:
- Как правило, удобны в использовании и обходятся дешевле, чем контакт непосредственно с фактической ситуацией.
- Требуют от пользователей организовывать и дополнять информацию, при этом в процессе работы могут обнаружиться области, где необходима дополнительная информация.
- Обеспечивают системный подход к решению проблем.
- Дают более ясное понимание проблемы.
- Позволяют руководству анализировать вопросы типа «а что если?..»
- Требуют, чтобы пользователи четко определяли цели анализа.
- Служат последовательным инструментом для оценки.
- Позволяют пользователям использовать всю мощь математики для решения проблемы.
- Обеспечивают единый подход к анализу проблем.
Несмотря на этот внушительный список преимуществ, модели имеют определенные ограничения, которые вы должны знать. Вот наиболее важные из них:
- Количественная информация может получить преувеличенное значение за счет качественной информации.
- Модели могут неправильно применяться и результаты неверно толковаться. Широко распространенное использование компьютеризованных моделей повышает этот риск, потому что сложные модели могут попасть в руки пользователей, недостаточно сильных в математике, чтобы адекватно оценить все аспекты определенной модели. Таким образом, они не способны правильно понять, при каких обстоятельствах можно эффективно применять данную модель.
- Создание модели может стать самоцелью.
Количественный подход
Количественный подход к решению проблем обычно состоит в попытке получить оптимальное решение проблем менеджмента математическим способом. Хотя количественны и метод был традиционно связан с производственным и оперативным менеджментом, вплоть до Второй мировой войны не делалось попыток разрабатывать и развивать эти методы. Чтобы решать сложные проблемы материально-технического обеспечения армии, были созданы межотраслевые команды (например, психологи, математики, экономисты) для объединения усилий в поиске осуществимых решений. Эти усилия продолжались и расширялись в послевоенное время, и много результативных технологий внедрялось в управление производством. Линейное программирование и соответствующие математические методы широко используются для оптимального распределения небольших и недостаточных ресурсов. Техника очередности, которая появилась около 1920 года в телефонной промышленности, но почти не использовалась до 50-60-х годов, полезна для анализа ситуаций, когда образуются линии в состоянии ожидания. Моделирование материально-производственных запасов также возникло довольно давно, однако пережило долгий период забвения перед тем, как теперь стало широко использоваться для контроля за производственными ресурсами. Модели проектов, такие как PERT (технология обзора и оценки программы) и СРМ (метод критического пути) очень полезны в планировании, координации и контроле крупномасштабных проектов. Техника прогнозирования широко применяется в планировании и разработке производственных графиков. Статистические модели в настоящее время активно используются в сфере выработки производственных решений.
В большой мере, количественный подход к принятию решения в сфере управления производством (и в других областях принятия решений) нашел применение благодаря появлению калькуляторов и быстродействующих компьютеров, способных обрабатывать необходимое количество информации. Компьютеры оказали огромное влияние на практику управления производством, особенно в области планирования и управления материально-производственными запасами. Благодаря своей способности к быстрым и безошибочным вычислениям и возможности хранить тысячи битов информации с мгновенным доступом к ней, – компьютеры произвели существенный прорыв в решении некоторых очень сложных проблем. Кроме того, постоянно расширяющийся доступ к готовым пакетам программ, охватывающих практически все виды количественного анализа, очень повысил степень использования компьютеров руководителями предприятий для решения проблем. Многие прежде непрактичные методы, типа многократного регрессивного анализа и линейного программирования, стало теперь легко использовать.
Компьютеры оказались незаменимы в моделировании, когда аналитики исследуют реальные проблемы, не поддающиеся анализу, изменяя параметры в многократно повторяемых компьютерных испытаниях и анализируя результаты, чтобы лучше понять проблему и выработать альтернативные решения.
Из-за акцента на количественный метод в создании решения в сфере управления производством, важно не упускать из внимания тот факт, что менеджеры обычно используют комбинацию качественных и количественных методов; и большое количество важных решений основано именно на качественном подходе. Причина особого акцента на количественный анализ в этой главе состоит в том, что количественный анализ обычно более труден для понимания без большого количества объяснений и наглядных примеров.
Анализ альтернатив
Производственные менеджеры сталкиваются с решениями, которые можно назвать альтернативными. Например, определяя величину материально-производственных запасов, руководитель должен принимать во внимание альтернативу между возможным повышением объема обслуживания потребителя в результате увеличения производственного запаса – и повышением затрат на содержание такого запаса. Подобным же образом, при выборе оборудования руководитель должен учитывать как преимущества дополнительных рабочих функций – так и дополнительные затраты на эти функции. Другой пример – использование сверхурочного времени для увеличения выпуска: менеджер должен взвесить стоимость увеличенного выпуска против увеличенных затрат на сверхурочное время (например, учитывать более низкую производительность, большую стоимость труда, более низкое качество, повышенную возможность производственного травматизма).
Повсюду в этой книге вам будут представлены модели решений, учитывающих подобные факторы. Менеджеры иногда решают такие проблемы, составляя список преимуществ и недостатков каждого варианта решения – про и контра – чтобы лучше понять возможные последствия.
Системный подход
С
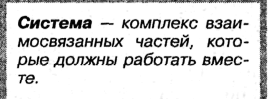
Одно нежелательное следствие использования количественных методов заключается в том, что они имеют тенденцию вырабатывать решения, которые являются оптимальными в узком смысле, но не могут быть оптимальными в более широком смысле (например, в пределах отдела, цеха, подразделения, или предприятия в целом). Следовательно, менеджеры должны оценить «оптимальные» решения, полученные количественным методом, в расширенном контексте и, возможно, соответственно изменять такие решения.
Мировой голод – проблема, которая носит системный характер. Мы читаем в газетах о людях, голодающих в одной части планеты, в то время как в другой части – переизбыток продовольствия, которое остается невостребованным, портится и уничтожается. Решение кажется простым: нужно послать лишние продукты тем, кто в них нуждается. К несчастью, это «решение» не учитывает некоторых аспектов проблемы. Надо преодолеть ряд основных препятствий. Одно из них – достаточно сложная задача транспортировки излишков продовольствия туда, где оно необходимо. Следует идентифицировать места скопления избыточного продовольствия, организовать временное хранение продуктов, произвести подготовку к отгрузке (определить сроки и графики, погрузочные и транспортировочные мощности, оплату расходов по отгрузке и т.д.). Еще более сложная задача – распределение продовольствия, когда оно доберется до страны назначения. Придется иметь дело не только с политической системой страны – возможно, коррумпированной и продажной – но и с транспортной системой региона. Часто регион имеет плохую транспортную систему (и вообще отсутствие дорог) и ограниченные возможности по доставке груза из порта вглубь страны. Подходящие летные поля и посадочные площадки могут отсутствовать. И даже в том случае, когда все эти трудности преодолены, решение проблемы будет всего лишь временным; более широкая проблема (окончательное решение проблемы голода в регионе) все равно останется. Таким образом, системная перспектива позволяет нам получить более реальную картину и увеличивает шансы достичь окончательного решения всей проблемы в целом.
Определение приоритетов
Практически в каждой ситуации менеджер обнаруживает, что одни аспекты более важны, чем другие. Осознание этого факта позволяет руководителю направить усилия туда, где они принесут наибольшую пользу и избежать пустой траты времени и энергии на малозначимые аспекты.
Давайте рассмотрим автомобиль. У него есть большое количество частей и систем, которые могут дать сбой. Некоторые из них жизненно важны для работы автомобиля. Он вообще не сможет работать без них, или же его эксплуатация станет опасной. Важнейшие части включают двигатель и систему передач, рулевой механизм, тормоза, электрическую систему и систему охлаждения. С точки зрения эксплуатации и ремонта автомобиля, эти части должны получить самый высокий приоритет, если общая цель состоит в том, чтобы эксплуатация автомобиля была надежной.
Имеются другие аспекты, гораздо менее важные, типа царапин на краске, незначительных деформаций кузова или изношенных покрышек. С точки зрения транспортировки, на них можно обращать внимание только после того, как решены проблемы первостепенной важности.
Между этими двумя крайностями находится целый диапазон пунктов промежуточной степени важности. Им следует уделять внимание в соответствии с их значимостью для конечной цели. В их список можно включить спустившиеся шины, слабый аккумулятор, расцентрированные оси, слабый глушитель, ржавчину, недействующее радио и подфарники, которые надо отрегулировать.
Достаточно очевидно, что определенные части автомобиля более важны для его работы, чем другие. То же положение действительно и для системы управления. Признавая этот факт и правильно определяя приоритеты, менеджер будет в состоянии более эффективно решать проблемы по мере их возникновения и даже предотвратить появление многих проблем.
П
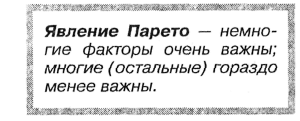
Идея состоит в том, что руководитель должен тщательно исследовать ситуацию в поисках тех немногих факторов, которые более всего будут способствовать усовершенствованию, и сконцентрироваться на них; фокусировка внимания на других, менее значимых факторах, даст для решения проблемы мало или вообще ничего. Это – одна из наиболее важных и широко распространенных концепций в управлении производством. Когда вы будете читать эту книгу дальше, попробуйте найти главу или отдельную тему, где бы эта концепция была неприменима. Вы неизбежно придете к заключению, что она применяется на всех уровнях производственного менеджмента и во всех аспектах выработки решения – будь то профессиональная или личная проблема.
Историческое развитие производственного менеджмента
Производственные системы существовали с древнейших времен. Китайская Великая Стена, египетские пирамиды, флот Римской и Испанской империй, дороги и акведуки Древнего Рима, – все они представляют собой наглядные примеры способности человека к организации производства. Однако большинство этих примеров можно классифицировать как общественные проекты. Производство товаров для продажи, по крайней мере в современном смысле, и современная фабричная система ведут свое начало от времен Промышленной Революции.
Промышленная Революция
Промышленная Революция началась в 1770-х годах в Англии и распространилась по Европе и Соединенным Штатам в течение девятнадцатого столетия. До того времени товары производились в маленьких мастерских ремесленниками и их учениками. Как правило, при такой системе создание изделия (будь то лошадиная повозка или предмет мебели) от начала до конца было задачей одного человека. Работали только простыми инструментами, – станки и оборудование, какие мы используем сегодня, еще не были изобретены. Изделия были сделаны из уникальных частей. Поэтому эти части небыли взаимозаменяемы: деталь, изготовленная для одной повозки, например, слегка отличалась от такой же детали любой другой повозки. Детали нельзя было изготавливать впрок, потому что не было никакой гарантии, что они будут соответствовать размерам будущих повозок. Более того, когда при использовании изделия ломались и нуждались в сменных частях, то эти части следовало изготавливать заново и подгонять вручную. Производство было медленным и трудоемким.
Затем, ряд изобретений навсегда изменили лицо производства, заменив работу человека работой машин. Возможно, наиболее важным из этих изобретений стал паровой двигатель, изобретенный Джеймсом Уаттом в 1764 г., потому что он обеспечил источник энергии для использования машин на фабриках. Прядильный станок (Дженни) Джеймса Харгрива (1770) и ткацкий станок Эдмунда Картрайта (1785) произвели революцию в текстильной промышленности. Обильные запасы угля и железной руды обеспечивали сырье для производства энергии и изготовления машин. Новые машины, сделанные из железа, были более мощными и долговечными, чем простые деревянные машины, которых они заменили.
П
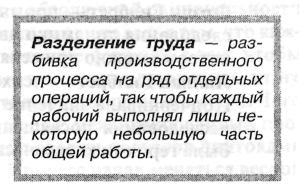
Это явление известно также как специализация труда. Преимущества такого подхода включали: сужение диапазона работы, которую рабочий должен уметь выполнять – таким образом, рабочий выучивался своему делу и приобретал профессионализм гораздо быстрее; избежание потерь времени, связанных с переключением рабочего с одной операции на другую (что происходило, когда каждый рабочий отвечал за изделие в целом); создание благоприятных условий для разработки специализированного оборудования в помощь работникам.

Другая веха связана с разработкой концепции взаимозаменяемых частей.
Иногда эту концепцию связывают с именем Эли Уитни (1790-е гг.), американского изобретателя, который разработал сборочную линию по производству мушкетов с такой системой допусков, что любая часть могла подойти к любому изделию; таким образом, детали не надо было изготавливать и подгонять вручную, они были полностью стандартизированы.
Фабрики стали быстро возникать и распространяться, обеспечивая работой бесчисленное множество людей, которые съезжались в города из сельской местности. Условия работы в то время были очень плохие, и на производстве было много несчастных случаев и высокая смертность.
Несмотря на коренное изменение производства, теория и практика управления не особенно прогрессировали. Было необходимо просвещение и более системный подход к управлению.
Научное управление
В эпоху научного управления широко распространились перемены в управлении фабриками и заводами. Движение было основано изобретателем и разработчиком системы эффективности производства, Фредериком Уинслоу Тейлором, которого часто называют отцом научного управления. В 1878 г. Тейлор начал работу в филадельфийской сталелитейной компании Мидвейл, президент которой верил в пользу экспериментов по улучшению методов работы фабрики. Тейлор начал как чернорабочий, но за шесть лет он достиг поста главного инженера.
Тейлор верил в науку управления, основанную на наблюдении, измерении, анализе и усовершенствовании методов работы и экономического стимулирования. Он изучал методы работы до мельчайших деталей, чтобы идентифицировать самый лучший способ выполнения каждой операции. Тейлор также полагал, что управление должно отвечать за планирование, за тщательный отбор и обучение рабочих, за определение оптимального способа выполнения каждого вида работы, за достижение сотрудничества между руководством и рабочими, и за разграничение деятельности по управлению производством и чисто производственной деятельности.
Методы, выявленные Тейлором, максимизируют выпуск продукции. Они не всегда были популярны среди рабочих, которые иногда считали, что эти методы используются для несправедливого увеличения выпуска без соответствующего увеличения компенсации. Безусловно, некоторые компании злоупотребляли рабочими в погоне за эффективностью. В конце концов, общественный протест достиг залов Конгресса, и по этому вопросу были проведены слушания. В 1911 году сам Тейлор был вызван для дачи показаний в Конгрессе, и в этом же году вышла его классическая книга Принципы научного управления. Общественный резонанс этих слушаний фактически помог принципам научного управления получить широкое применение в промышленности.
Среди других пионеров этого движения, которые тоже внесли в него весомый вклад, были следующие:
Фрэнк Гилбрет – промышленный инженер, которого часто называют отцом исследования динамики движений. Он разработал принципы экономии движения, которые можно применять к невероятно мелким частям процесса.
Лилиан Гилбрет – психолог, жена Фрэнка Гилбрета, работала вместе с мужем. Подчеркивала значение человеческого фактора в трудовом процессе. Многие ее исследования посвящены проблеме утомляемости рабочего. (Чета Гилбретов была героями классического фильма 50-х гг., Дешевле на дюжину.)
Гарри Гантг открыл значение нематериального стимулирования рабочих и разработал широко применяемую систему планирования, которую называют диаграмма Гантта.
Харрингтон Эмерсон применил идеи Тейлора к организационной структуре производства и способствовал использованию экспертов для повышения организационной эффективности. Он свидетельствовал на слушаниях в Конгрессе, что на железной дороге можно сэкономить миллион долларов в день, применяя принципы научного управления.
Генри Форд–промышленник, применил в автомобильной промышленности систему массового производства и подвижную сборочную линию, как это описано в следующем отрывке:
Модель Т была блистательно простой машиной; когда в ней что-нибудь ломалось, обычный владелец мог выйти и сам устранить поломку. Проложенные для лошадей тракты, которые составляли большую часть дорог в стране и были совершенно непригодны для более элегантных автомобилей, не представляли для этой машины никаких проблем. Колеса были поставлены высоко, и автомобиль ездил, не цепляя днищем дороги. Эта машина была, по словам биографа Форда, Кейт Сворд, сплошные кости и мышцы и ни грамма жира. Скоро самая большая проблема для компании Форда заключалась в том, чтобы успеть выполнить все поступающие заказы. К счастью для Форда, учение Фредерика Тейлора, главного авторитета в области научного управления промышленностью, только что получило широкое признание. Тейлор, вооруженный часами и прочным неверием в энтузиазм среднего рабочего, внедрил в сталелитейную и остальную промышленность новую методику исследований соотношения время-движение. Например, Тейлор измерил, какое количество работы один рабочий с лопатой может сделать за один день; он обнаружил, что максимальная эффективность работы достигается, когда на лопату берется не максимальное количество груза (38 фунтов), а меньше – 21 фунт; общее количество обработанного груза при этом гораздо больше. Эффективность труда стала важна, потому что таково было требование времени. Изучение эффективности приобретало особое значение по мере того, как в процессе производства машины стали теснить людей, и один производственный прорыв следовал за другим. Форд, очарованный эффективностью производства, полностью принял теорию Тейлора и начал использовать его принципы на своем заводе, внедряя и развивая их до фантастического уровня.
Поскольку модель Т имела такой успех – она пользовалась такой популярностью, что дилерам иногда приходилось приостанавливать прием заказов – внимание Форда переключилось на производство. Фабрика и, еще в большей степени, процесс производства стали его настоящей страстью. Процесс, как он говорил всем и каждому, был для него праздником, потому что каждый день он видел такие потрясающие перемены в возможностях и достижениях производства, что работа на заводе стала подобна работе в будущем. Еще до успеха модели Т, Форд уделял большое внимание промышленному процессу. В 1908 году он пригласил эксперта по вопросам эффективности производства Уолтера Фландерса и предложил ему вознаграждение в $20000, если он за 12 месяцев добьется, чтобы завод мог производить десять тысяч автомобилей. Фландерс полностью реорганизовал производство и установил контрольные сроки за два дня. Кроме того, он смог убедить Форда, что необходимо расширить производственные площади...
После этого Форд приобрел Хайленд Парк. Здесь он собирался осуществить самые современные производственные идеи, и в особенности идеи Фредерика Уин-слоу Тейлора. Эти идеи, предрекал Тейлор, приведут к абсолютной рациональности процесса промышленного производства. Основная мысль заключалась в том, что каждый производственный процесс разбивался на еще меньшие функции с тем, чтобы каждую из них можно было механизировать и ускорить – создав в конечном итоге непрерывное сборочное производство. Непрерывность процесса превыше всего. Чего он хотел, и что вскоре получил, это, по словам Кейт Сворд, механизированный процесс, подобный реке с ее притоками – когда процессы сборки подузлов притоками впадали в реку общего процесса сборки автомобиля. Процесс начал меняться весной 1913 г. Первой частью современной сборочной линии стала сборка магнитной катушки. Раньше рабочий – и это должен был быть высококвалифицированный рабочий – изготовлял маховик магнето от начала до конца. Хороший работник мог сделать от 35 до 40 штук в день. Теперь же появилась сборочная линия для магнето. Она подразделялась на 29 различных операций, которые выполнялись 29 работниками. При старой системе производства на изготовление одного магнето требовалось 20 минут; при новой системе – 13 минут.
Вскоре Форд и его соратники решили провести такую рационализацию труда по всему заводу. В короткий срок они создали похожую систему по сборке двигателей и коробки передач. Затем, летом 1913 г., они взялись за процесс конечной сборки, который, по мере ускорения всех остальных процессов, стал тормозить производство. Рабочие двигались вокруг неподвижного металлического объекта – автомобиля, который они собирали – так быстро, как только могли. А если бы люди могли оставаться на одном месте, а перемещался сборочный объект, то меньше времени рабочего – времени Форда – тратилось бы впустую.
Чарльз Соренсен, один из руководящей верхушки фордовского производства, попробовал медленно провести раму автомобиля модели Т на лебедке через все 250 футов производственного пространства цеха, постоянно проводя замеры времени. За ним шли 6 рабочих – они поднимали с пола детали, уложенные партиями через определенные (тщательно отмеренные) промежутки, и монтировали их к раме. Это стало рождением сборочной линии – идея такой линии произвела революцию в американской промышленности. Раньше для сборки автомобиля требовалось 13 часов – теперь же срок производства сократился вдвое, составив 5 часов 50 минут. Не останавливаясь на достигнутом, они продолжили преобразования, удлинили линию сборки и привлекли для конечного процесса рабочих более высокой квалификации. Через несколько недель сборка автомобиля занимала уже 2 часа 38 минут. Теперь прорывы в производстве пошли еще быстрее. В январе 1914 года Форд установил первый автоматический конвейер. Это была, по словам Форда, первая движущаяся линия на производственном предприятии; она была создана по образцу подвесного устройства, какое чикагские мясники использовали для перемещения туш. Через два месяца после внедрения этого новшества Форд уже мог собирать автомобиль за полтора часа. Это было потрясающее достижение, но оно лишь подхлестнуло их рвение. Теперь абсолютно все надо было измерить, рационализовать, разбить на составные элементы и ускорить. Всего несколько лет назад, в эпоху стационарной сборки, рекордные сроки по сборке автомобиля составляли 728 часов труда одного рабочего; с новой подвижной линией на это требовалось только 93 минуты. Руководители фордовских предприятий отпраздновали свою победу, дав большой обед в отеле Понтчартрейн в Детройте. В шутку, они установили в обеденном зале маленькую конвейерную ленту с велосипедной цепью и мотором в пять лошадиных сил – конвейер разносил еду вдоль стола. В этой шутке сказался дух того давнего времени – оптимизм, уверенность в своих силах и товарищество.
(Текст воспроизводится по изданию: David Halberstam, The Reckoning, 1986, стр. 79-81. Печатается с разрешения компании William Morrow & Company, Inc.)
Форд совершенствовал не только взаимозаменяемые части, но и взаимозаменяемого рабочего. К 1915 году, когда были полностью установлены сборочные линии Хайленд Парка и предприятие работало на полную мощность, число рабочих на конвейере превысило 7000 человек. Большинство из них только недавно приехали в Детройт, как правило, с близлежащих ферм. Многие вообще недавно приехали в Америку.
Проведенное в 1915 году исследование выявило, что рабочие Хайленд Парка говорят более чем на 50 языках, а многие с трудом объясняются на английском... Каким образом эта армия иностранцев смогла сплотиться и произвести такой объем сложнейшей продукции (модель Т), – гораздо больший, чем любая компания могла только мечтать? Да еще при этом работать с такой точностью и совершенством?
Ответ на эти вопросы заключается в идее разделения труда, в доведении этой идеи до логического конца, до крайности. В 1908 году квалифицированный рабочий мастерских Форда сам приносил на рабочее место все необходимые части и детали, приносил со склада инструменты, чинил их по мере необходимости, производил сложную подгонку деталей и сборку всего автомобиля, затем проверял свою работу перед тем, как отправить готовый автомобиль в отдел поставок.
В отличие от этого, у сборщика на фордовской линии массового производства была только одна задача – закрепить два болта или поставить одно колесо на каждую машину. Он даже не заказывал детали, не приносил инструменты, не ремонтировал свое оборудование, не проверял качество – и даже не знал, что делают справа и слева стоящие. Он не смотрел по сторонам и думал только о своем деле. При такой постановке дела, тот факт, что рабочий не говорил на том же языке, что его коллеги по сборке или мастер цеха, не имел абсолютно никакого значения для успеха фордовской системы (местоимение он используется намеренно – до Второй мировой войны рабочие на заводах Америки и Европы были исключительно мужчинами).
Разумеется, кому-то надо было думать о том, как собраны воедино все части, и о том, что именно должен делать каждый сборщик. Это стало задачей людей совершенно новой профессии – промышленных инженеров. Подобным же образом, кто-то должен был обеспечивать доставку деталей к конвейеру – этим обычно занимался производственный инженер, который разрабатывал конвейерные линии. Специальные уборщики периодически убирали все рабочие места, квалифицированные мастера-ремонтники обходили линию, заменяя и налаживая неисправное сборочное оборудование. Другие специалисты проверяли качество работы. При такой системе все дефекты работы обнаруживались только в конце сборочной линии, где в процесс включалась другая группа рабочих – они производили размонтировку и поэтому должны были обладать квалификацией сборщиков.
Такое разделение труда позволяло затрачивать на обучение сборщика буквально несколько минут. Более того, его труд беспощадно дисциплинировался скоростью самой сборочной линии – медлительным приходилось торопиться, а излишне активным надо было замедлять свои темпы, подстраивая их под общий ритм. Мастер цеха (прежде он был главой всего производственного пространства, с широким спектром полномочий и обязанностей, теперь же он стал всего лишь полуквалифицированным проверяющим) мог моментально заметить, когда рабочий отвлекается от дела или не может справиться со своей задачей. В результате, сборщики на линии стали такими же взаимозаменяемыми, как детали машины.
(Текст воспроизводится по изданию James P. Womack, Daniel T.Jones, Daniel Roos The Machine that Changed the World, 1990. Печатается с разрешения Rawson Associates/ Scribner, отделения компании Simon & Schuster, Inc.)
Роль человеческого фактора
В то время как школа научного управления производством делала особый акцент на технических аспектах организации труда, школа человеческих отношений всячески подчеркивала значимость личностного элемента в трудовом процессе. Ядром этой школы стали труды Элтона Мейо, работавшего в 1930-х гг. в Готорнском отделении компании Вестерн Электрик. Его исследования показали: помимо физических и технических аспектов трудового процесса, принципиальное значение для повышения производительности труда имеет мотивация рабочего.
Модели решений и наука управления
Модели решений – это количественные методы, которые направляют процесс выработки решения. В 1915 году Ф.У. Харрис разработал одну из первых моделей: математическую модель для управления запасами. В 1930-х гг., трое сотрудников телефонной компании Bell – Х.Ф.Додж, Х.Дж.Ромиг и У.Шухарт – разработали статистические процедуры для выборочного обследования и контроля за качеством. В 1935 г. Л.Х.С.Типпетт провел ряд исследований, которые заложили основу для теории выборочной статистики. Поначалу эти количественные модели не очень широко применялись в промышленности. Однако начало Второй мировой войны изменило это положение. Война оказала огромное давление на промышленное производство, и специалисты из самых разных областей объединили свои усилия, чтобы повысить эффективность военной промышленности. В послевоенное время работа по развитию и усовершенствованию количественных методов анализа продолжалась – и в результате были разработаны модели для прогнозирования, управления ресурсами, руководства проектами и других областей производственного менеджмента.
В 60-е и 70-е годы научные методы управления ценились очень высоко; в 80-е интерес к ним несколько угас. Однако широкое использование персональных компьютером дружественного программного обеспечения в рабочих процессах может снова повысить популярность этих методов.
Развитие технологий
До Промышленной революции в основе производства лежала физическая сила прежде всего людей, а также животных (лошадей, быков). Промышленная революция произвела резкий сдвиг в сторону машинного труда. В течение следующих 150 лет происходили постепенные усовершенствования технологий. Следующий рывок в технологическом развитии произошел с широким распространением автоматизации производства в 50-е и 60-е годы.
За этим последовало быстрое развитие компьютерных технологий на протяжении нескольких десятилетий. Следствием этого стало повсеместное использование в трудовых процессах компьютеров и компьютеризованного оборудования. Сегодня компьютеры используются в офисной автоматизации, разработке проектов, в управлении и контроле промышленного производства, разработке промышленных роботов, планировании и пр. В сущности, компьютеры стали неотъемлемой частью современных систем управления производством.
Влияние японской промышленности
Ряд японских промышленников развили или усовершенствовали практику управления производством, что дало им возможность увеличить производительность и повысить качество своих изделий. Это сделало их необычайно конкурентоспособными и пробудило интерес к новым подходам во многих неяпонских компаниях. В новом под ходе делается особый акцент на прикладные решения производственных проблем, активное вовлечение рабочего, особое внимание к качеству и непрерывному усовершенствованию продукта и полное удовлетворение заказчика товаром изготовителя. Именно японцам мы обязаны за качественную революцию, которая проходит сейчас в промышленно развитых странах, и за повсеместный интерес к производственному менеджменту, основанному на факторе времени.
Влияние японцев на американские компании производственной и обслуживающей сферы было огромно, и, скорее всего, продолжится в обозримом будущем. Учитывая это влияние, в данной книге будет приведена обширная информация о методах и достижениях японской промышленности.
Таблица 1-7 дает хронологию некоторых ключевых событий в развитии производственного менеджмента.
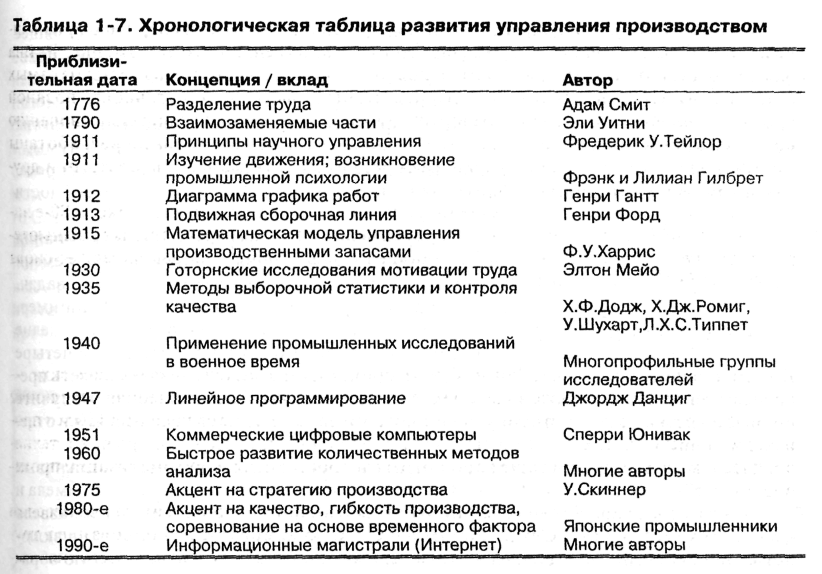
Последние тенденции
В настоящее время действует ряд факторов, очень существенных для развития бизнеса, поскольку они оказывают сильнейшее влияние на планирование производства и систему принятия решений. Многие из этих факторов связаны с понятием конкуренции, в особенности с иностранной конкуренцией и ее влиянием на производственные компании.