Учебное пособие Павлодар удк 622 012 (07) ббк 30. 3я7
Вид материала | Учебное пособие |
- Курс лекций Учебное пособие Волгоград 2009 удк 330. 01 Ббк 65. 012., 6756.22kb.
- Учебное пособие Павлодар Кереку 2010 удк 53 (075. 8) Ббк 22. 3я73, 1449.38kb.
- Учебное пособие Павлодар удк339. 9 (075. 8) Ббк 65., 1778.36kb.
- Учебное пособие Павлодар удк 94(574+470. 4/. 5+571. 1)(075. 8) Ббк 63. 3(5Каз+2Рос)5я73, 3633.95kb.
- Врамках программы «Прометей» Павлодар удк 94(574. 25)(075. 8) Ббк 63. 3(5Каз)я73, 3259kb.
- Учебное пособие для студентов естественных специальностей Павлодар, 2290.94kb.
- Учебное пособие разработано в соответствии с государственным стандартом специальности, 1131.24kb.
- Учебное пособие удк 159. 9(075) Печатается ббк 88. 2я73 по решению Ученого Совета, 5335.58kb.
- Практикум Новочеркасск юргту (нпи) 2010 удк 330 (075. 8) Ббк 65. 012. 1я73, 2097.42kb.
- Врамках программы «Прометей» Павлодар удк 94(574. 25) Ббк 63. 3(5Каз), 6238.86kb.
1.1 Оценка комплексности использования сырья
Оценка комплексности использования сырья производится в соответствия с методическими указаниями, утвержденными Министерством индустрии и торговли РК. Основные положения этих указаний сводятся к следующему. Количественная оценка состояния комплексности использования сырья осуществляется на основе показателей уровня использования сырьевых ресурсов. Уровень комплексности использования сырья может быть объективно охарактеризован лишь системой показателей, отражающих как результаты комплексного использования сырья в каждом конкретном случае, так и специфику самого сырья. К этим показателям относятся достигнутые или ожидаемые результаты рационального использования сырья – число извлекаемых компонентов, степень извлечения и потерь ценных компонентов и т. д.
Показатели уровня комплексного использования сырья используются при планировании, учете, отчетности и анализе производственной деятельности предприятий и подотраслей цветной металлургии. Эти показатели должны отвечать двум основным требованиям – обеспечивать полноту и сопоставимость данных для определения уровня комплексности использования сырья.
Уровень комплексного использования сырья зависит от особенностей сырья, применяемой технологии и оборудования, специализации, кооперирования и комбинирования предприятий, от потребностей народного хозяйства в продуктах комплексной переработки сырья и ряда других факторов.
Необходимым условием определения уровня комплексного использования сырья является четкое установление перечня ценных компонентов для каждого вида перерабатываемого сырья. Этот перечень должен быть обоснован с позиций народнохозяйственной эффективности и технической возможности извлечения каждого ценного компонента из конкретного сырьевого источника.
Показатели уровня комплексного использования сырья делятся на две группы – исходные и расчетные. В группу исходных показателей входят:
а) ценные компоненты в сырье (число, перечень, содержание в процентах или в граммах на тонну, весовое количество);
б) ценные компоненты в отходах (весовое количество отходов, весовое количество и содержание каждого ценного компонента);
в) ценные компоненты в оборотных продуктах (содержание и весовое количество их);
г) «неучтенные потери» ценных компонентов (весовое количество неучтенных потерь ценных компонентов).
К расчетным показателям относятся:
а) извлечение ценных компонентов (извлечение каждого ценного компонента в одноименные и разноименные продукты);
б) потери ценных компонентов (потери каждого ценного компонента по видам и источникам потерь);
в) доля стоимости сопутствующих ценных компонентов в сырье и товарной продукции (в процентах к общей стоимости основных и сопутствующих компонентов);
г) степень комплексности использования сырья (число и перечень ценных компонентов, извлекаемых в товарную продукцию);
д) полнота использования сырья (извлечение ценных компонентов в реализуемые и оплачиваемые по этим компонентам виды продукции);
е) условно обобщающий коэффициент комплексности использования сырья (отношение стоимости извлеченных компонентов к стоимости ценных компонентов в сырье по единым ценам). Различают фактический и потенциальный коэффициент комплексности использования сырья.
Три последних расчетных показателя – степень комплексности использования сырья, полнота использования сырья и обобщающий коэффициент комплексности использования сырья – относятся к числу результирующих показателей уровня комплексного использования сырья.
Фактический коэффициент комплексности отражает фактический уровень извлечения ценностей из перерабатываемого сырья за данный период. Потенциальный коэффициент комплексности представляет собой отношение стоимости полезных компонентов, извлечение которых целесообразно в ближайший перспективный период, при оптимальной полноте извлечения этих компонентов, к стоимости всех ценных компонентов в сырье. Он показывает, какая часть ценностей может быть извлечена из сырья при технически возможном и экономически оправданном уровне использования ценных компонентов. Разность между потенциальным и фактическим коэффициентами комплексности характеризует экономически обоснованные резервы использования сырья, а отношение указанных коэффициентов - степень использования потенциала сырья.
2 Пути рационального использования рудных месторождений
Дальнейший прогрессивный рост показателей извлечения металлов и улучшения комплексности использования сырья требует систематической работы на всех стадиях производства, начиная с горного дела, детального анализа состояния технологии, оборудования, организации труда и других решающих элементов производственного процесса.
При добыче руд цветных металлов, одновременно с бережным отношением к природным ресурсам и рациональным использованием недр, должны закладываться основы более полного и комплексного их использования на последующих переделах обогащения и металлургической переработки. Поэтому решение проблемы комплексного использования сырья неразрывно связано с производственно-технической деятельностью горных предприятий, перед которыми стоят три основные задачи: добыть руду с минимальными потерями ее в недрах; обеспечить определенный минералогический состав и заданное содержание металла в добытой руде; ритмично подавать руду на обогатительную фабрику.
За последние десятилетия горнодобывающие предприятия отрасли в результате разработки и внедрения ряда прогрессивных, технологических и организационных решений в основном успешно справились со своими задачами по рациональному использованию недр. Несмотря на значительное усложнение горно-геологических условий разработки месторождений, потери и разубоживание руд не увеличились. Однако в деле рационального использования недр еще далеко не все резервы вскрыты и не все возможности реализованы.
Эти возможности и резервы заключаются прежде всего в правильной и своевременной подготовке запасов руд к выемке, освоении высокоэффективных прогрессивных систем и способов разработки месторождений, применении там, где это возможно, селективной добычи, усреднении руд, организации добычи и переработки забалансовых и потерянных руд.
- Подготовка запасов руд к выемке
Научный подход к решению проблемы рационального использования недр и комплексной переработки рудного сырья требует всестороннего изучения месторождений и своевременной подготовки их к эксплуатации, так как большие потери металлов возникают чаще всего на тех предприятиях, где слабо изучено рудное тело, неизвестен подробный вещественный состав руд, не проводится своевременно технологическое опробование подлежащих к выемке запасов руд.
Своевременная подготовка запасов руд к добыче является необходимым условием рационального использования недр и ритмичного обеспечения кондиционным сырьем обогатительных фабрик. Важнейшим элементом этой работы в плане комплексного использования сырья является эксплуатационная разведка, посредством которой уточняют количество, качество и пространственное расположение залежей руд.
В зависимости от густоты эксплуатационно-разведочных скважин горняки получают геологические данные с различной степенью достоверности. Более полная геологическая информация, на основании которой проектируют и выполняют буровзрывные работы, способствует снижению потерь и разубоживания руд при добыче. Дополнительные затраты на бурение сгущенной сети разведочных скважин вполне компенсируются сокращением ущерба от потерь и разубоживания. Для снижения затрат времени и средств на разведочные работы передовые предприятия отрасли применяют при технической помощи научных организаций ядерно-геофизические методы опробования руд и пород.
Преимущество ядерно-геофизического метода при разведке месторождений установлено, в частности, практикой работы Никитовского рудника. До 1970 г. разведку здесь осуществляли в основном подземными горными выработками. При этом на разведку одного профиля затрачивала 300–350 м выработок. С 1970 г. разведку рудных тел проводят станками НКР-100 м путем бурения с применением ядерно-геофизического метода опробования.
Внедрение нового метода разведки позволило сократить проходку горных выработок более чем в 5 раз и снизить стоимость разведки в 1,5 раза.
В этом отношении заслуживает внимания накопленный на Кальмакырском карьере опыт изучения запасов руд, подлежащих выемке. Для правильной разработки Кальмакырского месторождения и рационального использования запасов медных руд необходимо было получить достоверное оконтуривание различных типов руд, т. е. установить границы между ними и горной массой, правильно определить их технологическую характеристику и выдать рекомендации для селективной добычи. Как показали экспериментальные исследования, в условиях Кальмакырского карьера достоверность оконтуривания различных сортов руд обеспечивается опробованием по принятой в практике буро-взрывной сети (8-10 м между скважинами при высоте интервала опробования 10 м).
Для определения технологических сортов руд на руднике создана флотационная лаборатория, оснащенная необходимым оборудованием. Лаборатория может проводить массовые исследования геологических проб на обогатимость в различных режимах, соответствующих режимам обогатительной фабрики. Кроме того, рудничными геологами разработана геолого-технологическая классификация, позволяющая определять различные типы руд по результатам полевых наблюдений.
На основании геологических и технологических данных составляют сортовой паспорт взрыва для селективной добычи руды. В паспорте указывают границы верхней и нижней бровок уступа и линии предполагаемого отрыва, устья пробуренных взрывных скважин, содержание меди в руде, процент сульфидности, контакты пород, границы рудных зон по типам и сортам, а в окварцованных участках – содержание кремнезема. Копию паспорта взрыва передают машинисту экскаватора для ориентирования при работе в забое. Горный диспетчер заказывает железнодорожные составы для каждого экскаватора, поэтому весь состав рудного поезда загружают рудой только одного сорта согласно паспорту взрыва.
Подобным образом загружают составы забалансовой рудой или горной массой. На каждый состав выписывают накладную, содержащую все данные, характеризующие содержимое вагонов. Накладная является первичным документом, на основании которого определяют направление движения и место разгрузки состава. Без наличия накладной разгрузку руды на обогатительной фабрике или горной массы на отвале не производят.
2.2 Прогрессивные системы и методы разработки месторождений
Месторождения руд черных и цветных металлов находятся в различных географических и климатических зонах: в средней полосе, Заполярье, Приморье, в пустынных и высокогорных районах. Рудные тела залегают на разной глубине и резко отличаются по горно-геологическим условиям. Все это делает невозможным поиски универсальных решений технологии их разработки с целью обеспечения низких потерь и разубоживания руды при добыче.
Однако там, где это экономически оправдано, предпочтение отдают открытому способу разработки месторождений, удельный вес которого в добыче руд в настоящее время превышает 65%. Открытому способу присущи более низкие потери и разубоживание по сравнению с подземной добычей. Вместе с тем и на открытых работах ряда горных предприятий еще имеют место высокие потери и разубоживание руд при добыче. Сложные горно-геологические условия на некоторых карьерах вынуждают применять валовой способ отбойки руды и породы с последующей экскаваторной сортировкой взорванной массы в процессе погрузки на транспорт.
Одним из радикальных путей улучшения показателей использования недр на открытых горных работах является раздельная отбойка руды и породы, обеспечивающая по сравнению с валовой снижение потерь в 1,3-1,6 раза, а разубоживания – в 1,5-2 раза.
Технико-экономические преимущества применения раздельной отбойки руды и породы подтверждены практикой работы карьеров Казахстана в самых различных горно-геологических условиях. В результате внедрения этого способа только на свинцово-цинковых карьерах получен экономический эффект около 1,5 млн. тенге в год. Раздельная отбойка руды и породы внедрена также на ряде карьеров никель-кобальтовой, медной и вольфрамо-молибденовой промышленности.
При небольшой мощности рудных тел, сложной форме контактов руды и пород, малом фронте работ, когда применение раздельной отбойки ограничено, лучшие показатели извлечения руд из недр на карьерах дает под уступная выемка. Особенно полно достоинства этого метода проявляются в сочетании с отбойкой горной массы в зажатой среде. Отбойка в зажиме позволяет уменьшить перемешивание руды и породы при взрыве, а под уступная выемка создает более благоприятные условия для сортировки руды при погрузке. Применение отбойки в зажиме вызывает удорожание добычных работ на 10-12% за счет сгущения сетки скважин, увеличения расхода взрывчатых веществ (ВВ) и применения экскаваторной сортировки при погрузке. Но это удорожание перекрывается экономией от снижения потерь и разубоживания руды.
В этом отношении представляет интерес положительный опыт снижения потерь и разубоживания руды на карьерах Алмалыкского горно-металлургического комбината. Для предупреждения попадания руды в отвал, а породы на фабрику погрузку горной массы нового взрыва начинают только после получения результатов опробования буро-взрывных скважин и составления паспорта взрыва.
Нормативные величины потерь и разубоживания руды при отработке при контактовых зон определяют следующим образом. Вначале по сортовым по горизонтным планам в контуре, намеченном к отработке в планируемый период, определяют исходные данные (параметры рудных тел, количество и длину контактов, содержание металла в при контактовых зонах в руде, в породе, количество балансовых запасов в этом контуре). Затем определяют браковочное содержание и рассчитывают допустимое разубоживание для каждого контакта. По этим двум величинам посредством специального графика определяют границу выемки для каждого контакта. Количество теряемой руды в разубоживающей массы определяют по разработанной формуле.
На подземных горных работах наиболее эффективным направлением повышения показателей извлечения руд из недр признана система с закладкой выработанного пространства твердеющими смесями. Наибольшее развитие эта технология получила при добыче богатых руд. В никель-кобальтовой промышленности системами с закладкой добывают около 60% всей руды. Применение системы с твердеющей закладкой имеет и другие преимущества, в частности, позволяет отрабатывать запасы, законсервированные в охранных целиках под промышленными и естественными объектами, а также разрабатывать месторождения комбинированными (открытым и подземным) способами. Так, на Лениногорском комбинате с использованием этой технологии отработаны рудные тела в охранных целиках шахты и рек Филипповки и Быструхи.
На месторождениях, где невысокое содержание металлов в рудах не позволяет рентабельно применять системы с твердеющей или иной закладкой, могут использоваться другие способы разработки, обеспечивающие снижение потерь и разубоживания руды.
На Миргалямсайском руднике внедрена разработанная ВНИИцветметом столбовая система с обрушением налегающих пород. Она позволила снизить потери руды в 1,5 раза и разубоживание – в 1,4 раза при одновременном улучшении показателей по себестоимости добычи и производительности труда по сравнению с прежней камерно-столбовой системой, приводящей также к высоким потерям свинца.
Большое значение для снижения потерь и разубоживания руд имеет правильно организованное планирование горных работ. Планирование горных работ осуществляют в два этапа. На первом этапе составляют годовой план. При этом тщательно изучают данные эксплуатационной разведки, уточняют на их основе промышленные контуры рудных тел, вносят коррективы в проектные решения в части отработки фланговых зон, глубины выемки и т. д. На этом же этапе определяют плановые показатели потерь и разубоживания при добыче, которые утверждаются вышестоящей организацией.
Второй этап заключается в составлении месячных планов горных работ, утверждаемых руководством предприятия. Эти планы являются рабочим документом для коллективов участков, смены, экскаваторной бригады; по ним определяют размеры материального поощрения. Исходными данными для составления месячных планов служат результаты всех стадий разведки, а также результаты под уступного опробования, которое производят при помощи шнековых скважин по сетке 10X25 м с одно-двухмесячным опережением.
Ценность месячных планов состоит в том, что при их составлении можно оперативно учитывать данные геолого-маркшейдерских служб по результатам работы за предыдущий месяц, вносить коррективы в годовые планы, предусматривать дополнительные мероприятия по снижению потерь и разубоживания.
2.3 Селективная добыча и усреднение руд
В цветной металлургии разрабатывают сотни самых разнообразных по запасам, форме и условиям залегания месторождений. Рудные тела в большинстве случаев характеризуются большой сложностью. Сплошные руды перемежаются вкрапленными с пустыми породами и забалансовыми рудами. Часто одно и то же месторождение содержит несколько технологических сортов руд, которые в силу их различных физико-химических свойств необходимо добывать и перерабатывать раздельно.
Специфической особенностью большинства месторождений является ухудшение горно-геологических условий с увеличением глубины разработки: уменьшаются мощности рудных тел, снижается содержание полезных компонентов, усложняется вещественный состав руд, ухудшаются физические и механические свойства руд и вмещающих пород.
Несмотря на такое многообразие изменяющихся факторов, необходимо обеспечить отгрузку на обогатительную фабрику руды постоянного состава в полном соответствии с техническими условиями для получения плановых технико-экономических показателей (извлечение металлов, качество концентратов и т. д.) при ее обогащении. Эту важную задачу решают двояко. При наличии нескольких резко отличающихся по своим технологическим свойствам сортов руд и благоприятных условиях их залегания производят их селективную добычу и отгрузку по сортам на обогатительную фабрику. В случае, когда отдельные типы руды несущественно различаются по технологическим свойствам, а селективная выемка невозможна, применяют метод усреднения руд на пути от забоя до дробильного отделения обогатительной фабрики, чаще всего – на промежуточном складе.
Селективная добыча различных типов руд и переработка их по сортам позволяет применять наиболее пригодные для данного сорта технологические схемы и режимы флотации, подобрать оптимальные реагенты и добиться максимального извлечения денных компонентов.
Изучение пространственного размещения сортов руд на Тишинском, Белоусовском и Салаирском рудниках показало, что сорта руд достаточно четко обособлены в пространстве и по горно-геологическим условиям предприятий могут быть добыты раздельно. Эта возможность была учтена при планировании добычных работ, что позволило подавать на фабрики руды требуемого состава и повысить извлечение металлов при их переработке.
В настоящее время раздельную добычу сульфидных и окисленных (смешанных) руд применяют повсеместно, причем окисленные руды или перерабатывают по специальным технологическим схемам (Джезказганская фабрика), или направляют в отвалы для временного хранения. Необходимо отметить, что в практике горных и горно-обогатительных предприятий для стабилизации состава руды, подаваемой на обогатительные фабрики, чаще используют методы усреднения.
Эффективность усреднения для повышения извлечения металлов при обогащении руд видна на примере создания прикарьерного усреднителыюго склада Сорского молибденового комбината. Сорское месторождение медно-молибденовых руд представляет собой штокверк сложной формы гидротермального происхождения. Четкой границы между промышленными и непромышленными участками нет. Условные контуры рудных тел определяют только по данным опробования буро-взрывных скважин. Для месторождения характерно относительно низкое содержание и неравномерное распределение полезных компонентов.
По техническим условиям обогащения руд колебания в содержании сульфидного молибдена в перерабатываемой руде не должны превышать γ 30%.
Данные опробования в массиве показывают, что содержание молибдена изменяется более чем в десять раз, а анализ среднесменных содержаний молибдена в добываемой руде колебался в пределах γ 3-60%. Вследствие этого при переработке легко и среднеобогатимых руд резко изменялось как извлечение молибдена, так и содержание его в концентрате.
На комбинате установили зависимость извлечения молибдена от содержания его в руде и разработали рациональную схему усреднения руд. Для внедрения этой схемы аккумулирующий склад был перестроен в усреднительный. Переработка усредненной руды позволила повысить извлечение молибдена в концентрат на 1,1%.
2.4 Добыча и переработка забалансовых, потерянных руд и вскрышных пород
На разрабатываемых и отработанных месторождениях цветных и черных металлов накопились большие запасы неиспользуемых забалансовых, потерянных руд и вскрышных пород. Эти запасы образовались по различным причинам: из-за пониженного против кондиций содержания металлов (забалансовые руды), сохранения в выработках охранных целиков, старой закладки, обрушенной кровли и маломощных, невыгодных для отработки участков рудных тел (потерянные руды). Отвалы образовались за счет поступления в них вскрышных пород с приконтактовых зон месторождений с небольшим содержанием металлов. Экономичная переработка указанных руд и вскрышных пород по стандартным технологическим схемам в большинстве случаев невозможна.
В связи со снижением содержания металлов на многих месторождениях и резким возрастанием потребностей промышленности всех стран в цветных металлах постоянно изыскиваются и разрабатываются новые способы для добычи и переработки забалансовых руд, извлечения металлов из потерянных руд и вскрышных пород.
Наиболее распространенными на практике методами являются добыча забалансовых руд с последующей концентрацией в тяжелых средах, гидрометаллургическое извлечение металлов из руд на месте залегания (подземное выщелачивание) и гидрометаллургическое извлечение металлов из руд и вскрышных пород, находящихся в отвалах на поверхности (кучное выщелачивание).
Забалансовые руды, признанные ранее некондиционными из-за низкого содержания в них полезных компонентов, могут быть извлечены из недр впоследствии обычными способами разработки, если кондиции на подобные руды будут пересмотрены в сторону снижения. Это, разумеется, может быть сделано только при наличии соответствующих горно-геологических условий залегания этих руд.
Пересмотр кондиции может быть осуществлен, прежде всего, на те руды, для которых технически возможно и экономически целесообразно предварительное отделение пустых пород в тяжелых средах в голове процесса обогащения. Примером эффективности предварительной концентрации руд в тяжелых средах служит практика работы Зыряновского свинцового комбината. Технология обогащения руд в тяжелых средах на этом предприятии позволила добывать открытым способом и эффективно перерабатывать значительные количества забалансовых руд, дополнительно извлекая из руд свинец, цинк, медь и золото. При этом Получены и другие технико-экономические результаты: повысилось извлечение металлов при обогащении тяжелой фракции руды на переделе флотации, продлен срок рентабельного существования предприятия.
При благоприятных горно-геологических условиях потерянные руды также могут быть добыты обычными горными работами из охранных целиков, зон обрушения и закладочных камер, если содержание в них металлов позволяет осуществить их рентабельную добычу и последующую переработку. Чаще всего такие возможности ограничены; и для извлечения металлов из потерянных руд используют метод подземного выщелачивания.
Подземное выщелачивание применяют в США. Подготовки рудных тел к выщелачиванию на месте их залегания содержащих медь, свинец, цинк и уран. Основным способом подготовки рудного тела является создание в нем системы скважин, по которым подают выщелачивающий раствор. Обогащенный металлом раствор откачивают на поверхность для извлечения из него ценных компонентов. Данный способ исключает выемку горной массы и связанные с этим затраты.
Обычно дробление руды на месте залегания рудного тела производят путем взрыва. Конструкция заряда должна соответствовать физико-механическим свойствам руды и вмещающих пород, чтобы дробление на всех участках рудного тела было одинаковым. Вид ВВ выбирают в зависимости от их мощности, водоустойчивости и стоимости. Расход ВВ колеблется в пределах 0,6-2,4 кг/м3. Используют два вида зарядов: скважинные и камерные. В скважинном заряде ВВ распределяются лучше, и упрощается схема взрывания, но он более дорогой.
Для повышения эффективности процесса применяют также гидравлическое дробление руды выщелачивающим раствором, подаваемым в скважины под большим давлением. Для получения оптимального дробления учитывают характер трещин, геологию участка, физико-химические свойства пород и их химический состав. При гидравлическом дроблении используют усилие растяжения, при котором энергии расходуется меньше, чем при усилии сжатия или среза.
При создании системы подземного выщелачивания следует учитывать возможность нарушения и сдвига пород, а также загрязнение грунтовых вод, и что эти недостатки в некоторых случаях сводят на нет преимущества, получаемые от этого способа добычи металлов.
Ниже приведены два примера подземного выщелачивания в США. Па руднике «Биг Майк» (штат Невада) в бортах и на дне карьера осталось 430 тыс. т смешанной сульфидно-окисленной медной руды. Опытами было установлено, что 70%-ное извлечение меди может быть достигнуто путем выщелачивания сернокислым раствором с рН-2 при сравнительно небольшом расходе кислоты. Для отбойки руды пробурили 6,3 км скважин диаметром 146, 229 и 251 мм. Для дробления 540 тыс. т горной массы было израсходовано 180 т различных ВВ, в том числе и водонаполненных. В борту карьера на раздробленной руде сделали четыре бермы и проложили по ним распределительные полихлорвиниловые шланги диаметром 50 мм с укрупненными на них насадками. По шлангам подавали кислый раствор в количестве 760 л/мин, с рН = 1,6:2,0.
Просачиваясь по трещинам в раздробленной руде, раствор выщелачивал медь и самотеком поступал в собирающие выработки, расположенные в нижней части карьера (рисунок 1). У бортов карьера, в местах возможной утечки пробурили несколько контрольных скважин, с помощью которых определили, что потерь раствора и загрязнения грунтовых вод не происходит. Обогащенный медью раствор (2 г/л) откачивали через эксплуатационную скважину, пройденную в дне карьера на глубину 54 м.
На руднике «Олд Релайбл» (штат Аризона) медь также добывают подземным выщелачиванием. Рудный штокверк диаметром 122 м с глубиной залегания до 150 м имел запасы 4 млн. т руды с содержанием меди 0,8%. Для дробления руды массовым взрывом на трех горизонтах было пройдено 2250 пог. м минных выработок сечением 1,8X1,8м и заряжено 1,8 тыс. т аммиачной селитры.
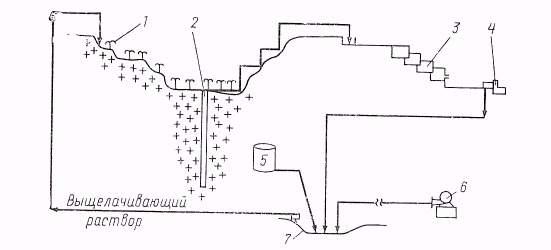
1 – система разбрызгивания; 2 – эксплуатационная скважина; 3 – камеры-отстойники; 4 – зумпф; 5 – емкость для серной кислоты; 6 – вспомогательный насос; 7 – бассейн для выщелачивающего раствора
Рисунок 1 – Схема подземного выщелачивания па руднике «Биг Майк»
При взрыве было отбито 3,6 млн. т руды и 1,9 тыс. т пустой породы. Расход ВВ при этом составил 330 г/т. Нарушение поверхности было минимальным, горная масса раздробилась на куски со средним размером 250 мм. В течение двух лет, с 1972 по 1974 г., добычу меди довели до 226 т. в месяц. В течение пяти лет должно быть добыто 13600 т. меди при извлечении 50%. Капиталовложения составили 2 млн. долл. Себестоимость металла на 30-50% ниже, чем на обычном руднике.
В цветной металлургии ведутся широкие исследования по извлечению меди из забалансовых, потерянных руд и вскрышных пород. Проведено обследование десятков горных предприятий с целью выявления возможности организации подземного и кучного выщелачивания подобных руд. Выполнены лабораторные и опытно-промышленные работы по определению режимов выщелачивания, расхода серной кислоты и других материалов. Разработаны методы экстракционного извлечения металла из растворов.
В настоящее время строятся и действуют несколько опытных, опытно-промышленных и промышленных установок для извлечения меди из руд методом кучного и подземного выщелачивания. Установки работают на рудниках Восточно-Казахстанского медно-химического, Медногорского медно-серного, Балхашского и Алмалыкского горно-металлургических комбинатов.
На Коунрадском руднике в настоящее время действует опытно-промышленная установка кучного выщелачивания забалансовых руд, построенная на основе результатов исследований Унипромеди. Отвал состоит из медной окисленной руды следующего состава, %: 1,46 Fe; 0,17 S; 76,32 SiO2; 11,86 А12О3; 0,17 СаО; 0,13 MgO; 0,002 Zn; 0,001 Pb. Медные минералы представлены на 76% окислами, на 13%-вторичными сульфидами, на 10,6% – первичными сульфидами и 0,4% составляют сульфаты. Максимальный размер кусков руды в отвале – в пределах 0,6-1 м. Отвал имеет уклон 1°.
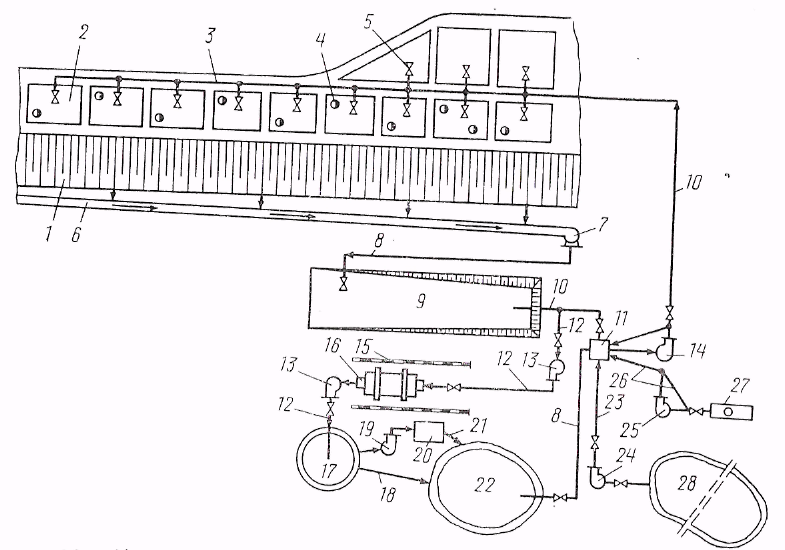
1 – отвал; 2 – оросительные прудки; 3 – трубопровод-коллектор диаметром 225 мм; 4 – скважины; 5 – задвижки; 6 – дренажная канава; 7 – насос; 8 – трубопровод диаметром 225 мм; 9 – прудок-отстойник емкостью 3000 м3; 10 – трубопровод диаметром 110 мм; 13, 14 – насосы; 15 – край-балка грузоподъемностью 2,5 т; 16 – цементатор производительностью 88 м3; 17 – сгуститель; 18 – желоб для слива осветленных растворов; 19 – насос; 20 – площадка для сушки цементной меди; 21 – желоб для стока растворов; 22 – прудок для хвостов емкостью 2500 м3; 23 – трубопровод диаметром 150 мм; 24, 25 – насосы; 26 – кислотопровод; 27 – кислотохранилище объемом 30 м3; 28 – бассеин поселка Коунрад
Рисунок 2 – Аппаратурно-технологическая схема кучного
выщелачивания на Коунрадском руднике
Для сбора растворов, вытекающих из-под отвала, с обеих сторон его пройдены дренажные канавы глубиной 1-1,5 м. На поверхности отвала имеется 12 оросительных прудков глубиной от 0,5 до 0,7 м, площадью по 250-270 м2. Аппаратурно-технологическая схема кучного выщелачивания показана на рисунке 2.
Приготовление орошающих растворов и их подкисленис серной кислотой производят в камере смешивания с помощью перекачивающего насоса, подающего часть растворов на рециркуляцию. Приготовленные растворы поступают по полиэтиленовым трубопроводам на поверхность отвала и распределяются по прудкам. Вытекающие из-под отвала медьсодержащие растворы собираются у кольцевой дамбы, откуда направляются на цементацию.
Цементацию осуществляют в барабанном цементаторе обезлуженным железным скрапом. Отстаивание цементной меди производят в сгустителе. Сгущенный продукт подвергают естественной сушке на асфальтированной площадке. Пробное выщелачивание ведут при содержании 5 г/л H2SO4 в орошающих растворах, плотности орошения 40 л/т, паузе в орошении 4 сут. В результате получают растворы с содержанием до 2,5 г/л Сu.
Результаты замачивания отвала водой и пробное выщелачивание свидетельствуют об отсутствии заметных потерь меди с растворами через грунт, что создает предпосылки для организации промышленного кучного выщелачивания забалансовых руд без перевалки их на специально подготовленные основания.
В меньшей степени готовности находятся исследовательские работы по подземному выщелачиванию медных руд, потерянных при разработке месторождений. Пока не найдено эффективных способов подготовки рудных тел к выщелачиванию для конкретных объектов, не установлена экономическая эффективность этой технологии и ряд других факторов.
Накопленный опыт позволяет сделать вывод о необходимости всемерного развития кучного выщелачивания забалансовых руд и вскрышных пород. Для решения вопроса о внедрении подземного выщелачивания медных руд требуется продолжение опытных работ в конкретных условиях того или иного месторождения.
3 Комплексная переработка руд на обогатительных
фабриках
Обогащение руд – основное звено в технологи переработки минерального сырья. Этот передел в значительной мере определяет комплексность использования сырья и технико-экономические показателя производства в целом по цветной металлургии. Металлы и другие ценные компоненты, которые не были извлечены из руд в процессе обогащения и остались в отвальных хвостах, по существу не будут использоваться долгие годы и обычно являются безвозвратными потерями.
На подготовку и обогащение руд затрачиваются огромные средства. Показатели извлечения металлов в металлургическом производстве в основном определяются качеством концентратов, вырабатываемых на обогатительных фабриках. Поэтому совершенствование техники и технологии обогащения руд является важнейшим звеном в повышении технического уровня цветной металлургии.
Комплексное использование рудного сырья на обогатительных фабриках будет улучшаться за счет совершенствования техники, технологии, организации производства и подготовки, руд с целью получения максимального прямого извлечения основных компонентов рудного сырья в готовую продукцию; внедрения технологических схем для извлечения из руд сопутствующих ценных компонентов; создания новых способов до извлечения металлов и других ценных составляющих из хвостов от обогащения руд; изыскания методов снижения потерь металлов с производственными растворами и сточными водами.
Совершенствование обогатительных процессов находится в прямой зависимости от создания тесной органической связи работы горных цехов и обогатительной фабрики, регламентированной соответствующими указаниями Министерства индустрии и торговли РК. Эти указания предусматривают детальное изучение вещественного состава руд на всех участках разрабатываемого месторождения; технологическое опробование руд; составление плана горных работ, обеспечивающих добычу руд нужного качества, и подготовку руд к обогащению.
3.1 Характеристика руд цветных и редких металлов
В настоящее время свыше 95% всех добываемых руд подвергают обогащению. Из них более 90% обогащают методом флотации. Небольшую часть руд направляют на металлургическую переработку. Независимо от того, обогащаются ли руды или поступают непосредственно на металлургические заводы, их химический и минералогический состав, физическое состояние оказывают большое влияние на полноту и комплексность извлечения ценных компонентов при последующей переработке. Ниже дается характеристика основных руд цветных и редких металлов.