Учебное пособие Павлодар удк 622 012 (07) ббк 30. 3я7
Вид материала | Учебное пособие |
- Курс лекций Учебное пособие Волгоград 2009 удк 330. 01 Ббк 65. 012., 6756.22kb.
- Учебное пособие Павлодар Кереку 2010 удк 53 (075. 8) Ббк 22. 3я73, 1449.38kb.
- Учебное пособие Павлодар удк339. 9 (075. 8) Ббк 65., 1778.36kb.
- Учебное пособие Павлодар удк 94(574+470. 4/. 5+571. 1)(075. 8) Ббк 63. 3(5Каз+2Рос)5я73, 3633.95kb.
- Врамках программы «Прометей» Павлодар удк 94(574. 25)(075. 8) Ббк 63. 3(5Каз)я73, 3259kb.
- Учебное пособие для студентов естественных специальностей Павлодар, 2290.94kb.
- Учебное пособие разработано в соответствии с государственным стандартом специальности, 1131.24kb.
- Учебное пособие удк 159. 9(075) Печатается ббк 88. 2я73 по решению Ученого Совета, 5335.58kb.
- Практикум Новочеркасск юргту (нпи) 2010 удк 330 (075. 8) Ббк 65. 012. 1я73, 2097.42kb.
- Врамках программы «Прометей» Павлодар удк 94(574. 25) Ббк 63. 3(5Каз), 6238.86kb.
7 Охрана природы и комплексное использование сырья
7.1 Использование отвалов и рекультивация земель
В условиях интенсивного развития горнодобывающей промышленности, когда в эксплуатацию вовлекается все большее число месторождений полезных ископаемых, а мощности горно-обогатительных предприятий увеличиваются, задача сохранения земельного фонда и сложившегося за тысячелетия природного комплекса приобретает исключительно важное значение для охраны окружающей среды.
В цветной металлургии эта задача решается путем рекультивации земель, нарушенных в ходе горных работ, и приведения земельных участков в безопасное и пригодное для использования в народном хозяйстве состояние. При рекультивации земель в определенной степени восстанавливаются нарушенные горными работами гидрогеологические режимы, прекращается загрязнение воздуха и вод, усыхание и гибель растительности и снижение урожайности сельскохозяйственных культур. Улучшаются также микроклимат и санитарно-гигиенические условия в районе действия предприятий.
Юридические документы РК обязывают промышленность выполнять рекультивацию нарушаемых земель не только при открытом, но и при подземном способе разработки полезных ископаемых, а также во всех других случаях нарушения земной поверхности.
Промышленные площадки рудников, обогатительных фабрик и металлургических заводов в пределах их ограждений занимают сравнительно небольшие территории -– порядка 20-60 га, реже около 100 га. Территории же, занятые отвалами гооной массы, забалансовых руд и хвостохранилищами обогатительных фабрик, исчисляются сотнями и даже тысячами гектаров. Поэтому в общем комплексе работ по рекультивации земель наиболее трудоемкие и дорогостоящие работы приходятся на планировку отвалов, террасирование и выполаживание их откосов.
Отвалы пустых пород, хвостов от обогащения руд, шлаков и других отходов металлургического производства, вследствие содержания в них химических соединений, отрицательно влияющих на растения, животных и человека, требуют особого отношения к их обезвреживанию. В свете этого требования обязанностью проектировщиков и руководителей предприятий является правильный выбор территорий под отвалы с целью предупреждения возможных утечек токсичных растворов и распыливания тонкодисперсной фракции отвальных материалов, а также метода складирования отходов, предусматривающего возможность их повторной переработки.
Радикальным средством предупреждения отрицательного влияния отвалов на окружающую среду служит возможно более полное использование отвальных материалов для строительных и других целей. При этом намного сокращается территория, занимаемая отвалами, и удешевляется стоимость рекультивации земель.
В этом отношении представляет большой интерес положительный опыт некоторых предприятий цветной металлургии (рудников, обогатительных фабрик, металлургических заводов), на которых организовано использование отвальных материалов для народнохозяйственных целей.
В качестве щебня вскрышные породы используются или реализуются на Башкирском горно-обогатительном, Норильском горно-металлургическом и Никитовском ртутном комбинатах, на комбинатах «Майкаинзолото» и «Уралзолото». Эти же породы в виде гравия применяют на ряде золотодобывающих предприятий. Всего на предприятиях цветной металлургии ежегодно используются для строительных целей миллионы кубических метров вскрышных пород.
К сожалению, не все отвальные породы и материалы могут быть использованы для строительных целей. Физико-химические превращения находящихся в них соединений происходят в строительных конструкциях в течение многих лет. Поэтому без предварительного тщательного и длительного изучения поведения различных компонентов отвальных материалов нельзя рекомендовать их для строительных целей.
При невозможности использования отвальных материалов текущего производства отвалы нужно соответствующим образом подготавливать для предупреждения размыва ливневыми водами и распыливания при ветровой эрозии. С этой целью поверхность отвалов и заполненных хвостохранилищ закрепляют с помощью битума, смол, пленочных покрытий и других материалов. При очень длительном хранении отвальных материалов, а также при нарушениях земной поверхности горными работами проводят рекультивацию земель.
Большая работа по рекультивации земель проводится на Верхнеднепровском горнометаллургическом комбинате, где вскрышные породы с помощью конвейерного транспорта и автосамосвалов укладывают в отработанное пространство. Растительный слой снимают и укладывают в специальные отвалы с последующим его использованием при рекультивации. Для биологического восстановления растительного слоя проводятся исследования в Днепропетровском сельскохозяйственном институте. На Иршинском горно-обогатительном комбинате отработанные площади засыпают вскрышными породами (песками) и на них производят посадку леса. Уже восстановлено и передано Гослесфонду около 200 га земель. Необходима дальнейшая работа по изысканию путей наиболее рационального применения отвальных пород и материалов.
7.2 Утилизация и обезвреживание металлургических газов
На предприятиях цветной металлургии образуется значительное количество отходящих газов, содержащих сернистый ангидрид, фтор, хлор и другие ценные компоненты, и вредные вещества. Утилизация и обезвреживание этих газов перед выбросом их в атмосферу имеет большое значение как для решения проблемы комплексного использования сырья, так и для защиты воздушного бассейна от загрязнения.
Одной из важных задач является использование металлургических серусодержащих газов. Наиболее высокий процент утилизации сернистого ангидрида – на предприятиях цинковой промышленности, а основные выбросы его в атмосферу имеют место на предприятиях медной и никелево-кобальтовой промышленности. Слабо еще используются отходящие газы свинцового производства.
Главные причины недостаточного использования серусодержащих газов в цветной металлургии заключаются в наличии большого количества газов с низким содержанием сернистого ангидрида. Непосредственная переработка этих газов на серную кислоту и другие химические продукты технически сложна и экономически нецелесообразна. Кроме того, имеет место отставание строительства новых мощностей сернокислотных производств па базе металлургических газов.
Ниже приведены данные о распределении серы в газах различной концентрации, %:

Как следует из этих данных, 87% общего объема серусодержащих газов составляют так называемые слабые газы, в которых концентрация S02 равна менее 3,5%. В этих газах находится 46% от общего количества серы. Таким образом, основная задача заключается в использовании и обезвреживании слабых сернистых газов. Решение проблемы утилизации серусодержащих газов предусматривается в следующих направлениях:
1) Сокращение объема газов и повышение концентрации в них S02 за счет совершенствования технологии металлургического производства, применения кислорода, строительства газоохлаждающих сооружений (котлов-утилизаторов, испарительного охлаждения), реконструкции газоотводящих систем и т. д.
2) Строительство новых, расширение и реконструкция действующих сернокислотных производств с применением двойного контактирования и промежуточной абсорбции газов (система DK/Dn).
3) Организация производства элементарівой серы из газов, содержащих более 10% SO2, в районах, значительно удаленных от мест потребления серной кислоты.
4) Разработка и внедрение экономичных методов обогащения слабоконцентрированных по содержанию SO2 газов, в том числе и путем сжигания в них элементарной серы, с целью последующего использования их для получения серной кислоты.
5) Разработка способов и строительство установок по санитарной очистке газов с очень низкой концентрацией SO2.
Реализация первого направления, т. е. сокращения количества образующихся технологических газов, обеспечивается разработкой и внедрением в производство автогенных процессов взвешенной плавки (Норильский горно-металлургический комбинат), кислородно-факельной плавки (Алмалыкский горно-металлургический комбинат), кивцэтным процессом (Иртышский полиметаллический, Усть-Каменогорский свинцово-цинковый комбинат, завод «Электроцинк» и др.), а также внедрением процессов плавки сульфидных концентратов в жидкой ванне.
Производство элементарной серы из отходящих сернистых газов многие медеплавильные компании США рассматривают как наиболее приемлемый способ утилизации металлургических газов. При этом в качестве восстановителя испытывают и применяют природный газ, окись углерода, сероводород, а в качестве катализатора – различные материалы на основе окиси алюминия с добавками железа, меди и некоторых других металлов.
Основным направлением при разработке способов получения элементарной серы является использование природного газа для восстановления S02. Газ с 12% S02 и более восстанавливают газообразным восстановителем до элементарной серы. Затем происходит охлаждение газов с целью конденсации образовавшейся серы, потом подогрев газа, взаимодействие остаточного количества SO2 с сероводородом и вторичная конденсация серы. В качестве катализатора применяют окись алюминия.
Наибольшее количество слабоконцентрированных сернистых газов (около 50%) получается на заводах медной промышленности в результате переработки сульфидного сырья в отражательных печах и на предприятиях никель-кобальтовой промышленности (43%), использующих шахтные печи для плавки окисленных никелевых руд. Поэтому разработка методов утилизации металлургических газов с низким содержанием SO2 особенно актуальна для этих подотраслей цветной металлургии.
Примером наиболее полного использования газов медеплавильного производства может служить завод «Онахама», который является единственным заводом в мировой практике, извлекающим серу из сырья на 97%. Это предприятие имеет две особенности. Во-первых, концентрация конверторных газов по содержанию SO2 доведена в среднем до 11% в результате применения особо плотных напыльников над конверторами, установки за каждым из них котлов-утилизаторов с минимальными подсосами газов и герметизации газоотводящей системы. Это дало возможность перерабатывать конверторные газы по схеме двойного контактирования и обеспечивать тем самым выбросы газов в атмосферу в пределах санитарных норм.
Характерно, что во избежание перебоев с питанием сернокислотной системы, а также при ее запуске на заводе сооружена и используется серусжигающая установка, работающая на элементарной сере. Сжигание серы с этой целью применяют и на шведском заводе «Болиден».
Во вторых, в целях использования газов отражательных печей для производства серной кислоты, содержащих 1,5-2,5% SO2, на заводе несколько лет (с 1970 по 1973 г.) эксплуатировался сернокислотный цех, работающий на этих газах с непрерывным их подогревом перед контактными узлами и очисткой хвостовых газов каустической содой. По некоторым данным, газы отражательных печей перед направлением на сернокислотное производство охлаждали на специальной установке до 18° С для более полной конденсации водяных паров.
Продолжая исследовательские и опытные работы по использованию газов отражательных печей, завод «Онахама» перешел затем па более экономичный способ улавливания из них SO2 с помощью окиси магния с последующим разложением сульфита и сульфата магния и переработкой более концентрированного газа па серную кислоту.
7.3 Очистка и утилизация промышленных стоков
Предприятия цветной металлургии являются крупными потребителями свежей воды. Вода расходуется на приготовление пульп и растворов, охлаждение пирометаллургических агрегатов и химической аппаратуры, на очистку газов и промывку различных осадков, получение пара и на другие цели. При этом большая часть воды загрязняется вредными веществами: металлами и их соединениями, а также хлором, фтором и другими примесями и сбрасывается обратно в водоемы в очищенном или неочищенном виде. Со сбросными водами теряется много ценных компонентов –цинка, кадмия, меди, молибдена, вольфрама, рения и других элементов.
В связи с указанным сокращение потребления свежей воды для технологических нужд, введение полного водооборота па предприятиях цветной металлургии и очистка всех промышленных стоков перед сбросом их в водоемы является не только важнейшей социальной проблемой, но и сложной технической задачей.
В последние время потребление воды резко возросло. Это объясняется не только ростом производства цветных металлов, но и вовлечением в переработку больших количеств руды с относительно низким содержанием металлов.
В отрасли проведена большая работа по рациональному использованию водных ресурсов. В настоящее время удельный вес водооборота в общем балансе недопотребления составляет 68%. Более 130 предприятий используют стоки в оборотном водоснабжении, из них на 62 водооборот достигает 97%, а на 22 полностью прекращен сброс сточных вод в водоемы. Так, Джезказганский медеплавильный завод, построенный по проекту Гипроцветмета, работает на полном водообороте и расходует свежую воду только на компенсацию потерь. Без применения водооборота этот завод расходовал бы в год многие десятки миллионов кубических метров свежей воды.
8 Перспективы создания безотходных технологических схем
в металлургическом производстве
Экономическая целесообразность и большое социальное значение замкнутой безотходной технологии с экономической точки зрения очевидна. В цветной металлургии имеется реальная возможность создать и освоить в будущем ряд замкнутых металлургических схем с полной переработкой полупродуктов и отходов производства.
Одной из таких схем является комплексная переработка нефелинового сырья в алюминиевой промышленности. Нефелиновое сырье перерабатывают двух видов – нефелиновые концентраты комбината «Апатит» и нефелиновые руды Кия-Шалтырского месторождения. Принципиальная схема переработки нефелиновой руды (концентрата) показана па рисунке 10. Как следует из схемы, шихту, приготовленную из нефелиновой руды и известняка, подвергают спеканию. Спекание осуществляют во вращающихся печах, отапливаемых жидким, газообразным или пылеугольным топливом. В печи шихту подают в виде пульпы с влажностью 27-30%. В результате спекания получают спек, состоящий в основном из алюминатов щелочных металлов (Na2O·Al2O3; К2O·А12Oз), двухкалыщевого силиката (2CaO· Si02) и феррита натрия (Na2O· Fe203).
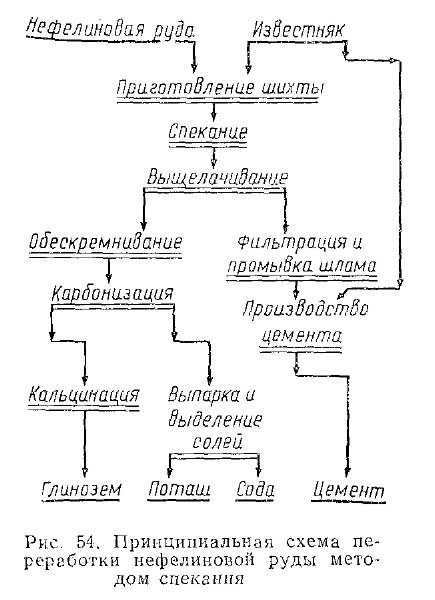
Рисунок 10 – Принципиальная схема переработки нефелиновой руды методом спекания
При выщелачивании спека алюминаты щелочных металлов переходят в раствор; феррит натрия гидролизует с образованием едкого натра и гидроокиси железа; двухкальциевый силикат взаимодействует с алюмининатным раствором, в результате чего получаются алюмосиликаты щелочных металлов и трехкальциевый гидроалюминат по реакции:
2CaO.Si02+ Na20.Al203+a → Na2O. А12О3 . 1,75SiO2 . 2Н2О +
+3СаОА1203. 6Н2О. (1.1)
Остаток от выщелачивания спека – нефелиновый шлам – после отделения от раствора и промывки направляют в смеси с известняком па производство цемента. Алюминатный раствор подвергают операции обескремнивания, при которой образуются малорастворимые соединения (алюмосиликаты), отделяемые затем фильтрацией.
Операция карбонизации имеет целью выделение из раствора гидроокиси алюминия. Ее осуществляют путем обработки растворов газами, содержащими СО2. При этом щелочи из каустической формы переходят в карбонатную, а гидроокись алюминия выпадает в осадок. Для получения товарного глинозема гидроокись алюминия необходимо прокаливать при температуре 1200-1250° С с последующим охлаждением. Это достигается во вращающихся печах кальцинации, оборудованных холодильниками.
Содовые продукты (Nа2СО3, К2СО3) получают путем упарки растворов после выделения гидроокиси алюминия в выпарных аппаратах в несколько стадий. Вначале выкристаллизовывается сода (Na2CO3), затем поташ (К2СО3).
Таким образом, технологическая схема комплексной переработки нефелинового сырья в принципе обеспечивает полное использование всех компонентов нефелиновой руды в виде товарных продуктов. По этой технологии на 1 т глинозема и эквивалентного количества цемента расходуют 3,9-4,3 т нефелиновой руды (концентрата), 11-13,8 т известняка, 2,97-3,3 т топлива, 4,12-4,68 Гкал пара, 1050-4190 кВт.ч электроэнергии. При этом производят 0,62-
0,78 т кальцинированной соды, 0,18-0,28 т поташа, 9-10 т портландцемента.
Эксплуатационные затраты на производство глинозема, соды, поташа, цемента, извлекаемых из нефелинового сырья, на 10-15% ниже, затрат при получении этих продуктов другими промышленными способами.
Однако в настоящее время весь нефелиновый шлам перерабатывают на портландцемент только на двух предприятиях – Волховском алюминиевом заводе и Пикалевском глиноземном комбинате.
Одним из путей создания комплексной безотходной технологии переработки сырья является организация комбинированного металлургического производства, которое позволяет осуществлять замкнутые технологические схемы с полным использованием полупродуктов производства как в рамках одного предприятия, так и в масштабе подотрасли.
8.1 Экономическая эффективность комплексного использования сырья
Трудно переоценить значение комплексного использования сырья для повышения экономической эффективности производства в цветной металлургии – оно огромно. Экономическая эффективность более полного и комплексного использования сырья проявляется в повышении производительности общественного труда, ускорении роста объемов производства продукции, более эффективном использовании капитальных вложений, снижении себестоимости продукции, ускорении развития отдельных экономических районов и ряде других экономических факторов.
Повышение полноты извлечения металлов и комплексности использования рудного сырья оказывает непосредственное влияние на улучшение технико-экономических показателей производства. Так, на Усть-Каменогорском свинцово-цинковом комбинате рентабельность большинства видов попутной продукции намного превосходит рентабельность основной продукции. Например, производство кадмия в 3,36 раза, а производство серной кислоты в 12,86 раза рентабельнее производства цинка. Получение черновой меди из свинцового сырья в 5,8 раза, а получение шлаковозгонов и висмута в дроссах соответственно в 5 и 6,7 раза рентабельней производства свинца.
В результате внедрения принципиально нового процесса электроплавки медистых шликеров и пылей свинцового завода Лениногорского полиметаллического комбината по разработкам Института металлургии и обогащения АН РК извлечение меди повысилось на 8-12%, свинца – более чем на 1 %. Комбинат за счет этого получил годовую экономию 450 тыс. т.
Внедрение мероприятий по повышению комплексного использования сырья на Чимкентском свинцовом заводе позволило также получить значительную экономическую выгоду. Организация комплексной переработки пылей и возгонов с извлечением цветных и редких металлов дала экономический эффект в сумме 400 тыс. т. Удельный вес попутной продукции увеличился с 18,17 до 22,62%. В результате снизилась себестоимость рафинированного свинца и увеличилась прибыль.
9 Основные направления повышения комплексности использования сырья в подотраслях цветной металлургии
9.1 Медная промышленность
В решении проблемы комплексного использования сырья в цветной металлургии медная промышленность занимает особое место. Объясняется это как относительно низким уровнем комплексности использования медных руд и концентратов, так и большим разнообразием медного сырья, сложностью вещественного состава руд, наличием довольно значительных запасов труднообогатимых руд, вовлекаемых в переработку, большими потерями серы в металлургическом производстве.
В собственно медных сульфидных рудах наряду с основным металлом находится до восьми сопутствующих ценных компонентов (сера, золото, серебро, молибден, кадмий, рений, селен, теллур). В медно-цинковых рудах число сопутствующих компонентов еще больше за счет присутствия в них индия, таллия, германия. Стоимость серы и сопутствующих металлов составляет от 40 до 50% общей стоимости всех ценных компонентов руды.
Исходя из этого, следует считать основной задачей улучшения комплексности использования сырья в медной промышленности – повышение извлечения наряду с медью всех сопутствующих ценных компонентов, и особенно серы, имеющей по стоимости наибольший удельный вес после меди. Рассмотрим главные направления рационального использования медного сырья при обогащении руд и металлургической переработке концентратов.
Основные потери металлов с хвостами обогащения на медных фабриках связаны как с недоизмельчением руды и недостаточным вскрытием минералов, так и с ее переизмельчением и шламообразованием. Поэтому в завимости от конкретных условий производства главными направлениями повышения извлечения металлов на обогатительных фабриках следует считать улучшение гранулометрической характеристики измельчения руд, внедрение стадийных схем измельчения и флотации, а также классификацию хвостов с доизмельчением и дофлотацией песковой фракции по опыту Балхашской обогатительной фабрики.
С целью повышения извлечения серы на всех без исключения фабриках должно быть организовано выделение пиритных концентратов с увеличением их выхода и улучшением качества.
Одной из главных задач специалистов медной промышленности является улучшение показателей обогащения медно-цинковых руд и повышение извлечения из них цинка.
В настоящее время степень извлечения цинка из уральских руд колеблется в пределах от 51,2% на Карабашской до 74,5% на Сибайской обогатительных фабриках. Разрыв в показателях извлечения превышает 20%. Безусловно, каждая руда требует своей особой технологии. Однако имеющиеся резервы в совершенствовании технологии еще полностью не используются.
В недостаточной степени используются еще комплексные руды Джезказганского, Урупского и некоторых других медных месторождений. Получение цинковых концентратов из них не организовано. Извлечение свинца в одноименный концентрат на Джезказганском комбинате еще низкое (около 69%). Поэтому организация комплексной переработки указанных руд также является одной из первостепенных задач работников медной промышленности.
Хотя резервы совершенствоания флотации трудно-обогатимых руд еще не исчерпаны, решить проблему комплексной переработки этих руд только обогатительными методами, по всей вероятности, не удастся. Поэтому в медной промышленности, как и в свинцово-цинковой и ряде других подотраслей цветной металлургии, большое значение приобретает сочетание технологии обогащения руд с металлургическими способами переработки коллективных продуктов обогащения.
Для переработки потерянных, забалансовых, окисленных и смешанных медных руд наиболее рациональными способами будут соответственно подземное выщелачивание с применением бактерий, кучное бактериальное выщелачивание и различные комбинированные процессы, сочетающие сернокислотное выщелачивание окисленных минералов с флотацией сульфидных минералов и сорбционным извлечением меди из растворов.
В последнее время дополнительными источниками медного сырья являются чрезвычайно сложные коллективные продукты обогащения типа медного концентрата, выделяемого при обогащении оловянных руд Солнечного горно-обогатительного комбината. В этом материале наряду с медью, цинком, свинцом, оловом и висмутом содержится также значительное количество мышьяка. Для переработки подобных материалов необходимо разработать новые, предпочтительно гидрометаллургические процессы, обеспечивающие комплексное извлечение всех ценных компонентов.
Прежде чем говорить об основных направлениях повышения комплексности использования сырья в металлургическом производстве следует сказать о том, что на обогатительных фабриках медной промышленности необходимо организовать флотацию всех без исключения руд с тем, чтобы на медеплавильных заводах перерабатывать только концентраты. Эффективность этого мероприятия видна из сопоставления показателей извлечения меди при плавке руды и медных концентратов. Так, на Медногорском и Карабашском заводах извлечение меди в черновую составляет соответственно 88,42 и 93,02% (данные 1976 г.), в то время как на Красноуральском и Средне-уральском кобинатах 93,88 и 94,8% соответственно. Ликвидация непосредственной металлургической переработки руд потребует времени и капитальных вложений, но даст дополнительно несколько тысяч тонн черновой меди.
Наряду с этим имеется возможность и с небольшими капитальными затратами повысить извлечение меди на металлургических заводах. Достаточно сопоставить показатели извлечения Среднеуральокого медеплавильного завода (94,8%) и Алавердского горно-металлургического комбината (88,6%), а также показатели Балхашского (97,71%) и Джезказганского (97,53%) комбинатов, чтобы сделать вывод о наличии значительных резервов использования сырья на Алавердском и Джезказганском комбинатах за счет лучшей организации производства.
В самом деле, Среднеуральский завод плавит обожженную шихту в отражательных печах, не имеющих пылеулавливания, Алавердский комбинат перерабатывает такую же шихту в электропечи, оснащенной пылеулавливающими устройствами. Тем не менее это предприятие теряет на 6% больше меди, чем Среднеуральский завод.
Джезказганский комбинат, применяющий для необожженных богатых концентратов (36,5% Сu) электроплавку, имеет более низкое (на 0,2%) извлечение меди против Балхашского комбината, использующего в качестве основного способа переработки сырья отражательную плавку. Следовательно, дело не только в уровне техники и технологии производства, но и в уровне организации производства, повышение которого является повседневной задачей специалистов и коллективов предприятий.
Наиболее эффективным направлением повышения комплексности использования сырья в производстве черновой меди является переход на автогенные процессы плавки медных концентратов. При этом решается комплекс вопросов, сдерживающих повышение технического уровня медной промышленности. Прежде всего увеличивается извлечение меди и сопутствующих металлов. Но основной эффект получается от улучшения использования серы. Поэтому важнейшей задачей специалистов медной промышленности продолжает оставаться перевод медеплавильных заводов в соответствии с намеченной программой на кислородно-факельную, кивцэтную плавку и плавку в жидкой ванне.
Отстающим участком работы по повышению комплексности использования сырья является переработка конверторных и отвальных шлаков медеплавильных заводов. Изыскание экономически целесообразных способов обеднения конверторных и комплексной переработки отвальных шлаков с использованием всех ценных компонентов значительно продвинет вперед решение этой проблемы.
Существенный вклад в улучшение показателей извлечения металлов и рационального использования металлургического сырья могут внести разработка и внедрение прогрессивных гидрометаллургических методов переработки пылей медеплавильного производства на основе сорбции и экстракции.
Медная промышленность располагает достаточным научным заделом по проблеме комплексного использования сырья. Реализация законченных научных разработок по этому вопросу является задачей первостепенной важности.
9.2 Свинцово-цинковая промышленность
За последние десятилетия достигнут значительный прогресс в комплексном использовании сырья на свинцовых и цинковых заводах. В настоящее время из полиметаллического сырья извлекают 18 элементов, выпускают около 40 видов товарной продукции. Передовые свинцовые заводы добились дальнейшего повышения показателей извлечения металлов. Так, на Усть-Каменогорском свинцово-цинковом комбинате извлечение свинца достигло 97,42%, на Дальневосточном горно-металлургическом комбинате 97,21%. Коэффициент комплексности использования сырья в свинцовом производстве этих предприятий составил соответственно 96,9 и 95,2%.
Из цинковых заводов наилучшие результаты по извлечению основного металла имеют Челябинский электролитный цинковый завод (96,64%) и Усть-Каменогорский свинцово-цинковый комбинат (96,5%). По извлечению цинка к ним приближается и Алмалыкский горно-металлургический комбинат (95,35%).
Вместе с тем в металлургическом производстве этой подотрасли имеется еще много неиспользованных резервов. Основными причинами неполного использования сырья являются: задалживание ценных компонентов в металлургических полупродуктах и отходах (кеках, пылях, раймовке, шлаках, клинкере), получение больших количеств отходящих газов, низкая степень использования серы на свинцовых заводах; высокие неучтенные потери металлов; несовершенство пылеулавливания и технологии переработки пылей и других полупродуктов.
В настоящее время в отвалах шлаков, цинковых кеков, раймовки, клинкера находится значительное количество металла; мощности шлакоперерабатывающих установок не обеспечивают пока переработки даже шлаков текущего производства. Кроме Чимкентского свинцового завода, агломерационные газы свинцового производства для получения серной кислоты нигде не используются. На Лениногорском полиметаллическом комбинате имеются еще большие отвалы цинковых кеков. Медленно перерабатываются клинкер печей вельцевания, раймовка и другие полупродукты.
Недостаточные мощности пылеулавливающих установок, низкий уровень их эксплуатации в ряде случаев, а также механические потери при транспортировке и перегрузках приводят к значительным неучтенным потерям свинца и цинка, составляющим соответственно 56 и 43% от общих потерь этих металлов.
Основными направлениями повышения комплексности использования сырья в металлургическом производстве свинцово-цинковой промышленности являются: дальнейшее расширение масштабов применения кислорода при обжиге цинковых концентратов, повышение концентрации кислорода в дутье печей КС; совершенствование агломерации свинцовых концентратов путем внедрения дутья снизу, рециркуляции газов и обогащения воздуха кислородом; переход на кислородно-факельную плавку свинцовых концентратов с использованием отходящих сернистых газов в производстве серной кислоты; внедрение гидрометаллургической переработки цинковых кеков с комплексным использованием остатков от выщелачивания; переработка всего объема текущих шлаков свинцовой плавки методом фьюмингования и холодных шлаков из отвалов в вельц-печах комплексным использованием всех ценных составляющих; организация пылеулавливания и очистки технологических и вентиляционных газов, образующихся в свинцовом и цинковом производствах с отдельной комплексной переработкой пылей, полупродуктов и отходов металлургического и сернокислотного производства.
Необходимо также производить очистку всех газов, выбрасываемых в атмосферу, до санитарных норм; организовать очистку промышленных стоков с полной утилизацией находящихся в них ценных компонентов и внедрением полного водооборота, позволяющего резко сократить потребление свежей воды. Большой эффект следует ожидать от применения современных средств использования вторичных энергоресурсов (котлов-утилизаторов, испарительного охлаждения и др.).
Сокращение механических потерь металлов при транспортировании и хранении сырья и организация комбинированного свинцово-цинкового и медного предприятия с замкнутой технологической схемой и взаимной переработкой полупродуктов и отходов позволяет значительно повысить технико-экономические показатели производства.
9.3 Никелевая промышленность
Переработку окисленных никелевых руд производят без предварительного обогащения в шахтных печах (Уральские предприятия) и в электропечах (Побужский завод). Плавка руд в шахтных печах на штейн вызывает большие потери никеля и кобальта с отвальными шлаками (соответственно 16 и 55%), а при конвертировании штейнов образуется значительное количество слабоконцентрированных сернистых газов, которые сбрасываются в атмосферу, загрязняя воздушный бассейн. При этом способе извлечение никеля составляет около 75%, кобальта – около 30%. Сера и железо полностью теряются.
Плавка окисленных никелевых руд на ферроникель является более прогрессивным процессом, так как при этом извлечение никеля повышается на 10–15% и утилизируется значительное количество железа. Значительные преимущества имеет плавка окисленных руд на ферроникель в печах с погруженным факелом, которая осуществляется на природном газе без расхода кокса. На этот процесс переден Уфалейский никелевый завод.
Заслуживает внимания и разработка процесса обогащения окисленных никелевых руд методом сегрегационного обжига. Исследования в этом направлении ведутся как за рубежом, так и в СНГ.
Основной проблемой комплексного использования сульфидных медно-никелевых руд является повышение извлечения никеля, меди, кобальта, драгоценных металлов и утилизация серы.
Эта проблема решается в нескольких направлениях. Ввиду большого содержания железа и серы в рудах Талнахского и Октябрьского месторождений в районе Норильска при флотации получают относительно бедные никелевые концентраты с высоким процентом серы и железа, для удаления которых в процессе обжига и плавки приходится соответственно затрачивать много средств и флюсов.
Механобр разработал технологию обогащения медно-никелевых руд с получением богатых никелевых концентратов, содержащих, % : 9,8 Ni; 5,5 Сu; 48 Fe; 33 S и отношением Fe:Ni=4,85 и S:Ni =3,35, и очищенного пирротинового концентрата состава, %: 2,53 Ni; 0,5 Сu; 52 Fe; 33,8 S с отношением Fe:Ni = 20,6 и S:Ni=13,6. Как видно из состава пирротинового концентрата, основное количество железа и серы сосредоточивается в этом продукте обогащения, что создает возможность организации раздельной переработки указанных материалов по оптимальным технологическим схемам.
Переработку богатых никелевых концентратов будут осуществлять автогенными процессами (взвешенной, кислородно-факельной плавкой и другими способами). При этом наряду с улучшением показателей извлечения металлов значительно увеличится степень использования серы, которую будут получать в виде элементарной.
Для переработки пирротинового концентрата, как уже говорилось выше, строят автоклавный передел на Надеждинском металлургическом заводе. Назначение передела – гидрометаллургическое обогащение пирротинового продукта с получением элементарной серы.
Результаты полупромышленных испытаний технологии автоклавной переработки пирротинового концентрата позволяют надеяться в перспективе на возможность создания гидрометаллургической технологии переработки никелевых концентратов без выделения из них пирротинов. Опытные работы в этом направлении продолжаются.
Наиболее серьезной проблемой является использование серы при переработке сульфидного сырья. В настоящее время никелевая промышленность по этому показателью стоит на последнем месте в отрасли, что объясняется не только невозможностью вывоза серной кислоты из района Норильска, но и недостаточными мощностями сернокислотного производства на предприятиях Кольского полуострова и отсутствием установок для утилизации серы на уральских заводах.
Эта проблема будет решаться путем разработки и внедрения метанового способа восстановления сернистого ангидрида до элементарной серы на Норильском комбинате, ввода новых сернокислотных мощностей на предприятиях Кольского полуострова и строительства сооружений для очистки слабоконцентрированных сернистых газов на уральских заводах.
На действующих предприятиях никелевой промышленности будут расширяться масштабы обеднения конверторных шлаков в электропечах и внедряться процесс получения анодного никеля в вертикальных конверторах, что позволит повысить извлечение никеля и кобальта.
Разрабатываются специальные мероприятия по увеличению извлечения металлов платиновой группы, сокращению потерь драгоценных, металлов по всему производственному циклу от обогащения руды до выпуска готовой продукции.
9.4 Алюминиевая промышленность
Алюминиевая промышленность является ведущей отраслью цветной металлургии. Производство алюминия базируется в настоящее время на трех видах сырья: бокситах, нефелинах и алунитах. В решении задачи комплексного использования сырья ведущая роль принадлежит наиболее крупному по масштабам глинозёмному производству. Вместе с тем большое значение для охраны окружающей среды, снижения потерь металла и фтористых солей и улучшения экономики производства имеет технический уровень электролиза алюминия. Основную часть глинозема производят в СНГ и за рубежом из бокситов. Традиционные способы переработки бокситов предусматривают извлечение из них только глинозема. Второй компонент – железо, как правило, не используют. Такое положение объясняется трудностями создания технологии переработки бокситов, обеспечивающей рентабельную работу предприятия, комплексность и безотходность производства. В СНГ перерабатывают различные по составу и качеству бокситы. Извлечение глинозема из них составляет 85-86%
Нефелиновые руды и концентраты являются вторым по значению видом сырья для алюминиевой промышленности. Переработку Кольского нефелинового концентрата производят Волховский алюминиевый завод и Пикалевский глиноземный комбинат. Нефелиновую руду Кия-Шалтырского месторождения перерабатывает Ачинский глиноземный комбинат. В результате комплексной переработки нефелинов и карбонатного сырья на первых двух предприятиях на 1т глинозема получают 0,62-0,7 т соды, 0,18-0,28 т поташа и 9-10 т портландцемента.
Товарный выход глинозема и щелочей составляет соответственно 83 и 80%. Дальнейшее повышение выхода глинозема и щелочей будет осуществляться путем совершенствования режима выщелачивания и промывки шлама, внедрения регенерации глинозема из шламов обескремнивания и безизвестковой технологии переработки растворов, а также посредством других организационно-техничеюких мероприятий. Первоочередными задачами Ачинского глиноземного комбината являются освоение проектных технико-экономических показателей (извлечение глинозема 82%, щелочи 78%) и полное использование шламов в производстве цемента и т. д.
На Кировабадском алюминиевом заводе впервые в промышленном масштабе осуществлена технология комплексной переработки алунитового сырья на глинозем, серную кислоту и сульфат калия. Решающее значение для успешного освоения этой технологии, повышения извлечения глинозема и серы имела разработка эффективного способа восстановления алунита. Проведение на этом заводе ряда других мероприятий (создание и освоение новой установки для обжига алунита, оптимизация передела выщелачивания, совершенствование аппаратуры) позволит перекрыть проектные показатели по извлечению ценных компонентов из сырья.
Как указывалось выше, бокситовое и другое алюминий содержащее сырье, включает наряду с глиноземом и железом много других ценных компонентов. В процессах переработки сырья в циркулирующих растворах глиноземного производства накапливаются ванадий, галлий и ряд других элементов. ВАМИ и ЦНЗиО АН РК разработали способы извлечения пятиокиси ванадия и галлия из алюминатных растворов.
При электролитическом производстве алюминия основное внимание должно быть обращено на снижение механических потерь глинозема в процессе доставки его от завода-поставщиков (около 1%) и при погрузочно-разгрузочных операциях (около 2%), улавливание и утилизацию газообразных и твердых фторсодержащих отходов. Эта задача представляется весьма актуальной как с точки зрения комплексного использования сырья, так и защиты воздушного бассейна в районе алюминиевых заводов от загрязнения токсичными соединениями.
Уменьшение механических потерь глинозема достигается применением специализированных вагонов-цистерн для его перевозки, автоматизацией приемных складов на заводах-потребителях, уплотнением узлов раздачи расходных силосов в корпусах электролиза и внедрением вакуумных пылеуборочных машин.
На алюминиевых заводах на 1 т получаемого металла выделяется с технологическими газами в среднем 18 кг общего фтора, 12 кг сернистого ангидрида и 85 кг пыли, состоящей в основном из глинозема и смолистых веществ. Потери глинозема и фтористых солей имеют место также с отработанной футеровкой электролизеров.
Очистку технологических газов на большинстве заводов осуществляют мокрым способом в двухступенчатых установках обеспечивающие улавливание фтористого водорода на 99,5%, сернистого ангидрида – на 95% и пыли – на 85%.
Для регенерации криолита из растворов газоочистки и угольной «пены» электролизеров на одних заводах действуют, а на других строятся соответствующие цехи и отделения.
Шлам из аппаратов газоочистки и пыль электрофильтров, содержащие фтор, алюминий и другие ценные компоненты, пока не перерабатывают и направляют в отвал. Разрабатывается более эффективный «сухой» способ сорбционной очистки газов от фтора глиноземом, обеспечивающий улавливание 98-99% фтора и пыли. ВАМИ подготовил к внедрению метод регенерации криолита из отработанной футеровки электролизеров. В ближайшие 10-15 лет намечается расширение существующих отделений регенерации с целью организации переработки всех твердых отходов от электролиза алюминия.
Осуществление комплекса мероприятий по совершенствованию и внедрению технологии очистки газов, переработки твердых отходов и регенерации фтористых соединений позволит сократить вредные выбросы в атмосферу и дополнительно возвратить в процесс около 8 кг фтора на 1 т алюминия.
По данным ВАМИ, выход фтора в товарную продукцию за последние три года увеличился на 2-3%. Для дальнейшего повышения степени использования сырья, серной кислоты и гидрата окиси алюминия намечено применить смесители специальной конструкции, замкнутый водооборот и т. д. Предусматривается также начать использование фторангидритных отходов в производстве строительного гипса и в цементной промышленности.
Литература
1 Снурников А.П. Комплексное использование сырья в цветной металлургии. – М. : Металлургия, 1977. – 272 с.
2 Никитин Г.М. Комплексное использование минерального сырья. – Павлодар: Павлодарский центр научно-технической информации, 2007. – 29 с.
3 Равич Б.М. Комплексное использование сырья и отходов / Б.М. Равич, В.П. Окладников. – М. : Химия, 1988. – 320 с.
4 Абжаров А.А. Комплексное использование низкокачественного глиноземсодержащего сырья Казахстана. – Алма-Ата: Гылым, 1988. – 178 с.
5 Абдулива А.А. Техногенное минеральное сырье рудных месторождений Казахстана / под ред. проф. А.А. Абдулива. – Алматы: Институт геологических наук, 2002. – 122 с.
Содержание
| Введение | 3 |
1 | Народнохозяйственное значение проблемы комплексного использования сырья | 5 |
1.1 | Оценка комплексности использования сырья | 7 |
2 | Пути рационального использования рудных месторождений | 9 |
2.1 | Подготовка запасов руд к выемке | 10 |
2.2 | Прогрессивные системы и методы разработки месторождений | 12 |
2.3 | Селективная добыча и усреднение руд | 14 |
2.4 | Добыча и переработка забалансовых, потерянных руд и вскрышных пород | 16 |
3 | Комплексная переработка руд на обогатительных фабриках | 21 |
3.1 | Характеристика руд цветных и редких металлов | 22 |
4 | Прогрессивные методы подготовки руды | 32 |
4.1 | Дробление руд | 32 |
4.2 | Самоизмельчение руд | 34 |
4.3 | Обогащение в тяжелых суспензиях | 37 |
4.4 | Совершенствование технологий измельчения и флотации | 40 |
4.5 | Доизвлечение металлов из хвостов от обогащения руд | 42 |
4.6 | Извлечение драгоценных металлов | 43 |
4.7 | Попутное извлечение нерудных ископаемых | 44 |
4.8 | Доизвлечение ценных компонентов из производственных растворов и сточных вод | 45 |
4.9 | Повышение качества концентратов | 47 |
5 | Проблема комплексного использования сырья в металлургическом производстве | 49 |
5.1 | Переработка коллективных продуктов обогащения | 52 |
5.2 | Переработка медно-свинцово-цинковых промпродуктов | 53 |
6 | Комплексная переработка полупродуктов металлургического производства | 55 |
6.1 | Переработка шлаков и возгонов | 55 |
6.2 | Гидрометаллургические процессы | 56 |
6.3 | Использование фторсодержащих отходов алюминиевого производства | 57 |
7 | Охрана природы и комплексное использование сырья | 59 |
7.1 | Использование отвалов и рекультивация земель | 59 |
7.2 | Утилизация и обезвреживание металлургических газов | 61 |
7.3 | Очистка и утилизация промышленных стоков | 64 |
8 | Перспективы создания безотходных технологических схем в металлургическом производстве | 65 |
8.1 | Экономическая эффективность комплексного использования сырья | 67 |
9 | Основные направления повышения комплексности использования сырья в подотраслях цветной металлургии | 68 |
9.1 | Медная промышленность | 68 |
9.2 | Свинцово-цинковая промышленность | 71 |
9.3 | Никелевая промышленность | 73 |
9.4 | Алюминиевая промышленность | 75 |
| Литература | 79 |
Рецензия
На учебное пособие Кенбеиловой С.Ж., Таскариной А.Ж.
Комплексное использование минерального сырья. – Павлодар, 2008
Курс «Комплексное использование минерального сырья» входит в вузовский компонент учебного плана специальности 050709 «Металлургия».
В учебном пособии освещены системы и методы разработки месторождений, обеспечивающие снижение потерь при добыче руд. Указаны пути повышения полноты и комплексности использования сырья при обогащении руд, металлургической переработке концентратов, коллективных продуктов обогащения, полупродуктов, пылей и газов металлургического производства. Приведены данные, характеризующие экономическую эффективность, и указываются основные направления повышения комплексности использования сырья в ведущих подотрослях металлургии.
Поэтому рецензируемое пособие следует считать весьма своевременным и актуальным.
Настоящее пособие, безусловно, поможет студентам в успешном изучении курса «Комплексное использование минерального сырья».
Профессор,
кандидат технических наук М.М. Суюндиков