Учебное пособие Павлодар удк 622 012 (07) ббк 30. 3я7
Вид материала | Учебное пособие |
- Курс лекций Учебное пособие Волгоград 2009 удк 330. 01 Ббк 65. 012., 6756.22kb.
- Учебное пособие Павлодар Кереку 2010 удк 53 (075. 8) Ббк 22. 3я73, 1449.38kb.
- Учебное пособие Павлодар удк339. 9 (075. 8) Ббк 65., 1778.36kb.
- Учебное пособие Павлодар удк 94(574+470. 4/. 5+571. 1)(075. 8) Ббк 63. 3(5Каз+2Рос)5я73, 3633.95kb.
- Врамках программы «Прометей» Павлодар удк 94(574. 25)(075. 8) Ббк 63. 3(5Каз)я73, 3259kb.
- Учебное пособие для студентов естественных специальностей Павлодар, 2290.94kb.
- Учебное пособие разработано в соответствии с государственным стандартом специальности, 1131.24kb.
- Учебное пособие удк 159. 9(075) Печатается ббк 88. 2я73 по решению Ученого Совета, 5335.58kb.
- Практикум Новочеркасск юргту (нпи) 2010 удк 330 (075. 8) Ббк 65. 012. 1я73, 2097.42kb.
- Врамках программы «Прометей» Павлодар удк 94(574. 25) Ббк 63. 3(5Каз), 6238.86kb.
Рисунок 3 – Принципиальные технологические схемы
рудного самоизмельчения
Из опыта работы обогатительных фабрик известны следующие разновидности рудного самоизмельчения:
1) полное рудное одно и двустадийное самоизмельчение. При двустадийном измельчении вторая стадия осуществляется в виде рудногалечного измельчения, для которой галю берет с первой стадии;
2) рудное комбинированное одно и двустадийное измельчение. По существу, здесь применяют полусамоизмельчения, так как измельчение в одну стадию производят с загрузкой в мельницу шаров, а при двустадийном вторую стадию проводят в шаровых мельницах.
Загрузка шаров в мельницы самоизмельчения преследует двоякую цель – восполнить недостаток в крупно-кусковом материале и измельчить фракнию критического размера (около 25мм). При этом производительность мельниц возрастает, расход электроэнергии на 1 т материала снижается, улучшается гранулометрическая характеристика продукта. Доизмельчение продукта рудного самоизмельчания в шаровых мельницах (вторая стадия) также позволяет повысить пропускную способность мельниц рудного самоизмельчения по руде и рассматривается, поэтому как один из способов интенсификации процесса.
Применение рудного самоизмельчения повышает производительность труда, так как численность персонала, обслуживающего дробильно-измельчительный комплекс, сокращается на 30-35%.
4.3 Обогащение в тяжелых суспензиях
Одним из прогрессивных способов рудоподготовки является предварительное обогащение в тяжелых суспензиях. Сущность этого процесса заключается в разделении рудного сырья по плотности в гравитационном или центробежном поле в суспензии, имеющей промежуточную плотность между тяжелой и легкой фракциями. Тяжелые суспензии, применяемые при обогащении, представляют собой механическую звесь мелкодисперсных тяжелых – минералов, сплавов, металлов (утяжелителей) в воде. В качестве утяжелителей используют пирит, пирротин, барит, галенит, магнетит, ферросилиций, свинец. Большое распространение получил ферросилиций.
Применение данного метода обогащения руд способствует интенсификации горных работ, вовлечению в эксплуатацию бедных руд. Получаемая при этом пустая порода может быть использована в качестве строительного материала. Благодаря низкой стоимости обогащения в тяжелых суспензиях снижается общая стоимость переработки руд.
Процесс обогащения в тяжелых суспензиях состоит из следующих операций: подготовки руды к разделению; разделения руды в суспензии на фракции различной плотности; дренажа рабочей суспензии и отмывки продуктов разделения; регенерации утяжелителя.
Подготовка руды к сепарации заключается в дроблении ее до крупности, при которой происходит освобождение основной массы пустой породы (обычно 100-25 мм). Дробленую руду подвергают грохочению и промывке для удаления шламов и мелких фракций (классов), так как обогащение мелких классов этим способом менее эффективно, чем обогащение крупных. Нижний предел крупности чаще всего принимают равным 4-6 мм.
Разделение руды в суспензиях производят в сепараторах различных конструкций. Конструкция сепараторов определяет гидродинамику потоков суспензии и влияет на эффективность обогащения. Различают сепараторы с глубокой ванной (конусные, пирамидальные, колесные) и с мелкой ванной (барабанные, со шнековой разгрузкой тяжелой фракции). Разгрузка легкой фракции осуществляется самотеком или принудительно при помощи механических устройств. Чаще применяют комбинированный способ. Тяжелую фракцию разгружают при помощи аэролифта, сифоном или различными механическими приспособлениями. В отечественной практике применяют конусные сепараторы (Зыряновская фабрика) и колесные.
Способ регенерация утяжелителя зависит от природы утяжелителя. Ферросилиций, магнетит и пирротин регенерируют магнитной сепарацией. Общие потери утяжелителя составляют 100-750 г/т, в том числе с продуктами обогащения 30-600 г/т, с хвостами регенерации 40-80 г/т, механические 30-70 г/т.
Согласно исследовательским данным, этот способ применим к рудам многих месторождений с возможной общей годовой производительностью более нескольких десятков миллионов тонн. В настоящее время обогащение в тяжелых суспензиях используют пока на небольшом числе фабрик.
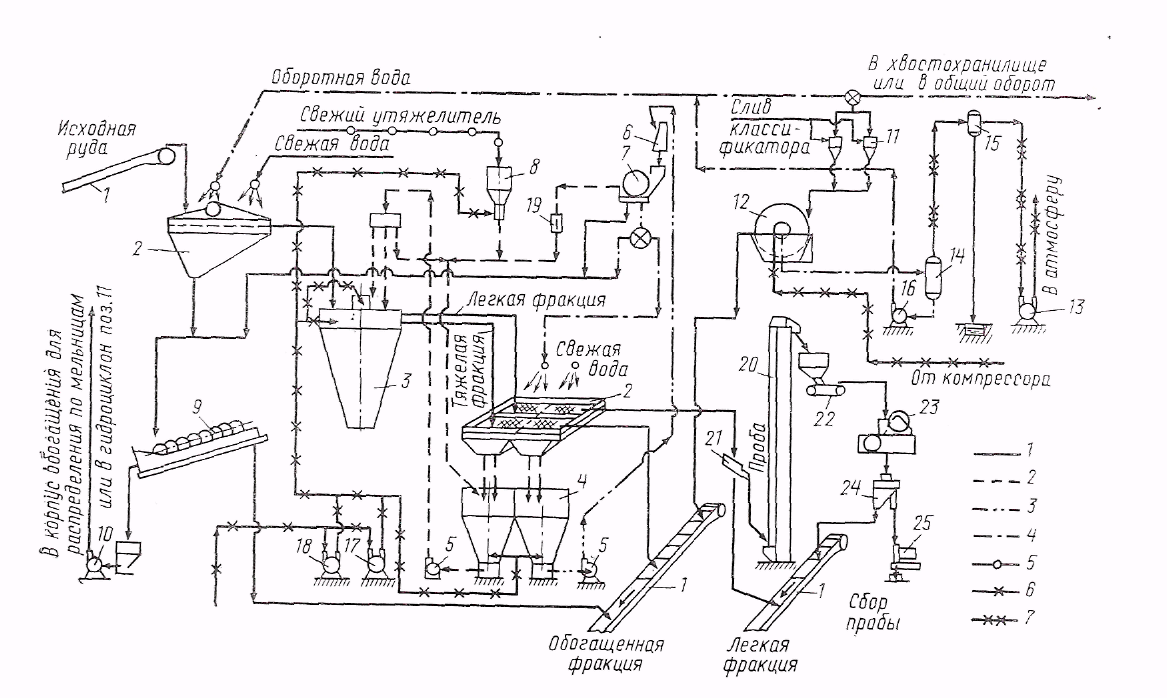
1– ленточный конвейер; 2 – самобалансный грохот (8 м2); 3 – конусный сепаратор диаметром 3 м; 4 – чаны кондиционной и разбавленной суспензии; 5 – насос для тяжелой суспензии; 6 – дуговой грохот; 7 – электромагнитный сепаратор диаметром 0,9 м; 8 – чан для приготовления суспензии; 9 – классификатор 1200X6500 мм; 10 – лесковый насос; 11 – гидроциклон диаметоом 350 мм; 12 – вакуум-фильтр; 13 – вакуум-насос; 14 – ресивер; 15 – ловушка; 16 – центробежный насос; 7 – компрессор; 18 – воздуходувка; 19 – размагничивающий аппарат 1200 Э; 20 – скиповой подъемник; 21 – пробоотбиратель; 22 – ленточный питатель; 23 – дробильный агрегат; 24 – сократитель; 25 – дисковый истиратель
Рисунок 4 – Схема цепи аппаратов опытно-промышленной
установки для обогащения руд в тяжелых суспензиях
В целях ускорения внедрения и сокращения сроков освоения этой технологии Механобр создал проект опытно-промышленного агрегата, представляющего собой малогабаритный комплекс аппаратов, объединенных поточной линией с минимальными высотными перепадами при их сопряжении. Производительность агрегата – до 100 т/ч. Схема цепи аппаратов приведена на рисунке 4.
В состав агрегата включен конусный сепаратор диаметром 3000 мм с комбинированным съемом легкой фракции и неподвижным центральным аэролифтом для разгрузки тяжелой фракции. Конусный сепаратор оборудован загрузочным устройством, позволяющим создавать горизонтальный поток на поверхности суспензии, что способствует повышению точности разделения за счет отсадки промпродуктовых фракций из слоя всплывшего материала.
Цикл регенерации состоит из одной стадии магнитной сепарации, осуществляемой в электромагнитном сепараторе 217-СЭ с напряженностью магнитного поля до 2500 Э. В схему включена также операция обезвоживания отсева класса – 6 мм для облегчения условий транспортирования его вместе с тяжелой фракцией при расположении агрегата на значительном расстоянии от корпуса обогащения. Проектом предусмотрены автоматический контроль и регулировка плотности и вязкости суспензии.
Несмотря на относительно высокую проектную производительность (100 т/ч), агрегат можно применять на рудниках малой мощности при работе его в одну или две смены, что экономичней работы в три смены агрегата менее высокой производительности. В то же время производительность указанного агрегата позволяет не только снизить удельный расход материалов, но и обеспечить получение надежных результатов.
Основные технико-экономические показатели агрегата при работе в три смены следующие:
Удельный расход на 1 т руды:
ферросилиция, кг ......... 0,120
магнетита, кг........... 0,080
электроэнергии, кВт-ч ....... 1,9
свежей воды, м3 ........ 0,5
Себестоимость передела 1 т руды, руб. 0,16
Численность обслуживающего персонала (технологического), чел/смену ..... 3
Выработка по руде на одного рабочего,
Т/Г°Д ......... 58300
Габаритные размеры, м........ 12Х18ХЮ
Масса агрегата в сборе ( руды), т.
В том числе технологического оборудования, т .............. 60
Агрегат запроектирован без привязки к конкретному промышленному объекту и может устанавливаться как вне здания, так и внутри производственных помещений шириной 12 м и более.
4.4 Совершенствование технологий измельчения и флотации
Большим резервом повышения комплексности использования рудного сырья на обогатительных фабриках является совершенствование технологических схем измельчения и флотации. Как показывает практика, при обогащении медных и медно-цинковых руд более 60% металла, теряемого с хвостами, содержится в классах менее 20 и более 70 мкм. Потери металлов в разноименных концентратах также в основном связаны с этими классами.
С. И. Митрофановым и другими специалистами рекомендуется несколько способов и технологических приемов повышения извлечения металлов из классов граничной крупности. Одно из перспективных направлений совершенствования процесса измельчения заключается в выводе готового по крупности продукта между стадиями измельчения или перед измельчением (рисунок 5). При этом снижается шламообразование и повышается производительность измельчительного отделения. Такая схема использовалась на Сибайской фабрике и позволила уменьшить выход класса – 5 мкм в питании флотации с 25-28 до 12-15%.
Если минералогический характер руд позволяет выделять часть минералов в пенный продукт при относительно грубом измельчении (межцикловая флотация, выделение медной или медно-цинковой «головки» и т.д.), то подготовку руд к флотации целесообразно осуществлять по схеме, представленной на рисунке 6. Схема предусматривает также контрольную флотацию шламовой части с получением отвальных хвостов с целью снижения переизмельчния.
Для предупреждения шламообразования при доизмельчении грубых концентратов и промпродуктов с большим эффектом можно использовать схему, показанную на рисунке 7. По этой схеме готовый класс из исходного продукта флотации выделяется перед доизмельчением в отдельной батарее гидроциклонов, а пески измельчаются в мельнице, работающей в замкнутом цикле с другими гидроциклокнами.
В некоторых случаях получение более тонкого материала в питании флотации, а также уменьшение количества готового материала в песках классификации, можно обеспечить путем введения контрольных операций в стадии классификации (рисунок 8). Применение этого метода на Среднеуральской обогатительной фабрике дало возможность получить в питании флотации 95-97% класса -– 0,074 мм.
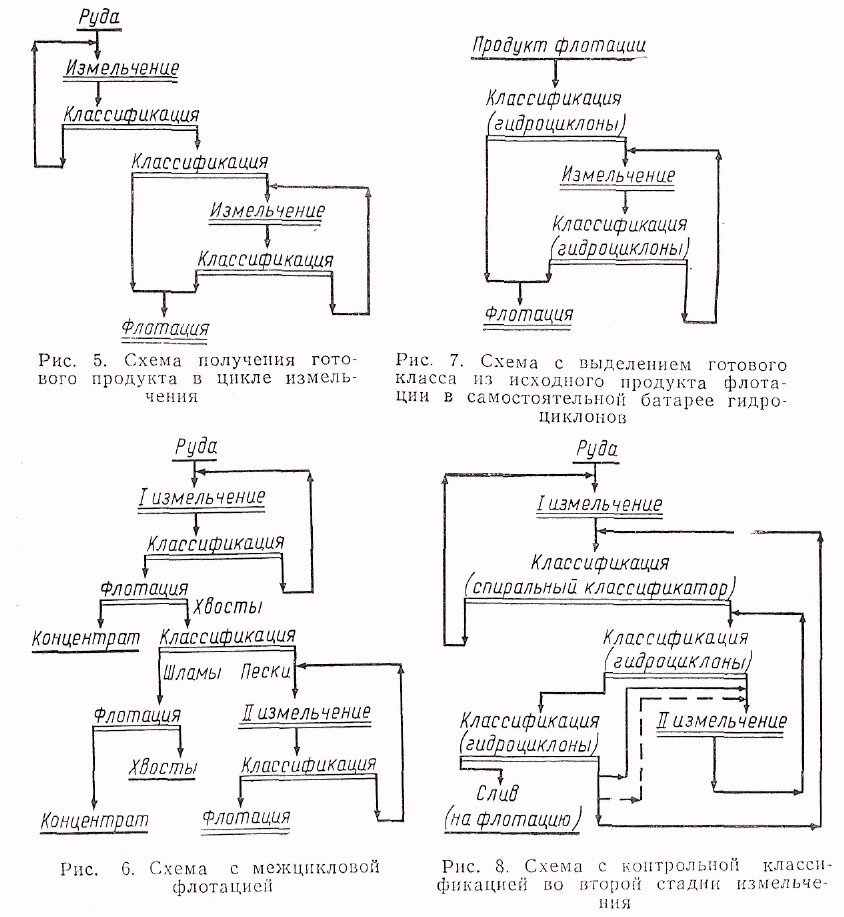
4. 5 Доизвлечение металлов из хвостов от обогащения руд
При изучении потерь металлов в хвостах обогатительной фабрики Балхашского горно-металлургического комбината от переработки коунрадских порфировых медно-молибденовых руд было установлено, что при среднем содержании в них 0,1-0,13% Сu и и 0,002% Мо в тонкой фракции хвостов содержится не более 0,06-0,1 % Сu и 0,0017% Мо. В песковой фракции содержание этих металлов составляет соответственно 0,16-0,2 и 0,0023-0,0027%.
После внедрения схемы доизвлечения меди и молибдена из песковой фракции хвостов на полный объем перерабатываемых на фабрике коунрадских руд и осуществления других мероприятий получили значительное количество меди и молибдена. При этом извлекали до 30-35% Сu и Мо путем флотации, доизмельчения и последующей перечистки, что соответствует извлечению 3% Сu и
5% Мо.
Для реализации указанной технологии были использованы шаровая мельница, гидроциклоны, флотомашины, насосы. Опыт Балхашского горно-металлургического комбината позволил на обогатительной фабрике №1 комбината «Печенганикель» в 1974 г. внедрить дофлотацию песковой фракции отвальных хвостов от обогащения руд Ждановского месторождения.
При обогащении медно-никелевых руд этого месторождения в хвостах флотации терялось по 25-27% Ni и Сu и свыше 30% Со. Основные потери наблюдались в виде сростков минералов с породой, магнетитом и пирротином в крупных (более 0,044 мм) классах, которые содержали 0,18-0,26% Ni, т. е. в 1,5 – и раза больше, чем в классах – 0,044 мм. Предварительными лабораторными исследованиями было установлено, что после обесшламливания хвостов из песковой фракции можно получить концентрат, содержащий 2-2,36 Ni: извлечение в него этого металла составляет 2,4-3,6% от массы руды.
Обесшламливание и классификацию хвостов осуществляли в гидроциклонах диаметром 750мм, перечистные операции – во флотомашинах М-7. Флотацию крупнозернистой фракции вели при плотности пульпы 40% твердого и следующем расходе реагентов, г/т руды: 20 – бутилового ксантогената; 3 – аэрофлота; 32 – ШЦ.
В результате промышленных испытаний получили концентрат содержащий 2,18% Ni. Извлечение никеля составило 2,75%. Содержание металла в объединенном товарном концентрате снизилось на 5% (отп.).
4. 6 Извлечение драгоценных металлов
Драгоценные металлы, в частности золото и серебро, присутствуют во многих сульфидных рудах цветных металлов (медных, свинцово-цинковых, сурьмяных, оловянных и др.) Более полное их извлечение повышает комплексность использования сырья и улучшает экономику производства. В отличие от металлургического передела, в котором золото и серебро получают с высокой степенью извлечения, на обогатительных фабриках допускаются еще значительные потери золота с хвостами, сливами, сточными водами и пиритными концентратами. Последние в большинстве случаев направляют на переработку на предприятия химической промышленности для производства серной кислоты, где все цветные металлы переходят при обжиге в огарок, который не подвергается дальнейшей переработке и накапливается в отвалах уже длительное время.
Разработка и освоение технологических процессов, способов и режимов работы обогатительных фабрик с целью повышения извлечения золота и серебра являются важнейшей научно-технической задачей научно-исследовательских организаций и промышленных предприятий.
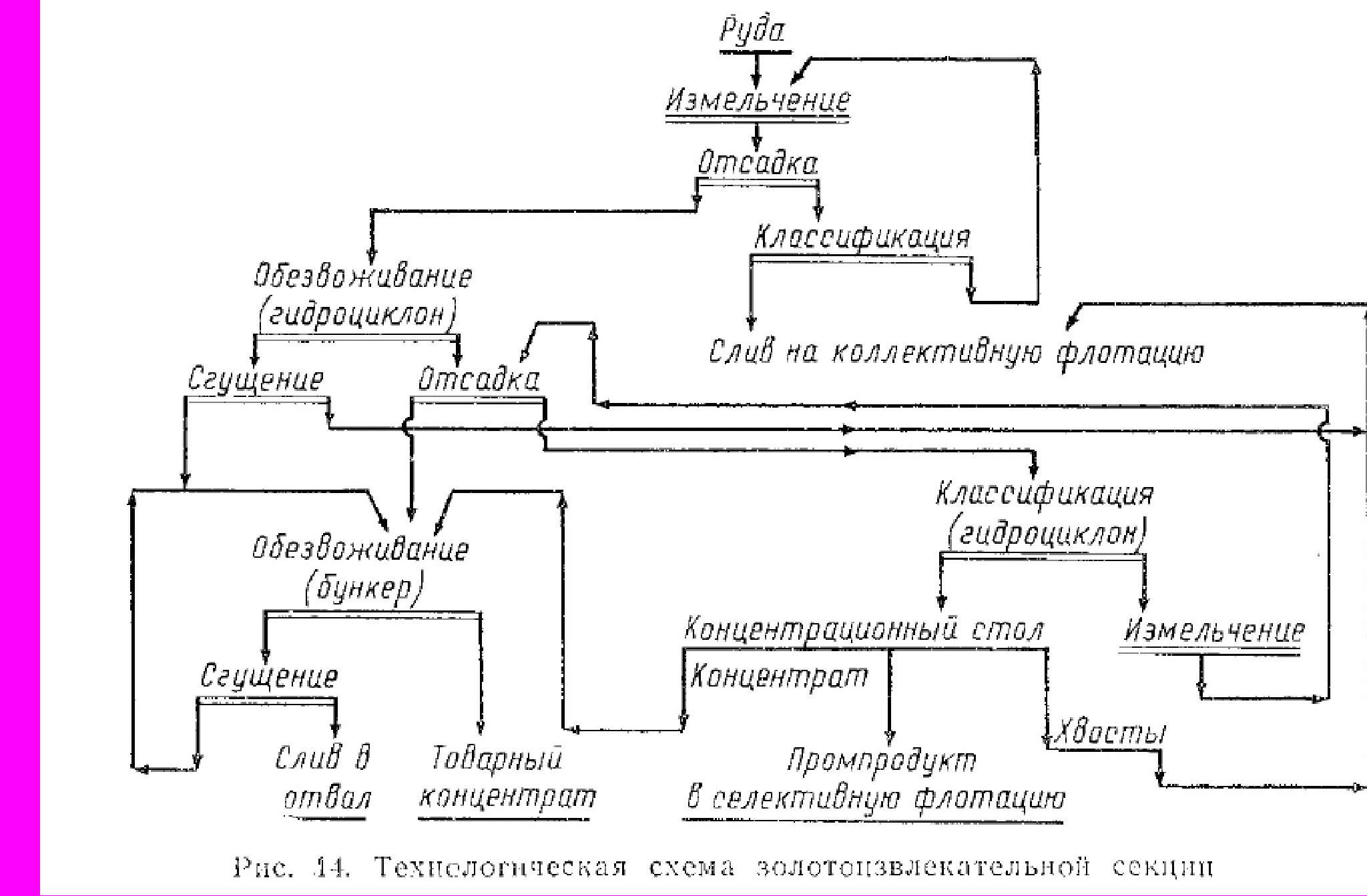
Рисунок 9 – Технологическая схема золотоизвлекательной
секции
Большим, еще недостаточно используемым резервом является извлечение присутствующего в рудах свободного золота.
Наиболее эффективными аппаратами для извлечения свободного золота в цикле измельчения являются отсадочные машины. Отсадочные машцны закрываются сверху металлической решеткой с отверстиями диаметром 9-10 мм, чтобы предупредить забивание постели крупным скрапом, поступающим из мельниц. Извлечение золота на этих машинах зависит от тонины помола руды, формы и размера свободного золога. Важно стабилизировать расход подрешетной воды, чтобы не выносить мелкое золото в хвосты отсадки. Черновой концентрат предпочтительней обрабатывать до товарного с содержанием золота 100-200 г/т.
Из отвальных хвостов золото извлекают перефлотацией после предварительной классификации и доизмельчения. Лучшие показатели достигаются при использовании комбинированной схемы с применением процессов гравитации, флотации и цианирования.
4.7 Попутное извлечение нерудных ископаемых
На одном из горно-обогатительных комбинатов совместно с рядом научно-исследовательских институтов разработана и внедрена на обогатительной фабрике технология извлечения слюды из отвальных хвостов от переработки пегматитовых редкометальных руд. Молотая слюда -– мусковит -– имеет большое хозяйственное значение. Мусковит широко применяют в производстве сварочных электродов, электроизоляционных смесей, обоев, лаков, красок, а также в резинотехнической и других отраслях промышленности. Технологическая схема включает операции доизмельчення хвостов гравитационного обогащения, их обесшламливание, коллективную флотацию мусковита и биотита катионным собирателем АНП-14 в содовой среде.
С целью снижения содержания железа в слюдяном концентрате схема дополнена операцией – флотацией биотита из коллективного концентрата олеатом натрия. С освоением этой операции удалось получить слюдяной концентрат, отвечающий по содержанию железа и фосфора требованиям производства сварочных электродов. Мусковитный концентрат подвергают сгущению в шламовых конусах, фильтрации на ленточных вакуум-фильтрах и сушке в барабанных электрических сушилках. Освоение технологии попутното извлечения слюды на Огневской обогатительной фабрике позволило наладить обеспечение производства сварочных электродов дефицитным материалом.
4.8 Доизвлечение ценных компонентов из производственных растворов и сточных вод
Полное и комплексное использование сырья цветной металлургии немыслимо без эффективных способов извлечения цветных и редких металлов из производственных растворов и сточных вод промышленных предприятий. К этим способам относятся ионная флотация, электролитическая флотация (электрофлотация) и адгезионная сепарация. Используя указанные процессы, можно извлекать малые количества растворенных и тонкодиспергированных веществ из больших объемов жидкости. Освоение процессов извлечения металлов из производственных растворов и сточных вод позволяет решить не только проблему комплексного использования сырья, но и проблему охраны водного бассейна.
Процесс ионной флотации молибдена из бедных растворов с содержанием металла 0,1-1 мг/л, получаемых при производстве молибдата кальция, освоен в промышленных условиях на Балхашском горно-металлургическом комбинате. Внедрение новой технологии позволило извлекать этот металл в высококачественную продукцию и сократить потери со сбросными растворами. Сквозное извлечение молибдена составило 85,6%.
На Зыряновской обогатительной фабрике впервые в цветной металлургии внедрена ионообменная очистка цианистых стоков фабрики с утилизацией цветных и драгоценных металлов. Опытно-промышленная ионообменная установка состоит из четырех сорбционных фильтров диаметром 3 и высотой 5,5 м, выпускаемых Таганрогским котельным заводом; электролизных ванн; четырех выпрямительных агрегатов ВАКГ-12/6-3000 и вспомогательного оборудования (баков, насосов, вентиляторов).
На установку направляют токсичный слив сгустителя медного концентрата в количестве 400-600 м3/сут следующего состава, мг/л: 500-700 – цианиды общие; 400-500 – медь комплексная; 40-50 Zn; до 0,7 Аи; до 4,5 Ag; 100-200 взвеси.
Слив сгустителя проходит последовательно сверху вниз два угольных фильтра для извлечения золота, серебра и очистки от органических веществ. Первый угольный фильтр одновременно выполняет роль песчаного фильтра, очищая стоки от взвешенных частиц. В качестве сорбента используют зернистый активированный уголь КАД-иодпый, загружаемый по 5 т в каждый фильтр при высоте слоя 2,5-3 м. Угольный сорбент состоит из 97% зерен класса – 5- 1 мм, 2% – 1+0,5 мм и 1%-0,5. Этот сорбент обладает высокой селективностью к золоту. На полном потоке производительность фильтров составляет 20-25 м3/ч при удельной нагрузке до 2 м3/м3 угля в час. Каждый из угольных фильтров работает непрерывно в среднем один месяц с нагрузкой 400-750 м3 стоков на 1 м3 угля. Извлечение золота составляет около 99%.
При нормальном режиме эксплуатации установки содержание золота в стоках после очистки оставляет от следов до 0,04 мг/л, серебра – от следов до 1,6 мг/л. Если не доводить сорбент до полного насыщения, степень очистки можно увеличить еще больше. Отработанный активированный уголь содержит 1-2 кг/т Аи и 1-3,5 кг/т Ag и направляется на переработку на Усть-Каменогорский свинщово-цинковый комбинат.
Кроме золота и серебра, в стоках содержится медь и цинк, которые извлекаются в третьем и четвертом ионитовых фильтрах, работающих попеременно. Сорбентом в них служит анионообменная смола марки АВ-17. Загрузка одного фильтра смолой составляет 3,5 т при высоте слоя 1 м. Фильтры работают по принципу противотока. Фильтрат из угольных фильтров подается снизу вверх в один из ионных фильтров (другой в это время находится на регенерации ионита и промывке). Скорость фильтрации на полном потоке поддерживают в пределах 3-4 м3/м3 ионита в час. Длительность сорбции цианистых соединений меди и цинка составляет 8-16 ч.
При полном использовании рабочей емкости фильтров извлечение меди и цинка достигает 95-99%. В сбросных растворах теряется 2-10 мг/л Сu и 0,6-2 мг/л Zn. Элюирование меди и цинка из ионита производится 18%-ным раствором поваренной соли с добавкой 2% каустической соды со скоростью 1 м3/м3 ионита в час. Извлечение меди и цинка из элюита и регенерацию последнего осуществляют в электролизере с нерастворимым графитовым анодом и медным катодом. Электролиз проводят при плотности тока 500-600 А/м2, температуре электролита 45-50°С и напражении на ванне, равном 5-5,5 В.
В процессе электролиза разрушаются цианистые соединения меди и цинка под действием хлора, выделяющегося при разложении поваренной соли. Наращивание катодного осадка происходит в течение месяца, после чего катод массой 60-70 кг заменяют новой медной основой. Состав катодного осадка зависит от соотношения металлов в стоках. Обычно в осадке содержатся: 45-80% Сu; 50- 15% Zn; 100-150 г/т Аu; 1000-1700 г/т Ag; и до 10 г/т Cd.
Трехлетняя эксплуатация опытно-промышленной установки для очистки стоков обогатительной фабрики полностью себя оправдала. Подтвердились удовлетворительные физико-химические свойства ионита АВ-17 при извлечении меди и цинка. Положительный опыт Зыряповского свинцового комбината может быть полезен для многих обогатительных предприятий отрасли.
4.9 Повышение качества концентратов
Экономическая эффективность металлургического производства в значительной мере зависит от качества исходного сырья – концентратов цветных металлов. Особое значение имеют содержание основного металла и количество вредных для последующего передела примесей.
Так, при пирометаллургическом производстве меди, никеля, свинца и других металлов приходится подвергать плавке всю массу концентрата с добавкой необходимого количества флюсов. Расход флюсов, топлива, электроэнергии, трудовые затраты на 1 т металла тем выше, чем меньше содержание основного металла в концентрате. При большом содержании в концентратах вредных примесей или породообразующих минералов, требующих ошлакования в процессе плавки, резко увеличивается расход флюсов, возрастают затраты на последующих переделах.
Существенное влияние на экономику металлургического передела оказывает извлечение металлов. При высоком содержании металла в концентратах потери их со шлаками, кеками и другими отходами сокращаются, а извлечение в товарную продукцию возрастает. Поэтому улучшение качества концентратов на обогатительных фабриках является одним из важных факторов повышения полноты извлечения металлов и комплексности использования сырья.
Есть несколько способов повышения качества флотационных концентратов. Обычный способ состоит в увеличении числа перечисток. Но он приводит к возрастанию циркуляционных нагрузок в процессе флотации до 500% и более и не всегда обеспечивает получение концентрата высокого качества, так как эффективность перечистных операций снижается по мере увеличения их количества.
С. И. Митрофанов и М. Я. Рыскин считают, что потери металлов при увеличении числа перечисток возрастают за счет тонких частиц – шламов, содержащихся в тонкоизмельченпой руде иногда в больших количествах. В связи с тем, что тонкие классы при различной твердости минералов обычно богаче металлом, чем крупные, эти исследователи предлагают улучшать качество концентрата не за счет увеличения числа флотационных перечисток, а путем классификации на шламы и пески с выводом шламов в товарный концентрат и последующей доработкой песков в цикле доизмельчения и флотации.
Предлагаемый метод был испытан на Урупской обогатительной фабрике. Шламовый анализ показал, что при классификации медного концентрата по классу 20 или 30 мкм можно получить шламовый концентрат с содержанием меди на 2-4% выше среднего и в 1,5-2 раза богаче песков при извлечении в него более 50% Сu. Из анализа флотационных хвостов следует, что более 70% Сu и драгоценных металлов концентрируется в тонких классах.
Ниже приведены результаты шламового анализа медного концентрата:
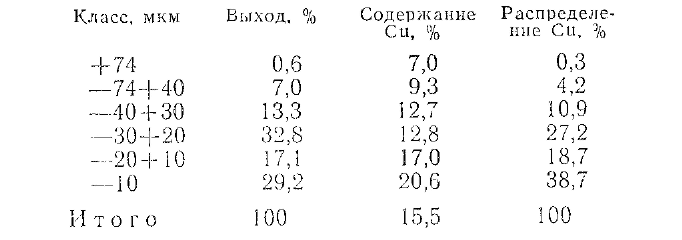
Для проведения промышленных испытаний во флотационном отделении фабрики были установлены два гидроциклона диаметром 350 мм. Концентрат второй перечистки классифицировали на одном из гидроциклонов. Шламы присоединяли к готовому медному концентрату, пески – на третью перечистку. Результаты классификации приведены в таблице 2.
Таблица 2 – Результаты классификации медного концентрата
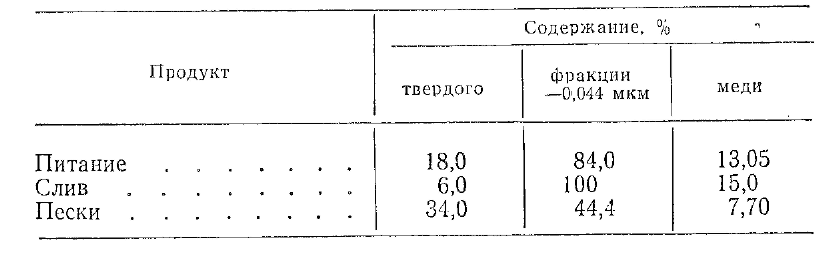
При повышении содержания меди в питании гидроциклона до 15-16% концентрация ее в сливе поднималась до 20-21 %.
Промышленные испытания показали, что классификация в гидроциклоне проходит успешно при снижении плотности пульпы в питании циклона до 17-20% твердого и что она полностью заменяет перечистку концентрата. В результате перечистки песков получали пенный продукт с 18-20% Сu и хвосты с 6-8% Сu. Общий медный концентрат содержал 16-18% Сu.
Сравнительные результаты испытаний по старой и новой схеме (с выводом шламов из концентрата второй перечистки в готовой продукт) приведены ниже, %:
Старая схема Новая схема
Медный концентрат..... 15,8/84,0 17,5/85,1
Хвосты......... 0,3/16,0 0,28/14,9
Примечание.
В числителе – содержание меди, в знаменателе – извлечение меди.
Таким образом, полученные в ходе испытаний результаты показывают, что повысить качество концентратов можно без снижения извлечения металла путем выделения шламов в готовый продукт перед последней перечисткой концентрата и доводкой песков классификации. При этом обеспечивается повышение содержания меди в концентрате на 1,5-2% и снижается себестоимость переработки руды за счет исключения операции доизмельчения грубого медного концентрата.
5 Проблема комплексного использования сырья в
металлургическом производстве
Металлургическое производство цветной металлургии характеризуется большим разнообразием сырья и применяемых технологических процессов, необходимых для извлечения в готовую продукцию и полупродукты 85 элементов Периодической системы
Д. И. Менделеева. Для большинства видов металлургической продукции стоимость сырья составляет основную статью затрат на производство. Все это определяет как экономическую целесообразность, так и техническую сложность более полного и комплексного использования сырья в производстве цветных, редких и драгоценных металлов.
За последние 15-20 лет в цветной металлургии осуществлен ряд крупных технических мероприятий, позволивших повысить комплексность использования сырья и технико-экономические показатели производства. Так, например, в свинцово-цинковсй и медной промышленности в результате внедрения кислорода при обжиге цинковых и агломерации свинцовых концентратов, при плавке медного и свинцового сырья в отражательных и шахтных печах и в процессе факельной плавки уменьшилось количество отходящих газов, сократились потери металлов, повысилось их извлечение. Наряду с этим возросла производительность агрегатов, снизился расход топлива.
Использование кислорода в шахтной свинцовой плавке позволило перейти на работу с высокоцинковистыми шлаками, что создало благоприятные условия для последующей переработки шлаков, так как выход их сократился и они стали богаче по содержанию цинка, кадмия и редких металлов. Уменьшение количества газов течей КС в цинковом производстве и повышение концентрации в них сернистого ангидрида положительно сказалось на работе смежного сернокислотного производства.
Значительный технико-экономический эффект был получен в результате совершенствования технологии рафинирования свинца, меди и очистки от примесей растворов медного, никелевого и цинкового производства. Внедрение современных систем пылеулавливания и газоочистки позволило резко сократить безвозвратные потери свинца, цинка, кадмия, селена и других ценных компонентов и улучшить условия труда в пирометаллургических цехах.
В настоящее время по степени извлечения основных металлов и комплексности использования сырья ряд металлургических предприятий свинцовой, цинковой, алюминиевой, медной, титано-магниевой, ртутно-сурьмяной и оловянной промышленности находятся на уровне показателей лучших зарубежных заводов. Вместе с тем в металлургическом переделе имеется еще немало неиспользованных резервов, реализация которых будет способствовать не только более рациональному использованию сырья, но и повышению технического уровня и улучшению экономики металлургического производства.
В числе неиспользованных резервов можно привести отсутствие пылеулавливающих сооружений за отражательными печами и недостаточную утилизацию конверторных газов в производстве серной кислоты на ряде медеплавильных заводов. Большим резервом является также организация комплексной переработки цинксодержащих шлаков свинцовой и медной шахтной плавки, разработка и освоение технологии комплексной переработки кеков, шламов, пылей и других полупродуктов и отходов металлургического производства.
Весьма эффективным направлением повышения комплексности использования сырья может служить дальнейшее внедрение технологических процессов с использованием кислорода и природного газа, развитие электротермии, разработка гидрометаллургических процессов с применением сорбции и экстракции, переход на непрерывные производственные операции, создание замкнутых технологических схем с полной переработкой полупродуктов, а также кооперирование и комбинирование различных производств в зависимости от характера перерабатываемого сырья.
Накопленный предприятиями и научно-исследовательскими институтами цветной металлургии опыт комплексного использования сырья показывает, что в целях достижения наилучших результатов эта работа должна быть организована, по следующим основным направлениям:
1) Повышение прямого извлечения цепных компонентов из сырья в товарную продукцию.
2) Комплексная переработка полупродуктов металлургического произволства.
3) Совершенствование пылеулавливания и газоочистки с переработкой пыле и утилизацией газов.
4) Доизвлечелие металлов из отвальных продуктов.
5) Организация водооборота и очистка промышленных стоков.
Основные потери металлов в пирометаллургическом производстве допускаются с отвальными шлаками и пылегазовыми выбросами. При гидрометаллургических процессах наибольшие потери происходят с твердыми отходами и промышленными стоками. Более полное извлечение ценных компонентов имеют те предприятия, на которых получается меньше отходов, газообразных выбросов и сточных вод. Наивысшие показатели имеют предприятия, применяющие близкую к безотходной технологию.
Создание безотходной технологии в металлургическом производстве является важнейшей задачей научно-исследовательских и проектных институтов цветной металлургии, а организация комбинированных производств – один из главных путей решения этой проблемы. Типичным примером подобных производств являются свинцово-цинковые и медно-никелевые предприятия, на которых образующиеся полупродукты в зависимости от их состава передают взаимно на переработку в соответствующую технологическую ветвь.
В связи с вовлечением в производство более бедных и труднообогатимых руд, усложнением их минералогического состава, необходимостью извлечения из сырья новых ценных для народного хозяйства компонентов задача комплексного использования сырья в металлургическом переделе становится все более трудной. Над ее решением работают крупные силы специалистов из многочисленных научных организаций и предприятий. Основные усилия науки направлены на разработку и внедрение высокоэффективных технологических процессов и оборудования, обеспечивающих наряду с повышением эффективности производства и производительности труда высокую комплексность использования сырья, улучшение санитарно-гигиенических условий труда и охрану окружающей среды.
5.1 Переработка коллективных продуктов обогащения
Генеральным направлением развития технологии обогащения руд цветных металлов была и остается – селективная флотация с получением монометаллических концентратов. Это направление обеспечивает наиболее полное и комплексное использование руд как при их обогащении, так и в металлургическом производстве.
Постоянное совершенствование средств и способов обогащения сложных по вещественному составу руд, применение новых более эффективных флотационных реагентов, внедрение многостадиальных технологических схем измельчения и флотации позволяет добиваться все более полной селекции минералов. Об этом красноречиво свидетельствует рост извлечения цинка из медно-цинковых руд Урала, повышение степени селекции свинца из комплексных руд Джезказганского месторождения и другие достижения обогатительных фабрик.
Вместе с тем в производство в возрастающих масштабах вовлекаются все более сложные руды, из которых получать монометаллические концентраты с высокими показателями извлечения значительно труднее. Поэтому выпуск концентратов высокого качества неизбежно связан с получением в процессе флотации промежуточных продуктов обогащения, содержащих сростки различных минералов, а также шламовые фракции, трудно поддающиеся селекции. В некоторых рудах взаимное прорастание сульфидов настолько велико, что разделить их механическими способами вообще невозможно. В таких случаях приходится после отделения пустой породы получать только коллективные концентраты. Состав этих продуктов самый различный и всецело зависит от характера руды и применяемой технологии обогащения.
В настоящее время с целью получения кондиционных концентратов промежуточные продукты обогащения подвергают неоднократным перечисткам и доводке и присоединяют к одному из монометаллических концентратов или разассигновывают по нескольким концентратам. При этом, естественно, часть металлов теряется с хвостами. Делается это вынужденно, так как металлургические методы переработки коллективных продуктов обогащения пока не получили широкого распространения.
Выделение промежуточных продуктов обогащения из цикла флотации и организация отдельной их переработки на металлургических предприятиях с более высокими, чем в обогащении, показателями, является одним из существенных резервов повышения сквозного извлечения металлов и комплексности использования сырья. Поэтому усилия научно-исследовательских институтов уже длительное время направлены на изыскание эффективных способов металлургической переработки коллективных продуктов обогащения.
В литературе описано достаточно много как пирометаллургических, так и гидрометаллургических методов переработки промежуточных продуктов обогащения, применение которых позволит повысить сквозное извлечение ценных компонентов из руды до металла.
5.2 Переработка медно-свинцово-цинковых промпродуктов
Большая исследовательская работа по переработке коллективных медно-свинцово-цинковых продуктов проведена
М. М. Лакерником с сотрудниками; ими разработаны и испытаны в полупромышленном масштабе на Иртышском медеплавильном заводе электротермические методы переработки различных коллективных продуктов обогащения.
Предварительными исследованиями было установлено, что наиболее целесообразным вариантом электротермической переработки медно-свинцово-цинковых продуктов является неполный обжиг с переводом части железа в штейн и части в шлак. Коллективный концентрат с добавкой флюсов и оборотных материалов обжигали на агломерационной машине, а агломерат плавили в закрытой, работающей под давлением, электропечи, оснащенной орошаемым свинцом или цинком конденсатором. В результате плавки получали отвальный шлак, медный штейн, черновой свинец, металлический цинк или возгоны. По этой технологии испытывали не только медно-свинцово-цинковые, но и медно-цинковые и свинцово-цинковые концентраты.
При переработке медно-свинцово-цинковых концентратов (2% Сu, 8,3% РЬ, 18,6% Zn, 21,7% Fe и 31% S) прямое извлечение меди в штейн составляло 96%, свинца в черновой свинец 32%, цинка в металл 64%. При плавке медно-цинкового концентрата (10,5% Сu; 2,3 РЬ; 16,5% Zn; 27% Fe и 39% S) извлечение меди в штейн достигало 97%, цинка в возгоны 87%, свинца в возгоны 83,2%.
Однако данный процесс не получил промышленного применения из-за низкого прямого извлечения цинка и свинца в черновые металлы, относительно больших потерь цинка в отвальных шлаках, малой производительности электропечи, а также низкого качества металлического цинка.
В Бухарестском институте цветных и редких металлов медно-свинцово-цинковый концентрат, содержащий, %: 4-7 Сu; 6-6,5 РЬ; 15-21,3 Zn; 23-26 Fe и 33-36 S, после соответствующей подготовки перерабатывали в опытной печи взвешенной плавки для последующего внедрения этого способа на заводе Байя-Маре. Плавку вели на штейн с содержанием 35-40% Сu. Свинец и цинк возгонялись и улавливались в виде пыли, состоящей из 16-20% РЬ и 43-45% Zn. В результате получили следующее распределение металлов по продуктам плавки, %:

Высокую степень отгонки цинка получали применением высокой температуры и окислительной атмосферы в реакционной шахте, что обеспечивалось применением шихто-воздушной горелки специальной конструкции. Процесс протекал с небольшим расходом топлива (природного газа) при высокой производительности печи
[5 т/(м3-сут)],
Из других возможных методов переработки медно-свинцово-цинковых промпродуктов следует назвать способ вельцевания. Если коллективные материалы не содержат большого количества свинца, то их можно предварительно обжигать в печах КС, а огарок подвергать восстановлению в трубчатых печах с возгонкой цинка, свинца и кадмия. Медьсодержащий клинкер перерабатывают в шахтных печах. Более подходящим материалом для вельцевания является медно-цинковый промпродукт, содержащий свинец в незначительных количествах.
Возможность гидрометаллургической переработки медно-свинцово-цинковых промпродуктов способом сульфатизации исследовал ВНИИцветмет. Промпродукт, имеющий состав, %: 24,8 Zn; 3,89 Сu; 6,86 Pb; 15,8 Fe и 28,2 S, подвергали перед сульфатизацией предварительному обжигу и выщелачивали затем слабой серной кислотой. Остаток от выщелачивания смешивали с серной кислотой и прокаливали в муфельной печи при 650° С в течение 4 ч. Сульфатный продукт выщелачивали водой, подкисленной серной кислотой.
Результаты опытов показали, что извлечение в раствор металлов составляет, %: 96,3 Zn; 95,5 Сu; 95,4 Cd. Железо, свинец и драгоценные металлы практически нацело концентрируются в свинцово-железистом кеке. Медь выделяли из раствора электролизом в виде губки при плотности тока 5000 А/м2. Цинковый раствор после очистки от примесей можно направлять на электролиз.
Таким образом, исследовательские и опытные работы свидетельствуют о принципиальной возможности отдельной металлургической переработки медно-свинцово-цинковых продуктов обогащения как пирометаллургическими, так и пидрометаллургическими методами. Необходимость дальнейшей разработки и практического применения этих методов должна определяться технико-экономическими расчетами для конкретных условий производства.
6 Комплексная переработка полупродуктов металлургического производства
6.1 Переработка шлаков и возгонов
На металлургических заводах в процессе обжига, агломерации, плавки сульфидного и окисленного сырья, конвертирования штейнов, получается значительное количество разнообразных по составу сухих пылей. Основную часть пылей составляют летучие металлы – свинец и цинк. Кроме них, в пылях концентрируются такие ценные компоненты, как кадмий, индий, селен, теллур. Вместе с тем в пыли переходят и элементы, значительно осложняющие их последующую переработку. К ним относятся мышьяк, хлор и фтор.
Наиболее тонкие пыли и несконденсировавшиеся металлы не улавливаются из газов в аппаратах сухого пылеулавливания – пылевых камерах, циклонах и сухих электрофильтрах – и выбрасываются в атмосферу (что является в настоящее время недопустимым) или улавливаются в устройствах для мокрой очистки газов – скрубберах, пенных аппаратах и мокрых электрофильтрах в виде пульпы. После сгущения пульпы получают шламы, содержащие также ряд ценных компонентов. Типичным представителем такого рода полупродуктов являются шламы промывного отделения сернокислотных цехов, в которых сосредоточиваются селен, ртуть, мышьяк и другие летучие элементы. В целях повышения комплексности использования сырья и повышения извлечения металлов металлурги стремятся разрабатывать новые и совершенствовать применяемые технологические процессы для уменьшения выхода пылей путем снижения температуры отходящих газов и скоростей в плавильных и обжиговых агрегатах.
Наряду с пылями в свинцово-цинковом и оловянном производстве в результате переработки шлаков и кеков образуются большие количества возгонов, в которых одновременно с цинком и свинцом концентрируются ценные компоненты и вредные примеси.
В силу специфичности своего состава пыли и возгоны, как правило, должны перерабатываться в отдельном цикле и по технологии, специально разработанной для данного материала. В этом случае достигается наибольшая полнота и степень использования большинства ценных компонентов. К сожалению, по различным причинам это делается не во всех случаях и часто пыли возвращаются в голову процесса, что значительно увеличивает потореи металлов.
6.2 Гидрометаллургические процессы
Гидрометаллургическая технология занимает особое место в решении проблемы комплексного использования сырья. Объясняется это рядом серьезных преимуществ гидрометаллургии перед пирометаллургическими методами. Общеизвестно, что с помощью гидрометаллургических процессов можно рентабельно перерабатывать бедное сырье, так как большинство производственных операций и соответствующих им затрат относится к количеству металла, а не к общей массе исходного сырья.
Благодаря высокой степени селективности гидрометаллургические методы обеспечивают более высокий коэффициент комплексности использования сырья и извлечение из него ценных компонентов, находящихся в незначительных количествах. В гидрометаллургических производствах наблюдаются меньшие безвозвратные потери металлов ввиду отсутствия газообразных продуктов процесса и возможности практически полно очищать промышленные стоки и растворы от цветных и редких металлов.
Большинство гидрометаллургических процессов осуществляется, как правило, непрерывно и легче поддается автоматизированному управлению, что создает предпосылки для получения высоких технико-экономических показателей.
Анализ развития гидрометаллургических методов показал, что пирометаллургические способы переработки сырья цветной металлургии имеют, как правило, ограниченные возможности по сравнению с гидрометаллургическими особенно при решении проблемы комплексного использования сырья и охраны окружающей среды. Пирометаллургические методы характеризуются значительными удельными капитальными затратами и высокими расходами топлива или электроэнергии. Органическим недостатком этих методов является выброс в атмосферу больших количеств токсичных газов и аэрозолей.
Вследствие этого за последние двадцать лет наблюдаются интенсивное развитие гидрометаллургических способов производства и неуклонное расширение масштабов и областей их применения в металлургии цветных металлов. Примером быстрого развития гидрометаллургических методов может служить медная промышленность.
Из имеющихся 50 зарубежных предприятий, использующих гидрометаллургию для производства меди, 19 находятся в США.
6.3 Использование фторсодержащих отходов алюминиевого производства
В электролитическом производстве алюминия получаются следующие отходы: хвосты флотации угольной пены, пыль электрофильтров, шламы газоочистки, угольные блоки, шамотный кирпич и т. д. Химический состав этих отходов весьма различен, но главными составляющими их являются углеродистая масса и соединения фтора с натрием и алюминием. Часть отходов образуется в виде пульпы и откачивается в отвал. Состав этих отходов приведен в таблице 3.
Таблица 3 -– Состав отходов при электролизе алюминия, %
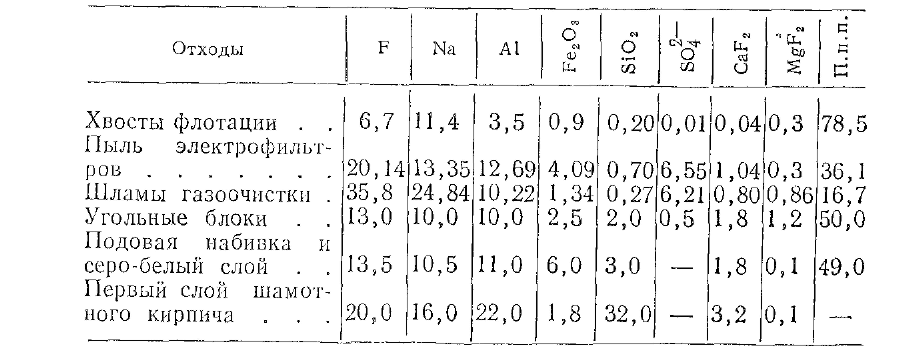
Красноярским алюминиевым заводом проведен ряд исследовательских работ по извлечению из отходов ценных компонентов путем их водного выщелачивания, а также щелочной и кислотной обработкой. Водное выщелачивание не дало положительных результатов. В раствор переходит в основном только небольшая часть сульфат-иона, карбоната и фторида натрия.
При щелочной обработке пылей электрофильтров и шламов газоочистки выход фторсолей составил 61,3% из обожженных и 37,9% из необожженных отходов.
При щелочной обработке выход конечного продукта получается низким, а расход щелочи высоким. Почти весь глинозем теряется с отвальным продуктом. Более эффективной является кислотная обработка отходов, которую проводят соляной, серной, азотной, а также плавиковой кислотами. Особенно хорошие результаты получены с применением плавиковой кислоты. Степень извлечения фтора и алюминия из обожженных продуктов была не ниже 90%. Результаты щелочной и кислотной обработки отходов и состав получспнбтх продуктов приведены ниже:
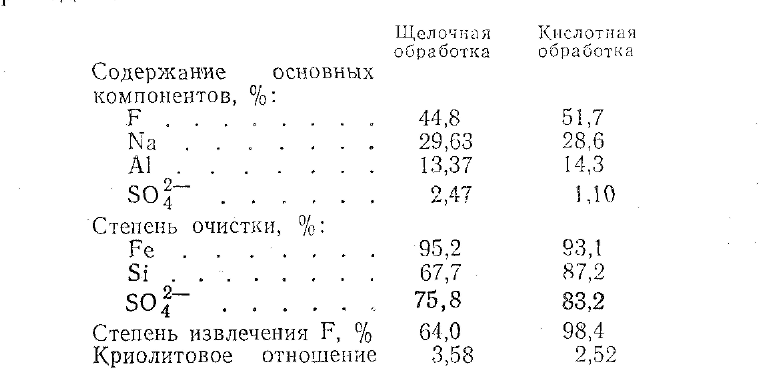
Красноярский алюминиевый завод совместно с Красноярским институтом цветных металлов им. М. И. Калинина ведет исследования процесса вакуумтермической отгонки фторсолей из угольных блоков и угольной пены. Предварительные исследования показали возможность извлечения фторсолей на 90%; фторидный конденсат получается хорошего качества (криолитовое отношение равно 2,7). Изыскиваются также возможности использования хвостов флотации угольной пены в производстве анодной массы.
Ряд работ, выполненных совместно с Сибпроектнии-цементом, направлен на использование твердых отходов в производстве строительных материалов в качестве минерализующих и катализирующих добавок взамен плавикового шпата.