Лекция 1 введение диагноз в переводе с греческого «диагнозис»
Вид материала | Лекция |
- И в переводе на русский язык означает исследование, 35.4kb.
- Термические ожоги. Классификация и прогноз, сортировка пострадавших Введение, 66kb.
- Лекция №1. Предмет физики. Физические измерения, 265.16kb.
- Тема: "Биология", 88.38kb.
- Шпаргалка по педагогике (для педагогов) Понятие педагогики и этапы ее развития, 2042.12kb.
- В середине XIX столетия появилось новое течение в геометрии топология. «Топология», 171.1kb.
- План практических занятий по неонатологии для студентов 6 курса педиатрического факультета, 37.57kb.
- «Отечественная история»», 1938.89kb.
- Тема Научные основы экономического анализа, 3309.82kb.
- Науч рук В. В. Инютин библейские мотивы в драме, 126.32kb.
Лекция 5
МАГНИТНЫЕ МЕТОДЫ КОНТРОЛЯ
Классификация и области применения магнитных методов контроля
Магнитные методы контроля основаны на регистрации магнитных полей рассеяния, возникающих над дефектами, или на определении магнитных свойств контролируемых изделий. Магнитные методы контроля в соответствии с ГОСТ 18353–73 классифицируют по способам регистрации магнитных полей рассеяния или определения магнитных свойств контролируемых изделий (рис. 2.1).
Для выявления дефектов типа нарушений сплошности металла в ферромагнитных изделиях применяют все магнитные методы (см. рис.12).
Магнитопорошковый метод является одним из самых распространенных методов обнаружения дефектов типа нарушения сплошности металла. Метод имеет следующие преимущества: высокую чувствительность; простоту контроля и возможность проверки различных по форме и размерам деталей на одном и том же дефектоскопе; возможность контроля деталей, находящихся в конструкции; сравнительно высокую производительность контроля.
Метод, основанный на эффекте Холла, используют для обнаружения дефектов и в приборах измерения толщины, контроля за структурой и механическими свойствами. Эффект Холла состоит в следующем. Если прямоугольную пластину, изготовленную из некоторых полупроводниковых материалов (например, германия, антимонида или арсенида индия), поместить в магнитное поле перпендикулярно к вектору напряженности и пропустить по ней ток в направлении граней a, b (рис. 13), то на гранях c, d возникнет электродвижущая сила (ЭДС) Холла Eх = Kх* iH/d, где Kх – постоянная Холла, Ом * см2/ А; i – ток в датчике (пластине), А; Н – вектор напряженности поля, перпендикулярный к наибольшей плоскости пластины, А/ см; d – толщина пластины, см.
Измерение напряженности магнитного поля с помощью датчиков Холла имеет следующие преимущества:
возможность измерения в узких зазорах, отверстиях небольшого диаметра, вследствие небольших размеров датчиков (минимальные размеры кристаллических датчиков Холла: площадь 0,7.0,7 мм2, толщина порядка 1 мм, в то время как толщина пленочных датчиков с подложкой – 0,1 мм);
возможность измерения экстремального значения напряженности, так как выходное напряжение датчика Холла пропорционально составляющей напряженности поля, нормальной к его плоскости;
датчик Холла – статический элемент, в отличие, например, от преобразователей индукционного типа;
возможность получения линейной зависимости выходного напряжения от напряженности поля в широких пределах.
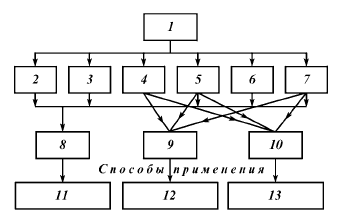
Рис. 12. Классификация магнитных методов и области применения:
1 – магнитные методы контроля; 2 – магнитопорошковый; 3 – магнито-
графический; 4 –феррозондовый; 5 – преобразователя Холла; 6 – индук-
ционный; 7 – пондеромоторный; 8 – дефектоскопия; 9 – измерение толщины; 10 – контроль за структурой и механическими свойствами; 11 – опре-
деление поверхностных и подповерхностных дефектов типа нарушений
сплошности металла в ферромагнитных изделиях; 12 – определение толщины немагнитных и слабомагнитных покрытий на ферромагнитных изделиях,толщины азотированного и цементированного слоев, слоя поверхностной закалки; 13 – определение качества термообработки, количества магнитной фазы в немагнитных сплавах, механических характеристик ферромагнитных сталей, остаточного аустенита, магнитной анизотропии
Индукционный метод нашел применение для обнаружения дефектов в железнодорожных рельсах, уложенных в путь.
Пондеромоторный метод, основанный на пондеромоторном взаимодействии измеряемого магнитного поля и магнитного поля тока в рамке прибора или магнита, нашел применение в дефектоскопах контроля железнодорожных рельсов, коэрцитиметрах.
Кроме обнаружения дефектов типа несплошностей материала (трещин, волосовин, закатов, флокенов и др.), магнитные методы позволяют решать задачи исследования структуры, определять качество термообработки деталей, наличие и количество остаточного аустенита, магнитную анизотропию, контролировать процесс распада твердого раствора и дисперсионного твердения, определять механические характеристики ферромагнитных сталей и чугунов по изменению их магнитных характеристик, а также контролировать толщину цементированного или азотированного слоев и толщину слоев поверхностной закалки изделий.
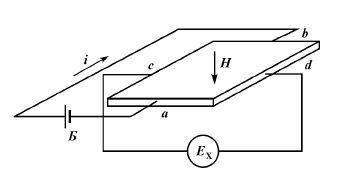
Рис. 13. Схема работы датчика Холла:
Eх – ЭДС Холла; H – вектор напряженности поля; Б – батарея; i – ток в
датчике; a, b, c, d – грани датчика
Намагничивание ферромагнитных материалов при магнитном контроле
Для намагничивания изделий при магнитном контроле используется магнитное поле, возникающее в пространстве вокруг проводника с током (рис. 14), между полюсами постоянного магнита или электромагнита (рис. 15, а) или соленоида (рис. 15, б), в обмотках 1 и 2 которых протекает электрический ток.
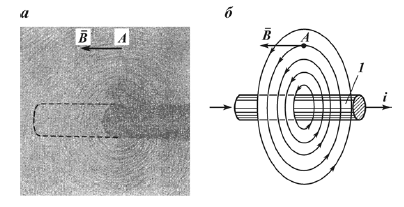
Рис. 14. Магнитное поле вокруг проводника 1 с током i:
а – спектр; б – схема магнитных линий поля; B – вектор магнитной ин-
дукции в точке А
В магнитной дефектоскопии используют следующие магнитные величины: магнитную индукцию В, магнитный поток Ф, напряженность магнитного поля Н, магнитную проницаемость µ, намагниченность J.
Магнитные свойства материала контролируемых деталей характеризуются петлей гистерезиса (рис. 16). Значение индукции на петле гистерезиса при Н = 0 называется остаточной индукцией Br, т.е. магнитной индукцией, оставшейся в образце после снятия поля.
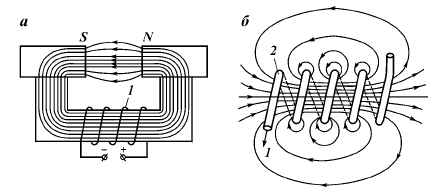
Рис. 15. Спектр магнитных полей
Величина Нr, соответствующая В = 0, называется коэрцитивной силой.
Индукция, соответствующая наибольшей намагниченности в образце, называется индукцией насыщения Bm.
Если перемагничивать деталь магнитным полем, напряженность которого на каждом цикле изменяется от – Н до + Н и уменьшается от цикла к циклу, то получится серия кривых перемагничивания – симметричных петель гистерезиса (рис. 17). Геометрическое место вершин симметричных петель гистерезиса называют основной кривой 1 намагничивания. Изменение индукции в предварительно размагниченном образце при возрастании поля от нуля до некоторого наибольшего значения выражается кривой 2, называемой кривой первоначального намагничивания, которая проходит несколько выше основной кривой намагничивания.
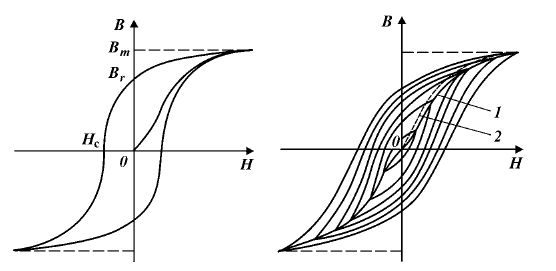
Рис. 16. Кривая перемагничивания Рис. 17. Семейство симметричных
стали (петля гистерезиса) петель гистерезиса
Контролируемая ферромагнитная деталь состоит из очень малых самопроизвольно намагниченных областей, так называемых доменов. В размагниченной детали магнитные поля доменов направлены самым различным образом и компенсируют друг друга. Суммарное магнитное поле доменов в этом случае равно нулю.
Если контролируемую деталь помещают в намагничивающее поле, то под его влиянием поля отдельных доменов устанавливаются по направлению внешнего поля, образуется результирующее магнитное поле доменов, и деталь намагничивается.
Величину, характеризующую способность материала намагничиваться, называют магнитной проницаемостью. В магнитной дефектоскопии используют магнитные проницаемости различных видов.
УЛЬТРАЗВУКОВОЙ КОНТРОЛЬ
Физической основой ультразвуковой дефектоскопии является свойство ультразвуковых волн отражаться от несплошностей.
Действие приборов ультразвукового контроля основано на посылке ультразвуковых импульсов и регистрации отраженных эхосигналов или ослабленных сигналов.
Посылка ультразвуковых импульсов и прием эхо-сигналов производится пьезоэлементами (пьезоэлектрическими преобразователями), преобразующими переменное электрическое поле в акустическое поле и наоборот.
В зависимости от типа дефекта ввод ультразвуковых волн осуществляется перпендикулярно или под определенным утлом к поверхности изделия. При контроле толщины стенки трубы и контроле дефектов, параллельных стенке трубы (расслоений, неметаллических включений), ультразвуковые колебания вводятся по нормали к поверхности трубы. При ручном контроле для этого используются прямые пьезопреобразователи-искатели. Толщина стенки трубы или расстояние до несплошности определяется путем измерения времени прохождения зондирующего (т.е. излучаемого в изделие) импульса от наружной до внутренней поверхности трубы или от наружной поверхности до несплошности и отраженного импульса в обратном направлении (5850 м/с для продольных волн).
Существует несколько методов (схем) ультразвукового контроля. Наиболее распространенным является импульсный эхометод, или просто эхометод. Метод основан на регистрации ультразвуковых волн, отраженных от несплошности при импульсном прозвучивании. Амплитуда эхосигнала при этом пропорциональна площади несплошности, служащей отражателем.
Ультразвуковой контроль проводится для выявления внутренних и выходящих на поверхность протяженных (ими могут быть: непровары, несплавления, трещины, подрезы, цепочки скопления пор и включений) и не протяженных (ими могут быть: одиночные газовые поры, шлаковые включения) дефектов.
Перед проведением контроля следует произвести очистку поверхности от изоляционного покрытия, пыли, грязи, окалины, застывших брызг металла, забоин и других неровностей и нанести контактную смазку.
Контроль сварных соединений осуществляют путем перемещения (сканирования) ПЭП по поверхности околошовной зоны сваренных элементов параллельно сварному шву с одновременным возвратно-поступательным движением в направлении, перпендикулярном ему.
Признаком обнаружения дефекта служит появление на поисковом уровне чувствительности эхо-сигнала на экране дефектоскопа. При появлении признаков обнаружения дефекта следует зафиксировать преобразователь в положении, при котором амплитуда наблюдаемого сигнала максимальна, и определить координаты и параметры дефекта.
Дефекты по результатам ультразвукового контроля относят к одному из следующих видов:
непротяженные (одиночные поры, компактные шлаковые включения);
протяженные (трещины, непровары, несплавления, удлиненные шлаковые включения и поры);
цепочки и скопления (цепочки и скопления пор и шлака - три и более дефекта).
Акустические колебания и волны.
Акустическими волнами называют колебания частичек среды в упругой среде. Различают четыре основных типа волн: продольные, поперечные поверхностные и нормальные волны.
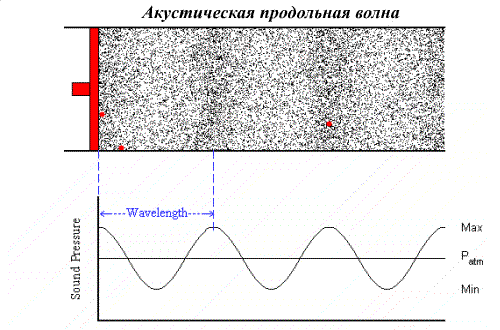
Рис. 18. Продольная волна.
Классификация методов контроля
Известно много акустических методов неразрушающего контроля, некоторые из которых применяются в нескольких вариантах. Классификация акустических методов показана на рисунке 19. Их делят на две большие группы - активные и пассивные методы. Активные методы основаны на излучении и приеме упругих волн, пассивные - только на приеме волн, источником которых служит сам контролируемый объект.
Активные методы делят на методы прохождения, отражения, комбинированные (использующие как прохождение, так и отражение), импедансные и методы собственных частот.
Методы прохождения используют излучающие и приемные преобразователи, расположенные по разные или по одну сторону контролируемого изделия. Применяют импульсное или (реже) непрерывное излучение и анализируют сигнал, прошедший через контролируемый объект.
В методах отражения используют как один, так и два преобразователя; применяют импульсное излучение. К этой подгруппе относят следующие методы дефектоскопии:
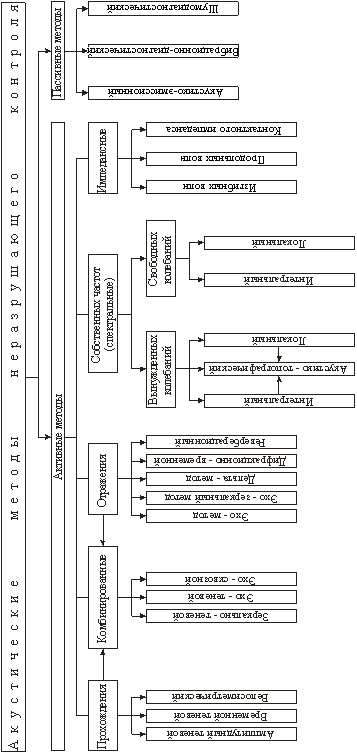
Рис. 19. Классификация акустических методов контроля
Эхо-метод (рис. 20, а) основан на регистрации эхо-сигналов от дефекта. На экране индикатора обычно наблюдают посланный (зондирующий) импульс I, импульс III, отраженный от противоположной поверхности (дна) изделия (донный сигнал) и эхо-сигнал от дефекта II. Время прихода импульсов II и III пропорционально глубине залегания дефекта и толщине изделия. При совмещенной схеме контроля (рис. 20, а) один и тот же преобразователь выполняет функции излучателя и приемника. Если эти функции выполняют разные преобразователи, то схему называют раздельной.
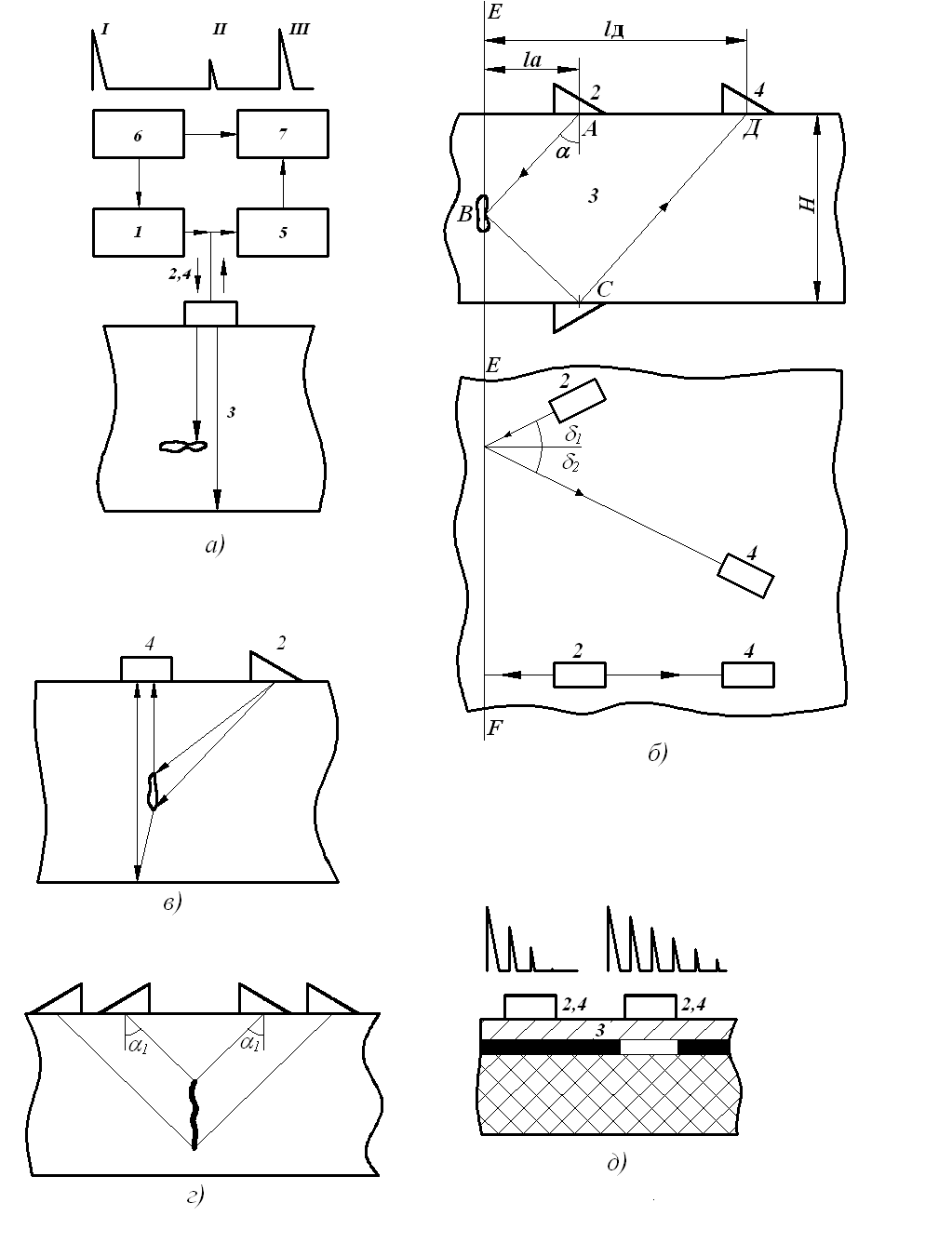
Рис. 20. Методы отражения:
а - эхо; б – эхо - зеркальный; в - дельта-метод;г - дифракционно - временной; д - реверберационный:
1 - генератор; 2 - излучатель; 3 - объект контроля; 4 - приемник;5 - усилитель; 6 - синхронизатор; 7 – индикатор
Эхо-зеркальный метод основан на анализе сигналов, испытавших зеркальное отражение от донной поверхности изделия и дефекта, т.е. прошедших путь АВСД (рис. 20, б). Вариант этого метода, рассчитанный на выявление вертикальных дефектов в плоскости ЕF, называют методом тандем. Для его реализации при перемещении преобразователей А и D поддерживают постоянным значение
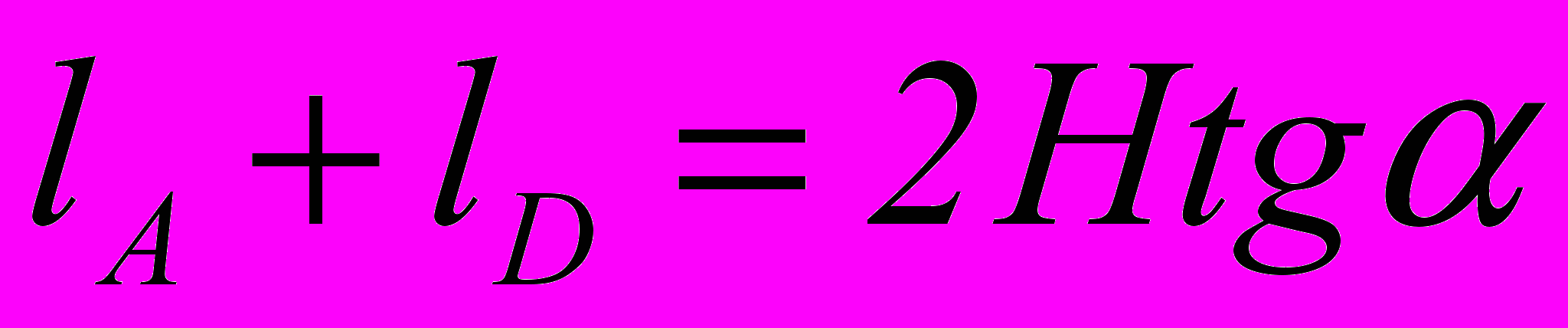
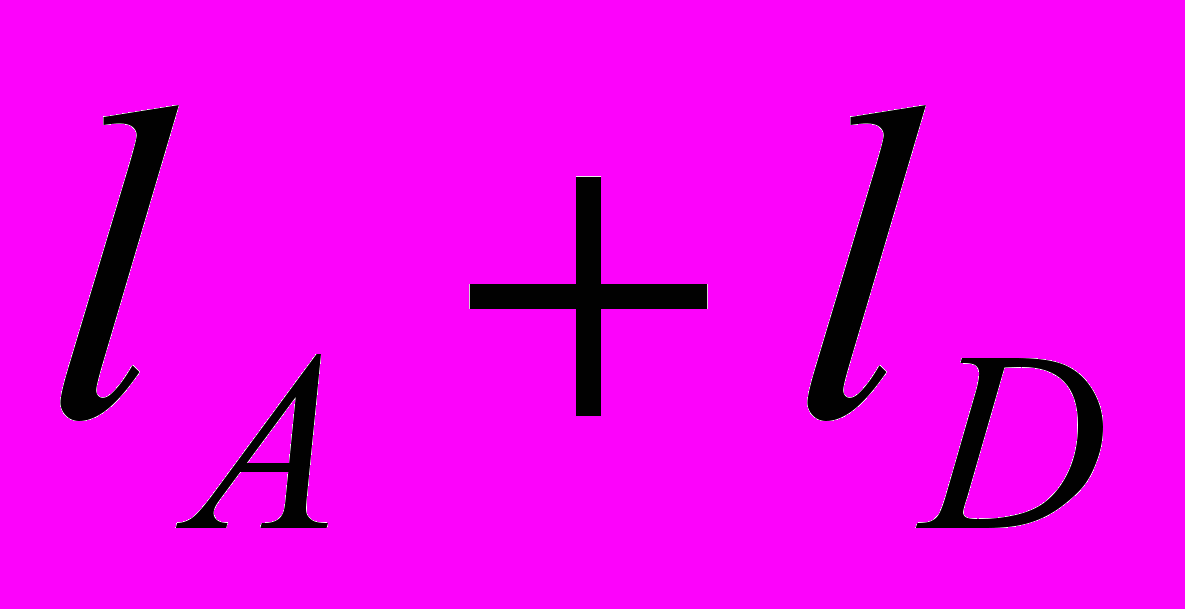
Дельта-метод (рис. 20, в) основан на приеме преобразователем для продольных волн 4, расположенным над дефектом, рассеянных на дефекте волн, излученных преобразователем для поперечных волн 2.
Дифракционно-временной метод (рис. 20, г), в котором излучатели 2 и 2, приемники 4 и 4 излучают и принимают либо продольные, либо поперечные волны, причем могут излучать и принимать разные типы волн. Преобразователи располагают так, чтобы получать максимумы эхо-сигналов волн, дифрагированных на концах дефекта. Измеряют амплитуды и время прихода сигналов от верхнего и нижнего концов дефекта.
Реверберационный метод (рис. 20, д) использует влияние дефекта на время затухания многократно отраженных ультразвуковых импульсов в контролируемом объекте. Например, при контроле клееной конструкции с наружным металлическим слоем и внутренним полимерным слоем дефект соединения препятствует передаче энергии во внутренний слой, что увеличивает время затухания многократных эхо-сигналов во внешнем слое. Отражения импульсов в полимерном слое обычно отсутствуют вследствие большого затухания ультразвука в полимере.
В комбинированных методах используют принципы как прохождения, так и отражения акустических волн.
Зеркально-теневой метод основан на измерении амплитуды донного сигнала. На рисунке 21, а отраженный луч условно смещен в сторону. По технике выполнения (фиксирует эхо-сигнал) его относят к методам отражения, а по физической сущности контроля (измеряют ослабление сигнала дважды прошедшего изделие в зоне дефекта) он близок к теневому методу.
Эхо-теневой метод основан на анализе как прошедших, так и отраженных волн (рис. 21, б).
В эхо-сквозном методе фиксируют сквозной сигнал I, сигнал II, испытавший двукратное отражение в изделии, а в случае появления полупрозрачного дефекта - также сигналы III и IV, соответствующие отражениям волн от дефекта и испытавших также отражение от верхней и нижней поверхностей изделия. Большой непрозрачный дефект обнаруживают по исчезновению или сильному уменьшению сигнала I, т.е. теневым методом, а также сигнала II. Полупрозрачные или небольшие дефекты обнаруживают по появлению сигналов III и IV, которые являются главными информационными сигналами.
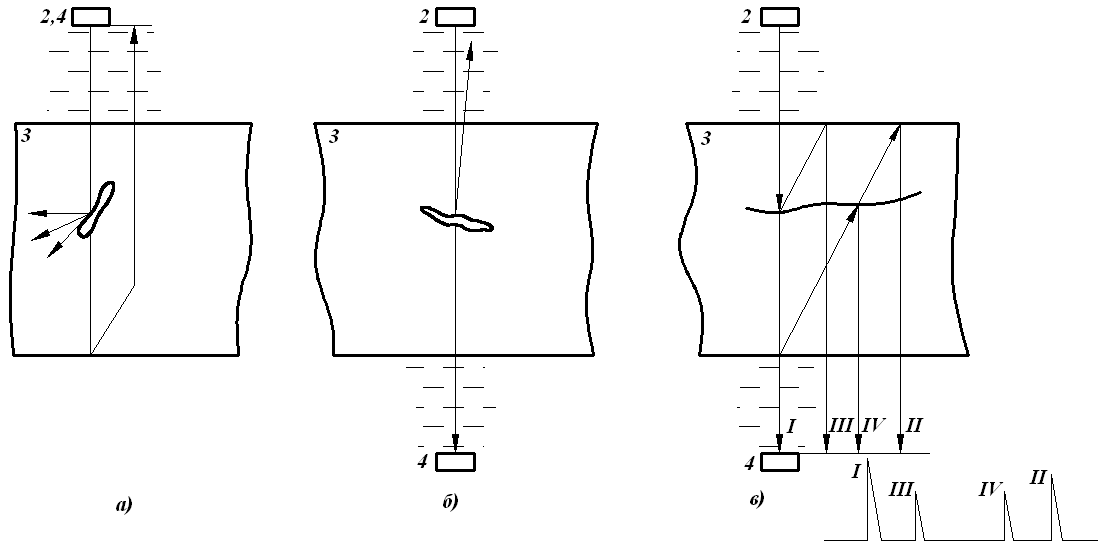
Рис. 21. Комбинированные методы, использующие прохождение и отражение: а - зеркально-теневой; б – эхо - теневой; в – эхо - сквозной:2 - излучатель; 4 - приемник; 3 - объект контроля
Методы собственных частот основаны на измерении этих частот (или спектров) колебаний контролируемых объектов. Собственные частоты измеряют при возбуждении в изделиях как вынужденных, так и свободных колебаний. Свободные колебания обычно возбуждают механическим ударом, вынужденные - воздействием гармонической силы меняющейся частоты.
Импедансные методы используют зависимость импедансов изделий при их упругих колебаниях от параметров этих изделий и наличия в них дефектов. Обычно оценивают механический импеданс
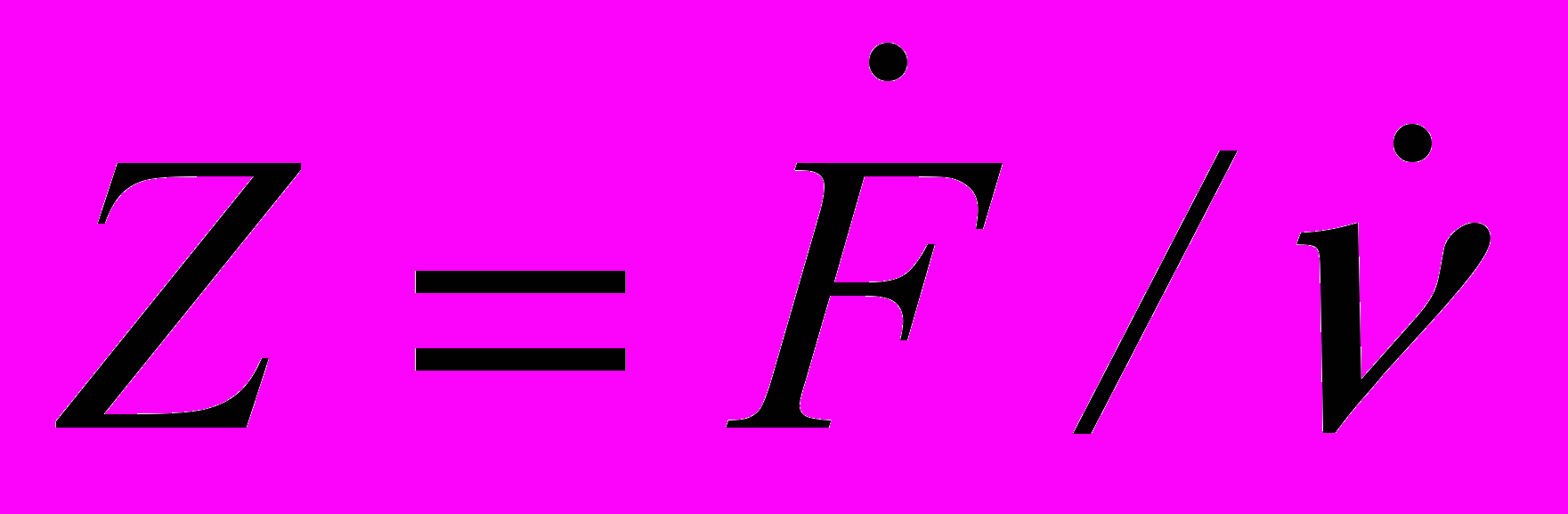
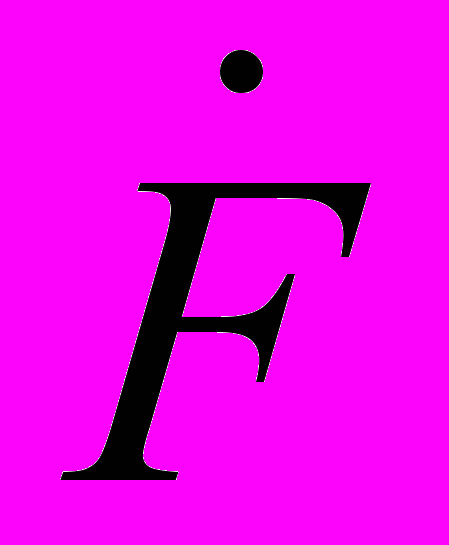
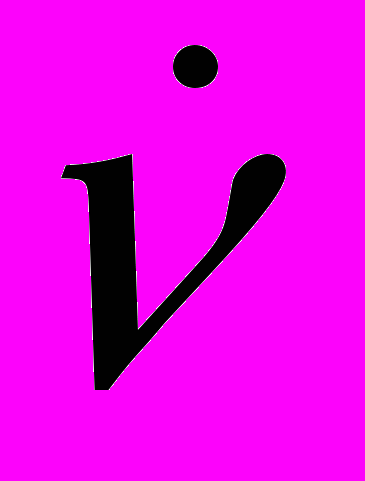
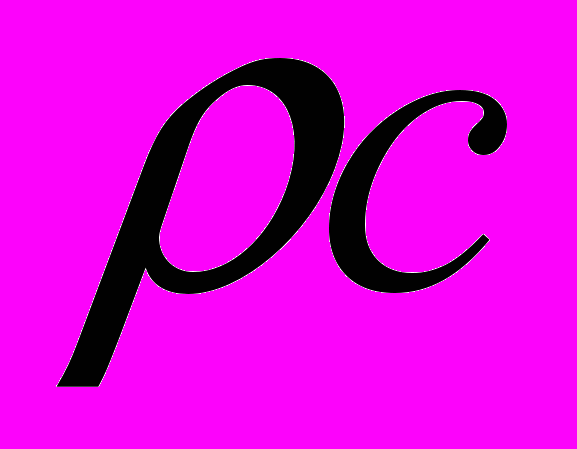
Пассивные акустические методы основаны на анализе упругих колебаний волн, возникающих в самом контролируемом объекте.
Наиболее характерным пассивным методом является акустико-эмиссионный метод. Явление акустической эмиссии состоит в том, что упругие волны излучаются самим материалом в результате внутренней динамической локальной перестройки его структуры. Такие явления, как возникновение и развитие трещин под влиянием внешней нагрузки, аллотропические превращения при нагреве или охлаждении, движение скоплений дислокаций,- наиболее характерные источники акустической эмиссии. Контактирующие с изделием пьезопреобразователи принимают упругие волны и позволяют установить место их источника (дефекта).
Пассивными акустическими методами являются вибрационно-диагностический и шумодиагностический. При первом анализируют параметры вибраций какой-либо отдельной детали или узла (ротора, подшипников, лопатки турбины) с помощью приемников контактного типа, при втором - изучают спектр шумов работающего механизма, обычно с помощью микрофонных приемников.
По частотному признаку акустические методы делят на низкочастотные и высокочастотные. К первым относят колебания в звуковом и низкочастотном (до нескольких десятков кГц), ультразвуковом диапазонах частот. Ко вторым - колебания в высокочастотном ультразвуковом диапазоне частот: обычно от нескольких сот кГц до 20 МГц. Высокочастотные методы обычно называют ультразвуковыми.
Области применения
Из рассмотренных акустических методов контроля наибольшее практическое применение находит эхо-метод. Около 90% объектов, контролируемых акустическими методами, проверяют эхо-методом. Применяя различные типы волн, с его помощью решают задачи дефектоскопии поковок, отливок, сварных соединений, многих неметаллических материалов. Эхо-метод используют также для измерения размеров изделий. Измеряют время прихода донного сигнала и, зная скорость ультразвука в материале, определяют толщину изделия при одностороннем доступе. Если толщина изделия неизвестна, то по донному сигналу измеряют скорость, оценивают затухание ультразвука, а по ним определяют физико-механические свойства материалов.
Эхо-зеркальный метод также применяют для выявления дефектов, ориентированных перпендикулярно поверхности ввода. При этом он обеспечивает более высокую чувствительность к таким дефектам, но требует, чтобы в зоне расположения дефектов был достаточно большой участок ровной поверхности (рис. 21, б). В рельсах, например, это требование не выполняется, поэтому там возможно применение только зеркально-теневого метода. Дефект может быть выявлен совмещенным наклонным преобразователем, расположенным в точке А. Однако, в этом случае зеркально-отраженная волна уходит в сторону и на преобразователь погадает лишь слабый рассеянный сигнал. Преобразователи, расположенные в точках С или D обнаруживают дефект с высокой чувствительностью.
Эхо-зеркальный метод в варианте "тандем" используют для выявления вертикальных трещин и непроваров при контроле сварных соединений. Дефекты некоторых видов сварки, например, непровар при электронно-лучевой сварке, имеют гладкую отражающую поверхность, очень слабо рассеивающую ультразвуковые волны, но такие дефекты хорошо выявляются эхо-зеркальным методом. Дефекты округлой формы (шлаковые включения, поры) дают большой рассеянный сигнал и хорошо регистрируются совмещенным преобразователем в точке А, в то же время зеркальное отражение от них слабое. В результате сравнения отраженных сигналов в точках А и D определяют форму дефекта сварного соединения.
Вариант "косой тандем" применяют, когда расположение преобразователей в одной плоскости затруднительно. Его используют, например, для выявления поперечных трещин в сварных швах. Преобразователи в этом случае располагают по разные стороны валика усиления шва. Углы
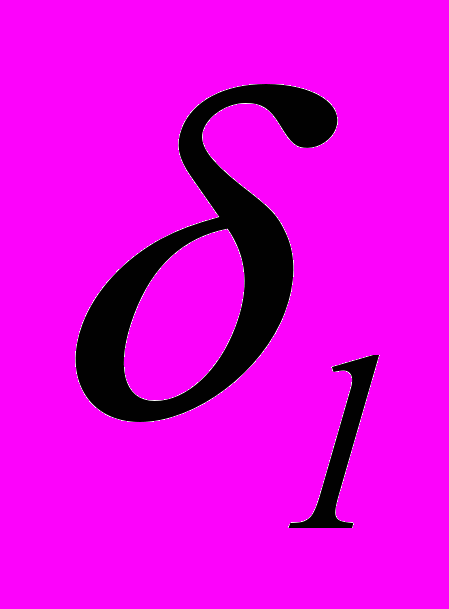
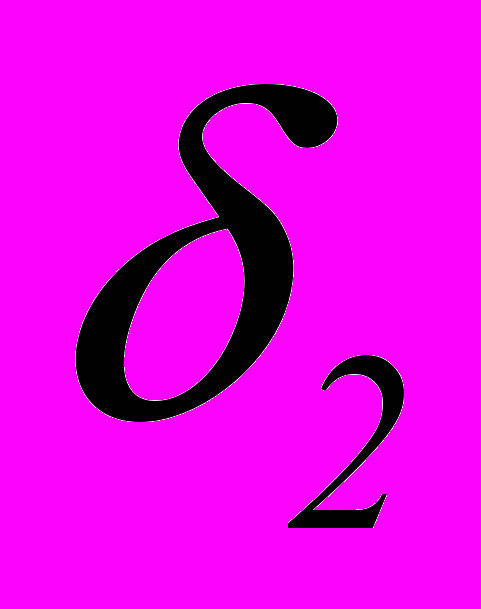
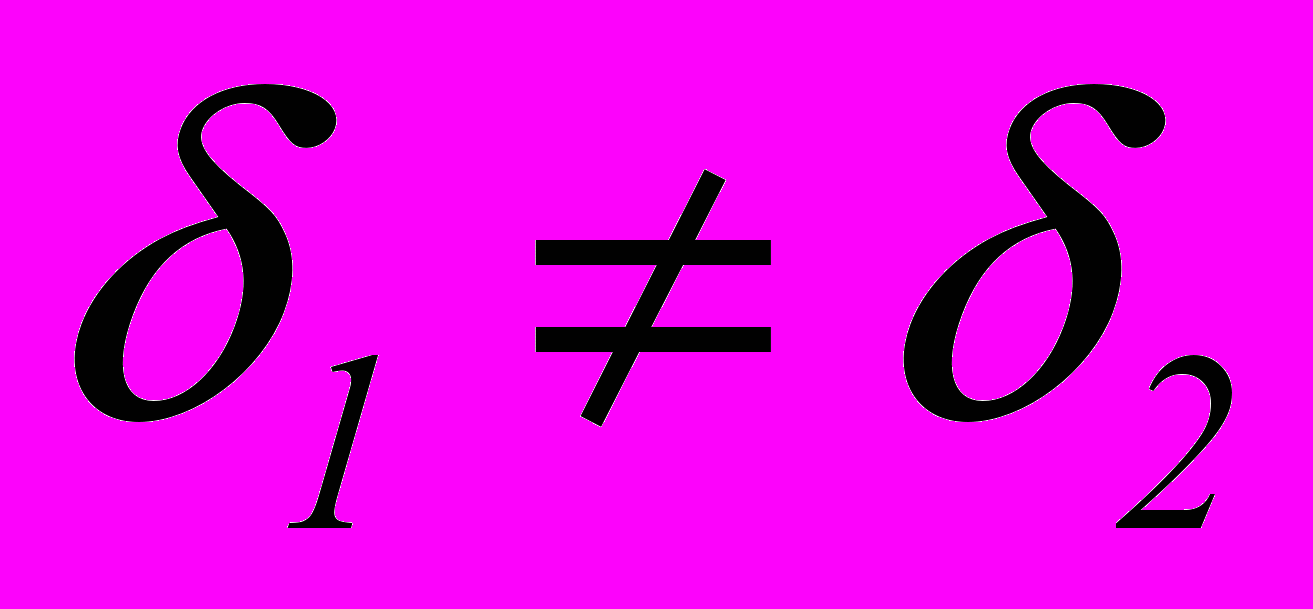
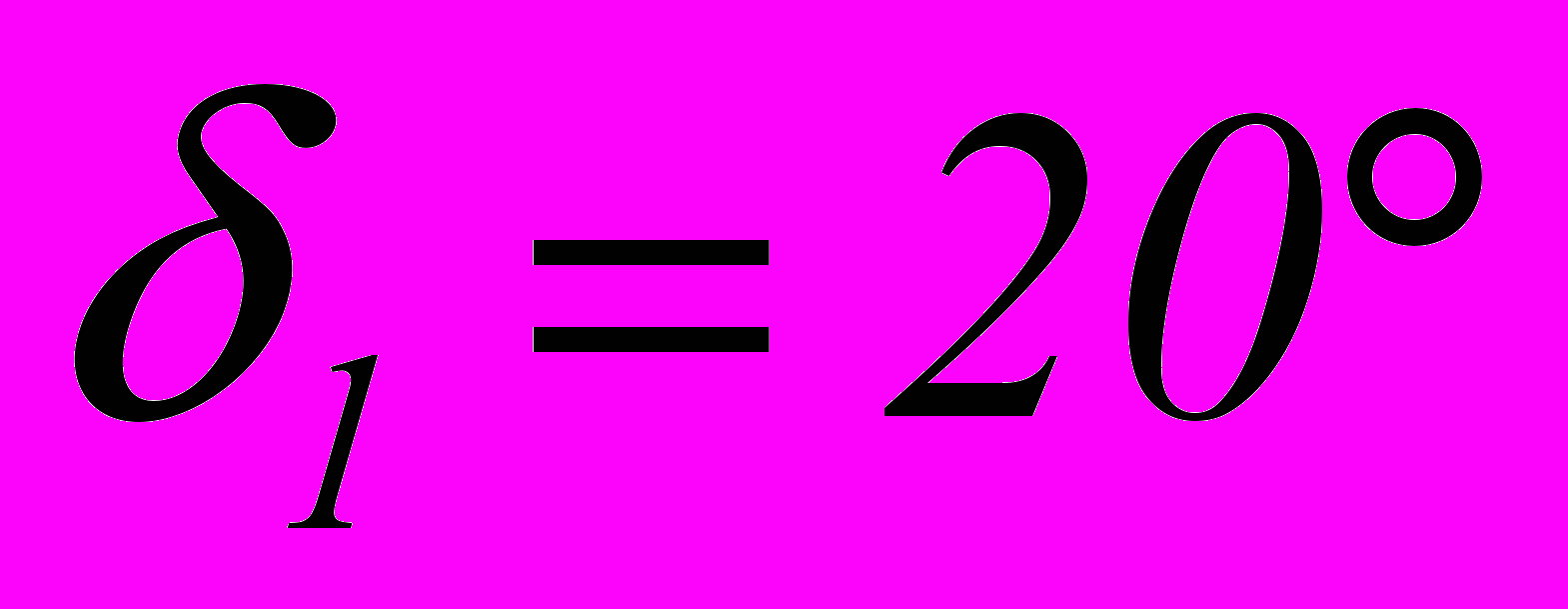
Дельта и дифракционно-временной методы также используют для получения дополнительной информации о дефектах при контроле сварных соединений. В варианте, показанном на рисунке 2,в, излучают поперечные, а принимают продольные волны. Эффективная трансформация волн на дефекте произойдет, если угол падения на плоский дефект меньше третьего критического, либо если продольная волна возникает в результате рассеяния на дефекте. Для создания хорошего контакта приемного прямого преобразователя с поверхностью сварного соединения валик усиления зачищают. С помощью этого метода довольно точно определяют положение дефекта вдоль сварного шва, что важно для его автоматической регистрации.
Лекция 6
контроль и диагностика трубопроводов
В связи с наличием множества возможных дефектов по виду и причинам образования, существует большое многообразие средств и методов их контроля. Наиболее оптимальной является комплексная последовательная методика контроля технического состояния трубопровода:
1 этап визуальный контроль;
2 этап контроль наличия дефектов геометрии;
3 этап контроль сплошности материала;
4 этап контроль состояния сварных швов.
1 этап визуального контроля связан с необходимостью определения местоположения трубопровода, участков оголения, провисания и нарушение изоляции. 2,3 и 4 этапы реализуются с помощью внутритрубных инспекционных снарядов (ВИС).
С 1995 года началась планомерная внутритрубная диагностика МНГП. Выявление дефектов в стенке трубы с указанием их точного местоположения, оценка их опасности и при необходимости «точечный» ремонт – в этом заключается новый метод профилактики МНГП.
Внутритрубная диагностика
При внутритрубной диагностике выявляются следующие дефекты стенки трубы:
1) дефекты, образовавшиеся при изготовлении труб, - расслоения, закаты, включения, дефекты продольных сварных стыков.
2) дефекты, образовавшиеся при строительстве трубопровода, - риски, задиры, вмятины, гофры, дефекты кольцевых стыков.
3) дефекты, образовавшиеся при эксплуатации - внешняя и внутренняя коррозия, усталостные трещины тела трубы и сварных стыков по причине воздействия малоцикловых нагрузок.
Для определения скорости коррозии проводится диагностика трубопроводов с интервалом в 3-5 лет. Сравнение результатов повторной диагностики с первичной позволяет рассчитать время утончения стенки трубы до критической величины.
Необходимая полнота контроля участка МН должна достигаться на основе реализации 4-х уровневой системы диагностирования, предусматривающей определение параметров дефектов и особенностей трубопровода, выходящих за пределы допустимых значений.
4-х уровневая система диагностирования:
- Выявление дефектов геометрии трубопровода, ведущих к уменьшению его проходного сечения (вмятины, гофры, овальность сечения, выступающие внутрь трубы элементы);
- Дефекты потери металла, уменьшающих толщину стенки трубопровода (коррозионные язвы, царапины, вырывы металла), а также расслоения и посторонние включения в стенке трубы;
- Поперечные трещины в теле трубы и кольцевых сварных швах;
- Продольные трещины в теле трубы и продольных сварных швах.
Перед проведением обследования эксплуатирующие предприятия проводят следующие подготовительные работы:
- проверка работы запорной арматуры;
- проверка работы концевых затворов камер запуска и приема, узлов их обвязки;
- определение необходимого числа и мест установки маркеров;
- подготовка участка трубопровода к обследованию – очистка внутренней полости.
Для получения качественной информации при проведении внутритрубной диагностики внутреннюю полость трубопровода необходимо тщательно очистить от парафино-смолистых отложений, остатков глиняных тампонов, появившихся при ремонте трубопровода, а также от посторонних предметов. Для очистки используют очистные устройства (ОУ) с чистящими дисками, изготовленными из высококачественного полиуретана. Разработаны и серийно выпускаются скребки нескольких типов:
стандартные типа СКР1 с чистящими дисками;
щеточные типа СКР1-1 с чистящими и щеточными дисками;
двухсекционные типа СКР2 с чистящими и щеточными дисками и подпружиненными щетками;
магнитные скребки типа СКРЗ с чистящими дисками и магнитными щетками для сбора металлических предметов из полости трубы (окалина, огарки электродов и т.п.);
скребки повышенной эффективности очистки СКР4.
Основные очистные скребки - типа СКР1. Этими скребками периодически очищают нефтепровод от отложений, а также перед пропуском ВИС.
На заключительной стадии очистки, непосредственно перед пропуском дефектоскопа, очищают трубу путем пропуска не менее двух специальных (щеточных) скребков типа СКР1-1 или двухсекционными СКР2, которые обеспечивают очистку и коррозионных карманов на внутренней поверхности трубы.
Наилучшие условия очистки обеспечиваются при скорости потока около 2м/с. Рекомендуемый порядок пропуска очистных скребков: первый очистной скребок пропускается с открытыми байпас-отверстиями для размыва парафиносмолистых отложений и предупреждения образования парафиновой пробки; второй очистной скребок пропускается с закрытыми байпас-отверстиями и обязательно оснащается передатчиком.
Число пропускаемых ОУ перед проведением ВТД должно определяться достижением результата, при котором последнее ОУ приходит в приемную камеру без механических повреждений корпуса, ведущих и чистящих дисков, а количество принесенных парафинсодержащих примесей и металлических предметов не превышает критериев оценки очистки нефтепроводов. Опыт показывает необходимость 6-14 пропусков ОУ.
На первом уровне диагностирования прежде всего должна быть получена информация об особенностях и дефектах геометрии трубопровода, вызывающих уменьшение его проходного сечения. Для получения такой информации следует использовать комплекс технических средств в составе скребка-калибра и снаряда-профилемера.
Снаряды-калибры позволяют определить минимальное проходное сечение обследуемого участка трубопровода. На секциях снаряда установлены калибровочные диски, содержащие пластины, которые деформируются при наличии в трубопроводе опасных сужений. После извлечения снаряда-калибра из камеры приёма по величине загиба металлических лепестков калибровочного диска оценивается проходное сечение трубопровода.
После успешного пропуска скребка-калибра, т.е. подтверждения необходимого безопасного проходного сечения трубопровода для пропуска ВИП осуществляется пропуск снаряда-профилемера, определяющего дефекты геометрии и особенности положения трубопровода (радиусы кривизны углов поворота трубопровода в плане и профиле). Минимальное проходное сечение трубопровода, необходимое для пропуска профилемера, составляет 70 % внутреннего диаметра трубопровода.
Профилемеры - электронно-механические устройства со множеством щупов, которые касаются внутренней поверхности трубы, отслеживая ее геометрию. Перемещения всех щупов преобразуются в электрический сигнал, который после обработки регистрируется в запоминающем устройстве.
Для определения положения геометрической особенности по окружности трубы в приборе предусматривается устройство для определения местной вертикали (обычно в виде механического маятника с датчиком угла поворота), электрический сигнал которого также регистрируется в запоминающем устройстве прибора.
Для измерения радиусов поворота профилемер чаще всего выполняют двухсекционным, при этом механическое устройство для измерения угла между осями секций встраивают в карданный шарнир.
Внутритрубный профилемер состоит из двух секций - стальных герметичных корпусов, связанных между собой карданным соединением. В передней и задней части первой секции установлены манжеты, предназначенные для центрирования и приведения в движение прибора в трубопроводе. Коническая манжета, установленная на передней секции предотвращает застревание прибора в трубах, имеющих тройное разветвление - «тройниках», не оборудованных предохранительными решетками. В носовой части первой секции установлен бампер, под решеткой которого находится антенна приемопередатчика в защитном кожухе, а на задней части, на подпружиненных рычагах, размещены одометрические колеса, предназначенные для измерения пройденного расстояния.
Для контроля за движением снаряда служат приемопередатчики, а также наземные приборы сопровождения, в состав которых входят локаторы и маркерные передатчики. Локаторные приемники предназначены для слежения за снарядами при их движении по трубопроводу. Приёмопередатчики инспекционных снарядов генерируют низкочастотные электромагнитные сигналы, которые улавливаются антенной локаторного приемника на поверхности.
Маркерные передатчики, сигналы которых улавливаются приемниками снарядов, необходимы для привязки диагностической информации к конкретным точкам трассы нефтепровода.
На второй секции установлены манжеты и измерительная система, состоящая из множества рычагов с колесами (так называемый «спайдер») для измерения проходного сечения и других геометрических особенностей трубы. Колеса спайдера прижимаются к внутренней поверхности трубы и при движении профилемера перекатываются через препятствия, встречающиеся на их пути, перемещая конец рычага, на котором они установлены, что вызывает изменение сигнала.
В запоминающем устройстве профилемера идет одновременная регистрация и хранение пяти параметров:
- данных спайдера (вмятины, гофры);
- угла поворота (ориентация дефекта по периметру трубы);
- сигналов одометра (дистанция в метрах от камеры пуска);
- маркерных передатчиков (для поправки одометрической информации);
- временные отметки (дата и время обнаружения дефекта)
По результатам профилеметрии предприятие, эксплуатирующее участки нефтепровода, должно устранить сужения, уменьшающие проходное сечение менее 85 % от наружного диаметра трубопровода.
Профилемер-топограф с сенсорами рычажного типа.
Профилемер Лайналог с эластичным преобразователем перемещений
Профилемер Рельеф с ультразвуковыми преобразователями
На втором уровне диагностирования должно производиться выявление дефектов типа потери металла, вызывающих уменьшение толщины стенки трубопровода, расслоений, включений в стенке трубы с использованием ультразвукового снаряда-дефектоскопа с радиально установленными в плоскости поперечного сечения трубы ультразвуковыми датчиками.
Дефекты, обнаруживаемые внутритрубным ультразвуковым дефектоскопом типа WM:
дефекты геометрии;
дефекты геометрии, примыкающие к сварным швам или расположенные на сварных швах;
дефекты геометрии в комбинации с потерей металла;
потеря металла точечные, сплошные;
расслоения;
расслоения с выходом на поверхность;
риски, царапины, задиры, вырывы;
смещения поперечного сварного шва труб;
разнотолщинности свариваемых труб;
недопустимые конструктивные элементы, ремонтные конструкции и методы ремонта.
Ультраскан типа WM по своему принципу работы может определять, как правило, только продольные дефекты, а поперечные не определяет.
В ультраскане WM преобразователи устанавливаются перпендикулярно к стенке трубы в гибком носителе, обеспечивающем фиксированный отступ (stand off — SO) между излучающей поверхностью преобразователя и внутренней поверхностью трубопровода. Между датчиком и поверхностью трубы нет непосредственного контакта. Чтобы ввести ультразвуковые волны необходимо обеспечить акустический контакт. Ввод ультразвуковых колебаний осуществляется через слой жидкости (т.е. нефть играет роль контактной смазки).
После излучения датчиком ультразвукового импульса происходит отражение ультразвукового сигнала сначала от внутренней, а затем от внешней стенки трубы. Отраженные сигналы фиксируются тем же датчиком. Время прихода первого отраженного сигнала преобразуется в расстояние от датчика до внутренней поверхности стенки трубы. Время прихода второго отраженного сигнала при известной скорости распространения звука в металле (5850) преобразуется в толщину стенки трубы.
В случае наружной коррозии время прохождения сигнала в стенке трубы уменьшается, что дает непосредственно количественную меру потери металла. В случае внутренней коррозии увеличивается время прохождения сигнала в нефти. Ультразвуковой дефектоскоп уверенно обнаруживает расслоения.
Минимальное проходное сечение трубопровода, необходимое для пропуска ультраскана, составляет 85 % внутреннего диаметра трубопровода.
Для трубопроводов диаметром 1220/1020 мм дефектоскоп выполнен двухсекционным, диаметром 820 мм и менее он состоит из трех-пяти секций. В передней части ведущей секции установлен бампер, закрывающий антенну приемопередатчика, находящуюся в защитном кожухе. Каждая секция и носитель датчиков снабжены полиуретановыми манжетами, предназначенными для центрирования и обеспечения движения прибора по трубопроводу потоком перекачиваемого продукта. На корпусе размещены также конические манжеты, служащие для предотвращения застревания прибора в тройниках, не оборудованных предохранительными решетками. В задней части секции электроники на подпружиненных рычагах установлены два одометрических колеса.
Для того чтобы на датчиках не откладывались парафиносмолистые отложения, конструкцией прибора предусмотрен проток перекачиваемого продукта через каналы полозов.
Количество датчиков для 1220 мм дефектоскопа - 448. Вдоль оси трубы опрос ведется через 3,3 мм при скорости движения прибора 1 м/с. Таким образом, обеспечивается толщинометрия всей внутренней поверхности трубы за один прогон прибора. Информация от каждого датчика обрабатывается бортовыми компьютерами, сжимается и записывается в накопителях информации одновременно с информацией одометрических колес, местной вертикали, времени и поступающими сигналами маркеров (60 Гбайт на 200 км). После окончания прогона по участку трубопровода и извлечения дефектоскопа из камеры приема информация считывается из накопителей и поступает на обработку.
На третьем уровне диагностирования должно производиться выявление поперечных трещин и трещиноподобных дефектов в кольцевых сварных швах с использованием магнитного снаряда-дефектоскопа (магнескан MFL).
Магнитный контроль основан на индикации эффекта взаимодействия магнитного поля с контролируемым объектом, изготовленным из ферромагнитного материала.
При движении снаряда система из постоянных магнитов намагничивает участок трубы. Наличие тех или иных особенностей в намагниченном металле стенки трубы вызывает искажение линий магнитного потока (рассеяние магнитного потока), которое фиксируется системой электромагнитных датчиков и регистрируется для последующей обработки.
Магнитный контроль проводится в приложенном или остаточном магнитном поле. Магнитное поле должно быть перпендикулярно направлению дефекта. Принципиальная схема работы магнитного дефектоскопа позволяет определять все поперечные дефекты трубопроводов, пропуская продольные трещины.
В магнитных приборах, используемых при проведении внутритрубной дефектоскопии, индикация магнитных полей рассеяния осуществляется специальными магниточувствительными датчиками, установленными на упругих носителях и сканирующими внутреннюю поверхность трубопровода. Показания датчиков преобразуются в электрические сигналы, регистрируемые запоминающей системой прибора.
Основными являются датчики I типа. Они находятся в мощном магнитном поле и служат для обнаружения особенностей трубопровода и определения размеров дефектов типа «потеря металла» и «аномалия поперечного сварного шва». Датчики представляют собой электромагнитные катушки. В трубах с постоянной (номинальной) толщиной стенки не происходит рассеяние магнитного потока за пределы поверхности трубы, и датчики не регистрируют сигнал. В зоне дефекта постоянный магнитный поток, созданный магнитами дефектоскопа, искажается, датчик реагирует на магнитный поток рассеяния, что вызывает появление в цепи датчика электрического тока, величина которого зависит от размеров и формы дефекта.
Датчики II типа находятся в слабом, локальном магнитном поле, которое проникает только в поверхностный слой металла, и служат для определения на какой поверхности трубы расположен дефект – на внутренней или на внешней. Принцип их работы аналогичен датчикам I типа. В нижнюю часть блока датчиков этого типа встроены небольшие постоянные магниты, сфера действия которого позволяет обнаружить наличие особенностей только в области внутренней поверхности трубы.
Датчики III типа предназначены для измерения абсолютной величины магнитного поля на внутренней поверхности трубопровода. По их показаниям рассчитывается номинальная толщина стенки трубы. Датчик представляет собой полупроводниковую микросхему, использующую эффект Холла.
Современные магнитные приборы высокого разрешения способны выявлять как дефекты потери металла, вызывающие уменьшение толщины стенки трубопровода, так и дефекты в сварных швах, и определять, на какой поверхности находятся дефекты потери металла - наружной или внутренней, но не обнаруживают продольные дефекты.
Продольное намагничивание до полного насыщения стенки трубопровода осуществляется мощными постоянными магнитами, установленными на корпусе передней (магнитной) секции снаряда. Замыкание магнитного потока на стенку трубы производится через гибкие магнитопроводы, выполненные в виде стальных щеток.
Первое кольцо датчиков, расположенное между полюсами магнитов, образуют датчики двух типов - 1 и 3. Основную часть из них составляют высокочувствительные индуктивные датчики типа 1. Датчики 3 типа в 20 раз меньше, чем датчиков типа 1.
На второй (приборной) секции магнитного дефектоскопа имеется кольцо датчиков типа 2, аналогичных датчикам типа 1, но обладающих меньшей чувствительностью и реагирующих только на дефекты потери металла, имеющиеся на внутренней поверхности трубопровода. По сигналам датчиков типа 1 и типа 2 можно определить, на какой поверхности - внутренней или наружной находится особенность (дефект).
Для того чтобы обеспечить беспрепятственное прохождение прибора через сужения, датчики устанавливаются на упругих носителях, которые могут перемещаться относительно корпуса прибора, приспосабливаясь к геометрии трубопровода.
Передняя секция удерживается в центре трубы с помощью щеток магнитного контура, а также поддерживающих колес, расположенных по окружности и поджимаемых к стенке трубы с помощью пружин. Спереди и сзади секции размещены манжеты, предназначенные для приведения дефектоскопа в движение.
Вторая секция дефектоскопа содержит систему обработки и записи данных, батареи. На внешней части корпуса расположены: второе кольцо датчиков, датчики температуры и давления, элементы электроники. Сзади установлены также три одометрических колеса.
Магнитный дефектоскоп имеет бортовую систему записи данных, в состав которой входит счетчик реального времени. Бортовое время магнитного дефектоскопа перед прогоном синхронизируется со временем используемого при подготовке персонального компьютера и с приборами маркерной системы - маглоггерами. Маглоггеры, расставляемые в маркерных точках, реагируют на магнитное поле, создаваемое прибором и регистрируют время его прохождения. После прогона дефектоскопа информацию с маглоггеров переписывают на компьютер и используют при обработке данных для определения местоположения дефектов.
Опрос датчиков I и II типа производится через каждые 3,3 мм, датчики III типа опрашиваются через каждые 100 мм дистанции. Опрос не зависит от скорости движения прибора в диапазоне рабочих скоростей от 0,35 до 4 м/с.
На четвертом уровне диагностирования должно производиться выявление продольных трещин в стенке трубы, трещин и трещиноподобных дефектов в сварных швах с применением комплекса технических средств в составе ультразвукового снаряда-дефектоскопа типа CD с наклонно расположенными в плоскости поперечного сечения трубы ультразвуковыми датчиками.
Дефекты, выявляемые внутритрубным ультразвуковым дефектоскопом типа CD:
дефекты геометрии без дополнительных дефектов и примыкания к сварным швам;
дефекты геометрии примыкающие к сварному шву или расположенные на сварном шве;
риски, царапины, задиры;
трещины по телу трубы или в сварных швах.
дефекты сварных швов, смещение поперечных и продольных швов.
расслоения с выходом на поверхность
дефекты поверхности (неоднородности поверхности).
Принцип обнаружения трещин, реализованный во внутритрубном ультразвуковом дефектоскопе типа CD заключается во введении наклонного ультразвукового луча в тело трубы. Угол падения луча (наклона датчика) выбирается таким, чтобы угол распространения преломленного луча в стенке трубы составлял 45 к поверхности трубы. В зависимости от типа нефти угол ввода УЗ луча составляет от 15 до 21 от вертикали.
При контроле дефектов, ориентированных перпендикулярно стенке трубы, и дефектов в сварных швах используются наклонные преобразователи. Для этого преобразователи устанавливаются в специальных призмах, изготовленных из оргстекла. Преобразователь в комплекте с такой призмой называется призматическим искателем. На границе между призмой и изделием происходит преломление луча ультразвуковых волн. Контроль дефектов в сварных швах может осуществляться прямым или однократно отраженным лучом. Чем меньше толщина контролируемого изделия, тем больше должен быть угол ввода луча.
Носитель датчиков ультразвукового дефектоскопа CD сконструирован таким образом, чтобы за один пропуск сканировался весь периметр трубы. Для обнаружения продольных трещин используется носитель с поперечным наклоном датчиков, а для обнаружения поперечных трещин – с продольным наклоном. Кроме того, часть датчиков расположена перпендикулярно стенке трубы для осуществления толщинометрии. Это необходимо для измерения реальной толщины стенки, а также для обнаружения поперечных швов и арматуры, что требуется для точной привязки дефектов.
Для обнаружения продольных трещин используется большое число датчиков, расположенных под углом к осевой плоскости трубы, половина которых сканирует в одном направлении, а половина - в другом. Число датчиков подобрано таким, что каждый следующий датчик сдвинут на половину диаметра датчика в сторону прозвучивания; кроме того, сканирование осуществляется в обе стороны. При этом обеспечивается избыточное сканирование всех участков стенки трубы, благодаря чему осуществляется более надежное обнаружение трещин на фоне возможных ложных сигналов из-за изменений геометрии стенки трубы.
В реальности число датчиков, например для прибора 28" (труба диаметром 720 мм), составляет 480 датчиков, расположенных на 16 полозах, при этом 240 датчиков сканируют по часовой стрелке, 240 - против часовой стрелки. На каждом полозе установлены два датчика для осуществления толщинометрии.
На вход УЗ датчика приходит очень сложный отраженный сигнал, из которого необходимо извлечь полезную информацию о наличии трещин и их параметрах. Это достигается обработкой приходящего сигнала электронными и программными средствами на борту прибора. Вследствие необходимости использования большого числа датчиков, а также сложных алгоритмов обработки информации резко возрастают объем электроники, потребляемая мощность и, как следствие, число секций и длина внутритрубного дефектоскопа.
На МГ ультразвуковая дефектоскопия применяется достаточно редко.