Вступ
Вид материала | Документы |
- Вступ, 323.48kb.
- Програма дисципліни кредитний модуль " основи радіоелектроніки" (для груп фф) Вступ, 153.44kb.
- Питания з Програми з курсу «Механіка», що виноситься на зм 1 вступ, 86.8kb.
- Робоча навчальна програма здисципліни: Принципи І методи аналізу художнього твору Спеціальність, 222.75kb.
- План, вступ, викладення змісту теми (як правило, 2 глави), висновок, а також список, 24.79kb.
- Вступ України до Світової огранізації торгівлі. Законодавчі зміни. Галузеві стратегії”, 72.41kb.
- Робоча навчальна програма Модуля Вступ до спеціальності Для студентів спеціальності, 404.17kb.
- Вступ до історії україни 5-й клас (35 годин), 86.86kb.
- Вступ до історії україни 5-й клас (35 годин), 104.36kb.
- М. В. Ломоносов; [вступ ст., сост., примеч. А. А. Морозова]. Ленинград : Сов писатель,, 249.18kb.
Лекція 6
3.3. Технології переробки відходів газифікації твердого палива.
Основним видом відходу при газифікації вугілля є шлак. В залежності від типу і походження вугілля кількість шлаку при його газифікації може складати від 5 до 50% при продуктивності газогенератора в 45 т/год.
Нижче показано процес, розроблений Ф.Ф.Фондристом (пат.США 4174974, 20 листопада 1979 p. Фірма "Стандарт Ойл Компані, шт. Індіана), який призначений для виробництва портландцементу з зольного шлаку процесу газифікації вугілля.
Розплавлений шлак із газогенератора переміщується в реактор, куди завантажується також вапняк і проходить взаємодія, внаслідок якої утворюється однорідна маса. її охолоджують у спеціальній камері, де вона твердне, утворюючи клінкер. Його подрібнюють перетворюють в порохо-подібний цемент. Цей процес зображено на мал. 4.
Кам'яне вугілля подається в газогенератор 3 через живлювач 1. Вугілля спочатку очищують І промивають водою для зменшення в ньому попелу і піриту. Підготовлене вугілля накопичується в завантажному бункері 2, який зачиняється І знаходиться під тиском. По мірі необхідності вугілля надходить в реактор 3, де проходить його неповне окислення і утворюється синтез-газ, який містить водень, пари води, оксид вуглецю, вуглекислий газ. Синтез-газ виводиться із реактора через вентиль 5 і використовується для виробництва аміаку, метанолу, оксоспиртів і синтетичних вуглеводнів, тобто моторного рідкого палива.
Зольний шлак 4 поступово осідає в нижній частині газогенератора 3 де є пристрій для виведення шлаку 6. Пристрій являє собою вентиль спеціальної конструкції, який дозволяє регулювати швидкість подачі рідкого шлаку і знаходиться під тиском. Шлак з температурою 1550-1600°С через вентиль 6 поступає в резервуар 7 і накопичується в завантажувальному бункері 13, куди він поступає по лінії 15. В резервуарі 7 вапняк або вапно підігрівають гарячим повітрям, що входить з охолоджувальної камери 10 по лінії 20 із всмоктувачем-насосом 21.
Нагрітий вапняк або вапно під дією своєї ваги надходить по живильній грубі 12 до золотника 11, який регулює швидкість подачі сировини таким чином, що крильчатки 22, які знаходяться в резервуарі 7, забезпечують повне змішування шлаку з вапняком або вапном. В ході реакції проходить виділення вуглекислого газу, який виводиться з резервуару 7 по лінії 8. Співвідношення шлаку і вапняку складає 1:2. Змішування маси продовжується до одержання однорідної пасти, яку через випускний отвір 9 виводять з резервуару в охолоджуючу камеру 10. Тут проходить охолодження і виділення пасти з утворенням клінкеру, діаметр частинок якого від 0,6 до 5см, а переважаючим є діаметр частинок менше 2,5 см.
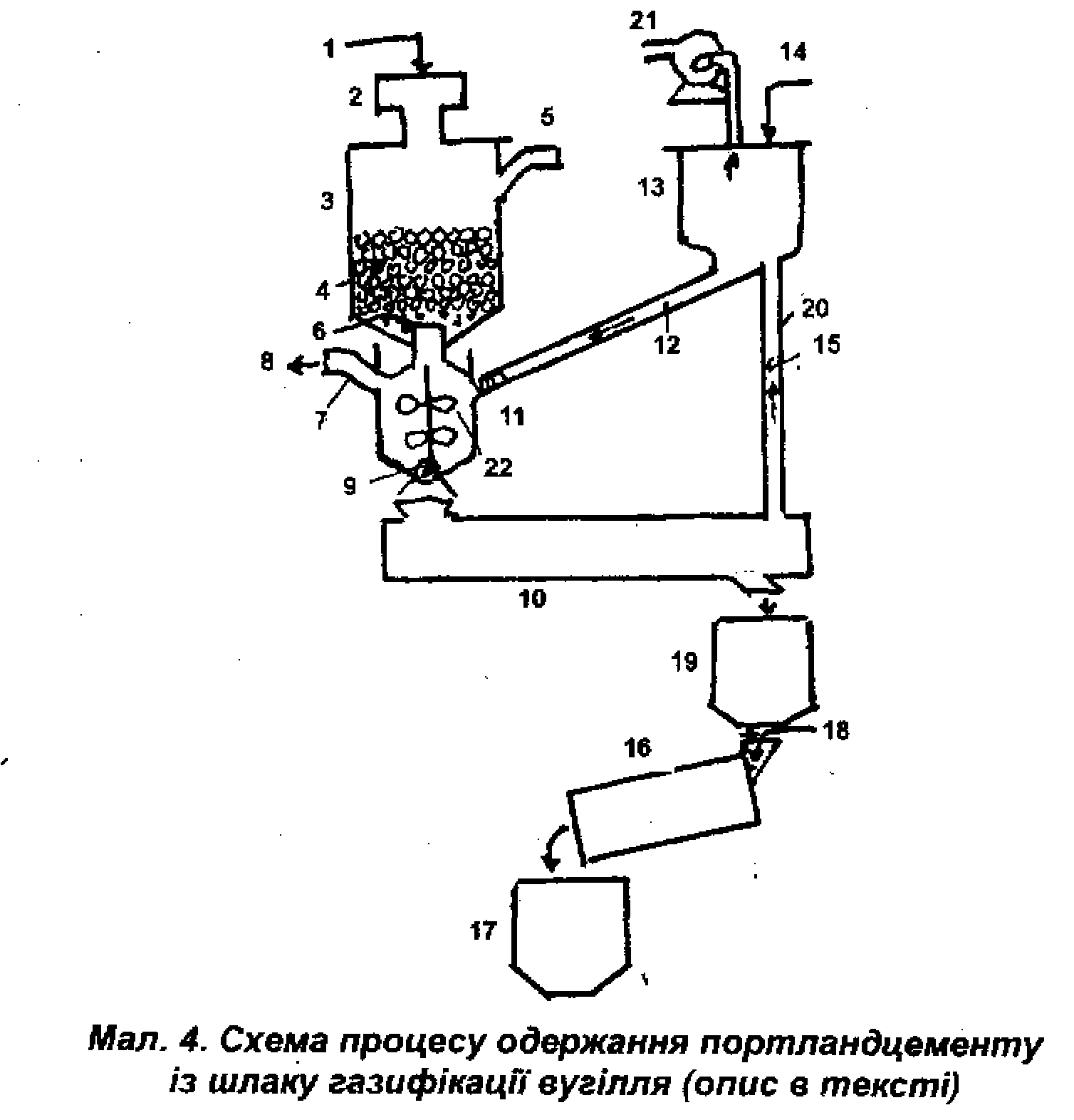
Стрічковий транспортер транспортує клінкер до місця його зберігання. Для охолодження клінкеру застосовується вода або повітря. Причому охолоджене повітря подають в камеру разом з пастою. Нагріте повітря виходить назовні.
3.4. Утилізація відходів коксохімії.
До відходів коксохімії відносяться кам'яновугільний пек, кам'яновугільний дьоготь, кисла смолка, фуси сульфітного відділення, полімери бензольного виробництва та ціаніди коксового газу.
Кам'яновугільний пек залишається після розгонки кам'яновугільної смоли при температурі вище 360°С і являє собою блискучий аморфний матеріал з характерним раковистим надломом. Він складається з високо-киплячих мас, смолистих речовин, вільного вуглецю, дисперсних частинок вугілля і коксу. Кам'яновугільний пек застосовується при виготовленні дьогтю і в шляховому будівництві.
Вимоги до кам'яновугільного пеку:
Щільність при 20°С, г/см3 1,20-1,30
вміст вільного вуглецю, в % не більше 28
вміст попелу, в % не більше 0,9
температура розм'якшення, °С 75-85
вміст води, в % не більше 5.
Кам'яновугільний дьоготь для шляхового будівництва готують на місці його використання. В котел заливають частину антраценового мастила, так, щоб воно покривало жарові труби. Потім завантажують кам'яновугільний пек, обезводнюють масу і нагрівають до 150°С. Топку виключають і доливають необхідну кількість передчасно обезводненого мастила, тобто яка залишилась. Вміст котла перемішують до одержання однорідної маси.
Кисла смолка утворюється в процесі очищення сірчаною кислотою бензольної фракції кам'яновугільної смоли. Це - чорна в'язка речовина із запахом сірчаної кислоти.
Властивості: щільність 1,24-1,26 г/см, в'язкість 7-11с. Центральна лабораторія Дніпропетровського хімічного заводу і Дніпропетровський інженерно-будівельний інститут запропонували використовувати кислу смолку після її нейтралізації для одержання шляхових дьогтів.
Розроблені три способи нейтралізації кислої смолки: гідрохімічний, холодний і теплополімеризаційний. Останній спосіб застосований на дослідно-промисловій установці Макіївського коксохімзаводу, а гідрохімічний - на Баглійському аналогічному підприємстві. Були одержані дослідні партії важких смол, тобто дьогтів.
Властивості нейтралізованої кислої смолки: щільність 1,24 г/см, в'язкість 20с. фракційний склад: відганяється до 170°С - 1,4% до 270°С -10% і до 300°С - 21%. Температура розм'якшення залишку після від бору фракції до 300°С дорівнює 46°С. Відноситься до властивостей шляхового кам'яновугільного дьогтю марок Д-4, Д-5, ДО. В 1970 р. на дослідній дільниці в Синельниковському районі Дніпропетровської області обладнане покриття на шляху методом співставлення, використанням нейтралізованої смолки Макіївського коксохімічного заводу. Експлуатація цієї дільниці шляху протягом шести років не погіршилася.
Фуси сульфітного відділення утворюються в процесі відстоювання кам'яновугільної смоли в сховищах. Вони складаються зі смолистих речовин (50-Н0%), вугільної та коксової пилюки, залізистих та інших залишків. Щільність tiycia 1,28-1,30 г/см3; Фуси розчиняються в ароматичних вуглеводнях - бензолі, юлуолі на 74-75% і являють собою в'язку масу чорного кольору. Кам'яновугільні фуси сульфітного відділення коксохімічних підприємств застосовують в якості в'яжучих речовин при устаткуванні шляхових фундаментів і покриттів. Перед використанням їх розбавляють антраценовим мастилом або .ирим кам'яновугільним дьогтем.
Полімери бензольного відділення - побічний продукт коксохімічної промисловості, який залишається після переробки прямого коксового газу. Полімери оензольного відділення - це речовини чорного кольору, в'язко-текучої консис-генції з неприємним запахом. Вони застосовуються для регенерації поглинаючого мастила, що вловлює бензол і інші ароматичні вуглеводні. На деяких підприємствах їх, як правило, спалюють, а тепло, що виділяється, використовують для потреб виробництва.
Властивості полімерів бензольного відділення: щільність 1,18-1-34г/см , температура розм'якшення 50-80°С; фракційний склад - відганяється до 170°С -1,7%, до 270°C - 9,2% і до, 300°С - 25%.
Ці речовини рекомендують також застосовувати як в'яжучі матеріали для укріплення грунтів під' фундаменти шляхів або при обладнанні покриттів на шляхах.
Одержання ціанідів з коксового газу. Коксовий газ містить багато компонентів і серед них невелику кількість ціаністих сполук, в,які переходять 1-2% .ізоту. що е в коксовому вугіллі. Утворення ціаністих сполук відбувається за рахунок реакції взаємодії аміаку, що є в газі, з оксидом вуглецю за оеакцією'

Деякі кількості ціаністого водню утворюється і в інших процесах, так, наприклад, в результаті взаємодії аміаку з вуглецем, метаном або етиленом- а також внаслідок розпаду триметиламіну, що знаходиться в газі, на ціаністий водень і метан.
При водному промиванні коксового газу в розчин переходять поряд з і.инільною кислотою також аміак, сірководень і вуглекислий газ. Дистиляція отриманого розчину дає можливість виділити з верхньої частини колони до 98% всієї кількості ціаністого водню з невеликою кількістю аміаку. '.Ірководень і вуглекислий газ виходять з колони в газоподібному стані. В «убі залишається до 99,5% аміаку у вигляді розбавленого розчину. Розчин чіаністого водню у воді, тобто синильну кислоту, перетворюють в сіль -цшністий натрій, обробкою розчином їдкого натрію; далі випаровують воду і кристалізують саму сіль.
3.5. Матеріали, які отримують при переробці відпрацьованих нафтопродуктів.
До відходів нафтопереробки відносять бітуми, які отримують після глибокого відгону з гудрону мастильних фракцій або при окисленні гудрону повітрям, а також залишки після вакуумної дистиляції. Відходи утворюються також при ректифікації вторинних продуктів-термічного та каталітичного крекінгу, риформінгу, гідролізу та дегідрогенізації.
Але основними відходами цієї галузі є використані нафтопродукти-відпрацьовані моторні, індустріальні і інші мастила, особливо ті, що залишаються після роботи в автодвигунах.
В процесі роботи у верстатах, машинах і механізмах мастила та й палива з нафтопродуктів стикаються з металами, повітрям, забруднюються водою, пилом, розбавляються паливом, вологою, металом, іншими речовинами, підлягають дії високої температури, тиску, електричного поля, світла, а також інших негативних впливів, які втрачають свої початкові властивості.
Як показали наукові організації, ресурси відпрацьованих мастил в народному господарстві колишнього СРСР складали в середньому близько 30% вихідних нафтопродуктів. Однак фактичні їх витрати значно більші, як і сам їх збір. Тільки в 1985 році збір використаних мастил і інших нафтопродуктів склав 2500 тис. т.
На Україні ця проблема в наш час набуває особливого значення в зв'язку з великою нестачею нафтопродуктів та інших енергоносіїв.
Відпрацьовані нафтопродукти забруднюють грунт, водойми, повітря. В той же час раціональне їх використання не тільки поліпшує забезпечення народного господарства нафтопродуктами та речовинами їх переробки, але й сприяє зберіганню запасів нафти і охороні довкілля.
Які ж є шляхи регенерації відпрацьованих нафтопродуктів!?
З метою спрощення технології збору, первинної обробки, а також більш повного повернення мастил у виробничий цикл, за технологічними умовами на відпрацьовані нафтопродукти їх поділяють на три основні групи в залежності від призначення:
1. ММВ - мастила моторні відпрацьовані і їх промислові суміші з в'язкістю не менше 30 сСт при 50°С.
2. МПВ - мастила промислові відпрацьовані і їх суміші, а також турбінні і компресорні.
3. СНВ - суміш нафтопродуктів відпрацьованих, в тому числі мастил, бензину, перегону і дизпалива, призначеного для переробки в суміші з нафтою.
Автомобільний транспорт України споживає приблизно 20% нафтопродуктів, що добуваються, а витрати на придбання палива і мастил складають більше 30% загальних витрат автогосподарств. З цієї кількості близько половини витрачається на заміну відпрацьованих мастил.
Дня кожної групи відпрацьованих мастил і нафтопродуктів повинні бути окремі резервуари з відповідним маркуванням і місткістю не менше 4м
Горловини резервуарів повинні мати захисну сітку з числом прорізів менше 900 в 1 см3 (75 меш) і герметичні кришки для запобігання потрапляння " резервуар сторонніх предметів і вологи.
Взимку сховища з відходами нафтопродуктів обладнують засобами підігріву або теплоізоляції, яка забезпечує вільну перекачку мастил в автоцистерни, якщо сховища-резервуари знаходяться в неопалюваних приміщеннях. Нафтопродукти, які мають механічні домішки, метали, вологу і ін., зберігаються окремо, якщо кількість сторонніх речовин складає більше норми. Зібрані так відходи нафтопродуктів централізовано транспортуються на спеціальні приймальні пункти.
Всі методи очищення нафтопродуктів поділяються на фізичні, хімічні, фізико-хімічні та комбіновані.
До фізичних або механічних методів очищення мастил відносяться відстій - перша операція будь-якого методу очищення мастил, фільтрування та сепарація з центрифугуванням.
Відпрацьовані індустріальні, компресорні, трансформаторні і турбінні мастила, а також інші нафтопродукти підлягають відстою для відділення води і механічних домішок.
Мастило, яке підлягає відстою, заливається в бак-відстійник і підігрівається до 80-90°С. Підігріте мастило відстоюється при виключених нагрівачах. Тривалість процесу відстоювання залежить від характеру обводнення і забрудненості мастила. Чим менше в мастилі води та механічних домішок і чим менші розміри частинок води та домішок, тим триваліший процес відстоювання.
Індустріальні мастила пропонують відстоювати протягом 24-48 годин. Щоб уникнути скаламучення мастила у відстійнику, не треба доливати нову порцію його за час відстоювання. Після охолодження до 30-40°С із відстійника випускають воду і бруд з нижньої частини - конусу апарату. Потім беруть пробу мастила на скло і перевіряють на світло якість очищення: якщо на склі у тонкому шарі мастила виявляється мутність або частинки механічних домішок, то мастило знов нагрівають до 80-90°С і продовжують відстоювання.
На мал. 5 зображені стаціонарні мастиловідстійники прямокутного перерізу періодичної дії. Шаровий поплавець 4 у шарнірному трубопроводі З дає можливість завжди забирати мастило з верхніх добре відстояних шарів.
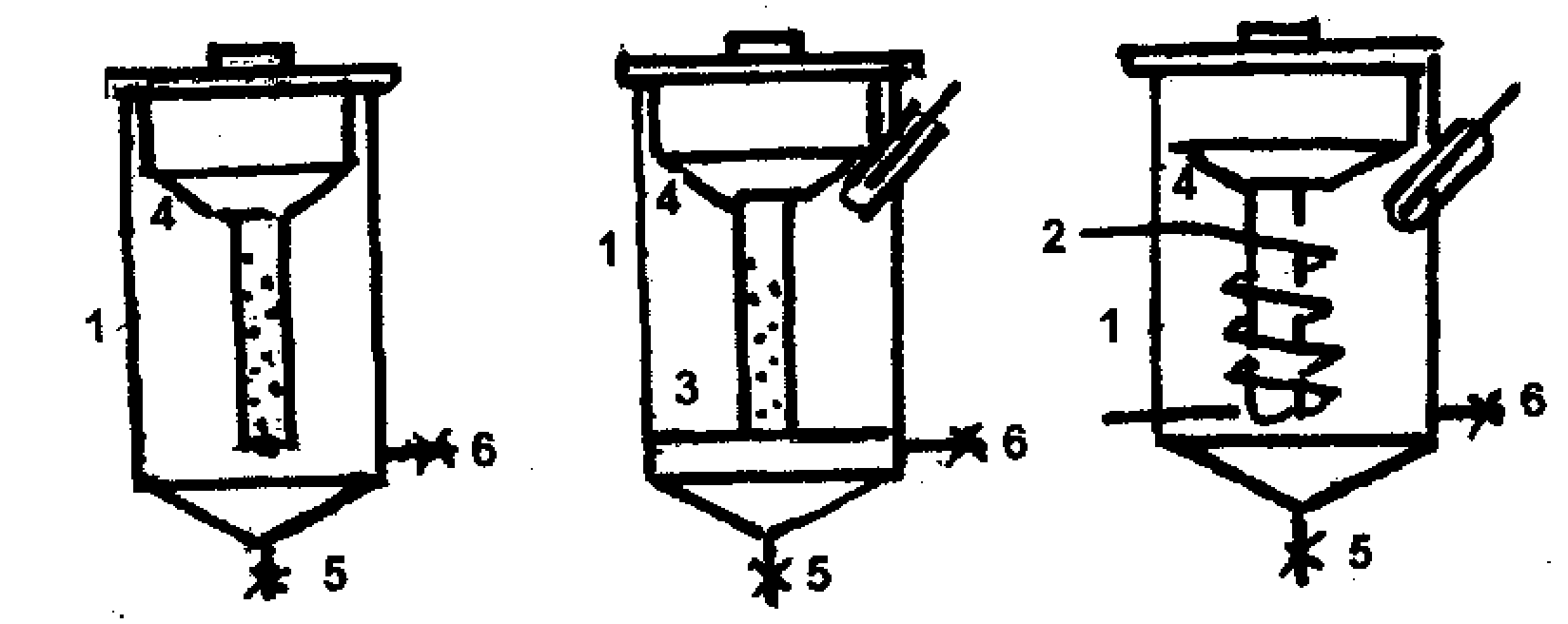
Мал. 5. Тили циліндричних відстійників періодичної дії
1 — корпус відстійника; 2 — паровий змійовик;
3 — електронагрівач;
4—лійка з сіткою; 5 — спусковий кран;
б — кран для зливу відпрацьованого мастила
На мал, 6 зображена схема праці відстійника безперервної дії. Мастило надходить у відсік, де осідають найбільш крупні і важкі частинки. Потім мастило переливається крізь проміжну ємкість у відсік 2, у якому внаслідок незначної швидкості руху мастило звільняється від більшої частини механічних домішок і далі поступає у відсік 3, звідки відділяється крізь трубу, яка розташована на половині височини відсіку.
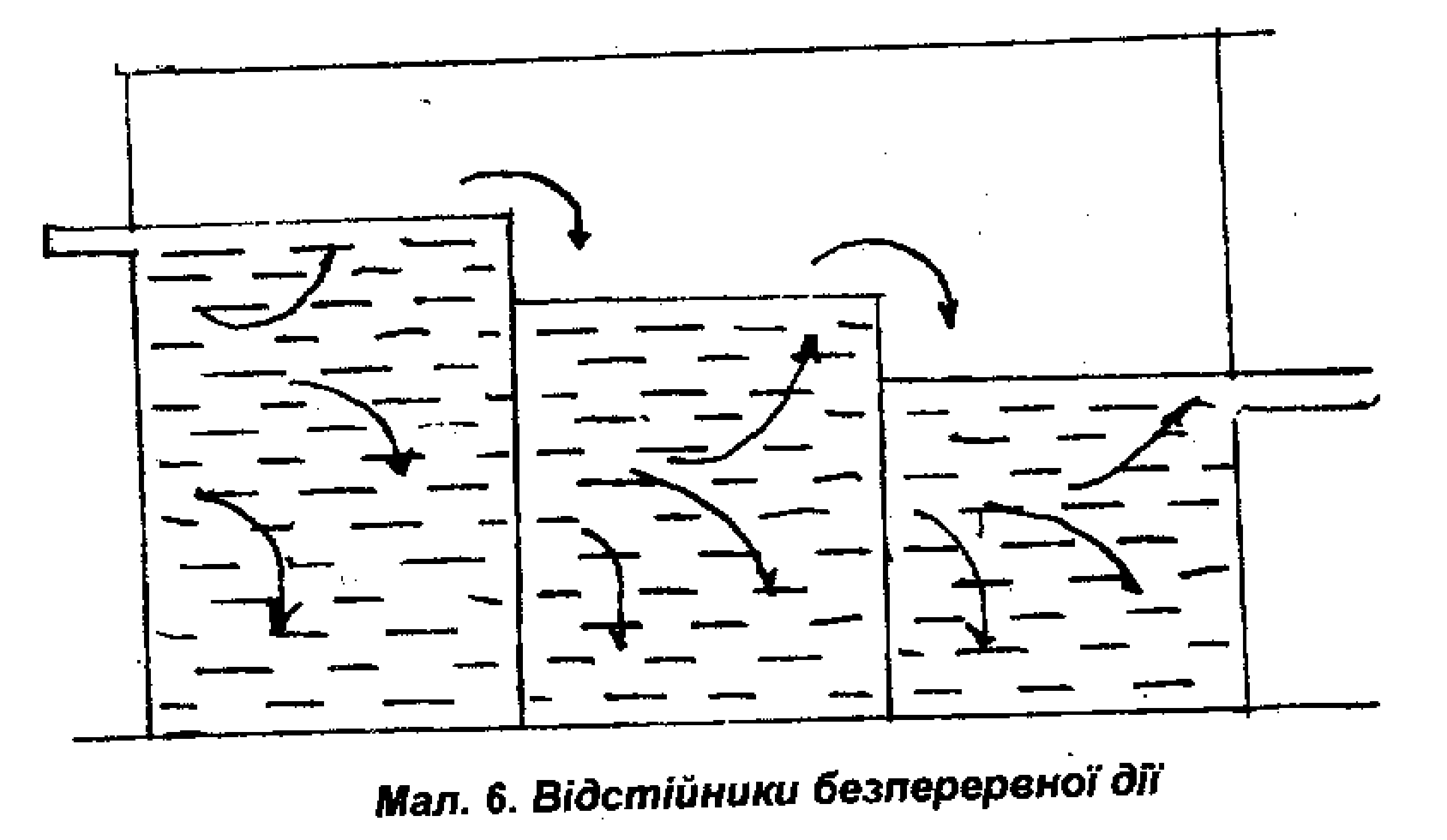
На мал. 7, 8 зображені ємкості спрощеного типу для збору відпрацьованих мастил.
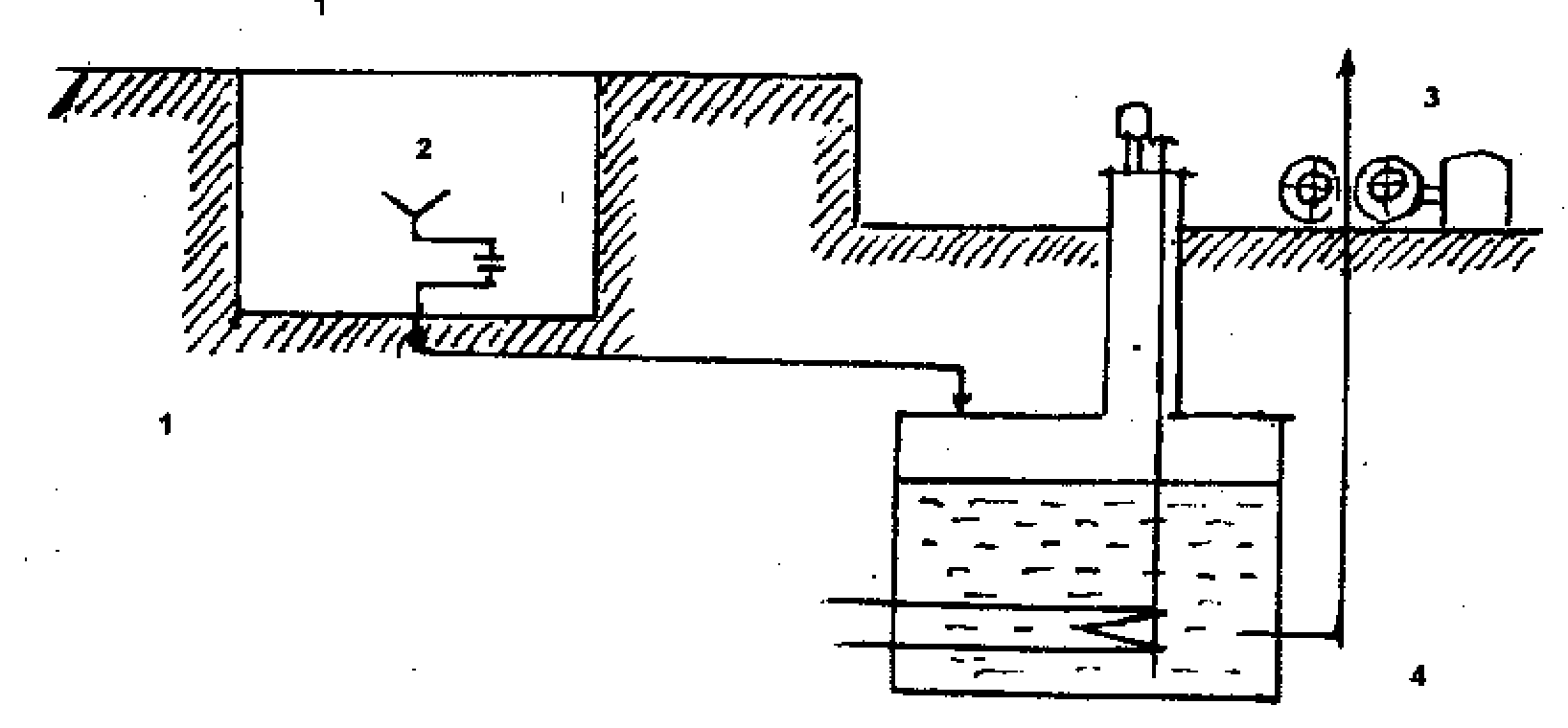
Мал. 7. Збір відпрацьованого моторного мастила при заглибленій нагромаджувальній ємкості
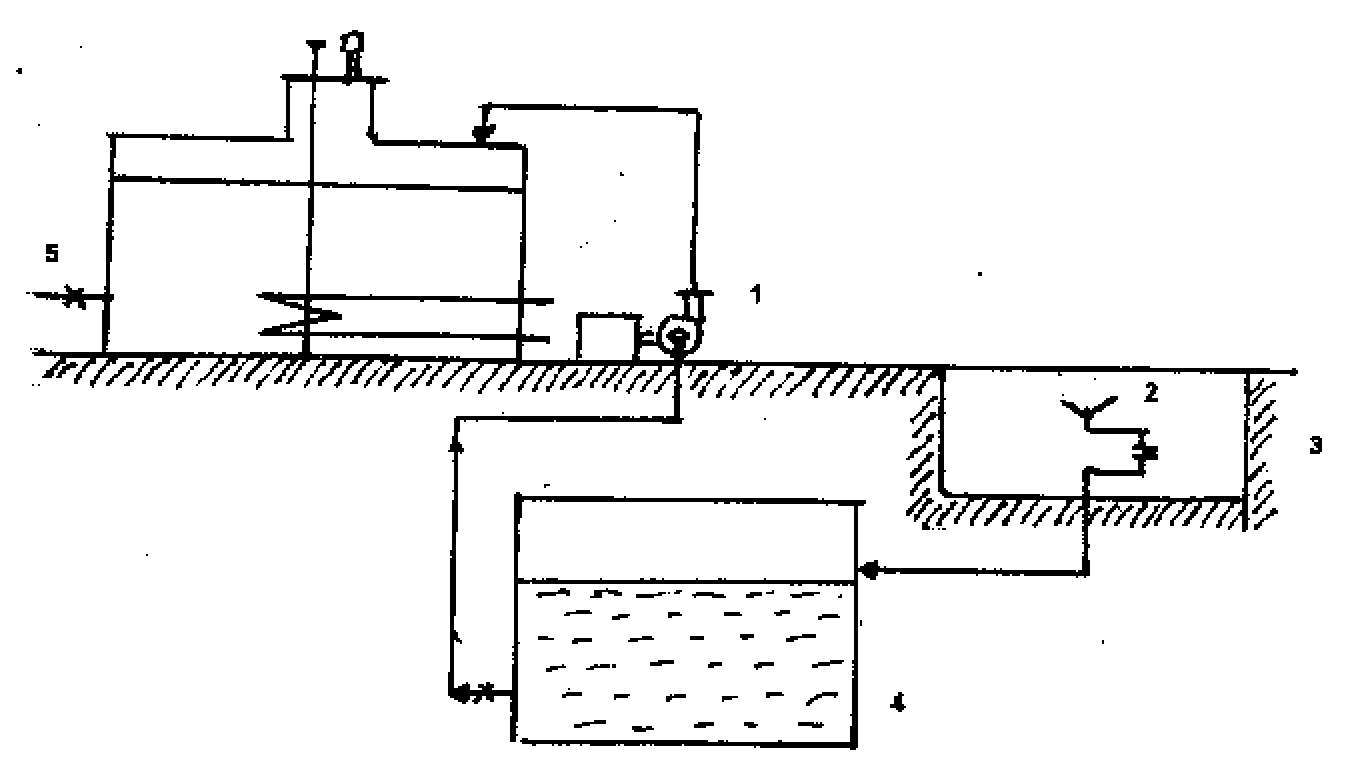
Мал. 8. Збір відпрацьованого мастила при наземній нагромаджувальній ємкості:
1 — насос; 2 — приймальна лійка: 3 — оглядова яма;
4 — проміжна ємкість; 5 — нагромаджувальна ємкість
Для більш повної очистки мастил використовують сепаратори, центрифуги, а також різні фільтри.
Забруднене мастило в сепаратори барабанного типу поступає через "губок в барабані, який обертається, і під дією відцентрових сил відбувається розподіл речовин і домішок у відповідності до їх густини. На кожусі осідають вода і механічні домішки, які потрапляють в шламозбірник, а мастило подається в наступний сепаратор, чим і досягається необхідний ступінь очищення мастил.
До хімічних методів регенерації нафтопродуктів відносять ]х обробку сірчаною кислотою Це найстаріший і найбільш розповсюджений спосіб очищення, нафтопродуктів. Цей метод дозволяє усунути із відпрацьованих нафтопродуктів асфальтні та смолисті речовини, а також. Інші продукти старіння. Для цього у відпрацьований матеріал при поступовому перемішуванні додають концентровану сірчану кислоту в кількості 4-16% від усієї маси нафтопродукту. Суміш відстоюють, відділяють верхній шар, тобто очищений продукт, а потім обробляють його лужним розчином для нейтралізації кислоти. Остання операція кількаразова промивка нейтралізованого нафтопродукту водою і висушування його продуванням гарячим повітрям.
Інколи практикують лужну очистку мастил, яка здійснюється міцним розчином каустичної соди. Після лужної обробки мастило або інший нафтопродукт промивають 3-4 рази водою до нейтральної реакції продукту. Остання операція - сушіння нафтопродукту гарячим повітрям. і
До фізико-хімічних методів очищення нафтопродуктів відносяться коагуляція і адсорбція. В процесі коагуляції відбувається злипання і укрупнення частинок забруднення колоїдної системи "мастило-вода" з утворенням пухких агрегатів, які через деякий час випадають в осад, тобто седиментують. В якості коагулянтів використовують речовини різної природи: електроліти, поверхнево-активні з'єднання, високомолекулярні сполуки і інші. Оптимальний час коагуляції 20-30 хв. при температурі 70-80°С. В якості апаратури застосовуються звичайні відстійники, які мають мішалки. Застосування адсорбції засновано на здатності адсорбентів або поглиначів, утримувати на своїй поверхні значну кількість смолистих речовин і кислотних з'єднань: ефірів, альдегідів, кетонів і інших продуктів старіння мастил і інших нафтопродуктів.
В якості адсорбентів використовують природні вибілюючі глини, бентоніти, боксити, цеоліти, інфузорну землю типу зікеєвської, а також штучні адсорбенти - силікагелі різних марок, оксиди алюмінію, цинку, титану, алюмосилікати, активоване вугілля та інші.
Процес очищення забруднених нафтопродуктів шляхом адсорбції здійснюється двома способами: статичним і динамічним.
Статичний спосіб полягає в тому, що в ємкість із забрудненим нафтопродуктом засипають адсорбент І інтенсивно перемішують вміст ємкості зі швидкістю 1000-1400 обертів за хвилину протягом півгодини. Потім відфільтровують адсорбент, який іде на регенерацію, тобто на відокремлення від нього нафтопродукту відстоюванням або прожарюванням.
Динамічний спосіб полягає в тому, що нафтопродукт пропускається крізь адсорбент, який знаходиться у вигляді зерен від 1,5 до 7 мм в циліндричній колоні. Матеріал, який очищується, проходить крізь адсорбент самопливом або під тиском.
Найбільш ефективним способом регенерації нафтопродуктів вважається селективна очистка їх за допомогою вибіркових розчинників, які вилучають продукти старіння: нітробензол, фурфурол, фенол та інші.
Комбінований спосіб очищення нафтопродуктів включає як фізичні, хімічні, так і фізико-хімічні методи очищення і дає найбільш якісні результати. Однак його використання коштує найдорожче.
Раціональним і перспективним використанням відпрацьованих мастил і Їх регенерація на спеціалізованих установках нафтопереробних підприємств, де використовують технологію ВИДІ - переробки нафти, яка дозволяє отримувати якісні марки мастил при значно менших експлуатаційних і капітальних витратах, ніж при виробництві нових мастил з нафти.
Якщо при очищенні не досягається потрібний ступінь очищення, то мастила направляють для використання в якості компонента котельного палива або на підприємства нафтопереробки.
Забруднені мастила додають до котельного палива тобто мазуту не більше 10-25% від всієї маси палива через підвищену зольність.
Наявність забруднень і неспрацьованих присадок в регенеруючих мастилах від'ємне впливає на працю електрознесолюваних приладів, тому кількість мастил додається до нафти, яка для їх сумісної переробки не повинна перевищувати 1%.
На мал 9 зображена принципова схема ділянки очищення мастил між нафтопереробним заводом і паливною системою двигуна.
Економічний ефект від переробки 150 тис. т відпрацьованих мастил складає більше 2,6 млн. крб. або більше 17 крб. на 1 т (в цінах 1989 p.).
Одержання з відходів нафтопереробки вуглецевих волокон. Десятки тисяч тонн важкої нафтової смоли утворюється у вигляді відходів на нафтопереробних заводах, їх завжди спалювали. Співпрацівники НТП "Автор" (Митищі) розробили технологію виготовлення з цих відходів вуглецевих волокон, а з їх допомогою - композитів Останні виявились придатними для виробництва ряду деталей автомобіля. Ці вуглецеві волокна володіють електропровідністю, жароміцністю, що дозволяє виробляти з них нагрівальні і теплозахисні панелі, які замінюють азбестові, шкідливі для здоров'я людини. З цих волокон можна виробляти фільтри, які характеризуються великою поверхнею. Так, горілка, яка пропущена скрізь такий фільтр, стає водою.
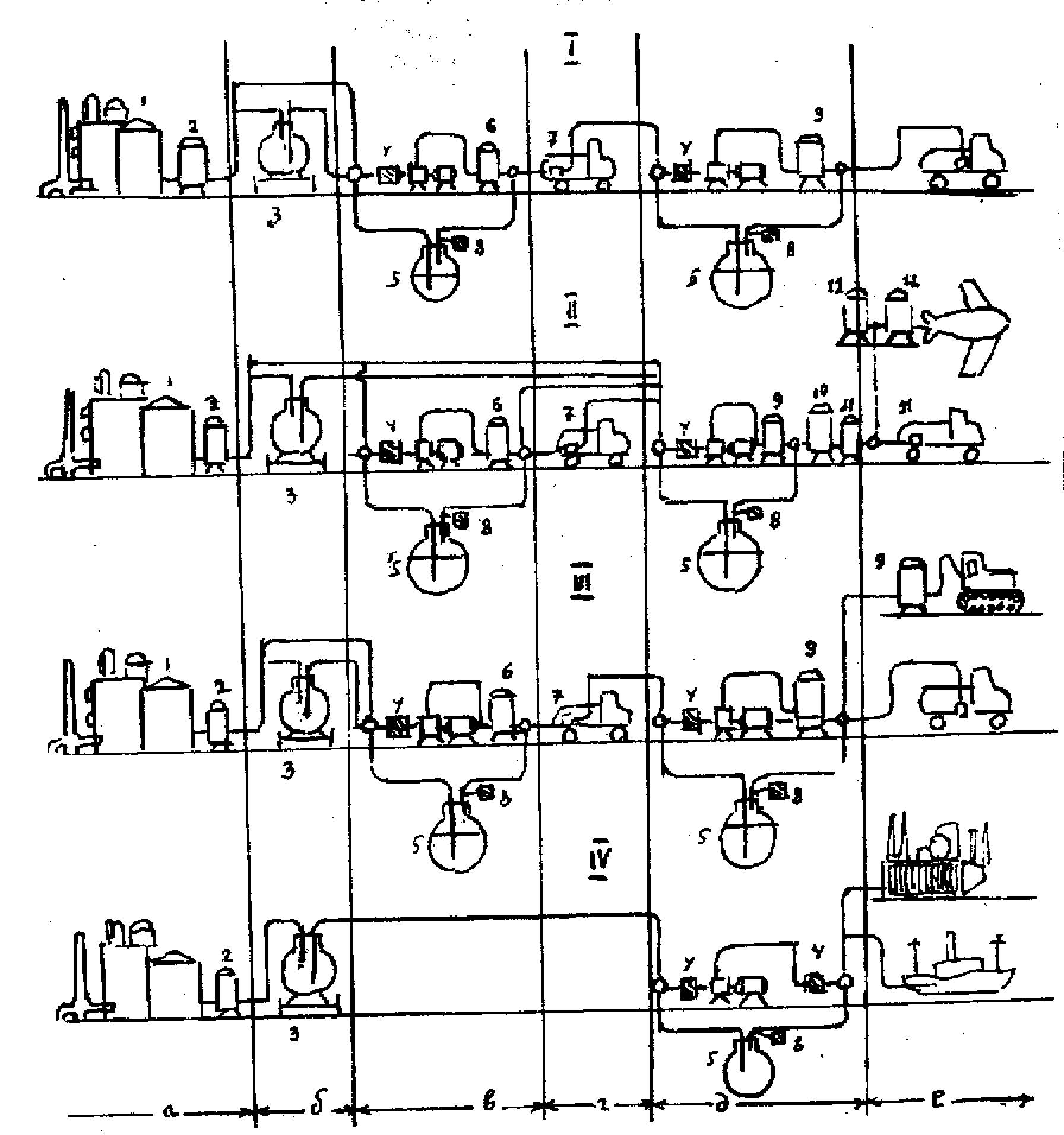
Мал. 9. Принципова схема очищення палив різного призначення між нафтопереробним заводом і паливною системою двигуна
а — нафтопереробний завод; б — залізничий шлях; в — склад тривалого зберігання; г — автомобільний транспорт; д — склад споживача; е — заправка двигуна або енергетичних агрегатів; 1 — товарна ємність нафтопереробного заводу; 2 — заводський паливний фільтр; 3 — залізничне шляхова цистерна; 4 — фільтр грубого очищення; 5 — відстійна ємність; б — фільтр тонкого очищення (15-20 мк); 7 — фільтр автомобільної цистерни (30-40 мк); а — повітряний фільтр; 9 -— фільтр тонкого очищення (10 мк);
10 — фільтр сепаратор; 11— фільтр тонкого очищення (5-8 мк); І — автомобільний бензин; II — авіаційне паливо; III — дизельне паливо; IV — мазут
3.6. Використання золи, шлаків і тепла теплових електростанцій.
3.6.1. Золи та Їх властивості.
Зола - неспалений залишок, який утворюється після згоряння різних видів палива. Склад золи в антрацитах, кам'яному і бурому вугіллі коливається в межах від 15 до 50%, а в горючих сланцях - від 5 до 80%, торфі - від 2 до 50%, дровах різних порід - до 1%, в інших видах рослинного палива від 3 до 8%, в мазуті - 0,2%.
Мінеральний хімічний склад золи, дисперсність (розмір частинок), кількість скловидних речовин, об'ємна маса, щільність і активність золи залежить від виду палива, способу і температури спалювання палива, конструкції топки, методу спалювання і відділення самої золи.
Із золи деяких рослин, а також вугілля отримують рідкі та розсіяні елементи - нікель, ванадій, селен, германій, галій та інші.
Появилась нова галузь видобувної промисловості - біологічний метод вилучення речовин.
В сільському господарстві зола рослин використовується як калійне добриво. Причому калій в золі знаходиться у вигляді легкозасвоюваної форми - вуглекислого калій або поташу. Він добре розчиняється у воді і швидко попадає в рослини. В рослинній золі знаходяться і інші мінеральні речовини, які необхідні для нормального розвитку і росту рослин, - фосфор, кальцій, магній, сірка, бор, марганець І інші макро- і мікроелементи. Високий вміст вуглекислого калію в золі сланців І торфу дозволяє використовувати їх для зниження кислотності грунту.
В нижченаведеній таблиці 2 подасться середній вміст основних елементів живлення в золі рослин, в %.
Таблиця 2 Середній вміст елементів живлення в попелі рослин
Вид попелу | Калія К20 | Фосфора P2Os | Кальція CaO |
Стебло соняшника Солома гречана Солома житня Солома пшенична Дрова березові Дрова ялинові Підстилання кізякове Дрова соснові Підстилання торф'яне Підстилання сланцеве | 30-35 25-35 10-11 9-18 10-12 8-4 10-12 10-12 0.5-4,8 0,5-1,2 | 2-4 2-4 4-6 3-9 4-6 2-3 4-6 4-6 1.2-7,0 1.0-1,5 | 18-20 16-18 8-18 4-7 35-40 23-26 7-9 30-40 15-36 38-48 |
Попіл, як калійне добриво, вносять у всі грунти і під усі культури, але |
найбільш доцільно підживлювати тютюн, картоплю, гречку та бобові культури - горох, квасолю, сою, чечевицю, а також льон та ягідні рослини. Попіл вносять під оранку, при перекопуванні грунту під кронами дерев в кількості від 4 до 15 ц/га, при посадці картоплі, розсади капусти і томатів (3-5ц/га). Попіл також використовують для удобрення пасовищ, пропашних та насіннєвих культур в кількості від 3 до 5 ц/га. При використанні попелу в якості добрива не рекомендують змішувати його з суперфосфатом, органічними та аміачними туками, а також іншими водорозчинними сполуками з метою запобігання витрат азоту та ретроградації, чим знижується засвоюваність фосфатів рослинами.
Хімічний склад та основні фізичні властивості попелу деяких видів палива, які спалюються на ТЕС, приведені в таблицях 3 і 4.
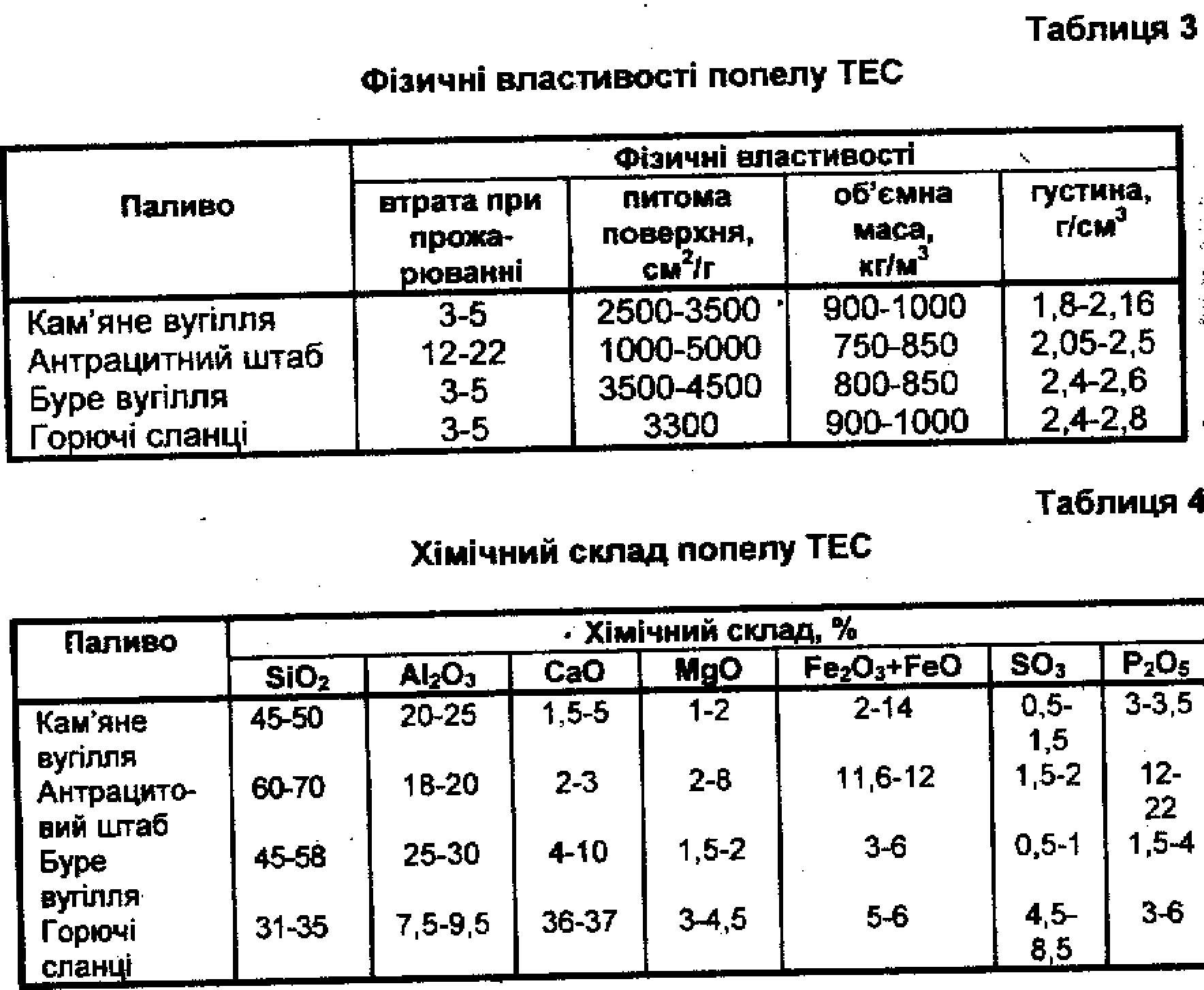
Питома поверхня зол знаходиться в межах від 2800 до 3500 см2 на грам. Порохоподібні золи та шлаки ТЕС - цінна технологічна сировина для виробництва будівельних матеріалів.
3.6.2. В'яжучі з добавленням золи ТЕС.
Золи ТЕС використовуються в якості активної мінеральної добавки для виробництва портландцементу з питомою поверхнею не менш 2800 см2/г.
В таблиці 5 показані властивості цементу з добавкою золи ТЕС. Із таблиці 5 видно, що введення порохоподібної золи в цемент збільшує потребу у воді і сповільнює строки схоплювання.
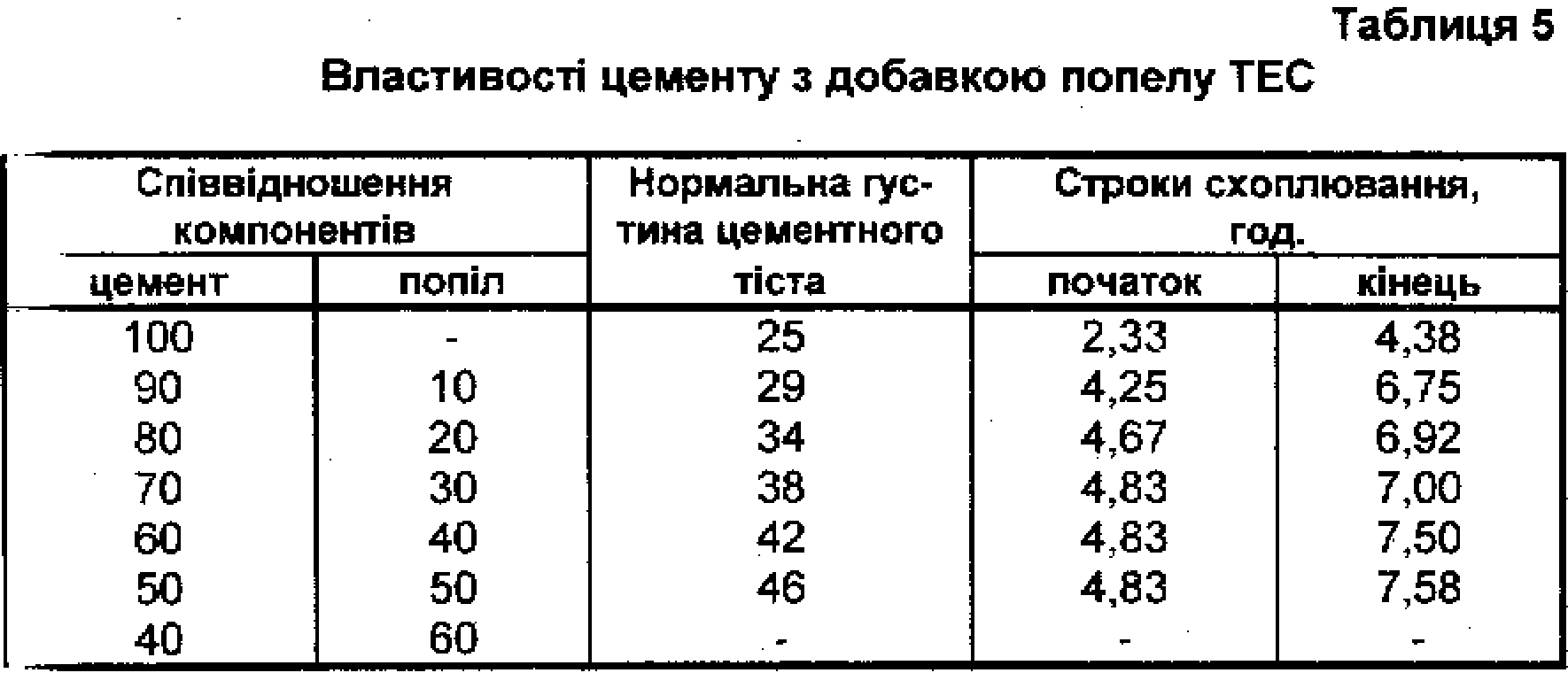
Суміш вкладалась у формі куба з ребром 10 см і ущільнювалась на лабораторній вібромашині з амплітудою коливань 0,55мм і частотою 2800 коливань за хвилину. Наслідки іспитів показали відносну низьку міцність бетонів на зольних цементах після однієї доби твердіння. В подальшому і постерігається ріст міцності до 365 діб і залишається рівноцінною, а іноді перевищує міцність звичайних бетонів.
3.6.3. Будівельні розчини з використанням золи ТЕС.
Золу ТЕС в кількості до 2% пропонують використовувати у складі будівельних розчинів з метою економії цементу.
Оптимальні склади будівельних розчинів марок 25,50 і 75 на різних цементах з частковою заміною піску золою приведені в таблиці 6.
Таблиця 6 Оптимальні склади кладочних розчинів з добавкою попелу ТЕС :
Вид цементу | Витрати матеріалів на 1 м3 кг | Економія цементу на 1 м3 розчину,кг | ||
цемент | пісок 1 попіл | |||
Розчин марки 25 | ||||
Вапняково-шлаковий марки 100 | 250 | 1150 | 200 | 130 |
Шлакопортландський марки 200 | 230 | 1220 | 160 | 130 |
Шлакопортландський марки 300 | 160 | 1270 | 170 | 130 |
Розчин марки 50 | ||||
Вапняково-шлаковий марки 100 | 350 | 1050 | 200 | 135 |
Шлакопортландський марки 200 | 345 | 1160 | 150 | 5 |
Шлакопортландський марки 300 | 265 | 1050 | 240 | 5 |
Розчин марки 75 | ||||
Вапняково-шлаковий марки 200 | 410 | 950 | 210 | 10 |
Шлакопортландський марки 300 | 330 | 1150 | 150 | 10 |
Шлакопортландський марки 400 | 310 | 1200 | 140 | 10 |
Із таблиці 6 видно, що використання золи ТЕС в кпадочних розчинах приводить до економії цементу. Причому розчинна суміш, яка утворюється при частковій заміні піску золою, більш пластична, мало розшаровується а меншим, ніж у цементно-піщаному водовідношенні. Крім того, ця суміш швидко набуває міцності, володіє підвищеною стійкістю до сульфатного і прісного середовища.
3.6.4. Зольний гравій.
Зольний гравій-штучний пористий заповнювач із зернятками круглої форми, який отримується гранулюванням золи ТЕС з послідуючим спіканням та набуханням гранул. Цей матеріал розроблений інститутом "Тепло-проект", а його виробництво засвоєно в 1965 році Каширським експериментальним цехом зольного гравію.
У Дніпропетровську цей матеріал виготовляється з 1975 року Придніпровським заводом залізобетонних конструкцій із золи Придніпровської ГРЕС. Зольний гравій містить зерна таких розмірів, які дозволяють отримувати всі необхідні фракції пористого заповнювача: до 1 мм; від 1,25 до 5мм; від 5 до 10 мм; від 10 до 20 мм; від 20 до 40 мм. Зерна зольного гравію мають злегка сплавлену поверхню з водопоглинанням в межах 7-12%. Характеристика зольного гравію зображена в таблиці 7.
Таблиця 7 Характеристика зольного гравію
Показники | Зольний гравій з попелу ТЕС, яка працює на | |||
кам'яному вугіллі | антрацитовому штабі | бурому вугіллі | горючих сланцях | |
Об'ємна насипна маса, к/м3 | 500-800 | 400-800 | 400-700 | 500-700 |
Межа , міцності при стиску, МПа кг с/см2 | 3,7-4,0 37-40 | 3,0-17,5 30-175 | 2,3-7.5 23-75 | 2,5-10,0 25-100 |
Для виготовлення зольного гравію золошлакова суміш відбирається з відвалів гідрозоловідділення ТЕС, змочується водою і подається в ящиковий подавач, а звідти - в сушильний барабан, крізь який протягуються відхідні гази, що утворюються в обертовій печі. Суха золошлакова маса транспортується в шаровий млин, де подрібнюється до потрібних розмірів і поступає в тарільчатий гранулятор. Тут маса змочується водою або водним розчином сульфідно-дріжджової бражки і перетворюється в гранули потрібного розміру. Для більшої міцності гранули пропускають крізь сушильний барабан. Потім їх прожарюють за допомогою обертової печі. Тут гранули спікаються і вспучуються при температурі 1150-1200°С. Далі гранули охолоджуються, сортуються на фракції і потрапляють на склад готової продукції.
На основі зольного гравію отримують легкі бетони марок 50-300, об'ємною масою відповідно від 900 до 1150 кг/м3, морозостійкістю більше 20 циклів заморожування і відтаювання.
Склади і властивості бетонів на основі зольного гравію приведені в таблицях 8 і 9.
Таблиця 8
Склад і характеристика легких бетонів на основі зольного гравію
| |||||||
Витрата матеріалів на 1 м3 бетону | Характеристи- ка бетону | ||||||
цемент марки 400кг | Гравій л | зольний пісок, л | попіл ТЕС, кг | кварцовий пісок, кґ | вода, л | Межа міцност кг с/см3 | об'єм на маса, кг/м3 |
140 . | І50 | 100 | 350 | - | 170 | 5/50 - | 850 |
200 | ЮО | 140 | 400 | - | 180 | 10/100 | 950 |
400 | 850 | - | - | 600 | 170 | 30/300 | 1150 |
Таблиця 9' Властивості легких бетонів на основі зольного гравію
Марка бетону | Призмова міцність, МПа | Міцність при осьовому розтягу, МПа | Модуль пружності, МПа | Коефіцієнт теплопровідності , Вт м °С | |
при стиску | при розтягу | ||||
50 100 300 | 4,4 8,5 25,7 | 0,52 0,73 2,00 | 5770 8000 18800 | 4450 8700 18400 | 0,25 0,30 • 0,43 |
|
3.6.5. Силікатна цегла із золою ТЕС.
Технологічний процес виробництва силікатної цегли із золою ТЕС подібний до процесу виробництва звичайної цегли, але має деякі особливості. Ця цегла отримується не на пресах типу револьверних, й на пресах типу СМ-301, які використовуються для напівсухого пресування глиняної цегли. Вологість вибирається в залежності від якості золи і коливається в межах 7-13%. Сировину необхідно висушити до постійної ваги.
Золосилікатна суміш готується в мішалках будь-якої ємкості. Компоненти змішуються сухими. Поступово вводять воду, 7-8%. Cуміш витримується в зачиненій ємкості протягом 18-22 годин. Після гасінні вапна додається вода для досягнення формувальної вологості. Золи вводиться до 30%. Відпресовані вироби запарюються в автоклаві при тиску 0,8 МПа (8кгс/см2) протягом 5+8+4 годин. Через добу, після запарювння силікатна цегла, в залежності від кількості добавленої води, має наступні властивості (див. таблицю 10). і.
Таблиця 10
Склади і властивості силікатної цегли з попелом ТЕС
Співвідношення між золою і піском, % | Вологість суміші, % | Об'ємна маса кг/м3 | Водо-поглинання % | Межа Міцності | Коефіцієнт | |||
попіл | пісок | при стиску | при згині | Морозостійкост | Розм’ягченні | |||
0 10 20 30 40 60 80 90 100 | 100 90 80 70 60 40 20 10 0 | 7 7,5 8,0 8.0 9,0 10,0 11,0 12,0 13,0 | 1793 1750 1727 1719 1661 1517 1452 1386 1358 | 14,5 15,0 17,7 21,1 21,7 26,2 30,5 32,5 34,8 | 13,4 12,5 12,1 12,0 11,8 12,1 11,7 11,9 12,0 | 13,6 3,6 2,9 2,8 2,7 2,8 2,6 2,5 2,3 | 0,71 0,75 0,73 0,73 0,69 0,61 0,56 0,59 0,51 | 1,71 0,84 0,95 0,97 0,97 0,93 0,88 0,76 0,65 |
Об'ємна маса цегли знижується з 1800 до 1350 кг/м3 при повній заміні піку золою ТЕС. Міцнісні характеристики виробів при введенні золи знижуються незначно. Цегла, яка містить 10% золи, відповідає марці 125, а з більшим вмістом золи - марці 100. Цегла з вмістом золи більше 30% втрачає морозостійкість.
3.6.6. Ванадій із золи ТЕС, які працюють на мазуті.
В стоках зольних відкладень мазутів, які використовують для поліпшення якості палива, містяться метали в кількості від 0,1 до 0,3%, в тому числі такі цінні, як ванадій, мідь, нікель та інші.
Концентрація ванадію в золі сягає 0,3-0,8 г/л разом з сірчаною кислотою. Спеціалісти Київського технічного університету розробили технологію вилучення ванадію із золи сірчистих мазутів. Для цього кислі обмивочні води нейтралізують каустичною содою і осаджують важкі метали у вигляді шламу-густої легко рухомої рідини; шлам далі сушать і відправляють на металургійні заводи для вилучення ванадію.
Зміст роботи установки для вилучення ванадію полягає в тому, що обмивочні води спочатку випаровують до концентрації сухих речовин в 10% і одержують брикети (див. мал. 10).
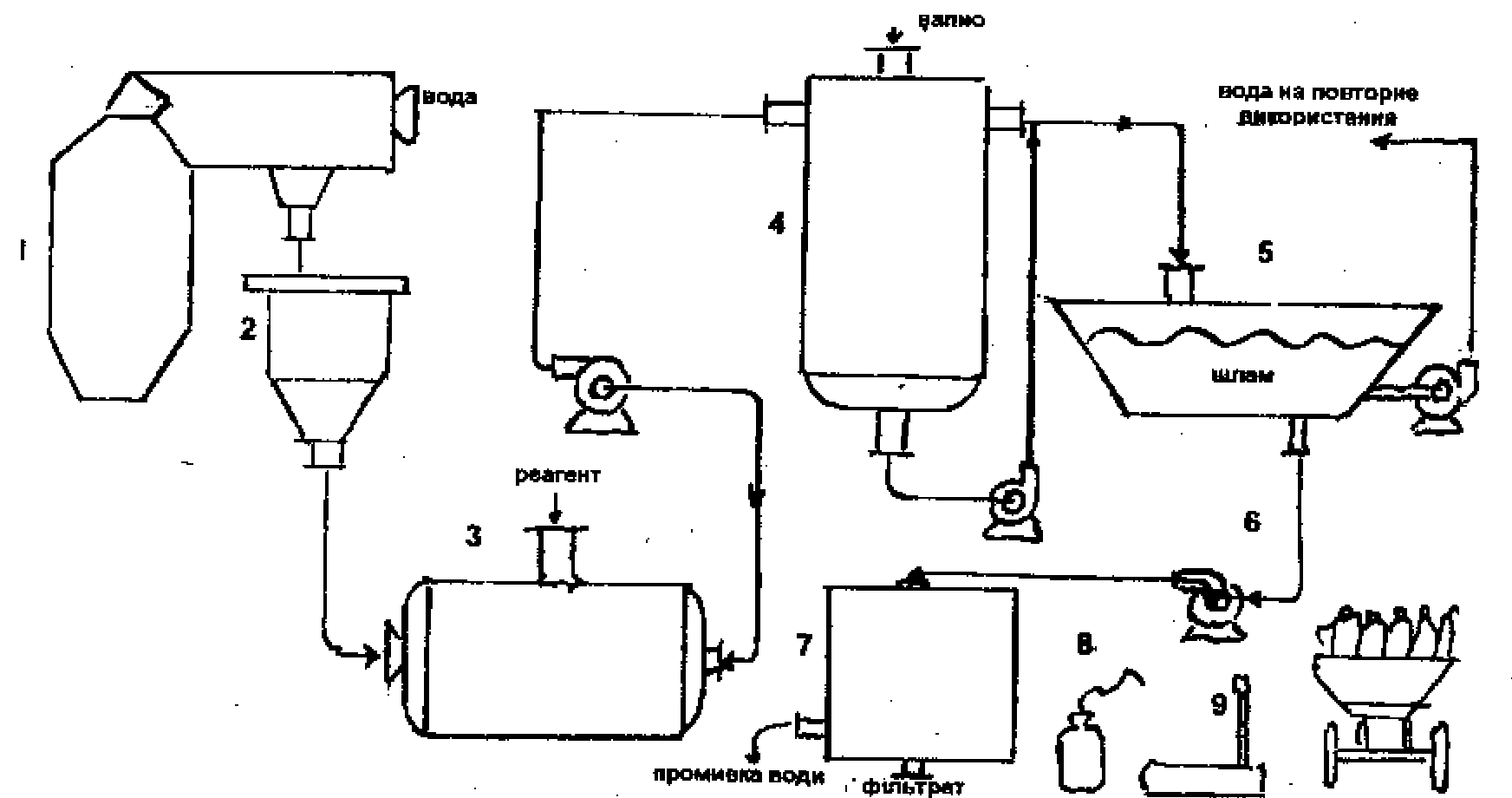
Мал. 10. Схема очищення обмивочних вод котлів, які спалюють сірчистий мазут для добування ванадію:
1 - котел; 2 — ємкість; 3 — змішувач; 4 — бак-нейтралізатор; 5 — шламо-нагромаджувач; 6 —шламовий насос; 7 —фіпьтр-прес для обезводнення шламу; 8 — розфасовка обезводненого шламу; 9 — ваги; 10 — транспорт для відправки шламу на металургійний комбінат.
Обмивочні води з котла поступають в ємкість 2, потім в змішувач З для усереднення складу. Обеззаражування стоків проходить в баці-нейтралізаторі 4.
Звідти продукт, який містить токсичні речовини, транспортується в шламонакоплювач 5, де його відстоюють. Далі розчин шламовим насосом 6 подається на фільтр-прес 7 для обезводнення. Осад з фільтрів потрапляє на розфасовку у крафт-мішки, а потім у вагони для відправлення до місця регенерації і вилучення ванадію.
3.6.7. Утилізація теплоти ТЕС.
Для охолодження потужних електроагрегатів ТЕС потрібно 30-50 м3 води в секунду. Дві третини тепла, яке одержується при згорянні палива, відходить в атмосферу зі стічними нагрітими водами.
Спеціалісти Атоменергопроекту, інституту ресурсів і Українського інституту водного транспорту пропонували проект комплексного використання теплоти цих вод.
Проект полягає в тому, що навколо енергооб'єктів створюється кілька блоків, які пов'язані єдиною технологією, і відходи одного блоку є сировиною для іншого. Ці блоки включають: завод для розведення риби (див. мал. 11), систему теплиць, які обігріваються відпрацьованою нагрітою водою. Відходи від вирощування риби дають протеїнові добрива. Бадилля від овочів теплиць іде на корм рибам як вітамінна добавка. Тут є і шампіньйонниця, яку також обігрівають теплою стічною водою. Добрива для грибів дають відходи рибозаводу. Є також мікробіологічний блок, який працює на відходах рибного та сільського господарства. Цей блок виробляє кормові дріжджі, ферменти і біогаз. В проект господарства включений також і обігрів відкритого грунту стічною водою, на якому можна отримувати два урожаї на рік. Теплиці і інші блоки, забираючи теплоту води, охолоджують її для повторного і оборотного використання в подачі на енергоагрегати.
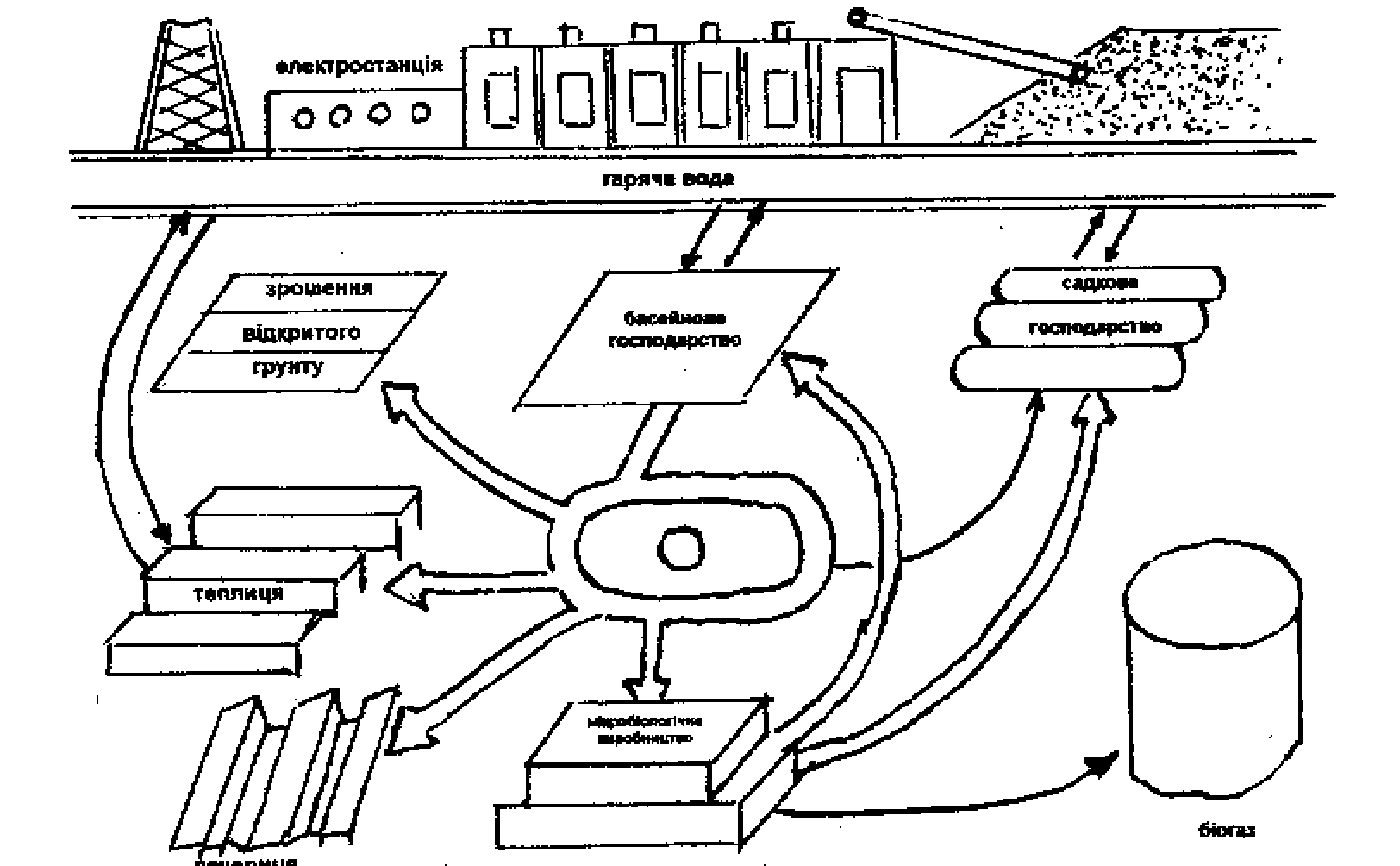
Мал, 11. Схема раціонального використання гарячої води наТЕС
Такий енергобіокомплекс створений на Курській АЕС, де рибозавод дає 2 тис. т риби на рік.
Будівництво АЕС в США зупинено вже 15 років. 67% відходів ТЕС в США є сировиною для одержання будівельних матеріалів, із них 30% йдуть на виробництво щебеню, 24% - цементу, 26% - для керамічних і 10% для силікатних виробів.
У нас мало використовується передових технологій: минулого року тільки на одному із 18 підприємств України впроваджували новітні технології.
В світі ТЕС працюють на комбінованому або парогазовому процесі, який дає ККД в 54-56% замість 32-33%. Промисловість України витрачає на одиницю продукції в 6-8 разів більше електроенергії, ніж в країнах Європи. Розрахунки показують, що за умовами раціонального використання електроенергії Україна може витрачати тільки 50 млрд. м3 природного газу, тобто майже в 2 рази менше, ніж зараз.