Вступ
Вид материала | Документы |
- Вступ, 323.48kb.
- Програма дисципліни кредитний модуль " основи радіоелектроніки" (для груп фф) Вступ, 153.44kb.
- Питания з Програми з курсу «Механіка», що виноситься на зм 1 вступ, 86.8kb.
- Робоча навчальна програма здисципліни: Принципи І методи аналізу художнього твору Спеціальність, 222.75kb.
- План, вступ, викладення змісту теми (як правило, 2 глави), висновок, а також список, 24.79kb.
- Вступ України до Світової огранізації торгівлі. Законодавчі зміни. Галузеві стратегії”, 72.41kb.
- Робоча навчальна програма Модуля Вступ до спеціальності Для студентів спеціальності, 404.17kb.
- Вступ до історії україни 5-й клас (35 годин), 86.86kb.
- Вступ до історії україни 5-й клас (35 годин), 104.36kb.
- М. В. Ломоносов; [вступ ст., сост., примеч. А. А. Морозова]. Ленинград : Сов писатель,, 249.18kb.
Лекція 7
3.6.6. Отримання нікелевого купоросу з електролітних заводів.
При електролітичному рафінуванні міді в якості побічного продукту отримують сульфат нікелю або нікелевий купорос. Розчин сульфату міді використовується в якості електроліту при електролітичному рафінуванні і сирої міді, яка служить анодом. Катод-листи чистої рафінованої міді. В процесі електролізу з сирої міді в розчин переходять і домішки нікелю, які і є в сирій міді. Переходять також і інші метали - цинк і залізо. Ці метали не осідають на катоді, як мідь, а постійно накопичуються в анодному просторі розчину електроліта. Це приводить до зменшення, розчинності сирої міді, сульфату міді і до погіршення умов електролізу. Тому для підтримання в електроліті мінімальної концентрації домішок частину розчину електроліту періодично виводять з циклу електролізу і на його місце додають сірчану кислоту.
Виведений розчин піддають регенерації і вилучають нікель у вигляді його сульфату. Сира мідь містить 0,1% нікелю. А розчин, який виділяють для регенерації, має такий склад, г/л: сірчаної кислоти 180; ' міді 40; нікелю 15; заліза 3; миш'яку 7,
Регенеруючий розчин нейтралізують мідним скрапом в затравочній і башті при продувці її повітрям. Надлишок води випаровують і кристалізують при охолодженні сульфат міді. Маточний розчин ще раз піддають випарці з наступною кристалізацією. Кінцевий маточний розчин має такий склад, г/л: сульфату міді 50; сульфату нікелю 50 і сірчаної кислоти 40. Цей розчин піддають електролізу зі свинцевими анодами. Сира мідь осідає на катодах. Відпрацьований електроліт, який містить до 120 г/л сірчаної кислоти, 55 г/л сульфату нікелю 12 г/л сульфату міді, випаровують для збільшення концентрації речовин і охолоджують. При цьому проходить кристалізація сульфату нікелю. Після цього маточний розчин, який залишився, другий раз випаровують, охолоджують, і піддають кристалізації, а потім перекристалізації і отримують чисту сіль сульфату нікелю або нікелевого купоросу. Кінцевий розчин сірчаної кислоти повертають в електролізер.
3.6.7. Переробка брухту поліметалів.
Велика маса брухту кольорових металів складається з двох або більше шарів різних металів, які нанесені на виріб гальванічним або електролітичним методом. Залізо або мідь є основою виробу, а в якості покриття використовують інші кольорові метали. До таких виробів в першу чергу відносяться деталі і вузли радіоелектронної апаратури.
Зібраний металобрухт кольорових металів проходить первинну обробку безпосередньо в гальванічному цеху.
Методи зняття основних видів гальванічних покриттів наведені в таблиці 14.
Таблиця 14
Електрохімічні методи зняття металевих покриттів
Вид покрит- тя | Матер. основи | Склад розчину | Вміст компо-нентів | Режим роботи, т-ра°С | Густина струму, А/дм2 | Додат-кові вказівки |
Мідь -\\- Мідь | Сталь -\\- Сталь | Склад 1: хромов. ангідрид, сірчанокислий амоній -\\- відпрацьований хромовий електроліт | 250-300 г/л 100-120 ҐУп -\\- | 15-30 120±5 20—25 | 5-10 7-14 | катод: нержав. сталь 1Х18Н8Т -\\- |
|
| ||||||
Мідь | Сталь | Склад2: фосфорна к-та, вода мідний ку-порос | 90% 10% 1 г/л | 25-65 | 20 | катод: свинець |
Цинк | Цинк та його сплави | Сірчистий натрій Сірчана к. Відпрац. хромовий ангідрид | 120г/л 50- 100 г/л | 20-25 | 20 | |
Нікель -\\- Нікель | Сталь Азотна Сталь -\\- Сталь | Сірчана к. (1,84) Азотна к. Залізо сірчанокисле закисне) Фос-на к-та Нікель сірчанокислий Вода Фос-на к-та Сірчана к. Хромовий анг. | 1 в.ч. 2 в.ч. 10-20 г/л 90% 1 г/л 10% 64% 8% 28 г/л | 20-25 20-65 35-20 | 20 30-70 | катод: свинець |
Хром | Сталь Нікель | Гідроксинатрію Гідроксинатрію | 100- 150г/л 40-50 г/л | 24-35 -\\- | напруга 4-6 вольт 2-4 вольт | катод: сталь |
Олово | Сталь | Гідроксид натрію Нітроаром. сполуки | 40-50 г/л 20-30 г/л | 20-30 -\\- | | |
Кадмій | Сталь | Азотоокис-лий амоній | 120 г/л | -\\- | | |
Срібло | Сталь | Сірчана к. 1,84 Азотна к-та 1,41 | 90г/л 10г/л | | | |
Золото | Сталь мідь, латунь | Соляна к. (1,18), Сірчана к. (1.18) | 50 в.ч. 50 в.ч. | 20 | 0,1-1,0 | катод: залізо, свинець |
Плати- на | -\\- | -\\- | -\\- | -\\- | 0,5-0,6 | катод: срібло, графіт |
Родій | -\\- | Азотна к-та (1,41) | 100 % | 20 | -\\- | -\\- |
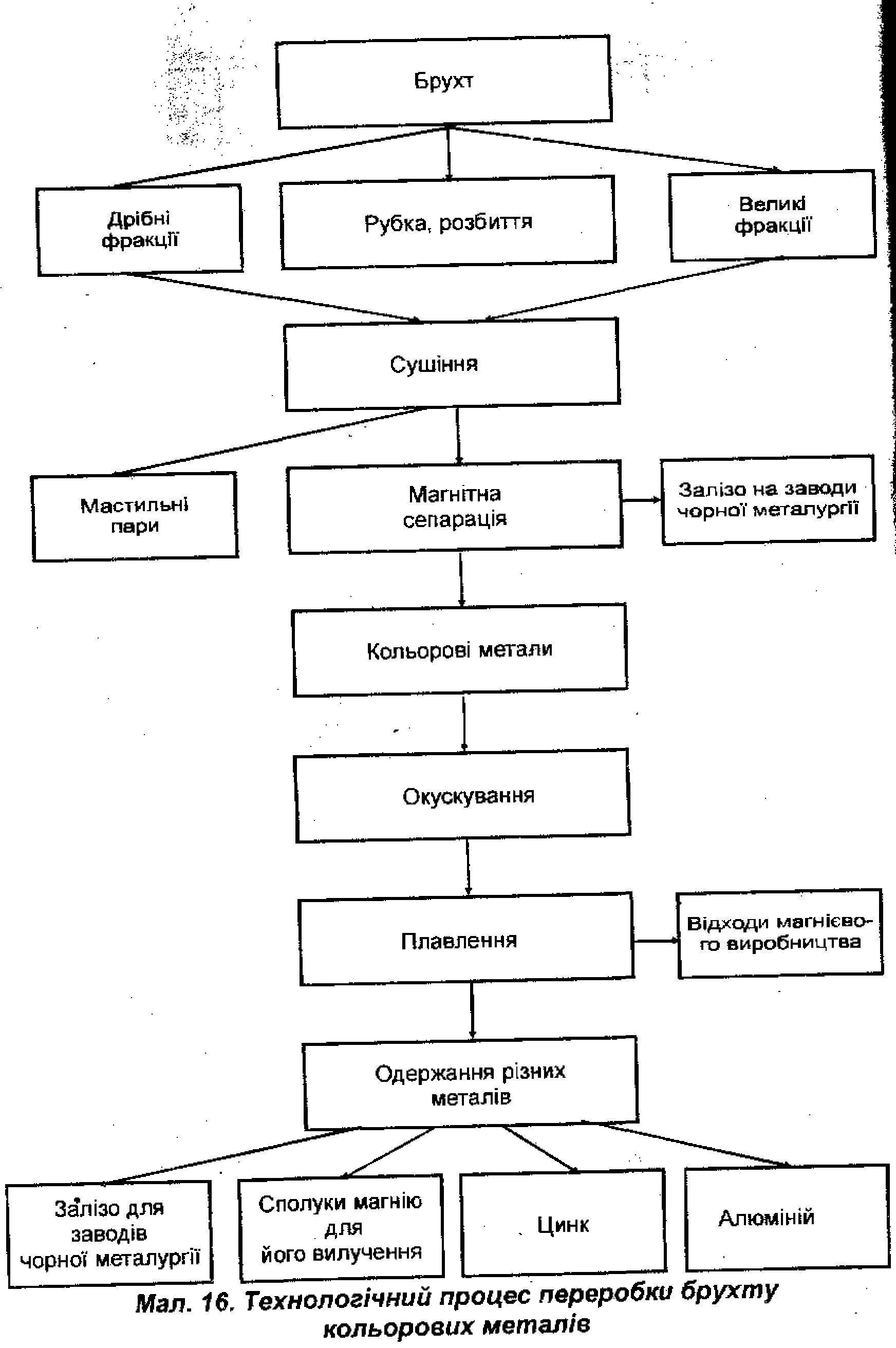
Олово з відходів білої жерсті отримують обробкою нагрітого до високої температури металу сухим хлором. При цьому утворюється сіль - двоххлористе олово, яке розчиняється у воді і відділяється від заліза жерсті.
Другий спосіб полягає в тому, що олово розчиняється в каустичній соді з концентрацією від 50 до 100 г/л при температурі 60-70°С і щільністю струму 3-5А на 1 дм площі електрода.
На мал. 16 поданий приклад технології переробки брухту кольорових металів у вигляді вторинних алюмінієвих сплавів. Спочатку металобрухт сортують, відділяючи чорні метали від кольорових. Далі відходи збагачують, відділяючи з них вологу, мастила і механічні домішки. Цей процес доводиться в обертових печах-сушарках і центрифугах з наступним вловлюванням та знешкодженням парів мастил. Процес збагачення здійснюється і іншими методами. Так, гравітаційний метод заснований на різній швидкості падіння матеріалів з різними питомими вагами у водяному або повітряному середовищі під впливом сили тяжіння. Для збагачення сипучих, зернистих і порохоподібних відходів кольорових металів застосовуються відсадочні машини, концентру вальні столи і обладнання повітряної сепарації. Перед збагаченням відходи краще розділити на різні класи за розмірами і кожний клас збагачувати окремо.
Процес відсадки у відсадочних машинах проводиться за допомогою води. На решітку машини поступають відходи, які повинні збагатити. Крізь решітку за допомогою спеціального пристрою подається вода. Більш важкі фракції, наприклад, залізні, залишаються на решітці, а більш легкі, наприклад, алюмінієві, спливають на поверхню води.
Для відділення порохоподібних частинок і окремих неметалевих домішок застосовується повітряна сепарація. Цей процес заснований на різній швидкості падіння частинок різних матеріалів в повітрі в залежності від їх маси. Повітря в повітряних сепараторах по-різному відхиляє падаючі частинки відходів легкі на більші відстані, а важчі - на менші, які попадають в окремі бункери.
Для відокремлення, чорних металів від загальної маси брухту застосовують магнітну сепарацію. Магнітне поле затримує чорні і пропускає кольорові метали.
З цих трьох процесів збагачення найбільш прийнятним є магнітний. тому, що при повітряній сепарації проходить порошіння матеріалу, а у відсадочних машинах вода забруднюється дрібними частинками, які виносяться у водойми.
Для попередження розсіювання дрібних частинок металу в атмосфері і інших середовищах проводять процес укрупнення, або грануляції відходів. Тоді застосовують процес спікання з горючим матеріалом, який проводиться в чашах або в спеціальних млинах конвеєрного типу. Під впливом високої температури частинки відходів спікаються в більш крупні агрегати. Збагачені гранульовані відходи завантажуються в плавильні печі, де подається паливо, і через деякий час шихта перетворюється в рідкий плав. Він складається з алюмінію, міді, цинку, частково заліза і інших компонентів. Важкий оксид алюмінію поступово випадає на дно печі.
Ванну, де залишилась рідка маса, покривають флюсом для захисту металів від окислення киснем повітря, водяною парою або сірчистими сполуками Флюс-суміш хлористого калію і хлористого натрію, або відпрацьований електроліті магнієвого виробництва. В процесі подальшого розплавлення до флюсу переходять оксид алюмінію і інші неметалеві домішки. Шлак відділяють і в розплав вводять легуючі елементи для покрашення складу сплаву.
Цинк і магній вилучають з розплаву його кип'ятінням. Пари цинку і магнію вловлюються в теплообміннику, де вони конденсуються.
На засіданні президії НАН України в 1996 році було обговорено питання про видобуток дорогоцінних та кольорових металів з вторинної сировини і було прийнято відповідне рішення, в якому відмічалося, що в країні вкрай загострилась проблема забезпечення народного господарства кольоровими та рідкісними металами, а їх виробництво обмежене. Тому треба передбачити вилучення їх з вторинної сировини та заміну екологічне небезпечних процесів екологічно чистими. Підкреслювалось, що багате таких відходів накопичилось на підприємствах військове-промислового комплексу, які треба негайно переробляти за новими технологіями.
Вторинне використання кольорових металів вже десятиліттями стали політикою розвинених країн. Для переробки алюмінієвого брухту потрібно в 40 разів менше електроенергії, ніж для вироблення алюмінієвої сировини. Японія свого часу оголосила програму переходу металургійної промисловості на сталевий брухт. Зарубіжні країни давно перейшли на мініметалургійні заводи з безперервною розливкою сталі, гнучким асортиментом продукції, використанням переважно металевого брухту в якості сировини, комплексної переробки рудних і сировинних матеріалів. Наша металургійна промисловість також повинна розвиватися в даному напрямі. Проводячи металозберігаючі технології треба ширше використовувати кераміку та вироби з неї.
4 .Технології переробки відходів машинобудування
4.1. Загальні положення.
Основними відходами машинобудування, яке включає заготівельні чавуноливарні, сталеплавильні (оброблюючі) ковальсько-пресові, механічні термічні, інструментальні і складальні цехи, у формовочно-відпрацьовані суміші, залишки чорних та кольорових металів у вигляді стружки, тирси, пороху, а також травильні розчини, мастильно-охолоджуючі рідини, абразивний порох, залишки відпрацьованого інструменту та інші.
Вторинні чорні метали класифікуються за вмістом вуглецю на два класи - сталевий і чавунний брухт, і відходи; за вмістом легуючих елементів на дві категорії - вуглецеві і леговані; за показниками якості на 28 видів, а за вмістом легованих домішок - на 67 груп.
За лінійними розмірами вторинні металургійні ресурси поділяються на габаритні, негабаритні та легковагомий брухт і відходи.
При металообробці утворюється обріз (при розкрої металу), металічна стружка, висічка, завусинки, клещевина і кінець (в ковальсько-пресовому виробництві).
Амортизаційний брухт утворюється від ліквідації основних засобів, від капітальних і біжучих ремонтів, вибулого змінного обладнання, технологічної оснастки, інструменту, малоцінного інвентаря, майна.
Зараз ресурси вторинних чорних металів, включаючи відходи металургійних підприємств, охоплюють біля 45% загальних потреб сировини для чавунноливарних та сталеплавильних підприємств. В 1985 році ці ресурси перевищили 100 млн. т.
Структура металовідходів характеризується такими даними: відходи металургійного виробництва 1,1%; ливарного 14,7%; металообробки в машинобудуванні 32%, в будівництві 1,6%.
Структура амортизаційного брухту: від ліквідації основних фондів 32,3%; капітальних і біжучих ремонтів 47,2%; вибуття оснастки. Інструменту, малоцінного інвентаря, включаючи майно населення, 7,2%. В загальних ресурсах вторинних чорних металів амортизаційний брухт складає 38%. В перспективі з прискоренням заміни фізично зношених і морально застарілих основних фондів доля амортизаційного брухту буде зростати, а брухт від капітальних ремонтів-скорочуватись.
Брухт і відходи чорних металів використовуються в металургійних, ливарних і інших виробництвах. Але основним споживачем його є сталеплавильне виробництво, на долю якого припадає більше 78% загального споживання чорних металів. Раціональне використання ресурсів, металобрухту є умовою досягнення високої продуктивності праці, тому що їх застосуванання дає велику економію суспільних витрат в народному господарстві.
Практично кожна тонна брухту чорних металів, перероблених у сталь, змінює 1 т чавуну. Питома капіталоємність виробництва 1 т чавуну із залізної руди в 7 раз перевищує питомі капітальні витрати на переробку 1 т брухту. Встановлено, що на кожний мільйон втягнутих у виробництво вторинних чорних металів народногосподарська економія капіталовкладень і складає біля 100 млн. крб., а з врахуванням вивільнення потужностей машинобудування і транспорту більше 120 млн. крб (в цінах 1989 року).
Однак, не всі ресурси металобрухту утилізуються. Частково вони стають не вилученими, незібраними і безповоротно губляться. В цілому безповоротні втрати металу, строк служби якого вийшов через неповний збір і вилучення, складають 12-15% по відношенню до утворених ресурсів. Крім нього, значна частина металу губиться в процесі експлуатації, відношення, корозії. Ці втрати оцінюються в середньому приблизно в 15%.
На металооброблюваних і машинобудівних підприємствах через неповний збір металобрухту безповоротно губиться біля 5% кускових метало-відходів і біля 15% стружки. Тому повний збір, належне сортування, зберігання від змішування при транспортуванні і підготовці до переплаву легованої вторинної сировини забезпечують велику економію в народному гоcподарстві. Найбільш великими постачальниками брухту і відходів кольорових металів є електротехнічна промисловість, чорна металургія, автомобільна суднобудівна, авіаційна промисловості і сільське господарство, машинобудування. Ці ж галузі є і основними споживачами кольорового металопрокату і сплавів. Крім того, основними джерелами утворення відходів кольорових металів є підприємства, де виробляються вони самі. Тут утворюються шлаки, шлами, всплески, зйоми та інші залишки. До цих джерел відносяться підприємства прокату, механообробки, де залишаються кінці, обрізки, обдирка, стружка, тирса і окалина; цехи фасонного лиття (литники, всплески, шлаки); заводи кабельної продукції, де залишаються кінці і обрізки дроту, путанка; виробництва хімічної промисловості, де залишаються відпрацьовані каталізатори, шлаки, а також цехи гарячого і електролітичного покриття (згарки і шлаки); цехи механічної обробки деталей і лиття (у вигляді висічок, обрізків, стружки, тирси); інструментальні підрозділи, де проводиться ремонт і виготовлення інструменту (у вигляді пилу і кускових відходів).
Заготівля брухту і відходів кольорових металів і сплавів подвоюється; кожних двадцять років, але в переробку втягуються не всі ресурси цієї сировини, Значна кількість брухту алюмінієвих і мідних сплавів надходить разом з брухтом чорних металів на виплавку сталі, погіршуючи її якість.
На Україні не використовується брухт консервних банок, які містять олово, хоч за кордоном ця проблема вирішена і більша частина металічного олова отримується з них. У нас також не збираються цинкові і інші елементи і батарейки, акумулятори; є суттєві втрати кобальту і вольфраму з порохоподібними відходами при заточці твердосплавного інструменту. Значна кількість кольорових металів витрачається зі шлаками, шламами та стічними водами гальванічних цехів і травильних ванн.
Багато брухту кольорових металів вивозиться на звалище, залишається у відпрацьованих шахтах, на будівництві і підприємствах.
60% брухту і відходів кольорових металів і сплавів здається в змішаному вигляді, а їх переробка потребує великих трудових затрат І додатком їх витрат енергії для їх розподілу.
5.2. Технології переробки відходів ливарного виробництва.
Ливарне виробництво - неодмінна приналежність підприємств машинобудування, тому що тут виробляються заготовки будь-яких деталей. Характерна особливість ливарного виробництва - висока витрата сировинних матеріалів і енергоресурсів Технологічний процес регенерації відпрацьованих формовочних сумішей складається з наступних операцій: подрібнення кусків, які спеклись, очищення їх від металевих включень, просіювання з одночасним продуванням повітрям і відсмоктуванням пилу, відтирки зерен піску від плівок зв’язуючого матеріалу і повторного знепилення. При такій схемі регенерації формуючі суміші повертаються у виробництво на 95%.
Подрібнення шматків, які спеклись, здійснюється у дві стадії: попередньої на валкових і остаточно до необхідного ступеня помолу - на роторних дробилках. Очистка формовочної суміші від металічних включень проводить за допомогою магнітних сепараторів на спеціальній установці, яка являє собою два стрічкоподібних конвеєри, що працюють в прямоточному режимі від одного приводу через ланцюгову передачу. Відпрацьована формовочна суміш першого ланцюгового транспортера падає на другий, а металічні включення при цьому притягуються до магніту і попадають в бункер.
В процесі дроблення, магнітної сепарації і обезпилювання відбувається часткове руйнування кірок і плівок, які зв'язують частинки з поверхнею зерен піску. Для очищення піску суміш пропускають через обтирочний прилад, який являє собою корпус з відбивними плитами, що прикріплені і його стінок з внутрішньої сторони. Прилад також має крильчатку повітрянодувку. Відтирка зерен піску від в'яжучого матеріалу здійснюється за рахунок зерен піску, які відкидаються відцентровою силою з відомими плитами і тертям зерен між собою. Регенеруюча формовочна суміш, яка пройшла дроблення, сепарацію і просів безперервно подасться в приймач регенератора і в камеру, з якої під дією сили тяжіння попадає в кінцевий отвір між вертикальною трубою і її кожухом. Попадаючи в щелепу між гирлом і труби і соплом, по якому подається повітря (тиск 0,2-0,3 кг/см2}, частинки піску і зростки зерен розмірами до 2,5 мм захоплюються повітряним потоком, розганяються і вилітають з великою швидкістю вверх. При виході з труби повітряно-пісковий потік зустрічає відбійний щит, на внутрішній поверхні якого утримується шар піску. Цей шар піску відіграє подвійну роль: приймаючи удар потоку на себе, пісок захищає щит від передчасного зносу :і другого боку, при обтіканні з внутрішньої поверхні відбійного щита піщинки піску, рухаючись з різною швидкістю в різних шарах потоку, стираються одна об одну. Внаслідок тертя зростки зерен розпадаються. Окремі зерна звільняються від плівок, глинистих оболонок і набувають нову форму. Очищений пісок відводиться в приймач, а повітря, втративши значну швидкість, виходить крізь завісу падаючого піску, втягує з coбою в атмосферу порох і дрібні частинки кварцу. Ця установка має низький коефіцієнт корисної дії, тому операції очищення формуючої суміші повторюють кілька разів.
Зараз для очищення формовочної суміші і піску використовують метод “киплячого шару”, який полягає в тому, що в рухомий шар піску в напрямку "вверх-вниз" вводять обертаючі лопатки. Швидкість повітряного потоку розраховується так, щоб гранули суміші не вбирались ним, а тільки знаходились у русі і були б у зваженому стані. Такі установки переробляють за 1г 100 кг формовочної суміші з залишковим вмістом глини в 2%. Вуглецеву плівку з частинок піску можна відділити і шляхом обпалу.
В цеху лиття по виплавляючим моделям застосовуються модельні розчини, в які входять: парафін, віск, церезин, стеарин і полістирол. Модельний розчин разом з водою стікає в розділювач, де звільняється від води і перекачується по нагрітому трубопроводу в плавильний цех для повторного використання.
В прокалочно-заливочному відділі сталь перед литтям виробів плавиться в індукційній печі. В якості шихтових матеріалів при литті по виплавляючих моделях використовують відходи ковальсько-штамповочних цехів механічної обробки, обрізки, висічку, облой, браковані вироби. Використовують також повернення ливарного виробництва: злитки, брак; всплески і т.п. Але це повернення піддається необхідній підготовці - очищенню і подрібненню. Використовування для плавки одного повернення не рекомендується, тому що при багаторазовій переплавці одних і тих же відходів збільшується газонасиченість металу і його забруднення оксидами. Кількість відходів, які вводять в нову плавку, не повинна бути більше 40% від маси шихти.
Для отримання стабільних результатів в переробці таким чином відходів слід постійно освіжати повернення, комплексуючи в балансі шихти витрати металу на гідні зливки, які виходять з ливарного цеху. Якщо виробляється декілька ливарних сплавів, то приймають міри, які попереджують змішування повернення різного складу. З цією метою залишки відходів зберігаються суворо в складі на шихтовому дворі в спеціально замаркованій тарі.
Відходи механічних і ковальсько-пресових цехів сортують і зберігають по марках. Ці відходи використовують в якості свіжих добавок в шихту. Коли ці або інші відходи мають відступи від норм за хімічним складом, то їх ізолюють і пускають в переплав тільки в кількості, передбаченій розрахунком шихти. А якщо повний контроль хімічного складу не можливий, змішані відходи переплавляють і з цього переплаву відливають злитки, які зручно використовувати для шихти в подальших плавках.
Суміш піску з водою з-під камери охолодження агрегату обпалення потрапляє в загальнозаводську систему регенерації піску системою гідро-прибирання.
В термообрубному відділі відходи, які були утворені при відбивці залишків оболонок і відділення відливок від стояка, системою конвеєрів транспортуються в короби, які періодично потрапляють із цеху для утилізації. Литники збирають в бункери і вивозять на дільницю підготовки і навантаження шихти.
Регенерація самозатверджуючих розчинів, які складаються з рідкого скла, здійснюється хімічним способом: обробкою піску в киплячому розчині лугу з концентрацією від 1 до 15% протягом 1 г при температурі 100°С. Після того, як плівка розчиниться, пісок відмивають від лугу водою просушують і поділяють на фракції просівом крізь сита. Ступінь вилучення рідкого скла сягає не менше 70%.
5.3.Переробка відходів, які отримуються обробкою металів тиском.
Оксид заліза вилучають із шламу, якай утворюється на прокатних станах. Технологія полягає в тому, що шлам осаджується у відстійниках для стічних вод прокатних станів. Шлам має вологість 20-30% і містить 2-3% і мастильних матеріалів. Його фільтрують від вологи. Після цього він містить 60-70% оксиду заліза. Для вилучення заліза існують два шляхи. Перший полягає в тому, що після відділення мастила на нього діють хімічними речовинами, а другий пропонує вилучати залізо після випалювання мастил, які присутні в шламі.
Вдосконалений технологічний процес вилучення заліза з шламу прокатних станів розроблений Т. Ісавою та іншими (Пат. США 4091545,30 травня 1979; фірма "Ніппен Кокан Кабушикі", Японія),
Шлам висушують для зниження вологості до 1-10% при температурі '0-200°С. При цьому використовують тепло, яке виділяється в теплообмінниках агломераційної установки, або тепло шламу, який відходить з гарячого прокатного стану. Для цього шлам частинами безперервно подається в зону виводу продукту агломерації, а звідти транспортується на гаряче сито в обертальний бункер агломераційної установки. Тут мастила вилучаються за рахунок випаровування. Обладнання і технологія цього процесу зображена на мал. 17.
Сировина визначеного складу подається живителем 3 на транспортер агломераційної печі А. Шихта загоряється, проходячи під запалювальним горном 4. Шихта спікається у міру проходження печі справа-наліво. Живильник 3 подає підсушений шлам в зону виводу продукту 6 агломераційній печі, періодично направляючи однакові порції шламу на транспортер :
Шлам нагрівається за рахунок тепла агломерату, разом з яким він поступає на розжарене сито 10, проходячи через дробилку 9. Внаслідок цих операцій вміст мастила в шламі значно знижується. Шлам 6 проходить крізь сито 10 і по транспортеру 11 потрапляє в поворотний бункер 12 для тимчасового зберігання. Частина агломерату, що залишилась на ситі 10, і подається для охолодження в холодильник 14. Частина охолоджуючого газу (або повітря), яка нагрівається в теплообміннику 14, подається вентилятором в сушарку для шламу 16, де він сушиться гарячими газами. А нам, який має високу вологість і містить мастило, збирається у відстійнику для стічних вод прокатних станів.
Якщо шлам, який подається в сушарку 16, містить 28% вологи і мастил, то після сушіння при 140-150°С протягом 15-20 хв. він містить уже 1,13% вологи і 06% мастила. З метою зниження в'язкості шламу бажано проводити його сушіння до вологості не більше 10%. Це забезпечує подачу шламу в живильник 5. 0станній подає висушений шлам в агломераційну піч яка на мал. 17 не зображена.
Вхідні гази, які містять порох та газоподібні продукти згоряння вбираються витяжним зонтом 7 у вологопиловловлювач, який на мал. 17 також не зображено. де проходить очищення газів, що виводяться ,з системи в атмосферу.
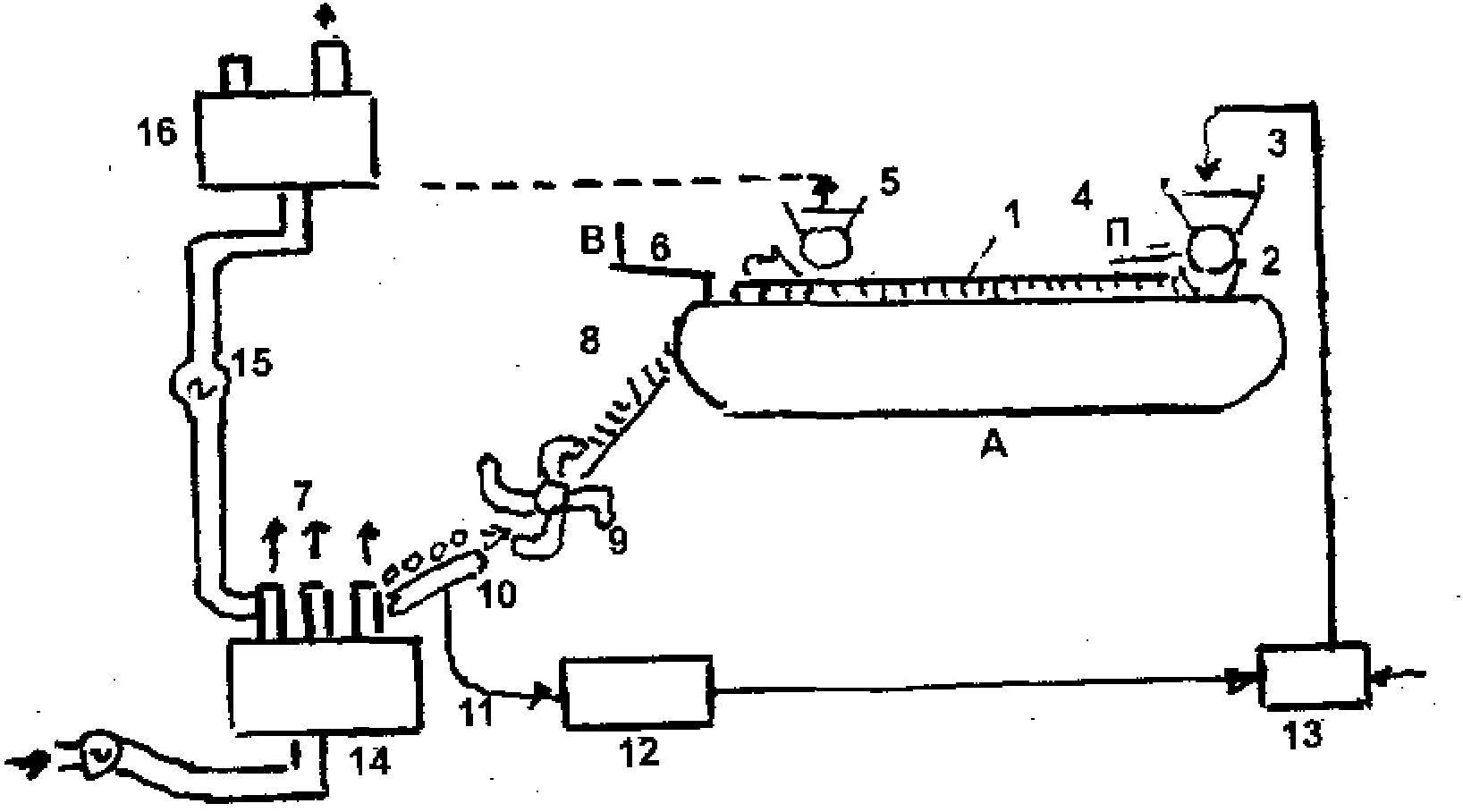
Мал 17 Схема процесу вилучення води і мастила із шламу прокатних станів з метою відділення оксиду заліза
Дегідратований і дегазований шлам і дрібні частинки агломерату оборотного бункера 12 змішують з сировиною для виробництв агломераті в необхідному співвідношенні в змішувачі 13. Із цієї суміші отримують гpaнули в грануляторі (на схемі його немає). Гранули подають в сировинний живитель 3.
5.4. Утилізація відходів, які отримують при обробці металів різанням.
Відпрацьовані ножівкові полотна на 70-80% використовуються в якості різців Недолік цих різців - обмежена глибина проходження їх у метал внаслідок плоскої форми інструмента.
Різці які виготовлені з відпрацьованих фрез, цього недоліку не мають тому, що дискові фрези вже мають кут осей від периферії до центру. Тому заточувати бокові кути різців з фрез не треба. Різці з відпрацьованих фрез готують, розрізуючи її дисковою пилою з алмазним або карборундовим напиленням на ряд заготівок, їх заточують і отримують серію різців. Коефіцієнт використання цих відходів сягає 0,5-0,6, а строк роботи великих фрез можна продовжити шляхом зменшення кількості зубців, у відпрацьованій фрезі, де переточка вже не можлива через зменшення діаметра інструмента і малої відстані між зубцями. Абразивним кругом сточують кожний другий зуб, щоб залишені зубці з'єднались між собою плавним закругленим переходом, як це зроблено у вихідній фрезі. За рахунок збільшення відстані між зубцями фрезу в міру її затуплення можна піддавати подальшій заточці.
Утилізація металевої тирси та стружки. Ці відходи утворюються при механічній обробці металів різанням, свердлінням, фрезеруванням, струганням, шліфуванням та при заточних операціях. Сучасне обладнання, як правило, забезпечується магнітними сепараторами для відділення частинок металу від частинок абразиву і мастильно-охолоджуючих рідин.
В умовах дрібносерійного виробництва на одному і тому ж обладнанні обробляють деталі із різних металів і сплавів. Найкращим методом утилізації є збір і відправка тирси і стружки металу на склад загального потоку металобрухту.
В масовому або великосерійному виробництві, де для обробки одного і гого ж виду деталей або виробів використовується поточне обладнання, можливості утилізації металобрухту значно ширші. Тому, що гранулометричний і хімічний склад металевого залишку характеризується повністю низначеними параметрами, що дуже важливо при застосуванні для переробки цих відходів методу порошкової металургії або металокераміки.
Окремим випадком утилізації залишків тирси або стружки є використання їх магнітних властивостей. Притягуючись до магніту, стружка або тирса угворює на полюсах магніту рихлі нарости. Якщо замкнути ці нарости між полюсами магніту і помістити в їх середовище швидкообертаючу деталь, то южна частинка металу тирси буде виступати як своєрідний різець. Тисячі таких різців значно прискорюють і полегшують полірування І доводку поверхні деталі до 13 класу чистоти. В цьому випадку необхідність в полірувальних пастах і промивних водах відпадає і дає економію в роботі.
Металева стружка і тирса можуть йти на переплавку, але спеціалісти вважають, що це порівняно дорогий метод утилізації відходу металу, тому що попереднє розділення сталей за марками - тривалий і трудомісткий процес і практично не вживається. Крім того, при переплавці зміщуваної стружки і тирси отримується сплав низької якості.
Метод гарячої штамповки виробів є новим методом утилізації змішаної тирси і стружки. Справа в тому, що метал відходів при температурі 1000-1200°С стає настільки пластичним, що безформна груда тирси і стружки перетворюється в монолітну деталь, яка не потребує подальшої обробки. Переваги цього методу утилізації відходів не тільки в тому, що процес проходить при більш низькій температурі, ніж при переплавці, але тут також відсутні витрати металу на угар і використовуються всі відходи без залишку.
НДІ надтвердих матеріалів України запропонував переробляти тирсу і стружку на порохоподібну сталь, що взагалі виключає процес лиття, і цей спосіб може бути використаний в будь-якому машинобудівному виробництві. Операції цього процесу полягають в тому, що сировину відмивають від мастил в бензині або гасі, завантажують в шаровий або вібраційний млин в середовище етилового спирту і подрібнюють до заданого ступеня помелу. Отриманий порошок змішують з розчином синтетичного каучуку в бензині, пресують на 500-тонному пресі. Пористість одержаного напівфабрикату складає 25-30%. Далі його спікають в захисній атмосфері або у вакуумі.
Наступна ковка і прокатка дозволяють отримати форму і розміри деталі або виробу, які мають зерна металу більш мілкі, ніж у литій сталі.
Спосіб вигідний тим, що дозволяє вводити в склад цієї сталі будь-які легуючі добавки і рівномірно розповсюджувати їх по всій масі металу. Встановлено, що стійкість і стабільність інструменту, який виготовлений за даною технологією, в три рази вищі, ніж у стандартних різців. А введення в суміш невеликої добавки титану підвищує твердість інструменту, не даючи йому схоплюватися з поверхнею оброблюваного металу, зменшує коефіцієнт тертя і збільшує строк служби різця,
Злитки і обрізки надтвердих сталей переплавляються у вакуумі або електрошлаковим методом в пульсуючому магнітному полі.
Зібраний металобрухт, відходи і брак відливок попередньо розплавляють у відкритій індукційній печі, зливають метал в чавунні кокілі, де він твердне, і таким чином дають злитки потрібного діаметра. Злитки відрізають з торців вулканітовим кругом і зварюють у заготовку, розміри і маса якої обумовлена габаритами майбутнього виробу.
Металевий порох із відходів механічної обробки одержують способом, який розробив С.М.Кауфман (Пат. США 4129248, 12 грудня 1979 p., фірма "Форд мотор Компані"). Технологічний процес полягає в тому, що на металеві залишки діють ударом при температурі нижчій температури переходу металу від пластичного до крихкого стану. Першу стадію удару проводять одночасно з введенням кріогенної речовини, а другу — при звичайній температурі в шаровому млині. Технологічна схема цього процесу зображена на мал. 18.
Стружку, тирсу і порох з низьколегованої сталі, до складу якої входять марганець, хром, нікель і молібден, по лінії 4 подають в шаровий млин З, куди одночасно додають кріогенну речовину - рідкий азот у вигляді -бризок. Частинки металу швидко замерзають І під впливом рухомих шарів перетворюються в порох 6, який має фракції різних розмірів від дрібних до великих. Другу стадію подрібнення проводять при кімнатній температурі також в шаровому млині. Матеріал, який отримують на другій стадії дроблення, пресують звичайним пресом 10 в злитки заданої густини в 6,6 г/см3. Форма для пресування металевого пороху виготовляється з необхідним допуском на усадку продукту пресування. Далі виріб заданої форми потрапляє в піч 12 для спікання при температурі 1100-1200оС.
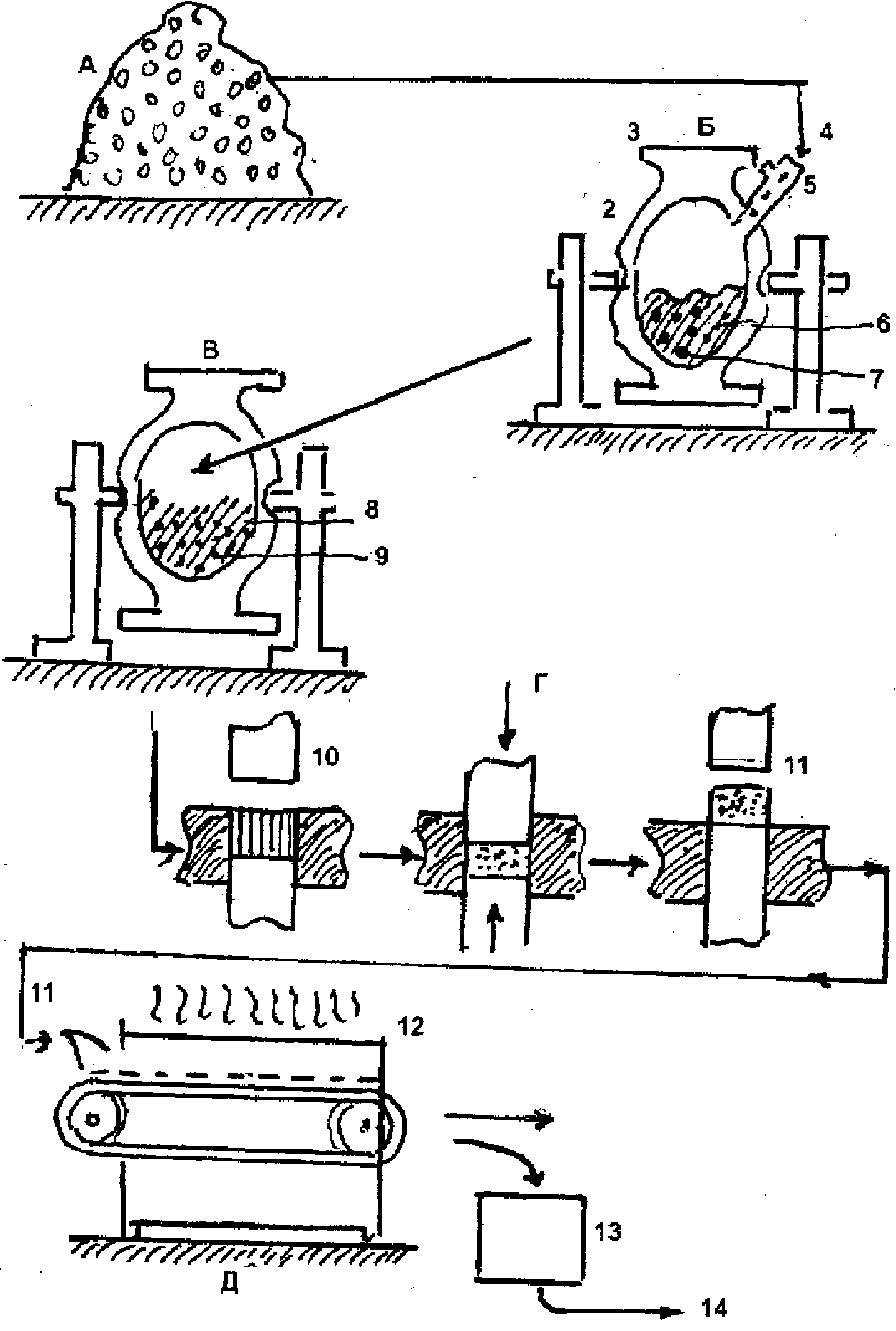
Мал. 18. Процес для покращання спікання залізного пороху, який отримується із подрібнених відходів