Лекция 1 введение диагноз в переводе с греческого «диагнозис»
Вид материала | Лекция |
- И в переводе на русский язык означает исследование, 35.4kb.
- Термические ожоги. Классификация и прогноз, сортировка пострадавших Введение, 66kb.
- Лекция №1. Предмет физики. Физические измерения, 265.16kb.
- Тема: "Биология", 88.38kb.
- Шпаргалка по педагогике (для педагогов) Понятие педагогики и этапы ее развития, 2042.12kb.
- В середине XIX столетия появилось новое течение в геометрии топология. «Топология», 171.1kb.
- План практических занятий по неонатологии для студентов 6 курса педиатрического факультета, 37.57kb.
- «Отечественная история»», 1938.89kb.
- Тема Научные основы экономического анализа, 3309.82kb.
- Науч рук В. В. Инютин библейские мотивы в драме, 126.32kb.
Капиллярный контроль (цветная дефектоскопия ПВК)
Капиллярный метод контроля предназначен для обнаружения поверхностных (выходящих на поверхность) и сквозных дефектов типа трещин, подрезов, несплавлений, незаваренных кратеров, прожогов, неметаллических включений, расслоений и т.п. и определения их расположения, протяженности и ориентации по поверхности.
К контролируемой поверхности должен быть обеспечен доступ, необходимый для нанесения индикаторного пенетранта, его удаления, нанесения проявителя и визуального осмотра индикаторного следа.
На контролируемой поверхности не должно быть следов масел, пыли и других загрязнений.
Дефектоскопические материалы используются в виде наборов в аэрозольных упаковках, включающих:
- индикаторный пенетрант;
- очиститель объекта контроля от пенетранта;
- проявитель индикаторного следа дефекта.
Подготовка поверхности контролируемого объекта производится путем последовательного выполнения следующих операций:
- зачистка поверхности контролируемого объекта от загрязнений;
- очистка полостей дефектов обезжириванием (ацетоном) с целью удаления следов масел, смазок и других загрязнений, с последующей протиркой чистой сухой безворсовой х/б тканью.
Нанесение индикаторного пенетранта на контролируемую поверхность производится при помощи аэрозольного баллона. Не допускается высыхание индикаторного пенетранта на поверхности.
Удаление индикаторного пенетранта производится с помощью соответствующего очистителя с последующей протиркой чистой сухой тканью.
Жидкий проявитель наносится тонким равномерным слоем с помощью аэрозольного баллона сразу после очистки контролируемой поверхности от пенетранта.
Осмотр контролируемой поверхности проводится 2 раза: сразу после высыхания проявителя и через 20 минут после первого осмотра. Обнаружение дефекта проводится визуально по яркому цветному индикаторному следу, образующемся на белом фоне проявителя, размер которого в любом направлении превышает 2,0 мм.
Лекция 3
ВИБРОДИАГНОСТИЧЕСКИЙ МЕТОД КОНТРОЛЯ
ТЕХНИЧЕСКОГО СОСТОЯНИЯ ОБОРУДОВАНИЯ
Вибродиагностический метод контроля технического состояния машин (вибродиагностика) является одним из информативных и доступных методов диагностики. Применительно к оборудованию НПС вибродиагностика позволяет контролировать техническое состояние магистральных и подпорных насосных агрегатов в режиме постоянного слежения за уровнем вибрации, а также оценивать работоспособность вентиляторов, насосов, систем охлаждения, маслоснабжения, отопления, откачки утечек и прочего оборудования путем периодического измерения и анализа параметров вибрации.
Широкое развитие вибродиагностики объясняется следующими факторами:
- доступностью установки датчиков вибрации на магистральных и подпорных насосных агрегатах, малыми габаритами и массой датчиков;
- возможностью осуществления постоянного автоматизированного контроля за техническим состоянием объекта путем непрерывного измерения и оценки вибрации, а в случае ее достижения предельных величин осуществлять «защиту» объекта путем подачи сигнала на аварийную остановку машины;
- большой информативностью параметров вибрации, позволяющей идентифицировать гидромеханические, механические и магнитно-электрические источники колебаний и распознавать многие неисправности;
- возможностью контролировать качество монтажа и ремонта оборудования.
Величина вибрации является одним из важных критериев, определяющих эксплуатационную надежность насосных агрегатов НА и другого оборудования НПС.
Вибрация – это колебания относительно неподвижной точки. Это результат динамических сил, проистекающих в машинах, которые имеют подвижные части. Различные части машины вибрируют на разных частотах и с различной амплитудой. Вибрация, как правило, вызывает износ и усталость механизмов, и зачастую, влияет на полный вывод механизма из работоспособного состояния.
Диагностирование состояния машин и оценка степени опасности повреждения на основе данных контроля вибрации - один из наиболее эффективных методов повышения надежности оборудования.
Вибрационное диагностирование объектов проводится в три этапа: первичное описание вибрационного состояния объекта, выделение признаков и принятие решения.
На этапе поиска информативных признаков ограничивают число измеряемых параметров вибрации, шума и ударов. При этом из множества параметров, характеризующих вибрационный процесс, выделяют только те, которые прямо или косвенно характеризуют состояние объекта. По этим параметрам формируют информативную систему признаков, используемых при диагностировании.
Колебания машин
При эксплуатации насосных агрегатов имеет место два принципиально различных метода измерения вибраций (колебаний) - при помощи датчиков измерения абсолютных колебаний и относительных колебаний. Колебания насосных агрегатов создаются преимущественно их вращающимися частями и пульсациями давления в насосе и подводящих трубопроводах. При этом, главным возбудителем колебаний является неуравновешенность роторов насоса и электродвигателя.
Ротор, имеющий дисбаланс, создает во время вращения свободные центробежные силы, зависимые от частоты вращения. Их величина вычисляется на основе следующего соотношения:
F = u r 2 | |
где F - центробежная сила; u - дисбаланс; r - радиус; - частота вращения.
Вызванные дисбалансом центробежные силы побуждают ротор и вал ротора к колебаниям. Через масляную пленку подшипников скольжения (или через подшипники качения) колебания и усилия передаются на опоры и на фундамент машины. Передаваемые колебания зависят от разных параметров. Самые существенные из них: жесткость и демпфирование масляной пленки, опор и фундаментов, а также масса роторов, опор и фундаментов.
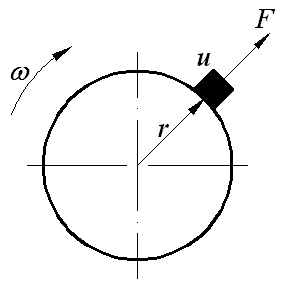
Рис. 1. Схема возникновения свободной центробежной силы F при дисбалансе ротора
Различают колебания трех видов.
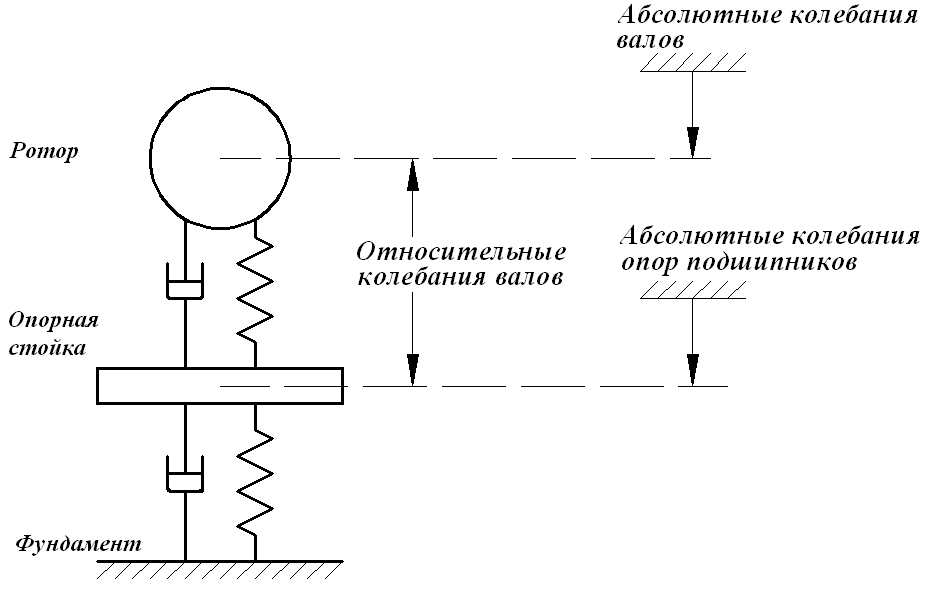
Рис. 2. Виды колебаний у машин
Относительные колебания валов. Это быстрые движения вала ротора по отношению к вкладышу подшипника.
Абсолютные колебания опор подшипников. Под этим подразумеваются быстрые движения вкладыша подшипника и корпуса подшипника по отношению к жесткой опорной точке в пространстве.
Абсолютные колебания валов. Это быстрые движения вала ротора по отношению к жестко установленной опорной точке в пространстве.
В области механических колебаний приняты три измеряемые величины:
- вибросмещение (амплитуда колебаний) s - отклонение точки измерения от положения покоя; единица измерения - мкм (1 мкм = 10-6 м);
- виброскорость v - скорость движения точки измерения вокруг своего положения покоя; единица измерения - мм/с;
- виброускорение а - ускорение движения точки измерения вокруг своего положения покоя; единица измерения - м/с2.
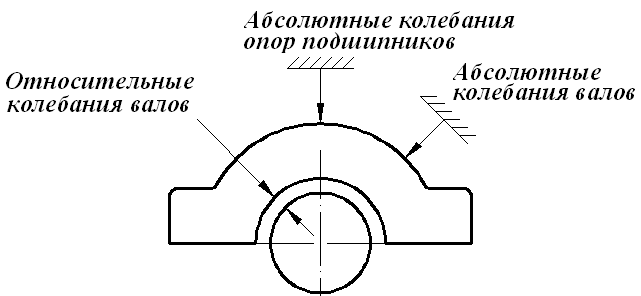
Рис. 3. Виды колебаний и места их измерения (на примере подшипника скольжения)
Чтобы выяснить причины, вызывающие вибрации насосного агрегата, необходимо провести диагностические работы с частотным анализом вибраций насосного агрегата. При частотном анализе с помощью виброизмерительной аппаратуры определяются все частотные составляющие вибраций, которые вызывают колебание машины.
Для правильной интерпретации частотных составляющих вибрации с присущими неисправностями, возникающими в диагностируемом оборудовании, необходимо четко представлять его конструкцию, знать характерные частотные составляющие вибрации, сопутствующие каждому виду неисправности для диагностируемого оборудования, иметь виброизмерительную аппаратуру, позволяющую определять необходимые частотные составляющие вибрации.
Частотный анализ вибраций с помощью виброизмерительной аппаратуры можно осуществлять, в основном, тремя способами: гармоническим анализом вибраций, полосовым выделением частотных составляющих и при применении перестраиваемых фильтров.
При гармоническом анализе вибрации виброизмерительная аппаратура сама определяет частоту вращения ротора машины, настраивает встроенный фильтр на эту частоту и фильтр «пропускает» только ту часть сигнала возмущения, которая соответствует частоте вращения ротора.
Данный способ выделения гармонических составляющих вибрации является наиболее точным, но требует применения (кроме датчика вибрации) датчика, определяющего частоту вращения вала машины (например, фотоэлектрического или лазерного).
Более простым способом выделения частотных составляющих вибрации является применение полосовых фильтров. Встроенные полосовые фильтры настраиваются на определенную частоту, которая зависит от положения переключателя прибора. При этом фильтр пропускает полосу частот, соответствующую его характеристикам. Поэтому, изменяя положение переключателя, мы можем определить, какие частотные составляющие присутствуют в общем уровне вибрации. Под общим уровнем вибрации понимается вся совокупность вибраций, вызванная имеющимися неисправностями в эксплуатируемом оборудовании.
Относительные колебания валов.
Ротор, имеющий дисбаланс, приводит к колебаниям вала. Центр вала движется во время вращения по траектории, именуемой кинетической траекторией вала (рис. 4).
В случае изотропного вала и изотропных подшипников кинетическая траектория, вызванная дисбалансом, составляет круг для каждого сечения ротора. Но обычно подшипники машин анизотропные, т.е. они имеют разную податливость в своих обоих главных направлениях жесткости. Поэтому их кинетическая траектория вала принимает характер эллипса, который в крайнем случае может приобрести форму прямой (см. рис. 5).
Величина, форма и положение кинетической траектории вала изменяется в зависимости от частоты вращения. Обычно кинетические траектории с наибольшим отклонением от оси вращения достигают максимума при критической частоте вращения вала.
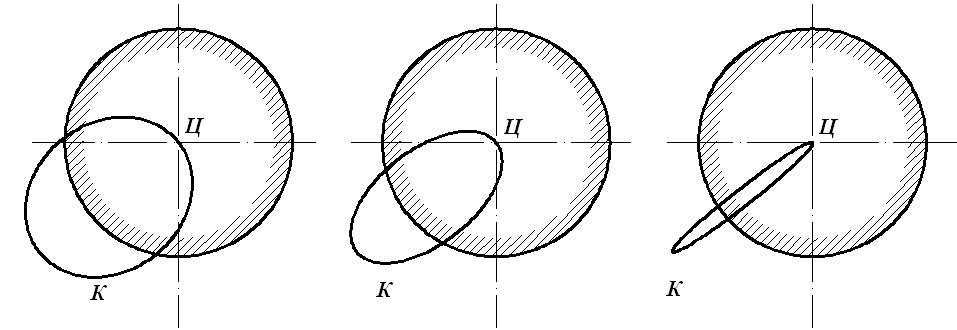
Рис. 4. Кинетическая траектория вала с изотропными (А) и анизотропными (В и С) подшипниками. Ц – центр вала или центр вращения ротора, К - кинетическая траектория вала
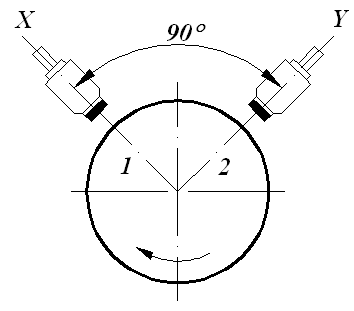
Рис. 5. Схема установки датчиков относительной вибрации для регистрации кинетической траектории вала: 1,2- направления измерений
Для измерения относительных колебаний вала используются бесконтактные датчики вибросмещения, работающие по принципу вихревых токов.
Абсолютные колебания опор
Колебания вала представляют непосредственную реакцию ротора на воздействующие на него переменные усилия. Через реагирующую как пружина пленку масла подшипника скольжения или через тело качения подшипника колебания вала передаются частично на опорную конструкцию, на раму и на фундамент. Эти колебания представляют косвенную реакцию на усилия ротора и называются как «колебания опоры».
При абсолютных колебаниях опор, рассматриваются колебания, возникающие на поверхности машины и, в особенности, при колебаниях вблизи опор или на самих опорах. Эти колебания чаще всего замеряются без особых трудностей в трех координатных направлениях на корпусах подшипниковых опор.
Общие требования к измерению вибрации
Для правильного замера параметров колебаний необходимо соблюдать следующие правила:
- Рабочий частотный и динамический диапазоны не должны быть ограничены в следствие ненадежного крепления акселерометра;
- Добавлении присущей акселерометрам массы не должно обусловить динамических характеристик вибрирующего объекта;
- Места крепления акселерометров должны быть точно определены и должны допускать многократное крепление используемых вибродатчиков;
- Необходимо как можно лучше подготовить поверхность (ровность, гладкость и чистота) исследуемого объекта (связано с собственной частотой колебаний акселерометра);
- Необходимо учитывать совпадение оси максимальной чувствительности закрепленного акселерометра с направлением, соответствующим условиям обследования (для уменьшения поперечной чувствительности акселерометра);
- Места крепления акселерометров нужно выбирать с учетом достижения как можно коротких и определенных путей распространения механических колебаний от источников к вибродатчикам. Между источником колебаний и местами крепления акселерометров должны находится только жесткие элементы, в то время как упругие и/или демпфирующие элементы (пружины, прокладки, крышки) нужно по мере возможности исключить.
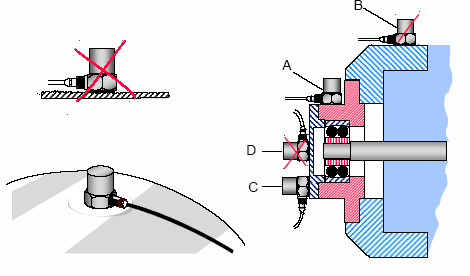
Рис. 6. Выбор позиции акселерометров
Требования к измерениям согласно ГОСТ
Вибрацию опор подшипников насосных агрегатов следует измерять и регистрировать контрольно-сигнальными средствами измерения, соответствующими требованиям ГОСТ 25865 , ГОСТ 17168. Вибрацию на элементах крепления агрегата к фундаменту следует измерять и регистрировать портативными средствами измерения, соответствующими требованиям ГОСТ 25865 и ГОСТ 25275.
Исполнение средств измерения вибрации должно отвечать требованиям ГОСТ 12.2.020, «Правил устройства электроустановок (ПУЭ)», соответствовать классу помещения, категории и группе перекачиваемых взрывоопасных сред по ГОСТ 12.1.011.
Диапазон измерения среднего квадратического значения виброскорости средств измерения вибрации 0-30 мм/с. Класс точности средств измерения вибрации должен быть не более 10 согласно ГОСТ 25865. Средства измерения вибрации должны иметь пломбы и свидетельства ведомственной поверки согласно ГОСТ 8.513-84.
Вибрацию основных магистральных и горизонтальных подпорных насосных агрегатов измеряют и контролируют на всех подшипниковых опорах во взаимно перпендикулярных направлениях. Вертикальную составляющую вибрации измеряют на верхней части крышки подшипника над серединой длины его вкладыша. Горизонтально-поперечную и горизонтально-осевую составляющие вибрации измеряют на уровне оси вала агрегата против середины длины опорного вкладыша. Вибрацию вертикальных подпорных насосных агрегатов измеряют на корпусе опорно-упорного подшипникового узла насоса в вертикальном осевом и горизонтально-поперечном направлениях. Вибрацию всех элементов крепления агрегата к фундаменту измеряют и контролируют в вертикальном направлении.
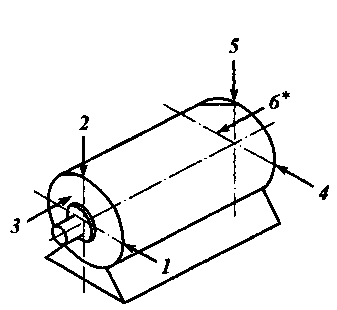
Рис.7. Расположение точек измерения вибрации для машин с высотой оси вращения 56-400 мм насосного агрегата для измерения вибрации в вертикальном направлении
Вибропреобразователи контрольно-сигнальных средств измерения следует крепить механическим способом (с помощью шпилек, винтов и т.д.). При измерении вертикальной составляющей вибрации вибропреобразователь крепится к площадке верхней крышки подшипников, горизонтальной - к специальным площадкам, жестко связанным с корпусом опоры в непосредственной близости к горизонтальному разъему корпуса подшипника.
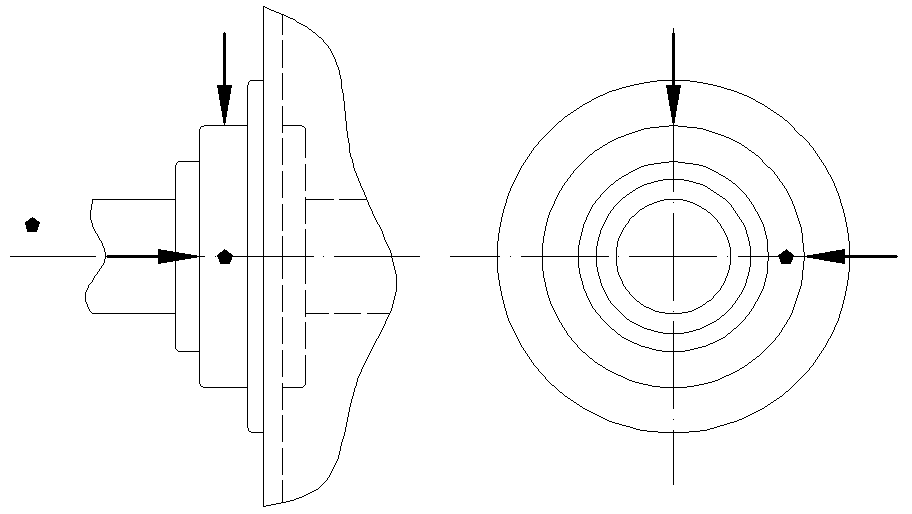
Рис. 8. Расположение точек измерения вибрации для машин с высотой оси вращения более 400 мм (применимо для обеих сторон машины)
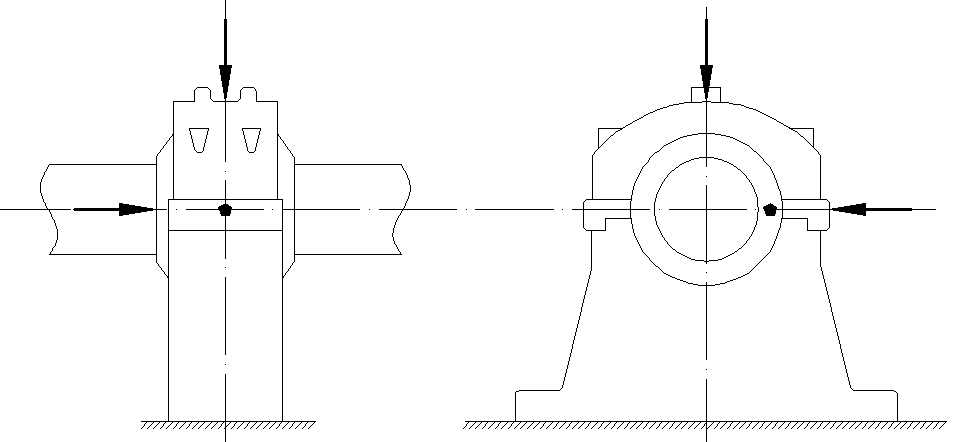
Рис. 9. Расположение точек измерения вибрации для машин с высотой оси вращения более 400 мм со стояковыми подшипниками (применимо для обеих сторон машины)
Лекция 4
НЕФТЯНОЙ НАСОСНЫЙ АГРЕГАТ КАК ОБЪЕКТ ДИАГНОСТИРОВАНИЯ
Конструкцией насоса предусмотрены места для установки вибродатчиков, приборов дистанционного контроля температуры подшипников, утечек жидкости через концевые уплотнения ротора, температуры перекачиваемой жидкости, давления на входе и выходе насоса.
Конструктивно насос и электродвигатель имеют выносные подшипники, корпуса которых используются для установки датчиков вибрации и датчика измерения частоты вращения ротора.
При эксплуатации насосных агрегатов необходимо проводить периодический контроль и оценку интенсивности вибрации агрегата в соответствии с нормами вибрации на них.
В общем случае вибродиагностические работы при эксплуатации насосного агрегата можно представить в следующем виде.
В начале эксплуатации, после окончания ремонтных работ, необходимо провести контроль качества ремонта и паспортизацию начальных его технических параметров. В процессе эксплуатации до момента времени, после которого виброактивность машины превысит оценки «хорошо», проводится периодический экспресс-анализ по общему уровню вибрации. После превышения интенсивности вибрации оценки «хорошо» устанавливается предварительный диагноз, определяется срок очередного проведения обследования и возможность дальнейшей эксплуатации.
При увеличении интенсивности колебаний выше уровня (0,8-0,9) от предельно допустимого проводится техническое обследование с установкой окончательного диагноза, определяется срок и объем ремонтных работ.
В качестве нормируемого параметра вибрации устанавливается среднее квадратическое значение виброскорости.
Таблица 1
Оценка интенсивности вибрации насосного агрегата
Определяющие величины среднего квадратического значения виброскорости,мм /с | Насос | Электродвигатель | ||
Оценка интенсивности вибрации | Оценка длительности эксплуатации | Оценка интенсивности вибрации | Оценка длительности эксплуатации | |
До 2,8 | Отлично | Длительная | Отлично | Длительная |
2,8-4,5 | Хорошо | Длительная | Хорошо | Длительная |
4,5-7,1 (для номи-нальных подач) | Удовлетворительно | Ограниченная | Удовлетворительно | Ограниченная |
4,5 -7,1 (для подач, отличных от номинальной) | Удовлетворительно | Длительная | Удовлетворительно, необходимо улучшение | Ограниченная |
7,1-11,2*(для подач, отличных от номинальной) | Удовлетвори- тельно, необ- ходимо улуч- шение | Ограниченная | Не допускается | Не допускается |
Свыше 11,2 | Не допускается | Не допускается | Не допускается | Не допускается |
* Эксплуатация НА ограничена до замены рабочего колеса насоса на меньшую подачу. |
Условно можно сгруппировать все неисправности по трем направлениям:
- неисправности, связанные с нарушением жесткости крепления машины и ее узлов;
- дефекты электромагнитного происхождения;
- неисправности механического и гидродинамического происхождения.
Неуравновешенность ротора - это состояние ротора, характеризующееся таким распределением масс, которое во время вращения вызывает переменные нагрузки на опоры ротора и его изгиб с частотой, равной частоте вращения ротора
Статическая неуравновешенность ротора - это неуравновешенность ротора, при которой ось ротора и его главная центральная ось инерции параллельна (рис. 10). При этом амплитуда виброскоростей опор ротора на обратной частоте одинаковы и имеют одинаковый фазовфй угол. Такая неуровновешенность полностью определяется главным вектором дисбаланса или эксцентриситетом центра массы ротора, или относительным смещением главной центральной оси инерции и оси ротора, равным значению эксцентриситета центра его массы.
Моментальная неуравновешенность ротора – это неуровновешенность ротора, при которой ось ротора и его главная центральная ось инерции пересекаются в центре масс (см. рис.10).
Моментальная неуравновешенность полностью определяется главным моментом лисбалансов ротора или двумя равными по значению антипараллельными векторами дисбалансов, лежащих в двух произвольных плоскостях, перпендикулярных к оси ротора. Другими словами, на опорах возникают одинаковые по величине и смещению на 1800 амплитуда виброскорости на оборотной частоте.
![]() | Рис. 10. Виды неуравновешенности ротора насоса: а – статическая неуравновешенность; б – динамическая неуравновешенность; в – моментальная неуравновешенность; А, В – подшипниковые узлы; R – усилие реакции подшипниковых узлов; F – главный вектор сил инерции; РР – пара сил моментной составляющей неуравновешенности |
Динамическая неуравновешенность ротора - это неуравновешенность, при которой ось ротора и его главная центральная ось инерции пересекаются не в центре масс или перекрещиваются (см. рис.10).
Динамическая неуравновешенность включает статическую и моментную неуравновешенности и полностью определяется главным вектором и главным моментом дисбалансов ротора или двумя векторами дисбалансов, в общем случае различных по значению и непараллельных, лежащих в двух произвольных плоскостях, перпендикулярных к оси ротора («крест дисбалансов»). При этом амплитуды виброскорости на оборотной частоте, измеряемые на опорах в радиальной плоскости, различаются как по значению, так и по фазе.
Квазистатическая неуравновешенность ротора - это неуравновешенность, при которой ось ротора и его главная центральная ось инерции пересекаются в центре масс ротора. При этом главный вектор дисбалансов ротора перпендикулярен к оси ротора, проходит через центр его масс и лежит в плоскости, содержащей главную центральную ось инерции и ось ротора, а главный момент дисбалансов перпендикулярен к этой плоскости. Дисбалансы ротора лежат в одной плоскости, содержащей ось ротора и его центр масс.
Наиболее распространенными на практике следует считать динамическую и квазистатическую неуравновешенности. Величину неуравновешенности уменьшают путем установки добавочных грузов или снятием металла в одной или двух плоскостях коррекции ротора с целью достижения допустимой величины дисбаланса.
Расцентровка
Следует выделить два возможных варианта расцентровки: расцентровка из-за несовпадения осей валов и расцентровка, обусловленная дефектным изготовлением соединительных муфт. В первом случае необходимо различать расцентровку, связанную с радиальным смещением валов (излом линии вала) и с угловым смещением валов (изгиб линии вала). При радиальном смещении валов (рис.11, а) на концы валов через полу муфты действуют дополнительные изгибающие силы, стремящиеся отклонить валы от осевого первоначального положения, данному отклонению препятствуют подшипниковые опоры, воспринимающие дополнительную нагрузку. Нагрузки, действующие на подшипниковые опоры, противоположны друг другу по направлению и вызывают рост вибрации подшипниковых узлов. Значительные нагрузки возникают при изгибе линии валов (рис. 11, б, в). Однако в данном случае нагрузки могут как совпадать по направлению, так и принимать противоположные направления. Возникающие дополнительные нагрузки на подшипниковые узлы асимметричны и являются суммой статической и динамической составляющих. Последняя является результатом неравномерного силового взаимодействия в зацеплении полумуфт.
Расцентровка, возникающая в результате сборки по дефектным полу муфтам, возникает реже. Возникающие в данном случае дополнительные нагрузки на подшипники аналогичны нагрузкам, возникающим при несовпадении осей валов. Они могут на подшипниковых узлах как совпадать по направлению, так и принимать противоположные направления, т.е. действовать в противофазе. Характерной особенностью данных нагрузок является их динамический характер. Точки приложения нагрузок жестко связаны с полумуфтами и в процессе вращения нагрузки меняют свое направление на 360° за один оборот вала, что приводит к изменению нагрузок на подшипники с частотой, совпадающей с частотой вращения вала соответственно.
![]() | Рис. 11. Схема расцентровок валов типа радиального (а) и углового (б, в) смещений осей: А, В, С, Д – подшипниковые опоры; R – реакции подшипниковых опор; 1,2 – ведомый и ведущий валы; 3 – проставки; 4 – полумуфты |
Наличие расцентровок, приводящих к дополнительным нагрузкам, может служить причиной появления других неисправностей, а именно интенсивного износа вкладышей подшипников скольжения, износа элементов зубчатого зацепления полу муфт, разрушения тел и дорожек качения радиально-упорных подшипников.
При вращении валов, сопряженных муфтами, без перекосов и смещений осей валов, а также при точном изготовлении муфт, все зубцы или пальцы последних нагружены равномерно, и на соединенные валы действуют только вращающие моменты. При наличии неточностей в шагах и форме зацеплений или втулок и пальцев нагрузка на зубцы или пальцы распределяется неравномерно, в результате чего на каждую полумуфту будет действовать радиальная неуравновешенная сила, вращающаяся вместе с муфтой. В предельном случае момент может передаваться ограниченным числом зубьев (пальцев). При этом действующая на вал неуравновешенная сила достигает наибольшего значения. Сила, действующая на палец, вызывает радиальную силу, момент относительно оси муфты. Противоположно направленная радиальная сила приложена к ведущей полумуфте. Эти силы вращаются с муфтой и создают дополнительный изгибающий момент на валу, т.е. в любой осевой неподвижной плоскости вызывают противофазные колебания с частотой вращения. Так как окружное усилие пропорционально передаваемому крутящему моменту, то размах виброперемещения каждого подшипника возрастает пропорционально передаваемой мощности.
В дополнение к указанным неуравновешенным силам действующим на валы при их вращении, перекос или смещение осей валов вызывают силы трения, препятствующие перемещению полумуфт. Эти силы создают периодически изменяющийся момент, который изгибает валы в плоскости перекоса или смещения их осей и вызывает вибрацию подшипников, а также периодически изменяющиеся изгибные напряжения на валах. На вибрацию основной частоты накладываются высокочастотные вибрации из-за неравномерной работы зубцов или пальцев
Муфты с хорошим состоянием рабочих поверхностей обеспечивают нормальную работу агрегата при расцентровке, достигающей значений 0,2-0,3 мм. Расцентровка приводит к быстрому износу элементов муфт.